Your Ultimate Guide to Sourcing Wittern Group Vending
Guide to Wittern Group Vending Machines
- Introduction: Navigating the Global Market for wittern group vending machines
- Understanding wittern group vending machines Types and Variations
- Key Industrial Applications of wittern group vending machines
- Strategic Material Selection Guide for wittern group vending machines
- In-depth Look: Manufacturing Processes and Quality Assurance for wittern group vending machines
- Comprehensive Cost and Pricing Analysis for wittern group vending machines Sourcing
- Spotlight on Potential wittern group vending machines Manufacturers and Suppliers
- Essential Technical Properties and Trade Terminology for wittern group vending machines
- Navigating Market Dynamics, Sourcing Trends, and Sustainability in the wittern group vending machines Sector
- Market Overview & Key Trends
- Sustainability & Ethical Sourcing in B2B
- Brief Evolution/History
- Frequently Asked Questions (FAQs) for B2B Buyers of wittern group vending machines
- Strategic Sourcing Conclusion and Outlook for wittern group vending machines
Introduction: Navigating the Global Market for wittern group vending machines
In today’s fast-paced global economy, Wittern Group vending machines stand out as a pivotal solution for businesses aiming to enhance their service offerings and improve customer satisfaction. These machines are not just about convenience; they represent a strategic investment in automation and customer engagement, providing access to a wide range of products in various settings—from corporate offices to educational institutions and public spaces. For international B2B buyers, particularly those from Africa, South America, the Middle East, and Europe, understanding the nuances of Wittern Group vending machines is essential for making informed purchasing decisions.
This comprehensive guide delves into critical aspects of Wittern Group vending machines, including the different types available, the materials used in their construction, manufacturing and quality control processes, reputable suppliers, and cost considerations. Each section is designed to equip buyers with the knowledge they need to navigate the complexities of the vending machine market effectively.
By offering insights into market trends and frequently asked questions, this guide empowers buyers to identify the best solutions tailored to their unique operational needs. As international markets continue to evolve, leveraging the right vending machine technology can significantly enhance operational efficiency and customer experience, making this guide an invaluable resource for savvy business leaders.
Understanding wittern group vending machines Types and Variations
Type Name | Key Distinguishing Features | Primary B2B Applications | Brief Pros & Cons for Buyers |
---|---|---|---|
Snack Vending Machines | Compact design, customizable product selection | Offices, schools, gyms | Pros: Easy to stock, low maintenance. Cons: Limited to dry goods. |
Beverage Vending Machines | Refrigerated compartments for drinks | Cafes, hotels, corporate events | Pros: High demand for drinks. Cons: Higher energy costs. |
Combo Vending Machines | Dual functionality for snacks and beverages | Convenience stores, airports | Pros: Versatile product offering. Cons: Requires more space. |
Healthy Food Vending Machines | Focus on nutritious options, fresh items | Hospitals, universities, gyms | Pros: Appeals to health-conscious consumers. Cons: Higher spoilage risk. |
Specialty Vending Machines | Niche products (e.g., electronics, cosmetics) | Airports, malls, high-traffic areas | Pros: Unique offerings can drive sales. Cons: Higher initial investment. |
Snack Vending Machines
Snack vending machines are designed for compact placement and typically offer a variety of dry snacks. Their customizable nature allows businesses to tailor selections to target demographics, making them ideal for locations like offices, schools, and gyms. When considering a purchase, buyers should evaluate the machine’s capacity, ease of restocking, and maintenance requirements, as well as the popularity of the snack options in their area.
Beverage Vending Machines
These machines are specifically engineered with refrigerated compartments to keep drinks cold, catering to a high-demand market. They find applications in cafes, hotels, and corporate events where quick access to beverages is crucial. Buyers should consider the energy consumption of these machines, as well as the need for regular maintenance to ensure optimal cooling performance and product freshness.
