Master the Cashless Vending Machine Market with Expert
Guide to Cashless Vending Machine
- Introduction: Navigating the Global Market for cashless vending machine
- Understanding cashless vending machine Types and Variations
- Key Industrial Applications of cashless vending machine
- Strategic Material Selection Guide for cashless vending machine
- In-depth Look: Manufacturing Processes and Quality Assurance for cashless vending machine
- Comprehensive Cost and Pricing Analysis for cashless vending machine Sourcing
- Spotlight on Potential cashless vending machine Manufacturers and Suppliers
- Essential Technical Properties and Trade Terminology for cashless vending machine
- Navigating Market Dynamics, Sourcing Trends, and Sustainability in the cashless vending machine Sector
- Frequently Asked Questions (FAQs) for B2B Buyers of cashless vending machine
- Strategic Sourcing Conclusion and Outlook for cashless vending machine
Introduction: Navigating the Global Market for cashless vending machine
In today’s fast-paced global economy, the demand for cashless vending machines is soaring, driven by a shift towards convenience and technological advancement. These machines not only streamline transactions but also enhance customer satisfaction by offering a seamless purchasing experience. For international B2B buyers, particularly those in Africa, South America, the Middle East, and Europe, understanding this market is crucial to staying competitive and meeting the evolving needs of consumers.
This guide provides a comprehensive overview of cashless vending machines, covering various types, materials used in their construction, and manufacturing quality control processes. Buyers will gain insights into reputable suppliers, pricing structures, and the broader market landscape, equipping them with the knowledge to make informed sourcing decisions.
Additionally, the guide addresses common FAQs, demystifying the complexities associated with these advanced vending solutions. Whether you are seeking to enhance an existing vending operation or looking to invest in new technology, this resource empowers you to navigate the cashless vending machine market effectively. By leveraging the insights presented, B2B buyers can optimize their procurement strategies, ensuring they remain at the forefront of the cashless revolution.
Understanding cashless vending machine Types and Variations
Type Name | Key Distinguishing Features | Primary B2B Applications | Brief Pros & Cons for Buyers |
---|---|---|---|
Traditional Cashless Vending Machine | Accepts credit/debit cards, mobile wallets; often retrofitted for cashless payments | Offices, schools, public transport | Pros: Easy to implement; Cons: Limited payment options compared to newer models |
Smart Vending Machines | Equipped with touch screens, IoT connectivity, and real-time inventory management | Retail, airports, malls | Pros: Enhanced user experience; Cons: Higher upfront costs and maintenance |
Micro Market Kiosks | Self-service retail environments with various payment methods; typically larger than standard machines | Corporate environments, hospitals | Pros: Variety of products; Cons: Requires more space and initial investment |
Healthy Vending Machines | Focus on nutritious snacks and beverages; often feature eco-friendly designs | Schools, gyms, health facilities | Pros: Supports healthy choices; Cons: May limit product variety for general consumers |
Automated Retail Solutions | Fully automated systems that integrate AI for product suggestions and personalized offers | Airports, train stations, large venues | Pros: Personalized customer engagement; Cons: Complexity in setup and higher costs |
Traditional Cashless Vending Machines
Traditional cashless vending machines are primarily designed to accept credit and debit cards, as well as mobile payment options. They are often retrofitted to accommodate cashless transactions, making them a popular choice for businesses looking to modernize. These machines are particularly suitable for environments such as offices and schools, where convenience is key. B2B buyers should consider the ease of implementation and potential for limited payment options compared to newer models.
Smart Vending Machines
Smart vending machines are characterized by their touch screens and IoT capabilities, allowing for real-time inventory management and enhanced user interaction. These machines are commonly found in retail spaces, airports, and malls. They offer an improved customer experience through features like product recommendations. However, B2B buyers should be aware of the higher upfront costs and ongoing maintenance associated with smart vending machines.
Micro Market Kiosks
Micro market kiosks provide a self-service retail environment that typically offers a wider range of products than traditional vending machines. They allow various payment methods, including cashless options, and are well-suited for corporate environments and hospitals. Buyers should note the advantages of product variety and the potential for increased sales, although these kiosks require more space and a larger initial investment.
Healthy Vending Machines
Healthy vending machines focus on providing nutritious snacks and beverages, often featuring eco-friendly designs. These machines are ideal for schools, gyms, and health facilities, where promoting healthy eating is a priority. B2B buyers should consider the benefits of supporting health initiatives, but they may also find that product variety is limited compared to standard vending options.
