Master Sourcing High-Quality CVS Vending Machines for Your
Guide to Cvs Vending Machine
- Introduction: Navigating the Global Market for cvs vending machine
- Understanding cvs vending machine Types and Variations
- Key Industrial Applications of cvs vending machine
- Strategic Material Selection Guide for cvs vending machine
- In-depth Look: Manufacturing Processes and Quality Assurance for cvs vending machine
- Comprehensive Cost and Pricing Analysis for cvs vending machine Sourcing
- Spotlight on Potential cvs vending machine Manufacturers and Suppliers
- Essential Technical Properties and Trade Terminology for cvs vending machine
- Navigating Market Dynamics, Sourcing Trends, and Sustainability in the cvs vending machine Sector
- Frequently Asked Questions (FAQs) for B2B Buyers of cvs vending machine
- Strategic Sourcing Conclusion and Outlook for cvs vending machine
Introduction: Navigating the Global Market for cvs vending machine
In today’s fast-paced global marketplace, the demand for convenience and accessibility has led to a surge in the popularity of CVS vending machines. These automated dispensers not only streamline the purchasing process for customers but also present lucrative opportunities for international B2B buyers seeking to enhance their product offerings. The CVS vending machine sector is characterized by innovative designs and an array of products, catering to diverse consumer needs across various regions.
This comprehensive guide serves as a vital resource for international buyers, particularly those operating in Africa, South America, the Middle East, and Europe, including key markets like Germany and Turkey. By delving into the types of CVS vending machines available, the materials used in their construction, and the critical aspects of manufacturing and quality control, this guide equips buyers with the knowledge necessary to make informed sourcing decisions.
Furthermore, we will explore the landscape of suppliers, pricing structures, and market dynamics, ensuring that you are well-prepared to navigate the complexities of international procurement. The FAQ section will address common queries, providing clarity on operational considerations and best practices. Whether you are looking to invest in CVS vending machines for retail, healthcare, or other sectors, this guide empowers you to capitalize on emerging trends and maximize your business potential in the global market.
Understanding cvs vending machine Types and Variations
Type Name | Key Distinguishing Features | Primary B2B Applications | Brief Pros & Cons for Buyers |
---|---|---|---|
Traditional Snack Vending | Offers a variety of snacks and beverages | Offices, schools, public spaces | Pros: Low initial cost, easy to maintain. Cons: Limited product range, susceptible to theft. |
Health and Wellness Vending | Focuses on nutritious snacks and beverages | Gyms, health clubs, corporate wellness | Pros: Attracts health-conscious consumers. Cons: Higher product costs, requires regular restocking. |
Automated Pharmacy Vending | Dispenses over-the-counter medications | Hospitals, clinics, pharmacies | Pros: Convenient access to medications. Cons: Regulatory compliance can be complex. |
Specialty Product Vending | Features niche items like electronics or cosmetics | Airports, hotels, specialty stores | Pros: Unique offerings can drive higher sales. Cons: Higher upfront investment, risk of low turnover. |
Interactive Vending Machines | Equipped with touchscreens for product selection | Events, trade shows, high-traffic areas | Pros: Enhanced user experience, customizable options. Cons: Higher maintenance costs, potential technical issues. |
Traditional Snack Vending
Traditional snack vending machines are the most common type, offering a range of snacks and beverages. These machines are typically found in offices, schools, and public spaces where convenience is paramount. For B2B buyers, the initial investment is relatively low, making it an accessible option. However, the limited product range and susceptibility to theft can pose challenges, particularly in high-traffic areas.
Health and Wellness Vending
Health and wellness vending machines cater to a growing market of health-conscious consumers by providing nutritious snacks and beverages. These machines are ideal for gyms, health clubs, and corporate wellness programs. When considering this type, B2B buyers should weigh the higher product costs against the potential for attracting a loyal customer base. Regular restocking is essential to maintain product freshness and appeal.
Automated Pharmacy Vending
Automated pharmacy vending machines dispense over-the-counter medications and health products, providing convenience in locations like hospitals, clinics, and pharmacies. For B2B buyers, these machines offer a unique value proposition by improving access to essential health items. However, compliance with regulatory standards can complicate the purchasing process, requiring careful consideration of local laws and guidelines.
Specialty Product Vending
Specialty product vending machines focus on niche items, such as electronics, cosmetics, or artisan foods. These machines are often placed in airports, hotels, and specialty stores, targeting specific consumer demographics. B2B buyers should consider the potential for higher sales from unique offerings, but also the higher upfront investment and risk of low turnover if the product selection does not resonate with the target market.
