Unlock Profits with Seaga Vending Machine: A Comprehensive
Guide to Seaga Vending Machine
- Introduction: Navigating the Global Market for seaga vending machine
- Understanding seaga vending machine Types and Variations
- Key Industrial Applications of seaga vending machine
- Strategic Material Selection Guide for seaga vending machine
- In-depth Look: Manufacturing Processes and Quality Assurance for seaga vending machine
- Comprehensive Cost and Pricing Analysis for seaga vending machine Sourcing
- Spotlight on Potential seaga vending machine Manufacturers and Suppliers
- Essential Technical Properties and Trade Terminology for seaga vending machine
- Navigating Market Dynamics, Sourcing Trends, and Sustainability in the seaga vending machine Sector
- Frequently Asked Questions (FAQs) for B2B Buyers of seaga vending machine
- Strategic Sourcing Conclusion and Outlook for seaga vending machine
Introduction: Navigating the Global Market for seaga vending machine
In the rapidly evolving landscape of global commerce, the demand for innovative solutions like Seaga vending machines is on the rise. These machines are not just a means of dispensing snacks and beverages; they represent a gateway to convenience and efficiency in various industries, ranging from hospitality to retail. For international B2B buyers, particularly in regions such as Africa, South America, the Middle East, and Europe, understanding the intricacies of sourcing Seaga vending machines can unlock new revenue streams and enhance customer satisfaction.
This guide serves as a comprehensive resource, meticulously designed to empower buyers with the knowledge they need to make informed decisions. We will explore the diverse types of Seaga vending machines, highlight the materials used in their construction, and delve into manufacturing and quality control processes. Additionally, we will provide insights into reputable suppliers and a thorough analysis of cost considerations. Understanding the market dynamics will further equip buyers to navigate this competitive landscape effectively.
By the end of this guide, you will possess actionable insights that facilitate strategic sourcing decisions, tailored to the unique needs of your business and market. Whether you are looking to expand your operations in Nigeria, Brazil, or elsewhere, the information provided here will enable you to leverage the potential of Seaga vending machines to enhance your offerings and drive growth.
Understanding seaga vending machine Types and Variations
Type Name | Key Distinguishing Features | Primary B2B Applications | Brief Pros & Cons for Buyers |
---|---|---|---|
Snack Vending Machine | Offers a variety of packaged snacks | Offices, schools, gyms | Pros: Wide selection, easy to restock. Cons: Limited to non-perishable items. |
Beverage Vending Machine | Dispenses cold drinks, including sodas and juices | Cafés, restaurants, waiting areas | Pros: High demand, quick turnover. Cons: Requires refrigeration, higher maintenance. |
Combination Vending Machine | Dual functionality for snacks and beverages | Hospitals, corporate offices, events | Pros: Versatile, maximizes space. Cons: Complexity in inventory management. |
Healthy Vending Machine | Focuses on nutritious snacks and drinks | Schools, wellness centers, corporate wellness programs | Pros: Appeals to health-conscious consumers. Cons: May have slower sales in less health-focused areas. |
Specialty Vending Machine | Customizable for niche products (e.g., electronics, personal care) | Airports, malls, tech hubs | Pros: Unique offerings can attract specific demographics. Cons: Higher initial investment and potential for slower sales. |
Snack Vending Machine
Snack vending machines are designed to provide a variety of packaged snacks, making them ideal for locations such as offices, schools, and gyms. These machines typically feature adjustable shelves to accommodate different product sizes. For B2B buyers, the key consideration is the machine’s ability to restock easily and handle high demand. Snack vending machines are generally low maintenance, but their limitation to non-perishable items may restrict product diversity.
Beverage Vending Machine
Beverage vending machines are tailored for dispensing cold drinks, including sodas, juices, and bottled water. They are commonly found in cafés, restaurants, and waiting areas. The primary B2B advantage lies in their high turnover rate, driven by consumer demand for beverages. However, these machines require refrigeration, leading to higher maintenance costs. Buyers should consider the energy efficiency of the machine to manage operational expenses effectively.
Combination Vending Machine
Combination vending machines integrate both snacks and beverages, making them highly versatile. They are particularly suitable for environments like hospitals, corporate offices, and events where diverse consumer needs must be met. While they maximize space and product offerings, the complexity of inventory management can be a challenge. B2B buyers should assess the machine’s layout to ensure efficient product rotation and minimize downtime.
