Master Owning a Vending Machine: Your Ultimate B2B Guide
Guide to Owning A Vending Machine
- Introduction: Navigating the Global Market for owning a vending machine
- Understanding owning a vending machine Types and Variations
- Key Industrial Applications of owning a vending machine
- Strategic Material Selection Guide for owning a vending machine
- In-depth Look: Manufacturing Processes and Quality Assurance for owning a vending machine
- Comprehensive Cost and Pricing Analysis for owning a vending machine Sourcing
- Spotlight on Potential owning a vending machine Manufacturers and Suppliers
- Essential Technical Properties and Trade Terminology for owning a vending machine
- Navigating Market Dynamics, Sourcing Trends, and Sustainability in the owning a vending machine Sector
- Frequently Asked Questions (FAQs) for B2B Buyers of owning a vending machine
- Strategic Sourcing Conclusion and Outlook for owning a vending machine
Introduction: Navigating the Global Market for owning a vending machine
In today’s fast-paced world, the vending machine industry presents a lucrative opportunity for B2B buyers looking to diversify their revenue streams and capitalize on the growing demand for convenience. With global sales projected to continue their upward trajectory, owning a vending machine can serve as a reliable source of passive income while meeting consumer needs across various sectors. This guide is designed to equip international buyers—especially those from Africa, South America, the Middle East, and Europe—with the insights needed to navigate this dynamic market effectively.
Throughout this comprehensive guide, we will explore the different types of vending machines available, the materials and manufacturing quality standards to consider, and potential suppliers that align with your business goals. We will also delve into cost structures, market trends, and frequently asked questions that can empower informed sourcing decisions. Understanding these elements is crucial for establishing a successful vending machine operation, whether in bustling urban centers or niche markets.
By leveraging the knowledge presented here, B2B buyers can make strategic choices that enhance their competitive advantage, ensuring they provide the right products in the right locations. As you embark on this journey, the insights shared will serve as a roadmap to navigate the complexities of owning a vending machine, driving profitability and growth in your business.
Understanding owning a vending machine Types and Variations
Type Name | Key Distinguishing Features | Primary B2B Applications | Brief Pros & Cons for Buyers |
---|---|---|---|
Snack Vending Machines | Dispenses packaged snacks and confectionery | Offices, schools, gyms | Pros: Low maintenance, popular items. Cons: Limited to snacks, may require frequent restocking. |
Beverage Vending Machines | Offers a variety of drinks, including cold beverages | Airports, hospitals, offices | Pros: High demand, 24/7 availability. Cons: Can be affected by temperature and shelf life. |
Combo Vending Machines | Combines snacks and beverages in one unit | Cafeterias, break rooms, events | Pros: Versatile, caters to diverse preferences. Cons: Higher initial cost, more complex maintenance. |
Healthy Vending Machines | Focuses on nutritious snacks and drinks | Gyms, wellness centers, schools | Pros: Growing market demand, promotes healthy choices. Cons: Potentially higher product costs, niche market. |
Specialty Vending Machines | Offers unique products like electronics or personal care items | Airports, malls, tech hubs | Pros: Differentiates from standard machines, caters to specific needs. Cons: Limited market, requires careful product selection. |
Snack Vending Machines
Snack vending machines are designed to dispense a wide range of packaged snacks and confectionery items. They are commonly placed in high-traffic areas such as offices, schools, and gyms, where quick and convenient access to snacks is desired. For B2B buyers, the key considerations include selecting machines with reliable inventory tracking systems to minimize downtime and ensuring that popular items are consistently stocked. While these machines require relatively low maintenance, they may necessitate frequent restocking to keep up with demand.
Beverage Vending Machines
Beverage vending machines specialize in offering a variety of drinks, including soft drinks, bottled water, and juices. They are ideal for locations like airports, hospitals, and offices, where consumers often seek refreshing beverages on the go. B2B buyers should consider the machine’s cooling capabilities and payment options, as modern machines increasingly support cashless transactions. Although beverage machines can generate substantial sales, they are sensitive to temperature variations, making proper maintenance essential to ensure product quality.
Combo Vending Machines
Combo vending machines combine both snacks and beverages in a single unit, providing convenience for consumers seeking a quick meal or snack. These machines are well-suited for cafeterias, break rooms, and event venues, where diverse offerings are appreciated. For B2B purchasers, the versatility of combo machines can attract a broader customer base. However, they often come with a higher initial cost and may require more complex maintenance due to their dual-functionality.
