Master Sourcing Mini Candy Vending Machines for Maximum
Guide to Mini Candy Vending Machine
- Introduction: Navigating the Global Market for mini candy vending machine
- Understanding mini candy vending machine Types and Variations
- Key Industrial Applications of mini candy vending machine
- Strategic Material Selection Guide for mini candy vending machine
- In-depth Look: Manufacturing Processes and Quality Assurance for mini candy vending machine
- Comprehensive Cost and Pricing Analysis for mini candy vending machine Sourcing
- Spotlight on Potential mini candy vending machine Manufacturers and Suppliers
- Essential Technical Properties and Trade Terminology for mini candy vending machine
- Navigating Market Dynamics, Sourcing Trends, and Sustainability in the mini candy vending machine Sector
- Frequently Asked Questions (FAQs) for B2B Buyers of mini candy vending machine
- Strategic Sourcing Conclusion and Outlook for mini candy vending machine
Introduction: Navigating the Global Market for mini candy vending machine
In an increasingly competitive global marketplace, the mini candy vending machine has emerged as a vital asset for businesses looking to enhance customer engagement and drive additional revenue streams. These compact, versatile machines cater to the growing demand for convenience and instant gratification among consumers, making them an attractive investment for various sectors, including retail, hospitality, and entertainment. For international B2B buyers, particularly those operating in Africa, South America, the Middle East, and Europe, understanding the nuances of this market is essential for making informed sourcing decisions.
This comprehensive guide delves into the diverse types of mini candy vending machines available, from traditional mechanical models to modern digital versions equipped with cashless payment systems. It explores the materials and manufacturing processes that impact durability and functionality, along with quality control measures to ensure product reliability. Furthermore, it highlights key suppliers, pricing strategies, and market trends that can influence purchasing decisions.
By equipping B2B buyers with actionable insights and answers to frequently asked questions, this guide empowers them to navigate the complexities of sourcing mini candy vending machines effectively. With the right knowledge, businesses can leverage these machines to meet consumer demands and enhance their operational efficiency, ultimately positioning themselves for success in a dynamic global market.
Understanding mini candy vending machine Types and Variations
Type Name | Key Distinguishing Features | Primary B2B Applications | Brief Pros & Cons for Buyers |
---|---|---|---|
Gravity Feed Vending Machine | Simple design utilizing gravity to dispense items | Schools, offices, and events | Pros: Low maintenance, easy restocking. Cons: Limited item variety. |
Spiral Vending Machine | Items stored in spiral racks, allowing visibility | Retail locations, entertainment | Pros: High product visibility, diverse product range. Cons: Higher initial cost. |
Bulk Candy Dispenser | Dispenses candy in bulk, allowing customization | Confectionery shops, fairs | Pros: Cost-effective for high sales volume. Cons: Requires more space. |
Electronic Vending Machine | Digital interface with cashless payment options | Modern retail, convenience stores | Pros: User-friendly, tracks inventory automatically. Cons: Higher maintenance costs. |
Combination Vending Machine | Combines snacks and drinks with candy options | Gym facilities, schools | Pros: Versatile product offering, maximizes space. Cons: Complexity in stock management. |
Gravity Feed Vending Machine
Gravity feed vending machines are the simplest form of mini candy vending machines. They operate on a gravity-based dispensing mechanism where items are placed in a vertical column and drop down as the customer makes a selection. These machines are particularly suitable for environments like schools and offices where ease of use and low maintenance are priorities. When considering this type, buyers should evaluate the frequency of use and the types of candy offered, as the limited variety may not cater to all customer preferences.
Spiral Vending Machine
Spiral vending machines feature a design where items are arranged in spiral racks, making them highly visible to customers. This type is often found in retail locations and entertainment venues. The visibility of products can lead to increased impulse purchases, making it an attractive option for B2B buyers looking to maximize sales. However, the higher initial cost and the need for ongoing maintenance should be factored into purchasing decisions.
Bulk Candy Dispenser
Bulk candy dispensers allow customers to fill their own bags or containers with candy, promoting a customizable experience. This type is ideal for confectionery shops and fairs where high volume sales are expected. While they offer cost-effectiveness, particularly for businesses with high turnover, buyers should consider the space requirements and the need for regular refilling to ensure product availability.
Electronic Vending Machine
Electronic vending machines incorporate advanced technology, including digital interfaces and cashless payment options. These machines are particularly suited for modern retail environments and convenience stores, where a seamless customer experience is paramount. The ability to track inventory in real-time can significantly benefit businesses, although buyers must weigh the higher maintenance costs against the potential for increased sales and customer satisfaction.
