Master Sourcing Popmart Vending Machines for Enhanced
Guide to Popmart Vending Machines
- Introduction: Navigating the Global Market for popmart vending machines
- Understanding popmart vending machines Types and Variations
- Key Industrial Applications of popmart vending machines
- Strategic Material Selection Guide for popmart vending machines
- In-depth Look: Manufacturing Processes and Quality Assurance for popmart vending machines
- Comprehensive Cost and Pricing Analysis for popmart vending machines Sourcing
- Spotlight on Potential popmart vending machines Manufacturers and Suppliers
- Essential Technical Properties and Trade Terminology for popmart vending machines
- Navigating Market Dynamics, Sourcing Trends, and Sustainability in the popmart vending machines Sector
- Frequently Asked Questions (FAQs) for B2B Buyers of popmart vending machines
- Strategic Sourcing Conclusion and Outlook for popmart vending machines
Introduction: Navigating the Global Market for popmart vending machines
In today’s fast-paced global economy, Popmart vending machines have emerged as a revolutionary solution for businesses seeking to enhance customer engagement and streamline operations. These innovative machines not only cater to the growing demand for convenience but also provide an interactive experience that can significantly boost sales and brand loyalty. For international B2B buyers, particularly those in Africa, South America, the Middle East, and Europe, understanding the nuances of the Popmart vending machine market is critical to making informed sourcing decisions.
This comprehensive guide delves into essential aspects of Popmart vending machines, including the various types available, the materials used in their construction, and insights into manufacturing and quality control practices. Furthermore, it provides a detailed overview of suppliers, cost considerations, and the current market landscape, ensuring that buyers are well-equipped to navigate this dynamic sector.
By addressing common FAQs and offering actionable insights, this guide empowers businesses to make strategic decisions that align with their operational goals and market demands. Whether you are a seasoned buyer or exploring vending solutions for the first time, this resource is designed to enhance your understanding of Popmart vending machines and facilitate successful procurement strategies. Embrace the opportunity to elevate your business offerings and meet the evolving needs of your customers.
Understanding popmart vending machines Types and Variations
Type Name | Key Distinguishing Features | Primary B2B Applications | Brief Pros & Cons for Buyers |
---|---|---|---|
Standard Popmart Machine | Classic design with a variety of product slots | Retail stores, malls, and offices | Pros: Cost-effective, easy to maintain. Cons: Limited customization options. |
Interactive Popmart Machine | Touchscreen interface for user engagement | Entertainment venues, airports | Pros: Enhances user experience, customizable content. Cons: Higher initial investment and maintenance costs. |
Mobile Popmart Machine | Compact design with wheels for portability | Events, trade shows, and festivals | Pros: Flexible location options, easy setup. Cons: Limited storage capacity. |
Specialty Popmart Machine | Focused on niche products (e.g., local snacks) | Specialty stores, tourist attractions | Pros: Attracts targeted customer segments. Cons: May require more market research to ensure product demand. |
Smart Popmart Machine | IoT-enabled for real-time inventory tracking | Large retail chains, tech hubs | Pros: Efficient inventory management, data analytics capabilities. Cons: Requires reliable internet connectivity. |
Standard Popmart Machine
The Standard Popmart Machine is the quintessential vending solution, featuring multiple product slots designed for a variety of snacks and beverages. This type is widely used in retail environments, malls, and office buildings, making it a staple for businesses looking to provide convenient access to refreshments. When considering a purchase, buyers should evaluate the machine’s capacity, ease of maintenance, and overall cost-effectiveness, ensuring it aligns with their operational needs.
Interactive Popmart Machine
Designed to engage consumers, the Interactive Popmart Machine incorporates touchscreen technology that allows users to browse and select products easily. Commonly found in airports and entertainment venues, these machines offer a modern shopping experience. B2B buyers should consider the initial investment and ongoing maintenance costs, but the potential for increased sales through enhanced customer interaction can justify the expense.
Mobile Popmart Machine
The Mobile Popmart Machine is characterized by its compact design and portability, making it ideal for events, trade shows, and festivals. This type allows businesses to offer products in various locations, adapting to customer traffic patterns. Buyers should weigh the machine’s storage capacity against its mobility, as a smaller unit may limit product offerings but enhance flexibility.
Specialty Popmart Machine
Focusing on niche markets, the Specialty Popmart Machine caters to specific consumer preferences, such as local snacks or health-conscious items. These machines are often placed in specialty stores or tourist attractions, targeting specific demographics. B2B buyers should conduct thorough market research to ensure the selected products meet customer demands, balancing the benefits of targeted offerings with the risk of limited appeal.
Smart Popmart Machine
The Smart Popmart Machine integrates Internet of Things (IoT) technology, allowing for real-time inventory tracking and data analytics. This type is particularly beneficial for large retail chains and tech-savvy environments, where efficient inventory management is crucial. Buyers must ensure reliable internet connectivity and consider the higher upfront costs against the potential for improved operational efficiencies and sales insights.
