Master the Art of Sourcing Cafe Vending Machines for Your
Guide to Cafe Vending Machine
- Introduction: Navigating the Global Market for cafe vending machine
- Understanding cafe vending machine Types and Variations
- Key Industrial Applications of cafe vending machine
- Strategic Material Selection Guide for cafe vending machine
- In-depth Look: Manufacturing Processes and Quality Assurance for cafe vending machine
- Comprehensive Cost and Pricing Analysis for cafe vending machine Sourcing
- Spotlight on Potential cafe vending machine Manufacturers and Suppliers
- Essential Technical Properties and Trade Terminology for cafe vending machine
- Navigating Market Dynamics, Sourcing Trends, and Sustainability in the cafe vending machine Sector
- Frequently Asked Questions (FAQs) for B2B Buyers of cafe vending machine
- Strategic Sourcing Conclusion and Outlook for cafe vending machine
Introduction: Navigating the Global Market for cafe vending machine
In an increasingly fast-paced world, the demand for convenient and efficient food and beverage solutions is higher than ever. Cafe vending machines stand at the forefront of this trend, offering businesses a profitable avenue to cater to consumers’ cravings for quality coffee and snacks without the need for extensive staff or infrastructure. For international B2B buyers, particularly those operating in diverse markets such as Africa, South America, the Middle East, and Europe, understanding the nuances of sourcing these machines is crucial for success.
This guide serves as a comprehensive roadmap, delving into various types of cafe vending machines, their construction materials, and manufacturing quality control processes. We provide insights into reputable suppliers, cost considerations, and market trends, equipping buyers with the knowledge necessary to make informed purchasing decisions.
Key areas of focus include:
- Types of Machines: Explore the spectrum of options available, from traditional coffee dispensers to modern, high-tech units.
- Materials and Durability: Understand the significance of material selection in ensuring longevity and reliability.
- Manufacturing and Quality Control: Learn about the best practices that guarantee superior performance.
- Supplier Insights: Identify trustworthy suppliers who meet the unique demands of your region.
- Cost Analysis: Gain clarity on pricing structures to optimize your investment.
- Market Overview: Stay informed about the evolving landscape of cafe vending machines.
- FAQs: Address common queries that arise during the procurement process.
By leveraging the insights provided in this guide, B2B buyers will be empowered to navigate the global market with confidence, ensuring they select the right cafe vending machines that align with their operational needs and customer expectations.
Understanding cafe vending machine Types and Variations
Type Name | Key Distinguishing Features | Primary B2B Applications | Brief Pros & Cons for Buyers |
---|---|---|---|
Traditional Coffee Vending | Offers a range of hot beverages including espresso and cappuccino | Offices, cafes, and public spaces | Pros: Wide variety, familiar to customers. Cons: Requires regular maintenance and supplies. |
Bean-to-Cup Machines | Grinds fresh coffee beans on demand for each cup | High-end cafes, hotels, and restaurants | Pros: Superior taste and freshness. Cons: Higher initial investment and maintenance costs. |
Snack and Beverage Combo | Combines snacks and drinks in one machine | Convenience stores and break rooms | Pros: Space-saving and versatile. Cons: May not offer premium coffee options. |
Cold Beverage Vending | Dispenses chilled drinks, including iced coffee | Outdoor events, sports venues | Pros: Appeals to customers seeking refreshing options. Cons: Limited to cold beverages. |
Automated Barista Machines | Uses advanced technology to replicate barista skills | Specialty coffee shops and kiosks | Pros: Consistent quality and speed. Cons: Complexity may deter some users. |
Traditional Coffee Vending Machines
Traditional coffee vending machines provide a selection of popular hot beverages, such as coffee, cappuccino, and hot chocolate. These machines are ideal for environments like offices, cafes, and public spaces where quick access to familiar beverages is crucial. When considering a purchase, buyers should evaluate the machine’s capacity, ease of use, and the frequency of required maintenance. Regular supply restocking is necessary, which can be a logistical consideration for businesses.
Bean-to-Cup Machines
Bean-to-cup machines are designed to grind fresh coffee beans for each cup, delivering a high-quality beverage experience. These machines are particularly suitable for high-end cafes, hotels, and restaurants where customer satisfaction is paramount. Buyers should consider the initial investment and ongoing maintenance costs, as these machines can be pricier than traditional options. However, the premium taste and aroma they provide can justify the expense in a competitive market.
