Master the Business License for Vending Machine: Essential
Guide to Business License For Vending Machine
- Introduction: Navigating the Global Market for business license for vending machine
- Understanding business license for vending machine Types and Variations
- Key Industrial Applications of business license for vending machine
- Strategic Material Selection Guide for business license for vending machine
- In-depth Look: Manufacturing Processes and Quality Assurance for business license for vending machine
- Comprehensive Cost and Pricing Analysis for business license for vending machine Sourcing
- Spotlight on Potential business license for vending machine Manufacturers and Suppliers
- Essential Technical Properties and Trade Terminology for business license for vending machine
- Navigating Market Dynamics, Sourcing Trends, and Sustainability in the business license for vending machine Sector
- Frequently Asked Questions (FAQs) for B2B Buyers of business license for vending machine
- Strategic Sourcing Conclusion and Outlook for business license for vending machine
Introduction: Navigating the Global Market for business license for vending machine
In the dynamic world of vending machine operations, obtaining the correct business license is not just a regulatory requirement—it is a crucial step towards ensuring your venture’s success. For international B2B buyers, particularly those from regions such as Africa, South America, the Middle East, and Europe, understanding the nuances of licensing can mean the difference between a flourishing business and costly setbacks. This guide serves as a comprehensive resource for navigating the complexities of vending machine licensing, empowering you to make informed sourcing decisions.
The importance of a business license cannot be overstated. It legitimizes your operations, enhances your brand credibility, and protects you against potential legal issues. In this guide, we will delve into various aspects, including the types of licenses required, essential materials for compliance, manufacturing and quality control standards, and reliable suppliers. Additionally, we will provide insights into cost considerations, market trends, and a robust FAQ section to address common queries.
By equipping yourself with this knowledge, you will be better positioned to navigate the global vending machine market effectively. Whether you’re exploring opportunities in Poland, Spain, or beyond, this guide will help you streamline your licensing process, mitigate risks, and ultimately enhance your business’s operational efficiency.
Understanding business license for vending machine Types and Variations
Type Name | Key Distinguishing Features | Primary B2B Applications | Brief Pros & Cons for Buyers |
---|---|---|---|
General Vending License | Required for all vending machine operations | Retail, food and beverage services | Pros: Broad coverage for various products; Cons: May involve extensive paperwork and fees. |
Health Permits | Specific to food vending machines, ensuring health compliance | Food service, snack vending | Pros: Essential for food safety; Cons: Can be time-consuming to obtain and renew. |
Location-Specific Permits | Required for placing machines in certain locations | Public spaces, office buildings | Pros: Ensures legal placement; Cons: Varies by region, potentially increasing complexity. |
Sales Tax Permit | Required to collect sales tax on vending transactions | All vending operations | Pros: Necessary for compliance; Cons: Ongoing tax reporting requirements. |
Specialty Licenses | For unique products (e.g., alcohol, tobacco) in vending | Niche markets, specialized vending | Pros: Access to lucrative markets; Cons: Stricter regulations and higher costs. |
General Vending License
The General Vending License is a fundamental requirement for operating vending machines across various sectors. This license allows businesses to sell a wide range of products, from snacks to beverages. B2B buyers should consider the regulatory environment in their specific region, as the requirements can vary significantly. While this license provides broad operational flexibility, it often entails a lengthy application process and various fees, which can be a hurdle for new entrants.
