Master Vending Machine Cage Procurement for Enhanced
Guide to Vending Machine Cage
- Introduction: Navigating the Global Market for vending machine cage
- Understanding vending machine cage Types and Variations
- Key Industrial Applications of vending machine cage
- Strategic Material Selection Guide for vending machine cage
- In-depth Look: Manufacturing Processes and Quality Assurance for vending machine cage
- Comprehensive Cost and Pricing Analysis for vending machine cage Sourcing
- Spotlight on Potential vending machine cage Manufacturers and Suppliers
- Essential Technical Properties and Trade Terminology for vending machine cage
- Navigating Market Dynamics, Sourcing Trends, and Sustainability in the vending machine cage Sector
- Frequently Asked Questions (FAQs) for B2B Buyers of vending machine cage
- Strategic Sourcing Conclusion and Outlook for vending machine cage
Introduction: Navigating the Global Market for vending machine cage
In today’s fast-paced global market, the demand for effective and efficient vending solutions is on the rise. A pivotal component of these solutions is the vending machine cage, which provides essential security and accessibility for products. As B2B buyers from diverse regions—including Africa, South America, the Middle East, and Europe—seek to enhance their vending operations, understanding the nuances of vending machine cages becomes crucial for informed purchasing decisions.
This comprehensive guide will delve into the various types of vending machine cages, examining the materials used, manufacturing processes, and quality control standards that ensure durability and reliability. It will also highlight key suppliers, offering insights into cost considerations and market trends that can impact procurement strategies. Additionally, frequently asked questions will be addressed to clarify common concerns and misconceptions.
By equipping international B2B buyers with this essential knowledge, this guide empowers stakeholders to make strategic sourcing decisions that align with their operational goals. Whether you are in Mexico, Saudi Arabia, or elsewhere, understanding the intricacies of vending machine cages will not only enhance your product offerings but also position your business for success in a competitive landscape. Embrace this opportunity to navigate the global market with confidence and insight.
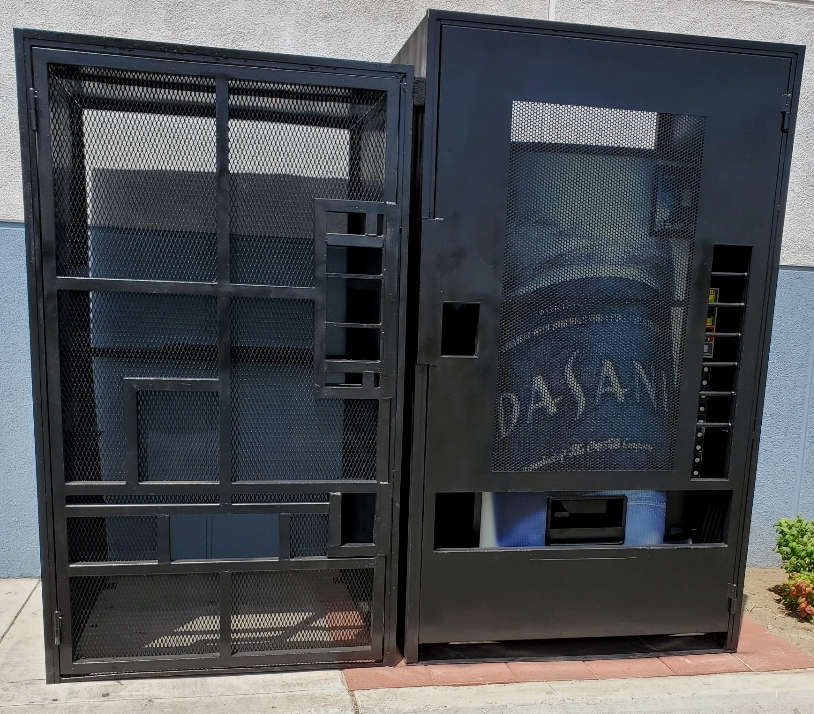
Illustrative Image (Source: Google Search)
Understanding vending machine cage Types and Variations
Type Name | Key Distinguishing Features | Primary B2B Applications | Brief Pros & Cons for Buyers |
---|---|---|---|
Open Frame Cages | Minimalist design allowing easy access to products | Retail environments, offices | Pros: Cost-effective, easy to maintain. Cons: Less secure, limited product protection. |
Enclosed Cages | Fully enclosed with lockable doors | High-security locations, warehouses | Pros: Enhanced security, protects against theft. Cons: Higher initial cost, may require additional space. |
Customizable Cages | Modular design for tailored configurations | Specialized retail, events | Pros: Flexibility in design, can accommodate various products. Cons: Potentially higher costs, longer lead times. |
Smart Cages | Integrated technology for inventory tracking | Tech-savvy businesses, logistics | Pros: Real-time inventory management, reduces human error. Cons: Higher upfront investment, requires tech support. |
Mobile Cages | Wheels for easy transport and repositioning | Trade shows, temporary events | Pros: Versatile and convenient, easy to relocate. Cons: Stability issues if not locked in place, limited capacity. |
Open Frame Cages
Open frame cages are characterized by their minimalist design, which allows for easy access to the products inside. They are commonly used in retail environments and offices where the emphasis is on visibility and accessibility. B2B buyers should consider the cost-effectiveness and ease of maintenance of these cages, but they must also be aware of the trade-off in terms of security, as they provide limited protection against theft or damage.
