Master the Home Vending Machine Market: Your Ultimate B2B
Guide to Home Vending Machine
- Introduction: Navigating the Global Market for home vending machine
- Understanding home vending machine Types and Variations
- Key Industrial Applications of home vending machine
- Strategic Material Selection Guide for home vending machine
- In-depth Look: Manufacturing Processes and Quality Assurance for home vending machine
- Comprehensive Cost and Pricing Analysis for home vending machine Sourcing
- Spotlight on Potential home vending machine Manufacturers and Suppliers
- Essential Technical Properties and Trade Terminology for home vending machine
- Navigating Market Dynamics, Sourcing Trends, and Sustainability in the home vending machine Sector
- Frequently Asked Questions (FAQs) for B2B Buyers of home vending machine
- Strategic Sourcing Conclusion and Outlook for home vending machine
Introduction: Navigating the Global Market for home vending machine
In today’s fast-paced environment, home vending machines have emerged as a transformative solution for convenience and accessibility, catering to the evolving demands of consumers globally. For international B2B buyers, particularly those from Africa, South America, the Middle East, and Europe, investing in home vending machines not only represents a lucrative business opportunity but also a means to enhance customer engagement and satisfaction. As urbanization accelerates and lifestyles shift, the demand for efficient, self-service options in homes and workplaces is on the rise.
This comprehensive guide delves into the multifaceted world of home vending machines, covering essential aspects such as types, materials, manufacturing quality control, supplier selection, cost analysis, and market trends. By understanding these critical components, B2B buyers can make informed sourcing decisions that align with their business goals and consumer preferences.
Furthermore, this guide addresses frequently asked questions that often arise during the procurement process, ensuring that buyers are equipped with the knowledge needed to navigate complexities in the global market. With actionable insights and expert recommendations, this resource empowers B2B buyers to optimize their vending machine offerings, streamline operations, and ultimately, maximize profitability. As you explore this guide, you will uncover strategies to not only source effectively but also to build lasting partnerships that foster growth in this dynamic industry.
Understanding home vending machine Types and Variations
Type Name | Key Distinguishing Features | Primary B2B Applications | Brief Pros & Cons for Buyers |
---|---|---|---|
Snack Vending Machines | Dispenses packaged snacks; typically has multiple compartments | Offices, schools, gyms | Pros: Easy to stock, popular items; Cons: Limited to non-perishable items. |
Beverage Vending Machines | Designed for canned or bottled drinks; often refrigerated | Workplaces, events, public spaces | Pros: High demand, quick sales; Cons: Requires power, potential for spoilage. |
Fresh Food Vending Machines | Offers perishable items like sandwiches and salads; refrigerated | Hospitals, airports, universities | Pros: Expands product range; Cons: Higher maintenance and spoilage risk. |
Health & Wellness Vending Machines | Focused on nutritious options; often includes supplements | Gyms, health clubs, corporate offices | Pros: Aligns with health trends; Cons: May have limited customer base. |
Specialty Item Vending Machines | Dispenses unique products (e.g., electronics, personal care) | Retail stores, tech hubs, airports | Pros: Attracts niche markets; Cons: Higher cost and niche demand. |
Snack Vending Machines
Snack vending machines are designed to dispense a variety of packaged snacks, making them a staple in many locations such as offices, schools, and gyms. These machines typically feature multiple compartments to accommodate different snack types, enhancing consumer choice. For B2B buyers, the key considerations include the machine’s capacity, ease of restocking, and the selection of popular snacks that align with consumer preferences. While they are easy to maintain, the limitation to non-perishable items can restrict product variety.
Beverage Vending Machines
Beverage vending machines are specifically engineered to hold and dispense canned or bottled drinks, often with refrigeration capabilities to ensure product freshness. They are commonly placed in workplaces, events, and public spaces, capitalizing on the high demand for cold beverages. B2B buyers should focus on the machine’s energy efficiency, capacity, and the variety of drinks offered. Although these machines can generate quick sales, they require a power source and may face issues with spoilage if not managed properly.
Fresh Food Vending Machines
Fresh food vending machines provide a unique offering by dispensing perishable items such as sandwiches, salads, and healthy snacks. These machines are ideal for locations like hospitals, airports, and universities, where consumers seek convenient, nutritious meal options. When purchasing, B2B buyers should consider the machine’s refrigeration capabilities, maintenance needs, and the sourcing of fresh products. While they can significantly expand product offerings, the risk of spoilage necessitates careful inventory management.