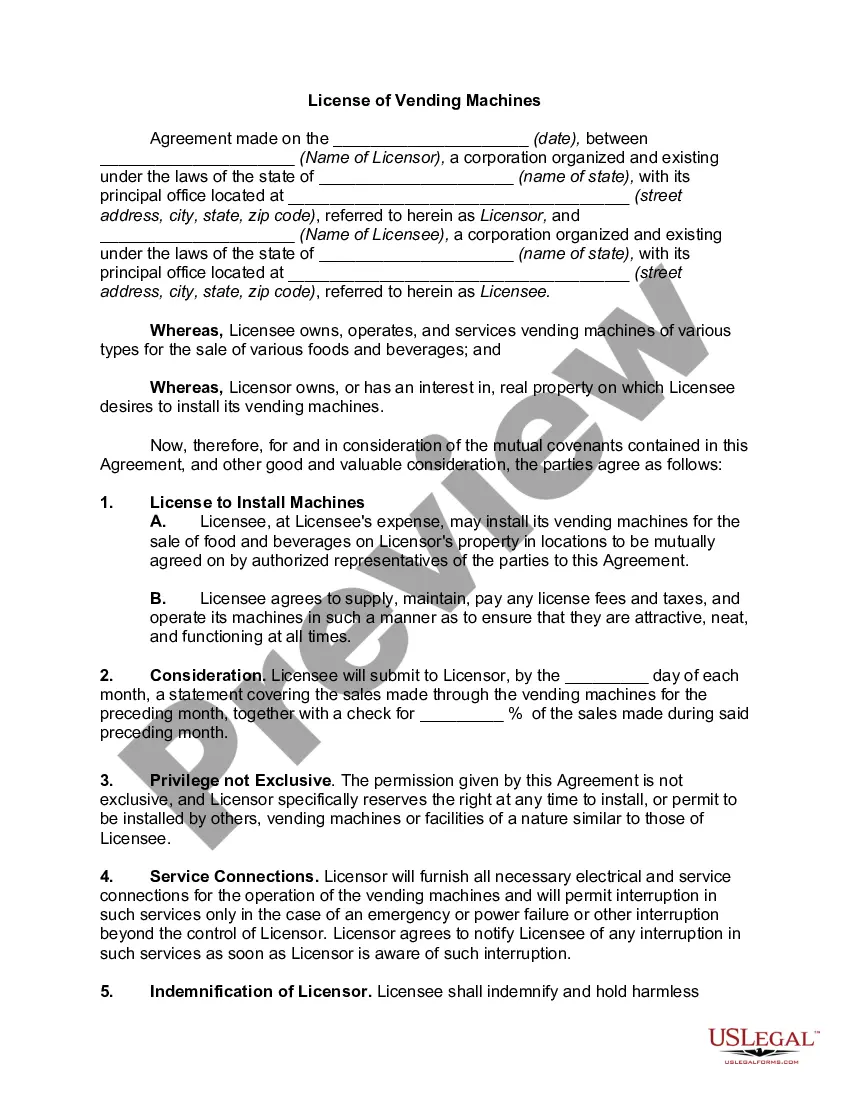
Illustrative Image (Source: Google Search)
Health Permits
Health permits are critical for vending machines that dispense food and beverages. These permits ensure compliance with local health regulations, safeguarding consumer health. Businesses in the food service industry must prioritize obtaining these permits, as they are essential for legal operation. While health permits validate the safety of food offerings, the process of securing and renewing them can be cumbersome and time-intensive, requiring careful planning by B2B buyers.
Location-Specific Permits
Location-specific permits are necessary for placing vending machines in public or private spaces, such as schools, parks, or office buildings. These permits ensure that the machines comply with local zoning laws and regulations. B2B buyers must be aware of the specific requirements in their intended locations, as these can differ widely. While securing these permits can validate the legitimacy of the vending operation, the varying regulations can complicate the setup process.
Sales Tax Permit
A Sales Tax Permit is essential for vending machine operators who sell taxable goods. This permit allows businesses to collect sales tax on transactions, ensuring compliance with tax regulations. It is crucial for all vending operations, as failure to obtain it can lead to penalties. While this permit is a straightforward requirement, it entails ongoing responsibilities for tax reporting and remittance, which can add administrative burdens for B2B buyers.
Specialty Licenses
Specialty licenses are required for vending machines that offer specific products, such as alcohol or tobacco. These licenses are crucial for businesses targeting niche markets and can open up lucrative opportunities. However, the regulations surrounding specialty licenses are often more stringent, requiring additional compliance measures. B2B buyers should weigh the potential profitability against the complexity and costs associated with obtaining these licenses, as they can significantly impact operational feasibility.
Related Video: The Explainer: What is a Business Model?
