Master Sourcing Wall Vending Machines to Boost Your
Guide to Wall Vending Machines
- Introduction: Navigating the Global Market for wall vending machines
- Understanding wall vending machines Types and Variations
- Key Industrial Applications of wall vending machines
- Strategic Material Selection Guide for wall vending machines
- In-depth Look: Manufacturing Processes and Quality Assurance for wall vending machines
- Comprehensive Cost and Pricing Analysis for wall vending machines Sourcing
- Spotlight on Potential wall vending machines Manufacturers and Suppliers
- Essential Technical Properties and Trade Terminology for wall vending machines
- Navigating Market Dynamics, Sourcing Trends, and Sustainability in the wall vending machines Sector
- Frequently Asked Questions (FAQs) for B2B Buyers of wall vending machines
- Strategic Sourcing Conclusion and Outlook for wall vending machines
Introduction: Navigating the Global Market for wall vending machines
In an increasingly fast-paced global marketplace, wall vending machines have emerged as a pivotal solution for businesses seeking to enhance customer engagement and streamline product distribution. These innovative machines not only maximize space utilization but also cater to diverse consumer needs, making them essential for retailers, hotels, and public venues across various regions. As international B2B buyers, particularly those from Africa, South America, the Middle East, and Europe, the ability to source and implement these machines can significantly boost operational efficiency and customer satisfaction.
This comprehensive guide delves into the multifaceted world of wall vending machines, offering insights into various types and materials available, alongside critical considerations for manufacturing and quality control. It also outlines key aspects of selecting reliable suppliers and provides a detailed analysis of cost factors to help you make informed purchasing decisions. Understanding the market trends and addressing common FAQs will empower you to navigate this evolving landscape with confidence.
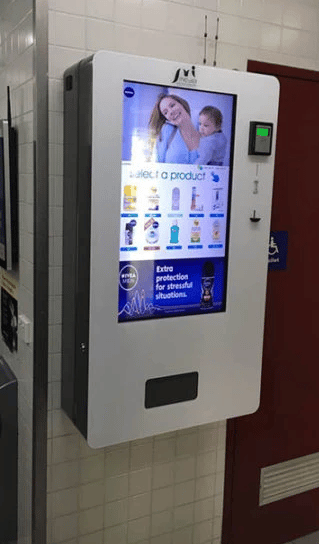
Illustrative Image (Source: Google Search)
By leveraging the insights provided in this guide, B2B buyers will be better equipped to identify the right solutions tailored to their unique operational needs. Whether you’re looking to enhance existing offerings or explore new opportunities, this resource serves as your roadmap to successful sourcing and implementation of wall vending machines in your business strategy.
Understanding wall vending machines Types and Variations
Type Name | Key Distinguishing Features | Primary B2B Applications | Brief Pros & Cons for Buyers |
---|---|---|---|
Snack and Beverage Vending | Offers a range of snacks and drinks, often refrigerated | Offices, schools, and public spaces | Pros: High demand, easy to stock; Cons: Limited product variety, potential for spoilage. |
Automated Retail Kiosks | Combines vending with e-commerce, offering electronics and more | Retail environments, airports | Pros: High margins, diverse product range; Cons: Higher initial investment, requires tech support. |
Health-Conscious Vending | Focused on healthy snacks and beverages, often organic | Gyms, health centers, schools | Pros: Appeals to health trends, attracts niche markets; Cons: Smaller target audience, higher costs. |
Customized Product Vending | Allows businesses to select and customize products offered | Corporate offices, events | Pros: Tailored to specific needs, enhances brand engagement; Cons: Higher operational complexity, needs regular updates. |
Multilingual Vending Machines | Provides options in multiple languages to cater to diverse populations | Tourist areas, international events | Pros: Increases accessibility, enhances user experience; Cons: May require additional maintenance and software updates. |
Snack and Beverage Vending
Snack and beverage vending machines are the most common types found in various environments, including offices, schools, and public spaces. These machines typically offer a range of snacks and drinks, often including refrigerated options for perishable items. For B2B buyers, these machines are appealing due to their high demand and ease of stocking; however, they may face challenges such as limited product variety and potential spoilage, especially for perishable goods.
