Master the Global Beauty Vending Machine Market: A B2B
Guide to Beauty Vending Machine
- Introduction: Navigating the Global Market for beauty vending machine
- Understanding beauty vending machine Types and Variations
- Key Industrial Applications of beauty vending machine
- Strategic Material Selection Guide for beauty vending machine
- In-depth Look: Manufacturing Processes and Quality Assurance for beauty vending machine
- Comprehensive Cost and Pricing Analysis for beauty vending machine Sourcing
- Spotlight on Potential beauty vending machine Manufacturers and Suppliers
- Essential Technical Properties and Trade Terminology for beauty vending machine
- Navigating Market Dynamics, Sourcing Trends, and Sustainability in the beauty vending machine Sector
- Frequently Asked Questions (FAQs) for B2B Buyers of beauty vending machine
- Strategic Sourcing Conclusion and Outlook for beauty vending machine
Introduction: Navigating the Global Market for beauty vending machine
In an era where convenience and accessibility are paramount, beauty vending machines have emerged as a transformative solution in the cosmetics industry. These innovative kiosks not only meet the rising demand for on-the-go beauty products but also cater to a diverse consumer base across various regions. For international B2B buyers, particularly those from Africa, South America, the Middle East, and Europe, understanding the intricacies of this market is essential for making informed sourcing decisions.
This comprehensive guide delves into the multifaceted world of beauty vending machines, offering insights into various types and models available in the market. We explore the materials used in manufacturing, ensuring quality control standards that align with global best practices. Additionally, we provide an overview of reputable suppliers and manufacturers that can facilitate your sourcing needs.
As you navigate the complexities of pricing and market dynamics, our guide addresses frequently asked questions, empowering you to make strategic choices that align with your business objectives. With a focus on actionable insights, this resource is designed to equip B2B buyers with the knowledge necessary to harness the potential of beauty vending machines, ultimately enhancing customer satisfaction and driving sales in your respective markets. Embrace the future of beauty retail with confidence and clarity as you explore the opportunities presented by this exciting sector.
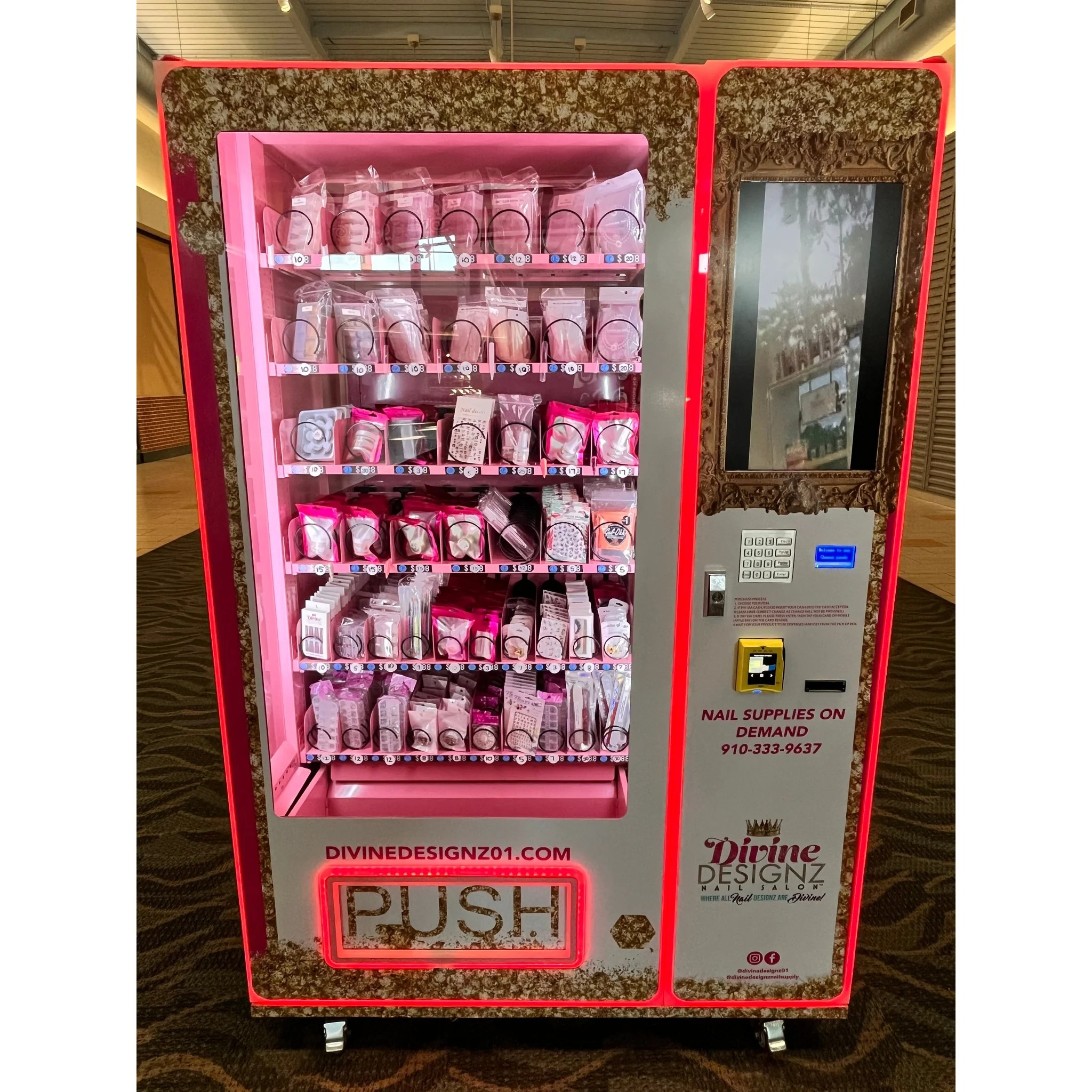
Illustrative Image (Source: Google Search)
Understanding beauty vending machine Types and Variations
Type Name | Key Distinguishing Features | Primary B2B Applications | Brief Pros & Cons for Buyers |
---|---|---|---|
Traditional Beauty Vending Machine | Offers a variety of beauty products in a standard vending format | Retail locations, salons, airports | Pros: Familiarity, ease of use. Cons: Limited product range; less customization. |
Smart Beauty Vending Machine | Features touchscreen interfaces and inventory tracking | High-traffic urban areas, events | Pros: Interactive experience, data collection. Cons: Higher initial investment and maintenance costs. |
Customized Beauty Vending Machine | Tailored product selection based on customer preferences | Specialty stores, luxury hotels | Pros: Personalized offerings, enhances customer loyalty. Cons: Requires in-depth market research. |
Eco-Friendly Beauty Vending Machine | Focuses on sustainable and organic products | Health-conscious markets, eco-friendly brands | Pros: Appeals to eco-conscious consumers. Cons: Limited product sourcing options. |
Mobile Beauty Vending Machine | Portable units that can be relocated easily | Events, festivals, pop-up shops | Pros: Flexibility in placement, can target specific demographics. Cons: Potential logistical challenges. |
Traditional Beauty Vending Machine
