Master Tiny Vending Machine Sourcing: Essential Insights
Guide to Tiny Vending Machine
- Introduction: Navigating the Global Market for tiny vending machine
- Understanding tiny vending machine Types and Variations
- Key Industrial Applications of tiny vending machine
- Strategic Material Selection Guide for tiny vending machine
- In-depth Look: Manufacturing Processes and Quality Assurance for tiny vending machine
- Comprehensive Cost and Pricing Analysis for tiny vending machine Sourcing
- Spotlight on Potential tiny vending machine Manufacturers and Suppliers
- Essential Technical Properties and Trade Terminology for tiny vending machine
- Navigating Market Dynamics, Sourcing Trends, and Sustainability in the tiny vending machine Sector
- Frequently Asked Questions (FAQs) for B2B Buyers of tiny vending machine
- Strategic Sourcing Conclusion and Outlook for tiny vending machine
Introduction: Navigating the Global Market for tiny vending machine
The tiny vending machine market represents a burgeoning opportunity for international B2B buyers, combining convenience with innovation in diverse environments. As urbanization continues to rise across Africa, South America, the Middle East, and Europe, the demand for compact, efficient vending solutions is surging. These machines not only cater to the fast-paced lifestyle of modern consumers but also serve niche markets, from healthy snacks to tech accessories, making them a versatile investment for businesses.
This comprehensive guide delves into the multifaceted world of tiny vending machines, covering essential topics such as types of machines, materials used, manufacturing and quality control processes, and supplier options. Buyers will gain insights into cost considerations and market trends, helping them to navigate the complexities of sourcing effectively. The guide also addresses frequently asked questions, providing a robust framework for making informed decisions.
By empowering B2B buyers with critical information and strategic insights, this resource aims to facilitate successful sourcing decisions that align with local market dynamics. Whether you are an established distributor or a newcomer looking to break into the vending machine sector, understanding the nuances of this market will enhance your competitive edge and drive profitability. Equip yourself with the knowledge to thrive in this vibrant industry and unlock the potential of tiny vending machines as a key asset in your business portfolio.
Understanding tiny vending machine Types and Variations
Type Name | Key Distinguishing Features | Primary B2B Applications | Brief Pros & Cons for Buyers |
---|---|---|---|
Snack & Beverage Machines | Compact design, refrigerated options, touchscreen | Office break rooms, gyms, schools | Pros: High demand for snacks; Cons: Requires regular restocking. |
Health & Wellness Vending | Focus on healthy snacks, supplements, and drinks | Corporate wellness programs, gyms | Pros: Aligns with health trends; Cons: Limited product selection may deter some customers. |
Specialty Product Machines | Dispenses niche items (e.g., tech accessories) | Airports, hotels, tech stores | Pros: Unique offerings attract specific clientele; Cons: Higher initial investment. |
Personal Care Vending | Offers personal hygiene products and cosmetics | Malls, universities, airports | Pros: High-margin products; Cons: Needs careful selection to avoid spoilage. |
Automated Retail Kiosks | Larger footprint, diverse product range, payment options | Retail environments, events | Pros: Versatile and can adapt to various products; Cons: Higher maintenance costs. |
Snack & Beverage Machines
Snack and beverage vending machines are among the most common types in the market. They typically feature a compact design with options for refrigeration, allowing for the sale of cold drinks and perishable snacks. These machines are ideal for placements in high-traffic areas such as office break rooms, gyms, and schools, where consumers seek quick, convenient food options. Buyers should consider the local demand for snacks and beverages, as well as the frequency of restocking, which can affect operational efficiency.
Health & Wellness Vending
These machines focus on offering healthy snacks, supplements, and beverages, catering to the growing consumer trend towards health-conscious choices. They are particularly suited for corporate wellness programs and gyms, where users are likely to seek nutritious options. B2B buyers should evaluate the product range offered by suppliers and consider the potential for higher margins, albeit with the trade-off of a more limited selection that may not appeal to all consumers.
Specialty Product Machines
Specialty product vending machines provide unique items, such as tech accessories or gourmet foods, appealing to niche markets. Their placement in locations like airports, hotels, and tech stores can attract a specific clientele looking for convenience and exclusivity. Buyers should assess the initial investment required for these machines against the potential for higher returns from unique offerings. Understanding the target demographic is crucial for success in this segment.
Personal Care Vending
These machines dispense personal hygiene products and cosmetics, filling a gap in convenience for consumers on the go. Ideal placements include malls, universities, and airports, where customers may need quick access to essential items. B2B buyers should focus on product selection to ensure quality and minimize spoilage, as well as consider the potential for high margins in personal care products. Understanding local consumer preferences can enhance machine profitability.