Automated Retail Kiosks
Automated retail kiosks represent a significant evolution in vending technology, merging traditional vending with e-commerce capabilities. These machines can offer a diverse range of products, including electronics and personal care items, making them suitable for retail environments and airports. While they present high profit margins and a broad product range, buyers must consider the higher initial investment and the need for ongoing technical support to maintain functionality.
Health-Conscious Vending
With a growing emphasis on wellness, health-conscious vending machines focus on offering organic snacks and beverages. These machines are particularly popular in gyms, health centers, and schools, appealing to consumers’ desire for healthier options. B2B buyers should note that while these machines can attract niche markets and align with health trends, they may have a smaller target audience and higher operational costs due to the premium nature of the products.
Customized Product Vending
Customized product vending machines allow businesses to curate and personalize the offerings based on specific needs and preferences. Commonly used in corporate offices and events, these machines enhance brand engagement by providing tailored product selections. While this approach can lead to increased customer satisfaction, it also introduces operational complexities and requires regular updates to maintain relevance and appeal.
Multilingual Vending Machines
Multilingual vending machines cater to diverse populations by offering language options that enhance user experience, particularly in tourist areas and international events. By increasing accessibility, these machines can attract a broader customer base. However, B2B buyers should be aware that maintaining such machines may require additional software updates and ongoing maintenance to ensure all language options function correctly.
Key Industrial Applications of wall vending machines
Industry/Sector | Specific Application of Wall Vending Machines | Value/Benefit for the Business | Key Sourcing Considerations for this Application |
---|---|---|---|
Retail | Automated retail for convenience items | Increased sales through 24/7 accessibility | Machine durability, payment system integration |
Healthcare | Dispensing of medical supplies | Quick access to essential items in emergencies | Compliance with health regulations, sterilization |
Education | Supply of stationery and snacks | Supports student convenience and satisfaction | Size and capacity, ease of restocking |
Transportation & Logistics | Offering travel essentials at transit hubs | Enhances passenger experience and generates additional revenue | Location suitability, vending machine maintenance |
Hospitality | Room service alternatives | Improves guest experience and operational efficiency | Product variety, user-friendly interface |
Retail
In the retail sector, wall vending machines serve as automated retail outlets for convenience items such as snacks, beverages, and personal care products. They allow businesses to operate around the clock, catering to customers’ needs outside traditional store hours. This model not only increases sales but also reduces labor costs associated with staffing. For international buyers, particularly in regions like Africa and South America, considerations include the machine’s durability in various climates and the integration of reliable payment systems that cater to local preferences.
Healthcare
In healthcare settings, wall vending machines can dispense essential medical supplies, such as first aid kits, personal protective equipment, and over-the-counter medications. These machines provide quick access to critical items during emergencies, significantly improving response times. Buyers in this sector must ensure compliance with health regulations, including sterilization and hygiene standards, to maintain patient safety. Sourcing machines that can withstand rigorous cleaning protocols is crucial, especially in hospitals and clinics.
Education
Wall vending machines in educational institutions primarily supply stationery, snacks, and beverages to students. This application enhances student convenience and satisfaction, allowing them to access essential items during busy school hours. For international B2B buyers from regions like the Middle East and Europe, it’s important to consider the machine’s size and capacity to meet the demands of varying student populations. Additionally, ease of restocking and maintenance is vital for uninterrupted service.
Transportation & Logistics
In the transportation sector, wall vending machines are strategically placed at transit hubs, such as airports and bus stations, to offer travel essentials like snacks, drinks, and personal care items. This application enhances the passenger experience and generates additional revenue for transportation providers. Buyers should assess the suitability of machine locations and ensure that maintenance services are readily available to keep machines operational. Understanding local consumer preferences is also key to stocking the right products.
Hospitality
In the hospitality industry, wall vending machines provide an alternative to traditional room service by offering guests a selection of snacks, drinks, and travel necessities. This not only improves the guest experience but also enhances operational efficiency by reducing the workload on staff. For B2B buyers, it’s essential to consider the variety of products offered and ensure that the machines feature a user-friendly interface for guest convenience. Additionally, sourcing machines that can adapt to different hotel environments is crucial for success.
Related Video: Kooler Ice Vending Machines – IM600XL vs. IM1000
Strategic Material Selection Guide for wall vending machines
When selecting materials for wall vending machines, international B2B buyers must consider several factors, including the specific application, environmental conditions, and compliance with regional standards. Below is an analysis of four common materials used in the construction of wall vending machines, focusing on their properties, advantages, disadvantages, and specific considerations for buyers from Africa, South America, the Middle East, and Europe.
