Master the Market: Opi All Your Dreams in Vending Machines
Guide to Opi All Your Dreams In Vending Machines
- Introduction: Navigating the Global Market for opi all your dreams in vending machines
- Understanding opi all your dreams in vending machines Types and Variations
- Key Industrial Applications of opi all your dreams in vending machines
- Strategic Material Selection Guide for opi all your dreams in vending machines
- In-depth Look: Manufacturing Processes and Quality Assurance for opi all your dreams in vending machines
- Comprehensive Cost and Pricing Analysis for opi all your dreams in vending machines Sourcing
- Spotlight on Potential opi all your dreams in vending machines Manufacturers and Suppliers
- Essential Technical Properties and Trade Terminology for opi all your dreams in vending machines
- Navigating Market Dynamics, Sourcing Trends, and Sustainability in the opi all your dreams in vending machines Sector
- Frequently Asked Questions (FAQs) for B2B Buyers of opi all your dreams in vending machines
- Strategic Sourcing Conclusion and Outlook for opi all your dreams in vending machines
Introduction: Navigating the Global Market for opi all your dreams in vending machines
In the rapidly evolving landscape of global commerce, the concept of “opi all your dreams in vending machines” stands out as a unique and compelling opportunity for B2B buyers. These innovative vending solutions not only cater to consumer convenience but also open avenues for businesses to diversify their offerings and enhance customer engagement. As the demand for automated retail solutions grows, understanding the intricacies of this market becomes crucial for informed sourcing decisions.
This comprehensive guide delves into the multifaceted world of vending machines tailored for diverse products and experiences. It covers essential aspects such as types of vending machines, materials used in manufacturing, quality control processes, and top suppliers in the industry. Furthermore, it provides insights into cost structures and an overview of the market trends that are shaping this dynamic sector.
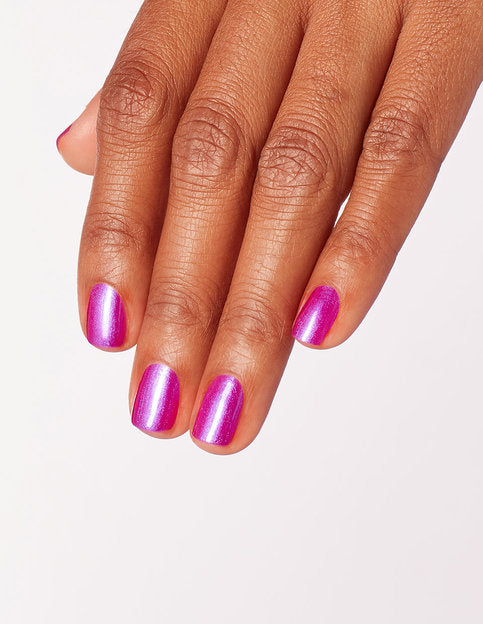
Illustrative Image (Source: Google Search)
For international B2B buyers, particularly those from Africa, South America, the Middle East, and Europe—including key markets like Spain and Italy—this guide serves as an invaluable resource. By addressing frequently asked questions and highlighting actionable insights, it empowers businesses to make strategic decisions that align with their operational goals and market demands. Embrace the future of retail with confidence, and unlock the potential of vending solutions that can truly fulfill your business aspirations.
Understanding opi all your dreams in vending machines Types and Variations
Type Name | Key Distinguishing Features | Primary B2B Applications | Brief Pros & Cons for Buyers |
---|---|---|---|
Traditional Snack Vending | Dispenses packaged snacks and beverages | Office break rooms, schools, hospitals | Pros: Low maintenance, familiar to users. Cons: Limited selection, may require frequent restocking. |
Healthy Options Vending | Focuses on nutritious snacks and beverages | Gyms, wellness centers, corporate offices | Pros: Appeals to health-conscious consumers. Cons: Higher cost, may have slower sales. |
Customized Product Vending | Allows personalization of items via touchscreen | Events, trade shows, retail environments | Pros: Engages customers with unique offerings. Cons: Higher initial investment, requires tech support. |
Cashless Payment Vending | Operates exclusively with digital payment methods | Urban areas, tech-savvy locations | Pros: Fast transactions, reduces cash handling. Cons: May alienate non-tech users, requires reliable internet. |
Eco-Friendly Vending | Uses sustainable materials and offers green products | Eco-conscious businesses, schools | Pros: Enhances brand image, appeals to environmentally aware consumers. Cons: Potentially higher costs, limited product range. |
Traditional Snack Vending
Traditional snack vending machines are the most recognizable type, typically offering a range of packaged snacks and beverages. These machines are ideal for high-traffic areas such as office break rooms, schools, and hospitals, where convenience is key. B2B buyers should consider the machine’s capacity and the frequency of restocking, as these factors can impact operational efficiency. Although low maintenance is a significant advantage, buyers should be aware that the limited selection may not meet the diverse preferences of all consumers.