Interactive Vending Machines
Interactive vending machines feature touchscreens that allow users to browse and select products. They are increasingly popular in events, trade shows, and high-traffic areas due to their engaging user experience. For B2B buyers, these machines offer customizable options that can enhance brand visibility. However, the higher maintenance costs and potential for technical issues should be factored into the purchasing decision to ensure a smooth operation.
Related Video: Machine Learning in 2024 – Beginner’s Course
Key Industrial Applications of cvs vending machine
Industry/Sector | Specific Application of cvs vending machine | Value/Benefit for the Business | Key Sourcing Considerations for this Application |
---|---|---|---|
Healthcare | Dispensing pharmaceuticals and medical supplies | Improved patient access to medications, reduced wait times | Compliance with health regulations, temperature control |
Retail | Automated retail for convenience goods | Increased sales during off-hours, reduced staffing costs | Product variety, payment system integration |
Education | Supply of snacks and beverages in schools | Enhanced student satisfaction, reduced food waste | Nutritional guidelines compliance, machine durability |
Corporate Offices | Providing refreshments and snacks for employees | Boosted employee morale, increased productivity | Customization options, maintenance and service support |
Transportation Hubs | Vending solutions for travel essentials | Convenience for travelers, increased foot traffic | Security features, payment method flexibility |
Healthcare
In the healthcare sector, CVS vending machines are utilized to dispense pharmaceuticals and essential medical supplies. This application addresses the challenge of ensuring patients have quick access to their medications, especially in remote or underserved areas. International buyers, particularly from regions like Africa and the Middle East, must consider compliance with local health regulations and the machine’s ability to maintain the required temperature for sensitive products. Investing in machines with robust monitoring systems can enhance reliability and patient trust.
Retail
In retail environments, CVS vending machines serve as automated retail solutions for convenience goods, allowing businesses to operate beyond traditional hours. This application is particularly beneficial for urban areas in South America and Europe, where consumer demand for 24/7 access is growing. By reducing the need for on-site staffing, retailers can lower operational costs while increasing sales. Buyers should focus on the machine’s capacity for diverse product offerings and its ability to integrate with existing payment systems to streamline operations.
Education
Within educational institutions, CVS vending machines provide a convenient source of snacks and beverages for students. This application not only enhances student satisfaction but also helps reduce food waste through efficient inventory management. Buyers in Europe and Africa should be aware of nutritional guidelines that govern the types of products that can be offered. Selecting machines that offer customizable options for healthy snacks can align with these regulations and promote better eating habits among students.
Corporate Offices
CVS vending machines in corporate offices offer refreshments and snacks to employees, contributing to improved morale and productivity. This application is crucial for businesses in regions like Turkey and Germany, where employee well-being is increasingly prioritized. When sourcing these machines, companies should consider customization options to cater to diverse dietary preferences, as well as the availability of maintenance and service support to ensure continuous operation.
Transportation Hubs
In transportation hubs, CVS vending machines provide travelers with quick access to essential items such as snacks, beverages, and personal care products. This application is vital for enhancing traveler convenience and can significantly increase foot traffic in busy terminals. International buyers should prioritize security features to prevent theft and ensure that the machines support multiple payment methods, catering to a diverse clientele. Investing in machines that can withstand high traffic and varying environmental conditions is also essential for long-term success.
Related Video: How to refill coins in the coin mechanism of your vending machine
Strategic Material Selection Guide for cvs vending machine
When selecting materials for CVS vending machines, it is crucial to consider properties that affect performance, durability, and compliance with international standards. Below is an analysis of several common materials used in the construction of CVS vending machines, along with their advantages, disadvantages, and specific considerations for international B2B buyers.
Stainless Steel
Key Properties: Stainless steel is known for its excellent corrosion resistance, high tensile strength, and ability to withstand high temperatures. It is often rated for various pressure levels, making it suitable for different environments.
Pros & Cons: The durability of stainless steel makes it ideal for high-traffic areas, as it can withstand impact and wear. However, it is more expensive compared to other materials, which can increase the overall cost of the vending machine. Manufacturing complexity can also be higher due to the need for specialized welding techniques.
Impact on Application: Stainless steel is compatible with a wide range of media, including food and beverages, making it a preferred choice for vending machines that dispense consumables.
Considerations for International Buyers: Buyers from regions like Europe (e.g., Germany) may prioritize materials that comply with EU regulations concerning food safety. Additionally, understanding the specific grades of stainless steel (e.g., 304 or 316) is essential for ensuring compliance with local standards.
Aluminum
Key Properties: Aluminum is lightweight, corrosion-resistant, and has good thermal conductivity. It typically has lower strength compared to stainless steel but can be alloyed to enhance its properties.