Health & Wellness Vending Machines
Health and wellness vending machines cater to the growing consumer demand for nutritious and health-oriented products, often including items like protein bars, organic snacks, and dietary supplements. They are commonly found in gyms, health clubs, and corporate offices, appealing to health-conscious consumers. B2B buyers should assess product variety, supplier reliability, and machine technology for ease of use. While they align well with health trends, these machines may have a more limited customer base compared to traditional snack and beverage options.
Specialty Item Vending Machines
Specialty item vending machines dispense unique products, ranging from electronics to personal care items. These machines are often placed in retail stores, tech hubs, and airports, attracting niche markets looking for convenience. B2B buyers should evaluate the machine’s capacity for diverse products, pricing strategies, and target demographic. Although they can draw interest from specific consumer segments, the higher cost of products and niche demand can pose challenges for broader market appeal.
Related Video: DIY Card Vending Machine – Easy Cardboard Craft
Key Industrial Applications of home vending machine
Industry/Sector | Specific Application of Home Vending Machine | Value/Benefit for the Business | Key Sourcing Considerations for this Application |
---|---|---|---|
Hospitality | Snacks and beverages in hotels and resorts | Enhances guest experience, generates additional revenue | Supplier reliability, product variety, compliance with health standards |
Education | Healthy snacks and drinks in schools and universities | Promotes healthy eating habits, increases student satisfaction | Nutritional compliance, supplier partnerships for bulk purchasing |
Corporate Offices | Quick access to refreshments and meals for employees | Boosts employee morale and productivity, reduces downtime | Diverse product offerings, reliable service, and maintenance support |
Residential Complexes | Automated grocery and essential items for residents | Provides convenience, reduces shopping frequency | Local sourcing for fresh items, inventory management capabilities |
Fitness Centers | Nutritional supplements and healthy snacks for gym-goers | Supports health-conscious clientele, increases membership retention | Compliance with dietary regulations, customizable product options |
Hospitality
In the hospitality sector, home vending machines can be strategically placed in hotels and resorts to provide guests with quick access to snacks and beverages. This not only enhances the guest experience but also creates an additional revenue stream for the establishment. Buyers in this sector must ensure that their vending machines comply with local health regulations and offer a variety of products to cater to diverse preferences. Building strong relationships with reliable suppliers can facilitate bulk purchasing and exclusive product offerings, which are crucial for maximizing profits.
Education
Home vending machines in educational institutions serve as convenient sources for healthy snacks and drinks, promoting better eating habits among students. By providing nutritious options, schools and universities can increase student satisfaction and engagement. B2B buyers in this sector should focus on sourcing products that meet nutritional guidelines, and establish partnerships with suppliers who can ensure timely deliveries and consistent quality. Additionally, understanding local regulations regarding food sales in educational environments is essential to avoid compliance issues.
Corporate Offices
In corporate settings, home vending machines can provide employees with quick access to refreshments and meals, significantly boosting morale and productivity. This convenience reduces downtime spent on food breaks and enhances overall employee satisfaction. When sourcing vending machines for offices, buyers should prioritize suppliers that offer a diverse range of products and reliable service. Maintenance support is also crucial to ensure machines are consistently operational, which directly impacts employee experience and retention.
Residential Complexes
Home vending machines in residential complexes can automate the availability of grocery items and essential products for residents, offering a high level of convenience. This service reduces the need for frequent shopping trips and caters to busy lifestyles. Buyers must consider local sourcing for fresh items to ensure product quality and customer satisfaction. Additionally, effective inventory management capabilities are important to maintain stock levels and meet resident demands promptly.
Fitness Centers
Fitness centers can benefit from home vending machines that offer nutritional supplements and healthy snacks tailored for gym-goers. This aligns with the health-conscious values of their clientele and can contribute to increased membership retention. Buyers should ensure that the products comply with dietary regulations and consider customizable options to cater to specific customer preferences. Collaborating with suppliers who specialize in health-focused products will enhance the vending offerings and support the overall brand image of the fitness center.
