Mastering Lottery Vending Machines: Your Essential B2B
Guide to Lottery Vending Machines
- Introduction: Navigating the Global Market for lottery vending machines
- Understanding lottery vending machines Types and Variations
- Key Industrial Applications of lottery vending machines
- Strategic Material Selection Guide for lottery vending machines
- In-depth Look: Manufacturing Processes and Quality Assurance for lottery vending machines
- Comprehensive Cost and Pricing Analysis for lottery vending machines Sourcing
- Spotlight on Potential lottery vending machines Manufacturers and Suppliers
- Essential Technical Properties and Trade Terminology for lottery vending machines
- Navigating Market Dynamics, Sourcing Trends, and Sustainability in the lottery vending machines Sector
- Frequently Asked Questions (FAQs) for B2B Buyers of lottery vending machines
- Strategic Sourcing Conclusion and Outlook for lottery vending machines
Introduction: Navigating the Global Market for lottery vending machines
In the evolving landscape of global commerce, lottery vending machines represent a lucrative opportunity for businesses seeking to tap into the burgeoning gaming and entertainment sectors. These machines not only streamline the ticket purchasing process but also enhance the consumer experience, making them an essential asset for retailers and operators in diverse markets. As demand for innovative gaming solutions grows, understanding the intricacies of lottery vending machines becomes critical for international B2B buyers.
This guide serves as a comprehensive resource, detailing various types of lottery vending machines, including self-service kiosks and multi-game units. It delves into the materials used in manufacturing, ensuring durability and compliance with industry standards, as well as quality control measures that guarantee reliability. Additionally, we provide insights into reputable suppliers, pricing structures, and market trends that can influence purchasing decisions.
For buyers from Africa, South America, the Middle East, and Europe—regions with unique regulatory environments and consumer behaviors—this guide empowers informed sourcing decisions. By addressing frequently asked questions and providing actionable insights, we aim to equip businesses with the knowledge necessary to navigate the complexities of the global lottery vending machine market. Whether you’re looking to expand your offerings or enhance customer engagement, understanding these machines is key to unlocking new revenue streams and staying competitive in a dynamic marketplace.
Understanding lottery vending machines Types and Variations
Type Name | Key Distinguishing Features | Primary B2B Applications | Brief Pros & Cons for Buyers |
---|---|---|---|
Traditional Lottery Vending | Mechanical or electronic systems for ticket sales | Retail outlets, convenience stores | Reliable and straightforward; may require regular maintenance |
Interactive Touchscreen Vending | User-friendly interfaces with game options | Casinos, entertainment venues | Engaging for users; higher initial investment |
Self-Serve Kiosk | Automated systems with ticket printing capabilities | Airports, train stations | Space-efficient; potential technical issues |
Mobile Lottery Vending Unit | Portable units for events and festivals | Outdoor events, fairs | Flexible and adaptable; may have limited ticket options |
Hybrid Lottery Machines | Combination of traditional and digital interfaces | Shopping malls, large retail spaces | Versatile; can cater to a wider audience, but complex to manage |
Traditional Lottery Vending Machines
Traditional lottery vending machines typically utilize mechanical or electronic systems to dispense lottery tickets. They are often placed in retail outlets and convenience stores, making them accessible to a wide range of customers. When considering a purchase, B2B buyers should evaluate the machine’s reliability and the availability of technical support. While these machines are generally straightforward to operate, they may require regular maintenance to ensure optimal performance.
Interactive Touchscreen Vending Machines
Interactive touchscreen vending machines offer a modern twist to lottery ticket sales, featuring user-friendly interfaces that allow customers to engage with various game options. Commonly found in casinos and entertainment venues, these machines enhance the user experience and can lead to higher sales. However, buyers should be aware of the higher initial investment and ongoing software updates required to keep the machines current and appealing to customers.
Self-Serve Kiosks
Self-serve kiosks are automated systems equipped with ticket printing capabilities, making them ideal for high-traffic areas like airports and train stations. They optimize space and streamline the ticket purchasing process for customers. B2B buyers should consider the potential for technical issues, as these machines require reliable internet connectivity and regular software updates. Their efficiency can lead to increased sales, provided that the kiosks are maintained properly.
Mobile Lottery Vending Units
Mobile lottery vending units are portable machines designed for use at outdoor events, fairs, and festivals. These units provide flexibility and adaptability, allowing businesses to reach customers in various locations. Buyers should consider the limited ticket options available on mobile units compared to stationary machines. However, the ability to attract new customers at events can be a significant advantage for those looking to expand their market presence.
Hybrid Lottery Machines
Hybrid lottery machines combine traditional ticket vending with digital interfaces, allowing for a versatile approach to sales. These machines are suitable for shopping malls and large retail spaces, catering to a diverse audience. B2B buyers must weigh the benefits of versatility against the complexity of managing such systems. While hybrid machines can appeal to both traditional and modern customers, they may require more extensive training for staff and ongoing maintenance.