Automated Retail Solutions
Automated retail solutions are advanced systems that utilize AI to offer personalized product suggestions and enhance customer engagement. These machines are increasingly popular in high-traffic locations such as airports and train stations. While they provide a unique shopping experience, B2B buyers must consider the complexity of setup and the higher costs associated with these sophisticated solutions.
Related Video: Machine Learning in 2024 – Beginner’s Course
Key Industrial Applications of cashless vending machine
Industry/Sector | Specific Application of Cashless Vending Machine | Value/Benefit for the Business | Key Sourcing Considerations for this Application |
---|---|---|---|
Healthcare | Automated medication dispensing | Increases medication adherence, reduces human error | Compliance with health regulations, secure payment systems |
Education | Campus snack and beverage sales | Provides convenient access for students, reduces labor costs | Robust inventory management, durable and secure machines |
Transportation | Ticketing and travel passes | Streamlines passenger flow, reduces queue times | Integration with existing transport systems, uptime reliability |
Corporate Offices | Employee refreshment stations | Enhances workplace satisfaction, boosts productivity | Variety of product offerings, customizable payment options |
Retail | Contactless retail sales | Expands sales channels, meets consumer demand for convenience | User-friendly interface, remote management capabilities |
Healthcare
In healthcare settings, cashless vending machines are increasingly used for automated medication dispensing. These machines ensure that patients have easy access to their prescribed medications, thereby enhancing medication adherence and minimizing the risk of human error during dispensing. For international buyers in this sector, it is crucial to ensure that the machines comply with local health regulations and have secure payment systems that protect sensitive patient information.
Education
Within educational institutions, cashless vending machines serve as convenient snack and beverage outlets for students. This application reduces the need for staff to manage sales, allowing them to focus on educational activities instead. For B2B buyers, sourcing machines with robust inventory management systems is essential to monitor product availability and minimize waste. Additionally, durability and security features are vital to withstand the high usage in school environments.
Transportation
Cashless vending machines are also deployed in the transportation sector for ticketing and travel passes. This application helps streamline passenger flow at stations and reduces waiting times by allowing quick and easy purchases. Buyers from this sector should consider machines that can integrate seamlessly with existing transport systems and offer high uptime reliability to ensure passenger satisfaction and operational efficiency.
Corporate Offices
In corporate environments, cashless vending machines can serve as employee refreshment stations, providing quick access to snacks and beverages. This convenience enhances workplace satisfaction and can lead to increased productivity among employees. For international B2B buyers, it is important to look for machines that offer a variety of product options and customizable payment systems to cater to diverse employee preferences.
Retail
The retail sector benefits from cashless vending machines as they offer contactless retail sales solutions. These machines expand sales channels and meet the growing consumer demand for convenience, especially in urban areas. Buyers should prioritize user-friendly interfaces and remote management capabilities to efficiently handle inventory and sales data, ensuring a smooth shopping experience for customers.
Related Video: How to Start a Vending Machine Business, Cost, Tips, How Much You Make
Strategic Material Selection Guide for cashless vending machine
When selecting materials for cashless vending machines, it is essential to consider their properties, advantages, and limitations. The choice of material can significantly impact the machine’s performance, durability, and overall cost-effectiveness. Below is an analysis of four common materials used in cashless vending machines, tailored for international B2B buyers from diverse regions.
Stainless Steel
Key Properties: Stainless steel is known for its excellent corrosion resistance, high strength, and ability to withstand high temperatures. It typically has a temperature rating of up to 800°C and is resistant to various chemicals.
Pros & Cons: The primary advantage of stainless steel is its durability and longevity, making it ideal for outdoor or high-traffic environments. However, it can be more expensive than other materials, and its manufacturing process can be complex, requiring specialized equipment.
Impact on Application: Stainless steel is suitable for components exposed to moisture or corrosive elements, such as payment interfaces and external casings. It is compatible with various media, including cashless payment systems.
Considerations for International Buyers: Buyers should ensure compliance with local standards such as ASTM or DIN for material specifications. In regions like Africa and South America, where environmental conditions may vary, selecting the appropriate grade (e.g., 304 or 316) is crucial.
Aluminum
Key Properties: Aluminum is lightweight, has good corrosion resistance, and can be easily machined. It typically withstands temperatures up to 400°C and offers a decent strength-to-weight ratio.
Pros & Cons: The lightweight nature of aluminum makes it easy to handle and transport, reducing shipping costs. However, it may not be as durable as stainless steel, especially in high-impact environments, and can be more prone to scratches.
Impact on Application: Aluminum is often used for internal components and frames of cashless vending machines. Its compatibility with electronic components makes it a preferred choice for housing payment systems.
