Master Vending Machine Repair Services for Optimal Business
Guide to Vending Machine Repair Services
- Introduction: Navigating the Global Market for vending machine repair services
- Understanding vending machine repair services Types and Variations
- Key Industrial Applications of vending machine repair services
- Strategic Material Selection Guide for vending machine repair services
- In-depth Look: Manufacturing Processes and Quality Assurance for vending machine repair services
- Comprehensive Cost and Pricing Analysis for vending machine repair services Sourcing
- Spotlight on Potential vending machine repair services Manufacturers and Suppliers
- Essential Technical Properties and Trade Terminology for vending machine repair services
- Navigating Market Dynamics, Sourcing Trends, and Sustainability in the vending machine repair services Sector
- Frequently Asked Questions (FAQs) for B2B Buyers of vending machine repair services
- Strategic Sourcing Conclusion and Outlook for vending machine repair services
Introduction: Navigating the Global Market for vending machine repair services
In today’s rapidly evolving marketplace, vending machine repair services have emerged as a critical component for businesses relying on automated retail solutions. With the increasing prevalence of vending machines in diverse environments—from corporate offices to public transportation hubs—ensuring their operational efficiency is paramount. A breakdown not only disrupts service but can also lead to lost revenue and customer dissatisfaction.
This comprehensive guide is designed to empower international B2B buyers, particularly those in Africa, South America, the Middle East, and Europe, with the insights necessary for informed sourcing decisions. We delve into various aspects of vending machine repair services, including types of repairs, essential materials, manufacturing quality control (QC), reliable suppliers, and an overview of cost considerations.
Additionally, we provide a detailed analysis of the current market landscape and address frequently asked questions to clear any doubts buyers may have. By equipping you with this knowledge, our guide aims to facilitate strategic partnerships and enhance operational performance. With the right information at your fingertips, you can navigate the complexities of vending machine repair services with confidence, ensuring your investments yield optimal returns while maintaining customer satisfaction across your business operations.
Understanding vending machine repair services Types and Variations
Type Name | Key Distinguishing Features | Primary B2B Applications | Brief Pros & Cons for Buyers |
---|---|---|---|
On-Site Repair Services | Technicians perform repairs at the location | Offices, factories, schools | Pros: Immediate service, reduced downtime. Cons: Higher costs due to travel. |
Preventive Maintenance Services | Regularly scheduled checks and maintenance tasks | Retail environments, corporate offices | Pros: Reduces unexpected breakdowns, prolongs machine life. Cons: Ongoing cost commitment. |
Component Replacement Services | Replacement of faulty parts like motors or sensors | Large enterprises with multiple machines | Pros: Specific issue resolution, extends machine functionality. Cons: May require inventory of parts. |
Remote Diagnostics Services | Use of technology to diagnose issues remotely | Organizations with multiple locations | Pros: Quick identification of issues, lower travel costs. Cons: Limited to specific problems that can be diagnosed remotely. |
Comprehensive Repair Contracts | All-inclusive service agreements covering all repairs | Large corporations, vending machine operators | Pros: Predictable costs, comprehensive coverage. Cons: Longer commitment, potential for underutilization. |
On-Site Repair Services
On-site repair services involve technicians who travel to the location of the vending machine to conduct repairs. This type of service is ideal for businesses that require quick fixes to minimize downtime, such as offices, factories, and schools. Buyers should consider the urgency of repairs and the potential travel costs associated with this service. While it provides immediate solutions, costs may be higher due to technician travel.
