Mastering the PPE Vending Machine: Key Insights for B2B
Guide to Ppe Vending Machine
- Introduction: Navigating the Global Market for ppe vending machine
- Understanding ppe vending machine Types and Variations
- Key Industrial Applications of ppe vending machine
- Strategic Material Selection Guide for ppe vending machine
- In-depth Look: Manufacturing Processes and Quality Assurance for ppe vending machine
- Comprehensive Cost and Pricing Analysis for ppe vending machine Sourcing
- Spotlight on Potential ppe vending machine Manufacturers and Suppliers
- Essential Technical Properties and Trade Terminology for ppe vending machine
- Navigating Market Dynamics, Sourcing Trends, and Sustainability in the ppe vending machine Sector
- Frequently Asked Questions (FAQs) for B2B Buyers of ppe vending machine
- Strategic Sourcing Conclusion and Outlook for ppe vending machine
Introduction: Navigating the Global Market for ppe vending machine
In an increasingly safety-conscious global market, PPE vending machines have emerged as an innovative solution for ensuring easy access to personal protective equipment. As industries around the world—from construction to healthcare—prioritize worker safety, the demand for efficient, automated dispensing systems has surged. This guide aims to equip international B2B buyers, particularly those from Africa, South America, the Middle East, and Europe, with the critical insights needed to navigate this evolving landscape.
Understanding the nuances of PPE vending machines is essential for informed sourcing decisions. This comprehensive resource delves into various types of machines, the materials used in their construction, and the manufacturing and quality control processes that ensure reliability and safety. Additionally, it provides an overview of potential suppliers, associated costs, and current market trends.
Furthermore, we address common FAQs to clarify key aspects of purchasing and implementing PPE vending solutions. By leveraging this guide, B2B buyers will not only enhance their procurement strategies but also align their operations with global safety standards. As you explore the offerings within this guide, you will gain valuable insights that empower you to make strategic decisions, ensuring your workforce is protected and your business remains compliant in an ever-changing market.
Understanding ppe vending machine Types and Variations
Type Name | Key Distinguishing Features | Primary B2B Applications | Brief Pros & Cons for Buyers |
---|---|---|---|
Standard PPE Vending Machine | Offers a range of PPE items like gloves, masks, and helmets. | Manufacturing, Construction | Pros: Versatile and widely accepted. Cons: Limited customization options. |
Customizable PPE Vending Machine | Tailored to specific industry needs with adjustable inventory. | Oil & Gas, Chemical Processing | Pros: High adaptability and inventory control. Cons: Higher initial investment. |
Smart PPE Vending Machine | Equipped with IoT technology for inventory tracking and usage analytics. | Warehousing, Logistics | Pros: Real-time data insights. Cons: Requires reliable internet connectivity. |
Mobile PPE Vending Machine | Portable units designed for on-site use in remote locations. | Mining, Construction | Pros: Flexibility and mobility for hard-to-reach areas. Cons: Limited capacity compared to stationary units. |
Eco-Friendly PPE Vending Machine | Utilizes sustainable materials and energy-efficient designs. | Green Construction, Eco-Friendly Projects | Pros: Supports corporate sustainability goals. Cons: May have a higher upfront cost. |
Standard PPE Vending Machine
Standard PPE vending machines are designed to dispense a variety of personal protective equipment (PPE) such as gloves, face masks, and safety goggles. These machines are commonly found in industries like manufacturing and construction, where compliance with safety regulations is critical. When considering this type, buyers should evaluate the machine’s capacity and the range of PPE items it can hold, as well as the ease of restocking. While they are versatile and widely accepted, customization options may be limited.
Customizable PPE Vending Machine
Customizable PPE vending machines allow businesses to tailor inventory to specific industry requirements, making them ideal for sectors like oil and gas or chemical processing. These machines can be adjusted to accommodate varying sizes and types of PPE, ensuring that workers have access to the appropriate gear. B2B buyers should consider the potential for enhanced inventory control and user satisfaction. However, the initial investment can be higher compared to standard models, which may deter some buyers.
Smart PPE Vending Machine
Smart PPE vending machines incorporate IoT technology, enabling features like inventory tracking and usage analytics. These machines are particularly beneficial in warehousing and logistics, where monitoring PPE usage can lead to improved efficiency and compliance. When purchasing, buyers should assess the machine’s connectivity requirements and the reliability of their internet service. The real-time data insights offered are a significant advantage, but the need for stable internet can be a drawback in remote areas.
Mobile PPE Vending Machine
Mobile PPE vending machines are designed for portability, making them suitable for on-site use in industries such as mining and construction. Their flexibility allows for easy relocation to different job sites, providing immediate access to necessary PPE. Buyers should consider the machine’s capacity and the types of PPE it can dispense, as mobility may come at the expense of storage space. While these machines offer significant advantages in terms of accessibility, they may not hold as much inventory as stationary units.
