Master Running a Vending Machine Business: Essential
Guide to Running A Vending Machine Business
- Introduction: Navigating the Global Market for running a vending machine business
- Understanding running a vending machine business Types and Variations
- Key Industrial Applications of running a vending machine business
- Strategic Material Selection Guide for running a vending machine business
- In-depth Look: Manufacturing Processes and Quality Assurance for running a vending machine business
- Comprehensive Cost and Pricing Analysis for running a vending machine business Sourcing
- Spotlight on Potential running a vending machine business Manufacturers and Suppliers
- Essential Technical Properties and Trade Terminology for running a vending machine business
- Navigating Market Dynamics, Sourcing Trends, and Sustainability in the running a vending machine business Sector
- Frequently Asked Questions (FAQs) for B2B Buyers of running a vending machine business
- Strategic Sourcing Conclusion and Outlook for running a vending machine business
Introduction: Navigating the Global Market for running a vending machine business
In an increasingly fast-paced world, the vending machine business stands as a compelling opportunity for international B2B buyers. The convenience of automated retailing has transformed consumer habits, making vending machines a popular choice across diverse markets, from bustling urban centers in Africa to the vibrant streets of South America, and even in the sophisticated environments of Europe and the Middle East. As a business model, vending machines offer a unique blend of low overhead, scalability, and flexibility, allowing entrepreneurs to cater to a variety of consumer preferences and demands.
This comprehensive guide serves as an invaluable resource for navigating the complexities of running a vending machine business. It covers essential topics including the different types of vending machines, materials used in their construction, manufacturing and quality control processes, reliable suppliers, cost considerations, and market trends. Additionally, it addresses frequently asked questions that arise in this dynamic industry.
By equipping B2B buyers with actionable insights and data-driven strategies, this guide empowers informed sourcing decisions that can lead to successful ventures in the vending machine sector. Whether you are based in Australia, Mexico, or anywhere in between, understanding these critical elements will help you capitalize on the growing demand for vending solutions and position your business for long-term success in the global market.
Understanding running a vending machine business Types and Variations
Type Name | Key Distinguishing Features | Primary B2B Applications | Brief Pros & Cons for Buyers |
---|---|---|---|
Traditional Snack Vending | Dispenses snacks and beverages, often coin-operated | Offices, schools, hospitals | Pros: Low maintenance, wide appeal. Cons: Limited product range, competition with convenience stores. |
Healthy Vending | Focuses on nutritious snacks and drinks | Gyms, health clubs, schools | Pros: Aligns with health trends, attracts health-conscious consumers. Cons: Higher product costs, niche market. |
Specialty Vending | Offers unique items (e.g., electronics, cosmetics) | Airports, malls, tourist attractions | Pros: High-profit margins, caters to specific consumer interests. Cons: Higher initial investment, requires careful product selection. |
Automated Retail Kiosks | High-tech vending with touchscreen interfaces | Retail environments, universities | Pros: Modern appeal, can offer a wide range of products. Cons: Higher maintenance costs, technology-dependent. |
Micro Markets | Self-service kiosks with open access to products | Office buildings, residential complexes | Pros: Greater product variety, operates without staff. Cons: Requires more space, initial setup costs can be high. |
Traditional Snack Vending
Traditional snack vending machines are the most common type, offering a range of snacks and beverages. They are typically coin-operated and require minimal maintenance, making them suitable for environments like offices, schools, and hospitals. Buyers should consider the location’s foot traffic and target demographics, as these factors will influence product selection and sales performance. While they have a broad appeal, competition with convenience stores can be a challenge.
Healthy Vending
Healthy vending machines focus on providing nutritious snacks and drinks, catering to the growing demand for healthier options. They are commonly found in gyms, health clubs, and schools, where health-conscious consumers are prevalent. Buyers should evaluate the cost of healthier products, which can be higher than traditional snacks, and consider the specific health trends in their target market. This type of vending aligns well with corporate wellness initiatives, making it an attractive option for B2B buyers.
Specialty Vending
Specialty vending machines offer unique products, such as electronics, cosmetics, or gourmet food items. These machines are typically placed in high-traffic areas like airports, malls, and tourist attractions. Buyers interested in this type should be prepared for higher initial investments and a more selective product approach, as success depends on carefully curated offerings that appeal to specific consumer interests. The potential for high-profit margins exists, but so does the risk of unsold inventory.