Key Industrial Applications of business license for vending machine
Industry/Sector | Specific Application of business license for vending machine | Value/Benefit for the Business | Key Sourcing Considerations for this Application |
---|---|---|---|
Retail | Automated retail solutions | Increases sales, reduces labor costs | Compliance with local regulations, payment systems |
Healthcare | Dispensing medical supplies | Provides 24/7 access to essential items | Licensing for pharmaceuticals, temperature control systems |
Education | Campus vending solutions | Enhances student convenience, increases campus revenue | Compliance with health and safety standards |
Transportation | Fuel vending stations | Streamlines refueling processes, reduces wait times | Licensing for fuel sales, environmental regulations |
Hospitality | Snack and beverage vending in hotels | Improves guest experience, generates additional income | Product variety, branding opportunities |
Retail: Automated Retail Solutions
In the retail sector, vending machines serve as automated retail solutions, providing quick access to a variety of products such as snacks, beverages, and personal care items. International B2B buyers must ensure that the business license for vending machines complies with local regulations, including health standards and payment processing requirements. This application allows retailers to operate with reduced labor costs while maximizing sales opportunities, especially in high-traffic areas.
Healthcare: Dispensing Medical Supplies
Vending machines in healthcare settings can dispense medical supplies, such as first aid kits, personal protective equipment, and over-the-counter medications. The business license is crucial for ensuring compliance with pharmaceutical regulations and ensuring that machines are equipped with temperature control systems for sensitive items. This application solves the problem of access to essential supplies outside regular hours, enhancing patient care and operational efficiency.
Education: Campus Vending Solutions
Educational institutions leverage vending machines to provide students with easy access to snacks and beverages on campus. The business license for vending machines in this sector must align with health regulations and consider the nutritional value of the products offered. This application not only enhances student convenience but also contributes to campus revenue through strategic placement in high-traffic areas.
Transportation: Fuel Vending Stations
Fuel vending stations represent a unique application of vending machines in the transportation sector, allowing drivers to refuel quickly and efficiently. A business license is necessary for compliance with local fuel sales regulations and environmental standards. This application addresses the need for streamlined refueling processes, reducing wait times for drivers and enhancing service delivery at transportation hubs.
Hospitality: Snack and Beverage Vending in Hotels
In the hospitality industry, vending machines provide guests with convenient access to snacks and beverages, enhancing their overall experience. The business license for these machines must consider local health and safety regulations, as well as product variety to meet diverse guest preferences. This application not only improves guest satisfaction but also generates additional income for hotels, making it a valuable investment for international B2B buyers.
Related Video: How to Start a Vending Machine Business, Cost, Tips, How Much You Make
Strategic Material Selection Guide for business license for vending machine
When selecting materials for vending machines, particularly for international B2B buyers, it is essential to consider various factors that impact performance, cost, and compliance with regional standards. The following analysis delves into three common materials used in the construction of vending machines, highlighting their properties, advantages, disadvantages, and considerations for international markets.
Stainless Steel
Key Properties:
Stainless steel is known for its excellent corrosion resistance, high strength, and durability. It can withstand a wide range of temperatures and pressures, making it suitable for various environments. The most common grades used in vending machines are 304 and 316, with 316 offering superior corrosion resistance, especially in coastal areas.
Pros & Cons:
Stainless steel is highly durable and requires minimal maintenance, which is a significant advantage for vending machine applications. However, it is more expensive than other materials, which can impact the overall cost of the vending machine. Manufacturing complexity can also be higher due to the need for specialized equipment for cutting and welding.
Impact on Application:
Stainless steel is compatible with a variety of media, including food and beverages, making it ideal for vending machines. Its non-reactive nature ensures that it does not impart any flavors or contaminants to the products stored within.
Considerations for International Buyers:
Buyers from regions such as Africa, South America, the Middle East, and Europe should ensure compliance with local health and safety standards. For instance, the European Union has strict regulations regarding food contact materials, which stainless steel meets. Buyers should also consider the availability of specific grades and their cost implications.
Aluminum
Key Properties:
Aluminum is lightweight, corrosion-resistant, and has good thermal conductivity. It is often used in the frames and panels of vending machines due to its favorable strength-to-weight ratio.
Pros & Cons:
The main advantage of aluminum is its low weight, which facilitates easier transportation and installation. However, it is less durable than stainless steel and may dent or scratch more easily. Additionally, while it is resistant to corrosion, it may require anodizing or coating for enhanced protection in harsh environments.
Impact on Application:
Aluminum is suitable for various applications, including non-food items, but may not be ideal for direct food contact unless properly treated. Its thermal properties can help in maintaining the temperature of refrigerated items.
