Master Sourcing Costco Vending Machines for Unmatched B2B
Guide to Costco Vending Machine
- Introduction: Navigating the Global Market for costco vending machine
- Understanding costco vending machine Types and Variations
- Key Industrial Applications of costco vending machine
- Strategic Material Selection Guide for costco vending machine
- In-depth Look: Manufacturing Processes and Quality Assurance for costco vending machine
- Comprehensive Cost and Pricing Analysis for costco vending machine Sourcing
- Cost Structure of Costco Vending Machines
- Spotlight on Potential costco vending machine Manufacturers and Suppliers
- Essential Technical Properties and Trade Terminology for costco vending machine
- Navigating Market Dynamics, Sourcing Trends, and Sustainability in the costco vending machine Sector
- Frequently Asked Questions (FAQs) for B2B Buyers of costco vending machine
- Strategic Sourcing Conclusion and Outlook for costco vending machine
Introduction: Navigating the Global Market for costco vending machine
Costco vending machines represent a strategic opportunity for international B2B buyers looking to enhance their product distribution and retail offerings. With a reputation for quality and value, these machines provide a unique avenue for businesses to tap into Costco’s extensive supply chain and product range, catering to a diverse clientele. Whether you are a buyer in Africa, South America, the Middle East, or Europe, understanding the nuances of sourcing and operating Costco vending machines can significantly impact your bottom line.
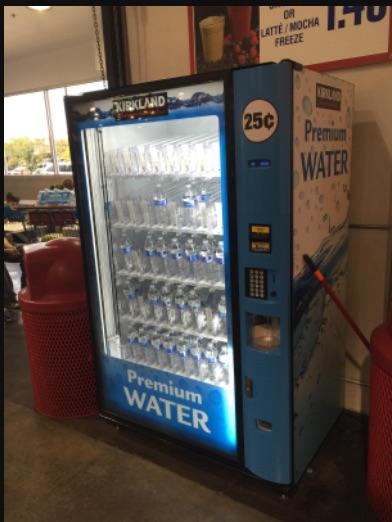
Illustrative Image (Source: Google Search)
This comprehensive guide delves into the various types of Costco vending machines available, the materials used in their construction, and the manufacturing and quality control processes that ensure reliability and longevity. It also highlights key suppliers, pricing structures, and market insights to empower informed purchasing decisions. Additionally, we address frequently asked questions to provide clarity on common concerns and considerations when integrating these machines into your business model.
By equipping yourself with this knowledge, you can navigate the complexities of the global market effectively. Understanding the benefits and operational aspects of Costco vending machines will enable you to make strategic sourcing decisions that align with your business goals, enhance customer satisfaction, and drive sales growth in your region.
Understanding costco vending machine Types and Variations
Type Name | Key Distinguishing Features | Primary B2B Applications | Brief Pros & Cons for Buyers |
---|---|---|---|
Snack and Beverage Vending Machine | Offers a wide range of snacks and drinks; typically compact. | Office break rooms, schools, gyms. | Pros: Easy to restock; high demand. Cons: Limited product variety compared to other types. |
Healthy Options Vending Machine | Focuses on nutritious snacks and beverages; often features fresh items. | Health clubs, corporate offices, schools. | Pros: Appeals to health-conscious consumers; can enhance brand image. Cons: Higher initial cost; may require more frequent restocking. |
Specialty Product Vending Machine | Dispenses niche items such as electronics, cosmetics, or gourmet food. | Airports, shopping malls, hotels. | Pros: Unique offerings can attract foot traffic; higher profit margins. Cons: Higher maintenance; specific target market may limit sales. |
Automated Retail Kiosk | Combines vending with technology; often includes touchscreen interfaces. | Retail stores, trade shows, events. | Pros: Interactive experience; can collect consumer data. Cons: Requires technical support; higher upfront investment. |
Coffee Vending Machine | Provides various coffee beverages, often with customizable options. | Offices, hotels, cafes. | Pros: High demand for coffee; can enhance customer satisfaction. Cons: Requires regular maintenance and cleaning. |
Snack and Beverage Vending Machine
Snack and beverage vending machines are the most common type found in various settings. They typically offer a wide selection of snacks and drinks, making them suitable for locations like office break rooms, schools, and gyms. B2B buyers should consider the demand in their target market, as these machines are easy to restock and maintain. However, they tend to have limited product variety compared to more specialized machines, which may not meet all consumer preferences.
