Master the Art of Sourcing Ring Vending Machines for Your
Guide to Ring Vending Machine
- Introduction: Navigating the Global Market for ring vending machine
- Understanding ring vending machine Types and Variations
- Key Industrial Applications of ring vending machine
- Strategic Material Selection Guide for ring vending machine
- In-depth Look: Manufacturing Processes and Quality Assurance for ring vending machine
- Comprehensive Cost and Pricing Analysis for ring vending machine Sourcing
- Spotlight on Potential ring vending machine Manufacturers and Suppliers
- Essential Technical Properties and Trade Terminology for ring vending machine
- Navigating Market Dynamics, Sourcing Trends, and Sustainability in the ring vending machine Sector
- Frequently Asked Questions (FAQs) for B2B Buyers of ring vending machine
- Strategic Sourcing Conclusion and Outlook for ring vending machine
Introduction: Navigating the Global Market for ring vending machine
Navigating the global market for ring vending machines presents a unique opportunity for international B2B buyers. As the demand for automated retail solutions continues to rise, ring vending machines have emerged as a crucial component of modern commerce. These machines not only cater to the growing need for convenience but also enhance customer engagement by offering a diverse range of products, from snacks to personal care items.
This guide offers a comprehensive overview of the ring vending machine market, covering essential topics that empower informed sourcing decisions. Buyers will explore various types of ring vending machines tailored to different business needs, the materials used in manufacturing, and the critical quality control measures that ensure reliability. In addition, a detailed analysis of suppliers and cost considerations will help streamline procurement processes.
Understanding market trends is vital for making strategic investments, especially for businesses in Africa, South America, the Middle East, and Europe. This guide equips buyers with the insights needed to navigate the complexities of sourcing ring vending machines effectively. From frequently asked questions to practical tips, this resource is designed to enhance your purchasing strategy, ensuring that you select the best solutions for your operational needs. Embrace the potential of ring vending machines and elevate your business to new heights in the automated retail landscape.
Understanding ring vending machine Types and Variations
Type Name | Key Distinguishing Features | Primary B2B Applications | Brief Pros & Cons for Buyers |
---|---|---|---|
Standard Ring Vending Machine | Basic design with a manual or electronic dispensing mechanism | Retail, Events, Trade Shows | Pros: Cost-effective, easy to operate. Cons: Limited customization options. |
Customizable Ring Vending Machine | Tailored design to fit specific product sizes and branding | Corporate Events, Promotions | Pros: High customization, brand visibility. Cons: Higher initial investment. |
Smart Ring Vending Machine | Integrated technology for cashless payments and inventory tracking | High-traffic locations, Airports, Malls | Pros: Enhanced user experience, real-time inventory management. Cons: Requires tech support and maintenance. |
Multi-Product Ring Vending Machine | Capable of dispensing various products in a single unit | Gyms, Offices, Public Spaces | Pros: Versatile, maximizes space usage. Cons: Complex maintenance, potential for jams. |
Eco-Friendly Ring Vending Machine | Made from sustainable materials with energy-efficient features | Eco-conscious businesses, Outdoor events | Pros: Positive brand image, sustainability. Cons: May have higher costs and limited product availability. |
Standard Ring Vending Machine
The standard ring vending machine is a straightforward option that typically features a manual or electronic dispensing mechanism. This type is most suitable for retail environments, events, and trade shows where a basic product offering suffices. When considering this option, B2B buyers should evaluate cost-effectiveness and ease of operation, though they may find limitations in customization and product variety.
Customizable Ring Vending Machine
Customizable ring vending machines are designed to meet specific business needs, allowing for tailored sizes and branding. This type is ideal for corporate events and promotional activities where brand visibility is essential. Buyers should consider the potential for high customization and how it aligns with their marketing strategies, bearing in mind that the initial investment may be higher compared to standard models.
Smart Ring Vending Machine
Smart ring vending machines incorporate advanced technology, enabling cashless payment options and real-time inventory tracking. These machines are particularly effective in high-traffic areas such as airports and malls. B2B buyers should weigh the benefits of enhanced user experience and operational efficiency against the need for ongoing tech support and potential maintenance costs.
Multi-Product Ring Vending Machine
Multi-product ring vending machines can dispense a variety of items from a single unit, making them suitable for gyms, offices, and public spaces. Their versatility allows businesses to maximize space usage and cater to diverse consumer needs. However, buyers should be aware of the complexities involved in maintenance and the risk of product jams, which may affect customer satisfaction.