Key Industrial Applications of lottery vending machines
Industry/Sector | Specific Application of Lottery Vending Machines | Value/Benefit for the Business | Key Sourcing Considerations for this Application |
---|---|---|---|
Retail | Point-of-Sale Lottery Ticket Sales | Increased foot traffic and sales opportunities | Compliance with local gaming regulations, machine reliability |
Hospitality | Integration in Casinos and Hotels | Enhanced customer experience and additional revenue | Customization options, ease of maintenance |
Transportation | Ticket Sales at Airports and Train Stations | Convenience for travelers, streamlined operations | Security features, payment method compatibility |
Sports Venues | On-site Lottery Sales during Events | Boosted engagement and revenue during events | Integration with event management systems, customer service support |
Online Platforms | Virtual Lottery Ticket Sales via Kiosks | Expanded market reach and customer base | Software integration capabilities, data security measures |
Retail Applications
In the retail sector, lottery vending machines serve as point-of-sale systems for lottery tickets, providing customers with easy access to purchase tickets while shopping. This application not only increases foot traffic but also boosts overall sales, as customers are more likely to make impulse purchases. International B2B buyers must ensure compliance with local gaming regulations and prioritize machines that are reliable and user-friendly to facilitate a smooth transaction process.
Hospitality Integration
In casinos and hotels, lottery vending machines enhance the customer experience by providing guests with convenient access to lottery tickets. This integration allows establishments to generate additional revenue streams while keeping patrons entertained. Buyers in this sector should look for machines that offer customization options to fit the branding of their establishments and ensure ease of maintenance to minimize downtime.
Transportation Sector
Lottery vending machines are increasingly deployed in transportation hubs, such as airports and train stations, where travelers can purchase tickets conveniently. This application addresses the need for quick and easy access to lottery products, catering to the fast-paced environment of travel. When sourcing these machines, international buyers should consider robust security features and compatibility with various payment methods to accommodate diverse traveler needs.
Sports Venues
Sports venues have begun to adopt lottery vending machines to facilitate on-site ticket sales during events. This application not only boosts audience engagement but also creates an additional revenue stream during high-traffic events. Buyers in this sector should prioritize machines that can integrate seamlessly with existing event management systems and provide reliable customer service support to enhance the overall experience for attendees.
Online Platforms
With the rise of digital solutions, lottery vending machines are now being integrated into online platforms via kiosks. This application allows businesses to expand their market reach and engage a broader customer base. B2B buyers should focus on machines that offer strong software integration capabilities and prioritize data security measures to protect sensitive customer information, ensuring compliance with international standards.
Related Video: ID now required at Texas Lottery vending machines
Strategic Material Selection Guide for lottery vending machines
When selecting materials for lottery vending machines, it is crucial to consider properties that directly influence performance, durability, and compliance with local standards. Below is an analysis of four common materials used in the construction of lottery vending machines, focusing on their key properties, advantages, disadvantages, and specific considerations for international B2B buyers.
1. Stainless Steel
Key Properties: Stainless steel is known for its excellent corrosion resistance, high strength, and ability to withstand high temperatures. It typically has a temperature rating of up to 800°C and is resistant to various chemicals.
Pros & Cons: The primary advantage of stainless steel is its durability and longevity, making it suitable for outdoor and high-traffic environments. However, it is more expensive than other materials, which can increase the overall cost of the vending machine. Manufacturing complexity is moderate, as it requires specialized tools to cut and shape.
Impact on Application: Stainless steel is compatible with a variety of media, including water and various cleaning agents, making it ideal for machines exposed to the elements.
Specific Considerations: In regions like Europe and the Middle East, stainless steel must comply with standards such as EN 10088 for stainless steel products. Buyers should also consider local sourcing to reduce costs and ensure compliance with environmental regulations.
2. Polycarbonate
Key Properties: Polycarbonate is a high-performance plastic known for its impact resistance and transparency. It can withstand temperatures ranging from -40°C to 120°C.
Pros & Cons: The lightweight nature of polycarbonate makes it easy to handle and install, reducing manufacturing and shipping costs. However, it is less durable than metals and may be susceptible to scratching and UV degradation over time.
Impact on Application: Polycarbonate is ideal for protective panels and displays in vending machines, allowing visibility of products while providing protection against vandalism.
Specific Considerations: Buyers in Africa and South America should be aware of the material’s UV resistance, especially in regions with high sunlight exposure. Compliance with ASTM standards for plastics is also essential.
3. Aluminum
Key Properties: Aluminum is lightweight, corrosion-resistant, and has a good strength-to-weight ratio. It typically has a temperature rating of up to 600°C.
