Master Vending Machine Repair Near Me for Optimal Business
Guide to Vending Machine Repair Near Me
- Introduction: Navigating the Global Market for vending machine repair near me
- Understanding vending machine repair near me Types and Variations
- Key Industrial Applications of vending machine repair near me
- Strategic Material Selection Guide for vending machine repair near me
- In-depth Look: Manufacturing Processes and Quality Assurance for vending machine repair near me
- Comprehensive Cost and Pricing Analysis for vending machine repair near me Sourcing
- Spotlight on Potential vending machine repair near me Manufacturers and Suppliers
- Essential Technical Properties and Trade Terminology for vending machine repair near me
- Navigating Market Dynamics, Sourcing Trends, and Sustainability in the vending machine repair near me Sector
- Frequently Asked Questions (FAQs) for B2B Buyers of vending machine repair near me
- Strategic Sourcing Conclusion and Outlook for vending machine repair near me
Introduction: Navigating the Global Market for vending machine repair near me
In today’s fast-paced marketplace, the functionality of vending machines plays a pivotal role in enhancing customer experience and driving sales. For international B2B buyers, particularly those operating in Africa, South America, the Middle East, and Europe, understanding the nuances of vending machine repair is essential. Reliable maintenance and timely repairs not only ensure operational efficiency but also extend the lifespan of these machines, ultimately safeguarding your investment.
This comprehensive guide delves into the critical aspects of vending machine repair, providing actionable insights that empower informed sourcing decisions. We cover a broad spectrum of topics, including various types of vending machines, essential repair materials, manufacturing and quality control standards, and a curated list of reputable suppliers. Additionally, we explore the cost implications of repairs, market trends, and frequently asked questions, equipping you with the knowledge needed to navigate the global landscape effectively.
With this guide, B2B buyers can identify trusted partners and establish robust maintenance protocols that enhance service delivery. By investing in proper repair strategies, businesses can avoid costly downtime, improve customer satisfaction, and maintain a competitive edge in their respective markets. Whether you’re in Poland or Argentina, this resource serves as a critical tool for optimizing your vending machine operations and ensuring that your business remains at the forefront of innovation and service excellence.
Understanding vending machine repair near me Types and Variations
Type Name | Key Distinguishing Features | Primary B2B Applications | Brief Pros & Cons for Buyers |
---|---|---|---|
Mechanical Repair | Involves fixing physical components and mechanisms | High-traffic locations, offices | Pros: Cost-effective; Cons: May require frequent maintenance. |
Electronic Repair | Focuses on circuit boards, sensors, and software | Retail environments, event venues | Pros: Ensures reliability; Cons: Can be complex and costly. |
Cosmetic Repair | Addresses aesthetic issues like scratches or dents | Hospitality, corporate offices | Pros: Enhances appearance; Cons: Minimal impact on functionality. |
Preventative Maintenance | Regular check-ups to prevent breakdowns | All vending machine locations | Pros: Reduces downtime; Cons: Requires scheduling and planning. |
Emergency Repair | Immediate response for urgent malfunctions | Busy public spaces, transit hubs | Pros: Quick resolution; Cons: Higher costs due to urgency. |
Mechanical Repair
Mechanical repair is essential for addressing the physical components of vending machines, such as levers, motors, and coin mechanisms. This type of repair is particularly relevant for high-traffic locations like offices and educational institutions, where machines endure heavy usage. When considering mechanical repairs, B2B buyers should evaluate the cost-effectiveness and the potential need for ongoing maintenance due to wear and tear, which can affect the overall efficiency of the vending service.
Electronic Repair
Electronic repair focuses on the circuitry and software that power modern vending machines. This includes fixing issues related to payment systems, user interfaces, and sensors. Businesses operating in retail environments or event venues often require reliable electronic systems for seamless transactions. B2B buyers should weigh the complexity and potential costs associated with electronic repairs, particularly if machines are equipped with advanced technology that requires specialized knowledge for maintenance.