Eco-Friendly Ring Vending Machine
Eco-friendly ring vending machines are constructed from sustainable materials and designed for energy efficiency, appealing to environmentally conscious businesses and outdoor events. This type can enhance a company’s brand image and commitment to sustainability. However, buyers should consider the potential for higher costs and the availability of products that fit within this eco-friendly framework.
Related Video: Machine Learning in 2024 – Beginner’s Course
Key Industrial Applications of ring vending machine
Industry/Sector | Specific Application of ring vending machine | Value/Benefit for the Business | Key Sourcing Considerations for this Application |
---|---|---|---|
Retail | Automated product dispensing | Increased sales volume, reduced labor costs | Reliability, ease of maintenance, payment options |
Hospitality | In-room amenities vending | Enhanced guest experience, additional revenue stream | Size, product variety, user-friendly interface |
Transportation & Logistics | Spare parts vending | Reduced downtime, immediate availability of parts | Inventory management, security features, tracking systems |
Education | Campus supplies vending | Convenience for students, reduced operational costs | Product range, payment flexibility, durability |
Manufacturing | Tool and equipment vending | Streamlined operations, reduced tool loss | Robustness, size specifications, inventory control |
Retail
In the retail sector, ring vending machines can automate the dispensing of various products, such as snacks, beverages, and personal care items. This automation leads to increased sales volume by providing customers with 24/7 access to products, reducing the need for staff to manage these items. For B2B buyers, key considerations include the reliability of the machine, ease of maintenance, and the variety of payment options available to cater to diverse customer preferences.
Hospitality
In the hospitality industry, ring vending machines are utilized to offer in-room amenities, such as snacks, beverages, and toiletries. This not only enhances the guest experience by providing convenience but also generates an additional revenue stream for hotels and resorts. Buyers from this sector should focus on the size of the vending machine, the variety of products it can hold, and the user-friendly interface that can accommodate guests’ needs.
Transportation & Logistics
For transportation and logistics companies, ring vending machines serve as a solution for dispensing spare parts and tools. This application significantly reduces downtime by ensuring that critical components are readily available for immediate use. Buyers should consider factors such as inventory management capabilities, security features to prevent theft, and integrated tracking systems to monitor usage and stock levels.
Education
In educational institutions, ring vending machines can be employed to dispense essential supplies such as stationery, snacks, and beverages. This convenience benefits students and faculty alike while also reducing operational costs associated with traditional supply management. When sourcing these machines, buyers should evaluate the product range offered, the flexibility of payment methods, and the overall durability of the machine to withstand frequent use.
Manufacturing
In the manufacturing sector, ring vending machines can be used to distribute tools and equipment, streamlining operations and minimizing tool loss. By ensuring that employees have immediate access to necessary tools, companies can enhance productivity and efficiency. Key sourcing considerations for buyers include the robustness of the machine, specific size requirements to fit within existing workspaces, and effective inventory control systems to manage tool availability.
Related Video: DIY Vending Machine – Arduino based Mechatronics Project
Strategic Material Selection Guide for ring vending machine
Material Analysis for Ring Vending Machines
When selecting materials for ring vending machines, international B2B buyers need to consider various factors that influence performance, durability, and compliance with regional standards. Below is an analysis of four common materials used in the manufacturing of ring vending machines, focusing on their properties, advantages, disadvantages, and implications for buyers in diverse markets.
1. Stainless Steel (e.g., AISI 304)
Key Properties:
Stainless steel is known for its excellent corrosion resistance, high-temperature tolerance, and mechanical strength. It can withstand harsh environments, making it suitable for vending machines exposed to moisture and varying temperatures.
Pros & Cons:
The primary advantage of stainless steel is its durability and resistance to rust and corrosion, which extends the lifespan of vending machines. However, it is more expensive than other materials, which can increase manufacturing costs. Additionally, the complexity of machining stainless steel can lead to higher production times.
Impact on Application:
Stainless steel is compatible with a wide range of media, including food and beverages, making it ideal for vending applications. Its non-reactive nature ensures that it does not contaminate products.
Considerations for International Buyers:
Buyers should ensure compliance with food safety standards such as FDA or EU regulations. In Europe, DIN standards are commonly referenced, while ASTM standards are prevalent in the U.S. and other regions.
