Master the Market for Mini Snack Vending Machines: A B2B
Guide to Mini Snack Vending Machine
- Introduction: Navigating the Global Market for mini snack vending machine
- Understanding mini snack vending machine Types and Variations
- Key Industrial Applications of mini snack vending machine
- Strategic Material Selection Guide for mini snack vending machine
- In-depth Look: Manufacturing Processes and Quality Assurance for mini snack vending machine
- Comprehensive Cost and Pricing Analysis for mini snack vending machine Sourcing
- Spotlight on Potential mini snack vending machine Manufacturers and Suppliers
- Essential Technical Properties and Trade Terminology for mini snack vending machine
- Navigating Market Dynamics, Sourcing Trends, and Sustainability in the mini snack vending machine Sector
- Frequently Asked Questions (FAQs) for B2B Buyers of mini snack vending machine
- Strategic Sourcing Conclusion and Outlook for mini snack vending machine
Introduction: Navigating the Global Market for mini snack vending machine
In the ever-evolving landscape of retail and food services, mini snack vending machines have emerged as a vital solution for businesses aiming to capitalize on convenience and consumer demand. These compact units provide an efficient way to deliver snacks in high-traffic areas, catering to an increasingly busy lifestyle. For international B2B buyers, particularly in regions like Africa, South America, the Middle East, and Europe, investing in mini snack vending machines not only enhances customer engagement but also opens new revenue streams.
This comprehensive guide delves into the multifaceted world of mini snack vending machines, addressing key components that influence purchasing decisions. It covers various types of machines, from traditional to innovative smart vending options, ensuring buyers understand the technological advancements shaping the market. Insight into materials and manufacturing quality control processes will empower buyers to select durable and reliable machines that align with their operational standards.
Moreover, the guide explores supplier options across different regions, offering insights into the most reputable manufacturers and distributors. Understanding the cost structures associated with different vending machines is crucial for budget-conscious buyers, while an analysis of the current market trends provides context for future investments. Lastly, a dedicated FAQ section will address common queries, equipping buyers with the knowledge to make informed sourcing decisions.
By navigating this guide, B2B buyers can strategically position themselves within the global market, ensuring they remain competitive and responsive to consumer needs.
Understanding mini snack vending machine Types and Variations
Type Name | Key Distinguishing Features | Primary B2B Applications | Brief Pros & Cons for Buyers |
---|---|---|---|
Traditional Mini Vending | Compact size, mechanical dispensing mechanism | Offices, schools, hospitals | Pros: Low maintenance, familiar design. Cons: Limited product variety. |
Smart Vending Machines | Digital interface, cashless payment options | Retail stores, malls, airports | Pros: Real-time inventory tracking, enhanced customer engagement. Cons: Higher initial investment. |
Healthy Snack Vending | Focus on nutritious snacks, often refrigerated | Gyms, wellness centers, schools | Pros: Appeals to health-conscious consumers. Cons: Requires more frequent stocking. |
Combo Vending Machines | Multiple product types (snacks and beverages) | Cafeterias, break rooms | Pros: Versatile offering, maximizes space usage. Cons: Can be complex to manage inventory. |
Customized Vending Solutions | Tailored to specific business needs and branding | Corporate events, trade shows | Pros: Unique branding opportunity, meets niche demands. Cons: Higher cost and longer lead time. |
Traditional Mini Vending
Traditional mini vending machines are characterized by their compact size and mechanical dispensing mechanisms. They are widely used in environments such as offices, schools, and hospitals, where space is limited. Buyers should consider the ease of maintenance and the familiarity of this design, as it requires minimal training for users. However, the product variety is often limited, which may not satisfy diverse consumer preferences in more dynamic settings.
Smart Vending Machines
Smart vending machines are equipped with digital interfaces and cashless payment options, making them increasingly popular in retail stores, malls, and airports. These machines offer real-time inventory tracking and enhanced customer engagement through touch screens and mobile app integration. While they provide a modern shopping experience, buyers should be prepared for a higher initial investment and the need for ongoing technical support.
Healthy Snack Vending
Focusing on nutritious snacks, healthy snack vending machines often include refrigerated compartments to maintain freshness. They are particularly suitable for gyms, wellness centers, and schools, appealing to health-conscious consumers. Buyers should consider the need for more frequent stocking and potentially higher costs associated with perishable goods. However, the demand for healthier options can lead to increased sales and customer loyalty.
