Master Sourcing Harm Reduction Vending Machines for Global
Guide to Harm Reduction Vending Machines
- Introduction: Navigating the Global Market for harm reduction vending machines
- Understanding harm reduction vending machines Types and Variations
- Key Industrial Applications of harm reduction vending machines
- Strategic Material Selection Guide for harm reduction vending machines
- In-depth Look: Manufacturing Processes and Quality Assurance for harm reduction vending machines
- Comprehensive Cost and Pricing Analysis for harm reduction vending machines Sourcing
- Spotlight on Potential harm reduction vending machines Manufacturers and Suppliers
- Essential Technical Properties and Trade Terminology for harm reduction vending machines
- Navigating Market Dynamics, Sourcing Trends, and Sustainability in the harm reduction vending machines Sector
- Frequently Asked Questions (FAQs) for B2B Buyers of harm reduction vending machines
- Strategic Sourcing Conclusion and Outlook for harm reduction vending machines
Introduction: Navigating the Global Market for harm reduction vending machines
In an evolving global landscape, the need for innovative solutions to address public health challenges is more pressing than ever. Harm reduction vending machines represent a vital tool in promoting health and safety, particularly in regions significantly affected by substance use issues. These machines not only provide essential supplies—such as clean needles, naloxone, and other health-related products—but also foster a non-judgmental approach to public health. This is crucial for reducing stigma and encouraging individuals to seek help.
This comprehensive guide delves into the multifaceted world of harm reduction vending machines, equipping international B2B buyers with the knowledge needed to make informed sourcing decisions. We will explore various types of machines, the materials used in their construction, and the manufacturing and quality control processes that ensure reliability and safety. Additionally, we will highlight key suppliers in the market, offer insights into cost considerations, and analyze the current market trends.
Buyers from Africa, South America, the Middle East, and Europe, including regions like Indonesia and Thailand, will find actionable insights tailored to their unique contexts. Through a thorough understanding of these components, stakeholders can effectively navigate the complexities of sourcing harm reduction vending machines, ultimately contributing to more robust public health strategies within their communities. This guide empowers you to make strategic decisions that align with both business goals and social responsibility.
Understanding harm reduction vending machines Types and Variations
Type Name | Key Distinguishing Features | Primary B2B Applications | Brief Pros & Cons for Buyers |
---|---|---|---|
Needle Exchange Vending Machine | Dispenses sterile needles and syringes | Public health initiatives, harm reduction programs | Pros: Reduces needle sharing, improves public health; Cons: Initial setup costs may be high. |
Naloxone Dispensing Machine | Provides naloxone kits for opioid overdose prevention | Emergency services, community health organizations | Pros: Saves lives, easy to deploy; Cons: Requires education on use. |
Safe Sex Product Vending Machine | Offers condoms, lubricants, and sexual health resources | Educational institutions, community centers | Pros: Promotes safe practices, increases accessibility; Cons: Limited product range. |
Mental Health Support Kiosk | Provides mental health resources and counseling access | Universities, workplaces, healthcare facilities | Pros: Addresses mental health stigma, fosters community support; Cons: May require ongoing maintenance and updates. |
Substance Use Recovery Kiosk | Connects users with local recovery resources and support | Treatment centers, rehabilitation programs | Pros: Facilitates access to support; Cons: Effectiveness depends on local partnerships. |
Needle Exchange Vending Machine
Needle Exchange Vending Machines are designed to dispense sterile needles and syringes. They are primarily utilized in public health initiatives aimed at reducing the transmission of bloodborne diseases among intravenous drug users. For B2B buyers, key considerations include the machine’s capacity, ease of use, and integration with existing health programs. While the initial investment may be substantial, the long-term benefits in public health and community safety can outweigh the costs.
Naloxone Dispensing Machine
These machines are equipped to provide naloxone kits, essential for reversing opioid overdoses. They are deployed by emergency services and community health organizations to enhance accessibility to life-saving medication. B2B buyers should evaluate the machine’s refill logistics, user interface, and educational materials accompanying the naloxone. The potential to save lives is a significant advantage, though buyers must also consider the need for training and awareness campaigns to ensure effective use.
Safe Sex Product Vending Machine
Safe Sex Product Vending Machines offer items such as condoms and lubricants, promoting sexual health and safety. They are often found in educational institutions and community centers to increase access to protective measures. Buyers should assess the product variety, machine visibility, and potential partnerships with health organizations. While these machines effectively promote safe practices, they may have limitations in the range of products offered, which could affect user satisfaction.