1. Stainless Steel
Key Properties: Stainless steel is known for its excellent corrosion resistance, high tensile strength, and ability to withstand a wide range of temperatures. It typically has a temperature rating of up to 800°F (427°C) and is resistant to rust and staining.
Pros & Cons: The durability of stainless steel makes it ideal for high-traffic areas. However, it can be more expensive than other materials, which may impact the overall cost of the vending machine. Manufacturing complexity is moderate, as it requires specialized welding techniques.
Impact on Application: Stainless steel is suitable for various media, including food and beverages, due to its non-reactive nature. This makes it a preferred choice for vending machines dispensing consumables.
Considerations for International Buyers: Buyers should ensure compliance with food safety standards such as FDA or EU regulations. Common grades like 304 and 316 are often specified based on the intended use and environmental exposure.
2. Mild Steel
Key Properties: Mild steel is characterized by its good weldability and machinability, with a typical tensile strength of around 250 MPa. It is less resistant to corrosion compared to stainless steel but can be treated for enhanced durability.
Pros & Cons: The primary advantage of mild steel is its lower cost, making it an economical choice for manufacturers. However, its susceptibility to rust and corrosion can limit its application in humid or harsh environments, necessitating protective coatings.
Impact on Application: Mild steel is suitable for non-food vending applications, such as dispensing tools or electronics. Its lower strength may not be ideal for heavy-duty use.
Considerations for International Buyers: Buyers should consider local environmental conditions that may affect the longevity of mild steel. Compliance with standards like ASTM A36 is essential for quality assurance.
3. Aluminum
Key Properties: Aluminum is lightweight, with a density of about 2.7 g/cm³, and offers good corrosion resistance. It has a melting point of approximately 660°C (1220°F), making it suitable for various applications.
Pros & Cons: The lightweight nature of aluminum facilitates easy installation and transport. However, it may not be as strong as steel, which can be a limitation for heavy-use scenarios. The cost is generally moderate, depending on the alloy used.
Impact on Application: Aluminum is often used in vending machines designed for outdoor use due to its corrosion resistance. It is compatible with a range of media, including snacks and beverages.
Considerations for International Buyers: Buyers should verify compliance with local regulations regarding aluminum use in food contact applications. Standards such as JIS H 4000 may apply in certain regions.
4. Polycarbonate
Key Properties: Polycarbonate is a high-impact thermoplastic with excellent transparency and UV resistance. It can withstand temperatures ranging from -40°C to 120°C (-40°F to 248°F), making it versatile for various environments.
Pros & Cons: The primary advantage of polycarbonate is its lightweight and shatter-resistant properties, making it ideal for transparent panels on vending machines. However, it may not be as durable as metals in terms of structural integrity and can be more expensive than other plastics.
Impact on Application: Polycarbonate is suitable for displaying products clearly while protecting them from environmental elements. It is commonly used for vending machines in public spaces.
Considerations for International Buyers: Buyers should ensure that polycarbonate materials meet relevant safety standards, such as those set by ASTM or ISO. Understanding the specific grades and their applications is crucial for performance.
Summary Table
Material | Typical Use Case for wall vending machines | Key Advantage | Key Disadvantage/Limitation | Relative Cost (Low/Med/High) |
---|---|---|---|---|
Stainless Steel | Food and beverage dispensing | Excellent corrosion resistance | Higher cost compared to other materials | High |
Mild Steel | Non-food items like tools or electronics | Cost-effective | Susceptible to rust without protective coating | Low |
Aluminum | Outdoor vending machines | Lightweight and corrosion-resistant | Lower strength compared to steel | Medium |
Polycarbonate | Transparent panels for product display | Shatter-resistant and lightweight | Less durable than metals | Medium |
This guide provides a comprehensive overview for international B2B buyers, enabling informed decisions based on material properties, application suitability, and compliance with regional standards.
In-depth Look: Manufacturing Processes and Quality Assurance for wall vending machines
Manufacturing Processes for Wall Vending Machines
The manufacturing of wall vending machines involves several critical stages that ensure both functionality and durability. Understanding these stages is essential for B2B buyers looking to procure high-quality vending machines.