Related Video: FIRST TIME SEEING A POPMART VENDING MACHINE?!? 🫣💸
Key Industrial Applications of popmart vending machines
Industry/Sector | Specific Application of popmart vending machines | Value/Benefit for the Business | Key Sourcing Considerations for this Application |
---|---|---|---|
Retail | Automated retail for snacks and beverages | Increases sales through 24/7 availability | Product variety, payment systems, and stock management |
Education | Campus convenience stores | Enhances student satisfaction and campus life | Product selection, vending machine size, and location |
Healthcare | Medication dispensing | Improves patient adherence to medication schedules | Compliance with health regulations, security features |
Hospitality | Guest amenities in hotels | Provides quick access to snacks and personal items | Custom branding, product offerings, and payment options |
Transportation | Travel hubs and airports | Streamlines food and beverage access for travelers | Durability, payment integration, and location strategy |
Retail
In the retail sector, popmart vending machines serve as automated retail outlets for snacks and beverages. By providing 24/7 access, these machines can significantly increase sales, especially in high-traffic areas. International B2B buyers should consider the variety of products offered, the integration of advanced payment systems, and effective stock management solutions to ensure a seamless shopping experience for customers.
Education
Popmart vending machines can be effectively utilized on college campuses as convenience stores, offering students easy access to snacks, beverages, and essential items. This application enhances student satisfaction and contributes positively to campus life. Buyers in the education sector should focus on product selection tailored to student preferences, the size of the machines to fit available spaces, and strategic placement to maximize foot traffic.
Healthcare
In healthcare settings, popmart vending machines can be employed for medication dispensing, ensuring patients have timely access to their prescriptions. This application not only improves patient adherence to medication schedules but also reduces the workload on pharmacy staff. Buyers in this sector must prioritize compliance with health regulations, incorporate security features to protect sensitive medications, and consider user-friendly interfaces for patients.
Hospitality
Within the hospitality industry, popmart vending machines can enhance guest amenities by providing quick access to snacks, personal care items, and beverages. This convenience can greatly improve the guest experience and encourage repeat business. B2B buyers should consider custom branding options, diverse product offerings tailored to guest demographics, and flexible payment options to cater to international travelers.
Transportation
In transportation hubs such as airports and train stations, popmart vending machines streamline access to food and beverages for travelers. This application addresses the need for quick service in busy environments, enhancing customer satisfaction during travel. Buyers should focus on the durability of the machines, integration of modern payment systems, and strategic placement to maximize visibility and accessibility for travelers.
Related Video: Kooler Ice Vending Machines – IM600XL vs. IM1000
Strategic Material Selection Guide for popmart vending machines
When selecting materials for Popmart vending machines, international B2B buyers must consider several factors that influence performance, durability, and compliance with local standards. Below, we analyze four common materials used in the construction of these machines, focusing on their properties, advantages, disadvantages, and specific considerations for buyers from diverse regions, including Africa, South America, the Middle East, and Europe.
Stainless Steel
Key Properties:
Stainless steel is known for its excellent corrosion resistance, high strength, and ability to withstand a wide range of temperatures. It typically has a temperature rating of up to 800°C (1472°F) and can handle moderate pressure levels.
Pros & Cons:
The durability of stainless steel makes it ideal for vending machines exposed to various environmental conditions. However, it is more expensive than other materials, which can impact overall project costs. Manufacturing complexity is moderate, requiring specialized equipment for cutting and welding.
Impact on Application:
Stainless steel is compatible with a wide range of media, including food and beverages, making it a popular choice for vending machines. Its resistance to corrosion is particularly beneficial in humid or wet environments.
Considerations for International Buyers:
Buyers should ensure compliance with local food safety standards, such as the EU regulations for food contact materials. Familiarity with ASTM or DIN standards is essential for quality assurance.
Aluminum
Key Properties:
Aluminum is lightweight, with a good strength-to-weight ratio, and is resistant to corrosion. It can withstand temperatures up to 400°C (752°F) and is often used in applications that require lower weight.
Pros & Cons:
The primary advantage of aluminum is its low cost and ease of manufacturing, which can lead to lower overall production costs. However, it is less durable than stainless steel and can be prone to deformation under high stress.
Impact on Application:
Aluminum is suitable for non-corrosive environments and is often used in the structural components of vending machines. Its lightweight nature aids in reducing shipping costs.
Considerations for International Buyers:
Buyers should consider the alloy grade, as different grades have varying properties. Compliance with local standards, such as JIS or ASTM, is crucial for ensuring material quality.
Polycarbonate
Key Properties:
Polycarbonate is a high-performance plastic known for its impact resistance and clarity. It can operate effectively at temperatures ranging from -40°C to 120°C (-40°F to 248°F).