Mental Health Support Kiosk
These kiosks provide access to mental health resources, including brochures, helpline information, and sometimes even virtual counseling options. They are ideal for placement in universities, workplaces, and healthcare facilities, addressing the growing concern of mental health stigma. B2B buyers should consider the machine’s content management system and the frequency of updates to ensure relevant information is available. While they foster community support, ongoing maintenance and resource allocation are necessary for sustained effectiveness.
Substance Use Recovery Kiosk
Substance Use Recovery Kiosks connect individuals with local recovery resources, treatment options, and support networks. These machines can be strategically placed in treatment centers and rehabilitation programs. For buyers, understanding local partnerships and the machine’s ability to provide updated information is crucial for maximizing impact. While they facilitate access to recovery resources, their effectiveness is heavily reliant on the strength of local community ties and services available.
Related Video: Harm Reduction Vending Machines
Key Industrial Applications of harm reduction vending machines
Industry/Sector | Specific Application of harm reduction vending machines | Value/Benefit for the Business | Key Sourcing Considerations for this Application |
---|---|---|---|
Healthcare | Distribution of sterile syringes and naloxone | Reduces needle sharing, saves lives from overdoses | Compliance with health regulations, product safety standards |
Education | Providing safe sex supplies in schools and universities | Promotes health awareness, reduces STIs, and unwanted pregnancies | Customization options, secure payment systems |
Hospitality & Tourism | Offering harm reduction supplies at festivals and events | Enhances guest safety, improves brand reputation | Inventory management, local compliance with laws |
Community Services | Vending machines in community centers for addiction support | Increases accessibility to essential supplies | Partnership with local NGOs, community engagement |
Corporate Wellness | Providing wellness supplies in workplaces | Supports employee health, reduces absenteeism | Integration with existing wellness programs, user-friendly interface |
Healthcare
Harm reduction vending machines in healthcare settings primarily focus on distributing sterile syringes and naloxone. These machines serve as a critical resource for individuals who are at risk of drug overdoses, providing immediate access to life-saving medications. For international B2B buyers, it is essential to ensure compliance with local health regulations and product safety standards. Additionally, the machines must be designed for high usage and easy maintenance to cater to diverse communities, especially in regions with high rates of substance abuse.
Education
In educational institutions, harm reduction vending machines can distribute safe sex supplies, such as condoms and dental dams. This application not only promotes health awareness among students but also plays a significant role in reducing the incidence of sexually transmitted infections (STIs) and unintended pregnancies. Buyers in this sector should consider customization options for branding and secure payment systems to ensure anonymity and accessibility. Collaborating with educational authorities can enhance the implementation of these machines.
Hospitality & Tourism
The hospitality and tourism industry can leverage harm reduction vending machines to offer supplies at festivals, events, and hotels. By providing essential items such as condoms and hygiene kits, businesses can enhance guest safety and improve their brand reputation. For B2B buyers, it is crucial to manage inventory effectively and ensure that the machines comply with local laws regarding the distribution of such supplies. This proactive approach not only mitigates risks but also demonstrates a commitment to guest welfare.
Community Services
Community centers can implement harm reduction vending machines to support individuals dealing with addiction. These machines can dispense supplies such as sterile needles, naloxone, and informational pamphlets. This initiative increases accessibility to essential resources, fostering a more supportive environment for those in recovery. Buyers should focus on forming partnerships with local NGOs to ensure community engagement and support. Additionally, understanding the community’s needs will guide the selection of products offered.
Corporate Wellness
Incorporating harm reduction vending machines into corporate wellness programs can significantly benefit employee health. These machines can provide wellness supplies, such as stress relief products and health information, promoting a healthier workplace. For international B2B buyers, integrating these machines with existing wellness initiatives is key. They should prioritize user-friendly interfaces and ensure that the products meet the diverse needs of employees. This investment not only supports employee well-being but also helps reduce absenteeism and boost productivity.
Related Video: Why Vending?
Strategic Material Selection Guide for harm reduction vending machines
When selecting materials for harm reduction vending machines, it is essential to consider properties that directly impact performance, durability, and compliance with international standards. Below is an analysis of four common materials used in the construction of these machines, focusing on their key properties, advantages, disadvantages, and implications for international B2B buyers.
Stainless Steel
Key Properties:
Stainless steel is known for its excellent corrosion resistance, high strength, and ability to withstand extreme temperatures. It typically has a temperature rating of up to 800°C and can handle moderate pressure levels.
Pros & Cons:
Stainless steel is highly durable and requires minimal maintenance, making it suitable for outdoor environments. However, it is more expensive than other materials, which can impact initial investment costs. Manufacturing complexity can also be higher due to the need for specialized equipment.
Impact on Application:
This material is compatible with various media, including liquids and gases, and is particularly effective in environments where hygiene is critical, such as dispensing medical supplies.
