Master How to Build a Vending Machine for International
Guide to Build A Vending Machine
- Introduction: Navigating the Global Market for build a vending machine
- Understanding build a vending machine Types and Variations
- Key Industrial Applications of build a vending machine
- Strategic Material Selection Guide for build a vending machine
- In-depth Look: Manufacturing Processes and Quality Assurance for build a vending machine
- Comprehensive Cost and Pricing Analysis for build a vending machine Sourcing
- Spotlight on Potential build a vending machine Manufacturers and Suppliers
- Essential Technical Properties and Trade Terminology for build a vending machine
- Navigating Market Dynamics, Sourcing Trends, and Sustainability in the build a vending machine Sector
- Frequently Asked Questions (FAQs) for B2B Buyers of build a vending machine
- Strategic Sourcing Conclusion and Outlook for build a vending machine
Introduction: Navigating the Global Market for build a vending machine
In an era where convenience and efficiency drive consumer behavior, the vending machine industry stands at the forefront of innovative retail solutions. For international B2B buyers, particularly those operating in Africa, South America, the Middle East, and Europe, understanding how to build a vending machine is not just a technical endeavor but a strategic opportunity to tap into a burgeoning market. The global demand for vending services continues to rise, fueled by changing lifestyles and the increasing preference for contactless transactions.
This comprehensive guide serves as a vital resource for B2B buyers looking to navigate the intricate landscape of vending machine construction and operation. It delves into critical aspects such as types of vending machines, materials required, manufacturing and quality control processes, supplier selection, and cost analysis. Additionally, it addresses market trends and frequently asked questions to equip buyers with the knowledge needed to make informed sourcing decisions.
By leveraging the insights contained within this guide, buyers can confidently select the right components and partners to enhance their vending machine offerings. Whether you’re based in Nigeria, Brazil, or Germany, this resource empowers you to transform challenges into strategic advantages, ensuring your vending operations are not only compliant but also positioned for sustained profitability. Engage with this guide to unlock the potential of the vending machine market and elevate your business to new heights.
Understanding build a vending machine Types and Variations
Type Name | Key Distinguishing Features | Primary B2B Applications | Brief Pros & Cons for Buyers |
---|---|---|---|
Snack & Drink Machines | Dispense a variety of snacks and beverages | Offices, schools, gyms | Pros: High demand; easy to maintain. Cons: Limited product diversity. |
Healthy Vending Machines | Focus on organic, low-calorie, and nutritious options | Hospitals, gyms, corporate offices | Pros: Growing market; appeals to health-conscious consumers. Cons: Higher initial costs. |
Coffee Vending Machines | Provide freshly brewed coffee and related beverages | Offices, hospitals, hotels | Pros: High profit margins; consistent demand. Cons: Requires regular maintenance and supplies. |
Specialty Vending Machines | Offer unique products like tech gadgets or personal care items | Airports, malls, universities | Pros: Niche market; potential for high margins. Cons: May require specialized sourcing. |
Combination Machines | Combine snacks, drinks, and other products in one unit | Varied locations | Pros: Versatile; maximizes space. Cons: Complexity in inventory management. |
Snack & Drink Machines
Snack and drink vending machines are the most common type, providing a range of popular items like chips, chocolates, and soft drinks. These machines are ideal for high-traffic areas such as offices, schools, and gyms where quick access to snacks is essential. B2B buyers should consider the location’s demographic and foot traffic when selecting products. While these machines are easy to maintain and generally have a high turnover, they may lack the variety needed to cater to niche markets.
Healthy Vending Machines
These machines focus on offering healthier food and beverage options, including organic snacks and low-calorie drinks. They are particularly suitable for environments such as hospitals, gyms, and corporate offices where health and wellness are priorities. B2B buyers should be aware of the growing consumer demand for healthy choices and the potential for higher profit margins. However, the initial investment can be higher due to the sourcing of quality products.