Cosmetic Repair
Cosmetic repair is aimed at enhancing the visual appeal of vending machines, addressing issues such as scratches, dents, or outdated branding. This type of repair is particularly important in hospitality settings or corporate offices where aesthetics can impact customer perception. While cosmetic repairs do not directly affect machine functionality, they can significantly enhance the user experience. Buyers should consider the balance between cosmetic upgrades and functional repairs, as the former may not always justify the costs.
Preventative Maintenance
Preventative maintenance involves routine inspections and servicing to avoid future breakdowns. This proactive approach is applicable across all vending machine locations and is vital for minimizing downtime and ensuring consistent operation. B2B buyers should recognize the importance of scheduling regular maintenance to enhance machine longevity and reliability. Although it requires advance planning, the long-term benefits often outweigh the initial investment in preventative services.
Emergency Repair
Emergency repair services are critical for addressing urgent malfunctions that can disrupt service in busy public spaces or transit hubs. This type of repair ensures that machines are back in operation as quickly as possible, minimizing lost revenue. However, B2B buyers should be aware that emergency repairs often come with higher costs due to the urgency and resources required. It is essential for businesses to have a reliable emergency repair service in place to mitigate the impact of unexpected breakdowns on their operations.
Related Video: What is E-Commerce? Definition, Types, and Business Models
Key Industrial Applications of vending machine repair near me
Industry/Sector | Specific Application of vending machine repair near me | Value/Benefit for the Business | Key Sourcing Considerations for this Application |
---|---|---|---|
Retail | Repair of snack and beverage vending machines | Increased customer satisfaction and sales through reliable service | Availability of certified technicians and parts |
Healthcare | Maintenance of vending machines in hospitals | Ensures availability of essential supplies for patients and staff | Compliance with health regulations and equipment standards |
Education | Support for vending machines in schools and universities | Enhances student experience and convenience | Understanding of specific needs for age groups and dietary options |
Transportation | Repair services for vending machines in airports and bus stations | Minimizes downtime and maximizes revenue opportunities | Quick response times and ability to work in high-traffic areas |
Corporate Offices | Servicing vending machines in office buildings | Improves employee morale and productivity | Reliable service agreements and flexibility in scheduling |
Retail
In the retail sector, vending machines serve as convenient points of sale for snacks and beverages. Regular repair services are essential to ensure these machines are operational, preventing lost sales due to outages. B2B buyers in this sector should prioritize sourcing technicians who can provide timely repairs and maintenance to minimize downtime. Additionally, ensuring the availability of certified parts can enhance the longevity and reliability of vending machines, directly impacting customer satisfaction and overall revenue.
Healthcare
In healthcare facilities, vending machines often provide essential items like snacks, beverages, and hygiene products. The reliable operation of these machines is crucial for both patient and staff needs. B2B buyers in this sector must consider vendors who understand healthcare compliance regulations, ensuring machines meet safety and hygiene standards. Regular maintenance and prompt repair services are necessary to prevent disruptions in service, which can impact patient care and staff efficiency.
Education
Vending machines in educational institutions cater to students’ needs for snacks and beverages throughout the day. Effective repair services are vital to maintain a steady supply of these conveniences. B2B buyers in the education sector should focus on providers who understand the unique demands of young consumers, including healthy options and dietary restrictions. Ensuring quick repair times can enhance the student experience, promoting higher usage rates and, ultimately, increased revenue for the institution.
Transportation
In the transportation industry, vending machines located in airports and bus stations serve travelers looking for quick refreshments. Given the high foot traffic in these areas, prompt repair services are necessary to minimize downtime and maximize sales opportunities. B2B buyers should seek repair services that can respond quickly to issues and have experience working in high-traffic environments. Understanding the unique needs of travelers, such as offering diverse product options, can also enhance customer satisfaction.
Corporate Offices
Corporate offices utilize vending machines to provide employees with convenient access to snacks and beverages. Regular servicing and prompt repairs are critical to maintaining employee morale and productivity. B2B buyers in this sector should consider establishing service agreements with providers who can offer flexible scheduling and reliable maintenance. This ensures that machines are always stocked and operational, thereby enhancing the workplace environment and contributing positively to employee satisfaction.
