Master Sourcing Pepsi Vending Machines for Optimal Customer
Guide to Pepsi Vending Machines
- Introduction: Navigating the Global Market for pepsi vending machines
- Understanding pepsi vending machines Types and Variations
- Key Industrial Applications of pepsi vending machines
- Strategic Material Selection Guide for pepsi vending machines
- In-depth Look: Manufacturing Processes and Quality Assurance for pepsi vending machines
- Comprehensive Cost and Pricing Analysis for pepsi vending machines Sourcing
- Spotlight on Potential pepsi vending machines Manufacturers and Suppliers
- Essential Technical Properties and Trade Terminology for pepsi vending machines
- Navigating Market Dynamics, Sourcing Trends, and Sustainability in the pepsi vending machines Sector
- Frequently Asked Questions (FAQs) for B2B Buyers of pepsi vending machines
- Strategic Sourcing Conclusion and Outlook for pepsi vending machines
Introduction: Navigating the Global Market for pepsi vending machines
In the rapidly evolving landscape of consumer engagement, Pepsi vending machines have emerged as a pivotal asset for businesses looking to enhance their service offerings. These machines not only provide convenience but also serve as a powerful marketing tool, capable of delivering brand visibility and customer interaction in high-traffic areas. As international B2B buyers from Africa, South America, the Middle East, and Europe explore opportunities in this sector, understanding the nuances of vending machine selection becomes paramount.
This comprehensive guide delves into various types of Pepsi vending machines, examining the materials used in their construction, manufacturing processes, and quality control measures that ensure durability and reliability. Buyers will gain insights into leading suppliers and the pricing structures associated with these machines, enabling informed decisions based on market dynamics and regional specifics.
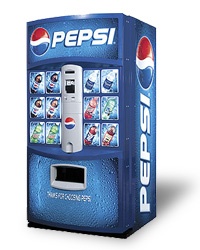
Illustrative Image (Source: Google Search)
Furthermore, the guide addresses frequently asked questions, providing clarity on operational aspects, maintenance, and customization options. By equipping B2B buyers with actionable information and strategic insights, this resource empowers them to navigate the global market effectively, ensuring that their investments in Pepsi vending machines yield optimal returns and enhance customer satisfaction. Whether you are in Thailand or Poland, this guide serves as your roadmap to successful sourcing in the vending machine market.
Understanding pepsi vending machines Types and Variations
Type Name | Key Distinguishing Features | Primary B2B Applications | Brief Pros & Cons for Buyers |
---|---|---|---|
Traditional Vending Machine | Standard design, accepts coins and bills | Offices, schools, public areas | Pros: Reliable, easy to maintain. Cons: Limited product variety, less modern payment options. |
Smart Vending Machine | Equipped with touch screens and cashless payment options | Retail stores, malls, airports | Pros: Enhanced user experience, real-time inventory tracking. Cons: Higher initial cost, requires internet connectivity. |
Refrigerated Vending Machine | Maintains cold temperatures for beverages | Restaurants, gyms, convenience stores | Pros: Ideal for cold drinks, increases sales potential. Cons: Higher energy costs, requires regular maintenance. |
Snack Vending Machine | Offers a variety of snacks alongside beverages | Break rooms, leisure centers | Pros: Diversifies offerings, caters to snack preferences. Cons: May require more frequent restocking. |
Combo Vending Machine | Combines snacks and drinks in one unit | Corporate offices, events | Pros: Space-efficient, caters to varied customer needs. Cons: Complexity can lead to more breakdowns. |
Traditional Vending Machine
Traditional vending machines are the most common type, designed to accept coins and bills, making them accessible in various locations. They are particularly suitable for offices, schools, and public areas where users expect straightforward transactions. When considering a purchase, B2B buyers should evaluate the machine’s reliability and ease of maintenance, as these factors significantly influence operational costs. However, the limited product variety and lack of modern payment options may deter some customers.
Smart Vending Machine
Smart vending machines are equipped with advanced features such as touch screens and cashless payment systems, appealing to tech-savvy consumers. These machines are ideal for retail stores, malls, and airports, where user experience is paramount. Buyers should consider the initial investment and the need for internet connectivity, which can increase operational costs. While they offer enhanced inventory management and customer engagement, the higher upfront costs can be a barrier for some businesses.