Automated Retail Kiosks
Automated retail kiosks incorporate advanced technology, often featuring touchscreen interfaces that enhance user experience. These machines can operate in various retail environments, including universities and shopping centers. While they can provide a diverse range of products, buyers should consider the higher maintenance costs and the reliance on technology. Additionally, understanding the target market’s tech-savviness is crucial for successful implementation.
Micro Markets
Micro markets consist of self-service kiosks that allow consumers to browse and select products without the need for staff. They are typically found in office buildings and residential complexes, providing a greater variety of items than traditional vending machines. Buyers should evaluate the space available for setup and the initial costs, as these can be significant. However, the ability to operate without staff and the appeal of a more extensive product offering can lead to increased sales and customer satisfaction.
Key Industrial Applications of running a vending machine business
Industry/Sector | Specific Application of running a vending machine business | Value/Benefit for the Business | Key Sourcing Considerations for this Application |
---|---|---|---|
Education | Snack and beverage vending in schools and universities | Enhances student satisfaction and convenience | Compliance with health regulations, variety of options |
Healthcare | Medicine and health product vending in hospitals | Improves access to essential items for patients | Security features, temperature control for perishables |
Corporate Offices | Refreshment vending for employee break rooms | Boosts employee morale and productivity | Customization options, reliable supply chain |
Transportation Hubs | Vending services in airports and train stations | Provides quick access to snacks for travelers | High durability, payment flexibility |
Hospitality | Mini-bar vending solutions in hotels | Increases guest convenience and generates revenue | Inventory management, aesthetic design |
Education
In educational institutions, vending machines serve as a convenient source for snacks and beverages for students and staff. These machines can be strategically placed in high-traffic areas, providing easy access to food options during breaks. The key for B2B buyers in this sector is to ensure compliance with health regulations, offering healthy choices that align with dietary needs. Additionally, a diverse product range can enhance student satisfaction and promote healthier eating habits.
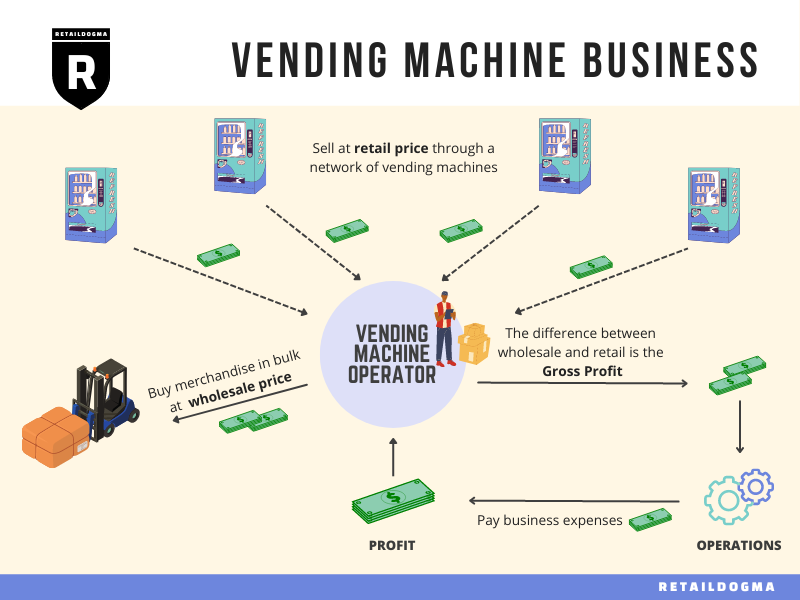
Illustrative Image (Source: Google Search)
Healthcare
In healthcare settings, vending machines that dispense medicines and health-related products are increasingly popular. These machines provide patients and staff quick access to essential items, reducing wait times and improving overall service efficiency. For international B2B buyers in the healthcare industry, it is crucial to consider security features to prevent unauthorized access and temperature controls to maintain the integrity of perishable medical products. Compliance with healthcare regulations is also essential to ensure safety and reliability.
Corporate Offices
Vending machines in corporate environments are vital for employee satisfaction and productivity. By offering a range of refreshments in break rooms, companies can foster a positive workplace culture. B2B buyers in this sector should focus on customization options to cater to diverse employee preferences and ensure a reliable supply chain to avoid stockouts. This approach not only enhances employee morale but also serves as a cost-effective solution for providing snacks and beverages.
Transportation Hubs
Vending machines located in airports and train stations cater to the needs of travelers looking for quick snacks and drinks on the go. The convenience offered by these machines can significantly enhance the travel experience. For buyers in this sector, sourcing machines that are durable and capable of handling high foot traffic is essential. Additionally, offering various payment options, including mobile payments, can improve accessibility for international travelers.