Related Video: How to Start a Vending Machine Business, Cost, Tips, How Much You Make
Strategic Material Selection Guide for vending machine repair near me
When selecting materials for vending machine repair, it is crucial to consider the properties, advantages, limitations, and specific regional compliance requirements. Below is an analysis of four common materials used in vending machine repair, focusing on their performance characteristics and implications for international B2B buyers.
1. Stainless Steel
Key Properties:
Stainless steel is known for its excellent corrosion resistance, high strength, and ability to withstand extreme temperatures. It typically has a temperature rating of up to 800°C and is resistant to rust and staining.
Pros & Cons:
The durability of stainless steel makes it ideal for vending machines exposed to various environmental conditions. It is relatively easy to clean and maintain, which is critical for hygiene in food and beverage applications. However, the initial cost can be high compared to other materials, and it may require specialized welding techniques, increasing manufacturing complexity.
Impact on Application:
Stainless steel is compatible with a wide range of media, including food and beverages, making it a preferred choice for components like frames, doors, and internal mechanisms.
Considerations for International Buyers:
Buyers should ensure compliance with food safety standards such as FDA regulations in the U.S. and EFSA in Europe. Common standards like ASTM A240 should be referenced for material specifications.
2. Aluminum
Key Properties:
Aluminum is lightweight, corrosion-resistant, and has a good strength-to-weight ratio. It can handle temperatures up to 400°C, making it suitable for various components in vending machines.
Pros & Cons:
Aluminum is cost-effective and easy to machine, which simplifies manufacturing processes. However, it is less durable than stainless steel and can be prone to deformation under high stress. Its susceptibility to oxidation can also be a concern in certain environments.
Impact on Application:
Aluminum is often used for structural components and panels, but its compatibility with certain chemicals should be assessed, especially in vending machines dispensing beverages.
Considerations for International Buyers:
Buyers in regions like South America and Africa should consider local environmental conditions that may affect aluminum’s performance. Standards such as ASTM B221 for aluminum extrusions should be adhered to.
3. Carbon Steel
Key Properties:
Carbon steel is known for its high tensile strength and durability. It can withstand high pressures and temperatures, typically rated up to 500°C.
Pros & Cons:
While carbon steel is cost-effective and strong, it is susceptible to corrosion unless coated or treated. This can lead to increased maintenance costs over time.
Impact on Application:
Carbon steel is often used in structural applications within vending machines, but it should not be used in environments where it will be exposed to moisture or corrosive substances without proper protection.
Considerations for International Buyers:
Compliance with regional standards such as DIN 17100 in Europe or ASTM A36 in the U.S. is essential. Buyers should also consider the availability of protective coatings to enhance longevity.
4. Plastic (Polycarbonate or ABS)
Key Properties:
Plastics like polycarbonate and ABS are lightweight, impact-resistant, and can handle temperatures up to 100°C. They are also resistant to many chemicals.
Pros & Cons:
Plastics are generally low-cost and easy to mold, making them suitable for complex shapes. However, they may not be as durable as metals and can degrade under UV exposure or extreme temperatures.
Impact on Application:
Plastics are often used for components like display panels and internal trays. Their compatibility with various media should be evaluated, particularly in food applications.
Considerations for International Buyers:
Buyers should ensure that the selected plastic materials meet regional safety standards, such as REACH in Europe. Understanding the local market for plastics and their recyclability can also influence purchasing decisions.
Summary Table
Material | Typical Use Case for vending machine repair near me | Key Advantage | Key Disadvantage/Limitation | Relative Cost (Low/Med/High) |
---|---|---|---|---|
Stainless Steel | Frames, doors, internal mechanisms | Excellent corrosion resistance | High initial cost, complex welding | High |
Aluminum | Structural components, panels | Lightweight, cost-effective | Less durable, prone to deformation | Med |
Carbon Steel | Structural applications | High tensile strength | Susceptible to corrosion | Low |
Plastic (Polycarbonate/ABS) | Display panels, internal trays | Lightweight, impact-resistant | Less durable, potential UV degradation | Low |
This guide provides actionable insights for international B2B buyers, helping them make informed decisions regarding material selection for vending machine repairs. Understanding the properties and implications of each material will facilitate better procurement strategies and compliance with regional standards.