Refrigerated Vending Machine
Refrigerated vending machines are specifically designed to maintain cold temperatures, making them suitable for beverages like Pepsi. They are commonly found in restaurants, gyms, and convenience stores, where cold drinks are in high demand. B2B buyers should weigh the benefits of increased sales potential against the higher energy costs and maintenance requirements. Regular upkeep is essential to ensure optimal performance and product freshness.
Snack Vending Machine
Snack vending machines provide a variety of snack options alongside beverages, making them popular in break rooms and leisure centers. These machines cater to diverse consumer preferences, enhancing customer satisfaction. However, B2B buyers should consider the increased frequency of restocking due to the diverse offerings. The ability to cater to different tastes can lead to higher sales, but it also requires careful inventory management.
Combo Vending Machine
Combo vending machines combine snacks and drinks into a single unit, maximizing space efficiency. They are ideal for corporate offices and events where space is limited but a variety of options is desired. Buyers should evaluate the complexity of these machines, as they may lead to more frequent breakdowns compared to simpler models. The ability to meet varied customer needs can drive sales, but operational challenges should be carefully considered.
Related Video: How to make Pepsi Vending Machine
Key Industrial Applications of pepsi vending machines
Industry/Sector | Specific Application of pepsi vending machines | Value/Benefit for the Business | Key Sourcing Considerations for this Application |
---|---|---|---|
Hospitality | Hotel lobbies and conference centers | Enhances guest experience, generates additional revenue | Machine reliability, product variety, payment options |
Education | University campuses | Convenient access to beverages for students, supports campus events | Durability, energy efficiency, customizable branding |
Healthcare | Hospitals and clinics | Provides quick refreshment options for patients and staff | Compliance with health regulations, ease of cleaning |
Corporate Offices | Break rooms and lounges | Improves employee satisfaction, encourages social interaction | Space requirements, maintenance support, product rotation |
Retail | Shopping malls and grocery stores | Increases foot traffic, offers on-the-go beverage options | Location analysis, promotional capabilities, inventory management |
Hospitality
In the hospitality sector, Pepsi vending machines are strategically placed in hotel lobbies and conference centers to enhance guest experience. These machines provide a convenient option for refreshments, allowing guests to access beverages without waiting in line at a bar or restaurant. For international buyers, considerations such as machine reliability and the ability to offer a variety of products are crucial, as they directly impact guest satisfaction and revenue generation.
Education
On university campuses, Pepsi vending machines serve as essential convenience points for students and staff. They provide quick access to beverages during busy schedules and support campus events by offering refreshments. Buyers in this sector should prioritize durability and energy efficiency, as machines must withstand heavy usage while minimizing operational costs. Customizable branding options can also enhance the institution’s image.
Healthcare
In healthcare settings, such as hospitals and clinics, Pepsi vending machines offer quick refreshment options for both patients and staff. They help improve the patient experience by providing easy access to beverages during long wait times. Buyers must ensure that machines comply with health regulations and are easy to clean, as hygiene is paramount in these environments. Additionally, the ability to offer healthier beverage options can be a significant consideration.
Corporate Offices
Pepsi vending machines in corporate offices contribute to employee satisfaction by providing easy access to refreshments in break rooms and lounges. They encourage social interaction among employees during breaks, which can enhance workplace morale. When sourcing machines for this application, key considerations include space requirements, maintenance support, and the ability to rotate products to keep offerings fresh and appealing.
Retail
In retail environments like shopping malls and grocery stores, Pepsi vending machines increase foot traffic by offering consumers on-the-go beverage options. These machines can be strategically placed near entrances or popular shopping areas to maximize visibility and convenience. Buyers should conduct location analysis to determine the best placement and consider promotional capabilities to drive sales. Effective inventory management is also vital to ensure popular products are always available.
Related Video: How to Build Money Operated Pepsi Vending Machine
Strategic Material Selection Guide for pepsi vending machines
When selecting materials for Pepsi vending machines, it is crucial to consider their properties, advantages, disadvantages, and compliance with international standards. Below is an analysis of four common materials used in the manufacturing of these machines, focusing on their application in various regions, including Africa, South America, the Middle East, and Europe.