Pros & Cons: The primary advantage of aluminum is its lower cost and ease of manufacturing, which can reduce production times. However, it is less durable than stainless steel and may not withstand heavy impacts as effectively.
Impact on Application: Aluminum is suitable for applications where weight is a concern, such as portable vending machines. However, its compatibility with certain media should be evaluated, especially if acidic or alkaline products are involved.
Considerations for International Buyers: Buyers in the Middle East and Africa should consider the local climate, as extreme temperatures can affect aluminum’s performance. Compliance with standards like ASTM for aluminum alloys is also essential.
Polycarbonate
Key Properties: Polycarbonate is a durable thermoplastic known for its high impact resistance and optical clarity. It can withstand a wide temperature range but may have lower chemical resistance compared to metals.
Pros & Cons: The lightweight nature of polycarbonate makes it easy to handle and install. It is also cost-effective compared to metals. However, its lower resistance to UV light can lead to degradation over time, particularly in outdoor settings.
Impact on Application: Polycarbonate is often used for transparent panels in vending machines, allowing visibility of products. However, it may not be suitable for applications involving harsh chemicals.
Considerations for International Buyers: Buyers should ensure that the polycarbonate used meets local safety standards, particularly in regions with stringent regulations, such as Europe. The choice of UV-stabilized grades can enhance longevity in sunny climates.
Mild Steel
Key Properties: Mild steel is characterized by its ductility, malleability, and good weldability. It has moderate strength and is often treated to improve corrosion resistance.
Pros & Cons: Mild steel is cost-effective and easy to work with, making it a popular choice for many applications. However, it is susceptible to rust if not properly coated, which can limit its lifespan in humid environments.
Impact on Application: While suitable for structural components of vending machines, mild steel may not be appropriate for areas exposed to moisture or corrosive substances.
Considerations for International Buyers: Buyers in South America and Africa should consider the environmental conditions where the vending machines will be deployed. Compliance with local standards for coatings and treatments is critical to ensure durability.
Summary Table
Material | Typical Use Case for cvs vending machine | Key Advantage | Key Disadvantage/Limitation | Relative Cost (Low/Med/High) |
---|---|---|---|---|
Stainless Steel | Structural and exterior components for durability | Excellent corrosion resistance | Higher cost and manufacturing complexity | High |
Aluminum | Lightweight, portable vending machines | Cost-effective and easy to manufacture | Less durable under heavy impact | Med |
Polycarbonate | Transparent panels for product visibility | High impact resistance | UV degradation over time | Low |
Mild Steel | Structural elements, especially in dry environments | Cost-effective and easy to work with | Susceptible to rust without proper coating | Low |
This guide provides a comprehensive overview of material options for CVS vending machines, helping international B2B buyers make informed decisions based on their specific needs and regional considerations.
In-depth Look: Manufacturing Processes and Quality Assurance for cvs vending machine
The manufacturing of CVS vending machines involves a series of well-defined processes and stringent quality assurance measures. Understanding these can help international B2B buyers make informed decisions about suppliers, ensuring they acquire reliable and high-quality products.
Manufacturing Processes
1. Material Preparation
The first stage in manufacturing CVS vending machines is material preparation. This involves sourcing high-quality materials such as steel, plastic, and electronic components. Buyers should look for suppliers who prioritize sustainable sourcing practices and can provide certifications for materials used.
- Key Techniques:
- Supplier Audits: Verify that suppliers adhere to best practices in sourcing raw materials.
- Material Certification: Check for certifications like ISO 14001, which indicates a commitment to environmental management.
2. Forming
Once materials are prepared, the next step is forming, where raw materials are shaped into the desired components. This can involve processes such as stamping, bending, and injection molding.
- Key Techniques:
- CNC Machining: Ensures precision in creating parts that fit together seamlessly.
- Robotic Automation: Increases efficiency and consistency in forming processes.
3. Assembly
Assembly is where all the formed components come together. This stage requires skilled labor and precise coordination to ensure that mechanical, electrical, and software components function together effectively.
- Key Techniques:
- Lean Manufacturing Principles: Helps minimize waste and streamline the assembly process.
- Modular Assembly Systems: Allow for flexibility in production and easier maintenance.
4. Finishing
Finishing processes enhance the aesthetic and functional qualities of the vending machine. This may include painting, coating, or applying decals.
- Key Techniques:
- Powder Coating: Provides a durable and attractive finish, resistant to wear and corrosion.
- Quality Control During Finishing: Regular checks ensure that the finish meets specified standards.
Quality Assurance
Quality assurance is critical in ensuring that CVS vending machines meet international standards and consumer expectations.
