Master Sourcing Mini Soda Vending Machines for Profitable
Guide to Mini Soda Vending Machines
- Introduction: Navigating the Global Market for mini soda vending machines
- Understanding mini soda vending machines Types and Variations
- Key Industrial Applications of mini soda vending machines
- Strategic Material Selection Guide for mini soda vending machines
- In-depth Look: Manufacturing Processes and Quality Assurance for mini soda vending machines
- Comprehensive Cost and Pricing Analysis for mini soda vending machines Sourcing
- Spotlight on Potential mini soda vending machines Manufacturers and Suppliers
- Essential Technical Properties and Trade Terminology for mini soda vending machines
- Navigating Market Dynamics, Sourcing Trends, and Sustainability in the mini soda vending machines Sector
- Frequently Asked Questions (FAQs) for B2B Buyers of mini soda vending machines
- Strategic Sourcing Conclusion and Outlook for mini soda vending machines
Introduction: Navigating the Global Market for mini soda vending machines
In today’s competitive landscape, mini soda vending machines have emerged as a vital asset for businesses looking to enhance customer experience and drive revenue. These compact machines not only offer convenience but also cater to diverse consumer preferences, making them essential in various settings—from busy urban centers in Europe to bustling markets in Africa and South America. As international B2B buyers, understanding the nuances of this market can significantly impact your sourcing decisions.
This comprehensive guide delves into the various aspects of mini soda vending machines, including their different types, materials, manufacturing processes, quality control standards, and leading suppliers. We will also explore pricing structures and market trends, providing you with a holistic view of the industry. By addressing frequently asked questions, this guide aims to empower buyers with the knowledge necessary to make informed decisions that align with their specific needs and regional market dynamics.
With insights tailored to the unique challenges faced by buyers in Africa, South America, the Middle East, and Europe, including key markets like Mexico and Kenya, you will gain a deeper understanding of how to leverage mini soda vending machines to enhance your business operations. This guide is not just a resource; it is a roadmap to strategic sourcing and profitable investments in the global vending machine market.
Understanding mini soda vending machines Types and Variations
Type Name | Key Distinguishing Features | Primary B2B Applications | Brief Pros & Cons for Buyers |
---|---|---|---|
Compact Floor Model | Space-efficient design, typically holds 200-300 cans | Offices, small retail outlets | Pros: Ideal for limited spaces; Cons: Limited product variety available. |
Wall-Mounted Vending Machine | Mounted on walls, saving floor space | Gyms, schools, hospitals | Pros: Frees up floor space; Cons: Installation may require wall reinforcements. |
Mini Tabletop Unit | Small countertop model, often with a glass front | Cafés, small restaurants | Pros: Attractive display; Cons: Lower capacity than larger models. |
Outdoor Weatherproof Model | Designed to withstand outdoor elements | Parks, recreational areas | Pros: Durable and weather-resistant; Cons: Higher initial investment. |
Touchscreen Interactive Model | Features a digital interface for user interaction | High-traffic venues, events | Pros: Engaging user experience; Cons: Higher maintenance costs due to tech. |
Compact Floor Model
The compact floor model is designed for environments where space is a premium. With a capacity to hold between 200 to 300 cans, these machines are perfect for offices and small retail outlets. When considering this model, buyers should evaluate the available floor space and the anticipated foot traffic to ensure it meets their needs. The primary advantage is its ability to fit into tight areas, but buyers may need to compromise on product variety.
Wall-Mounted Vending Machine
Wall-mounted vending machines are an excellent choice for locations such as gyms, schools, and hospitals where floor space is limited. These machines are affixed to walls, allowing for a streamlined setup that minimizes the footprint. Buyers should assess the structural integrity of the wall before installation, as it may require reinforcements. The key benefit is the efficient use of space, though potential installation challenges can be a drawback.
Mini Tabletop Unit
Mini tabletop units are designed to sit on countertops and are often visually appealing, featuring glass fronts that showcase the products. These machines are particularly suited for cafés and small restaurants, providing a convenient way to offer drinks to customers. When purchasing, businesses should consider the lower capacity, which may necessitate more frequent restocking. The attractive display can enhance customer engagement, but the limited capacity may hinder sales in high-demand situations.