1. Stainless Steel
Key Properties:
Stainless steel is known for its excellent corrosion resistance, high strength, and ability to withstand high temperatures and pressures. It is often used in environments where hygiene is paramount, making it suitable for food and beverage applications.
Pros & Cons:
The durability of stainless steel is a significant advantage, as it can withstand the rigors of outdoor environments and frequent use. However, it is relatively expensive compared to other materials, which can impact the overall cost of the vending machine. Manufacturing complexity is moderate, as it requires specialized equipment for cutting and welding.
Impact on Application:
Stainless steel is compatible with various media, including carbonated beverages, and does not impart flavors or contaminants. Its resistance to rust and staining makes it ideal for vending machines exposed to moisture.
Specific Considerations for International Buyers:
Compliance with food safety standards such as FDA and EU regulations is essential. Buyers should also consider local standards like ASTM or DIN for material specifications. In regions like Africa and South America, the availability of stainless steel may vary, influencing sourcing decisions.
2. Powder-coated Steel
Key Properties:
Powder-coated steel combines the strength of steel with a protective coating that enhances corrosion resistance and aesthetic appeal. The coating process involves applying a dry powder that is then cured under heat.
Pros & Cons:
The primary advantage of powder-coated steel is its cost-effectiveness and variety of color options, which can enhance branding opportunities. However, it is less durable than stainless steel and can chip or scratch, exposing the underlying steel to corrosion.
Impact on Application:
This material is suitable for indoor vending machines or those in sheltered environments. It may not be ideal for areas with high humidity or exposure to harsh weather conditions.
Specific Considerations for International Buyers:
Buyers should ensure that the powder coating meets relevant environmental and safety standards. In Europe, for example, compliance with REACH regulations is important. Availability may vary, impacting lead times and costs.
3. Aluminum
Key Properties:
Aluminum is lightweight, corrosion-resistant, and has good thermal conductivity. It is often used in applications where weight savings are critical, such as portable vending machines.
Pros & Cons:
The lightweight nature of aluminum makes it easy to transport and install. However, it is generally less durable than steel and can be more susceptible to dents and scratches. The manufacturing process is relatively straightforward, but care must be taken to ensure proper joining techniques.
Impact on Application:
Aluminum is suitable for non-corrosive environments and can handle a variety of beverages. It is particularly effective in applications where thermal insulation is required.
Specific Considerations for International Buyers:
Buyers should be aware of the aluminum grades available and their specific properties. Compliance with international standards such as ISO may be necessary, and buyers should consider local sourcing options to mitigate costs.
4. Polycarbonate
Key Properties:
Polycarbonate is a durable thermoplastic known for its impact resistance and optical clarity. It is often used for transparent components in vending machines, such as windows and displays.
Pros & Cons:
The key advantage of polycarbonate is its high impact resistance, making it suitable for high-traffic areas. However, it can be more expensive than glass and may scratch more easily, requiring protective coatings.
Impact on Application:
Polycarbonate is ideal for applications where visibility is important, such as showcasing products. It is also resistant to UV light, making it suitable for outdoor use.
Specific Considerations for International Buyers:
Buyers should ensure that polycarbonate meets relevant safety standards, especially in regions with stringent regulations. In Europe, compliance with EN standards may be necessary, while buyers in Africa may face different regulatory environments.
Summary Table
Material | Typical Use Case for Pepsi Vending Machines | Key Advantage | Key Disadvantage/Limitation | Relative Cost (Low/Med/High) |
---|---|---|---|---|
Stainless Steel | Structural components, external casing | Excellent corrosion resistance, durability | Higher cost, moderate manufacturing complexity | High |
Powder-coated Steel | Indoor machines, branding applications | Cost-effective, aesthetic flexibility | Less durable, can chip or scratch | Medium |
Aluminum | Portable machines, lightweight structures | Lightweight, good thermal conductivity | Less durable, susceptible to dents | Medium |
Polycarbonate | Transparent panels, displays | High impact resistance, UV resistant | Scratches easily, higher cost than glass | Medium |
This guide provides actionable insights for international B2B buyers, helping them make informed decisions regarding material selection for Pepsi vending machines tailored to their regional needs.