Combination Vending Machine
Combination vending machines provide a diverse offering by integrating candy, snacks, and beverages in one unit. This versatility makes them ideal for gym facilities and schools, where customers may seek various products in a single transaction. While they maximize space efficiency, buyers should be aware of the complexities involved in managing stock across different product types, which can impact operational efficiency.
Related Video: DIY Mini Candy Vending Machine from Paper – Actually Works!
Key Industrial Applications of mini candy vending machine
Industry/Sector | Specific Application of mini candy vending machine | Value/Benefit for the Business | Key Sourcing Considerations for this Application |
---|---|---|---|
Retail | Point-of-sale impulse buy locations | Increases customer engagement and boosts sales | Size, product capacity, payment options |
Education | School cafeterias and common areas | Provides convenient snack options for students | Health and safety standards, product variety |
Hospitality | Hotel lobbies and waiting areas | Enhances guest experience with quick snack availability | Aesthetic design, ease of maintenance, product range |
Healthcare | Hospitals and clinics’ waiting rooms | Offers quick snacks for patients and visitors | Compliance with health regulations, product freshness |
Corporate Offices | Break rooms and employee lounges | Improves employee satisfaction and productivity | Reliability, ease of restocking, payment methods |
Retail Sector
In retail environments, mini candy vending machines serve as effective point-of-sale impulse buy locations. They attract customers with their colorful displays and convenient access to snacks. Retailers can benefit from increased sales, especially during peak shopping times. International buyers should consider the machine’s size and product capacity to fit within their store layouts, as well as the payment options available to cater to diverse customer preferences.
Education Sector
In educational institutions, mini candy vending machines are commonly placed in cafeterias and common areas, providing students with easy access to snacks. This application addresses the need for quick and convenient food options, particularly during busy school hours. Buyers in this sector should prioritize compliance with health and safety standards and seek machines that offer a variety of healthy snacks, aligning with contemporary dietary trends.
Hospitality Sector
Within the hospitality industry, mini candy vending machines can enhance guest experiences in hotel lobbies and waiting areas. By offering quick snack options, hotels can keep guests satisfied while they wait for check-in or other services. Buyers should focus on the aesthetic design of the machines to match the hotel’s branding, as well as ensuring ease of maintenance to keep operations smooth and efficient.
Healthcare Sector
In healthcare settings, such as hospitals and clinics, mini candy vending machines are strategically placed in waiting rooms to provide quick snacks for patients and visitors. This application helps alleviate hunger during long wait times, improving the overall experience. Buyers in the healthcare sector must ensure that vending machines comply with health regulations and prioritize product freshness to maintain high standards of service.
Corporate Offices
Corporate offices utilize mini candy vending machines in break rooms and employee lounges to improve employee satisfaction and productivity. These machines offer a convenient way for employees to grab a snack during breaks, contributing to a positive work environment. When sourcing for this application, businesses should consider the reliability of the machines, ease of restocking, and the variety of payment methods accepted to accommodate a diverse workforce.
Related Video: How To Make Money Operated Candy Machine | Easy Cardboard Gumball Vending Machine +FREE TEMPLATE
Strategic Material Selection Guide for mini candy vending machine
When selecting materials for mini candy vending machines, it is crucial to consider properties that affect performance, durability, and cost. The following analysis covers four common materials used in the construction of these machines, focusing on their key properties, advantages, disadvantages, and specific considerations for international B2B buyers.
1. Stainless Steel
Key Properties:
Stainless steel is known for its excellent corrosion resistance and high strength. It can withstand a wide range of temperatures and is durable in various environments.
Pros & Cons:
The durability of stainless steel makes it a preferred choice for vending machines, as it can handle frequent use without significant wear. However, it is more expensive than other materials, which could impact overall production costs. Manufacturing complexity is moderate, as it requires specialized tools for cutting and welding.
Impact on Application:
Stainless steel is compatible with a variety of media, including sugary products, due to its non-reactive nature. This makes it ideal for candy vending machines, where hygiene is paramount.
Considerations for International Buyers:
Buyers from regions like Europe and the Middle East should ensure compliance with local food safety standards, such as the EU’s regulations on materials in contact with food. Common standards like ASTM A240 for stainless steel can also guide material selection.
2. Polycarbonate
Key Properties:
Polycarbonate is a lightweight, high-impact plastic that offers good transparency and UV resistance. It can withstand temperatures up to approximately 120°C.
Pros & Cons:
The primary advantage of polycarbonate is its lightweight nature, which reduces shipping costs and makes installation easier. However, it is less durable than metals and can scratch easily, which may affect the machine’s appearance over time.