Hospitality
In the hospitality industry, mini-bar vending solutions in hotels provide guests with easy access to snacks and drinks without the need for staff intervention. This model not only enhances guest convenience but also opens up additional revenue streams for hotel operators. B2B buyers should consider factors such as aesthetic design and inventory management systems to streamline operations and enhance the guest experience. Customization of product offerings can further align with the hotel’s brand and guest preferences.
Related Video: How to Start a Vending Machine Business, Cost, Tips, How Much You Make
Strategic Material Selection Guide for running a vending machine business
Material Analysis for Vending Machine Business
When selecting materials for a vending machine business, several factors must be considered, including durability, cost, and compliance with international standards. Here, we analyze four common materials used in the construction of vending machines, focusing on their properties, advantages, disadvantages, and specific considerations for international B2B buyers.
1. Stainless Steel
Key Properties: Stainless steel is known for its excellent corrosion resistance, high strength, and ability to withstand high temperatures. It typically has a temperature rating of up to 800°C and can handle pressures up to 150 psi, depending on the grade.
Pros & Cons: The primary advantage of stainless steel is its durability and resistance to rust and stains, making it ideal for environments where hygiene is critical. However, it can be more expensive than other materials, and its manufacturing process is complex, which may lead to longer lead times.
Impact on Application: Stainless steel is compatible with a wide range of media, including beverages and snacks, and is often used for machine exteriors and internal components that require frequent cleaning.
Considerations for International Buyers: Buyers should ensure compliance with international standards such as ASTM A240 for stainless steel sheets. In regions like Africa and South America, sourcing local suppliers can mitigate costs associated with import tariffs.
2. Aluminum
Key Properties: Aluminum is lightweight, has good corrosion resistance, and can withstand temperatures up to 600°C. Its pressure rating varies significantly based on the alloy used.
Pros & Cons: The main advantage of aluminum is its low weight, which makes it easier to transport and install. However, it is less durable than stainless steel and may not withstand heavy impacts, which can be a limitation in high-traffic areas.
Impact on Application: Aluminum is suitable for components that do not require high strength, such as panels and frames. It is also commonly used in vending machines for its aesthetic appeal.
Considerations for International Buyers: Buyers should be aware of the differences in aluminum grades and their respective standards (e.g., ASTM B221). In Europe, compliance with EN standards is essential, while in the Middle East, local regulations may apply.
3. Polycarbonate
Key Properties: Polycarbonate is a high-performance plastic known for its impact resistance and clarity. It can withstand temperatures up to 120°C and is resistant to UV light.
Pros & Cons: The key advantage of polycarbonate is its lightweight nature and high impact resistance, making it ideal for transparent panels and displays. However, it can be prone to scratching and may not be as durable as metals.
Impact on Application: Polycarbonate is often used for the viewing windows of vending machines, allowing customers to see the products inside. Its transparency enhances the visual appeal of the machine.
Considerations for International Buyers: Buyers should check for compliance with safety standards such as ISO 9001. In regions like South America, where UV exposure may be high, selecting UV-stabilized polycarbonate is advisable.
4. Carbon Steel
Key Properties: Carbon steel is strong and cost-effective, with a temperature rating of up to 300°C. However, it is susceptible to corrosion if not properly treated.
Pros & Cons: The primary advantage of carbon steel is its low cost and high strength, making it suitable for structural components. The downside is its vulnerability to rust, requiring protective coatings or treatments.
Impact on Application: Carbon steel is often used for the internal framework of vending machines, where strength is critical. However, it is less suitable for external surfaces exposed to moisture.
Considerations for International Buyers: Buyers should ensure compliance with standards such as ASTM A36. In regions with high humidity, such as parts of Africa and the Middle East, additional corrosion protection measures should be considered.
Summary Table
Material | Typical Use Case for running a vending machine business | Key Advantage | Key Disadvantage/Limitation | Relative Cost (Low/Med/High) |
---|---|---|---|---|
Stainless Steel | Machine exteriors, internal components | Excellent durability and hygiene | Higher cost, complex manufacturing | High |
Aluminum | Panels and frames | Lightweight and easy to install | Less durable than stainless steel | Medium |
Polycarbonate | Viewing windows | High impact resistance, clarity | Prone to scratching | Medium |
Carbon Steel | Structural components | Cost-effective, strong | Susceptible to corrosion | Low |
This strategic material selection guide provides actionable insights for international B2B buyers, ensuring they make informed decisions that align with their operational needs and regional compliance requirements.
