Master the Vending Machine Business Near Me: Essential
Guide to Vending Machine Business Near Me
- Introduction: Navigating the Global Market for vending machine business near me
- Understanding vending machine business near me Types and Variations
- Key Industrial Applications of vending machine business near me
- Strategic Material Selection Guide for vending machine business near me
- In-depth Look: Manufacturing Processes and Quality Assurance for vending machine business near me
- Comprehensive Cost and Pricing Analysis for vending machine business near me Sourcing
- Spotlight on Potential vending machine business near me Manufacturers and Suppliers
- Essential Technical Properties and Trade Terminology for vending machine business near me
- Navigating Market Dynamics, Sourcing Trends, and Sustainability in the vending machine business near me Sector
- Frequently Asked Questions (FAQs) for B2B Buyers of vending machine business near me
- Strategic Sourcing Conclusion and Outlook for vending machine business near me
Introduction: Navigating the Global Market for vending machine business near me
In an increasingly globalized economy, the vending machine sector offers lucrative opportunities for B2B buyers seeking innovative solutions to enhance customer experience and streamline operations. With the rapid growth of urbanization and changing consumer behaviors, vending machines have evolved beyond simple snack dispensers to versatile platforms offering a wide range of products, from healthy snacks to tech gadgets. This guide is designed to empower international B2B buyers, particularly from regions such as Africa, South America, the Middle East, and Europe, by providing essential insights into the vending machine business landscape.
Understanding the dynamics of the vending machine market is crucial for making informed sourcing decisions. This comprehensive guide covers various types of vending machines, including traditional, smart, and specialty options, while delving into the materials used in their construction, manufacturing processes, and quality control standards. We will also explore supplier networks, pricing structures, and market trends that influence procurement strategies.
By navigating the complexities of the vending machine business, buyers will gain valuable insights that enable them to assess suppliers, negotiate better terms, and ultimately enhance their product offerings. Whether you’re a seasoned operator or a newcomer to the industry, this guide will equip you with the knowledge necessary to thrive in the competitive vending landscape, ensuring you capitalize on this dynamic sector’s growth potential.
Understanding vending machine business near me Types and Variations
Type Name | Key Distinguishing Features | Primary B2B Applications | Brief Pros & Cons for Buyers |
---|---|---|---|
Traditional Snack Vending | Offers a variety of packaged snacks and beverages | Offices, schools, hospitals | Pros: Low initial investment; Cons: Limited product variety |
Healthy Food Vending | Focuses on nutritious options like salads and fruits | Gyms, corporate wellness programs | Pros: Appeals to health-conscious consumers; Cons: Higher costs |
Coffee Vending | Specializes in coffee and related beverages | Cafés, office buildings, events | Pros: High demand; Cons: Requires regular maintenance |
Specialty Item Vending | Provides niche products like electronics or beauty items | Airports, malls, tourist attractions | Pros: Unique offerings; Cons: Higher risk of unsold inventory |
Automated Retail Kiosks | Combines vending with e-commerce capabilities | Retail environments, events | Pros: Innovative shopping experience; Cons: Higher technical complexity |
Traditional Snack Vending
Traditional snack vending machines are the most common type, providing a wide range of packaged snacks and beverages. These machines are best suited for environments like offices, schools, and hospitals where quick access to snacks is desired. When considering a purchase, B2B buyers should evaluate the machine’s capacity, ease of restocking, and the variety of products it can hold. The low initial investment makes it appealing; however, the limited product variety might not cater to all consumer preferences.
Healthy Food Vending
Healthy food vending machines are designed to offer nutritious snacks and meals, such as salads and fresh fruits. They are particularly suitable for gyms and corporate wellness programs, where health-conscious consumers are prevalent. Buyers should consider the sourcing of fresh ingredients and the machine’s ability to maintain proper temperature and freshness. While these machines can attract a niche market, the higher costs associated with healthier products can be a drawback for some businesses.
Coffee Vending
Coffee vending machines focus on providing a range of coffee and related beverages, making them ideal for cafés, office buildings, and events. These machines can cater to the high demand for quality coffee, especially in business environments. B2B buyers should look into the variety of options available, including specialty coffees and customization features. While they can generate significant revenue, regular maintenance and the potential for equipment failure need to be factored into the purchasing decision.
Specialty Item Vending
Specialty item vending machines offer unique products, such as electronics or beauty items, targeting specific consumer interests. They are often found in high-traffic areas like airports, malls, and tourist attractions. When evaluating these machines, B2B buyers should assess the demand for the specific items offered and the potential for unsold inventory. While these machines can provide a unique shopping experience, the higher risk of unsold stock and the need for regular updates can pose challenges.