Outdoor Weatherproof Model
For outdoor settings such as parks and recreational areas, weatherproof vending machines are essential. These models are built to withstand various environmental conditions, ensuring reliability and longevity. Businesses should weigh the higher initial investment against the potential for increased sales in outdoor venues. While these machines are durable and capable of generating revenue in outdoor settings, the upfront costs may deter some buyers.
Touchscreen Interactive Model
Touchscreen interactive models are designed for high-traffic venues and events, offering an engaging user experience through digital interfaces. This modern technology can attract customers and streamline the purchasing process. Buyers should consider the higher maintenance costs associated with technology and the need for regular updates. While these machines can enhance customer engagement and sales, they require a commitment to ongoing support and maintenance.
Related Video: DIY Mini Vending Machine
Key Industrial Applications of mini soda vending machines
Industry/Sector | Specific Application of mini soda vending machines | Value/Benefit for the Business | Key Sourcing Considerations for this Application |
---|---|---|---|
Corporate Offices | Employee refreshment stations | Increases employee satisfaction and productivity | Size, energy efficiency, payment options |
Educational Institutions | Campus beverage services | Provides convenient access to refreshments for students | Durability, ease of use, product variety |
Healthcare Facilities | Patient and visitor refreshment kiosks | Enhances visitor experience and patient comfort | Hygiene standards, accessibility, compact design |
Transportation Hubs | Vending at airports and bus stations | Reduces wait times and improves traveler convenience | Reliability, payment methods, product stocking capacity |
Retail Environments | Pop-up soda vending at events and festivals | Attracts customers and increases sales opportunities | Portability, branding options, ease of restocking |
Corporate Offices
Mini soda vending machines are increasingly being integrated into corporate environments as refreshment stations. By providing employees with easy access to beverages, companies can boost morale and productivity. International buyers should consider the energy efficiency of these machines, as well as their size to fit within office layouts. Additionally, payment options should cater to a diverse workforce, including cashless methods.
Educational Institutions
In schools and universities, mini soda vending machines serve as convenient beverage services for students. They help to keep students hydrated and energized throughout the day, thereby supporting academic performance. Buyers in this sector must prioritize durability and ease of use, ensuring that machines can withstand high traffic and provide a variety of drink options to cater to diverse preferences.
Healthcare Facilities
In healthcare settings, mini soda vending machines are placed strategically in waiting areas for patients and visitors. They enhance the overall experience by offering quick access to refreshments, which can be particularly comforting during stressful visits. Buyers from this sector should focus on hygiene standards and accessibility features, ensuring that machines are easy to clean and usable by individuals with varying physical abilities.
Transportation Hubs
Airports and bus stations are prime locations for mini soda vending machines, providing quick refreshment options for travelers on the go. These machines help reduce wait times and enhance the convenience of travel, catering to a fast-paced environment. Key considerations for sourcing in this sector include reliability and payment methods that accommodate international travelers, as well as the machine’s capacity to handle high demand.
Retail Environments
At events and festivals, mini soda vending machines can serve as pop-up refreshment points, attracting customers and increasing sales. They provide an innovative way to enhance the customer experience while generating additional revenue streams. When sourcing for this application, businesses should consider the portability of the machines, branding options to align with event themes, and the ease of restocking to ensure continuous service.
Strategic Material Selection Guide for mini soda vending machines
When selecting materials for mini soda vending machines, it is essential to consider their properties, advantages, disadvantages, and the specific needs of international markets, particularly in Africa, South America, the Middle East, and Europe. Below, we analyze four common materials used in the construction of these machines.
1. Stainless Steel
Key Properties:
Stainless steel is known for its excellent corrosion resistance, high strength, and ability to withstand high temperatures and pressures. It typically has a temperature rating of up to 800°F (427°C), making it suitable for various environments.
Pros & Cons:
The primary advantages of stainless steel include its durability, aesthetic appeal, and ease of cleaning, which is crucial for hygiene in food and beverage applications. However, it is more expensive than other materials and can be challenging to fabricate due to its hardness.
Impact on Application:
Stainless steel is compatible with carbonated beverages and can withstand the pressures associated with soda dispensing. Its resistance to rust and staining makes it ideal for outdoor installations in humid or coastal environments.
Considerations for International Buyers:
Buyers should be aware of compliance with international standards such as ASTM and ISO for food safety. In regions like Africa and South America, where corrosion resistance is critical due to environmental factors, stainless steel is often preferred despite its higher cost.