Enclosed Cages
Enclosed cages offer a higher level of security with fully lockable doors, making them suitable for high-security locations such as warehouses or areas where valuable items are stored. These cages protect against theft and unauthorized access. While they come with enhanced security features, buyers should weigh the higher initial costs and the requirement for additional space against the benefits of safeguarding their inventory.
Customizable Cages
Customizable cages feature a modular design that allows businesses to tailor their configuration based on specific needs. They are particularly useful in specialized retail settings or during events where unique product displays are necessary. While the flexibility in design can accommodate various products effectively, buyers should be prepared for potentially higher costs and longer lead times associated with custom orders.
Smart Cages
Smart cages incorporate integrated technology for real-time inventory tracking and management. They are ideal for tech-savvy businesses and logistics operations where accurate inventory management is crucial. The benefits include reduced human error and enhanced operational efficiency; however, the initial investment can be higher, and ongoing tech support may be required, which could be a consideration for some buyers.
Mobile Cages
Mobile cages are designed with wheels, allowing for easy transport and repositioning, making them perfect for trade shows and temporary events. Their versatility and convenience are significant advantages, but buyers should be mindful of potential stability issues if the cages are not locked in place and the limitations on capacity due to their mobile nature.
Related Video: FINTECH BUSINESS MODELS EXPLAINED
Key Industrial Applications of vending machine cage
Industry/Sector | Specific Application of vending machine cage | Value/Benefit for the Business | Key Sourcing Considerations for this Application |
---|---|---|---|
Retail | Automated product dispensing and inventory control | Increased efficiency, reduced labor costs | Durability, size compatibility, ease of integration |
Education | Snack and beverage vending in schools | Promotes healthy eating, provides convenience | Compliance with health regulations, payment options |
Healthcare | Medication dispensing in hospitals | Enhances patient compliance, reduces medication errors | Security features, temperature control, user interface |
Corporate Offices | Employee refreshment stations | Boosts employee morale and productivity | Customization options, maintenance support, payment systems |
Transportation Hubs | Food and beverage services at airports and stations | Quick service, caters to high foot traffic | Space constraints, product variety, payment integration |
Retail
In the retail sector, vending machine cages are utilized for automated product dispensing and inventory control. These systems streamline the purchasing process, allowing customers to quickly access products without the need for staff intervention. The primary challenges include ensuring the machines are durable and capable of handling various product sizes. International buyers should prioritize sourcing machines that are easy to integrate with existing retail systems and that offer robust inventory management features.
Education
Vending machine cages in educational institutions serve the dual purpose of providing snacks and beverages while promoting healthier eating habits among students. These machines can be stocked with nutritious options, addressing the growing concern over student health. Buyers in this sector must consider compliance with local health regulations and the ability to accept multiple payment methods, including cashless options, to enhance convenience for students.
Healthcare
In healthcare settings, vending machine cages are increasingly used for medication dispensing, allowing hospitals to enhance patient compliance and minimize medication errors. These machines are designed with advanced security features to ensure that medications are stored and dispensed safely. Buyers must focus on sourcing machines that offer temperature control for sensitive medications and a user-friendly interface for both staff and patients.
Corporate Offices
Corporate offices leverage vending machine cages to create employee refreshment stations, which can significantly boost morale and productivity. By providing easy access to snacks and beverages, companies can foster a more engaging workplace environment. Key considerations for procurement include customization options to align with corporate branding, ongoing maintenance support, and systems for cashless payments to accommodate diverse employee preferences.
Transportation Hubs
Vending machine cages are vital in transportation hubs like airports and train stations, where they provide quick food and beverage services to travelers. The high foot traffic in these locations necessitates machines that can handle a wide variety of products while ensuring quick service. Buyers should assess machines for their ability to fit within space constraints and to offer a range of payment options, including mobile payments, to cater to the modern traveler.