Pros & Cons:
The transparency of polycarbonate allows for visibility of products inside the vending machine, enhancing customer engagement. However, it is less durable than metals and can scratch easily, which may affect aesthetics over time.
Impact on Application:
Polycarbonate is ideal for windows and display panels in vending machines, providing a clear view of the products while protecting them from environmental factors.
Considerations for International Buyers:
Buyers should ensure that the selected polycarbonate meets local safety and environmental standards, especially regarding recyclability and impact resistance.
Mild Steel
Key Properties:
Mild steel is a low-carbon steel that offers good weldability and strength, with a temperature rating of up to 300°C (572°F). It is often used in structural applications.
Pros & Cons:
While mild steel is cost-effective and easy to work with, it is susceptible to corrosion without proper treatment. Its durability is adequate for many applications, but it may require protective coatings.
Impact on Application:
Mild steel is suitable for the structural framework of vending machines but may not be ideal for environments with high humidity or exposure to corrosive substances.
Considerations for International Buyers:
Buyers should be aware of local corrosion resistance standards and consider applying protective coatings to enhance durability. Compliance with ASTM or DIN standards is also necessary for quality assurance.
Material | Typical Use Case for popmart vending machines | Key Advantage | Key Disadvantage/Limitation | Relative Cost (Low/Med/High) |
---|---|---|---|---|
Stainless Steel | External casing and internal components for durability | Excellent corrosion resistance, high strength | Higher cost than alternatives, moderate manufacturing complexity | High |
Aluminum | Structural components and frames for lightweight design | Cost-effective, lightweight | Less durable than stainless steel, prone to deformation | Medium |
Polycarbonate | Windows and display panels for product visibility | Impact-resistant, clear visibility | Scratches easily, less durable than metals | Medium |
Mild Steel | Structural framework for cost-effective builds | Cost-effective, good weldability | Susceptible to corrosion, requires protective coatings | Low |
This material selection guide provides a comprehensive overview for international B2B buyers, helping them make informed decisions based on performance, cost, and compliance with local standards.
In-depth Look: Manufacturing Processes and Quality Assurance for popmart vending machines
Manufacturing a vending machine like the Popmart involves a series of intricate processes designed to ensure efficiency, durability, and user satisfaction. For B2B buyers, especially from diverse markets such as Africa, South America, the Middle East, and Europe, understanding these manufacturing processes and the associated quality assurance measures is crucial for making informed purchasing decisions.
Manufacturing Processes
Material Preparation
The manufacturing process begins with the careful selection and preparation of materials. Common materials for Popmart vending machines include steel for the frame, high-impact plastic for the housing, and glass for the display panels. Key steps in this stage include:
– Material Sourcing: Suppliers should meet international standards to guarantee quality and sustainability.
– Cutting and Shaping: Advanced machinery, such as CNC machines, is often used to cut and shape materials precisely to design specifications.
Forming
Once the materials are prepared, the forming stage involves shaping components into their final forms. This process can include:
– Stamping: Used for creating the outer shell and internal parts, ensuring uniformity and strength.
– Injection Molding: This technique is particularly effective for producing plastic components, allowing for intricate designs that are lightweight yet sturdy.
Assembly
The assembly phase is where the various parts come together to create the complete vending machine. Key techniques include:
– Automated Assembly Lines: Utilizing robotics and conveyor systems to enhance speed and accuracy.
– Manual Assembly: Certain components may require skilled labor for precise placement and adjustments, ensuring that every machine meets quality standards.
Finishing
Finishing processes enhance both the aesthetic and functional aspects of the vending machine. This includes:
– Painting and Coating: Powder coating is commonly used to provide a durable, attractive finish that resists corrosion and wear.
– Quality Checks: Each machine undergoes a series of inspections to ensure all components are correctly installed and functioning as intended.
Quality Assurance
Quality assurance (QA) is integral to the manufacturing of Popmart vending machines, ensuring that every unit meets international standards and industry regulations.
International Standards
B2B buyers should be familiar with relevant standards such as:
– ISO 9001: This certification ensures that the manufacturer adheres to quality management principles, focusing on customer satisfaction and continuous improvement.
– CE Marking: For machines sold in Europe, CE marking indicates compliance with EU safety, health, and environmental protection standards.
Industry-Specific Certifications
In addition to general standards, specific certifications may apply, such as:
– API Certification: Relevant for machines that dispense food or beverages, ensuring compliance with food safety standards.
– RoHS Compliance: Ensures that hazardous materials are restricted in the manufacturing process.
Quality Control Checkpoints
Quality control is typically structured around several checkpoints, including:
– Incoming Quality Control (IQC): Materials and components are inspected upon arrival to ensure they meet specifications before production begins.