Relevant International Standards
B2B buyers should be aware of various international standards that govern the quality of vending machines:
- ISO 9001: This standard focuses on quality management systems and is crucial for ensuring consistent quality across manufacturing processes.
- CE Marking: For machines sold within the European market, CE marking indicates compliance with health, safety, and environmental protection standards.
- API Standards: Particularly relevant for machines that dispense pharmaceuticals or other sensitive products.
Quality Control Checkpoints
Quality control is performed at various stages of the manufacturing process:
- Incoming Quality Control (IQC): Inspects raw materials and components upon arrival.
- In-Process Quality Control (IPQC): Monitors processes during manufacturing to catch defects early.
- Final Quality Control (FQC): Conducts a comprehensive check of the finished product before it is packaged and shipped.
Common Testing Methods
Testing methods are essential to validate the quality of CVS vending machines:
- Functional Testing: Ensures that all electronic and mechanical components operate as intended.
- Durability Testing: Simulates long-term use to assess the machine’s performance over time.
- Safety Testing: Confirms compliance with electrical safety standards and other relevant regulations.
Verifying Supplier Quality Control
For international B2B buyers, especially from regions like Africa, South America, the Middle East, and Europe, verifying a supplier’s quality control processes is vital. Here are some actionable steps:
- Supplier Audits: Conduct regular audits to assess compliance with quality standards. This can be done by the buyer or through third-party inspection agencies.
- Request Quality Reports: Ask suppliers for detailed quality assurance documentation, including results from IQC, IPQC, and FQC stages.
- Third-Party Inspections: Engage independent inspection firms to evaluate the manufacturing processes and quality control measures of potential suppliers.
- Certifications Verification: Always check the authenticity of quality certifications provided by suppliers. This can involve direct communication with certifying bodies.
Quality Control and Certification Nuances
International B2B buyers must navigate various nuances related to quality control and certification. Here are some considerations:
- Regional Regulations: Different regions have varying regulations. For instance, products sold in the EU must meet CE certification, while those in the Middle East may require local compliance certificates.
- Cultural Considerations: Be aware of cultural differences that may affect quality perceptions. For example, what is considered acceptable quality in one region may not meet the standards in another.
- Post-Purchase Support: Investigate the warranty and post-purchase support provided by suppliers, as this can be a significant aspect of quality assurance.
Conclusion
A comprehensive understanding of manufacturing processes and quality assurance measures is essential for international B2B buyers considering CVS vending machines. By focusing on material preparation, forming, assembly, and finishing, along with rigorous quality control standards, buyers can ensure that they partner with reputable suppliers who deliver high-quality products that meet international standards. Engaging in thorough verification processes will further safeguard against potential risks and enhance the overall purchasing experience.
Related Video: SMART Quality Control for Manufacturing
Comprehensive Cost and Pricing Analysis for cvs vending machine Sourcing
Understanding the cost and pricing structure for CVS vending machines is essential for international B2B buyers looking to make informed sourcing decisions. The complexity of these machines, combined with various influencing factors, necessitates a thorough analysis of both cost components and pricing influencers to achieve optimal procurement strategies.
Cost Components
-
Materials: The primary materials for CVS vending machines include metal, plastics, electronic components, and glass. The choice of materials significantly impacts the overall cost. For instance, higher-quality materials can enhance durability but may increase the initial investment.
-
Labor: Labor costs vary by region and can be influenced by local wage standards and the skill level of the workforce. In countries with higher labor costs, such as Germany, it’s essential to factor in these expenses when calculating total costs.
-
Manufacturing Overhead: This includes costs associated with utilities, facility maintenance, and administrative expenses. Efficient manufacturing processes can help minimize these overheads, but buyers should be aware that such efficiencies may not be equally present across all suppliers.
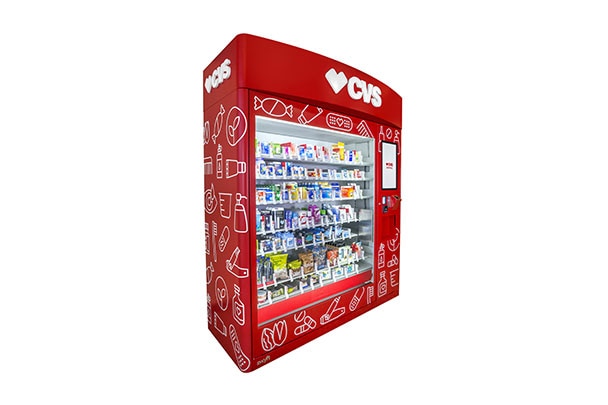
Illustrative Image (Source: Google Search)
-
Tooling: Custom tooling for specific machine designs can lead to substantial upfront costs. Buyers should assess whether the tooling costs can be amortized over large production runs to reduce the overall cost per unit.