Healthy Vending Machines
Healthy vending machines focus on offering nutritious snacks and beverages, catering to the growing demand for healthier food options. They are typically placed in gyms, wellness centers, and schools, where health-conscious consumers are prevalent. B2B buyers should evaluate the product sourcing to ensure quality and appeal to local tastes. While these machines can tap into a lucrative niche market, the higher product costs and limited selection may pose challenges in certain areas.
Specialty Vending Machines
Specialty vending machines provide unique products, ranging from electronics to personal care items, targeting specific consumer needs in high-traffic environments like airports and malls. For B2B buyers, the key is to identify a niche market with sufficient demand, as these machines can differentiate their offerings from standard vending options. However, careful product selection is crucial, as the market for specialty items can be limited, and success relies heavily on understanding consumer preferences.
Related Video: How To Start A Vending Machine Business Step-By-Step (With $0)
Key Industrial Applications of owning a vending machine
Industry/Sector | Specific Application of owning a vending machine | Value/Benefit for the Business | Key Sourcing Considerations for this Application |
---|---|---|---|
Healthcare | Medicine and Health Supplies Vending | Provides quick access to essential items, improving patient care and satisfaction | Compliance with health regulations, machine sanitation, and product sourcing from certified suppliers |
Education | Snack and Beverage Vending in Schools | Enhances student convenience and satisfaction, providing healthy options to promote wellness | Understanding local dietary preferences, nutritional guidelines, and partnership with local suppliers |
Corporate Offices | Coffee and Snack Stations | Boosts employee morale and productivity by offering convenient refreshments | Selection of high-quality machines, variety of products, and reliable maintenance services |
Transportation Hubs | Travel Essentials Vending | Meets the needs of travelers for quick snacks and essentials, enhancing customer experience | Strategic placement in high-traffic areas, diverse product offerings, and partnerships with local vendors |
Fitness Centers | Healthy Snack and Beverage Vending | Supports health-conscious clientele by providing nutritious options, increasing facility appeal | Sourcing from health-focused suppliers, machine features for cashless payments, and regular inventory updates |
Healthcare
In the healthcare sector, vending machines can be deployed to dispense medicine and health supplies, such as band-aids, antiseptics, or personal hygiene products. This application addresses the challenge of ensuring patients and visitors have quick access to essential items without the need for pharmacy staff. International buyers must consider compliance with local health regulations and ensure that the machines are regularly sanitized. Sourcing products from certified suppliers is critical to maintaining safety and efficacy standards.
Education
Vending machines in schools offer snacks and beverages tailored to student preferences, promoting convenience and healthy eating habits. This application can help schools manage snack distribution efficiently while addressing the increasing demand for healthier options. Buyers should understand local dietary preferences and nutritional guidelines to ensure compliance with school policies. Partnering with local suppliers can also help in sourcing products that resonate with the student body.
Corporate Offices
In corporate environments, vending machines can serve coffee and snacks, significantly enhancing employee satisfaction and productivity. This application provides staff with easy access to refreshments during work hours, which can contribute to a more enjoyable workplace culture. When sourcing machines, businesses should prioritize high-quality options that offer diverse products and ensure reliable maintenance services to minimize downtime.
Transportation Hubs
Vending machines strategically placed in transportation hubs like airports and train stations can provide travelers with quick access to snacks and essentials. This application caters to the fast-paced nature of travel, ensuring that customers have convenient options readily available. Buyers should focus on high-traffic areas for placement and consider offering a diverse range of products to meet various customer needs. Collaborating with local vendors can enhance product offerings and ensure freshness.
Fitness Centers
Fitness centers can utilize vending machines to provide healthy snacks and beverages, catering to health-conscious clientele. This application not only supports the wellness goals of gym-goers but also enhances the overall appeal of the facility. When sourcing products, it is essential to focus on health-oriented suppliers and consider machine features that support cashless payments for convenience. Regular inventory updates based on customer preferences can further optimize sales and customer satisfaction.
Related Video: How to Start a Vending Machine Business, Cost, Tips, How Much You Make
Strategic Material Selection Guide for owning a vending machine
When selecting materials for vending machines, it is crucial to consider properties that affect performance, durability, and compliance with international standards. Below, we analyze four common materials used in vending machine construction, focusing on their key properties, advantages, disadvantages, and specific considerations for international B2B buyers.
1. Stainless Steel
Key Properties:
Stainless steel is known for its excellent corrosion resistance, high strength, and ability to withstand high temperatures. It typically has a temperature rating of up to 800°C (1472°F) and can handle moderate pressure.
Pros & Cons:
The primary advantage of stainless steel is its durability and resistance to rust and staining, making it ideal for environments where hygiene is critical, such as food and beverage vending. However, it is relatively expensive compared to other materials and can be more complex to manufacture due to its hardness.