– In-Process Quality Control (IPQC): Continuous monitoring during the manufacturing process helps identify defects early, minimizing waste and rework.
– Final Quality Control (FQC): A comprehensive inspection of the finished product to verify that it meets all quality standards before shipment.
Common Testing Methods
B2B buyers should be aware of common testing methods used to ensure product quality:
– Functional Testing: Ensures that the vending machine operates correctly, including all electronic components and mechanisms.
– Durability Testing: Simulates real-world usage to assess how well the machine withstands wear and tear over time.
– Safety Testing: Checks for electrical safety and compliance with health regulations, particularly important for machines that dispense food and beverages.
Verifying Supplier Quality Control
For international B2B buyers, verifying the quality control processes of suppliers is essential. Here are actionable steps:
– Audits: Conducting regular audits of manufacturing facilities can provide insights into the operational standards and quality practices in place.
– Quality Reports: Requesting detailed quality reports from suppliers helps assess their compliance with international standards.
– Third-Party Inspections: Engaging third-party inspection services can offer an unbiased evaluation of the manufacturing processes and quality assurance measures.
Quality Control and Certification Nuances
B2B buyers from diverse regions may face specific challenges related to quality control and certification:
– Regulatory Differences: Understanding the regulatory landscape in different regions, such as food safety regulations in South America or electrical standards in Europe, is vital.
– Language Barriers: Buyers should ensure that documentation, including quality certifications and reports, is available in their preferred language to avoid misunderstandings.
– Cultural Differences: Recognizing that manufacturing practices and quality expectations may vary across regions can help buyers set realistic standards and maintain effective communication with suppliers.
In conclusion, a thorough understanding of the manufacturing processes and quality assurance practices for Popmart vending machines equips B2B buyers with the knowledge needed to make informed purchasing decisions. By focusing on quality standards, verifying supplier practices, and understanding regional nuances, buyers can ensure they are investing in reliable, high-quality vending solutions.
Related Video: The Production Planning Process
Comprehensive Cost and Pricing Analysis for popmart vending machines Sourcing
When sourcing Popmart vending machines, understanding the comprehensive cost structure and pricing dynamics is crucial for international B2B buyers. Below is an in-depth analysis of the key cost components, price influencers, and actionable tips for negotiation and procurement.
Cost Components
-
Materials: The raw materials used in manufacturing vending machines significantly impact the overall cost. Common materials include metal for the frame, glass for the front panel, and various electronic components. The choice of materials affects durability and aesthetic appeal.
-
Labor: Labor costs include wages for the workforce involved in assembly, quality control, and maintenance. In regions with higher labor costs, such as Europe, this can be a significant portion of the total cost.
-
Manufacturing Overhead: This encompasses costs associated with factory operations, such as utilities, rent, equipment depreciation, and administrative expenses. Efficient manufacturing processes can help reduce overhead costs.
-
Tooling: The cost of specialized tools and machinery necessary for production can vary greatly. Custom tooling for unique machine designs or features can increase initial costs but may lead to higher efficiency in production.
-
Quality Control (QC): Ensuring that vending machines meet quality standards involves inspection processes and testing. Investing in QC can prevent costly defects and returns, thereby enhancing the machine’s reliability.
-
Logistics: Shipping and handling costs are essential to consider, especially when sourcing internationally. Factors such as freight rates, customs duties, and insurance can add to the total cost.
-
Margin: Suppliers will typically apply a profit margin to their costs. This margin can fluctuate based on market demand, competition, and the supplier’s position within the industry.
Price Influencers
-
Volume/MOQ (Minimum Order Quantity): Larger orders often lead to reduced unit prices due to economies of scale. Negotiating favorable terms based on projected sales can yield significant savings.
-
Specifications/Customization: Customized features or specifications can elevate costs. Buyers should weigh the benefits of unique features against the associated price increase.
-
Materials: The choice of high-quality materials can enhance the machine’s lifespan but may also increase the upfront cost. Buyers should evaluate the long-term benefits of investing in quality materials.
-
Quality/Certifications: Machines that comply with international quality standards and certifications may command higher prices. However, these certifications can provide assurance of reliability and safety.
-
Supplier Factors: The reputation and experience of the supplier can influence pricing. Established suppliers may offer better warranties and support but might charge a premium.
-
Incoterms: The agreed terms of shipping can significantly affect pricing. Buyers should understand the implications of Incoterms (e.g., FOB, CIF) on total costs, including shipping responsibilities and risk transfer.
Buyer Tips
-
Negotiation: Effective negotiation can lead to better pricing. Buyers should prepare by understanding market rates and competitor pricing to leverage their position.
-
Cost-Efficiency: Assess the total cost of ownership, including maintenance and operational costs, rather than focusing solely on the purchase price.
-
Pricing Nuances: Be aware of regional pricing differences. For instance, prices in Europe may differ from those in Africa or South America due to market conditions and economic factors.