-
Quality Control (QC): Implementing stringent QC measures is critical to ensure the reliability and safety of vending machines. The costs associated with QC processes should be considered, as they can vary widely between manufacturers.
-
Logistics: Transportation and shipping costs can greatly affect the final price, especially for international buyers. Factors such as distance, shipping method, and customs duties must be accounted for.
-
Margin: Supplier margins are often influenced by market demand, competition, and the perceived value of the product. Understanding the supplier’s margin can provide insights into pricing flexibility during negotiations.
Price Influencers
-
Volume/MOQ: Minimum order quantities (MOQ) can significantly affect pricing. Bulk purchases typically yield discounts, allowing buyers to lower their unit costs.
-
Specifications/Customization: Custom features or specifications can lead to increased costs. Buyers should clearly define their requirements upfront to avoid unexpected expenses later in the process.
-
Materials: The quality of materials used can influence both the initial price and the long-term performance of the vending machine. Buyers should weigh the benefits of premium materials against their budget constraints.
-
Quality/Certifications: Machines that meet international quality standards or come with certifications may carry a higher price tag. However, investing in certified products often results in lower maintenance costs and better reliability.
-
Supplier Factors: The reputation and reliability of suppliers can affect pricing. Established suppliers may charge more due to their proven track record, while new entrants might offer lower prices to gain market share.
-
Incoterms: Understanding Incoterms is crucial for international transactions. The chosen Incoterm can impact logistics costs and responsibilities, ultimately influencing the total price.
Buyer Tips
-
Negotiation: Leverage volume purchases and long-term contracts to negotiate better prices. Building a solid relationship with suppliers can lead to more favorable terms.
-
Cost-Efficiency: Evaluate the Total Cost of Ownership (TCO) rather than just the purchase price. Consider factors such as maintenance, energy consumption, and lifespan when making decisions.
-
Pricing Nuances: Be aware of regional pricing differences. For instance, prices may vary significantly between European and African markets due to local economic conditions and demand levels.
-
Local Partnerships: Consider partnering with local distributors or agents who understand the regional market dynamics and can help navigate the complexities of sourcing CVS vending machines.
In conclusion, understanding the cost structure and pricing influences is vital for international B2B buyers sourcing CVS vending machines. By considering these factors and employing strategic negotiation techniques, buyers can optimize their purchasing decisions to achieve cost-effective solutions tailored to their unique requirements.
- Disclaimer: Prices and cost structures mentioned are indicative and subject to change based on market conditions, supplier negotiations, and specific buyer requirements.*
Spotlight on Potential cvs vending machine Manufacturers and Suppliers
- (No specific manufacturer data was available or requested for detailed profiling in this section for cvs vending machine.)*
Essential Technical Properties and Trade Terminology for cvs vending machine
Key Technical Properties of CVS Vending Machines
When considering the procurement of CVS vending machines, understanding their technical specifications is crucial for making informed purchasing decisions. Below are several essential properties to consider:
-
Material Grade
– Definition: The quality of materials used in the construction of the vending machine, typically stainless steel or high-grade plastic.
– Importance: High-grade materials enhance durability and resistance to environmental factors, which is critical in outdoor installations or high-traffic areas. For international buyers, this ensures longevity and lower maintenance costs. -
Power Consumption
– Definition: The amount of electricity the vending machine consumes during operation, usually measured in watts.
– Importance: Understanding power consumption is vital for calculating operational costs and ensuring compliance with local energy regulations. Buyers in regions with high energy costs or strict energy efficiency standards must prioritize machines with lower consumption rates. -
Capacity and Dimensions
– Definition: The number of products the vending machine can hold and its physical size.
– Importance: Buyers need to consider the machine’s capacity in relation to foot traffic and product variety. Additionally, dimensions affect placement options in various settings, from small shops to large corporate offices. -
User Interface Technology
– Definition: The technology used for user interaction, including touch screens, cashless payment systems, and mobile app integration.
– Importance: A modern user interface can significantly enhance customer experience and increase sales. International buyers should look for machines that support multiple languages and payment methods, catering to diverse clientele. -
Temperature Control System
– Definition: The mechanism that regulates the internal temperature for perishable items.
– Importance: For vending machines offering food or beverages, effective temperature control is essential to maintain product quality and safety. Buyers must ensure compliance with local health regulations regarding food storage. -
Security Features
– Definition: Measures such as anti-theft locks, surveillance cameras, and alarm systems integrated into the vending machine.
– Importance: Enhanced security features can deter theft and vandalism, making them particularly important for installations in high-risk areas. Buyers should assess the security needs based on the machine’s location.