Impact on Application:
Stainless steel is compatible with a wide range of media, including water, soft drinks, and snacks. Its non-porous surface helps maintain hygiene, which is vital for food safety.
International Considerations:
B2B buyers must ensure compliance with local food safety regulations and standards, such as ASTM and ISO. In regions like Europe, the use of food-grade stainless steel (e.g., AISI 304 or 316) is often required.
2. Mild Steel
Key Properties:
Mild steel is characterized by its good weldability and machinability, with a tensile strength typically around 370 MPa. It has moderate corrosion resistance and can be treated for enhanced durability.
Pros & Cons:
Mild steel is cost-effective and widely available, making it a popular choice for vending machine frames. However, it is susceptible to corrosion if not properly coated or maintained, which can lead to increased long-term costs.
Impact on Application:
This material is suitable for non-food contact surfaces and structural components. It is less ideal for areas exposed to moisture or food products unless adequately protected.
International Considerations:
Buyers should consider local standards for structural integrity and corrosion resistance, especially in humid climates found in parts of Africa and South America. Coatings like galvanization or powder coating may be necessary to comply with local regulations.
3. Polycarbonate
Key Properties:
Polycarbonate is a thermoplastic known for its high impact resistance and clarity. It can withstand temperatures from -40°C to 120°C (-40°F to 248°F) and is lightweight.
Pros & Cons:
The primary advantage of polycarbonate is its shatter resistance, making it suitable for transparent panels in vending machines. However, it can be more expensive than glass and may scratch easily without proper treatment.
Impact on Application:
Polycarbonate is ideal for viewing windows and protective covers, ensuring visibility of products while providing safety. It is not suitable for high-temperature applications.
International Considerations:
B2B buyers should ensure that polycarbonate materials meet relevant safety standards, such as those set by ASTM or EU regulations. Its use in regions with extreme weather conditions may require additional UV protection.
4. Aluminum
Key Properties:
Aluminum is lightweight, corrosion-resistant, and has a tensile strength of about 70 MPa. It can be anodized for improved durability and aesthetic appeal.
Pros & Cons:
Aluminum’s lightweight nature makes it easy to transport and install, and its corrosion resistance is beneficial for outdoor vending machines. However, it can be less durable than stainless steel and may dent easily.
Impact on Application:
Aluminum is suitable for machine casings and components that do not require high strength. Its lightweight nature can enhance the portability of vending machines.
International Considerations:
Buyers should be aware of recycling standards and environmental regulations in their respective regions, as aluminum is highly recyclable. Compliance with local standards for structural integrity is also essential.
Summary Table
Material | Typical Use Case for owning a vending machine | Key Advantage | Key Disadvantage/Limitation | Relative Cost (Low/Med/High) |
---|---|---|---|---|
Stainless Steel | Machine casing, food contact surfaces | Excellent corrosion resistance | Higher cost and manufacturing complexity | High |
Mild Steel | Structural components, non-food surfaces | Cost-effective | Susceptible to corrosion | Low |
Polycarbonate | Viewing windows, protective covers | Shatter-resistant | Scratches easily | Med |
Aluminum | Machine casings, lightweight components | Lightweight and corrosion-resistant | Less durable than stainless steel | Med |
This guide provides a comprehensive overview of material selection for vending machines, assisting international B2B buyers in making informed decisions that align with their operational needs and compliance requirements.
In-depth Look: Manufacturing Processes and Quality Assurance for owning a vending machine
When considering the acquisition of vending machines, international B2B buyers must understand the manufacturing processes and quality assurance measures that ensure the reliability and effectiveness of these machines. This section provides an in-depth overview of the typical manufacturing stages, quality control practices, and international standards relevant to vending machine production.
Manufacturing Processes
The manufacturing of vending machines involves several key stages, each critical to the final product’s quality and functionality.
1. Material Preparation
The initial phase involves sourcing high-quality materials suitable for the machine’s structure and components. Common materials include:
– Metal: Steel or aluminum is typically used for the frame and casing due to their durability.
– Plastic: High-density polyethylene (HDPE) or polycarbonate is often used for display panels and internal components.
– Electronic Components: Circuit boards, sensors, and payment systems are sourced from specialized suppliers.
During this stage, suppliers should be vetted for material quality to ensure compliance with relevant standards.
2. Forming
The forming process includes shaping the materials into the required components. Techniques employed in this stage may include:
– Stamping: Used for creating metal panels and frames.
– Injection Molding: Utilized for producing plastic parts.
– CNC Machining: Employed for precision components, ensuring accuracy in dimensions.