Considerations for International Buyers:
Buyers should ensure compliance with standards like ASTM A240 for stainless steel grades. In regions like Africa and South America, where cost sensitivity is high, the initial investment might be a barrier despite long-term savings.
High-Density Polyethylene (HDPE)
Key Properties:
HDPE is a lightweight, durable thermoplastic known for its excellent impact resistance and chemical stability. It can withstand temperatures up to 120°C and is resistant to many solvents and acids.
Pros & Cons:
The primary advantage of HDPE is its cost-effectiveness and ease of manufacturing, which allows for rapid production. However, it is less durable than metals and can degrade under UV exposure unless treated.
Impact on Application:
HDPE is suitable for storing and dispensing consumables, particularly in environments where chemical exposure is a concern. Its flexibility makes it ideal for various designs.
Considerations for International Buyers:
Compliance with local regulations regarding plastic materials is crucial. In the Middle East and Europe, buyers should check for adherence to standards like DIN EN ISO 1183.
Aluminum
Key Properties:
Aluminum is lightweight and has good corrosion resistance, with a temperature rating of around 200°C. It is also known for its strength-to-weight ratio, making it an attractive option for portable vending machines.
Pros & Cons:
Aluminum is relatively inexpensive and easy to machine, but it can be less durable than stainless steel in high-stress applications. It is also more susceptible to corrosion if not properly treated.
Impact on Application:
Ideal for environments where weight is a concern, aluminum is suitable for mobile harm reduction vending machines. However, its lower strength may limit its use in high-impact scenarios.
Considerations for International Buyers:
Buyers should be aware of the need for anodization or other protective coatings to enhance durability. Compliance with JIS standards can also be a consideration in Asian markets.
Glass Reinforced Plastic (GRP)
Key Properties:
GRP combines fiberglass with resin, providing excellent strength and corrosion resistance. It can withstand temperatures up to 80°C and is highly resistant to chemicals.
Pros & Cons:
The primary advantage of GRP is its lightweight nature and high durability, making it suitable for various applications. However, it can be more expensive than traditional plastics and may require specialized manufacturing processes.
Impact on Application:
GRP is ideal for environments where corrosion is a significant concern, such as coastal areas or regions with high humidity.
Considerations for International Buyers:
Understanding local regulations regarding composite materials is essential, particularly in Europe, where stringent environmental standards exist. Buyers should also consider the availability of skilled labor for manufacturing and maintenance.
Summary Table
Material | Typical Use Case for harm reduction vending machines | Key Advantage | Key Disadvantage/Limitation | Relative Cost (Low/Med/High) |
---|---|---|---|---|
Stainless Steel | Outdoor machines, medical supply dispensing | Excellent durability and corrosion resistance | Higher initial cost, complex manufacturing | High |
High-Density Polyethylene (HDPE) | Storing and dispensing consumables | Cost-effective, easy to manufacture | Less durable, UV degradation | Low |
Aluminum | Portable vending machines | Lightweight, cost-effective | Less durable under stress, corrosion risk | Medium |
Glass Reinforced Plastic (GRP) | Corrosive environments, coastal areas | High strength and corrosion resistance | Higher cost, specialized manufacturing | Medium |
This guide provides actionable insights for international B2B buyers, ensuring they can make informed decisions about material selection for harm reduction vending machines based on their specific regional needs and compliance requirements.
In-depth Look: Manufacturing Processes and Quality Assurance for harm reduction vending machines
The manufacturing process for harm reduction vending machines involves several critical stages, each contributing to the overall efficiency and reliability of the end product. Understanding these stages can empower B2B buyers to make informed decisions when sourcing these machines.
Manufacturing Process Overview
1. Material Preparation
The first stage focuses on the selection and preparation of materials. Common materials used include stainless steel for durability, tempered glass for visibility, and various plastics for internal components. Buyers should ensure that suppliers use high-quality, non-toxic materials, especially given the health implications associated with harm reduction initiatives.
Key Techniques:
– Material Sourcing: Verify that suppliers source materials from reputable vendors, emphasizing sustainability and compliance with local regulations.
– Pre-processing: This includes cutting, machining, and treating materials to enhance performance and longevity.
2. Forming
The forming stage involves shaping the prepared materials into components of the vending machine. Various techniques are employed depending on the material and design specifications.
Key Techniques:
– CNC Machining: Provides precision in creating complex parts.
– Injection Molding: Used for producing plastic components in large quantities with consistent quality.
– Laser Cutting: Ensures clean edges and intricate designs, particularly for metal parts.
3. Assembly
Once the components are formed, they undergo assembly. This stage is crucial for ensuring that all parts fit together correctly and function as intended.
Key Techniques:
– Modular Assembly: Allows for easy installation and maintenance, which is vital for machines that may be deployed in diverse environments.