2. Aluminum
Key Properties:
Aluminum is lightweight, has good corrosion resistance, and can be easily extruded into various shapes. It typically has a melting point of around 1,221°F (660°C) and is suitable for moderate temperature applications.
Pros & Cons:
Aluminum’s main advantages include its lightweight nature, which reduces shipping costs, and its lower price compared to stainless steel. However, it is less durable and can be prone to denting and scratching, which may affect the machine’s longevity.
Impact on Application:
Aluminum is suitable for vending machines that require mobility or frequent relocation. However, it may not be ideal for high-pressure applications without additional reinforcement.
Considerations for International Buyers:
Buyers should consider the availability of aluminum in their region and any specific local regulations regarding aluminum use in food and beverage applications. Standards such as ANSI and ASTM are relevant for ensuring quality.
3. Polycarbonate
Key Properties:
Polycarbonate is a strong thermoplastic with excellent impact resistance and clarity. It can withstand temperatures up to 240°F (115°C) and is UV resistant, making it suitable for outdoor applications.
Pros & Cons:
The primary advantage of polycarbonate is its lightweight nature and high impact resistance, which is ideal for areas with high foot traffic. However, it is less resistant to scratches and may yellow over time when exposed to UV light.
Impact on Application:
Polycarbonate is often used for the transparent panels of vending machines, allowing visibility of the products inside. Its ability to withstand impact makes it suitable for high-traffic areas.
Considerations for International Buyers:
Buyers should ensure that the polycarbonate used complies with safety standards for food contact, such as those set by the FDA or EFSA. In regions with high UV exposure, selecting UV-stabilized grades is essential.
4. Mild Steel with Protective Coating
Key Properties:
Mild steel is a low-cost material with good strength and formability. When coated with protective finishes (like powder coating), it can achieve moderate corrosion resistance.
Pros & Cons:
The advantages of mild steel include its low cost and ease of fabrication. However, without adequate protection, it is susceptible to rust and corrosion, which can limit its lifespan in humid environments.
Impact on Application:
Mild steel is often used in structural components of vending machines. The protective coating can enhance its durability, but buyers must ensure that the coating is suitable for food contact applications.
Considerations for International Buyers:
Buyers should be mindful of the coating standards and certifications required in their region. In climates with high humidity or salt exposure, additional protective measures may be necessary.
Summary Table
Material | Typical Use Case for mini soda vending machines | Key Advantage | Key Disadvantage/Limitation | Relative Cost (Low/Med/High) |
---|---|---|---|---|
Stainless Steel | Structural and exterior components | Excellent corrosion resistance | Higher cost, difficult to fabricate | High |
Aluminum | Lightweight, mobile vending machines | Lightweight and lower cost | Less durable, prone to dents | Medium |
Polycarbonate | Transparent panels for product visibility | High impact resistance | Scratches easily, UV degradation | Medium |
Mild Steel with Protective Coating | Structural components | Low cost and easy to fabricate | Susceptible to corrosion without protection | Low |
This guide provides B2B buyers with actionable insights into the strategic selection of materials for mini soda vending machines, ensuring they can make informed decisions tailored to their specific market needs.
In-depth Look: Manufacturing Processes and Quality Assurance for mini soda vending machines
The manufacturing of mini soda vending machines involves a series of meticulous processes designed to ensure product quality, functionality, and compliance with international standards. For international B2B buyers, particularly those from Africa, South America, the Middle East, and Europe, understanding these processes can be crucial in selecting reliable suppliers. This section outlines the typical manufacturing stages, quality assurance protocols, and how buyers can verify supplier quality controls.
Manufacturing Processes
-
Material Preparation
– Material Sourcing: The first step involves sourcing high-quality materials, such as stainless steel for the exterior, plastic for the internal components, and electronic parts for the control system. Buyers should ensure that suppliers use certified materials that comply with international safety standards.
– Material Testing: Before use, materials undergo testing for durability and resistance to corrosion, ensuring they can withstand various environmental conditions. -
Forming
– Cutting and Shaping: Using advanced CNC (Computer Numerical Control) machines, raw materials are cut and shaped into components like panels, doors, and frames. Precision in this stage is crucial to ensure that all parts fit together seamlessly during assembly.
– Injection Molding: For plastic components, injection molding techniques are employed to create complex shapes that are lightweight yet robust. -
Assembly
– Component Assembly: Skilled technicians assemble the various components, including the vending mechanism, refrigeration unit, and electronic control systems. This stage often involves using automated assembly lines to enhance efficiency.