Healthy Options Vending
These machines cater to the growing demand for healthier eating habits by offering nutritious snacks and beverages. They are particularly suitable for environments like gyms, wellness centers, and corporate offices where health is a priority. B2B buyers should evaluate the product sourcing and pricing, as healthy options often come at a higher cost compared to traditional snacks. While they can attract health-conscious consumers, the initial investment may be higher, and sales might be slower if not strategically placed.
Customized Product Vending
Customized product vending machines allow consumers to personalize their purchases through interactive touchscreens. This type is increasingly popular at events, trade shows, and retail environments, where unique offerings can enhance customer engagement. B2B buyers must consider the technological requirements and potential higher initial investment, as well as the ongoing need for technical support. While these machines can provide a competitive edge, they also require careful planning to ensure that the customization options resonate with the target audience.
Cashless Payment Vending
Cashless payment vending machines are designed for digital transactions only, making them ideal for urban areas and locations frequented by tech-savvy consumers. B2B buyers should assess the reliability of the internet connection and the payment systems used, as these factors can significantly affect customer experience. The speed of transactions and reduced cash handling are notable advantages, but buyers must also consider the risk of alienating customers who prefer cash payments.
Eco-Friendly Vending
Eco-friendly vending machines prioritize sustainability by using recyclable materials and offering green product options. These machines are well-suited for eco-conscious businesses and educational institutions that aim to promote environmental responsibility. When considering an eco-friendly vending option, B2B buyers should evaluate the cost implications and the range of products available. While these machines can enhance a brand’s image and attract environmentally aware consumers, they may also come with a higher price point and limited product selection.
Related Video: Large Language Models (LLMs) – Everything You NEED To Know
Key Industrial Applications of opi all your dreams in vending machines
Industry/Sector | Specific Application of opi all your dreams in vending machines | Value/Benefit for the Business | Key Sourcing Considerations for this Application |
---|---|---|---|
Retail | Automated product dispensing for consumer goods | Increased sales volume, reduced labor costs | Product compatibility, vending machine reliability |
Hospitality | In-room vending solutions for hotels and resorts | Enhanced guest experience, 24/7 service availability | Space constraints, product variety, payment options |
Healthcare | Medicine and personal care product dispensers | Improved medication adherence, reduced pharmacy workload | Compliance with health regulations, secure storage |
Education | Snack and beverage vending in schools and universities | Promotes healthy eating, convenient access for students | Nutritional standards, age-appropriate products |
Transportation | Vending solutions at airports and train stations | Captures impulse purchases, caters to travelers’ needs | Fast service, payment flexibility, product freshness |
Retail
In the retail sector, ‘opi all your dreams in vending machines’ can revolutionize how consumer goods are dispensed. Automated product dispensing allows businesses to increase sales volume while significantly reducing labor costs. By offering a diverse range of products, including snacks, beverages, and personal care items, retailers can cater to a wider audience. International buyers, especially from Africa and South America, should consider product compatibility and the reliability of vending machines to ensure continuous operation in diverse environments.
Hospitality
In the hospitality industry, in-room vending solutions provide guests with a convenient way to access snacks and beverages at any time. This 24/7 service enhances the overall guest experience, allowing hotels and resorts to differentiate themselves in a competitive market. For buyers in Europe, particularly in Spain and Italy, considerations such as space constraints and the variety of products offered are critical to meet diverse guest preferences and dietary requirements.
Healthcare
Within healthcare, ‘opi all your dreams in vending machines’ can be utilized for dispensing medicine and personal care products. This application improves medication adherence by providing patients with easy access to their prescriptions and essential health items. It also reduces the workload on pharmacy staff, allowing them to focus on patient care. Buyers from the Middle East must ensure compliance with health regulations and consider secure storage options to protect sensitive products.