Traditional beauty vending machines are straightforward units that dispense a range of beauty products such as cosmetics, skincare, and haircare items. They are typically found in high-traffic retail environments, salons, or airports, appealing to consumers looking for convenience. For B2B buyers, the main consideration is the machine’s capacity and product range, as well as the reliability of the vending mechanism. While these machines are familiar and easy to use, they may lack the customization options that some markets demand.
Smart Beauty Vending Machine
Smart beauty vending machines integrate advanced technology, including touchscreen interfaces and inventory management systems. These machines are well-suited for urban areas and events where engagement and data collection are critical. B2B buyers should consider the upfront investment and ongoing maintenance costs, as well as the potential for increased customer interaction and sales through personalized recommendations. Although these machines offer a modern experience, the complexity of technology may require additional training for staff.
Customized Beauty Vending Machine
Customized beauty vending machines allow businesses to curate product selections based on customer preferences and local trends. They are particularly effective in specialty stores and luxury hotel settings where personalized service is paramount. B2B buyers need to conduct thorough market research to identify the right products to offer, which can enhance customer loyalty and brand perception. However, the necessity for customization can complicate inventory management and increase operational costs.
Eco-Friendly Beauty Vending Machine
Eco-friendly beauty vending machines focus on offering sustainable and organic beauty products, catering to the growing segment of health-conscious consumers. They are ideal for markets that prioritize sustainability, such as eco-friendly brands and health-focused retail environments. B2B buyers should evaluate the sourcing of products to ensure alignment with their brand values. While appealing to eco-conscious consumers, these machines may face challenges in product availability and sourcing.
Mobile Beauty Vending Machine
Mobile beauty vending machines are designed for flexibility, allowing businesses to relocate them as needed for events, festivals, or pop-up shops. This adaptability enables B2B buyers to target specific demographics and capitalize on seasonal or event-driven sales. When considering mobile units, logistics and transportation costs are crucial factors, along with the potential for rapid sales in high-traffic areas. However, the need for effective planning and execution can present challenges in maintaining consistent inventory and service levels.
Key Industrial Applications of beauty vending machine
Industry/Sector | Specific Application of beauty vending machine | Value/Benefit for the Business | Key Sourcing Considerations for this Application |
---|---|---|---|
Retail | Standalone beauty product sales | Increased sales through 24/7 availability | Location selection, product assortment, payment systems |
Hospitality | In-room beauty product dispensing | Enhanced guest experience, additional revenue stream | Compliance with health regulations, product quality assurance |
Fitness and Wellness | On-site beauty essentials for clients | Convenience for clients, promotes brand loyalty | Custom branding options, inventory management systems |
Events and Exhibitions | Pop-up beauty product sales | Immediate access to target demographics, brand visibility | Logistics for setup, product range tailored to audience |
Corporate Offices | Employee wellness and beauty stations | Boosts employee morale, enhances workplace environment | Product selection based on employee demographics, maintenance plans |
Retail
In the retail sector, beauty vending machines serve as a standalone solution for beauty product sales, providing customers with 24/7 access to popular items. This model addresses the challenge of limited store hours and enhances customer convenience, leading to increased sales. International B2B buyers should focus on location selection—high foot traffic areas are critical—and ensure a diverse product assortment that caters to local preferences. Additionally, integrating payment systems that accommodate local currencies can facilitate smoother transactions.