Strategic Material Selection Guide for home vending machine
When selecting materials for home vending machines, it’s essential to consider various factors that affect performance, durability, and cost. Below, we analyze four common materials used in the construction of vending machines, highlighting their key properties, advantages, disadvantages, and specific considerations for international B2B buyers.
1. Stainless Steel
Key Properties:
Stainless steel is known for its excellent corrosion resistance, high strength, and ability to withstand high temperatures. It typically has a temperature rating of up to 800°F (427°C) and offers good pressure resistance.
Pros & Cons:
The primary advantage of stainless steel is its durability and resistance to rust and staining, making it ideal for food and beverage applications. However, it can be more expensive than other materials and may require specialized manufacturing processes, which can increase production costs.
Impact on Application:
Stainless steel is compatible with various media, including food and beverages, and is often used for the exterior and internal components of vending machines.
Considerations for International Buyers:
Buyers should ensure compliance with local health and safety regulations regarding food-grade materials. Standards such as ASTM A240 for stainless steel may apply. In regions like Africa and South America, sourcing from local suppliers can mitigate import costs.
2. Plastic (Polycarbonate)
Key Properties:
Polycarbonate is a lightweight, impact-resistant plastic that can withstand temperatures ranging from -40°F to 240°F (-40°C to 116°C). It offers good clarity and UV resistance.
Pros & Cons:
The main advantage of polycarbonate is its low weight and high impact resistance, making it suitable for transparent panels in vending machines. However, it is less durable than metals and can become brittle over time, particularly under UV exposure.
Impact on Application:
Polycarbonate is often used for viewing windows and internal components that require visibility. It is compatible with various media but should not be exposed to harsh chemicals.
Considerations for International Buyers:
Buyers should check for compliance with standards like ASTM D635 for flammability. In regions like the Middle East, where UV exposure is high, selecting UV-stabilized polycarbonate can enhance longevity.
3. Aluminum
Key Properties:
Aluminum is lightweight, corrosion-resistant, and has a temperature rating of approximately 1,200°F (649°C). It is also an excellent conductor of heat and electricity.
Pros & Cons:
Aluminum’s lightweight nature makes it easy to handle and install. It is generally less expensive than stainless steel but may not offer the same level of strength and durability. It can be prone to denting and scratching.
Impact on Application:
Aluminum is suitable for various components, including frames and panels, and is compatible with most media used in vending machines.
Considerations for International Buyers:
Buyers should be aware of the specific grades of aluminum, as they can vary in strength and corrosion resistance. Compliance with standards like ASTM B221 is essential, especially in regions with stringent material regulations.
4. Glass
Key Properties:
Glass is rigid, offers excellent clarity, and can withstand moderate temperatures. However, it is fragile and can break under impact.
Pros & Cons:
The primary advantage of glass is its aesthetic appeal and the ability to showcase products effectively. Its main disadvantage is its fragility, which can lead to higher replacement costs and safety concerns.
Impact on Application:
Glass is commonly used for display panels in vending machines, providing visibility for products. It is compatible with most media but should be handled with care to avoid breakage.
Considerations for International Buyers:
Buyers should ensure that the glass used complies with safety standards such as ANSI Z97.1. In regions like Europe, where safety regulations are stringent, tempered glass may be required to enhance safety.
Material | Typical Use Case for home vending machine | Key Advantage | Key Disadvantage/Limitation | Relative Cost (Low/Med/High) |
---|---|---|---|---|
Stainless Steel | Exterior and internal components | Excellent corrosion resistance | Higher cost, complex manufacturing | High |
Plastic (Polycarbonate) | Viewing windows and internal components | Lightweight, impact-resistant | Less durable, can become brittle | Medium |
Aluminum | Frames and panels | Lightweight, cost-effective | Prone to denting, less durable | Medium |
Glass | Display panels | Aesthetic appeal, product visibility | Fragile, higher replacement costs | Medium |
This strategic material selection guide provides B2B buyers with critical insights into the materials used in home vending machines, enabling informed decision-making that aligns with operational needs and regional compliance requirements.
In-depth Look: Manufacturing Processes and Quality Assurance for home vending machine
The manufacturing process for home vending machines involves several critical stages, each designed to ensure the final product meets industry standards and customer expectations. Understanding these stages, along with the quality assurance measures in place, is crucial for international B2B buyers, especially those from diverse markets such as Africa, South America, the Middle East, and Europe. Here’s a detailed breakdown of the typical manufacturing processes and quality control measures that buyers should consider.