Healthy Vending Machine
Healthy vending machines focus on providing nutritious snacks and drinks, catering to the growing health-conscious market. They are increasingly popular in schools, wellness centers, and corporate wellness programs. The appeal to health-conscious consumers is a significant advantage, but these machines may experience slower sales in areas less focused on health. Buyers should evaluate product selection and pricing strategies to align with local consumer preferences.
Specialty Vending Machine
Specialty vending machines are customizable to offer niche products such as electronics, personal care items, or local artisan goods. These machines are often placed in high-traffic areas like airports, malls, and tech hubs. Their unique offerings can attract specific demographics, providing a competitive edge. However, the higher initial investment and potential for slower sales cycles necessitate careful market analysis before purchase. B2B buyers should consider the target audience and location to ensure profitability.
Key Industrial Applications of seaga vending machine
Industry/Sector | Specific Application of seaga vending machine | Value/Benefit for the Business | Key Sourcing Considerations for this Application |
---|---|---|---|
Healthcare | Dispensing medical supplies and snacks | Improved patient satisfaction and convenience | Compliance with health regulations, reliability in supply |
Education | Providing quick snacks and beverages on campus | Enhances student experience and retention | Variety of offerings, ease of use, payment options |
Corporate Offices | Offering refreshments in break rooms | Boosts employee morale and productivity | Customization options, maintenance service availability |
Transportation Hubs | Vending in airports and train stations | Reduces wait times, increases revenue opportunities | Durability, diverse product range, payment flexibility |
Retail | Self-service kiosks for product sampling | Engages customers, enhances shopping experience | Integration with inventory systems, promotional capabilities |
Healthcare Applications
In healthcare settings, seaga vending machines serve as vital dispensers of medical supplies, snacks, and beverages for patients and staff. These machines alleviate the challenge of accessing essential items during non-traditional hours, thereby enhancing patient satisfaction. For B2B buyers in regions like Africa and South America, sourcing machines that comply with health regulations and provide reliable supply chains is crucial. Additionally, the ability to customize offerings based on local dietary preferences can further enhance user experience.
Educational Institutions
Seaga vending machines are increasingly utilized in educational institutions to provide quick access to snacks and beverages for students. This not only improves the overall student experience but also fosters a conducive learning environment. For buyers in Europe and the Middle East, it’s important to consider the variety of products offered, as well as the ease of use for students of all ages. Furthermore, having machines that accept various payment methods, including mobile payments, can significantly boost sales.
Corporate Offices
In corporate environments, seaga vending machines can transform break rooms by offering a range of refreshments. This service not only boosts employee morale but also enhances productivity by reducing the time spent searching for food options. Buyers in regions like Africa and Brazil should prioritize machines that can be customized to reflect local tastes and dietary restrictions. Additionally, ensuring availability of ongoing maintenance services can minimize downtime and optimize employee satisfaction.
Transportation Hubs
Transportation hubs, including airports and train stations, benefit from the installation of seaga vending machines that provide travelers with quick snacks and beverages. This application reduces wait times and enhances the overall travel experience, making it an attractive option for B2B buyers in these sectors. Key considerations include the durability of the machines to withstand high traffic and the ability to offer a diverse range of products. Flexibility in payment options, such as contactless payments, is also essential to cater to the diverse traveler demographic.
Retail Environments
In retail settings, seaga vending machines can be utilized as self-service kiosks for product sampling, thereby engaging customers and enhancing their shopping experience. For B2B buyers, integrating these machines with existing inventory systems can streamline operations and improve sales tracking. In regions like the Middle East and Europe, promotional capabilities, such as discounts or loyalty programs, can significantly increase foot traffic and customer retention. Ensuring that the machines are equipped with intuitive interfaces can further enhance customer interaction and satisfaction.
Related Video: Loading a Vertical Drop Bottle Vending Machine by Seaga
Strategic Material Selection Guide for seaga vending machine
When selecting materials for Seaga vending machines, international B2B buyers must consider various factors that impact performance, durability, and compliance with regional standards. Below is an analysis of four common materials used in the construction of Seaga vending machines, focusing on their properties, advantages, disadvantages, and specific considerations for buyers from diverse regions such as Africa, South America, the Middle East, and Europe.
1. Stainless Steel
Key Properties:
Stainless steel is renowned for its excellent corrosion resistance, high strength, and ability to withstand high temperatures. It typically has a temperature rating of up to 800°F (427°C) and can handle moderate pressure levels.