Snack and Beverage Combo Machines
Snack and beverage combo machines offer a convenient solution by providing both snacks and drinks in a single unit. They are particularly effective in convenience stores and employee break rooms, where space is limited. Buyers should assess the machine’s layout and product offerings to ensure they meet customer preferences. While these machines are versatile, they may not cater to those seeking a premium coffee experience.
Cold Beverage Vending Machines
Cold beverage vending machines focus on dispensing chilled drinks, including iced coffee and other refreshing options. They are well-suited for outdoor events, sports venues, and places with high foot traffic during warm weather. Buyers should evaluate the machine’s cooling capabilities and product variety. While they attract customers looking for cold refreshments, their limitation to cold beverages may restrict their appeal in colder climates.
Automated Barista Machines
Automated barista machines leverage advanced technology to replicate the skills of a professional barista, offering a range of specialty coffee drinks at the push of a button. These machines are ideal for specialty coffee shops and kiosks where speed and consistency are essential. Buyers should consider the complexity of operation and potential training requirements for staff. Although they provide high-quality beverages, their sophisticated technology may not be suited for all business models.
Related Video: CS 198-126: Lecture 12 – Diffusion Models
Key Industrial Applications of cafe vending machine
Industry/Sector | Specific Application of cafe vending machine | Value/Benefit for the Business | Key Sourcing Considerations for this Application |
---|---|---|---|
Corporate Offices | Employee break rooms and lounges | Enhances employee satisfaction, reduces downtime | Machine size, product variety, payment options |
Educational Institutions | Cafeterias and student lounges | Provides convenient access to refreshments, boosts student morale | Health and safety compliance, energy efficiency |
Healthcare Facilities | Waiting areas and staff lounges | Improves patient and staff experience, promotes wellness | Hygiene standards, accessibility features |
Retail Environments | Shopping malls and airports | Drives additional revenue, enhances customer experience | Location analysis, machine durability |
Hospitality Industry | Hotels and resorts | Offers 24/7 access to coffee, increases guest satisfaction | Customization options, branding opportunities |
Corporate Offices
In corporate environments, cafe vending machines are strategically placed in break rooms and lounges to provide employees with easy access to coffee and snacks. This convenience helps enhance employee satisfaction and can significantly reduce downtime during work hours. For international buyers, it is crucial to consider machine size to fit available space, product variety to cater to diverse tastes, and payment options that align with employee preferences.
Educational Institutions
In schools and universities, cafe vending machines can be installed in cafeterias and student lounges, offering students quick access to beverages and snacks between classes. This not only boosts student morale but also encourages healthy snacking habits. When sourcing machines for educational institutions, buyers must ensure compliance with health and safety regulations, as well as prioritize energy efficiency to minimize operational costs.
Healthcare Facilities
Healthcare facilities, including hospitals and clinics, utilize cafe vending machines in waiting areas and staff lounges to improve the experience of both patients and staff. These machines can provide nutritious options that promote wellness. Buyers in this sector should focus on hygiene standards, ensuring machines are easy to clean and maintain, as well as incorporating accessibility features for all users.
Retail Environments
In retail settings such as shopping malls and airports, cafe vending machines serve as a convenient option for customers seeking refreshments while shopping or traveling. This application not only drives additional revenue but also enhances the overall customer experience. Key considerations for sourcing machines in retail environments include conducting a thorough location analysis to identify high-traffic areas and ensuring machine durability to withstand heavy usage.
Hospitality Industry
Hotels and resorts can greatly benefit from cafe vending machines by providing guests with 24/7 access to coffee and snacks. This convenience can significantly increase guest satisfaction and encourage repeat visits. When sourcing machines for the hospitality sector, buyers should look for customization options that allow for branding opportunities, ensuring the machines align with the overall aesthetic of the property while offering a unique guest experience.
Related Video: How to Start a Vending Machine Business, Cost, Tips, How Much You Make
Strategic Material Selection Guide for cafe vending machine
When selecting materials for cafe vending machines, international B2B buyers must consider various factors that influence performance, durability, and compliance. Below is an analysis of four common materials used in the construction of these machines, focusing on their properties, advantages, disadvantages, and specific considerations for buyers in Africa, South America, the Middle East, and Europe.