2. Carbon Steel (e.g., A216 WCB)
Key Properties:
Carbon steel offers good strength and toughness but is susceptible to corrosion if not properly treated. It typically has lower temperature and pressure ratings compared to stainless steel.
Pros & Cons:
The cost-effectiveness of carbon steel makes it a popular choice for many applications. However, its susceptibility to rust can lead to increased maintenance costs over time. Additionally, it may require protective coatings, which can complicate the manufacturing process.
Impact on Application:
Carbon steel is suitable for non-corrosive fluids and environments. Its use in vending machines should be limited to dry or controlled environments to prevent rust.
Considerations for International Buyers:
Buyers should be aware of the need for protective coatings and consider the local climate when using carbon steel. Compliance with ASTM standards is crucial, especially in regions like the U.S. and parts of Europe.
3. Aluminum
Key Properties:
Aluminum is lightweight, corrosion-resistant, and has good thermal conductivity. It is often used in applications where weight savings are critical.
Pros & Cons:
The main advantage of aluminum is its lightweight nature, which can reduce shipping costs and ease installation. However, it may not be as strong as stainless or carbon steel, making it less suitable for heavy-duty applications. Additionally, aluminum can be more expensive than carbon steel.
Impact on Application:
Aluminum is compatible with various products but may not be suitable for high-temperature applications due to its lower melting point compared to steel.
Considerations for International Buyers:
Buyers should ensure that aluminum components meet local standards, such as JIS in Japan or EN in Europe. The choice of aluminum grade can significantly impact performance and cost.
4. Plastic (e.g., Polypropylene)
Key Properties:
Plastic materials like polypropylene are lightweight, resistant to corrosion, and can be molded into complex shapes. They are also non-conductive and have good chemical resistance.
Pros & Cons:
The primary advantage of plastic is its low cost and ease of manufacturing. However, plastics may not be as durable as metals and can be affected by UV exposure, leading to degradation over time.
Impact on Application:
Plastic is suitable for non-food applications or for components that do not require high strength. It is often used in vending machines for components like buttons or housing.
Considerations for International Buyers:
Buyers should ensure compliance with local regulations regarding the use of plastics, especially in food-related applications. Understanding the specific grade and its properties is essential for ensuring performance.
Summary Table
Material | Typical Use Case for ring vending machine | Key Advantage | Key Disadvantage/Limitation | Relative Cost (Low/Med/High) |
---|---|---|---|---|
Stainless Steel (e.g., AISI 304) | Food and beverage dispensing, high corrosion environments | Excellent corrosion resistance, durable | Higher cost, complex machining | High |
Carbon Steel (e.g., A216 WCB) | General service, non-corrosive fluids for valve bodies | Cost-effective, good strength | Susceptible to corrosion without treatment | Low |
Aluminum | Lightweight components, non-food applications | Lightweight, easy to manufacture | Less strength than steel, higher cost | Med |
Plastic (e.g., Polypropylene) | Buttons, housing for vending machines | Low cost, easy to mold | Less durable, UV degradation | Low |
This guide provides a comprehensive overview of material considerations for ring vending machines, aiding international B2B buyers in making informed decisions that align with their operational needs and regional compliance requirements.
In-depth Look: Manufacturing Processes and Quality Assurance for ring vending machine
The manufacturing processes and quality assurance protocols for ring vending machines are critical aspects that international B2B buyers must understand to make informed purchasing decisions. This section will provide an in-depth look into the various stages of manufacturing, the quality control measures involved, and how buyers can verify the standards and practices of their suppliers.
Manufacturing Processes
The manufacturing of ring vending machines involves several key stages, each integral to ensuring the final product meets industry standards and customer expectations. The main stages include:
1. Material Preparation
Material preparation is the foundational stage where raw materials are sourced and processed. Common materials used in ring vending machines include high-quality metals (like steel or aluminum) for structural components and durable plastics for the machine casing.
- Sourcing: Suppliers should ensure that materials meet international quality standards, such as ASTM or ISO specifications.
- Inspection: Incoming materials undergo inspection (Incoming Quality Control – IQC) to verify compliance with specified standards before they are accepted for production.
2. Forming
In this stage, raw materials are shaped into the necessary components for the vending machine. This often includes processes like stamping, bending, and machining.
- Techniques: Common techniques include CNC machining for precision parts and laser cutting for intricate designs.
- Quality Control: During forming, quality checkpoints (In-Process Quality Control – IPQC) are established to monitor dimensions and tolerances, ensuring that components conform to specifications.