In-depth Look: Manufacturing Processes and Quality Assurance for pepsi vending machines
The manufacturing processes and quality assurance protocols for Pepsi vending machines are critical for ensuring product reliability and customer satisfaction. This section will delve into the main stages of manufacturing, key techniques employed, relevant international standards for quality assurance, and actionable insights for international B2B buyers, particularly those from Africa, South America, the Middle East, and Europe.
Manufacturing Processes
Material Preparation
The manufacturing process begins with the selection and preparation of high-quality materials. Common materials include stainless steel for durability, plastic for the vending compartment, and electronic components for payment systems. Suppliers are chosen based on their ability to meet stringent specifications, and materials are often sourced from certified vendors to ensure consistency. Buyers should inquire about the origin of materials and whether suppliers adhere to sustainable practices.
Forming
The forming stage involves shaping the materials into the necessary components of the vending machine. This includes processes such as stamping, bending, and injection molding. Advanced technologies like CNC machining and laser cutting may be utilized for precision. Buyers should look for manufacturers that employ innovative forming techniques to enhance the structural integrity of the machines.
Assembly
Assembly is a critical stage where various components are brought together. This includes the installation of mechanical parts, electronic systems, and refrigeration units. Automated assembly lines are often used to improve efficiency, but manual assembly may be employed for complex configurations. Buyers should verify that manufacturers utilize skilled labor and ergonomic practices to ensure quality during this stage.
Finishing
Finishing involves surface treatments, painting, and branding. This stage not only enhances aesthetics but also protects against corrosion and wear. Common techniques include powder coating and UV printing. Buyers should ensure that the finishing processes meet local environmental regulations and standards, particularly concerning VOC emissions and waste management.
Quality Assurance
International Standards
Quality assurance in the manufacturing of Pepsi vending machines is governed by various international standards, with ISO 9001 being a cornerstone. This standard ensures that manufacturers maintain a quality management system focused on customer satisfaction and continuous improvement. Additionally, industry-specific certifications such as CE marking for compliance in the European market and API standards for mechanical components may apply.
Quality Control Checkpoints
Quality control is integrated into the manufacturing process through various checkpoints:
-
Incoming Quality Control (IQC): Raw materials are inspected upon arrival to ensure they meet specifications. Buyers should request IQC reports from suppliers.
-
In-Process Quality Control (IPQC): Ongoing inspections during the manufacturing process help identify defects early. This might include checks on dimensions and tolerances.
-
Final Quality Control (FQC): Completed machines undergo rigorous testing to ensure they function correctly and meet safety standards. Buyers should inquire about the FQC protocols in place.
Common Testing Methods
Testing methods for quality assurance may include:
- Functional Testing: Ensuring the machine operates as intended, including payment systems, refrigeration, and dispensing mechanisms.
- Durability Testing: Assessing the machine’s ability to withstand environmental conditions and user interactions.
- Safety Testing: Verifying compliance with electrical and safety standards, crucial for markets in Europe and North America.
Verifying Supplier Quality Control
For international B2B buyers, verifying a supplier’s quality control processes is essential. Here are several strategies:
-
Supplier Audits: Conduct regular audits of suppliers to evaluate their compliance with ISO standards and internal quality processes. This can be done through on-site visits or third-party audit services.
-
Quality Reports: Request detailed quality reports that outline testing results, defect rates, and corrective actions taken for any issues identified.
-
Third-Party Inspections: Engage third-party inspection agencies to verify product quality before shipment. This is especially important when dealing with suppliers from regions with varying quality standards.
Quality Control and Certification Nuances
International B2B buyers should be aware of specific quality control and certification nuances when dealing with suppliers from different regions:
-
Cultural Differences: Understanding local business practices and cultural attitudes towards quality can help buyers navigate supplier relationships more effectively.
-
Regulatory Compliance: Different regions may have varying regulations regarding product safety and environmental impact. It is crucial for buyers to ensure that their suppliers comply with all relevant local regulations.
-
Language Barriers: Effective communication is key to ensuring that quality expectations are understood and met. Buyers may need to employ translators or local representatives to facilitate discussions.
Conclusion
Understanding the manufacturing processes and quality assurance protocols for Pepsi vending machines is vital for B2B buyers aiming to establish reliable partnerships. By focusing on material preparation, forming, assembly, and finishing, alongside rigorous quality control practices, buyers can ensure they select suppliers that deliver high-quality products. Additionally, being proactive in verifying supplier quality can significantly mitigate risks and enhance operational efficiency in diverse international markets.