1. Material Preparation
The initial stage of manufacturing begins with material selection and preparation. Common materials used include:
- Steel: Often used for the machine’s frame due to its strength and durability.
- Plastic: Used for internal components and sometimes for external casing to reduce weight.
- Glass: Utilized for display windows to showcase products.
Materials undergo processes such as cutting, bending, and treating to enhance durability and resistance to environmental factors. Buyers should inquire about the sourcing and specifications of these materials to ensure compliance with international standards.
2. Forming
In this stage, raw materials are shaped into the necessary components. Key techniques include:
- CNC Machining: This technology allows for precise cutting and shaping of metal parts, ensuring uniformity and reducing waste.
- Injection Molding: Commonly used for plastic parts, this process enables the mass production of complex shapes with high precision.
- Sheet Metal Fabrication: Essential for creating the outer shell of the vending machines, this process involves cutting, folding, and welding metal sheets.
Buyers should evaluate suppliers based on their capabilities in these techniques, as they directly impact the machine’s quality and longevity.
3. Assembly
The assembly process involves integrating all the manufactured components. Key steps include:
- Component Assembly: This includes the installation of electronic systems, payment mechanisms, and product storage compartments.
- Testing of Mechanical Parts: Each component is tested for functionality, ensuring that moving parts operate smoothly.
- Integration of Software: If applicable, software systems for inventory management and user interface are installed and tested.
International B2B buyers should ensure that suppliers have a documented assembly procedure, including training for assembly line workers, to maintain quality control.
4. Finishing
The final stage of manufacturing focuses on the aesthetic and functional finishing touches:
- Painting and Coating: Machines are often powder-coated or painted to enhance appearance and protect against corrosion.
- Quality Inspection: Visual inspections are conducted to check for surface defects and overall finish quality.
- Final Assembly Check: A comprehensive check is performed to ensure that all components fit together correctly and function as intended.
B2B buyers should request samples or images of finished products to assess the quality of the finish.
Quality Assurance (QA) in Manufacturing
Quality assurance is crucial in the manufacturing of wall vending machines. It ensures that the machines not only meet functional requirements but also comply with international standards.
International Standards
Key international standards relevant to the manufacturing process include:
- ISO 9001: This standard focuses on quality management systems and ensures that suppliers maintain high standards in their manufacturing processes.
- CE Marking: This indicates compliance with EU safety, health, and environmental requirements, crucial for buyers in Europe.
- API Standards: Particularly relevant for vending machines that dispense food or beverages, ensuring hygiene and safety standards are met.
Understanding these standards helps buyers assess potential suppliers’ credibility and product safety.
Quality Control Checkpoints
Quality control (QC) checkpoints are essential throughout the manufacturing process:
- Incoming Quality Control (IQC): This involves inspecting raw materials upon arrival to ensure they meet specified standards.
- In-Process Quality Control (IPQC): Regular inspections during manufacturing help catch defects early in the process.
- Final Quality Control (FQC): A comprehensive inspection of the finished product ensures it meets all functional and aesthetic requirements.
Buyers should inquire about the frequency and nature of these inspections to gauge the supplier’s commitment to quality.
Common Testing Methods
Testing methods employed during the manufacturing process include:
- Functional Testing: Ensures that all electronic components and payment systems work correctly.
- Durability Testing: Simulates real-world conditions to assess the machine’s resilience.
- Safety Testing: Checks for electrical safety and compliance with regulatory standards.
B2B buyers should seek suppliers that provide detailed reports on testing outcomes, which can serve as proof of quality assurance.
Verifying Supplier Quality Control
For international B2B buyers, verifying a supplier’s quality control processes is vital. Here are actionable strategies:
- Audits: Conduct regular audits of supplier facilities to assess their adherence to quality standards and manufacturing processes.
- Quality Reports: Request detailed quality assurance documentation, including IQC, IPQC, and FQC reports.
- Third-Party Inspections: Engage independent inspectors to evaluate the manufacturing process and product quality.
Understanding the nuances of quality control and assurance can significantly impact the reliability of wall vending machines purchased, especially in diverse markets such as Africa, South America, the Middle East, and Europe.
Conclusion
A comprehensive understanding of the manufacturing processes and quality assurance practices for wall vending machines is crucial for B2B buyers. By focusing on material preparation, forming, assembly, and finishing, along with rigorous quality control measures, buyers can make informed decisions that align with their operational needs and international standards.