3. Assembly
Once the components are formed, they are assembled into the final vending machine structure. This includes fitting together the mechanical, electronic, and aesthetic parts.
- Methods: The assembly line may use manual labor combined with automated systems to enhance efficiency and accuracy.
- Quality Checks: Each assembly stage incorporates quality checks to verify the correct assembly of components, alignment, and functionality.
4. Finishing
The finishing stage involves applying surface treatments and coatings to enhance the machine’s appearance and protect against corrosion.
- Processes: Techniques such as powder coating, painting, or anodizing are commonly used.
- Final Quality Assurance: Before moving to the next phase, Finishing Quality Control (FQC) is conducted to ensure surface quality and adherence to aesthetic standards.
Quality Assurance
Quality assurance in the manufacturing of ring vending machines is paramount for reliability and customer satisfaction. Here are the key elements of quality assurance that international B2B buyers should consider:
International Standards
Manufacturers should adhere to various international standards to ensure product quality and safety, including:
- ISO 9001: This standard focuses on quality management systems and is essential for manufacturers looking to demonstrate their commitment to quality.
- CE Marking: For machines sold in Europe, CE marking indicates conformity with health, safety, and environmental protection standards.
- API Standards: Particularly relevant for machines that may interact with food products, API standards ensure that materials and processes are safe for consumer use.
Quality Control Checkpoints
Quality control involves multiple checkpoints throughout the manufacturing process:
- Incoming Quality Control (IQC): Ensures that raw materials meet specified standards before production begins.
- In-Process Quality Control (IPQC): Monitors the manufacturing process to detect defects early.
- Final Quality Control (FQC): Conducted on the finished product to ensure it meets all operational and aesthetic specifications.
Testing Methods
Manufacturers should employ various testing methods to assess the performance and safety of ring vending machines, including:
- Functional Testing: Verifying that all mechanical and electronic components work as intended.
- Stress Testing: Assessing the machine’s durability under simulated usage conditions.
- Safety Testing: Ensuring that the machine complies with safety regulations to prevent hazards.
Verifying Supplier Quality Control
For B2B buyers, especially those from diverse regions like Africa, South America, the Middle East, and Europe, verifying supplier quality control practices is crucial. Here are actionable steps to ensure compliance and quality:
- Conduct Audits: Regular audits of suppliers can help assess their adherence to quality standards. Buyers should request audit reports and certifications to verify compliance with international standards.
- Request Documentation: Buyers should ask for quality assurance documentation, including inspection reports, test results, and compliance certificates. This transparency helps in assessing supplier reliability.
- Third-Party Inspections: Engaging third-party inspection agencies can provide an unbiased assessment of the manufacturing process and product quality before shipment.
QC and Certification Nuances for International Buyers
When dealing with international suppliers, B2B buyers should be aware of several nuances:
- Cultural and Regulatory Differences: Different regions may have varying standards and regulations. Buyers should familiarize themselves with local regulations that might affect product compliance.
- Language Barriers: Ensure that documentation is available in a language that the buyer understands, which aids in clarity and compliance checks.
- Local Certifications: In some regions, local certifications may be required in addition to international standards. Understanding these requirements can prevent delays in customs and market entry.
By focusing on these manufacturing processes and quality assurance practices, B2B buyers can make informed decisions, ensuring that the ring vending machines they purchase meet their operational needs and quality expectations.
Related Video: Amazing scenes。Top 6 Most Popular Factory Manufacturing Videos in China
Comprehensive Cost and Pricing Analysis for ring vending machine Sourcing
In the sourcing of ring vending machines, understanding the cost structure and pricing dynamics is crucial for international B2B buyers. The costs associated with these machines can be categorized into several key components, each influencing the final pricing.
Cost Components
-
Materials: The primary materials include steel, plastics, and electronic components. The choice of materials significantly impacts durability and functionality, thus affecting costs. For instance, high-grade materials may incur higher upfront costs but can lead to lower maintenance expenses over time.
-
Labor: Labor costs vary by region and can be influenced by local wage rates and labor laws. When sourcing from countries with lower labor costs, buyers may find more competitive pricing, but this may also come with trade-offs in terms of quality and reliability.
-
Manufacturing Overhead: This encompasses the indirect costs associated with production, including utilities, rent, and administrative expenses. Buyers should inquire about the manufacturer’s overhead to gauge how it affects the final price.
