Master the Art of Sourcing Vending Machine Locksmith
Guide to Vending Machine Locksmith
- Introduction: Navigating the Global Market for vending machine locksmith
- Understanding vending machine locksmith Types and Variations
- Key Industrial Applications of vending machine locksmith
- Strategic Material Selection Guide for vending machine locksmith
- In-depth Look: Manufacturing Processes and Quality Assurance for vending machine locksmith
- Comprehensive Cost and Pricing Analysis for vending machine locksmith Sourcing
- Spotlight on Potential vending machine locksmith Manufacturers and Suppliers
- Essential Technical Properties and Trade Terminology for vending machine locksmith
- Navigating Market Dynamics, Sourcing Trends, and Sustainability in the vending machine locksmith Sector
- Frequently Asked Questions (FAQs) for B2B Buyers of vending machine locksmith
- Strategic Sourcing Conclusion and Outlook for vending machine locksmith
Introduction: Navigating the Global Market for vending machine locksmith
Navigating the global market for vending machine locksmith services is crucial for businesses looking to enhance security, improve operational efficiency, and safeguard their investments in vending equipment. As the vending industry continues to grow, the need for specialized locksmith services that cater specifically to vending machines has never been more significant. These services not only protect against theft and vandalism but also ensure the seamless operation of vending machines, which are vital revenue-generating assets.
This comprehensive guide aims to equip international B2B buyers—particularly those from Africa, South America, the Middle East, and Europe (including Turkey and Poland)—with the essential knowledge to make informed sourcing decisions. We will explore various types of locksmith services tailored for vending machines, the materials used in manufacturing locks, quality control standards, and an overview of reputable suppliers in the market. Additionally, we will delve into cost considerations and market trends that could impact your procurement strategy.
By providing answers to frequently asked questions and actionable insights, this guide empowers buyers to navigate the complexities of the vending machine locksmith market confidently. Whether you are a distributor, operator, or service provider, understanding these elements will help you optimize your operations and enhance the security of your vending assets.
Understanding vending machine locksmith Types and Variations
Type Name | Key Distinguishing Features | Primary B2B Applications | Brief Pros & Cons for Buyers |
---|---|---|---|
Standard Vending Machine Lock | Mechanical lock with basic security features | General vending operations | Pros: Cost-effective, easy to replace. Cons: Basic security may be insufficient for high-value products. |
Electronic Lock | Keypad or card-based access with programmable features | High-security environments, tech-savvy locations | Pros: Enhanced security, customizable access. Cons: Higher initial cost, requires power source. |
Combination Lock | Mechanical or digital combinations for access | Locations requiring moderate security | Pros: No keys needed, can be reset. Cons: Possible lockout if combinations are forgotten. |
Smart Lock | IoT-enabled locks with remote access capabilities | Modern businesses, mobile vending units | Pros: Remote management, real-time monitoring. Cons: Vulnerable to cyber threats, requires tech support. |
High-Security Lock | Advanced locking mechanisms with anti-drill features | High-value merchandise, sensitive environments | Pros: Maximum security, durable materials. Cons: Expensive, may require specialized installation. |
Standard Vending Machine Lock
Standard vending machine locks are the most common type found in vending operations. They typically feature a mechanical design that requires a key for access. These locks are suitable for low to moderate security needs, making them ideal for general vending applications. When considering a purchase, buyers should evaluate the balance between cost and security, as these locks are easy to replace but may not adequately protect high-value products.
Electronic Lock
Electronic locks utilize keypads or card access systems, providing a higher level of security compared to standard locks. These locks are programmable, allowing businesses to manage access permissions easily. They are particularly useful in high-security environments or tech-savvy locations where enhanced security is paramount. Buyers should weigh the benefits of increased security against the higher initial investment and the necessity of a power source.
Combination Lock
Combination locks can be mechanical or digital, requiring users to input a specific sequence to gain access. This type of lock eliminates the need for physical keys, which can be lost or stolen. Combination locks are suitable for locations that require moderate security. However, buyers must consider the risk of lockout if the combination is forgotten, which could lead to operational disruptions.
Smart Lock
Smart locks are the latest innovation in vending machine security, integrating IoT technology to offer remote access and monitoring capabilities. These locks are ideal for modern businesses and mobile vending units, allowing for real-time management of access permissions. While smart locks offer significant advantages, such as convenience and enhanced security, buyers should be aware of potential cyber threats and the need for ongoing technical support.
High-Security Lock
High-security locks feature advanced mechanisms designed to resist tampering and unauthorized access, often incorporating anti-drill and anti-pick features. These locks are best suited for environments where high-value merchandise is stored or sensitive operations are conducted. While they provide maximum security, buyers should be prepared for a higher upfront cost and the possibility of requiring specialized installation services.
