Master Sourcing Small Vending Machines for Sale: Top
Guide to Small Vending Machines For Sale
- Introduction: Navigating the Global Market for small vending machines for sale
- Understanding small vending machines for sale Types and Variations
- Key Industrial Applications of small vending machines for sale
- Strategic Material Selection Guide for small vending machines for sale
- In-depth Look: Manufacturing Processes and Quality Assurance for small vending machines for sale
- Comprehensive Cost and Pricing Analysis for small vending machines for sale Sourcing
- Spotlight on Potential small vending machines for sale Manufacturers and Suppliers
- Essential Technical Properties and Trade Terminology for small vending machines for sale
- Navigating Market Dynamics, Sourcing Trends, and Sustainability in the small vending machines for sale Sector
- Frequently Asked Questions (FAQs) for B2B Buyers of small vending machines for sale
- Strategic Sourcing Conclusion and Outlook for small vending machines for sale
Introduction: Navigating the Global Market for small vending machines for sale
Vending machines have evolved significantly, becoming essential assets for businesses seeking to enhance customer convenience and increase revenue streams. Small vending machines, in particular, cater to a diverse range of environments—from bustling urban centers to remote locations—making them an attractive investment for B2B buyers across the globe. As businesses in regions such as Africa, South America, the Middle East, and Europe look to optimize their service offerings, understanding the nuances of small vending machines becomes critical.
This guide serves as a comprehensive resource for international B2B buyers, detailing everything from the various types of small vending machines available—such as snack, beverage, and specialty machines—to the materials and manufacturing quality standards that ensure durability and reliability. Buyers will also find insights into reputable suppliers, an overview of typical costs, and a thorough analysis of the market trends shaping the vending industry.
By equipping buyers with actionable insights, this guide empowers informed sourcing decisions, enabling businesses to select the right machines tailored to their specific needs. Whether you’re an entrepreneur in Colombia looking to launch a vending business or an established company in Europe aiming to expand your product range, understanding the landscape of small vending machines is essential for success in today’s competitive marketplace.
Understanding small vending machines for sale Types and Variations
Type Name | Key Distinguishing Features | Primary B2B Applications | Brief Pros & Cons for Buyers |
---|---|---|---|
Snack Vending Machines | Compact design, typically holds snacks and candies | Offices, schools, gyms | Pros: Low maintenance, high demand in busy areas. Cons: Limited product range; may require frequent restocking. |
Beverage Vending Machines | Offers chilled drinks, often with a glass front | Malls, airports, restaurants | Pros: High turnover, diverse product options. Cons: Higher energy consumption; requires regular cleaning. |
Combo Vending Machines | Combines snacks and beverages in one unit | Event venues, hotels, workplaces | Pros: Space-efficient, versatile product offering. Cons: More complex maintenance; potential for technical issues. |
Specialty Vending Machines | Focuses on niche products (e.g., healthy snacks, electronics) | Hospitals, universities, gyms | Pros: Targets specific consumer needs; high profit margins. Cons: Limited audience; higher upfront investment. |
Wall-Mounted Vending Machines | Space-saving design, can be mounted on walls | Small offices, waiting rooms | Pros: Ideal for limited space; easy to install. Cons: Limited capacity; may not offer diverse product range. |
Snack Vending Machines
Snack vending machines are designed to dispense a variety of snacks, including chips, candy bars, and healthier options. Their compact design makes them ideal for high-traffic areas such as offices, schools, and gyms. When purchasing, consider the machine’s capacity, ease of restocking, and the variety of products it can hold. Snack machines typically require low maintenance, but buyers should be aware of the need for frequent restocking, especially in popular locations.
Beverage Vending Machines
These machines specialize in providing chilled beverages, including soft drinks, water, and sometimes hot beverages like coffee. They are commonly found in malls, airports, and restaurants, where quick access to drinks is essential. Key factors for B2B buyers include energy efficiency, maintenance requirements, and the machine’s ability to maintain optimal temperatures. While beverage machines often enjoy high turnover rates, they can have higher energy consumption and may require more frequent cleaning to ensure product quality.