Healthy Options Vending Machine
These machines are designed to cater to the growing demand for healthier snack choices. They often include fresh items such as salads, fruits, and low-calorie snacks, making them ideal for health clubs, corporate offices, and educational institutions. B2B buyers should evaluate the health trends in their region, as these machines can enhance a company’s brand image. While they attract health-conscious consumers, they may also come with a higher initial cost and require more frequent restocking to maintain freshness.
Specialty Product Vending Machine
Specialty product vending machines focus on niche markets by offering unique items like electronics, cosmetics, or gourmet food. These machines are often found in high-traffic areas such as airports, shopping malls, and hotels, where they can attract a specific audience. B2B buyers should assess the potential foot traffic and consumer interests in their location, as these machines can yield higher profit margins. However, they may require more maintenance and a clear understanding of the target market to ensure profitability.
Automated Retail Kiosk
Automated retail kiosks blend vending with modern technology, often featuring touchscreen interfaces that allow for a more interactive consumer experience. These kiosks are suitable for retail stores, trade shows, and events, where engaging customers can drive sales. B2B buyers should consider the investment in technology and the potential for data collection to enhance marketing strategies. While these kiosks can provide a unique shopping experience, they also necessitate technical support and a higher upfront investment.
Coffee Vending Machine
Coffee vending machines are designed to meet the high demand for coffee beverages, often providing customizable options such as lattes, cappuccinos, and espressos. They are commonly found in offices, hotels, and cafes, where they can significantly enhance customer satisfaction. B2B buyers should consider the preferences of their clientele, as these machines can be a valuable addition to any establishment. However, they require regular maintenance and cleaning to ensure optimal performance and customer enjoyment.
Related Video: Machine Learning in 2024 – Beginner’s Course
Key Industrial Applications of costco vending machine
Industry/Sector | Specific Application of Costco Vending Machine | Value/Benefit for the Business | Key Sourcing Considerations for this Application |
---|---|---|---|
Hospitality | Guest amenities in hotels and resorts | Enhances guest experience with convenient access to snacks and beverages | Bulk purchasing agreements, product variety, and quality assurance |
Education | Campus snack stations in universities | Provides quick, healthy snack options for students and staff | Nutritional value of products, compliance with dietary needs |
Corporate Offices | Employee break rooms and lounges | Increases employee satisfaction and productivity with easy access to refreshments | Supply chain reliability, product turnover rates, and cost efficiency |
Healthcare Facilities | Patient and visitor vending solutions | Offers accessible food and beverage options for patients and visitors | Compliance with health regulations, product freshness, and variety |
Manufacturing | Break rooms in factories | Provides employees with quick meals and snacks, improving morale | Machine durability, maintenance requirements, and product selection |
Hospitality
In the hospitality industry, Costco vending machines serve as convenient guest amenities in hotels and resorts. By providing easy access to snacks and beverages, these machines enhance the overall guest experience, catering to varying preferences and dietary restrictions. International buyers, particularly from regions like Africa and the Middle East, should consider bulk purchasing agreements to ensure a diverse product range that aligns with local tastes. Additionally, quality assurance is crucial to maintain brand reputation.
Education
Costco vending machines are increasingly being utilized in educational institutions, particularly on university campuses. These machines offer quick and healthy snack options for students and staff, addressing the need for convenient food solutions during busy schedules. Buyers from South America and Europe should focus on the nutritional value of the products offered, ensuring compliance with dietary needs and preferences prevalent in their regions. This attention to detail can foster a healthier campus environment.
Corporate Offices
In corporate settings, installing Costco vending machines in employee break rooms and lounges can significantly boost employee satisfaction and productivity. By providing easy access to refreshments, companies can create a more enjoyable work environment. B2B buyers in Europe and Africa should prioritize sourcing machines with reliable supply chains to maintain product turnover rates and cost efficiency, ensuring that employees always have access to fresh snacks.
Healthcare Facilities
Healthcare facilities are adopting Costco vending machines to provide accessible food and beverage options for patients and visitors. These machines can help address the needs of individuals who may have limited access to food options while in care. Buyers from the Middle East and Africa must ensure compliance with health regulations and focus on product freshness and variety to cater to diverse dietary requirements, enhancing the experience for all stakeholders involved.
Manufacturing
In manufacturing environments, Costco vending machines can serve break rooms, providing employees with quick meals and snacks that improve morale. International B2B buyers, particularly from regions with high manufacturing activity, should consider the durability and maintenance requirements of the machines to ensure long-term service. Additionally, a well-curated product selection can meet the varied preferences of a diverse workforce, further enhancing employee satisfaction.