-
Supplier Relationships: Building strong relationships with suppliers can lead to more favorable terms and conditions. Regular communication can help in negotiating better prices and understanding market trends.
-
Research and Compare: Conduct thorough market research and compare multiple suppliers before making a decision. This can uncover variations in pricing and service offerings.
Disclaimer
Prices and costs presented here are indicative and can vary based on market conditions, specific supplier agreements, and customization requirements. Always consult with suppliers for the most accurate pricing tailored to your needs.
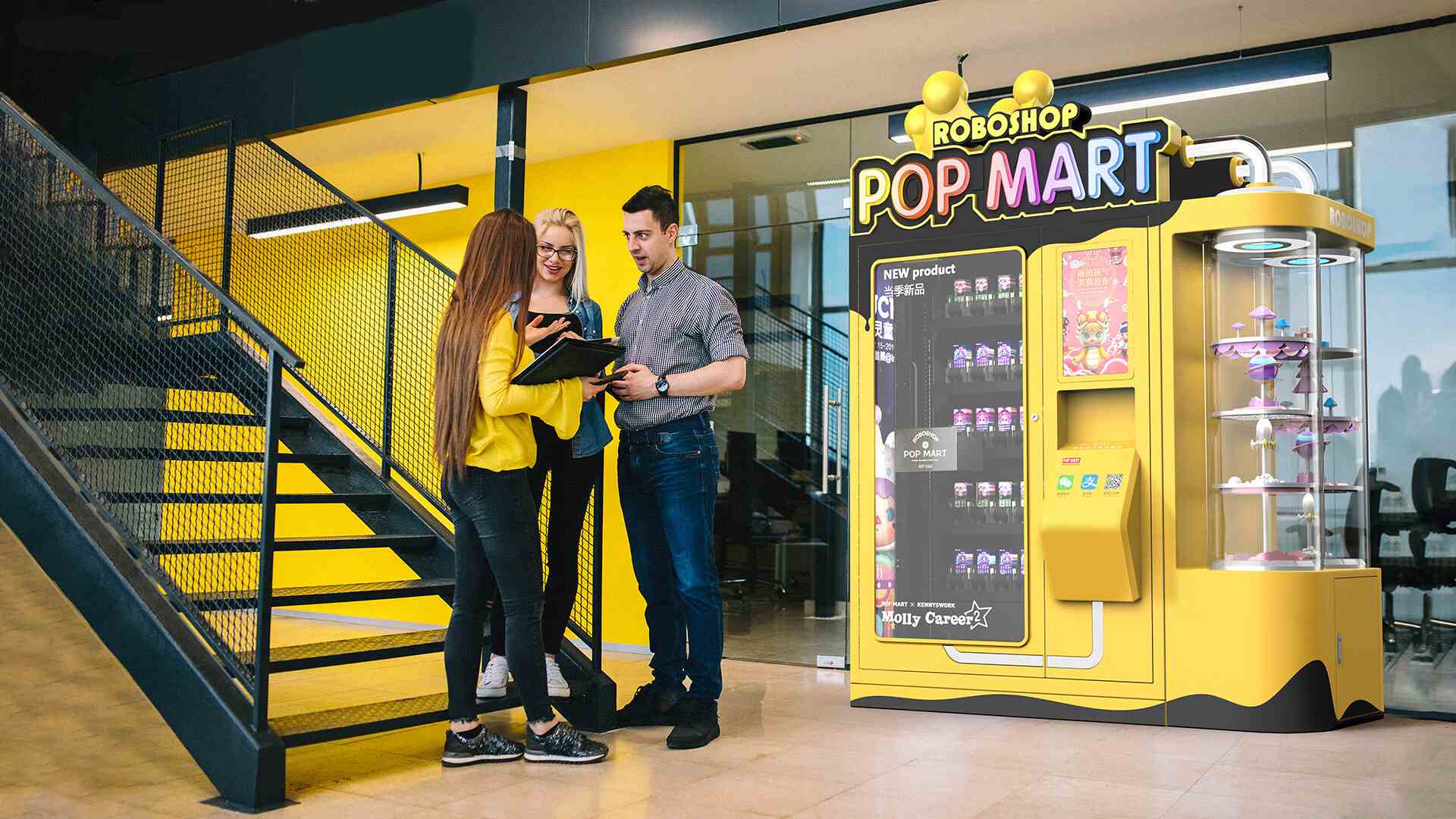
Illustrative Image (Source: Google Search)
Spotlight on Potential popmart vending machines Manufacturers and Suppliers
This section offers a look at a few manufacturers active in the ‘popmart vending machines’ market. This is a representative sample for illustrative purposes; B2B buyers must conduct their own extensive due diligence before any engagement. Information is synthesized from public sources and general industry knowledge.
