Master Your Vending Machine Agreement for Maximum
Guide to Vending Machine Agreement
- Introduction: Navigating the Global Market for vending machine agreement
- Understanding vending machine agreement Types and Variations
- Key Industrial Applications of vending machine agreement
- Strategic Material Selection Guide for vending machine agreement
- In-depth Look: Manufacturing Processes and Quality Assurance for vending machine agreement
- Comprehensive Cost and Pricing Analysis for vending machine agreement Sourcing
- Spotlight on Potential vending machine agreement Manufacturers and Suppliers
- Essential Technical Properties and Trade Terminology for vending machine agreement
- Navigating Market Dynamics, Sourcing Trends, and Sustainability in the vending machine agreement Sector
- Frequently Asked Questions (FAQs) for B2B Buyers of vending machine agreement
- Strategic Sourcing Conclusion and Outlook for vending machine agreement
Introduction: Navigating the Global Market for vending machine agreement
In today’s fast-paced global economy, vending machines represent a lucrative opportunity for businesses seeking to enhance customer engagement and streamline sales processes. A well-structured vending machine agreement is not just a contractual formality; it is a vital instrument that ensures clarity, compliance, and mutual benefit between suppliers and operators. For international B2B buyers from regions such as Africa, South America, the Middle East, and Europe, understanding the intricacies of these agreements can unlock significant advantages in a competitive marketplace.
This comprehensive guide aims to demystify the complexities surrounding vending machine agreements. We will explore various types of agreements, delve into essential materials and manufacturing quality control, and provide insights into selecting reliable suppliers. Additionally, we will discuss cost structures and market trends that influence pricing strategies, ensuring that buyers can make informed decisions tailored to their specific needs.
Moreover, the guide will address frequently asked questions, equipping B2B buyers with the knowledge necessary to navigate negotiations and establish successful partnerships. By leveraging the insights contained within, businesses can not only optimize their sourcing strategies but also enhance their operational efficiencies, ultimately driving profitability. As you embark on this journey through the global vending machine landscape, prepare to empower your business with the tools and knowledge required for success.
Understanding vending machine agreement Types and Variations
Type Name | Key Distinguishing Features | Primary B2B Applications | Brief Pros & Cons for Buyers |
---|---|---|---|
Traditional Vending Agreement | Standard contracts for machine placement and product supply | Offices, schools, public spaces | Pros: Established model; predictable costs. Cons: Limited flexibility in product selection. |
Franchise Vending Agreement | Operates under a recognized brand with specific operational guidelines | Retail environments, shopping malls | Pros: Brand recognition; support from franchisor. Cons: Higher initial investment; strict adherence to brand standards. |
Revenue Share Agreement | Revenue is split between the machine owner and the location provider | High-traffic areas, events | Pros: Lower upfront costs; shared risk. Cons: Potentially lower profits depending on traffic. |
Placement Agreement | Focuses on the location and terms of machine placement without product supply specifics | Temporary events, trade shows | Pros: Flexible terms; suitable for short-term needs. Cons: Lack of product control; may require frequent restocking. |
Service and Maintenance Agreement | Covers ongoing maintenance and service for vending machines | Long-term installations, busy venues | Pros: Ensures machine uptime; reduces operational headaches. Cons: Additional recurring costs; may require negotiation on service levels. |
Traditional Vending Agreement
Traditional vending agreements are the most common type, where a vending machine operator places machines in specified locations and supplies products. This model is suitable for businesses looking for a straightforward arrangement without the complexities of branding or revenue sharing. B2B buyers should consider factors such as location traffic, product selection, and maintenance responsibilities when entering these agreements, as they directly impact profitability and operational efficiency.
Franchise Vending Agreement
Franchise vending agreements allow businesses to operate under a well-known brand, offering a range of products that align with that brand’s standards. This type is particularly advantageous for B2B buyers seeking to leverage brand recognition to attract customers in retail or high-traffic environments. However, the initial investment can be significant, and adherence to strict operational guidelines is required, which may not suit all businesses.
Revenue Share Agreement
In revenue share agreements, vending machine operators share profits with the location provider, making it an attractive option for businesses with limited upfront capital. This model is ideal for high-traffic areas or events where sales potential is significant. B2B buyers should evaluate the expected foot traffic and sales volume to determine if this arrangement aligns with their financial goals, as shared revenues can dilute profits.
