Master Sourcing American Rounds Vending Machines for Global
Guide to American Rounds Vending Machine
- Introduction: Navigating the Global Market for american rounds vending machine
- Understanding american rounds vending machine Types and Variations
- Key Industrial Applications of american rounds vending machine
- Strategic Material Selection Guide for american rounds vending machine
- In-depth Look: Manufacturing Processes and Quality Assurance for american rounds vending machine
- Comprehensive Cost and Pricing Analysis for american rounds vending machine Sourcing
- Spotlight on Potential american rounds vending machine Manufacturers and Suppliers
- Essential Technical Properties and Trade Terminology for american rounds vending machine
- Navigating Market Dynamics, Sourcing Trends, and Sustainability in the american rounds vending machine Sector
- Frequently Asked Questions (FAQs) for B2B Buyers of american rounds vending machine
- Strategic Sourcing Conclusion and Outlook for american rounds vending machine
Introduction: Navigating the Global Market for american rounds vending machine
In today’s fast-paced global economy, the demand for American rounds vending machines has surged, driven by their versatility and ability to cater to diverse consumer needs. These machines offer a unique blend of convenience and accessibility, making them a vital asset for businesses aiming to enhance their product distribution. As B2B buyers from regions such as Africa, South America, the Middle East, and Europe seek to capitalize on this trend, understanding the intricacies of the market becomes paramount.
This comprehensive guide is designed to empower international buyers with the knowledge they need to make informed sourcing decisions. We will explore various types of American rounds vending machines, delve into the materials used in their construction, and provide insights into manufacturing processes and quality control standards. Furthermore, we will highlight key suppliers, analyze cost factors, and assess market trends that influence purchasing strategies.
By equipping you with actionable insights and practical information, this guide aims to simplify the complexities of navigating the global market for American rounds vending machines. Whether you are in Egypt looking to diversify your retail offerings or in South America aiming to enhance customer engagement through innovative solutions, this resource will serve as your roadmap to success. Prepare to unlock new opportunities and drive growth in your business with confidence.
Understanding american rounds vending machine Types and Variations
Type Name | Key Distinguishing Features | Primary B2B Applications | Brief Pros & Cons for Buyers |
---|---|---|---|
Traditional Snack Vending Machine | Offers a variety of snacks and beverages | Offices, schools, public spaces | Pros: Wide selection; easy to stock. Cons: Limited to non-perishable items. |
Healthy Food Vending Machine | Focuses on nutritious snacks and meals | Gyms, wellness centers, corporate offices | Pros: Appeals to health-conscious consumers. Cons: Higher initial investment. |
Coffee Vending Machine | Specializes in various coffee beverages | Cafés, workplaces, events | Pros: High demand; generates frequent sales. Cons: Requires maintenance and supplies. |
Combo Vending Machine | Combines snacks and beverages in one unit | Airports, train stations, shopping malls | Pros: Versatile; caters to diverse customer preferences. Cons: More complex to manage. |
Specialty Vending Machine | Dispenses niche products like electronics or beauty items | Retail environments, events, trade shows | Pros: Targets specific markets; unique offerings. Cons: Smaller customer base; higher risk. |
Traditional Snack Vending Machine
The Traditional Snack Vending Machine is a staple in various environments, providing a wide range of snacks and beverages. These machines are typically compact and designed for high traffic areas such as offices, schools, and public spaces. When purchasing, buyers should consider factors such as product variety, ease of stocking, and machine reliability. While these machines are user-friendly and maintain a consistent demand, they are limited to non-perishable items, which may restrict product offerings.