Automated Retail Kiosks
Automated retail kiosks blend vending with e-commerce, allowing consumers to browse and purchase a variety of products. These kiosks are increasingly popular in retail environments and at events, offering an innovative shopping experience. B2B buyers should consider the technology required for operation, including payment processing and inventory management systems. Although they can enhance customer engagement and sales, the complexity of setup and maintenance may deter some businesses from investing.
Related Video: How to Start a Vending Machine Business, Cost, Tips, How Much You Make
Key Industrial Applications of vending machine business near me
Industry/Sector | Specific Application of vending machine business near me | Value/Benefit for the Business | Key Sourcing Considerations for this Application |
---|---|---|---|
Retail | Automated product dispensing for convenience stores | Increased sales through 24/7 availability | Machine compatibility with local products and payment methods |
Healthcare | Medicine and healthcare supplies vending | Improved access to essential health products | Compliance with health regulations and product safety standards |
Education | Snack and beverage vending in schools | Enhanced student satisfaction and engagement | Nutritional content regulations and machine customization |
Hospitality | In-room vending solutions for hotels | Additional revenue stream with minimal staffing | High-quality products and aesthetic alignment with hotel branding |
Corporate Offices | Snack and beverage vending for employee break rooms | Boosted employee morale and productivity | Variety of options to cater to diverse employee preferences |
Retail
In the retail sector, vending machines serve as automated product dispensers, particularly in convenience stores. They enable businesses to offer a wide range of products, including snacks, beverages, and even personal care items, without the need for constant staff oversight. This 24/7 availability can significantly increase sales, especially in high-footfall areas. For international buyers, it’s essential to consider machine compatibility with local products and payment methods, such as mobile payments, which are increasingly popular in regions like Africa and South America.
Healthcare
Vending machines in healthcare settings provide essential supplies, such as over-the-counter medications and first aid kits. They offer patients and visitors quick access to necessary items, thus improving the overall experience in hospitals and clinics. For B2B buyers in this sector, understanding compliance with health regulations and product safety standards is crucial to ensure that the vending solutions meet the required legal and operational guidelines, particularly in the Middle East and Europe, where regulations can be stringent.
Education
In educational institutions, vending machines have become a staple for providing snacks and beverages to students. By offering a variety of healthy options, schools can enhance student satisfaction and engagement while addressing nutritional concerns. International buyers must navigate local regulations regarding nutritional content and machine customization to ensure compliance and appeal to students’ preferences, especially in diverse markets across Africa and Europe.
Hospitality
The hospitality industry benefits from in-room vending solutions that cater to guests’ needs for snacks and drinks without requiring significant staffing. This additional revenue stream allows hotels to provide convenience while also enhancing the guest experience. When sourcing vending machines for this sector, it’s important for B2B buyers to focus on high-quality products and ensure that the vending machines align aesthetically with the hotel’s branding, which can vary significantly across regions, including the UAE and South America.
Corporate Offices
Vending machines in corporate offices serve as a convenient source of snacks and beverages for employees, contributing to increased morale and productivity. By offering a diverse range of options, businesses can cater to various dietary preferences and restrictions, fostering a positive workplace environment. B2B buyers should prioritize sourcing machines that provide a variety of choices to meet employee needs and preferences, especially in multi-national companies operating in regions like Europe and Africa, where cultural dietary practices may differ.
Strategic Material Selection Guide for vending machine business near me
When selecting materials for vending machines, international B2B buyers must consider a variety of factors, including performance characteristics, cost implications, and compliance with regional standards. Here, we analyze four common materials used in the manufacturing of vending machines, focusing on their properties, advantages, disadvantages, and specific considerations for buyers from Africa, South America, the Middle East, and Europe.
1. Stainless Steel
Key Properties: Stainless steel is renowned for its excellent corrosion resistance, high strength, and ability to withstand a wide range of temperatures. It typically has a temperature rating of up to 870°C (1600°F) and is resistant to rust and staining.
Pros & Cons: The primary advantage of stainless steel is its durability and long lifespan, making it ideal for outdoor and high-traffic environments. However, it is more expensive than other materials, which can increase the overall cost of the vending machine. Manufacturing complexity is moderate, as it requires specialized techniques for cutting and welding.
Impact on Application: Stainless steel is compatible with a variety of media, including food and beverages, making it a preferred choice for vending machines.
Considerations for International Buyers: Buyers should ensure compliance with food safety regulations and standards such as ASTM A240 for stainless steel. In regions like the UAE, adherence to local health and safety regulations is critical.