Placement Agreement
Placement agreements focus solely on the terms of machine installation without specifying product supply. This flexibility makes them ideal for temporary events or trade shows, allowing businesses to adapt quickly to changing needs. Buyers should consider the logistics of product sourcing and restocking, as frequent changes may be necessary to meet consumer demands, potentially leading to increased operational complexity.
Service and Maintenance Agreement
Service and maintenance agreements ensure that vending machines remain operational through regular maintenance and support. This type is essential for businesses that rely on vending machines for consistent revenue, particularly in high-traffic venues. B2B buyers must assess the cost of these agreements against the potential downtime and customer satisfaction, as well-maintained machines are crucial for maximizing sales and minimizing disruptions.
Related Video: 10 Change Management Models Explained in 10 Minutes
Key Industrial Applications of vending machine agreement
Industry/Sector | Specific Application of vending machine agreement | Value/Benefit for the Business | Key Sourcing Considerations for this Application |
---|---|---|---|
Food and Beverage | Automated snack and beverage distribution | Increased convenience, reduced labor costs | Product variety, supply chain reliability, local tastes |
Healthcare | Pharmaceutical vending machines | 24/7 access to medications, improved patient compliance | Regulatory compliance, temperature control, security |
Education | Campus vending solutions | Enhanced student satisfaction, revenue generation | Payment systems, product range, maintenance services |
Corporate Offices | Employee refreshment stations | Boosted morale and productivity, reduced downtime | Customization options, inventory management, service frequency |
Transportation Hubs | Travel retail vending | Quick access to essentials, increased foot traffic revenue | Location analysis, product selection, branding opportunities |
Food and Beverage
In the food and beverage industry, vending machine agreements facilitate automated snack and drink distribution. This application addresses the need for convenience, allowing businesses to operate without the high overhead costs associated with traditional retail. International buyers should consider sourcing machines that cater to local tastes, ensuring a diverse product range that appeals to their customer base. Additionally, reliable supply chains are crucial to maintain stock levels and minimize disruptions.
Healthcare
Vending machines in healthcare settings, particularly for pharmaceuticals, provide critical 24/7 access to medications and health products. This application enhances patient compliance by ensuring that necessary items are readily available, especially in emergency situations. Buyers in this sector must prioritize regulatory compliance and the ability to maintain specific temperature controls for sensitive medications. Security features are also essential to prevent unauthorized access and ensure patient safety.
Education
In educational institutions, vending machine agreements can significantly improve student satisfaction by providing easy access to snacks and drinks on campus. This application not only enhances the student experience but also generates additional revenue for the institution. When sourcing vending solutions, buyers should focus on payment systems that accommodate various transaction methods, including cashless options, and consider the maintenance services required to keep machines operational.
Corporate Offices
Corporate environments can benefit from vending machines that serve as employee refreshment stations. This application helps to boost morale and productivity by providing quick access to snacks and beverages, minimizing downtime during work hours. B2B buyers should look for customization options that align with their corporate culture, as well as effective inventory management solutions to ensure popular items are always in stock. Service frequency is another vital consideration to maintain machine functionality.
Transportation Hubs
Vending machines in transportation hubs, such as airports and train stations, cater to travelers seeking quick access to essentials. This application addresses the high foot traffic in these areas, allowing businesses to capitalize on impulse purchases and increase revenue. Buyers should conduct thorough location analyses to identify optimal placement for machines, consider the product selection to meet diverse traveler needs, and explore branding opportunities to enhance visibility and attract customers.
Related Video: How to Start a Vending Machine Business, Cost, Tips, How Much You Make
Strategic Material Selection Guide for vending machine agreement
When selecting materials for vending machine agreements, it’s crucial to consider the specific properties and performance of each material. This selection impacts not only the durability and functionality of the machines but also compliance with international standards, which vary by region. Below, we analyze four common materials used in vending machine construction, highlighting their key properties, advantages, disadvantages, and considerations for international buyers.
1. Stainless Steel
Key Properties: Stainless steel is known for its excellent corrosion resistance, high strength, and ability to withstand a wide range of temperatures. It typically has a temperature rating of up to 800°F (427°C) and is resistant to various chemicals.
Pros & Cons: The durability of stainless steel makes it suitable for high-traffic environments, as it resists dents and scratches. However, it can be more expensive than other materials, which may impact budget constraints. Manufacturing complexity is moderate, as it requires specialized tools for cutting and welding.