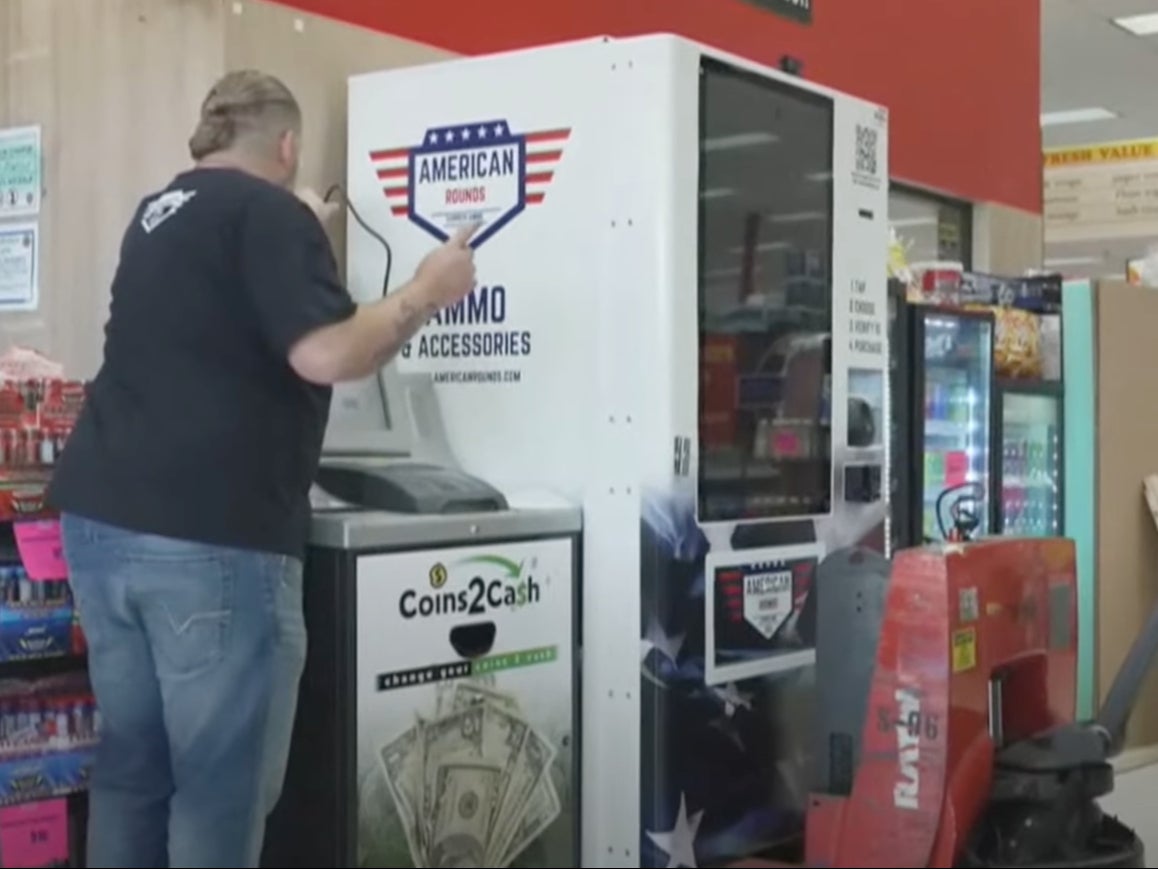
Illustrative Image (Source: Google Search)
Healthy Food Vending Machine
The Healthy Food Vending Machine caters to the growing trend of health-conscious consumers by offering nutritious snacks and meals. These machines are particularly suitable for gyms, wellness centers, and corporate offices that promote healthy lifestyles. B2B buyers should evaluate the machine’s ability to maintain freshness and the range of healthy options available. Although these machines can require a higher initial investment, their appeal can lead to increased foot traffic and customer loyalty.
Coffee Vending Machine
Coffee Vending Machines are specialized units that serve various coffee beverages, making them ideal for locations such as cafés, workplaces, and events. These machines often feature advanced brewing technology to deliver quality coffee quickly. Buyers should consider the machine’s capacity, maintenance requirements, and supply chain for coffee products. While they generate frequent sales due to high demand, they also necessitate regular maintenance and supply replenishment, which can add to operational costs.
Combo Vending Machine
Combo Vending Machines combine snacks and beverages into a single unit, making them versatile options for high-traffic locations like airports, train stations, and shopping malls. They cater to diverse customer preferences, allowing buyers to maximize sales opportunities. When selecting a combo machine, B2B buyers should assess the balance of product offerings and the complexity of inventory management. While they provide a broad selection, the complexity of operations can present challenges in stock management.
Specialty Vending Machine
Specialty Vending Machines dispense niche products such as electronics, beauty items, or gourmet foods. These machines are often found in retail environments, events, and trade shows, targeting specific markets with unique offerings. B2B buyers should consider the potential customer base and market demand for the products offered. Although they can provide high margins and cater to specific consumer needs, the smaller customer base may result in a higher risk for inventory turnover.
Related Video: US: Bullet vending machines legalised in Alabama, Oklahoma & Texas | World News | WION
Key Industrial Applications of american rounds vending machine
Industry/Sector | Specific Application of American Rounds Vending Machine | Value/Benefit for the Business | Key Sourcing Considerations for this Application |
---|---|---|---|
Manufacturing | Employee break rooms and production areas | Enhances employee satisfaction and productivity | Energy efficiency, maintenance support, and capacity |
Education | Campus facilities and dormitories | Provides convenient access to snacks and drinks | Payment system integration, bulk purchasing options |
Healthcare | Hospitals and clinics | Improves patient and staff experience with quick access to refreshments | Compliance with health regulations, product variety |
Retail | Shopping malls and supermarkets | Increases foot traffic and additional revenue streams | Location analysis, machine design for high visibility |
Transportation | Airports and train stations | Offers travelers quick access to food and beverages | Durability, payment flexibility, and product selection |
Manufacturing
In manufacturing settings, American rounds vending machines serve as a vital resource in employee break rooms and production areas. They provide quick access to snacks and beverages, which can significantly enhance employee satisfaction and productivity. For international buyers, particularly from Africa and South America, sourcing machines that are energy-efficient and require minimal maintenance is crucial. Additionally, understanding local preferences for snack options can further improve employee morale.
