Mastering Vending Machine Locations for Sale: Your Ultimate
Guide to Vending Machine Locations For Sale
- Introduction: Navigating the Global Market for vending machine locations for sale
- Understanding vending machine locations for sale Types and Variations
- Key Industrial Applications of vending machine locations for sale
- Strategic Material Selection Guide for vending machine locations for sale
- In-depth Look: Manufacturing Processes and Quality Assurance for vending machine locations for sale
- Comprehensive Cost and Pricing Analysis for vending machine locations for sale Sourcing
- Spotlight on Potential vending machine locations for sale Manufacturers and Suppliers
- Essential Technical Properties and Trade Terminology for vending machine locations for sale
- Navigating Market Dynamics, Sourcing Trends, and Sustainability in the vending machine locations for sale Sector
- Frequently Asked Questions (FAQs) for B2B Buyers of vending machine locations for sale
- Strategic Sourcing Conclusion and Outlook for vending machine locations for sale
Introduction: Navigating the Global Market for vending machine locations for sale
In an increasingly competitive global marketplace, the strategic placement of vending machines can significantly influence a business’s profitability and market reach. Vending machine locations for sale are more than just physical spaces; they represent opportunities for revenue generation, brand visibility, and customer engagement across diverse sectors. As international B2B buyers, particularly from Africa, South America, the Middle East, and Europe, understanding the nuances of these locations is crucial for making informed investment decisions.
This comprehensive guide delves into the critical aspects of vending machine locations, equipping buyers with insights into various types of locations, materials used in machine construction, manufacturing and quality control standards, and the key suppliers in the market. We will also explore cost considerations, market trends, and frequently asked questions that address common concerns and challenges faced by B2B buyers.
By navigating this guide, you will gain actionable insights that empower you to identify lucrative vending machine locations that align with your business objectives. Whether you are looking to expand your operations in established markets like the UK or venture into emerging economies in Africa and South America, understanding the global landscape of vending machine placements will enhance your sourcing strategy and ultimately drive your business success.
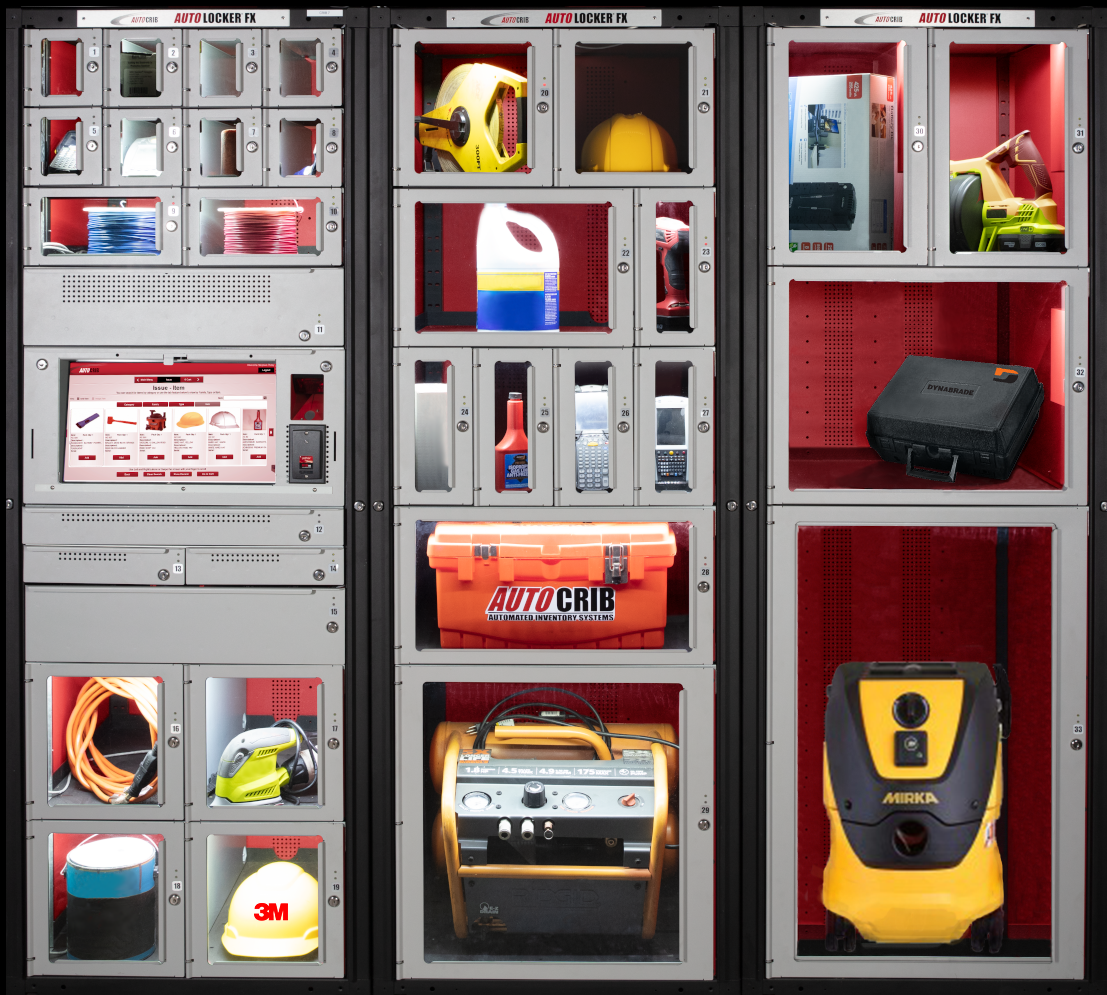
Illustrative Image (Source: Google Search)
Understanding vending machine locations for sale Types and Variations
Type Name | Key Distinguishing Features | Primary B2B Applications | Brief Pros & Cons for Buyers |
---|---|---|---|
High Foot Traffic Locations | Near busy streets, malls, or transport hubs | Retail, hospitality, transportation | Pros: High sales potential; Cons: Higher rental costs |
Office Complexes | Located in corporate buildings and business parks | Corporate snacks, beverages | Pros: Steady demand; Cons: Limited variety of products |
Educational Institutions | Positioned in schools, colleges, and universities | Student snacks, beverages | Pros: Regular foot traffic; Cons: Seasonal demand fluctuations |
Healthcare Facilities | Found in hospitals, clinics, and medical offices | Patient and visitor refreshments | Pros: Essential services; Cons: Strict regulations on products |
Industrial Sites | Installed in factories and warehouses | Employee snacks, beverages | Pros: Consistent usage; Cons: Potential for lower margins |
High Foot Traffic Locations
High foot traffic locations include areas such as busy streets, shopping malls, and transport hubs. These sites are ideal for B2B buyers looking to maximize sales volume due to the constant flow of potential customers. When considering this type of location, buyers should evaluate the rental costs against the expected foot traffic and sales potential. It’s crucial to conduct thorough market research to understand local demographics and consumer behavior.
