Master Sourcing the Best Ball Vending Machine for Your
Guide to Ball Vending Machine
- Introduction: Navigating the Global Market for ball vending machine
- Understanding ball vending machine Types and Variations
- Key Industrial Applications of ball vending machine
- Strategic Material Selection Guide for ball vending machine
- In-depth Look: Manufacturing Processes and Quality Assurance for ball vending machine
- Comprehensive Cost and Pricing Analysis for ball vending machine Sourcing
- Spotlight on Potential ball vending machine Manufacturers and Suppliers
- Essential Technical Properties and Trade Terminology for ball vending machine
- Navigating Market Dynamics, Sourcing Trends, and Sustainability in the ball vending machine Sector
- Frequently Asked Questions (FAQs) for B2B Buyers of ball vending machine
- Strategic Sourcing Conclusion and Outlook for ball vending machine
Introduction: Navigating the Global Market for ball vending machine
In an increasingly competitive global market, the ball vending machine has emerged as a critical asset for businesses aiming to enhance customer engagement and drive revenue. These machines not only offer a unique and interactive experience but also tap into the growing trend of automated retail solutions. As international B2B buyers, particularly from Africa, South America, the Middle East, and Europe, you must understand the intricacies of sourcing and implementing these machines to leverage their full potential.
This comprehensive guide serves as your essential resource, providing valuable insights into various aspects of ball vending machines. From exploring the different types available—such as traditional, digital, and themed machines—to understanding the materials used in their construction, we cover all bases. Additionally, we delve into manufacturing processes and quality control measures that ensure durability and reliability, alongside a curated list of reputable suppliers.
Cost analysis is a key component, highlighting not only the initial investment but also long-term operational expenses. Moreover, we examine market trends, helping you identify lucrative opportunities within your region. To address common concerns, our FAQ section offers straightforward answers to your pressing questions.
By equipping yourself with this knowledge, you will make informed sourcing decisions that align with your business goals, ensuring you stay ahead in the dynamic landscape of automated retail.
Understanding ball vending machine Types and Variations
Type Name | Key Distinguishing Features | Primary B2B Applications | Brief Pros & Cons for Buyers |
---|---|---|---|
Standard Ball Vending | Simple design, mechanical operation | Retail stores, amusement parks | Pros: Easy maintenance, cost-effective. Cons: Limited product variety. |
Electronic Ball Vending | Digital interface, accepts cash and cards | Shopping malls, sports venues | Pros: Higher security, diverse payment options. Cons: Higher initial cost. |
Customizable Vending | Tailored design for specific products | Specialty stores, events | Pros: Increased brand visibility, tailored offerings. Cons: Longer lead times, higher investment. |
Dual-Product Vending | Dispenses two types of balls simultaneously | Sports facilities, schools | Pros: Versatile use, increased sales potential. Cons: More complex mechanics, potential for jams. |
Eco-friendly Vending | Made from sustainable materials, energy-efficient | Eco-conscious businesses, parks | Pros: Appeals to environmentally aware consumers. Cons: Potentially higher costs, limited availability. |
Standard Ball Vending
Standard ball vending machines are characterized by their straightforward mechanical design, making them easy to operate and maintain. These machines typically dispense a single type of ball and are widely used in retail environments and amusement parks. When considering a purchase, B2B buyers should note the low initial costs and ease of maintenance, but they may find the limited product variety a drawback for attracting diverse customer interests.
Electronic Ball Vending
Electronic ball vending machines incorporate digital interfaces and accept various payment methods, including cash and credit cards. This feature makes them suitable for high-traffic areas such as shopping malls and sports venues. Buyers should weigh the benefits of enhanced security and convenience against the higher initial investment and potential technical issues that may arise with electronic components.
Customizable Vending
Customizable vending machines allow businesses to tailor the design and product offerings to meet specific customer needs. These machines are ideal for specialty stores and events where branding is crucial. While they offer increased brand visibility and tailored product selections, buyers must consider the longer lead times and higher costs associated with customization, which may not be feasible for every business.