Eco-Friendly PPE Vending Machine
Eco-friendly PPE vending machines focus on sustainability by utilizing recyclable materials and energy-efficient designs. These machines are increasingly popular in green construction and eco-friendly projects, supporting businesses’ sustainability goals. When evaluating these options, B2B buyers should weigh the benefits of aligning with environmental standards against potentially higher upfront costs. While they contribute positively to corporate responsibility initiatives, the initial investment may be a consideration for budget-conscious buyers.
Related Video: Machine Learning in 2024 – Beginner’s Course
Key Industrial Applications of ppe vending machine
Industry/Sector | Specific Application of PPE Vending Machine | Value/Benefit for the Business | Key Sourcing Considerations for this Application |
---|---|---|---|
Construction | On-site safety gear distribution | Ensures immediate access to PPE, reducing downtime | Compliance with local safety regulations, stock variety |
Manufacturing | Personal protective equipment replenishment | Streamlines supply chain, enhances worker safety | Durable machines, ease of inventory management |
Oil & Gas | Hazardous environment safety equipment | Minimizes risk of accidents, ensures compliance | Weather-resistant units, secure payment options |
Mining | Emergency PPE access | Provides quick access during emergencies, saves lives | Robust design for harsh conditions, remote monitoring |
Healthcare | Infection control supplies | Promotes health and safety, reduces contamination risks | Sterilization features, support for diverse PPE types |
Construction
In the construction industry, PPE vending machines are strategically placed on job sites to provide immediate access to essential safety gear such as helmets, gloves, and high-visibility clothing. This not only minimizes downtime due to workers searching for equipment but also ensures compliance with safety regulations. For international buyers, particularly in Africa and South America, it is crucial to ensure that the vending machines are compliant with local safety standards and can accommodate a wide variety of PPE to meet diverse worker needs.
Manufacturing
Manufacturers can benefit significantly from PPE vending machines by implementing them in production areas where personal protective equipment is frequently needed. These machines can streamline the supply chain by ensuring that workers have quick access to gloves, goggles, and ear protection, thus enhancing overall safety. Buyers from the Middle East and Europe should focus on sourcing machines that are durable, easy to maintain, and equipped with inventory management systems to track usage and restocking needs efficiently.
Oil & Gas
In the oil and gas sector, PPE vending machines are essential for providing safety equipment in hazardous environments. These machines can dispense specialized gear like flame-resistant clothing and respirators, crucial for compliance with industry regulations. For international B2B buyers in regions like Europe, it is important to select machines that are weather-resistant and equipped with secure payment options to ensure reliability in remote locations.
Mining
The mining industry often faces unique challenges regarding worker safety, especially in emergencies. PPE vending machines installed in mines allow for rapid access to emergency gear such as respirators and protective suits, thereby potentially saving lives. Buyers, particularly from Africa, should consider machines that are robust enough to withstand harsh conditions and may benefit from features like remote monitoring to ensure constant operation.
Healthcare
In healthcare settings, PPE vending machines are pivotal for infection control by providing quick access to masks, gloves, and gowns. These machines help reduce the risk of contamination and promote a safer environment for both healthcare workers and patients. Buyers from Europe and South America should prioritize machines with sterilization capabilities and those that can support a diverse range of PPE types to meet varying healthcare demands effectively.
Related Video: Select PPE Vending Machine Solution
Strategic Material Selection Guide for ppe vending machine
When selecting materials for PPE vending machines, it is crucial to consider various factors that impact performance, durability, and compliance with international standards. Below is an analysis of four common materials used in the construction of PPE vending machines, focusing on their properties, advantages, disadvantages, and considerations for international buyers.
1. Stainless Steel
Key Properties:
Stainless steel is known for its excellent corrosion resistance, high strength, and ability to withstand high temperatures. It typically has a temperature rating of up to 800°C and can handle pressures exceeding 2000 psi, depending on the grade.
Pros & Cons:
The primary advantage of stainless steel is its durability and resistance to rust and corrosion, making it suitable for outdoor environments. However, it can be more expensive than other materials, and manufacturing processes may require specialized techniques, increasing complexity.
Impact on Application:
Stainless steel is compatible with various media, including water, oils, and chemicals, making it versatile for different PPE types. Its aesthetic appeal also contributes to a professional appearance in retail settings.
Considerations for International Buyers:
Buyers from regions like Europe and the Middle East should ensure compliance with standards such as ASTM A240 for stainless steel. Additionally, understanding local sourcing options can help mitigate costs.