Combo Vending Machines
Combo vending machines offer a versatile selection of snacks and beverages, making them ideal for cafeterias and break rooms. These machines maximize space usage and cater to a wider range of consumer preferences. While they provide the advantage of variety, buyers may face challenges in managing inventory due to the complexity of stocking multiple product types. It’s essential to ensure that the machine’s design facilitates easy access and replenishment.
Customized Vending Solutions
Customized vending solutions are tailored to meet specific business needs and branding requirements. They are especially useful for corporate events and trade shows, where unique branding opportunities can enhance visibility. Buyers should weigh the benefits of meeting niche demands against the potential for higher costs and longer lead times associated with custom designs. Investing in a customized solution can differentiate a business in a competitive market, but careful planning is essential to ensure alignment with overall marketing strategies.
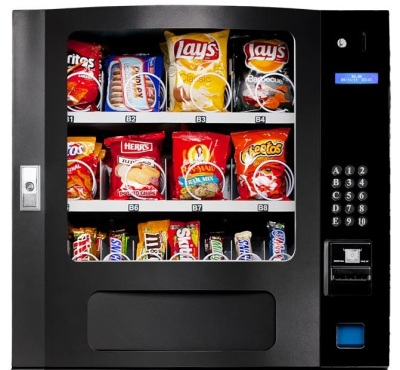
Illustrative Image (Source: Google Search)
Key Industrial Applications of mini snack vending machine
Industry/Sector | Specific Application of mini snack vending machine | Value/Benefit for the Business | Key Sourcing Considerations for this Application |
---|---|---|---|
Corporate Offices | Providing quick snack options for employees | Enhances employee satisfaction and productivity | Ensure machine size fits office space, consider healthy snack options |
Educational Institutions | Snack stations for students during breaks | Promotes healthy eating habits and convenience | Assess payment options for diverse student demographics |
Manufacturing Facilities | Breakroom vending for factory workers | Reduces downtime by offering on-site refreshments | Choose robust machines that withstand industrial environments |
Hospitals and Clinics | Vending for visitors and staff in waiting areas | Improves visitor experience and provides quick access to snacks | Compliance with health regulations, variety of dietary options |
Transportation Hubs | Snack vending at airports and bus stations | Captures impulse purchases and caters to travelers’ needs | Compact design for space constraints, payment flexibility |
Corporate Offices
In corporate settings, mini snack vending machines serve as convenient snack stations for employees. They provide quick access to refreshments, which can enhance morale and productivity. International B2B buyers should consider the machine’s size to ensure it fits the office environment and the types of snacks offered, particularly those that align with local dietary preferences. Additionally, offering healthy snack options can promote well-being among employees, which is increasingly important in modern workplaces.
Educational Institutions
Mini snack vending machines are particularly effective in educational institutions, catering to students during breaks. They offer a variety of snacks that can foster healthy eating habits while providing convenience. Buyers in this sector should assess payment options, as students may have varied preferences for cashless transactions. Furthermore, it’s essential to consider the nutritional value of the snacks to comply with health initiatives aimed at promoting student wellness.
Manufacturing Facilities
In manufacturing environments, mini snack vending machines can be strategically placed in breakrooms to provide on-site refreshments for workers. This setup reduces downtime, allowing employees to quickly grab a snack and return to work. B2B buyers should focus on sourcing robust machines that can withstand the demands of industrial settings, including potential exposure to dust and temperature fluctuations. Additionally, offering a range of snacks that cater to different dietary needs can enhance employee satisfaction.
Hospitals and Clinics
Hospitals and clinics benefit from mini snack vending machines positioned in waiting areas for visitors and staff. These machines improve the overall experience by providing quick access to food and drinks during long wait times. Buyers in this sector must ensure compliance with health regulations and consider offering a variety of dietary options, including gluten-free and low-sugar snacks, to cater to diverse needs. The selection of snacks can significantly impact visitor satisfaction and staff morale.
Transportation Hubs
In transportation hubs like airports and bus stations, mini snack vending machines cater to the fast-paced needs of travelers. They capture impulse purchases and provide essential snacks for those on the go. B2B buyers should prioritize compact designs that fit within limited space constraints and ensure the machines accept various payment methods, including mobile payments, to accommodate a diverse clientele. Offering local snacks can also enhance the travel experience, making it more memorable for passengers.