Stainless Steel
Key Properties: Stainless steel is known for its excellent corrosion resistance, high-temperature tolerance, and mechanical strength. It typically withstands temperatures up to 800°C and pressures of 1500 psi, making it suitable for hot beverage applications.
Pros & Cons: The durability of stainless steel is a significant advantage, as it can withstand harsh environments and is easy to clean. However, it is more expensive than other materials, which may impact the overall cost of the vending machine. Manufacturing complexity is moderate, requiring specialized equipment for shaping and welding.
Impact on Application: Stainless steel is compatible with a wide range of media, including water, coffee, and milk, making it ideal for cafe vending machines.
Considerations for International Buyers: Buyers should ensure compliance with relevant standards such as ASTM A240 for stainless steel. In regions like Europe, adherence to EU regulations on food safety is crucial. The cost may vary significantly based on local market conditions.
Aluminum
Key Properties: Aluminum is lightweight, corrosion-resistant, and has good thermal conductivity. It can handle temperatures up to 200°C and is often used in components that require heat dissipation.
Pros & Cons: The primary advantage of aluminum is its low weight, which can reduce shipping costs. However, it is less durable than stainless steel and may dent or scratch more easily. Manufacturing processes for aluminum are generally simpler and less costly.
Impact on Application: Aluminum is suitable for non-corrosive media and is often used in external components of vending machines, but care must be taken with acidic beverages.
Considerations for International Buyers: Buyers should check for compliance with local standards such as ASTM B221. In regions with high humidity, additional coatings may be required to enhance corrosion resistance.
Polycarbonate
Key Properties: Polycarbonate is a thermoplastic known for its high impact resistance and transparency. It can withstand temperatures up to 120°C and has good chemical resistance.
Pros & Cons: The main advantage of polycarbonate is its lightweight nature and ability to provide visibility for product displays. However, it is less durable than metals and can scratch easily. Manufacturing is generally less complex and cost-effective.
Impact on Application: Polycarbonate is ideal for components that require visibility, such as product hoppers, but may not be suitable for direct contact with high-temperature liquids.
Considerations for International Buyers: Buyers should ensure that the polycarbonate used meets food safety standards, such as FDA regulations in the US or EFSA in Europe. The material’s performance can vary based on local climate conditions, particularly UV exposure.
Glass
Key Properties: Glass is known for its excellent chemical resistance and aesthetic appeal. It can withstand high temperatures but is more fragile than other materials, with a typical thermal limit of around 300°C.
Pros & Cons: The advantage of glass is its ability to provide a premium look and feel, enhancing the consumer experience. However, it is heavy and can break easily, leading to higher shipping costs and potential safety concerns.
Impact on Application: Glass is often used for display panels or containers for beverages, but its fragility limits its use in high-traffic areas.
Considerations for International Buyers: Compliance with safety standards is essential, especially in regions where glass breakage could pose a risk. Buyers should also consider the logistics of transporting glass components, especially in regions with less developed infrastructure.
Summary Table
Material | Typical Use Case for cafe vending machine | Key Advantage | Key Disadvantage/Limitation | Relative Cost (Low/Med/High) |
---|---|---|---|---|
Stainless Steel | Structural components, hot beverage systems | Excellent durability and corrosion resistance | Higher cost compared to alternatives | High |
Aluminum | External components, heat dissipators | Lightweight, cost-effective | Less durable, prone to dents | Medium |
Polycarbonate | Product hoppers, visibility panels | Lightweight, good visibility | Scratches easily, less durable | Low |
Glass | Display panels, beverage containers | Premium aesthetic appeal | Fragile, heavy | Medium |
This strategic material selection guide provides essential insights for international B2B buyers, enabling informed decisions that align with their specific needs and regional considerations.
In-depth Look: Manufacturing Processes and Quality Assurance for cafe vending machine
Understanding the Manufacturing Processes for Cafe Vending Machines
The manufacturing of cafe vending machines involves several critical stages that ensure the product meets the demands of international markets. For B2B buyers, particularly those from Africa, South America, the Middle East, and Europe, understanding these processes can aid in making informed purchasing decisions.