Related Video: Machine Learning in 2024 – Beginner’s Course
Key Industrial Applications of vending machine locksmith
Industry/Sector | Specific Application of vending machine locksmith | Value/Benefit for the Business | Key Sourcing Considerations for this Application |
---|---|---|---|
Retail | Securing vending machines in high-traffic areas | Reduces theft, increases customer trust | Compatibility with various vending machine models |
Education | Locking mechanisms for campus vending machines | Ensures safety and accessibility for students | Durability and ease of use in high-traffic environments |
Hospitality | Access control for hotel room vending machines | Enhances guest experience and security | Customization options for different machine types |
Transportation | Locking systems for vending machines at transit hubs | Improves security and reduces operational losses | Compliance with local regulations and standards |
Healthcare | Vending machines in hospitals and clinics | Provides reliable access to essentials for patients | Hygiene standards and ease of maintenance |
In the retail sector, vending machine locksmiths play a crucial role in securing machines located in high-traffic areas. By ensuring that vending machines are properly locked, businesses can significantly reduce theft and vandalism. This not only protects inventory but also fosters customer trust, as shoppers feel more secure purchasing from machines that are well-maintained. Buyers in this sector should consider compatibility with various vending machine models to ensure effective security solutions.
Within educational institutions, vending machine locksmiths are essential for managing access to machines on campus. These locksmiths provide locking mechanisms that ensure safety and accessibility for students, particularly in areas that experience heavy foot traffic. For international buyers in regions like Africa and South America, durability and ease of use are critical factors, as machines often endure high usage rates.
In the hospitality industry, locksmiths are responsible for access control on vending machines located in hotels. By implementing secure locking systems, hotels can enhance the guest experience, ensuring that guests have reliable access to snacks and beverages while maintaining security. Buyers should prioritize customization options to cater to different machine types and hotel aesthetics, ensuring a seamless integration into the hotel’s overall design.
For the transportation sector, vending machine locksmiths help secure machines located at transit hubs, such as airports and train stations. These systems improve overall security and help reduce operational losses due to theft. B2B buyers must consider local regulations and standards when sourcing these locksmith solutions to ensure compliance and effectiveness in their specific environment.
In healthcare, vending machine locksmiths are vital for machines located in hospitals and clinics, providing patients and staff with reliable access to essential items. The key benefit here is ensuring that these machines remain secure while still being accessible to those in need, particularly in high-stress situations. Buyers should focus on hygiene standards and ease of maintenance when selecting locksmith solutions, as these factors are crucial in a healthcare setting where cleanliness is paramount.
Related Video: What is Industrial Automation?
Strategic Material Selection Guide for vending machine locksmith
When selecting materials for vending machine locksmith applications, it is essential to consider properties that directly influence performance, durability, and cost-effectiveness. The following analysis focuses on four common materials used in this field: stainless steel, brass, aluminum, and carbon steel. Each material has distinct characteristics, advantages, and limitations that international B2B buyers should evaluate based on their specific operational requirements and regional standards.
Stainless Steel
Key Properties: Stainless steel exhibits excellent corrosion resistance, high tensile strength, and can withstand a wide range of temperatures. Its ability to resist rust and staining makes it ideal for environments exposed to moisture.
Pros & Cons: The durability of stainless steel is a significant advantage, as it can endure harsh conditions without degrading. However, it tends to be more expensive than other materials, which can impact overall project costs. Manufacturing complexity is moderate, as it requires specialized equipment for cutting and shaping.
Impact on Application: Stainless steel is compatible with various media and is particularly suitable for environments where hygiene is crucial, such as in food vending machines.
Considerations for International Buyers: Buyers from regions like Europe and the Middle East should ensure compliance with standards such as ASTM A240 for stainless steel sheet and plate. The availability of different grades (e.g., 304, 316) may also influence selection based on local corrosion resistance needs.
Brass
Key Properties: Brass is known for its excellent machinability and corrosion resistance, particularly in water applications. It has a lower melting point compared to stainless steel, which facilitates easier manufacturing.
Pros & Cons: The primary advantage of brass is its aesthetic appeal and antimicrobial properties, making it a preferred choice for visible components. However, it is less durable than stainless steel and can corrode in salty or acidic environments, which limits its use in certain applications.
Impact on Application: Brass is often used for locks and fittings due to its good mechanical properties and resistance to wear.
Considerations for International Buyers: Buyers should be aware of the different brass compositions (e.g., C36000, C37700) and their respective compliance with standards like ASTM B16. In regions like Africa and South America, local sourcing of brass may vary, impacting lead times and costs.