In-depth Look: Manufacturing Processes and Quality Assurance for vending machine repair near me
Understanding the Manufacturing Processes for Vending Machine Repair
When sourcing vending machine repair services, it’s essential to comprehend the manufacturing processes involved. This knowledge enables international B2B buyers to make informed decisions regarding suppliers, ensuring they partner with companies that adhere to high standards of quality and efficiency.
Main Stages of Manufacturing
- Material Preparation
The first step involves selecting the right materials, which typically include metals, plastics, and electronic components. Suppliers must ensure that these materials meet industry specifications and are sourced from reputable vendors. This stage also includes cutting, shaping, and treating materials to prepare them for the next phases.
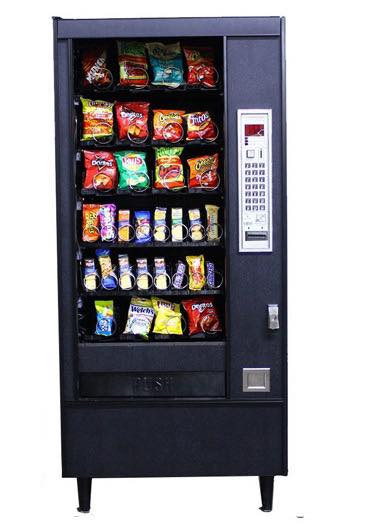
Illustrative Image (Source: Google Search)
-
Forming
Forming processes such as stamping, molding, or machining are employed to create the various parts of the vending machine. Advanced techniques like CNC machining and injection molding are common in this stage. These methods allow for high precision and repeatability, crucial for maintaining quality across multiple units. -
Assembly
The assembly process combines individual components into a complete vending machine unit. This stage may involve both manual labor and automated systems. Skilled technicians often oversee the assembly to ensure that each component fits correctly and functions as intended. Attention to detail is critical here, as improper assembly can lead to mechanical failures. -
Finishing
After assembly, finishing processes such as painting, coating, or surface treatment are applied to enhance durability and aesthetics. Quality control checks are also conducted at this stage to ensure that the final product meets the required specifications and standards.
Quality Assurance in Vending Machine Repair
Quality assurance is paramount in manufacturing, especially for B2B buyers who require reliable and long-lasting equipment. Understanding the relevant international standards and quality control measures can help buyers assess potential suppliers effectively.
Relevant International Standards
-
ISO 9001: This is a globally recognized standard that outlines the requirements for a quality management system. Suppliers with ISO 9001 certification demonstrate their commitment to consistent quality and customer satisfaction.
-
CE Marking: This certification indicates compliance with European health, safety, and environmental protection standards. For buyers in Europe, CE marking is essential when sourcing vending machines or parts.
-
API Standards: For vending machines that dispense specific products (like beverages or snacks), adherence to the American Petroleum Institute (API) standards may also be relevant, particularly regarding safety and performance.
Quality Control Checkpoints
To ensure that manufacturing processes meet the necessary quality standards, various checkpoints are implemented:
-
Incoming Quality Control (IQC): This initial checkpoint involves inspecting materials and components upon arrival. Suppliers should have a robust IQC process to verify that all incoming materials meet the required specifications.
-
In-Process Quality Control (IPQC): During the manufacturing process, regular inspections are performed to catch defects early. This proactive approach helps minimize waste and rework.
-
Final Quality Control (FQC): Once the vending machines are assembled, a comprehensive FQC process is conducted. This involves functional testing and visual inspections to ensure that the final product meets all specifications.
Common Testing Methods
Testing methods are essential for verifying the performance and safety of vending machines. Common methods include:
- Functional Testing: Ensures that all mechanical and electronic components operate correctly.
- Durability Testing: Assesses how well the vending machine withstands wear and tear over time.
- Safety Testing: Verifies that the vending machines meet safety regulations, particularly regarding electrical components.
Verifying Supplier Quality Control
For international B2B buyers, verifying the quality control processes of potential suppliers is critical. Here are some actionable insights:
-
Conduct Audits: Regular audits of suppliers can provide insight into their manufacturing processes and quality assurance practices. Buyers should ask suppliers about their audit schedules and findings.