Pros & Cons:
The durability of stainless steel makes it ideal for high-traffic environments, as it resists wear and tear. However, it is more expensive than other materials, which can affect overall project budgets. Manufacturing complexity is moderate, as it requires specialized welding techniques.
Impact on Application:
Stainless steel is compatible with a wide range of media, including food and beverages, making it suitable for vending machines that dispense perishable items.
Considerations for International Buyers:
Compliance with food safety standards (e.g., FDA in the U.S., EFSA in Europe) is crucial. Buyers should also consider local standards such as ASTM or DIN for material specifications.
2. Powder-Coated Steel
Key Properties:
Powder-coated steel offers a protective layer that enhances corrosion resistance and aesthetic appeal. It can withstand temperatures up to 200°F (93°C) and has moderate pressure resistance.
Pros & Cons:
This material is cost-effective and provides a wide range of color options for branding. However, the coating can chip or scratch, exposing the steel underneath, which may lead to corrosion over time. Manufacturing processes are relatively straightforward.
Impact on Application:
While powder-coated steel is suitable for general use in vending machines, it may not be ideal for environments with high humidity or exposure to harsh chemicals.
Considerations for International Buyers:
Buyers should ensure that the powder coating complies with local environmental regulations and standards, which may vary significantly between regions.
3. Aluminum
Key Properties:
Aluminum is lightweight, corrosion-resistant, and can handle temperatures up to 400°F (204°C). It has good strength-to-weight ratios, making it suitable for portable vending solutions.
Pros & Cons:
The primary advantage of aluminum is its lightweight nature, which facilitates easy transportation and installation. However, it is less durable than stainless steel and can be more expensive depending on the alloy used. Manufacturing complexity is low, as aluminum is easy to machine and weld.
Impact on Application:
Aluminum is compatible with many media types but may not be suitable for highly acidic or alkaline substances, which can lead to corrosion.
Considerations for International Buyers:
Buyers should verify that the aluminum used meets regional standards such as JIS in Japan or EN standards in Europe, especially for food-grade applications.
4. High-Density Polyethylene (HDPE)
Key Properties:
HDPE is a strong, durable plastic that is resistant to impact and moisture. It can withstand temperatures up to 120°F (49°C) and is not suitable for high-pressure applications.
Pros & Cons:
HDPE is lightweight and cost-effective, making it an attractive option for budget-conscious buyers. However, it has a lower temperature tolerance and may not be suitable for all vending machine applications. Manufacturing is simple and cost-efficient.
Impact on Application:
HDPE is ideal for non-food items or products that do not require temperature control. It is commonly used in vending machines that dispense snacks or beverages in sealed containers.
Considerations for International Buyers:
Buyers should ensure compliance with local regulations regarding plastics, particularly in food safety, as standards can vary widely.
Summary Table
Material | Typical Use Case for seaga vending machine | Key Advantage | Key Disadvantage/Limitation | Relative Cost (Low/Med/High) |
---|---|---|---|---|
Stainless Steel | High-traffic food and beverage vending machines | Excellent durability and corrosion resistance | Higher cost, moderate manufacturing complexity | High |
Powder-Coated Steel | General use vending machines | Cost-effective, aesthetic versatility | Susceptible to chipping and corrosion | Medium |
Aluminum | Portable vending solutions | Lightweight, easy to transport | Less durable than stainless steel | Medium |
High-Density Polyethylene (HDPE) | Non-food item vending machines | Lightweight, cost-effective | Lower temperature tolerance | Low |
This material selection guide aims to equip international B2B buyers with the insights needed to make informed decisions when sourcing Seaga vending machines, ensuring compliance and suitability for their specific markets.
In-depth Look: Manufacturing Processes and Quality Assurance for seaga vending machine
The manufacturing processes and quality assurance protocols for Seaga vending machines are integral to ensuring product reliability and customer satisfaction. For B2B buyers, particularly from regions like Africa, South America, the Middle East, and Europe, understanding these processes is crucial for making informed procurement decisions.
Manufacturing Processes
1. Material Preparation
The first stage involves sourcing high-quality materials that meet industry standards. Steel and plastics are commonly used for the machine’s structure and components. Suppliers must provide material certifications to confirm compliance with international quality standards. Buyers should ensure that materials are resistant to corrosion and wear, especially in humid or harsh environments typical of certain regions.
2. Forming
Once materials are prepared, the forming process begins. This includes cutting, bending, and shaping the materials into the required components. CNC (Computer Numerical Control) machining is often employed for precision and consistency. This technology allows for intricate designs and ensures that components fit together seamlessly, reducing assembly time and potential errors.