– Quality Fixtures: Utilize jigs and fixtures to enhance accuracy during assembly, reducing the likelihood of defects.
4. Finishing
The finishing stage enhances the aesthetic and functional properties of the vending machine. This includes painting, coating, and surface treatments to prevent corrosion and improve durability.
Key Techniques:
– Powder Coating: Provides a robust, long-lasting finish that is resistant to scratches and chemicals.
– Screen Printing: Used for branding and user interface elements, ensuring clarity and visibility.
Quality Assurance Practices
Quality assurance (QA) is critical in the manufacturing of harm reduction vending machines, ensuring they meet international standards and are safe for public use.
Relevant International Standards
- ISO 9001: A general quality management standard that ensures consistent quality in products and services.
- CE Marking: Indicates compliance with European health, safety, and environmental protection standards.
- API Standards: Particularly relevant if the vending machine dispenses medical products, ensuring that they meet necessary health regulations.
Quality Control Checkpoints
To maintain product quality throughout the manufacturing process, several quality control (QC) checkpoints should be implemented:
- Incoming Quality Control (IQC): Involves inspecting raw materials upon delivery to ensure they meet specified standards.
- In-Process Quality Control (IPQC): Continuous monitoring during the manufacturing process to detect and correct defects early.
- Final Quality Control (FQC): A thorough inspection of the completed machines before shipment to ensure they meet all specifications and standards.
Common Testing Methods
Testing is vital to confirm the functionality and safety of vending machines. Common methods include:
– Electrical Testing: Ensures that all electrical components function correctly and safely.
– Durability Testing: Simulates real-world use over an extended period to assess reliability.
– User Experience Testing: Evaluates the interface and ease of use, ensuring that the machine is intuitive for end users.
Verifying Supplier Quality Control
B2B buyers must have robust methods to verify the quality control processes of suppliers. Here are actionable steps:
- Supplier Audits: Conduct on-site audits to assess manufacturing practices and quality control systems.
- Request QC Reports: Ask suppliers for detailed reports on QC procedures, including testing results and compliance certifications.
- Engage Third-Party Inspectors: Utilize third-party inspection services to validate the quality and compliance of machines before shipment. This is especially important for buyers in regions with stringent regulatory requirements.
Quality Control and Certification Nuances for International Buyers
When sourcing harm reduction vending machines, international buyers from regions such as Africa, South America, the Middle East, and Europe should consider regional regulations and certifications that may differ from global standards.
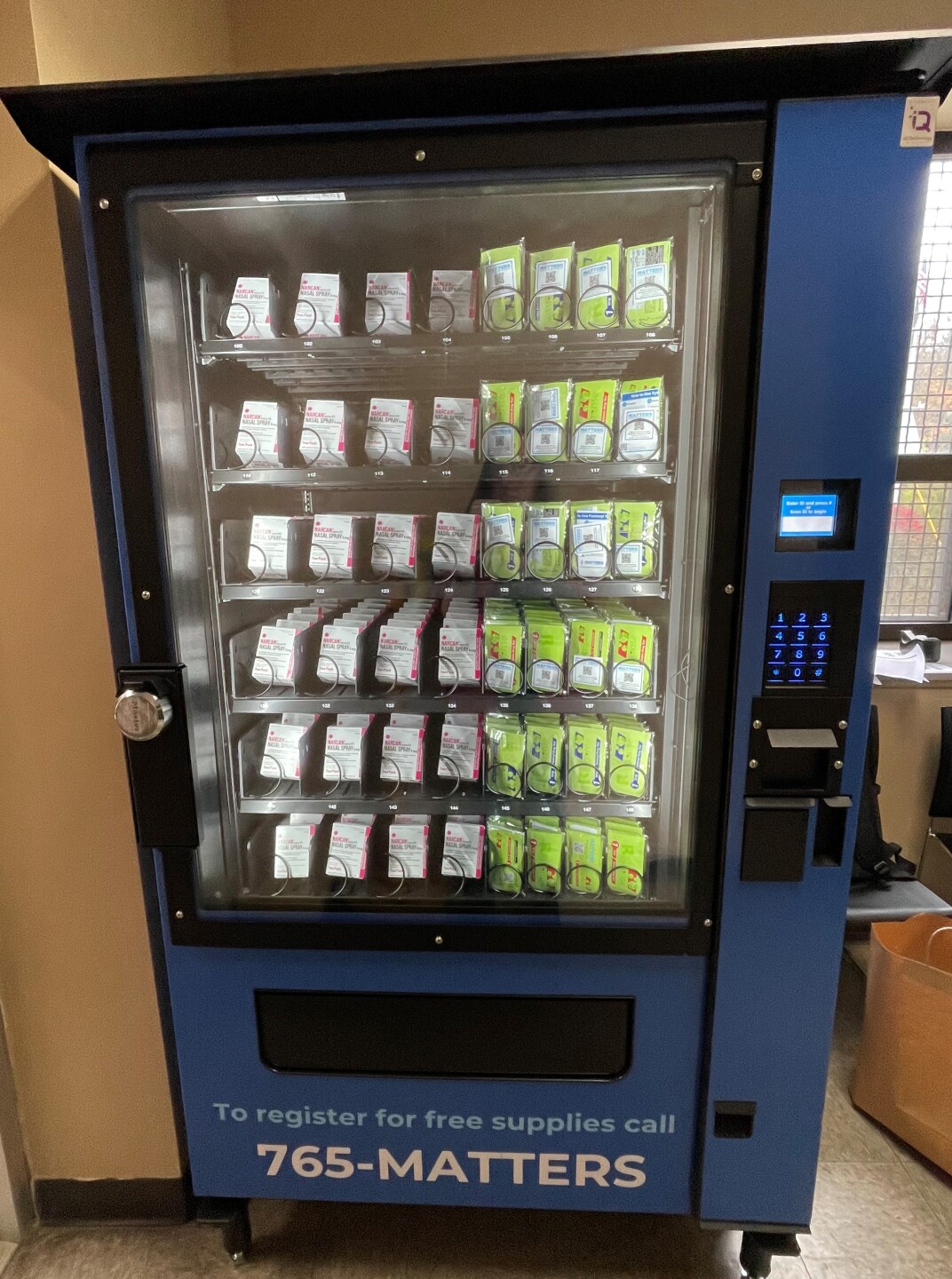
Illustrative Image (Source: Google Search)
- Local Regulations: Ensure that the product complies with local laws regarding health and safety, which may require additional certifications.
- Cultural Sensitivities: Consider the cultural context in which the vending machines will operate, as this may influence design and functionality.