In-depth Look: Manufacturing Processes and Quality Assurance for running a vending machine business
Manufacturing Processes for Vending Machines
The manufacturing of vending machines involves several critical stages that ensure the final product meets both functional and aesthetic standards. Understanding these processes can help international B2B buyers make informed decisions about sourcing and quality assurance.
Main Stages of Manufacturing
-
Material Preparation
– The initial phase involves selecting and preparing raw materials, which typically include metals, plastics, and electronic components. Suppliers should provide certifications for materials to ensure compliance with local regulations and international standards.
– Key Techniques:- Cutting and Shaping: Metals are cut using laser cutting or CNC machining, while plastics are often molded through injection molding.
- Surface Treatment: Processes such as powder coating or anodizing are employed to enhance durability and aesthetics.
-
Forming
– This stage involves transforming raw materials into specific shapes required for the vending machine components.
– Key Techniques:- Bending and Stamping: Metals are bent into desired shapes using hydraulic presses, while stamping is used for creating intricate designs and cutouts.
- Molding: For plastic components, various molding techniques (e.g., blow molding) are utilized to achieve the necessary shapes.
-
Assembly
– The assembly process combines all components into a cohesive unit. This stage requires precision to ensure that all parts fit together correctly and function as intended.
– Key Techniques:- Automated Assembly Lines: Robotics may be used for high-volume production, ensuring speed and consistency.
- Manual Assembly: For complex parts or lower volumes, skilled labor may be employed to assemble components carefully.
- Finishing
– The final stage involves adding any necessary finishes or coatings to enhance the product’s appearance and functionality.
– Key Techniques:- Painting and Coating: This includes applying protective coatings to prevent corrosion and improve aesthetics.
- Quality Checks: Each machine undergoes a final inspection to ensure it meets quality standards before shipping.
Quality Assurance in Vending Machine Manufacturing
Quality assurance (QA) is vital for ensuring that vending machines operate reliably and meet customer expectations. B2B buyers should be aware of the relevant international standards and quality control checkpoints.
International Standards
- ISO 9001: This standard outlines the criteria for a quality management system and is crucial for manufacturers looking to establish a robust QA framework. Compliance indicates a commitment to quality and continuous improvement.
- CE Marking: In Europe, CE marking demonstrates that a product meets safety, health, and environmental protection standards, which is essential for vending machines.
- API Standards: For vending machines that dispense food or beverages, adherence to American Petroleum Institute (API) standards may be necessary to ensure safety and compatibility.
Quality Control Checkpoints
-
Incoming Quality Control (IQC)
– This initial checkpoint involves inspecting raw materials upon arrival at the manufacturing facility. Verifying that materials meet specified standards is crucial for maintaining product quality. -
In-Process Quality Control (IPQC)
– Throughout the manufacturing process, regular checks are performed to monitor compliance with specifications. This can include visual inspections and functional tests on components as they are produced. -
Final Quality Control (FQC)
– Once the vending machines are fully assembled, they undergo thorough testing to ensure they function correctly. This may include electrical testing, performance checks, and safety assessments.
Common Testing Methods
- Functional Testing: Each machine is tested for operational efficiency, including payment processing and product dispensing mechanisms.
- Durability Testing: Machines are subjected to stress tests to evaluate their resilience under various conditions, such as temperature and humidity extremes.
- Safety Testing: This includes checks for electrical safety, ensuring that machines comply with relevant electrical codes and standards.
Verifying Supplier Quality Control
For international B2B buyers, especially those from Africa, South America, the Middle East, and Europe, verifying the quality control practices of suppliers is crucial. Here are effective methods to ensure quality:
-
Audits: Conduct regular audits of suppliers’ manufacturing facilities to assess their compliance with international standards and internal QA processes. This can include reviewing documentation, inspecting production lines, and evaluating safety protocols.
-
Quality Reports: Request detailed quality assurance reports from suppliers. These should outline the results of IQC, IPQC, and FQC processes, including any non-conformance issues and corrective actions taken.
-
Third-Party Inspections: Engage independent third-party inspection services to verify the quality of products before shipment. This can provide an unbiased assessment and increase confidence in the supplier’s capabilities.
Quality Control Nuances for International B2B Buyers
-
Regulatory Compliance: Buyers must be aware of the specific regulatory requirements for vending machines in their respective countries. Understanding local laws can prevent costly compliance issues.