Related Video: How Pepsi is Made In Factory | Pepsi Factory Process
Comprehensive Cost and Pricing Analysis for pepsi vending machines Sourcing
In the sourcing of Pepsi vending machines, understanding the comprehensive cost structure and pricing dynamics is essential for international B2B buyers. The costs associated with these machines encompass various components that can significantly affect the total expenditure.
Cost Components
- Materials: The primary materials include metal, plastics, and electronic components. The quality and source of these materials can substantially impact the overall cost. Buyers should inquire about material specifications and certifications, which can influence durability and operational efficiency.
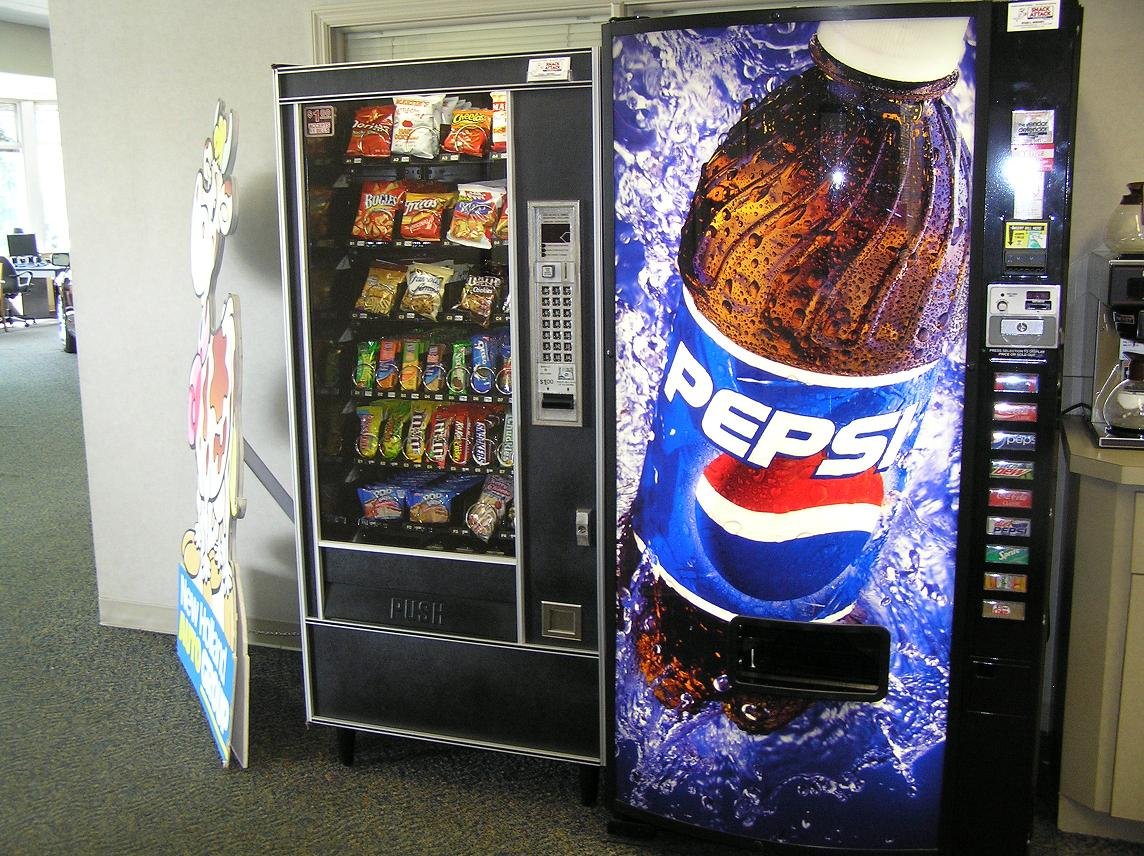
Illustrative Image (Source: Google Search)
-
Labor: Labor costs can vary depending on the manufacturing location. Countries with lower labor costs may offer competitive pricing, but it’s important to evaluate the trade-offs in quality and manufacturing practices.
-
Manufacturing Overhead: This includes costs related to factory operation, utilities, and administrative expenses. Understanding the overhead can help buyers assess the overall pricing strategy of suppliers.