Education
In educational institutions, American rounds vending machines are commonly placed in campus facilities and dormitories. They enable students to access snacks and drinks conveniently, fostering a more engaging campus environment. For B2B buyers from Europe and the Middle East, it is essential to consider the integration of advanced payment systems, such as cashless transactions, as well as options for bulk purchasing to manage costs effectively.
Healthcare
In healthcare environments like hospitals and clinics, American rounds vending machines play a key role in improving the experience of both patients and staff. They provide quick access to refreshments, which can be particularly beneficial during long wait times. Buyers should focus on compliance with health regulations, ensuring that the products offered are safe and varied enough to meet diverse dietary needs. Additionally, machines must be easy to clean and maintain to uphold hygiene standards.
Retail
Within the retail sector, American rounds vending machines can be strategically placed in shopping malls and supermarkets to increase foot traffic and create additional revenue streams. They offer a convenient shopping alternative for customers on the go. For international B2B buyers, conducting a thorough location analysis to determine high-traffic areas is essential. Furthermore, the machine design should be visually appealing and functional to enhance customer interaction.
Transportation
In transportation hubs such as airports and train stations, American rounds vending machines provide travelers with quick access to food and beverages, catering to their on-the-go lifestyle. This convenience not only improves the travel experience but also drives additional revenue for the facility. Buyers should prioritize sourcing machines that are durable and capable of withstanding high usage, while also offering flexible payment options to accommodate diverse customer preferences.
Related Video: How to Start a Vending Machine Business, Cost, Tips, How Much You Make
Strategic Material Selection Guide for american rounds vending machine
When selecting materials for American rounds vending machines, it is crucial to consider the unique properties and applications of various materials. This guide analyzes four common materials: stainless steel, aluminum, plastic, and carbon steel. Each material has distinct advantages and limitations that can significantly influence the performance, durability, and cost-effectiveness of the vending machines.
Stainless Steel
Stainless steel is a highly favored material for vending machines due to its excellent corrosion resistance and durability. It can withstand a wide range of temperatures and pressures, making it suitable for various environments, from humid climates in Africa to the harsher conditions in the Middle East.
Pros: Stainless steel is strong and resistant to rust and staining, which is essential for maintaining hygiene in food-related applications. It also has a long lifespan, reducing the need for frequent replacements.
Cons: The primary drawback is its higher cost compared to other materials. Additionally, manufacturing stainless steel components can be more complex, requiring specialized equipment.
Impact on Application: Stainless steel is compatible with a wide range of media, including food and beverages, making it an ideal choice for vending machines.
Considerations for International Buyers: Compliance with international standards such as ASTM and DIN is crucial. Buyers should ensure that the stainless steel grades used meet local regulations, particularly in regions like Europe and South America, where food safety standards are stringent.
Aluminum
Aluminum is another popular choice for vending machines, known for its lightweight and corrosion-resistant properties. This material is particularly beneficial for machines that require mobility or frequent relocation.
Pros: Aluminum is cost-effective and easy to manufacture, allowing for more intricate designs. It also provides good thermal conductivity, which can be advantageous in temperature-sensitive applications.
Cons: While aluminum is resistant to corrosion, it is less durable than stainless steel and can be prone to dents and scratches, which may affect the machine’s aesthetic over time.
Impact on Application: Aluminum is suitable for non-corrosive media and can be used effectively in dry environments. However, it may not be ideal for locations with high humidity or exposure to salty air.
Considerations for International Buyers: Buyers should consider the local climate when selecting aluminum. In regions like the Middle East, where temperatures can soar, ensuring proper anodization or coating is essential to enhance durability.
Plastic
Plastic materials, such as polycarbonate and ABS, are increasingly used in vending machines for their versatility and cost-effectiveness. They are particularly suitable for exterior components and internal parts that do not require high strength.
Pros: Plastics are lightweight, easy to mold, and can be produced in various colors and finishes, allowing for customization. They are also resistant to corrosion and can be less expensive than metal alternatives.
Cons: Plastics may not withstand high temperatures or heavy loads as well as metals, which can limit their use in certain applications. They can also degrade over time when exposed to UV light unless treated.
Impact on Application: Plastic is best suited for non-structural components and for environments where weight reduction is a priority.
Considerations for International Buyers: Compliance with material safety standards is essential, especially in food-related applications. Buyers should also consider the environmental impact of plastic use and disposal in their regions.
Carbon Steel
Carbon steel is often used in vending machine structures where strength is a priority. It is a cost-effective option for non-corrosive environments.
Pros: Carbon steel is strong and durable, making it suitable for heavy-duty applications. It is also relatively inexpensive compared to stainless steel.
Cons: The major limitation of carbon steel is its susceptibility to corrosion, which necessitates protective coatings or paints.