-
Tooling: The initial setup for manufacturing, including molds and dies, represents a significant investment. Custom designs or modifications will typically require additional tooling costs, which can be amortized over larger production volumes.
-
Quality Control (QC): Ensuring the machines meet specific standards is vital. The costs associated with QC processes can vary based on the supplier’s quality assurance protocols and the certifications required in the buyer’s region.
-
Logistics: Shipping costs can fluctuate based on distance, mode of transport, and the chosen Incoterms. Understanding these costs is essential for calculating the total landed cost of the machines.
-
Margin: Supplier profit margins can vary widely based on market conditions, competition, and the unique value proposition of the machines offered. Buyers should be aware of typical margins in the industry to assess pricing fairness.
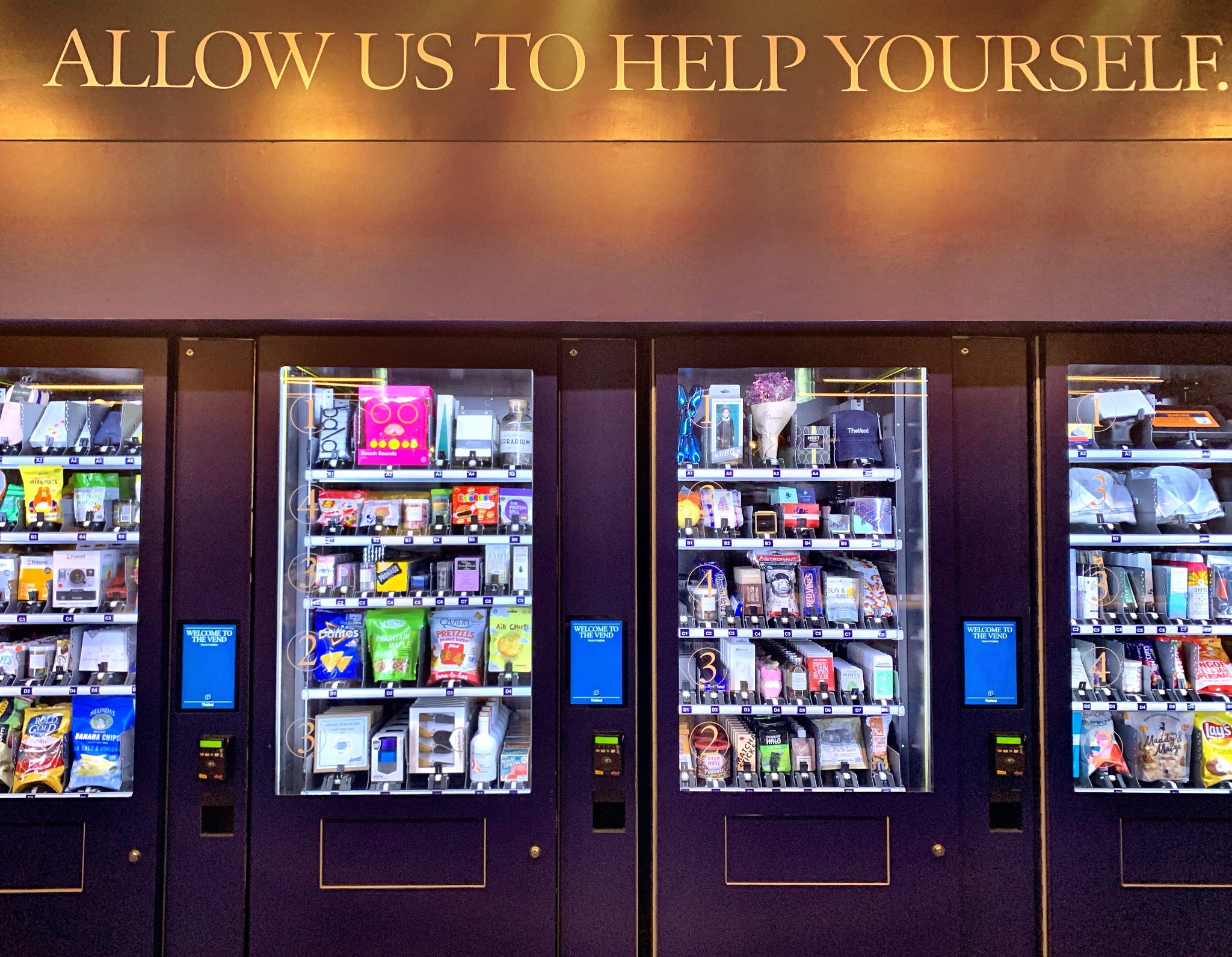
Illustrative Image (Source: Google Search)
Price Influencers
Several factors can affect the pricing of ring vending machines:
-
Volume/MOQ: Minimum order quantities (MOQ) and bulk purchasing can lead to significant cost savings. Suppliers are often willing to negotiate better prices for larger orders.