Considerations for International Buyers:
International buyers should be aware of the specific alloys used, as they can vary widely in terms of strength and corrosion resistance. Compliance with standards such as ASTM for aluminum alloys is crucial, particularly in regions with stringent material regulations.
Plastic (Polycarbonate)
Key Properties:
Polycarbonate is a high-performance plastic known for its impact resistance and transparency. It can withstand temperatures up to 120°C and is often used for components such as windows and panels in vending machines.
Pros & Cons:
The primary advantage of polycarbonate is its lightweight nature and high impact resistance, making it less likely to shatter or break compared to glass. However, it can be less durable than metals and may degrade under UV exposure unless treated.
Impact on Application:
Polycarbonate is suitable for applications requiring visibility, such as display panels for food items. Its non-toxic nature makes it safe for food contact, provided it meets relevant safety standards.
Considerations for International Buyers:
For buyers in regions like Europe, compliance with REACH regulations regarding chemical safety is essential. Additionally, buyers should consider the environmental impact of plastic materials and the availability of recycling options in their regions.
Summary Table
Material | Typical Use Case for business license for vending machine | Key Advantage | Key Disadvantage/Limitation | Relative Cost (Low/Med/High) |
---|---|---|---|---|
Stainless Steel (304/316) | Structural components, food storage areas | Excellent durability and corrosion resistance | Higher cost and manufacturing complexity | High |
Aluminum | Frames and non-food contact areas | Lightweight and easy to transport | Less durable, may require coatings | Medium |
Plastic (Polycarbonate) | Display panels, protective covers | High impact resistance and visibility | Less durable than metals, UV degradation | Low |
This strategic material selection guide aims to provide actionable insights for international B2B buyers, ensuring they make informed decisions that align with their operational needs and compliance requirements.
In-depth Look: Manufacturing Processes and Quality Assurance for business license for vending machine
The manufacturing processes and quality assurance for vending machines are critical to ensuring reliability and compliance in the competitive B2B market. For international buyers, particularly from Africa, South America, the Middle East, and Europe, understanding these processes is essential to making informed purchasing decisions.
Manufacturing Processes
The production of vending machines involves several key stages:
1. Material Preparation
This initial phase focuses on sourcing high-quality materials that meet the specific requirements of the vending machines. Common materials include:
- Metal Components: Typically steel or aluminum for the frame and outer casing due to their durability.
- Plastic Parts: Used for internal components and aesthetic features, often requiring specific grades for strength and resistance to wear.
- Electronic Components: Such as payment systems and control boards, which must meet industry standards for functionality and security.
2. Forming
In this stage, raw materials undergo various processes to achieve the desired shapes and sizes. Key techniques include:
- Stamping: Used for creating metal panels and frames through a die and press.
- Injection Molding: Common for producing plastic components, allowing for complex shapes and high-volume production.
- Laser Cutting: Utilized for precision cutting of metal sheets, ensuring accurate dimensions.
3. Assembly
The assembly process combines all manufactured components into a final product. This stage typically involves:
- Automated Assembly Lines: Where machines assist in the rapid assembly of parts, enhancing efficiency.
- Manual Assembly: For intricate components that require skilled labor, particularly in the integration of electronic systems and final testing.
- Quality Checks During Assembly: To ensure that components fit correctly and function as intended, reducing the risk of defects.
4. Finishing
Finishing touches are applied to enhance durability and aesthetics. This may include:
- Painting or Powder Coating: To protect metal surfaces from corrosion and improve visual appeal.
- Surface Treatment: Such as anodizing or galvanizing to enhance the lifespan of components exposed to the elements.
- Final Assembly: Where additional features, such as branding and signage, are applied.
Quality Assurance
Quality assurance is paramount in the manufacturing of vending machines to ensure safety, reliability, and customer satisfaction. Key aspects include:
Relevant International Standards
International standards play a significant role in quality assurance. For vending machine manufacturing, the following are particularly relevant:
- ISO 9001: A globally recognized standard for quality management systems, ensuring that manufacturers maintain consistent quality and continuous improvement.
- CE Marking: Indicates compliance with European health, safety, and environmental protection standards, essential for machines sold in Europe.
- API Standards: Especially relevant for machines that dispense food or beverages, ensuring safety and hygiene in production.