Essential Technical Properties and Trade Terminology for popmart vending machines
Key Technical Properties of Popmart Vending Machines
Understanding the technical specifications of popmart vending machines is crucial for international B2B buyers. Here are some essential properties that impact performance, durability, and overall investment:
-
Material Grade
– Definition: The quality of materials used in manufacturing the vending machine, often categorized by standards such as stainless steel or high-grade plastics.
– Importance: High-grade materials enhance durability and resistance to corrosion and wear, ensuring the machine can withstand various environmental conditions, particularly in regions with extreme weather, such as Africa and the Middle East. -
Power Consumption
– Definition: The amount of electrical power the vending machine requires to operate, typically measured in watts.
– Importance: Understanding power consumption is vital for operational cost assessments. Machines with lower energy requirements can significantly reduce long-term operational expenses, making them more appealing to buyers in regions with high electricity costs. -
Capacity
– Definition: The total number of items the vending machine can hold, usually quantified in terms of product slots or total volume.
– Importance: Capacity directly affects sales potential. Machines with larger capacities are ideal for high-traffic areas, ensuring that they can meet demand without frequent restocking, which is crucial for maximizing revenue. -
Temperature Control Range
– Definition: The operational temperature range that the vending machine can maintain for perishable items, typically indicated in degrees Celsius.
– Importance: For machines dispensing food or beverages, effective temperature control is essential to ensure product safety and quality. Buyers in regions with varying climates should prioritize machines that can adapt to temperature fluctuations. -
User Interface Technology
– Definition: The technology used for customer interaction, which can include touch screens, cashless payment systems, and mobile app integration.
– Importance: A user-friendly interface can enhance customer satisfaction and increase sales. Machines equipped with modern payment options cater to a wider audience, especially in urban areas of Europe and South America where cashless transactions are prevalent.
Common Trade Terminology in the Vending Machine Industry
Familiarity with industry jargon is beneficial for B2B buyers when negotiating and managing purchases. Here are some common terms:
-
OEM (Original Equipment Manufacturer)
– Definition: A company that produces parts or equipment that may be marketed by another manufacturer.
– Usage: Buyers should understand whether they are purchasing directly from the OEM or through a reseller, as this can affect warranty and service options. -
MOQ (Minimum Order Quantity)
– Definition: The smallest amount of product that a supplier is willing to sell.
– Usage: Knowing the MOQ helps buyers assess whether the supplier’s offerings align with their inventory needs, especially for smaller businesses or startups. -
RFQ (Request for Quotation)
– Definition: A document sent to suppliers requesting pricing information on specific products or services.
– Usage: Utilizing RFQs can help buyers compare prices and terms from multiple suppliers, ensuring they make informed purchasing decisions. -
Incoterms (International Commercial Terms)
– Definition: A set of predefined international sales terms published by the International Chamber of Commerce (ICC), which clarify the responsibilities of buyers and sellers.
– Usage: Understanding Incoterms is crucial for international transactions, as they dictate shipping responsibilities, risk, and cost, helping buyers avoid potential disputes. -
Lead Time
– Definition: The amount of time it takes from placing an order to receiving the product.
– Usage: Knowing the lead time is essential for inventory management and planning, especially in markets where demand can fluctuate rapidly.
By grasping these technical properties and trade terms, international B2B buyers can make more informed decisions when investing in popmart vending machines, ultimately enhancing their business operations and profitability.
Navigating Market Dynamics, Sourcing Trends, and Sustainability in the popmart vending machines Sector
Market Overview & Key Trends
The popmart vending machines sector is experiencing a significant transformation driven by various global trends. As urbanization continues, especially in regions like Africa and South America, there is an increasing demand for convenient retail solutions. International B2B buyers are now prioritizing vending machines that integrate advanced technologies such as cashless payment systems, IoT connectivity, and AI-driven inventory management. These technologies not only enhance customer experience but also optimize operational efficiency.
In Europe and the Middle East, sustainability is becoming a crucial factor in purchasing decisions. Buyers are increasingly looking for machines that utilize eco-friendly materials and energy-efficient technologies. Emerging trends also include the customization of vending machines to cater to local tastes and preferences, which is particularly relevant for diverse markets in Africa and South America. Additionally, the rise of health-conscious consumers is prompting suppliers to offer healthy snacks and beverages in their vending machines, thus aligning with broader consumer trends toward wellness.
To navigate these market dynamics, international buyers should focus on partnerships with suppliers who demonstrate agility in adapting to technological advancements and consumer preferences. Engaging in thorough market research to understand regional preferences and compliance requirements can significantly enhance sourcing strategies.
Sustainability & Ethical Sourcing in B2B
Sustainability in the popmart vending machine sector is increasingly critical, with environmental concerns shaping buyer behavior. The production of vending machines can have a considerable ecological footprint, from the materials used to the energy consumed during operation. Thus, buyers are encouraged to seek suppliers who prioritize ethical sourcing and sustainable practices. This includes the use of recycled materials in machine construction and energy-efficient components that reduce carbon emissions.