Dual-Product Vending
Dual-product vending machines can dispense two different types of balls at once, making them versatile options for sports facilities and schools. This capability can enhance sales potential by catering to varied customer preferences. However, buyers should be aware of the more complex mechanics involved, which may lead to potential jams and require more frequent maintenance.
Eco-friendly Vending
Eco-friendly vending machines are constructed from sustainable materials and designed to be energy-efficient. They cater to environmentally conscious businesses and parks looking to reduce their carbon footprint. While these machines can attract eco-aware consumers and enhance corporate responsibility, buyers should consider the potentially higher costs and availability challenges, as these products may not be as widely produced.
Related Video: Machine Learning in 2024 – Beginner’s Course
Key Industrial Applications of ball vending machine
Industry/Sector | Specific Application of ball vending machine | Value/Benefit for the Business | Key Sourcing Considerations for this Application |
---|---|---|---|
Retail | Automated product dispensing | Increased sales volume, reduced labor costs | Machine size, customization options, payment systems |
Sports & Recreation | Sports equipment rental | Enhanced customer experience, convenience | Durability, inventory tracking, maintenance support |
Education | Educational supplies distribution | Improved access to learning materials | Product variety, ease of use, refill frequency |
Events & Entertainment | Promotional item distribution | Brand visibility, customer engagement | Custom branding options, security features, location |
Healthcare | Medical supplies dispensing | Improved efficiency in patient care | Compliance with health regulations, product safety, reliability |
Retail
In the retail sector, ball vending machines serve as automated product dispensers for items such as snacks, beverages, and small electronics. They are strategically placed to maximize visibility and accessibility, allowing customers to purchase products quickly and conveniently. This reduces the need for staff to manage sales directly, thus lowering labor costs. International buyers should focus on machine size, customization options, and integrated payment systems to ensure a seamless shopping experience.
Sports & Recreation
In sports and recreation, ball vending machines are used to rent out sports equipment, such as balls for soccer, basketball, or tennis. These machines are often located in parks, sports complexes, or recreation centers, providing easy access for users. They enhance customer experience by offering a convenient way to obtain equipment without the need for staff assistance. Buyers should prioritize durability, inventory tracking capabilities, and maintenance support when sourcing these machines, especially in regions with high usage rates.
Education
Educational institutions utilize ball vending machines to distribute learning materials like stationery, textbooks, or even educational toys. This automated distribution model ensures that students have easy access to essential supplies, fostering a better learning environment. For international buyers, it is critical to consider the variety of products offered, ease of use for students, and the frequency of restocking to maintain inventory levels efficiently.
Events & Entertainment
In the events and entertainment industry, ball vending machines can be employed to distribute promotional items, such as branded merchandise or event souvenirs. This not only boosts brand visibility but also enhances customer engagement during events. When sourcing these machines, it is essential to look for options that allow for custom branding, security features to protect merchandise, and strategic placement for maximum impact at events.
Healthcare
In healthcare settings, ball vending machines are increasingly used to dispense medical supplies like bandages, sanitizers, or over-the-counter medications. This innovation streamlines patient care by providing easy access to essential items, especially in emergency situations. Buyers in the healthcare sector must ensure compliance with health regulations, prioritize product safety, and evaluate the reliability of the machines to maintain high standards of care.
Related Video: DIY Vending Machine – Arduino based Mechatronics Project
Strategic Material Selection Guide for ball vending machine
When selecting materials for ball vending machines, it is essential to consider their properties, advantages, disadvantages, and suitability for specific applications. Below is a detailed analysis of four common materials used in the construction of ball vending machines, tailored for international B2B buyers from regions such as Africa, South America, the Middle East, and Europe.
1. Stainless Steel
Key Properties:
Stainless steel offers excellent corrosion resistance, high strength, and durability. It can withstand a wide range of temperatures and pressures, making it suitable for various environments.
Pros & Cons:
The primary advantage of stainless steel is its resistance to rust and corrosion, which is crucial for machines exposed to moisture and varying temperatures. However, it is more expensive than other materials and can be challenging to machine, potentially increasing manufacturing complexity.
Impact on Application:
Stainless steel is compatible with a variety of media, including food products, making it ideal for vending machines that dispense snacks or beverages. Its hygienic properties also make it suitable for food-grade applications.