2. Polycarbonate
Key Properties:
Polycarbonate is a lightweight, impact-resistant thermoplastic with a temperature tolerance of -40°C to 120°C. It is also resistant to UV radiation and can handle moderate chemical exposure.
Pros & Cons:
The lightweight nature of polycarbonate makes it easy to handle and install, while its impact resistance reduces the risk of damage during use. However, it may not be as durable as metals in harsh environments, and its chemical resistance can vary significantly based on the specific formulation.
Impact on Application:
Polycarbonate is particularly suitable for transparent components of PPE vending machines, such as viewing windows. Its compatibility with various PPE items, including goggles and face shields, enhances visibility and user experience.
Considerations for International Buyers:
Buyers should look for compliance with relevant standards such as ASTM D648 for heat resistance. In regions like Africa and South America, sourcing polycarbonate from local manufacturers can reduce shipping costs and lead times.
3. Mild Steel
Key Properties:
Mild steel is characterized by its good tensile strength and ductility, with a typical temperature rating of up to 300°C. However, it is prone to corrosion without protective coatings.
Pros & Cons:
Mild steel is cost-effective and easy to fabricate, making it a popular choice for many applications. The downside is its susceptibility to rust, which necessitates additional coatings or treatments, potentially increasing long-term maintenance costs.
Impact on Application:
Mild steel is suitable for structural components of PPE vending machines but may require protective coatings for outdoor use. Its strength can support heavy loads, making it ideal for machines dispensing heavier PPE items.
Considerations for International Buyers:
Buyers in regions with high humidity or corrosive environments, such as coastal areas in Brazil, should prioritize corrosion-resistant coatings. Understanding local regulations on material usage can also prevent compliance issues.
4. Aluminum
Key Properties:
Aluminum is lightweight, corrosion-resistant, and has a temperature rating of up to 600°C. Its strength-to-weight ratio makes it an attractive option for various applications.
Pros & Cons:
The key advantage of aluminum is its resistance to corrosion and lightweight nature, which facilitates easy installation and transport. However, it can be more expensive than mild steel and may require additional treatments for enhanced strength.
Impact on Application:
Aluminum is ideal for components that require both strength and lightness, such as frames and supports in PPE vending machines. Its aesthetic appeal can also enhance the overall design.
Considerations for International Buyers:
When sourcing aluminum, buyers should be aware of standards such as ASTM B221 for aluminum extrusions. In Europe, compliance with EN 573-3 is essential, especially for applications requiring specific alloy grades.
Summary Table
Material | Typical Use Case for PPE Vending Machine | Key Advantage | Key Disadvantage/Limitation | Relative Cost (Low/Med/High) |
---|---|---|---|---|
Stainless Steel | Structural components, outdoor applications | Excellent corrosion resistance | Higher cost, manufacturing complexity | High |
Polycarbonate | Transparent viewing panels, lightweight components | Lightweight, impact-resistant | Moderate chemical resistance | Medium |
Mild Steel | Structural framework, heavy load applications | Cost-effective, easy to fabricate | Susceptible to corrosion | Low |
Aluminum | Frames and supports, aesthetically pleasing designs | Lightweight, corrosion-resistant | Higher cost than mild steel | Medium |
In-depth Look: Manufacturing Processes and Quality Assurance for ppe vending machine
Manufacturing a PPE vending machine involves a series of well-defined processes and stringent quality assurance measures. For international B2B buyers, particularly those from Africa, South America, the Middle East, and Europe, understanding these aspects is crucial for ensuring product reliability and compliance with international standards.
Manufacturing Processes
Material Preparation
The first step in the manufacturing process is material preparation. This involves sourcing high-quality materials that meet specific durability and safety standards. Common materials used include:
- Metal Alloys: Often used for the machine frame and components for their strength and resistance to wear.
- Plastics: Used for external casing and internal mechanisms, selected for their lightweight and corrosion-resistant properties.
- Electronic Components: Such as sensors and payment systems, which must comply with electrical safety standards.
Buyers should verify that suppliers use certified materials by requesting Material Safety Data Sheets (MSDS) and certifications.
Forming
The forming stage includes shaping materials into the desired components. Techniques used in this phase may include:
- Metal Stamping: For creating precise metal parts.
- Injection Molding: Commonly used for plastic components to ensure uniformity and strength.
- CNC Machining: For high-precision components, ensuring tight tolerances necessary for mechanical functionality.
It is essential for B2B buyers to inquire about the technologies used and their implications for product longevity and performance.
Assembly
Once all components are formed, the assembly process begins. This stage can involve:
- Automated Assembly Lines: For high-volume production, ensuring efficiency and consistency.
- Manual Assembly: In cases where precision is critical, such as assembling electronic components.
Buyers should consider suppliers with robust assembly protocols to minimize errors and enhance product integrity.