-
Request Quality Reports: Suppliers should be willing to share their quality control reports, including IQC, IPQC, and FQC outcomes. This transparency is a good indicator of their commitment to quality.
-
Engage Third-Party Inspectors: For added assurance, consider hiring third-party inspection services. These independent auditors can provide objective assessments of the supplier’s quality control processes.
QC and Certification Nuances for International Buyers
When sourcing from different regions, B2B buyers should be aware of certification nuances:
-
Regional Compliance: Certifications may vary by region. For example, a supplier in Africa may have different compliance requirements than one in Europe. Understanding these differences is crucial for ensuring that products meet local regulations.
-
Cultural Considerations: Communication styles and business practices can differ significantly across regions. B2B buyers should be mindful of these cultural nuances when engaging with suppliers to ensure clear expectations regarding quality.
-
Supply Chain Transparency: In regions with less stringent regulatory environments, it is vital for buyers to demand greater transparency in the supply chain. This includes knowing the origin of materials and the processes involved in manufacturing.
Conclusion
Navigating the complexities of manufacturing processes and quality assurance is crucial for B2B buyers in the vending machine repair sector. By understanding the stages of manufacturing, relevant international standards, and effective quality control measures, buyers can make more informed decisions. Engaging suppliers who prioritize quality assurance not only enhances operational efficiency but also fosters long-term partnerships built on trust and reliability.
Related Video: SMART Quality Control for Manufacturing
Comprehensive Cost and Pricing Analysis for vending machine repair near me Sourcing
Understanding the Cost Structure of Vending Machine Repair
When sourcing vending machine repair services, it’s essential to comprehend the various cost components involved. The cost structure typically includes:
-
Materials: This encompasses spare parts, tools, and any additional supplies required for repairs. The cost can vary significantly based on the type of vending machine and the complexity of the repair needed.
-
Labor: Skilled technicians are required for effective repair services. Labor costs can fluctuate based on regional wage standards and the expertise level of the technicians.
-
Manufacturing Overhead: This includes expenses related to the maintenance of the service facility, utilities, and administrative costs. Understanding these indirect costs can help buyers gauge the pricing structure better.
-
Tooling: Specialized tools may be required for specific repairs. This adds to the overall cost, especially if the repair service needs to invest in new equipment.
-
Quality Control (QC): Ensuring that repairs meet quality standards may incur additional costs, particularly if certifications are needed.
-
Logistics: Transportation costs associated with moving parts or technicians to the repair site can be significant, especially for international sourcing.
-
Margin: Suppliers will add a profit margin to cover their business risks and ensure sustainability. This margin can vary based on the supplier’s market positioning.
Factors Influencing Pricing
Several factors can impact the pricing of vending machine repair services:
-
Volume/MOQ (Minimum Order Quantity): Larger orders may attract discounts, making it more cost-effective to source repairs in bulk, particularly for businesses with multiple machines.
-
Specifications/Customization: Custom repairs or modifications can increase costs. Clear communication about the specific needs can help in getting accurate quotes.
-
Materials: The quality and availability of materials can heavily influence costs. Opting for higher-quality parts may increase initial expenditures but can lead to lower long-term maintenance costs.
-
Quality Certifications: Services that come with certifications or warranties typically command higher prices due to the assurance of quality.
-
Supplier Factors: The reputation, reliability, and location of the supplier can significantly affect pricing. Established suppliers may charge a premium for their services.
-
Incoterms: Understanding the Incoterms associated with the transaction is vital, as they define the responsibilities of buyers and sellers in terms of shipping, risk, and insurance.
Buyer Tips for Cost-Efficiency
To achieve a favorable outcome in sourcing vending machine repair services, consider the following strategies:
-
Negotiate Effectively: Approach suppliers with a clear understanding of your needs and budget. Don’t hesitate to negotiate terms, especially for larger orders or long-term partnerships.
-
Evaluate Total Cost of Ownership (TCO): Look beyond the initial repair costs. Consider the longevity of repairs, potential downtime, and the cost of recurring issues. This holistic view can lead to better financial decisions.