Impact on Application: Stainless steel is compatible with various media, including food and beverages, making it ideal for vending machines. Its non-porous surface also ensures hygiene, which is critical in food service applications.
Considerations for International Buyers: Buyers in regions like Europe and the Middle East should ensure compliance with standards such as ASTM A240 for stainless steel products. In Africa and South America, local sourcing of stainless steel can affect costs and availability.
2. Powder-Coated Steel
Key Properties: Powder-coated steel combines the strength of steel with a protective layer that enhances corrosion resistance. The coating can withstand temperatures up to 200°F (93°C) and is available in various colors.
Pros & Cons: This material is cost-effective and offers aesthetic flexibility due to its range of colors. However, the coating can chip or scratch, exposing the underlying steel to corrosion. Manufacturing is relatively simple, but care must be taken during the coating process.
Impact on Application: Powder-coated steel is suitable for exterior vending machines, as the coating can provide UV protection. However, it may not be ideal for environments with high humidity or exposure to harsh chemicals.
Considerations for International Buyers: Buyers should verify that the powder coating meets local environmental regulations, particularly in Europe, where compliance with REACH (Registration, Evaluation, Authorisation and Restriction of Chemicals) is mandatory.
3. Aluminum
Key Properties: Aluminum is lightweight, corrosion-resistant, and has good thermal conductivity. It typically has a temperature rating of around 400°F (204°C) and is easy to fabricate.
Pros & Cons: The lightweight nature of aluminum makes it easy to transport and install, reducing shipping costs. However, it is softer than steel, which can lead to dents and scratches. The manufacturing process is straightforward, allowing for quick production.
Impact on Application: Aluminum is suitable for vending machines that require frequent relocation or installation in areas with limited structural support. However, it may not be suitable for high-security applications due to its lower strength compared to steel.
Considerations for International Buyers: In regions like South America, where aluminum is often sourced locally, buyers should consider the alloy grades to ensure compatibility with local climate conditions. Compliance with international standards such as ISO 9001 can also be a factor.
4. Glass
Key Properties: Glass offers excellent visibility for products and is resistant to moisture and UV light. It can withstand a range of temperatures but is fragile compared to metals.
Pros & Cons: The primary advantage of glass is its aesthetic appeal and the ability to showcase products effectively. However, its fragility poses a risk of breakage, which can lead to increased maintenance costs. Manufacturing complexity is high, as it requires specialized handling and installation techniques.
Impact on Application: Glass is ideal for vending machines that sell premium products, as it enhances visibility and attractiveness. However, it may not be suitable for high-traffic or outdoor environments where breakage is a concern.
Considerations for International Buyers: Buyers should ensure that glass used in vending machines complies with safety standards, such as ANSI Z97.1 in the U.S. and EN 12150 in Europe, to mitigate risks associated with breakage.
Summary Table
Material | Typical Use Case for vending machine agreement | Key Advantage | Key Disadvantage/Limitation | Relative Cost (Low/Med/High) |
---|---|---|---|---|
Stainless Steel | High-traffic vending machines for food/beverages | Excellent durability and corrosion resistance | Higher cost compared to alternatives | High |
Powder-Coated Steel | Exterior vending machines in various climates | Cost-effective with aesthetic options | Coating can chip, exposing steel | Medium |
Aluminum | Lightweight, portable vending machines | Easy to transport and install | Softer than steel, prone to dents | Medium |
Glass | Premium product display vending machines | Enhances product visibility | Fragile, risk of breakage | Medium |
This comprehensive analysis provides international B2B buyers with actionable insights into material selection for vending machine agreements, ensuring informed decisions that align with regional standards and market conditions.
In-depth Look: Manufacturing Processes and Quality Assurance for vending machine agreement
Understanding the Manufacturing Process for Vending Machines
When entering into a vending machine agreement, it is critical for international B2B buyers to grasp the intricacies of manufacturing processes. The production of vending machines typically involves several key stages: material preparation, forming, assembly, and finishing. Each stage employs specific techniques that contribute to the overall quality and functionality of the final product.
1. Material Preparation
The initial step in the manufacturing process is material preparation, where raw materials such as steel, aluminum, plastics, and electronic components are sourced. Buyers should ensure that suppliers adhere to stringent material quality standards. This involves:
- Sourcing Quality Materials: Verify that materials meet industry standards and are sourced from reputable suppliers.
- Material Testing: Conduct tests to check for durability and resistance to environmental factors, especially in regions with extreme climates.