2. Mild Steel
Key Properties: Mild steel is characterized by its good weldability, ductility, and cost-effectiveness. It has a lower corrosion resistance compared to stainless steel and is typically rated for temperatures up to 400°C (752°F).
Pros & Cons: The main advantage of mild steel is its low cost, making it an attractive option for budget-conscious buyers. However, its susceptibility to rust and corrosion limits its use in outdoor applications unless properly coated or treated. The manufacturing process is relatively straightforward.
Impact on Application: Mild steel is suitable for internal components of vending machines but may not be ideal for parts exposed to moisture or harsh environments.
Considerations for International Buyers: Buyers in regions with high humidity, such as parts of South America, should consider additional protective coatings to enhance corrosion resistance. Compliance with local standards, such as ASTM A36, is also essential.
3. Aluminum
Key Properties: Aluminum is lightweight, corrosion-resistant, and has a good strength-to-weight ratio. It can withstand temperatures up to 660°C (1220°F) and is often used in applications where weight reduction is critical.
Pros & Cons: The lightweight nature of aluminum offers significant advantages in terms of transport and installation. However, it can be more expensive than mild steel and may not have the same level of durability under heavy loads. Manufacturing processes for aluminum can be more complex due to its properties.
Impact on Application: Aluminum is ideal for components that require weight savings, such as exterior panels and frames of vending machines.
Considerations for International Buyers: Buyers should be aware of the specific grades of aluminum used in vending machines and ensure compliance with standards such as ASTM B221. In Europe, adherence to EN standards is crucial.
4. Polycarbonate
Key Properties: Polycarbonate is a durable thermoplastic known for its high impact resistance and transparency. It can withstand temperatures ranging from -40°C to 120°C (-40°F to 248°F).
Pros & Cons: The key advantage of polycarbonate is its lightweight nature and excellent impact resistance, making it suitable for transparent panels in vending machines. However, it is less durable than metals and can be prone to scratching and UV degradation over time.
Impact on Application: Polycarbonate is often used for viewing windows and protective covers in vending machines, allowing visibility of products while providing safety.
Considerations for International Buyers: Buyers should consider the UV stability of polycarbonate when selecting materials for sunny regions, such as parts of Africa and South America. Compliance with standards such as ASTM D635 is also important.
Summary Table
Material | Typical Use Case for vending machine business near me | Key Advantage | Key Disadvantage/Limitation | Relative Cost (Low/Med/High) |
---|---|---|---|---|
Stainless Steel | External panels and internal components | Excellent durability and corrosion resistance | Higher cost than other materials | High |
Mild Steel | Internal structural components | Cost-effective and easy to manufacture | Susceptible to corrosion | Low |
Aluminum | Lightweight frames and external panels | Lightweight and good strength-to-weight ratio | More expensive and complex to manufacture | Medium |
Polycarbonate | Transparent panels and protective covers | High impact resistance and lightweight | Prone to scratching and UV degradation | Medium |
This strategic material selection guide provides essential insights for international B2B buyers looking to optimize their vending machine business. By carefully evaluating these materials, buyers can make informed decisions that align with their operational needs and regional standards.
In-depth Look: Manufacturing Processes and Quality Assurance for vending machine business near me
Understanding Manufacturing Processes in the Vending Machine Industry
For international B2B buyers entering the vending machine market, grasping the manufacturing processes is crucial for ensuring product quality and reliability. The manufacturing process typically involves several key stages, each contributing to the overall quality of the vending machines.
Main Stages of Manufacturing
-
Material Preparation
– The first step involves sourcing high-quality raw materials such as metals, plastics, and electronic components. Buyers should prioritize suppliers who demonstrate a commitment to using durable and sustainable materials.
– Conducting a material certification check can assure buyers of the quality of the sourced components. -
Forming
– This stage includes processes like stamping, bending, and molding to shape the machine’s components. Advanced techniques such as CNC machining are commonly employed to ensure precision.
– Buyers should look for manufacturers that utilize modern technology to enhance accuracy and reduce material waste. -
Assembly
– The assembly process integrates all components into the final product. Automated assembly lines are prevalent, significantly speeding up production while minimizing human error.
– Effective communication with suppliers regarding the assembly process can lead to better customization options for your specific market needs. -
Finishing
– This final stage includes painting, coating, and quality checks before packaging. The finishing touches not only enhance aesthetics but also provide protection against environmental factors.
– Suppliers should be able to show certifications related to their finishing processes, ensuring compliance with international standards.
Quality Assurance in Vending Machine Manufacturing
Quality assurance (QA) is integral to maintaining product integrity and customer satisfaction. For international buyers, understanding the relevant standards and checkpoints in the QA process is essential.