– Integration of Systems: The integration of electronic systems for payment processing and inventory management is performed at this stage. Ensuring compatibility among components is critical for the machine’s overall functionality. -
Finishing
– Surface Treatment: The machines undergo surface treatments such as painting or powder coating to enhance aesthetics and protect against wear and tear.
– Final Assembly: In this stage, all final components are assembled, including touch screens, coin mechanisms, and branding elements. Attention to detail is vital to ensure the final product meets design specifications.
Quality Assurance
Quality assurance is integral to the manufacturing process, ensuring that each machine meets both regulatory and customer expectations. Key quality standards and checkpoints include:
-
International Standards
– ISO 9001: This standard focuses on quality management systems, emphasizing consistent product quality and customer satisfaction. Buyers should confirm that their suppliers are ISO 9001 certified.
– CE Marking: For machines sold within Europe, CE marking indicates compliance with EU safety, health, and environmental protection standards. -
Industry-Specific Standards
– API (American Petroleum Institute): While primarily for oil and gas, certain principles may apply to vending machine components that involve energy efficiency and safety.
– Local Certifications: Depending on the region, additional certifications may be necessary. For instance, buyers in Africa or South America should check for local compliance to ensure market acceptance. -
Quality Control Checkpoints
– Incoming Quality Control (IQC): Inspects raw materials upon delivery to ensure they meet specified standards.
– In-Process Quality Control (IPQC): Conducted during the assembly process to identify and rectify any defects early.
– Final Quality Control (FQC): A thorough examination of the completed machines, including functionality tests, to confirm they operate as intended. -
Testing Methods
– Functional Testing: Each machine is tested for operational efficiency, including the vending mechanism and electronic systems.
– Durability Testing: Machines are subjected to stress tests to simulate real-world usage conditions, ensuring longevity and reliability.
– Safety Testing: Compliance with electrical safety standards is verified through rigorous testing procedures.
Verifying Supplier Quality Control
B2B buyers can take several steps to ensure their suppliers maintain high-quality standards:
-
Supplier Audits
– Conducting on-site audits of manufacturing facilities can provide insight into the supplier’s processes, equipment, and adherence to quality standards. This hands-on approach allows buyers to assess the environment in which their products are made. -
Quality Reports
– Requesting regular quality reports from suppliers can help track compliance with agreed-upon standards. These reports should detail any issues encountered during manufacturing and corrective measures taken. -
Third-Party Inspections
– Engaging third-party inspection agencies can provide an unbiased evaluation of the manufacturing processes and final products. This can be particularly useful for buyers in regions with varying regulatory standards. -
Certification Verification
– Buyers should verify the authenticity of any certifications claimed by suppliers. This can often be done through the issuing organizations or regulatory bodies.
Conclusion
Understanding the manufacturing processes and quality assurance protocols for mini soda vending machines is essential for international B2B buyers. By focusing on material preparation, forming, assembly, and finishing, along with adhering to international quality standards, buyers can make informed decisions when selecting suppliers. Implementing thorough verification methods further ensures that the chosen suppliers can deliver high-quality products that meet both market and regulatory demands.
Related Video: Amazing coca cola manufacturing line – Inside the soft drink factory – Filling Machine
Comprehensive Cost and Pricing Analysis for mini soda vending machines Sourcing
Understanding Cost Structure for Mini Soda Vending Machines
When sourcing mini soda vending machines, understanding the comprehensive cost structure is critical for international B2B buyers. The main components of the cost structure include:
-
Materials: The choice of materials significantly impacts the overall cost. Common materials for vending machines include steel, glass, and electronic components. High-quality materials may increase initial costs but can lead to lower maintenance expenses and longer machine life.
-
Labor: Labor costs vary widely by region and can affect both manufacturing and assembly. In markets like Africa and South America, labor may be less expensive than in Europe or the Middle East, but this can also impact the quality of craftsmanship.
-
Manufacturing Overhead: This includes utilities, rent, and administrative expenses related to production. Efficient manufacturing processes can help minimize these costs.
-
Tooling: Customization often requires specialized tooling, which can add to initial costs. Consider the potential need for molds or fixtures for specific machine designs.
-
Quality Control (QC): Implementing stringent QC measures ensures product reliability but can increase costs. Investing in quality can reduce long-term expenses related to repairs and replacements.