Related Video: How to Start a Vending Machine Business, Cost, Tips, How Much You Make
Strategic Material Selection Guide for costco vending machine
Material Analysis for Costco Vending Machines
In the design and manufacturing of vending machines for Costco, selecting the right materials is crucial for ensuring durability, functionality, and cost-effectiveness. Here, we analyze four common materials used in vending machines, focusing on their properties, advantages, disadvantages, and specific considerations for international B2B buyers.
1. Stainless Steel
Key Properties:
Stainless steel is known for its excellent corrosion resistance, high strength, and ability to withstand high temperatures and pressures. It typically has a temperature rating up to 800°F (427°C) and can handle various environmental conditions without degrading.
Pros & Cons:
Stainless steel is highly durable and resistant to rust and staining, making it ideal for vending machines that may be exposed to moisture. However, it can be more expensive than other materials and may require specialized manufacturing techniques, increasing production complexity.
Impact on Application:
Stainless steel is compatible with a wide range of media, including food and beverages, ensuring safety and hygiene. Its non-reactive nature helps maintain product integrity.
Considerations for International Buyers:
Buyers should ensure compliance with international food safety standards, such as those set by the FDA or EFSA. Additionally, different grades (e.g., 304, 316) may be preferred based on local regulations, particularly in regions like Europe and the Middle East.
2. Carbon Steel
Key Properties:
Carbon steel offers good tensile strength and is suitable for general service applications. Its temperature rating can vary but typically withstands up to 500°F (260°C).
Pros & Cons:
It is cost-effective and widely available, making it a popular choice for structural components. However, carbon steel is susceptible to corrosion, necessitating protective coatings or treatments, which can add to manufacturing complexity.
Impact on Application:
Carbon steel is suitable for non-corrosive environments but may not be ideal for machines exposed to high humidity or wet conditions.
Considerations for International Buyers:
Buyers should be aware of local standards regarding corrosion resistance and may need to ensure compliance with ASTM or DIN standards, especially in regions like Africa and South America where environmental conditions can vary significantly.
3. Polycarbonate
Key Properties:
Polycarbonate is a high-impact thermoplastic known for its transparency, high strength, and resistance to UV light. It can withstand temperatures up to 250°F (121°C) and has excellent dimensional stability.
Pros & Cons:
This material is lightweight and offers good insulation properties, making it suitable for display panels and protective covers. However, it can be more expensive than other plastics and may not be as durable as metals in high-stress environments.
Impact on Application:
Polycarbonate is ideal for transparent components, allowing visibility of products while providing protection. Its chemical resistance makes it suitable for various applications, including food and beverage vending.
Considerations for International Buyers:
When sourcing polycarbonate, buyers should check for compliance with relevant safety standards, such as those set by the EU for food contact materials. The availability of specific grades may also vary by region.
4. Aluminum
Key Properties:
Aluminum is lightweight, corrosion-resistant, and has good thermal conductivity. It can handle temperatures up to 600°F (316°C) and is known for its malleability.
Pros & Cons:
Aluminum is cost-effective and easy to work with, making it suitable for various components in vending machines. However, it may not provide the same strength as stainless steel and can be prone to denting.
Impact on Application:
Aluminum is suitable for structural applications and exterior panels, providing a good balance between weight and strength. Its corrosion resistance makes it ideal for outdoor or humid environments.
Considerations for International Buyers:
Buyers should consider local recycling regulations, as aluminum is highly recyclable. Compliance with standards like JIS in Japan or EN in Europe may also be necessary, depending on the target market.
Summary Table
Material | Typical Use Case for Costco Vending Machine | Key Advantage | Key Disadvantage/Limitation | Relative Cost (Low/Med/High) |
---|---|---|---|---|
Stainless Steel | Structural components, food contact surfaces | Excellent corrosion resistance | Higher cost, complex manufacturing | High |
Carbon Steel | Frame and structural elements for non-corrosive areas | Cost-effective, good strength | Susceptible to corrosion | Low |
Polycarbonate | Display panels, protective covers | Lightweight, good impact resistance | More expensive, less durable than metals | Medium |
Aluminum | Exterior panels, structural components | Lightweight, corrosion-resistant | Less strength than stainless steel | Medium |
This strategic material selection guide provides international B2B buyers with essential insights into choosing the right materials for Costco vending machines, ensuring compliance with local standards and optimizing product performance.
In-depth Look: Manufacturing Processes and Quality Assurance for costco vending machine
Manufacturing Processes for Costco Vending Machines
The manufacturing process of Costco vending machines encompasses several key stages, ensuring that the final product meets the high standards of quality and functionality expected by B2B buyers. Understanding these stages can help international buyers from regions such as Africa, South America, the Middle East, and Europe to make informed procurement decisions.