Quality Control Checkpoints
Quality control (QC) checkpoints are strategically placed throughout the manufacturing process to catch defects early:
- Incoming Quality Control (IQC): Inspects raw materials and components upon arrival to ensure they meet specifications.
- In-Process Quality Control (IPQC): Conducts checks during the manufacturing process to monitor quality and prevent defects from progressing.
- Final Quality Control (FQC): A thorough inspection of the finished product before shipping, ensuring it meets all specifications and standards.
Common Testing Methods
Testing methods are crucial to validate the performance and safety of vending machines:
- Functional Testing: Ensures all electronic components work correctly, including payment systems and user interfaces.
- Stress Testing: Simulates extreme conditions to verify durability, such as temperature extremes and mechanical stress.
- Safety Testing: Assesses compliance with electrical safety standards to prevent hazards.
Verification of Supplier Quality Control
For B2B buyers, verifying a supplier’s quality control processes is essential to ensure product reliability. Here are effective methods:
- Supplier Audits: Conducting on-site audits allows buyers to assess the manufacturing processes and quality assurance systems in place.
- Quality Assurance Reports: Requesting detailed reports from suppliers can provide insights into their QC practices and compliance with international standards.
- Third-Party Inspections: Engaging independent inspection agencies can offer an unbiased evaluation of the manufacturing process and product quality.
Quality Control and Certification Nuances for International Buyers
International buyers must navigate various certifications and standards specific to their regions:
- Understanding Local Regulations: Different countries may have unique requirements for vending machines, particularly regarding food safety and electrical standards. Buyers must ensure compliance with local laws to avoid penalties.
- Cultural Considerations: Buyers from Africa, South America, the Middle East, and Europe may face different expectations regarding quality. Understanding these nuances can help in selecting the right supplier and product specifications.
- Language Barriers: Documentation and communication can pose challenges. Ensuring that suppliers provide information in a language that is clear to the buyer can mitigate misunderstandings.
In conclusion, a comprehensive understanding of the manufacturing processes and quality assurance practices for vending machines is crucial for international B2B buyers. By focusing on these aspects, buyers can make informed decisions that lead to successful long-term partnerships with suppliers, ensuring quality products that meet their specific needs.
Related Video: SMART Quality Control for Manufacturing
Comprehensive Cost and Pricing Analysis for business license for vending machine Sourcing
Understanding the cost structure and pricing dynamics of obtaining a business license for vending machine operations is crucial for international B2B buyers, especially those from Africa, South America, the Middle East, and Europe. The following analysis outlines the key cost components, price influencers, and strategic buyer tips.
Cost Components
-
Materials: The cost of materials primarily includes the necessary documentation and compliance-related materials required to apply for a business license. This could involve fees for legal consultations, document preparation, and submission.
-
Labor: Labor costs encompass the time spent by personnel in preparing, submitting, and following up on the license application. This could include administrative staff, legal advisors, or consultants specialized in local regulations.
-
Manufacturing Overhead: While not directly related to the license itself, understanding the overhead costs tied to vending machine production (if applicable) can provide insight into overall operational expenses. This includes utilities, rent, and administrative expenses.
-
Tooling: If specific adaptations or modifications are needed for vending machines to comply with local regulations, tooling costs may arise. This could involve customizing vending machines to meet health and safety standards.
-
Quality Control (QC): Ensuring that vending machines meet local standards often requires additional QC measures. This may involve fees for inspections or certifications to validate compliance with local laws.
-
Logistics: The costs associated with transporting the vending machines to their intended locations after obtaining the license should also be considered. This includes shipping fees, customs duties, and any other logistics-related expenses.
-
Margin: Suppliers may include a profit margin in their pricing, which can vary significantly based on their operational costs, market demand, and competition.
Price Influencers
-
Volume/MOQ (Minimum Order Quantity): Larger orders often attract bulk pricing discounts, making it essential for buyers to consider their purchasing strategy.
-
Specifications/Customization: Customized vending machines may incur additional costs. Buyers should clearly define their specifications to avoid unexpected expenses.
-
Materials: The choice of materials used in vending machine production can influence both the initial cost and the long-term maintenance expenses. Higher-quality materials may lead to increased upfront costs but can reduce maintenance and repair costs over time.
-
Quality/Certifications: Compliance with local regulations may require specific certifications, which can add to the cost. Buyers should verify what certifications are necessary in their target markets.