Considerations for International Buyers: Buyers should be aware of local recycling regulations, as aluminum is highly recyclable. Compliance with JIS standards may also be relevant in certain regions, particularly in Japan.
Polycarbonate
Key Properties: Polycarbonate is a robust thermoplastic known for its impact resistance and optical clarity. It can withstand temperatures ranging from -40°C to 120°C and offers good UV resistance.
Pros & Cons: The primary advantage of polycarbonate is its lightweight and transparent nature, which allows for easy visibility of products inside the vending machine. However, it can be more expensive than other plastics and may scratch easily.
Impact on Application: Polycarbonate is ideal for transparent panels or windows in vending machines, enhancing user experience by allowing customers to see available products. Its chemical resistance makes it suitable for various environments.
Considerations for International Buyers: Buyers should ensure that the polycarbonate used meets relevant safety standards, particularly in regions with strict regulations on plastic use. Understanding local preferences for materials can also guide purchasing decisions.
Carbon Steel
Key Properties: Carbon steel is known for its high strength and toughness, with a temperature rating typically up to 600°C. However, it is susceptible to corrosion without proper coatings.
Pros & Cons: The cost-effectiveness of carbon steel makes it a popular choice for structural components. However, its susceptibility to rust can be a significant drawback, necessitating protective coatings.
Impact on Application: Carbon steel is often used for internal frames and structural supports in cashless vending machines. It is suitable for environments where moisture exposure is minimal.
Considerations for International Buyers: Buyers should consider the need for protective coatings to prevent corrosion, especially in humid climates like those found in parts of Africa and South America. Compliance with local manufacturing standards is also crucial.
Summary Table
Material | Typical Use Case for cashless vending machine | Key Advantage | Key Disadvantage/Limitation | Relative Cost (Low/Med/High) |
---|---|---|---|---|
Stainless Steel | External casings, payment interfaces | Excellent durability and corrosion resistance | Higher cost, complex manufacturing | High |
Aluminum | Internal components, frames | Lightweight, easy to handle | Less durable, prone to scratches | Medium |
Polycarbonate | Transparent panels, windows | Impact resistance, visibility | More expensive, scratches easily | Medium |
Carbon Steel | Structural supports, internal frames | Cost-effective, high strength | Susceptible to corrosion | Low |
This strategic material selection guide provides valuable insights for international B2B buyers, helping them make informed decisions based on performance, cost, and regional considerations.
In-depth Look: Manufacturing Processes and Quality Assurance for cashless vending machine
The manufacturing process of cashless vending machines is crucial for ensuring their functionality, durability, and user satisfaction. For international B2B buyers, particularly from Africa, South America, the Middle East, and Europe, understanding the intricacies of manufacturing and quality assurance can significantly influence purchasing decisions.
Manufacturing Processes
1. Material Preparation
The first stage in manufacturing cashless vending machines involves selecting high-quality materials. Common materials include:
- Metal Alloys: Used for structural components to ensure strength and durability.
- Plastics: Employed for outer casings and internal components, offering lightweight and corrosion resistance.
- Electronic Components: Including payment systems, sensors, and microcontrollers, which are essential for cashless transactions.
Buyers should inquire about the source and specifications of these materials, as they directly impact the machine’s longevity and performance.
2. Forming
This stage involves shaping the prepared materials into usable components. Key techniques include:
- Stamping: Used for metal parts, allowing for precise shapes and sizes.
- Injection Molding: Commonly used for plastic components, ensuring uniformity and complexity in design.
- CNC Machining: Employed for creating intricate parts that require high precision.
B2B buyers should understand the capabilities of the supplier’s machinery and technology, as this can affect production efficiency and product quality.
3. Assembly
Once components are formed, they are assembled into the final product. This process includes:
- Component Integration: Installing electronic systems, payment modules, and mechanical parts.
- Wiring and Connectivity: Ensuring that all electronic components are properly connected for optimal functionality.
- Testing During Assembly: Conducting preliminary tests to identify any issues before final assembly.
Buyers should ensure that suppliers have a structured assembly process, as this can minimize errors and enhance product reliability.
4. Finishing
The finishing stage focuses on enhancing the aesthetic and functional aspects of the vending machine. Key activities include:
- Surface Treatment: Coatings and finishes to improve durability and appearance (e.g., powder coating or painting).
- Quality Control Checks: Ensuring that the machine meets design specifications and is free of defects.
This stage is vital for creating a product that is not only functional but also visually appealing to customers.
Quality Assurance
Quality assurance is integral to the manufacturing process, ensuring that the final product meets international standards and customer expectations.
International Standards
For cashless vending machines, compliance with relevant international standards is essential. Key certifications include:
- ISO 9001: This standard focuses on quality management systems and is widely recognized across industries. It ensures that manufacturers have consistent processes in place.