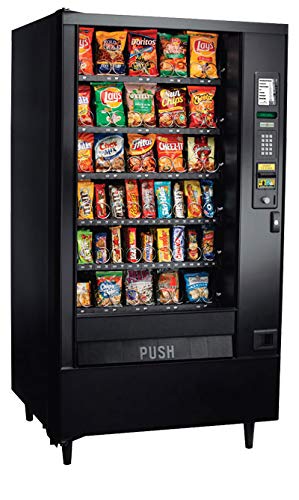
Illustrative Image (Source: Google Search)
Combo Vending Machines
Combo vending machines combine snacks and beverages into a single unit, making them a versatile option for various environments such as event venues, hotels, and workplaces. These machines save space while offering a broader product selection. Buyers should evaluate the machine’s adaptability to different product types and its maintenance needs, as these can be more complex due to the dual functionality. Despite their advantages, combo machines may face technical issues that require specialized service.
Specialty Vending Machines
Specialty vending machines cater to specific consumer needs, offering products such as healthy snacks, electronics, or hygiene items. These machines are particularly effective in settings like hospitals, universities, and gyms, where there is a demand for niche products. When considering a purchase, B2B buyers should analyze the target market, potential profit margins, and the higher upfront costs associated with these specialized machines. Although they can command higher prices, their limited audience may restrict sales volume.
Wall-Mounted Vending Machines
Wall-mounted vending machines are designed to save space by being installed directly on walls, making them perfect for small offices or waiting rooms. These machines typically have a limited capacity but can still provide essential snacks or drinks. Buyers should consider installation logistics, product variety, and the machine’s overall durability. While these machines are easy to install and ideal for limited spaces, they may not offer the diverse product range needed to attract a broader customer base.
Related Video: I Bought A Vending Machine Route For $20,000!! (4 Machines)
Key Industrial Applications of small vending machines for sale
Industry/Sector | Specific Application of small vending machines for sale | Value/Benefit for the Business | Key Sourcing Considerations for this Application |
---|---|---|---|
Healthcare | Distributing medical supplies and hygiene products | Increases accessibility and convenience for patients | Compliance with health regulations, payment options, machine size |
Education | Providing snacks and beverages in schools and universities | Enhances student satisfaction and boosts on-campus sales | Energy efficiency, space constraints, variety of products offered |
Corporate Offices | Offering snacks and drinks in office break rooms | Promotes employee satisfaction and productivity | Maintenance support, payment flexibility, machine reliability |
Transportation Hubs | Supplying refreshments at airports and bus stations | Meets traveler demand for quick, on-the-go options | Compact design, weather resistance, high capacity |
Retail | Selling specialty items like electronics or beauty products | Diversifies product offerings and attracts foot traffic | Customization options, user-friendly interface, inventory management |
Healthcare
In healthcare settings, small vending machines can be strategically placed to dispense medical supplies, personal hygiene products, and healthy snacks. This application addresses the need for quick access to essential items, especially for patients and visitors in hospitals and clinics. International buyers should prioritize machines that comply with local health regulations, offer multiple payment options, and fit within the often limited space of healthcare facilities.
Education
Schools and universities can leverage small vending machines to provide students with snacks and beverages, enhancing their campus experience. By offering a variety of healthy options, educational institutions can promote better eating habits while generating additional revenue. For B2B buyers in this sector, it’s crucial to consider energy-efficient models that can operate within tight budgets and meet the dietary preferences of diverse student populations.
Corporate Offices
In corporate environments, small vending machines serve as convenient refreshment points in break rooms, helping to improve employee morale and productivity. These machines can offer a selection of snacks and drinks tailored to the workforce’s preferences. Key considerations for sourcing include the reliability of the machines, the availability of maintenance support, and the flexibility of payment options to accommodate a cashless workforce.
Transportation Hubs
Small vending machines are particularly effective in transportation hubs like airports and bus stations, where they provide travelers with quick access to refreshments. These machines can be designed to withstand various weather conditions and cater to high foot traffic, ensuring that they remain stocked and operational. Buyers in this sector should focus on compact designs that maximize product variety while ensuring ease of use for a diverse customer base.