Impact on Application:
Polycarbonate is suitable for transparent panels in vending machines, allowing customers to view the products inside. Its chemical resistance is adequate for most candy types but may not be suitable for all food products.
Considerations for International Buyers:
International buyers should be aware of the varying regulations regarding plastics in food applications, particularly in Africa and South America. Compliance with standards like FDA regulations in the U.S. or REACH in Europe is essential.
3. Aluminum
Key Properties:
Aluminum is lightweight, corrosion-resistant, and has good thermal conductivity. It can be easily machined and formed into complex shapes.
Pros & Cons:
Aluminum offers a good balance between strength and weight, making it a cost-effective option for vending machines. However, it is not as strong as stainless steel and can be prone to denting and scratching.
Impact on Application:
Aluminum is suitable for structural components and housing of vending machines, but care must be taken to ensure it is adequately protected from corrosion, especially in humid environments.
Considerations for International Buyers:
Buyers should consider the local availability of aluminum and its alloys, as well as compliance with international standards such as ASTM B221. In regions with high humidity, additional protective coatings may be necessary.
4. Mild Steel
Key Properties:
Mild steel is a low-carbon steel known for its good weldability and machinability. It has moderate strength and is more susceptible to corrosion than stainless steel.
Pros & Cons:
Mild steel is one of the most cost-effective materials available, making it attractive for budget-conscious buyers. However, its susceptibility to rust means it requires protective coatings, which can add to long-term maintenance costs.
Impact on Application:
Mild steel can be used for structural components but is not ideal for parts that come into direct contact with food unless properly coated.
Considerations for International Buyers:
Buyers should ensure that any coatings used are compliant with food safety standards. In regions like Africa and South America, where humidity can be high, additional protective measures may be necessary.
Material | Typical Use Case for mini candy vending machine | Key Advantage | Key Disadvantage/Limitation | Relative Cost (Low/Med/High) |
---|---|---|---|---|
Stainless Steel | Structural components, exterior panels | Excellent corrosion resistance | Higher cost compared to other materials | High |
Polycarbonate | Transparent panels for product visibility | Lightweight and easy to install | Scratches easily, less durable | Medium |
Aluminum | Structural components and housing | Good strength-to-weight ratio | Prone to denting, requires corrosion protection | Medium |
Mild Steel | Structural components | Cost-effective | Susceptible to rust, requires protective coating | Low |
This strategic material selection guide provides a comprehensive overview for international B2B buyers, helping them make informed decisions based on performance, cost, and compliance with relevant standards.
In-depth Look: Manufacturing Processes and Quality Assurance for mini candy vending machine
The manufacturing process of mini candy vending machines involves several critical stages that ensure the machines are produced efficiently and meet the required quality standards. Understanding these stages, alongside the quality assurance protocols, is essential for international B2B buyers, particularly those from Africa, South America, the Middle East, and Europe.
Manufacturing Processes
1. Material Preparation
The first step in manufacturing mini candy vending machines is the preparation of raw materials. Common materials include:
- Metal Components: Steel or aluminum for the machine’s frame and structure.
- Plastic Parts: High-density polyethylene (HDPE) or polycarbonate for the vending compartment and display.
- Electrical Components: Wiring, motors, and payment processing systems.
Manufacturers often source materials from local suppliers to reduce costs and lead times. Buyers should assess the quality of materials used, as this directly impacts the machine’s durability and performance.
2. Forming
Once materials are prepared, they undergo various forming techniques:
- Metal Stamping: Used to create precise metal parts. This technique allows for high-volume production and consistency in dimensions.
- Injection Molding: Employed for plastic components, ensuring complex shapes are achieved with minimal waste.
- Laser Cutting: Utilized for creating detailed designs on metal surfaces, enhancing aesthetics and branding opportunities.
Buyers should inquire about the forming techniques used, as advanced methods can lead to better quality and longer-lasting products.
3. Assembly
The assembly stage combines all the individual components into a complete machine. This process typically involves:
- Mechanical Assembly: Securing metal parts together and integrating plastic components.
- Electrical Assembly: Installing wiring, motors, and payment systems, ensuring all components are compatible and function correctly.
- Software Integration: Programming the machine to accept various payment methods and dispense products accurately.
Efficient assembly lines often utilize automation to enhance speed and accuracy, reducing labor costs and minimizing human error.
4. Finishing
The final stage involves applying finishes that improve both functionality and aesthetics:
- Powder Coating: Provides a durable and attractive surface finish to metal components, protecting against corrosion and wear.
- Screen Printing: Used for branding and operational instructions on the machine’s exterior.
- Quality Polishing: Enhances the appearance of visible components, contributing to a polished, professional look.