Related Video: DIY Mini Vending Machine
Strategic Material Selection Guide for mini snack vending machine
When selecting materials for mini snack vending machines, international B2B buyers must consider various factors, including durability, cost, and compliance with regional standards. The following analysis covers four common materials used in the construction of these machines, highlighting their properties, advantages, disadvantages, and specific considerations for buyers from Africa, South America, the Middle East, and Europe.
Stainless Steel
Key Properties: Stainless steel is known for its excellent corrosion resistance, high strength, and ability to withstand a wide range of temperatures. It typically has a temperature rating of up to 800°F (427°C) and is resistant to various chemicals.
Pros & Cons: The durability of stainless steel makes it ideal for high-traffic environments, while its aesthetic appeal is a plus for retail settings. However, it can be more expensive than other materials, and its manufacturing process can be complex, requiring specialized equipment.
Impact on Application: Stainless steel is suitable for environments where hygiene is critical, such as food service, as it is easy to clean and sanitize. Its corrosion resistance makes it compatible with various snack types, including those with high moisture content.
Considerations for International Buyers: Buyers should ensure compliance with food safety standards such as FDA or EU regulations. In regions like Africa and South America, local standards may vary, so understanding local compliance is essential.
Polycarbonate
Key Properties: Polycarbonate is a lightweight, impact-resistant plastic that can withstand temperatures ranging from -40°F to 240°F (-40°C to 115°C). It is also known for its clarity and UV resistance.
Pros & Cons: The main advantage of polycarbonate is its low weight, which facilitates easier installation and maintenance. However, it may not be as durable as metals and can be susceptible to scratching and chemical damage over time.
Impact on Application: Ideal for transparent components like viewing windows, polycarbonate allows customers to see the products inside the vending machine, enhancing the buying experience. It is compatible with most snack types but may not be suitable for very hot or corrosive products.
Considerations for International Buyers: Buyers should check for compliance with local safety standards, especially in regions like the Middle East, where temperature extremes can affect material performance.
Mild Steel
Key Properties: Mild steel is a low-carbon steel that offers good weldability and machinability. It typically has a temperature rating of around 300°F (149°C) and is relatively strong.
Pros & Cons: Mild steel is cost-effective and widely available, making it a popular choice for many applications. However, it is prone to rusting if not properly coated or maintained, which can limit its lifespan in humid or wet environments.
Impact on Application: While suitable for structural components, mild steel may require additional treatment (like powder coating) to enhance its durability and corrosion resistance, especially in regions with high humidity.
Considerations for International Buyers: Compliance with standards such as ASTM or DIN is crucial, particularly in Europe. Buyers in Africa and South America should also consider local environmental conditions when selecting mild steel.
Aluminum
Key Properties: Aluminum is lightweight, corrosion-resistant, and has a melting point of about 1,220°F (660°C). It is also an excellent conductor of heat and electricity.
Pros & Cons: The lightweight nature of aluminum makes it easy to transport and install. It is also resistant to corrosion, making it suitable for outdoor applications. However, it can be more expensive than mild steel and may not offer the same strength.
Impact on Application: Aluminum is ideal for components that require a balance of strength and weight, such as frames and panels. Its corrosion resistance makes it suitable for various snack types, including those that may produce moisture.
Considerations for International Buyers: Buyers should be aware of the differences in aluminum grades and their respective standards, such as JIS in Japan or EN in Europe. Understanding local material preferences can also impact purchasing decisions.
Summary Table
Material | Typical Use Case for mini snack vending machine | Key Advantage | Key Disadvantage/Limitation | Relative Cost (Low/Med/High) |
---|---|---|---|---|
Stainless Steel | Structural components, exterior panels | Excellent corrosion resistance | Higher cost, complex manufacturing | High |
Polycarbonate | Viewing windows, internal compartments | Lightweight, impact-resistant | Susceptible to scratches, chemical damage | Medium |
Mild Steel | Structural framework, support beams | Cost-effective, good weldability | Prone to rust, requires coating | Low |
Aluminum | Frames, panels, and lightweight components | Lightweight, corrosion-resistant | More expensive, lower strength than steel | Medium |
This strategic material selection guide provides B2B buyers with actionable insights to make informed decisions when sourcing materials for mini snack vending machines, considering both performance and regional compliance.