- Import Regulations: Be aware of import tariffs and compliance requirements that may affect the cost and feasibility of sourcing from different regions.
Conclusion
A comprehensive understanding of the manufacturing processes and quality assurance practices for harm reduction vending machines can significantly enhance the decision-making capabilities of B2B buyers. By focusing on quality, compliance, and supplier verification, buyers can ensure they procure reliable and effective solutions tailored to their specific regional needs.
Related Video: Amazing Production Process with Modern Machines and Skilful Workers
Comprehensive Cost and Pricing Analysis for harm reduction vending machines Sourcing
When considering the sourcing of harm reduction vending machines, understanding the comprehensive cost structure is crucial for international B2B buyers. This analysis encompasses various cost components that collectively contribute to the final pricing of these machines.
Cost Components
-
Materials: The primary materials used in vending machine construction include high-grade metals, plastics, and electronic components. Quality and sourcing of these materials can significantly affect costs. For instance, sourcing locally in Africa or South America may reduce shipping costs but could limit material options.
-
Labor: Labor costs can vary widely based on the region. In Europe, labor costs are typically higher due to stringent labor laws and wage expectations. Conversely, in regions like Africa and South America, labor may be more affordable, but quality and skills can vary greatly.
-
Manufacturing Overhead: This refers to indirect costs such as utilities, rent, and administrative expenses associated with production. Manufacturing overhead can be optimized through efficient processes, which can be a negotiation point with suppliers.
-
Tooling: Customization of vending machines often requires specific tooling, which can be a significant upfront cost. Buyers should consider whether the tooling costs can be amortized over a larger production run to reduce per-unit costs.
-
Quality Control (QC): Ensuring that each machine meets international standards necessitates a dedicated QC process, which adds to overall costs. It’s beneficial for buyers to inquire about the QC measures suppliers implement to ensure reliability and compliance.
-
Logistics: Transportation costs can vary drastically depending on the shipping method, distance, and any customs duties or tariffs applicable. Buyers should evaluate Incoterms carefully to understand their responsibilities and potential additional costs.
-
Margin: Suppliers typically build a margin into the pricing structure, which can vary based on competition and market demand. Understanding market dynamics can empower buyers to negotiate better terms.
Price Influencers
Several factors can influence the pricing of harm reduction vending machines:
-
Volume/MOQ: Higher order volumes usually lead to reduced per-unit costs. Buyers should assess their needs and consider negotiating for a lower minimum order quantity (MOQ) if they are just starting.
-
Specifications/Customization: Custom features or specifications can significantly increase costs. Buyers should weigh the benefits of customization against the potential for increased expenses.
-
Materials and Quality/Certifications: The choice of materials and the certifications required (such as ISO standards) can impact pricing. Suppliers with recognized certifications may charge a premium but offer better quality assurance.