Hospitality
In the hospitality industry, beauty vending machines can be strategically placed in hotel rooms or lobbies to dispense essential beauty products. This not only enhances the guest experience but also creates an additional revenue stream for hotels. Buyers in this sector must consider compliance with health regulations to ensure that products meet safety standards. Furthermore, product quality assurance is essential to maintain brand reputation and guest satisfaction.
Fitness and Wellness
Fitness centers and wellness studios utilize beauty vending machines to provide clients with on-site beauty essentials, such as skincare products or cosmetics. This convenience can significantly enhance the client experience and foster brand loyalty. B2B buyers should explore custom branding options to align with their facility’s image and consider inventory management systems that track product turnover and client preferences, ensuring that popular items are always available.
Events and Exhibitions
Beauty vending machines are increasingly used in events and exhibitions for pop-up sales, allowing brands to connect with target demographics directly. This setup provides immediate access to potential customers and boosts brand visibility in a competitive market. Buyers should pay attention to logistics for setup, ensuring that machines are operational and stocked with products tailored to the audience. A well-curated product range can significantly enhance the appeal and effectiveness of the vending machine.
Corporate Offices
In corporate settings, beauty vending machines can serve as wellness stations for employees, offering a selection of beauty and personal care products. This initiative not only boosts employee morale but also enhances the overall workplace environment. B2B buyers should select products based on employee demographics to ensure relevance and appeal. Additionally, establishing maintenance plans for regular restocking and servicing can ensure the machines remain functional and inviting.
Related Video: DIY Vending Machine – Arduino based Mechatronics Project
Strategic Material Selection Guide for beauty vending machine
When selecting materials for beauty vending machines, it’s essential to consider various factors that influence performance, durability, and compliance with international standards. Below, we analyze four common materials used in the construction of beauty vending machines, focusing on their properties, advantages, disadvantages, and specific considerations for international B2B buyers.
1. Stainless Steel
Key Properties:
Stainless steel is known for its excellent corrosion resistance, high strength, and ability to withstand varying temperatures and pressures. Its non-reactive nature makes it ideal for storing beauty products, particularly those that may contain sensitive ingredients.
Pros & Cons:
Stainless steel is durable and easy to clean, making it suitable for high-traffic environments. However, it can be more expensive than other materials, and its manufacturing complexity may lead to higher production costs.
Impact on Application:
This material is compatible with a wide range of beauty products, including liquids, creams, and powders. Its non-porous surface helps maintain product integrity.
Considerations for International Buyers:
Compliance with standards such as ASTM and DIN is crucial. Buyers from regions like Africa and the Middle East should ensure that the stainless steel used meets local health and safety regulations, especially for cosmetic applications.
2. Polycarbonate
Key Properties:
Polycarbonate is a lightweight, impact-resistant thermoplastic with good thermal stability. It can handle moderate temperatures but is less resistant to UV exposure over time.
Pros & Cons:
The primary advantage of polycarbonate is its cost-effectiveness and ease of manufacturing. However, it may not be suitable for all beauty products, particularly those sensitive to temperature changes or UV light.
Impact on Application:
Polycarbonate is often used for transparent panels or containers within vending machines, allowing customers to view products easily. However, its chemical compatibility must be assessed for specific media.
Considerations for International Buyers:
Buyers should verify that the polycarbonate complies with regulations in their respective countries, particularly regarding food-grade materials. In Europe, for example, adherence to REACH regulations is essential.
3. Aluminum
Key Properties:
Aluminum is lightweight, resistant to corrosion, and has a good strength-to-weight ratio. It can withstand moderate temperatures and pressures, making it suitable for various applications.
Pros & Cons:
While aluminum is relatively inexpensive and easy to work with, it may not be as durable as stainless steel in high-impact scenarios. Additionally, it can be prone to scratching and denting.
Impact on Application:
Aluminum is often used for structural components of vending machines and can be coated for added protection. It is compatible with many beauty products, but its chemical resistance should be evaluated.
Considerations for International Buyers:
Buyers from South America and Africa should ensure that aluminum components meet local standards for durability and safety. Compliance with ASTM and other relevant standards is critical for ensuring product quality.
4. Glass
Key Properties:
Glass is a non-reactive material with excellent clarity and aesthetic appeal. It is capable of withstanding high temperatures, but it can be fragile and susceptible to breakage.
Pros & Cons:
Glass provides a premium look and is easy to clean, making it appealing for beauty products. However, its fragility can be a significant drawback, especially in high-traffic areas where machines may be subject to rough handling.