Pros & Cons: Aluminum is cost-effective and easy to fabricate, making it a popular choice for various components of vending machines. However, it may not be as durable as stainless steel in harsh environments, leading to potential wear and tear over time.
Impact on Application: Aluminum is suitable for structural components and housing, providing a good balance of weight and strength while being resistant to corrosion.
Specific Considerations: In regions like Italy and Egypt, buyers should ensure compliance with EN 573 for aluminum alloys and consider the local availability of recycled aluminum to enhance sustainability.
4. Galvanized Steel
Key Properties: Galvanized steel is carbon steel coated with zinc to enhance its corrosion resistance. It is suitable for temperatures up to 400°C.
Pros & Cons: The cost-effectiveness of galvanized steel makes it an attractive option for budget-conscious projects. However, it may not perform as well as stainless steel in highly corrosive environments and can be heavier, impacting shipping costs.
Impact on Application: Galvanized steel is often used for structural frames and supports in vending machines, providing strength while protecting against rust.
Specific Considerations: Buyers should be aware of local standards such as ASTM A123 for galvanized coatings, especially in humid regions of Africa and South America, where corrosion can be a significant concern.
Summary Table
Material | Typical Use Case for lottery vending machines | Key Advantage | Key Disadvantage/Limitation | Relative Cost (Low/Med/High) |
---|---|---|---|---|
Stainless Steel | External casing and structural components | Excellent durability and corrosion resistance | Higher cost and manufacturing complexity | High |
Polycarbonate | Protective panels and displays | Lightweight and impact-resistant | Susceptible to scratching and UV degradation | Medium |
Aluminum | Structural components and housing | Cost-effective and easy to fabricate | Less durable than stainless steel | Medium |
Galvanized Steel | Structural frames and supports | Cost-effective and good strength | Heavier and less corrosion-resistant than stainless steel | Low |
This guide aims to provide actionable insights for international buyers, ensuring they make informed decisions based on material properties, application suitability, and compliance with regional standards.
In-depth Look: Manufacturing Processes and Quality Assurance for lottery vending machines
Overview of Manufacturing Processes for Lottery Vending Machines
When engaging in the procurement of lottery vending machines, understanding the manufacturing process is crucial for ensuring product quality and longevity. The production of these machines typically encompasses several key stages: material preparation, forming, assembly, and finishing. Each stage employs specific techniques that play a vital role in the overall functionality and reliability of the machines.
1. Material Preparation
The foundation of any quality product lies in the materials used. Common materials for lottery vending machines include high-grade metals, plastics, and electronic components. During the material preparation stage, suppliers focus on:
- Material Selection: Choosing durable and weather-resistant materials that can withstand diverse environmental conditions, especially in regions like Africa and the Middle East where climate can be extreme.
- Pre-Processing: This may involve cutting, shaping, and treating materials to ensure they meet the specifications required for the subsequent forming process.
2. Forming
The forming stage involves shaping the prepared materials into the components of the vending machine. Techniques used include:
- Metal Stamping: Efficient for creating complex shapes from sheet metal, which is essential for the machine’s casing.
- Injection Molding: Used for plastic parts, enabling high precision and the ability to produce intricate designs that enhance user interaction.
- Laser Cutting: Provides accuracy in cutting metal and plastic components, ensuring that parts fit together seamlessly.
3. Assembly
Once components are formed, they move to the assembly stage where they are put together to create the final product. Key practices during assembly include:
- Modular Assembly: This allows for easier repairs and upgrades, which is particularly beneficial in regions with limited access to spare parts.
- Automated Assembly Lines: Increase efficiency and consistency, reducing human error and ensuring that each unit meets quality standards.
4. Finishing
The finishing stage is critical for both aesthetics and functionality. It often includes:
- Surface Treatment: Processes such as powder coating or anodizing protect against corrosion and wear, enhancing the machine’s lifespan.
- Quality Checks: Initial inspections are performed to ensure that all components are assembled correctly and function as intended.
Quality Assurance in Manufacturing
Quality assurance (QA) is integral to the manufacturing process, ensuring that each lottery vending machine meets international standards and customer expectations. B2B buyers should be familiar with the following aspects of quality assurance:
International Standards
- ISO 9001: This standard focuses on quality management systems and is applicable across various industries, including manufacturing. Suppliers should be ISO 9001 certified, indicating they follow rigorous quality management protocols.
- CE Marking: Particularly relevant in Europe, CE marking signifies that a product meets EU safety, health, and environmental protection standards. This is crucial for buyers in European markets.
- API Standards: For machines that handle financial transactions, compliance with industry-specific standards such as those set by the American Petroleum Institute (API) may be necessary.