-
Supplier Factors: The reputation and reliability of suppliers can affect costs. Established suppliers may offer higher prices but come with assurances of quality and service, reducing long-term risks.
-
Incoterms: Understanding the implications of Incoterms on shipping responsibilities and costs is essential. For example, choosing DDP (Delivered Duty Paid) can simplify logistics but may come with a higher initial price.
Buyer Tips
-
Negotiation: Engage suppliers in discussions about pricing structures. Be prepared to provide insights into your purchasing potential, which can lead to more favorable terms.
-
Cost-Efficiency: Always calculate the Total Cost of Ownership (TCO), which includes not only the purchase price but also operational, maintenance, and disposal costs over the machine’s lifecycle.
-
Pricing Nuances: International buyers, especially from regions like Africa and South America, should be cognizant of currency fluctuations and economic conditions that could affect pricing. Building relationships with local suppliers can help mitigate some of these risks.
-
Research and Due Diligence: Conduct thorough research on potential suppliers, their product offerings, and their reputations. This can avoid potential pitfalls and ensure informed decision-making.
Disclaimer
Prices mentioned in discussions around harm reduction vending machines may vary significantly based on market conditions, specific buyer requirements, and supplier negotiations. Always seek updated quotes and conduct comprehensive evaluations before finalizing any purchasing decisions.
Spotlight on Potential harm reduction vending machines Manufacturers and Suppliers
- (No specific manufacturer data was available or requested for detailed profiling in this section for harm reduction vending machines.)*
Essential Technical Properties and Trade Terminology for harm reduction vending machines
Key Technical Properties of Harm Reduction Vending Machines
In the procurement of harm reduction vending machines, understanding their technical properties is essential for ensuring compliance, efficiency, and user satisfaction. Below are critical specifications that international B2B buyers should consider:
-
Material Grade
– Definition: The quality and type of materials used in the construction of the vending machine, such as stainless steel, aluminum, or high-density plastics.
– Importance: Higher-grade materials enhance durability, corrosion resistance, and overall lifecycle of the machine, which is crucial for maintaining hygiene in harm reduction applications. -
Tolerance
– Definition: The permissible limit or limits of variation in a physical dimension of the machine components.
– Importance: Tight tolerances ensure that machine parts fit together correctly, which is vital for functionality and reliability. This is particularly important in environments where precision is needed to dispense items safely. -
Power Consumption
– Definition: The amount of electrical power required to operate the vending machine.
– Importance: Efficient power consumption not only reduces operational costs but also minimizes environmental impact. Buyers must consider energy efficiency to align with sustainability goals. -
User Interface Design
– Definition: The layout and functionality of the machine’s control panel and display.
– Importance: A user-friendly interface is vital for accessibility, especially in diverse markets. Intuitive controls can enhance user experience and promote higher usage rates among target demographics. -
Capacity and Dimensions
– Definition: The volume of products the machine can hold and its physical size.
– Importance: Understanding capacity allows buyers to evaluate stock turnover and ensure that the machine fits within designated spaces. This is crucial for maximizing the machine’s utility in various environments. -
Connectivity Features
– Definition: The machine’s ability to connect with internet-based systems for remote monitoring and inventory management.
– Importance: Connectivity features enable real-time data tracking, improving inventory management and reducing downtime. This is particularly beneficial for monitoring usage patterns and product demand.
Common Trade Terminology
Familiarity with industry terminology can greatly assist B2B buyers in making informed decisions. Here are some essential terms:
-
OEM (Original Equipment Manufacturer)
– Definition: A company that produces parts or equipment that may be marketed by another manufacturer.
– Relevance: Understanding OEM relationships is crucial for sourcing components and ensuring product quality, especially when tailoring machines to specific market needs. -
MOQ (Minimum Order Quantity)
– Definition: The smallest number of units a supplier is willing to sell.
– Relevance: Knowing the MOQ helps buyers manage budgets and inventory levels, particularly important for smaller organizations or new market entrants. -
RFQ (Request for Quotation)
– Definition: A document sent to suppliers requesting price and other details for a specific quantity of goods.
– Relevance: Issuing an RFQ enables buyers to compare prices and terms from multiple suppliers, ensuring they secure the best deals available. -
Incoterms (International Commercial Terms)
– Definition: A set of predefined international trade terms published by the International Chamber of Commerce (ICC).
– Relevance: Familiarity with Incoterms is vital for understanding the responsibilities of buyers and sellers in terms of shipping, insurance, and risk management. -
Lead Time
– Definition: The time it takes from placing an order to receiving the goods.
– Relevance: Understanding lead times is essential for inventory planning and ensuring timely availability of products in the market.