2. Forming
Once materials are prepared, the forming process takes place. This stage involves shaping the materials into components of the vending machine. Key techniques include:
- Metal Stamping: Used to create panels and frames, metal stamping ensures precision and consistency.
- Injection Molding: Common for plastic parts, this technique allows for complex shapes and is cost-effective for high-volume production.
B2B buyers should seek suppliers who utilize advanced forming techniques to ensure efficiency and reduce waste.
3. Assembly
After forming, the next stage is assembly, where components are put together to create the vending machine. This process often involves:
- Automated Assembly Lines: Many manufacturers employ robotics to enhance speed and precision.
- Manual Assembly: Skilled workers may perform delicate tasks that require human touch, especially in complex areas like electronics.
During this stage, it is essential for buyers to understand the workforce’s skill level and the technology used, as these factors directly affect the quality of the final product.
4. Finishing
The final stage in the manufacturing process is finishing, which includes painting, coating, and quality checks. This stage is vital for aesthetics and durability. Key activities include:
- Surface Treatment: Techniques like powder coating enhance resistance to corrosion and wear, which is crucial for machines placed in outdoor settings.
- Final Inspections: Before packaging, each machine undergoes thorough inspections to ensure compliance with specifications.
Quality Assurance in Vending Machine Manufacturing
Quality assurance (QA) is a cornerstone of the manufacturing process, ensuring that vending machines meet both international and industry-specific standards. For B2B buyers, understanding these standards is critical for maintaining product integrity.
Relevant International Standards
- ISO 9001: This standard focuses on quality management systems and is applicable across various industries, including vending machine manufacturing. Suppliers certified under ISO 9001 are more likely to provide consistent quality.
- CE Marking: This certification indicates that a product meets EU safety, health, and environmental protection standards, which is particularly relevant for buyers in Europe.
Industry-Specific Standards
In addition to international standards, certain industry-specific certifications may apply:
- API (American Petroleum Institute): For vending machines that dispense fuel or lubricants, API certification ensures compliance with safety and quality standards.
- UL (Underwriters Laboratories): This certification is essential for electrical safety, especially for machines with complex electronic components.
Quality Control Checkpoints
Quality control (QC) is implemented at various checkpoints throughout the manufacturing process to ensure that products meet the required standards. The primary QC checkpoints include:
- Incoming Quality Control (IQC): Inspecting raw materials upon arrival to ensure they meet specifications.
- In-Process Quality Control (IPQC): Continuous monitoring during production to catch defects early.
- Final Quality Control (FQC): Comprehensive testing and inspection of the finished product before shipment.
B2B buyers should request detailed QC reports from suppliers to understand their processes and outcomes.
Common Testing Methods
To ensure product quality, various testing methods are employed, including:
- Functional Testing: Assessing the operational capabilities of the vending machine, such as payment processing and product dispensing.
- Environmental Testing: Evaluating how machines perform under extreme conditions, which is particularly relevant for buyers in regions with harsh climates.
- Durability Testing: Simulating long-term usage to assess wear and tear.
Verifying Supplier Quality Control
For international B2B buyers, verifying a supplier’s QC processes is crucial. Here are actionable steps:
- Conduct Audits: Regularly schedule audits to assess supplier facilities and QC practices.
- Request Reports: Obtain documentation of past QC results, including any corrective actions taken.
- Third-Party Inspections: Engage independent inspectors to evaluate supplier quality before finalizing agreements.
Quality Control and Certification Nuances for International Buyers
Navigating the nuances of QC and certification can be complex, especially for buyers from diverse regions such as Africa, South America, the Middle East, and Europe. Here are some considerations:
- Regional Standards: Be aware of local regulations and standards that may affect product compliance.
- Cultural Differences: Understand that quality expectations and manufacturing practices can vary significantly between regions. Engage with suppliers who have a proven track record in your target market.
- Logistics Considerations: Factor in transportation and handling when assessing quality, as these can affect product condition upon arrival.
By comprehensively understanding the manufacturing processes and quality assurance practices involved in vending machine agreements, B2B buyers can make informed decisions that align with their operational needs and market expectations.
Related Video: Inspection and Quality control in Manufacturing
Comprehensive Cost and Pricing Analysis for vending machine agreement Sourcing
Understanding the cost structure and pricing dynamics of vending machine agreements is crucial for international B2B buyers seeking to make informed purchasing decisions. The following analysis outlines the key cost components, price influencers, and actionable buyer tips tailored for organizations in Africa, South America, the Middle East, and Europe, such as Colombia and Germany.