Quality Control Checkpoints
To ensure the highest quality, manufacturers implement several quality control (QC) checkpoints throughout the production process:
- Incoming Quality Control (IQC): This involves inspecting raw materials upon arrival to ensure they meet specified standards before production begins.
- In-Process Quality Control (IPQC): Continuous monitoring during the manufacturing process helps catch defects early, minimizing waste and rework.
- Final Quality Control (FQC): At this stage, the completed machines undergo rigorous testing to ensure they function correctly and meet all regulatory standards.
Common Testing Methods
Buyers should inquire about the testing methods used by suppliers, which may include:
- Functional Testing: Ensures that all electronic and mechanical components operate as intended.
- Durability Testing: Simulates various environmental conditions to evaluate how well the machine withstands wear and tear.
- Security Testing: Particularly important for machines handling financial transactions, ensuring they are resilient against tampering and fraud.
Verifying Supplier Quality Control
To ensure that suppliers maintain high-quality standards, B2B buyers should take proactive steps to verify their quality control processes:
- Supplier Audits: Conducting regular audits of suppliers’ facilities can provide insights into their manufacturing practices and adherence to quality standards.
- Reviewing Quality Reports: Requesting detailed quality assurance reports can help assess a supplier’s commitment to quality.
- Third-Party Inspections: Engaging independent inspectors to evaluate the manufacturing process and final products can provide an unbiased assessment of quality.
Quality Control Nuances for International Buyers
B2B buyers from different regions should be aware of specific nuances related to quality control:
- Regional Standards: Understanding local regulations and standards is crucial, especially in regions like Africa and the Middle East where compliance requirements may differ significantly from those in Europe or South America.
- Cultural Considerations: Different regions may have varying expectations regarding product quality and after-sales service. Buyers should communicate these expectations clearly to suppliers.
- Logistics and Supply Chain: Consider the implications of shipping and handling on product quality. Ensure that suppliers have robust logistics plans to protect machines during transit.
Conclusion
Understanding the manufacturing processes and quality assurance measures for lottery vending machines is essential for international B2B buyers. By focusing on material selection, forming techniques, assembly methods, and stringent quality control practices, buyers can make informed decisions that ensure they procure reliable and high-quality machines tailored to their specific market needs.
Related Video: Top 5 Mass Production Techniques: Manufacturing Process
Comprehensive Cost and Pricing Analysis for lottery vending machines Sourcing
In the landscape of lottery vending machines, understanding the cost structure and pricing dynamics is critical for international B2B buyers, particularly those from regions such as Africa, South America, the Middle East, and Europe. This analysis will delve into the various cost components, pricing influencers, and provide actionable insights for effective sourcing.
Cost Components
-
Materials: The primary materials used in manufacturing lottery vending machines include high-grade steel for the chassis, durable plastics for the casing, electronic components for the ticket dispensing mechanism, and advanced software systems. The quality and source of these materials significantly influence the overall cost.
-
Labor: Labor costs vary significantly by region. In countries with higher wage standards, labor can account for a larger portion of the total cost. Conversely, sourcing from regions with lower labor costs may reduce expenses but could impact quality and compliance with international standards.
-
Manufacturing Overhead: This includes costs related to factory operations, utilities, equipment maintenance, and administration. Efficient production processes and automation can help mitigate overhead costs, making it essential to evaluate potential suppliers on their manufacturing capabilities.
-
Tooling: Custom tooling can be a substantial upfront investment, particularly for machines with unique specifications. Buyers should assess whether suppliers have the necessary tooling in place or if additional costs will be incurred for custom designs.