Combo Vending Machines
Combo vending machines offer the flexibility of stocking both snacks and beverages, making them suitable for convenience stores and airports where diverse consumer needs must be met. Their versatility is a significant advantage, but buyers should be mindful of the space requirements and potential complexity in managing inventory across different product types. The ability to cater to a wider audience can enhance sales potential.
Healthy Food Vending Machines
With an increasing focus on health and wellness, these machines provide nutritious food options, such as salads and wraps, targeting health-conscious consumers. They are particularly effective in settings like hospitals, universities, and gyms. However, buyers must consider the higher risk of spoilage associated with fresh items and ensure regular restocking to maintain product quality and appeal.
Specialty Vending Machines
Specialty vending machines cater to niche markets by offering unique products, such as electronics or cosmetics. These machines are often found in high-traffic areas like airports and malls, where consumers are looking for convenience and novelty. While they can drive significant sales through unique offerings, buyers should weigh the higher initial investment and the need for targeted marketing strategies to attract customers effectively.
Key Industrial Applications of wittern group vending machines
Industry/Sector | Specific Application of Wittern Group Vending Machines | Value/Benefit for the Business | Key Sourcing Considerations for this Application |
---|---|---|---|
Healthcare | Medication dispensing in hospitals | Improved patient adherence, reduced pharmacy workload | Compliance with health regulations, secure payment options |
Education | Snack and beverage vending in schools | Enhanced student satisfaction, increased revenue | Durability, ease of use, and payment flexibility |
Corporate Offices | Refreshment stations in break rooms | Increased employee morale, productivity boost | Customization options, reliable supply chain management |
Manufacturing | Parts and tool vending for production lines | Streamlined inventory management, reduced downtime | Inventory tracking capabilities, robust security features |
Retail | Automated kiosks for product sales | Expanded sales channels, reduced labor costs | Integration with existing systems, payment processing options |
Healthcare Applications
In the healthcare sector, Wittern Group vending machines can be utilized for medication dispensing in hospitals. These machines facilitate the distribution of medications, ensuring that patients have access to their prescribed treatments at all times. By automating the dispensing process, hospitals can improve patient adherence to medication regimens while significantly reducing the workload on pharmacy staff. International buyers must consider compliance with local health regulations and the need for secure payment options, especially in regions with stringent healthcare standards.
Educational Sector Solutions
In educational institutions, Wittern Group vending machines serve as snack and beverage dispensers, enhancing student satisfaction and providing a source of revenue for schools. By offering a variety of healthy options, schools can promote better eating habits among students. For international buyers, it’s crucial to ensure that machines are durable and user-friendly, catering to diverse student populations while providing flexible payment methods to accommodate different financial systems.
Corporate Office Enhancements
Wittern Group vending machines can transform corporate break rooms into refreshment stations that boost employee morale and productivity. These machines can offer a range of snacks and beverages tailored to employee preferences, creating a more enjoyable workplace. When sourcing these machines, businesses should focus on customization options and the reliability of supply chain management to ensure consistent product availability.
Manufacturing Efficiency
In the manufacturing sector, Wittern Group vending machines can be employed to dispense parts and tools directly on production lines. This application streamlines inventory management, reduces downtime, and enhances operational efficiency by ensuring that workers have immediate access to the tools they need. International buyers should prioritize machines with robust security features and advanced inventory tracking capabilities to prevent loss and optimize resource allocation.
Retail Opportunities
Wittern Group vending machines can also serve as automated kiosks in retail settings, allowing businesses to expand their sales channels without the need for additional staff. This solution can significantly reduce labor costs while providing customers with a convenient shopping experience. When considering these machines, it is essential for buyers to ensure seamless integration with existing systems and reliable payment processing options to facilitate smooth transactions.
Related Video: Fawn Manufacturing – The Wittern Group
Strategic Material Selection Guide for wittern group vending machines
When selecting materials for Wittern Group vending machines, international B2B buyers must consider a variety of factors that impact product performance, durability, and compliance with regional standards. Below is an analysis of four common materials used in vending machine construction, focusing on their properties, advantages, disadvantages, and specific considerations for buyers from Africa, South America, the Middle East, and Europe.