Aluminum
Key Properties: Aluminum is lightweight, resistant to corrosion, and has good thermal conductivity. It is often anodized for enhanced surface protection.
Pros & Cons: The lightweight nature of aluminum makes it ideal for portable vending machines. However, its lower strength compared to steel can be a disadvantage in high-security applications. Manufacturing processes are generally straightforward, allowing for cost-effective production.
Impact on Application: Aluminum is suitable for components that do not require high strength but benefit from reduced weight, such as housing or panels.
Considerations for International Buyers: Compliance with standards like ASTM B221 is essential for ensuring quality. In Europe, buyers should consider the implications of the EU’s REACH regulations concerning aluminum alloys.
Carbon Steel
Key Properties: Carbon steel is known for its high strength and toughness, making it suitable for heavy-duty applications. However, it is susceptible to corrosion if not properly treated.
Pros & Cons: The primary advantage of carbon steel is its cost-effectiveness and strength. However, its susceptibility to rust can be a significant drawback, particularly in humid environments.
Impact on Application: Carbon steel is often used in structural components of vending machines where strength is paramount, but it requires protective coatings to prevent corrosion.
Considerations for International Buyers: Buyers should ensure compliance with standards such as ASTM A36. In regions with high humidity, like parts of Africa and South America, additional protective measures may be necessary.
Summary Table
Material | Typical Use Case for vending machine locksmith | Key Advantage | Key Disadvantage/Limitation | Relative Cost (Low/Med/High) |
---|---|---|---|---|
Stainless Steel | Locks, panels, and structural components | Excellent corrosion resistance | Higher cost compared to other materials | High |
Brass | Locks and fittings | Aesthetic appeal and antimicrobial | Less durable, susceptible to corrosion | Medium |
Aluminum | Housing and panels for lightweight applications | Lightweight and corrosion-resistant | Lower strength compared to steel | Low |
Carbon Steel | Structural components requiring high strength | Cost-effective and strong | Susceptible to corrosion without treatment | Low |
This strategic material selection guide provides essential insights for international B2B buyers, enabling them to make informed decisions based on performance requirements, cost considerations, and compliance with regional standards.
In-depth Look: Manufacturing Processes and Quality Assurance for vending machine locksmith
The manufacturing processes and quality assurance protocols for vending machine locks are critical for ensuring product reliability and longevity. For B2B buyers, especially those operating in diverse markets such as Africa, South America, the Middle East, and Europe, understanding these processes can aid in making informed procurement decisions. This section delves into the main stages of manufacturing, key techniques employed, relevant quality control standards, and actionable insights for verifying supplier quality.
Manufacturing Processes
1. Material Preparation
The first stage involves selecting appropriate materials that meet the strength and durability requirements of vending machine locks. Common materials include:
- Zinc Alloy: Offers good corrosion resistance and is cost-effective.
- Stainless Steel: Provides higher durability and resistance to tampering.
- Plastic Composites: Used for internal components, offering lightweight and cost benefits.
During this stage, suppliers should ensure that materials are sourced from reputable vendors, backed by certificates of conformity to guarantee quality.
2. Forming
Once materials are prepared, they undergo various forming processes, which may include:
- Casting: Molten metal is poured into molds to create lock housings.
- Machining: Processes like milling and turning are employed to create precision parts. This is crucial for the lock mechanism, where tolerances must be tight to prevent jamming or failure.
- Stamping: Used for creating flat components from metal sheets, which are then shaped into parts of the lock assembly.
These processes require advanced machinery and skilled operators to ensure consistency and precision in production.
3. Assembly
In the assembly phase, individual components are brought together to create the final product. Key techniques include:
- Automated Assembly: Robotics may be used for high-volume production, increasing efficiency and reducing human error.
- Manual Assembly: In cases where precision is paramount, skilled labor is utilized to assemble intricate lock mechanisms.
Effective assembly lines should include visual aids and standardized work procedures to ensure quality and speed.
4. Finishing
The finishing stage involves several treatments to enhance the lock’s durability and aesthetics:
- Plating: Electroplating with materials like nickel or chrome provides corrosion resistance and a polished appearance.
- Coating: Powder coating or painting can be applied for additional protection against environmental factors.
- Quality Inspection: Each lock should undergo inspection for surface defects, proper functioning, and adherence to specifications.
Quality Assurance
International Standards
For B2B buyers, adherence to international quality standards is essential. The following certifications are relevant:
- ISO 9001: This standard ensures that a company has a quality management system in place. It covers all aspects of production, from material selection to customer service.
- CE Marking: Required for products sold within the European Economic Area, indicating conformity with health, safety, and environmental protection standards.