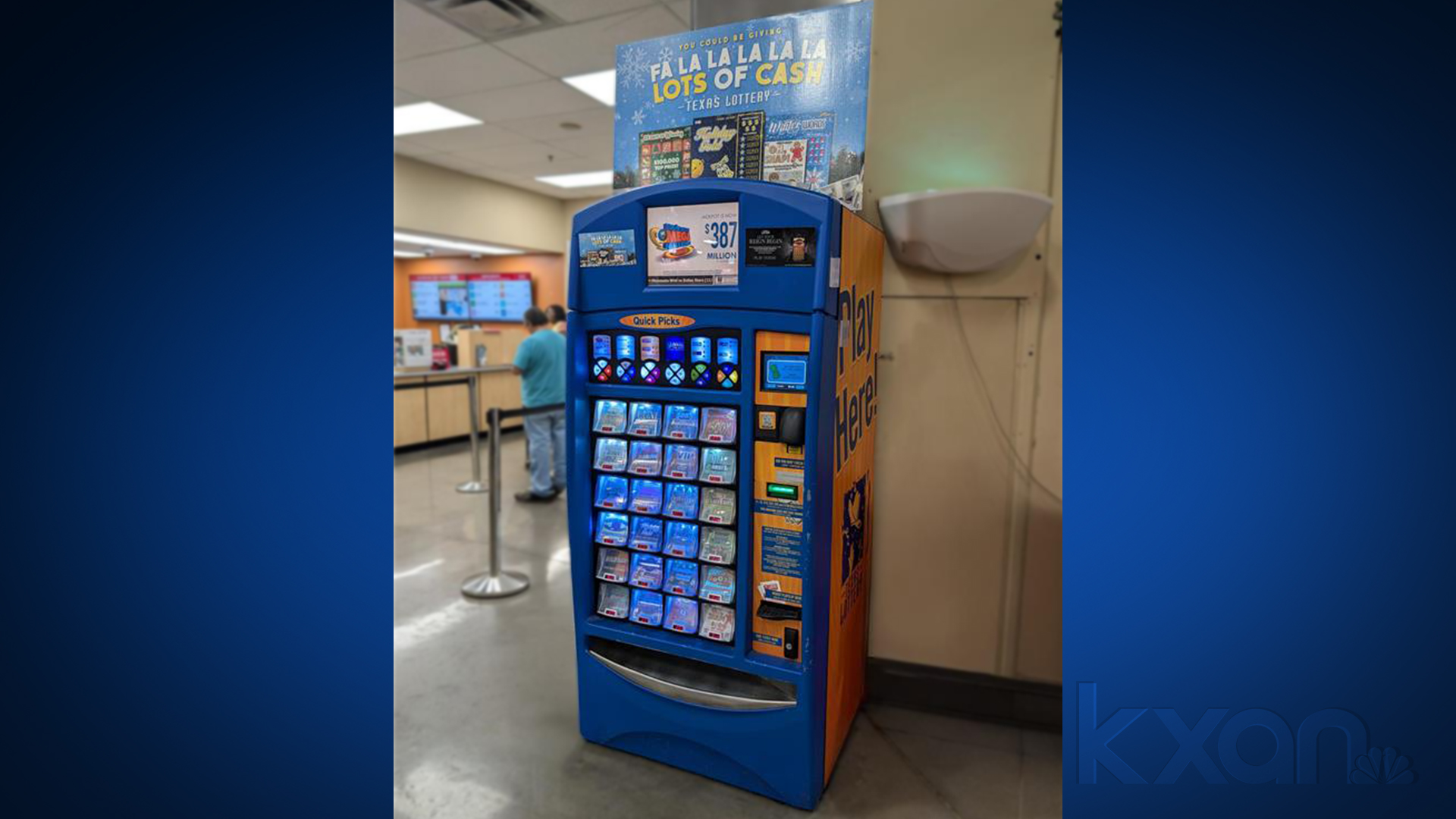
Illustrative Image (Source: Google Search)
-
Quality Control (QC): Implementing robust QC measures is vital to ensure product reliability and compliance with international standards. Investing in quality control can prevent costly recalls or repairs down the line.
-
Logistics: Shipping costs are influenced by the distance from the supplier, the mode of transport, and current fuel prices. Understanding potential tariffs and customs duties is crucial for accurate cost estimation.
-
Margin: Suppliers typically add a profit margin on top of the total costs. This margin can vary based on the supplier’s market positioning, brand reputation, and the perceived value of the machine.
Price Influencers
-
Volume/MOQ: Bulk purchasing can lead to significant discounts. Establishing a minimum order quantity (MOQ) with suppliers is a common practice that can enhance cost-efficiency.
-
Specifications/Customization: Custom features or specifications may drive costs higher. Buyers should weigh the benefits of customization against the potential increase in price.
-
Materials: The choice of materials directly impacts both cost and machine durability. Opting for premium materials might increase initial investment but could enhance longevity and reduce total cost of ownership.
-
Quality/Certifications: Machines that meet international quality standards or possess specific certifications may carry a premium price. However, these certifications often translate into reliability and market acceptance.
-
Supplier Factors: The reputation, experience, and reliability of suppliers can greatly influence pricing. Established suppliers may offer better quality assurance but at a higher cost.
-
Incoterms: Understanding Incoterms is essential for determining who bears the cost and risk at various stages of shipping. This can affect the overall cost of sourcing.
Buyer Tips
-
Negotiation: Engage in negotiations to explore pricing flexibility, especially for larger orders. Suppliers may be willing to adjust pricing based on commitment levels.
-
Cost-Efficiency: Look beyond the initial purchase price. Consider long-term factors such as maintenance, operational costs, and potential downtime to assess the total cost of ownership.
-
Pricing Nuances: Be aware of regional pricing variations. For instance, machines may be priced differently in Europe compared to Africa due to market conditions and economic factors.
-
Due Diligence: Conduct thorough research on suppliers, including reviews and case studies from other buyers in your region. This can provide insights into quality and reliability.