Relevant International Standards
-
ISO 9001
– This standard is essential for establishing a quality management system (QMS). Manufacturers with ISO 9001 certification demonstrate their ability to consistently provide products that meet customer and regulatory requirements. -
CE Marking
– For products sold within the European market, CE marking signifies compliance with health, safety, and environmental protection standards. It is crucial for buyers in Europe to ensure their suppliers are CE compliant. -
API Standards
– While more commonly associated with the oil and gas industry, API standards can be relevant for vending machines that dispense specialized products. Buyers should verify if their suppliers follow these standards where applicable.
Quality Control Checkpoints
-
Incoming Quality Control (IQC)
– This step involves inspecting raw materials and components upon arrival. Buyers should request reports detailing IQC processes to ensure that only high-quality materials are used. -
In-Process Quality Control (IPQC)
– IPQC is conducted during various stages of manufacturing. It helps catch defects early, reducing waste and rework costs. B2B buyers should inquire about the frequency and methods of IPQC checks. -
Final Quality Control (FQC)
– This is the last checkpoint before products are shipped. It includes comprehensive testing of the completed vending machines to ensure they meet specifications. Buyers can request FQC reports to verify compliance with quality standards.
Common Testing Methods
Functional Testing
- Ensures that the vending machine operates as intended, including payment processing, product dispensing, and user interface functionality.
Environmental Testing
- Simulates various environmental conditions to test the machine’s durability and functionality in extreme temperatures or humidity levels.
Safety Testing
- Checks for electrical safety, including grounding and insulation tests, to prevent malfunctions that could lead to hazards.
Verifying Supplier Quality Control
For international B2B buyers, verifying the quality control practices of suppliers is vital. Here are key strategies:
-
Supplier Audits
– Conducting on-site audits can provide in-depth insights into the manufacturing processes and quality control practices of potential suppliers. -
Requesting Quality Reports
– Regular quality reports and certifications from suppliers should be requested. This documentation serves as a tangible record of compliance with international standards. -
Third-Party Inspection
– Engaging third-party inspection services can offer an unbiased assessment of a supplier’s quality control practices. This is especially important for buyers in regions with different regulatory environments.
Quality Control Nuances for International Buyers
B2B buyers from Africa, South America, the Middle East, and Europe must navigate a complex landscape of regulations and quality expectations. Here are some considerations:
-
Regulatory Variance: Different regions may have varying compliance requirements. It’s critical for buyers to familiarize themselves with both local and international regulations that affect vending machine standards.
-
Cultural Sensitivity: Understanding cultural nuances can enhance communication with suppliers. For instance, buyers from the UAE may prioritize rapid response times, while those from Argentina might focus more on cost-effectiveness.
-
Logistical Challenges: Shipping and logistics can impact quality. Buyers should ensure that suppliers have robust logistics strategies in place to maintain quality throughout transportation.
Conclusion
A thorough understanding of manufacturing processes and quality assurance is essential for international B2B buyers in the vending machine industry. By focusing on the manufacturing stages, relevant quality standards, effective testing methods, and verification strategies, buyers can make informed decisions that ensure they procure high-quality vending machines tailored to their market needs.
Related Video: SMART Quality Control for Manufacturing
Comprehensive Cost and Pricing Analysis for vending machine business near me Sourcing
Understanding the cost structure and pricing dynamics of the vending machine business is crucial for international B2B buyers, particularly those from Africa, South America, the Middle East, and Europe. This analysis will guide you through key cost components, price influencers, and practical buyer tips to optimize your sourcing strategy.
Cost Components
-
Materials: The primary materials involved in vending machine production include metal (for the frame), glass (for the display), and electronics (for payment systems). Sourcing high-quality materials can significantly affect both the initial cost and the longevity of the machines.
-
Labor: Labor costs vary widely based on manufacturing location. For instance, countries in Europe may have higher labor costs compared to regions in Africa or South America. Understanding local wage standards and labor laws can help in negotiating better prices.
-
Manufacturing Overhead: This encompasses utility costs, rent, and other indirect costs associated with running a manufacturing facility. Overhead can vary based on the operational efficiency of the supplier and the location of the manufacturing plant.
-
Tooling: Initial tooling costs for custom machines can be substantial. If your order requires unique specifications, consider the tooling costs as a part of your negotiation strategy, as these can be amortized over larger volumes.
-
Quality Control (QC): Effective QC processes ensure that machines meet specified standards, which can prevent costly returns and repairs. Buyers should inquire about the QC measures in place and how they impact pricing.
-
Logistics: Freight costs, customs duties, and insurance must be factored into the total cost calculation. Logistics can become complex for international shipments, so understanding Incoterms is essential for managing these costs effectively.