Impact on Application:
Glass is ideal for displaying beauty products, particularly high-end items. Its non-porous surface helps maintain product integrity, but care must be taken to ensure it does not shatter.
Considerations for International Buyers:
In regions like Europe and the Middle East, buyers should consider safety regulations regarding glass use in public spaces. Compliance with safety standards is essential to mitigate risks associated with breakage.
Summary Table
Material | Typical Use Case for beauty vending machine | Key Advantage | Key Disadvantage/Limitation | Relative Cost (Low/Med/High) |
---|---|---|---|---|
Stainless Steel | Structural components and product storage | Excellent corrosion resistance | Higher cost, complex manufacturing | High |
Polycarbonate | Transparent panels and product containers | Cost-effective, lightweight | Limited UV resistance | Medium |
Aluminum | Structural components and casing | Lightweight, good strength-to-weight ratio | Susceptible to scratches and dents | Low |
Glass | Display cases for beauty products | Premium look, easy to clean | Fragile, risk of breakage | Medium |
This strategic material selection guide provides essential insights for international B2B buyers, helping them make informed decisions tailored to their specific market needs and regulatory environments.
In-depth Look: Manufacturing Processes and Quality Assurance for beauty vending machine
The manufacturing of beauty vending machines involves a series of well-defined stages, each contributing to the overall quality and functionality of the final product. Understanding these processes and the associated quality assurance measures is essential for international B2B buyers seeking reliable suppliers.
Manufacturing Processes
1. Material Preparation
The first stage in manufacturing beauty vending machines is material preparation. This involves sourcing high-quality materials that meet specific design and functional requirements. Common materials include:
- Metal: Typically steel or aluminum for the structural frame, chosen for durability and strength.
- Plastic: Used for components such as buttons and displays, selected for aesthetic appeal and ease of cleaning.
- Electronic Components: These include sensors, touch screens, and payment systems, sourced from reputable suppliers to ensure reliability.
Buyers should verify that suppliers use materials compliant with international safety standards, such as RoHS (Restriction of Hazardous Substances) and REACH (Registration, Evaluation, Authorisation and Restriction of Chemicals).
2. Forming
Once materials are prepared, the next step is forming. This process shapes the materials into the required components using techniques such as:
- CNC Machining: Provides precision in cutting and shaping metal parts.
- Injection Molding: Commonly used for plastic components, allowing for intricate designs and high-volume production.
- Sheet Metal Fabrication: Used to create the body of the vending machine, ensuring strength and durability.
Buyers should inquire about the technology and machinery used in this stage, as advanced methods can lead to better quality and lower production costs.
3. Assembly
The assembly stage is critical for ensuring that all components fit together properly and function as intended. This stage typically involves:
- Sub-Assembly: Smaller groups of components are assembled first, such as electronic systems or mechanical parts.
- Final Assembly: The complete machine is assembled, including the integration of software for operating the vending machine.
- Quality Checks: At this stage, initial quality checks may be performed to ensure that each component meets standards before final assembly.
Buyers should assess the assembly process for efficiency and the skill level of the workforce, as these factors can impact production timelines and product quality.
4. Finishing
Finishing processes enhance the aesthetics and functionality of the vending machines. This can include:
- Painting and Coating: Protective and decorative finishes that enhance durability and appeal.
- Quality Control Measures: Final checks before packaging, ensuring that all functionalities are operational and meet design specifications.
Inquire about the types of finishes used and whether they comply with international standards, as this can affect the longevity and user satisfaction of the machines.
Quality Assurance (QA)
Quality assurance is integral to the manufacturing process, ensuring that the final product meets both international and industry-specific standards. Key components of a robust QA program include:
Relevant International Standards
- ISO 9001: This standard focuses on quality management systems (QMS) and ensures consistency in quality across processes. Suppliers should be certified to demonstrate their commitment to quality.
- CE Marking: Required for products sold in the European Economic Area (EEA), indicating compliance with health, safety, and environmental protection standards.
- API Standards: For electronic components, compliance with the American Petroleum Institute standards can indicate reliability and safety.
Quality Control Checkpoints
Quality control involves several checkpoints throughout the manufacturing process:
- Incoming Quality Control (IQC): Inspection of raw materials and components upon arrival to ensure they meet specified standards.
- In-Process Quality Control (IPQC): Continuous monitoring during the manufacturing process to detect and rectify issues in real-time.
- Final Quality Control (FQC): Comprehensive testing and inspection of the completed machines to ensure they function correctly and meet all specifications.
Common Testing Methods
Testing methods vary based on component requirements and may include:
- Functional Testing: Ensures that all electronic components operate correctly.
- Durability Testing: Assesses the machine’s resistance to wear and tear over time.
- Compliance Testing: Checks adherence to safety and quality standards.
Verifying Supplier Quality Control
For international B2B buyers, verifying a supplier’s quality control measures is crucial. Here are effective methods to do so:
- Audits: Conducting regular audits of potential suppliers can provide insight into their manufacturing processes and quality assurance practices. Buyers should look for ISO 9001 certification as a baseline.