Buyers should consider the finishing techniques employed, as these can affect the machine’s longevity and market appeal.
Quality Assurance
Quality assurance is paramount in the manufacturing of mini candy vending machines. International standards and industry-specific regulations guide the processes involved.
International Standards
- ISO 9001: A globally recognized standard for quality management systems (QMS). Compliance indicates that a manufacturer has established processes to ensure consistent quality and customer satisfaction.
- CE Marking: Required for products sold within the European Economic Area (EEA), CE marking indicates conformity with health, safety, and environmental protection standards.
Industry-Specific Standards
- API (American Petroleum Institute): While not directly related, some vending machines may include components adhering to API standards, especially if they involve petroleum products (like energy drinks).
- RoHS Compliance: Essential for electronics, ensuring that hazardous substances are limited in components.
Quality Control Checkpoints
Quality control is typically structured around three critical checkpoints:
- Incoming Quality Control (IQC): Inspects raw materials upon arrival to ensure they meet specifications before production begins.
- In-Process Quality Control (IPQC): Ongoing checks during the manufacturing process to identify defects early and minimize waste.
- Final Quality Control (FQC): A thorough inspection of the finished product to ensure it meets all specifications and standards before shipment.
Common testing methods include:
- Functional Testing: Verifying that the vending machine operates correctly under various conditions.
- Durability Testing: Assessing how well the machine withstands physical stress and environmental factors.
- Safety Testing: Ensuring compliance with electrical safety standards and protecting against hazards.
Verifying Supplier Quality Control
For B2B buyers, especially those in diverse markets, verifying supplier quality control practices is crucial. Here are actionable steps to ensure quality:
- Conduct Audits: Regular audits can help assess a supplier’s adherence to quality standards and operational efficiency.
- Request Quality Reports: Suppliers should provide documentation of their quality control processes, results of testing, and compliance with standards.
- Engage Third-Party Inspectors: Hiring independent inspectors can provide an unbiased assessment of the manufacturing process and product quality.
Nuances for International Buyers
When dealing with international suppliers, B2B buyers must navigate different regulatory environments and quality standards. Here are some considerations:
- Customs and Compliance: Ensure that the machines meet import regulations in your country, including safety and environmental standards.
- Cultural Differences: Understand that manufacturing practices and quality perceptions may vary across regions. Building strong relationships with suppliers can help bridge these gaps.
- Language Barriers: Effective communication is vital; consider using translators or local representatives to facilitate discussions about quality standards and specifications.
By understanding the manufacturing processes and quality assurance practices associated with mini candy vending machines, international B2B buyers can make informed decisions and ensure they are sourcing high-quality products that meet their specific needs.
Related Video: Parle-G Biscuits Manufacturing process – Food Factory Tour- Modern Food factory, Mega Factory II
Comprehensive Cost and Pricing Analysis for mini candy vending machine Sourcing
When sourcing mini candy vending machines, understanding the comprehensive cost structure and pricing dynamics is crucial for international B2B buyers. This analysis covers the key cost components, pricing influencers, and essential tips for effective negotiations, particularly for buyers from Africa, South America, the Middle East, and Europe.
Cost Components
-
Materials: The primary materials used in mini candy vending machines include metal, plastic, and electronic components. The choice of materials significantly impacts both cost and quality. For instance, opting for higher-quality metals may increase initial costs but enhance durability and reduce long-term maintenance expenses.
-
Labor: Labor costs vary significantly by region. Countries with lower labor costs can offer competitive pricing, but this may also reflect on the quality of workmanship. Understanding local labor market conditions is essential for evaluating total costs.
-
Manufacturing Overhead: This includes utilities, rent, and equipment depreciation associated with the production process. Efficient production facilities can reduce overhead costs, which is a critical consideration when comparing suppliers.
-
Tooling: Custom tooling for machine parts can be a substantial upfront cost. Buyers should assess whether the supplier has existing tooling that meets their specifications or if new tooling will be necessary.
-
Quality Control (QC): Implementing quality control measures can add to the overall cost but is essential for ensuring product reliability. Buyers should consider suppliers with robust QC processes to mitigate risks associated with defective products.
-
Logistics: Shipping and handling costs can vary widely based on the destination and Incoterms. Understanding the full logistics chain, including potential tariffs and customs duties, is vital for accurate cost assessments.
-
Margin: Suppliers typically apply a margin over their costs to ensure profitability. This margin can fluctuate based on market demand, competition, and buyer negotiations.
Price Influencers
-
Volume/MOQ: Larger orders often lead to lower per-unit costs due to economies of scale. Buyers should negotiate minimum order quantities (MOQs) to optimize pricing.
