Master the Purchase Vending Machine Route for Maximum
Guide to Purchase Vending Machine Route
- Introduction: Navigating the Global Market for purchase vending machine route
- Understanding purchase vending machine route Types and Variations
- Key Industrial Applications of purchase vending machine route
- Strategic Material Selection Guide for purchase vending machine route
- In-depth Look: Manufacturing Processes and Quality Assurance for purchase vending machine route
- Comprehensive Cost and Pricing Analysis for purchase vending machine route Sourcing
- Spotlight on Potential purchase vending machine route Manufacturers and Suppliers
- Essential Technical Properties and Trade Terminology for purchase vending machine route
- Navigating Market Dynamics, Sourcing Trends, and Sustainability in the purchase vending machine route Sector
- Market Overview & Key Trends
- Sustainability & Ethical Sourcing in B2B
- Brief Evolution/History
- Frequently Asked Questions (FAQs) for B2B Buyers of purchase vending machine route
- Strategic Sourcing Conclusion and Outlook for purchase vending machine route
Introduction: Navigating the Global Market for purchase vending machine route
In today’s rapidly evolving global marketplace, the purchase vending machine route represents a strategic opportunity for B2B buyers seeking to enhance their product distribution and customer engagement. As businesses across Africa, South America, the Middle East, and Europe look to streamline their operations, understanding the nuances of vending machine routes becomes increasingly critical. This guide serves as a comprehensive resource, detailing the various types of vending machines, essential materials, manufacturing and quality control standards, and the most reputable suppliers in the industry.
International buyers will benefit from insights into cost structures, market trends, and best practices for sourcing vending machines that align with their specific business needs. With a focus on actionable strategies, this guide empowers decision-makers to navigate the complexities of the vending machine landscape, ensuring they make informed choices that drive profitability and customer satisfaction.
Moreover, the guide addresses common FAQs, providing clarity on operational challenges and solutions. Whether you are a seasoned buyer or exploring vending machines for the first time, this resource will equip you with the knowledge necessary to capitalize on emerging opportunities and optimize your vending routes for success. Embrace the potential of vending machines as a transformative asset in your supply chain strategy and unlock new avenues for growth and customer connection.
Understanding purchase vending machine route Types and Variations
Type Name | Key Distinguishing Features | Primary B2B Applications | Brief Pros & Cons for Buyers |
---|---|---|---|
Traditional Snack Vending | Offers a range of snacks and beverages | Offices, schools, hospitals | Pros: Familiarity, easy maintenance. Cons: Limited variety, less healthy options. |
Healthy Food Vending | Focus on nutritious snacks and meals | Gyms, health clubs, corporate offices | Pros: Appeals to health-conscious consumers. Cons: Higher price point, niche market. |
Specialty Beverage Vending | Focus on unique beverages (e.g., craft drinks) | Cafés, restaurants, event venues | Pros: Differentiates from competitors. Cons: Requires careful inventory management. |
Fresh Food Vending | Provides fresh meals, salads, or sandwiches | Airports, universities, corporate cafeterias | Pros: High demand for fresh options. Cons: Short shelf life, requires refrigeration. |
Automated Retail Kiosks | Advanced vending machines with touch screens | Retail environments, shopping malls, airports | Pros: Interactive experience, diverse product offerings. Cons: Higher initial investment, tech maintenance. |
Traditional Snack Vending
Traditional snack vending machines are characterized by their straightforward offerings of popular snacks and beverages, making them a staple in various environments. They are commonly found in offices, schools, and hospitals, providing quick access to food for busy individuals. B2B buyers should consider the machine’s maintenance needs, ease of restocking, and the variety of products offered, as these factors significantly influence customer satisfaction and sales.

Illustrative Image (Source: Google Search)
Healthy Food Vending
Healthy food vending machines cater to the growing demand for nutritious options, featuring items such as salads, protein bars, and low-calorie snacks. They are especially suitable for locations like gyms, health clubs, and corporate offices where health-conscious consumers seek convenient meal solutions. Buyers must evaluate the cost of products, shelf life, and the potential return on investment, as these machines often have a higher price point but can attract a dedicated customer base.
Specialty Beverage Vending
Specialty beverage vending machines focus on unique drink offerings, such as craft sodas, organic juices, or premium coffees. These machines are ideal for cafés, restaurants, and event venues looking to enhance their beverage selection. B2B buyers should assess the potential for differentiation in a competitive market, as well as the logistical challenges of managing diverse inventory and ensuring product freshness.