-
Cultural Considerations: Different regions may have varying expectations regarding quality and performance. B2B buyers should communicate their quality standards clearly to suppliers to avoid misunderstandings.
-
Supply Chain Transparency: Establishing transparent communication channels with suppliers is vital. This includes sharing expectations regarding quality standards and being open to feedback during the manufacturing process.
In conclusion, understanding the manufacturing processes and quality assurance practices for vending machines is essential for international B2B buyers. By focusing on these aspects, businesses can ensure they source reliable, high-quality vending machines that meet the diverse needs of their markets.
Related Video: The Production Planning Process
Comprehensive Cost and Pricing Analysis for running a vending machine business Sourcing
To successfully navigate the vending machine business landscape, understanding the comprehensive cost structure and pricing analysis is critical for international B2B buyers. The cost components involved in sourcing vending machines are multifaceted and can significantly impact the overall financial viability of the venture.
Cost Components
-
Materials: The primary costs arise from the materials used in vending machine production. This includes metals, plastics, and electronic components. Sourcing quality materials is essential, as it directly influences the machine’s durability and functionality.
-
Labor: Labor costs vary significantly based on geographical location. In regions with higher wages, labor costs will be more substantial, affecting the final price. Understanding local labor markets in Africa, South America, the Middle East, and Europe can help buyers gauge these costs.
-
Manufacturing Overhead: This encompasses indirect costs such as utilities, rent, and equipment depreciation. It’s important for buyers to consider suppliers’ overhead rates, as these can vary widely across different regions and impact pricing.
-
Tooling: Tooling costs are associated with the creation of molds and machinery necessary for production. These are often significant for custom machines and should be factored into the total cost.
-
Quality Control (QC): Ensuring product quality through rigorous QC processes is essential. Investing in quality control can mitigate the risk of defects and returns, which can be costly.
-
Logistics: Shipping and handling costs are critical, especially for international buyers. Factors such as shipping distance, mode of transport, and the complexity of customs regulations can add to logistics expenses.
-
Margin: Suppliers typically incorporate a profit margin into their pricing, which can fluctuate based on demand, competition, and market conditions. Understanding the margin expectations of suppliers in different regions can aid in negotiations.
Price Influencers
Several factors can influence the pricing structure of vending machines:
-
Volume/MOQ (Minimum Order Quantity): Bulk purchases often lead to lower per-unit costs. Negotiating for favorable terms on larger orders can significantly reduce overall expenditure.
-
Specifications/Customization: Custom features or specifications can increase costs. Buyers should clarify their requirements early on to avoid unexpected expenses.
-
Materials: The choice of materials impacts both quality and cost. Buyers should explore alternative materials that may offer cost savings without sacrificing quality.
-
Quality/Certifications: Machines that meet certain quality standards or certifications may command higher prices. However, investing in certified machines can lead to long-term savings through reduced maintenance and increased reliability.
-
Supplier Factors: The reputation and reliability of the supplier can affect pricing. Established suppliers may offer better quality but at a premium. Conducting thorough supplier evaluations is essential.
-
Incoterms: Understanding international shipping terms (Incoterms) is vital. These terms define the responsibilities of buyers and sellers in logistics, affecting overall costs.
Buyer Tips
-
Negotiation: Approach negotiations with a clear understanding of your budget and the market. Leverage data on competitor pricing to secure better deals.
-
Cost-Efficiency: Analyze the Total Cost of Ownership (TCO) rather than just the initial purchase price. Consider long-term operational costs, including maintenance, energy consumption, and potential downtime.
-
Pricing Nuances: Be aware of regional pricing strategies. For example, suppliers in Europe may have different pricing structures compared to those in Africa or South America due to varying economic conditions.
-
Local Market Insights: Engage with local suppliers and industry experts to gain insights into market trends and pricing strategies specific to your region.
Disclaimer
Prices and cost structures can vary widely based on numerous factors, including market conditions, supplier negotiations, and specific machine configurations. It is advisable for buyers to conduct thorough research and obtain multiple quotes to ensure they are making informed purchasing decisions.
Spotlight on Potential running a vending machine business Manufacturers and Suppliers
This section offers a look at a few manufacturers active in the ‘running a vending machine business’ market. This is a representative sample for illustrative purposes; B2B buyers must conduct their own extensive due diligence before any engagement. Information is synthesized from public sources and general industry knowledge.