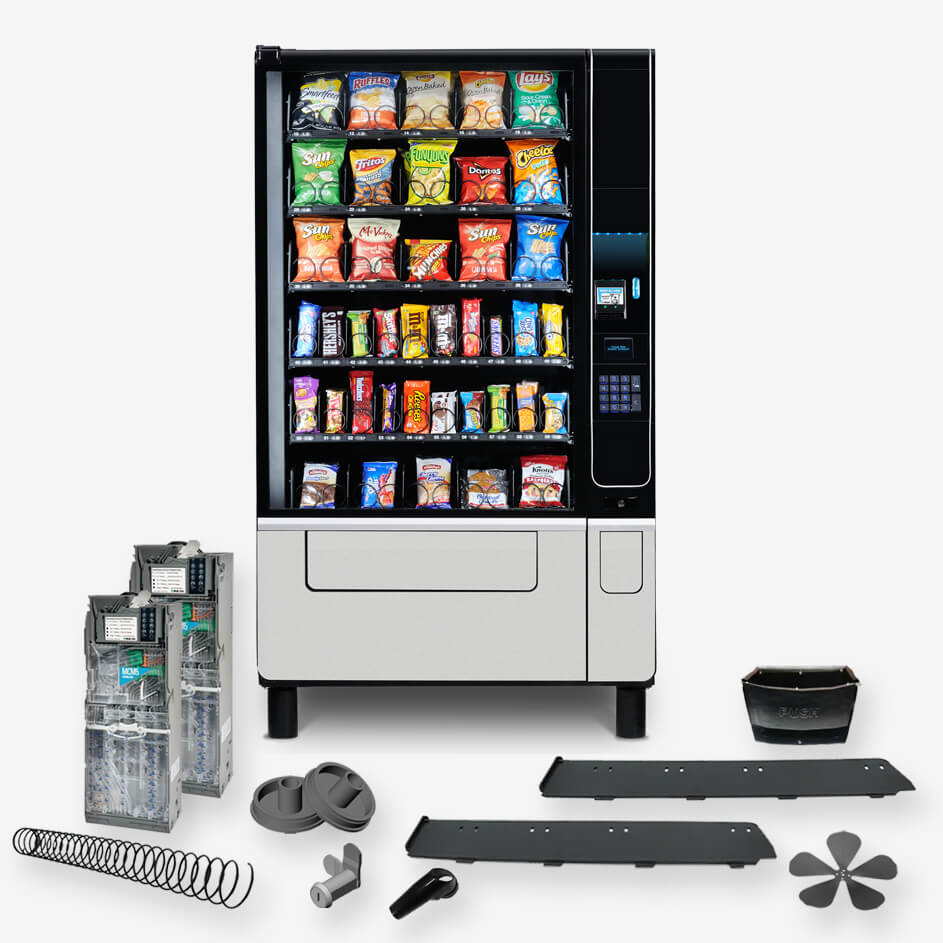
Illustrative Image (Source: Google Search)
Preventive Maintenance Services
Preventive maintenance services are designed to perform regular checks and maintenance tasks on vending machines. This proactive approach is essential for retail environments and corporate offices that rely heavily on vending operations. By investing in regular maintenance, businesses can reduce unexpected breakdowns and extend the lifespan of their machines. However, buyers must weigh the ongoing costs against the benefits of fewer disruptions.
Component Replacement Services
Component replacement services focus on replacing faulty parts of vending machines, such as motors, sensors, or payment systems. This service is particularly beneficial for large enterprises that operate multiple machines, as it allows for targeted repairs. While this option can effectively resolve specific issues and extend the functionality of vending machines, businesses should be prepared for the necessity of maintaining an inventory of replacement parts.
Remote Diagnostics Services
Remote diagnostics services utilize technology to identify issues without the need for a technician to be physically present. This service is well-suited for organizations with multiple locations, as it allows for quick problem identification and can reduce travel costs. However, it is important for buyers to understand that this method may be limited to issues that can be diagnosed without on-site inspection, which could lead to incomplete resolutions.
Comprehensive Repair Contracts
Comprehensive repair contracts offer an all-inclusive agreement covering all repairs and maintenance for vending machines. This type of service is particularly attractive to large corporations and vending machine operators who want predictable costs and extensive coverage. While these contracts can provide peace of mind and minimize unexpected expenses, buyers need to be cautious of committing to long-term agreements that may lead to underutilization of services if machine usage fluctuates.
Related Video: SE 12 : All SDLC Models Revision | Software Engineering Full Course
Key Industrial Applications of vending machine repair services
Industry/Sector | Specific Application of vending machine repair services | Value/Benefit for the Business | Key Sourcing Considerations for this Application |
---|---|---|---|
Retail | Maintenance of snack and beverage vending machines | Ensures continuous operation, reducing downtime | Availability of local technicians, response time |
Healthcare | Repair of vending machines in hospitals | Provides quick access to refreshments for staff/patients | Compliance with health regulations, machine sanitization |
Education | Servicing vending machines in schools and universities | Supports student convenience and satisfaction | Understanding of school schedules, reliability of service |
Transportation | Maintenance of vending machines in airports and stations | Enhances traveler experience, increases sales | Specialized knowledge of high-traffic environments |
Corporate Offices | Repair of vending machines in office buildings | Boosts employee morale and productivity | Customization options for product offerings, service contracts |
Retail
In the retail sector, vending machine repair services are crucial for maintaining snack and beverage machines. Retailers face the challenge of ensuring these machines are operational to meet customer demand and avoid revenue loss. Regular maintenance and quick repair services minimize downtime, allowing retailers to maximize sales opportunities. Buyers in this sector should consider the availability of local technicians and the response time for repairs to maintain service continuity.