Manufacturing Process
1. Material Preparation
The first stage in manufacturing home vending machines involves selecting and preparing raw materials. Common materials include:
- Metal (steel or aluminum): Used for structural components due to strength and durability.
- Plastic (ABS or polycarbonate): Utilized for outer casings and internal mechanisms for lightweight and corrosion resistance.
- Electronic components: Includes circuit boards, sensors, and payment systems.
In this phase, materials are sourced from reputable suppliers, and certifications regarding material quality (such as ASTM or ISO standards) are often obtained to ensure compliance.
2. Forming
Once the materials are prepared, the forming process begins. This stage involves various techniques, including:
- Stamping: Used to create metal parts by pressing flat sheets into desired shapes using dies.
- Injection Molding: A common technique for producing plastic components, where melted plastic is injected into molds to form specific shapes.
- Laser Cutting: Employed for precise cutting of metal and plastic components, ensuring accuracy and reducing waste.
These techniques are critical for creating the various components that will make up the vending machine, ensuring they fit together seamlessly.
3. Assembly
The assembly stage is where individual components come together to form the final product. This process typically includes:
- Mechanical assembly: Joining metal and plastic parts using screws, rivets, or welding.
- Electrical assembly: Installing wiring, circuit boards, and payment processing systems.
- Quality checks: At this stage, initial quality checks are performed to ensure that components are correctly installed and functioning.
Manufacturers often use automated systems alongside skilled labor to enhance efficiency and accuracy during assembly.
4. Finishing
The final stage of manufacturing involves finishing processes designed to enhance the aesthetic and functional qualities of the vending machine. Key activities include:
- Surface treatment: Applying coatings, paints, or finishes to protect against corrosion and wear while also improving appearance.
- Final inspections: Conducting thorough inspections to ensure that the machine meets all design specifications and quality standards.
This stage is crucial for ensuring that the product is ready for the market and can withstand operational demands.
Quality Assurance
Quality assurance (QA) is an integral part of the manufacturing process, ensuring that every vending machine meets international standards and customer expectations. Here are the key aspects of QA that B2B buyers should be aware of:
International Standards
Many manufacturers adhere to international quality standards, such as:
- ISO 9001: This standard outlines criteria for a quality management system and ensures that products consistently meet customer and regulatory requirements.
- CE Marking: Required for products sold in the European Economic Area, indicating compliance with health, safety, and environmental protection standards.
- API Standards: Relevant for certain components, particularly those related to electrical and electronic systems.
These certifications provide assurance that the manufacturing process meets stringent quality criteria.
Quality Control Checkpoints
Quality control (QC) involves several critical checkpoints throughout the manufacturing process:
- Incoming Quality Control (IQC): Inspecting raw materials and components upon arrival to ensure they meet specified standards.
- In-Process Quality Control (IPQC): Ongoing inspections during the manufacturing process to catch defects early and ensure compliance with specifications.
- Final Quality Control (FQC): A comprehensive review of the finished product to verify functionality, safety, and adherence to design specifications.
These checkpoints help to minimize defects and ensure a high-quality end product.
Common Testing Methods
Various testing methods are employed to verify the quality and safety of vending machines:
- Functional Testing: Ensures that all mechanical and electronic components operate as intended.
- Safety Testing: Involves checking for electrical safety, fire hazards, and compliance with local regulations.
- Durability Testing: Simulates real-world usage to evaluate how the machine withstands wear and tear.
These tests help to identify potential issues before the product reaches the market.
Verifying Supplier Quality Control
For B2B buyers, verifying a supplier’s quality control measures is essential to ensure product reliability. Here are actionable steps to assess supplier QC:
-
Conduct Audits: Regular audits of suppliers can provide insights into their manufacturing processes and quality assurance practices. This can be done through on-site visits or third-party audits.
-
Request Quality Reports: Suppliers should provide documentation detailing their QC processes, testing results, and certifications. This transparency is crucial for building trust.
-
Engage Third-Party Inspectors: Utilizing independent inspectors can validate the quality of the machines before shipment, ensuring they meet the agreed specifications.
-
Understand Certification Nuances: Different regions may have varying requirements for product certifications. For instance, EU regulations may differ significantly from those in Africa or South America. Buyers should familiarize themselves with these nuances to ensure compliance.