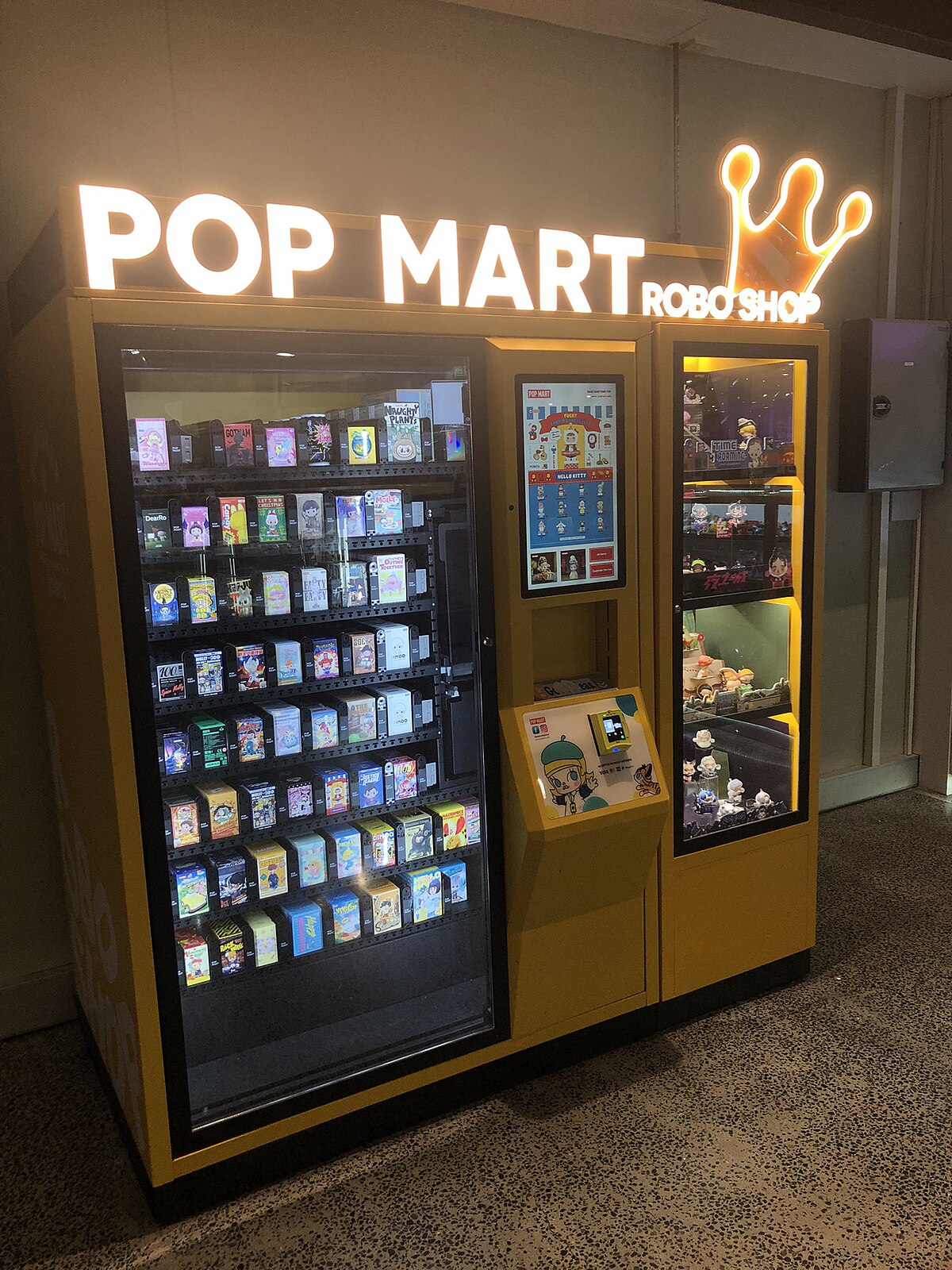
Illustrative Image (Source: Google Search)
Moreover, obtaining green certifications can serve as a competitive advantage in the marketplace. Certifications such as Energy Star or ISO 14001 demonstrate a commitment to environmental management and sustainability. For buyers in regions like Europe, where regulations around sustainability are stringent, aligning with certified suppliers can facilitate compliance and enhance brand reputation.
In addition, ethical sourcing extends to ensuring fair labor practices within the supply chain. B2B buyers should inquire about suppliers’ labor practices and transparency in their operations. By emphasizing sustainability and ethics, companies can not only meet regulatory requirements but also appeal to an increasingly environmentally conscious consumer base.