- CE Marking: Required for products sold in the European Economic Area, indicating conformity with health, safety, and environmental protection standards.
- API Standards: For machines that might integrate with specific technology platforms, adherence to industry-specific standards is crucial.
B2B buyers should verify that suppliers hold these certifications, as they reflect a commitment to quality.
Quality Control Checkpoints
A robust quality control system typically includes several checkpoints:
- Incoming Quality Control (IQC): Inspection of raw materials upon arrival to ensure they meet specifications.
- In-Process Quality Control (IPQC): Ongoing checks during manufacturing to catch defects early.
- Final Quality Control (FQC): A comprehensive evaluation of the finished product before it leaves the factory.
B2B buyers can enhance their purchasing confidence by requesting detailed reports on these QC processes.
Common Testing Methods
Various testing methods are employed to ensure product integrity:
- Functional Testing: Verifying that all electronic components function correctly.
- Durability Testing: Simulating wear and tear to assess long-term performance.
- Safety Testing: Ensuring compliance with electrical and mechanical safety standards.
Buyers should inquire about the testing protocols used by suppliers and request test reports to validate quality claims.
Verification of Supplier Quality Control
To ensure that suppliers maintain high-quality standards, B2B buyers can implement several strategies:
- Supplier Audits: Conducting on-site audits to assess manufacturing processes and quality control measures firsthand.
- Requesting Quality Reports: Regularly obtaining quality assurance reports that detail QC activities and outcomes.
- Third-Party Inspections: Engaging independent inspectors to evaluate products before shipment, providing an unbiased assessment of quality.
These measures can significantly reduce the risk of receiving subpar products.
QC/Certifications Nuances for International B2B Buyers
International B2B buyers must be aware of specific nuances regarding quality control and certifications:
- Regional Compliance: Different regions may have varying standards. For example, CE marking is crucial for European markets, while UL certification may be required in North America.
- Cultural Considerations: Understanding local business practices and expectations can facilitate smoother negotiations and partnerships.
- Logistics and Supply Chain: Factors such as shipping regulations and import duties can influence purchasing decisions, necessitating thorough due diligence.
By considering these aspects, international buyers can make informed decisions that align with their operational needs and market demands.
In conclusion, a comprehensive understanding of the manufacturing processes and quality assurance mechanisms in cashless vending machines can empower B2B buyers to select reliable suppliers. By focusing on material quality, manufacturing techniques, and stringent quality control measures, buyers can ensure they invest in durable, efficient, and compliant products that meet their business objectives.
Related Video: Exploring 5 Intriguing Factory Mass Production Processes in China.
Comprehensive Cost and Pricing Analysis for cashless vending machine Sourcing
Analyzing the cost structure and pricing for cashless vending machine sourcing is essential for international B2B buyers, particularly those from Africa, South America, the Middle East, and Europe. Understanding the components that contribute to the overall cost can help buyers make informed purchasing decisions.
Cost Components
-
Materials: The primary materials used in cashless vending machines include metals (for the casing), electronic components (such as payment processors), and plastics. The choice of materials can significantly impact the overall cost, with higher-quality components leading to better durability and performance.
-
Labor: Labor costs can vary widely based on the manufacturing location. Countries with lower labor costs may offer more competitive pricing, but it’s crucial to assess whether the quality of workmanship meets international standards.
-
Manufacturing Overhead: This includes costs related to factory maintenance, utilities, and administrative expenses. Efficient manufacturing processes can help reduce these overheads, allowing suppliers to offer more competitive pricing.
-
Tooling: The initial investment in tooling can be substantial, especially for custom designs. Buyers should inquire whether the tooling costs are included in the quoted price or if they will be charged separately.
-
Quality Control (QC): Implementing rigorous quality control processes is vital to ensure that machines meet the specified standards. This can add to costs but is essential for long-term reliability.
-
Logistics: Shipping costs can vary significantly based on distance, mode of transportation, and any applicable tariffs or duties. Understanding the logistics involved will help buyers factor these costs into their overall budget.
- Margin: Suppliers will add a profit margin to cover their costs and risks. This margin can vary based on the supplier’s market position and the competitiveness of their offerings.
Price Influencers
-
Volume/MOQ: The minimum order quantity (MOQ) can affect pricing. Larger orders typically result in lower per-unit costs due to economies of scale.
-
Specifications/Customization: Custom features, such as branding or specific payment options, can increase costs. Buyers should weigh the benefits of customization against budget constraints.
-
Materials: As mentioned, the choice of materials affects cost. Opting for standard materials can keep prices down, while premium materials will increase the cost.