Conclusion
Understanding the manufacturing processes and quality assurance measures for home vending machines is vital for international B2B buyers. By focusing on the manufacturing stages—material preparation, forming, assembly, and finishing—along with robust quality control practices, buyers can make informed decisions when sourcing vending machines. Establishing strong relationships with suppliers who adhere to international standards and demonstrate transparency in their QC processes will further enhance the success of vending machine ventures across diverse markets.
Related Video: Amazing scenes。Top 6 Most Popular Factory Manufacturing Videos in China
Comprehensive Cost and Pricing Analysis for home vending machine Sourcing
Understanding the cost structure and pricing dynamics of home vending machines is essential for international B2B buyers looking to make informed sourcing decisions. This section breaks down the key cost components, pricing influencers, and offers actionable tips for effective negotiation and procurement.
Cost Components
-
Materials: The primary cost driver in manufacturing vending machines involves raw materials such as steel, plastics, and electronic components. The selection of high-quality materials impacts durability and functionality, which can lead to higher upfront costs but reduced long-term maintenance expenses.
-
Labor: Labor costs vary significantly based on geographic location and the complexity of the machine. Countries with lower labor costs might offer cheaper manufacturing, but the trade-off could be in quality and compliance with international standards.
-
Manufacturing Overhead: This includes expenses related to factory operations, utilities, and administrative costs. Efficient manufacturing processes can help minimize overhead, thus affecting overall pricing.
-
Tooling: Initial tooling costs for custom designs can be substantial. Buyers should factor these costs into the total investment, particularly for machines requiring unique specifications or branding.
-
Quality Control (QC): Ensuring product quality through rigorous testing and inspection can add to costs but is critical for maintaining brand reputation and customer satisfaction. Consider suppliers with robust QC processes to mitigate risks associated with defective products.
-
Logistics: Shipping and handling costs vary based on the destination, shipping method, and Incoterms used. International buyers should plan for potential tariffs and import duties, which can significantly affect the total cost.
-
Margin: Supplier profit margins can vary widely depending on the market and the level of competition. Understanding a supplier’s pricing strategy can provide insight into negotiating better terms.
Price Influencers
-
Volume/MOQ: Minimum order quantities (MOQs) can significantly impact pricing. Larger orders often lead to discounts, making it beneficial for buyers to consolidate purchases when feasible.
-
Specifications/Customization: Custom features can increase costs. Buyers should clearly define their needs to avoid unexpected expenses associated with modifications.
-
Materials: The choice of materials directly affects both cost and quality. High-quality materials may increase initial expenditure but can lead to lower maintenance costs over the product’s lifecycle.
-
Quality/Certifications: Products that meet international quality standards or possess relevant certifications may command higher prices. However, these certifications can also enhance marketability and customer trust.
-
Supplier Factors: The reliability and reputation of suppliers play a crucial role in pricing. Established suppliers may offer better terms due to their experience and established processes.
-
Incoterms: The chosen Incoterms can influence total costs related to shipping responsibilities and risks. Understanding the implications of terms like FOB (Free on Board) or CIF (Cost, Insurance, and Freight) is vital for budgeting.
Buyer Tips
-
Negotiation: Cultivate relationships with suppliers to enhance negotiation outcomes. Long-term partnerships can lead to better pricing and terms as trust develops.
-
Cost-Efficiency: Evaluate the total cost of ownership (TCO), not just the purchase price. Consider factors like maintenance, energy consumption, and expected lifespan when assessing value.
-
Pricing Nuances for International Buyers: Understand regional market dynamics and currency fluctuations, which can affect costs. Buyers from Africa, South America, the Middle East, and Europe should also be aware of local import regulations and potential tariffs.
-
Stay Informed: Regularly review industry trends and supplier capabilities to ensure that you are making competitive and informed sourcing decisions.
Disclaimer
Prices and costs mentioned herein are indicative and subject to change based on market conditions, supplier negotiations, and regional economic factors. Always conduct thorough due diligence and obtain multiple quotes to ensure competitive pricing.
Spotlight on Potential home vending machine Manufacturers and Suppliers
This section offers a look at a few manufacturers active in the ‘home vending machine’ market. This is a representative sample for illustrative purposes; B2B buyers must conduct their own extensive due diligence before any engagement. Information is synthesized from public sources and general industry knowledge.