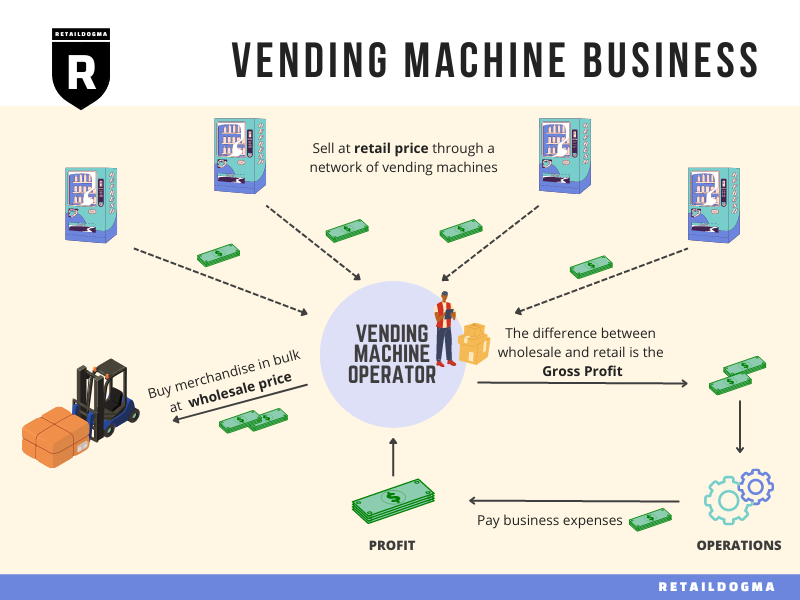
Illustrative Image (Source: Google Search)
Coffee Vending Machines
Coffee vending machines serve freshly brewed coffee, tea, and other hot beverages, making them ideal for workplaces and healthcare facilities. The demand for quality coffee has surged, and these machines can offer high profit margins. B2B buyers need to consider the ongoing maintenance and supply requirements, as well as the need for quality coffee beans, which can impact operational efficiency.
Specialty Vending Machines
Specialty vending machines cater to niche markets by offering unique products such as tech gadgets, personal care items, or even PPE. These machines are often placed in locations like airports, shopping malls, or universities, where specific consumer needs exist. Buyers should evaluate the potential for high margins and the uniqueness of the product offerings. However, sourcing these specialized items can be more complex and may require strong supplier relationships.
Combination Machines
Combination vending machines provide a versatile solution by offering a mix of snacks, drinks, and sometimes even healthy options in one unit. This flexibility allows businesses to maximize their space and cater to diverse consumer preferences. B2B buyers should assess the potential for increased sales from various product categories. However, managing inventory can be more complex, requiring careful planning and supplier coordination to ensure product freshness and availability.
Related Video: How To Start A Vending Machine Business Step-By-Step (With $0)
Key Industrial Applications of build a vending machine
Industry/Sector | Specific Application of build a vending machine | Value/Benefit for the Business | Key Sourcing Considerations for this Application |
---|---|---|---|
Healthcare | Automated medication dispensing machines | Improves patient compliance, reduces pharmacy workload | Compliance with health regulations, reliability of dispensing mechanisms |
Education | Snack and beverage vending in schools and universities | Enhances student satisfaction, generates additional revenue | Product variety, health-conscious options, payment flexibility |
Corporate Offices | Coffee and snack vending machines for employee break rooms | Boosts employee morale, increases productivity | Quality of products, maintenance support, supplier reliability |
Transportation Hubs | Vending machines for travel essentials at airports and stations | Convenience for travelers, generates high foot traffic sales | High-demand product selection, payment system adaptability |
Retail and E-commerce | Specialty vending for tech gadgets and accessories | Captures impulse buying, enhances customer experience | Sourcing trendy products, stock turnover rate, machine visibility |
Healthcare
In the healthcare sector, vending machines are increasingly utilized for automated medication dispensing. These machines not only ensure that patients receive their medications on time but also alleviate the workload for pharmacy staff. For international buyers, particularly from regions like Africa and the Middle East, compliance with local health regulations is essential. Therefore, sourcing machines that meet stringent safety and reliability standards is crucial to avoid potential legal issues while ensuring that the devices function effectively in high-demand environments.
Education
Vending machines in educational institutions provide quick access to snacks and beverages for students and staff. This application enhances student satisfaction and can serve as an additional revenue stream for schools and universities. When sourcing machines for this sector, it is vital to consider health-conscious product options, as many educational bodies prioritize student wellness. Buyers should also evaluate the payment systems, ensuring they accommodate cashless transactions, which are becoming increasingly popular among younger demographics in Europe and South America.
Corporate Offices
In corporate environments, vending machines offering coffee, snacks, and healthy food options can significantly boost employee morale and productivity. By providing convenient access to refreshments, businesses can create a more inviting workplace. When sourcing these machines, companies should focus on the quality of products offered, as well as the reliability of suppliers for maintenance and support. Understanding the specific preferences of the workforce can also guide product selection, which is particularly important in diverse regions like Africa and Europe.