Impact on Application: Carbon steel is compatible with non-corrosive media but should be avoided in environments with high humidity or exposure to water.
Considerations for International Buyers: Buyers should ensure that carbon steel components are properly treated to prevent rust, especially in humid regions like parts of Africa and the Middle East. Compliance with local standards for structural materials is also essential.
Summary Table
Material | Typical Use Case for american rounds vending machine | Key Advantage | Key Disadvantage/Limitation | Relative Cost (Low/Med/High) |
---|---|---|---|---|
Stainless Steel (e.g., 304) | Food and beverage dispensing, exterior panels | Excellent corrosion resistance, durability | Higher cost, complex manufacturing | High |
Aluminum (e.g., 6061) | Lightweight components, mobile machines | Cost-effective, easy to manufacture | Less durable, prone to dents | Medium |
Plastic (e.g., ABS) | Non-structural components, decorative parts | Lightweight, customizable, cost-effective | Limited temperature resistance, UV degradation | Low |
Carbon Steel (e.g., A36) | Structural components in dry environments | Strong and durable, low cost | Susceptible to corrosion, requires protection | Low |
This strategic material selection guide provides essential insights for international B2B buyers, enabling them to make informed decisions that align with their operational needs and local compliance requirements.
In-depth Look: Manufacturing Processes and Quality Assurance for american rounds vending machine
Manufacturing Processes for American Rounds Vending Machines
The production of American rounds vending machines involves several critical stages, each designed to ensure the final product meets stringent quality and performance standards. Understanding these processes can help international B2B buyers evaluate suppliers effectively.
1. Material Preparation
The first stage in the manufacturing process is material preparation. This involves sourcing high-quality raw materials such as steel for the frame, polycarbonate for the windows, and various electronic components for the vending mechanisms. Buyers should ensure that suppliers use materials that comply with international standards, such as ASTM (American Society for Testing and Materials) specifications, which indicate the quality and durability of the materials used.
2. Forming
Once materials are prepared, the next step is forming. This typically includes:
- Cutting: Raw materials are cut into specified dimensions using laser cutting or water jet cutting for precision.
- Bending: Steel parts are bent using CNC (Computer Numerical Control) machines, ensuring consistent angles and shapes.
- Molding: Plastic components may be created through injection molding, allowing for intricate designs and robust structures.
B2B buyers should inquire about the technology and machinery used in these processes, as advanced equipment often leads to better quality and efficiency.
3. Assembly
The assembly stage is where various components come together. This process can be divided into:
- Sub-Assembly: Individual components, such as the coin mechanism, display, and payment systems, are assembled separately before being integrated into the main unit.
- Final Assembly: The sub-assemblies are combined, and additional features such as lighting and branding are added.
During this phase, it is crucial for manufacturers to adhere to assembly line best practices to minimize errors and ensure uniformity. B2B buyers can assess the supplier’s assembly capabilities by requesting details about their workforce training and assembly protocols.
4. Finishing
The finishing stage enhances both the aesthetics and functionality of the vending machines. This includes:
- Painting and Coating: Applying powder coating or paint to protect against corrosion and wear.
- Quality Testing: Conducting tests for functionality, such as ensuring that the vending mechanism operates smoothly and that electronic components are properly integrated.
Buyers should verify that suppliers employ environmentally friendly finishing processes, as this can reflect a commitment to sustainability.
Quality Assurance in Manufacturing
Quality assurance is a critical aspect of the manufacturing process, ensuring that the vending machines meet established standards and customer expectations. For international B2B buyers, understanding the quality control measures in place is essential.
International Standards
Suppliers of American rounds vending machines should comply with relevant international standards, including:
- ISO 9001: This standard focuses on quality management systems and continuous improvement. Certification indicates that the supplier follows effective quality assurance practices.
- CE Marking: For products sold in the European Union, CE marking demonstrates compliance with health, safety, and environmental protection standards.
- API Standards: The American Petroleum Institute standards may apply if the vending machines incorporate any oil or gas-related components.
B2B buyers should request copies of these certifications to ensure compliance.
QC Checkpoints
Quality control checkpoints throughout the manufacturing process are essential to maintaining product integrity. Common checkpoints include:
- Incoming Quality Control (IQC): Inspection of raw materials upon arrival to ensure they meet specifications.
- In-Process Quality Control (IPQC): Continuous monitoring during the manufacturing process to catch defects early.
- Final Quality Control (FQC): A comprehensive inspection of the finished product before it is packaged and shipped.
B2B buyers should inquire about the frequency and methods used at each checkpoint.
Common Testing Methods
To verify quality, manufacturers typically employ various testing methods, including:
- Functional Testing: Ensuring that all electronic components operate as intended.
- Durability Testing: Simulating conditions the vending machines will face in real-world scenarios to assess their robustness.
- Safety Testing: Checking for compliance with electrical safety standards to prevent hazards.
Buyers should seek detailed reports on these tests to understand the reliability of the machines they are purchasing.