Cost Components
-
Materials
The raw materials used in vending machines, including metal, plastics, electronic components, and refrigeration systems, significantly affect the overall cost. Buyers should assess the quality and sourcing of these materials, as they directly impact durability and functionality. -
Labor
Labor costs can vary widely based on the country of manufacture. In regions with higher labor costs, like Western Europe, pricing may be elevated compared to emerging markets in Africa and South America. Understanding local wage standards and labor practices is essential for accurate budgeting. -
Manufacturing Overhead
This includes indirect costs associated with the production process, such as utilities, rent, and administrative expenses. Buyers should inquire about the manufacturing facility’s efficiency and operational practices, which can lead to cost reductions. -
Tooling
Custom tooling for unique designs or specifications can add significant upfront costs. Buyers requiring tailored solutions should consider how these costs will affect their total investment. -
Quality Control (QC)
Rigorous quality control processes ensure the machines meet required standards. Buyers should factor in QC costs and certifications when evaluating suppliers, as these can affect the machine’s reliability and lifespan.
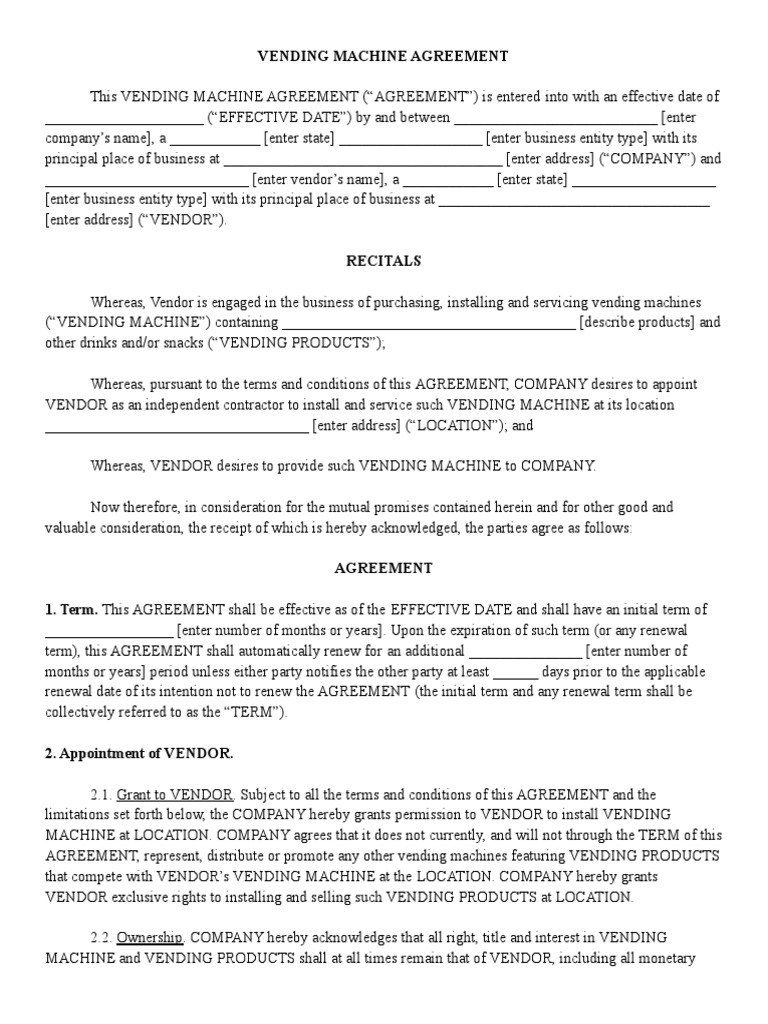
Illustrative Image (Source: Google Search)
-
Logistics
Shipping and transportation costs can fluctuate based on the origin of the machines and the chosen delivery method. Understanding Incoterms is crucial for managing these expenses effectively. -
Margin
Suppliers typically build a profit margin into their pricing, which can vary based on market conditions and competition. Buyers should be aware of typical margins in their region to assess fair pricing.