Investing in advanced machinery during this stage can significantly enhance the efficiency and precision of the manufacturing process.
3. Assembly
Once the components are formed, they undergo assembly. This stage typically involves:
– Component Integration: Combining mechanical parts with electronic systems, such as motors and payment processors.
– Wiring and Testing: Ensuring all electronic components are correctly connected and functional before final assembly.
– Quality Checks: Conducting initial quality checks at various stages of assembly to identify defects early.
Effective communication between assembly teams and quality assurance personnel is vital to minimize errors.
4. Finishing
The finishing process enhances the aesthetic and functional qualities of the vending machines. This stage includes:
– Painting and Coating: Applying protective and decorative finishes to the machine’s exterior.
– Final Assembly: Installing additional features such as lighting, signage, and user interfaces.
– Final Testing: Conducting comprehensive tests to ensure all functionalities operate as intended.
Quality Assurance
Quality assurance is crucial in the vending machine manufacturing process, as it directly impacts machine reliability and customer satisfaction.
Relevant International Standards
International standards play a significant role in ensuring quality. Key standards include:
– ISO 9001: This standard outlines the criteria for a quality management system, emphasizing consistent product quality and customer satisfaction.
– CE Marking: For machines sold in Europe, CE marking indicates compliance with EU safety, health, and environmental protection standards.
– API Standards: Applicable in certain regions, API standards may govern the quality of mechanical components used in vending machines.
Quality Control Checkpoints
Quality control (QC) checkpoints are strategically placed throughout the manufacturing process to monitor quality and performance. Key checkpoints include:
– Incoming Quality Control (IQC): Assessing raw materials and components upon arrival to ensure they meet specifications.
– In-Process Quality Control (IPQC): Monitoring the production process to detect defects during manufacturing.
– Final Quality Control (FQC): Conducting a thorough inspection of the finished machines to verify functionality and compliance with standards.
Common Testing Methods
Various testing methods are employed to ensure that vending machines function correctly and meet quality standards. These include:
– Functional Testing: Verifying that all operational features (e.g., coin acceptors, product dispensing) work as intended.
– Durability Testing: Assessing the machine’s resistance to wear and tear, ensuring it can withstand heavy usage.
– Electrical Safety Testing: Ensuring that all electrical components comply with safety regulations to prevent hazards.
Verifying Supplier Quality Control
For B2B buyers, especially those from Africa, South America, the Middle East, and Europe, verifying a supplier’s quality control measures is essential. Here are strategies to ensure quality compliance:
– Audits: Conduct regular audits of suppliers to assess their manufacturing processes and quality control measures. This can be done through on-site visits or third-party auditing services.
– Documentation Review: Request detailed quality assurance documentation, including inspection reports and compliance certificates, to verify adherence to international standards.
– Third-Party Inspection: Consider hiring independent inspectors to evaluate the manufacturing process and the final product. This adds an extra layer of assurance regarding quality.
QC and Certification Nuances for International Buyers
International buyers must be aware of specific quality assurance and certification nuances that may impact their procurement decisions:
– Regional Compliance: Different regions may have varying requirements for certifications. For example, CE marking is mandatory for European markets, while UL certification is essential in North America.
– Language Barriers: Ensure that all quality assurance documents are available in a language you understand, or seek translation services to avoid miscommunication.
– Cultural Considerations: Be mindful of cultural differences in business practices and quality expectations, which may influence negotiations and supplier relationships.
Conclusion
Understanding the manufacturing processes and quality assurance measures for vending machines is vital for international B2B buyers. By focusing on material quality, robust manufacturing practices, and stringent quality control protocols, buyers can ensure they invest in reliable and efficient vending machines. Implementing thorough supplier verification processes will further safeguard investments, paving the way for successful vending operations across diverse markets.
Related Video: SMART Quality Control for Manufacturing
Comprehensive Cost and Pricing Analysis for owning a vending machine Sourcing
To successfully navigate the vending machine business landscape, international B2B buyers must conduct a comprehensive cost and pricing analysis. Understanding the cost structure and the various pricing influences can significantly impact profitability and operational efficiency.
Cost Components
-
Materials: The primary materials involved in vending machine sourcing include the machine itself, which can range from $2,000 to $10,000 depending on specifications and features. Additionally, the cost of initial inventory—snacks, beverages, and possibly specialty items—typically falls between $500 and $1,000 per machine.
-
Labor: While vending machines operate autonomously, there is a need for periodic restocking and maintenance. Labor costs can vary based on local wages and the frequency of service required. Budgeting for at least one dedicated staff member can be crucial for larger operations.