Brief Evolution/History
The vending machine industry has evolved significantly since its inception in the late 19th century. Initially, machines were simple mechanisms that dispensed products like cigarettes and postcards. The introduction of electricity in the 1930s revolutionized the sector, allowing for refrigerated machines and a wider array of products.
In recent decades, the evolution has been marked by technological advancements. The advent of digital payment systems and connectivity has transformed vending machines into smart retail solutions. This evolution is particularly relevant for international B2B buyers, as the modern vending machine must now cater to diverse consumer needs while integrating seamlessly into the digital economy. As the industry continues to innovate, understanding this historical context can help buyers make informed decisions about future investments in vending technology.
Related Video: Is global trade transforming? | Counting the Cost
Frequently Asked Questions (FAQs) for B2B Buyers of popmart vending machines
-
What should I consider when vetting suppliers for Popmart vending machines?
When vetting suppliers, ensure they have a solid reputation and experience in the vending machine industry. Request references from previous clients and check online reviews. It’s crucial to assess their manufacturing capabilities and quality control processes. Certifications such as ISO or CE can indicate compliance with international standards. Additionally, consider suppliers who have experience exporting to your region, as they will be familiar with local regulations and customs requirements. -
Can I customize Popmart vending machines to fit my brand?
Yes, many suppliers offer customization options for Popmart vending machines. You can typically request branding elements like colors, logos, and specific product selections tailored to your target market. Discuss your requirements upfront and ask for samples or mock-ups to ensure they align with your vision. Be aware that extensive customization may affect the lead time and minimum order quantities (MOQs). -
What are the typical minimum order quantities (MOQ) and lead times for Popmart vending machines?
MOQs can vary significantly between suppliers, but they often range from 10 to 50 units. Lead times can also differ based on customization and production schedules, typically spanning 4 to 12 weeks. It’s advisable to discuss these details early in your negotiations to align your purchasing plans with the supplier’s capabilities. Additionally, factor in shipping times when planning your inventory. -
What payment methods are commonly accepted when purchasing vending machines internationally?
Payment methods can vary by supplier, but most will accept wire transfers, credit cards, and letters of credit for larger transactions. Always negotiate favorable terms, considering factors like deposit percentages and payment milestones. For international orders, using a secure payment method can help mitigate risks associated with cross-border transactions. Ensure that payment terms are clearly outlined in your purchase agreement. -
What quality assurance measures should I expect from suppliers?
Reputable suppliers will have stringent quality assurance (QA) processes in place. This should include regular inspections during production, testing of machines before shipping, and adherence to international quality standards. Request documentation of QA protocols and any relevant certifications. Additionally, inquire about warranties and after-sales support to ensure you have recourse in case of defects or operational issues. -
How do logistics and shipping work for international orders of vending machines?
Logistics for international orders typically involve coordination between the supplier and freight forwarders. Discuss who will handle shipping and the associated costs, including duties and taxes. Suppliers should provide detailed shipping timelines and tracking information. Ensure that the machines are adequately packaged to prevent damage during transit. Familiarize yourself with the import regulations of your country to avoid delays. -
What steps can I take to resolve disputes with a supplier?
To resolve disputes effectively, establish clear communication channels with your supplier from the beginning. Document all agreements, including specifications, payment terms, and delivery schedules. If issues arise, attempt to resolve them amicably through direct communication. If necessary, refer to the dispute resolution clause in your contract, which may specify mediation or arbitration. Keeping a record of all correspondence can be crucial in case formal action is required. -
What certifications should I look for in Popmart vending machines?
Look for certifications that demonstrate compliance with international safety and quality standards, such as CE (European Conformity), UL (Underwriters Laboratories), or ISO 9001 (Quality Management Systems). These certifications indicate that the machines have passed rigorous testing and meet specific safety requirements. Additionally, inquire about any local certifications that may be relevant in your market to ensure compliance with regional regulations.
Strategic Sourcing Conclusion and Outlook for popmart vending machines
In summary, strategic sourcing for Popmart vending machines presents a significant opportunity for international B2B buyers to enhance their operational efficiency and customer engagement. By leveraging key insights into market trends, supplier capabilities, and technological advancements, businesses can make informed purchasing decisions that align with their long-term goals.
Key takeaways include the importance of evaluating suppliers not just on price but also on reliability, after-sales support, and innovation in product offerings. Furthermore, understanding regional market dynamics—particularly in Africa, South America, the Middle East, and Europe—can lead to better tailored solutions that meet local demands.
Looking ahead, the vending machine sector is poised for growth, driven by advancements in technology and changing consumer behaviors. International B2B buyers should actively seek partnerships with reputable suppliers who can provide not only quality machines but also integrated solutions that enhance customer experience.
Take action today by exploring the diverse offerings in the market and aligning them with your business strategy. Embrace the evolving landscape of vending solutions and position your company for success in the competitive marketplace.