-
Supplier Factors: Supplier reputation, location, and reliability can affect pricing. Local suppliers might offer more competitive prices due to lower logistics costs, while international suppliers might provide better technology or unique designs.
-
Incoterms: Understanding Incoterms (International Commercial Terms) is vital as they define responsibilities for shipping, insurance, and tariffs. This knowledge can help buyers negotiate better terms and avoid hidden costs.
Buyer Tips
-
Negotiation: Always negotiate pricing with suppliers. Many suppliers have flexibility in their pricing, especially for larger orders or long-term contracts.
-
Cost Efficiency: Look beyond the initial price. Consider the Total Cost of Ownership (TCO), which includes maintenance, energy consumption, and potential downtime costs.
-
Pricing Nuances: Buyers from different regions may face unique pricing challenges. For example, tariffs and import duties can significantly affect the cost for buyers in Africa and South America, whereas European buyers may need to consider VAT and local taxes.
-
Research Local Regulations: Understanding local laws and regulations can help avoid additional fees or penalties. This knowledge can also aid in negotiating better terms with suppliers who are familiar with compliance requirements.
Disclaimer
Prices for business licenses and vending machines can vary widely based on numerous factors, including regional regulations and market conditions. Buyers should conduct thorough research and seek quotes from multiple suppliers to obtain accurate pricing tailored to their specific needs.
Spotlight on Potential business license for vending machine Manufacturers and Suppliers
This section offers a look at a few manufacturers active in the ‘business license for vending machine’ market. This is a representative sample for illustrative purposes; B2B buyers must conduct their own extensive due diligence before any engagement. Information is synthesized from public sources and general industry knowledge.
Essential Technical Properties and Trade Terminology for business license for vending machine
Key Technical Properties for Vending Machines
When considering the acquisition of vending machines, understanding specific technical properties is essential for making informed purchasing decisions. Here are several critical specifications to keep in mind:
-
Material Grade
Vending machines are typically constructed from stainless steel or high-grade plastic. Stainless steel offers durability and resistance to corrosion, making it ideal for high-traffic environments. In contrast, high-grade plastic may be lighter and less expensive but could be more susceptible to wear and tear. Selecting the appropriate material is crucial for ensuring longevity and minimizing maintenance costs. -
Power Requirements
Understanding the power consumption of vending machines is vital for operational planning. Most machines require a standard voltage of 110V or 220V, depending on the region. This specification influences installation costs and energy efficiency. Buyers should assess the energy consumption rates to evaluate potential operating expenses.
-
Capacity and Size
The capacity, often measured in the number of items the machine can hold, is a significant factor. Machines vary in size from compact models that fit in small spaces to larger units designed for high-demand environments. Buyers should consider the space available and the expected foot traffic to select a machine that meets their needs without overextending their resources. -
Temperature Control
For vending machines that dispense perishable items, effective temperature control is critical. Machines should have built-in refrigeration systems that maintain optimal temperatures for food safety and quality. Understanding the refrigeration capacity and cooling efficiency can help buyers ensure compliance with local health regulations. -
User Interface
The user interface, including touch screens or keypad designs, affects customer interaction. Intuitive interfaces enhance user experience and can lead to increased sales. Buyers should evaluate the ease of use and accessibility, especially for diverse customer demographics. -
Payment Systems
Modern vending machines often integrate various payment options, including cash, credit/debit cards, and mobile payment systems. Understanding the payment capabilities is essential for meeting customer preferences and maximizing sales opportunities.
Common Trade Terminology
Familiarity with industry jargon is essential for effective communication during transactions. Here are several common terms that international B2B buyers should know:
-
OEM (Original Equipment Manufacturer)
An OEM refers to a company that produces parts or equipment that may be marketed by another manufacturer. In the vending machine industry, OEMs often provide components such as payment systems or refrigeration units, allowing businesses to customize machines according to their specifications. -
MOQ (Minimum Order Quantity)
MOQ denotes the smallest number of units a supplier is willing to sell. Understanding the MOQ is crucial for budgeting and inventory management, especially for smaller businesses looking to enter the vending machine market. -
RFQ (Request for Quotation)
An RFQ is a document sent to suppliers requesting pricing information for specific products or services. This formal request enables buyers to compare costs and terms from various vendors, facilitating informed purchasing decisions. -
Incoterms
Incoterms are international commercial terms that define the responsibilities of buyers and sellers in a transaction. They specify who is responsible for shipping, insurance, and tariffs, which is vital for managing logistics and cost expectations in international trade. -
Lead Time
Lead time refers to the period between placing an order and receiving the goods. Understanding lead times is essential for inventory planning and ensuring that vending machines are available when needed. -
Warranty
A warranty is a guarantee provided by the manufacturer regarding the repair or replacement of a product within a specified period. Buyers should always inquire about warranty terms to protect their investment and ensure support for any potential issues.