Education
In educational institutions, vending machines can offer healthy snacks and beverages to students, promoting better eating habits. This solution provides convenient access to nutritious options, especially in schools and universities where time is limited. International buyers should focus on nutritional standards and ensure that the products offered are age-appropriate, catering to the health and wellness of students across diverse regions.
Transportation
Vending solutions at airports and train stations cater to travelers’ needs by providing quick access to food and beverages. This not only captures impulse purchases but also enhances the travel experience by addressing the demand for convenience. Buyers in these sectors should prioritize fast service, payment flexibility, and product freshness to meet the expectations of a diverse, international clientele.
Related Video: Lab Tools and Equipment – Know your glassware and become an expert Chemist! | Chemistry
Strategic Material Selection Guide for opi all your dreams in vending machines
When selecting materials for “opi all your dreams in vending machines,” it is crucial to consider the specific requirements of the application, including durability, cost, and compatibility with various media. Below is an analysis of four common materials used in vending machines, focusing on their properties, advantages, disadvantages, and considerations for international B2B buyers.
1. Stainless Steel
Key Properties:
Stainless steel is known for its excellent corrosion resistance, making it suitable for environments where moisture and chemicals are present. It typically has a high-temperature rating and can withstand significant pressure.
Pros & Cons:
Stainless steel is highly durable and easy to clean, which is vital for maintaining hygiene in vending machines. However, it tends to be more expensive than other materials and may require specialized manufacturing processes.
Impact on Application:
This material is compatible with a wide range of media, including beverages and snacks, ensuring that it can handle various products without degradation.
Considerations for International Buyers:
Buyers should ensure compliance with international standards such as ASTM and DIN. In regions like Europe, stainless steel grades (e.g., AISI 304 or 316) are preferred for their corrosion resistance.
2. Aluminum
Key Properties:
Aluminum is lightweight and has good corrosion resistance, although it is less robust than stainless steel. It can handle moderate temperatures and pressures.
Pros & Cons:
Aluminum is cost-effective and easy to machine, making it a popular choice for many vending machine components. However, its lower strength compared to stainless steel can be a limitation in high-stress applications.
Impact on Application:
Aluminum is suitable for dry goods and beverages but may not be ideal for highly acidic or alkaline products, which can corrode the material over time.
Considerations for International Buyers:
When sourcing aluminum, buyers should be aware of specific grades and their properties, particularly in regions like Africa and South America, where local standards may vary.
3. Polycarbonate
Key Properties:
Polycarbonate is a strong, transparent thermoplastic that offers high impact resistance and good optical clarity. It is also lightweight and can withstand moderate temperatures.
Pros & Cons:
The material is excellent for visibility and protection of products, making it ideal for display panels in vending machines. However, it can be more susceptible to scratches and UV degradation over time.
Impact on Application:
Polycarbonate is best suited for non-food applications or as a protective cover for food items, as it does not interact with most media.
Considerations for International Buyers:
Buyers should check for compliance with food safety standards, especially in Europe, where regulations can be stringent regarding materials in contact with food.
4. Carbon Steel
Key Properties:
Carbon steel is known for its high strength and durability, making it suitable for structural components of vending machines. However, it is prone to corrosion without proper coatings.
Pros & Cons:
It is one of the most cost-effective materials available, offering excellent performance in structural applications. The downside is its susceptibility to rust, which necessitates protective coatings or treatments.
Impact on Application:
Carbon steel is suitable for non-corrosive environments and can be used for frames or supports but is not ideal for components that come into direct contact with food or beverages.
Considerations for International Buyers:
Buyers should ensure that any carbon steel components are properly coated to prevent corrosion, especially in humid climates found in parts of Africa and the Middle East.
Summary Table
Material | Typical Use Case for opi all your dreams in vending machines | Key Advantage | Key Disadvantage/Limitation | Relative Cost (Low/Med/High) |
---|---|---|---|---|
Stainless Steel | Structural and exterior components for durability | Excellent corrosion resistance | Higher cost, requires special processing | High |
Aluminum | Lightweight components, display panels | Cost-effective, easy to machine | Lower strength than stainless steel | Med |
Polycarbonate | Protective covers, display cases | High impact resistance, visibility | Susceptible to scratches and UV damage | Med |
Carbon Steel | Structural supports, frames | Cost-effective, high strength | Prone to corrosion, needs protective coating | Low |
This guide should assist international B2B buyers in making informed decisions regarding material selection for vending machines, taking into account the specific needs of their markets and compliance with local standards.