1. Stainless Steel
Key Properties: Stainless steel is known for its excellent corrosion resistance and high strength-to-weight ratio. It can withstand a wide range of temperatures and pressures, making it suitable for various environments.
Pros & Cons: The primary advantage of stainless steel is its durability and resistance to rust and staining, which is crucial for vending machines exposed to moisture. However, it is generally more expensive than other materials and can be challenging to manufacture due to its hardness.
Impact on Application: Stainless steel is particularly compatible with food and beverage applications, ensuring hygiene and safety. It is also easy to clean, which is an essential factor for machines that dispense consumables.
Specific Considerations: Buyers should ensure compliance with food safety standards, such as those set by the FDA or EU regulations. Additionally, understanding the grades of stainless steel (e.g., 304 vs. 316) can help in selecting the right material for specific environments, especially in coastal regions where saltwater corrosion is a concern.
2. Carbon Steel
Key Properties: Carbon steel offers good strength and toughness, making it suitable for structural components of vending machines. It has a lower temperature and pressure rating compared to stainless steel but is adequate for many applications.
Pros & Cons: The main advantage of carbon steel is its cost-effectiveness, making it an attractive option for manufacturers. However, it is prone to corrosion and requires protective coatings or treatments to enhance its durability.
Impact on Application: Carbon steel is best suited for non-corrosive environments or where protective measures can be implemented. It is less ideal for applications involving food and beverages unless adequately protected.
Specific Considerations: Buyers in regions with high humidity or corrosive environments should carefully evaluate the use of carbon steel and consider compliance with local standards regarding protective coatings. Familiarity with standards such as ASTM A36 can be beneficial.
3. Aluminum
Key Properties: Aluminum is lightweight and has good corrosion resistance, making it suitable for various components in vending machines. It has a lower strength compared to steel but compensates with its ease of fabrication.
Pros & Cons: The primary advantage of aluminum is its lightweight nature, which reduces shipping costs and makes installation easier. However, it is less durable than steel and can be more susceptible to dents and deformation.
Impact on Application: Aluminum is often used for decorative panels and internal components where weight savings are critical. Its corrosion resistance makes it suitable for environments with high moisture levels.
Specific Considerations: Buyers should be aware of the specific grades of aluminum (e.g., 6061 vs. 5052) and their respective properties. Compliance with standards like JIS H 4000 can help ensure quality and performance.
4. Plastic Composites
Key Properties: Plastic composites are engineered materials that combine plastic with other materials to enhance strength and durability. They are generally lightweight and resistant to corrosion and chemicals.
Pros & Cons: The key advantage of plastic composites is their versatility and lower manufacturing costs compared to metals. However, they may not provide the same structural integrity as metals and can be less suitable for high-stress applications.
Impact on Application: These materials are often used for components that require insulation or where weight is a critical factor. They can be tailored for specific media compatibility, making them suitable for various vending machine applications.
Specific Considerations: Buyers should evaluate the specific type of plastic composite and ensure it meets relevant standards for safety and performance. Understanding local regulations regarding plastic materials is also essential.
Summary Table
Material | Typical Use Case for Wittern Group Vending Machines | Key Advantage | Key Disadvantage/Limitation | Relative Cost (Low/Med/High) |
---|---|---|---|---|
Stainless Steel | Structural and exterior components | Excellent corrosion resistance | Higher cost, manufacturing complexity | High |
Carbon Steel | Structural components for non-corrosive applications | Cost-effective, good strength | Prone to corrosion without protection | Low |
Aluminum | Decorative panels and lightweight components | Lightweight, easy to fabricate | Less durable, susceptible to dents | Medium |
Plastic Composites | Insulation and non-structural components | Versatile, lower manufacturing cost | Less structural integrity | Low |
This guide provides a comprehensive overview of materials commonly used in Wittern Group vending machines, offering actionable insights for international B2B buyers to make informed decisions based on their specific needs and regional standards.