-
Margin: Suppliers typically build in a profit margin, which can vary by region and market demand. Knowing the industry standard margins can help you identify when prices are inflated.
Price Influencers
-
Volume/MOQ: Larger orders often lead to better pricing due to economies of scale. Negotiating minimum order quantities (MOQs) can help reduce per-unit costs.
-
Specifications/Customization: Customized machines or specific features can significantly affect pricing. Be clear about your needs, but be prepared for potential price increases based on complexity.
-
Materials: The choice of materials can influence both the cost and durability of vending machines. Higher-quality materials may come with a higher upfront cost but can lead to long-term savings.
-
Quality/Certifications: Machines that meet international standards or have specific certifications may be priced higher. However, these certifications can also reduce liability and increase customer trust.
-
Supplier Factors: A supplier’s reputation, experience, and production capabilities can impact pricing. Established suppliers may command higher prices due to reliability and quality assurance.
-
Incoterms: Understanding the implications of different Incoterms (such as FOB, CIF, etc.) is crucial for comprehending who bears the costs and risks during shipping. This can influence overall pricing strategies.
Buyer Tips
-
Negotiation: Always enter negotiations with a clear understanding of the market prices and the breakdown of costs. Be prepared to discuss each component and how it affects the overall price.
-
Cost-Efficiency: Look beyond the initial purchase price; consider aspects like maintenance costs, energy efficiency, and potential downtime. These factors contribute to the Total Cost of Ownership (TCO).
-
Pricing Nuances: Be aware of regional pricing differences. For instance, suppliers in the UAE may have different pricing structures compared to those in Argentina, reflecting local economic conditions and market dynamics.
-
Local Partnerships: Establishing relationships with local distributors or agents can enhance your understanding of the market and provide insights into effective negotiation strategies.
Disclaimer
Prices and cost structures provided in this analysis are indicative and can vary based on market fluctuations, supplier negotiations, and specific requirements. Always conduct thorough due diligence before finalizing any sourcing agreements.
Spotlight on Potential vending machine business near me Manufacturers and Suppliers
- (No specific manufacturer data was available or requested for detailed profiling in this section for vending machine business near me.)*
Essential Technical Properties and Trade Terminology for vending machine business near me
Essential Technical Properties
When considering the procurement of vending machines, understanding the essential technical properties can significantly influence purchasing decisions. Here are some critical specifications to keep in mind:
-
Material Grade
Vending machines are typically made from various materials, including stainless steel, plastic, and tempered glass. The material grade affects durability, aesthetic appeal, and maintenance requirements. Stainless steel, for instance, is preferred for its corrosion resistance and strength, making it ideal for high-traffic environments. -
Power Consumption
This specification refers to the amount of electricity the vending machine uses. Lower power consumption is vital for reducing operational costs, especially in regions with high electricity tariffs. Buyers should assess power efficiency ratings and consider machines that use energy-efficient technologies to minimize utility expenses. -
Capacity
Capacity indicates the number of items a vending machine can hold, which directly impacts sales potential. Machines come in various sizes, and understanding the target market’s demand is essential for selecting the right machine. For example, in bustling urban areas, higher-capacity machines may yield better returns. -
Temperature Control
For vending machines that dispense perishable items, precise temperature control is critical. The ability to maintain suitable temperatures ensures food safety and product quality. Buyers should inquire about the machine’s refrigeration system and its capability to handle varying external temperatures, especially in regions with extreme climates.
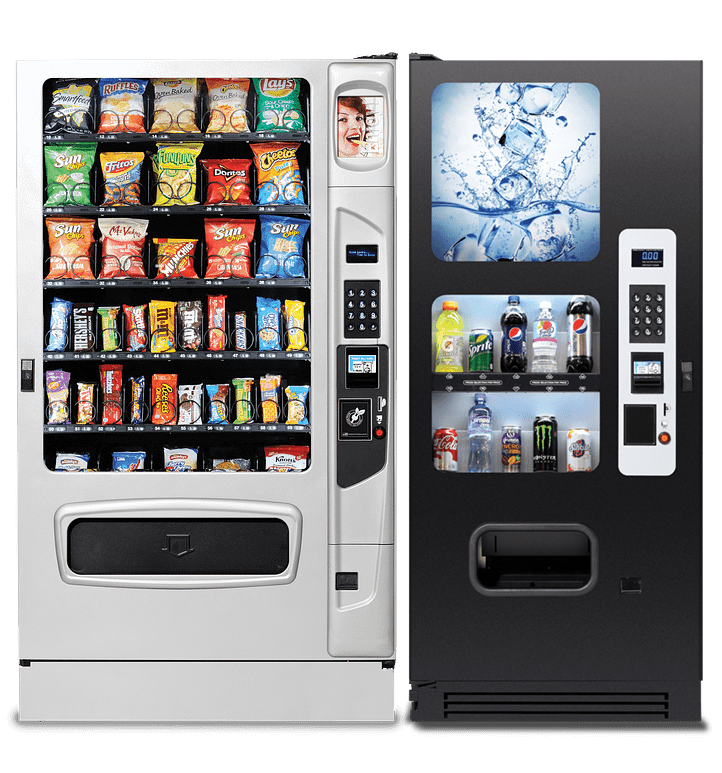
Illustrative Image (Source: Google Search)
- User Interface
A user-friendly interface enhances customer experience and can lead to increased sales. Look for machines that offer intuitive touchscreens, multilingual options, and contactless payment methods. Modern interfaces also provide data analytics capabilities, allowing operators to track sales trends and inventory levels.