Considerations for International Buyers:
Buyers should ensure compliance with food safety standards (e.g., FDA in the USA, EU regulations in Europe). Common grades like 304 and 316 should meet ASTM and DIN standards.
2. Carbon Steel
Key Properties:
Carbon steel is known for its high strength and durability but lacks the corrosion resistance found in stainless steel.
Pros & Cons:
It is cost-effective and easy to machine, making it a popular choice for structural components of vending machines. However, it is susceptible to corrosion if not adequately protected, which may lead to increased maintenance costs over time.
Impact on Application:
Carbon steel is suitable for non-corrosive environments and can be used for internal components that do not come into direct contact with food or liquids.
Considerations for International Buyers:
Buyers should consider protective coatings or galvanization to enhance corrosion resistance. Compliance with standards like ASTM A36 is essential for structural integrity.
3. Aluminum
Key Properties:
Aluminum is lightweight, corrosion-resistant, and has good thermal conductivity. It is also easy to machine and form.
Pros & Cons:
The main advantage of aluminum is its lightweight nature, which can reduce shipping costs and ease installation. However, it may not be as strong as steel and can be more expensive than carbon steel.
Impact on Application:
Aluminum is suitable for components that require a lightweight yet durable material, such as the outer casing of vending machines. Its corrosion resistance makes it ideal for outdoor applications.
Considerations for International Buyers:
International buyers should ensure that the aluminum grade meets relevant standards (e.g., ASTM B221). Consideration of local environmental conditions is also vital, as certain alloys may perform better in specific climates.
4. Plastic (Polycarbonate or ABS)
Key Properties:
Plastics like polycarbonate and ABS are lightweight, impact-resistant, and offer good chemical resistance.
Pros & Cons:
Plastic materials are cost-effective and easy to mold into complex shapes, making them suitable for various components. However, they may not withstand high temperatures and can degrade under UV exposure unless treated.
Impact on Application:
Plastics are ideal for transparent panels or components that require visibility, such as the viewing windows of vending machines. They are also suitable for internal parts that do not experience heavy loads.
Considerations for International Buyers:
Buyers should verify that the plastic materials comply with local regulations regarding food safety and environmental impact. Standards such as ASTM D638 for tensile properties may also be relevant.
Summary Table
Material | Typical Use Case for ball vending machine | Key Advantage | Key Disadvantage/Limitation | Relative Cost (Low/Med/High) |
---|---|---|---|---|
Stainless Steel | Food-grade applications, external casing | Excellent corrosion resistance | Higher cost, machining complexity | High |
Carbon Steel | Structural components, internal parts | Cost-effective, high strength | Susceptible to corrosion | Low |
Aluminum | Outer casing, lightweight components | Lightweight, good corrosion resistance | Lower strength than steel | Medium |
Plastic (Polycarbonate/ABS) | Transparent panels, internal components | Cost-effective, easy to mold | Limited temperature resistance, UV degradation | Low |
This guide provides a comprehensive overview of the strategic material selection for ball vending machines, enabling international B2B buyers to make informed decisions based on their specific needs and regional considerations.
In-depth Look: Manufacturing Processes and Quality Assurance for ball vending machine
Manufacturing Processes for Ball Vending Machines
The manufacturing of ball vending machines involves several critical stages, each designed to ensure the final product meets the required quality and functionality standards. Below is an overview of the main stages in the manufacturing process:
1. Material Preparation
The first step involves sourcing high-quality materials that can withstand the rigors of operation in various environments. Common materials include:
- Metal (steel or aluminum) for structural components, ensuring durability and resistance to wear.
- Plastic for the vending mechanism and exterior casing, often selected for its lightweight properties and ease of molding.
- Electronic components such as motors and sensors, which are crucial for the machine’s operation.
Before manufacturing begins, materials undergo inspections to verify their quality and compliance with international standards.
2. Forming
This stage typically involves several techniques to shape the prepared materials into the desired components:
- Cutting and Machining: Metal sheets are cut and machined to form the chassis and other structural parts. Precision is critical to ensure all components fit together seamlessly.
- Injection Molding: Used for creating plastic parts, this technique allows for complex shapes and is efficient for mass production.