In-depth Look: Manufacturing Processes and Quality Assurance for wittern group vending machines
The manufacturing process of Witten Group vending machines is a complex and precise operation that ensures high-quality products for B2B buyers. Understanding this process, along with the quality assurance measures in place, is crucial for international buyers looking to invest in vending machines, especially in diverse markets like Africa, South America, the Middle East, and Europe.
Manufacturing Process
1. Material Preparation
The first stage of the manufacturing process involves the careful selection and preparation of materials. Witten Group utilizes high-grade steel, durable plastics, and electronic components sourced from reliable suppliers. The materials undergo rigorous inspections to ensure they meet the required specifications before moving to the next stage. This step is vital as it lays the foundation for the machine’s durability and functionality.
2. Forming
In this phase, raw materials are shaped into parts using various techniques such as stamping, bending, and machining. Advanced CNC (Computer Numerical Control) machines are often employed to achieve high precision and consistency. The forming process is critical as it dictates the overall design and functionality of the vending machines.
3. Assembly
Once the components are formed, the assembly process begins. This is typically done in a clean and controlled environment to minimize contamination and defects. Skilled workers or automated systems assemble the parts, integrating mechanical, electronic, and software components. Each assembly line is designed to optimize efficiency while maintaining high standards of quality.
4. Finishing
The finishing stage includes painting, coating, and surface treatment to enhance the aesthetic appeal and protect against corrosion. Quality control checks are performed at this stage to ensure that the finishing meets both aesthetic and functional requirements. This step is particularly important for vending machines that will be exposed to various environmental conditions.
Quality Assurance
Quality assurance is a cornerstone of Witten Group’s manufacturing philosophy. The company adheres to international standards such as ISO 9001, which emphasizes a process-oriented approach to quality management. This certification is essential for B2B buyers as it indicates a commitment to continuous improvement and customer satisfaction.
Relevant International Standards
- ISO 9001: Focuses on quality management systems and processes.
- CE Marking: Ensures compliance with health, safety, and environmental protection standards within the European Economic Area.
- API Standards: Relevant for machines used in specific industries, ensuring they meet the necessary operational criteria.
Quality Control Checkpoints
Quality control is integrated throughout the manufacturing process, with multiple checkpoints designed to catch defects early:
- Incoming Quality Control (IQC): Inspects raw materials upon arrival to ensure they meet specifications.
- In-Process Quality Control (IPQC): Monitors the manufacturing process to ensure compliance with standards during production.
- Final Quality Control (FQC): Conducts thorough inspections and testing on finished products before they are shipped.
Common Testing Methods
Witten Group employs various testing methods to ensure the machines function as intended:
– Functional Testing: Ensures all mechanical and electronic components work correctly.
– Durability Testing: Simulates long-term use to identify potential failures.
– Safety Testing: Confirms that machines comply with safety regulations and standards.
Verifying Supplier Quality Control
For B2B buyers, especially those from regions such as Africa, South America, the Middle East, and Europe, verifying a supplier’s quality control processes is crucial. Here are several strategies to ensure the integrity of the manufacturing process:
-
Supplier Audits: Conduct on-site audits to assess the manufacturing facilities and quality control practices. This provides firsthand insight into the supplier’s operations.
-
Quality Assurance Reports: Request detailed quality assurance documentation, including inspection reports and compliance certificates. This documentation should outline the processes followed and any issues encountered during production.
-
Third-Party Inspections: Engage independent inspection agencies to evaluate the manufacturing process and product quality. These inspections can provide an unbiased assessment of the supplier’s capabilities.