Common Trade Terminology
Familiarity with industry terminology can significantly streamline the purchasing process. Below are key terms that international buyers should know:
-
OEM (Original Equipment Manufacturer)
– Definition: A company that produces parts or equipment that may be marketed by another manufacturer.
– Relevance: Understanding OEM relationships can help buyers identify reliable suppliers and ensure compatibility with existing systems or machines. -
MOQ (Minimum Order Quantity)
– Definition: The smallest quantity of a product that a supplier is willing to sell.
– Relevance: Knowing the MOQ is essential for budgeting and inventory management, especially for buyers looking to minimize upfront costs while ensuring a stable supply. -
RFQ (Request for Quotation)
– Definition: A document sent to suppliers requesting pricing and terms for a specific quantity of goods.
– Relevance: Issuing an RFQ allows buyers to compare offers, negotiate prices, and make informed purchasing decisions based on competitive bids. -
Incoterms (International Commercial Terms)
– Definition: A set of rules that define the responsibilities of sellers and buyers regarding the delivery of goods.
– Relevance: Familiarity with Incoterms is vital for understanding shipping costs, risks, and responsibilities, particularly when dealing with international suppliers. -
Lead Time
– Definition: The amount of time it takes from placing an order until the goods are delivered.
– Relevance: Understanding lead times helps buyers plan inventory levels and ensure timely availability of products, which is critical for maintaining customer satisfaction. -
Warranty and Service Agreement
– Definition: A guarantee provided by the manufacturer regarding the performance and upkeep of the vending machine.
– Relevance: Buyers should carefully review warranty terms and service agreements to understand their rights and the support available for maintenance or repairs.
By grasping these technical properties and trade terminologies, international B2B buyers can make more strategic decisions when sourcing CVS vending machines, ensuring they meet their operational needs while maximizing return on investment.
Navigating Market Dynamics, Sourcing Trends, and Sustainability in the cvs vending machine Sector
Market Overview & Key Trends
The global CVS vending machine market is experiencing a significant transformation driven by technological advancements, evolving consumer preferences, and a growing emphasis on convenience. International B2B buyers, particularly from Africa, South America, the Middle East, and Europe, should be aware of the following key trends:
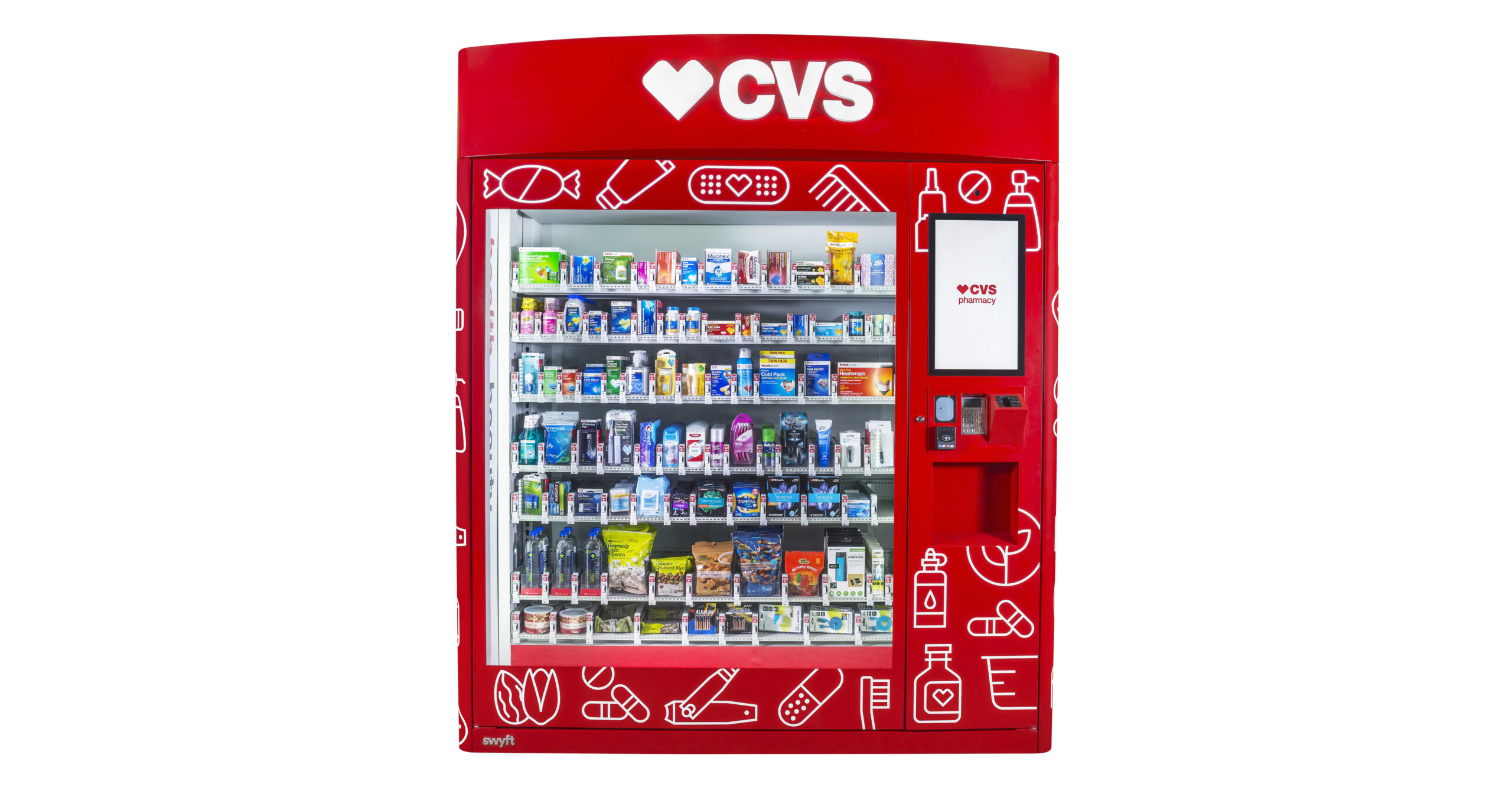
Illustrative Image (Source: Google Search)
-
Technological Integration: The rise of IoT (Internet of Things) and AI (Artificial Intelligence) is revolutionizing vending machines. Smart machines equipped with cashless payment systems, inventory management software, and real-time analytics are becoming the norm. Buyers should seek suppliers who offer these cutting-edge technologies to enhance operational efficiency and customer satisfaction.
-
Health and Wellness Focus: As consumers increasingly prioritize health, CVS vending machines are adapting by offering organic, gluten-free, and low-calorie options. B2B buyers should consider sourcing machines that can accommodate diverse product ranges to meet local market demands.
-