Essential Technical Properties and Trade Terminology for running a vending machine business
Key Technical Properties for Vending Machines
When considering the operation of a vending machine business, understanding the technical specifications of the machines is crucial. Here are several essential properties that should be taken into account:
-
Material Grade
– Definition: The quality of materials used in vending machines, typically stainless steel or high-grade plastics.
– Importance: Higher material grades offer better durability and corrosion resistance, which is essential for machines exposed to varying climates, particularly in regions like Africa and South America. This impacts the longevity of the machines and reduces maintenance costs. -
Power Consumption
– Definition: The amount of electricity a vending machine requires to operate efficiently.
– Importance: Understanding power consumption is vital for calculating operating costs. Machines with lower energy requirements can significantly reduce overhead expenses, making them more attractive to buyers, especially in regions with high energy costs. -
Capacity
– Definition: The number of items a vending machine can hold, measured in slots or total volume.
– Importance: The capacity directly influences sales potential. A higher capacity machine can serve more customers without frequent restocking, which is especially beneficial in high-traffic areas.
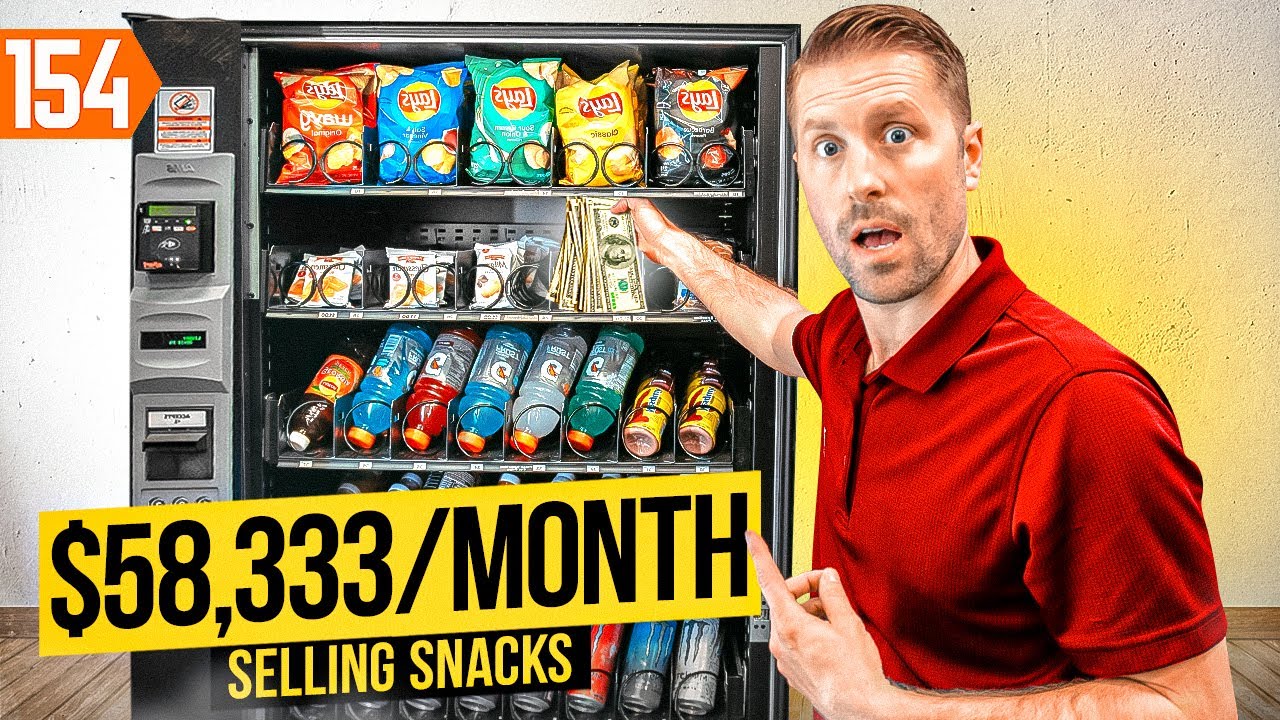
Illustrative Image (Source: Google Search)
-
Dimensions and Weight
– Definition: The physical size and weight of the vending machine.
– Importance: These specifications affect placement options and transportation costs. For international buyers, understanding these dimensions is crucial for shipping logistics and compliance with local regulations. -
Temperature Control
– Definition: The ability of a vending machine to maintain specific temperatures for products, particularly for refrigerated items.