-
Local Regulations: Familiarize yourself with local regulations regarding lottery vending machines in your market. Compliance may influence sourcing decisions and costs.
Disclaimer
Prices and cost estimates provided in this analysis are indicative and may vary based on market conditions, supplier negotiations, and specific buyer requirements. It is advisable for buyers to conduct comprehensive market research to obtain accurate pricing relevant to their sourcing needs.
Spotlight on Potential lottery vending machines Manufacturers and Suppliers
- (No specific manufacturer data was available or requested for detailed profiling in this section for lottery vending machines.)*
Essential Technical Properties and Trade Terminology for lottery vending machines
Key Technical Properties of Lottery Vending Machines
When considering the procurement of lottery vending machines, international B2B buyers must focus on several critical technical properties. Understanding these specifications ensures that the machines meet operational demands and regulatory compliance in diverse markets.
-
Material Grade
The material grade refers to the quality of materials used in the construction of the vending machine, which typically includes metal alloys, plastics, and electronic components. High-grade materials enhance durability and resistance to environmental factors, such as moisture and temperature fluctuations. For buyers, investing in machines made from superior materials can reduce maintenance costs and extend the lifespan of the equipment, leading to better ROI. -
Tolerance
Tolerance indicates the permissible limit of variation in a physical dimension. It is crucial in the manufacturing of lottery vending machines, especially for parts that must fit precisely to ensure proper functionality. Tight tolerances can enhance the reliability and accuracy of the machine’s operations, such as ticket dispensing and cash handling. Buyers should prioritize vendors who can guarantee specific tolerances to avoid operational issues that could affect customer satisfaction. -
Power Consumption
This specification reflects the amount of electrical energy the vending machine requires to operate. Machines with lower power consumption are more environmentally friendly and can lead to cost savings in energy bills. For B2B buyers, understanding power requirements is essential, especially in regions with fluctuating energy costs or limited electrical infrastructure. -
User Interface Design
The user interface (UI) of a lottery vending machine plays a significant role in customer interaction. A well-designed UI enhances user experience by providing clear instructions and easy navigation. Buyers should look for machines that offer customizable interfaces to cater to local languages and cultural preferences, improving accessibility and engagement with diverse demographics. -
Security Features
Security is paramount in lottery vending machines due to the handling of cash and sensitive player information. Essential security features may include tamper-proof locks, surveillance cameras, and encrypted data transmission systems. Buyers must assess the security protocols of potential machines to minimize risks associated with theft and fraud. -
Compliance Standards
Lottery vending machines must adhere to specific regulatory standards that vary by region. Compliance with local gaming regulations ensures that the machines are legally operable and can avoid costly fines or operational shutdowns. B2B buyers should conduct thorough research on the compliance requirements in their respective markets to ensure that the machines they purchase meet these standards.
Common Trade Terms in the Lottery Vending Machine Industry
Understanding the jargon and trade terminology in the lottery vending machine sector is vital for effective negotiation and procurement.
-
OEM (Original Equipment Manufacturer)
An OEM refers to a company that produces parts or equipment that may be marketed by another manufacturer. In the context of lottery vending machines, buyers often source components from OEMs to ensure quality and compatibility. Establishing relationships with reputable OEMs can lead to better pricing and availability of parts. -
MOQ (Minimum Order Quantity)
MOQ is the minimum number of units that a supplier is willing to sell at a given price. For B2B buyers, understanding MOQ is crucial for budgeting and inventory management. Negotiating lower MOQs can be beneficial for businesses looking to test new products without committing to large orders. -
RFQ (Request for Quotation)
An RFQ is a document that a buyer sends to suppliers requesting pricing and terms for specific products or services. Issuing an RFQ for lottery vending machines allows buyers to compare offerings from multiple suppliers and make informed purchasing decisions. -
Incoterms (International Commercial Terms)
Incoterms are standardized trade terms that define the responsibilities of buyers and sellers in international transactions. Familiarity with these terms helps buyers understand shipping costs, risk allocation, and the point at which ownership transfers. Properly negotiating Incoterms can mitigate unforeseen costs during shipping and delivery.