3. Assembly
The assembly phase is where the individual components come together to form the complete vending machine. This stage requires skilled labor and often involves the use of automated assembly lines to enhance efficiency. Key components, such as the coin mechanism, payment systems, and refrigeration units, are integrated during this phase. Buyers should inquire about the assembly techniques used and whether they employ lean manufacturing principles to minimize waste and improve productivity.
4. Finishing
After assembly, the finishing process enhances both the aesthetic and functional aspects of the vending machines. This can include painting, coating, and applying decals. The finishing process not only protects the machine from environmental factors but also aligns it with branding requirements. Buyers should consider the durability of finishes, especially in outdoor or high-traffic locations, where wear and tear can be significant.
Quality Assurance
Quality assurance is a critical aspect of manufacturing that ensures products meet specified requirements and standards. For international B2B buyers, understanding the quality assurance processes is essential for mitigating risks associated with procurement.
International Standards
Seaga vending machines typically adhere to several international quality standards, including:
- ISO 9001: This standard focuses on quality management systems and is essential for ensuring consistent product quality and customer satisfaction.
- CE Marking: This indicates that the vending machines comply with EU safety, health, and environmental requirements, making them suitable for the European market.
- API Standards: For machines involving specific functionalities, compliance with American Petroleum Institute standards may be relevant, especially for machines that dispense oil or fuel.
Quality Control Checkpoints
Quality control checkpoints are strategically placed throughout the manufacturing process to catch defects early and ensure product integrity. Key checkpoints include:
- Incoming Quality Control (IQC): At this stage, raw materials and components are inspected upon arrival to verify their quality against specifications.
- In-Process Quality Control (IPQC): During the manufacturing process, ongoing inspections ensure that each stage meets quality standards, reducing the likelihood of defects in the final product.
- Final Quality Control (FQC): Before shipping, a comprehensive inspection is performed on the completed vending machines to ensure they function correctly and meet all quality standards.
Common Testing Methods
Various testing methods are employed to ensure the vending machines meet performance and safety standards. These may include:
- Functional Testing: Ensures all mechanisms (e.g., payment systems, dispensing units) operate correctly.
- Durability Testing: Assesses how well machines withstand physical stress and environmental conditions.
- Electrical Safety Testing: Verifies that all electrical components comply with safety standards to prevent hazards.
Verification of Supplier Quality Control
B2B buyers can take several steps to verify the quality control processes of their suppliers:
- Audits: Conducting on-site audits allows buyers to observe manufacturing practices and quality control measures in action. This hands-on approach can reveal insights about the supplier’s commitment to quality.
- Quality Reports: Requesting detailed quality reports that outline testing methodologies and results can provide transparency into the supplier’s quality assurance processes.
- Third-Party Inspections: Engaging independent inspection agencies can offer an unbiased assessment of the manufacturer’s quality standards. This is particularly important for buyers in regions with different regulatory environments, ensuring that products meet the buyer’s local standards.
Quality Control Nuances for International B2B Buyers
When sourcing Seaga vending machines, international buyers must navigate several quality control nuances:
- Regulatory Compliance: Different regions may have varying regulatory requirements. Buyers in Europe, for example, must ensure compliance with CE marking, while those in South America may need to adhere to local certifications.
- Cultural Considerations: Understanding cultural differences in manufacturing practices can aid in communication with suppliers. Buyers from Africa or the Middle East may find that establishing strong relationships with suppliers can lead to better quality control outcomes.
- Logistics and Supply Chain: The geographical location of suppliers can impact lead times and the ability to address quality issues promptly. Buyers should consider the implications of distance on quality assurance, especially in terms of shipping times and the potential for damage during transport.
Conclusion
In summary, the manufacturing processes and quality assurance protocols for Seaga vending machines are vital for ensuring product reliability and safety. By understanding these processes, B2B buyers from Africa, South America, the Middle East, and Europe can make informed decisions, ensuring they procure high-quality vending machines that meet their specific needs and regulatory requirements. Engaging in thorough supplier evaluations and understanding the nuances of international standards will further enhance the procurement experience.
Related Video: SMART Quality Control for Manufacturing
Comprehensive Cost and Pricing Analysis for seaga vending machine Sourcing
Understanding the Cost Structure of Seaga Vending Machines
When sourcing Seaga vending machines, it is crucial to comprehend the various components that contribute to the overall cost. The primary cost structure can be categorized into several key components:
- Materials: The choice of materials significantly affects the pricing of vending machines. High-quality components, such as durable plastics and metals, can increase initial costs but may reduce long-term maintenance expenses.