Verifying Supplier Quality Control
B2B buyers can take several steps to verify a supplier’s quality control processes:
-
Conduct Audits: Regular audits of the supplier’s manufacturing facility can provide insights into their operational practices and adherence to quality standards.
-
Request Quality Reports: Suppliers should be willing to share quality control reports, including any non-conformance issues and resolutions.
-
Engage Third-Party Inspectors: Employing third-party inspection services can offer an unbiased assessment of the manufacturing and quality assurance processes.
QC/Cert Nuances for International Buyers
For buyers from Africa, South America, the Middle East, and Europe, there are specific nuances to consider:
- Cultural Differences: Understanding local practices and communication styles can facilitate better negotiations and partnerships.
- Regulatory Compliance: Be aware of the regulations in your region regarding imported goods, as different countries have varying requirements for certifications and testing.
- Supply Chain Logistics: Assess the supplier’s ability to meet shipping and delivery timelines, especially in light of potential disruptions in global supply chains.
By focusing on these aspects, international B2B buyers can make informed decisions when selecting suppliers for American rounds vending machines, ensuring they receive high-quality products that meet their operational needs.
Related Video: Modern Ammunition Manufacturing Process: Inside Gun Factory
Comprehensive Cost and Pricing Analysis for american rounds vending machine Sourcing
Cost Structure of American Rounds Vending Machines
When sourcing American rounds vending machines, understanding the comprehensive cost structure is essential for international B2B buyers. The main components include:
-
Materials: The primary materials involved in manufacturing vending machines typically include steel, plastics, and electronic components. Prices can fluctuate based on global supply chain dynamics, so it’s crucial to keep an eye on raw material trends.
-
Labor: Labor costs vary significantly based on the manufacturing location. For instance, factories in Eastern Europe might have lower labor costs compared to those in Western Europe or North America. Consider the implications of local wage laws and productivity levels when evaluating supplier quotes.
-
Manufacturing Overhead: This encompasses costs related to factory operations, such as utilities and maintenance. Suppliers may include these costs in their pricing, so clarity on overhead calculations is essential.
-
Tooling: Custom tooling for unique designs can be a significant upfront investment. Buyers should assess whether the tooling costs can be amortized over a large order quantity to enhance cost efficiency.
-
Quality Control (QC): Implementing stringent quality control processes can add to the overall cost but can prevent costly defects and returns. Ensure that your supplier has robust QC protocols in place, especially if sourcing from regions with varying quality standards.
-
Logistics: Shipping costs can vary widely depending on the origin of the machines and the destination country. Factors such as freight rates, insurance, and customs duties must be factored into the total cost.
-
Margin: Suppliers will typically mark up their costs to achieve a profit margin. Understanding the standard margins in the industry can help buyers negotiate better prices.
Influencers on Pricing
Several factors influence the pricing of American rounds vending machines, including:
-
Volume/MOQ: Suppliers often provide better pricing for larger orders. Establishing a Minimum Order Quantity (MOQ) can significantly reduce per-unit costs.
-
Specifications/Customization: Customized machines or those with advanced features may incur higher costs. Clearly define your needs to avoid unexpected expenses.
-
Materials and Quality Certifications: Machines built with higher-quality materials or that meet specific certifications (e.g., ISO, CE) may command a premium. Ensure that the value justifies the higher cost.
-
Supplier Factors: The reputation and reliability of the supplier can affect pricing. Established suppliers with a track record of quality may charge more but can provide peace of mind.
-
Incoterms: The terms of trade can significantly impact total costs. Familiarize yourself with Incoterms (e.g., FOB, CIF) to understand who bears the costs and risks at each stage of transportation.
Buyer Tips for Cost Efficiency
To optimize the sourcing process for American rounds vending machines, consider the following actionable insights:
-
Negotiate Effectively: Don’t accept the first offer. Use comparative quotes from multiple suppliers to leverage negotiations. Highlight your potential for repeat business to secure better terms.
-
Evaluate Total Cost of Ownership (TCO): Look beyond initial purchase prices. Consider long-term costs associated with maintenance, operational efficiency, and lifespan when evaluating suppliers.
-
Understand Pricing Nuances: Be aware of regional price differences. For instance, suppliers in South America may offer lower prices than those in Europe, but consider shipping costs and import tariffs.
-
Plan for Currency Fluctuations: When dealing with international suppliers, currency exchange rates can impact costs. Lock in prices where possible or negotiate terms that account for currency volatility.
-
Research Local Regulations: In regions like Africa and the Middle East, import duties and local regulations can significantly affect pricing. Ensure compliance to avoid unexpected costs.
Disclaimer
The prices discussed in this analysis are indicative and subject to change based on market conditions, supplier negotiations, and other external factors. Always conduct thorough due diligence when sourcing equipment.