Price Influencers
-
Volume/MOQ (Minimum Order Quantity)
Larger orders often lead to better pricing due to economies of scale. Buyers should explore the possibility of consolidating orders to reduce per-unit costs. -
Specifications and Customization
Unique features or custom designs can increase costs. Buyers should clearly outline their needs to avoid unnecessary expenses and ensure that suppliers can meet specific requirements. -
Materials and Quality Certifications
Higher quality materials or certifications (e.g., ISO standards) can drive up costs but may offer better long-term value. Buyers should weigh the benefits of investing in higher quality against their budget constraints. -
Supplier Factors
The reputation and reliability of suppliers can influence pricing. Established suppliers may charge more due to their track record, while newer entrants might offer lower prices to gain market share. -
Incoterms
Understanding the implications of different Incoterms (e.g., FOB, CIF) is essential for managing logistics costs and risks associated with shipping. Buyers should negotiate terms that provide clarity on responsibilities and costs.
Buyer Tips
-
Negotiation
Effective negotiation can lead to favorable pricing. Buyers should be prepared with market data and competitor pricing to support their discussions. -
Cost-Efficiency
Consider the Total Cost of Ownership (TCO), which includes purchase price, maintenance, and operational costs. This holistic view can help in selecting the most cost-effective solution. -
Pricing Nuances
Be aware of regional pricing differences. For example, suppliers in Europe may have higher prices due to labor and regulatory standards compared to those in South America or Africa.
Disclaimer
Prices for vending machine agreements can vary widely based on numerous factors, including market conditions, currency fluctuations, and supplier negotiations. It is advisable for buyers to conduct thorough market research and obtain multiple quotes to ensure competitive pricing.
By understanding these cost components, price influencers, and strategic tips, international B2B buyers can make informed decisions when sourcing vending machine agreements that align with their business needs and budget.
Spotlight on Potential vending machine agreement Manufacturers and Suppliers
- (No specific manufacturer data was available or requested for detailed profiling in this section for vending machine agreement.)*
Essential Technical Properties and Trade Terminology for vending machine agreement
Essential Technical Properties of Vending Machines
When entering into a vending machine agreement, understanding the essential technical properties is crucial for ensuring product reliability, safety, and compliance. Here are several key specifications to consider:
-
Material Grade: The grade of materials used in vending machines, such as stainless steel or high-density polyethylene, affects durability and corrosion resistance. High-grade materials ensure longevity, particularly in harsh environments, which is vital for buyers in diverse climates across Africa, South America, the Middle East, and Europe.
-
Dimensions and Capacity: This includes the size of the machine and the volume of products it can hold. Understanding these specifications is essential for optimizing space in retail locations and ensuring that the machine meets demand without frequent restocking.
-
Energy Efficiency: Vending machines are increasingly being designed for energy efficiency, which can significantly lower operational costs. Look for machines with energy-saving modes or those certified by recognized energy efficiency programs, as these can align with sustainability goals and reduce overall expenses.
-
User Interface and Technology: The sophistication of the user interface, including touchscreen capabilities and payment options (cash, credit card, mobile payments), impacts customer experience. Machines equipped with advanced technology can offer better service and attract more customers, which is particularly relevant in competitive markets.
-
Tolerance Levels: This refers to the acceptable limits of variation in the machine’s components. Understanding tolerance is essential for ensuring proper functionality and compatibility with various product sizes. It can prevent operational issues that could lead to revenue loss.
Common Trade Terminology in Vending Machine Agreements
Familiarity with industry jargon can streamline negotiations and help buyers make informed decisions. Here are key terms to know:
-
OEM (Original Equipment Manufacturer): This term refers to companies that produce parts or equipment that may be marketed by another manufacturer. Understanding the role of OEMs is crucial for sourcing high-quality components that meet your specifications.
-
MOQ (Minimum Order Quantity): This is the smallest quantity of a product that a supplier is willing to sell. Knowing the MOQ helps buyers manage inventory and budget constraints, particularly important for smaller businesses or those testing new markets.
-
RFQ (Request for Quotation): This is a document used to solicit price proposals from suppliers. An effective RFQ includes detailed specifications, quantities, and delivery requirements, enabling buyers to compare offers and negotiate better terms.
-
Incoterms (International Commercial Terms): These are standardized trade terms used in international shipping contracts that clarify the responsibilities of buyers and sellers. Familiarizing yourself with Incoterms can help mitigate risks related to shipping costs and responsibilities, ensuring smoother transactions.
-
Lead Time: This refers to the time taken from placing an order to delivery. Understanding lead times is crucial for planning inventory levels and ensuring that your vending machines are operational when needed.