Office Complexes
Vending machines in office complexes cater primarily to corporate employees, offering snacks and beverages throughout the workday. These locations provide a steady demand due to the predictable daily routines of office workers. Buyers should focus on selecting machines that offer a mix of healthy and indulgent options to cater to varying employee preferences. Additionally, understanding the office culture can help in curating product selections that resonate with the workforce.
Educational Institutions
Vending machines placed in educational institutions, such as schools and universities, serve students and staff with quick snack and beverage options. The key to success in this environment is to offer products that appeal to a younger demographic, including healthy snacks and energy drinks. Buyers should be aware of seasonal demand fluctuations, especially during exam periods or holidays, and consider flexible contract terms to accommodate these changes.
Healthcare Facilities
Vending machines in healthcare facilities, including hospitals and clinics, provide essential refreshments for patients, visitors, and staff. This type of location often has strict regulations regarding the types of products that can be sold, focusing on healthy options and dietary restrictions. B2B buyers must ensure compliance with health standards and consider offering a diverse range of products that cater to various dietary needs. The reliability of sales in such locations makes them attractive, despite the regulatory challenges.
Industrial Sites
Industrial sites, such as factories and warehouses, are prime locations for vending machines targeting employees on long shifts. These machines typically offer hearty snacks and beverages to keep workers energized. When considering these locations, buyers should assess the potential for consistent usage and the types of products that will best meet the needs of the workforce. Understanding the work schedules and preferences of employees can significantly enhance product selection and sales performance.
Related Video: How I Got My BEST Vending Machine Location – Rayzo Vending
Key Industrial Applications of vending machine locations for sale
Industry/Sector | Specific Application of vending machine locations for sale | Value/Benefit for the Business | Key Sourcing Considerations for this Application |
---|---|---|---|
Retail | Snack and beverage vending in high-traffic areas | Increased impulse purchases, 24/7 availability | Foot traffic analysis, local preferences, competition |
Healthcare | Medical supplies vending in hospitals | Quick access to essential items, reduced wait times | Compliance with health regulations, product range |
Education | Campus vending machines for students | Convenient access to snacks and drinks, boosts student satisfaction | Location density, payment options, health-conscious selections |
Corporate Offices | Employee refreshment stations | Enhances employee morale, increases productivity | Variety of offerings, machine maintenance, payment systems |
Transportation Hubs | Vending in airports and train stations | Captures transient customers, generates high sales volume | Location visibility, product mix, payment methods |
Retail Sector
In retail environments, vending machine locations for sale can capitalize on high-traffic areas such as shopping malls or busy streets. These machines offer snacks and beverages, providing convenience and encouraging impulse purchases. Buyers must consider local consumer preferences, competitive offerings, and foot traffic analysis to optimize placement and product selection. Understanding peak shopping times and adapting inventory accordingly can significantly enhance sales potential.