-
Specifications/Customization: Customized machines or those with enhanced features typically command higher prices. Buyers should weigh the benefits of customization against their budget constraints.
-
Material Quality/Certifications: High-quality materials and compliance with international certifications (e.g., ISO, CE) can increase costs but also enhance reliability and marketability.
-
Supplier Factors: Established suppliers with a strong reputation may charge higher prices due to perceived reliability and quality assurance. Conversely, newer entrants may offer lower prices to gain market share.
-
Incoterms: The terms of shipment (e.g., FOB, CIF) can significantly influence total costs. Buyers must understand how these terms affect responsibility for shipping costs and risk.
Buyer Tips
-
Negotiation: Engage suppliers in discussions to explore flexible pricing options, especially for larger orders. Establishing a good relationship can lead to better terms.
-
Cost-Efficiency: Consider the total cost of ownership (TCO), including maintenance and operational costs, rather than just the purchase price. This holistic view can lead to better long-term investment decisions.
-
Pricing Nuances for International Buyers: Buyers from Africa, South America, the Middle East, and Europe should be aware of currency fluctuations and potential import duties that can affect the final price. Understanding local market conditions can also provide leverage in negotiations.
-
Disclaimer for Indicative Prices: Pricing for ring vending machines can vary based on numerous factors, including market demand and supplier capabilities. It is advisable to obtain detailed quotes tailored to specific needs to ensure accurate budgeting.
By understanding these cost components and pricing influences, B2B buyers can make informed decisions that align with their operational needs and financial goals.
Spotlight on Potential ring vending machine Manufacturers and Suppliers
This section offers a look at a few manufacturers active in the ‘ring vending machine’ market. This is a representative sample for illustrative purposes; B2B buyers must conduct their own extensive due diligence before any engagement. Information is synthesized from public sources and general industry knowledge.
Essential Technical Properties and Trade Terminology for ring vending machine
When considering the procurement of ring vending machines, understanding their essential technical properties and industry-specific terminology is vital for making informed purchasing decisions. Here, we outline critical specifications and common jargon relevant to B2B buyers.
Key Technical Properties
-
Material Grade
– Definition: The quality of materials used in the construction of the vending machine, often specified by standards such as stainless steel or aluminum.
– Importance: Higher-grade materials enhance durability and resistance to corrosion, which is crucial for machines exposed to various environmental conditions, particularly in outdoor settings. -
Tolerance Levels
– Definition: The permissible limits of variation in dimensions and physical properties of components.
– Importance: Accurate tolerances ensure that parts fit together correctly, leading to optimal functionality and reducing maintenance costs. This is particularly significant for machines operating in high-traffic areas. -
Capacity
– Definition: The maximum number of items (e.g., rings, tokens) the vending machine can hold at one time.
– Importance: A larger capacity reduces the frequency of restocking, which is beneficial for operations in high-demand locations. Buyers should assess their target market’s needs to select a suitable capacity. -
Power Requirements
– Definition: The electrical specifications needed for the machine to function, including voltage and wattage.
– Importance: Understanding power requirements helps ensure compatibility with local electrical standards and can prevent costly electrical upgrades during installation. -
User Interface Features
– Definition: The design and functionality of the machine’s user interface, which may include touchscreen displays, payment options, and accessibility features.
– Importance: A user-friendly interface can enhance customer experience and increase sales. Features like multiple payment methods cater to diverse consumer preferences, particularly in different regions.
Common Trade Terminology
-
OEM (Original Equipment Manufacturer)
– Definition: A company that produces parts or equipment that may be marketed by another manufacturer.
– Importance: Understanding OEM relationships can help buyers identify reliable sources for parts and ensure that they are purchasing quality machines that meet industry standards. -
MOQ (Minimum Order Quantity)
– Definition: The smallest quantity of a product that a supplier is willing to sell.