Retail
In the retail sector, small vending machines can be used to sell specialty items such as electronics, beauty products, or even local artisan goods. This application not only diversifies product offerings but also attracts foot traffic, especially in high-traffic areas. When sourcing machines for retail, international buyers should consider customization options, user-friendly interfaces, and robust inventory management systems to optimize sales and customer engagement.
Strategic Material Selection Guide for small vending machines for sale
When selecting materials for small vending machines, it’s crucial to consider their properties, advantages, and limitations to ensure optimal performance and longevity. Below is an analysis of four common materials used in the construction of small vending machines, tailored for international B2B buyers.
1. Stainless Steel
Key Properties:
Stainless steel is known for its excellent corrosion resistance, high strength, and ability to withstand various temperatures. It typically has a temperature rating of up to 800°F (427°C) and is resistant to rust and staining.
Pros & Cons:
Stainless steel is highly durable and easy to clean, making it suitable for food and beverage applications. However, it is more expensive than other materials like carbon steel and can be challenging to fabricate due to its hardness.
Impact on Application:
This material is ideal for vending machines that dispense food and beverages, as it prevents contamination and maintains hygiene standards.
Considerations for International Buyers:
Buyers in regions like Africa and the Middle East should ensure compliance with local health regulations. In Europe, adherence to standards such as EN 10088 for stainless steel is essential.
2. Powder-Coated Steel
Key Properties:
Powder-coated steel offers a protective layer that enhances corrosion resistance and provides aesthetic appeal. It can withstand moderate temperatures and is available in various colors.
Pros & Cons:
It is generally less expensive than stainless steel and provides a good balance of durability and aesthetics. However, the coating can chip or scratch, exposing the underlying steel to corrosion.
Impact on Application:
This material is suitable for vending machines located in low-humidity environments, where aesthetics and cost-effectiveness are priorities.
Considerations for International Buyers:
Buyers should verify that the powder coating meets local environmental regulations, particularly in Europe, where compliance with REACH regulations is critical.
3. Aluminum
Key Properties:
Aluminum is lightweight, corrosion-resistant, and has a melting point of approximately 1,220°F (660°C). It is also a good conductor of heat, which can be beneficial for temperature-sensitive products.
Pros & Cons:
Aluminum is easy to fabricate and transport due to its lightweight nature. However, it is less durable than stainless steel and can be prone to dents and scratches.
Impact on Application:
Ideal for portable vending machines or those requiring frequent relocation, aluminum is suitable for environments where weight is a critical factor.
Considerations for International Buyers:
In regions like South America, where humidity levels can be high, buyers should ensure that the aluminum is treated to enhance its corrosion resistance.
4. Polycarbonate
Key Properties:
Polycarbonate is a strong, transparent plastic that can withstand impact and has a temperature tolerance of up to 240°F (115°C). It is also lightweight and offers excellent visibility for products.
Pros & Cons:
This material is cost-effective and provides good visibility for merchandise, enhancing customer interaction. However, it is not as durable as metals and can become scratched or discolored over time.
Impact on Application:
Polycarbonate is often used for vending machine fronts or panels, allowing customers to see the products inside while protecting them from environmental factors.
Considerations for International Buyers:
Buyers should ensure that the polycarbonate used meets safety standards, especially in regions with strict regulations regarding plastic materials.
Material | Typical Use Case for small vending machines for sale | Key Advantage | Key Disadvantage/Limitation | Relative Cost (Low/Med/High) |
---|---|---|---|---|
Stainless Steel | Food and beverage vending machines | Excellent durability and corrosion resistance | Higher cost and difficult to fabricate | High |
Powder-Coated Steel | General vending machines in low-humidity areas | Cost-effective and aesthetically pleasing | Can chip or scratch, exposing steel | Medium |
Aluminum | Portable vending machines | Lightweight and easy to transport | Less durable, prone to dents | Medium |
Polycarbonate | Vending machine fronts for visibility | Good visibility and impact resistance | Less durable, can scratch or discolor | Low |
This strategic material selection guide provides a comprehensive overview for B2B buyers, ensuring informed decisions based on performance, cost, and regional considerations.