Related Video: Most Satisfying Factory Production Processes And Heavy-Duty Factory Machines!
Comprehensive Cost and Pricing Analysis for wall vending machines Sourcing
Cost Structure of Wall Vending Machines
When sourcing wall vending machines, understanding the cost components is essential for effective budgeting and negotiating with suppliers. The primary cost elements include:
-
Materials: The cost of raw materials such as metal, plastics, and electronic components can vary significantly based on quality and sourcing location. For instance, locally sourced materials may reduce costs but could compromise on quality.
-
Labor: Labor costs depend on the region where manufacturing occurs. Countries with lower labor costs, like some in Southeast Asia, may offer more competitive pricing, but buyers should consider the trade-offs in terms of quality and reliability.
-
Manufacturing Overhead: This includes utilities, rent, and administrative expenses related to production. Efficient manufacturing processes can help reduce these costs.
-
Tooling: Initial setup costs for molds and machinery used to create the vending machines can be substantial. These costs are often spread over larger production runs, making bulk orders more cost-effective.
-
Quality Control (QC): Ensuring that the machines meet specified standards requires investment in quality control processes. This could involve additional testing and inspection protocols, which should be factored into the overall cost.
-
Logistics: Shipping costs can vary widely based on the distance, shipping method, and Incoterms. Understanding these can help buyers anticipate total costs.
-
Margin: Suppliers will typically include a profit margin in their pricing, which can vary based on market conditions and competition.
Price Influencers in Sourcing
Several factors influence the pricing of wall vending machines:
-
Volume/MOQ: Minimum order quantities (MOQ) can significantly impact pricing. Higher volumes often lead to lower per-unit costs due to economies of scale.
-
Specifications/Customization: Customized machines that meet specific requirements may incur additional costs. Standard models are generally more affordable.
-
Materials Quality/Certifications: Higher quality materials and certifications (like ISO or CE) typically increase costs but can enhance machine durability and reliability.
-
Supplier Factors: The supplier’s reputation, location, and relationship with buyers can affect pricing. Established suppliers may offer better terms but at a higher price point.
-
Incoterms: The terms of shipping (e.g., FOB, CIF) play a crucial role in determining the final cost. Understanding these terms can help buyers manage risks and costs associated with transportation.
Buyer Tips for Cost-Efficiency
For international B2B buyers, particularly in Africa, South America, the Middle East, and Europe, the following tips can enhance cost-efficiency:
-
Negotiation: Leverage competitive quotes from multiple suppliers to negotiate better terms. Highlighting long-term partnership potential can also yield favorable pricing.
-
Total Cost of Ownership (TCO): Evaluate not just the initial purchase price but also the long-term costs associated with maintenance, repair, and operational efficiency. A higher upfront cost may be justified by lower TCO.
-
Pricing Nuances: Be aware of regional pricing strategies. For example, suppliers in Europe may have different pricing structures compared to those in Asia or Africa, influenced by local demand, currency fluctuations, and import tariffs.
-
Customization Awareness: If customization is necessary, ensure that the specifications are clear to avoid unexpected costs. Request samples or prototypes to validate quality before committing to larger orders.
-
Stay Updated on Market Trends: Understanding current market trends, including supply chain disruptions or material shortages, can help in making informed purchasing decisions and anticipating price fluctuations.
Disclaimer on Pricing
It is important to note that the prices for wall vending machines can vary widely based on the factors discussed. Buyers should seek detailed quotations and conduct thorough market research to obtain the most accurate pricing information for their specific needs.
Spotlight on Potential wall vending machines Manufacturers and Suppliers
This section offers a look at a few manufacturers active in the ‘wall vending machines’ market. This is a representative sample for illustrative purposes; B2B buyers must conduct their own extensive due diligence before any engagement. Information is synthesized from public sources and general industry knowledge.