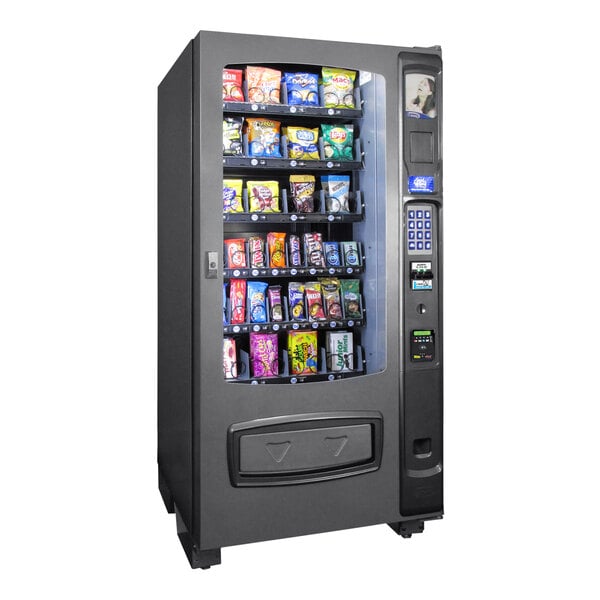
Illustrative Image (Source: Google Search)
-
Labor: Labor costs vary by region and can influence the final price. In regions with higher labor costs, manufacturers may pass these expenses onto buyers. Conversely, sourcing from areas with lower labor costs can provide savings.
-
Manufacturing Overhead: This includes costs related to factory operations, such as utilities, equipment maintenance, and administrative expenses. Efficient production processes can help minimize these costs.
-
Tooling: Custom tooling for unique designs or specifications can be a significant expense. Buyers should consider whether standard models meet their needs or if custom tooling is necessary.
-
Quality Control (QC): Ensuring that the vending machines meet specific quality standards involves additional costs. Investing in thorough QC processes can prevent future issues, thus saving costs in the long run.
-
Logistics: Transporting vending machines from the manufacturer to the buyer’s location includes shipping fees, insurance, and potential tariffs. Understanding logistics costs is essential for accurate budgeting.
-
Margin: Suppliers typically include a profit margin in their pricing. This margin can vary significantly based on market conditions and the supplier’s business model.
Price Influencers in Vending Machine Sourcing
Several factors can influence the pricing of Seaga vending machines for international buyers:
-
Volume/MOQ: Purchasing in bulk can lead to significant discounts. Understanding the minimum order quantities (MOQ) and negotiating for larger orders can result in cost savings.
-
Specifications/Customization: Custom features or specifications can lead to higher costs. Buyers should assess whether customization is essential for their market or if standard models suffice.
-
Materials: The choice of materials impacts both the cost and durability of the vending machines. Opting for higher-quality materials can provide a better return on investment.
-
Quality/Certifications: Machines that meet international quality standards or certifications may come at a premium. However, these certifications can enhance marketability and reduce liability.
-
Supplier Factors: The reputation, reliability, and financial stability of the supplier can affect pricing. Conducting due diligence on potential suppliers can help mitigate risks.
-
Incoterms: Understanding the terms of shipping (Incoterms) can have significant cost implications. Buyers should clarify responsibilities for shipping, insurance, and tariffs to avoid unexpected expenses.
Buyer Tips for Cost-Efficiency
For international B2B buyers, particularly in Africa, South America, the Middle East, and Europe, several strategies can enhance cost-efficiency:
-
Negotiate: Always negotiate prices, especially when ordering in bulk or when establishing long-term relationships. Suppliers may have flexibility in their pricing.
-
Total Cost of Ownership (TCO): Evaluate not just the purchase price but also the ongoing costs associated with maintenance, operation, and potential repairs. TCO can provide a clearer picture of the overall investment.
-
Pricing Nuances: Be aware of regional pricing differences due to local market conditions, currency fluctuations, and import tariffs. Understanding these nuances can help in better budgeting.
-
Leverage Local Partnerships: Collaborating with local distributors or agents can reduce logistics costs and provide insights into regional market demands.
Disclaimer on Indicative Prices
It’s important to note that the prices for Seaga vending machines can vary widely based on the aforementioned factors. Buyers should obtain multiple quotes from suppliers and consider both the initial purchase price and the long-term costs associated with ownership.