- API Certification: Relevant for locks used in specific industries, such as oil and gas, where additional safety and quality measures are necessary.
Quality Control Checkpoints
Quality control should be integrated at multiple stages of the manufacturing process:
- Incoming Quality Control (IQC): Inspect raw materials upon receipt to ensure they meet specified standards.
- In-Process Quality Control (IPQC): Conduct inspections during production to catch defects early. This includes monitoring dimensions, tolerances, and assembly techniques.
- Final Quality Control (FQC): Before shipping, each lock should undergo a comprehensive inspection to ensure it meets all specifications and functions correctly.
Common Testing Methods
Testing methods for vending machine locks typically include:
- Functional Testing: Ensuring that locks operate correctly under simulated conditions.
- Durability Testing: Subjecting locks to stress tests to evaluate their performance over time.
- Corrosion Testing: Exposing locks to various environmental conditions to assess resistance to rust and degradation.
Verifying Supplier Quality
B2B buyers must actively verify the quality assurance practices of their suppliers. Key actions include:
- Supplier Audits: Conduct regular audits of suppliers to assess their compliance with quality standards. This can include reviewing their quality management system and manufacturing practices.
- Quality Reports: Request documentation that outlines the quality control processes in place, including records of inspections and testing results.
- Third-Party Inspections: Engage independent inspection services to evaluate the quality of products before shipment, ensuring they meet specified standards.
Regional Considerations
For international buyers, particularly in Africa, South America, the Middle East, and Europe, understanding regional standards and practices is crucial. Each region may have specific requirements and expectations regarding product quality and certification. For instance, buyers in Europe should prioritize CE marking, while those in the Middle East might focus on local certifications that ensure compliance with regional safety standards.
Conclusion
A comprehensive understanding of manufacturing processes and quality assurance practices is essential for B2B buyers in the vending machine locksmith sector. By focusing on material preparation, forming, assembly, and finishing, along with adherence to international standards, buyers can ensure they source reliable and durable products. Implementing robust verification processes will further enhance confidence in supplier capabilities, leading to better procurement decisions and long-term partnerships.
Related Video: SMART Quality Control for Manufacturing
Comprehensive Cost and Pricing Analysis for vending machine locksmith Sourcing
Understanding the Cost Structure of Vending Machine Locksmith Services
When sourcing vending machine locksmith services, it’s essential for international B2B buyers to grasp the cost structure involved. This understanding aids in budgeting, negotiation, and ultimately securing a favorable deal. The primary cost components include:
-
Materials: These encompass the cost of locks, electronic components, and any specialized parts required for specific vending machine models. The choice of materials can significantly affect both quality and price.
-
Labor: Skilled locksmith labor is a significant portion of the cost. Labor rates can vary widely based on geographic location and the skill level of technicians. For instance, labor in Europe may be more expensive compared to Africa or South America.
-
Manufacturing Overhead: This includes the costs associated with running the locksmithing operation, such as utilities, rent, and administrative expenses. Efficient overhead management can help suppliers offer more competitive pricing.
-
Tooling: The initial investment in specialized tools and equipment required for locksmithing services also contributes to costs. This may involve one-time expenses or ongoing maintenance costs.
-
Quality Control (QC): Ensuring that products meet safety and performance standards incurs costs related to inspections, testing, and certifications. High-quality locksmith services often have stringent QC processes, which can increase overall costs.
-
Logistics: Shipping and handling costs, especially for international orders, must be factored in. This includes customs duties, freight charges, and local transportation.
-
Margin: Suppliers typically add a profit margin to cover their costs and ensure sustainability. This margin can vary widely based on competition, service reputation, and geographical market conditions.
Price Influencers in Vending Machine Locksmith Sourcing
Several factors influence the pricing of locksmith services, and understanding these can provide a competitive edge for buyers:
-
Volume/MOQ: Purchasing in bulk often leads to reduced per-unit costs. Suppliers may offer better pricing for larger orders or long-term contracts.
-
Specifications/Customization: Custom locks or specialized services tailored to specific vending machines can significantly affect pricing. The more unique the requirement, the higher the cost may be.
-
Materials: The choice of high-quality materials will increase costs, but they may offer better longevity and security, ultimately saving money in the long run.
-
Quality/Certifications: Products that meet international standards or possess specific certifications (e.g., ISO) may come at a premium but offer assurances of quality and reliability.
-
Supplier Factors: The reputation, location, and financial stability of the supplier can also influence pricing. Established suppliers with a track record of reliability might charge more due to their reputation and service quality.