Common Trade Terminology
Familiarity with industry jargon is crucial for effective communication and negotiation in the vending machine business. Here are some common terms that B2B buyers should know:
-
OEM (Original Equipment Manufacturer)
This term refers to companies that produce parts and equipment that may be marketed by another manufacturer. For buyers, partnering with reputable OEMs ensures high-quality machines and components, which can lead to fewer maintenance issues and a better return on investment. -
MOQ (Minimum Order Quantity)
This is the smallest quantity of a product a supplier is willing to sell. Understanding MOQ is essential for budget planning and inventory management. Buyers should negotiate MOQs that align with their sales forecasts to avoid overstocking or running out of products. -
RFQ (Request for Quotation)
An RFQ is a document sent to suppliers requesting pricing information for specific products. It’s a critical step in the procurement process that allows buyers to compare prices and terms effectively. Crafting a detailed RFQ can help in receiving accurate and competitive quotes. -
Incoterms (International Commercial Terms)
These are standardized terms used in international trade to clarify the responsibilities of buyers and sellers regarding shipping, insurance, and tariffs. Familiarity with Incoterms can help buyers negotiate better shipping terms and avoid unexpected costs during transportation. -
Lead Time
This term refers to the time taken from placing an order to the delivery of the product. Understanding lead times is vital for inventory planning and ensuring that vending machines are operational when needed. Buyers should communicate their timelines clearly with suppliers to avoid delays.
By mastering these technical properties and trade terms, B2B buyers can make informed decisions, negotiate effectively, and ultimately enhance their vending machine business operations.
Navigating Market Dynamics, Sourcing Trends, and Sustainability in the vending machine business near me Sector
Market Overview & Key Trends
The vending machine industry is experiencing a significant transformation driven by technological advancements, changing consumer preferences, and a focus on convenience. For international B2B buyers, particularly those in regions like Africa, South America, the Middle East, and Europe, understanding these dynamics is crucial for making informed sourcing decisions. The rise of cashless transactions, mobile payments, and contactless interactions has reshaped the purchasing process, pushing operators to integrate smart technologies into their machines. This shift not only enhances user experience but also provides valuable data analytics to optimize inventory and streamline operations.
Emerging trends such as the demand for healthy snack options and locally sourced products are reshaping inventory strategies. B2B buyers should consider partnering with suppliers who can provide organic, gluten-free, and sustainably sourced products to meet growing consumer expectations. Additionally, the rise of e-commerce platforms is enabling businesses to source vending machines and products directly from manufacturers, bypassing traditional distribution channels and reducing costs.
Furthermore, the push for automation and IoT integration is likely to continue, increasing operational efficiency and providing real-time monitoring capabilities. For buyers in regions like Argentina and the UAE, investing in vending machines equipped with these technologies can offer a competitive advantage in a rapidly evolving marketplace.
Sustainability & Ethical Sourcing in B2B
As the global market increasingly prioritizes sustainability, the vending machine sector is no exception. The environmental impact of vending operations—ranging from energy consumption to waste generation—has prompted businesses to rethink their sourcing strategies. International B2B buyers should prioritize ethical sourcing by selecting suppliers who demonstrate a commitment to sustainable practices, such as using energy-efficient machines and sustainable packaging.
Certification programs, such as ISO 14001 for environmental management systems, can serve as benchmarks for evaluating suppliers’ sustainability credentials. Moreover, utilizing materials that are recyclable or biodegradable not only reduces the carbon footprint but also appeals to eco-conscious consumers. For instance, sourcing machines constructed from recycled materials or featuring energy-efficient technologies can significantly enhance a company’s brand image while contributing to a circular economy.