Sustainability in Sourcing: The pressure for sustainable practices is reshaping supply chains. Companies that prioritize eco-friendly materials and energy-efficient machines are likely to gain a competitive edge. Buyers should prioritize vendors with transparent sourcing practices and sustainability certifications.
-
Regional Market Adaptation: Understanding regional preferences is crucial. For instance, buyers in Europe may favor machines that support local artisanal products, while those in the Middle East might look for options that cater to specific dietary laws. Conducting market research to identify these nuances can drive successful sourcing strategies.
-
E-Commerce Integration: The integration of e-commerce platforms with vending solutions is emerging, enabling consumers to pre-order items for pick-up. This trend presents opportunities for B2B buyers to expand their service offerings and enhance customer engagement.
Sustainability & Ethical Sourcing in B2B
Sustainability is no longer just a buzzword; it is a fundamental consideration in the CVS vending machine sector. The environmental impact of sourcing and operating vending machines can be significant, from the materials used in construction to the energy consumed during operation.
-
Importance of Ethical Supply Chains: Buyers should prioritize suppliers that adhere to ethical sourcing practices. This includes ensuring fair labor conditions and responsible sourcing of materials. Transparency in the supply chain not only builds trust but also aligns with increasing consumer expectations for corporate responsibility.
-
Green Certifications and Materials: Look for vending machines made from recycled materials or those that have received green certifications such as LEED (Leadership in Energy and Environmental Design) or ISO 14001. These credentials indicate a commitment to sustainability and can enhance a company’s reputation in the marketplace.
-
Energy Efficiency: Opt for machines that are designed to minimize energy consumption. Energy-efficient vending machines can significantly reduce operational costs while also appealing to environmentally conscious consumers.
-
Waste Management Solutions: Implementing effective waste management strategies, such as recycling programs or compostable product offerings, can further enhance sustainability efforts. B2B buyers should inquire about these capabilities when selecting vendors.
Brief Evolution/History
The CVS vending machine sector has evolved dramatically over the past few decades. Initially, vending machines primarily dispensed snacks and beverages, with limited technological integration. However, advancements in technology have transformed these machines into sophisticated retail solutions capable of offering a wide array of products, including health and wellness items, electronics, and personal care products.
The introduction of cashless payment systems and smart technology has made vending machines more accessible and user-friendly. Furthermore, the global pandemic accelerated the adoption of contactless payments and hygienic practices, solidifying the role of CVS vending machines as essential retail solutions in various environments, from offices to public spaces.
As the sector continues to evolve, international B2B buyers must stay informed about these developments to make strategic sourcing decisions that align with market demands and sustainability goals.