- Bending and Stamping: These processes shape metal components, particularly for the machine’s frame and panels.
3. Assembly
Once individual components are formed, they are assembled into the final product. Key steps include:
- Mechanical Assembly: This involves fitting together metal and plastic parts, securing them with screws, bolts, or welding where necessary.
- Electrical Assembly: Wiring for motors, sensors, and control systems is installed. This stage may also include programming any necessary software for machine operation.
- Integration Testing: Preliminary tests are conducted to ensure that all components work together as intended before moving to the finishing stage.
4. Finishing
The final stage of manufacturing focuses on aesthetics and protective measures:
- Surface Treatment: This may include powder coating, painting, or galvanizing to enhance appearance and corrosion resistance.
- Quality Control Checks: Each finished machine undergoes a series of quality checks to ensure compliance with design specifications and operational functionality.
Quality Assurance for Ball Vending Machines
Quality assurance (QA) is critical in the manufacturing process to guarantee that the ball vending machines are safe, reliable, and meet customer expectations. Here are the key aspects of QA:
Relevant International Standards
B2B buyers should be aware of the following standards that may apply to ball vending machines:
- ISO 9001: This quality management standard ensures that manufacturers consistently provide products that meet customer and regulatory requirements.
- CE Marking: Required for products sold in the European Economic Area, CE marking demonstrates compliance with safety and health requirements.
- API Standards: While more common in the oil and gas industries, certain API standards may apply if the vending machine is designed for specific environments (e.g., offshore).
Quality Control Checkpoints
Quality control is conducted at various checkpoints during the manufacturing process:
- Incoming Quality Control (IQC): This involves inspecting materials upon arrival to ensure they meet specified standards before production begins.
- In-Process Quality Control (IPQC): Checks are performed during the manufacturing stages to catch any defects early, ensuring issues are addressed before the final assembly.
- Final Quality Control (FQC): The finished products undergo rigorous testing to ensure they function correctly and meet all specifications.
Common Testing Methods
To ensure the quality of ball vending machines, manufacturers may utilize several testing methods:
- Functional Testing: Verifying that the machine operates correctly, including dispensing mechanisms and electronic components.
- Load Testing: Assessing the machine’s ability to handle expected usage levels without failure.
- Durability Testing: Simulating prolonged use to identify any potential wear or failure points.
Verifying Supplier Quality Control
For B2B buyers, especially those from Africa, South America, the Middle East, and Europe, verifying the quality control practices of suppliers is crucial. Here are actionable steps to ensure supplier reliability:
- Conduct Audits: Regular audits of suppliers can reveal their adherence to quality standards and manufacturing processes.
- Request Quality Reports: Suppliers should provide documentation of their quality control processes, including IQC, IPQC, and FQC results.
- Engage Third-Party Inspectors: Utilizing independent inspection services can provide unbiased assessments of product quality before shipment.
QC/Cert Nuances for International B2B Buyers
Understanding the nuances of quality control and certification is vital for international B2B buyers. Here are some considerations:
- Regional Standards Compliance: Different regions may have specific standards that must be adhered to. For instance, the UAE may have different requirements than those in Europe.
- Documentation and Traceability: Ensure that suppliers maintain thorough records of their manufacturing processes and quality checks. This documentation is crucial for compliance and can facilitate smoother transactions.
- Cultural and Legal Considerations: Be aware of any cultural or legal factors that may influence supplier operations in different regions, particularly in areas like dispute resolution and warranty claims.
In conclusion, a thorough understanding of the manufacturing processes and quality assurance protocols is essential for B2B buyers looking to procure ball vending machines. By focusing on supplier verification and compliance with international standards, buyers can significantly reduce risks and ensure they are investing in high-quality products.
Related Video: SMART Quality Control for Manufacturing
Comprehensive Cost and Pricing Analysis for ball vending machine Sourcing
To effectively source ball vending machines, understanding the cost structure and pricing dynamics is crucial for international B2B buyers, particularly in regions like Africa, South America, the Middle East, and Europe.
Cost Components
-
Materials: The primary materials used in ball vending machines include metal, plastic, and electronic components. The cost can vary significantly based on the quality and type of materials selected. For example, stainless steel components may incur higher costs compared to standard steel, but offer better durability.