-
Understand Pricing Nuances: International buyers must be cognizant of currency fluctuations, import duties, and local taxes that may affect the overall cost. Establishing relationships with local suppliers can mitigate some of these challenges.
-
Research Local Market Rates: Prices can vary significantly across regions. Conducting market research can help you benchmark costs and avoid overpaying.
-
Build Relationships: Establishing a long-term relationship with a reliable repair service can lead to better pricing, faster service, and prioritized support in emergencies.
Disclaimer on Pricing
It is important to note that the prices associated with vending machine repair services can vary widely based on numerous factors, including geographic location, service complexity, and supplier reputation. Buyers are encouraged to seek multiple quotes and conduct thorough due diligence to ensure they are receiving competitive pricing aligned with their specific needs.
Spotlight on Potential vending machine repair near me Manufacturers and Suppliers
This section offers a look at a few manufacturers active in the ‘vending machine repair near me’ market. This is a representative sample for illustrative purposes; B2B buyers must conduct their own extensive due diligence before any engagement. Information is synthesized from public sources and general industry knowledge.
Essential Technical Properties and Trade Terminology for vending machine repair near me
Key Technical Properties for Vending Machine Repair
When considering vending machine repair, understanding specific technical properties is crucial for making informed decisions. Here are some essential specifications that B2B buyers should be aware of:
-
Material Grade
The material grade refers to the quality and type of materials used in vending machines, such as stainless steel or ABS plastic. Higher grades, such as 304 stainless steel, offer better corrosion resistance, making them ideal for machines exposed to various environments. For B2B buyers, selecting the right material grade can significantly affect the durability and maintenance costs of the machines. -
Tolerance
Tolerance indicates the allowable deviation from a specified dimension or property in machine components. In vending machines, precise tolerances are vital for parts like coin mechanisms and dispensing systems. Understanding tolerances ensures compatibility with existing parts and minimizes operational issues, which is critical for maintaining service efficiency. -
Voltage and Power Requirements
Vending machines operate on specific voltage and power requirements, typically between 110V and 240V, depending on the region. Knowledge of these specifications is essential for ensuring that machines operate safely and efficiently within local electrical standards. For international buyers, compliance with regional power regulations can prevent costly downtime and repairs. -
Weight Capacity
Each vending machine has a defined weight capacity for the products it can hold, which directly impacts inventory management. Buyers must assess the machine’s weight limits to ensure they meet the demands of their target market. Overloading machines can lead to mechanical failures and increased repair costs, making it essential to understand these specifications. -
Environmental Ratings
Environmental ratings, such as IP (Ingress Protection) ratings, indicate the machine’s ability to withstand dust and moisture. For regions with harsh climates, such as Africa and the Middle East, selecting machines with higher IP ratings can prolong their lifespan and reduce maintenance needs. This is particularly important for B2B buyers looking to optimize operational efficiency.
Common Trade Terminology in Vending Machine Repair
Familiarity with industry jargon can enhance communication and negotiation with suppliers and service providers. Here are some commonly used terms in the vending machine repair sector:
-
OEM (Original Equipment Manufacturer)
OEM refers to the company that originally manufactured the vending machine or its parts. When sourcing replacement components, choosing OEM parts ensures compatibility and quality. B2B buyers should prioritize OEM parts for reliable repairs and longevity of their machines. -
MOQ (Minimum Order Quantity)
MOQ indicates the smallest number of units a supplier is willing to sell. Understanding MOQs is crucial for budgeting and inventory management. Buyers from Africa and South America, where supply chains may vary, should negotiate MOQs that align with their operational needs to avoid excess inventory costs. -
RFQ (Request for Quotation)
An RFQ is a formal document sent to suppliers to obtain pricing and terms for specific products or services. For B2B buyers, crafting a comprehensive RFQ that outlines detailed specifications can lead to more accurate quotes and better negotiation leverage. -
Incoterms (International Commercial Terms)
Incoterms define the responsibilities of buyers and sellers in international transactions. Understanding these terms is essential for managing shipping costs and risks. Buyers should familiarize themselves with terms like FOB (Free On Board) and CIF (Cost, Insurance, and Freight) to ensure clarity in their contracts and logistics. -
Lead Time
Lead time refers to the time taken from placing an order to receiving the goods. For vending machine repairs, understanding lead times for parts can help businesses minimize downtime. Buyers should account for lead times when planning maintenance schedules to maintain service continuity.