-
Warranty and Service Level Agreement (SLA): A warranty outlines the conditions under which repairs or replacements will be made, while an SLA specifies the expected service standards. Both are critical for ensuring that the vending machines remain operational and that any issues are promptly addressed.
By understanding these technical properties and trade terms, international B2B buyers can make informed decisions, negotiate effectively, and ultimately enhance their vending machine operations.
Navigating Market Dynamics, Sourcing Trends, and Sustainability in the vending machine agreement Sector
Market Overview & Key Trends
The vending machine agreement sector is experiencing significant transformation driven by technological advancements and changing consumer behaviors. One of the primary global drivers is the increasing demand for contactless payment options, a trend accelerated by the COVID-19 pandemic. This shift is particularly relevant for international B2B buyers in regions like Africa and South America, where mobile payment solutions are rapidly gaining traction. Additionally, the integration of IoT (Internet of Things) technology in vending machines allows for real-time inventory management and enhanced customer experiences, enabling suppliers to optimize operations and reduce costs.
Emerging trends also highlight the growing importance of personalization and product variety. Vending machines are evolving from traditional snack and beverage dispensers to platforms offering healthy food options, local products, and even tech accessories. This diversification presents opportunities for international buyers to source innovative products that cater to the preferences of diverse markets, including Europe and the Middle East.
Moreover, sustainability is becoming a key consideration in the procurement process. B2B buyers are increasingly prioritizing suppliers that demonstrate commitment to environmentally friendly practices, such as energy-efficient machines and recyclable packaging. Understanding these dynamics is essential for international buyers looking to establish fruitful partnerships within the vending machine sector.
Sustainability & Ethical Sourcing in B2B
Sustainability in the vending machine sector is not just a trend; it’s a necessity. The environmental impact of vending operations, including energy consumption and waste generation, has prompted stakeholders to seek more sustainable solutions. B2B buyers should prioritize partnerships with suppliers that are committed to reducing their carbon footprint through energy-efficient machines and renewable energy sources.
Ethical sourcing is equally crucial. Buyers must ensure that their supply chains are transparent and that suppliers adhere to fair labor practices. This includes sourcing materials from suppliers who prioritize worker rights and environmental stewardship. Certifications such as Fair Trade and ISO 14001 can serve as indicators of a supplier’s commitment to sustainability and ethical practices.
Utilizing ‘green’ materials in vending machine agreements, such as biodegradable packaging and recycled components, can enhance brand reputation and appeal to environmentally conscious consumers. By aligning with sustainable practices, international B2B buyers can not only mitigate risks but also capitalize on the growing demand for responsible sourcing.
Brief Evolution/History
The vending machine industry has evolved significantly since its inception in the early 20th century. Initially focused on simple snack and beverage distribution, the sector has transformed with advancements in technology and changing consumer preferences. The introduction of electronic payment systems in the 1980s marked a pivotal shift, allowing for greater convenience and efficiency in transactions.
In recent years, the rise of digital technology and the Internet of Things has further revolutionized the industry, enabling smarter machines that can provide data analytics, enhance user interaction, and streamline supply chain operations. As the market continues to evolve, international B2B buyers must stay informed about historical trends to make informed sourcing decisions that align with future developments in the vending machine sector.
Related Video: How Global Trade Runs on U.S. Dollars | WSJ
Frequently Asked Questions (FAQs) for B2B Buyers of vending machine agreement
-
What should I consider when vetting suppliers for vending machines?
When vetting suppliers, prioritize their experience in the vending machine industry and their ability to provide references from previous clients. Evaluate their production capacity and whether they can meet your specific needs, including customization options. Check for certifications that align with international standards, such as ISO or CE markings, to ensure quality and safety. Additionally, assess their financial stability and check reviews or ratings from other international buyers to gauge reliability. -
Can I customize vending machines according to my market needs?
Yes, many suppliers offer customization options for vending machines. This can include branding, machine configuration, and product selection tailored to local preferences. When negotiating your vending machine agreement, clearly outline your customization requirements and ask for prototypes or samples to ensure they meet your expectations. Be aware that customization may affect lead times and minimum order quantities, so factor this into your planning. -
What are the typical minimum order quantities (MOQs) and lead times for vending machines?