-
Labor: Labor costs depend on the geographical location of the manufacturing facility. Regions with lower labor costs, such as parts of Africa and South America, can offer competitive pricing. However, it’s essential to consider the skill level required for assembly and quality assurance.
-
Manufacturing Overhead: This includes expenses related to utilities, rent, and administrative costs associated with the manufacturing facility. Overhead can be a substantial part of the total cost, particularly in areas with higher operational costs.
-
Tooling: Initial tooling costs can be significant, especially for customized or complex designs. Investing in durable tooling can lead to long-term savings through increased production efficiency.
-
Quality Control (QC): Implementing robust QC processes ensures that the machines meet safety and operational standards. While this adds to upfront costs, it can prevent costly recalls or repairs later.
-
Logistics: Transportation costs are influenced by the distance from the manufacturer to the buyer, as well as the chosen shipping method. Incoterms such as FOB (Free on Board) or CIF (Cost, Insurance, and Freight) will affect the total logistics costs.
-
Margin: Suppliers will typically add a margin on top of their costs to ensure profitability. This margin can vary based on market competition and the perceived value of the product.
Price Influencers
Several factors influence the pricing of ball vending machines:
-
Volume/MOQ (Minimum Order Quantity): Larger orders often lead to discounts. Buyers should assess their market demand to negotiate favorable terms.
-
Specifications/Customization: Custom features, such as branding or specific functionalities, can increase costs. Buyers should weigh the benefits of customization against the added expense.
-
Materials: The choice of materials can significantly impact price. Buyers should balance quality with cost to ensure a good return on investment.
-
Quality/Certifications: Machines that meet international safety and quality standards may be priced higher. Investing in certified products can lead to long-term savings by reducing warranty claims and maintenance costs.
-
Supplier Factors: Established suppliers with a proven track record may charge a premium for their products. However, their reliability can mitigate risks associated with sourcing.
-
Incoterms: Understanding shipping terms is critical. Buyers should clarify responsibilities for costs and risks associated with transportation to avoid unexpected charges.
Buyer Tips
-
Negotiation: Engage in negotiations with suppliers to explore flexible payment terms or bulk discounts. Building a good relationship can lead to better pricing in the long run.
-
Cost-Efficiency: Evaluate the total cost of ownership, which includes purchase price, maintenance, and operational costs over the machine’s lifespan. This analysis can reveal more cost-effective options.
-
Pricing Nuances for International Buyers: Be aware of currency fluctuations and potential tariffs that can affect pricing. Understanding local market conditions is vital for making informed purchasing decisions.
-
Disclaimer for Indicative Prices: Prices can vary widely based on the aforementioned factors and should be treated as indicative. Buyers should request quotes to obtain accurate pricing tailored to their specific needs.
By understanding these cost components and pricing influencers, international B2B buyers can make informed decisions when sourcing ball vending machines, ultimately leading to better procurement outcomes.
Spotlight on Potential ball vending machine Manufacturers and Suppliers
This section offers a look at a few manufacturers active in the ‘ball vending machine’ market. This is a representative sample for illustrative purposes; B2B buyers must conduct their own extensive due diligence before any engagement. Information is synthesized from public sources and general industry knowledge.
Essential Technical Properties and Trade Terminology for ball vending machine
Key Technical Properties of Ball Vending Machines
When considering the purchase of ball vending machines, it’s essential to understand the technical specifications that can impact performance, durability, and overall value. Here are some critical specifications:
-
Material Grade
The material used in the construction of a vending machine significantly affects its durability and resistance to environmental factors. Common materials include stainless steel for its corrosion resistance and high-impact plastics for lightweight applications. Selecting a high-grade material ensures longevity, especially in high-traffic areas, reducing the need for frequent replacements. -
Capacity
Capacity refers to the number of balls a vending machine can hold and dispense at one time. This specification is crucial for businesses that anticipate high demand, as it directly impacts sales potential. A machine with a larger capacity can reduce restocking frequency, saving time and labor costs. -
Tolerance Levels
Tolerance indicates the allowable deviation in dimensions during manufacturing. For vending machines, maintaining tight tolerances ensures proper functioning of mechanical parts, which can enhance the machine’s reliability and user experience. Understanding tolerance levels helps buyers evaluate the quality of the machine’s construction. -
Power Requirements
This specification includes the voltage and power consumption of the vending machine. Knowing the power requirements is essential for compatibility with local electrical systems, especially in regions with varying voltage standards. Efficient power usage can also lead to lower operational costs. -
Dimensions and Weight
The physical size and weight of the vending machine are critical for installation and placement considerations. Buyers should ensure that the machine fits the intended location while also considering the logistics of moving and setting it up. Additionally, weight can influence stability, especially in outdoor settings. -
User Interface
The design of the user interface affects customer interaction and satisfaction. Features such as touch screens, payment options, and clear instructions can enhance user experience. A well-designed interface can lead to increased sales, as customers find it easier and more enjoyable to use.