-
Logistics: Shipping costs can fluctuate based on the distance, weight, and size of the machines. Buyers should consider local suppliers to reduce logistics expenses.
-
Margin: Suppliers typically add a profit margin to their costs. Understanding the supplier’s pricing strategy can aid in negotiations.
Influencing Factors on Pricing
Several factors can influence the pricing of mini soda vending machines:
-
Volume/MOQ: Ordering in larger quantities can lead to significant discounts. Establishing long-term relationships with suppliers may also yield better pricing.
-
Specifications/Customization: Custom features (like branding or unique functionalities) can increase costs. Buyers should assess the necessity of customization against budget constraints.
-
Materials Quality/Certifications: Machines that meet international standards or specific certifications may carry a premium price. However, these certifications can enhance the machine’s reliability and marketability.
-
Supplier Factors: The reputation and reliability of the supplier play a crucial role. Established suppliers may charge more but often provide better support and warranty terms.
-
Incoterms: Understanding Incoterms is essential for international buyers, as they define the responsibilities of buyers and sellers in shipping and logistics, affecting overall cost.
Buyer Tips for Cost-Efficiency
To optimize sourcing for mini soda vending machines, consider the following strategies:
-
Negotiation: Engage in discussions with suppliers to explore flexible pricing options based on volume or long-term contracts. Transparency in your purchasing intentions can foster better deals.
-
Total Cost of Ownership (TCO): Evaluate not just the purchase price but also the long-term costs associated with maintenance, operation, and energy consumption. A slightly higher initial investment may lead to lower operational costs over time.
-
Pricing Nuances: Be aware that prices can vary significantly based on the region. For instance, machines sourced from Europe may include higher labor and regulatory costs compared to those from regions like Asia or Latin America.
-
Cultural and Regional Considerations: Understanding local market dynamics in regions like Africa or South America can provide leverage in negotiations. Tailor your approach based on regional practices and supplier expectations.
Disclaimer
The prices mentioned in this analysis are indicative and may vary based on market conditions, supplier negotiations, and specific buyer requirements. Always conduct thorough research and obtain multiple quotes to ensure competitive pricing.
Spotlight on Potential mini soda vending machines Manufacturers and Suppliers
This section offers a look at a few manufacturers active in the ‘mini soda vending machines’ market. This is a representative sample for illustrative purposes; B2B buyers must conduct their own extensive due diligence before any engagement. Information is synthesized from public sources and general industry knowledge.
Essential Technical Properties and Trade Terminology for mini soda vending machines
Key Technical Properties of Mini Soda Vending Machines
When considering mini soda vending machines, several technical specifications are crucial for international B2B buyers. Understanding these properties not only facilitates better purchasing decisions but also ensures that the machines meet operational requirements.
-
Material Grade
The construction material of vending machines is typically stainless steel or high-grade plastic. Stainless steel offers durability and resistance to corrosion, making it suitable for various environments, especially in humid regions like parts of Africa and South America. High-grade plastics can reduce weight and cost while providing sufficient strength. Buyers should assess the material grade to ensure longevity and reliability in different climates. -
Power Consumption
Power consumption is a critical specification, as it directly impacts operational costs. Mini soda vending machines generally have a power rating of 100 to 500 watts. Buyers need to consider energy-efficient models to minimize electricity expenses, particularly in regions where energy costs are high or supply is inconsistent. -
Temperature Control Range
The ability to maintain a consistent temperature is vital for preserving the quality of beverages. Most mini soda vending machines operate effectively within a temperature range of 2°C to 10°C. Understanding this specification helps buyers ensure that the machine can adequately serve their target markets, especially in warmer climates. -
Capacity
Capacity refers to the number of products the vending machine can hold, typically measured in liters or the number of cans/bottles. A standard mini soda vending machine may hold between 200 to 400 cans. Buyers should choose a model that aligns with their expected sales volume and customer traffic to avoid frequent restocking. -
Payment Options
Modern vending machines often support multiple payment methods, including cash, credit/debit cards, and mobile payments. This feature is essential for maximizing convenience for consumers and can influence purchasing decisions. Buyers should ensure that the vending machines they select are compatible with the payment systems preferred in their target markets. -
Dimensions and Weight
The size and weight of the machine affect installation and placement. Mini soda vending machines typically range from 1.5 to 2 meters in height and weigh between 50 to 150 kg. Buyers must consider these factors to ensure compatibility with their intended locations, especially in spaces with limited room.