Automated Retail Kiosks
Automated retail kiosks represent a larger footprint in the vending machine market, offering a diverse range of products and sophisticated payment options. These machines are suited for retail environments and events, providing flexibility in product offerings. Buyers must weigh the versatility and adaptability of these kiosks against higher maintenance costs, ensuring they have the necessary support infrastructure in place. The ability to cater to various consumer needs can enhance sales potential significantly.
Related Video: Machine Learning in 2024 – Beginner’s Course
Key Industrial Applications of tiny vending machine
Industry/Sector | Specific Application of tiny vending machine | Value/Benefit for the Business | Key Sourcing Considerations for this Application |
---|---|---|---|
Healthcare | Dispensing over-the-counter medications | Increases accessibility to medications for patients | Compliance with health regulations, product safety standards |
Education | Providing snacks and drinks in schools | Enhances student satisfaction and reduces hunger | Supplier reliability, variety of healthy options |
Hospitality | Offering quick snacks in hotels and resorts | Improves guest experience and increases ancillary revenue | Customization options, product freshness |
Retail | Selling small electronics or accessories | Captures impulse purchases and increases foot traffic | Product diversity, supplier reputation |
Transportation | Providing refreshments at airports or train stations | Enhances customer service and convenience for travelers | Location-specific regulations, payment system compatibility |
Healthcare Applications
In the healthcare sector, tiny vending machines can effectively dispense over-the-counter medications, such as pain relievers or allergy medications, in hospitals and clinics. This application addresses the challenge of accessibility, allowing patients and visitors to obtain necessary products without having to navigate through larger pharmacy areas. For international buyers, particularly in regions like Africa and the Middle East, compliance with local health regulations and product safety standards is critical. Ensuring that the vending machine suppliers can provide verified compliance documentation will safeguard the business against legal issues.
Education Applications
Tiny vending machines are increasingly being utilized in educational institutions to provide snacks and drinks to students. This application not only enhances student satisfaction but also helps to reduce hunger during school hours, promoting better focus and performance. For B2B buyers in Europe and South America, the key sourcing considerations include the reliability of suppliers and the variety of healthy options available, as schools are increasingly seeking to promote wellness among students.
Hospitality Applications
In the hospitality industry, tiny vending machines can serve as a convenient option for hotels and resorts to offer quick snacks and beverages to guests. This enhances the guest experience by providing easy access to refreshments, potentially increasing ancillary revenue streams. Buyers in this sector should prioritize suppliers that offer customization options to align with their brand and ensure product freshness to maintain high-quality standards.
Retail Applications
Retail environments can leverage tiny vending machines to sell small electronics or accessories, thereby capturing impulse purchases from customers. This application is particularly valuable in high-traffic areas, such as shopping malls or airports, where foot traffic is significant. Buyers should focus on sourcing diverse product offerings and selecting reputable suppliers to ensure product availability and quality, which can significantly influence customer satisfaction and sales.
Transportation Applications
In transportation hubs like airports and train stations, tiny vending machines provide essential refreshments for travelers on the go. This application enhances customer service by offering convenient access to food and drinks, contributing to a positive travel experience. International buyers must consider location-specific regulations and ensure that the vending machines are compatible with various payment systems to cater to a diverse customer base.
Related Video: Venduino, Arduino Vending Machine
Strategic Material Selection Guide for tiny vending machine
When selecting materials for tiny vending machines, it is essential to consider the properties, advantages, disadvantages, and specific regional compliance requirements. Below is an analysis of four common materials used in the construction of tiny vending machines, focusing on their performance and suitability for international B2B buyers.
1. Stainless Steel
Key Properties:
Stainless steel is known for its excellent corrosion resistance, high strength, and ability to withstand various temperatures. It typically has a temperature rating of up to 500°F (260°C) and exhibits good pressure resistance.
Pros & Cons:
The durability of stainless steel makes it ideal for high-traffic environments, as it can withstand mechanical wear and tear. However, it is more expensive than other materials and can be challenging to manufacture due to its hardness. Its aesthetic appeal is a significant advantage, making it suitable for consumer-facing applications.
Impact on Application:
Stainless steel is compatible with a wide range of products, including food and beverages. Its non-reactive nature ensures that it does not alter the taste or quality of the items dispensed.