-
Incoterms: International buyers should be aware of Incoterms as they define the responsibilities of buyers and sellers in shipping arrangements. Understanding these can help avoid unexpected costs.
Buyer Tips for Effective Sourcing
For international B2B buyers, especially from Africa, South America, the Middle East, and Europe (e.g., Turkey, Poland), here are some actionable tips:
-
Negotiate: Don’t hesitate to negotiate pricing and terms. Suppliers often have room for flexibility, especially for large orders or long-term partnerships.
-
Focus on Cost Efficiency: Assess the total cost of ownership (TCO), not just the initial purchase price. Consider factors such as durability, maintenance costs, and potential downtime.
-
Understand Pricing Nuances: Be aware of how local market conditions and currency fluctuations may affect pricing. Engaging with local suppliers can sometimes mitigate these risks.
-
Request Detailed Quotes: Always ask for detailed quotes that break down costs. This transparency helps in understanding the pricing structure and identifying potential areas for savings.
-
Evaluate Multiple Suppliers: Don’t settle for the first supplier. Comparing quotes from multiple sources can provide leverage during negotiations and help identify the best value.
Disclaimer
Pricing for locksmith services can vary significantly based on the factors discussed above. The information provided is indicative and should be used as a guideline for understanding potential costs and negotiating terms. Always conduct thorough market research and supplier vetting to ensure accuracy and reliability in sourcing decisions.
Spotlight on Potential vending machine locksmith Manufacturers and Suppliers
This section offers a look at a few manufacturers active in the ‘vending machine locksmith’ market. This is a representative sample for illustrative purposes; B2B buyers must conduct their own extensive due diligence before any engagement. Information is synthesized from public sources and general industry knowledge.
Essential Technical Properties and Trade Terminology for vending machine locksmith
Vending machine locksmiths play a crucial role in ensuring the security and functionality of vending machines. Understanding essential technical properties and trade terminology is key for international B2B buyers, especially those operating in regions such as Africa, South America, the Middle East, and Europe. Here, we outline critical specifications and common industry terms to aid decision-making.
Key Technical Properties
-
Material Grade
– Definition: Refers to the quality and type of materials used in the construction of locks and components. Common materials include stainless steel, brass, and zinc alloys.
– B2B Importance: High-grade materials enhance durability and resistance to corrosion, which is vital for machines exposed to various environmental conditions. Buyers should prioritize suppliers who use robust materials to reduce maintenance costs over time. -
Lock Tolerance
– Definition: This specification indicates the permissible limits of variation in the lock’s dimensions, ensuring that parts fit together correctly.
– B2B Importance: Precise tolerances are essential for effective locking mechanisms. Poor tolerances can lead to malfunctioning locks, resulting in lost revenue and increased service calls. B2B buyers must verify that their suppliers adhere to strict tolerance standards. -
Keyway Design
– Definition: The specific shape and configuration of the key slot within a lock, which determines the type of keys that can operate it.
– B2B Importance: Keyway designs can dictate security levels; complex designs are harder to duplicate, enhancing security. Buyers should consider keyway compatibility with existing systems when purchasing locks. -
Security Rating
– Definition: A classification that indicates the level of security a lock provides, often assessed by independent testing organizations.
– B2B Importance: Higher security ratings imply better protection against unauthorized access. B2B buyers should seek locks with recognized security certifications to ensure compliance with safety standards. -
Operational Cycle Rating
– Definition: This rating measures the number of successful operations (locking and unlocking) a lock can perform before failure.
– B2B Importance: A higher operational cycle rating signifies reliability and longevity, reducing the frequency of replacements. Buyers should assess this rating to understand the long-term value of their investment.
Common Trade Terminology
-
OEM (Original Equipment Manufacturer)
– Definition: A company that produces parts or equipment that may be marketed by another manufacturer.
– Significance: Engaging with OEMs can provide access to specialized parts that are specifically designed for certain vending machines, ensuring compatibility and performance. -
MOQ (Minimum Order Quantity)
– Definition: The smallest amount of a product that a supplier is willing to sell.
– Significance: Understanding MOQ is crucial for buyers to manage inventory costs effectively. Ordering below the MOQ may lead to higher per-unit costs or inability to purchase. -
RFQ (Request for Quotation)
– Definition: A document sent to suppliers requesting a quote for specific products or services.
– Significance: An RFQ helps buyers compare pricing and terms from different suppliers, facilitating better decision-making based on cost-effectiveness.