Related Video: How to Start a Vending Machine Business, Cost, Tips, How Much You Make
Strategic Material Selection Guide for vending machine cage
When selecting materials for vending machine cages, international B2B buyers must consider various factors that influence product performance, durability, and compliance with local standards. Below is an analysis of four common materials used in the construction of vending machine cages, focusing on their properties, advantages, disadvantages, and specific considerations for buyers from regions such as Africa, South America, the Middle East, and Europe.
1. Carbon Steel
Key Properties:
Carbon steel is known for its excellent strength-to-weight ratio, making it suitable for heavy-duty applications. It typically has a temperature rating of up to 400°F (204°C) and can withstand moderate pressure. However, it is prone to corrosion without proper treatment.
Pros & Cons:
Carbon steel is cost-effective and widely available, which makes it a popular choice for vending machine cages. Its high strength ensures durability, but it requires protective coatings (like galvanization) to prevent rusting, which can increase manufacturing complexity and costs.
Impact on Application:
This material is suitable for environments where exposure to moisture is limited. However, in humid or corrosive environments, carbon steel may not be the best option unless adequately protected.
Considerations for International Buyers:
Buyers should ensure compliance with local standards such as ASTM A36 for structural steel. In regions like Saudi Arabia, where humidity is high, additional protective measures are crucial.
2. Stainless Steel
Key Properties:
Stainless steel offers excellent corrosion resistance, making it ideal for vending machines exposed to various environmental conditions. It can handle temperatures up to 1,500°F (815°C) and has good pressure ratings.
Pros & Cons:
While stainless steel is more expensive than carbon steel, its durability and low maintenance requirements often justify the cost. The manufacturing complexity is higher due to the need for specialized welding techniques.
Impact on Application:
This material is suitable for vending machines that dispense food or beverages, as it meets hygiene standards and is easy to clean. It is also resistant to staining and rust, ensuring a longer lifespan.
Considerations for International Buyers:
Compliance with standards such as ASTM A240 is essential. In Europe, EN 10088-1 outlines the specifications for stainless steel, which buyers should consider when sourcing materials.
3. Aluminum
Key Properties:
Aluminum is lightweight yet strong, with a temperature rating of approximately 600°F (316°C). It also has a good corrosion resistance, particularly when anodized.
Pros & Cons:
The primary advantage of aluminum is its low weight, which can reduce shipping costs. However, it is softer than steel, making it less durable under heavy impacts. Its cost is generally medium, depending on the alloy used.
Impact on Application:
Aluminum is suitable for vending machines located in environments with moderate exposure to the elements. It is commonly used in outdoor applications due to its corrosion resistance.
Considerations for International Buyers:
Buyers should be aware of the specific aluminum grades (e.g., 6061, 5052) that comply with local standards. In regions like South America, where environmental conditions can vary, selecting the right alloy is crucial.
4. Polycarbonate
Key Properties:
Polycarbonate is a thermoplastic known for its high impact resistance and transparency. It can withstand temperatures up to 270°F (132°C) and is lightweight.
Pros & Cons:
The key advantage of polycarbonate is its resistance to shattering, making it an excellent choice for safety applications. However, it is not as durable as metals in terms of structural integrity and can be more expensive.
Impact on Application:
This material is often used for transparent panels in vending machines, allowing visibility of products while providing security. It is suitable for indoor applications where impact resistance is a priority.
Considerations for International Buyers:
Compliance with safety standards is critical, especially in regions with stringent regulations. Buyers should verify that the polycarbonate meets relevant standards, such as ASTM D635 for flammability.
Summary Table
Material | Typical Use Case for vending machine cage | Key Advantage | Key Disadvantage/Limitation | Relative Cost (Low/Med/High) |
---|---|---|---|---|
Carbon Steel | General service, non-corrosive fluids | Cost-effective, good strength | Susceptible to corrosion if not protected | Low |
Stainless Steel | Food and beverage vending machines | Excellent corrosion resistance | Higher cost, complex manufacturing | High |
Aluminum | Outdoor vending machines | Lightweight, good corrosion resistance | Less durable under heavy impacts | Medium |
Polycarbonate | Transparent panels for vending machines | High impact resistance, lightweight | Less structural integrity, higher cost | Medium |
This guide provides a comprehensive overview of material options for vending machine cages, enabling international B2B buyers to make informed decisions based on performance, cost, and compliance with local standards.