- Quality Reports: Requesting detailed quality reports can help buyers understand the supplier’s QA metrics, defect rates, and corrective actions taken for non-conformance.
- Third-Party Inspections: Engaging third-party inspection agencies can provide an unbiased assessment of the supplier’s quality control processes and final products.
Quality Control and Certification Nuances
When dealing with international suppliers, it’s essential to understand the nuances of quality control and certification:
- Regional Compliance: Different regions may have specific requirements. For example, CE marking is crucial for Europe, while UL certification might be needed in North America.
- Cultural Considerations: Understanding the cultural context of suppliers in Africa, South America, the Middle East, and Europe can help in negotiating quality standards and ensuring compliance.
- Communication: Clear communication about quality expectations and standards from the outset can prevent misunderstandings and ensure that the final product meets buyers’ needs.
Conclusion
For B2B buyers in the beauty vending machine market, a thorough understanding of manufacturing processes and quality assurance is essential. By focusing on material preparation, forming, assembly, and finishing, alongside robust quality control measures, buyers can ensure they select reliable suppliers that meet international standards. Verifying supplier practices through audits, reports, and third-party inspections further enhances confidence in the quality of the products procured.
Related Video: SMART Quality Control for Manufacturing
Comprehensive Cost and Pricing Analysis for beauty vending machine Sourcing
When sourcing beauty vending machines, understanding the comprehensive cost structure and pricing dynamics is crucial for international B2B buyers. This analysis delves into the various cost components and pricing influencers that affect the procurement of these machines, particularly for buyers from Africa, South America, the Middle East, and Europe.
Cost Components
-
Materials: The primary materials used in beauty vending machines include high-quality plastics, metals, and electronic components. The selection of materials significantly impacts the cost; for instance, machines using durable, weather-resistant materials may have higher upfront costs but lower maintenance expenses.
-
Labor: Labor costs can vary greatly depending on the production location. Regions with lower labor costs, such as parts of Asia, may offer more competitive pricing. However, consider the potential trade-offs in quality and service.
-
Manufacturing Overhead: This encompasses the indirect costs associated with production, including utilities, rent, and equipment depreciation. Efficient production processes can help minimize overhead, thus reducing the overall cost.
-
Tooling: Initial tooling costs for customized machines can be substantial. Buyers should be aware that the complexity of design and the need for specialized tools will influence these expenses.
-
Quality Control (QC): Implementing rigorous QC processes ensures that the machines meet safety and performance standards. While this may add to the cost, it is essential for reducing long-term liabilities and enhancing customer satisfaction.
-
Logistics: Shipping costs can vary based on distance, shipping method, and volume. Understanding the logistics landscape, including potential tariffs and customs fees, is vital for accurate cost estimation.
-
Margin: Suppliers will typically include a profit margin in their pricing. This margin can fluctuate based on market demand, competition, and buyer relationships.
Price Influencers
-
Volume/MOQ: The minimum order quantity (MOQ) can significantly affect pricing. Larger orders often qualify for bulk discounts, which can result in substantial savings.
-
Specifications/Customization: Custom features or specifications can increase the base price. It’s advisable to clearly define requirements to avoid unexpected costs later.
-
Materials and Quality Certifications: Higher-quality materials and certifications (e.g., ISO, CE) can lead to increased costs but may offer better durability and compliance with regulations.
-
Supplier Factors: The reputation and reliability of the supplier can influence pricing. Established suppliers may charge more due to their proven track record and quality assurance.
-
Incoterms: Understanding Incoterms is crucial for international transactions. Different terms (e.g., FOB, CIF) determine who bears the cost at various points in the shipping process, affecting the total landed cost.
Buyer Tips
-
Negotiation: Engage in thorough negotiations with suppliers. Leverage your purchasing power and explore options for volume discounts or favorable payment terms.
-
Cost-Efficiency: Consider the Total Cost of Ownership (TCO), which includes purchase price, maintenance, and operational costs. Opting for slightly more expensive machines with lower operational costs may result in greater long-term savings.
-
Pricing Nuances: International buyers should be aware of currency fluctuations, which can affect pricing. Additionally, differences in local market conditions may influence supplier pricing strategies.
-
Research Local Regulations: Ensure compliance with local regulations regarding imports and product safety standards, as non-compliance can incur additional costs.
Disclaimer
The prices discussed are indicative and may vary based on market conditions, supplier negotiations, and specific buyer requirements. It is recommended to obtain quotes from multiple suppliers to better understand the pricing landscape before making a decision.
Spotlight on Potential beauty vending machine Manufacturers and Suppliers
- (No specific manufacturer data was available or requested for detailed profiling in this section for beauty vending machine.)*
Essential Technical Properties and Trade Terminology for beauty vending machine
Key Technical Properties for Beauty Vending Machines
Understanding the technical properties of beauty vending machines is essential for B2B buyers to make informed purchasing decisions. Here are several critical specifications to consider:
-
Material Grade
– Definition: This refers to the type of materials used in the construction of the vending machine, such as stainless steel, plastic, or glass.