-
Tooling: Customization often requires specialized tooling, which can add to the initial costs. Buyers should clarify if tooling costs are included in the quoted price or billed separately.
-
Quality Control (QC): Rigorous QC processes ensure the machines meet industry standards. Suppliers may charge more for enhanced QC measures, but this can save costs in the long run by reducing defects and ensuring operational reliability.
-
Logistics: Shipping and handling costs can vary widely depending on the destination. It’s crucial for buyers to consider shipping methods, tariffs, and insurance when calculating total expenses.
-
Margin: Suppliers typically include a profit margin in their pricing. Understanding the typical margins in the vending machine industry can help buyers negotiate more effectively.
Price Influencers
Several factors can influence the pricing of vending machines:
-
Volume/MOQ: Larger orders often qualify for discounts due to economies of scale. Buyers should assess their needs against minimum order quantities (MOQ) to maximize cost-effectiveness.
-
Specifications/Customization: Customized machines tailored to specific market needs may incur additional costs. It’s advisable to evaluate whether the benefits of customization justify the higher price.
-
Materials and Quality Certifications: High-quality materials and recognized quality certifications can lead to increased costs but may enhance the longevity and performance of the machines.
-
Supplier Factors: The reputation, location, and financial stability of the supplier can impact pricing. Engaging with reputable suppliers can lead to better service and reliability.
-
Incoterms: Understanding Incoterms is essential for determining who bears costs and risks during transportation. This can significantly affect the final price.
Buyer Tips
-
Negotiation: Engage suppliers in discussions to explore possible discounts, especially for larger orders. Don’t hesitate to request price breakdowns to understand cost structures.
-
Cost-Efficiency: Look beyond initial prices. Assess the Total Cost of Ownership (TCO), which includes maintenance, energy consumption, and potential revenue generation from the machines.
-
Pricing Nuances: Be aware of regional pricing differences. Factors such as local demand, competition, and economic conditions can influence prices across different markets, particularly in Africa, South America, the Middle East, and Europe.
-
Disclaimer for Indicative Prices: Prices for Pepsi vending machines can vary widely based on the factors mentioned above. It is advisable to obtain quotes from multiple suppliers and consider conducting a market analysis to ensure competitive pricing.
By understanding the cost structure and pricing dynamics, B2B buyers can make informed decisions, ensuring they source Pepsi vending machines that meet their operational needs while optimizing costs.
Spotlight on Potential pepsi vending machines Manufacturers and Suppliers
This section offers a look at a few manufacturers active in the ‘pepsi vending machines’ market. This is a representative sample for illustrative purposes; B2B buyers must conduct their own extensive due diligence before any engagement. Information is synthesized from public sources and general industry knowledge.
Essential Technical Properties and Trade Terminology for pepsi vending machines
When considering the procurement of Pepsi vending machines, understanding essential technical properties and industry-specific terminology is crucial for making informed purchasing decisions. This section outlines the critical specifications and common jargon that international B2B buyers, especially from Africa, South America, the Middle East, and Europe, should be familiar with.
Key Technical Properties
-
Material Grade
– Definition: Refers to the type of materials used in the construction of the vending machine, such as stainless steel or high-grade plastic.
– Importance: High-quality materials ensure durability and resistance to corrosion, which is vital for machines placed in outdoor or high-traffic environments. Selecting the right material can also affect maintenance costs and machine longevity. -
Capacity
– Definition: The number of products the vending machine can hold, typically measured in terms of number of cans or bottles.
– Importance: A higher capacity allows for less frequent restocking, which is beneficial for operational efficiency. Understanding the expected foot traffic in a location can help determine the appropriate capacity needed. -
Power Supply
– Definition: The electrical requirements of the vending machine, including voltage and power consumption.
– Importance: Compatibility with local electrical standards is critical to avoid installation issues. Knowing the power requirements can also help in estimating operational costs based on energy consumption. -
Temperature Control
– Definition: The ability of the vending machine to maintain specific temperatures for beverages.
– Importance: Effective temperature control is essential for product quality, especially for beverages that require refrigeration. Buyers should assess the machine’s cooling efficiency and temperature range to ensure it meets the needs of the products being sold.