-
Manufacturing Overhead: This includes costs related to machine production, such as facility expenses, utilities, and indirect labor. These costs are often reflected in the machine’s purchase price and can be a significant factor for buyers sourcing from manufacturers.
-
Tooling: Custom vending machines may require specialized tooling, which can increase initial costs. Buyers should consider the implications of customization on both the price and the delivery timeline.
-
Quality Control (QC): Ensuring that machines meet certain quality standards is essential. This may involve additional inspection and testing, which can add to the overall cost. B2B buyers should inquire about the QC processes of their suppliers to ensure that they receive reliable products.
-
Logistics: Shipping costs can vary significantly based on the origin of the machines and the destination. Consideration of Incoterms is crucial; they define who bears the cost and risk during transportation. Freight forwarding and customs duties may also add to the total costs.
-
Margin: Suppliers typically include a margin in their pricing to cover their costs and ensure profitability. Understanding the typical margins within the vending machine industry can help buyers negotiate better deals.
Price Influencers
-
Volume/MOQ (Minimum Order Quantity): Larger orders often lead to lower per-unit costs. Buyers should assess their market potential to negotiate favorable terms based on volume.
-
Specifications/Customization: Highly customized machines that cater to specific markets may come at a premium. Buyers must weigh the benefits of customization against the potential for increased costs.
-
Materials Quality/Certifications: Machines made from higher-quality materials or those that meet specific certifications may command higher prices. Buyers in regions with stringent regulations should prioritize certified equipment.
-
Supplier Factors: The reputation and reliability of suppliers can influence pricing. Established suppliers may charge more for their products but often provide better service and support.
-
Incoterms: Understanding the shipping terms can affect total costs significantly. Terms such as FOB (Free on Board) or CIF (Cost, Insurance, and Freight) dictate who is responsible for transportation costs and risks.
Buyer Tips
-
Negotiation: Leverage market research to negotiate better prices. Understanding local competition and demand can provide a stronger bargaining position.
-
Cost-Efficiency: Always calculate the Total Cost of Ownership (TCO), which includes purchase price, maintenance, operational costs, and potential downtime. This holistic view can reveal more cost-effective options.
-
Pricing Nuances for International Buyers: Buyers from Africa, South America, the Middle East, and Europe should be aware of currency fluctuations, import tariffs, and local market conditions that can affect pricing. Establishing relationships with local suppliers can mitigate some of these risks.
-
Disclaimer on Indicative Prices: Prices mentioned are indicative and subject to change based on market conditions, supplier negotiations, and specific requirements. Always obtain quotes tailored to your specific needs and operational contexts.
By thoroughly analyzing these components and influences, international B2B buyers can make informed decisions that enhance their chances of success in the vending machine market.
Spotlight on Potential owning a vending machine Manufacturers and Suppliers
- (No specific manufacturer data was available or requested for detailed profiling in this section for owning a vending machine.)*
Essential Technical Properties and Trade Terminology for owning a vending machine
Key Technical Properties for Vending Machines
Understanding the technical specifications of vending machines is crucial for B2B buyers, especially those venturing into this industry. Here are several essential properties to consider:
-
Material Grade
– Vending machines are typically constructed from high-grade stainless steel or durable plastics. Stainless steel offers superior resistance to corrosion and wear, which is critical for machines placed in high-traffic environments. For B2B buyers, selecting machines made from high-quality materials ensures longevity and reduces maintenance costs. -
Power Requirements
– The power specifications of a vending machine, usually expressed in volts (V) and watts (W), indicate the energy consumption and compatibility with local electrical systems. Understanding these requirements is essential for ensuring proper installation and operation, particularly in regions with varying electrical standards. -
Capacity and Size
– The capacity of a vending machine refers to the number of products it can hold, which directly affects sales volume. This is often measured in terms of slots or bins. Buyers must assess the size of the machine to ensure it fits the intended location while maximizing product offerings to meet consumer demand. -
Payment System Compatibility
– Modern vending machines often come equipped with multiple payment options, including cash, credit/debit cards, and mobile payment systems. The flexibility of payment systems can significantly influence customer satisfaction and sales. B2B buyers should prioritize machines that support cashless transactions, as this trend is increasingly popular among consumers. -
Temperature Control
– For machines dispensing perishable items, temperature control specifications are critical. This includes the range of temperatures maintained within the machine, which should be compliant with food safety regulations. Buyers must ensure that the machine’s cooling systems are efficient and reliable to prevent spoilage and maintain product quality.