– Importance: High-quality materials ensure durability and resistance to wear and tear, which is crucial in high-traffic environments. For buyers in regions like Africa and South America, where conditions may vary significantly, selecting the right material can affect longevity and maintenance costs. -
Size and Dimensions
– Definition: The physical dimensions of the vending machine, including height, width, and depth.
– Importance: Understanding the size is vital for determining the machine’s placement in retail spaces. Buyers must ensure that the machine fits well within their intended environment while maximizing product visibility and accessibility. -
Power Consumption
– Definition: The amount of electricity the vending machine requires to operate.
– Importance: Low power consumption is essential for minimizing operational costs, especially in regions with high energy prices. This aspect is particularly relevant for businesses in the Middle East, where energy efficiency can significantly impact profitability. -
Temperature Control
– Definition: The ability of the vending machine to maintain specific temperature ranges for products, especially for items like cosmetics that may require refrigeration.
– Importance: Proper temperature control extends the shelf life of beauty products and ensures product efficacy. This feature is especially critical for buyers in tropical climates, where heat can compromise product integrity. -
User Interface Technology
– Definition: The interface through which customers interact with the machine, which may include touch screens, mobile app integration, or QR code scanning.
– Importance: A user-friendly interface enhances customer experience, increasing sales. B2B buyers should consider the technology that appeals to their target demographic, particularly in Europe, where tech-savvy consumers expect seamless interactions. -
Payment Options
– Definition: The methods available for customers to pay for their purchases, including cash, credit/debit cards, and mobile payments.
– Importance: A diverse range of payment options can lead to higher sales volumes. As digital payment methods become increasingly popular, especially in urban areas, buyers should prioritize machines that support multiple payment methods.
Common Trade Terminology in the Beauty Vending Machine Industry
Familiarity with industry jargon can help B2B buyers navigate negotiations and contracts effectively. Here are some common terms:
-
OEM (Original Equipment Manufacturer)
– Definition: A company that produces parts or equipment that may be marketed by another manufacturer.
– Usage: Buyers should understand whether they are purchasing from an OEM or a reseller, as this can affect warranty and support agreements. -
MOQ (Minimum Order Quantity)
– Definition: The smallest quantity of a product that a supplier is willing to sell.
– Usage: Knowing the MOQ is crucial for buyers to manage inventory and cash flow. Suppliers with high MOQs may be less flexible for smaller businesses or startups. -
RFQ (Request for Quotation)
– Definition: A document that a buyer sends to suppliers to request pricing and other details for a specific product.
– Usage: Utilizing an RFQ can help buyers compare prices and terms from different suppliers, ensuring they get the best deal. -
Incoterms (International Commercial Terms)
– Definition: A set of international rules that define the responsibilities of sellers and buyers in international transactions.
– Usage: Understanding Incoterms is vital for managing shipping costs and risks. For buyers in Africa and South America, being clear about delivery terms can prevent unexpected expenses. -
Lead Time
– Definition: The amount of time it takes from placing an order to receiving the product.
– Usage: Buyers should inquire about lead times to manage stock levels and avoid disruptions in service. -
Warranty and Support Terms
– Definition: Conditions under which the manufacturer will repair or replace faulty products.
– Usage: Understanding warranty terms is critical for assessing long-term risk and support, particularly in regions where maintenance services may be limited.
By familiarizing themselves with these technical properties and trade terminologies, B2B buyers can enhance their purchasing strategies and ensure successful integration of beauty vending machines into their operations.
Navigating Market Dynamics, Sourcing Trends, and Sustainability in the beauty vending machine Sector
Market Overview & Key Trends
The beauty vending machine sector is experiencing significant transformation, driven by various global factors. The surge in demand for convenience, personalization, and on-the-go beauty solutions has positioned vending machines as a viable retail channel. Particularly in regions like Africa, South America, the Middle East, and Europe, the adoption of these machines is being fueled by urbanization and the growing popularity of e-commerce.
Key trends include the integration of technology such as AI and IoT, which enhance the consumer experience by offering personalized product recommendations and real-time inventory management. Additionally, the emergence of contactless payment systems is making transactions smoother and more secure, appealing to health-conscious consumers post-pandemic. In markets like Turkey and Mexico, local brands are increasingly leveraging vending machines to reach customers in high-traffic areas, such as airports, malls, and universities, thereby expanding their market reach without the overhead costs associated with traditional retail outlets.
Moreover, sustainability is becoming a significant driver in purchasing decisions. International B2B buyers are now more inclined to source products from vendors who prioritize sustainable practices, leading to a rise in eco-friendly beauty products being offered through vending machines. As these machines evolve, they are expected to incorporate features such as solar-powered units and biodegradable packaging, aligning with the growing consumer demand for environmentally responsible options.