In-depth Look: Manufacturing Processes and Quality Assurance for small vending machines for sale
When considering the procurement of small vending machines, understanding the manufacturing processes and quality assurance protocols is essential. These factors not only influence the reliability and performance of the machines but also ensure compliance with international standards, which can be crucial for B2B buyers from diverse markets such as Africa, South America, the Middle East, and Europe.
Manufacturing Processes
The manufacturing of small vending machines typically involves several key stages, each critical to the final product’s quality and functionality.
1. Material Preparation
The first step in the manufacturing process is material preparation. This involves sourcing high-quality materials, such as steel for the structure, plastic for components, and electronic parts for functionality. Suppliers must ensure that materials meet specific standards, which could vary by region. For example, steel might need to comply with ASTM standards in the U.S. or EN standards in Europe.
2. Forming
Once materials are prepared, the next stage is forming. This can include cutting, bending, and shaping the metal and plastic components. Techniques such as laser cutting and CNC machining are often employed to ensure precision and reduce waste. Forming is crucial as it directly affects the durability and aesthetics of the vending machines.
3. Assembly
The assembly stage is where the various components come together. This process typically follows a systematic approach to ensure efficiency and accuracy. Components such as the vending mechanism, electronic systems, and user interface are integrated. Skilled labor and automation are combined to enhance productivity. During assembly, manufacturers often utilize jigs and fixtures to maintain alignment and consistency.
4. Finishing
Finishing processes such as painting, coating, or adding decals enhance the machine’s appearance and protect it from environmental factors. This stage often includes applying powder coatings or using environmentally friendly paint options to comply with sustainability standards. Quality checks during this phase ensure that the aesthetic quality meets customer expectations.
Quality Assurance
Quality assurance (QA) is an integral part of the manufacturing process, ensuring that the final product meets both industry and customer standards.
International Standards
For international B2B buyers, awareness of relevant quality standards is critical. The following standards are often applicable:
- ISO 9001: This standard outlines the criteria for a quality management system, ensuring consistent quality in products and services.
- CE Marking: For products sold in the European Economic Area, CE marking indicates conformity with health, safety, and environmental protection standards.
- API Certification: Particularly relevant for machines that handle specific products (e.g., food or pharmaceuticals), API certification can assure buyers of safety and quality.
Quality Control Checkpoints
Throughout the manufacturing process, several quality control (QC) checkpoints are implemented:
- Incoming Quality Control (IQC): This involves inspecting raw materials and components upon arrival to ensure they meet specified standards.
- In-Process Quality Control (IPQC): During manufacturing, processes are monitored to identify and rectify any deviations from quality standards in real-time.
- Final Quality Control (FQC): Before shipping, the completed machines undergo thorough testing to ensure they function correctly and meet all specifications.
Common Testing Methods
Testing methods for small vending machines often include:
- Functional Testing: Verifying that all mechanical and electronic components operate as intended.
- Durability Testing: Assessing the machine’s ability to withstand wear and tear over time.
- Safety Testing: Ensuring compliance with electrical safety standards, particularly for machines that dispense food or beverages.
Verifying Supplier Quality Control
B2B buyers can take several steps to verify a supplier’s quality control measures:
- Conduct Audits: Regular audits of suppliers can help assess their adherence to quality standards and identify areas for improvement.
- Request Quality Reports: Suppliers should provide documentation detailing their quality control processes, inspection results, and compliance with relevant standards.
- Engage Third-Party Inspectors: Utilizing independent inspectors can provide an unbiased assessment of the manufacturing and quality assurance processes.
Regional Considerations for International Buyers
For international buyers, particularly from Africa, South America, the Middle East, and Europe, it is crucial to understand the nuances of quality assurance in different regions:
- Cultural Differences: Business practices and quality expectations can vary significantly across regions. Understanding local regulations and consumer preferences can enhance supplier relationships.
- Logistical Challenges: Importing vending machines can involve complex logistics, including customs regulations and tariffs. Ensure that suppliers are familiar with these processes to avoid delays.
- Sustainability Expectations: Increasingly, buyers are prioritizing sustainability. Suppliers should be prepared to demonstrate eco-friendly practices and compliance with international environmental standards.