Fresh Food Vending
Fresh food vending machines provide a selection of fresh meals, salads, or sandwiches, appealing to consumers seeking healthier, ready-to-eat options. They are particularly popular in high-traffic areas like airports, universities, and corporate cafeterias. Buyers must consider the machine’s refrigeration capabilities, the sourcing of fresh ingredients, and the machine’s ability to handle short shelf life, which can affect profitability.
Automated Retail Kiosks
Automated retail kiosks represent the next generation of vending solutions, incorporating advanced technology such as touch screens and cashless payment options. These kiosks can offer a wide range of products, from snacks to electronics, making them suitable for retail environments, shopping malls, and airports. B2B buyers should weigh the higher initial investment and ongoing tech maintenance against the potential for increased customer engagement and sales through a modern, interactive experience.
Related Video: Machine Learning in 2024 – Beginner’s Course
Key Industrial Applications of purchase vending machine route
Industry/Sector | Specific Application of purchase vending machine route | Value/Benefit for the Business | Key Sourcing Considerations for this Application |
---|---|---|---|
Retail | Automated product dispensing for convenience items | Increased sales through 24/7 accessibility and reduced labor costs | Machine durability, payment options, product variety |
Healthcare | Dispensing medical supplies and personal protective equipment | Immediate access to critical supplies, reduced wait times | Compliance with health regulations, security features |
Education | Providing snacks and beverages in schools and universities | Enhanced student satisfaction and convenience | Nutritional standards, machine capacity, maintenance support |
Transportation | Offering travel essentials at transit hubs | Improved traveler experience and additional revenue streams | Location analysis, product selection, machine customization |
Hospitality | Mini-bar solutions for hotels and resorts | Increased guest satisfaction and additional revenue opportunities | Inventory management, payment systems, branding options |
Retail
In the retail sector, purchase vending machines serve as automated dispensing units for convenience items such as snacks, beverages, and personal care products. They provide customers with 24/7 access to essential items, significantly boosting sales while minimizing labor costs associated with staffing. International buyers should consider machine durability and flexibility in payment options to cater to diverse customer preferences across different regions.
Healthcare
In healthcare settings, purchase vending machines can be utilized to dispense medical supplies, personal protective equipment (PPE), and over-the-counter medications. This application addresses the urgent need for immediate access to essential supplies, thereby reducing wait times and enhancing patient care. Buyers in this sector must ensure compliance with health regulations and prioritize security features to protect sensitive medical items from theft or misuse.
Education
Educational institutions, including schools and universities, benefit from purchase vending machines by providing students with easy access to snacks and beverages. This enhances student satisfaction and convenience during breaks or study sessions. Buyers must consider nutritional standards for the products offered, machine capacity to handle high foot traffic, and ongoing maintenance support to ensure operational efficiency.
Transportation
In transportation hubs such as airports and train stations, vending machines offer travel essentials like snacks, drinks, and hygiene products. This enhances the traveler experience by providing quick access to necessary items and generating additional revenue streams for the operators. Key considerations for international buyers include conducting thorough location analysis to determine optimal machine placements and selecting a diverse product range that caters to various traveler needs.
Hospitality
In the hospitality industry, purchase vending machines can serve as mini-bar solutions in hotels and resorts, offering guests a selection of snacks and drinks without the need for staff intervention. This not only increases guest satisfaction but also creates additional revenue opportunities for the establishment. Buyers should focus on effective inventory management systems, integrated payment solutions, and branding options to align with the hotel’s image and guest expectations.
Related Video: How to Start a Vending Machine Business, Cost, Tips, How Much You Make
Strategic Material Selection Guide for purchase vending machine route
When selecting materials for a purchase vending machine route, it’s crucial to consider the properties, advantages, disadvantages, and specific regional compliance requirements. Below is an analysis of four common materials used in this context: Stainless Steel, Aluminum, Polycarbonate, and Carbon Steel.
Stainless Steel
Key Properties: Stainless steel is known for its excellent corrosion resistance, high strength, and ability to withstand high temperatures. Common grades used include 304 and 316, which offer varying levels of resistance to chlorides and acids.