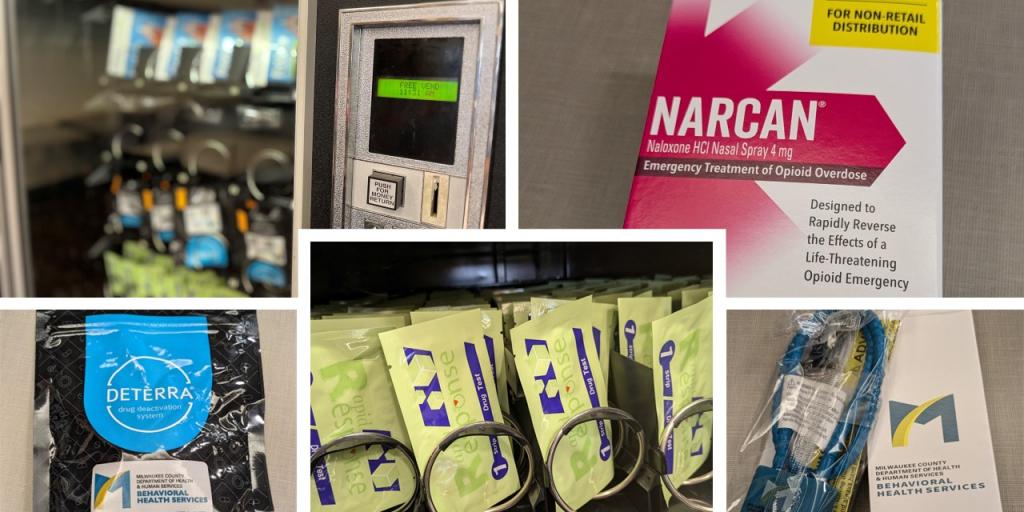
Illustrative Image (Source: Google Search)
- Warranty and Support Terms
– Definition: Conditions under which the manufacturer or supplier will repair or replace defective products.
– Relevance: Clear warranty terms are crucial for risk management, providing assurance of product reliability and support in case of issues.
By grasping these essential technical properties and trade terminologies, international B2B buyers can make informed decisions when sourcing harm reduction vending machines, ultimately enhancing their operational efficiency and service delivery.
Navigating Market Dynamics, Sourcing Trends, and Sustainability in the harm reduction vending machines Sector
Market Overview & Key Trends
The harm reduction vending machines sector is experiencing significant growth as global awareness of addiction issues and the need for safer access to harm reduction supplies increases. International B2B buyers, particularly from regions such as Africa, South America, the Middle East, and Europe, should note several key drivers influencing this market. Firstly, public health initiatives and government policies are increasingly supportive of harm reduction strategies, leading to greater acceptance and installation of vending machines that dispense safe injection equipment, naloxone, and other essential supplies.
Emerging technologies are also reshaping the landscape of harm reduction vending machines. Features such as cashless payment options, real-time inventory tracking, and user-friendly interfaces are becoming standard. Additionally, machine connectivity through IoT (Internet of Things) allows for data collection, enabling operators to optimize service delivery based on user patterns and local needs. This technological evolution presents opportunities for B2B buyers to invest in state-of-the-art solutions that enhance operational efficiency and user engagement.
Market dynamics reflect a growing trend toward localized sourcing and customization. Buyers are encouraged to engage with local suppliers who understand the specific cultural and regulatory contexts of their regions. This approach not only supports local economies but also ensures that the machines meet community-specific needs, fostering greater acceptance and use.
Sustainability & Ethical Sourcing in B2B
Sustainability is becoming a critical consideration in the harm reduction vending machine sector. The environmental impact of manufacturing and operating these machines is under scrutiny, with stakeholders advocating for eco-friendly practices. International buyers should prioritize suppliers that utilize sustainable materials and practices in their vending machine production. This includes the use of recycled materials and energy-efficient technologies that minimize the carbon footprint.
Ethical sourcing is equally vital. Buyers should seek partnerships with suppliers who maintain transparency in their supply chains and adhere to fair labor practices. Certifications such as ISO 14001 for environmental management and Fair Trade can serve as indicators of a supplier’s commitment to sustainability and ethical practices. By aligning with these principles, B2B buyers not only enhance their corporate social responsibility (CSR) profiles but also appeal to a growing segment of environmentally conscious consumers.
Brief Evolution/History
The concept of harm reduction vending machines has evolved significantly over the past two decades. Initially conceived as a response to public health crises such as the HIV/AIDS epidemic, these machines have expanded to address a wider range of substance use issues. The introduction of vending machines in various countries has demonstrated their effectiveness in increasing access to harm reduction supplies while reducing stigma associated with their use.