Industry Trade Terminology
Understanding key trade terms is essential for navigating the purchasing process for mini soda vending machines. Here are some common jargon and their meanings:
- OEM (Original Equipment Manufacturer)
This term refers to companies that manufacture products that are sold under another company’s brand. Buyers should look for OEMs that provide high-quality machines, as this can often ensure better reliability and service support.
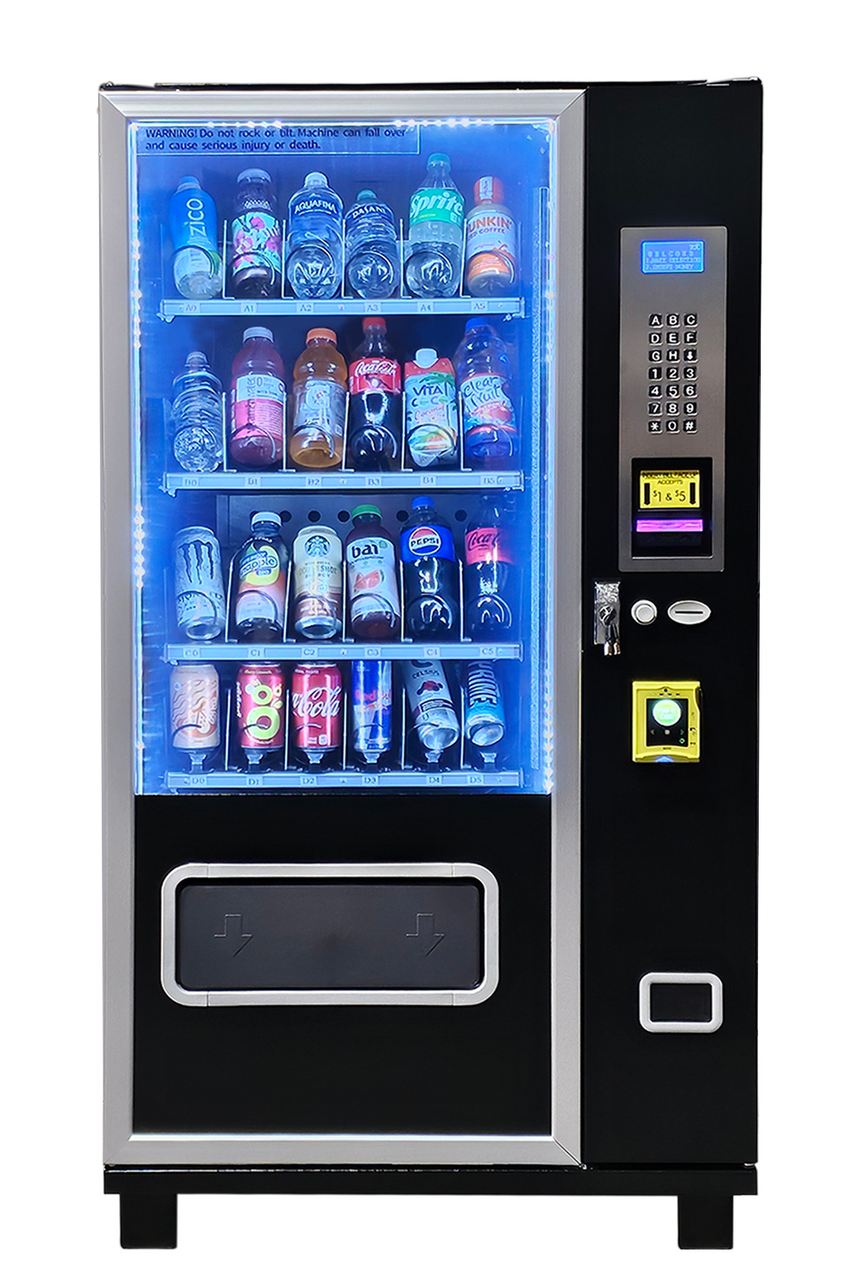
Illustrative Image (Source: Google Search)
-
MOQ (Minimum Order Quantity)
MOQ indicates the smallest number of units a supplier is willing to sell. This is crucial for buyers to understand to manage inventory effectively and negotiate better pricing, especially when purchasing in bulk. -
RFQ (Request for Quotation)
An RFQ is a document sent to suppliers to solicit pricing and terms for specific goods or services. For buyers, issuing an RFQ can help gather comparative quotes and negotiate the best deal for mini soda vending machines. -
Incoterms (International Commercial Terms)
These are standardized terms used in international trade to define the responsibilities of buyers and sellers in shipping. Understanding Incoterms helps buyers clarify who is responsible for costs, risks, and insurance during transportation. -
Lead Time
Lead time refers to the time taken from placing an order until the product is delivered. Buyers must factor in lead times when planning inventory and sales strategies to ensure they meet customer demand without delays. -
Warranty Period
This term indicates the duration during which the manufacturer guarantees the product against defects. A longer warranty period can provide buyers with peace of mind regarding the quality and reliability of their investment in vending machines.