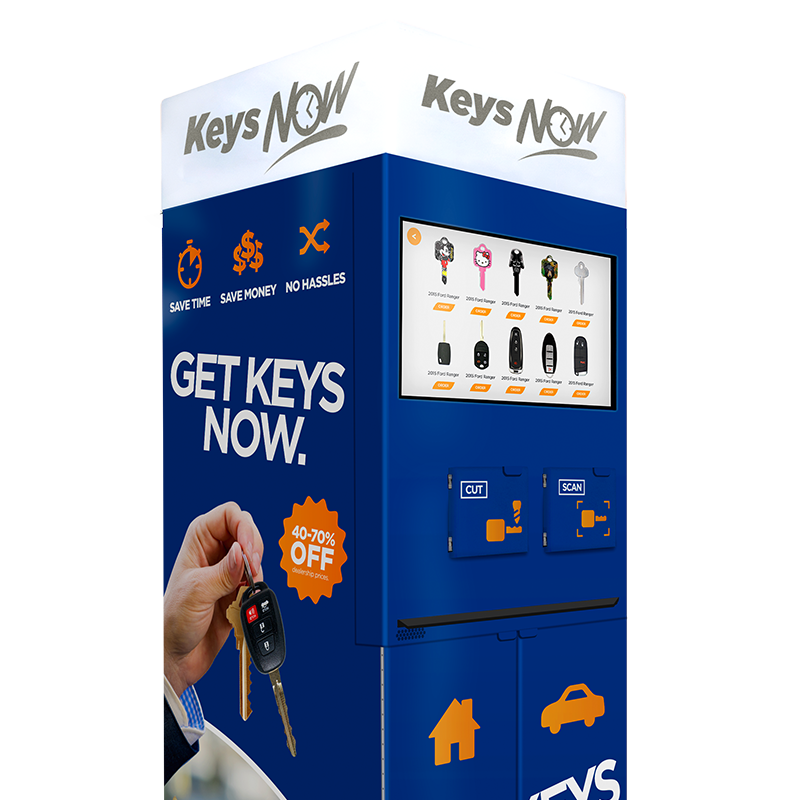
Illustrative Image (Source: Google Search)
-
Incoterms (International Commercial Terms)
– Definition: A set of predefined commercial terms published by the International Chamber of Commerce that clarify the responsibilities of buyers and sellers in international transactions.
– Significance: Familiarity with Incoterms helps buyers understand their obligations regarding shipping, insurance, and tariffs, which is essential for effective logistics management. -
Lead Time
– Definition: The time taken from placing an order to its delivery.
– Significance: Knowing the lead time allows buyers to plan operations and inventory levels accurately, which is vital for maintaining service efficiency in vending machine operations.
By understanding these technical properties and trade terms, international B2B buyers can make informed decisions that enhance their vending machine security and operational efficiency.
Navigating Market Dynamics, Sourcing Trends, and Sustainability in the vending machine locksmith Sector
Market Overview & Key Trends
The vending machine locksmith sector is witnessing transformative changes driven by several global factors. Increased urbanization, coupled with a growing demand for convenient access to goods, is propelling the expansion of vending machine installations worldwide. Particularly in regions such as Africa, South America, the Middle East, and Europe, businesses are increasingly integrating vending solutions to cater to fast-paced lifestyles and diverse consumer needs.
Emerging technologies are reshaping sourcing trends within this sector. The rise of smart vending machines, which utilize IoT (Internet of Things) for enhanced monitoring and security, is a key development. These machines often come equipped with advanced locking systems that require specialized locksmith services. B2B buyers should consider suppliers that offer robust, tech-savvy locksmith solutions that can integrate seamlessly with these machines. Additionally, the demand for multi-functional locks that support cashless transactions is growing, emphasizing the need for locksmiths who can provide electronic and digital solutions.
International buyers are also navigating a dynamic market influenced by regulatory changes and security concerns. Compliance with local regulations regarding machine security and data protection is essential. Moreover, the competition is intensifying, with numerous players entering the market, making it crucial for buyers to establish strong partnerships with reliable locksmith suppliers who can offer innovative and secure solutions.
Sustainability & Ethical Sourcing in B2B
Sustainability is becoming a pivotal consideration in the vending machine locksmith sector. As environmental concerns gain prominence, buyers are increasingly seeking locksmith solutions that minimize ecological impact. This includes the use of recycled materials in lock manufacturing and sustainable practices throughout the supply chain.
Ethical sourcing is equally important, particularly in regions where labor conditions may vary. Buyers should prioritize suppliers that adhere to fair labor practices and can provide transparency in their supply chains. This commitment not only enhances brand reputation but also fosters trust among consumers who are increasingly conscious of the origins of the products they purchase.
In addition to ethical considerations, acquiring certifications such as ISO 14001 for environmental management can serve as a competitive advantage. B2B buyers should look for locksmith suppliers who are committed to sustainability initiatives, such as reducing waste and energy consumption in their production processes. By aligning with green-certified vendors, businesses can contribute to a more sustainable future while meeting consumer expectations for responsible sourcing.