Essential Technical Properties and Trade Terminology for home vending machine
Key Technical Properties of Home Vending Machines
Understanding the technical properties of home vending machines is crucial for B2B buyers looking to make informed purchasing decisions. Here are several critical specifications to consider:
-
Material Grade
The construction material of a vending machine significantly impacts its durability and aesthetics. Common materials include stainless steel for the body, which offers corrosion resistance and strength, and tempered glass for visibility and security. Selecting high-grade materials can enhance longevity and reduce maintenance costs. -
Capacity
Capacity refers to the volume of products the vending machine can hold, typically measured in the number of product slots or total weight. A machine with a higher capacity can cater to larger customer bases and reduce the frequency of restocking, thus optimizing operational efficiency. For B2B buyers, understanding capacity is essential for meeting demand without incurring excess operational costs. -
Power Consumption
This specification indicates the energy efficiency of the vending machine, usually measured in watts. Machines with lower power consumption are more cost-effective in the long run, especially in regions with high electricity rates. Buyers should evaluate energy efficiency ratings to ensure alignment with sustainability goals and operational budgets. -
Payment Options
Modern vending machines offer various payment methods, including cash, credit/debit cards, and mobile payments. The versatility of payment options can significantly influence sales volume and customer satisfaction. B2B buyers should prioritize machines that support multiple payment methods to accommodate diverse consumer preferences. -
Temperature Control
For machines that dispense perishable items, effective temperature control is crucial. Specifications may include temperature range and cooling technology (like compressor or thermoelectric systems). Proper temperature regulation ensures product quality and compliance with health regulations, thus protecting your brand’s reputation. -
Connectivity Features
Many contemporary vending machines come equipped with IoT capabilities, allowing for remote monitoring and management. Features like telemetry can provide real-time data on stock levels and machine performance, enabling proactive maintenance and inventory management. This technological integration can lead to significant operational efficiencies and enhanced customer experiences.
Common Trade Terms in Vending Machine Industry
Navigating the vending machine marketplace requires familiarity with specific jargon. Here are essential terms that B2B buyers should know:
-
OEM (Original Equipment Manufacturer)
This term refers to a company that produces parts and equipment that may be marketed by another manufacturer. In the context of vending machines, an OEM could provide components that ensure compatibility and quality assurance for your machines. Establishing relationships with reputable OEMs can lead to better pricing and product reliability. -
MOQ (Minimum Order Quantity)
MOQ denotes the smallest quantity of a product that a supplier is willing to sell. Understanding MOQ is critical for managing inventory and cash flow. Buyers should assess their demand forecasts to negotiate favorable terms with suppliers, ensuring that they can meet market needs without overcommitting resources. -
RFQ (Request for Quotation)
An RFQ is a formal request sent to suppliers to obtain pricing and terms for specific products or services. This process is crucial for comparing costs and evaluating potential vendors. B2B buyers should utilize RFQs to gather competitive bids and make informed purchasing decisions. -
Incoterms (International Commercial Terms)
These are a series of pre-defined commercial terms published by the International Chamber of Commerce, covering various aspects of shipping and freight. Understanding Incoterms helps buyers clarify responsibilities for shipping, insurance, and tariffs. This knowledge is essential for international transactions to prevent disputes and ensure smooth logistics. -
Lead Time
Lead time refers to the time taken from placing an order to the delivery of goods. Shorter lead times can enhance operational efficiency and customer satisfaction. B2B buyers should inquire about lead times during negotiations to align their supply chain strategies with market demands.
- Warranty Period
This term indicates the duration during which a product is guaranteed against defects. A robust warranty period can signify a manufacturer’s confidence in their product’s quality. B2B buyers should evaluate warranty terms as part of their overall cost-benefit analysis to safeguard their investment in vending machines.
By understanding these technical properties and industry terms, international B2B buyers can make strategic decisions that enhance their vending machine operations and profitability.
Navigating Market Dynamics, Sourcing Trends, and Sustainability in the home vending machine Sector
Market Overview & Key Trends
The home vending machine sector is experiencing significant growth, driven by shifts in consumer behavior, technological advancements, and the rise of convenience-oriented lifestyles. In international markets such as Africa, South America, the Middle East, and Europe, buyers are increasingly seeking innovative solutions that cater to the demand for quick and accessible products. This surge is largely fueled by the growing urban population, increased disposable incomes, and a shift towards cashless transactions facilitated by mobile payment technologies.