By comprehensively understanding these technical specifications and trade terms, international B2B buyers can navigate the vending machine market more effectively, ensuring they make well-informed decisions that align with their business needs.
Navigating Market Dynamics, Sourcing Trends, and Sustainability in the business license for vending machine Sector
Market Overview & Key Trends
The global vending machine market is experiencing significant growth, driven by the increasing demand for convenience and automation in retail. This trend is particularly evident in urban areas across Africa, South America, the Middle East, and Europe, where busy lifestyles necessitate quick and easy access to products. Notably, advancements in technology are reshaping the sector; for instance, cashless payment systems and IoT-enabled machines are becoming standard. These innovations enhance user experience and provide operators with valuable data analytics to optimize inventory and sales strategies.
Emerging B2B tech trends include the integration of artificial intelligence (AI) and machine learning for predictive analytics, enabling businesses to forecast demand accurately and tailor their offerings accordingly. Furthermore, sustainability is increasingly influencing purchasing decisions, as buyers look for machines that support eco-friendly practices. This is evident in the rise of energy-efficient machines and those utilizing recyclable materials, aligning with a broader shift towards sustainability in the B2B landscape.
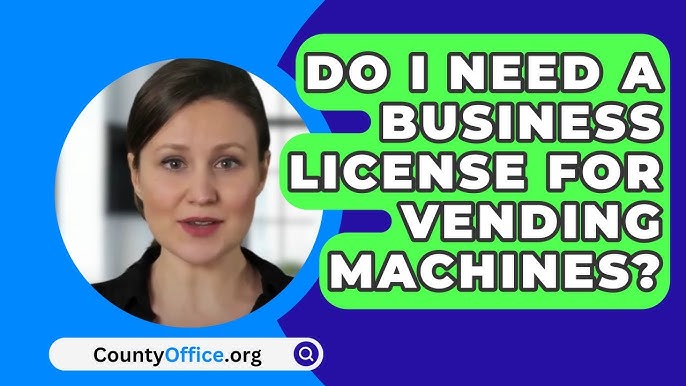
Illustrative Image (Source: Google Search)
International B2B buyers should also consider regional regulations and compliance requirements when sourcing vending machines. For example, in Europe, compliance with EU standards for energy efficiency and product safety is mandatory. Understanding these market dynamics is crucial for making informed sourcing decisions and establishing a competitive edge.
Sustainability & Ethical Sourcing in B2B
Sustainability in the vending machine sector is not merely a trend but a necessity, as environmental concerns take center stage globally. The production and operation of vending machines can have significant environmental impacts, including energy consumption and waste generation. Consequently, B2B buyers are increasingly prioritizing suppliers who demonstrate a commitment to sustainable practices. This includes using energy-efficient components, minimizing plastic use, and opting for materials that are recyclable or biodegradable.
Ethical sourcing is another critical consideration. Buyers are encouraged to partner with manufacturers that maintain transparent supply chains and adhere to fair labor practices. Implementing sustainability certifications, such as ISO 14001 for environmental management, can further assure buyers of a supplier’s commitment to responsible sourcing.
Moreover, utilizing ‘green’ materials and technologies in vending machine production, such as solar-powered units or those that use eco-friendly refrigerants, can significantly reduce the carbon footprint. For businesses looking to enhance their brand reputation and attract eco-conscious consumers, integrating sustainability into their sourcing strategy is not just beneficial—it’s essential.
Brief Evolution/History
The vending machine industry has evolved significantly since its inception in the late 19th century, when the first machines dispensed simple items like postcards and chewing gum. Over the decades, the sector has expanded to include a vast array of products, from snacks and beverages to electronics and personal care items. The introduction of electronic payment systems in the 1980s revolutionized the industry, making machines more user-friendly and versatile.