Essential Technical Properties and Trade Terminology for wall vending machines
Key Technical Properties of Wall Vending Machines
When considering the procurement of wall vending machines, understanding their technical specifications is crucial for ensuring that the product meets operational requirements and regulatory standards. Here are several critical specifications:
-
Material Grade
Wall vending machines are typically constructed from materials such as stainless steel or high-grade plastic. Stainless steel is favored for its durability, corrosion resistance, and aesthetic appeal, while high-grade plastics can reduce weight and costs. Selecting the right material impacts the machine’s lifespan and maintenance needs. -
Dimensions and Weight Capacity
The size of the vending machine, including height, width, and depth, is essential for installation in specific wall spaces. Additionally, understanding the weight capacity ensures that the machine can support the products intended for sale, minimizing the risk of structural failure. -
Power Consumption
This specification indicates how much energy the vending machine will use during operation. A lower power consumption rating not only reduces operational costs but also supports sustainability initiatives. Buyers should consider energy-efficient models that comply with local regulations. -
Temperature Control Range
For machines intended to sell perishable goods, temperature control is vital. Specifications should include the operational temperature range and the ability to maintain consistent temperatures, which is essential for food safety and product quality. -
User Interface Technology
The interface of the vending machine—whether touchscreen, keypad, or app-based—affects user experience and operational efficiency. An intuitive interface can reduce transaction times and enhance customer satisfaction, which is critical for maximizing sales. -
Payment Acceptance Options
Modern vending machines support multiple payment methods, including cash, credit/debit cards, and mobile payments. Understanding the payment options available is vital for attracting a broader customer base and ensuring seamless transactions.
Common Trade Terminology in the Vending Machine Industry
Familiarity with industry jargon can streamline communication and negotiations in the procurement process. Here are key terms often encountered:
-
OEM (Original Equipment Manufacturer)
This term refers to companies that produce components that are used in another company’s end products. In the context of wall vending machines, an OEM might supply specific parts or the entire machine, which can affect pricing and quality assurance. -
MOQ (Minimum Order Quantity)
MOQ is the smallest quantity of a product that a supplier is willing to sell. Understanding the MOQ is essential for budgeting and inventory management, particularly for international buyers looking to optimize shipping costs and stock levels. -
RFQ (Request for Quotation)
An RFQ is a document sent to suppliers requesting a quote for specific products or services. For wall vending machines, an RFQ can include specifications, quantities, and delivery timelines, allowing buyers to compare offers effectively. -
Incoterms (International Commercial Terms)
These are predefined commercial terms published by the International Chamber of Commerce (ICC) that clarify the responsibilities of buyers and sellers in international transactions. Familiarity with Incoterms such as FOB (Free On Board) or CIF (Cost Insurance and Freight) can help buyers manage shipping logistics and costs effectively. -
Lead Time