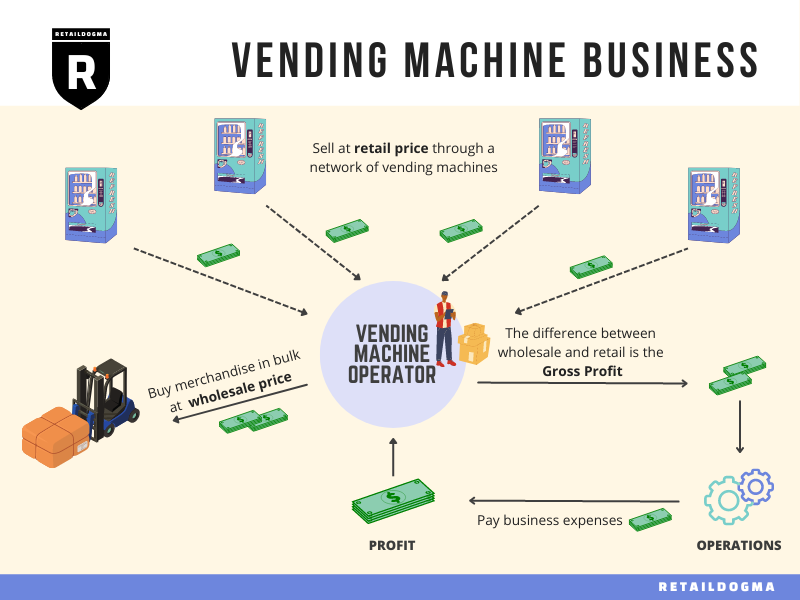
Illustrative Image (Source: Google Search)
- User Interface
– The design and functionality of the user interface, including touchscreens and product selection buttons, play a significant role in customer experience. An intuitive interface can enhance user engagement and reduce transaction times, leading to increased sales. Buyers should evaluate the interface’s ease of use, particularly in diverse markets with varying levels of technological proficiency.
Common Trade Terminology in the Vending Machine Industry
Familiarizing yourself with industry jargon can enhance communication and negotiation with suppliers and partners. Here are several critical terms:
-
OEM (Original Equipment Manufacturer)
– Refers to companies that produce parts or equipment that may be marketed by another manufacturer. Understanding OEM relationships is vital when sourcing machines or components, as it can affect warranty and support services. -
MOQ (Minimum Order Quantity)
– This is the smallest quantity of a product that a supplier is willing to sell. Knowing the MOQ is essential for budgeting and inventory planning, especially when entering new markets or launching new product lines. -
RFQ (Request for Quotation)
– An RFQ is a standard business process in which a company solicits bids from suppliers for specific products or services. For B2B buyers, issuing an RFQ helps in comparing prices and terms, ensuring they get the best value for their investment.
-
Incoterms (International Commercial Terms)
– These are internationally recognized rules that define the responsibilities of sellers and buyers in international transactions. Understanding Incoterms is crucial for B2B buyers to clarify shipping responsibilities, risk transfer, and cost distribution. -
Lead Time
– This term refers to the amount of time between the initiation of a process and its completion. In the context of vending machines, lead time can impact product availability and inventory management. Buyers should consider lead times when planning purchases and stocking strategies. -
Service Level Agreement (SLA)
– An SLA is a contract that outlines the expected level of service between a service provider and a client. For vending machine operators, having clear SLAs with suppliers ensures accountability for machine maintenance and restocking, which can enhance operational efficiency.
By understanding these technical properties and trade terms, B2B buyers can make informed decisions that enhance their vending machine business operations and overall profitability.
Navigating Market Dynamics, Sourcing Trends, and Sustainability in the owning a vending machine Sector
Market Overview & Key Trends
The global vending machine market is experiencing robust growth, driven by factors such as urbanization, increasing consumer demand for convenience, and technological advancements. In regions like Africa, South America, the Middle East, and Europe, the market is projected to expand significantly, with a compound annual growth rate (CAGR) of over 4% expected through 2025. International B2B buyers should focus on the rising demand for healthy and diverse product offerings, as consumers increasingly seek nutritious options alongside traditional snacks and beverages.
Emerging technologies are reshaping the vending landscape, with cashless payment systems and IoT-enabled machines becoming standard. This technological shift not only enhances user experience but also allows operators to monitor inventory and sales data in real-time, enabling more efficient restocking and maintenance. Additionally, sustainability is becoming a key market driver, with buyers looking for machines that minimize environmental impact and support eco-friendly practices.
Moreover, the location of vending machines plays a crucial role in their success. High-traffic areas such as offices, schools, and transportation hubs are ideal for maximizing visibility and sales. For international buyers, understanding local consumer preferences and behaviors is essential for tailoring product offerings to specific markets. Engaging in thorough market research and competitive analysis will provide valuable insights into potential opportunities and challenges in various regions.