In-depth Look: Manufacturing Processes and Quality Assurance for opi all your dreams in vending machines
Manufacturing Processes for Vending Machines
When considering the manufacturing of vending machines, particularly those themed around “opi all your dreams,” it’s essential for B2B buyers to understand the various stages involved. The manufacturing process can be broken down into four main stages: material preparation, forming, assembly, and finishing.
Material Preparation
The first step involves selecting the right materials, typically metals like stainless steel for the outer casing, along with plastics and electronic components. Buyers should ensure that suppliers use high-quality materials that can withstand the wear and tear associated with vending machine use.
- Key Considerations:
- Source materials that are durable and resistant to corrosion, especially for machines placed in outdoor settings.
- Verify that the materials meet international standards (e.g., RoHS for electronics) to avoid future compliance issues.
Forming
In this stage, the raw materials are shaped into the necessary components. Techniques such as laser cutting, bending, and molding are commonly used.
- Key Techniques:
- Laser Cutting: Provides precision in cutting metal sheets to create the machine’s structure.
- Injection Molding: Used for producing plastic parts like buttons and display panels.
B2B buyers should inquire about the machinery and technology used by suppliers to ensure they can produce parts to exact specifications.
Assembly
Once components are formed, they are assembled into the final product. This stage often involves both manual labor and automated processes.
- Key Points:
- Confirm that assembly is conducted in a clean, controlled environment to prevent contamination.
- Check if the assembly line is equipped with robotics for tasks requiring high precision, which can enhance efficiency.
Finishing
The final stage involves applying coatings, conducting tests, and ensuring that the vending machines meet quality standards. This may include painting, applying decals, and ensuring all electrical components function properly.
- Important Aspects:
- Ensure that finishing processes include quality checks for aesthetic and functional aspects.
- Ask about the types of paints and coatings used to guarantee they are environmentally friendly and safe.
Quality Assurance for Vending Machines
Quality assurance (QA) is critical in the manufacturing of vending machines to ensure reliability and customer satisfaction. B2B buyers must be aware of international standards and industry-specific certifications that suppliers should adhere to.
International Standards
- ISO 9001: This is a widely recognized standard for quality management systems. Suppliers who are ISO 9001 certified demonstrate their commitment to quality and continuous improvement.
- CE Marking: Essential for products sold in the European Economic Area, the CE mark indicates that the product meets EU safety, health, and environmental requirements.
Industry-Specific Certifications
- API (American Petroleum Institute): If vending machines dispense fuel or related products, API certification ensures they meet safety and performance standards.
- UL Certification: For electrical components, UL certification indicates that the product has been tested for safety.
Quality Control Checkpoints
Quality control (QC) is implemented at various stages of the manufacturing process.
- Incoming Quality Control (IQC): This involves inspecting raw materials and components upon arrival to ensure they meet specified standards.
- In-Process Quality Control (IPQC): Conducted during the manufacturing process, this step ensures that each phase meets quality standards before moving to the next.
- Final Quality Control (FQC): Before shipment, a final inspection checks that the complete machine functions properly and adheres to all specifications.
Common Testing Methods
B2B buyers should be familiar with common testing methods used to ensure the quality and reliability of vending machines, including:
- Functional Testing: Ensures all components, including payment systems and dispensers, work correctly.
- Stress Testing: Checks the machine’s performance under various conditions to simulate real-world use.
- Safety Testing: Ensures that electrical and mechanical components meet safety regulations.
Verifying Supplier Quality Control
To ensure that suppliers maintain high-quality standards, B2B buyers should consider the following verification methods:
- Supplier Audits: Conduct regular audits of suppliers to assess their manufacturing processes and quality control measures.
- Quality Reports: Request detailed reports on quality control processes and outcomes from suppliers.
- Third-Party Inspections: Utilize independent inspection services to evaluate the quality of goods before shipment.
Navigating Quality Control for International Buyers
For international B2B buyers, particularly from regions like Africa, South America, the Middle East, and Europe, understanding the nuances of quality control is crucial.
- Documentation: Ensure that all quality certificates and inspection reports are available in a language you understand, and confirm their validity.
- Cultural Sensitivity: Be aware of cultural differences that may affect communication and expectations regarding quality standards.
- Logistics Considerations: Understand the shipping and handling processes, as these can impact product quality during transportation.