Minimum order quantities can vary significantly by supplier and region. Generally, MOQs may range from 5 to 50 units for standard machines, while customized machines could require higher quantities. Lead times often depend on the complexity of the order and the supplier’s production schedule, typically ranging from 4 to 12 weeks. It’s vital to discuss these details upfront to avoid delays and ensure your inventory aligns with market demand. -
What payment terms should I expect when sourcing vending machines internationally?
Payment terms can vary, but most suppliers will request a deposit (usually 30-50%) upon order confirmation, with the balance due before shipment. Be cautious of suppliers requiring full payment upfront, especially if you are unfamiliar with their reputation. Consider using secure payment methods such as letters of credit or escrow services to protect your investment. Negotiate terms that align with your cash flow needs while ensuring supplier accountability.
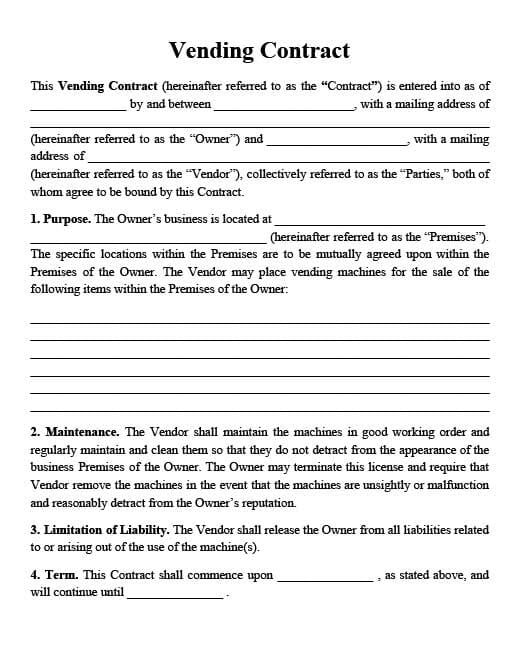
Illustrative Image (Source: Google Search)
-
How can I ensure quality assurance and certifications for vending machines?
To ensure quality, request documentation of relevant certifications and compliance with international standards. Ask suppliers for quality assurance processes, including testing procedures and warranty details. It’s advisable to conduct an on-site inspection or hire a third-party inspection service to verify product quality before shipment. Establishing clear quality expectations in your vending machine agreement can help mitigate risks related to defective products. -
What logistics considerations should I keep in mind when importing vending machines?
Logistics is crucial when importing vending machines. Assess shipping methods, costs, and estimated delivery times. Choose a reliable freight forwarder experienced in handling similar products to ensure compliance with customs regulations. Factor in duties and taxes, which can vary based on your location and the origin of the machines. It’s also wise to plan for potential delays and have contingency strategies in place to address any shipping issues. -
How can I handle disputes with vending machine suppliers?
To handle disputes effectively, include a clear dispute resolution clause in your vending machine agreement. This should outline steps for addressing issues, such as mediation or arbitration, to avoid lengthy litigation. Maintain open communication with the supplier and document all correspondence related to the dispute. If necessary, consult legal counsel familiar with international trade laws to navigate the resolution process. -
What are the best practices for maintaining a successful long-term relationship with vending machine suppliers?
To foster a successful long-term relationship, prioritize open and transparent communication. Regularly provide feedback on product performance and address any issues promptly. Consider visiting suppliers to strengthen ties and enhance collaboration. Establish a partnership mindset rather than a transactional relationship, which can lead to better pricing, priority service, and access to new products or technologies. Additionally, sharing market insights can benefit both parties and enhance mutual growth.
Strategic Sourcing Conclusion and Outlook for vending machine agreement
In summary, effective strategic sourcing for vending machine agreements is crucial for international B2B buyers seeking to optimize their operations and enhance customer satisfaction. By carefully evaluating supplier capabilities, negotiating favorable terms, and considering the unique needs of different markets—such as those in Africa, South America, the Middle East, and Europe—businesses can secure agreements that not only reduce costs but also improve service quality.
Key takeaways include the importance of building strong relationships with suppliers, leveraging data analytics for informed decision-making, and staying attuned to market trends that can impact product offerings. Investing in strategic sourcing not only drives profitability but also fosters innovation and agility, enabling businesses to respond swiftly to changing consumer preferences.
As you look to the future, consider how evolving technologies, such as cashless payment systems and smart vending solutions, can enhance your vending machine offerings. The landscape is ripe with opportunities for those willing to adapt and innovate. Now is the time to take action—evaluate your current sourcing strategies and explore new partnerships that can propel your business forward in this dynamic market.