QC and Certification Nuances for International Buyers
International buyers must be aware of the specific certifications and quality standards that may vary by region. For instance, while CE marking is vital for European markets, compliance with local regulations may be more significant in African or South American countries. Understanding these nuances can help buyers make informed decisions and ensure that they are purchasing compliant and reliable vending machines.
Moreover, international buyers should consider the logistical implications of quality assurance. For example, shipping products from manufacturers in different regions can introduce risks related to damage or non-compliance with local standards. Therefore, establishing strong communication channels with suppliers and understanding their quality assurance measures is essential for mitigating these risks.
Conclusion
The manufacturing processes and quality assurance measures employed by Witten Group are designed to produce high-quality vending machines that meet the diverse needs of international B2B buyers. By understanding these processes and actively engaging in quality verification, buyers can ensure they are making sound investments in reliable vending solutions.
Related Video: Most Satisfying Factory Production Processes And Heavy-Duty Factory Machines!
Comprehensive Cost and Pricing Analysis for wittern group vending machines Sourcing
In sourcing Wittern Group vending machines, understanding the comprehensive cost structure and pricing factors is crucial for international B2B buyers, especially from regions like Africa, South America, the Middle East, and Europe. This analysis will provide actionable insights into the cost components, price influencers, and strategic tips for effective negotiation.
Cost Components
-
Materials: The primary costs in vending machines come from the materials used. High-quality metals, plastics, and electronic components are essential for durability and functionality. Prices can fluctuate based on global commodity markets, so buyers should consider sourcing strategies that mitigate these risks.
-
Labor: Labor costs vary significantly based on the manufacturing location. For instance, labor in Southeast Asia may be cheaper than in Europe or North America. Understanding local labor rates can help buyers assess the total cost.
-
Manufacturing Overhead: This includes costs related to utilities, rent, and administrative expenses associated with production. It’s important to inquire about the supplier’s overhead to better understand how it impacts the overall pricing.
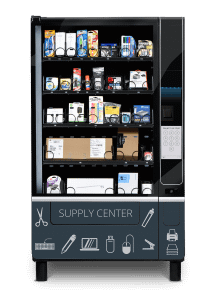
Illustrative Image (Source: Google Search)
-
Tooling: Initial tooling costs for custom designs can be substantial. Buyers should evaluate whether to invest in tooling for specific configurations, especially when large order quantities justify this cost.
-
Quality Control (QC): Ensuring product quality through rigorous QC processes can add to the cost but is essential for maintaining operational reliability. Buyers should ask about the QC measures in place and any associated costs.
-
Logistics: Shipping and handling fees can vary widely depending on the destination. Factors like distance, shipping method, and customs duties all influence logistics costs, which can be significant for international buyers.
-
Margin: Suppliers will typically include a profit margin in their pricing, which can vary based on market demand and competition. Understanding typical margins in the vending machine industry can aid in negotiation.
Price Influencers
-
Volume/MOQ (Minimum Order Quantity): Ordering in bulk can often reduce the per-unit cost. Buyers should assess their demand forecasts to negotiate better terms based on volume.
-
Specifications/Customization: Customized machines may incur higher costs due to specialized materials or design. Buyers should balance their need for customization with budget constraints.
-
Materials: The choice of materials directly affects the machine’s durability and price. Buyers should consider the long-term benefits of investing in higher-quality materials versus short-term savings.
-
Quality/Certifications: Machines that comply with international safety and quality standards may come at a premium. Buyers should weigh the benefits of certified products against their budget.
-
Supplier Factors: Established suppliers may offer better reliability and support but could charge higher prices. Newer suppliers may offer competitive pricing but with potential risks in service and quality.
-
Incoterms: Understanding the Incoterms agreed upon can significantly impact total costs. Terms like FOB (Free on Board) or CIF (Cost, Insurance, and Freight) will dictate who is responsible for shipping costs and risks.
Buyer Tips
-
Negotiation: Establish a clear understanding of the total cost breakdown and be prepared to negotiate on each component. Leverage volume commitments to secure better pricing.