Sustainability & Ethical Sourcing in B2B
As sustainability becomes a central theme in global commerce, the vending machine industry is not left behind. B2B buyers are increasingly prioritizing environmentally friendly practices, which include sourcing products from suppliers who adhere to ethical and sustainable production methods. This shift is not only beneficial for the environment but also aligns with consumer expectations, as more individuals prefer to purchase from brands that demonstrate social responsibility.
Incorporating sustainable materials into vending machine operations is essential. Buyers should consider machines made from recycled materials or those that have energy-efficient features to reduce carbon footprints. Additionally, obtaining certifications such as Green Seal or Energy Star can enhance credibility and appeal to eco-conscious consumers.
Investing in ethical supply chains also means ensuring that all products sold through vending machines are sourced responsibly. This includes choosing suppliers who comply with fair labor practices and environmental regulations. By focusing on sustainability and ethical sourcing, international B2B buyers can enhance their brand image and attract a growing segment of environmentally aware consumers.
Brief Evolution/History
The vending machine industry has evolved significantly since its inception in the late 19th century when the first machines dispensed simple products such as postcards and chewing gum. Over the decades, advancements in technology have transformed these machines into sophisticated units capable of offering a wide variety of products, including beverages, snacks, and even fresh food.
In recent years, the integration of digital payment systems and online inventory management has further modernized the sector, allowing operators to streamline operations and enhance customer experience. This evolution reflects broader trends in consumer behavior, emphasizing convenience and accessibility, which continue to shape the future of the vending machine business.
As the market progresses, international B2B buyers must stay informed about these historical shifts and emerging trends to effectively navigate the competitive landscape and capitalize on new opportunities.
Related Video: International Trade 101 | Economics Explained
Frequently Asked Questions (FAQs) for B2B Buyers of owning a vending machine
-
What should I consider when vetting suppliers for vending machines?
When vetting suppliers, prioritize those with a proven track record in the vending machine industry. Look for certifications such as ISO or CE, which indicate quality and compliance with international standards. Evaluate their customer service responsiveness, warranty offerings, and after-sales support. Request references from other B2B clients and analyze their reviews online. Additionally, check if the supplier has a local presence or partnerships in your region to facilitate easier communication and logistics. -
Can I customize my vending machines to fit local preferences?
Yes, many suppliers offer customization options for vending machines. This can include branding, machine color, product selection, and payment options. When negotiating with suppliers, inquire about their ability to tailor machines to meet local tastes, such as healthier snack options or region-specific beverages. Customization can enhance customer engagement and satisfaction, making your machines more appealing to your target market. -
What are the typical minimum order quantities (MOQs) and lead times for vending machines?
MOQs can vary significantly between suppliers and depend on the type of vending machine. Generally, you might expect MOQs to range from 1 to 10 units for new machines, while used machines may have lower MOQs. Lead times for orders can range from 4 to 12 weeks, depending on the supplier’s inventory and customization requirements. Always clarify these details upfront to plan your inventory and budget effectively. -
What payment options are usually available when purchasing vending machines?
Suppliers typically offer various payment options, including upfront payments, installment plans, or leasing arrangements. For international transactions, consider using letters of credit or escrow services to protect both parties. Ensure that you understand the currency exchange implications and any additional fees associated with cross-border payments. Discussing payment terms early in negotiations can help avoid misunderstandings later. -
How can I ensure quality assurance (QA) and certification compliance for my vending machines?
To ensure quality, request detailed information on the supplier’s QA processes and certifications. Check if they conduct routine testing and inspections during production. Certifications such as ISO 9001 or local safety standards (e.g., CE in Europe) can provide assurance of quality. Additionally, consider conducting on-site inspections or third-party quality audits, especially for larger orders, to verify compliance with your specifications and standards. -
What logistics considerations should I keep in mind when importing vending machines?
Logistics play a crucial role in the vending machine supply chain. Assess shipping methods (air vs. sea) based on cost and delivery time. Ensure that your supplier has experience with international shipping and customs clearance. It’s also essential to account for import duties, taxes, and insurance during transport. Collaborating with a reliable logistics partner can help streamline the process and mitigate potential delays or issues. -
How should I handle disputes with vending machine suppliers?
Effective dispute resolution begins with clear communication and well-defined contracts. Ensure that your agreement outlines terms regarding delivery, quality, and payment. In the event of a dispute, attempt to resolve it amicably through direct communication. If necessary, consider mediation or arbitration as a means to settle disagreements. Having a legal advisor familiar with international trade can be invaluable in navigating complex situations and protecting your interests. -
What ongoing support should I expect from my vending machine supplier?