Main Stages of Manufacturing
-
Material Preparation
– This initial stage involves selecting high-quality materials, such as stainless steel for durability and food safety, and plastics that can withstand various environmental conditions.
– Suppliers should source materials that comply with international standards, ensuring they are suitable for food contact, which is crucial for vending machines. -
Forming
– The forming process includes cutting, bending, and shaping the materials into the desired components. Techniques such as laser cutting or CNC machining are commonly employed to achieve precision.
– Advanced forming technologies enhance efficiency and reduce waste, which is vital for cost management in large-scale production. -
Assembly
– After forming, components are assembled. This may involve manual assembly or automated processes, depending on the manufacturer’s capabilities.
– Key components include the dispensing mechanism, payment systems, and user interface. Ensuring these components are integrated seamlessly is critical for machine reliability. -
Finishing
– The finishing stage focuses on the aesthetic and functional aspects of the vending machine. This includes painting, coating, or applying decals.
– High-quality finishing not only improves the machine’s appearance but also adds protective layers against corrosion and wear, enhancing longevity.
Quality Assurance in Manufacturing
Quality assurance (QA) is a vital part of the manufacturing process for cafe vending machines. It ensures that products meet specified standards and function as intended, which is essential for maintaining customer satisfaction and compliance with regulatory requirements.
International and Industry-Specific Standards
-
ISO 9001
– This international standard outlines the criteria for a quality management system (QMS). Manufacturers seeking ISO 9001 certification demonstrate their commitment to quality and customer satisfaction.
– B2B buyers should inquire if suppliers are ISO certified, as this can indicate a structured approach to quality management. -
CE Marking
– For machines sold in the European Economic Area, CE marking indicates compliance with EU safety, health, and environmental protection standards.
– Ensure that suppliers provide documentation proving CE certification, as this is crucial for legal compliance in European markets. -
API Standards
– The American Petroleum Institute (API) standards may apply if the vending machines are designed to dispense beverages with specific requirements, such as oil or gas-related products.
– Understanding these standards is essential for buyers in industries where compliance with API is critical.
Quality Control Checkpoints
Effective quality control (QC) involves several checkpoints throughout the manufacturing process:
-
Incoming Quality Control (IQC)
– IQC involves inspecting raw materials before they enter the manufacturing process. This step is crucial to identify any defects early and avoid costly issues later in production. -
In-Process Quality Control (IPQC)
– IPQC monitors the production process in real-time, ensuring that all components meet the specified standards. This can include visual inspections and automated testing. -
Final Quality Control (FQC)
– FQC checks the finished product against quality standards before it is shipped. This may include functional testing of the vending machine to ensure it operates correctly.
Common Testing Methods
B2B buyers should be familiar with the various testing methods used to ensure product quality:
- Functional Testing: Verifying that all machine components work as intended, including payment processing and dispensing mechanisms.
- Durability Testing: Assessing how the machine withstands stress, wear, and environmental factors over time.
- Safety Testing: Ensuring that the machine complies with safety regulations, particularly those related to electrical components and food safety.
Verifying Supplier Quality Control
To ensure that suppliers maintain high-quality standards, B2B buyers can take several actionable steps:
-
Conduct Audits
– Regular audits of suppliers can provide insights into their manufacturing processes and quality control measures. This can be done through on-site visits or third-party auditing services. -
Request Quality Reports
– Suppliers should provide documentation of their quality control processes, including reports from IQC, IPQC, and FQC. Reviewing these reports can help buyers assess the supplier’s commitment to quality. -
Utilize Third-Party Inspection Services
– Engaging third-party inspection services can provide an unbiased assessment of the manufacturing process and product quality. This is especially useful for international buyers who may face challenges in verifying supplier claims.
Navigating QC and Certification Nuances
For international B2B buyers, understanding the nuances of quality control and certification is essential. Different regions may have specific requirements or certifications that are recognized locally but not internationally.
- Regional Compliance: Buyers in Africa and South America may face different regulatory standards compared to those in Europe or the Middle East. Familiarizing oneself with these regional differences can prevent compliance issues.
- Documentation: Ensure that all certifications and quality control documents are available in the required languages and formats, as this can facilitate smoother transactions and regulatory compliance.