Pros & Cons: The primary advantage of stainless steel is its durability and long lifespan, making it ideal for outdoor vending applications. However, it tends to be more expensive than other materials, and its manufacturing process can be complex, requiring specialized equipment.
Impact on Application: Stainless steel is highly compatible with a range of media, including food and beverages, making it a preferred choice for vending machines that dispense consumables.
Considerations for International Buyers: Buyers in regions like Europe and the Middle East should ensure compliance with food safety standards such as the EU Regulation 1935/2004. In South America and Africa, local standards may vary, so it’s essential to verify compliance with local health regulations.
Aluminum
Key Properties: Aluminum is lightweight, resistant to corrosion, and has good thermal conductivity. It is often anodized for additional protection against environmental factors.
Pros & Cons: The lightweight nature of aluminum makes it easier to handle and install, which can reduce shipping costs. However, it is less durable than stainless steel and can be prone to denting and scratching.
Impact on Application: Aluminum is suitable for vending machines that are not exposed to harsh environments. Its corrosion resistance allows it to be used in humid or coastal areas.
Considerations for International Buyers: Buyers should consider the specific alloy used, as different grades may be subject to varying regulations. In the UAE and Australia, adherence to local standards for aluminum products is crucial for ensuring safety and quality.
Polycarbonate
Key Properties: Polycarbonate is a strong, impact-resistant thermoplastic. It offers high transparency and can withstand a wide temperature range, making it suitable for various applications.
Pros & Cons: The primary advantage of polycarbonate is its lightweight and shatter-resistant nature, making it ideal for vending machine windows. However, it can be susceptible to scratching and UV degradation over time if not treated.
Impact on Application: Polycarbonate is particularly useful for vending machines that require visibility of the products inside, enhancing customer engagement.
Considerations for International Buyers: Compliance with environmental regulations regarding plastics is essential, especially in Europe, where directives such as REACH may apply. Buyers should also consider the impact of UV exposure in regions like Africa and the Middle East.
Carbon Steel
Key Properties: Carbon steel is known for its high strength and durability, with varying grades offering different levels of hardness and tensile strength.
Pros & Cons: It is cost-effective and widely available, making it a popular choice for structural components of vending machines. However, carbon steel is susceptible to corrosion and requires protective coatings to enhance its longevity.
Impact on Application: Carbon steel is suitable for internal components and frames where exposure to moisture is minimal. Its strength makes it ideal for heavy-duty applications.
Considerations for International Buyers: Buyers should ensure that carbon steel components are treated or coated to prevent rust, especially in humid climates found in parts of Africa and South America. Compliance with ASTM standards is common in the US and may be referenced in other regions.
Summary Table
Material | Typical Use Case for purchase vending machine route | Key Advantage | Key Disadvantage/Limitation | Relative Cost (Low/Med/High) |
---|---|---|---|---|
Stainless Steel | External casing and internal components for food vending machines | Excellent corrosion resistance and durability | Higher cost and complex manufacturing | High |
Aluminum | Lightweight frames and panels for vending machines | Lightweight and corrosion-resistant | Less durable, prone to dents and scratches | Medium |
Polycarbonate | Windows and transparent sections of vending machines | Impact-resistant and lightweight | Susceptible to scratching and UV degradation | Medium |
Carbon Steel | Structural components and frames | Cost-effective and strong | Susceptible to corrosion without treatment | Low |
This guide provides a comprehensive overview of material selection for purchase vending machine routes, considering various factors relevant to international B2B buyers. Understanding these materials and their implications will aid in making informed purchasing decisions tailored to specific regional needs.
In-depth Look: Manufacturing Processes and Quality Assurance for purchase vending machine route
Manufacturing vending machines for purchase routes involves a series of intricate processes designed to ensure that the final product is reliable, efficient, and meets the specific needs of B2B buyers. For international buyers from regions like Africa, South America, the Middle East, and Europe, understanding the manufacturing and quality assurance (QA) processes is critical for making informed purchasing decisions. Below is a comprehensive overview of typical manufacturing processes, quality assurance measures, and actionable insights for B2B buyers.
Manufacturing Process Stages
-
Material Preparation
– Sourcing: The process begins with the sourcing of high-quality materials such as metals, plastics, and electronic components. Buyers should ensure suppliers use materials that meet local and international standards.