Spotlight on Potential seaga vending machine Manufacturers and Suppliers
- (No specific manufacturer data was available or requested for detailed profiling in this section for seaga vending machine.)*
Essential Technical Properties and Trade Terminology for seaga vending machine
Essential Technical Properties
When evaluating Seaga vending machines, several key technical properties are crucial for B2B buyers. Understanding these specifications will help make informed decisions regarding quality, performance, and suitability for various markets.
-
Material Grade: The materials used in vending machine construction significantly impact durability and aesthetics. Common materials include stainless steel for the exterior and high-density polyethylene for internal components. A higher grade of material not only enhances the machine’s lifespan but also ensures it withstands various environmental conditions, which is particularly important in regions with extreme weather like Africa and the Middle East.
-
Energy Efficiency Rating: This property indicates how much energy the vending machine consumes relative to its output. Machines with higher energy efficiency ratings can lead to significant cost savings in electricity, making them more attractive in markets where operational costs are a concern, such as Brazil and Nigeria. Buyers should look for machines that meet international energy standards, which also reflect a commitment to sustainability.
-
Capacity: The capacity of a vending machine refers to the number of items it can hold. Understanding the capacity is vital for aligning product offerings with consumer demand. For instance, a higher capacity machine may be beneficial in high-traffic areas, while smaller units might be more suitable for niche markets. Buyers should assess their target locations to choose the optimal capacity.
-
User Interface: The design and functionality of the user interface can greatly affect customer experience. Features such as touchscreen displays, multilingual options, and cashless payment systems enhance usability. In diverse markets, particularly in Europe and Africa, a user-friendly interface can drive higher sales and customer satisfaction.
-
Serviceability: This property encompasses how easily a vending machine can be maintained and repaired. Machines designed for easy access to internal components reduce downtime and service costs. Buyers should inquire about serviceability features, such as modular designs and diagnostic displays, which can significantly impact operational efficiency.
Common Trade Terms
Familiarity with industry terminology is essential for B2B buyers to navigate negotiations and procurement processes effectively. Here are some common terms related to Seaga vending machines:
-
OEM (Original Equipment Manufacturer): This term refers to companies that produce parts and equipment that may be marketed by another manufacturer. Understanding OEM relationships is crucial for buyers as it often determines the quality and compatibility of parts used in vending machines.
-
MOQ (Minimum Order Quantity): MOQ is the smallest number of units a supplier is willing to sell. This term is particularly relevant for international buyers looking to import vending machines, as it can impact inventory management and initial investment costs. Buyers should negotiate MOQs that align with their market entry strategies.
-
RFQ (Request for Quotation): An RFQ is a document sent to suppliers to solicit price quotes for specific products or services. For international buyers, submitting a detailed RFQ can lead to better pricing and terms. It’s advisable to include specifications, quantities, and delivery timelines in the RFQ to receive accurate responses.
-
Incoterms (International Commercial Terms): These are pre-defined commercial terms published by the International Chamber of Commerce (ICC) that clarify the responsibilities of buyers and sellers in international transactions. Understanding Incoterms is vital for B2B buyers to manage risks related to shipping, insurance, and customs duties.
-
Lead Time: This term refers to the amount of time it takes from placing an order to receiving the product. For vending machines, lead time can vary significantly based on production schedules and shipping logistics. Buyers should factor in lead times when planning inventory to ensure product availability in target markets.
-
Warranty: A warranty is a guarantee provided by the manufacturer regarding the condition of the product and the commitment to repair or replace it if necessary. Understanding warranty terms is crucial for buyers as it reflects the manufacturer’s confidence in their product and can significantly impact long-term operational costs.
By grasping these technical properties and trade terms, B2B buyers can better navigate the procurement landscape of Seaga vending machines, ensuring they make decisions that align with their business goals and market demands.
Navigating Market Dynamics, Sourcing Trends, and Sustainability in the seaga vending machine Sector
Market Overview & Key Trends
The global market for Seaga vending machines is experiencing a significant transformation driven by several key factors. First, the rising demand for contactless payment solutions has accelerated the adoption of advanced vending technology. Buyers from regions like Africa and South America are increasingly seeking machines that support mobile payments and digital wallets, catering to a tech-savvy customer base. Additionally, the COVID-19 pandemic has heightened consumer awareness around hygiene, prompting a shift towards machines that emphasize sanitation and touchless interfaces.