By being well-informed about the manufacturing processes and quality assurance measures for vending machines, B2B buyers can make educated decisions, ensuring they source reliable and compliant products that meet their business needs.
Related Video: Amazing scenes。Top 6 Most Popular Factory Manufacturing Videos in China
Comprehensive Cost and Pricing Analysis for opi all your dreams in vending machines Sourcing
Understanding the Cost Structure for OPI All Your Dreams in Vending Machines
In the B2B landscape of vending machine sourcing, particularly for the “OPI All Your Dreams” product line, understanding the cost structure is paramount. The total cost of a vending machine encompasses several critical components:
-
Materials: This includes the raw materials for the machine and the products it dispenses. High-quality materials will naturally increase costs but are essential for durability and customer satisfaction.
-
Labor: Labor costs encompass both direct labor for manufacturing and indirect labor for administration and support. Countries with higher labor costs, such as those in Europe, may see a significant impact on overall pricing.
-
Manufacturing Overhead: This involves indirect costs associated with the production process, such as utilities, maintenance, and factory management. Efficient manufacturing processes can help reduce these overheads.
-
Tooling: The cost of molds and tools required for production can vary significantly based on the complexity of the machine design. Custom tooling for unique specifications often incurs higher costs.
-
Quality Control (QC): Implementing stringent QC measures is vital to ensure product reliability. This adds to the cost but is essential for maintaining brand reputation and customer trust.
-
Logistics: Shipping and handling costs vary widely based on the destination. Factors such as distance, transport mode, and shipping regulations can significantly affect pricing.
-
Margin: Suppliers typically add a profit margin to their total costs, which can vary based on market demand and competition.
Price Influencers in Vending Machine Sourcing
Several factors influence pricing for international B2B buyers when sourcing vending machines:
-
Volume/MOQ (Minimum Order Quantity): Larger orders typically yield better pricing due to economies of scale. Negotiating for a lower MOQ can help smaller buyers manage costs while still receiving competitive pricing.
-
Specifications/Customization: Custom features increase costs. Buyers should evaluate the necessity of customizations against their budget and market demand.
-
Materials and Quality Certifications: Higher quality materials and certifications (like ISO) can lead to increased costs but may enhance product reliability and marketability.
-
Supplier Factors: The reputation, reliability, and location of suppliers can affect pricing. Established suppliers may charge a premium but often provide better quality assurance.
-
Incoterms: Understanding the terms of trade is crucial. Incoterms dictate who is responsible for shipping, insurance, and tariffs, which can affect the total landed cost.
Buyer Tips for Cost Efficiency
International B2B buyers, especially from regions like Africa, South America, the Middle East, and Europe, should consider the following strategies:
-
Negotiation: Cultivating strong relationships with suppliers can lead to better pricing and terms. Don’t hesitate to negotiate volume discounts or extended payment terms.
-
Total Cost of Ownership (TCO): When evaluating suppliers, consider not just the purchase price but the TCO, which includes maintenance, repair, and operational costs over the machine’s lifespan.
-
Pricing Nuances: Be aware that pricing can fluctuate based on currency exchange rates, political stability, and local economic conditions. Staying informed about market trends can help in making timely purchasing decisions.
Conclusion
In summary, understanding the comprehensive cost structure and the various price influencers is essential for B2B buyers looking to source “OPI All Your Dreams” vending machines effectively. By employing strategic negotiation and considering the total cost of ownership, buyers can make informed decisions that optimize their investments. It is advisable to seek multiple quotes and conduct thorough due diligence to ensure competitiveness and quality in the sourcing process.
Disclaimer: Prices and costs mentioned in this analysis are indicative and may vary based on specific circumstances, including supplier negotiations, market conditions, and individual buyer requirements.
Spotlight on Potential opi all your dreams in vending machines Manufacturers and Suppliers
This section offers a look at a few manufacturers active in the ‘opi all your dreams in vending machines’ market. This is a representative sample for illustrative purposes; B2B buyers must conduct their own extensive due diligence before any engagement. Information is synthesized from public sources and general industry knowledge.