– Inspection: Incoming materials undergo inspection to confirm they meet specified quality standards. This step is crucial as it prevents defects from entering the production line. -
Forming
– Techniques: Common forming techniques include stamping, bending, and machining. For example, metal parts may be stamped from sheets, while plastics might be injection molded.
– Equipment: High-precision machinery is employed to ensure that components are manufactured to exact specifications, reducing the risk of assembly issues later. -
Assembly
– Integration: Components are assembled in a clean, controlled environment to minimize contamination and defects. Automated assembly lines may be used for efficiency, but manual assembly is also common for complex parts.
– Sub-assemblies: Key components, such as payment systems and refrigeration units, are often pre-assembled before being integrated into the main machine.
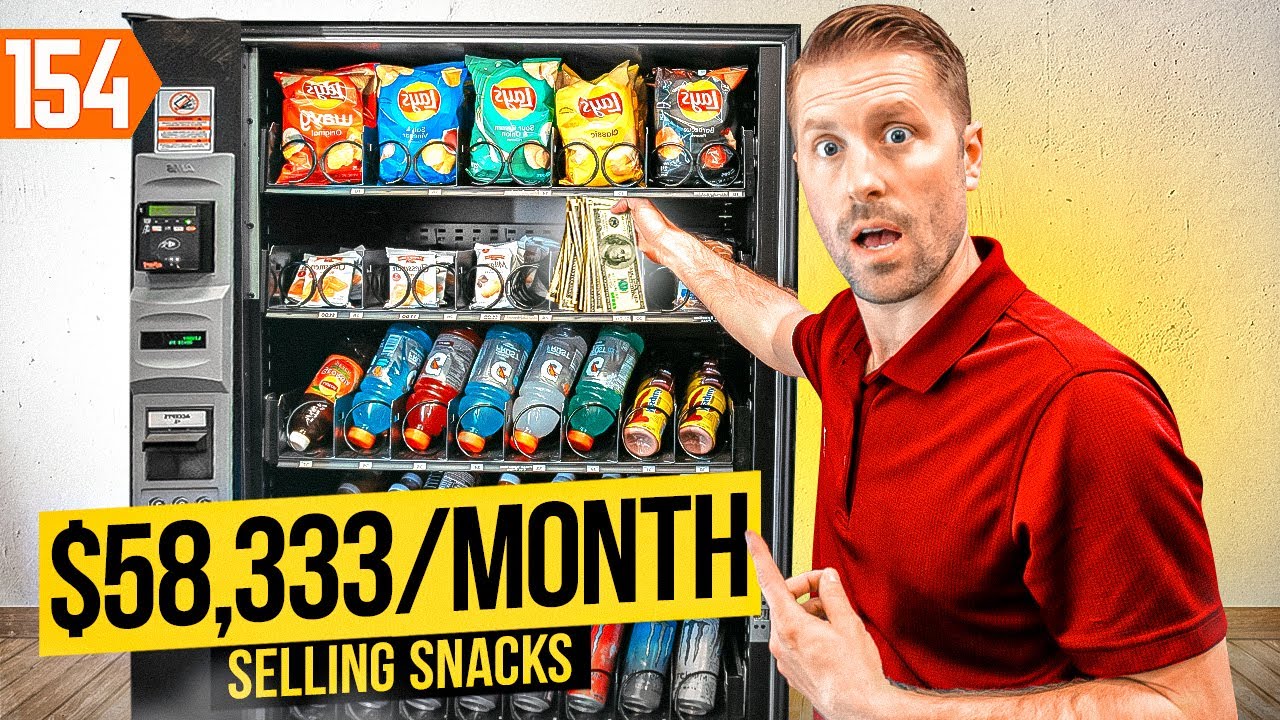
Illustrative Image (Source: Google Search)
- Finishing
– Coating and Painting: To enhance durability and aesthetics, machines are coated or painted. This process may include powder coating or electroplating, which protects against corrosion.
– Final Assembly: After finishing, all parts undergo final assembly. This includes the installation of electronic systems, wiring, and user interfaces.
Quality Assurance Measures
To ensure that the manufacturing processes yield high-quality products, various quality assurance measures are implemented:
-
International Standards
– ISO 9001: This standard outlines the requirements for a quality management system (QMS). Suppliers adhering to ISO 9001 demonstrate a commitment to quality and continuous improvement.