By familiarizing themselves with these technical properties and trade terminology, international B2B buyers can make informed decisions that enhance their operational efficiency and profitability in the vending machine market.
Navigating Market Dynamics, Sourcing Trends, and Sustainability in the mini soda vending machines Sector
Market Overview & Key Trends
The mini soda vending machines sector is experiencing a surge driven by several global trends. Increasing urbanization, particularly in regions like Africa and South America, is propelling demand for convenient and efficient beverage solutions. As cities expand, the need for accessible refreshment options in high-traffic areas such as schools, offices, and public transport hubs is becoming crucial.
Technological advancements are reshaping the landscape as well. Innovations in cashless payment systems, remote monitoring, and IoT-enabled machines are enhancing operational efficiency and customer experience. International B2B buyers should consider sourcing machines equipped with these technologies, as they offer improved inventory management and customer engagement.
Emerging markets, especially in Kenya and Mexico, are witnessing a shift toward healthier beverage options, prompting manufacturers to adapt their offerings. This trend aligns with global health movements, where consumers are increasingly seeking lower-calorie and organic drinks. Consequently, suppliers must stay ahead by incorporating diverse product lines into their vending solutions to meet evolving consumer preferences.
Furthermore, sustainability is becoming a focal point in sourcing strategies. Companies are increasingly scrutinizing the environmental impact of their supply chains. For buyers, understanding these dynamics is essential for making informed purchasing decisions that align with both market demand and corporate social responsibility initiatives.
Sustainability & Ethical Sourcing in B2B
Sustainability is a key consideration for international buyers in the mini soda vending machine market. The environmental impact of traditional vending machines, particularly concerning energy consumption and waste generation, necessitates a shift towards more sustainable practices. Buyers should prioritize machines that utilize energy-efficient technologies, such as LED lighting and low-energy refrigeration systems, to minimize their carbon footprint.
Moreover, ethical sourcing of materials is gaining traction. Manufacturers are encouraged to adopt responsible supply chain practices, ensuring that components are sourced from suppliers who adhere to sustainable and ethical standards. This includes using recyclable materials for machine construction and packaging, which not only reduces waste but also appeals to environmentally conscious consumers.
Buyers should also look for certifications such as ENERGY STAR and ISO 14001, which indicate a commitment to sustainability and environmental management. These certifications can enhance brand reputation and foster trust among consumers who are increasingly making purchasing decisions based on environmental considerations.
Brief Evolution/History
The mini soda vending machine has evolved significantly since its inception in the early 20th century. Originally simple mechanical devices, these machines have transformed into sophisticated, technology-driven solutions. The integration of electronic payment systems in the 1980s marked a pivotal shift, increasing convenience for consumers.
In recent years, the introduction of IoT capabilities has revolutionized the sector, allowing for real-time inventory tracking and remote machine management. This evolution has made mini soda vending machines not only a source of revenue but also a vital part of the retail ecosystem, capable of providing valuable data insights to operators. As this trend continues, B2B buyers must stay informed about technological advancements to remain competitive in the market.
Related Video: Incoterms for beginners | Global Trade Explained
Frequently Asked Questions (FAQs) for B2B Buyers of mini soda vending machines
-
What should I consider when vetting suppliers for mini soda vending machines?
When vetting suppliers, prioritize their experience in the vending machine industry and check for customer testimonials. Verify their manufacturing capabilities and quality control processes. Additionally, assess their compliance with local regulations and international standards, particularly in your target market. Conduct a factory visit, if possible, or request product samples to evaluate quality firsthand. Ensure they have a reliable supply chain to prevent disruptions. -
Can I customize the mini soda vending machines to fit my brand?