In-depth Look: Manufacturing Processes and Quality Assurance for vending machine cage
Manufacturing Processes for Vending Machine Cages
The manufacturing of vending machine cages involves several critical stages that ensure durability, functionality, and compliance with industry standards. Understanding these processes is essential for international B2B buyers, especially those in Africa, South America, the Middle East, and Europe. Here’s a detailed breakdown of the typical manufacturing stages, key techniques used, and what to look for in quality assurance.
Main Stages of Manufacturing
-
Material Preparation
– Selection of Materials: The primary materials used in vending machine cages are typically steel or aluminum due to their strength and corrosion resistance. For enhanced aesthetics, stainless steel or powder-coated finishes may be considered.
– Cutting and Shaping: Sheets of metal are cut into specific dimensions using laser cutting or CNC machines. This precision is crucial as it minimizes waste and ensures that parts fit correctly during assembly. -
Forming
– Bending and Shaping: After cutting, metal sheets undergo bending processes to form various components of the cage, such as walls and shelves. Techniques like roll forming or press braking are commonly used.
– Welding: Components are joined together through welding, which provides structural integrity. TIG (Tungsten Inert Gas) or MIG (Metal Inert Gas) welding is often preferred for its strength and quality. -
Assembly
– Component Integration: The assembled parts are fitted together, including locks, hinges, and electronic components for payment systems. Proper alignment and fitting are critical to ensure operational efficiency.
– Final Adjustments: Before finishing, adjustments are made to ensure that all components function correctly and are securely attached. -
Finishing
– Surface Treatment: This stage includes processes like powder coating, painting, or galvanizing to protect against corrosion and enhance aesthetics. The choice of finish can affect the durability of the cage in different environments.
– Quality Check: After finishing, the cages undergo a final inspection to ensure that all surfaces are free from defects and meet the specified standards.
Quality Assurance in Manufacturing
Quality assurance is a vital aspect of the manufacturing process, ensuring that products meet customer expectations and regulatory requirements. For vending machine cages, the following international and industry-specific standards are relevant:
Relevant International Standards
- ISO 9001: This standard focuses on quality management systems (QMS) and is crucial for manufacturers aiming to ensure consistent quality in their products and services.
- CE Marking: For products sold within the European Economic Area, CE marking indicates compliance with health, safety, and environmental protection standards.
- API Standards: While primarily associated with the oil and gas industry, some API standards may apply if the vending machines are designed for specialized environments.
Quality Control Checkpoints
-
Incoming Quality Control (IQC)
– Inspection of raw materials upon arrival to ensure they meet specified quality standards.
– Verification of certificates of compliance from suppliers. -
In-Process Quality Control (IPQC)
– Continuous monitoring during manufacturing processes, including dimensional checks and visual inspections at various stages of assembly.
– Use of gauges and measuring tools to ensure parts are within tolerances. -
Final Quality Control (FQC)
– Comprehensive testing of the finished product, including functional tests and visual inspections to identify any defects before shipment.
– Documentation of test results and compliance with standards.
Common Testing Methods
- Mechanical Testing: This may include tensile strength tests, impact tests, and fatigue tests to ensure that the cage can withstand operational stresses.
- Environmental Testing: Assessing the product’s resistance to corrosion, humidity, and temperature variations, especially important for regions with extreme climates.
Verifying Supplier Quality Control
B2B buyers must take proactive steps to verify the quality control practices of suppliers. Here are actionable insights:
-
Conduct Audits: Regularly schedule audits of suppliers to evaluate their manufacturing processes and quality assurance systems. This can be done through on-site visits or third-party audit services.
-
Request Documentation: Ask suppliers for detailed quality management documentation, including quality control plans, inspection reports, and certifications (ISO, CE, etc.).
-
Third-Party Inspections: Engage third-party inspection agencies to conduct independent assessments of the manufacturing process and product quality. This adds an additional layer of verification.
-
Supplier Ratings and References: Review supplier ratings and seek references from other B2B buyers in your industry. This can provide insights into their reliability and quality of products.
Quality Control Nuances for International Buyers
International B2B buyers should be particularly aware of:
-
Cultural Differences in Quality Standards: Different regions may have varying expectations for quality and compliance. Understanding local regulations and industry norms is crucial.
-
Shipping and Handling Concerns: Ensure that quality checks extend to the shipping process to prevent damage during transit. Packaging should be robust enough to withstand international shipping conditions.
-
Post-Delivery Inspections: Consider implementing a post-delivery inspection process to confirm that the received products meet agreed-upon specifications and quality standards.