Transportation Hubs
Vending machines located in airports and train stations cater to travelers seeking convenience for quick snacks, drinks, or travel essentials. This application capitalizes on high foot traffic and can generate significant revenue. Buyers in this sector must consider the selection of high-demand products, such as ready-to-eat meals and travel accessories. Additionally, ensuring that the vending machines support various payment methods, including contactless options, is essential for accommodating the diverse customer base found in international transportation hubs.
Retail and E-commerce
Specialty vending machines that dispense tech gadgets and accessories are becoming popular in retail environments, as they capture impulse buying opportunities. This application enhances the customer experience by providing instant access to trending products. International B2B buyers should focus on sourcing trendy and high-turnover items to ensure that their machines remain stocked with desirable products. Additionally, machine visibility and strategic placement in high-traffic areas can significantly impact sales performance, making sourcing decisions critical for success in this competitive sector.
Related Video: Build a Vending Machine with Gumball from Cardboard
Strategic Material Selection Guide for build a vending machine
When building a vending machine, the selection of materials is critical to ensure durability, functionality, and compliance with local regulations. Below is an analysis of four common materials used in vending machine construction, focusing on their properties, advantages, disadvantages, and considerations for international B2B buyers.
1. Stainless Steel
Key Properties:
Stainless steel is known for its excellent corrosion resistance, high strength, and ability to withstand high temperatures. It is also non-reactive, making it suitable for food and beverage applications.
Pros & Cons:
The durability of stainless steel makes it ideal for high-traffic environments. However, it can be more expensive than other materials, and its manufacturing process is complex due to the need for specialized welding techniques.
Impact on Application:
Stainless steel is particularly effective in environments where hygiene is paramount, such as in food vending machines. Its resistance to corrosion ensures that the machine remains functional and visually appealing over time.
Considerations for International Buyers:
Buyers should ensure that the stainless steel used meets local standards such as ASTM or DIN. In regions like Africa and South America, sourcing from local suppliers can reduce costs and lead times.
2. Mild Steel
Key Properties:
Mild steel is characterized by its good tensile strength and ductility, making it easy to work with during manufacturing. However, it has lower corrosion resistance compared to stainless steel.
Pros & Cons:
Mild steel is cost-effective and readily available, making it a popular choice for budget-conscious projects. However, it requires protective coatings to prevent rust, which can add to maintenance costs.
Impact on Application:
While suitable for non-food vending machines, mild steel may not be ideal for environments exposed to moisture or corrosive substances. Proper treatment and maintenance are essential to prolong its lifespan.
Considerations for International Buyers:
Buyers should consider local climate conditions that may affect the longevity of mild steel. Compliance with local regulations regarding coatings and safety standards is also crucial.
3. Aluminum
Key Properties:
Aluminum is lightweight, corrosion-resistant, and has good thermal conductivity. It is also non-toxic, making it suitable for food applications.
Pros & Cons:
The lightweight nature of aluminum allows for easier transportation and installation of vending machines. However, it is generally less durable than steel and can be more expensive depending on the alloy used.
Impact on Application:
Aluminum is often used in vending machines that require mobility or frequent relocation. Its resistance to corrosion makes it suitable for outdoor installations.
Considerations for International Buyers:
When sourcing aluminum, buyers should check for compliance with international standards such as JIS. Additionally, understanding the local market for aluminum alloys can help in making cost-effective decisions.
4. Polycarbonate
Key Properties:
Polycarbonate is a strong, impact-resistant plastic that offers excellent clarity and UV resistance. It is lightweight and can be molded into complex shapes.
Pros & Cons:
Polycarbonate is highly durable and can withstand harsh environmental conditions. However, it may not be suitable for high-temperature applications and can be more expensive than other plastics.
Impact on Application:
This material is often used for transparent panels in vending machines, allowing customers to view products. Its resistance to UV light ensures that the machine’s aesthetics remain intact over time.
Considerations for International Buyers:
Buyers should verify that the polycarbonate used meets safety and quality standards specific to their region. Understanding local preferences for materials can also guide sourcing decisions.