Essential Technical Properties and Trade Terminology for opi all your dreams in vending machines
Critical Technical Properties
-
Material Grade
The quality of materials used in vending machines significantly impacts their durability and functionality. Common materials include stainless steel for the outer casing and high-grade plastics for internal components. Choosing the right material grade ensures resistance to corrosion, wear, and environmental conditions, which is crucial for machines placed in diverse climates across Africa, South America, the Middle East, and Europe. -
Power Consumption
Energy efficiency is a vital specification for vending machines, particularly as businesses increasingly focus on sustainability. Understanding the power consumption of a vending machine helps in calculating operational costs and aligning with local energy regulations. Machines that consume less power not only reduce expenses but also appeal to environmentally conscious consumers. -
Temperature Control Range
For vending machines that dispense perishable items, maintaining the correct temperature is essential. The temperature control range specifies how low or high the machine can regulate temperatures to keep products fresh. This specification is particularly important for markets in warm climates, ensuring that products like beverages and snacks remain safe for consumption. -
Capacity and Size
The capacity of a vending machine, defined by the number of items it can hold, directly influences sales potential. Buyers should consider the size of the machine in relation to the intended placement location and expected foot traffic. A well-sized vending machine maximizes product turnover and profitability. -
User Interface and Payment Systems
The complexity and usability of the user interface are essential for customer satisfaction. Machines equipped with modern payment systems, including mobile payment options and contactless cards, cater to diverse consumer preferences. A straightforward interface enhances user experience, leading to increased sales.
Common Trade Terminology
-
OEM (Original Equipment Manufacturer)
This term refers to companies that produce parts and equipment that may be marketed by another manufacturer. Understanding OEM relationships is critical for B2B buyers as it affects product availability, quality control, and pricing structures. -
MOQ (Minimum Order Quantity)
MOQ is the smallest quantity of a product that a supplier is willing to sell. For international buyers, knowing the MOQ helps in budgeting and inventory management. It’s essential to negotiate this term to ensure it aligns with business needs and cash flow. -
RFQ (Request for Quotation)
An RFQ is a standard business process to invite suppliers to bid on specific products or services. For B2B buyers, issuing an RFQ can streamline procurement processes, allowing for comparison of prices and terms from multiple vendors, ensuring the best value. -
Incoterms (International Commercial Terms)
Incoterms are a series of pre-defined commercial terms published by the International Chamber of Commerce (ICC) that clarify the responsibilities of buyers and sellers in international transactions. Understanding these terms is crucial for B2B transactions to avoid disputes over shipping costs, insurance, and risk. -
Lead Time
This term refers to the amount of time from the placement of an order to the delivery of the product. Knowing the lead time is essential for planning inventory and ensuring that vending machines are operational during peak sales periods.
- Warranty
A warranty is a guarantee provided by the manufacturer regarding the condition of the product and the commitment to repair or replace it if necessary. For B2B buyers, understanding warranty terms is crucial for risk management and long-term operational planning, especially when investing in equipment like vending machines.
By grasping these technical properties and trade terms, international B2B buyers can make informed decisions, ensuring that their investments in vending machines are strategic and beneficial for their business operations.
Navigating Market Dynamics, Sourcing Trends, and Sustainability in the opi all your dreams in vending machines Sector
Market Overview & Key Trends
The vending machine sector, particularly focusing on the innovative concept of “opi all your dreams in vending machines,” is witnessing substantial growth driven by several global factors. The increasing demand for convenience in food and beverage consumption is leading to the proliferation of vending machines in urban areas across Africa, South America, the Middle East, and Europe. This trend is further fueled by advancements in technology, such as cashless payment systems, smart vending solutions, and AI integration, allowing for enhanced user experiences and operational efficiency.
In emerging markets, international B2B buyers are noticing a shift towards more personalized vending solutions, where machines are tailored to local tastes and preferences. For instance, in Europe, particularly in Spain and Italy, there is a growing inclination towards gourmet and health-conscious offerings. Additionally, the pandemic has accelerated the need for contactless vending options, prompting manufacturers to innovate rapidly. As a result, buyers should prioritize suppliers who are adaptable and can provide technologically advanced solutions that align with market demands.
Furthermore, sustainability is becoming a crucial driver in the vending machine industry. Buyers are increasingly seeking partnerships with manufacturers that prioritize eco-friendly practices, including energy-efficient machines and biodegradable packaging. Understanding these market dynamics will empower international buyers to make informed sourcing decisions that not only meet consumer demands but also align with broader environmental goals.
Sustainability & Ethical Sourcing in B2B
The environmental impact of vending machines is significant, given their energy consumption and waste generation. Therefore, sustainability is no longer just an option; it is a necessity for B2B buyers in this sector. Ethical sourcing practices are critical, as they not only minimize environmental footprints but also enhance brand reputation among increasingly conscious consumers.