Healthcare
Vending machines in healthcare facilities, such as hospitals, provide essential snacks and beverages for staff and patients. Repair services ensure these machines remain operational, providing quick access to refreshments, which can be vital during long shifts. For international buyers, it is important to ensure compliance with health regulations and the ability to sanitize machines regularly to meet hygiene standards, particularly in sensitive environments like hospitals.
Education
In educational institutions, vending machines serve students by offering quick access to snacks and drinks between classes. Repair services are essential to keep these machines functional, thereby supporting student convenience and satisfaction. Buyers from educational sectors should be aware of school schedules to plan maintenance and repairs effectively, ensuring minimal disruption to students and staff while maintaining a reliable service.
Transportation
Vending machines located in transportation hubs, such as airports and train stations, require regular maintenance to enhance traveler experiences. These machines cater to a high volume of customers and can significantly impact overall satisfaction. Buyers should seek repair services that understand the unique demands of high-traffic environments, ensuring machines are stocked and operational at all times to capture sales opportunities.
Corporate Offices
In corporate environments, vending machines play a role in boosting employee morale and productivity by providing convenient access to snacks and drinks. Repair services help maintain these machines, ensuring they are always stocked and functioning. Companies should look for service providers that offer customization options for product offerings and flexible service contracts, allowing them to adapt to changing employee preferences and needs.
Related Video: How to Start a Vending Machine Business, Cost, Tips, How Much You Make
Strategic Material Selection Guide for vending machine repair services
When selecting materials for vending machine repair services, it is critical to consider the specific properties and performance requirements of each material. Below, we analyze four common materials used in vending machine components, focusing on their key properties, advantages and disadvantages, and their impact on applications. Additionally, we highlight specific considerations for international B2B buyers, particularly from Africa, South America, the Middle East, and Europe.
1. Stainless Steel (e.g., AISI 304)
Key Properties: Stainless steel is known for its excellent corrosion resistance, high strength, and ability to withstand a wide range of temperatures. It typically has a temperature rating of up to 870°C (1600°F) and maintains structural integrity under pressure.
Pros & Cons: Stainless steel is durable and easy to clean, making it ideal for food-related applications. However, it is more expensive than other metals and can be challenging to machine, leading to increased manufacturing complexity.
Impact on Application: Its corrosion resistance makes it suitable for environments where moisture is prevalent, such as in vending machines dispensing beverages. It is compatible with various media, including water and soft drinks.
Considerations for International Buyers: Buyers should ensure compliance with international standards such as ASTM and EN for food safety. In regions like Europe, certifications for food-grade materials are essential.
2. Carbon Steel (e.g., A216 WCB)
Key Properties: Carbon steel is characterized by its high tensile strength and toughness. It typically has a temperature rating of around 400°C (752°F) and is less resistant to corrosion compared to stainless steel.
Pros & Cons: This material is cost-effective and widely available, making it suitable for structural components. However, it is prone to rusting if not properly coated or maintained, which can lead to reduced lifespan in humid environments.
Impact on Application: Carbon steel is often used in the structural framework of vending machines where corrosion is not a primary concern. It is compatible with various mechanical components but may not be suitable for direct contact with food or beverages.
Considerations for International Buyers: Buyers should consider local environmental conditions that may affect the longevity of carbon steel components. Compliance with standards like ASTM is crucial for ensuring quality.
3. Polycarbonate
Key Properties: Polycarbonate is a thermoplastic known for its high impact resistance, clarity, and lightweight nature. It can withstand temperatures up to 120°C (248°F) and has excellent dimensional stability.
Pros & Cons: Polycarbonate is highly durable and resistant to shattering, making it ideal for transparent components like vending machine windows. However, it can be susceptible to scratching and UV degradation over time.