By focusing on these manufacturing processes and quality assurance measures, B2B buyers can make informed decisions when sourcing vending machine cages, ensuring they receive high-quality products that meet their operational needs.
Related Video: SMART Quality Control for Manufacturing
Comprehensive Cost and Pricing Analysis for vending machine cage Sourcing
In the sourcing of vending machine cages, understanding the comprehensive cost structure and pricing dynamics is crucial for international B2B buyers. Below, we break down the key cost components and influential pricing factors, along with actionable tips for effective purchasing.
Cost Components
-
Materials: The primary materials used in vending machine cage production include steel, aluminum, and various plastics. The choice of material impacts durability and weight, influencing the overall cost. Higher-grade materials often come with a price premium but can enhance longevity and resistance to wear and tear.
-
Labor: Labor costs vary significantly based on geographic location and manufacturing processes. Countries with lower labor costs, such as those in Southeast Asia, may offer more competitive pricing, but this can also affect quality. Consider the skill level required for assembly and finishing when evaluating labor expenses.
-
Manufacturing Overhead: This encompasses costs related to utilities, facility maintenance, and indirect labor. A higher overhead can indicate a more established supplier with better quality assurance processes, but it also adds to the final cost.
-
Tooling: Custom tooling for specific designs can represent a significant upfront investment. Buyers should inquire about the tooling costs and consider shared tooling for larger orders to mitigate expenses.
-
Quality Control (QC): Effective QC processes are essential for ensuring that the cages meet safety and regulatory standards. Suppliers with robust QC systems may charge more, but this can reduce costs related to returns and warranty claims in the long run.
-
Logistics: Freight costs can vary dramatically based on shipping methods, distances, and incoterms. For international buyers, understanding the total logistics costs, including customs duties and local taxes, is essential to budget accurately.
-
Margin: Suppliers will include a profit margin in their pricing, which varies based on market conditions and competition. Buyers should be aware of the typical margins in their region to identify potential negotiation opportunities.
Price Influencers
-
Volume/MOQ (Minimum Order Quantity): Larger orders generally reduce the per-unit cost. Buyers should assess their requirements and consider bulk purchasing to benefit from economies of scale.
-
Specifications/Customization: Custom designs or features will typically increase costs. Clearly defining requirements upfront can prevent unexpected expenses later.
-
Materials and Quality/Certifications: Opting for higher quality materials or specific certifications (e.g., ISO standards) may raise costs but can enhance product reliability and marketability.
-
Supplier Factors: The reputation and reliability of suppliers can influence pricing. Established suppliers may charge more but offer better service, reliability, and support.
-
Incoterms: Understanding the implications of various Incoterms (e.g., FOB, CIF) is vital for calculating total costs, including transportation and insurance.
Buyer Tips
-
Negotiation: Approach negotiations with a clear understanding of your budget and desired specifications. Leverage competitive quotes from multiple suppliers to strengthen your position.
-
Cost-Efficiency: Always evaluate the total cost of ownership, not just the purchase price. Consider maintenance, durability, and potential returns when assessing value.
-
Pricing Nuances: International buyers, especially from regions like Africa and South America, should be mindful of currency fluctuations and geopolitical factors that may affect pricing. Always clarify payment terms and currency options.
-
Engage Local Expertise: Utilizing local sourcing agents or consultants can provide valuable insights into market dynamics and help navigate potential pitfalls.
Disclaimer
Prices can vary widely based on the factors mentioned above, and the information provided is indicative. Buyers should conduct thorough market research and supplier evaluations to obtain accurate pricing tailored to their specific needs.
Spotlight on Potential vending machine cage Manufacturers and Suppliers
This section offers a look at a few manufacturers active in the ‘vending machine cage’ market. This is a representative sample for illustrative purposes; B2B buyers must conduct their own extensive due diligence before any engagement. Information is synthesized from public sources and general industry knowledge.
Essential Technical Properties and Trade Terminology for vending machine cage
When considering the procurement of vending machine cages, it is essential to understand both the technical specifications that define product quality and the trade terminology that governs transactions. This knowledge aids international B2B buyers from regions such as Africa, South America, the Middle East, and Europe in making informed purchasing decisions.
Key Technical Properties
-
Material Grade
– Definition: Refers to the type and quality of material used in manufacturing vending machine cages, commonly steel, aluminum, or high-grade plastic.
– Importance: Higher-grade materials offer increased durability and resistance to corrosion, which is crucial for outdoor or high-traffic environments. Buyers should assess the material based on the intended use and environmental conditions. -
Tolerance Levels
– Definition: Tolerance refers to the allowable deviation from specified dimensions in the manufacturing process.