Common Trade Terms in the Vending Machine Industry
Familiarity with industry jargon is vital for B2B buyers to navigate negotiations and procurement processes effectively. Here are several key terms:
-
OEM (Original Equipment Manufacturer)
OEM refers to a company that produces parts or equipment that may be marketed by another manufacturer. In the context of vending machines, buyers may seek OEM components to ensure compatibility and quality, especially for repairs or upgrades. -
MOQ (Minimum Order Quantity)
MOQ is the smallest quantity of a product that a supplier is willing to sell. Understanding MOQ is essential for buyers to manage inventory effectively and to negotiate better pricing. Suppliers often set MOQs to optimize production and shipping costs. -
RFQ (Request for Quotation)
An RFQ is a document sent to suppliers requesting a price quote for specific goods or services. B2B buyers use RFQs to gather competitive bids and understand the market pricing for vending machines. This process is crucial for budget planning and supplier selection. -
Incoterms (International Commercial Terms)
Incoterms are a series of pre-defined international trade terms used in sales contracts. They clarify the responsibilities of buyers and sellers regarding shipping, insurance, and tariffs. Familiarity with Incoterms can help buyers mitigate risks associated with international shipping. -
Lead Time
Lead time refers to the amount of time it takes for an order to be fulfilled after it is placed. Understanding lead times is critical for inventory planning and ensuring that vending machines are available when needed, especially for seasonal demands. -
Warranty Period
The warranty period is the duration for which the manufacturer agrees to repair or replace defective products. Knowing the warranty terms can provide peace of mind and financial protection for buyers, making it a crucial factor in the purchasing decision.
By grasping these essential technical properties and trade terms, B2B buyers can make informed decisions that align with their operational needs and business objectives.
Navigating Market Dynamics, Sourcing Trends, and Sustainability in the ball vending machine Sector
Market Overview & Key Trends
The ball vending machine sector is experiencing significant growth driven by several global factors. Increasing urbanization, particularly in Africa and South America, is leading to a higher demand for convenient, on-the-go recreational options. This trend is complemented by the growing popularity of sports and outdoor activities, making vending machines an attractive option for both consumers and businesses. Moreover, technological advancements are reshaping the industry, with innovations such as cashless payment systems, mobile app integrations, and smart vending solutions enhancing customer engagement and operational efficiency.
International B2B buyers should be aware of emerging sourcing trends, including a shift towards local suppliers to reduce lead times and transportation costs. This trend is particularly relevant for buyers in regions like the Middle East and Europe, where local sourcing can also enhance brand reputation through community support. Additionally, there is a notable movement towards customization and personalization of vending machines, allowing businesses to cater to specific customer preferences and local tastes.
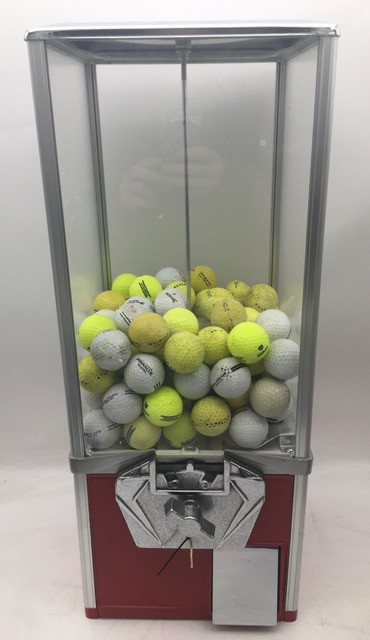
Illustrative Image (Source: Google Search)
Furthermore, sustainability is becoming a key concern for stakeholders in the ball vending machine sector. Buyers are increasingly seeking vendors who prioritize eco-friendly practices, from the materials used in machine production to the energy efficiency of the machines themselves. Understanding these dynamics will enable buyers to make informed decisions and align their purchasing strategies with market demands.