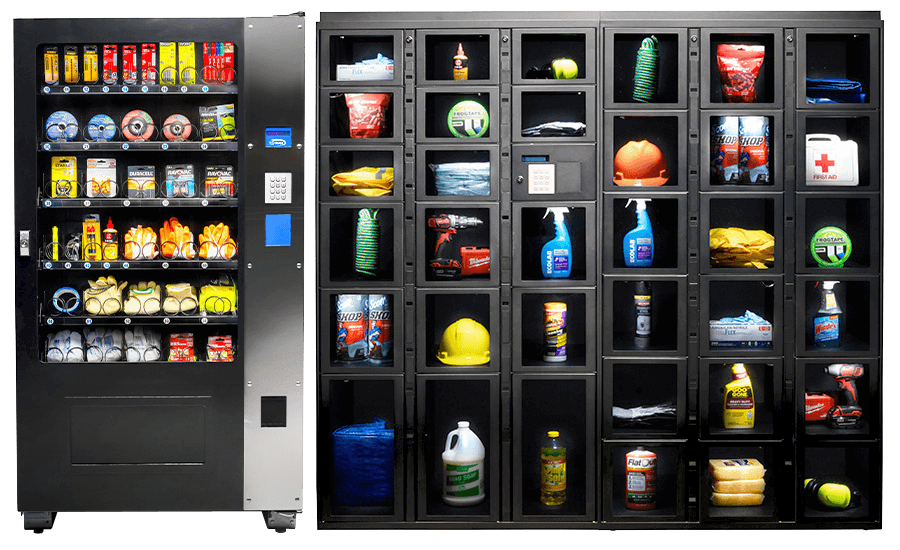
Illustrative Image (Source: Google Search)
B2B buyers should be aware of several key sourcing trends. First, the integration of IoT (Internet of Things) technology into vending machines is revolutionizing the sector, allowing for real-time inventory tracking and data analytics that can inform stocking decisions. This technology not only enhances operational efficiency but also provides insights into consumer preferences, enabling suppliers to offer tailored products that resonate with local markets. Additionally, the rise of customization options is becoming a critical differentiator. Machines that offer personalized selections or healthy options are more likely to attract and retain customers.
Moreover, sustainability is becoming a focal point for international buyers. Consumers are increasingly aware of environmental impacts, prompting a demand for eco-friendly products and packaging. B2B buyers in these regions should prioritize suppliers that align with these values, ensuring their offerings are both appealing and responsible.
Sustainability & Ethical Sourcing in B2B
Sustainability in the home vending machine industry is not merely a trend but an essential consideration for B2B buyers. The environmental impact of sourcing practices can significantly influence brand reputation and consumer loyalty. As a result, businesses must focus on creating ethical supply chains that prioritize responsible sourcing, waste reduction, and energy-efficient operations.
One effective strategy is to seek out suppliers who utilize green certifications and sustainable materials in their products. These certifications, such as Fair Trade or FSC (Forest Stewardship Council), not only help in minimizing environmental footprints but also enhance the credibility of the vending machine offerings. Furthermore, opting for machines that incorporate energy-efficient technologies can lead to substantial cost savings over time, particularly in regions where energy prices are high.
Implementing a circular economy approach, where machines are designed for easy repair and recycling, is another way to demonstrate commitment to sustainability. Buyers should engage with suppliers who are transparent about their sustainability practices and are willing to provide documentation on their sourcing methods and environmental impact.
Brief Evolution/History
The vending machine industry has evolved significantly since its inception in the late 19th century, transitioning from simple coin-operated devices to complex systems equipped with advanced technology. Initially, vending machines offered basic products like snacks and beverages. However, the advent of technology has enabled the introduction of diverse offerings, including healthy snacks, personal care items, and even electronics.
In recent years, the rise of smart vending machines equipped with touchscreens, cashless payment options, and remote inventory management systems has transformed the landscape. This evolution is particularly relevant for international B2B buyers, as it allows for greater flexibility and responsiveness to market trends. As the industry continues to innovate, understanding this historical context can aid buyers in making informed decisions about future investments and partnerships.