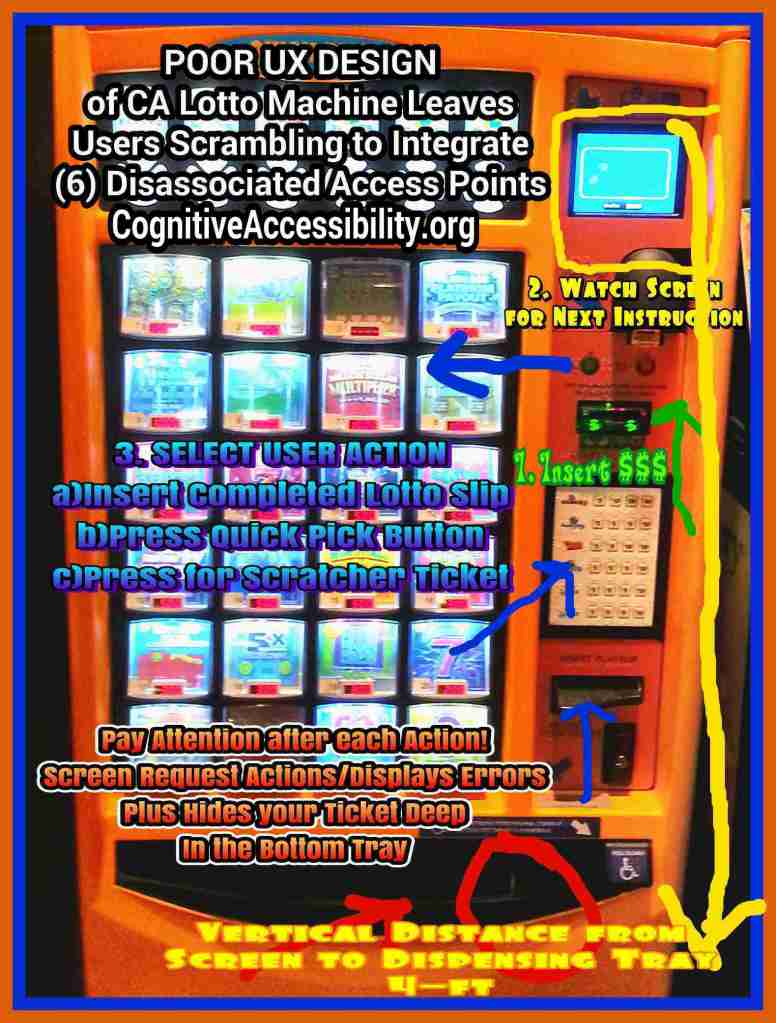
Illustrative Image (Source: Google Search)
- Lead Time
Lead time is the duration from the placement of an order to the delivery of the goods. For lottery vending machines, understanding lead time is critical for planning deployments and ensuring machines are operational when needed. Buyers should factor lead times into their project timelines to avoid disruptions.
By grasping these essential technical properties and trade terms, international B2B buyers can navigate the procurement process for lottery vending machines more effectively, ensuring they make informed decisions that align with their operational needs and market demands.
Navigating Market Dynamics, Sourcing Trends, and Sustainability in the lottery vending machines Sector
Market Overview & Key Trends
The lottery vending machine sector is undergoing significant transformation, driven by advancements in technology and changing consumer behaviors. International B2B buyers, particularly in regions like Africa, South America, the Middle East, and Europe, are witnessing a surge in demand for automated lottery solutions. Key drivers include increased smartphone penetration, which facilitates mobile payments and engagement, and the rising popularity of instant lottery games that offer immediate gratification.
Emerging trends in this sector highlight the integration of smart technologies, such as IoT-enabled devices that allow for real-time monitoring and analytics. These innovations not only enhance operational efficiency but also provide valuable insights into consumer preferences and purchasing patterns. Moreover, the shift towards contactless transactions has accelerated, necessitating the adoption of advanced payment systems within vending machines.
Market dynamics are further influenced by regulatory changes and the push for enhanced security features to combat fraud. B2B buyers should remain informed about local regulations, which can vary significantly across regions, affecting the type of machines and technologies that can be deployed. Additionally, partnerships with local distributors and technology providers can facilitate smoother market entry and compliance with regional laws.
Sustainability & Ethical Sourcing in B2B
As global awareness of environmental issues grows, sustainability has become a critical consideration in the lottery vending machine sector. B2B buyers are increasingly prioritizing suppliers that demonstrate a commitment to sustainable practices, including the use of eco-friendly materials and energy-efficient technologies. This shift is not only beneficial for the environment but also enhances brand reputation and customer loyalty.
Ethical sourcing is paramount, particularly in regions where supply chains can be complex. Buyers should seek suppliers that adhere to fair labor practices and transparent supply chains. Certifications such as ISO 14001 for environmental management and Fair Trade can serve as indicators of a supplier’s commitment to sustainability and ethical practices.
Incorporating ‘green’ materials in the manufacturing of lottery vending machines, such as recyclable plastics and energy-efficient components, is becoming a standard expectation. These practices not only reduce the environmental impact but also align with the corporate social responsibility goals of many businesses today. By choosing suppliers who prioritize sustainability, B2B buyers can contribute to a more responsible industry while also appealing to environmentally-conscious consumers.
Brief Evolution/History
The lottery vending machine sector has evolved significantly since its inception in the early 20th century. Originally, these machines were simple devices that dispensed paper lottery tickets, primarily in physical retail locations. Over the decades, technological advancements have transformed them into sophisticated automated systems capable of processing digital transactions and offering a variety of gaming options.