-
Cost-Efficiency: Assess the Total Cost of Ownership (TCO), which includes not just the purchase price but also maintenance, energy consumption, and potential downtime costs.
-
Pricing Nuances: International buyers must be aware of currency fluctuations and their impact on pricing. Consider negotiating fixed prices in a stable currency to avoid unexpected costs.
-
Research Local Market Conditions: Understanding regional demand and competition can provide leverage in negotiations. Price sensitivity can vary greatly between markets, influencing how much wiggle room you have.
Disclaimer
Prices and costs mentioned are indicative and subject to change based on market conditions, supplier negotiations, and specific buyer requirements. Always conduct thorough due diligence and obtain multiple quotes to ensure competitive pricing.
Spotlight on Potential wittern group vending machines Manufacturers and Suppliers
This section offers a look at a few manufacturers active in the ‘wittern group vending machines’ market. This is a representative sample for illustrative purposes; B2B buyers must conduct their own extensive due diligence before any engagement. Information is synthesized from public sources and general industry knowledge.
Essential Technical Properties and Trade Terminology for wittern group vending machines
Key Technical Properties of Wittern Group Vending Machines
Understanding the technical specifications of Wittern Group vending machines is crucial for international B2B buyers. Here are some essential properties to consider:
-
Material Grade
Wittern vending machines are typically constructed from high-quality stainless steel or durable plastics. Stainless steel offers superior resistance to corrosion and wear, ensuring longevity and minimal maintenance. Selecting the right material is vital for buyers operating in diverse climates, as it impacts the machine’s durability and overall lifespan. -
Dimensions and Capacity
The dimensions of vending machines, including height, width, and depth, directly affect where they can be installed. Capacity refers to how many items the machine can hold, which is critical for maximizing revenue potential. Buyers must assess their location’s space and consumer demand to choose the appropriate size and capacity. -
Power Requirements
Understanding the power specifications, including voltage and amperage, is essential for proper installation. Wittern machines may require specific electrical setups to operate efficiently. Buyers should ensure that their facilities can accommodate these requirements to avoid operational disruptions. -
Temperature Control Systems
Many Wittern vending machines are equipped with advanced refrigeration systems for perishable items. Buyers should consider the temperature range and efficiency of these systems, particularly in regions with extreme temperatures, to maintain product quality and safety. -
User Interface Technology
Modern Wittern vending machines feature touch screens and cashless payment options, enhancing user experience. Understanding the technology behind these interfaces is important for ensuring customer satisfaction and operational efficiency. Buyers should evaluate whether the machines support local payment methods popular in their regions. -
Service and Maintenance Requirements
Each vending machine comes with specific maintenance needs, including how often to restock, clean, and service the machines. Buyers should inquire about the recommended maintenance schedule to ensure the machines remain functional and profitable over time.
Common Trade Terminology
Familiarity with industry jargon can significantly streamline the purchasing process. Here are some key terms related to Wittern Group vending machines:
-
OEM (Original Equipment Manufacturer)
This term refers to companies that produce parts and equipment that may be marketed by another manufacturer. Understanding OEM relationships can help buyers identify authentic parts and maintenance services, ensuring the longevity of their vending machines. -
MOQ (Minimum Order Quantity)
MOQ indicates the smallest number of units that a supplier is willing to sell. Knowing the MOQ is essential for buyers to manage inventory costs effectively and avoid overstocking or understocking. -
RFQ (Request for Quotation)
An RFQ is a document sent to suppliers requesting pricing information for specific products or services. For B2B buyers, issuing an RFQ helps compare prices and terms from multiple suppliers, facilitating informed purchasing decisions. -
Incoterms (International Commercial Terms)
These are standardized terms that define the responsibilities of buyers and sellers in international transactions. Familiarity with Incoterms such as FOB (Free on Board) or CIF (Cost, Insurance, and Freight) is crucial for understanding shipping costs and responsibilities. -
Lead Time
This term refers to the time between placing an order and receiving the product. Understanding lead times helps buyers plan their procurement process and manage inventory effectively. -
Warranty
A warranty is a guarantee from the manufacturer regarding the condition of the product. Knowing the warranty terms for Wittern vending machines helps buyers assess the risk of investment and potential costs associated with repairs or replacements.