Buyers should focus on suppliers who demonstrate commitment to sustainability through certifications such as ISO 14001 for environmental management and Fair Trade for ethical sourcing. Additionally, incorporating ‘green’ materials, such as recycled plastics and energy-efficient components, into vending machines can greatly reduce overall environmental impact.
Moreover, the shift towards circular economy principles is gaining traction, where machines are designed for longevity and recyclability. By prioritizing suppliers who adopt these practices, international buyers can ensure that their vending solutions are not only compliant with current regulations but also positioned to thrive in a future where sustainability is paramount.
Brief Evolution/History
The vending machine industry has evolved significantly from its inception in the late 19th century, originally offering simple items like postcards and gum. With technological advancements, the sector has transformed dramatically, introducing sophisticated machines capable of dispensing a diverse range of products, including fresh food and beverages.
In recent years, the integration of digital technology has further revolutionized the industry, enabling features such as remote monitoring, inventory management, and personalized marketing. This evolution reflects broader consumer trends towards convenience, customization, and sustainability, positioning vending machines as a key player in the modern retail landscape. For B2B buyers, understanding this historical context is essential for identifying reliable partners and innovative solutions that meet evolving market needs.
Related Video: Global Trade & Logistics – What is Global Trade?
Frequently Asked Questions (FAQs) for B2B Buyers of opi all your dreams in vending machines
-
What should I consider when vetting suppliers for ‘opi all your dreams in vending machines’?
When vetting suppliers, prioritize their experience in the vending machine industry, check their references, and assess their production capabilities. Look for certifications that indicate compliance with international standards, such as ISO. Additionally, evaluate their customer service responsiveness and after-sales support. Conducting a site visit, if feasible, can provide further assurance of their operational integrity and capacity. -
Can I customize the vending machines to fit my brand requirements?
Yes, most suppliers offer customization options for vending machines, including branding, size, and product selection. Be sure to communicate your specific requirements clearly and confirm the supplier’s ability to accommodate these requests. Discuss the customization process, timelines, and any additional costs involved to ensure alignment with your business goals. -
What are the minimum order quantities (MOQ) and lead times for purchasing?
MOQs can vary significantly among suppliers, often depending on the machine specifications and customization levels. Typically, you may encounter MOQs ranging from 10 to 50 units. Lead times also depend on the complexity of your order; standard machines may take 4-6 weeks, while customized units could take longer. Always confirm these details upfront to avoid disruptions in your supply chain. -
What payment terms are common in international B2B transactions?
Payment terms can vary, but common practices include upfront deposits (usually 30-50%), with the balance due upon delivery or before shipping. Letters of credit and escrow services are also popular for securing large transactions. Always negotiate terms that protect your interests while ensuring the supplier is comfortable with the arrangement. Be cautious of payment methods that lack recourse in case of disputes. -
How can I ensure quality assurance and compliance with certifications?
Request documentation that verifies the supplier’s quality management systems, such as ISO 9001 certification. Additionally, inquire about their quality control processes, including inspections and testing protocols. Regular audits or third-party inspections can also be beneficial. It’s wise to establish clear quality criteria in your contract to ensure that the delivered products meet your standards. -
What logistics considerations should I keep in mind when importing vending machines?
Logistics is critical in international trade. Ensure you understand the shipping options, estimated delivery times, and costs involved. Work with a freight forwarder experienced in handling machinery to navigate customs and tariffs effectively. Additionally, clarify the supplier’s responsibilities regarding shipping and insurance to mitigate risks during transit. -
How should I handle disputes with suppliers?
Establish a clear dispute resolution process in your contract, outlining steps such as mediation or arbitration before pursuing legal action. Document all communications and agreements meticulously, as this will help resolve misunderstandings. If issues arise, maintain open lines of communication with the supplier to seek amicable solutions, as many disputes can be resolved through dialogue. -
What are the best practices for maintaining ongoing supplier relationships?
Building strong relationships with suppliers involves regular communication, feedback, and collaboration on future projects. Schedule periodic reviews to discuss performance, address concerns, and explore new opportunities. Being transparent about your business needs and challenges fosters mutual trust, ensuring both parties can adapt and grow together in a competitive market.