Conclusion
Understanding the manufacturing processes and quality assurance measures for cafe vending machines is crucial for international B2B buyers. By focusing on material preparation, forming, assembly, and finishing, along with adhering to international standards and conducting thorough quality control, buyers can ensure they are sourcing reliable and high-quality products. Engaging in proactive measures to verify supplier quality will further enhance confidence in purchasing decisions, ultimately leading to successful business outcomes.
Related Video: Parle-G Biscuits Manufacturing process – Food Factory Tour- Modern Food factory, Mega Factory II
Comprehensive Cost and Pricing Analysis for cafe vending machine Sourcing
When sourcing cafe vending machines, understanding the comprehensive cost structure and pricing dynamics is crucial for international B2B buyers. This analysis breaks down the various cost components and price influencers that affect the overall expenditure, while also providing actionable tips for negotiating better deals.
Cost Components
-
Materials: The cost of raw materials significantly impacts the pricing of vending machines. Key materials include metals for the frame, plastics for casing, and electronic components for functionality. Buyers should consider sourcing from regions with lower material costs or negotiating bulk purchase agreements to reduce expenses.
-
Labor: Labor costs vary by region. Countries with lower labor costs can offer competitive pricing but may affect quality. It’s essential to assess the labor practices of suppliers to ensure compliance with international labor standards.
-
Manufacturing Overhead: This includes utilities, rent, and administrative expenses related to production. Understanding a supplier’s overhead can provide insights into their pricing structure. Look for suppliers with efficient operations that can pass on savings.
-
Tooling: Specialized tooling for customized machines can add to the cost. Buyers needing unique specifications should factor in these additional expenses and discuss tooling fees upfront.
-
Quality Control (QC): QC processes ensure the machines meet required standards. Suppliers with rigorous QC measures may charge more but can result in fewer defects and lower long-term costs.
-
Logistics: Shipping costs can fluctuate based on distance, shipping method, and fuel prices. Consider the total logistics cost, including customs duties, when evaluating supplier quotes.
-
Margin: The supplier’s profit margin is another factor in the final price. Understanding the market rates for vending machines can help buyers gauge if a supplier’s margin is reasonable.
Price Influencers
-
Volume/MOQ: Larger orders often lead to lower per-unit costs due to economies of scale. Buyers should negotiate minimum order quantities (MOQs) to achieve better pricing.
-
Specifications/Customization: Highly customized machines can incur additional costs. Buyers should weigh the need for customization against budget constraints and consider standard models where possible.
-
Materials and Quality/Certifications: Premium materials and certifications (like ISO or CE) can drive up costs but may offer better durability and compliance. Assess the trade-off between initial investment and long-term reliability.
-
Supplier Factors: The reputation, location, and reliability of the supplier can affect pricing. Established suppliers with a strong track record may charge more, but they often provide better service and quality assurance.
-
Incoterms: The choice of Incoterms (International Commercial Terms) affects responsibility for shipping and insurance costs. Understanding these terms is essential for calculating total landed costs.
Buyer Tips
-
Negotiation: Always approach negotiations with a clear understanding of the market price. Leverage competitive quotes to negotiate better terms and pricing.
-
Cost-Efficiency: Evaluate not just the upfront costs but also the Total Cost of Ownership (TCO), which includes maintenance, energy consumption, and operational efficiencies.
-
Pricing Nuances for International Buyers: Be aware of currency fluctuations and international tariffs that may affect pricing. Engaging with suppliers who have experience in your region can mitigate these risks.
-
Engage Local Experts: For buyers in Africa, South America, the Middle East, and Europe, collaborating with local sourcing experts can provide insights into regional market dynamics and help navigate logistical challenges.
Disclaimer
The prices and cost components discussed here are indicative and may vary based on specific suppliers, market conditions, and buyer requirements. Always conduct thorough due diligence before making purchasing decisions.
Spotlight on Potential cafe vending machine Manufacturers and Suppliers
This section offers a look at a few manufacturers active in the ‘cafe vending machine’ market. This is a representative sample for illustrative purposes; B2B buyers must conduct their own extensive due diligence before any engagement. Information is synthesized from public sources and general industry knowledge.
Essential Technical Properties and Trade Terminology for cafe vending machine
Understanding the essential technical properties and trade terminology associated with cafe vending machines is crucial for B2B buyers navigating the international market. This knowledge not only facilitates better purchasing decisions but also enhances negotiations and operational efficiency.