Impact on Application: This material is often used for protective covers and panels, allowing visibility while protecting internal components. It is compatible with a range of media but should be evaluated for chemical compatibility with specific products.
Considerations for International Buyers: Buyers should ensure that polycarbonate components meet relevant safety and environmental regulations. In regions like Europe, compliance with REACH regulations is essential.
4. Rubber (e.g., EPDM)
Key Properties: EPDM rubber is known for its excellent weather resistance, flexibility, and thermal stability. It can perform well in temperatures ranging from -40°C to 120°C (-40°F to 248°F).
Pros & Cons: Rubber provides good sealing properties and is cost-effective for gaskets and seals. However, it may degrade over time when exposed to certain chemicals or UV light, which can limit its lifespan.
Impact on Application: EPDM is commonly used in sealing applications within vending machines, ensuring that moisture and contaminants do not enter sensitive areas. It is compatible with a variety of fluids, including water and oils.
Considerations for International Buyers: Buyers should verify that rubber materials comply with local standards for safety and durability. In the Middle East, for example, high temperatures can affect rubber performance, necessitating careful selection.
Summary Table
Material | Typical Use Case for vending machine repair services | Key Advantage | Key Disadvantage/Limitation | Relative Cost (Low/Med/High) |
---|---|---|---|---|
Stainless Steel (e.g., AISI 304) | Food contact surfaces, structural components | Excellent corrosion resistance, durability | Higher cost, manufacturing complexity | High |
Carbon Steel (e.g., A216 WCB) | Structural framework, non-food contact parts | Cost-effective, high strength | Prone to corrosion without protection | Low |
Polycarbonate | Windows, protective covers | High impact resistance, lightweight | Susceptible to scratching and UV damage | Medium |
Rubber (e.g., EPDM) | Seals and gaskets | Good sealing properties, cost-effective | Degrades with certain chemicals/UV exposure | Low |
This strategic material selection guide aims to equip international B2B buyers with the necessary insights to make informed decisions regarding material choices for vending machine repair services, ensuring optimal performance and compliance with regional standards.
In-depth Look: Manufacturing Processes and Quality Assurance for vending machine repair services
Manufacturing and quality assurance processes in vending machine repair services are critical for ensuring reliability and efficiency. For international B2B buyers, particularly those in Africa, South America, the Middle East, and Europe, understanding these processes can significantly impact procurement decisions. Below is a comprehensive overview of typical manufacturing stages, quality control measures, and actionable insights for verifying supplier capabilities.
Manufacturing Processes
The manufacturing of vending machine components and repair services typically involves several key stages:
1. Material Preparation
Material selection is crucial in the manufacturing process. Common materials include metals (e.g., steel for frames), plastics (for buttons and casings), and electronic components (for circuitry).
- Sourcing: Reliable suppliers should provide materials that meet international standards to ensure durability and safety.
- Inspection: Incoming materials undergo inspection for quality assurance, checking for defects or non-compliance with specifications.
2. Forming
This stage involves shaping the materials into required forms. Techniques include:
- Stamping: Used for creating metal parts like frames and panels.
- Molding: Common for plastic components, ensuring precise shapes for buttons and interfaces.
3. Assembly
In this phase, the various components are brought together.
- Automated Assembly Lines: Many manufacturers utilize automated systems to enhance precision and efficiency.
- Manual Assembly: Skilled workers may assemble intricate parts, especially in more complex machines or custom repairs.
4. Finishing
The final stage involves surface treatments and coatings to enhance durability and aesthetics.
- Painting and Coating: Protective coatings are applied to prevent corrosion and improve appearance.
- Quality Checks: Each finished product undergoes rigorous inspection to ensure it meets specifications.
Quality Assurance
Quality assurance is fundamental to maintaining standards in vending machine repair services. Adhering to recognized international standards and conducting thorough inspections at various checkpoints are essential practices.
Relevant International Standards
- ISO 9001: This standard focuses on quality management systems and is crucial for ensuring consistent quality in manufacturing processes.
- CE Marking: Indicates compliance with European health, safety, and environmental protection standards.
- API Standards: Relevant for components that may be used in specialized applications, particularly in regions with specific regulatory requirements.
Quality Control Checkpoints
Quality control involves several checkpoints throughout the manufacturing process:
- Incoming Quality Control (IQC): Inspection of raw materials upon arrival to ensure they meet specified standards.