In recent years, the focus has shifted towards technology-driven solutions, with innovations such as touchless payments and remote monitoring systems gaining traction. This evolution reflects broader consumer trends towards convenience and immediacy, positioning vending machines as a crucial component of modern retail strategies. As the market continues to adapt to new consumer demands and technological advancements, B2B buyers must stay informed about historical shifts to effectively navigate future opportunities.
Related Video: Incoterms for beginners | Global Trade Explained
Frequently Asked Questions (FAQs) for B2B Buyers of business license for vending machine
-
What are the key steps to vetting suppliers for vending machine business licenses?
When vetting suppliers, ensure they are licensed and registered in their respective countries. Request references and case studies from previous clients to assess their reliability. It’s crucial to verify their compliance with local regulations, especially regarding health and safety standards. Additionally, evaluate their experience with international buyers and their ability to meet specific market needs. -
Can I customize the vending machines according to my market’s preferences?
Yes, many suppliers offer customization options for vending machines, including product selection, branding, and machine design. It’s essential to communicate your specific requirements clearly during the negotiation phase. Ensure the supplier has a proven track record of successful custom projects to minimize risks and enhance customer satisfaction. -
What are the typical minimum order quantities (MOQs) and lead times for vending machines?
MOQs can vary widely depending on the supplier and the level of customization. Typically, expect MOQs to range from 5 to 50 machines. Lead times may also differ based on production schedules and shipping logistics; they can range from 4 to 12 weeks. Always confirm these details upfront to align your inventory strategy with the supplier’s capabilities. -
What payment terms are common when sourcing vending machine licenses?
Payment terms can vary based on the supplier’s policies and your negotiation. Common options include a 30% deposit upon order confirmation, with the remaining balance due before shipment. Some suppliers may offer credit terms for established buyers. Always ensure that payment methods are secure and that you have a clear understanding of any potential additional costs, such as shipping and customs fees. -
How can I ensure quality assurance and certifications for vending machines?
Request documentation that verifies the supplier’s compliance with international quality standards, such as ISO certifications. It’s advisable to conduct pre-shipment inspections to ensure that the machines meet your specifications and quality expectations. Additionally, inquire about warranty and service agreements to protect your investment. -
What logistical considerations should I be aware of when importing vending machines?
Logistics can be complex, especially when dealing with international suppliers. Ensure you understand the shipping terms (e.g., FOB, CIF) and the responsibilities for customs clearance. Work with a freight forwarder experienced in handling machinery imports to navigate regulations effectively. Be mindful of potential delays due to customs inspections or local regulations in your target market. -
How should I handle disputes with suppliers regarding vending machine orders?
To manage disputes effectively, establish clear terms and conditions in your contract, including dispute resolution mechanisms. Maintain open lines of communication with your supplier to address issues promptly. If a dispute arises, document all correspondence and agreements, and consider involving a neutral third party or arbitration if necessary. -
Are there specific regulations I need to comply with when operating vending machines in different countries?
Yes, regulations can vary significantly by country and region. Common requirements include obtaining local business licenses, adhering to health and safety regulations, and ensuring compliance with consumer protection laws. Research the specific legal obligations in your target market, and consult with local legal experts to avoid potential fines or operational disruptions.
Strategic Sourcing Conclusion and Outlook for business license for vending machine
In summary, navigating the complexities of obtaining a business license for vending machines is crucial for international B2B buyers seeking to expand their operations in diverse markets. Key takeaways include understanding local regulations, engaging with reliable suppliers, and leveraging strategic sourcing practices to optimize procurement processes.
By prioritizing strategic sourcing, businesses can significantly enhance operational efficiency and ensure compliance with regulatory standards. This approach not only mitigates risks but also opens avenues for innovation and growth.
As you consider entering or expanding in markets across Africa, South America, the Middle East, and Europe, it is essential to conduct thorough market research and establish strong local partnerships. Investing in these relationships will not only facilitate smoother licensing processes but also position your business for long-term success.
Looking ahead, now is the time to act. Embrace the opportunities presented by the vending machine industry and leverage the insights gained from strategic sourcing to create a robust framework for your business. Take the next steps in your journey with confidence, and make informed decisions that will shape the future of your operations.