In-depth Look: Manufacturing Processes and Quality Assurance for mini snack vending machine
Understanding the Manufacturing Processes for Mini Snack Vending Machines
The manufacturing of mini snack vending machines involves several critical stages, each designed to ensure that the final product meets both functionality and quality standards. For B2B buyers, particularly those from Africa, South America, the Middle East, and Europe, understanding these processes can aid in making informed purchasing decisions.
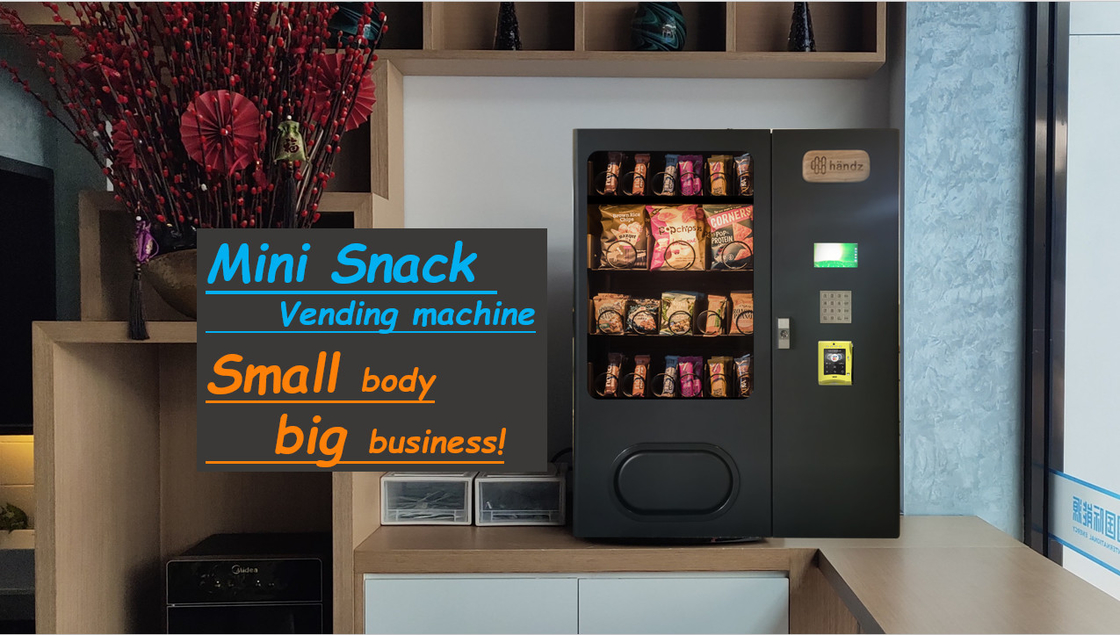
Illustrative Image (Source: Google Search)
1. Material Preparation
The first stage in the manufacturing process is material preparation, which includes sourcing high-quality raw materials that meet international standards. Common materials used include:
- Metals: Steel and aluminum for the frame and structural components.
- Plastics: High-density polyethylene (HDPE) or polycarbonate for the vending windows and internal components.
- Electrical Components: Wiring, sensors, and control systems that adhere to safety standards.
Buyers should ensure that suppliers provide material certifications, such as ISO 9001, which guarantees that the materials used are of high quality and sourced responsibly.
2. Forming
Once materials are prepared, the next step is forming, where raw materials are shaped into the required components. This can involve:
- Cutting: Using laser cutting for precision components.
- Bending: Employing hydraulic presses to create the machine’s structure.
- Injection Molding: For plastic parts, which allows for complex shapes and features.
For international buyers, understanding the forming techniques used by manufacturers can indicate the level of precision and quality control they maintain. Techniques such as CNC machining are often preferred for their accuracy.
3. Assembly
The assembly stage is where all formed components come together. This process typically involves:
- Mechanical Assembly: Fixing components using screws, bolts, and welds.
- Electrical Assembly: Integrating wiring, sensors, and control systems to ensure the machine operates correctly.
Quality assurance during this phase is crucial. Manufacturers should have a structured assembly line with skilled labor to minimize errors. Buyers should inquire about the assembly workforce’s training and experience, as this directly impacts the machine’s reliability.
4. Finishing
Finishing processes are applied to enhance the aesthetic and functional aspects of the vending machine. These include:
- Surface Treatment: Powder coating or painting to prevent corrosion and enhance appearance.
- Quality Inspection: Conducting visual inspections and tests to ensure that all components meet specifications.