Conclusion
Navigating the manufacturing processes and quality assurance protocols for small vending machines is essential for B2B buyers. By understanding these factors, buyers can make informed decisions, ensuring they procure reliable machines that meet their operational needs and comply with international standards. Engaging with suppliers who prioritize quality at every stage of production will ultimately lead to a more successful vending machine investment.
Related Video: Most Satisfying Factory Production Processes And Heavy-Duty Factory Machines!
Comprehensive Cost and Pricing Analysis for small vending machines for sale Sourcing
When sourcing small vending machines for sale, understanding the comprehensive cost structure and pricing dynamics is essential for international B2B buyers. This analysis covers the cost components involved in vending machine production, price influencers, and actionable tips for effective negotiations, particularly relevant for buyers in Africa, South America, the Middle East, and Europe.
Cost Components of Small Vending Machines
-
Materials: The primary cost driver, materials include metal, plastics, electronic components, and other consumables. Quality certifications, such as those from ISO, can increase material costs but are crucial for ensuring durability and compliance with local regulations.
-
Labor: Labor costs vary by region and impact the overall pricing structure. In countries with higher labor costs, manufacturers might pass these expenses onto buyers, influencing pricing.
-
Manufacturing Overhead: This encompasses utilities, rent, and administrative costs associated with production facilities. Efficient manufacturing processes can reduce overhead, allowing for competitive pricing.
-
Tooling: Initial tooling costs for custom designs can be significant, especially for specialized machines. These costs are typically amortized over production runs, affecting the pricing of smaller orders.
-
Quality Control (QC): Rigorous QC processes ensure that machines meet safety and operational standards. While this adds to the overall cost, it is essential for minimizing defects and ensuring customer satisfaction.
-
Logistics: Transportation costs can vary greatly depending on the shipping method and destination. Buyers should consider the total logistics cost, including import duties and taxes, especially when sourcing from international suppliers.
-
Margin: Suppliers typically add a profit margin to cover their risks and operational costs. This margin can vary based on the supplier’s market position and the competitiveness of their offerings.
Price Influencers
-
Volume/MOQ: Bulk purchases generally lead to lower per-unit costs. Buyers should negotiate minimum order quantities (MOQs) to maximize savings.
-
Specifications/Customization: Custom features (e.g., branding, unique product offerings) can significantly increase costs. Buyers should weigh the benefits of customization against potential price increases.
-
Materials and Quality: Higher quality materials and advanced technology (like touchscreens or cashless payment systems) will increase the initial purchase price but can lead to lower maintenance costs and improved customer satisfaction in the long run.
-
Supplier Factors: Supplier reputation and reliability can influence pricing. Established suppliers with a track record of quality may charge higher prices but offer better support and warranty options.
-
Incoterms: Understanding international shipping terms (Incoterms) is crucial. Different terms (e.g., FOB, CIF) can affect the final price and responsibilities for shipping costs and risks.
Buyer Tips for Cost Efficiency
-
Negotiation: Engage in open discussions with suppliers about pricing, especially for larger orders. Many suppliers are willing to negotiate terms and prices, particularly if you demonstrate long-term purchasing potential.
-
Total Cost of Ownership (TCO): Evaluate the TCO, which includes not just the purchase price but also operating costs, maintenance, and potential revenue generation. A higher upfront cost may be justified if it leads to lower operational expenses.
-
Pricing Nuances: Be aware of seasonal fluctuations in pricing, especially during peak manufacturing periods. Planning purchases ahead of time can help mitigate unexpected price increases.
-
Local Regulations: Familiarize yourself with local import regulations and tariffs that may apply to vending machines. These can significantly affect the total cost and should be factored into your budget.
-
Supplier Relationships: Building strong relationships with suppliers can lead to better prices and terms. Regular communication and trust can facilitate smoother negotiations and better service.
Disclaimer
Prices for small vending machines vary widely based on specifications, supplier, and market conditions. The figures presented here are indicative and should be validated with suppliers for accurate budgeting and planning.
By understanding these cost components, price influencers, and implementing strategic negotiation techniques, international B2B buyers can make informed decisions when sourcing small vending machines tailored to their market needs.