Key Technical Properties
-
Material Grade
– Definition: The quality and type of materials used in the construction of the vending machine, typically stainless steel or high-grade plastics.
– Importance: High-grade materials ensure durability and longevity, which are essential for machines placed in high-traffic areas. For buyers, investing in machines made from superior materials minimizes maintenance costs and downtime. -
Capacity
– Definition: The total number of products the vending machine can hold, usually measured in liters or the number of individual items (e.g., cups of coffee).
– Importance: Understanding capacity helps buyers assess how well a machine can meet customer demand. Larger capacities are beneficial in busy locations, whereas smaller machines might be adequate for niche markets. -
Power Consumption
– Definition: The amount of electrical energy the vending machine uses, typically measured in watts.
– Importance: For businesses, lower power consumption translates to reduced operational costs. Buyers should look for energy-efficient models that comply with international energy standards, which can also enhance their sustainability credentials.
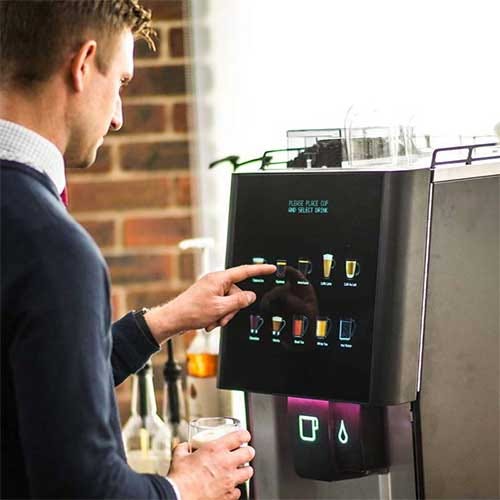
Illustrative Image (Source: Google Search)
-
Temperature Control
– Definition: The ability of the machine to maintain optimal temperatures for beverages, often measured in degrees Celsius.
– Importance: Proper temperature control is vital for preserving the quality and flavor of coffee. Buyers need to ensure that machines have reliable thermostats and heating elements to deliver a consistent product. -
User Interface
– Definition: The system through which users interact with the machine, which may include touchscreen displays, buttons, or mobile app integration.
– Importance: A user-friendly interface can enhance customer experience, leading to higher sales. B2B buyers should evaluate the technology used to ensure it aligns with customer preferences and ease of use.
Common Trade Terminology
-
OEM (Original Equipment Manufacturer)
– Definition: A company that produces parts or equipment that may be marketed by another manufacturer.
– Usage: Understanding OEM relationships can help buyers identify quality suppliers who provide reliable components for cafe vending machines, enhancing the overall product quality. -
MOQ (Minimum Order Quantity)
– Definition: The smallest quantity of a product that a supplier is willing to sell.
– Usage: Knowing the MOQ is essential for buyers to plan their inventory and budget. It can also indicate the supplier’s production capabilities and commitment to serving smaller businesses. -
RFQ (Request for Quotation)
– Definition: A document sent to suppliers to request pricing and terms for specific products or services.
– Usage: Buyers should utilize RFQs to obtain detailed pricing information and compare offers from multiple suppliers, ensuring they make informed purchasing decisions. -
Incoterms (International Commercial Terms)
– Definition: A set of predefined international rules that clarify the responsibilities of buyers and sellers in international transactions.
– Usage: Familiarity with Incoterms helps buyers understand shipping costs, risks, and liabilities. This knowledge is crucial for negotiating terms that align with their logistical capabilities. -
Lead Time
– Definition: The amount of time between the initiation of an order and its completion.
– Usage: Understanding lead times is vital for effective inventory management. Buyers must factor in lead times when planning product launches or promotions to ensure adequate stock levels.
By grasping these technical properties and trade terms, international B2B buyers can make more strategic decisions when sourcing cafe vending machines, ultimately enhancing their operational efficiency and customer satisfaction.