- In-Process Quality Control (IPQC): Continuous monitoring during the manufacturing process to identify defects early.
- Final Quality Control (FQC): A thorough inspection of finished products to verify compliance with specifications before shipment.
Common Testing Methods
Testing methods are essential for verifying the quality and functionality of vending machines:
- Functional Testing: Ensures all components operate correctly, such as coin mechanisms and display screens.
- Durability Testing: Simulates real-world conditions to assess the longevity of components.
- Electrical Safety Testing: Verifies that all electronic components meet safety standards to prevent hazards.
Verifying Supplier Quality Control
For international B2B buyers, ensuring that suppliers maintain high-quality standards is crucial. Here are actionable steps to verify supplier capabilities:
Audits and Inspections
- Conduct Supplier Audits: Regular audits can help assess a supplier’s quality management practices and adherence to standards.
- Third-Party Inspections: Engaging independent inspectors can provide an unbiased evaluation of manufacturing processes and product quality.
Documentation and Reporting
- Request Quality Reports: Suppliers should provide documentation of their quality control processes, including inspection reports and compliance certifications.
- Traceability: Ensure that suppliers can trace materials back to their source, which is essential for accountability and quality assurance.
Understanding Quality Control Nuances
International buyers should be aware of specific quality control nuances in different regions. For example:
- Regulatory Requirements: Different countries may have varying regulatory requirements affecting the quality assurance process. Understanding these can help buyers ensure compliance.
- Cultural Differences: There may be different approaches to quality assurance and manufacturing, influenced by regional practices. Building strong relationships with suppliers can facilitate better communication and understanding.
Conclusion
In summary, the manufacturing processes and quality assurance measures for vending machine repair services are essential for ensuring product reliability and safety. International B2B buyers, especially from Africa, South America, the Middle East, and Europe, should prioritize suppliers who adhere to recognized standards and demonstrate robust quality control practices. By taking proactive steps to verify supplier capabilities, buyers can significantly enhance their procurement outcomes and ensure the longevity of their vending machine operations.
Related Video: The Production Planning Process
Comprehensive Cost and Pricing Analysis for vending machine repair services Sourcing
In the realm of vending machine repair services, understanding the cost structure and pricing dynamics is crucial for international B2B buyers, especially those operating in regions such as Africa, South America, the Middle East, and Europe, including Turkey and Saudi Arabia. This analysis will provide insights into the key components of costs, pricing influencers, and practical tips for negotiation and procurement.
Cost Components
-
Materials: The cost of materials is often the largest component in the repair of vending machines. This includes parts such as electrical components, motors, and structural elements. Sourcing high-quality materials can impact longevity and performance, thus influencing overall repair costs.
-
Labor: Labor costs include wages for technicians who perform repairs. In regions with varying labor costs, this can significantly affect the total cost. Skilled labor often commands higher wages, but can lead to faster and more reliable repairs.
-
Manufacturing Overhead: This includes indirect costs associated with running a repair facility, such as utilities, rent, and equipment depreciation. Depending on the supplier’s location, these costs can vary widely.
-
Tooling: Specialized tools may be required for specific repairs, adding to the cost. For instance, vending machines with advanced technology may necessitate unique diagnostic tools.
-
Quality Control (QC): Ensuring that repairs meet industry standards can incur additional costs. Implementing robust QC processes may include testing and certifications that assure the reliability of the repaired units.
-
Logistics: Shipping and handling costs can be substantial, especially for international transactions. Factors such as shipping distance, mode of transport, and customs duties should be considered in total logistics costs.
-
Margin: Suppliers will typically add a margin to cover their operational risks and ensure profitability. Understanding the market rates for margins in specific regions can help buyers gauge fair pricing.
Price Influencers
-
Volume/MOQ: Purchasing in bulk can lead to significant discounts. Suppliers often have minimum order quantities (MOQs) that can impact pricing, particularly for international buyers.
-
Specifications/Customization: Custom repairs or specialized parts may come at a premium. Buyers should assess whether standard components can suffice to keep costs down.
-
Materials: The choice of materials directly affects both cost and quality. Higher-grade materials may have a higher upfront cost but can reduce long-term maintenance expenses.
-
Quality/Certifications: Suppliers with recognized certifications may charge more, but this can be a worthwhile investment for ensuring reliability and compliance with local regulations.