Related Video: International Trade 101 | Economics Explained
Frequently Asked Questions (FAQs) for B2B Buyers of cvs vending machine
-
How do I vet suppliers of CVS vending machines?
Vetting suppliers is crucial for ensuring quality and reliability. Start by researching potential suppliers through industry directories and trade shows. Verify their business credentials, such as registration and financial stability. Request references from other clients, especially those in your region, to gauge their performance. Additionally, consider third-party verification services for a more thorough assessment. For international purchases, ensure the supplier has experience exporting to your country and understands local regulations. -
Can I customize my CVS vending machines?
Yes, most manufacturers offer customization options to meet specific business needs. Common customizations include branding, product selection, payment methods, and machine size. When discussing customization, be clear about your requirements and expectations. Ensure the supplier provides a detailed proposal outlining the customization process, timelines, and any associated costs. Custom solutions can enhance customer experience and align with local market preferences, making them a worthwhile investment. -
What are the typical minimum order quantities (MOQs) and lead times?
Minimum order quantities vary by supplier and can range from a single unit to several dozen. Larger orders often come with discounts, so consider your demand forecasts when negotiating. Lead times for CVS vending machines typically range from 4 to 12 weeks, depending on customization and production schedules. Always confirm these details upfront, and factor in potential delays due to shipping or customs clearance, especially when importing to regions like Africa or South America. -
What payment methods are recommended when purchasing CVS vending machines?
Payment methods can vary widely by supplier and region. Common options include wire transfers, letters of credit, and online payment platforms. For larger transactions, letters of credit provide a secure way to ensure both parties fulfill their obligations. Always negotiate payment terms that protect your interests, such as partial payments upon order confirmation and the balance upon delivery. Ensure you are aware of any additional fees associated with international transactions, such as currency conversion costs. -
What quality assurance measures should I look for?
Quality assurance (QA) is critical when sourcing CVS vending machines. Inquire about the supplier’s QA processes, including certifications like ISO or CE marking, which indicate compliance with international standards. Request detailed documentation on testing procedures, warranties, and after-sales support. Conducting a factory visit, if possible, or using third-party inspection services can further ensure that the machines meet your quality expectations before shipment. -
How do I handle logistics and shipping for CVS vending machines?
Logistics is a key consideration when importing vending machines. Discuss shipping options with your supplier, including freight methods (air, sea, or land) and associated costs. Ensure the supplier can provide the necessary export documentation to facilitate customs clearance. Consider partnering with a logistics company experienced in international trade to navigate complexities such as tariffs, duties, and local regulations. Proper logistics planning can help minimize delays and ensure a smooth delivery process. -
What should I do in case of disputes with a supplier?
Disputes can arise over various issues, such as product quality, delivery times, or payment terms. To mitigate risks, establish clear contracts that outline expectations, responsibilities, and procedures for resolving conflicts. In the event of a dispute, attempt to resolve the issue amicably through direct communication. If necessary, consider mediation or arbitration, particularly if you are dealing with international suppliers. Keeping detailed records of all transactions and communications can be invaluable in supporting your case. -
Are there any specific certifications or regulations I should be aware of?
Yes, different regions have specific certifications and regulations for vending machines. For instance, machines sold in Europe may need to comply with CE standards, while other regions might have distinct health and safety regulations. Familiarize yourself with local laws governing electrical appliances and consumer safety. Ensure your supplier is knowledgeable about these requirements and can provide necessary documentation. Compliance not only ensures legal operation but also builds trust with your customers.
Strategic Sourcing Conclusion and Outlook for cvs vending machine
In conclusion, strategic sourcing for CVS vending machines presents a significant opportunity for international B2B buyers seeking to enhance their service offerings. By prioritizing supplier relationships and leveraging regional advantages, buyers from Africa, South America, the Middle East, and Europe can effectively navigate the complexities of the vending machine market.
Key takeaways include:
- Cost Efficiency: Streamlining sourcing processes can lead to substantial cost savings, allowing companies to invest in better technology and customer engagement strategies.
- Customization: Understanding local consumer preferences enables businesses to select vending machines that cater to specific market needs, enhancing customer satisfaction and retention.
- Sustainability: Emphasizing eco-friendly products and practices not only aligns with global sustainability trends but also appeals to a growing base of environmentally conscious consumers.
As you look towards the future, consider how strategic sourcing can drive competitive advantage in your market. Engage with suppliers who share your vision and values, and explore innovative solutions that can differentiate your offerings. By doing so, you position your business to thrive in an increasingly interconnected global economy. Take the next step in optimizing your vending machine strategy and unlock new growth opportunities today.