Sustainability & Ethical Sourcing in B2B
Sustainability is not just a trend but a necessity in today’s B2B landscape. The ball vending machine sector faces scrutiny regarding its environmental impact, particularly in terms of plastic waste from ball packaging and energy consumption. International buyers must prioritize suppliers who adopt sustainable practices, such as using recyclable materials and energy-efficient components in their machines.
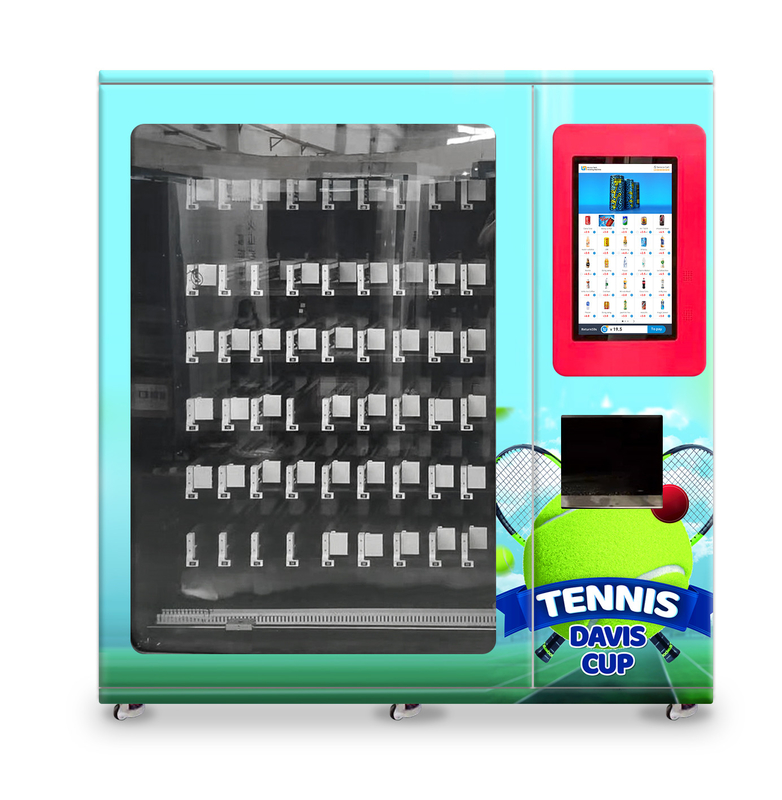
Illustrative Image (Source: Google Search)
Ethical sourcing is equally crucial. Buyers should ensure that their suppliers adhere to fair labor practices and maintain transparency in their supply chains. Certifications such as ISO 14001 (Environmental Management) and Fair Trade can serve as indicators of a supplier’s commitment to sustainable and ethical practices. Additionally, opting for machines that utilize biodegradable or eco-friendly materials can significantly reduce the environmental footprint.
The integration of ‘green’ certifications in the procurement process not only enhances brand reputation but also attracts environmentally conscious consumers. As the demand for sustainable products continues to rise, aligning sourcing strategies with these principles will be essential for long-term success in the ball vending machine market.
Brief Evolution/History
The ball vending machine sector has evolved significantly since its inception in the mid-20th century. Originally designed to dispense simple products like gumballs and toys, these machines have transformed into sophisticated retail solutions. The introduction of technology has played a pivotal role in this evolution, enabling features such as digital displays, touchless payment options, and remote inventory management.
In recent years, the focus has shifted towards enhancing user experience and accessibility, making vending machines a staple in public spaces such as parks, schools, and shopping malls. This evolution reflects broader trends in retail, where convenience and immediacy are paramount. For B2B buyers, understanding this historical context is vital, as it informs current market dynamics and consumer expectations.