Finishing
The finishing stage involves applying protective coatings and aesthetic features. This may include:
- Powder Coating: For corrosion resistance and improved aesthetics.
- Quality Control Inspections: Conducted at various stages to ensure all parts meet specifications.
B2B buyers should ensure that finishing processes do not compromise the machine’s functionality and that they comply with relevant health and safety regulations.
Quality Assurance
Quality assurance (QA) is critical in manufacturing PPE vending machines. International standards and industry-specific certifications play a vital role in ensuring product reliability.
Relevant International Standards
Buyers should look for compliance with:
- ISO 9001: This standard focuses on quality management systems, ensuring a consistent quality of products and services.
- CE Marking: Indicates compliance with European health, safety, and environmental protection standards.
- API Standards: For machines that incorporate advanced technology, such as automated dispensing systems.
Understanding these certifications can help buyers assess the credibility and reliability of suppliers.
Quality Control Checkpoints
Quality control is typically divided into several checkpoints:
- Incoming Quality Control (IQC): Inspecting raw materials before production to ensure they meet specified requirements.
- In-Process Quality Control (IPQC): Monitoring the manufacturing process to identify defects early.
- Final Quality Control (FQC): Conducting comprehensive testing on finished products before shipment.
Buyers can request detailed reports from suppliers on these checkpoints to gauge their commitment to quality.
Common Testing Methods
Testing methods for PPE vending machines may include:
- Functional Testing: Ensuring all mechanical and electronic components operate as intended.
- Stress Testing: Evaluating the machine’s durability under extreme conditions.
- Safety Testing: Verifying compliance with electrical safety and operational safety standards.
B2B buyers should request access to test results and certifications to ensure transparency.
Verifying Supplier Quality Control
To ensure suppliers maintain high-quality standards, international B2B buyers can adopt several strategies:
- Audits: Conduct regular audits of supplier facilities to assess their manufacturing and quality assurance processes. This can be done through third-party inspection services, which provide an unbiased evaluation.
- Reports and Documentation: Request detailed QC reports that outline testing methods, results, and corrective actions taken for any non-conformance.
- Third-Party Inspection: Engage third-party inspection agencies to conduct independent quality checks at various stages of production.
Quality Control and Certification Nuances
Navigating the landscape of quality control and certifications can be complex, especially for buyers from diverse regions. Here are some key considerations:
- Regional Standards: Understand that different regions may have specific standards. For instance, CE marking is crucial for European markets, while other regions may prioritize different certifications.
- Cultural Differences: Be aware of cultural differences in manufacturing practices and quality expectations. This can impact supplier relationships and negotiations.
- Supply Chain Risks: Consider geopolitical factors that might affect supply chains and the availability of certified products.
By focusing on these manufacturing processes and quality assurance practices, B2B buyers can make informed decisions, ensuring they partner with reliable suppliers who deliver high-quality PPE vending machines that meet international standards.
Related Video: SMART Quality Control for Manufacturing
Comprehensive Cost and Pricing Analysis for ppe vending machine Sourcing
When sourcing PPE vending machines, understanding the comprehensive cost structure and pricing analysis is essential for international B2B buyers. This section outlines the critical components of cost and pricing factors, offering actionable insights for effective sourcing decisions.
Cost Components
-
Materials: The quality of materials used in PPE vending machines directly impacts the overall cost. High-grade steel, durable plastics, and advanced electronic components contribute to a higher upfront price but can enhance longevity and reliability.
-
Labor: Labor costs vary significantly across regions. For example, manufacturing in countries with lower labor costs may initially seem attractive, but consider the potential trade-offs in quality and after-sales support.
-
Manufacturing Overhead: This includes utilities, rent, and other indirect costs associated with production. Understanding the overhead structure of a supplier can help in negotiating better pricing.
-
Tooling: Custom tooling for specialized designs or features can be a significant investment. Buyers should assess whether the added functionality justifies the tooling costs.
-
Quality Control (QC): Effective QC processes ensure that the machines meet industry standards and certifications. Investing in robust QC can prevent costly returns and reputational damage.
-
Logistics: Shipping costs can vary widely based on the origin of the machine, destination, and chosen Incoterms. Additionally, consider customs duties and tariffs that may apply.
-
Margin: Suppliers will typically have a markup on their costs. Understanding typical margins in the industry can provide leverage during negotiations.
Price Influencers
-
Volume/MOQ: Minimum order quantities (MOQ) can significantly affect pricing. Larger orders often lead to bulk discounts, which can reduce the unit cost substantially.
-
Specifications/Customization: Customized machines tailored to specific needs will usually come at a premium. Clearly defining your requirements can help avoid unnecessary costs.