Healthcare Sector
Vending machines in healthcare settings, particularly hospitals, serve a critical role by providing immediate access to medical supplies and personal care items. This application addresses the need for efficiency and reduces wait times for patients and staff. International buyers must ensure compliance with health regulations and focus on a diverse product range that meets various medical needs. Location is paramount, as machines should be placed in areas with high foot traffic, such as waiting rooms or emergency departments.
Education Sector
In educational institutions, vending machines cater to students’ needs for quick snacks and beverages between classes. This not only enhances student satisfaction but also promotes healthy eating habits when appropriately stocked. For B2B buyers in the education sector, understanding the demographic profile of students and their preferences is crucial. Additionally, offering cashless payment options can facilitate sales, especially in regions where mobile payments are prevalent.
Corporate Offices
Vending machines placed in corporate offices provide employees with convenient access to refreshments, which can improve morale and productivity. Businesses should focus on a variety of offerings, including healthy snacks and beverages, to cater to diverse employee preferences. Key considerations for B2B buyers include machine maintenance schedules and the integration of modern payment systems to ensure seamless transactions. The strategic placement of machines in break rooms or near common areas can significantly increase usage.
Transportation Hubs
Vending machines in transportation hubs like airports and train stations target transient customers looking for quick, convenient options. These locations can generate high sales volumes, especially during peak travel times. B2B buyers should consider the visibility of the machines and the product mix to attract diverse travelers. Additionally, offering multiple payment methods, including mobile payments, can enhance customer convenience and encourage purchases in these fast-paced environments.
Related Video: How I Started My Vending Machine Business & Got My First Locations
Strategic Material Selection Guide for vending machine locations for sale
When selecting materials for vending machine locations, it is crucial to consider the specific properties and performance characteristics that will impact the longevity and functionality of the machines. Below is an analysis of four common materials used in vending machine construction, focusing on their properties, advantages, disadvantages, and considerations for international B2B buyers.
1. Stainless Steel
Key Properties:
Stainless steel is known for its excellent corrosion resistance and high strength-to-weight ratio. It can withstand a wide range of temperatures and pressures, making it suitable for various environments.
Pros & Cons:
The durability of stainless steel is one of its main advantages, as it can resist rust and staining, ensuring a long service life. However, it is generally more expensive than other materials, which can impact initial investment costs. Manufacturing complexity can also be higher due to the need for specialized welding techniques.
Impact on Application:
Stainless steel is compatible with a variety of media, including food and beverages, making it an ideal choice for vending machines. Its non-reactive nature ensures that it does not affect the quality of the products dispensed.
Considerations for International Buyers:
Buyers should ensure compliance with local food safety standards, which can vary significantly between regions. For instance, in Europe, compliance with regulations such as the EU’s food contact materials (FCM) legislation is essential.
2. Mild Steel
Key Properties:
Mild steel is characterized by its ductility and malleability, making it easy to work with. It has moderate strength and is typically less resistant to corrosion compared to stainless steel.
Pros & Cons:
Mild steel is cost-effective and widely available, making it a popular choice for many applications. However, its susceptibility to rust and corrosion can be a significant drawback, especially in humid or wet environments. Protective coatings can mitigate this issue but may add to manufacturing complexity.
Impact on Application:
Mild steel is suitable for internal components of vending machines where exposure to moisture is minimal. However, its use in external parts is limited unless adequately protected.
Considerations for International Buyers:
Buyers should be aware of the need for protective coatings and the potential for increased maintenance costs. Compliance with local standards, such as ASTM in the U.S. or DIN in Germany, is also critical.
3. Aluminum
Key Properties:
Aluminum is lightweight and has good corrosion resistance, making it suitable for various applications. It has a lower strength compared to steel but offers excellent thermal conductivity.
Pros & Cons:
The primary advantage of aluminum is its lightweight nature, which can reduce shipping costs and ease installation. However, it can be more expensive than mild steel and may not be as durable under heavy loads.
Impact on Application:
Aluminum is often used in vending machine exteriors and components that require a lightweight material. Its corrosion resistance makes it suitable for outdoor applications, but care must be taken with certain acidic products.
Considerations for International Buyers:
Buyers should consider the availability of aluminum and its cost in their region. Compliance with international standards for aluminum alloys, such as JIS in Japan, may also be necessary.