When purchasing vending machines, inquire about the supplier’s ongoing support, including maintenance, repairs, and inventory management assistance. Many suppliers offer service contracts or support plans that provide technical support and spare parts. Understanding these terms can help you manage operational downtime and ensure your machines remain functional. Regular communication with your supplier can also facilitate better service and prompt responses to any issues that arise.
Strategic Sourcing Conclusion and Outlook for owning a vending machine
In conclusion, owning a vending machine business presents a significant opportunity for international B2B buyers, especially in emerging markets like Africa, South America, the Middle East, and Europe. The industry’s steady growth, driven by an increasing demand for convenience and accessible products, underscores the importance of strategic sourcing. By conducting thorough market research, identifying high-traffic locations, and selecting the right products tailored to local preferences, operators can maximize their return on investment.
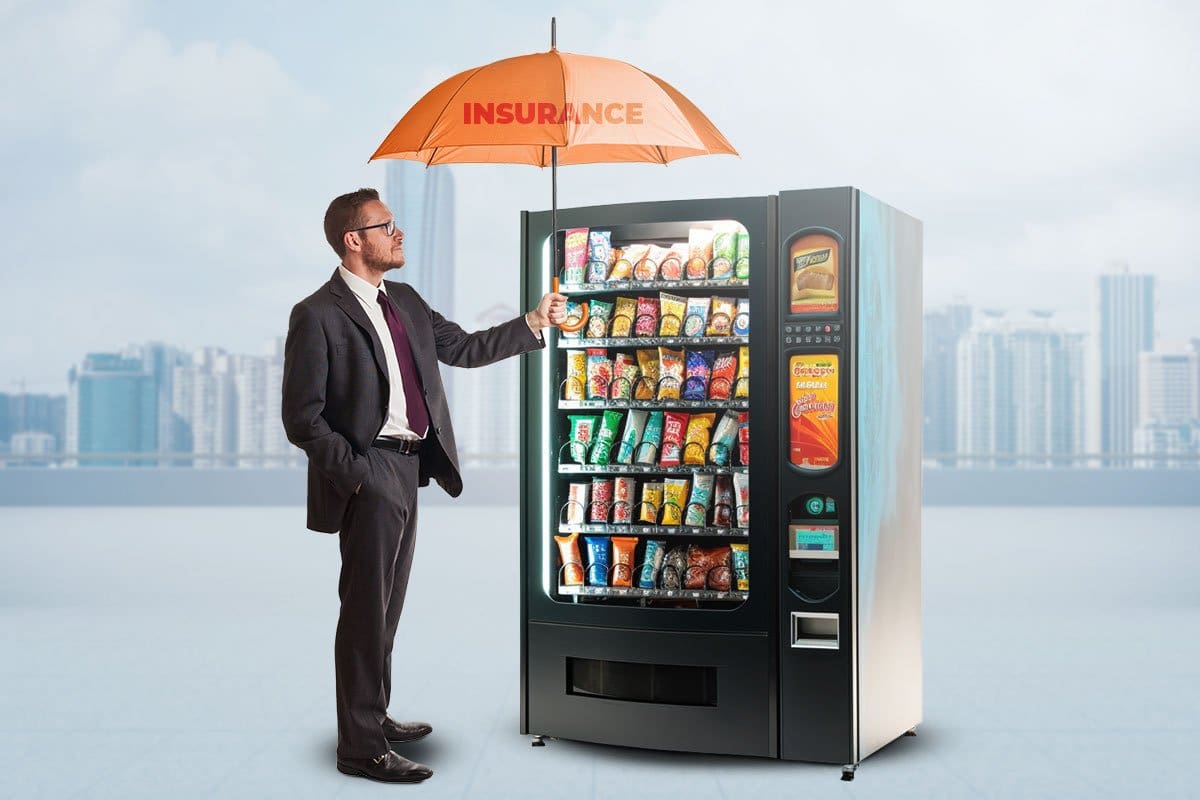
Illustrative Image (Source: Google Search)
Key takeaways for B2B buyers include:
- Understanding Local Demand: Tailor your offerings to meet regional tastes and needs, ensuring a competitive edge.
- Strategic Location Selection: Prioritize placements in busy environments such as schools, offices, and hospitals to drive sales.
- Cost Management: Carefully evaluate the initial investment and ongoing operational costs to maintain profitability.
As the vending industry continues to evolve with technological advancements, now is the time to invest. Embrace the opportunity to innovate your offerings and enhance customer experiences. Start your journey into the vending machine market today, and position your business for success in the global landscape.