Material Preparation
The first stage in the manufacturing process involves the careful selection and preparation of materials. Common materials for vending machines include:
- Metal: Typically steel or aluminum for structural integrity and durability.
- Plastics: Used for various components, such as buttons and display panels, ensuring lightweight and cost-effective production.
- Electrical Components: Including wiring, motors, and sensors that are crucial for the machine’s operation.
Suppliers must ensure that all materials comply with relevant international standards, such as ISO 9001, which outlines quality management systems. This compliance is critical for maintaining product quality and safety.
Forming
Once materials are prepared, the forming stage begins. This stage includes various techniques such as:
- Stamping: Used for creating metal parts like panels and frames. This process allows for high-volume production with precision.
- Injection Molding: Ideal for producing plastic components, allowing for intricate designs and efficient mass production.
- Bending and Welding: Employed to shape metal parts and assemble components, ensuring structural strength.
The choice of forming technique depends on the design specifications and the expected volume of production. This is where manufacturers can optimize for cost and efficiency, which is crucial for competitive pricing in the vending machine market.
Assembly
The assembly process is where all components come together to create the vending machine. This stage typically involves:
- Component Integration: Electrical, mechanical, and structural components are assembled, ensuring that all parts function harmoniously.
- Quality Checks: During assembly, manufacturers often conduct initial quality checks (IPQC – In-Process Quality Control) to identify and rectify issues early in the production process.
Efficient assembly processes can reduce production time and costs, which is particularly important for B2B buyers looking for timely delivery and competitive pricing.
Finishing
The finishing stage enhances the vending machine’s aesthetic and protective qualities. This includes:
- Painting and Coating: To improve the machine’s appearance and protect it from corrosion and wear.
- Labeling: Ensuring compliance with safety and regulatory standards, including CE markings for the European market.
- Final Quality Control (FQC): A thorough inspection of the assembled machine to verify functionality, safety, and compliance with specifications.
This stage is critical as it ensures that the vending machines not only look appealing but are also safe for end users.
Quality Assurance in Manufacturing
Quality assurance is an integral part of the manufacturing process for Costco vending machines. Implementing a robust QA system ensures that the final products meet international quality standards and customer expectations.
International Standards
International buyers must be aware of various standards that govern product quality. Key standards include:
- ISO 9001: Focuses on quality management systems, ensuring consistent quality in products and services.
- CE Marking: Indicates compliance with European health, safety, and environmental protection standards.
- API Standards: Relevant for components that may interact with sensitive products, ensuring safety and reliability.
Compliance with these standards not only facilitates market access but also enhances the credibility of manufacturers in the eyes of international buyers.
Quality Control Checkpoints
The manufacturing process includes several quality control checkpoints to ensure that products meet specified standards:
- Incoming Quality Control (IQC): Inspecting raw materials and components upon arrival at the manufacturing facility to ensure they meet quality standards.
- In-Process Quality Control (IPQC): Ongoing inspections during the manufacturing process to catch defects early.
- Final Quality Control (FQC): Comprehensive testing of the finished product to ensure it meets all specifications and functions correctly.
These checkpoints are essential for maintaining a high standard of quality throughout the manufacturing process.
Common Testing Methods
B2B buyers should be aware of common testing methods used to ensure quality:
- Functional Testing: Verifying that all machine functions operate as intended.
- Durability Testing: Assessing the machine’s resistance to wear and tear over time.
- Safety Testing: Ensuring that the machine meets safety standards and poses no risks to users.
Understanding these testing methods allows buyers to assess the reliability and safety of the vending machines they are considering for purchase.
Verifying Supplier Quality Control
For international B2B buyers, particularly those from regions like Africa, South America, the Middle East, and Europe, verifying a supplier’s quality control measures is crucial. Here are several approaches:
- Supplier Audits: Conducting audits to evaluate a supplier’s manufacturing processes and quality assurance systems can provide insight into their capabilities.
- Quality Reports: Requesting documentation of previous quality control results, including IQC, IPQC, and FQC reports, can help assess a supplier’s reliability.
- Third-Party Inspections: Engaging third-party inspection services can provide an unbiased evaluation of the supplier’s quality control measures and manufacturing processes.
These methods help ensure that buyers are partnering with manufacturers that uphold high standards of quality.
Conclusion
Understanding the manufacturing processes and quality assurance measures for Costco vending machines is essential for international B2B buyers. By familiarizing themselves with material preparation, forming, assembly, and finishing stages, as well as relevant quality control standards and practices, buyers can make informed decisions that align with their business needs. Ensuring compliance with international standards and verifying supplier quality control will enhance the likelihood of successful procurement and long-term satisfaction with their vending machine investments.