4. High-Density Polyethylene (HDPE)
Key Properties:
HDPE is a thermoplastic known for its high strength-to-density ratio and excellent chemical resistance. It is lightweight and can withstand a wide range of temperatures.
Pros & Cons:
The main advantage of HDPE is its resistance to impact and chemicals, making it suitable for vending machines that dispense various products. However, it may not be as aesthetically pleasing as metal options and can have limitations in structural applications.
Impact on Application:
HDPE is ideal for internal components and storage areas within vending machines, especially those that require resistance to spills and leaks. Its flexibility also allows for various design configurations.
Considerations for International Buyers:
Buyers should ensure that the HDPE used complies with local regulations regarding food safety and environmental impact. Standards such as ASTM for plastics should be considered.
Material | Typical Use Case for vending machine locations for sale | Key Advantage | Key Disadvantage/Limitation | Relative Cost (Low/Med/High) |
---|---|---|---|---|
Stainless Steel | External casing and components for food and beverage vending machines | Excellent corrosion resistance and durability | Higher cost and manufacturing complexity | High |
Mild Steel | Internal components where corrosion is minimal | Cost-effective and widely available | Susceptible to rust without protective coatings | Low |
Aluminum | Exteriors and lightweight components | Lightweight, reducing shipping costs | Lower strength compared to steel | Medium |
High-Density Polyethylene (HDPE) | Internal storage areas and components | Excellent chemical resistance and impact strength | Less aesthetic appeal and structural limitations | Medium |
In-depth Look: Manufacturing Processes and Quality Assurance for vending machine locations for sale
Understanding the Manufacturing Processes for Vending Machines
The production of vending machines involves several key stages, each crucial for ensuring the final product meets both performance and quality standards. For international B2B buyers, especially those from regions like Africa, South America, the Middle East, and Europe, understanding these processes can help in making informed purchasing decisions.
Main Stages of Manufacturing
- Material Preparation
– Sourcing Raw Materials: The manufacturing process begins with the procurement of high-quality raw materials such as steel for the casing, electronic components for the operating system, and plastics for the product dispensing areas. Buyers should ensure that suppliers have a reliable sourcing strategy that prioritizes sustainability and quality.
– Material Testing: Before production, raw materials undergo rigorous testing to ensure they meet specified standards. This includes checking for durability, corrosion resistance, and functionality.
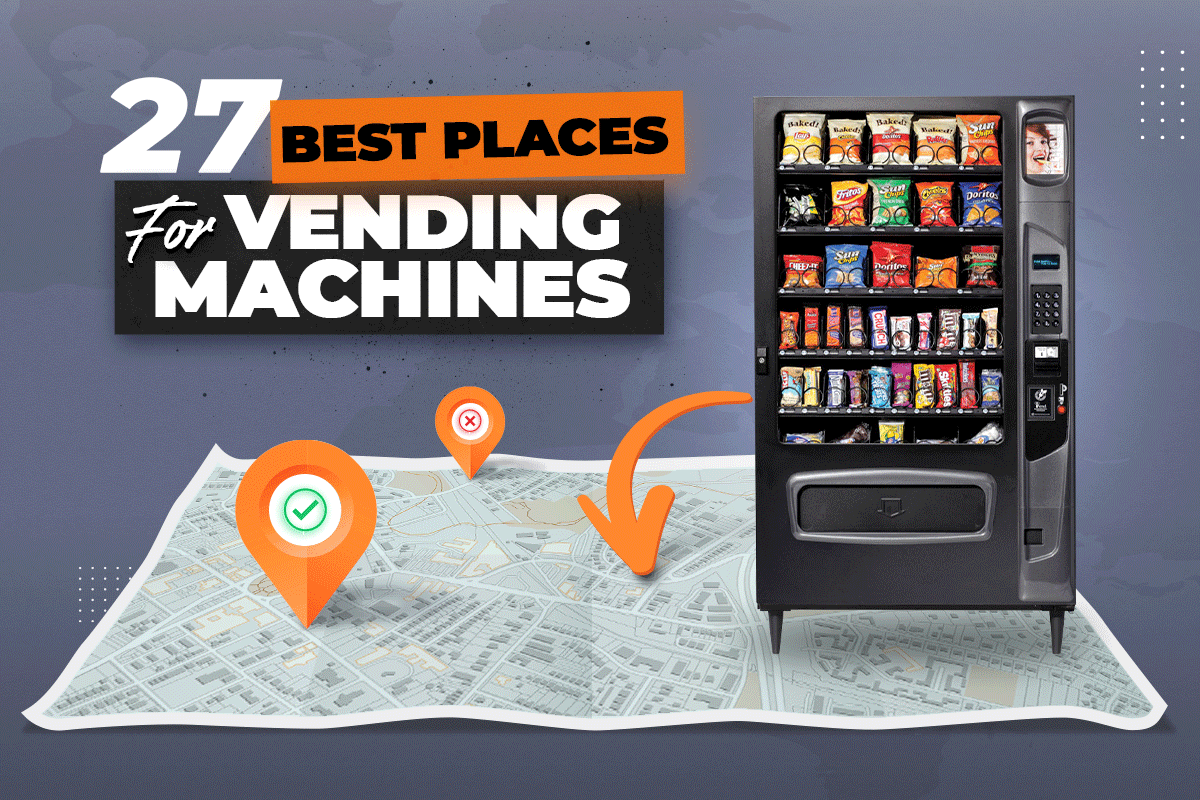
Illustrative Image (Source: Google Search)
-
Forming
– Cutting and Shaping: Using advanced technologies such as laser cutting and CNC machining, materials are shaped into the required components. Precision in this stage is vital to ensure parts fit together seamlessly during assembly.