Summary Table
Material | Typical Use Case for build a vending machine | Key Advantage | Key Disadvantage/Limitation | Relative Cost (Low/Med/High) |
---|---|---|---|---|
Stainless Steel | Food and beverage vending machines | Excellent corrosion resistance | Higher cost, complex manufacturing | High |
Mild Steel | Non-food vending machines | Cost-effective, easy to work with | Requires protective coatings, less durable | Low |
Aluminum | Mobile or outdoor vending machines | Lightweight, corrosion-resistant | Less durable than steel, can be costly | Med |
Polycarbonate | Transparent panels in vending machines | Strong, impact-resistant, UV resistant | Not suitable for high temperatures | Med |
Choosing the right materials for building a vending machine is essential for ensuring longevity, compliance, and customer satisfaction. By understanding the properties and implications of each material, international B2B buyers can make informed decisions that align with their business goals and local market conditions.
In-depth Look: Manufacturing Processes and Quality Assurance for build a vending machine
The manufacturing process of vending machines is a complex and multifaceted journey that requires careful attention to detail and adherence to quality standards. For international B2B buyers, understanding this process is crucial for ensuring that the machines purchased meet operational and regulatory requirements.
Manufacturing Processes
Material Preparation
The first step in the manufacturing process involves selecting and preparing the materials. Common materials used in vending machines include:
- Metal: Typically steel or aluminum, used for the frame and housing due to their durability.
- Plastics: Utilized for components like buttons, panels, and product dispensers for their lightweight properties and ease of molding.
- Electronics: Circuit boards and sensors that control machine functions and user interfaces.
The preparation stage may involve cutting, machining, and treating materials to enhance durability and resistance to corrosion. For instance, metal components may undergo galvanization to prevent rust.
Forming
Once materials are prepared, the forming stage begins. This involves shaping materials into their final forms using various techniques:
- Stamping: Metal sheets are stamped into specific shapes required for the machine’s structure.
- Molding: Plastic components are created using injection molding to form complex shapes that fit seamlessly into the machine.
- Welding: Metal parts are welded together to create a sturdy frame that can withstand the rigors of usage.
Precision in this stage is critical, as inaccuracies can lead to structural weaknesses and operational failures.
Assembly
The assembly stage integrates all components into a fully functional vending machine. Key steps include:
- Component Integration: Installing mechanical parts like motors, levers, and dispensers.
- Electrical Assembly: Connecting wiring, circuit boards, and power supplies to ensure the machine operates correctly.
- Software Installation: Uploading the machine’s operating software, which controls user interfaces and inventory management.
Efficient assembly lines often employ automation to enhance speed and accuracy while reducing labor costs.
Finishing
The final stage is finishing, where the machine is prepared for delivery. This includes:
- Painting and Coating: Applying protective finishes to prevent wear and enhance aesthetic appeal.
- Quality Checks: Conducting final inspections to ensure all components function as intended.
- Packaging: Safely packaging the machines for shipping, ensuring they arrive in optimal condition.
Quality Assurance
Quality assurance (QA) is paramount in the manufacturing of vending machines, ensuring that each unit meets international standards and customer expectations. Key elements include:
International Standards
B2B buyers should ensure that their suppliers comply with relevant international standards, such as:
- ISO 9001: A standard that outlines criteria for a quality management system, ensuring consistent quality in manufacturing processes.
- CE Marking: Indicates compliance with health, safety, and environmental protection standards within the European Economic Area.
These certifications provide assurance that the machines have undergone rigorous testing and meet essential regulatory requirements.
Industry-Specific Standards
In addition to general quality standards, vending machines may need to comply with industry-specific regulations, including:
- API (American Petroleum Institute): Relevant for machines that dispense fuel or related products.
- NSF International: Ensures that machines dispensing food and beverages meet safety and sanitation requirements.
Quality Control Checkpoints
Quality control (QC) involves systematic checks at various stages of the manufacturing process:
- Incoming Quality Control (IQC): Inspecting raw materials upon arrival to ensure they meet specified standards.
- In-Process Quality Control (IPQC): Monitoring production processes to identify and rectify issues as they arise.
- Final Quality Control (FQC): Conducting comprehensive tests on completed machines to verify their functionality and safety.
These checkpoints help maintain high standards throughout the manufacturing process.
Common Testing Methods
To ensure that vending machines meet quality standards, several testing methods are employed:
- Functional Testing: Verifying that all mechanical and electronic components operate correctly.
- Durability Testing: Subjecting machines to stress tests to evaluate their performance under extreme conditions.
- Safety Testing: Ensuring compliance with safety standards to prevent hazards during operation.
Verifying Supplier Quality Control
For international B2B buyers, verifying the quality control processes of suppliers is essential. Here are several strategies:
- Supplier Audits: Conducting on-site audits to evaluate the manufacturing processes and quality assurance measures in place. This helps establish trust and transparency.