-
Supplier Factors: The supplier’s reputation, reliability, and service level can influence pricing. Established suppliers may command higher prices but often provide better service and assurance of quality.
-
Incoterms: Understanding Incoterms (International Commercial Terms) is essential for determining who bears the costs and risks at each stage of shipping. This can significantly affect the total landed cost of repairs.
Buyer Tips
-
Negotiation: Always negotiate terms and pricing, especially when dealing with larger orders. Establishing long-term relationships can also lead to better terms.
-
Cost-Efficiency: Consider total cost of ownership, which includes not just the initial repair costs but also potential future maintenance and downtime.
-
Pricing Nuances: Be aware of regional pricing differences. What may seem expensive in one market could be standard in another. Research local market conditions thoroughly.
-
Supplier Assessment: Evaluate potential suppliers not just on price but on their ability to deliver timely and quality service. Request references and conduct site visits if possible.
-
Stay Informed: Keep abreast of changes in material costs and labor rates, as these can fluctuate due to economic conditions or local regulations.
Disclaimer
Prices and costs mentioned are indicative and may vary based on specific circumstances, including location, order size, and supplier capabilities. Always consult with suppliers for precise quotes tailored to your needs.
Spotlight on Potential vending machine repair services Manufacturers and Suppliers
This section offers a look at a few manufacturers active in the ‘vending machine repair services’ market. This is a representative sample for illustrative purposes; B2B buyers must conduct their own extensive due diligence before any engagement. Information is synthesized from public sources and general industry knowledge.
Essential Technical Properties and Trade Terminology for vending machine repair services
Key Technical Properties for Vending Machine Repair Services
When considering vending machine repair services, understanding critical technical properties can significantly influence procurement decisions. Here are some essential specifications to keep in mind:
-
Material Grade: The quality of materials used in vending machines, such as stainless steel or high-grade plastics, affects durability and resistance to wear and tear. High-quality materials ensure longevity and reduce maintenance costs, making it vital for buyers to prioritize suppliers that adhere to industry standards.
-
Tolerance Levels: Tolerance refers to the allowable variation in dimensions during manufacturing. Precision in tolerances ensures that parts fit together correctly, which is crucial for the optimal functioning of vending machines. For B2B buyers, selecting vendors that maintain strict tolerance standards can lead to fewer operational issues and lower repair frequency.
-
Voltage Ratings: Understanding the electrical specifications, including voltage ratings and compatibility, is essential for safe operation. Vending machines often operate at specific voltage levels, and improper ratings can lead to equipment failure or safety hazards. Buyers should ensure that repair services are knowledgeable about the electrical requirements of the machines they service.
-
Load Capacity: Each vending machine has a defined load capacity for the products it can carry. When sourcing repair services, buyers must ensure that the service provider understands the implications of exceeding these capacities, which can lead to mechanical failure or safety risks.
-
Service Interval Recommendations: Regular maintenance intervals, typically recommended by manufacturers, can vary based on machine usage. Understanding these intervals helps buyers establish maintenance contracts that align with their operational needs and prevent downtime.
-
Warranty Coverage: Warranty terms on parts and services provided can vary significantly among vendors. Buyers should seek clear information regarding warranty length and coverage, as this can impact long-term maintenance costs and service reliability.
Common Trade Terminology in Vending Machine Repair Services
Familiarity with industry jargon can enhance communication with suppliers and streamline procurement processes. Here are several common terms:
-
OEM (Original Equipment Manufacturer): Refers to companies that produce parts or equipment that may be marketed by another manufacturer. Understanding OEM parts is crucial for ensuring compatibility and quality in repairs.
-
MOQ (Minimum Order Quantity): The smallest quantity of a product that a supplier is willing to sell. Knowing the MOQ helps buyers manage inventory effectively and avoid excess costs.
-
RFQ (Request for Quotation): A formal request to suppliers to provide pricing information for specific products or services. An effective RFQ process allows buyers to compare costs and select the best vendor based on price and service quality.
-
Incoterms (International Commercial Terms): A set of pre-defined commercial terms published by the International Chamber of Commerce. They clarify the responsibilities of buyers and sellers in international transactions, including shipping, insurance, and tariffs, which is critical for cross-border procurement.
-
Lead Time: The time it takes for an order to be fulfilled after it has been placed. Understanding lead times helps buyers plan for repairs and replacements, minimizing downtime for vending operations.