– Metal Fabrication: Techniques like bending, welding, and stamping are employed to create the machine’s frame and structural components. Understanding the fabrication methods used can help buyers assess the durability and robustness of the final product. -
Assembly
– Component Integration: The assembly process involves integrating the electronic components, mechanisms for product delivery, and the outer casing. Automated assembly lines are often used to enhance efficiency and reduce human error.
– Quality Checks During Assembly: In-process quality control (IPQC) is critical at this stage. Inspections are performed to ensure that components are correctly installed and functioning as intended. -
Finishing
– Surface Treatment: After assembly, machines undergo finishing processes such as powder coating or painting to enhance aesthetics and protect against wear and corrosion. The choice of finish can affect the machine’s longevity and appeal to consumers.
– Final Assembly: This includes installing any additional features like payment systems, lighting, and digital displays. The final product is then cleaned and prepared for shipping.
Quality Assurance in Vending Machine Manufacturing
Quality assurance (QA) is an integral part of the manufacturing process, ensuring that the vending machines meet international standards and industry-specific regulations.
Relevant International Standards
- ISO 9001: This standard outlines the criteria for a quality management system (QMS). It is essential for suppliers to demonstrate compliance, as it indicates a commitment to quality and customer satisfaction.
- CE Marking: For products sold within the European Economic Area (EEA), CE marking signifies conformity with health, safety, and environmental protection standards. B2B buyers in Europe should prioritize suppliers with CE certification.
- API Standards: In regions where API standards are relevant, such as for certain electronic components, compliance can indicate a higher level of quality assurance.
Quality Control Checkpoints
-
Incoming Quality Control (IQC)
– Incoming materials are inspected upon arrival to ensure they meet specified quality standards. This step prevents defective materials from entering the production line. -
In-Process Quality Control (IPQC)
– Regular inspections are conducted throughout the assembly process. This includes testing functionalities, verifying component alignment, and ensuring safety features are operational. -
Final Quality Control (FQC)
– Before shipment, each vending machine undergoes a thorough inspection to check for overall functionality, safety compliance, and aesthetic quality. This is the last opportunity to catch defects before the product reaches the customer.
Common Testing Methods
- Functional Testing: Ensures that all electronic systems, including payment processing and product dispensing, work correctly.
- Durability Testing: Machines are subjected to stress tests to simulate long-term use, verifying their reliability in various environments.
- Safety Testing: This includes electrical safety tests to prevent hazards associated with faulty wiring or short circuits.
How B2B Buyers Can Verify Supplier Quality Control
To ensure that suppliers maintain high quality standards, B2B buyers should consider the following strategies:
- Supplier Audits: Conducting regular audits of the manufacturing facility can provide insights into the supplier’s processes, adherence to standards, and overall quality management practices.
- Requesting Quality Reports: Buyers should ask for detailed reports on quality control measures, including records of IQC, IPQC, and FQC processes.
- Third-Party Inspections: Engaging independent inspection agencies to evaluate the manufacturing processes can provide an unbiased assessment of the supplier’s quality management.
Quality Control and Certification Nuances for International Buyers
For B2B buyers in Africa, South America, the Middle East, and Europe, there are specific nuances to consider when evaluating suppliers:
- Cultural Differences: Understand the local manufacturing culture, as practices may vary significantly between regions. This includes attitudes towards quality and compliance.
- Regulatory Variances: Be aware of different regulatory requirements that might affect product certification and compliance in various countries. For instance, while CE marking is critical in Europe, other regions may have different compliance standards.