Spotlight on Potential american rounds vending machine Manufacturers and Suppliers
- (No specific manufacturer data was available or requested for detailed profiling in this section for american rounds vending machine.)*
Essential Technical Properties and Trade Terminology for american rounds vending machine
When considering the procurement of American rounds vending machines, it is crucial for international B2B buyers to understand both the technical specifications and the relevant trade terminology. This knowledge not only aids in making informed purchasing decisions but also facilitates smoother negotiations and operations across different markets.
Key Technical Properties
-
Material Grade
– The material used in vending machines, such as steel or aluminum, directly impacts durability and longevity. A higher grade of material often equates to better resistance against wear and tear, which is crucial for machines placed in high-traffic areas. For buyers, understanding material grade can help ensure that they select a machine suited to their specific environmental conditions. -
Power Consumption
– This specification refers to the amount of electricity the vending machine requires to operate efficiently. Machines with lower power consumption are more cost-effective in the long run, especially for businesses in regions where energy costs are high. Buyers should consider energy-efficient models that comply with international energy standards to minimize operational costs. -
Capacity
– Capacity indicates the number of products the vending machine can hold, which is vital for maximizing sales potential. Understanding the capacity helps buyers assess whether a specific machine meets their market demands. For example, a higher capacity machine may be ideal for busy locations, while smaller machines may suffice for less frequented areas. -
Temperature Control
– For vending machines that dispense perishable goods, effective temperature control is essential. This property ensures that products remain fresh and safe for consumption. Buyers should look for machines equipped with advanced refrigeration systems and insulation technologies to maintain optimal conditions for food items. -
User Interface
– The user interface encompasses the controls and display features of the vending machine. A user-friendly interface can enhance customer experience and encourage repeat purchases. Buyers should evaluate the technology used, such as touch screens or mobile payment options, to align with consumer preferences in their target market.
Common Trade Terminology
-
OEM (Original Equipment Manufacturer)
– This term refers to companies that produce parts or equipment that may be marketed by another manufacturer. Understanding OEM relationships is critical for buyers looking to ensure quality and reliability in the machines they source. This knowledge can also influence warranty and service agreements. -
MOQ (Minimum Order Quantity)
– MOQ is the smallest number of units that a supplier is willing to sell. For international buyers, knowing the MOQ is essential for budgeting and inventory planning. A high MOQ may lead to excess stock, while a low MOQ may increase per-unit costs, affecting overall profitability. -
RFQ (Request for Quotation)
– An RFQ is a document sent to suppliers to solicit price quotes for specific products or services. Crafting a detailed RFQ can help buyers receive accurate pricing and terms from multiple vendors, facilitating competitive comparisons. This process is particularly beneficial for bulk orders or long-term contracts. -
Incoterms (International Commercial Terms)
– These terms define the responsibilities of buyers and sellers in international trade. Familiarity with Incoterms is vital for understanding shipping costs, risk management, and liability. For instance, terms like FOB (Free on Board) or CIF (Cost, Insurance, and Freight) dictate who bears the cost and risk at various points in the shipping process. -