B2B buyers should request information about the finishing techniques used, as this can affect the longevity and maintenance of the machines.
Quality Assurance Standards and Practices
Quality assurance (QA) is an integral part of the manufacturing process for mini snack vending machines. International and industry-specific standards help ensure that products meet safety and performance requirements.
International Standards
- ISO 9001: This standard focuses on quality management systems, ensuring that manufacturers consistently provide products that meet customer and regulatory requirements.
- CE Marking: For products sold in Europe, this marking indicates conformity with health, safety, and environmental protection standards.
Industry-Specific Standards
- API Standards: Relevant for electrical components, ensuring safety and reliability.
- RoHS Compliance: Ensures that hazardous substances are limited in electrical and electronic equipment.
Quality Control Checkpoints
Quality control is typically structured around several checkpoints during the manufacturing process:
- Incoming Quality Control (IQC): Inspecting raw materials upon arrival to ensure they meet specified standards.
- In-Process Quality Control (IPQC): Monitoring the manufacturing process to catch defects early.
- Final Quality Control (FQC): Conducting comprehensive tests on the finished product to ensure it meets all specifications.
Common Testing Methods
B2B buyers should be familiar with common testing methods to verify the quality of vending machines, including:
- Functional Testing: Ensuring that the vending machine operates correctly, including product dispensing and payment processing.
- Durability Testing: Assessing the machine’s resistance to wear and tear, particularly for high-traffic environments.
- Safety Testing: Evaluating electrical safety and compliance with international safety standards.
Verifying Supplier Quality Control
To ensure a reliable supply chain, B2B buyers should take proactive steps to verify the quality control measures employed by suppliers. Here are some actionable strategies:
-
Conduct Audits: Regular audits of the manufacturing facilities can provide insights into the production processes and quality management systems in place.
-
Request Quality Reports: Suppliers should provide detailed reports on their quality assurance processes, including results from IQC, IPQC, and FQC tests.
-
Engage Third-Party Inspectors: Consider hiring independent inspection agencies to conduct thorough assessments of the manufacturing processes and the quality of finished products.
-
Check Certifications: Ensure that suppliers have the relevant certifications for their quality management systems and product compliance.
Navigating Quality Control Nuances for International Buyers
For B2B buyers from different regions, particularly Africa, South America, the Middle East, and Europe, understanding the nuances of quality control is essential:
- Cultural Differences: Be aware of how quality is perceived and enforced in different regions. In some cultures, informal agreements may suffice, while in others, rigorous documentation is crucial.
- Local Regulations: Familiarize yourself with local regulations that may affect product compliance and safety standards.
- Supply Chain Considerations: Consider the logistics of shipping and handling, as international transport can affect the quality of products if not managed properly.
By understanding the manufacturing processes and quality assurance practices, B2B buyers can make informed decisions that enhance their procurement strategies, ensuring they source reliable and high-quality mini snack vending machines tailored to their market needs.
Related Video: Parle-G Biscuits Manufacturing process – Food Factory Tour- Modern Food factory, Mega Factory II
Comprehensive Cost and Pricing Analysis for mini snack vending machine Sourcing
Understanding the Cost Structure of Mini Snack Vending Machines
When sourcing mini snack vending machines, understanding the cost structure is paramount for international B2B buyers. The primary cost components include:
-
Materials: The choice of materials directly impacts both the durability and aesthetics of the vending machine. Common materials include metal, plastic, and glass. Higher-quality materials often lead to a higher upfront cost but can result in lower maintenance expenses over time.
-
Labor: Labor costs vary significantly by region. In countries with higher labor costs, such as those in Western Europe, expect to pay more for manufacturing. Conversely, sourcing from regions with lower labor costs, such as parts of Asia or South America, may yield savings.
-
Manufacturing Overhead: This includes indirect costs associated with production, such as factory utilities and administrative expenses. Understanding how these costs are calculated can aid in price negotiation.
-
Tooling: If customization is required, tooling costs can increase. Custom parts or designs may necessitate specialized machinery, which can add to the initial investment.
-
Quality Control (QC): A robust QC process ensures that machines meet safety and performance standards. Investing in quality control can prevent future costs related to repairs or replacements.
-
Logistics: Shipping costs can vary based on the machine’s size, weight, and the distance from the supplier. International buyers should also consider tariffs and customs fees, which can affect the total landed cost.