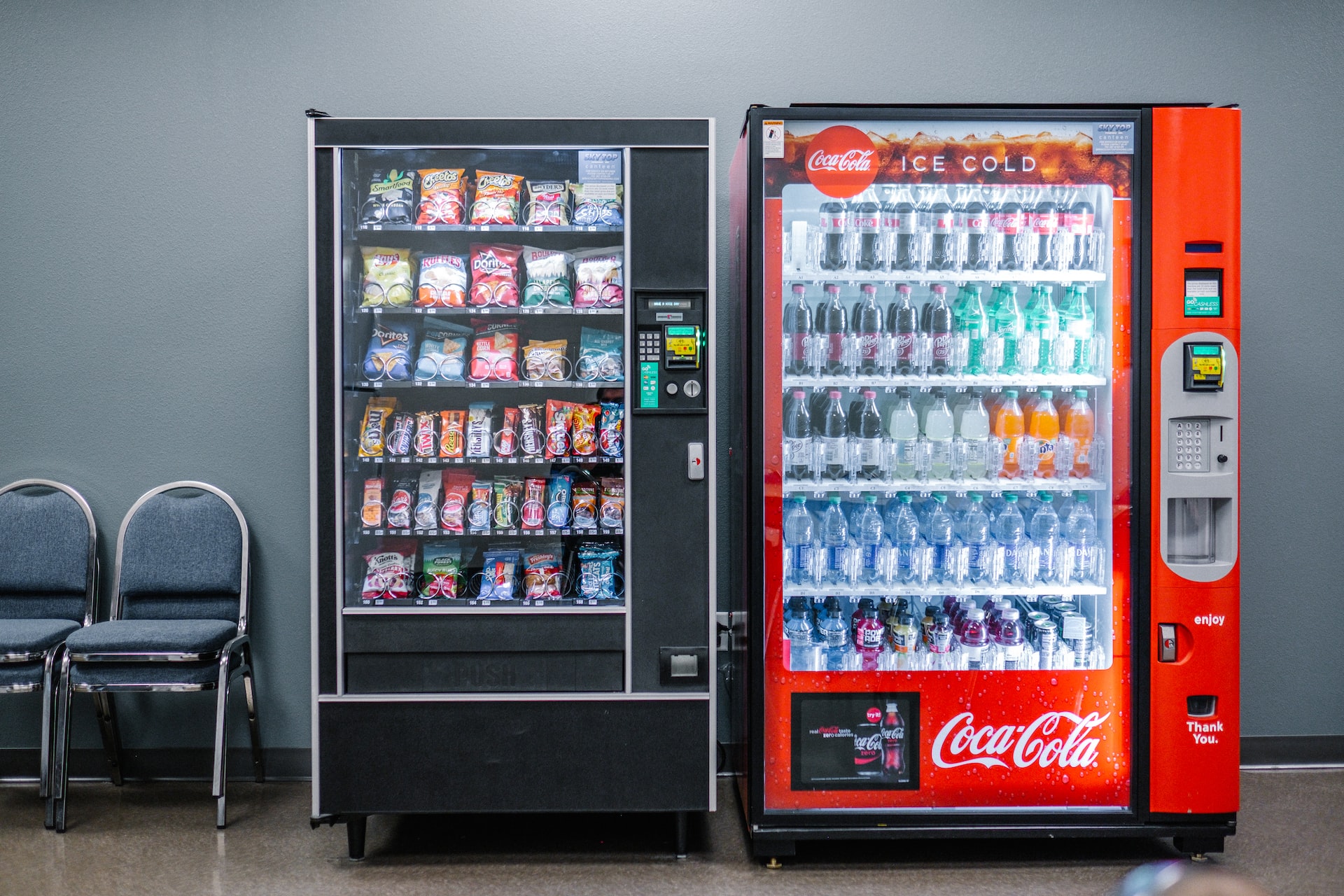
Illustrative Image (Source: Google Search)
In regions like Europe and the Middle East, there is a growing emphasis on transparency in supply chains. Buyers should engage with suppliers that provide clear information about their sourcing processes and environmental policies. By doing so, businesses can ensure compliance with international standards and foster trust with consumers, ultimately leading to a more resilient and ethical vending machine operation.
Brief Evolution/History
The vending machine industry has evolved remarkably since its inception in the early 1880s. Initially focused on dispensing simple products like postcards and cigarettes, the sector has transitioned into a high-tech market offering a diverse range of goods, from fresh food to electronics. The introduction of coin-operated machines revolutionized accessibility, paving the way for modern innovations such as cashless payments and app-based services.