– Importance: Precise tolerances ensure that parts fit together correctly and function as intended. For vending machines, this affects everything from assembly to the security of the contents. Tighter tolerances may also indicate better manufacturing quality. -
Weight Capacity
– Definition: The maximum weight that the vending machine cage can safely hold.
– Importance: Knowing the weight capacity is vital for ensuring that the cage can support the intended products without risk of failure. This is particularly important for machines that dispense heavier items like bottles or snacks. -
Finish and Coating
– Definition: The surface treatment applied to the cage, such as powder coating or galvanization.
– Importance: A good finish protects against wear and environmental factors, enhancing the longevity of the cage. For international buyers, understanding the finish can also impact shipping and installation requirements. -
Dimensions and Configuration
– Definition: The overall size and design of the vending machine cage, including height, width, and depth.
– Importance: Dimensions must match the intended vending machine model and installation space. Buyers should ensure compatibility with existing machines and consider the layout for optimal customer access.
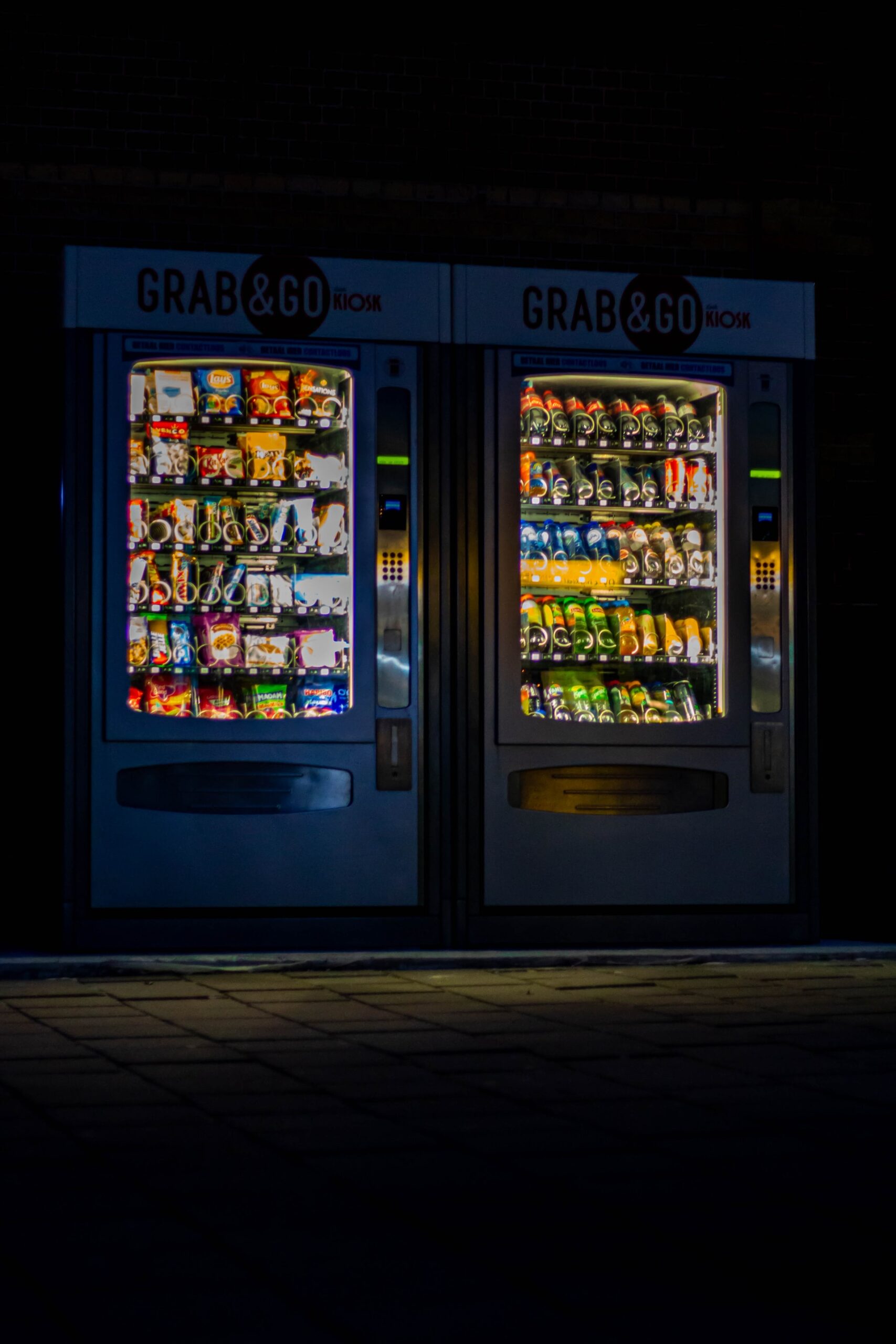
Illustrative Image (Source: Google Search)
Common Trade Terminology
-
OEM (Original Equipment Manufacturer)
– Definition: A company that produces parts or equipment that may be marketed by another manufacturer.