Strategic Sourcing Conclusion and Outlook for opi all your dreams in vending machines
In the rapidly evolving landscape of vending machine solutions, strategic sourcing emerges as a critical element for international B2B buyers. By prioritizing quality suppliers, companies can ensure the delivery of innovative and reliable products that meet diverse consumer needs. Buyers from Africa, South America, the Middle East, and Europe should focus on building strong partnerships with manufacturers who prioritize sustainability and technology integration, thereby enhancing operational efficiency and customer satisfaction.
Key takeaways include:
- Market Adaptation: Understanding regional preferences and local market dynamics is essential for tailoring product offerings.
- Supplier Relationships: Developing long-term relationships with suppliers can yield better pricing, improved service, and collaborative innovation.
- Risk Management: Diversifying the supply chain mitigates risks associated with geopolitical uncertainties and fluctuating market conditions.
As you embark on your sourcing journey, consider leveraging data analytics and market research to refine your strategies. The future of vending solutions is bright, and by embracing strategic sourcing, you can position your business for success in this competitive sector. Take the next step: engage with key suppliers and explore innovative vending solutions that can transform your offerings and meet the demands of tomorrow’s consumers.
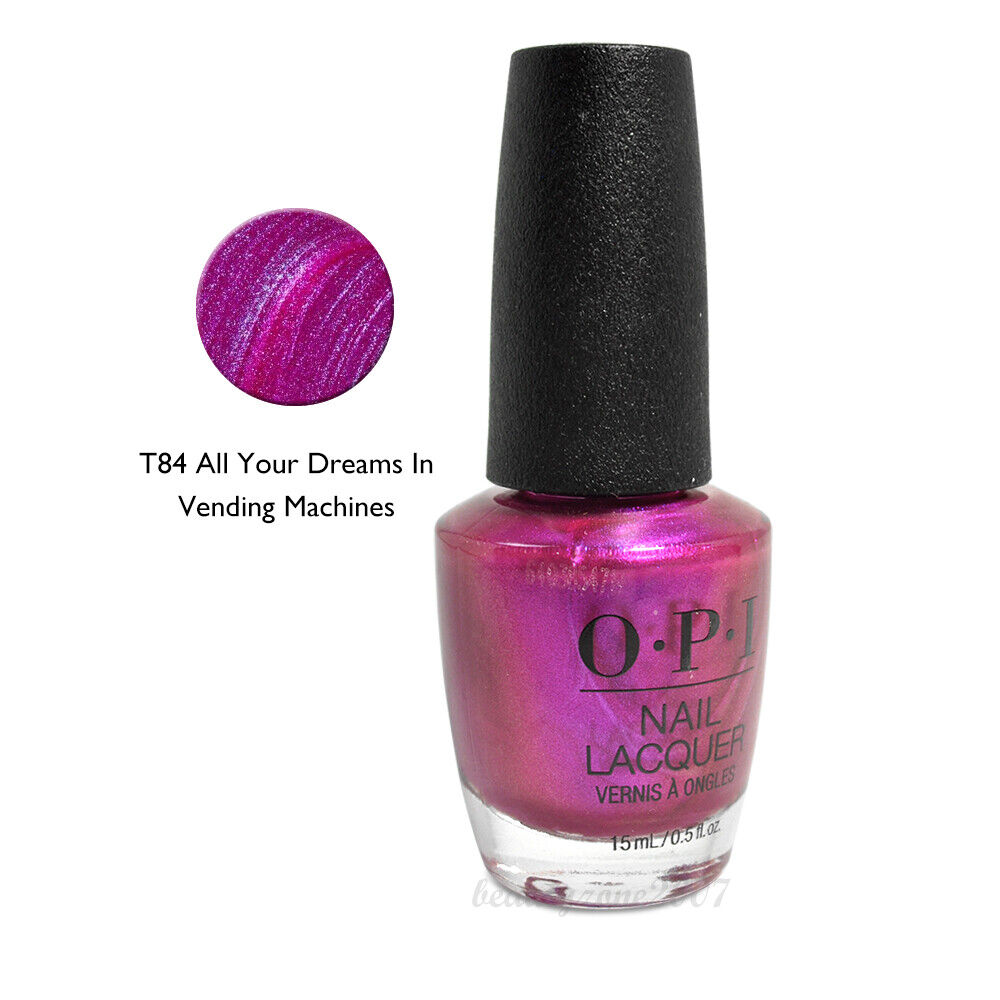
Illustrative Image (Source: Google Search)