By grasping these technical properties and trade terms, B2B buyers can make informed decisions, ensuring that their investment in Wittern Group vending machines aligns with their operational needs and market demands.
Navigating Market Dynamics, Sourcing Trends, and Sustainability in the wittern group vending machines Sector
Market Overview & Key Trends
The Wittern Group vending machines sector is currently experiencing significant shifts driven by technological advancements and changing consumer preferences. Global drivers such as urbanization, increased demand for convenience, and evolving workplace dynamics are propelling the vending industry forward. In regions like Africa and South America, the rise of the middle class and urban population growth are opening new markets for vending solutions. In contrast, the Middle East and Europe are seeing a shift towards healthier options and premium products in vending machines, influenced by consumer health consciousness and regulatory changes.
Current and emerging B2B tech trends include the integration of smart technology in vending machines, such as cashless payment systems, IoT connectivity, and real-time inventory management. These innovations enhance operational efficiency and customer experience, making it crucial for international buyers to consider these features when sourcing equipment. Furthermore, sustainability is becoming a significant factor in purchasing decisions, with buyers increasingly looking for machines that align with eco-friendly practices.
Market dynamics for international B2B buyers are characterized by a competitive landscape where established brands are challenged by new entrants offering innovative solutions. Buyers should be aware of the regional preferences that influence product selection. For instance, in Europe, there is a strong demand for machines that offer locally sourced products, while in Africa, cost-effectiveness and durability are key considerations. Understanding these dynamics is essential for making informed sourcing decisions that align with market demands.
Sustainability & Ethical Sourcing in B2B
Sustainability and ethical sourcing are becoming pivotal in the Wittern Group vending machines sector. The environmental impact of manufacturing and operating vending machines is significant, leading to increased scrutiny from consumers and regulatory bodies. As a result, companies are focusing on reducing their carbon footprint through energy-efficient designs and materials.
The importance of ethical supply chains cannot be overstated. Buyers are encouraged to seek vendors that prioritize transparency and ethical practices in their sourcing. This includes ensuring fair labor practices, responsible material sourcing, and compliance with environmental regulations. The growing consumer preference for brands that demonstrate social responsibility further emphasizes the need for ethical sourcing.
To meet these demands, many manufacturers are now offering ‘green’ certifications and using sustainable materials in their machines. Look for certifications like Energy Star, which signifies energy efficiency, or materials sourced from recycled content. Implementing these practices not only enhances brand reputation but also aligns with the increasing regulatory pressures for sustainability in international markets.
Brief Evolution/History
The Wittern Group, established in the 1930s, has evolved significantly from its early days of simple mechanical vending machines. Over the decades, it has embraced technological advancements, transitioning to electronic and digital vending solutions that cater to changing consumer needs. Today, Wittern Group stands at the forefront of the vending industry, offering innovative solutions that integrate modern technology with sustainability. This evolution reflects broader trends in the vending sector, where adaptability and forward-thinking strategies are essential for success in a competitive global marketplace.
In summary, international B2B buyers from diverse regions must navigate a landscape that increasingly values technology, sustainability, and ethical sourcing. By staying informed about market trends and the evolution of vending solutions, they can make strategic purchasing decisions that align with both their operational needs and consumer expectations.
Related Video: Global Trade & Logistics – What is Global Trade?
Frequently Asked Questions (FAQs) for B2B Buyers of wittern group vending machines
-
How can I effectively vet suppliers of Wittern Group vending machines?