Spotlight on Potential small vending machines for sale Manufacturers and Suppliers
- (No specific manufacturer data was available or requested for detailed profiling in this section for small vending machines for sale.)*
Essential Technical Properties and Trade Terminology for small vending machines for sale
Key Technical Properties of Small Vending Machines
When considering the purchase of small vending machines, understanding their technical specifications is crucial for making informed decisions. Below are several key properties that B2B buyers should evaluate:
1. Material Grade
– Definition: This refers to the quality of materials used in the construction of the vending machine, including metals, plastics, and glass.
– Importance: High-grade materials enhance durability and resistance to wear and tear, ensuring the machine can withstand high-traffic environments. For buyers in diverse climates, like those in Africa or the Middle East, corrosion resistance is particularly important.
2. Power Consumption
– Definition: This specifies the amount of energy the vending machine requires to operate efficiently.
– Importance: Machines with lower power consumption are more cost-effective and environmentally friendly. Buyers should seek ENERGY STAR-rated models, which can significantly reduce operational costs, especially in regions with high electricity prices.
3. Dimensions and Capacity
– Definition: This includes the physical size of the vending machine and the volume of products it can hold.
– Importance: Compact designs are essential for locations with limited space, such as small offices or convenience stores. Capacity impacts inventory management; choosing a machine with optimal space utilization can enhance sales potential.
4. Payment Options
– Definition: The types of payment methods supported by the vending machine, including cash, credit/debit cards, mobile wallets, and cryptocurrencies.
– Importance: Offering multiple payment options increases accessibility and convenience for customers, which can lead to higher sales. In regions where cashless transactions are gaining popularity, such as South America and Europe, this feature is especially relevant.
5. User Interface
– Definition: This refers to the design and functionality of the machine’s control panel or touchscreen interface.
– Importance: An intuitive user interface improves customer experience, leading to quicker transactions and higher satisfaction rates. Features like clear product labeling and interactive displays can enhance engagement and sales.
6. Maintenance Requirements
– Definition: This encompasses the ease of cleaning, restocking, and repairing the vending machine.
– Importance: Machines that are easy to maintain reduce downtime and operational disruptions. For international buyers, understanding the service support from manufacturers is crucial to ensure ongoing operational efficiency.
Common Trade Terms in Vending Machine Procurement
Navigating the procurement process for vending machines involves understanding specific industry terminology. Here are essential terms that B2B buyers should be familiar with:
1. OEM (Original Equipment Manufacturer)
– Definition: A company that produces parts or equipment that may be marketed by another manufacturer.
– Importance: Buyers should consider purchasing from reputable OEMs to ensure quality and reliability of the machines. This is crucial for maintaining brand reputation and customer satisfaction.
2. MOQ (Minimum Order Quantity)
– Definition: The smallest quantity of a product that a supplier is willing to sell.
– Importance: Understanding MOQ helps buyers manage inventory and cash flow. For small businesses, negotiating a lower MOQ can be beneficial, especially when testing new markets.
3. RFQ (Request for Quotation)
– Definition: A document issued by a buyer to solicit price offers from suppliers for specific products or services.
– Importance: An RFQ helps buyers obtain competitive pricing and terms, allowing for better budget planning and negotiation strategies.
4. Incoterms (International Commercial Terms)
– Definition: A set of international rules that define the responsibilities of sellers and buyers in international transactions.
– Importance: Familiarity with Incoterms is essential for understanding shipping costs, risk management, and delivery responsibilities. This is particularly important for international buyers from Africa, South America, and the Middle East.
5. Warranty
– Definition: A promise made by a manufacturer or seller to repair or replace a product if necessary within a specified period.
– Importance: Warranties provide assurance to buyers regarding product quality and longevity, influencing purchasing decisions. Buyers should carefully review warranty terms to safeguard their investments.
6. Lead Time
– Definition: The time taken from placing an order to delivery of the product.
– Importance: Understanding lead times is vital for inventory planning and ensuring that machines are available when needed, especially in high-demand situations.
By grasping these technical properties and trade terms, international B2B buyers can make more informed decisions, optimize their procurement strategies, and ultimately enhance their vending machine business operations.