-
Margin: Suppliers typically add a margin to cover their costs and profit. This margin can fluctuate based on competition, demand, and the specific market conditions in the buyer’s region.
Key Price Influencers
Several factors influence the pricing of mini snack vending machines:
-
Volume/MOQ (Minimum Order Quantity): Larger orders often lead to discounts. Buyers should assess their needs and negotiate accordingly.
-
Specifications/Customization: Custom features can increase the cost. Buyers should determine essential specifications versus optional features to manage expenses.
-
Materials and Quality Certifications: Machines built with higher-quality materials and recognized certifications (such as ISO) can command higher prices but may offer better performance and reliability.
-
Supplier Factors: The reputation and reliability of the supplier can affect pricing. Established suppliers may charge more but provide better support and warranty services.
-
Incoterms: Understanding the Incoterms (International Commercial Terms) is crucial for determining who is responsible for shipping, insurance, and duties. Terms like FOB (Free on Board) or CIF (Cost, Insurance, and Freight) can significantly impact total costs.
Buyer Tips for Cost-Efficient Sourcing
-
Negotiate: Don’t hesitate to negotiate prices, especially for larger orders. Suppliers often have flexibility in pricing, particularly when they want to secure a deal.
-
Consider Total Cost of Ownership (TCO): Beyond the initial purchase price, factor in maintenance, operational costs, and potential downtime. A cheaper machine might lead to higher costs in the long run.
-
Understand Pricing Nuances: International buyers should be aware that prices may vary due to exchange rates, local demand, and supply chain disruptions. Keeping abreast of these factors can help in making informed purchasing decisions.
-
Conduct Market Research: Analyze the market to understand pricing trends and competitor offerings. This insight can empower buyers during negotiations.
-
Evaluate Supplier Performance: Before finalizing a supplier, consider their track record in terms of delivery times, product quality, and customer service. A slightly higher price may be justified by superior service and reliability.
Disclaimer
The prices discussed in this analysis are indicative and may vary based on market conditions, supplier negotiations, and specific buyer requirements. It is advisable for buyers to conduct thorough research and obtain multiple quotes to ensure the best possible deal.
Spotlight on Potential mini snack vending machine Manufacturers and Suppliers
- (No specific manufacturer data was available or requested for detailed profiling in this section for mini snack vending machine.)*
Essential Technical Properties and Trade Terminology for mini snack vending machine
When considering the acquisition of a mini snack vending machine, it is essential for international B2B buyers to understand the critical technical properties and terminology that will influence their purchasing decisions. This knowledge not only aids in selecting the right machine but also ensures smooth negotiations and operations across different markets.
Key Technical Properties
-
Material Grade
– Definition: This refers to the quality and type of materials used in the construction of the vending machine, such as stainless steel, plastic, or aluminum.
– B2B Importance: Higher-grade materials typically offer better durability and resistance to wear, crucial for machines placed in high-traffic environments. For buyers in regions with harsh climates, selecting machines with appropriate material grades can minimize maintenance costs and extend operational life. -
Capacity
– Definition: The number of products a vending machine can hold, usually measured in terms of slots or total weight.
– B2B Importance: Understanding capacity is vital for ensuring that the machine meets demand without frequent restocking. For buyers in populous areas or busy commercial zones, a higher capacity can lead to increased sales and lower operational downtime. -
Power Consumption
– Definition: The amount of electrical energy required to operate the vending machine, typically measured in watts.
– B2B Importance: Energy-efficient machines can significantly reduce operating costs, especially in countries where electricity prices are high. Buyers should look for machines with energy-saving features to enhance profitability. -
User Interface
– Definition: The design and functionality of the machine’s control panel, including payment systems (cash, card, mobile).
– B2B Importance: A user-friendly interface can enhance customer experience and reduce transaction times. This is particularly important in fast-paced environments such as airports or train stations, where speed and convenience are paramount. -
Dimensions and Weight
– Definition: The physical size and weight of the vending machine.
– B2B Importance: Understanding the dimensions is crucial for ensuring that the machine fits in designated spaces. Additionally, heavier machines may require more robust installation practices, influencing shipping and handling costs.
Common Trade Terms
-
OEM (Original Equipment Manufacturer)
– Definition: A company that produces parts or equipment that may be marketed by another manufacturer.
– B2B Importance: Buyers should understand OEM relationships as they can impact product quality and availability. Working directly with OEMs may yield better pricing and customization options. -
MOQ (Minimum Order Quantity)
– Definition: The smallest quantity of a product that a supplier is willing to sell.