To vet suppliers, first, check their business credentials and industry reputation. Look for verified certifications, such as ISO or local equivalents, which indicate compliance with international standards. Engage in direct communication to assess their responsiveness and willingness to share references from previous clients. Additionally, consider visiting their facilities if feasible, or use third-party inspection services to ensure they meet your quality expectations. -
Are customization options available for Wittern Group vending machines?
Yes, Wittern Group offers a range of customization options. Buyers can request specific branding, colors, and configurations to suit their market needs. It’s advisable to discuss your requirements early in the procurement process to ensure that the supplier can accommodate your requests without significant delays. Be prepared to provide detailed specifications and examples of desired features to facilitate the customization process. -
What are the minimum order quantities (MOQ) and lead times for ordering vending machines?
Minimum order quantities vary based on the model and the supplier’s production capabilities. Generally, MOQs can range from a few units to several dozen. Lead times are influenced by production schedules and customization requirements, typically ranging from 4 to 12 weeks. Always confirm these details during negotiations to align your expectations with the supplier’s capabilities, especially if you have tight project timelines. -
What payment options are available when purchasing vending machines internationally?
Payment options can include bank transfers, letters of credit, and escrow services, depending on the supplier’s policies. International buyers should ensure that the chosen payment method provides sufficient security and mitigates risks related to currency fluctuations. Negotiate payment terms that suit your cash flow needs, such as partial payments upfront and the remainder upon delivery or installation. -
How can I ensure quality assurance and certification for the vending machines?
Request copies of quality assurance certifications and compliance documents from the supplier, such as CE or UL certifications, which verify product safety and performance standards. It’s beneficial to ask about their quality control processes, including inspections and testing conducted during production. Establish clear expectations for quality and performance metrics in your purchase agreement to safeguard your investment. -
What logistics considerations should I be aware of when importing vending machines?
Logistics for importing vending machines involve several key considerations, including freight forwarding, customs clearance, and insurance. Work with a logistics partner experienced in handling large machinery to navigate international shipping regulations. Ensure that all shipping documentation is accurate and complete to avoid delays. Also, factor in additional costs such as tariffs, taxes, and local transportation upon arrival. -
How should I handle disputes that may arise during the procurement process?
To effectively manage disputes, establish clear communication channels and outline conflict resolution procedures in your contract. Consider including mediation or arbitration clauses to facilitate a quicker resolution. Maintain comprehensive records of all transactions and communications to support your position if a dispute arises. Engaging legal counsel familiar with international trade can also provide guidance on navigating complex issues. -
What after-sales support can I expect from Wittern Group suppliers?
After-sales support varies by supplier but typically includes installation assistance, maintenance services, and access to spare parts. Confirm the level of support provided during the negotiation phase, including warranty terms and response times for service requests. Establish a clear contact point for after-sales inquiries to ensure timely assistance and keep your vending machines operational, which is critical for maximizing your investment.
Strategic Sourcing Conclusion and Outlook for wittern group vending machines
In conclusion, strategic sourcing for Wittern Group vending machines offers a myriad of opportunities for international B2B buyers, particularly in regions such as Africa, South America, the Middle East, and Europe. By leveraging a thorough understanding of the global supply chain, buyers can secure not only competitive pricing but also ensure access to innovative vending solutions that cater to diverse consumer needs.
Key Takeaways:
– Understand Market Trends: Familiarize yourself with local consumer preferences to select vending machines that resonate with your target audience.
– Evaluate Supplier Reliability: Assess the Wittern Group’s track record for quality and service to mitigate risks associated with procurement.
– Leverage Technology: Consider machines equipped with smart technology to enhance customer experience and streamline operations.
The value of strategic sourcing cannot be overstated; it empowers businesses to make informed decisions that align with their long-term goals. As the vending machine market evolves, staying ahead of trends will be crucial for success.
Call to Action: Engage with Wittern Group to explore tailored solutions that meet your specific business needs. By doing so, you position your organization to capitalize on emerging opportunities and thrive in an increasingly competitive landscape.