-
Quality/Certifications: Machines that meet international quality standards and certifications may come at a premium but can save costs in maintenance and downtime over their lifespan.
-
Supplier Factors: A supplier’s reputation, experience, and service offerings can influence pricing. Established suppliers might charge more due to their reliability and service levels.
-
Incoterms: Understanding the terms of delivery (Incoterms) is crucial, as they define the responsibilities of buyers and sellers regarding shipping, insurance, and tariffs. This can affect the total landed cost.
Buyer Tips
-
Negotiate: Always negotiate pricing and terms with suppliers. Establishing a good relationship can lead to better deals, especially for repeat purchases.
-
Cost-Efficiency: Consider the total cost of ownership (TCO) rather than just the initial purchase price. This includes maintenance, operation, and potential downtime costs.
-
Pricing Nuances: Be aware of pricing differences based on geographical markets. For instance, suppliers in Europe may have different pricing structures compared to those in Africa or South America due to local economic conditions.
-
Request Detailed Quotes: Ensure that quotes break down all cost components. This transparency allows for easier comparison between suppliers.
-
Explore Multiple Suppliers: Diversifying suppliers can lead to more competitive pricing and reduce reliance on a single source.
Disclaimer
Prices for cashless vending machines can fluctuate based on market conditions, supplier capabilities, and changes in raw material costs. Buyers should always seek updated quotes and be prepared for negotiations to achieve the best possible pricing.
Spotlight on Potential cashless vending machine Manufacturers and Suppliers
This section offers a look at a few manufacturers active in the ‘cashless vending machine’ market. This is a representative sample for illustrative purposes; B2B buyers must conduct their own extensive due diligence before any engagement. Information is synthesized from public sources and general industry knowledge.
Essential Technical Properties and Trade Terminology for cashless vending machine
When considering the procurement of cashless vending machines, understanding essential technical properties and industry terminology is crucial for making informed purchasing decisions. This section outlines the key specifications and terms that B2B buyers should be familiar with.
Key Technical Properties
-
Material Grade
– Definition: This refers to the quality and type of materials used in the construction of the vending machine, such as stainless steel, aluminum, or high-grade plastics.
– Importance: High-quality materials ensure durability, resistance to corrosion, and longevity, reducing maintenance costs and enhancing the machine’s lifespan, which is critical in commercial environments. -
Power Supply Compatibility
– Definition: The specifications related to the electrical input required for the vending machine to operate, including voltage and amperage.
– Importance: Understanding power requirements is essential for ensuring compatibility with local electrical systems, preventing operational failures, and avoiding additional installation costs. -
Dimensions and Capacity
– Definition: The physical size of the vending machine and its storage capacity for products.
– Importance: Buyers must assess the space where the machine will be installed and the volume of products it needs to dispense. This affects customer satisfaction and sales efficiency. -
Payment System Integration
– Definition: The types of cashless payment options supported, such as credit/debit cards, mobile wallets, or contactless payments.
– Importance: A flexible payment system can attract more customers, especially in regions where cash transactions are declining. Ensuring compatibility with popular payment methods in the target market is vital for maximizing sales. -
User Interface Features
– Definition: This includes touchscreen displays, multilingual support, and user-friendly navigation.
– Importance: An intuitive interface enhances user experience, reduces transaction times, and can increase customer engagement, particularly in diverse markets. -
Security Features
– Definition: Security measures that protect the machine and transactions, such as encryption protocols and tamper-proof designs.
– Importance: Ensuring the security of transactions is critical for building customer trust and preventing financial losses due to fraud.