Navigating Market Dynamics, Sourcing Trends, and Sustainability in the small vending machines for sale Sector
Market Overview & Key Trends
The small vending machine sector is experiencing significant transformation, driven by technological advancements and changing consumer preferences. Globally, the adoption of cashless payment systems, such as mobile wallets and contactless cards, is reshaping how transactions occur, especially in regions like Africa and South America where digital payment infrastructure is rapidly evolving. This shift not only enhances convenience but also caters to a younger, tech-savvy demographic that prioritizes seamless experiences.
Emerging trends include the integration of Internet of Things (IoT) technology, enabling real-time monitoring and predictive maintenance capabilities. This technology allows operators to manage inventory more efficiently, reducing downtime and optimizing restocking schedules. As a result, B2B buyers should seek vending machines equipped with smart technology to ensure operational efficiency and maximize profitability.
Moreover, the demand for specialty vending machines offering healthier snacks and beverages is on the rise, reflecting a global shift towards wellness and sustainability. This trend presents a unique opportunity for international buyers to differentiate their offerings in competitive markets. For B2B buyers from regions like the Middle East and Europe, understanding local consumer preferences and adapting product assortments accordingly can drive sales and enhance customer satisfaction.
Sustainability & Ethical Sourcing in B2B
Sustainability is becoming a pivotal factor for B2B buyers in the small vending machine sector. As businesses worldwide commit to reducing their environmental impact, the demand for energy-efficient machines is escalating. Machines that are ENERGY STAR certified not only lower operational costs but also resonate with environmentally conscious consumers. Buyers should prioritize suppliers who offer sustainable options, ensuring their products meet rigorous environmental standards.
In addition to energy efficiency, ethical sourcing is crucial. This involves ensuring that materials used in vending machines are responsibly sourced, minimizing harm to the environment and communities. Buyers should look for vendors that utilize recyclable materials and adhere to fair labor practices. Certifications such as ISO 14001 (Environmental Management) and Fair Trade can serve as indicators of a supplier’s commitment to sustainable and ethical practices.
Investing in sustainable vending solutions is not merely a compliance measure; it can also enhance brand reputation and customer loyalty, particularly in regions where consumers are increasingly prioritizing corporate social responsibility.
Brief Evolution/History
The evolution of vending machines dates back to the 19th century, originally offering simple items like postcards and chewing gum. Over the decades, they have transformed significantly, adapting to technological advancements and changing consumer demands. The introduction of electronic payment systems in the late 20th century marked a pivotal shift, leading to the development of modern vending machines capable of offering a diverse range of products, from snacks to electronics.
Today, the focus is on enhancing user experience through smart technology and sustainable practices. This historical context underscores the importance of innovation and adaptability for B2B buyers in the vending machine market, as they seek to meet the needs of an increasingly sophisticated consumer base.
Related Video: Incoterms for beginners | Global Trade Explained
Frequently Asked Questions (FAQs) for B2B Buyers of small vending machines for sale
-
What should I consider when vetting suppliers for small vending machines?
When vetting suppliers, evaluate their experience in the vending industry, customer reviews, and certifications. Look for suppliers that have been in business for several years and have a solid reputation. Request references from previous clients to gauge reliability and service quality. Additionally, assess their product offerings for customization options and technological advancements, as well as their ability to provide ongoing support and maintenance services. -
Can I customize the vending machines to suit my business needs?
Yes, many manufacturers offer customization options for small vending machines. You can tailor the machine’s design, size, and product offerings to align with your target market and location. Discuss your specific requirements with suppliers, such as branding, payment systems, and product types. Ensure that the customization process is clearly outlined, including any additional costs and lead times associated with these modifications. -
What are the minimum order quantities (MOQ) and lead times for ordering?
Minimum order quantities can vary significantly among suppliers, often ranging from one unit to several dozen. It’s essential to clarify the MOQ during your discussions with potential vendors. Lead times for production and shipping can also differ based on the supplier’s location and the complexity of the order. Typically, expect 4-12 weeks for custom machines. Always confirm timelines in writing to avoid delays in your operations. -
What payment terms should I expect when purchasing vending machines internationally?