Lead Time
– Lead time refers to the period between placing an order and receiving the goods. For B2B buyers, understanding lead times is crucial for inventory management and customer fulfillment. Shorter lead times can enhance a company’s responsiveness to market demands, while longer lead times may require strategic planning to avoid stockouts.
By familiarizing themselves with these essential technical properties and trade terminology, international B2B buyers can make informed decisions regarding American rounds vending machines, ensuring they select the right products for their markets while optimizing costs and operational efficiency.
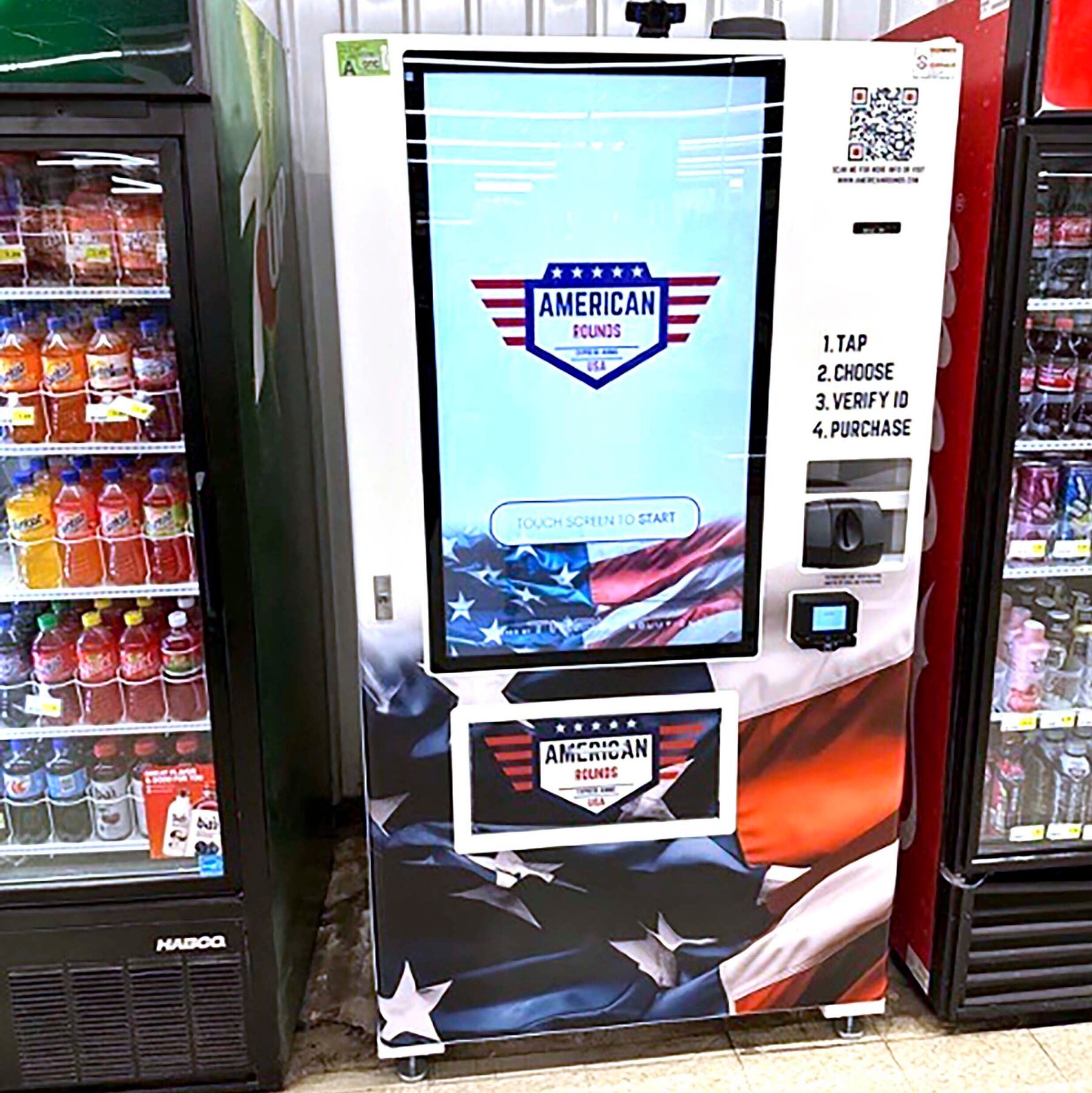
Illustrative Image (Source: Google Search)
Navigating Market Dynamics, Sourcing Trends, and Sustainability in the american rounds vending machine Sector
Market Overview & Key Trends
The American rounds vending machine sector is witnessing significant growth, driven by a combination of technological advancements and changing consumer preferences. Key global drivers include the increasing demand for convenience, the rise of cashless payment systems, and the integration of IoT technology, which allows for real-time inventory management and enhanced customer engagement. For international B2B buyers, particularly in regions like Africa, South America, the Middle East, and Europe, understanding these dynamics is crucial for making informed sourcing decisions.
Emerging trends in the sector include the proliferation of smart vending machines that offer personalized experiences through data analytics and AI. These machines not only cater to individual preferences but also optimize inventory based on purchasing patterns. Additionally, sustainability is becoming a pivotal factor, with buyers increasingly seeking eco-friendly options in vending machine design and operation. This trend is particularly relevant for buyers from regions with stringent environmental regulations, as compliance can influence market entry strategies.
In terms of market dynamics, competition is intensifying, with both established manufacturers and new entrants vying for market share. International buyers should consider partnering with suppliers who offer innovative solutions, competitive pricing, and robust after-sales support to navigate this evolving landscape effectively. Furthermore, as the sector evolves, leveraging digital platforms for sourcing and procurement can streamline operations and enhance supply chain transparency.
Sustainability & Ethical Sourcing in B2B
Sustainability is a growing concern in the American rounds vending machine sector, impacting both sourcing strategies and consumer preferences. The environmental impact of vending machines, from energy consumption to waste generation, is prompting buyers to prioritize sustainable practices. International buyers should focus on suppliers who implement energy-efficient technologies and utilize renewable energy sources in their operations.
Ethical sourcing is equally important, as it ensures that materials used in vending machines are obtained responsibly. Buyers should seek manufacturers who prioritize fair labor practices and maintain transparency in their supply chains. Certifications such as ISO 14001 for environmental management and Fair Trade can serve as indicators of a supplier’s commitment to sustainability and ethical practices.
Moreover, the use of ‘green’ materials, such as recycled plastics and biodegradable components, is becoming increasingly popular. By choosing suppliers who adhere to these practices, B2B buyers can enhance their brand reputation while contributing to environmental conservation efforts. This focus on sustainability not only meets regulatory demands but also aligns with consumer expectations, fostering loyalty and trust in the brand.