By grasping these technical properties and trade terms, international B2B buyers can enhance their decision-making processes and ensure effective vending machine operations.
Navigating Market Dynamics, Sourcing Trends, and Sustainability in the vending machine repair near me Sector
Market Overview & Key Trends
The vending machine repair sector is experiencing significant transformation driven by technological advancements and shifting consumer expectations. As global markets recover from disruptions caused by the pandemic, B2B buyers are increasingly looking for reliable repair services that ensure minimal downtime and maximize machine performance. Key drivers include the rise in cashless transactions, which necessitates specialized repair skills for electronic components, and the growing demand for healthy vending options, prompting the need for machines that accommodate diverse product offerings.
Emerging trends in this sector include the integration of IoT technology, which allows for remote monitoring of machine health and performance. This trend not only enhances operational efficiency but also provides valuable data analytics that can inform maintenance schedules and reduce costs. B2B buyers, particularly from regions like Africa and South America, are urged to consider partnerships with service providers that offer advanced diagnostic tools and predictive maintenance capabilities.
Moreover, sustainability is becoming a central theme in sourcing strategies. European buyers, for instance, are increasingly prioritizing vendors that demonstrate eco-friendly practices, such as using energy-efficient machines and sustainable repair materials. Understanding local market dynamics, such as regulatory requirements and consumer preferences, is essential for international buyers looking to optimize their vending machine operations.
Sustainability & Ethical Sourcing in B2B
The environmental impact of the vending machine repair industry is significant, primarily due to electronic waste and the use of non-recyclable materials. As global awareness of sustainability grows, B2B buyers are encouraged to adopt ethical sourcing practices that prioritize environmental responsibility. This includes partnering with suppliers who utilize sustainable materials and environmentally friendly repair techniques.
Certifications such as ISO 14001 (Environmental Management) and the Energy Star label can serve as benchmarks for evaluating potential service partners. These certifications not only signify compliance with environmental standards but also demonstrate a commitment to reducing carbon footprints. Buyers should actively seek vendors who emphasize the use of recycled components and sustainable practices in their repair processes.
Furthermore, embracing a circular economy model—where products are designed for longevity and recyclability—can enhance brand reputation and customer loyalty. For B2B buyers in regions like the Middle East and Europe, aligning with partners who share a commitment to sustainability can also open doors to new market opportunities, as more consumers demand ethical and green practices from the brands they support.
Brief Evolution/History
The vending machine repair sector has evolved significantly over the last few decades, transitioning from basic mechanical repairs to a sophisticated service industry that leverages advanced technology. Initially, repairs focused on mechanical issues and coin mechanisms, but the advent of digital technology has transformed the landscape.
Today, repair services encompass a wide range of capabilities, including software troubleshooting, electronic component replacement, and IoT integration. This evolution reflects broader trends in consumer behavior and technological innovation, making it crucial for B2B buyers to stay informed about advancements in repair technologies and services. Understanding this history helps buyers appreciate the complexity of modern vending machine operations and the importance of choosing the right service partners for sustained success.
Related Video: What global trade deals are really about (hint: it’s not trade) | Haley Edwards | TEDxMidAtlantic
Frequently Asked Questions (FAQs) for B2B Buyers of vending machine repair near me
-
What criteria should I use to vet suppliers for vending machine repair services?
When vetting suppliers, prioritize their experience in the vending machine industry, customer reviews, and service history. Request references from previous clients, especially those in your region, to gauge reliability. Additionally, evaluate their technical expertise and whether they offer specialized services for the types of machines you operate. Certifications in relevant standards (ISO, etc.) can also indicate a commitment to quality. -
Can I customize the repair services according to my specific vending machines?