As consumer preferences shifted over the decades—first towards convenience and then towards health and sustainability—the industry responded with advancements in machine design and product offerings. Today, vending machines are equipped with smart technology that allows for remote monitoring and management, enabling operators to adapt swiftly to market demands. For B2B buyers, understanding this evolution is essential for recognizing the opportunities and challenges present in today’s competitive landscape.
Related Video: Is global trade transforming? | Counting the Cost
Frequently Asked Questions (FAQs) for B2B Buyers of vending machine business near me
-
How can I effectively vet suppliers for vending machines near me?
When vetting suppliers, consider their reputation, experience, and customer reviews. Look for certifications or industry affiliations that indicate quality standards. Request references from other international buyers, particularly those from your region, and assess their responsiveness and communication skills. Additionally, visit their facility if possible, or utilize virtual tours to get a sense of their operations and product quality. This thorough approach will help ensure you partner with a reliable supplier. -
What customization options are available for vending machines?
Many suppliers offer various customization options, including size, design, product selection, and branding. Specify your requirements based on local market preferences and consumer behavior. Discuss potential technology integrations, such as cashless payment systems or remote monitoring capabilities. Ensure the supplier can accommodate your specific needs and ask for samples or mock-ups to visualize the final product before committing to large orders. -
What are the typical minimum order quantities (MOQ) and lead times?
MOQs vary widely depending on the supplier and the complexity of the vending machines. Generally, you can expect an MOQ ranging from 10 to 50 units. Lead times can also differ based on customization, ranging from a few weeks for standard models to several months for highly tailored solutions. Always clarify these details upfront and consider negotiating terms that align with your business capacity and market demands. -
What payment terms should I expect when purchasing vending machines?
Payment terms can vary significantly by supplier and region. Common terms include a deposit (usually 30-50%) upon order confirmation and the balance upon delivery. Be cautious of suppliers who demand full payment upfront. Evaluate options for escrow services or letters of credit to mitigate risks. Always ensure that payment methods are secure and consider the implications of currency fluctuations on international transactions. -
How do I ensure quality assurance and necessary certifications?
Request documentation for quality assurance processes and certifications relevant to your region, such as ISO standards or safety certifications. Inquire about the supplier’s quality control measures, including testing procedures and warranty policies. It’s beneficial to conduct a factory audit if possible or have third-party inspection services assess the products before shipment to ensure compliance with your standards. -
What logistics considerations should I be aware of when importing vending machines?
Logistics play a crucial role in the import process. Consider factors such as shipping methods (air vs. sea), customs clearance procedures, and potential tariffs or duties. Work with logistics partners experienced in international trade to navigate these complexities. Ensure that the supplier provides proper packaging and documentation to facilitate smooth transit. Additionally, plan for potential delays and have contingency plans in place. -
How can I handle disputes with suppliers effectively?
To manage disputes, establish clear communication channels and maintain documentation of all agreements and transactions. If issues arise, address them promptly and professionally, seeking to understand the supplier’s perspective. Utilize mediation or arbitration as an alternative to legal action, as this can be less costly and time-consuming. Always review the contract for dispute resolution clauses and consider involving a legal expert familiar with international trade laws if necessary. -
What are the best practices for maintaining a long-term relationship with vending machine suppliers?
Building a strong relationship with your suppliers involves regular communication, transparency, and mutual respect. Provide feedback on product performance and market trends, which can help suppliers innovate and improve their offerings. Schedule regular check-ins or visits to keep the partnership active. Consider collaborating on promotions or marketing strategies to benefit both parties. A solid relationship will enhance reliability and foster better service and pricing in the long run.
Strategic Sourcing Conclusion and Outlook for vending machine business near me
In navigating the vending machine business landscape, strategic sourcing emerges as a key driver of success for international B2B buyers. Understanding local market dynamics, including consumer preferences and regulatory environments, is essential for tailoring offerings to meet diverse regional needs. Buyers must prioritize partnerships with reliable suppliers to ensure quality, sustainability, and innovation in their product offerings.
Leveraging technology for inventory management and customer engagement can significantly enhance operational efficiency and drive sales. It is also crucial to keep an eye on emerging trends, such as healthier snack options and cashless payment systems, which are reshaping the vending experience.
As the global market continues to evolve, so too does the opportunity for growth in the vending machine sector. B2B buyers from regions like Africa, South America, the Middle East, and Europe should embrace strategic sourcing as a means to not only optimize costs but also to foster long-term relationships with suppliers that can offer insights and support tailored to their unique markets.
In conclusion, the future of the vending machine business is promising. By taking proactive steps in strategic sourcing today, international buyers can position themselves for success in a competitive landscape. Now is the time to act—explore partnerships, innovate your offerings, and stay ahead of market trends to capitalize on this burgeoning industry.