– CE Marking: For machines sold in Europe, CE marking indicates compliance with EU safety, health, and environmental protection standards. -
Industry-Specific Standards
– API Standards: For vending machines that dispense specific products (e.g., pharmaceuticals), compliance with API (American Petroleum Institute) standards may be necessary.
– Local Regulations: Understanding and complying with local regulations in the regions of operation (e.g., the UAE or South America) is crucial for market entry. -
Quality Control Checkpoints
– Incoming Quality Control (IQC): Inspects raw materials before production begins to ensure they meet quality specifications.
– In-Process Quality Control (IPQC): Monitors processes during manufacturing to identify and rectify issues in real-time.
– Final Quality Control (FQC): Conducts comprehensive testing of the finished machines to ensure they operate as intended and meet all quality standards. -
Common Testing Methods
– Performance Testing: Machines are tested for functionality, including payment processing, product dispensing, and user interface responsiveness.
– Durability Testing: Machines undergo stress tests to assess their ability to withstand different environmental conditions (e.g., heat, humidity).
– Safety Testing: Ensures compliance with electrical safety standards and verifies that all components function safely.
Verifying Supplier Quality Control
B2B buyers should adopt a proactive approach to verify the quality control processes of their suppliers:
-
Supplier Audits
– Conduct regular audits of potential suppliers to assess their manufacturing processes, quality control measures, and compliance with international standards.
– Buyers can use third-party audit firms to provide an unbiased evaluation. -
Quality Reports
– Request detailed quality reports that outline the results of IQC, IPQC, and FQC processes. This documentation can provide insight into the supplier’s commitment to quality.
– Reports should also include records of any non-conformities and corrective actions taken. -
Third-Party Inspections
– Engage third-party inspection services to evaluate the machines before shipment. This step ensures that the products meet specified standards and are free from defects.
– Consider using internationally recognized inspection firms for added credibility.
Quality Control and Certification Nuances for International Buyers
International buyers, particularly from diverse regions, should be aware of the following nuances in quality control and certification:
-
Cultural and Regulatory Differences
– Understand that quality standards and regulations may vary significantly between regions. Familiarity with local regulations in Africa, South America, the Middle East, and Europe is essential for compliance and market acceptance.
– Engage local experts or consultants who can provide insights into regional standards and practices. -
Language and Communication Barriers
– Ensure that all quality documentation is available in a language understood by the buyer’s team. Miscommunication can lead to misunderstandings regarding quality expectations.
– Establish clear lines of communication with suppliers to facilitate ongoing dialogue about quality issues and resolutions. -
Building Long-Term Relationships
– Establishing long-term relationships with suppliers can lead to improved quality assurance. Suppliers that understand your specific needs are more likely to prioritize quality in their processes.
– Regular feedback and collaboration on quality improvement initiatives can enhance the overall product quality.
By understanding these manufacturing processes and quality assurance measures, B2B buyers can make informed decisions when sourcing vending machines for purchase routes, ensuring they select reliable suppliers who adhere to high-quality standards.
Related Video: Business English Vocabulary : VV 47 – Manufacturing & Production Process (1) | English Vocabulary
Comprehensive Cost and Pricing Analysis for purchase vending machine route Sourcing
The cost structure for purchasing a vending machine route involves multiple components that B2B buyers must carefully consider. Understanding these costs can lead to more informed purchasing decisions and better negotiation outcomes.
Cost Components
-
Materials: The primary costs involve the vending machines themselves, which can vary significantly based on brand, features, and technology (e.g., cashless payment systems). Additionally, the products stocked in the machines will contribute to the overall material costs.
-
Labor: This encompasses both direct labor costs for installation and maintenance, as well as indirect costs associated with training staff to manage the vending machines. Depending on the complexity of the machines and their locations, labor costs can fluctuate.
-
Manufacturing Overhead: This includes costs related to the production of vending machines such as utilities, rent for manufacturing facilities, and equipment depreciation. Buyers should consider how these costs may affect the final price of the machines.
-
Tooling: Customization often requires specialized tools for production, which can increase costs. If buyers are looking for bespoke machines or specific features, they should account for these additional expenses.
-
Quality Control (QC): Ensuring that vending machines meet certain standards may involve additional testing and inspections, which can impact overall costs. Buyers should inquire about the QC processes of suppliers to ensure product reliability.
-
Logistics: Shipping and handling costs are critical, especially for international buyers. The distance from the manufacturing facility to the destination and any import tariffs or duties can significantly influence total costs.