In recent years, the sector has gained further momentum due to increasing recognition of addiction as a public health issue rather than a criminal one. As a result, vending machines have become an innovative solution for delivering essential services quickly and discreetly, marking a pivotal shift in how communities approach harm reduction. International buyers today have the opportunity to leverage this evolution by investing in modern, sustainable solutions that align with global health objectives.
Related Video: Is global trade transforming? | Counting the Cost
Frequently Asked Questions (FAQs) for B2B Buyers of harm reduction vending machines
-
What should I consider when vetting suppliers of harm reduction vending machines?
When vetting suppliers, prioritize their experience in the harm reduction sector and the quality of their machines. Look for certifications that demonstrate compliance with health and safety standards, such as ISO or CE marks. Engage with references or case studies from previous clients to assess their reliability and service history. Additionally, consider their commitment to after-sales support, including maintenance and spare parts availability, which is crucial for ongoing operations. -
Can harm reduction vending machines be customized to meet local needs?
Yes, many suppliers offer customization options to cater to specific local requirements, such as language, product selection, and design. It’s essential to communicate your needs clearly during the negotiation process. Discuss features like payment methods that align with local preferences, and explore options for branding to enhance community engagement. Customization can significantly improve acceptance and effectiveness in diverse markets. -
What are the typical minimum order quantities (MOQ) and lead times for these machines?
MOQs can vary widely depending on the supplier and the complexity of the machine. Some manufacturers may require a minimum order of five to ten units, while others might accommodate smaller orders. Lead times also vary based on customization requests and production capacity, generally ranging from a few weeks to several months. Always clarify these terms before finalizing your order to ensure they align with your project timelines. -
How should I handle payment terms when purchasing vending machines internationally?
Payment terms can differ significantly by region and supplier. Common options include upfront payments, letters of credit, or payment upon delivery. Consider using secure payment methods that provide buyer protection, such as escrow services. Negotiate terms that allow flexibility, especially if you’re ordering customized machines. Ensure that the payment schedule aligns with your budget and project timelines to avoid cash flow issues. -
What quality assurance measures should I expect from suppliers?
Reputable suppliers should provide detailed quality assurance (QA) protocols, including product testing for safety and functionality before shipment. Request copies of any QA certifications and inspection reports. It’s also wise to inquire about warranties and return policies for defective machines. Establishing a clear understanding of these measures can protect your investment and ensure that you receive machines that meet your operational standards. -
What logistics considerations should I keep in mind for international shipping?
When planning logistics, consider the shipping method, customs regulations, and potential tariffs in your country. Work with suppliers who have experience in exporting vending machines and can provide guidance on necessary documentation, such as invoices and certificates of origin. Additionally, account for potential delays in shipping due to customs clearance. Collaborating with a reliable freight forwarder can facilitate smoother logistics management. -
How can disputes with suppliers be effectively resolved?
Disputes can arise over various issues, including delivery delays or product quality. To mitigate potential conflicts, establish clear terms in your purchase agreement, including a dispute resolution process. This may involve mediation or arbitration rather than litigation, which can be costly and time-consuming. Maintain open communication with your supplier throughout the process to address concerns promptly and maintain a positive working relationship. -
What regulatory considerations should I be aware of when sourcing harm reduction vending machines?
Regulatory requirements can vary significantly by region, impacting the types of products you can distribute through vending machines. Research local laws regarding harm reduction initiatives, product approval processes, and health regulations. Engage with local health authorities to ensure compliance and understand any licensing requirements. Being proactive about regulatory considerations can help you avoid legal complications and enhance the credibility of your initiative.
Strategic Sourcing Conclusion and Outlook for harm reduction vending machines
As the landscape of harm reduction continues to evolve, strategic sourcing emerges as a critical component for international B2B buyers looking to invest in vending machines that offer essential support for public health initiatives. Key takeaways from this guide highlight the importance of understanding local needs, regulatory frameworks, and community engagement to ensure that products meet the demands of diverse markets across Africa, South America, the Middle East, and Europe.
Value of Strategic Sourcing:
– Adaptability: Tailor offerings to align with regional health challenges and cultural contexts.
– Cost Efficiency: Leverage competitive pricing and favorable terms through well-negotiated supplier relationships.
– Quality Assurance: Prioritize suppliers who demonstrate compliance with health standards and sustainability practices.
Looking ahead, the potential for harm reduction vending machines is vast. International buyers are encouraged to actively engage with suppliers who are innovative in their approach, committed to social responsibility, and equipped to navigate the regulatory landscapes of different regions. By prioritizing strategic sourcing, businesses can not only enhance their operational efficiency but also contribute to meaningful health outcomes in communities worldwide. The time to invest in this transformative technology is now—embrace the opportunity to make a difference while driving sustainable growth.