-
Specifications/Customization: Custom features or specifications can increase costs. Buyers should balance the need for customization with budget constraints to ensure they receive value without overspending.
-
Materials: The choice of materials directly influences pricing. For example, eco-friendly materials may come at a premium but can enhance brand reputation and attract environmentally conscious consumers.
-
Quality/Certifications: Machines with certifications (e.g., ISO, CE) may carry higher costs but offer assurances of quality and compliance. These certifications can also facilitate smoother international transactions.
-
Supplier Factors: The reputation, reliability, and negotiation flexibility of suppliers can affect pricing. Conducting thorough due diligence on potential suppliers is essential.
-
Incoterms: Understanding Incoterms is crucial for determining responsibility for shipping costs and risks. This knowledge can significantly impact the total landed cost of the machines.
Buyer Tips
-
Negotiation: Approach negotiations with a clear understanding of your cost structure and pricing expectations. Leverage competitive quotes to negotiate better terms.
-
Cost-Efficiency: Consider the Total Cost of Ownership (TCO), which includes initial purchase price, maintenance, and operational costs. A cheaper upfront cost may lead to higher long-term expenses.
-
Pricing Nuances: International buyers should be aware of fluctuations in currency exchange rates, which can affect pricing. Additionally, cultural differences may influence negotiation styles and expectations.
-
Market Research: Regularly assess the market landscape for mini candy vending machines to stay informed about pricing trends and new suppliers.
-
Risk Management: Establish clear agreements regarding warranties, service support, and return policies to mitigate potential risks associated with sourcing.
In summary, a thorough understanding of the cost structure, pricing influencers, and strategic negotiation techniques is essential for B2B buyers sourcing mini candy vending machines. This knowledge not only aids in making informed purchasing decisions but also enhances overall operational efficiency in the long run.
Spotlight on Potential mini candy vending machine Manufacturers and Suppliers
This section offers a look at a few manufacturers active in the ‘mini candy vending machine’ market. This is a representative sample for illustrative purposes; B2B buyers must conduct their own extensive due diligence before any engagement. Information is synthesized from public sources and general industry knowledge.
Essential Technical Properties and Trade Terminology for mini candy vending machine
Key Technical Properties of Mini Candy Vending Machines
Understanding the essential technical properties of mini candy vending machines is crucial for B2B buyers, especially when evaluating products for import or distribution. Here are the critical specifications to consider:
-
Material Grade
– Definition: This refers to the type and quality of materials used in the construction of the vending machine, such as stainless steel, ABS plastic, or tempered glass.
– Importance: Higher material grades enhance durability and resistance to wear and tear. For buyers in regions with varying climates, selecting machines made from corrosion-resistant materials is vital. -
Capacity
– Definition: Capacity indicates the volume or number of candy products the vending machine can hold, typically measured in liters or number of items.
– Importance: A larger capacity is essential for high-traffic areas, ensuring that the machine can accommodate demand without frequent restocking. Buyers should assess their target market’s foot traffic to determine appropriate capacity. -
Power Consumption
– Definition: This measures the amount of energy the machine uses, often expressed in watts.
– Importance: Low power consumption is vital for reducing operational costs. Buyers should consider energy-efficient models, especially in markets where electricity costs are high. -
Dimensions and Weight
– Definition: The physical size and weight of the vending machine, which affects installation and placement options.
– Importance: Understanding dimensions is crucial for ensuring the machine fits the intended space. Buyers must also consider weight for transportation and installation logistics. -
Payment System Compatibility
– Definition: This refers to the types of payment methods accepted by the vending machine, such as coins, notes, credit cards, or mobile payments.
– Importance: A diverse payment system can increase sales potential. B2B buyers should analyze customer preferences in their region to ensure the machine meets those needs. -
User Interface
– Definition: The design and functionality of the machine’s interface, including buttons, touchscreens, or app integration.
– Importance: A user-friendly interface can enhance customer experience and drive sales. Buyers should prioritize machines with intuitive designs that cater to their target demographic.
Common Trade Terminology
Familiarity with industry jargon is essential for effective communication and negotiation in the B2B space. Here are key terms related to mini candy vending machines:
-
OEM (Original Equipment Manufacturer)
– Definition: A company that produces parts and equipment that may be marketed by another manufacturer.
– Relevance: Buyers should consider OEMs for sourcing quality components and ensuring compatibility with existing machines. -
MOQ (Minimum Order Quantity)
– Definition: The smallest quantity of a product that a supplier is willing to sell.
– Relevance: Understanding MOQ is critical for budget management. Buyers need to evaluate if the MOQ aligns with their sales forecasts and inventory strategy. -
RFQ (Request for Quotation)
– Definition: A document issued by a buyer to solicit price quotes from suppliers for specific products or services.