The introduction of electronic and online lottery systems in the late 1990s marked a pivotal moment, allowing players to purchase tickets remotely. This evolution not only expanded the market reach but also increased accessibility for consumers. Today, with the convergence of technology and gaming, the future of lottery vending machines looks promising, with innovations poised to enhance user experience and operational efficiency for B2B stakeholders.
Related Video: Is global trade transforming? | Counting the Cost
Frequently Asked Questions (FAQs) for B2B Buyers of lottery vending machines
-
What key factors should I consider when vetting suppliers for lottery vending machines?
When vetting suppliers, prioritize their industry experience, reputation, and customer reviews. Ensure they have a proven track record in manufacturing lottery vending machines that comply with local regulations in your target market. It’s also important to check for certifications, such as ISO, to confirm quality standards. Engage in direct communication to assess their responsiveness and willingness to customize solutions according to your needs. -
Can I customize lottery vending machines to suit my market’s preferences?
Yes, customization is often available and can be essential for success in different regions. Discuss specific requirements with suppliers, such as branding, language options, payment systems, and features that cater to local consumer behavior. Ensure the supplier has a flexible manufacturing process that accommodates modifications without significantly impacting lead times or costs. -
What are the typical minimum order quantities (MOQ) and lead times for lottery vending machines?
MOQs can vary widely depending on the supplier and the complexity of the machines. Generally, expect MOQs to range from 5 to 50 units for standard models. Lead times typically range from 6 to 12 weeks, but this can be influenced by customization requests and production schedules. Always confirm these details upfront to align your purchasing strategy with your operational needs. -
What payment terms should I expect when purchasing lottery vending machines internationally?
Payment terms can differ significantly among suppliers. Common practices include advance payments, letters of credit, or net payment terms based on delivery milestones. It’s advisable to negotiate terms that protect your investment, such as partial payment upon order confirmation and the balance upon successful delivery. Be aware of currency exchange rates and transaction fees that may apply. -
How can I ensure quality assurance and certifications for lottery vending machines?
Request detailed information on the supplier’s quality control processes and certifications relevant to your market. Look for compliance with international standards like CE or UL, which indicate safety and reliability. Conduct factory visits or request third-party inspections to verify manufacturing practices. Additionally, ask for warranty terms and after-sales support to ensure product longevity. -
What logistics considerations should I keep in mind when importing lottery vending machines?
Logistics is crucial when importing machines. Ensure you understand shipping methods, potential customs duties, and import regulations in your country. Work with logistics providers experienced in handling heavy machinery and ensure they can manage documentation requirements. Consider insurance options to protect your investment during transit, and plan for installation and maintenance logistics upon arrival. -
How can I resolve disputes with suppliers during the procurement process?
Disputes can arise over various issues, including delivery delays or product quality. Establish clear communication channels and document all agreements in detail to prevent misunderstandings. If a dispute occurs, initiate dialogue with the supplier first to seek an amicable resolution. If necessary, refer to the contract for dispute resolution mechanisms, such as mediation or arbitration, to ensure a fair process. -
What are the best practices for maintaining lottery vending machines once purchased?
Regular maintenance is key to ensuring the longevity of your lottery vending machines. Establish a routine inspection schedule to check for software updates, hardware malfunctions, and cleanliness. Train your staff on basic troubleshooting and maintenance procedures. Additionally, maintain open communication with the supplier for technical support and to order replacement parts as needed, ensuring minimal downtime for your operations.
Strategic Sourcing Conclusion and Outlook for lottery vending machines
In the evolving landscape of lottery vending machines, strategic sourcing emerges as a pivotal factor for international B2B buyers. Understanding local market dynamics and regulatory frameworks is crucial, particularly for regions such as Africa, South America, the Middle East, and Europe. Engaging with reliable suppliers who demonstrate compliance and innovation will not only streamline procurement processes but also enhance operational efficiency.
Key Takeaways:
- Market Research: Conduct thorough research to identify emerging trends and consumer preferences within your target region.
- Supplier Relationships: Build strong partnerships with manufacturers and distributors to ensure consistent product quality and support.
- Regulatory Compliance: Stay informed about local laws governing lottery operations, as compliance can significantly affect market entry and sustainability.
As you navigate this competitive sector, remember that strategic sourcing is not merely a transactional process; it’s an investment in future growth. By leveraging insights and fostering relationships with key stakeholders, you can position your organization for success.
Looking ahead, the demand for innovative lottery solutions is poised to increase. Embrace this opportunity to enhance your offerings and tap into new markets. Engage with your network today and explore how strategic sourcing can lead to sustainable growth in the lottery vending machine sector.