– B2B Importance: Knowing the MOQ helps buyers plan their inventory and budget. This is particularly relevant for startups or smaller businesses that may have limited cash flow. -
RFQ (Request for Quotation)
– Definition: A document sent to suppliers to request pricing and other details about a product or service.
– B2B Importance: An RFQ is essential for comparing offers from multiple suppliers, ensuring that buyers get the best value for their investment. -
Incoterms (International Commercial Terms)
– Definition: A series of predefined commercial terms published by the International Chamber of Commerce (ICC) relating to international commercial law.
– B2B Importance: Understanding Incoterms is crucial for clarifying shipping responsibilities, costs, and risks. This knowledge is especially important for international buyers to avoid misunderstandings during the shipping process. -
Lead Time
– Definition: The time it takes from placing an order to the delivery of the product.
– B2B Importance: Knowing the lead time allows buyers to plan accordingly, ensuring that machines are available when needed. This is crucial for businesses that rely on timely product availability to meet customer demand.
By familiarizing themselves with these technical properties and trade terms, B2B buyers can make informed decisions when sourcing mini snack vending machines, ultimately enhancing their operational efficiency and profitability.
Navigating Market Dynamics, Sourcing Trends, and Sustainability in the mini snack vending machine Sector
Market Overview & Key Trends
The mini snack vending machine sector is experiencing significant growth, driven by evolving consumer preferences and technological advancements. Global demand for convenience foods, particularly in urban areas across Africa, South America, the Middle East, and Europe, is propelling the expansion of vending solutions. Key trends include the integration of cashless payment systems, which cater to the rising preference for contactless transactions, particularly in regions adapting to digital payment ecosystems. Additionally, smart vending machines equipped with IoT technology are gaining traction, allowing for real-time inventory management and enhanced customer engagement through personalized marketing.
B2B buyers should also be aware of the increasing popularity of health-conscious snack options, which is influencing machine stocking strategies. As consumers become more health-aware, there is a shift towards offering organic, gluten-free, and low-calorie snacks in vending machines. This trend is particularly relevant in Europe, where regulatory measures are encouraging healthier eating habits. Furthermore, the expansion of vending machine networks into less traditional locations, such as offices, schools, and public transport hubs, presents lucrative opportunities for international buyers seeking to diversify their offerings.
Emerging markets in Africa and South America are particularly promising, with increasing urbanization and a growing middle class driving demand for convenient food options. Buyers from these regions should focus on sourcing machines that can accommodate local snack preferences and are adaptable to varying power and connectivity conditions.
Sustainability & Ethical Sourcing in B2B
Sustainability is becoming a critical factor in the mini snack vending machine sector, as consumers and businesses alike are increasingly prioritizing environmental responsibility. The environmental impact of vending machines, particularly in terms of energy consumption and waste generation, necessitates the adoption of more sustainable practices. B2B buyers should consider machines that are energy-efficient and utilize environmentally friendly refrigerants to minimize their carbon footprint.
The importance of ethical supply chains cannot be overstated. Buyers should seek vendors who are committed to ethical sourcing practices, ensuring that the snacks offered are produced under fair labor conditions and with sustainable ingredients. Certifications such as Fair Trade, USDA Organic, and Rainforest Alliance can serve as valuable indicators of a supplier’s commitment to ethical practices.
Additionally, incorporating recyclable or biodegradable packaging in vending machine offerings can significantly enhance sustainability efforts. This not only appeals to environmentally conscious consumers but also aligns with increasingly stringent regulations regarding waste management in various regions. By prioritizing sustainable sourcing and ethical practices, B2B buyers can differentiate themselves in a competitive market, thereby attracting a growing base of eco-conscious customers.
Brief Evolution/History
The mini snack vending machine industry has evolved significantly since its inception in the early 20th century. Initially, vending machines offered simple snacks like gum and candy, but advancements in technology have transformed the sector into a sophisticated market. The introduction of electronic payment systems in the late 20th century marked a turning point, allowing for greater transaction flexibility and consumer convenience.
In recent years, the focus has shifted towards integrating smart technology and health-oriented products. Today’s machines not only offer a diverse range of snacks, including healthy options, but also incorporate features such as touchless payment and inventory tracking. This evolution reflects changing consumer behaviors and the need for businesses to adapt to a more digital and health-conscious marketplace. As the sector continues to innovate, international B2B buyers must stay informed about these developments to remain competitive and responsive to market demands.