- Supply Chain Integrity: Investigate the entire supply chain, from raw material sourcing to final assembly. Ensuring that each link in the chain adheres to quality standards is crucial for the overall integrity of the product.
By understanding these manufacturing processes and quality assurance practices, international B2B buyers can make informed decisions when purchasing vending machines, ensuring they receive high-quality products that meet their specific needs.
Related Video: SMART Quality Control for Manufacturing
Comprehensive Cost and Pricing Analysis for vending machine locations for sale Sourcing
In the vending machine industry, understanding the comprehensive cost structure and pricing analysis for vending machine locations is crucial for international B2B buyers. This section outlines the key cost components, price influencers, and provides actionable tips for effective sourcing.
Cost Components
-
Materials: The initial investment in vending machine locations often includes the cost of the machines themselves, as well as any necessary fixtures or modifications to the site. High-quality materials can significantly affect the durability and functionality of the machines, impacting long-term operational costs.
-
Labor: Labor costs encompass installation, maintenance, and any necessary training for staff operating the machines. Depending on the region, labor rates can vary widely, influencing the total cost of ownership. Engaging local labor can often reduce costs but may require additional oversight and training.
-
Manufacturing Overhead: This includes indirect costs such as utilities, rent for production facilities, and administrative expenses. Buyers should inquire about the manufacturer’s overhead costs, as these can affect the final pricing of vending machine locations.
-
Tooling: Customization of vending machines may require specialized tools or molds, which can add to initial costs. Buyers should consider whether the customization aligns with their market needs and how it impacts the overall pricing structure.
-
Quality Control (QC): Ensuring the machines meet quality standards is vital for operational success. QC processes can add to upfront costs but are essential for minimizing long-term failures and maintenance issues.
-
Logistics: Shipping and handling costs are significant, especially for international transactions. Factors such as distance, shipping method, and urgency can dramatically alter logistics costs. Understanding Incoterms is essential to clarify who bears these costs.
-
Margin: Suppliers typically include a profit margin in their pricing. Understanding typical margins within the vending machine market can help buyers negotiate better deals.
Price Influencers
Several factors influence pricing for vending machine locations:
-
Volume/MOQ: Bulk purchases often lead to lower per-unit costs. Buyers should assess their capacity to invest upfront for long-term savings.
-
Specifications/Customization: Custom features can increase costs. Buyers should determine if the added value justifies the additional expense.
-
Material Quality/Certifications: Higher-quality materials and certifications (e.g., ISO) often correlate with increased pricing but can lead to enhanced performance and reliability.
-
Supplier Factors: The reputation and reliability of the supplier can influence pricing. Established suppliers may charge more but often provide better warranties and support.
-
Incoterms: Understanding shipping terms (e.g., FOB, CIF) can significantly affect total costs. Buyers should clarify terms to avoid unexpected expenses.
Buyer Tips
-
Negotiation: Always negotiate pricing. Suppliers may have flexibility based on order size or payment terms. Leverage your position as a buyer to seek discounts or better terms.
-
Cost-Efficiency: Evaluate the Total Cost of Ownership (TCO), which includes purchase price, maintenance, operation, and potential downtime. A lower initial cost may not always translate to overall savings.
-
Pricing Nuances for International Buyers: Buyers from Africa, South America, the Middle East, and Europe should be aware of currency fluctuations and import taxes that can impact costs. Researching local regulations and potential tariffs is essential.
-
Disclaimer for Indicative Prices: Keep in mind that prices can vary significantly based on market conditions, regional economic factors, and supplier relationships. Always seek updated quotes before making purchasing decisions.
By understanding these components and influencers, international B2B buyers can make informed decisions when sourcing vending machine locations, ensuring a successful investment that aligns with their business objectives.
Spotlight on Potential vending machine locations for sale Manufacturers and Suppliers
- (No specific manufacturer data was available or requested for detailed profiling in this section for vending machine locations for sale.)*
Essential Technical Properties and Trade Terminology for vending machine locations for sale
Key Technical Properties of Vending Machine Locations
When evaluating vending machine locations for sale, understanding essential technical properties is crucial for making informed purchasing decisions. Here are several critical specifications to consider:
-
Foot Traffic Volume
The number of potential customers passing by a location is fundamental. High foot traffic often correlates with increased sales opportunities. For B2B buyers, assessing foot traffic through surveys or local demographic studies can provide insights into the viability of a vending machine site. -
Visibility and Accessibility
A location’s visibility can significantly impact sales. Machines placed in easily accessible areas, such as near entrances or common areas, tend to attract more customers. B2B buyers should evaluate the layout of the location to ensure the machine is prominently displayed and easy to reach. -
Electrical Supply and Connectivity
Vending machines require a reliable power source. Understanding the electrical specifications—such as voltage requirements and outlet availability—is critical. Additionally, for smart vending machines that utilize IoT technology, access to Wi-Fi or cellular data may be necessary. Buyers should confirm these technical details with the property owner. -
Space Dimensions and Compliance
Each vending machine has specific space requirements. Buyers must ensure that the location can accommodate the machine’s dimensions while adhering to local regulations regarding spacing and safety. This compliance is essential to avoid fines and ensure a smooth installation process. -
Surrounding Amenities
The presence of complementary businesses or amenities can enhance the attractiveness of a vending machine location. For instance, vending machines near cafes, gyms, or schools may benefit from increased customer traffic. B2B buyers should analyze the surrounding environment and potential customer demographics. -
Security Features
Security is paramount for vending machine operations. Buyers should assess the safety of the location, including lighting, surveillance systems, and the presence of security personnel. A secure environment reduces the risk of theft and vandalism, ensuring a stable revenue stream.