Yes, many suppliers offer customization options to cater to different brands and models of vending machines. When discussing your needs, provide detailed specifications about the machines, including make, model, and any known issues. This will help suppliers tailor their services effectively. Ensure that they have experience with your specific machines to avoid compatibility issues. -
What are the common minimum order quantities (MOQ) and lead times for repair services?
MOQs can vary significantly among suppliers, often influenced by the scale of repairs required. Some may have no minimum, while others might require a minimum number of machines or repairs to justify travel or service costs. Lead times typically range from a few days to several weeks, depending on the complexity of the repairs and the supplier’s workload. Always clarify these details upfront to align with your operational timelines. -
What payment terms should I expect when engaging with international suppliers?
Payment terms can differ widely based on the supplier’s location and your negotiation. Common practices include upfront payments, deposits, or payment upon completion of services. It’s advisable to establish clear terms, including currency, payment methods (bank transfer, credit card, etc.), and deadlines. Additionally, consider escrow services for larger projects to mitigate risks associated with international transactions.
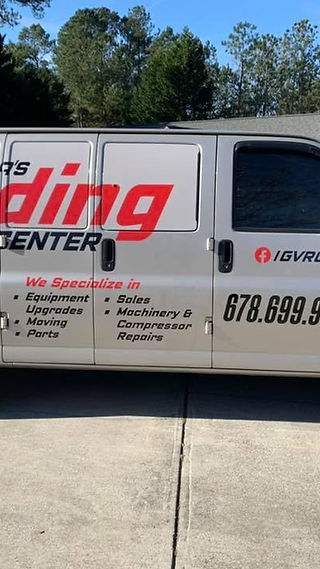
Illustrative Image (Source: Google Search)
-
How can I ensure quality assurance (QA) and certifications from repair suppliers?
Request documentation of quality assurance processes and certifications relevant to vending machine repairs. Look for suppliers who follow industry standards, such as ISO 9001, which indicates a commitment to quality management. Additionally, inquire about their repair processes, warranty policies, and any guarantees they offer on parts and labor. A robust QA process can significantly reduce the risk of future breakdowns. -
What logistical considerations should I keep in mind when sourcing repair services internationally?
Logistics play a critical role in the timely delivery of repair services. Consider the supplier’s location, shipping options, and potential customs delays. It’s essential to discuss transportation responsibilities and costs upfront. Additionally, check if the supplier has local technicians available in your area to minimize travel time and costs, which can enhance service efficiency. -
How can disputes be effectively managed with repair service providers?
To minimize disputes, establish clear contracts detailing the scope of work, timelines, and payment terms. Include clauses that address potential issues such as delays or unsatisfactory repairs. Open communication is vital; maintain regular contact with the supplier throughout the repair process. In case of a dispute, refer to the contract and attempt to resolve issues amicably before considering legal avenues. -
What after-service support should I expect from my vending machine repair provider?
After-service support can vary by supplier but is crucial for ongoing machine performance. Look for providers who offer maintenance packages, follow-up inspections, or troubleshooting assistance post-repair. Ensure you understand their availability for emergency repairs and the terms of any warranties on services rendered. A reliable support system can help sustain machine functionality and prevent future breakdowns.
Strategic Sourcing Conclusion and Outlook for vending machine repair near me
In conclusion, strategic sourcing for vending machine repair services is a critical component for businesses aiming to optimize operations and enhance customer satisfaction. By identifying reliable local partners, international B2B buyers can ensure timely service, reduce downtime, and maintain the functionality of their vending machines. Key takeaways include the importance of assessing vendor qualifications, understanding regional service capabilities, and leveraging technology for efficient communication and service tracking.
For businesses in Africa, South America, the Middle East, and Europe, establishing strong relationships with local repair providers can lead to significant cost savings and improved service quality. Engaging with suppliers who understand the local market dynamics and can offer tailored solutions is essential for maximizing the investment in vending machine infrastructure.
As we look toward the future, the demand for vending machine services is expected to grow, driven by changing consumer behaviors and technological advancements. Now is the time for international B2B buyers to evaluate their sourcing strategies. By prioritizing strategic partnerships and staying informed about industry trends, companies can position themselves for success in this evolving market. Take the next step today by exploring local repair options and fostering connections that will benefit your business in the long run.