Another prominent trend is the integration of smart technology. Vending machines equipped with IoT capabilities allow operators to monitor inventory levels in real-time, optimize restocking schedules, and analyze customer purchasing behavior. This data-driven approach not only enhances operational efficiency but also improves customer experience, making it a compelling selling point for B2B buyers looking to invest in modern vending solutions.
Sourcing trends are also evolving, with an increasing emphasis on local suppliers to reduce lead times and transportation costs. For international buyers from the Middle East and Europe, establishing partnerships with regional manufacturers can yield significant benefits, such as better adaptability to local market needs and enhanced supply chain resilience. Furthermore, sustainability is becoming a crucial aspect of purchasing decisions. Buyers are now prioritizing vending machines that utilize energy-efficient technologies and sustainable materials, reflecting a broader trend towards responsible consumption.
Sustainability & Ethical Sourcing in B2B
In the context of the Seaga vending machine sector, sustainability is not just a buzzword; it is becoming a critical component of business strategy. The environmental impact of vending machines, from energy consumption to waste generation, necessitates a proactive approach to sustainability. B2B buyers are increasingly looking for machines that incorporate energy-efficient components, such as LED lighting and eco-friendly refrigeration systems, which can significantly reduce the carbon footprint.
Moreover, the importance of ethical sourcing cannot be overstated. As international buyers become more conscious of the social and environmental implications of their purchases, they are seeking suppliers that adhere to strict ethical standards. This includes using materials certified by recognized environmental organizations, ensuring fair labor practices, and minimizing the use of harmful substances in manufacturing processes.
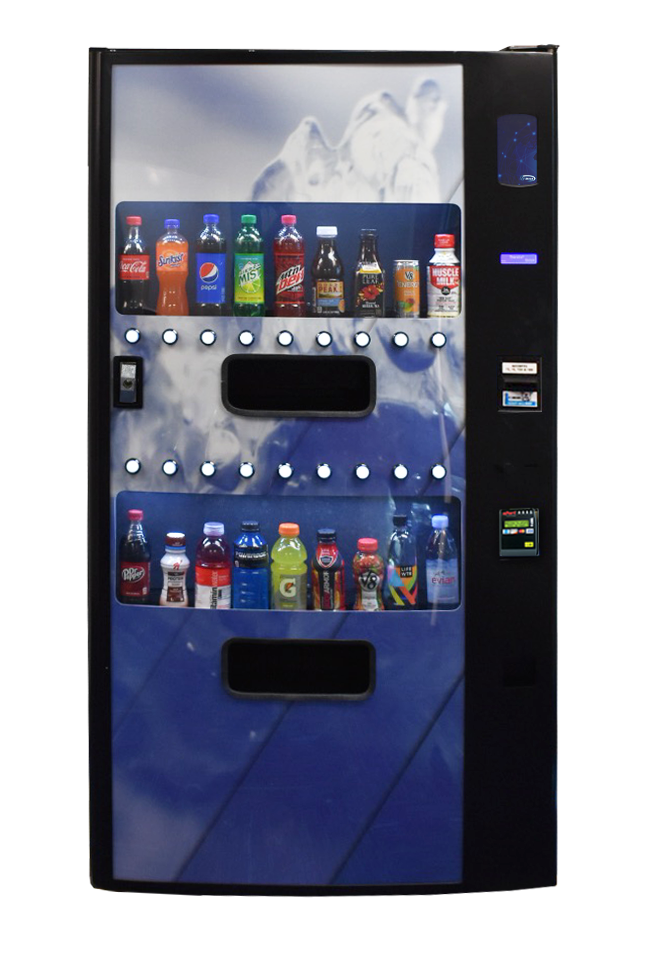
Illustrative Image (Source: Google Search)
Investing in green certifications and sustainable materials not only enhances brand reputation but also opens up new market opportunities, particularly in regions where consumers are prioritizing eco-conscious products. For instance, buyers from Europe may find that emphasizing sustainability in their vending solutions can lead to competitive advantages in increasingly eco-aware markets.
Brief Evolution/History
The Seaga vending machine has evolved significantly since its inception, reflecting broader technological advancements and changing consumer preferences. Initially, vending machines offered a limited selection of snacks and beverages, but over the years, the introduction of electronic payment systems and advanced inventory management has transformed the landscape.