- Quality Reports: Requesting detailed QC reports from suppliers that outline the results of inspections and tests performed during manufacturing.
- Third-Party Inspections: Engaging independent inspection services to assess product quality before shipment. This adds an extra layer of assurance regarding compliance and safety.
Quality Control Nuances for International Buyers
B2B buyers from regions such as Africa, South America, the Middle East, and Europe must navigate unique challenges when sourcing vending machines:
- Regulatory Variances: Understanding local regulations and ensuring that suppliers comply with them can be complex. Buyers should familiarize themselves with the specific requirements in their regions.
- Supply Chain Reliability: Establishing relationships with suppliers who have robust logistics capabilities is vital, especially when importing machines from overseas.
- Cultural Considerations: Effective communication and relationship-building are crucial in international transactions. Understanding cultural nuances can enhance negotiations and foster long-term partnerships.
By comprehensively understanding the manufacturing processes and quality assurance measures, B2B buyers can make informed decisions, ensuring that the vending machines they procure are reliable, compliant, and capable of delivering value in their markets.
Related Video: SMART Quality Control for Manufacturing
Comprehensive Cost and Pricing Analysis for build a vending machine Sourcing
Analyzing the cost structure and pricing for sourcing a vending machine is crucial for international B2B buyers. Understanding the various components involved can help buyers make informed decisions that maximize profitability and minimize expenses.
Cost Components
- Materials: The primary materials for vending machines include metal casings, electronic components, refrigeration units (for food and beverage machines), and payment systems (like cashless payment options). The choice of materials can significantly affect the overall cost. For instance, stainless steel is more expensive than powder-coated steel but offers greater durability.
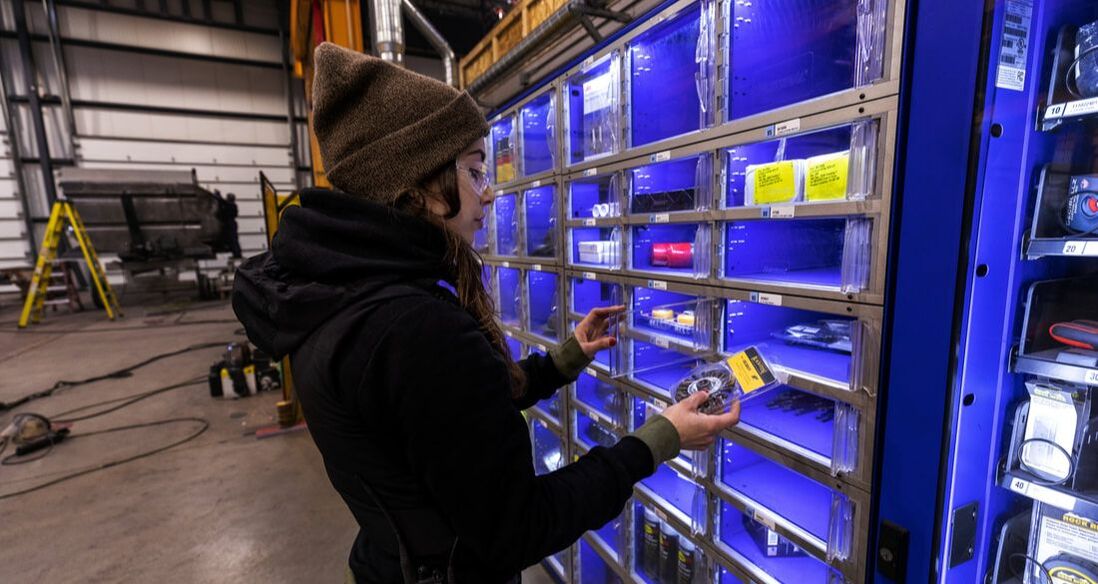
Illustrative Image (Source: Google Search)
-
Labor: Labor costs encompass both direct and indirect labor involved in the manufacturing process. This includes wages for assembly workers, quality control personnel, and engineering staff. Depending on the manufacturing location, labor costs can vary significantly, influencing the final price of the vending machine.
-
Manufacturing Overhead: This includes expenses related to factory operations that are not directly tied to production, such as utilities, rent, and administrative salaries. Understanding the overhead structure can provide insights into potential cost-saving areas.
-
Tooling: Initial costs for tools and dies necessary for production can be substantial. Buyers should inquire about these costs, especially if they are considering custom designs or features for their machines.