Lead time refers to the period between placing an order and receiving the product. Understanding lead times is crucial for inventory planning, especially when coordinating with suppliers across different regions.
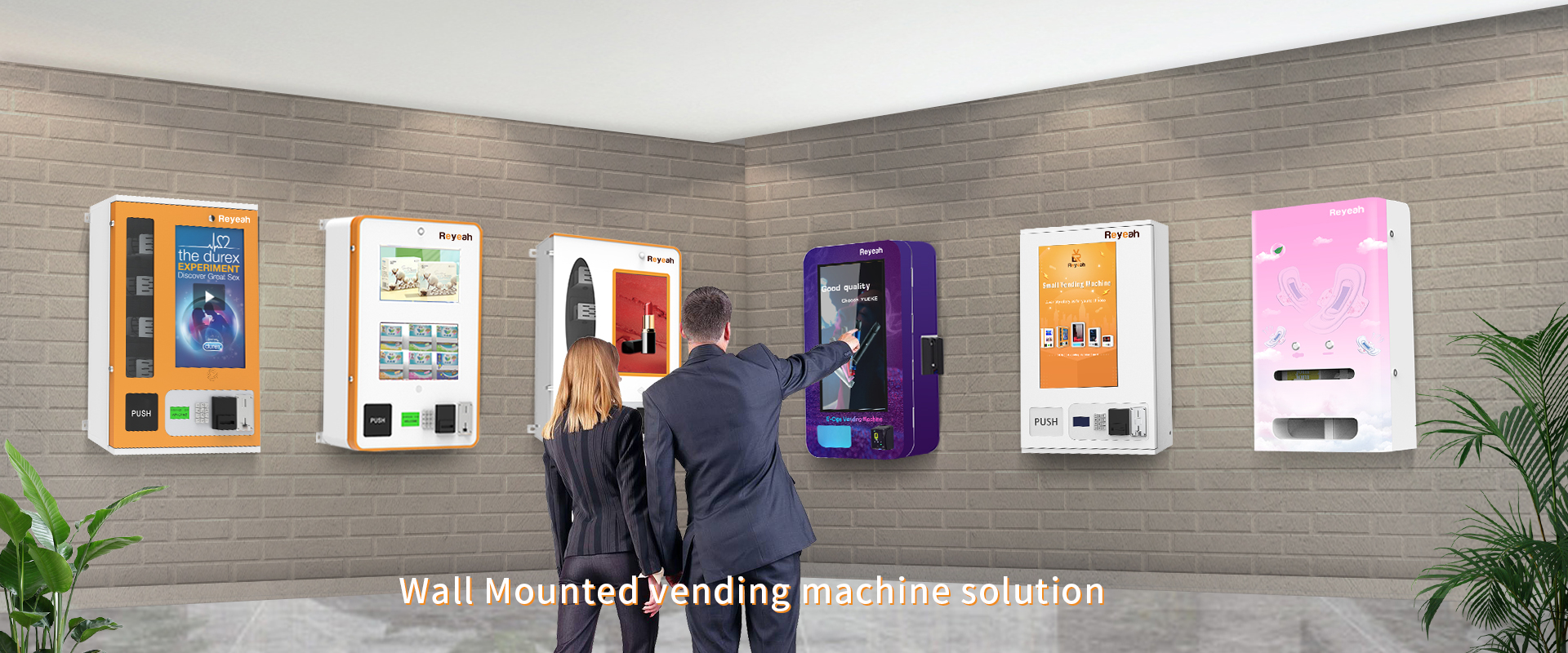
Illustrative Image (Source: Google Search)
- Warranty
A warranty is a promise made by the manufacturer regarding the condition of the product, typically covering repairs or replacements for a specified period. Knowing the warranty terms can provide buyers with peace of mind regarding the long-term performance of their vending machines.
Understanding these technical specifications and trade terminologies will equip international B2B buyers with the necessary insights to make informed purchasing decisions regarding wall vending machines, enhancing both operational efficiency and customer satisfaction.
Navigating Market Dynamics, Sourcing Trends, and Sustainability in the wall vending machines Sector
Global demand for wall vending machines has been fueled by several market drivers, including urbanization, technological advancements, and changing consumer behaviors. As more people live in urban areas and seek convenience, wall vending machines offer quick access to snacks, beverages, and essential goods. Emerging technologies, such as cashless payment systems and remote inventory management, are transforming the vending machine landscape. Buyers should keep an eye on trends like smart vending solutions that integrate IoT technology, allowing for real-time data analysis and enhanced customer engagement.
For international B2B buyers, understanding regional market dynamics is crucial. In Africa and South America, the rising middle class and increased disposable income are propelling demand for vending machines in public spaces. Meanwhile, in the Middle East and Europe, there is a growing emphasis on customization and premium offerings, with businesses seeking machines that cater to local tastes and preferences. Additionally, sustainability is becoming a key concern, with companies looking for energy-efficient machines and sustainable products.
Sustainability & Ethical Sourcing in B2B
The environmental impact of vending machines is an important consideration for B2B buyers. The energy consumption of traditional machines can be significant, prompting a shift towards energy-efficient models that reduce carbon footprints. Buyers should look for wall vending machines equipped with LED lighting, energy-saving compressors, and eco-friendly materials.
Moreover, ethical sourcing is critical in today’s market. Suppliers should prioritize transparent supply chains that ensure fair labor practices and sustainable material sourcing. Certifications such as Fair Trade, ISO 14001 (Environmental Management), and LEED (Leadership in Energy and Environmental Design) can guide buyers in selecting responsible vendors. Using recyclable materials and promoting waste reduction initiatives can also enhance brand reputation and attract environmentally conscious consumers.
Brief Evolution/History
The concept of vending machines dates back to ancient Greece, where devices dispensed holy water in exchange for coins. However, the modern vending machine era began in the late 19th century, with the introduction of coin-operated machines for selling postcards and gum. Over the decades, vending machines evolved to include a wider range of products, adapting to consumer needs and technological advancements. Today, wall vending machines represent a fusion of convenience and innovation, meeting the demands of a fast-paced world while embracing sustainability and ethical practices.