Related Video: Is global trade transforming? | Counting the Cost
Frequently Asked Questions (FAQs) for B2B Buyers of mini snack vending machine
-
What should I consider when vetting suppliers for mini snack vending machines?
When vetting suppliers, prioritize their experience in the industry, production capacity, and reputation. Request references and case studies from similar markets, especially in your region. Verify certifications such as ISO or compliance with local regulations, and assess their ability to provide after-sales support. Conduct a site visit if possible, or utilize third-party audit services. This diligence helps ensure reliability and quality, reducing risks associated with international trade. -
Can I customize the mini snack vending machines to fit my brand?
Yes, many manufacturers offer customization options for mini snack vending machines. You can typically customize the machine’s exterior design, color schemes, and branding elements. Additionally, inquire about the possibility of tailoring the internal configuration to accommodate specific snack types. When discussing customization, ensure you clarify timelines and any additional costs involved to avoid unexpected expenses. -
What are the typical minimum order quantities (MOQ) and lead times for these machines?
MOQs for mini snack vending machines can vary widely based on the supplier and the complexity of the order. Generally, MOQs range from 10 to 50 units for initial orders. Lead times can also fluctuate based on customization and production schedules, typically ranging from 4 to 12 weeks. Always confirm these details upfront to align your inventory needs with supplier capabilities, especially if you are launching in a competitive market. -
What payment terms should I expect when purchasing internationally?
Payment terms can differ significantly among suppliers. Common methods include letters of credit, wire transfers, and payment on delivery. It’s advisable to negotiate terms that provide some level of security, such as partial upfront payment with the balance upon delivery. Be aware of any additional costs related to currency exchange and international transaction fees. Clear communication about payment terms can help prevent disputes later in the process. -
How can I ensure quality assurance and certifications for the machines?
To ensure quality assurance, request detailed documentation of the supplier’s quality control processes and product certifications. Look for internationally recognized certifications, such as CE marking in Europe or ISO standards, which indicate compliance with safety and performance criteria. Consider asking for samples or arranging for third-party testing to verify that the machines meet your specifications before placing a large order. -
What logistics considerations should I keep in mind when importing these machines?
Logistics is crucial when importing mini snack vending machines. Assess the shipping methods available, such as sea freight or air freight, and consider the associated costs and timelines. Work with a freight forwarder experienced in handling machinery imports, especially regarding customs clearance and documentation. Ensure you understand the duties and tariffs applicable in your country to avoid unexpected financial burdens. -
How should I handle disputes with suppliers?
To effectively manage disputes, establish clear terms and conditions in your purchase agreement. This should include details on payment terms, delivery timelines, and quality expectations. In case of a dispute, first attempt to resolve the issue through open communication. If necessary, consider mediation or arbitration, especially if the supplier is based in another country. Familiarize yourself with international trade laws and regulations that may impact your rights and obligations. -
What are the trends in the mini snack vending machine market that I should be aware of?
Current trends include the increasing demand for healthy snack options and the integration of cashless payment systems, such as mobile wallets. Additionally, sustainability is becoming a priority, with more suppliers offering eco-friendly machines. Staying informed about these trends can help you choose machines that align with consumer preferences and market demands, enhancing your competitive edge in the vending market.
Strategic Sourcing Conclusion and Outlook for mini snack vending machine
In conclusion, strategic sourcing of mini snack vending machines presents a significant opportunity for international B2B buyers across diverse markets, including Africa, South America, the Middle East, and Europe. Key takeaways emphasize the importance of understanding local consumer preferences and regulatory environments, as these factors directly influence product selection and operational success. By prioritizing suppliers who can offer customization, reliability, and innovative payment solutions, businesses can ensure a competitive edge in their respective markets.
The value of strategic sourcing extends beyond cost savings; it fosters long-term partnerships that enhance supply chain resilience and adaptability. As demand for convenient snacking options continues to grow, particularly in urban areas, investing in high-quality vending solutions will be essential for capturing market share.
Looking ahead, B2B buyers should remain agile and informed about emerging trends, such as healthier snack offerings and sustainable sourcing practices. This proactive approach will not only meet evolving consumer demands but also position businesses as leaders in the vending machine sector. Embrace the potential of mini snack vending machines and take the next step towards transforming your operations today.