-
Quality Control (QC): Ensuring that products meet specific quality standards is vital. QC processes incur costs, but they are essential for maintaining reliability and customer satisfaction.
-
Logistics: Shipping costs can vary based on the size and weight of the vending machines, as well as the distance from the manufacturing site to the buyer’s location. International shipping may involve additional tariffs and duties, which should be factored into the total cost.
- Margin: Suppliers typically add a profit margin to their costs, which can range from 10% to 30%, depending on market conditions and competition. Understanding this margin can help buyers negotiate better pricing.
Price Influencers
Several factors can influence the final price of vending machines:
-
Volume/MOQ (Minimum Order Quantity): Ordering in larger quantities often results in lower per-unit costs. Buyers should assess their demand to negotiate favorable pricing.
-
Specifications/Customization: Customized machines or specific features (like specialized payment systems or unique product displays) may incur additional costs. Buyers should weigh the benefits of customization against potential price increases.
-
Materials: The choice of materials significantly impacts costs. Higher quality or specialized materials will lead to higher prices but can improve the machine’s longevity and reliability.
-
Quality/Certifications: Machines that meet specific international certifications (like ISO or CE) may command higher prices due to the assurance of quality and compliance with regulations.
-
Supplier Factors: The reputation and reliability of the supplier can affect pricing. Established suppliers with proven track records may charge more but offer better service and product quality.
-
Incoterms: Understanding the terms of trade (Incoterms) is crucial for international buyers. These terms define who is responsible for shipping costs, insurance, and tariffs, which can significantly affect overall expenses.
Buyer Tips
-
Negotiation: Engage suppliers in discussions to secure better pricing. Highlighting potential long-term partnerships can incentivize suppliers to offer discounts.
-
Cost-Efficiency: Consider total cost of ownership (TCO) rather than just initial purchase price. This includes operational costs such as maintenance and energy consumption.
-
Pricing Nuances: Be aware of regional market trends and pricing strategies. For buyers in Africa or South America, understanding local demand for specific products can influence purchasing decisions.
-
Research Suppliers: Perform due diligence on potential suppliers. Look for those who have experience working with international buyers and can navigate the complexities of shipping and customs.
-
Consider Local Regulations: Ensure that the vending machines comply with local laws and regulations to avoid unexpected costs associated with non-compliance.
Disclaimer
Prices and cost structures mentioned are indicative and may vary based on market conditions, supplier negotiations, and specific buyer requirements. Always conduct thorough research and consult with multiple suppliers to ensure the best deal.
Spotlight on Potential build a vending machine Manufacturers and Suppliers
This section offers a look at a few manufacturers active in the ‘build a vending machine’ market. This is a representative sample for illustrative purposes; B2B buyers must conduct their own extensive due diligence before any engagement. Information is synthesized from public sources and general industry knowledge.
Essential Technical Properties and Trade Terminology for build a vending machine
Key Technical Properties for Building a Vending Machine
When constructing a vending machine, several technical specifications are critical to ensure functionality, durability, and compliance with industry standards. Understanding these properties is vital for B2B buyers who wish to invest wisely in vending machine technology.
-
Material Grade: The choice of materials, such as stainless steel or high-grade plastics, affects the machine’s durability and resistance to wear and tear. Stainless steel is preferred for its corrosion resistance and strength, making it ideal for machines located in high-traffic areas. This property is essential for minimizing maintenance costs and extending the machine’s lifespan.
-
Tolerance Levels: Tolerance refers to the allowable variation in dimensions during manufacturing. For vending machines, precise tolerances ensure that components fit together seamlessly, which is crucial for mechanical parts like motors and dispensing systems. Tight tolerances can lead to better performance and reliability, reducing the risk of jams and malfunctions.
-
Power Requirements: This specification indicates the voltage and current needed for the machine’s operation. Different regions may have varying electrical standards, making it essential for international buyers to ensure compatibility with local power supplies. Understanding power requirements can help avoid costly modifications and ensure compliance with local regulations.
-
Dimensions and Weight: The physical size and weight of a vending machine impact installation and location choices. Machines must fit in designated spaces and be manageable for transportation. Additionally, heavier machines may require reinforced flooring or structural support in high-traffic locations. Buyers should evaluate the machine’s dimensions against available locations to optimize placement.
-
User Interface Features: This includes touchscreen displays, card payment systems, and accessibility features. The user interface significantly affects customer experience and operational efficiency. A well-designed interface can increase sales by making transactions smoother and more intuitive for users.