– Importance: This is critical for food safety and product quality. Machines with advanced temperature control systems can minimize spoilage and enhance customer satisfaction, particularly in warmer climates. -
User Interface Technology
– Definition: The technology used for customer interaction, including touchscreens, card readers, and mobile payment options.
– Importance: A modern user interface can improve customer experience and increase sales. It’s especially relevant in regions with high smartphone penetration and digital payment adoption.
Common Trade Terminology in Vending Machine Business
Navigating the vending machine industry requires familiarity with specific jargon. Here are several key terms:
-
OEM (Original Equipment Manufacturer)
– Definition: A company that produces parts and equipment that may be marketed by another manufacturer.
– Importance: Understanding OEM relationships is essential for B2B buyers seeking quality components or machines, ensuring they are investing in reliable products. -
MOQ (Minimum Order Quantity)
– Definition: The smallest quantity of a product that a supplier is willing to sell.
– Importance: Knowing the MOQ helps businesses manage inventory and cash flow effectively. It is crucial for international buyers to negotiate favorable terms that align with their market demands. -
RFQ (Request for Quotation)
– Definition: A document that solicits a quote from suppliers for specific products or services.
– Importance: RFQs are a critical step in the procurement process, allowing buyers to compare prices and services from various vendors, ensuring they make informed purchasing decisions. -
Incoterms (International Commercial Terms)
– Definition: A set of predefined international rules that clarify the responsibilities of buyers and sellers in international transactions.
– Importance: Familiarity with Incoterms is vital for international B2B transactions, as they dictate shipping responsibilities, risk management, and cost allocation. -
Lead Time
– Definition: The time between the initiation of a process and its completion, particularly in manufacturing and delivery.
– Importance: Understanding lead times is crucial for inventory management. It helps businesses plan for demand and avoid stockouts, which can impact customer satisfaction. -
Warranty
– Definition: A guarantee provided by the manufacturer regarding the condition of the product and the terms for repair or replacement.
– Importance: Knowledge of warranty terms is essential for buyers to assess the risk and reliability of their investments in vending machines. A strong warranty can offer peace of mind and reduce long-term costs.
By grasping these technical properties and trade terms, international B2B buyers can make more informed decisions when investing in vending machines, ultimately enhancing their business operations and profitability.
Navigating Market Dynamics, Sourcing Trends, and Sustainability in the running a vending machine business Sector
Market Overview & Key Trends
The vending machine business is witnessing dynamic shifts, driven by technological advancements and changing consumer behaviors. Globally, the rise of contactless payment systems and mobile wallet integrations has transformed how consumers interact with vending machines. This trend is particularly strong in regions like Europe and Australia, where technology adoption is high. In contrast, markets in Africa and South America are gradually catching up, with an increasing number of machines being equipped to accept digital payments.
Emerging technologies such as AI and IoT are enabling operators to optimize inventory management and enhance customer experience. For example, smart vending machines equipped with sensors can monitor stock levels in real time, allowing for efficient restocking processes. Additionally, data analytics tools are being utilized to analyze consumer purchasing patterns, enabling tailored product offerings that cater to local preferences.
International buyers should also be aware of the regulatory landscape, which is increasingly focused on consumer safety and product labeling. As such, compliance with local laws in the regions they operate in is essential. The demand for healthy snack options is another notable trend, influenced by a global push towards healthier lifestyles. This shift is particularly evident in educational institutions and corporate environments, where vending machines are increasingly stocked with nutritious alternatives.
Sustainability & Ethical Sourcing in B2B
Sustainability is becoming a cornerstone of the vending machine industry, impacting both sourcing and operational practices. As environmental concerns rise globally, businesses are under pressure to minimize their ecological footprint. For B2B buyers, selecting suppliers who prioritize sustainability can enhance their brand reputation and meet consumer expectations for ethical business practices.
Incorporating eco-friendly materials into vending machines—such as recycled plastics and biodegradable packaging—can significantly reduce environmental impact. Additionally, suppliers offering certifications such as FSC (Forest Stewardship Council) or Cradle to Cradle can help businesses demonstrate their commitment to sustainability.
Moreover, energy-efficient vending machines that utilize LED lighting and low-energy refrigeration systems not only lower operational costs but also appeal to environmentally conscious consumers. Adopting a sustainable supply chain is crucial; this includes ensuring that suppliers adhere to ethical labor practices and environmental regulations. By prioritizing sustainability and ethical sourcing, B2B buyers can position themselves as leaders in responsible vending solutions.