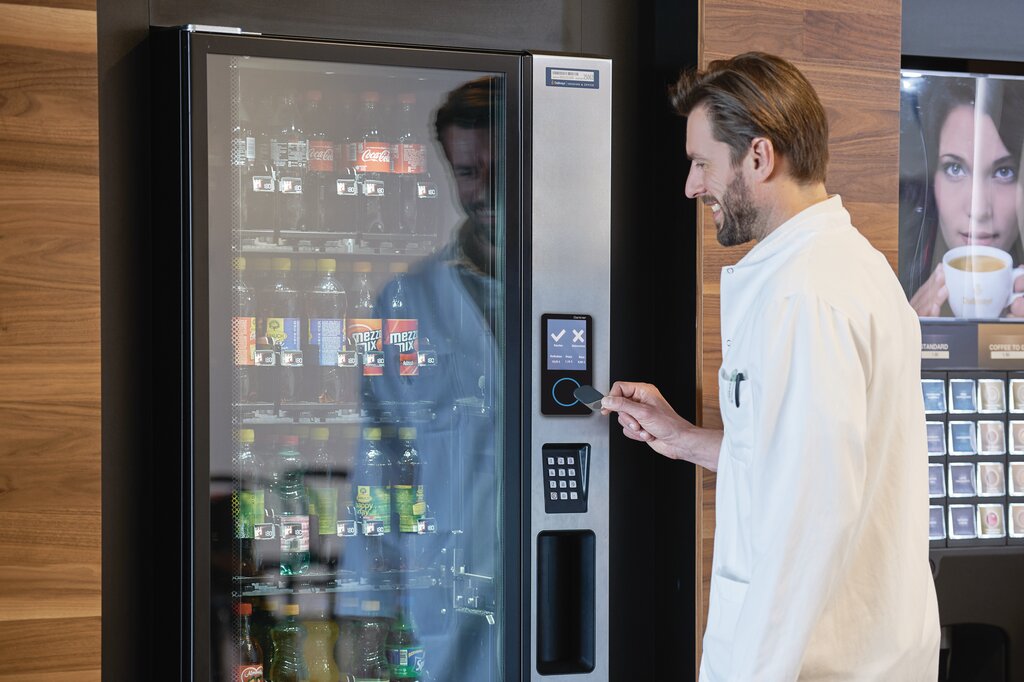
Illustrative Image (Source: Google Search)
Common Industry Terms
-
OEM (Original Equipment Manufacturer)
– Definition: A company that produces parts or equipment that may be marketed by another manufacturer.
– Relevance: Understanding OEM relationships can help buyers identify reliable manufacturers and ensure quality compliance in their purchases. -
MOQ (Minimum Order Quantity)
– Definition: The smallest amount of product that a supplier is willing to sell.
– Relevance: Knowing the MOQ is crucial for budgeting and inventory management, particularly for smaller businesses or startups. -
RFQ (Request for Quotation)
– Definition: A document sent to suppliers to request pricing and terms for specific products or services.
– Relevance: Issuing an RFQ helps buyers compare offers from different suppliers, ensuring competitive pricing and terms. -
Incoterms (International Commercial Terms)
– Definition: A set of rules that define the responsibilities of sellers and buyers in international transactions.
– Relevance: Familiarity with Incoterms helps buyers understand shipping costs, risk transfer, and delivery responsibilities, which are essential for international procurement. -
Lead Time
– Definition: The amount of time from placing an order to the delivery of the product.
– Relevance: Knowing lead times is vital for planning inventory and ensuring timely availability of vending machines in the market. -
Warranty and Service Agreements
– Definition: Contracts that outline the terms of service and support provided for the vending machine.
– Relevance: Understanding warranty conditions and service options helps buyers mitigate risks associated with maintenance and repairs, ensuring machine reliability.
By grasping these technical properties and industry terms, B2B buyers from various regions can make more informed decisions, ensuring they select cashless vending machines that meet their operational needs and market demands.
Navigating Market Dynamics, Sourcing Trends, and Sustainability in the cashless vending machine Sector
Market Overview & Key Trends
The cashless vending machine sector has seen robust growth, driven by the increasing demand for contactless payment solutions, particularly in the wake of the COVID-19 pandemic. Global trends indicate a shift towards digital transactions, with buyers in Africa, South America, the Middle East, and Europe increasingly favoring cashless options. This shift is fueled by advancements in mobile payment technologies and the proliferation of smartphones, which facilitate seamless transactions and enhance user experience.
In terms of sourcing trends, international B2B buyers are now prioritizing smart vending solutions that incorporate IoT (Internet of Things) capabilities. These machines not only accept a variety of payment methods—including mobile wallets and cryptocurrencies—but also collect data on consumer behavior, enabling better inventory management and personalized marketing strategies. Additionally, buyers are focusing on vendors that provide robust customer support and flexible financing options, making it easier to integrate these systems into existing operations.
Market dynamics are also influenced by regulatory frameworks aimed at promoting cashless transactions. Countries in Europe, for instance, have implemented policies to reduce cash usage, while regions in Africa are embracing mobile money solutions, creating new opportunities for cashless vending. As competition intensifies, B2B buyers should seek out innovative suppliers who demonstrate a commitment to technological advancements and customer-centric solutions.
Sustainability & Ethical Sourcing in B2B
As sustainability becomes a key concern for consumers and businesses alike, the cashless vending machine sector is not exempt from scrutiny regarding its environmental impact. B2B buyers are increasingly aware of the importance of ethical supply chains, which encompass the entire lifecycle of products—from sourcing raw materials to end-of-life disposal. This awareness is leading to a demand for vending machines made from recyclable materials and those that utilize energy-efficient technologies.