– Importance: Knowing the MOQ is crucial for budgeting and inventory management. Buyers must ensure that they can meet this threshold without overcommitting resources. -
RFQ (Request for Quotation)
– Definition: A document sent to suppliers requesting a quote for specific products or services.
– Importance: An RFQ allows buyers to compare prices and terms from multiple suppliers, enabling more informed purchasing decisions and potentially better pricing. -
Incoterms (International Commercial Terms)
– Definition: A series of predefined commercial terms published by the International Chamber of Commerce (ICC) relating to international commercial law.
– Importance: Familiarity with Incoterms helps buyers understand the responsibilities of buyers and sellers during shipping, including who pays for shipping and insurance. This is particularly relevant for international transactions. -
Lead Time
– Definition: The time it takes from placing an order to receiving the product.
– Importance: Understanding lead times is essential for planning and managing supply chains effectively. Buyers should factor in lead times when scheduling deployments or restocking efforts. -
Warranty Terms
– Definition: The conditions under which a manufacturer will repair or replace defective products.
– Importance: Clear warranty terms protect buyers from financial loss due to equipment failure and provide peace of mind regarding the longevity of their investment.
By familiarizing themselves with these technical properties and trade terms, international B2B buyers can make informed decisions that align with their operational needs and market conditions.
Navigating Market Dynamics, Sourcing Trends, and Sustainability in the ring vending machine Sector
Market Overview & Key Trends
The ring vending machine sector is experiencing robust growth driven by several global factors. Increased urbanization, changing consumer behaviors, and the demand for convenient retail solutions are propelling the market forward. For international B2B buyers, particularly in Africa, South America, the Middle East, and Europe, understanding these dynamics is crucial for making informed sourcing decisions.
Current and Emerging B2B Tech Trends:
– Digital Integration: The rise of smart vending machines equipped with IoT technology enables real-time inventory management and customer engagement through mobile apps. This trend is especially relevant for buyers looking to enhance operational efficiency and customer experiences.
– Payment Flexibility: Machines that accept a variety of payment methods, including mobile wallets and cryptocurrencies, are gaining traction. This flexibility caters to diverse consumer preferences, making it essential for buyers to consider payment technologies when sourcing machines.
– Customization and Branding: Brands are increasingly seeking machines that can be customized to reflect their identity and values. This trend highlights the importance of sourcing from manufacturers that offer design flexibility.
Market Dynamics: Buyers should be aware of regional differences in consumer behavior and regulatory environments. For instance, European markets are leaning towards eco-friendly solutions, while emerging markets in Africa and South America may prioritize cost-effectiveness and durability. Understanding these nuances can lead to better sourcing strategies that align with local demands.
Sustainability & Ethical Sourcing in B2B
Sustainability is becoming a key focus in the ring vending machine industry, reflecting a broader trend towards environmental responsibility. The environmental impact of vending machines, from energy consumption to waste generation, is under scrutiny. Buyers must consider machines that are energy-efficient and use recyclable materials to minimize their ecological footprint.
Importance of Ethical Supply Chains: Buyers are increasingly prioritizing suppliers who adhere to ethical sourcing practices. This includes fair labor practices and sustainable sourcing of materials. By partnering with manufacturers who demonstrate transparency and accountability, buyers can enhance their brand reputation and appeal to environmentally-conscious consumers.
‘Green’ Certifications and Materials: Look for vendors that offer machines with recognized sustainability certifications, such as Energy Star or similar local certifications. Additionally, sourcing machines made from recycled or sustainable materials can further align with corporate social responsibility goals. This proactive approach not only supports environmental initiatives but also meets the growing consumer demand for sustainability.
Brief Evolution/History
The evolution of vending machines has transitioned from simple mechanical devices to sophisticated, technology-driven solutions. Initially designed to dispense basic items like snacks and beverages, modern ring vending machines now incorporate advanced technologies, such as touchscreens and cashless payment systems, to enhance user experience. This evolution reflects a shift in consumer expectations and the growing importance of convenience in retail. As the market continues to innovate, B2B buyers must stay informed about technological advancements to remain competitive in their sourcing strategies.
Related Video: Is global trade transforming? | Counting the Cost
Frequently Asked Questions (FAQs) for B2B Buyers of ring vending machine
-
What factors should I consider when vetting suppliers for ring vending machines?