-
Service Level Agreement (SLA): A contract that outlines the expected level of service between a service provider and a client. This agreement is crucial in defining response times, repair timelines, and overall service expectations, ensuring that both parties have clear understandings of their responsibilities.
By grasping these technical properties and industry terms, B2B buyers can make informed decisions that align with their operational needs and enhance the efficiency of their vending machine services.
Navigating Market Dynamics, Sourcing Trends, and Sustainability in the vending machine repair services Sector
Market Overview & Key Trends
The vending machine repair services sector is experiencing significant transformation driven by technological advancements and evolving consumer preferences. International B2B buyers, particularly from regions such as Africa, South America, the Middle East, and Europe, are witnessing a shift towards smart vending solutions. These machines are equipped with IoT (Internet of Things) capabilities, allowing for real-time monitoring and predictive maintenance. This not only reduces downtime but also enhances operational efficiency, making it imperative for businesses to partner with service providers who can support these technologies.
Another key trend is the rise of e-commerce platforms that facilitate easier sourcing of parts and services. Buyers can now leverage digital marketplaces to compare vendors, access customer reviews, and make informed decisions quickly. Moreover, the demand for enhanced customer experiences is driving vending service providers to adopt cashless payment systems and personalized product offerings, aligning with consumer trends towards convenience and customization.
The competitive landscape is also evolving, with an increasing emphasis on service quality and customer support. B2B buyers must prioritize partnerships with repair service providers that offer comprehensive support packages, including remote diagnostics and rapid response times, to stay ahead in a market that values reliability and speed.
Sustainability & Ethical Sourcing in B2B
Sustainability has become a cornerstone for businesses operating in the vending machine repair services sector. The environmental impact of traditional vending operations is significant, from energy consumption to waste generated by single-use products. Thus, international buyers are increasingly seeking out service providers who adopt eco-friendly practices. This includes the use of energy-efficient vending machines and biodegradable or recyclable materials in the products offered.
Ethical sourcing is equally important, as buyers are now focusing on supply chains that prioritize fair labor practices and sustainable materials. Vending machine repair services that are certified with ‘green’ labels or that utilize environmentally friendly components in their repairs not only enhance their brand image but also attract a growing segment of eco-conscious consumers.
By integrating sustainability into their operations, service providers can differentiate themselves in a competitive market. For B2B buyers, this means aligning with partners who are committed to sustainable practices, thus ensuring that their own operations contribute positively to environmental goals.
Brief Evolution/History
The vending machine repair services industry has evolved significantly since its inception in the early 20th century. Initially focused on mechanical repairs, the sector has transformed with the advent of digital technologies. The introduction of electronic and later smart vending machines has shifted the focus of repair services from simple mechanical fixes to complex electronic and software troubleshooting.
As consumer preferences have changed, so too have the offerings within the vending sector. The integration of payment technology, such as contactless payments and mobile wallets, has necessitated a new skill set for repair technicians. Today, successful service providers are those who not only repair machines but also enhance them to meet modern consumer expectations, making ongoing training and development a critical component of their service delivery.
Related Video: Incoterms for beginners | Global Trade Explained
Frequently Asked Questions (FAQs) for B2B Buyers of vending machine repair services
-
How do I vet suppliers for vending machine repair services?
When vetting suppliers, consider their industry experience, reputation, and certifications. Request references from previous clients and check online reviews to gauge reliability. It’s also essential to evaluate their technical expertise in specific vending machine brands and models. Conducting a site visit, if possible, can provide insights into their operational capabilities and adherence to quality standards. -
Can I customize the vending machine repair services offered?
Most suppliers offer customization options tailored to your specific needs, such as service frequency, types of machines serviced, and parts used. Discuss your requirements upfront to ensure they can accommodate your requests. Additionally, inquire about the flexibility of service agreements to adjust to seasonal demand or unexpected machine failures. -
What are the minimum order quantities (MOQ) and lead times for services?
MOQs for vending machine repair services can vary widely depending on the supplier and the complexity of the required repairs. Typically, suppliers may not have strict MOQs for repair services, but lead times can range from a few days to several weeks. Always clarify these terms during negotiations to ensure they align with your operational timelines.