– Relevance: An RFQ is essential for comparing prices and terms from different suppliers, enabling buyers to make informed purchasing decisions. -
Incoterms (International Commercial Terms)
– Definition: A set of predefined international trade terms published by the International Chamber of Commerce (ICC) that clarify the responsibilities of buyers and sellers.
– Relevance: Understanding Incoterms is crucial for determining shipping responsibilities, costs, and risk management in international transactions. -
Lead Time
– Definition: The time taken from placing an order to receiving the goods.
– Relevance: Buyers should factor lead time into their inventory planning to avoid stockouts, especially in markets with high demand. -
Warranty
– Definition: A guarantee provided by the manufacturer regarding the condition and longevity of the vending machine.
– Relevance: A robust warranty can signify product quality and reduce long-term costs for buyers, making it an essential consideration during procurement.
By understanding these technical properties and trade terms, B2B buyers can make informed decisions when sourcing mini candy vending machines, ensuring they meet market demands and operational requirements effectively.
Navigating Market Dynamics, Sourcing Trends, and Sustainability in the mini candy vending machine Sector
Market Overview & Key Trends
The mini candy vending machine sector is experiencing a robust transformation driven by several global dynamics. The rise in urbanization and the growing inclination towards convenience have significantly increased the demand for vending machines, especially in densely populated regions across Africa, South America, the Middle East, and Europe. Furthermore, technological advancements such as cashless payment options, IoT connectivity, and mobile app integrations are shaping the future of vending solutions, making them more appealing to consumers.
Emerging trends indicate a shift towards healthier snack options, prompting manufacturers to diversify their product offerings beyond traditional candies. This aligns with consumer preferences for healthier lifestyles, particularly in markets like Europe and parts of South America. As a B2B buyer, it is essential to stay informed about these shifts to ensure that your vending solutions meet market demands. Additionally, the integration of AI for inventory management and customer interaction is becoming prevalent, enhancing operational efficiency and customer satisfaction.
B2B buyers should also consider the rising emphasis on localization in sourcing practices. This involves collaborating with local suppliers to cater to regional tastes and preferences while reducing supply chain risks. The global supply chain’s volatility, highlighted by recent disruptions, necessitates a more agile approach to sourcing, ensuring that your business remains competitive in a fast-evolving landscape.
Sustainability & Ethical Sourcing in B2B
In today’s market, sustainability is no longer optional; it is a critical factor influencing purchasing decisions. The mini candy vending machine sector is increasingly scrutinized for its environmental impact, particularly concerning packaging waste and energy consumption. B2B buyers must prioritize suppliers who adopt sustainable practices, such as using eco-friendly materials and energy-efficient machines.
Ethical sourcing is another vital consideration. Consumers are more aware of the origins of their products, demanding transparency in supply chains. This includes ensuring that ingredients are sourced responsibly, with fair labor practices and minimal environmental impact. Certifications such as Fair Trade, Rainforest Alliance, and other ‘green’ credentials can enhance your brand’s reputation and appeal to a socially conscious consumer base.
Investing in sustainable vending solutions not only meets consumer expectations but can also lead to cost savings in the long term. For instance, energy-efficient machines can reduce operational costs, while sustainable packaging can minimize waste disposal fees. As you navigate your sourcing strategies, consider suppliers who prioritize sustainability and ethical practices, as they will be pivotal in ensuring your business aligns with current market expectations.
Brief Evolution/History
The mini candy vending machine has evolved significantly since its inception in the early 20th century. Initially, these machines offered a limited selection of candy, primarily focusing on bulk items. However, the introduction of technology in the late 20th century revolutionized the sector, allowing for diverse product offerings and improved payment methods.
In the 21st century, the focus has shifted towards convenience and personalization, with machines now equipped to dispense a variety of snacks, beverages, and even healthy options. This evolution reflects changing consumer behaviors and preferences, particularly in urban environments where quick access to snacks is increasingly desired. For B2B buyers, understanding this evolution is crucial for making informed decisions about product offerings and machine capabilities that resonate with contemporary consumer needs.
Related Video: Global Trade & Logistics – What is Global Trade?
Frequently Asked Questions (FAQs) for B2B Buyers of mini candy vending machine
-
What should I consider when vetting suppliers for mini candy vending machines?
When vetting suppliers, prioritize their industry experience, reputation, and certifications. Check for customer reviews and case studies showcasing their previous work. It’s also advisable to request references from other B2B clients. Ensure they comply with international quality standards and have a track record of timely deliveries. Consider visiting their facility if possible, or use virtual tours to assess their manufacturing capabilities and quality control processes. -
Can I customize the mini candy vending machines to fit my brand?