Yes, most manufacturers offer customization options. You can often choose the color, branding, and even the machine’s layout to cater to your specific market needs. Discuss your requirements early in the negotiation process to understand the available options and potential costs. Ensure that the customization aligns with local consumer preferences and cultural nuances to enhance market acceptance. -
What are the typical minimum order quantities (MOQ) and lead times for these machines?
MOQs can vary significantly between suppliers, often ranging from 10 to 100 units for custom orders. Standard models may have lower MOQs. Lead times typically range from 4 to 12 weeks, depending on customization and the supplier’s production capacity. Always confirm these details upfront and consider building in extra time for potential delays, especially when importing to countries with complex customs processes. -
What payment terms are commonly accepted when purchasing vending machines internationally?
Payment terms can vary by supplier, but common practices include a deposit (often 30-50%) upfront, with the balance due before shipment or upon delivery. Some suppliers may offer letter of credit options, which provide security for both parties. Always clarify payment methods and terms early to avoid misunderstandings. Be cautious of suppliers who demand full payment upfront without established credibility. -
What quality assurance measures should I look for in vending machines?
Ensure the supplier has robust quality assurance (QA) processes in place, including ISO certifications or equivalent. Ask for documentation on product testing and quality control procedures. It’s beneficial to request a quality inspection report for your machines before shipment. Familiarize yourself with the warranty policies to protect your investment against defects or malfunctions. -
How can I handle logistics for importing mini soda vending machines?
Partnering with a reliable logistics provider experienced in international shipping is crucial. They can assist with customs clearance, duties, and local regulations in your destination country. Understand the shipping terms (Incoterms) used in your agreement, as they define responsibility for costs and risks. Plan for potential delays in transit and consider insurance to safeguard against loss or damage during shipping. -
What steps can I take if a dispute arises with my supplier?
Establish clear communication channels and documentation from the outset to facilitate dispute resolution. In the event of a disagreement, attempt to resolve issues amicably through direct negotiation. If necessary, refer to the contract clauses regarding dispute resolution, which may include mediation or arbitration. Having an attorney familiar with international trade can help navigate legal complexities if the situation escalates. -
Are there specific certifications I should look for in mini soda vending machines?
Yes, look for certifications relevant to safety and quality, such as CE marking for European markets, UL certification in the U.S., or local certifications applicable in your region. These certifications indicate compliance with industry standards and regulations, ensuring the machines are safe for consumer use. Request documentation from your supplier to verify these certifications before proceeding with your order.
Strategic Sourcing Conclusion and Outlook for mini soda vending machines
In conclusion, the strategic sourcing of mini soda vending machines presents a lucrative opportunity for international B2B buyers, particularly in emerging markets across Africa, South America, the Middle East, and Europe. By leveraging local insights and market trends, buyers can identify suppliers who not only meet quality standards but also offer competitive pricing and innovative technology.
Key takeaways for B2B buyers include:
- Market Adaptation: Understand regional preferences and consumption habits to tailor offerings effectively. This increases customer satisfaction and potential sales.
- Supplier Relationships: Building strong partnerships with manufacturers can lead to better pricing, priority access to new products, and enhanced support.
- Sustainability Focus: Consider suppliers that prioritize eco-friendly practices and energy-efficient machines, aligning with global sustainability trends.
As the demand for convenient beverage solutions continues to grow, now is the time to invest in mini soda vending machines. By strategically sourcing these machines, businesses can enhance their service offerings and tap into new revenue streams. Seize this opportunity to elevate your business portfolio and meet the evolving needs of consumers in your region.
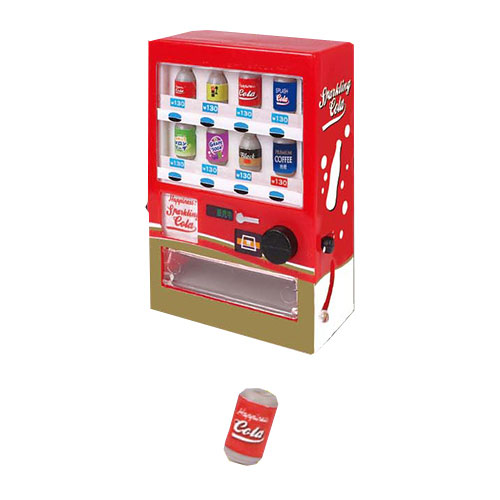
Illustrative Image (Source: Google Search)