Brief Evolution/History
The vending machine locksmith sector has evolved significantly over the decades. Initially, traditional locks were the norm, primarily focusing on physical security. However, with advancements in technology, the introduction of electronic locks and smart systems has revolutionized the industry.
The shift towards automated and self-service solutions in the 1990s set the stage for more sophisticated locking mechanisms. Today, locksmiths are not just tasked with physical security; they are integral to the development and maintenance of high-tech security systems that protect the valuable assets within vending machines. This evolution highlights the importance of continuous innovation in locksmith services to meet the demands of a rapidly changing market.
As international B2B buyers navigate this landscape, understanding these dynamics will be crucial in making informed sourcing decisions that align with their operational goals and sustainability commitments.
Related Video: Incoterms for beginners | Global Trade Explained
Frequently Asked Questions (FAQs) for B2B Buyers of vending machine locksmith
-
How can I vet suppliers for vending machine locksmith services?
Vetting suppliers is crucial for ensuring quality and reliability. Start by checking for certifications relevant to locksmithing, such as ISO 9001 or regional equivalents. Look for reviews and testimonials from previous clients, and request case studies that demonstrate their expertise. Additionally, consider suppliers with a robust online presence and active participation in industry associations. Communication is key; engage in discussions to assess their responsiveness and willingness to customize solutions for your needs. -
What customization options are typically available for vending machine locks?
Many suppliers offer customizable locking solutions tailored to your specific vending machine models. Common customization options include key types, lock mechanisms (e.g., electronic, mechanical), and security features like anti-picking systems. Discuss your requirements with potential suppliers to explore how they can meet your needs. It’s also beneficial to request prototypes or samples to ensure that the lock’s design aligns with your operational requirements before placing a bulk order. -
What are the typical minimum order quantities (MOQ) and lead times for vending machine locksmith products?
Minimum order quantities can vary significantly among suppliers, often ranging from 50 to 500 units depending on the type of lock and customization. Lead times typically span from 4 to 12 weeks, influenced by factors such as order size, complexity, and the supplier’s production capacity. To avoid delays, communicate your timeline requirements early on and confirm the supplier’s ability to meet your deadlines before finalizing orders. -
What payment terms should I expect when sourcing from international suppliers?
Payment terms can differ based on the supplier’s policies and the nature of the transaction. Common arrangements include advance payment, 30% upfront with the balance upon delivery, or letters of credit for larger orders. It’s important to clarify these terms upfront to avoid disputes later. Additionally, consider using secure payment methods, such as escrow services, especially for larger transactions, to protect your investment. -
What quality assurance measures should I look for in locksmith products?
Quality assurance is essential for ensuring the reliability and durability of locksmith products. Look for suppliers who conduct thorough testing on their locks, including resistance to tampering and environmental conditions. Request documentation of their quality control processes and certifications, such as CE marking in Europe or ANSI standards in the U.S. Additionally, inquire about warranty policies and after-sales support, as these can indicate the supplier’s confidence in their products. -
How do logistics and shipping work for international orders of locksmith products?
Logistics for international orders can be complex, involving customs regulations and shipping timelines. Discuss with your supplier their preferred shipping methods and partners. Air freight is faster but more expensive, while sea freight is cost-effective but slower. Ensure that the supplier provides all necessary documentation for customs clearance, including invoices and certificates of origin. It’s also wise to confirm who bears the shipping costs and responsibilities in the event of damage or loss during transit. -
What should I do if there’s a dispute with a supplier?
In the event of a dispute, start by communicating directly with the supplier to resolve the issue amicably. Document all interactions and agreements in writing. If the matter cannot be resolved through direct communication, refer to any contracts or agreements that outline dispute resolution procedures. Depending on the severity, you may consider mediation or arbitration, especially if you have a contractual obligation to do so. Always keep a record of all correspondence and agreements as evidence.