Yes, many suppliers offer customization options for mini candy vending machines. You can request branding elements such as logos, colors, and design modifications to align with your corporate identity. Discuss specific features like payment systems or product dispensing mechanisms that may be tailored to your target market. Ensure that the supplier has a portfolio of previous custom projects to evaluate their capability and creativity in design. -
What are the typical minimum order quantities (MOQs) and lead times?
MOQs for mini candy vending machines can vary significantly between suppliers, often depending on the level of customization and production capacity. Generally, expect MOQs to range from 50 to 200 units. Lead times can also differ, typically ranging from 4 to 12 weeks after order confirmation. Always clarify these details upfront and consider negotiating terms that suit your operational needs, especially if you are a smaller business. -
What payment terms are usually available when sourcing from international suppliers?
Payment terms can vary based on the supplier’s policies and your negotiation. Common terms include a deposit (usually 30-50%) upfront, with the balance due before shipment. Some suppliers may offer letters of credit or escrow services for added security. Be cautious of suppliers requiring full payment in advance, especially if they are unfamiliar or lack a solid reputation. Ensure that all payment terms are documented clearly in the contract to avoid disputes. -
How do I ensure quality assurance and compliance with international standards?
To ensure quality assurance, request documentation of the supplier’s quality management system, such as ISO certifications. Ask for product samples prior to bulk orders to evaluate quality firsthand. Inquire about their testing procedures and warranty policies. Additionally, consider hiring a third-party inspection service to conduct quality checks during production and prior to shipment, especially if you are importing to regions with strict regulatory standards. -
What logistics considerations should I keep in mind when importing mini candy vending machines?
Logistics can be complex when importing vending machines. Consider shipping methods (air vs. sea) based on your budget and urgency. Factor in customs duties, taxes, and potential import restrictions specific to your country. Collaborate with a logistics partner experienced in handling large equipment to navigate these challenges smoothly. Ensure that the supplier provides all necessary documentation, such as bills of lading and certificates of origin, to facilitate customs clearance. -
How can I handle disputes with suppliers effectively?
To handle disputes effectively, establish clear communication channels and maintain a documented record of all correspondence. Before escalating issues, attempt to resolve them amicably through negotiation. If disputes arise over contract terms, product quality, or delivery timelines, refer to the terms outlined in your agreement. Consider including a dispute resolution clause in your contract, such as mediation or arbitration, to provide a structured approach to conflict resolution. -
What certifications should I look for in mini candy vending machines?
When sourcing mini candy vending machines, look for certifications that indicate compliance with safety and quality standards, such as CE marking for European markets or UL certification in North America. Additionally, check for food safety certifications if the machines dispense consumables. These certifications not only ensure product safety but also enhance marketability, as they demonstrate adherence to international quality standards that can boost consumer confidence.
Strategic Sourcing Conclusion and Outlook for mini candy vending machine
As the market for mini candy vending machines continues to evolve, strategic sourcing emerges as a critical component for international B2B buyers. Understanding the unique demands of diverse markets in Africa, South America, the Middle East, and Europe is essential. Key takeaways include the importance of selecting reliable suppliers who prioritize quality and compliance with local regulations. Furthermore, leveraging data analytics can enhance procurement strategies, enabling businesses to anticipate market trends and consumer preferences.