Navigating Market Dynamics, Sourcing Trends, and Sustainability in the cafe vending machine Sector
Market Overview & Key Trends
The global cafe vending machine market is witnessing substantial growth, driven by increasing consumer demand for convenience and quality. This trend is particularly pronounced in urban areas across Africa, South America, the Middle East, and Europe, where busy lifestyles have made quick access to quality coffee essential. The introduction of advanced technologies, such as cashless payment systems and IoT-enabled machines, is reshaping the landscape, enabling operators to enhance user experiences and streamline operations.
Emerging B2B sourcing trends include a shift towards modular and customizable vending solutions that cater to diverse consumer preferences. Buyers are increasingly looking for machines that can offer a variety of beverage options, from classic espresso to specialty drinks, thus appealing to a wider audience. Furthermore, sustainability is becoming a significant factor in purchasing decisions. B2B buyers are prioritizing suppliers that demonstrate a commitment to eco-friendly practices and materials, reflecting a broader shift towards responsible consumption.
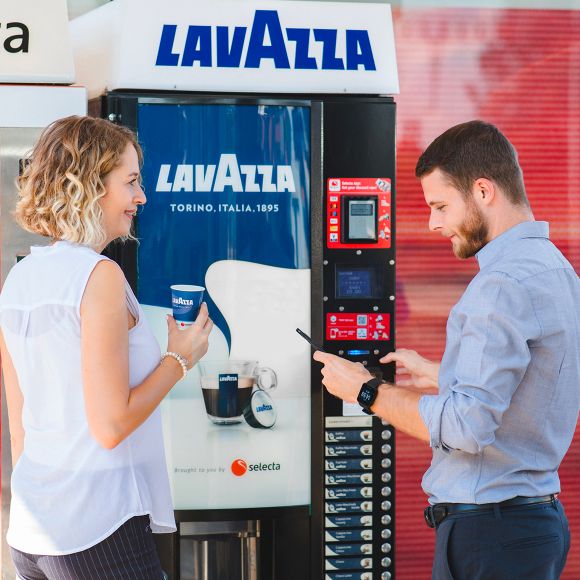
Illustrative Image (Source: Google Search)
Market dynamics are also influenced by regional factors. In Africa, for example, the growth of mobile payment systems is facilitating transactions in vending operations, while in Europe, stringent regulations on food safety and sustainability are shaping product offerings. International buyers must remain adaptable and informed about local trends to effectively navigate this evolving market.
Sustainability & Ethical Sourcing in B2B
Sustainability is no longer just a buzzword; it has become a critical component of business strategy for many B2B buyers in the cafe vending machine sector. The environmental impact of vending machines, particularly concerning energy consumption and waste generation, is prompting businesses to seek greener alternatives. Machines that utilize energy-efficient technologies and offer biodegradable or recyclable packaging are increasingly in demand.
Ethical sourcing is equally important. Buyers are encouraged to engage with suppliers who adhere to fair trade practices and possess certifications that demonstrate responsible sourcing of coffee and other ingredients. Certifications such as Fair Trade, Rainforest Alliance, and USDA Organic not only enhance brand reputation but also resonate with environmentally conscious consumers.
Investing in “green” materials, such as recycled plastics or sustainably sourced wood for machine construction, can also provide a competitive edge. B2B buyers should consider the entire supply chain and prioritize partnerships with suppliers that share a commitment to sustainability. This approach not only meets consumer expectations but also contributes to long-term operational efficiency and cost savings.
Brief Evolution/History
The cafe vending machine sector has evolved significantly since its inception in the early 20th century. Initially, these machines offered only basic coffee options, primarily catering to the needs of busy workers. However, advancements in technology have transformed the sector, leading to the introduction of high-quality coffee machines that can replicate café-style beverages.
In recent years, the focus has shifted towards user experience and personalization, with machines now capable of providing customized drink options based on consumer preferences. This evolution reflects broader trends in the food and beverage industry, where quality and convenience are paramount. As the market continues to innovate, B2B buyers must stay informed about the latest developments to remain competitive and meet the evolving demands of consumers.
Related Video: International Trade 101 | Economics Explained
Frequently Asked Questions (FAQs) for B2B Buyers of cafe vending machine
-
What key factors should I consider when vetting suppliers for cafe vending machines?