Related Video: Global Trade & Logistics – What is Global Trade?
Frequently Asked Questions (FAQs) for B2B Buyers of ball vending machine
-
What key factors should I consider when vetting suppliers for ball vending machines?
When vetting suppliers, assess their industry experience, reputation, and customer reviews. Verify their certifications and compliance with international standards, such as ISO. Request references from previous clients, particularly those in your region, to gauge reliability and service quality. Furthermore, consider their ability to provide ongoing support and maintenance, as this can significantly affect your operational efficiency. -
Can I customize the ball vending machines to suit my branding and specific needs?
Yes, many manufacturers offer customization options for ball vending machines. You can request modifications in design, size, and color to align with your branding. Additionally, inquire about the possibility of integrating specific features, such as payment systems or product types. Ensure you discuss these needs during initial communications to confirm the supplier can meet your specifications. -
What are the typical minimum order quantities (MOQ) and lead times for ball vending machines?
MOQs can vary widely depending on the supplier and the complexity of the machines. Generally, you might encounter MOQs ranging from 10 to 50 units for customized orders. Lead times typically span from 4 to 12 weeks, influenced by the customization level and production schedules. Always confirm these details upfront to avoid delays in your supply chain. -
What payment terms should I expect when sourcing ball vending machines internationally?
Payment terms can differ based on supplier policies and the buyer’s location. Common arrangements include a deposit of 30-50% upfront with the balance due before shipping. For larger orders, consider negotiating favorable terms, such as extended payment periods or letter of credit options. Always ensure that payment methods are secure and provide adequate protection against fraud. -
How can I ensure quality assurance and certifications for the machines I purchase?
Request detailed information on the quality assurance processes employed by the supplier. Look for certifications such as CE, RoHS, or UL that demonstrate compliance with safety and quality standards. It may also be beneficial to conduct factory audits or third-party inspections before shipment to verify that the machines meet your quality expectations. -
What logistics options are available for shipping ball vending machines internationally?
Shipping options include air freight for faster delivery or sea freight for cost-effectiveness. When selecting a logistics provider, consider their experience with heavy machinery and customs regulations in your region. Discuss insurance options to protect your investment during transit and ensure that the supplier provides all necessary documentation for customs clearance. -
How should I handle disputes with suppliers over delivery or product quality?
Establish clear communication channels and maintain documentation of all transactions and agreements. If a dispute arises, first attempt to resolve it amicably through direct communication. If necessary, involve a third-party mediator or refer to the dispute resolution clauses in your contract. Always ensure that your contracts include specific terms regarding quality standards and delivery timelines to protect your interests. -
Are there specific considerations for compliance with local regulations when importing ball vending machines?
Yes, compliance with local regulations is crucial. Research import tariffs, product safety standards, and any certifications required in your country before proceeding. Engage with local customs brokers who can assist in navigating these regulations and ensure that all required documentation is in order. Failing to comply can result in delays or additional costs, so it’s essential to be proactive in this area.
Strategic Sourcing Conclusion and Outlook for ball vending machine
The strategic sourcing of ball vending machines presents a significant opportunity for international B2B buyers across Africa, South America, the Middle East, and Europe. By understanding market dynamics and leveraging supplier relationships, businesses can enhance their operational efficiency and maximize profitability. Key takeaways include the importance of evaluating supplier capabilities, ensuring compliance with local regulations, and recognizing the growing demand for innovative vending solutions that cater to diverse consumer needs.
Investing in high-quality ball vending machines not only improves customer experience but also positions businesses competitively within the marketplace. Buyers should prioritize suppliers who offer customization options and robust support services, ensuring their vending solutions are tailored to specific market demands.
As we move forward, the trend towards automation and smart vending solutions will continue to reshape the industry. International B2B buyers are encouraged to stay ahead of these trends by actively engaging with suppliers who are committed to innovation and sustainability. By doing so, they can secure a strategic advantage and contribute to the evolving landscape of vending solutions globally. Embrace the future of vending and explore the diverse opportunities that strategic sourcing can offer.