-
Materials: Opting for premium materials can lead to higher initial costs but may result in lower Total Cost of Ownership (TCO) due to reduced maintenance and replacement needs.
-
Quality/Certifications: Machines that meet international safety and quality certifications may cost more upfront. However, compliance can reduce liability risks and enhance marketability.
-
Supplier Factors: The reputation, reliability, and location of the supplier can influence pricing. Established suppliers may offer better warranties and support, justifying a higher price.
-
Incoterms: The choice of Incoterms affects the responsibilities and costs associated with shipping. Understanding these terms can help buyers better manage logistics costs.
Buyer Tips
-
Negotiation: Leverage volume and long-term partnerships to negotiate better pricing. Be prepared to discuss your needs and expectations clearly.
-
Cost Efficiency: Analyze not just the purchase price but the TCO, including maintenance, logistics, and potential downtime costs. This holistic view will guide more informed purchasing decisions.
-
Pricing Nuances: International buyers should be aware of currency fluctuations and economic conditions in both the supplier’s and buyer’s country, as these can impact overall costs.
-
Due Diligence: Conduct thorough research on suppliers, including their production capabilities, quality assurance practices, and past performance. Consider seeking testimonials or references from other buyers in similar markets.
-
Market Conditions: Stay informed about market trends and pricing fluctuations in the PPE vending machine sector. Being aware of supply chain disruptions or shifts in demand can provide a competitive edge in negotiations.
Disclaimer
The prices discussed in this section are indicative and may vary based on specific circumstances, negotiations, and market conditions. It is advisable to conduct thorough market research and obtain multiple quotes for accurate budgeting.
Spotlight on Potential ppe vending machine Manufacturers and Suppliers
- (No specific manufacturer data was available or requested for detailed profiling in this section for ppe vending machine.)*
Essential Technical Properties and Trade Terminology for ppe vending machine
Key Technical Properties of PPE Vending Machines
When considering the procurement of PPE vending machines, understanding their technical specifications is crucial for ensuring reliability and compliance with safety standards. Here are some essential properties to evaluate:
-
Material Grade
The material used in the construction of a PPE vending machine significantly impacts its durability and performance. Common materials include stainless steel, which offers corrosion resistance, and high-grade plastics, which can be lightweight yet sturdy. Buyers should prioritize machines made from materials that can withstand harsh environmental conditions, particularly in industrial settings. -
Capacity and Size
The capacity of a vending machine refers to how many PPE items it can hold. This is typically measured in terms of the number of compartments and the size of each compartment. Understanding the required capacity is essential for ensuring that the machine meets the demands of your workforce, especially in high-traffic areas where quick access to PPE is vital. -
Power Requirements
PPE vending machines may require different power sources, such as standard electrical outlets or battery power. Knowing the power requirements helps buyers assess installation needs and compatibility with existing infrastructure. Machines with energy-efficient designs can also reduce operational costs over time.
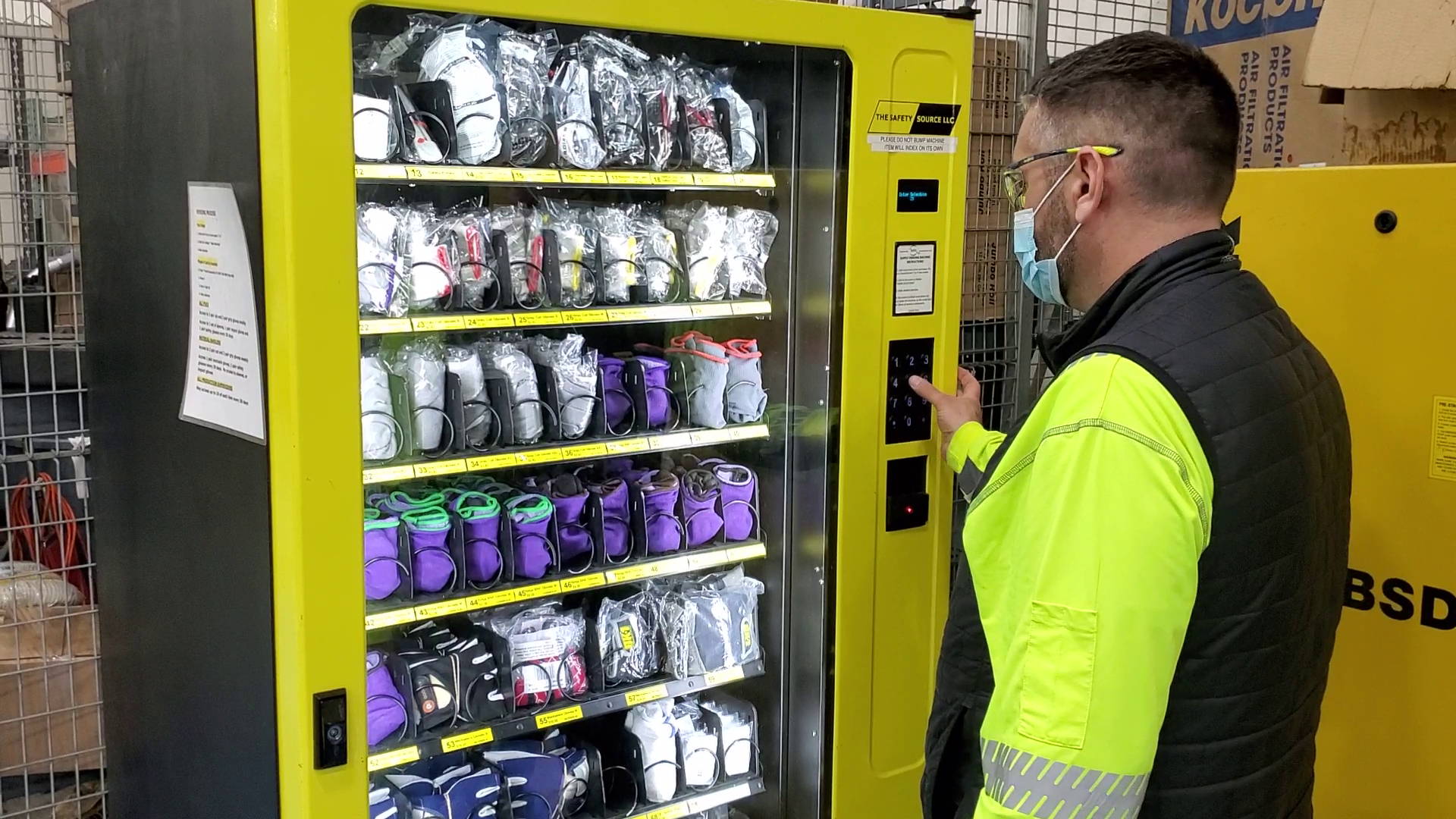
Illustrative Image (Source: Google Search)
-
User Interface and Accessibility
A user-friendly interface is crucial for ensuring quick and efficient access to PPE. Features like touchscreen displays, multiple language options, and accessibility for individuals with disabilities enhance usability. For B2B buyers, investing in machines with intuitive interfaces can lead to higher employee compliance and satisfaction. -
Security Features
Security is paramount in environments where PPE theft or misuse can occur. Key security features to consider include lockable compartments, tamper-proof designs, and inventory tracking systems. These elements not only protect the investment but also ensure that PPE is available when needed.
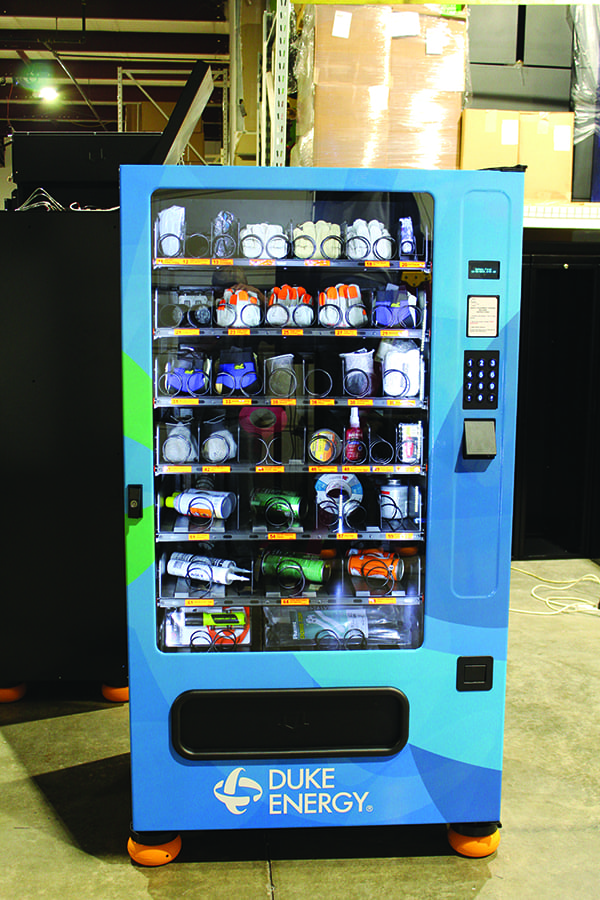
Illustrative Image (Source: Google Search)
- Compliance Standards
Compliance with local and international safety standards is essential for PPE vending machines. Buyers should verify that machines meet relevant regulations, such as those set by the Occupational Safety and Health Administration (OSHA) or equivalent bodies in their regions. Compliance ensures that the PPE dispensed is safe and effective.