Sustainability & Ethical Sourcing in B2B
As the beauty vending machine sector grows, sustainability and ethical sourcing have emerged as critical considerations for B2B buyers. The environmental impact of beauty products, from production to disposal, cannot be overlooked. Buyers are increasingly scrutinizing supply chains, seeking partnerships with manufacturers who demonstrate a commitment to reducing their carbon footprint and utilizing sustainable practices.
Importance of ethical supply chains cannot be overstated. Consumers are more aware than ever of the environmental and social implications of their purchases. Brands that prioritize transparency in sourcing and production are more likely to gain consumer trust and loyalty. This trend is particularly pronounced in regions with a burgeoning middle class, such as parts of Africa and South America, where consumers are willing to pay a premium for products that align with their values.
B2B buyers should also look for green certifications and sustainable materials when selecting beauty products for their vending machines. Certifications like EcoCert and Fair Trade can serve as indicators of a brand’s commitment to sustainability. Additionally, sourcing products that utilize recyclable packaging or sustainable ingredients not only meets the expectations of environmentally conscious consumers but also differentiates offerings in a competitive market.
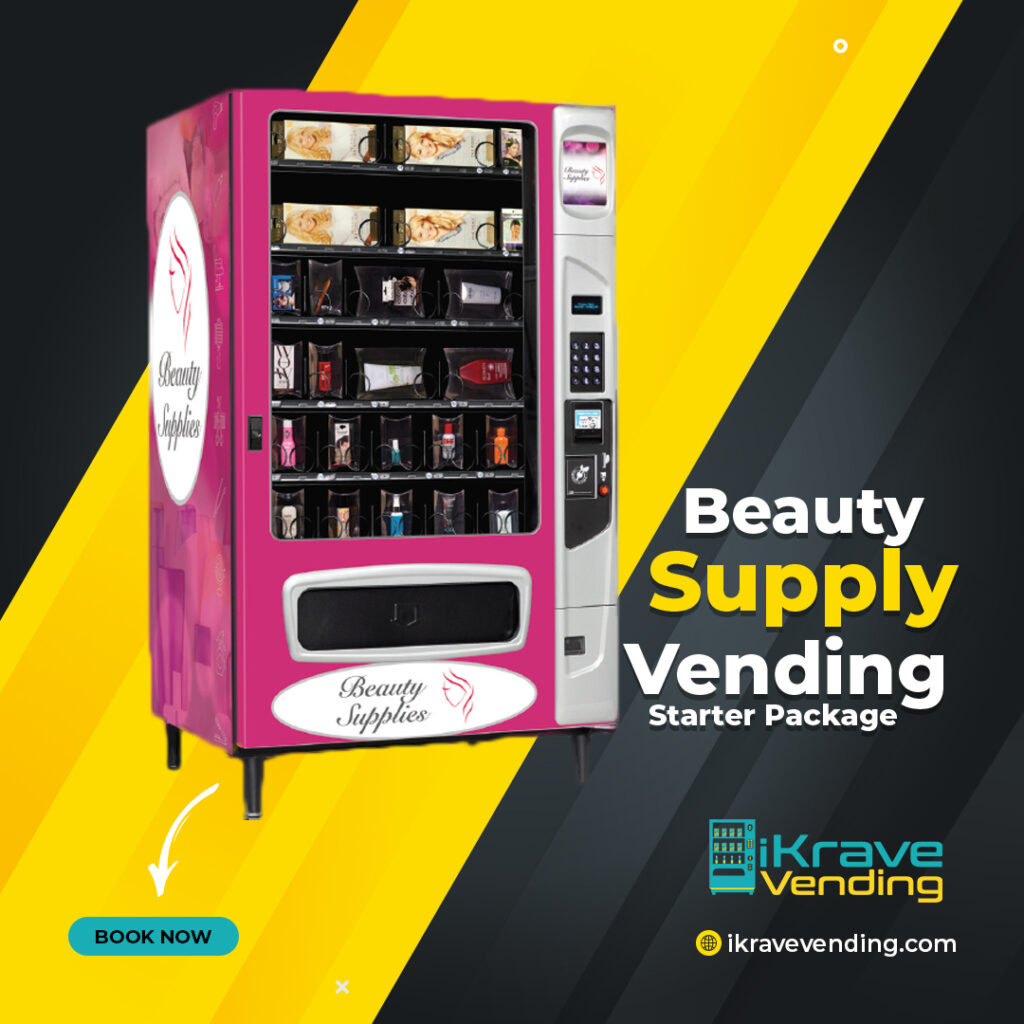
Illustrative Image (Source: Google Search)
Brief Evolution/History
The beauty vending machine concept has evolved significantly over the past few decades. Initially seen as a novelty, these machines have transitioned into a mainstream retail channel, particularly in urban settings. Early models focused primarily on convenience, offering basic beauty products. However, advancements in technology and changing consumer preferences have led to a more sophisticated approach, integrating digital interfaces, personalized offerings, and a wider range of high-quality products.