When vetting suppliers, prioritize their industry experience, customer reviews, and certifications. Verify their manufacturing capabilities and inquire about their compliance with international quality standards, such as ISO certifications. It’s also crucial to assess their financial stability and production capacity to ensure they can meet your demand. Conducting site visits or virtual tours can further help in establishing trust. Lastly, evaluate their responsiveness and willingness to engage in post-sale support, which is vital for long-term partnerships. -
Can I customize my cafe vending machines according to my brand requirements?
Most suppliers offer customization options, including branding, machine color, and product offerings. Discuss your specific needs during initial conversations to understand the extent of customization available. Factors like minimum order quantities (MOQ) and additional costs should also be clarified. Customization can enhance brand visibility and customer experience, making it a worthwhile investment. Ensure you receive prototypes or samples before finalizing the order to ensure the designs align with your expectations. -
What are the typical minimum order quantities (MOQ) and lead times for cafe vending machines?
MOQs for cafe vending machines can vary significantly depending on the supplier and the complexity of the machine. Generally, MOQs can range from 5 to 50 units. Lead times may also differ based on customization and the supplier’s production schedule, typically ranging from 4 to 12 weeks. It’s advisable to discuss your specific requirements and timelines early on. Understanding these factors will help you plan your inventory and cash flow effectively. -
What payment terms should I expect when sourcing cafe vending machines internationally?
Payment terms can vary by supplier and region. Common arrangements include a deposit (often 30-50%) with the balance due upon shipment or delivery. Letters of credit or escrow services can provide additional security for larger orders. Always confirm the accepted payment methods, as some suppliers may prefer bank transfers, while others may accept credit cards or online payment systems. Understanding payment terms is crucial for managing your budget and reducing financial risks. -
What quality assurance measures and certifications should I look for?
Quality assurance is vital in ensuring the longevity and reliability of cafe vending machines. Look for suppliers that adhere to international standards like ISO 9001 for quality management systems. Certifications specific to electrical safety and food-grade materials are also essential. Request detailed information about the QA process, including testing procedures and warranty policies. A comprehensive QA plan not only protects your investment but also ensures compliance with local regulations in your target market. -
How can I effectively manage logistics and shipping for international orders?
Logistics can be complex when sourcing machines internationally. Collaborate with your supplier to understand their shipping options and choose a reliable freight forwarder experienced in handling machinery. Discuss packaging requirements to prevent damage during transit. Additionally, factor in customs regulations and duties in your budget. Establish clear communication regarding shipping timelines and tracking options to avoid delays and ensure a smooth delivery process. -
What should I do if I encounter disputes with my supplier?
In the event of a dispute, start by reviewing your contract and any agreements regarding terms and conditions. Maintain open communication with your supplier to resolve issues amicably. If necessary, escalate the matter to a higher management level within the supplier’s organization. If a resolution cannot be reached, consider mediation or arbitration as alternative dispute resolution methods. Always document all communications and agreements to protect your interests. -
What ongoing support should I expect after purchasing a cafe vending machine?
Post-sale support is crucial for the successful operation of your vending machines. Discuss warranty coverage, maintenance services, and technical support options with your supplier before finalizing the purchase. Ensure they provide clear guidelines for troubleshooting and repairs. Some suppliers may offer training for your staff on machine operation and maintenance. Establishing a good relationship with your supplier can facilitate timely support, ensuring your machines remain operational and profitable.
Strategic Sourcing Conclusion and Outlook for cafe vending machine
As the demand for cafe vending machines continues to rise across diverse markets, strategic sourcing emerges as a critical component for international B2B buyers. By leveraging data-driven insights and fostering strong supplier relationships, businesses can enhance operational efficiency and improve product offerings. Key takeaways include the importance of understanding regional consumer preferences, investing in technology for better inventory management, and ensuring compliance with local regulations to mitigate risks.
Furthermore, the value of sustainability cannot be overstated. Buyers should prioritize suppliers who adopt eco-friendly practices and provide energy-efficient machines, aligning with the growing consumer demand for sustainable solutions.
Looking ahead, the landscape for cafe vending machines is poised for innovation, particularly with advancements in contactless payment systems and AI-driven customer insights. International B2B buyers from Africa, South America, the Middle East, and Europe should capitalize on these trends to stay ahead of the competition.
Embrace the future of vending by strategically sourcing your cafe solutions today. Engage with suppliers who not only meet your immediate needs but also contribute to your long-term growth and sustainability goals.