Related Video: SMART Quality Control for Manufacturing
Comprehensive Cost and Pricing Analysis for costco vending machine Sourcing
Cost Structure of Costco Vending Machines
When sourcing Costco vending machines, international B2B buyers should be aware of the various cost components that contribute to the overall pricing structure. Understanding these elements will enable buyers to make informed decisions and negotiate effectively.
Key Cost Components
-
Materials: The primary materials for vending machines include steel for the frame, glass for the front, and electronic components for the vending mechanism. Costs can fluctuate based on market prices for raw materials, which can be influenced by global supply chain issues.
-
Labor: Labor costs can vary significantly depending on the manufacturing location. Countries with higher labor costs will see an increase in the final price of the vending machines. It’s essential to consider not only the direct labor costs but also any indirect costs associated with workforce training and maintenance.
-
Manufacturing Overhead: This includes costs related to the production facility, utilities, equipment depreciation, and administrative expenses. Efficient manufacturing processes, like Costco’s “No Touch” policy, help minimize these overheads, which can lead to lower prices for buyers.
-
Tooling: Specific tooling is required for machine assembly and production. This can be a significant upfront cost, particularly for customized machines. Buyers should consider whether they require standard models or bespoke solutions, as this will directly affect tooling costs.
-
Quality Control (QC): Ensuring that machines meet quality standards is vital. QC processes can add to the cost structure but are essential for maintaining product reliability and customer satisfaction.
-
Logistics: Shipping costs will vary based on the distance from the manufacturing site to the buyer’s location, as well as the chosen Incoterms. Buyers should be aware of potential import duties and tariffs that may apply when sourcing from other countries.
-
Margin: Suppliers typically include a profit margin in their pricing. This margin can vary based on competition, the supplier’s market position, and the perceived value of the vending machines.
Price Influencers
Several factors can influence the pricing of Costco vending machines:
-
Volume/MOQ: Larger orders often qualify for discounts. Understanding the minimum order quantities (MOQ) can help buyers leverage better pricing.
-
Specifications/Customization: Custom features, such as branding or specific functionalities, can lead to higher costs. Buyers should clearly define their needs to avoid unnecessary expenses.
-
Materials and Quality: Higher quality materials typically increase costs. Buyers must balance quality with budget constraints, especially when catering to diverse markets.
-
Supplier Factors: The reputation and reliability of suppliers can impact pricing. Established suppliers with a track record of quality may charge more but can offer long-term reliability.
-
Incoterms: Understanding Incoterms is crucial for international transactions. Terms like FOB (Free on Board) or CIF (Cost, Insurance, and Freight) can affect pricing and risk allocation during shipping.
Buyer Tips
-
Negotiation: Effective negotiation strategies can significantly impact pricing. Buyers should be prepared to discuss volume discounts, payment terms, and delivery timelines.
-
Cost-Efficiency: Assess the total cost of ownership (TCO) rather than just the purchase price. Consider maintenance, energy consumption, and potential downtime costs when evaluating options.
-
Pricing Nuances for International Buyers: For buyers in Africa, South America, the Middle East, and Europe, understanding local market conditions and currency fluctuations is vital. Be mindful of how these factors can influence overall costs.
-
Research and Due Diligence: Conduct thorough research on potential suppliers to ensure they meet quality and reliability standards. This can prevent costly issues down the line.
Disclaimer
Prices and cost components mentioned in this analysis are indicative and may vary based on market conditions, supplier negotiations, and specific buyer requirements. Always seek updated quotes and conduct thorough assessments before finalizing purchases.
Spotlight on Potential costco vending machine Manufacturers and Suppliers
- (No specific manufacturer data was available or requested for detailed profiling in this section for costco vending machine.)*
Essential Technical Properties and Trade Terminology for costco vending machine
Key Technical Properties of Costco Vending Machines
When considering the procurement of Costco vending machines, understanding their technical properties is essential for effective decision-making. Below are critical specifications that should be taken into account:
-
Material Grade: The construction of vending machines typically involves materials like stainless steel and high-grade plastics. Stainless steel is preferred for its durability, resistance to corrosion, and ease of cleaning. B2B buyers should prioritize machines made from high-quality materials to ensure longevity and minimize maintenance costs.
-
Capacity: This refers to the number of products that a vending machine can hold, often measured in cubic feet. Understanding the capacity is crucial for businesses to determine how frequently the machine will need restocking, affecting labor and operational costs. For instance, a larger capacity may be advantageous in high-traffic areas.
-
Power Requirements: Vending machines typically operate on standard electrical specifications (e.g., 110V or 220V). Buyers must ensure that their installation site can accommodate these requirements to avoid additional costs for electrical upgrades. Understanding power consumption is also important for estimating operational costs.