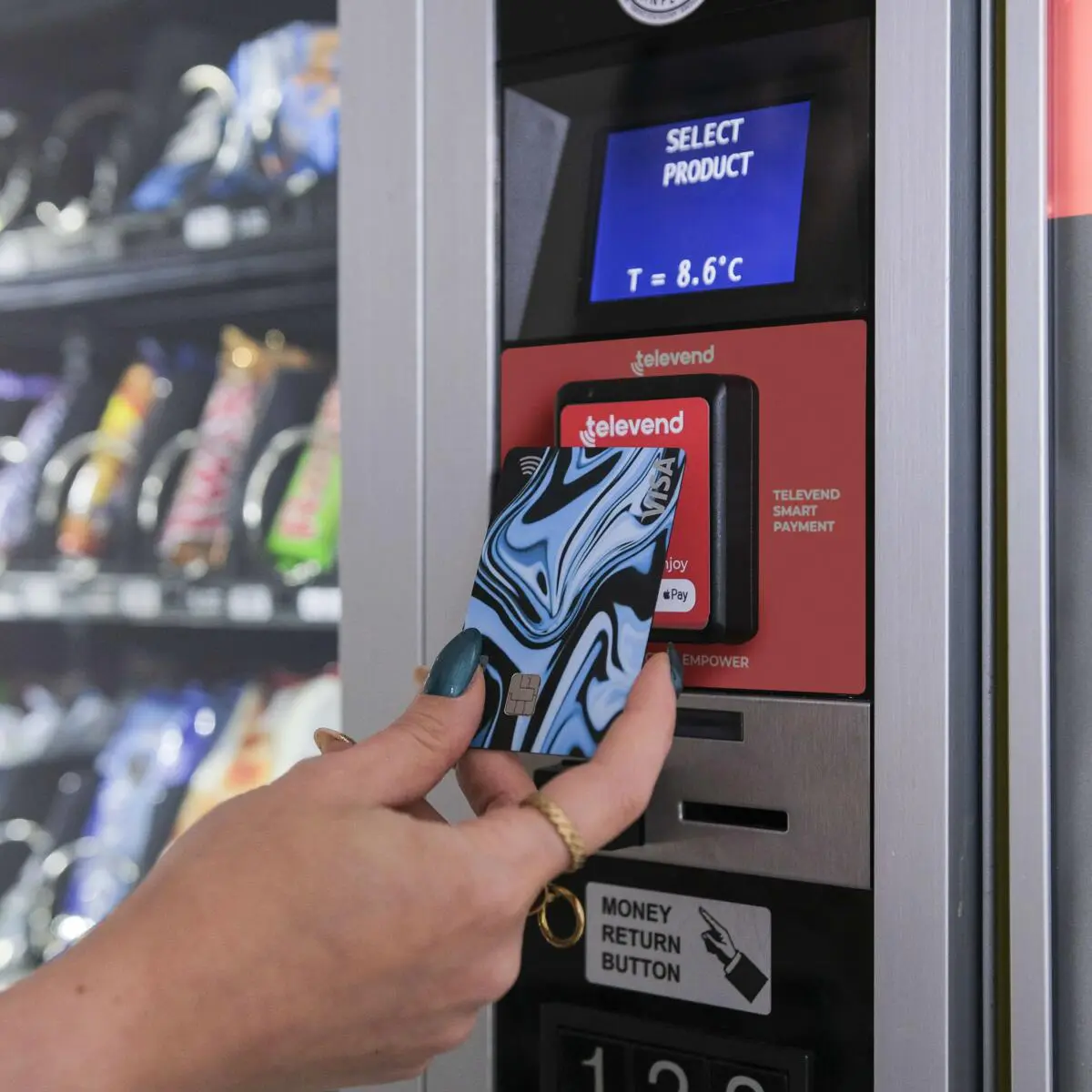
Illustrative Image (Source: Google Search)
Buyers should prioritize suppliers who hold certifications such as ISO 14001 (Environmental Management) and those that commit to using eco-friendly materials. For example, opting for machines constructed from recycled plastics not only reduces environmental impact but also aligns with corporate sustainability goals. Furthermore, machines that feature energy-saving components can significantly lower operational costs while contributing to a greener footprint.
By aligning purchasing decisions with sustainability objectives, international B2B buyers can enhance their brand reputation and meet the growing consumer demand for environmentally responsible products. Establishing partnerships with manufacturers that prioritize sustainability will ensure a competitive edge in a market that increasingly values ethical practices.