Common Trade Terminology
Understanding industry jargon is essential for effective communication and negotiation in the procurement process. Here are key terms that every B2B buyer should know:
-
OEM (Original Equipment Manufacturer)
This term refers to companies that produce parts and equipment that may be marketed by another manufacturer. For PPE vending machines, identifying the OEM can help buyers understand the quality and reliability of the components used. -
MOQ (Minimum Order Quantity)
MOQ denotes the smallest quantity of a product that a supplier is willing to sell. Being aware of MOQs is critical for budgeting and inventory planning, particularly for international buyers who may need to manage shipping costs and storage space. -
RFQ (Request for Quotation)
An RFQ is a formal document issued by a buyer to solicit price quotes from suppliers. It typically includes specifications, quantities, and delivery requirements. Crafting a detailed RFQ can lead to competitive pricing and better supplier relationships. -
Incoterms (International Commercial Terms)
These are predefined commercial terms published by the International Chamber of Commerce (ICC) that clarify the responsibilities of buyers and sellers in international transactions. Familiarity with Incoterms is essential for international buyers to understand shipping costs, risk transfer, and delivery obligations. -
Lead Time
Lead time refers to the time it takes from placing an order to receiving the goods. Understanding lead times is crucial for effective supply chain management, especially in industries where PPE is critical for safety and compliance. -
Warranty and Service Agreement
This term encompasses the guarantees provided by the manufacturer regarding the performance and reliability of the vending machine. Buyers should scrutinize warranty terms and service agreements to ensure support for maintenance and repairs, which can impact long-term operational efficiency.
By familiarizing themselves with these technical properties and trade terminologies, international B2B buyers can make informed decisions when purchasing PPE vending machines, ultimately enhancing workplace safety and operational efficiency.
Navigating Market Dynamics, Sourcing Trends, and Sustainability in the ppe vending machine Sector
Market Overview & Key Trends
The PPE vending machine sector is experiencing significant growth driven by various global factors, including heightened health awareness and regulatory changes due to the COVID-19 pandemic. International B2B buyers, particularly from Africa, South America, the Middle East, and Europe, should note that the demand for automated dispensing solutions is surging. This trend is primarily fueled by the increasing need for accessible personal protective equipment (PPE) in high-risk environments such as construction sites, healthcare facilities, and public spaces.
Emerging technologies are also shaping the PPE vending machine market. Innovations such as IoT connectivity allow for real-time inventory management and predictive analytics, which enhance operational efficiency. Additionally, contactless payment systems are becoming standard, catering to a tech-savvy clientele while ensuring safety. Buyers should prioritize suppliers who integrate these technologies into their vending solutions, as this can lead to reduced operational costs and increased customer satisfaction.
Furthermore, the market dynamics indicate a shift towards customization and scalability. Businesses are now looking for tailored solutions that can adapt to specific industry needs. For instance, a PPE vending machine designed for a healthcare setting may require different features than one for a construction site. Buyers should consider suppliers that offer modular designs and flexible inventory options to meet the diverse needs of their operations.
Sustainability & Ethical Sourcing in B2B
Sustainability has become a pivotal concern in the PPE vending machine sector, with environmental impacts prompting buyers to seek more responsible sourcing practices. The production and disposal of PPE contribute significantly to plastic waste, raising the need for sustainable materials and processes. B2B buyers should prioritize partnerships with manufacturers that utilize recycled materials and sustainable manufacturing practices to mitigate their environmental footprint.
Moreover, ethical sourcing is increasingly crucial in the global supply chain. Buyers must ensure that their suppliers adhere to labor laws and ethical practices, particularly in regions where exploitation is a risk. Certifications such as Fair Trade and Global Organic Textile Standard (GOTS) can serve as indicators of a supplier’s commitment to ethical practices. By opting for vendors with these certifications, businesses not only bolster their corporate social responsibility (CSR) profile but also cater to a growing consumer base that values sustainability.
Additionally, the introduction of “green” PPE products—such as biodegradable masks and recyclable face shields—presents an opportunity for B2B buyers to enhance their sustainability credentials. Incorporating these eco-friendly options into vending machines not only meets regulatory demands but also aligns with the values of environmentally conscious consumers.
Brief Evolution/History
The PPE vending machine concept has evolved significantly over the past few decades, transitioning from simple dispensing units to sophisticated automated systems. Initially, these machines primarily served basic needs in industrial settings. However, the onset of global health crises, particularly the COVID-19 pandemic, catalyzed a transformation in the sector.