-
Temperature Control: Many vending machines have built-in refrigeration systems for perishable items. The ability to maintain specific temperature ranges is vital for food safety and compliance with health regulations. B2B buyers should verify that the vending machines meet local standards for food storage.
-
User Interface: This includes touchscreen displays, payment options (credit/debit cards, mobile payments), and accessibility features. A user-friendly interface can enhance customer experience, leading to higher sales. It’s important for businesses to consider the demographic of their target audience when selecting these features.
-
Warranty and Support: Understanding the warranty terms and the availability of technical support is crucial. A robust warranty can protect businesses from unexpected repairs, while responsive support can minimize downtime, ensuring consistent operation.
Common Trade Terminology
In the B2B landscape, familiarity with specific trade terms can facilitate smoother transactions and negotiations. Here are some essential terms related to vending machine procurement:
-
OEM (Original Equipment Manufacturer): This term refers to companies that produce parts and equipment that may be marketed by another manufacturer. When purchasing vending machines, working with OEMs can ensure that buyers receive high-quality products tailored to their specifications.
-
MOQ (Minimum Order Quantity): This is the smallest quantity of a product that a supplier is willing to sell. Understanding the MOQ is critical for budgeting and inventory planning, especially for smaller businesses or those testing new products in the market.
-
RFQ (Request for Quotation): This is a document that an organization sends to suppliers to solicit price quotes for specific products or services. B2B buyers should utilize RFQs to obtain competitive pricing and evaluate multiple suppliers before making a purchase decision.
-
Incoterms (International Commercial Terms): These are standardized trade terms that define the responsibilities of buyers and sellers in international transactions. Familiarity with Incoterms can help buyers understand shipping costs, risk management, and delivery responsibilities.
-
Lead Time: This refers to the time taken from placing an order to receiving the product. Understanding lead times is essential for inventory management and planning, especially in industries where demand can fluctuate.
-
After-Sales Service: This encompasses the support provided to customers after the purchase of a product. For vending machines, after-sales service may include installation, maintenance, and troubleshooting support. Strong after-sales service can enhance customer satisfaction and loyalty.
By familiarizing themselves with these properties and terms, international B2B buyers can make informed decisions that align with their operational needs and strategic goals.
Navigating Market Dynamics, Sourcing Trends, and Sustainability in the costco vending machine Sector
Market Overview & Key Trends
The global vending machine market is undergoing significant transformation, driven by advancements in technology, changing consumer preferences, and a growing demand for convenience. For international B2B buyers, particularly from regions like Africa, South America, the Middle East, and Europe, understanding these dynamics is crucial for making informed purchasing decisions.
Key Trends:
-
Smart Vending Technology: The integration of IoT and AI in vending machines is reshaping the landscape. Smart vending machines equipped with touchless payment systems, real-time inventory tracking, and personalized marketing are becoming increasingly popular. This trend is particularly relevant for buyers looking to enhance customer experience and operational efficiency.
-
Health and Wellness Focus: There is a noticeable shift towards healthier snack options in vending machines. This trend is driven by consumer awareness about health and wellness, pushing suppliers to stock organic, gluten-free, and low-calorie products. B2B buyers should consider sourcing machines that offer flexibility in product selection to cater to diverse consumer preferences.