- Margin: Suppliers will typically include a profit margin in their pricing, which can vary based on competition, market demand, and exclusivity of the product.
Price Influencers
Several factors influence the pricing of vending machine routes:
-
Volume/MOQ (Minimum Order Quantity): Larger orders often lead to better pricing due to economies of scale. Buyers should evaluate their demand to maximize potential savings.
-
Specifications/Customization: Custom features will generally increase costs. Buyers should assess whether these features are essential or if standard models would suffice.
-
Materials: The quality and type of materials used in vending machines can significantly affect pricing. Higher-quality materials may lead to better durability but at a higher upfront cost.
-
Quality Certifications: Machines that comply with international quality standards may cost more but can provide reassurance regarding their reliability and safety.
-
Supplier Factors: The reputation and reliability of suppliers can influence pricing. Established suppliers may charge a premium, but they often provide better service and warranty options.
-
Incoterms: Understanding the shipping terms and responsibilities can affect the total cost. Buyers should clarify who is responsible for shipping and insurance to avoid unexpected expenses.
Buyer Tips
-
Negotiation: Engage in negotiations with suppliers to explore volume discounts or flexible payment terms. Building relationships with suppliers can also lead to better pricing in the long term.
-
Cost-Efficiency: Look beyond the initial purchase price. Consider the Total Cost of Ownership (TCO), which includes maintenance, operational costs, and potential revenue generation from the machines.
-
Pricing Nuances: International B2B buyers should be aware of currency fluctuations, import taxes, and shipping costs that can affect the overall pricing landscape. Buyers from Africa, South America, the Middle East, and Europe (including the UAE and Australia) should factor these elements into their purchasing strategy.
Disclaimer
Prices and costs mentioned are indicative and can vary based on market conditions, supplier negotiations, and specific buyer requirements. Always conduct thorough market research and supplier evaluations to obtain the most accurate and relevant pricing information.
Spotlight on Potential purchase vending machine route Manufacturers and Suppliers
This section offers a look at a few manufacturers active in the ‘purchase vending machine route’ market. This is a representative sample for illustrative purposes; B2B buyers must conduct their own extensive due diligence before any engagement. Information is synthesized from public sources and general industry knowledge.
Essential Technical Properties and Trade Terminology for purchase vending machine route
Key Technical Properties for Vending Machine Routes
When considering the purchase of vending machine routes, international B2B buyers should be aware of several critical technical properties that can influence performance, reliability, and profitability.
-
Material Grade
– The construction materials of vending machines significantly affect durability and maintenance needs. Common materials include stainless steel, plastic, and tempered glass. Stainless steel is preferred for its corrosion resistance and strength, making it ideal for outdoor placements. Buyers should assess the material grade to ensure it meets local environmental conditions. -
Capacity
– Capacity refers to the number of products a vending machine can hold. This varies widely among models, impacting inventory turnover and profit margins. A higher capacity machine can reduce the frequency of restocking, which is essential for maintaining service efficiency. Buyers should evaluate their product offerings to choose a machine that matches their expected sales volume. -
Power Consumption
– Energy efficiency is crucial for operating costs. Vending machines with lower power consumption can lead to significant savings over time, especially in regions with high electricity costs. Look for machines that are energy star-rated or designed with energy-saving features. This not only benefits the bottom line but also aligns with sustainability goals. -
User Interface
– The design and functionality of the user interface can greatly affect customer experience. Touchscreen interfaces, for example, offer a more interactive experience and can display nutritional information or promotions. Buyers should consider the target market’s preferences and the need for accessibility features. -
Payment Options
– Modern vending machines should support multiple payment methods, including cash, credit/debit cards, and mobile payments. Flexibility in payment options can increase sales by catering to a broader customer base. Ensure that the chosen machine complies with local payment processing standards. -
Connectivity Features
– Many vending machines now come equipped with IoT capabilities, allowing for real-time inventory tracking and remote management. This connectivity can enhance operational efficiency by providing data on sales trends and machine status. Buyers should assess the technology options available and their integration with existing systems.
Common Trade Terminology
Understanding industry jargon is essential for effective communication and negotiations in the vending machine market.