The modern PPE vending machine now incorporates advanced technology, including touchless interfaces, cloud connectivity, and inventory management systems, making them indispensable in various industries. This evolution reflects the changing landscape of workplace safety and health, emphasizing the need for immediate access to protective equipment. As the sector continues to innovate, B2B buyers are encouraged to stay informed about the latest advancements to ensure they are sourcing the most effective and efficient solutions.
Related Video: Global Trade & Logistics – What is Global Trade?
Frequently Asked Questions (FAQs) for B2B Buyers of ppe vending machine
-
What should I consider when vetting suppliers for PPE vending machines?
When vetting suppliers, focus on their industry reputation, experience, and client testimonials. Verify their certifications, such as ISO or local safety standards, to ensure compliance with regulatory requirements in your region. It’s also important to assess their production capacity and lead times. Request samples or case studies of previous installations to gauge their reliability and the quality of their machines. Engage in discussions about their after-sales support and warranty policies, as ongoing service is crucial for maintaining operational efficiency. -
Can PPE vending machines be customized to fit specific business needs?
Yes, many suppliers offer customization options for PPE vending machines. You can request alterations in size, design, and features to align with your operational requirements. For instance, you might want to integrate cashless payment systems or specific branding elements. Before placing an order, communicate your needs clearly and confirm the supplier’s ability to meet these specifications. Ensure that any modifications comply with local regulations and safety standards. -
What are the typical minimum order quantities (MOQ) and lead times for PPE vending machines?
Minimum order quantities can vary significantly based on the supplier and the complexity of the machines. Typically, MOQs range from 1 to 10 units for standard models, while custom orders may require larger quantities. Lead times can also differ; expect anywhere from 4 to 12 weeks depending on customization, production schedules, and shipping logistics. Always clarify these details upfront to align your procurement strategy with your operational timeline. -
What payment terms should I expect when purchasing PPE vending machines?
Payment terms can vary widely among suppliers, but common practices include a 30% deposit upon order confirmation and the balance prior to shipment. Some suppliers may offer financing options or payment plans, particularly for larger orders. Always review the supplier’s payment terms and negotiate if necessary to ensure they align with your cash flow management strategies. Additionally, consider using secure payment methods to mitigate the risk of fraud. -
How can I ensure the quality and safety of PPE vending machines?
To ensure quality, request detailed information about the manufacturing processes and materials used in the machines. Verify that the machines comply with international safety standards and possess relevant certifications. Conduct a thorough quality assurance (QA) audit by asking for test results or certifications from third-party testing labs. Additionally, consider implementing a trial period or pilot program to evaluate the machine’s performance before committing to a larger order. -
What logistics challenges should I anticipate when importing PPE vending machines?
Logistics challenges may include customs clearance, shipping delays, and additional tariffs or taxes. Familiarize yourself with the import regulations specific to your country, as these can vary significantly across regions. Work closely with your supplier to understand their shipping practices and timelines. Engaging a reliable freight forwarder with experience in handling PPE equipment can also help mitigate potential logistics issues and streamline the import process. -
How should disputes with suppliers be handled?
Disputes can arise due to delivery delays, product defects, or miscommunication regarding specifications. It’s crucial to have a clear contract that outlines terms and conditions, including dispute resolution processes. Start by addressing the issue directly with the supplier through formal communication. If necessary, involve a third party for mediation or arbitration. Maintaining a professional and solution-focused approach can help preserve the business relationship while resolving the issue effectively. -
What support can I expect post-purchase for PPE vending machines?
Post-purchase support varies by supplier but typically includes installation assistance, training for your staff, and ongoing technical support. Ensure the supplier provides a clear outline of their after-sales services, including warranty details and maintenance schedules. Some suppliers may offer remote support options or on-site visits for repairs. Establishing a good line of communication with your supplier post-purchase is essential for addressing any operational challenges that may arise.
Strategic Sourcing Conclusion and Outlook for ppe vending machine
In the rapidly evolving landscape of personal protective equipment (PPE), the integration of vending machines presents a transformative opportunity for businesses across various sectors. Strategic sourcing of PPE vending machines enables organizations to enhance workplace safety, streamline supply chains, and respond swiftly to fluctuating demand. By leveraging local suppliers in regions such as Africa, South America, the Middle East, and Europe, companies can reduce costs and ensure timely access to essential protective gear.
Key takeaways include the importance of evaluating supplier reliability, understanding regional compliance regulations, and considering the technological capabilities of vending solutions. Prioritizing these factors not only mitigates risks but also fosters sustainable business practices.
As we look to the future, the demand for PPE vending machines is set to increase, driven by heightened health awareness and regulatory requirements. International B2B buyers are encouraged to embrace this trend, investing in innovative solutions that will safeguard their workforce and enhance operational resilience. Now is the time to explore strategic partnerships that align with your business goals, ensuring a safer and more efficient workplace for all.