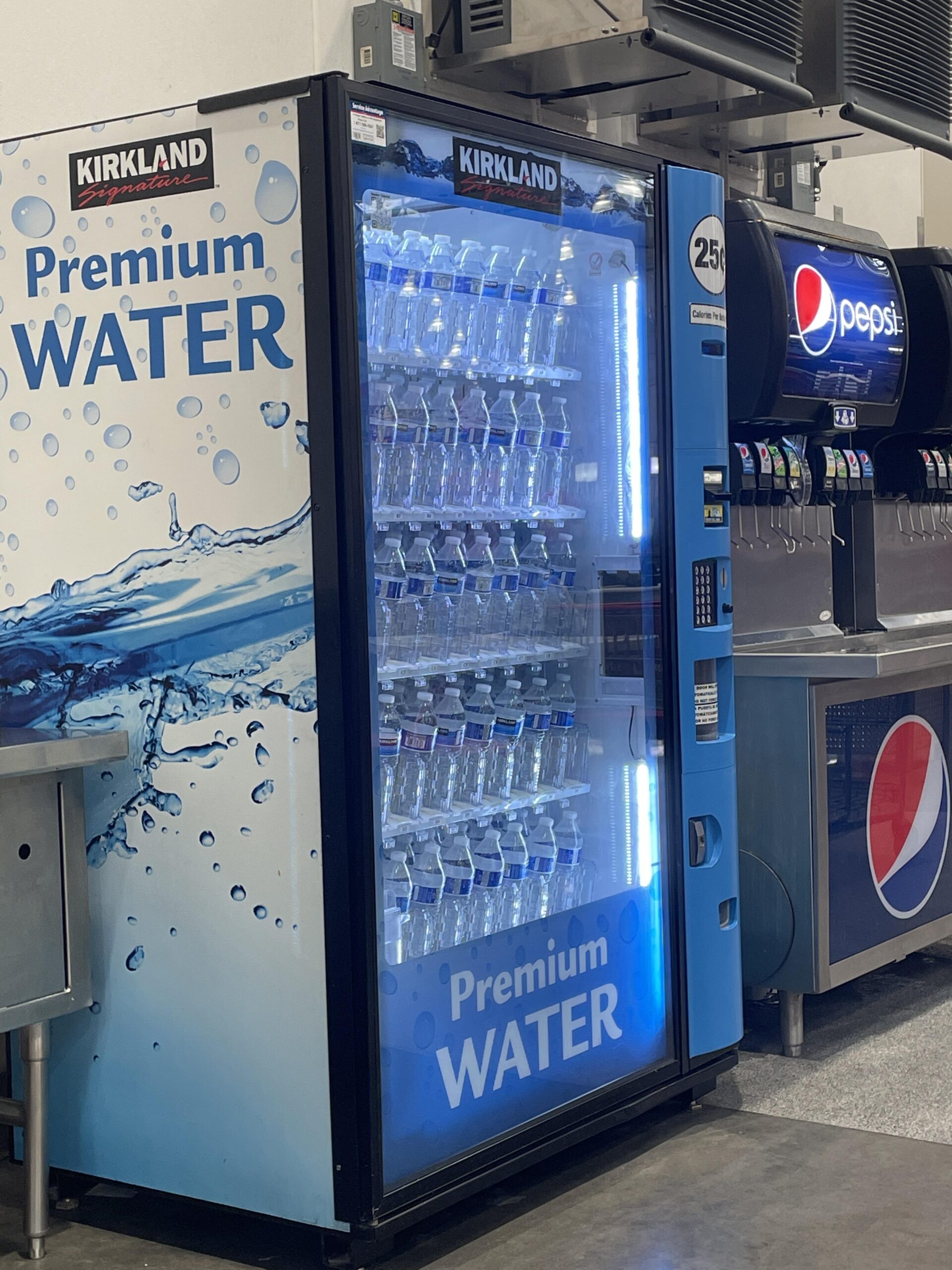
Illustrative Image (Source: Google Search)
-
Sustainability Initiatives: Sustainability is now a priority for businesses worldwide. Vending machine operators are increasingly seeking eco-friendly options, such as machines made from recycled materials or those that use energy-efficient technologies. International buyers should look for suppliers that align with these sustainability goals to enhance their brand reputation.
-
Regional Adaptations: Different markets have unique preferences and regulations. For instance, vending machines in Italy may focus on gourmet coffee and pastries, while those in Kenya might prioritize local snacks. Understanding these regional nuances is vital for sourcing machines that will perform well in specific markets.
Sustainability & Ethical Sourcing in B2B
As the emphasis on sustainability grows, B2B buyers in the vending machine sector must prioritize ethical sourcing and environmental responsibility. The production and operation of vending machines can have significant environmental impacts, from energy consumption to waste generation.
Key Considerations:
-
Sustainable Materials: When sourcing vending machines, look for options that utilize sustainable materials. Machines made from recycled plastics or metals not only reduce environmental impact but can also appeal to eco-conscious consumers.
-
Energy Efficiency: Investing in energy-efficient vending machines can lead to substantial cost savings over time. Machines that use LED lighting and low-energy cooling systems help minimize electricity consumption, making them a smart choice for long-term sustainability.
-
Ethical Supply Chains: Ensuring that suppliers adhere to ethical sourcing practices is crucial. This includes fair labor practices and environmentally friendly manufacturing processes. Buyers should seek vendors with certifications such as ISO 14001 for environmental management and SA8000 for social accountability.
-
Waste Reduction Programs: Collaborating with suppliers who have waste reduction initiatives in place can enhance sustainability efforts. This can include programs for recycling packaging materials and minimizing operational waste.
Brief Evolution/History
The vending machine industry has evolved significantly since its inception in the early 20th century. Initially focused on simple mechanical operations, modern vending machines now incorporate advanced technology, offering diverse products and services.