Common Trade Terminology
Understanding industry terminology is essential for effective communication and negotiation in the vending machine market. Here are some common terms that B2B buyers should be familiar with:
-
OEM (Original Equipment Manufacturer)
This term refers to a company that produces parts or equipment that may be marketed by another manufacturer. In the context of vending machines, knowing the OEM can help buyers assess quality and reliability. -
MOQ (Minimum Order Quantity)
MOQ indicates the smallest quantity of a product that a supplier is willing to sell. This term is crucial for B2B buyers as it affects inventory management and cost efficiency. Buyers should negotiate MOQs to align with their business needs and budget constraints. -
RFQ (Request for Quotation)
An RFQ is a formal document requesting pricing and terms from suppliers. B2B buyers should prepare detailed RFQs to ensure they receive accurate and competitive quotes, facilitating better decision-making. -
Incoterms (International Commercial Terms)
These are internationally recognized rules that define the responsibilities of buyers and sellers in shipping goods. Familiarity with Incoterms can help B2B buyers understand shipping costs, risks, and obligations, aiding in smoother international transactions. -
Lead Time
Lead time refers to the time taken from placing an order to its delivery. Understanding lead times is essential for B2B buyers to manage inventory effectively and plan for machine installation and operational readiness. -
Site Analysis
This term encompasses the evaluation of a location’s potential based on factors such as demographics, competition, and environmental conditions. Conducting a thorough site analysis is vital for buyers to make informed decisions about vending machine placements.
By grasping these technical properties and trade terms, B2B buyers can enhance their decision-making processes, ensuring they select the most profitable vending machine locations for their businesses.
Navigating Market Dynamics, Sourcing Trends, and Sustainability in the vending machine locations for sale Sector
Market Overview & Key Trends
The vending machine locations for sale sector is experiencing notable growth driven by several global dynamics. Increasing urbanization, particularly in Africa and South America, is resulting in higher demand for convenient food and beverage options. Additionally, the rise of health-conscious consumers is pushing operators to seek vending solutions that offer healthier alternatives. As a B2B buyer, understanding these trends is crucial for making informed decisions.
Emerging technologies are also reshaping the landscape. Contactless payment systems, smart vending machines with IoT capabilities, and data analytics for consumer behavior are becoming standard. These innovations not only enhance customer experience but also allow for better inventory management and operational efficiency. International buyers should prioritize suppliers that leverage these technologies to stay competitive.
Moreover, the market dynamics reflect a shift towards strategic partnerships. For instance, collaboration between vending operators and local businesses can improve location viability and product offerings. Buyers from Europe and the Middle East should focus on sourcing from vendors who demonstrate flexibility and adaptability to local market conditions, ensuring sustainable growth.
Sustainability & Ethical Sourcing in B2B
Sustainability has become a focal point in the vending machine sector, driven by increasing consumer awareness and regulatory pressures. The environmental impact of vending machines, from energy consumption to waste generation, is significant. International B2B buyers are encouraged to seek out vendors that prioritize energy-efficient machines and sustainable practices.
Ethical sourcing is equally important. Buyers should assess the supply chains of potential partners to ensure they adhere to fair labor practices and environmental standards. Certifications such as ISO 14001 (Environmental Management) and Fair Trade can serve as indicators of a supplier’s commitment to sustainability.
Furthermore, consider the materials used in vending machines and their components. Opting for recyclable or biodegradable materials not only aligns with sustainability goals but also appeals to a growing segment of eco-conscious consumers. By prioritizing these factors, B2B buyers can enhance their brand reputation while contributing positively to the environment.
Brief Evolution/History
The vending machine industry has evolved significantly since its inception in the late 19th century. Initially focused on simple products like postcards and gum, the sector has expanded to include a wide variety of food and beverage options. The introduction of electronic payment systems in the 1980s marked a pivotal shift, allowing for greater convenience and a broader customer base.