– Context: When sourcing vending machine cages, buyers may consider OEM products for reliability and support, as these often meet industry standards. -
MOQ (Minimum Order Quantity)
– Definition: The smallest quantity of a product that a supplier is willing to sell.
– Context: Understanding MOQ is crucial for budget planning and inventory management. Buyers should negotiate MOQs to avoid excess stock while ensuring sufficient supply. -
RFQ (Request for Quotation)
– Definition: A document sent to suppliers requesting pricing and terms for specific products.
– Context: Sending an RFQ allows buyers to compare offers from multiple suppliers, ensuring they secure the best price and terms for vending machine cages. -
Incoterms (International Commercial Terms)
– Definition: A series of predefined commercial terms published by the International Chamber of Commerce (ICC) that define the responsibilities of buyers and sellers in international transactions.
– Context: Familiarity with Incoterms is vital for understanding shipping responsibilities, insurance, and risk management. For instance, terms like FOB (Free On Board) and CIF (Cost, Insurance, and Freight) determine who bears costs and risks at various stages of transport. -
Lead Time
– Definition: The amount of time it takes from placing an order to receiving the goods.
– Context: Knowing the lead time helps buyers plan their inventory and avoid stockouts. Longer lead times may necessitate advance ordering to meet demand.
Understanding these technical specifications and trade terminologies not only equips B2B buyers with the knowledge to make informed decisions but also enhances their negotiation power and operational efficiency in acquiring vending machine cages.
Navigating Market Dynamics, Sourcing Trends, and Sustainability in the vending machine cage Sector
Market Overview & Key Trends
The global vending machine cage market is witnessing significant transformation driven by several key factors. Increasing urbanization and fast-paced lifestyles in regions such as Africa, South America, the Middle East, and Europe are propelling the demand for convenient and efficient vending solutions. B2B buyers are particularly interested in integrating advanced technology into vending machines, including cashless payment systems, IoT capabilities for real-time inventory management, and user-friendly interfaces. These innovations enhance customer experience and operational efficiency.
Emerging sourcing trends highlight a shift towards automation and digitalization. Suppliers are increasingly adopting AI and machine learning to optimize supply chains and predict consumer preferences. Moreover, the trend of personalization is gaining traction, with vending machines being equipped to offer tailored product recommendations based on purchase history. As a result, international B2B buyers must stay attuned to these technological advancements to remain competitive.
Market dynamics also reflect a growing emphasis on localized sourcing. Buyers are encouraged to engage with regional manufacturers to ensure supply chain resilience and reduce lead times. In regions like Mexico and Saudi Arabia, partnerships with local suppliers can facilitate better market penetration and compliance with regional regulations, thus enhancing operational agility.
Sustainability & Ethical Sourcing in B2B
Sustainability has become a cornerstone of strategic sourcing in the vending machine cage sector. The environmental impact of manufacturing and disposing of vending machines is substantial, prompting buyers to prioritize eco-friendly practices. It is essential for B2B buyers to consider suppliers who utilize sustainable materials and processes, as this not only reduces carbon footprints but also aligns with growing consumer expectations for corporate responsibility.
Ethical supply chains are increasingly important in the decision-making processes of international buyers. Certifications such as ISO 14001 for environmental management and FSC (Forest Stewardship Council) for sustainable materials are crucial indicators of a supplier’s commitment to sustainability. By sourcing from certified manufacturers, businesses can ensure that their vending machines are produced responsibly, mitigating risks associated with labor exploitation and environmental degradation.
Furthermore, the integration of recyclable and biodegradable materials in vending machine cages is gaining popularity. This not only addresses environmental concerns but also enhances brand reputation among increasingly eco-conscious consumers. For buyers in regions like Europe, where stringent regulations around waste management are in place, adopting sustainable sourcing practices is not just beneficial but necessary for compliance and market acceptance.