- User Interface
– Definition: The design and functionality of the machine’s interface, including payment options and product selection mechanisms.
– Importance: A user-friendly interface can enhance customer satisfaction and increase sales. Consideration of local payment preferences (e.g., cash, credit card, mobile payments) is also essential for market acceptance.
Common Trade Terminology
-
OEM (Original Equipment Manufacturer)
– Definition: A company that produces parts or equipment that may be marketed by another manufacturer.
– Importance: Understanding whether a vending machine is an OEM product can help buyers assess reliability and warranty options, ensuring they are purchasing high-quality equipment. -
MOQ (Minimum Order Quantity)
– Definition: The smallest quantity of a product that a supplier is willing to sell.
– Importance: Knowing the MOQ helps buyers plan their purchases effectively, especially if they are looking to enter new markets or expand their offerings. -
RFQ (Request for Quotation)
– Definition: A document sent to suppliers to solicit price and terms for specific products or services.
– Importance: RFQs enable buyers to compare different suppliers’ offerings, ensuring competitive pricing and favorable terms. -
Incoterms (International Commercial Terms)
– Definition: A set of predefined international trade terms that clarify the responsibilities of buyers and sellers.
– Importance: Familiarity with Incoterms is essential for understanding shipping costs, risk management, and delivery responsibilities, particularly for international transactions. -
Lead Time
– Definition: The time it takes from placing an order to receiving the product.
– Importance: Knowing the lead time helps businesses plan their inventory and sales strategies, especially in markets with high demand variability.
Incorporating these technical properties and trade terminologies into your procurement strategy will enhance decision-making and foster successful business relationships in the competitive market for Pepsi vending machines.
Navigating Market Dynamics, Sourcing Trends, and Sustainability in the pepsi vending machines Sector
Market Overview & Key Trends
The global market for Pepsi vending machines is experiencing significant transformation, driven by technological advancements and changing consumer behaviors. One of the primary drivers is the increasing demand for contactless payment solutions, propelled by the COVID-19 pandemic. B2B buyers, particularly in regions like Africa, South America, the Middle East, and Europe, are witnessing a surge in the adoption of cashless transactions, including mobile payments and digital wallets, as these technologies enhance convenience and security.
Emerging trends also include the integration of smart technology into vending machines. Features such as remote monitoring, inventory management, and data analytics are becoming standard. These advancements allow operators to optimize stock levels, reduce waste, and enhance the customer experience through personalized offerings. For instance, machines equipped with AI can analyze purchasing patterns and adjust product selections accordingly, catering to local preferences.
Furthermore, sustainability is becoming a crucial factor in sourcing decisions. International buyers are increasingly seeking vending machines that utilize eco-friendly materials and energy-efficient technologies. This aligns with global initiatives aimed at reducing carbon footprints, especially in regions with strict environmental regulations. Buyers must stay informed about these market dynamics to effectively navigate the evolving landscape and make informed purchasing decisions.
Sustainability & Ethical Sourcing in B2B
Sustainability is no longer a mere trend but a fundamental expectation in the B2B landscape, particularly in the vending machine sector. For international buyers, understanding the environmental impact of vending machine operations is essential. Traditional vending machines often contribute to energy waste and excessive plastic use. In contrast, modern machines are designed with energy-efficient components and use recyclable materials, significantly reducing their environmental footprint.
Ethical sourcing is also paramount. B2B buyers should prioritize suppliers who demonstrate a commitment to sustainability through transparent supply chains and certifications. Look for vendors that provide “green” certifications, such as ISO 14001 or Energy Star, which indicate compliance with environmental standards. Additionally, utilizing biodegradable materials for packaging and promoting recycling initiatives can enhance a company’s sustainability profile.
Investing in sustainable vending machines not only meets regulatory requirements but also resonates with consumers who increasingly prefer brands committed to environmental responsibility. This shift can enhance brand loyalty and open new markets, particularly in regions where eco-consciousness is a driving consumer behavior.
Brief Evolution/History
The vending machine industry has evolved dramatically since its inception in the early 20th century. Initially, machines dispensed simple products like candies and cigarettes. However, the introduction of automated technology in the 1970s marked a significant turning point, allowing for the sale of a broader range of items, including beverages like Pepsi.