-
OEM (Original Equipment Manufacturer)
– This term refers to companies that produce parts or equipment that may be marketed by another manufacturer. In the context of vending machines, it’s important to identify OEMs for reliable sourcing of components and maintenance support. -
MOQ (Minimum Order Quantity)
– MOQ indicates the smallest quantity of a product that a supplier is willing to sell. For vending machines, understanding MOQ is crucial for budgeting and inventory management. Suppliers with lower MOQs can provide flexibility for startups or smaller businesses. -
RFQ (Request for Quotation)
– An RFQ is a document issued by a buyer to solicit price quotes from suppliers for specific products or services. In the vending machine industry, submitting an RFQ can help buyers compare prices and terms from multiple vendors, facilitating better decision-making. -
Incoterms (International Commercial Terms)
– These are pre-defined commercial terms published by the International Chamber of Commerce (ICC) that outline the responsibilities of buyers and sellers regarding shipping, insurance, and tariffs. Familiarity with Incoterms helps buyers negotiate delivery and cost terms effectively. -
Lead Time
– This term refers to the time it takes from placing an order to receiving the product. In the vending machine industry, lead time can vary based on customization and supply chain factors. Understanding lead time is critical for planning inventory and ensuring timely operations. -
Warranty Period
– The warranty period is the timeframe during which a manufacturer is liable for defects or issues with the product. Buyers should carefully review warranty terms to protect their investment and ensure they are covered for maintenance or replacement costs.
By familiarizing themselves with these technical properties and trade terminologies, international B2B buyers can make informed decisions when purchasing vending machine routes, optimizing their operations and enhancing profitability.
Navigating Market Dynamics, Sourcing Trends, and Sustainability in the purchase vending machine route Sector
Market Overview & Key Trends
The purchase vending machine route sector is experiencing notable transformation driven by technological advancements and shifting consumer preferences. As urbanization continues to rise, particularly in regions like Africa and South America, the demand for convenient and accessible consumer goods is increasing. This trend is being accelerated by the proliferation of smartphones, which facilitate cashless payments and enable real-time inventory management.
One significant trend is the integration of IoT (Internet of Things) technology into vending machines. This allows for remote monitoring and management, enhancing operational efficiency and reducing downtime. B2B buyers are increasingly seeking suppliers who offer machines equipped with smart technology, enabling predictive maintenance and data analytics for better decision-making.
Moreover, sustainability is becoming a critical factor in purchasing decisions. Vending operators are expected to prioritize suppliers who align with eco-friendly practices, such as using recyclable materials and energy-efficient machines. This trend is particularly pronounced in Europe and the Middle East, where regulatory frameworks are pushing for greener initiatives.
Finally, the rise of personalized vending experiences, driven by AI and data analytics, is reshaping the market. Machines that can adapt to local preferences or offer tailored product suggestions are gaining traction, presenting opportunities for B2B buyers to invest in innovative solutions that meet evolving consumer demands.
Sustainability & Ethical Sourcing in B2B
As the emphasis on sustainability intensifies, international B2B buyers in the purchase vending machine route sector must consider the environmental impact of their sourcing decisions. The production and operation of vending machines can contribute to significant waste and energy consumption. Therefore, ethical sourcing practices are crucial in mitigating these effects.
B2B buyers should prioritize suppliers who utilize sustainable materials in their vending machine construction, such as recycled plastics and metals. Moreover, machines designed for energy efficiency can significantly reduce carbon footprints. Certifications such as ISO 14001 (Environmental Management) and Energy Star can help identify suppliers committed to sustainable practices.
Additionally, the importance of ethical supply chains cannot be overstated. Ensuring that materials are sourced responsibly, with fair labor practices and minimal environmental impact, is becoming a prerequisite for many buyers. This approach not only enhances brand reputation but also aligns with the values of increasingly eco-conscious consumers.
Investing in vending machines that adhere to these sustainability standards not only satisfies regulatory compliance but also positions businesses as leaders in the transition toward a more sustainable economy.
Brief Evolution/History
The vending machine sector has evolved significantly since its inception in the late 19th century. Originally designed to dispense simple items like postcards and chewing gum, the industry has transformed into a sophisticated channel for a diverse range of products.
In the late 20th century, the introduction of electronic payment systems revolutionized the vending experience, paving the way for cashless transactions. The 21st century has seen the rise of smart vending machines equipped with IoT capabilities, allowing for real-time inventory tracking and consumer interaction. This evolution has been particularly relevant in emerging markets, where the demand for convenience and accessibility drives innovation in the vending machine route sector.