Brief Evolution/History
The vending machine cage sector has evolved significantly over the past few decades. Initially designed for basic product distribution, vending machines have transformed into sophisticated retail platforms capable of offering a wide array of products, from snacks to electronics. The introduction of technology in the 2000s, including cashless payment systems and inventory tracking, marked a pivotal shift in the industry.
As consumer preferences evolved, vending machines began to incorporate healthier options and more diverse products, catering to changing dietary trends. Today, the focus is on integrating advanced technology and sustainability practices, reflecting a broader shift towards innovation and responsibility in the marketplace. This evolution presents opportunities for international B2B buyers to engage with forward-thinking suppliers who prioritize technology and sustainability in their offerings.
Related Video: Global Trade & Logistics – What is Global Trade?
Frequently Asked Questions (FAQs) for B2B Buyers of vending machine cage
-
How can I effectively vet suppliers for vending machine cages?
When vetting suppliers, prioritize those with a proven track record in international trade. Check their certifications, such as ISO 9001, to ensure quality standards. Request references from previous clients, especially from your region, to assess reliability. Additionally, use platforms like Alibaba or ThomasNet to find reviews and ratings. Conduct video calls to gauge their professionalism and willingness to engage in transparent communication. -
Are customization options available for vending machine cages?
Yes, many suppliers offer customization options tailored to your specific needs. You can request changes in size, material, color, and branding elements to align with your business identity. Ensure you communicate your requirements clearly and ask for prototypes or samples before finalizing orders. It’s also wise to confirm if the supplier has experience in delivering customized solutions to avoid misalignment in expectations.
-
What are the typical minimum order quantities (MOQ) and lead times?
MOQs can vary significantly between suppliers, typically ranging from 50 to 500 units for vending machine cages. Lead times often depend on the complexity of the order and can range from 4 to 12 weeks. Always discuss your timeline upfront and consider suppliers who can meet your deadlines, especially if you’re launching a new product or entering a competitive market. -
What payment methods are commonly accepted, and are there any risks?
Common payment methods include bank transfers, letters of credit, and payment platforms like PayPal. Each method has its benefits and risks; for instance, bank transfers are secure but less flexible for disputes. Always negotiate terms that protect your investment, such as partial payments upfront and the remainder upon delivery. Consider using escrow services to hold funds until you confirm receipt of quality products. -
What quality assurance measures should I expect from suppliers?
Reputable suppliers will implement comprehensive quality assurance (QA) processes, including inspections at various production stages. Ask for documentation of their QA protocols and certifications. You might also want to arrange for third-party inspections before shipment to ensure the products meet your standards and specifications. This proactive approach can mitigate risks associated with subpar quality. -
Are there specific certifications I should look for?
Yes, certifications can indicate a supplier’s commitment to quality and safety. Look for ISO certifications, CE marking for compliance with European standards, and local certifications relevant to your region. These certifications ensure that the vending machine cages meet industry standards, which is crucial for compliance and customer safety. -
What logistics considerations should I keep in mind when sourcing internationally?
Logistics play a crucial role in international sourcing. Consider factors such as shipping methods, costs, and customs regulations in your country. Work with suppliers who have experience in international shipping and can provide a clear logistics plan, including freight forwarding and insurance. Always factor in potential delays due to customs, especially when importing from regions with stringent regulations. -
How should disputes be handled with suppliers?
To effectively manage disputes, establish clear terms in your contract, including dispute resolution mechanisms. Opt for arbitration or mediation clauses to resolve conflicts without resorting to litigation. Maintain thorough documentation of all communications and transactions, as this will be invaluable should a dispute arise. Building a solid relationship based on trust and transparency can also help mitigate conflicts before they escalate.
Strategic Sourcing Conclusion and Outlook for vending machine cage
In summary, the strategic sourcing of vending machine cages is essential for international B2B buyers looking to enhance operational efficiency and profitability. By focusing on quality, supplier reliability, and cost-effectiveness, businesses can ensure they are making informed purchasing decisions that align with their long-term goals. Engaging with suppliers who understand regional demands and compliance requirements is crucial, especially for buyers from diverse markets such as Africa, South America, the Middle East, and Europe.
Key Takeaways:
– Prioritize suppliers that offer high-quality products and robust after-sales support.
– Assess total cost of ownership, not just the initial purchase price, to maximize return on investment.
– Foster relationships with local suppliers who can navigate regional regulations and logistics.
As the vending machine industry continues to evolve with technological advancements and changing consumer preferences, proactive sourcing strategies will be pivotal. Buyers are encouraged to keep abreast of market trends and innovations to remain competitive. Take the next step in your sourcing journey today—explore partnerships that will drive your business forward in this dynamic marketplace.