Payment terms can vary based on the supplier and your location. Common methods include wire transfers, letters of credit, or payment through escrow services. Be sure to discuss payment schedules, including deposits and final payments, and confirm any additional costs such as shipping fees, customs duties, and taxes. Understand the implications of currency exchange rates if dealing with international suppliers, as this can affect your overall costs. -
How do I ensure the quality and compliance of the vending machines?
To ensure quality, request certifications that demonstrate compliance with international safety and quality standards, such as CE, ISO, or ENERGY STAR. Ask suppliers for details about their quality assurance processes, including testing and inspection methods. It’s also advisable to visit the manufacturing facility if possible or request third-party inspections before shipment, particularly for large orders, to verify that the machines meet your specifications. -
What logistics considerations should I keep in mind when importing vending machines?
Logistics are crucial when importing vending machines. Consider shipping methods, customs clearance, and local regulations that may affect import processes. Work with logistics providers experienced in international shipping to navigate potential challenges. Additionally, factor in shipping costs, insurance, and estimated delivery times. Ensure that the machines are adequately packaged to prevent damage during transit. -
How can disputes with suppliers be effectively managed?
To manage disputes, establish clear contractual agreements outlining the terms of sale, including delivery timelines, payment terms, and warranty conditions. Maintain open communication with suppliers to address issues as they arise. If disputes occur, try to resolve them amicably through negotiation. If necessary, consider mediation or arbitration as outlined in your contract, particularly for international transactions, to avoid lengthy legal battles. -
What are the best practices for after-sales support and maintenance?
After-sales support is critical for the long-term success of your vending operations. Ensure that your supplier provides comprehensive training on machine operation, maintenance, and troubleshooting. Confirm the availability of spare parts and the supplier’s response time for service requests. Establish a maintenance schedule to keep machines in optimal condition, and consider a service agreement for regular upkeep, which can prevent costly downtime and enhance customer satisfaction.
Strategic Sourcing Conclusion and Outlook for small vending machines for sale
Investing in small vending machines represents a strategic opportunity for B2B buyers looking to enhance their service offerings and meet consumer demand across diverse markets. Key considerations include selecting the right type of machine—whether snack, beverage, or specialty—to maximize profitability and customer satisfaction. Emphasizing advanced technology and energy efficiency can significantly reduce operational costs and improve the user experience.
Moreover, understanding the total cost of ownership, including upfront investment and ongoing maintenance, is essential for achieving a favorable return on investment. By leveraging comprehensive market insights and evaluating suppliers based on reliability and support, international buyers can make informed decisions that align with their unique operational needs.
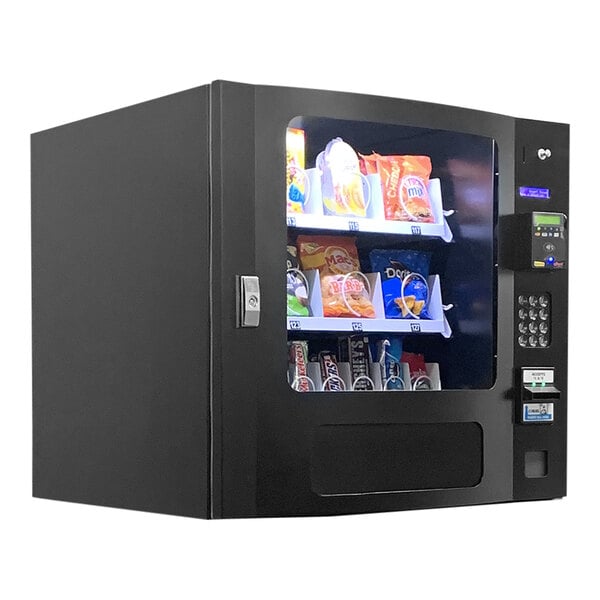
Illustrative Image (Source: Google Search)
Looking ahead, the vending machine landscape is evolving with innovations that promise enhanced functionality and user engagement. As trends towards cashless payments and smart vending solutions grow, there’s a clear opportunity for B2B buyers from Africa, South America, the Middle East, and Europe to capitalize on these advancements. Engage with suppliers who can offer tailored solutions that not only meet current demands but also position your business for future growth. Seize this moment to invest strategically in vending solutions that cater to your market and customer preferences.