As international B2B buyers navigate this dynamic landscape, understanding these historical shifts can provide valuable insights into current trends and future opportunities.
Related Video: Is global trade transforming? | Counting the Cost
Frequently Asked Questions (FAQs) for B2B Buyers of purchase vending machine route
-
What criteria should I use to vet suppliers for vending machine routes?
When vetting suppliers, prioritize their experience in the vending machine industry, customer testimonials, and their track record in international trade. Verify their financial stability and business licenses to ensure compliance with local regulations. Request product samples to assess quality and consider their ability to provide customization options. Additionally, inquire about their logistics capabilities, including shipping and handling, to ensure they can meet your specific needs. -
Can I customize vending machines for my market?
Most suppliers offer customization options tailored to your specific market needs. This can include branding, product selection, and machine features. Discuss your requirements with potential suppliers early in the negotiation process to understand their capabilities. Keep in mind that extensive customization may lead to longer lead times and higher minimum order quantities (MOQs), so plan accordingly. -
What are the typical minimum order quantities (MOQs) and lead times?
MOQs for vending machines can vary significantly by supplier and product type, ranging from a few units to several dozen. It’s crucial to clarify MOQs during initial discussions to ensure they align with your budget and business strategy. Lead times can also differ based on customization and the supplier’s production capacity, typically ranging from 4 to 12 weeks. Always confirm these details upfront to avoid unexpected delays. -
What payment methods are typically accepted in international trade?
Common payment methods include wire transfers, letters of credit, and payment platforms like PayPal. For large transactions, using a letter of credit can provide security for both parties, ensuring that funds are only released upon meeting agreed-upon conditions. Discuss payment terms with your supplier, including deposits and final payments, to establish a clear financial arrangement that protects your interests. -
What quality assurance measures should I expect from suppliers?
Reputable suppliers should have robust quality assurance processes in place, including certifications such as ISO 9001 or industry-specific standards. Request documentation of these certifications and inquire about their quality control procedures. Regular inspections and testing of the machines before shipment should be standard practice. Establishing these quality benchmarks will help mitigate risks and ensure you receive reliable products.
-
How can I manage logistics effectively when sourcing vending machines?
Effective logistics management involves understanding shipping options, customs regulations, and local delivery methods. Collaborate with your supplier to determine the best shipping method (air, sea, or land) based on cost and urgency. Familiarize yourself with import duties and taxes that may apply in your country. Working with a freight forwarder can also simplify the logistics process, ensuring timely and efficient delivery. -
What should I do if I encounter disputes with my supplier?
Establish clear communication and documentation throughout your transactions to minimize disputes. If issues arise, address them directly with the supplier as soon as possible. Refer to the terms outlined in your contract regarding dispute resolution procedures, which may include mediation or arbitration. It’s wise to keep a record of all correspondence and agreements to support your case if the dispute escalates. -
Are there specific certifications I should look for in vending machines?
Yes, specific certifications can indicate the quality and safety of vending machines. Look for CE marking in Europe, UL certification in the USA, or other regional standards relevant to your market. These certifications demonstrate compliance with safety regulations and quality standards. Ensure your supplier can provide documentation for these certifications, as they will be essential for importation and resale in your local market.
Strategic Sourcing Conclusion and Outlook for purchase vending machine route
In conclusion, strategic sourcing in the purchase vending machine route presents significant opportunities for international B2B buyers across Africa, South America, the Middle East, and Europe. By focusing on cost efficiency, supplier reliability, and market adaptability, businesses can enhance their operational effectiveness and customer satisfaction. The integration of technology in vending solutions, such as cashless payments and data analytics, offers a competitive edge, ensuring that vending machines meet evolving consumer preferences.
Buyers are encouraged to engage with suppliers who demonstrate a commitment to sustainability and innovation, as these factors are increasingly influencing purchasing decisions. Furthermore, establishing strong relationships with local distributors can facilitate smoother market entry and enhance service levels.
As the global market for vending machines continues to expand, now is the time for B2B buyers to leverage strategic sourcing initiatives. By proactively seeking partnerships and investing in advanced vending solutions, businesses can position themselves for success in a rapidly changing landscape. Embrace this opportunity to redefine your vending operations and meet the demands of modern consumers.