In summary, international B2B buyers should consider market dynamics, sustainability, and ethical sourcing when navigating the wall vending machine sector. By staying informed about trends and prioritizing responsible practices, businesses can not only enhance their operational efficiency but also contribute positively to the environment and society.
Related Video: Global Trade & Logistics – What is Global Trade?
Frequently Asked Questions (FAQs) for B2B Buyers of wall vending machines
-
What should I consider when vetting suppliers for wall vending machines?
When vetting suppliers, prioritize their reputation, experience, and certifications. Check for industry-specific accreditations and customer reviews. Request references and case studies to assess their previous work. It’s also essential to verify their production capacity and compliance with international standards. Engaging in direct conversations can provide insights into their reliability and responsiveness, ensuring they align with your operational needs. -
Can I customize wall vending machines to fit my brand?
Yes, most manufacturers offer customization options, including branding, size, and features. Discuss your specific requirements with potential suppliers, such as color schemes, logo placements, and product offerings. Ensure that the customization process is clearly outlined, including design proofs and timelines. This way, you can create a unique vending solution that resonates with your target market while maintaining operational efficiency. -
What are typical minimum order quantities (MOQ) and lead times?
Minimum order quantities vary by supplier, often ranging from 10 to 100 units. Lead times can depend on customization requirements and manufacturing capabilities, typically taking 4 to 12 weeks. Be sure to clarify these details during negotiations and consider potential delays due to shipping or production issues. Understanding these factors helps in planning your inventory and cash flow effectively. -
What payment terms should I expect when purchasing wall vending machines?
Payment terms can vary widely among suppliers. Common practices include a deposit (20-50%) upon order confirmation, with the balance due before shipment. Some suppliers may offer credit terms or payment through letters of credit for larger orders. Always negotiate terms that align with your cash flow and risk tolerance, and ensure all agreements are documented to avoid disputes. -
How can I ensure quality assurance and certifications for wall vending machines?
Request documentation of quality assurance processes and relevant certifications (e.g., CE, ISO) from suppliers. Conduct audits or inspections before shipment to verify compliance with your quality standards. Additionally, inquire about warranty terms and after-sales support, which can safeguard your investment and ensure customer satisfaction in your market. -
What logistics considerations should I keep in mind for importing wall vending machines?
Logistics can be complex when importing wall vending machines. Evaluate shipping methods, customs regulations, and potential tariffs in your country. Collaborate with logistics partners experienced in international trade to streamline the import process. Additionally, ensure that the supplier provides proper documentation to facilitate smooth customs clearance and timely delivery. -
How should I handle disputes with suppliers?
Establish clear communication channels and protocols for resolving disputes before finalizing contracts. In the event of a disagreement, attempt to resolve issues amicably through direct dialogue. If necessary, refer to the terms outlined in your purchase agreement regarding dispute resolution, which may include mediation or arbitration. Maintaining a professional relationship can often lead to favorable outcomes for both parties. -
What are the best practices for maintaining wall vending machines?
Regular maintenance is crucial for the longevity of wall vending machines. Establish a routine cleaning and restocking schedule to ensure optimal performance. Train your staff on basic troubleshooting and maintenance procedures. Additionally, consider implementing a monitoring system to track sales and inventory levels, which can help in timely restocking and identifying any operational issues early on.
Strategic Sourcing Conclusion and Outlook for wall vending machines
In conclusion, the strategic sourcing of wall vending machines presents significant opportunities for international B2B buyers, particularly in emerging markets across Africa, South America, the Middle East, and Europe. Buyers should focus on understanding local consumer preferences, regulatory requirements, and technological advancements to maximize their investment in this sector. Engaging with reliable suppliers who offer customized solutions can enhance operational efficiency and drive sales.
Key takeaways include:
- Market Demand: Assess the growing demand for convenience and automated solutions in various industries.
- Supplier Relationships: Cultivate strong partnerships with manufacturers that understand local market dynamics and can provide ongoing support.
- Innovation and Adaptation: Stay informed about the latest trends in vending technology, including cashless payments and smart inventory management.
As the wall vending machine market evolves, now is the time for buyers to act strategically. By leveraging these insights, businesses can position themselves for success in a competitive landscape. Take the next step by exploring potential suppliers and solutions that align with your business objectives, ensuring you remain at the forefront of this dynamic industry.