Brief Evolution/History
The cashless vending machine sector has evolved significantly since its inception in the late 20th century. Initially, vending machines operated solely on coin-based systems, limiting their convenience and accessibility. The early 2000s marked a pivotal shift with the introduction of credit card readers, paving the way for a gradual acceptance of electronic payments.
The rapid advancement of technology has since propelled the sector into a new era, characterized by the integration of mobile payment solutions and smart technology. Today’s machines are equipped with touch screens, AI-driven analytics, and remote management capabilities, allowing operators to optimize their offerings and enhance customer engagement. This evolution reflects a broader trend towards digital transformation across industries, positioning cashless vending machines as vital components of modern retail ecosystems.
Related Video: Global Trade & Logistics – What is Global Trade?
Frequently Asked Questions (FAQs) for B2B Buyers of cashless vending machine
-
What should I consider when vetting suppliers for cashless vending machines?
When vetting suppliers, prioritize their experience in the vending machine industry, especially regarding cashless technology. Look for suppliers with proven track records, positive client testimonials, and relevant certifications. Verify their compliance with local regulations in your target market, as this can affect product acceptance. Conduct background checks to ensure financial stability and reliability, and consider visiting their manufacturing facilities if possible. -
Can cashless vending machines be customized to meet specific needs?
Yes, many manufacturers offer customization options for cashless vending machines. This can include branding, size adjustments, and specific functionalities such as product offerings or payment methods. Discuss your requirements with potential suppliers early in the negotiation process to understand the extent of customization available and any associated costs. Ensure that the customization aligns with your target market’s preferences. -
What are the typical minimum order quantities (MOQ) and lead times for cashless vending machines?
Minimum order quantities can vary significantly by supplier, typically ranging from 10 to 100 units. Lead times also vary based on the complexity of the machines and customization requests, often taking between 4 to 12 weeks from order confirmation to delivery. Clarify these details upfront to align your purchasing strategy with your business needs, especially if you plan to enter a competitive market.
-
What payment options are available when sourcing cashless vending machines?
Payment options usually include bank transfers, letters of credit, and sometimes online payment platforms. Some suppliers may offer financing options or payment terms that allow for installment payments based on delivery milestones. Always negotiate payment terms that protect your investment, such as placing funds in escrow until the machines are delivered and meet quality standards. -
What quality assurance processes and certifications should I look for?
Look for suppliers that adhere to international quality standards such as ISO 9001. Certifications related to electrical safety, like CE or UL, are also critical, especially for European and North American markets. Ask about their quality control processes during production and post-manufacturing testing. A solid warranty and return policy can also indicate confidence in their product quality. -
How can I manage logistics when importing cashless vending machines?
Managing logistics involves coordinating with freight forwarders to handle customs clearance and shipping. Understand the shipping terms (like FOB or CIF) and ensure that the supplier provides the necessary documentation for a smooth import process. Factor in potential tariffs and duties applicable in your country. Establishing a reliable logistics partner can mitigate delays and ensure timely delivery. -
What steps should I take in case of disputes with a supplier?
In the event of a dispute, first, attempt to resolve the issue amicably through direct communication. If that fails, refer to your contract for clauses regarding dispute resolution, which may include mediation or arbitration. Document all communications and agreements related to the dispute. If necessary, consult legal counsel familiar with international trade laws to understand your options. -
What are the common challenges when sourcing cashless vending machines internationally?
Common challenges include navigating different regulatory environments, understanding local consumer preferences, and managing currency fluctuations. Additionally, language barriers can complicate negotiations. To mitigate these risks, conduct thorough market research and consider partnering with local distributors who understand the regional landscape. Establishing a clear line of communication with your supplier is crucial for overcoming these challenges.
Strategic Sourcing Conclusion and Outlook for cashless vending machine
In conclusion, the strategic sourcing of cashless vending machines presents a transformative opportunity for businesses across Africa, South America, the Middle East, and Europe. By prioritizing the adoption of cashless payment technologies, companies can enhance customer convenience, streamline operations, and ultimately boost sales. Key takeaways include the importance of evaluating suppliers based on technological capabilities, support services, and integration with existing systems.
Investing in cashless vending solutions is not merely a trend; it is a strategic move that aligns with global shifts towards digital transactions and contactless services. Buyers are encouraged to leverage this shift by conducting thorough market research, understanding regional payment preferences, and assessing the scalability of solutions to ensure long-term success.
As we look to the future, embracing cashless vending machines will be crucial in meeting the evolving demands of consumers and staying competitive in a rapidly changing marketplace. Now is the time for international B2B buyers to engage with suppliers, explore innovative solutions, and position themselves at the forefront of this cashless revolution.