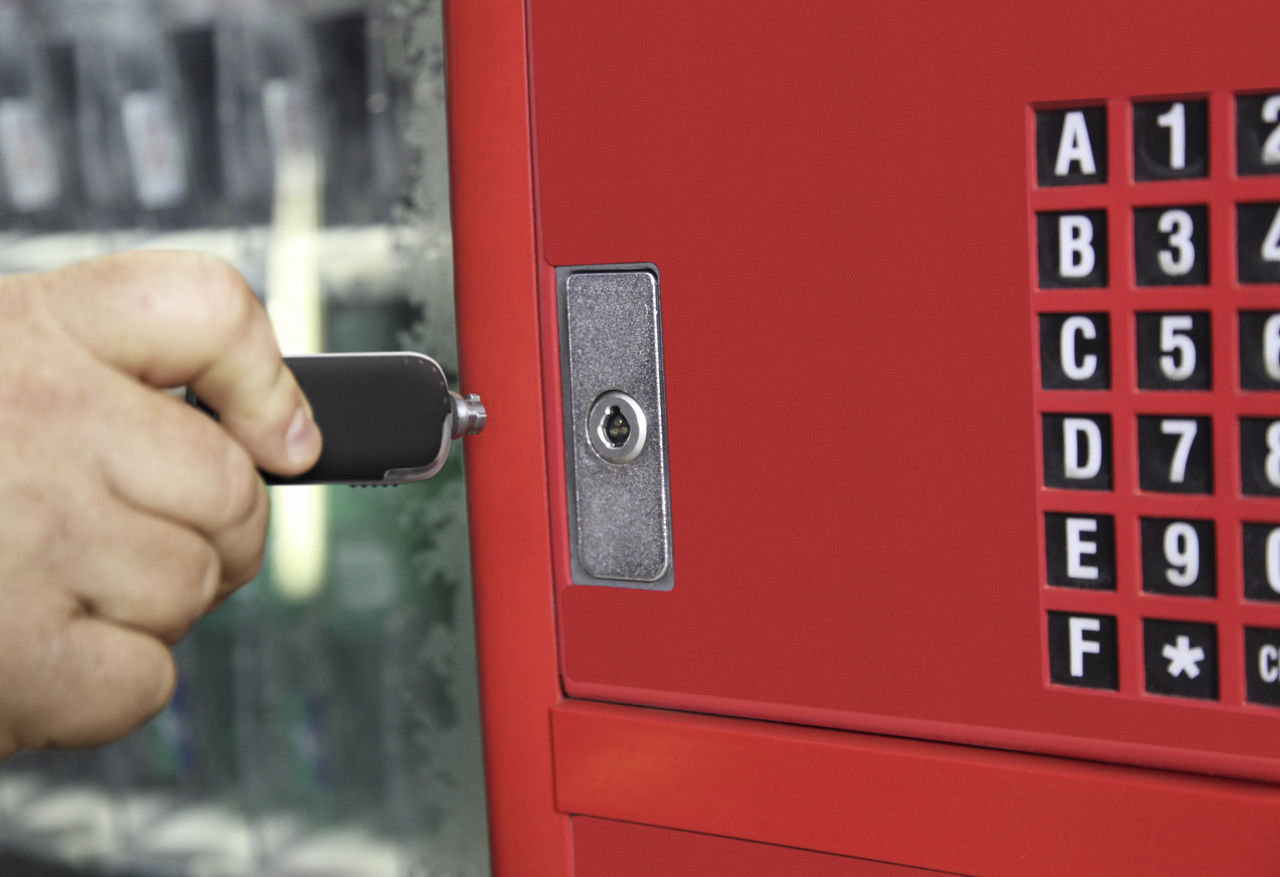
Illustrative Image (Source: Google Search)
- Are there specific certifications or standards for locksmith products that I should be aware of?
Yes, there are several certifications and standards that can indicate the quality and security of locksmith products. In Europe, look for CE marking, which signifies compliance with EU safety and environmental requirements. In the U.S., ANSI (American National Standards Institute) grades locks based on their durability and security features. Additionally, ISO certifications demonstrate a company’s commitment to quality management. Ensure that your supplier provides documentation for these certifications to ensure compliance with local regulations and standards.
Strategic Sourcing Conclusion and Outlook for vending machine locksmith
In summary, strategic sourcing for vending machine locksmith services is a vital consideration for B2B buyers looking to optimize their operations across various regions, including Africa, South America, the Middle East, and Europe. By engaging with reputable locksmiths who understand local market dynamics, businesses can ensure timely and effective service, reducing downtime and enhancing customer satisfaction.
Key Takeaways:
- Value of Local Partnerships: Establishing relationships with local locksmiths can facilitate faster response times and tailored solutions that meet regional demands.
- Investment in Quality: Prioritizing quality over cost can lead to long-term savings through reduced repair needs and enhanced security.
- Technology Integration: Embrace advancements in locksmith technology, such as smart locks and remote monitoring systems, to improve operational efficiency.
As the market for vending machine services continues to evolve, international B2B buyers are encouraged to leverage strategic sourcing not only as a means of cost reduction but as a pathway to innovation and competitive advantage. Act now to secure partnerships that will drive your business forward, ensuring you remain at the forefront of the vending machine industry.