Related Video: International Trade 101 | Economics Explained
Frequently Asked Questions (FAQs) for B2B Buyers of home vending machine
-
What criteria should I use to vet suppliers for home vending machines?
When vetting suppliers, consider their reputation, experience, and customer reviews. Verify their business licenses and compliance with local regulations, particularly in your country. Assess their production capabilities and the quality of their machines through samples or certifications. It’s also beneficial to inquire about their supply chain management to ensure timely delivery and reliability. Establishing a good rapport and clear communication with suppliers can significantly enhance your partnership. -
Can I customize the vending machines to fit my branding or specific product offerings?
Yes, many suppliers offer customization options for home vending machines. This can include branding elements such as logos, colors, and product selections tailored to your target market. Discuss your specific needs with potential suppliers to understand the extent of customization available. Be sure to clarify any additional costs associated with customization and how it may affect lead times. -
What are the typical minimum order quantities (MOQ) and lead times for home vending machines?
MOQs can vary significantly between suppliers, with some allowing orders as low as one machine, while others may require a larger purchase to ensure cost-effectiveness. Lead times also depend on the supplier’s production capacity and the complexity of your order. Typically, expect lead times ranging from 4 to 12 weeks. Always confirm these details upfront to avoid any disruptions in your supply chain. -
What payment terms should I expect when sourcing vending machines internationally?
Payment terms can differ based on the supplier’s policies and your negotiation power. Common terms include a deposit upfront (usually 30-50%) and the balance upon delivery or before shipping. For international transactions, consider using secure payment methods like letters of credit or escrow services to protect your investment. Always clarify the currency in which payments will be made to avoid exchange rate issues. -
How can I ensure quality assurance and compliance with certifications?
Request documentation for quality assurance processes, such as ISO certifications or compliance with safety standards relevant to your region. Engage suppliers who can provide samples for inspection before finalizing large orders. It’s also advisable to conduct factory visits, if feasible, or hire third-party inspection services to verify that the machines meet your quality expectations and regulatory requirements. -
What logistics considerations should I take into account when importing vending machines?
Logistics involve several factors, including shipping methods, customs clearance, and local regulations. Determine whether the supplier offers shipping services or if you need to coordinate with freight forwarders. Understand the customs duties and tariffs applicable in your country, and ensure all documentation is complete to avoid delays. Tracking shipments can help you stay updated on delivery status and manage inventory effectively. -
How can I handle disputes with suppliers effectively?
Establish clear communication channels and document all agreements to minimize misunderstandings. If a dispute arises, attempt to resolve it through direct negotiation first. If necessary, refer to the contract for resolution procedures, including mediation or arbitration clauses. Maintaining a professional relationship with suppliers can often lead to amicable solutions, but ensure you know your rights and obligations under international trade laws. -
What after-sales support should I expect from vending machine suppliers?
After-sales support is crucial for the longevity of your vending machines. Inquire about warranty terms, repair services, and the availability of spare parts. A reliable supplier will offer training for your staff on machine operation and maintenance. Additionally, check if they provide ongoing technical support or troubleshooting assistance, which can be invaluable in minimizing downtime and ensuring customer satisfaction.
Strategic Sourcing Conclusion and Outlook for home vending machine
The journey toward successful strategic sourcing in the home vending machine sector is pivotal for international B2B buyers. By leveraging strong supplier partnerships, businesses can unlock opportunities for cost-effective inventory management and exclusive product access. Understanding local legal requirements is essential to ensure compliance, which protects against potential liabilities and fosters trust with customers and suppliers alike.
Moreover, embracing innovative sourcing strategies allows companies to adapt to evolving consumer preferences and market trends, ensuring a competitive edge. Key takeaways include the importance of supplier reliability, a diverse product catalog, and a commitment to transparency in vendor relationships. These elements are vital for optimizing your supply chain and maximizing profitability.
Looking ahead, the home vending machine market is poised for growth, especially in dynamic regions such as Africa, South America, the Middle East, and Europe. As the demand for convenient and diverse product offerings rises, now is the time for B2B buyers to explore strategic sourcing opportunities. Invest in building robust supplier networks and stay ahead of market trends to capitalize on this burgeoning sector. Your proactive approach today will set the foundation for success tomorrow.