In recent years, the focus has shifted towards technology integration and sustainability. The rise of smart vending machines equipped with touchscreens and remote monitoring capabilities reflects changing consumer expectations. As international markets continue to evolve, understanding this historical context can help B2B buyers make strategic sourcing decisions that align with current and future trends.
Related Video: Incoterms for beginners | Global Trade Explained
Frequently Asked Questions (FAQs) for B2B Buyers of vending machine locations for sale
-
What should I consider when vetting suppliers for vending machine locations?
When vetting suppliers, prioritize their experience in the vending machine industry and their track record with international buyers. Check for references and reviews from other B2B clients, focusing on their reliability and responsiveness. Additionally, assess their compliance with local regulations and certifications, as this can impact your operations. Lastly, ensure they provide clear documentation regarding their locations, including lease agreements and site performance metrics. -
Can vending machine locations be customized to fit my business needs?
Yes, many suppliers offer customization options for vending machine locations. This may include the selection of products to be sold, the machine’s branding, and even specific operational hours. Communicate your requirements early in the negotiation process to ensure the supplier can accommodate them. Understanding local consumer preferences can also guide your customization efforts, making the locations more appealing to potential customers. -
What are typical minimum order quantities (MOQ) and lead times for vending machine locations?
MOQs for vending machine locations can vary significantly based on the supplier and the region. Generally, suppliers may require a commitment to a certain number of machines or locations to ensure profitability. Lead times can range from a few weeks to several months, depending on the complexity of the agreement and the customization required. Always discuss these factors upfront to avoid delays in your operations. -
How do I handle payment terms with international suppliers?
Payment terms can differ widely between suppliers, so it’s crucial to negotiate terms that safeguard your investment. Common arrangements include upfront deposits with the balance due upon delivery or after installation. Consider using secure payment methods, such as letters of credit or escrow services, especially for large transactions. Ensure that all payment terms are clearly outlined in the contract to mitigate any potential disputes. -
What quality assurance measures should I expect from suppliers?
Reputable suppliers should have established quality assurance (QA) protocols to ensure their vending machine locations meet specified standards. Inquire about their QA process, including inspections, testing, and certifications. Request documentation that verifies compliance with local health and safety regulations, as this will impact your ability to operate legally. Regular audits and performance reviews can further ensure sustained quality over time. -
What logistics considerations should I be aware of when sourcing vending machine locations?
Logistics can be complex when dealing with international suppliers. Key considerations include transportation costs, customs clearance, and the potential need for local partnerships to facilitate installation. Ensure that the supplier provides a clear logistics plan, including timelines and responsibilities. Be aware of local infrastructure challenges that may affect delivery and installation, particularly in remote areas. -
How can disputes with suppliers be effectively managed?
To manage disputes effectively, establish clear communication channels from the outset. Include a dispute resolution clause in your contract that outlines the steps to take in case of disagreements. Consider alternative dispute resolution methods, such as mediation or arbitration, as they can be more efficient than litigation. Keeping detailed records of all transactions and communications can also be invaluable should a dispute arise. -
What certifications should I look for in vending machine locations?
When considering vending machine locations, look for certifications that demonstrate compliance with local laws and industry standards. Key certifications may include health and safety compliance, product safety standards, and environmental regulations. Additionally, some suppliers may have industry-specific certifications that indicate a commitment to quality and sustainability. Verifying these certifications can help ensure that you are partnering with a reputable supplier, reducing the risk of operational issues down the line.
Strategic Sourcing Conclusion and Outlook for vending machine locations for sale
In conclusion, strategic sourcing for vending machine locations is pivotal for international B2B buyers aiming to enhance their market presence and optimize their operational efficiencies. By focusing on high-traffic areas such as office complexes, shopping centers, and transportation hubs, businesses can maximize revenue potential. Understanding local consumer preferences and regulatory environments is crucial, especially when navigating diverse markets across Africa, South America, the Middle East, and Europe.
Key Takeaways:
– Market Research: Conduct thorough research to identify optimal locations that align with target demographics.
– Partnerships: Build relationships with property managers and local businesses to secure advantageous agreements.
– Adaptability: Remain flexible to adapt offerings based on regional consumer trends and technological advancements.
As the vending machine market continues to evolve, leveraging data analytics and consumer insights will be essential for sustained growth. B2B buyers should actively seek opportunities to innovate and differentiate their offerings. The future of vending machine locations is bright, and proactive engagement today will set the stage for success tomorrow. Embrace strategic sourcing as a vital tool in your business arsenal to secure lucrative locations and foster long-term partnerships.