Brief Evolution/History
The American rounds vending machine has undergone significant evolution since its inception in the early 20th century. Originally designed to dispense simple snacks and beverages, these machines have transformed into sophisticated, tech-enabled units that offer a wide range of products, including fresh food and health-conscious options. The introduction of digital payment systems and interactive screens has further enhanced the consumer experience, making vending machines a viable option for various settings, from offices to public transportation hubs.
This evolution reflects broader trends in consumer behavior and technological advancements, providing B2B buyers with numerous opportunities to innovate and expand their product offerings. As the market continues to evolve, staying abreast of these historical shifts will be essential for making strategic sourcing decisions.
Related Video: How Global Trade Runs on U.S. Dollars | WSJ
Frequently Asked Questions (FAQs) for B2B Buyers of american rounds vending machine
-
What should I consider when vetting suppliers for American rounds vending machines?
When vetting suppliers, prioritize their experience and reputation in the vending machine market. Look for established companies with a track record of exporting to your region. Verify certifications and compliance with international standards, particularly those relevant to safety and quality. Request references from other international buyers in your area. Additionally, consider their customer service responsiveness and willingness to provide after-sales support, which is crucial for maintaining your machines. -
Can American rounds vending machines be customized to meet local preferences?
Yes, many suppliers offer customization options for American rounds vending machines to cater to local tastes and preferences. This can include adjusting the product offerings, modifying the machine’s design, or integrating payment systems that are popular in your region. When discussing customization, ensure that you communicate your specific needs clearly, and request samples or prototypes if possible. Customization can also enhance the machine’s appeal and increase sales in your target market. -
What are the typical minimum order quantities (MOQs) and lead times for these machines?
Minimum order quantities can vary significantly based on the supplier and the complexity of the machines. Generally, MOQs for American rounds vending machines range from 5 to 20 units. Lead times also differ, often falling between 4 to 12 weeks, depending on the customization and production schedules. It’s advisable to discuss these factors upfront with your supplier to plan your inventory and ensure timely delivery for your market launch. -
What payment terms are commonly accepted by suppliers of American rounds vending machines?
Payment terms can vary widely among suppliers. Most will accept options like bank transfers, letters of credit, or payment through secure platforms like PayPal for smaller orders. It’s important to clarify the payment schedule, including any deposits required before production. Negotiate terms that align with your cash flow needs, and be cautious of suppliers demanding full payment upfront, especially if you are working with them for the first time. -
How can I ensure quality assurance and certification for the machines?
To ensure quality, request detailed information about the supplier’s quality assurance processes and any relevant certifications, such as ISO 9001 or CE marking. Ask for inspection reports and product samples before finalizing your order. Additionally, consider arranging third-party inspections during production or before shipment to verify that the machines meet your specifications and compliance standards in your country. -
What logistics considerations should I keep in mind when importing these machines?
Logistics are crucial when importing American rounds vending machines. Be aware of shipping methods, customs regulations, and potential tariffs in your region. Work with experienced freight forwarders who understand the complexities of international shipping and can help navigate customs clearance. Ensure that your supplier provides all necessary documentation, including bills of lading and invoices, to facilitate a smooth import process. -
How should I handle disputes with suppliers?
Disputes can arise over quality, delivery times, or payment terms. To manage these effectively, establish clear communication channels and document all agreements in writing. If issues arise, first attempt to resolve them directly with the supplier. If direct negotiation fails, refer to the contract terms regarding dispute resolution. Consider involving a third-party mediator or legal expert familiar with international trade laws if necessary. -
What support can I expect after purchasing American rounds vending machines?
After purchasing, most reputable suppliers will offer some form of after-sales support, which may include installation assistance, maintenance services, and access to spare parts. Clarify the specifics of the support offered, including warranty terms and the duration of coverage. It’s beneficial to establish a relationship with the supplier for ongoing communication, which can help resolve any operational issues that may arise and ensure the longevity of your vending machines.
Strategic Sourcing Conclusion and Outlook for american rounds vending machine
As the market for American rounds vending machines continues to evolve, strategic sourcing emerges as a vital approach for international B2B buyers. By leveraging local suppliers and understanding regional consumer preferences, businesses can optimize their procurement strategies. Key takeaways include the importance of evaluating suppliers based on quality, reliability, and compliance with local regulations, which is especially crucial for markets in Africa, South America, the Middle East, and Europe.
Moreover, fostering partnerships with manufacturers that prioritize innovation can lead to a competitive edge. Buyers should also consider the implications of logistics and supply chain management, as these factors significantly impact the total cost of ownership.
Looking ahead, the demand for versatile and user-friendly vending solutions is expected to rise, making it essential for businesses to stay ahead of market trends. International buyers are encouraged to actively engage with suppliers, attend trade shows, and participate in industry forums to build valuable connections and gain insights into emerging technologies. By adopting a proactive approach to strategic sourcing, B2B buyers can not only enhance their operational efficiency but also secure a sustainable competitive advantage in the vending machine market.