-
Cooling and Heating Systems: If the vending machine offers perishable items or hot beverages, effective cooling or heating systems are necessary. These systems must maintain the appropriate temperature for product safety and quality. Buyers should assess the efficiency of these systems to ensure they meet the demand of their target market.
Common Trade Terminology in the Vending Machine Industry
Familiarity with industry jargon is crucial for effective communication and negotiation in the vending machine business. Here are several key terms that B2B buyers should know:
-
OEM (Original Equipment Manufacturer): This term refers to companies that produce parts or equipment that may be marketed by another manufacturer. When sourcing machines or components, understanding OEM relationships can help buyers identify quality suppliers and negotiate better terms.
-
MOQ (Minimum Order Quantity): This is the smallest quantity of a product that a supplier is willing to sell. Knowing the MOQ is essential for budgeting and inventory planning, as it impacts initial investment and stock levels.
-
RFQ (Request for Quotation): An RFQ is a document that buyers send to suppliers to request pricing and terms for specific products. This process is vital for comparing suppliers and ensuring competitive pricing, which can significantly affect profit margins.
-
Incoterms: Short for International Commercial Terms, Incoterms are a set of standardized trade terms that define the responsibilities of buyers and sellers in international transactions. Understanding these terms helps clarify shipping responsibilities, costs, and risk management, which is especially important for buyers operating across different regions.
-
Lead Time: This term indicates the time required from placing an order to receiving the goods. Understanding lead times is crucial for inventory management and ensuring that vending machines are adequately stocked to meet customer demand.
-
Warranty and Service Agreements: These are contractual terms that outline the responsibilities of the manufacturer regarding repairs and replacements. A solid warranty can protect buyers from unexpected costs and ensure long-term support for their vending machines.
By grasping these essential properties and terms, international B2B buyers can make informed decisions that enhance their vending machine operations and foster successful supplier relationships.
Navigating Market Dynamics, Sourcing Trends, and Sustainability in the build a vending machine Sector
Market Overview & Key Trends
The global vending machine market is experiencing a significant transformation, driven by technological advancements and changing consumer preferences. Key trends include the integration of contactless payment systems, which have become essential, particularly in regions like Europe and South America where cash transactions are declining. Additionally, the rise of smart vending machines equipped with IoT capabilities allows operators to monitor inventory in real-time, optimizing product selection and minimizing downtime.
For international B2B buyers, understanding the regional market dynamics is crucial. In Africa, for instance, the growth of urban centers is leading to increased demand for convenient food and beverage options, while in the Middle East, the focus is on high-quality, premium products that cater to evolving consumer tastes. Buyers must also consider regional regulations and compliance standards that vary significantly across countries, impacting sourcing strategies and operational viability.
Emerging trends such as the demand for healthy and organic products are reshaping product offerings. Vending machines are evolving from traditional snacks and drinks to include options like fresh meals and health-oriented items, which can attract a broader customer base. This shift emphasizes the need for buyers to cultivate strong relationships with suppliers who can provide diverse, quality products that align with these trends.
Sustainability & Ethical Sourcing in B2B
As the global focus on sustainability intensifies, ethical sourcing is becoming a cornerstone of successful vending machine operations. B2B buyers must be aware of the environmental impact associated with product selection, packaging, and machine materials. Sustainable practices not only enhance brand reputation but also meet the growing consumer demand for eco-friendly products.
Investing in green certifications and sourcing materials that are recyclable or biodegradable can distinguish a vending business in competitive markets. Buyers should prioritize suppliers who demonstrate a commitment to sustainability through their practices and product offerings. This includes sourcing ingredients from ethical farms or using machines constructed from sustainable materials.
Additionally, implementing efficient logistics and supply chain practices can reduce carbon footprints and enhance operational efficiency. For example, consolidating shipments from suppliers minimizes transportation emissions. As consumers increasingly prefer brands that prioritize sustainability, integrating these practices into the vending machine sector not only fulfills ethical responsibilities but also opens new avenues for market differentiation and customer loyalty.
Brief Evolution/History
The vending machine industry has evolved significantly since its inception in the late 19th century. Initially, these machines offered simple items like postcards and chewing gum. The real transformation began in the 20th century with the introduction of snack and beverage machines, which capitalized on the growing demand for convenience.