Over the decades, advancements in technology have continuously shaped the sector. The 1990s saw the integration of electronic payment systems, while the 2000s introduced touchscreen interfaces and digital displays, enhancing user experience. Today, the focus is on smart vending solutions that leverage IoT and data analytics, providing a seamless and personalized customer experience. For B2B buyers, understanding this evolution is crucial for selecting machines that not only meet current demands but are also equipped to adapt to future trends.
Related Video: Global Trade & Logistics – What is Global Trade?
Frequently Asked Questions (FAQs) for B2B Buyers of pepsi vending machines
-
What should I consider when vetting suppliers of Pepsi vending machines?
When vetting suppliers, prioritize their experience and reputation in the vending machine market. Look for suppliers with a proven track record in international sales and positive customer feedback. Verify their certifications and compliance with local regulations in your region. Request references and assess their capacity for after-sales support, including maintenance and spare parts availability, as this will impact your long-term satisfaction and operational efficiency. -
Can I customize my Pepsi vending machines?
Yes, many suppliers offer customization options for Pepsi vending machines. You can request branding elements, color schemes, and features like cashless payment systems or touchscreen interfaces. Discuss your specific needs with potential suppliers early in the negotiation process to ensure they can accommodate your requests. Be mindful that customization may affect lead times and pricing. -
What are the minimum order quantities (MOQ) and lead times for purchasing?
MOQs and lead times can vary significantly between suppliers. Typically, MOQs range from 5 to 20 machines, depending on the supplier’s production capabilities and your customization requests. Lead times may range from 4 to 12 weeks after order confirmation. Always clarify these details upfront to align your procurement plans and avoid unexpected delays in your supply chain. -
What payment terms should I expect when sourcing internationally?
Payment terms may vary by supplier and region, but common practices include upfront deposits (20-50%) with the balance due before shipment. Letters of credit are often used for larger transactions, providing security for both parties. Discuss payment methods, currency options, and any potential fees upfront to ensure a smooth transaction process and avoid currency exchange losses. -
What quality assurance measures should I look for in vending machines?
Ensure that the supplier adheres to international quality standards, such as ISO certifications. Request documentation of quality control processes and testing protocols for the machines. Understanding the warranty terms and what they cover is also crucial. A reliable supplier should provide clear information on product quality and support, including how they handle defective units. -
How can I manage logistics and shipping for my vending machines?
Logistics can be complex when importing vending machines. Collaborate with suppliers who have experience in international shipping and understand the customs regulations of your country. Discuss shipping options, including freight forwarders and insurance. It’s also advisable to request a delivery timeline and be prepared for potential delays due to customs clearance or transportation issues. -
What steps should I take if there’s a dispute with my supplier?
Establish a clear communication channel with your supplier from the outset. In case of disputes, refer to your contract for terms regarding conflict resolution. Most suppliers will have a process in place for handling disputes, which may include mediation or arbitration. Document all communications and agreements, and consider involving a legal professional if the situation escalates. -
Are there specific certifications required for vending machines in my region?
Yes, different regions may have specific certifications for vending machines, such as CE marking in Europe or safety certifications in the Middle East. Research the local regulations in your market to ensure compliance. Request that your supplier provides the necessary documentation and certifications to facilitate a smooth import process and avoid issues with local authorities.
Strategic Sourcing Conclusion and Outlook for pepsi vending machines
In conclusion, strategic sourcing plays a pivotal role in optimizing the procurement process for Pepsi vending machines, particularly for international B2B buyers in Africa, South America, the Middle East, and Europe. By leveraging data-driven insights, buyers can identify reliable suppliers, negotiate favorable terms, and ensure a steady supply of high-quality machines that meet local market demands.
Key takeaways include the importance of understanding regional market dynamics, evaluating total cost of ownership, and fostering strong relationships with suppliers to enhance service and support. As markets continue to evolve, the ability to adapt sourcing strategies will be crucial for maintaining a competitive edge.
Looking ahead, businesses are encouraged to invest in technology and analytics to improve decision-making processes and enhance operational efficiency. Now is the time to seize opportunities in the vending machine sector, ensuring that your supply chain is resilient and responsive to market changes. Engage with suppliers who align with your vision and values, and prepare to capitalize on emerging trends in consumer preferences and technology advancements.