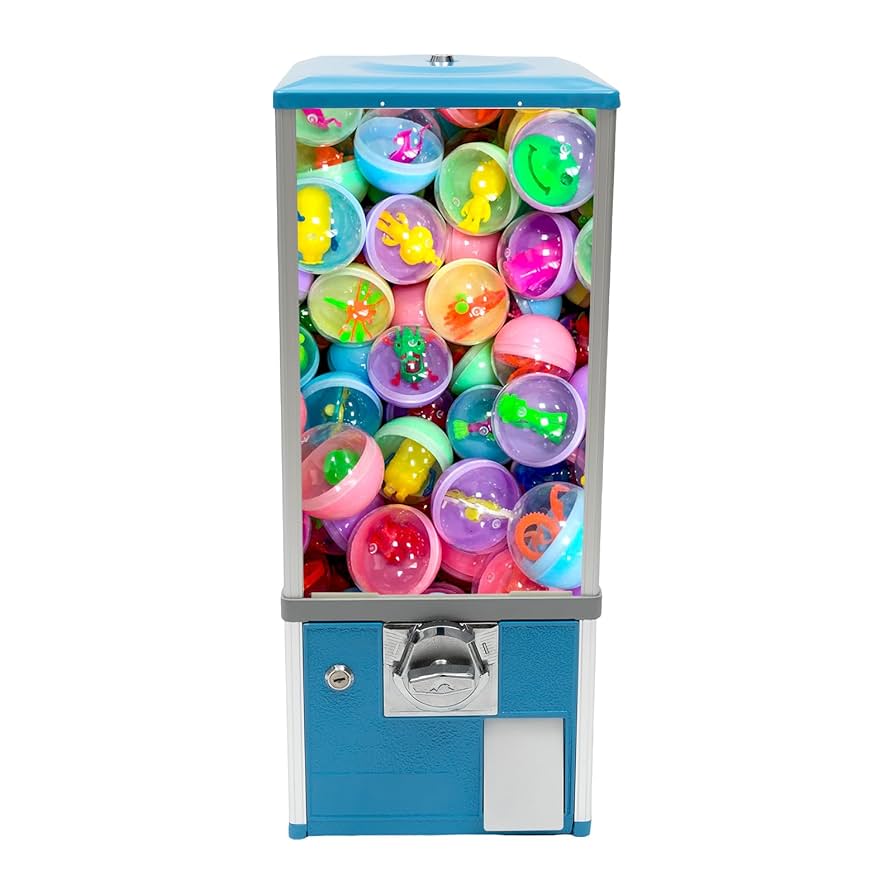
Illustrative Image (Source: Google Search)
Investing in innovative vending solutions not only meets the growing demand for convenience but also aligns with sustainability efforts, appealing to eco-conscious consumers. Buyers should also consider partnerships that offer technological advancements, such as cashless payment systems and inventory management tools, which can streamline operations and improve customer experience.
Looking ahead, the potential for growth in the mini candy vending machine sector is substantial. International buyers are encouraged to engage with suppliers who can provide tailored solutions and robust support. By prioritizing strategic sourcing, businesses can position themselves for success in an increasingly competitive landscape. The time to act is now—embrace the opportunities that await in this dynamic market.
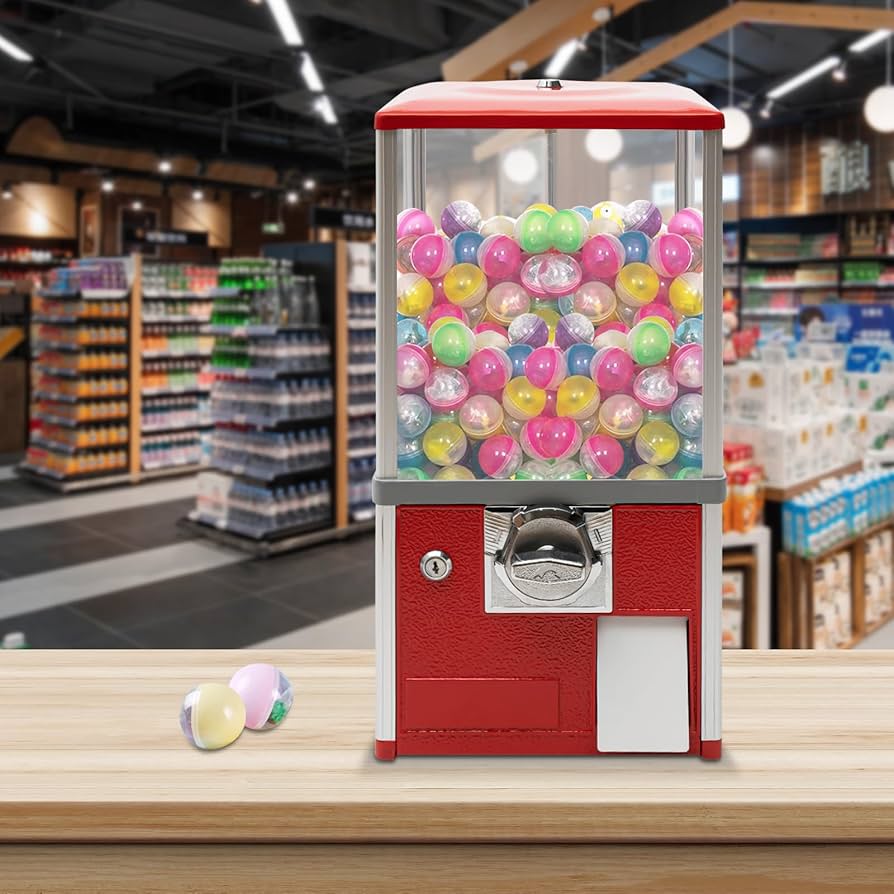
Illustrative Image (Source: Google Search)