When vetting suppliers, prioritize their experience in manufacturing vending machines, particularly ring vending models. Check for certifications such as ISO 9001 that indicate quality management practices. Assess customer reviews and testimonials to gauge reliability. Additionally, inquire about their production capacity, lead times, and whether they have experience exporting to your region, which can affect logistics and compliance with local regulations. -
Can I customize the design and features of the ring vending machine?
Most manufacturers offer customization options. Discuss your specific requirements such as size, color, branding, and functionality. Some may allow you to choose the payment systems (cash, card, mobile payments) and the types of rings to be dispensed. Ensure you clarify these options upfront to avoid misunderstandings later in the process. -
What are the typical minimum order quantities (MOQ) and lead times for ring vending machines?
MOQs can vary significantly based on the supplier’s production capabilities and the complexity of customization. Generally, expect MOQs to range from 10 to 50 units. Lead times are typically 4 to 12 weeks depending on the supplier’s location, order size, and customization level. Always confirm these details before finalizing your order to manage your inventory effectively. -
What payment terms are usually offered by suppliers?
Payment terms can differ widely, but common practices include a 30% deposit upon order confirmation and the remaining balance before shipment. Some suppliers may offer letters of credit or escrow services for larger orders. Always negotiate payment terms that align with your cash flow needs and ensure transparency to avoid disputes. -
How do I ensure quality assurance and certifications for the ring vending machines?
Request detailed information about the supplier’s quality control processes and any relevant certifications. Look for compliance with international standards such as CE or UL, which indicate adherence to safety and quality regulations. Additionally, consider requesting samples or conducting a factory visit to verify quality before committing to a larger order. -
What logistics considerations should I keep in mind when importing ring vending machines?
Logistics can be complex, especially with bulky items like vending machines. Determine whether the supplier can assist with shipping and customs clearance. Assess shipping costs, delivery times, and the reliability of freight forwarders. It’s also wise to understand your country’s import regulations to avoid unexpected delays or costs.
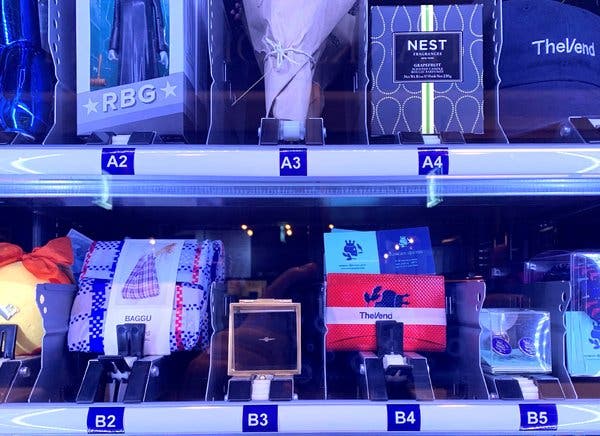
Illustrative Image (Source: Google Search)
-
How can I resolve disputes with suppliers during the procurement process?
Establish clear communication channels and document all agreements in writing. If disputes arise, first attempt to resolve them amicably through direct negotiation. If necessary, refer to the contract for dispute resolution mechanisms, which may include mediation or arbitration. Keeping a detailed record of all correspondence can also support your case. -
What after-sales support should I expect from suppliers?
Inquire about the warranty period and what it covers, including parts and labor. A reputable supplier should offer ongoing support such as maintenance services, spare parts availability, and technical assistance. Understanding the level of after-sales support can significantly impact your operational efficiency and customer satisfaction in the long run.
Strategic Sourcing Conclusion and Outlook for ring vending machine
The strategic sourcing of ring vending machines is essential for international B2B buyers aiming to optimize their operations and enhance customer satisfaction. Key takeaways include the importance of selecting suppliers who offer not only competitive pricing but also innovative features and reliable after-sales support. Understanding regional market dynamics—especially in diverse areas such as Africa, South America, the Middle East, and Europe—can provide a competitive edge, allowing businesses to tailor their offerings to meet local demands.
Investing in strategic sourcing not only facilitates cost savings but also fosters long-term partnerships that can drive growth. As the vending machine market evolves, embracing technology such as cashless payment systems and IoT capabilities will be crucial for staying ahead of consumer preferences.
Looking ahead, international B2B buyers are encouraged to leverage these insights to make informed purchasing decisions. By focusing on strategic partnerships and technological advancements, businesses can position themselves for success in an increasingly competitive landscape. Engage with suppliers who share a vision for innovation and sustainability, ensuring your vending solutions are not just functional but also future-proof.