Today, the beauty vending machine sector represents a fusion of retail innovation and consumer demand for convenience and sustainability, making it a compelling opportunity for international B2B buyers looking to enter or expand in this growing market.
Related Video: What global trade deals are really about (hint: it’s not trade) | Haley Edwards | TEDxMidAtlantic
Frequently Asked Questions (FAQs) for B2B Buyers of beauty vending machine
-
What should I consider when vetting suppliers for beauty vending machines?
When vetting suppliers, prioritize their experience in the beauty industry and track record in manufacturing vending machines. Request references and case studies to assess their reliability. Evaluate their production capabilities, technological advancements, and adherence to international quality standards. Additionally, confirm if they possess necessary certifications (e.g., CE, ISO) that ensure product safety and compliance with your local regulations. For international transactions, check their ability to navigate customs and trade regulations in your region. -
Can beauty vending machines be customized to fit my brand?
Yes, most suppliers offer customization options to align the vending machines with your brand identity. This can include tailored aesthetics, such as color schemes and logo placements, as well as product selection tailored to your target market. Discuss your specific requirements with potential suppliers, including the types of beauty products you want to offer. It’s crucial to ensure that the customization process does not significantly extend lead times or increase costs beyond your budget. -
What are the typical minimum order quantities (MOQs) and lead times?
Minimum order quantities can vary significantly between suppliers, often ranging from 10 to 100 units depending on the manufacturer’s production capabilities. Lead times typically range from 6 to 12 weeks, but this can be affected by the complexity of customization and the supplier’s current workload. Always clarify these details upfront and consider negotiating MOQs if you are testing the market or entering a new region. Be sure to account for potential delays in logistics, especially when shipping internationally. -
How can I ensure quality assurance and certification of the machines?
To ensure quality assurance, request detailed documentation regarding the manufacturing process and quality control measures in place at the supplier’s facility. Inquire about their testing procedures for durability and performance. Certifications such as ISO 9001 or specific safety certifications relevant to your country are essential indicators of quality. It’s advisable to ask for samples or conduct a factory visit if possible, especially for larger orders, to witness the quality control measures firsthand. -
What payment terms should I expect when sourcing beauty vending machines?
Payment terms can vary widely among suppliers. Generally, expect to pay a deposit (often 30-50%) upfront, with the balance due upon delivery or prior to shipping. Some suppliers may offer financing options or flexible payment plans, especially for larger orders. It’s crucial to clearly define payment terms in the contract to avoid misunderstandings. Additionally, consider using secure payment methods that offer buyer protection, especially for international transactions, to mitigate risks. -
How should I approach logistics and shipping for international orders?
When dealing with logistics, it’s essential to understand the shipping methods available (e.g., air freight vs. sea freight) and their associated costs and timelines. Discuss with your supplier who will handle logistics—some may offer to manage shipping while others will require you to arrange it. Be aware of customs duties and import taxes that will apply in your country. Collaborating with a freight forwarder who specializes in international shipping can streamline this process and ensure compliance with all regulations. -
What steps can I take to resolve disputes with suppliers?
Establish clear communication channels and expectations from the outset to minimize disputes. If issues arise, document all correspondence and agreements to support your position. Engage in open discussions with the supplier to seek amicable resolutions. If necessary, refer to the terms outlined in your contract regarding dispute resolution processes. Consider mediation or arbitration as alternatives to litigation, as they can be more cost-effective and quicker, particularly in international contexts. -
Are there any specific regulations I need to be aware of when importing beauty vending machines?
Yes, each country has specific regulations concerning the importation of machinery and beauty products. Familiarize yourself with local laws regarding safety standards, labeling requirements, and any restrictions on certain ingredients or materials. In regions like Europe, compliance with the General Product Safety Directive is critical. It’s advisable to consult with a trade expert or legal advisor familiar with your target market to ensure compliance and avoid costly delays or penalties during customs clearance.
Strategic Sourcing Conclusion and Outlook for beauty vending machine
The beauty vending machine sector represents a dynamic opportunity for international B2B buyers, particularly those in Africa, South America, the Middle East, and Europe. As consumer demand for convenience and accessibility rises, strategic sourcing becomes essential to capitalize on this trend. Key takeaways include the importance of identifying reliable suppliers, understanding local market preferences, and leveraging technology for inventory management and customer engagement.
Investing in beauty vending machines not only enhances brand visibility but also caters to the growing desire for on-the-go beauty solutions. Buyers should prioritize partnerships with manufacturers who can provide customization options and robust support services to ensure a seamless integration into existing business models. Additionally, keeping an eye on emerging trends such as eco-friendly products and digital payment solutions will position businesses favorably in a competitive landscape.
Looking ahead, the potential for growth in this sector is significant. International B2B buyers are encouraged to take proactive steps in exploring partnerships and sourcing strategies that align with their market goals. By doing so, they can secure a competitive edge and meet the evolving needs of consumers in their regions. Embrace this opportunity and lead the way in transforming the beauty retail experience.