Over the decades, vending machines transitioned from dispensing candy and soft drinks to providing a wide range of food and beverages, including fresh items. The rise of cashless payment options and mobile integrations has further transformed the sector, catering to the growing consumer demand for convenience. As a result, today’s vending machines not only serve as points of sale but also as platforms for delivering personalized experiences, reflecting broader trends in retail and consumer engagement.
For international B2B buyers, recognizing this evolution is essential in identifying the right suppliers and products that align with current market demands.
Related Video: What global trade deals are really about (hint: it’s not trade) | Haley Edwards | TEDxMidAtlantic
Frequently Asked Questions (FAQs) for B2B Buyers of costco vending machine
-
What should I consider when vetting suppliers for Costco vending machines?
When vetting suppliers, focus on their experience with vending machines and their understanding of international trade regulations. Check for certifications like ISO and CE, which indicate quality and compliance with safety standards. Evaluate their track record through customer references and reviews, and ensure they can provide warranty and support services. Also, consider their logistical capabilities to meet your specific region’s demands, including shipping and delivery times. -
Can I customize my Costco vending machine order?
Yes, many suppliers offer customization options for Costco vending machines to suit your specific needs. This may include branding with your logo, choosing the types of products you want to vend, or adjusting the machine’s size and features. It’s essential to discuss your requirements upfront with the supplier to determine the available options and any additional costs associated with customization. -
What are the typical minimum order quantities (MOQ) and lead times?
Minimum order quantities (MOQ) for Costco vending machines can vary widely depending on the supplier and the level of customization required. Generally, MOQs can range from a single machine to multiple units. Lead times also depend on the supplier’s production capacity and shipping logistics, often ranging from a few weeks to several months. It’s crucial to clarify these details during negotiations to align expectations with your business timelines. -
What payment terms should I expect when purchasing?
Payment terms can vary between suppliers, but common practices include a deposit upfront (typically 30-50%) with the balance due upon delivery or installation. Some suppliers may offer financing options or extended payment terms for larger orders. Always ensure that payment methods are secure and consider using letters of credit for international transactions to protect your investment. -
How do I ensure quality assurance and certification for my vending machines?
Request documentation of quality assurance processes from your supplier, including any relevant certifications such as ISO 9001 or CE marking. These certifications indicate that the machines meet specific quality and safety standards. Conducting a factory audit can also provide insights into their production practices and quality control measures, ensuring the machines you receive are reliable and compliant with international standards. -
What logistics considerations should I keep in mind?
Logistics play a critical role in the procurement of Costco vending machines. Confirm the supplier’s ability to handle international shipping, including customs clearance and duties. Discuss shipping options (e.g., air freight vs. sea freight) to balance cost and delivery speed. Additionally, inquire about the supplier’s experience with local logistics partners in your region to facilitate smooth delivery and installation. -
How can I address potential disputes with my supplier?
To mitigate disputes, establish clear contracts detailing terms of sale, delivery timelines, and responsibilities of both parties. Include clauses for dispute resolution, such as mediation or arbitration, to avoid lengthy legal processes. Regular communication with your supplier can also help preempt issues. If disputes arise, document all interactions and agreements to support your case. -
What should I do if the vending machine is damaged during shipping?
If the vending machine is damaged during shipping, immediately document the damage with photographs and written notes. Contact the supplier as soon as possible to report the issue and refer to the shipping insurance policy, if applicable. Most reputable suppliers will have policies in place for handling shipping damage, which may include repair, replacement, or compensation. Ensure you keep all relevant documentation to expedite the claims process.
Strategic Sourcing Conclusion and Outlook for costco vending machine
As international B2B buyers explore the Costco vending machine opportunity, several key insights emerge. Strategic sourcing remains paramount in securing a competitive advantage. By leveraging Costco’s efficient supply chain, characterized by its no-touch policy and limited SKUs, buyers can optimize procurement processes while minimizing costs. This operational simplicity not only enhances inventory management but also fosters stronger supplier relationships, creating avenues for cost savings that can be passed on to consumers.
Moreover, understanding the dynamics of Costco’s market positioning—particularly its ability to adapt to competitive pressures—equips buyers to anticipate market trends and consumer preferences. For businesses in regions like Africa, South America, the Middle East, and Europe, aligning with Costco’s model can lead to substantial efficiencies and improved service delivery.
Looking ahead, it is crucial for B2B buyers to embrace these insights and consider the strategic advantages of integrating Costco vending machines into their operations. Act now to tap into Costco’s innovative approach, ensuring your business not only meets but exceeds evolving consumer demands. By doing so, you position yourself to thrive in an increasingly competitive landscape.