Today, Seaga machines are designed not only for traditional vending but also for offering healthier food options, catering to a growing demand for wellness-focused products. This evolution has made them more appealing to a diverse range of international buyers, from convenience store operators in Brazil to corporate offices in Nigeria, seeking innovative solutions that align with modern consumer trends. As the market continues to evolve, staying informed about these historical shifts is essential for B2B buyers looking to capitalize on emerging opportunities.
Related Video: Global Trade & Logistics – What is Global Trade?
Frequently Asked Questions (FAQs) for B2B Buyers of seaga vending machine
-
What criteria should I consider when vetting suppliers for Seaga vending machines?
When vetting suppliers for Seaga vending machines, prioritize their experience in the industry, reputation, and customer reviews. Verify their certifications and compliance with international standards, particularly safety and quality certifications. Assess their financial stability to ensure they can fulfill orders reliably. Additionally, consider their responsiveness and customer service capabilities, as these will be crucial during the procurement process and beyond. -
Can Seaga vending machines be customized for my specific needs?
Yes, Seaga offers customization options for their vending machines to meet various business needs. You can choose from a range of features, including machine size, product selection, branding, and payment systems. When discussing customization with suppliers, be specific about your requirements, such as product types or branding elements, to ensure the final product aligns with your business goals. -
What is the minimum order quantity (MOQ) and typical lead time for Seaga vending machines?
The MOQ for Seaga vending machines can vary depending on the supplier and the specific models ordered. Typically, you might expect an MOQ of 5-10 units for bulk orders. Lead times can range from 4 to 12 weeks, influenced by factors like customization, production schedules, and shipping arrangements. Always clarify these details upfront with your supplier to align your inventory needs with their capabilities. -
What payment options are available for purchasing Seaga vending machines?
Payment options for purchasing Seaga vending machines usually include bank transfers, letters of credit, and payment through secure online platforms. Discuss payment terms with your supplier, such as deposit requirements and payment schedules, to avoid misunderstandings. For international transactions, consider using escrow services to ensure secure payment and delivery conditions that protect both parties. -
How can I ensure quality assurance and certification for Seaga vending machines?
To ensure quality assurance, request documentation of relevant certifications from your supplier, such as ISO standards or CE markings. Conduct quality checks during production if possible, or arrange for third-party inspections before shipment. Establish a clear return policy and warranty terms with your supplier to address any potential quality issues post-delivery. -
What logistics considerations should I keep in mind when importing Seaga vending machines?
Logistics is a critical aspect of importing Seaga vending machines. Consider shipping methods, freight costs, and customs clearance procedures in your country. Collaborate with experienced freight forwarders who understand the regulations and can handle documentation efficiently. Additionally, factor in potential delays at ports, and ensure you have a plan for storage and distribution upon arrival. -
How should I handle disputes with suppliers of Seaga vending machines?
In the event of a dispute with a supplier, first attempt to resolve the issue through direct communication. Clearly outline your concerns and refer to your contract terms. If necessary, consider mediation or arbitration, especially for international transactions, to avoid lengthy legal battles. Establishing a well-defined contract with clear terms and conditions from the outset can help mitigate disputes. -
What are the key features of Seaga vending machines that can enhance my business?
Seaga vending machines are equipped with various features that can enhance your business, such as cashless payment options, energy-efficient designs, and customizable displays. Many models also offer telemetry systems that allow remote monitoring of inventory and sales data. Consider these features when selecting a machine, as they can improve customer experience and operational efficiency while providing valuable insights for your business strategy.
Strategic Sourcing Conclusion and Outlook for seaga vending machine
In conclusion, the strategic sourcing of Seaga vending machines presents significant opportunities for international B2B buyers, especially in regions like Africa, South America, the Middle East, and Europe. By prioritizing quality, innovation, and supplier reliability, businesses can enhance their operational efficiency and customer satisfaction. The adaptability of Seaga machines to diverse markets allows for tailored solutions that meet local consumer demands, whether in bustling urban centers or remote areas.
Key Takeaways:
– Market Adaptation: Seaga vending machines can be customized to cater to local tastes and preferences, providing a competitive edge.
– Supplier Relationships: Establishing strong partnerships with reliable suppliers ensures consistent product availability and support.
– Cost Efficiency: Strategic sourcing can lead to lower operational costs through bulk purchasing and optimized logistics.
As the vending industry continues to evolve, now is the time for B2B buyers to invest in innovative solutions that align with emerging market trends. Engage with reputable suppliers, explore financing options, and leverage technology to enhance your vending operations. By doing so, you position your business for sustainable growth and success in an increasingly competitive landscape.