In recent years, the industry has seen a digital revolution, with advancements such as cashless payments and smart technology reshaping consumer interactions. This evolution has made vending machines not just points of sale but integral components of a broader retail strategy. For B2B buyers, understanding this historical context is essential as it informs current trends and consumer expectations, guiding strategic sourcing and operational decisions.
Related Video: Global Trade & Logistics – What is Global Trade?
Frequently Asked Questions (FAQs) for B2B Buyers of build a vending machine
-
How can I effectively vet suppliers for building vending machines?
To ensure you partner with reliable suppliers, conduct thorough research that includes checking their business history, client testimonials, and industry certifications. Request samples of their previous work to evaluate quality. Additionally, consider reaching out to other businesses in your network that have engaged with the supplier. Establishing clear communication about expectations, timelines, and support is crucial. Utilize platforms like LinkedIn or industry-specific forums to gather insights and recommendations. -
Can I customize the vending machines to suit my market needs?
Yes, many suppliers offer customization options for vending machines. You can tailor features such as size, product selection, payment systems, and branding to align with your target market preferences. Ensure to discuss your specific requirements during initial conversations with suppliers. Customization may involve additional costs, so inquire about the implications for minimum order quantities (MOQs) and lead times. -
What are the typical minimum order quantities (MOQs) and lead times for vending machines?
MOQs and lead times vary widely among suppliers based on their production capabilities and your customization requests. Generally, MOQs can range from one machine for smaller suppliers to larger quantities for major manufacturers. Lead times may be anywhere from a few weeks to several months, depending on the complexity of the order and supplier location. Always clarify these details upfront to avoid delays in your business launch. -
What payment terms should I expect when sourcing vending machines internationally?
Payment terms can differ significantly based on supplier policies and your negotiation outcomes. Common arrangements include upfront payments, deposits followed by balance payments upon delivery, or net payment terms after receipt. For international transactions, consider using escrow services or letters of credit to mitigate risk. Always confirm the accepted payment methods, as options like wire transfers or credit terms may vary by region. -
How can I ensure quality assurance and compliance with certifications?
Quality assurance is essential when sourcing vending machines. Request documentation from suppliers that demonstrates their compliance with international standards and safety regulations relevant to your market. This may include ISO certifications or specific health and safety approvals. Establish a quality control process, such as inspecting machines upon arrival and conducting regular maintenance checks to ensure continued compliance and performance. -
What logistics considerations should I keep in mind when importing vending machines?
Logistics is a critical factor in international sourcing. Assess the shipping methods available, including air freight for faster delivery or sea freight for cost savings. Understand customs regulations in your country to ensure compliance and avoid unexpected fees. Collaborating with a freight forwarder can simplify the shipping process, as they can manage documentation and navigate local laws effectively. -
How should I handle disputes or issues with suppliers?
Having a clear dispute resolution process in place is essential. Begin by establishing open lines of communication with your supplier to address issues promptly. Document all interactions and agreements to serve as a reference in case of disputes. If resolution fails, consider mediation or arbitration as a means of settling conflicts. Additionally, ensure your contracts include clauses that outline how disputes will be managed to protect your interests. -
What are the best practices for maintaining a successful relationship with suppliers?
Building a strong partnership with your suppliers is vital for long-term success. Maintain regular communication to keep them informed about your needs and market changes. Provide feedback on product quality and service to foster transparency and improvement. Consider visiting suppliers to strengthen relationships and gain insights into their operations. Establishing mutual trust and collaboration can lead to better pricing, exclusive products, and improved service over time.
Strategic Sourcing Conclusion and Outlook for build a vending machine
In conclusion, mastering the art of strategic sourcing is pivotal for international B2B buyers looking to thrive in the vending machine industry. By forging strong supplier relationships, understanding legal requirements, and optimizing product selection, businesses can transform their vending operations into profitable ventures. The ability to source effectively allows operators to align inventory with customer preferences, ensuring that machines remain stocked with high-demand products.
Key takeaways include the importance of reliable suppliers, which can significantly enhance operational efficiency, and the need to stay compliant with local regulations, safeguarding your business from potential pitfalls. Additionally, understanding market trends and consumer preferences in different regions—such as Africa, South America, the Middle East, and Europe—can help tailor your product offerings for maximum impact.
As the vending industry continues to evolve, embracing innovative solutions and flexible sourcing strategies will be crucial for success. For B2B buyers, the call to action is clear: invest time in building strategic supplier partnerships and stay informed about market dynamics to seize emerging opportunities. The future of vending is bright, and with the right sourcing approach, your business can lead the charge into this expanding market.