Brief Evolution/History
The vending machine industry has evolved significantly since its inception in the early 1880s, originally offering simple items like postcards and cigarettes. The introduction of electric vending machines in the 20th century paved the way for greater product variety, including snacks and beverages. Over the decades, technological advancements have transformed the landscape, with cashless payment systems and smart vending solutions emerging in the 21st century. Today, the industry is characterized by a focus on customer experience, technology integration, and sustainability, reflecting broader societal shifts towards convenience and ethical consumption. For B2B buyers, understanding this evolution is key to navigating current market dynamics and capitalizing on emerging opportunities.
Related Video: Can India-US Secure Trade Deal Soon? | Trump Tariffs War | Global Trade War | US News | News18
Frequently Asked Questions (FAQs) for B2B Buyers of running a vending machine business
-
What criteria should I use to vet suppliers for vending machines?
When vetting suppliers, focus on their experience, reputation, and product quality. Check for certifications relevant to your market, such as ISO or CE markings, which indicate adherence to international standards. Request references or case studies from existing clients, particularly those in your region. Additionally, consider their financial stability and production capabilities to ensure they can meet your demand consistently. -
Can I customize vending machines to fit my brand?
Yes, many suppliers offer customization options for vending machines, including branding, color schemes, and product selection. Discuss your specific requirements upfront to ensure the supplier can accommodate your needs. Customization can enhance brand visibility and customer engagement, so consider this aspect as part of your overall business strategy. -
What is the typical minimum order quantity (MOQ) for vending machines?
MOQs can vary significantly among suppliers, often ranging from a few units to several dozen. When negotiating, consider your budget and storage capabilities. If you are a new entrant, seek suppliers willing to offer lower MOQs or flexible terms. This approach can help you manage initial costs while testing the market response to your vending offerings. -
What are the usual lead times for ordering vending machines?
Lead times typically depend on the supplier’s location, production capacity, and your specific order details. On average, expect a lead time of 4 to 12 weeks from order confirmation to delivery. It’s advisable to discuss lead times during your initial conversations with suppliers to align your business plans accordingly, especially if you have a specific launch date in mind. -
How can I ensure the quality of the vending machines I purchase?
To ensure quality, request samples or visit the supplier’s manufacturing facility if possible. Ask for quality assurance certifications and details about their production processes. Additionally, establish a clear quality control agreement that outlines inspection protocols and what constitutes acceptable quality levels. This proactive approach helps mitigate risks associated with poor-quality products. -
What logistics considerations should I keep in mind when importing vending machines?
Logistics can be complex, especially when dealing with international suppliers. Consider factors such as shipping methods, customs regulations, and import duties. Work with a logistics partner experienced in handling machinery to ensure compliance and timely delivery. Also, factor in local regulations regarding the installation and operation of vending machines in your target market. -
How should I handle disputes with suppliers?
To effectively manage disputes, establish clear terms and conditions in your purchase agreement, including dispute resolution mechanisms. Maintain open communication throughout the process, and document all interactions. If a dispute arises, attempt to resolve it amicably through negotiation. If necessary, consider mediation or arbitration as alternative dispute resolution methods before escalating to legal action. -
What certifications should I look for in vending machine suppliers?
Look for certifications that indicate compliance with international safety and quality standards. Common certifications include ISO 9001 for quality management, CE marking for European markets, and UL certification for electrical safety. These certifications not only ensure product reliability but also enhance your credibility when marketing to customers, particularly in regulated markets.
Strategic Sourcing Conclusion and Outlook for running a vending machine business
In conclusion, strategic sourcing is fundamental for the success and sustainability of a vending machine business in today’s competitive landscape. By leveraging data-driven insights, international B2B buyers can optimize supplier relationships, reduce costs, and enhance product offerings. Key takeaways include the importance of identifying reliable suppliers, negotiating favorable terms, and continuously assessing market trends to adapt to consumer preferences.
Additionally, investing in technology—such as inventory management systems and customer engagement tools—can streamline operations and improve profitability. As markets in Africa, South America, the Middle East, and Europe continue to evolve, businesses that prioritize strategic sourcing will be better positioned to capitalize on emerging opportunities.
Looking ahead, now is the time for international buyers to forge partnerships that can innovate and differentiate their vending machine offerings. By embracing strategic sourcing principles, you can not only enhance your operational efficiencies but also create a compelling value proposition for your customers. Take proactive steps today to secure your place in this dynamic industry and ensure long-term success.