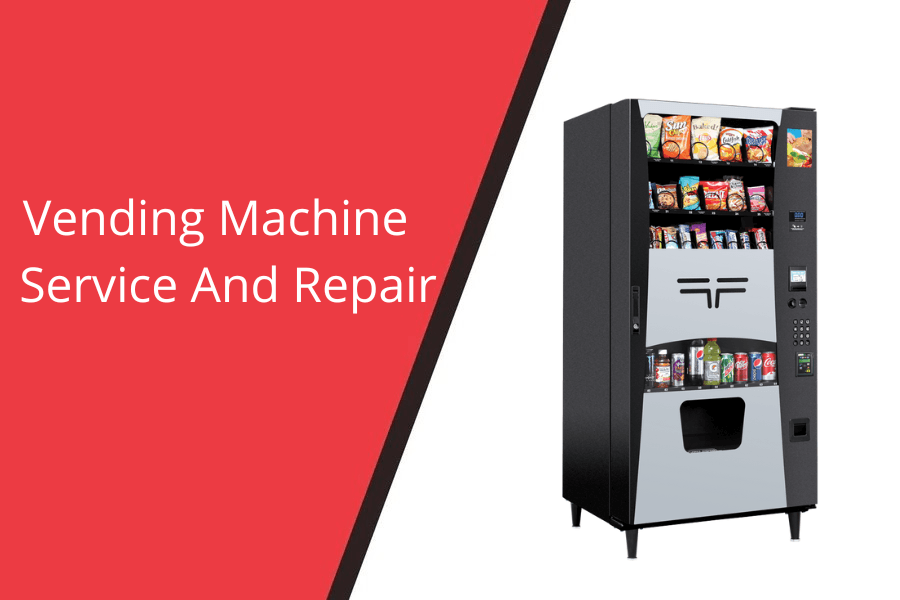
Illustrative Image (Source: Google Search)
-
What payment terms should I expect when sourcing these services?
Payment terms can differ by supplier, but common practices include upfront deposits, net 30/60 days, or pay-per-service completed. Consider establishing a clear agreement that outlines payment schedules, acceptable payment methods, and any potential penalties for late payments. This clarity helps prevent misunderstandings and ensures a smoother transaction process. -
What quality assurance measures and certifications should I look for?
Verify that suppliers adhere to industry standards and possess relevant certifications, such as ISO 9001 for quality management systems. Ask about their quality assurance processes, including how they handle defective parts and service guarantees. Request documentation of their compliance with local regulations, especially if you are operating in different countries. -
How does logistics work for international service calls?
Logistics for international service calls can involve various factors, including shipping parts and coordinating technician travel. Discuss with your supplier how they manage logistics, including timelines for shipping parts and their ability to send technicians abroad. Establish clear communication channels to handle any logistical challenges that may arise during the service process. -
What should I do if I encounter a dispute with my supplier?
In the event of a dispute, start by reviewing your contract to understand your rights and obligations. Engage in open communication with your supplier to seek a resolution. If necessary, involve a third-party mediator or arbitration service, especially for international contracts, to ensure a fair outcome. Document all communications and agreements to support your position. -
Are there any specific regulations I need to be aware of when sourcing these services?
Yes, regulations can vary significantly by country and region. Research local laws related to vending machine operations, safety standards, and repair services. For instance, some countries may require specific certifications for technicians or compliance with environmental regulations regarding waste disposal. Engaging a local legal expert can help you navigate these requirements effectively.
Strategic Sourcing Conclusion and Outlook for vending machine repair services
As international B2B buyers navigate the complexities of sourcing vending machine repair services, strategic sourcing emerges as a pivotal approach to ensure operational efficiency and reliability. Key takeaways include the importance of establishing strong relationships with service providers, understanding local market nuances, and leveraging technology for better service management.
Investing in quality repair services not only minimizes downtime but also enhances customer satisfaction and loyalty. Buyers from regions such as Africa, South America, the Middle East, and Europe should prioritize vendors that offer comprehensive service packages, including preventive maintenance and rapid response times. This proactive stance can significantly reduce long-term costs and increase the lifespan of vending machines.
Looking ahead, the demand for vending machine repair services is set to grow, driven by the expansion of automated retail solutions. To capitalize on this trend, international buyers are encouraged to evaluate potential partners carefully, focusing on those that demonstrate innovation, reliability, and a commitment to customer service. By embracing strategic sourcing, businesses can secure a competitive edge in the evolving marketplace.