Considerations for International Buyers:
Buyers should ensure compliance with local health and safety regulations, particularly in food handling. Common standards such as ASTM A240 for stainless steel grades should be adhered to, especially in regions like Europe and the Middle East.
2. ABS Plastic
Key Properties:
Acrylonitrile Butadiene Styrene (ABS) is a lightweight thermoplastic known for its impact resistance and good thermal stability. It can typically withstand temperatures up to 200°F (93°C).
Pros & Cons:
ABS is cost-effective and easy to mold, making it suitable for complex designs. However, it is less durable than metals and can be prone to scratching and fading when exposed to UV light.
Impact on Application:
This material is ideal for non-food items and low-temperature environments. It is commonly used in vending machines that dispense toys or small electronics.
Considerations for International Buyers:
Buyers should verify that ABS complies with local regulations regarding plastics, especially in regions with stringent environmental standards like Europe. Look for certifications such as RoHS compliance.
3. Aluminum
Key Properties:
Aluminum is lightweight, corrosion-resistant, and has a good strength-to-weight ratio. It can handle temperatures up to 400°F (204°C) and is often anodized for additional protection.
Pros & Cons:
Aluminum is relatively affordable and easy to machine, making it a popular choice for various applications. However, it can be less durable than stainless steel and may require additional coatings to enhance corrosion resistance.
Impact on Application:
Aluminum is suitable for both food and non-food applications, but care must be taken with acidic products, which can corrode the surface over time.
Considerations for International Buyers:
Ensure compliance with local standards such as ASTM B221 for aluminum extrusions. In regions like Africa and South America, consider local sourcing options to reduce costs and improve supply chain efficiency.
4. Glass
Key Properties:
Glass is non-porous, chemically resistant, and can withstand temperatures up to 500°F (260°C). It provides excellent visibility for displayed products.
Pros & Cons:
Glass offers a premium look and can enhance the aesthetic appeal of vending machines. However, it is fragile and can break easily, making it less suitable for high-traffic areas.
Impact on Application:
Glass is ideal for showcasing high-end products, such as gourmet snacks or beverages, where visibility can drive sales.
Considerations for International Buyers:
Buyers should ensure that glass components meet safety standards, particularly in regions with strict regulations on breakable materials. Compliance with standards such as DIN EN 12150 for tempered glass is crucial in Europe.
Summary Table
Material | Typical Use Case for tiny vending machine | Key Advantage | Key Disadvantage/Limitation | Relative Cost (Low/Med/High) |
---|---|---|---|---|
Stainless Steel | Food and beverage dispensing | Excellent durability and corrosion resistance | Higher cost and manufacturing complexity | High |
ABS Plastic | Toy and non-food item dispensing | Cost-effective and easy to mold | Less durable, prone to scratching | Low |
Aluminum | General use, food and non-food applications | Lightweight and affordable | Less durable than stainless steel | Medium |
Glass | High-end product display | Premium aesthetic appeal | Fragile and prone to breakage | Medium |
This strategic material selection guide provides a comprehensive overview for international B2B buyers, helping them make informed decisions that align with their operational needs and regional compliance requirements.
In-depth Look: Manufacturing Processes and Quality Assurance for tiny vending machine
The manufacturing process for tiny vending machines involves several critical stages, each designed to ensure the final product meets industry standards and customer expectations. Understanding these stages can help international B2B buyers make informed decisions when sourcing these machines.
Manufacturing Process
1. Material Preparation
The first stage in manufacturing tiny vending machines is material preparation. This involves selecting high-quality materials, such as steel, aluminum, and high-grade plastics, which are essential for durability and longevity. Suppliers often conduct a thorough analysis of materials to ensure they meet strength and weight specifications.
- Key Techniques:
- Material Testing: Samples undergo tensile and impact tests to verify their suitability.
- Supplier Verification: Buyers should ensure that materials are sourced from ISO-certified suppliers to guarantee quality.
2. Forming
Once materials are prepared, they undergo the forming process. This stage includes cutting, bending, and shaping the materials into the desired components of the vending machine.
- Key Techniques:
- CNC Machining: Computer Numerical Control (CNC) machines provide high precision in cutting and shaping parts.
- Metal Stamping: This technique is commonly used for creating panels and frames, ensuring uniformity and strength.
3. Assembly
The assembly stage is where all components come together. This process can be manual or automated, depending on the manufacturer’s capabilities and the complexity of the vending machine design.
- Key Techniques:
- Modular Assembly: Components are assembled in modules, allowing for easier repairs and upgrades.
- Automated Assembly Lines: These increase production efficiency and reduce human error.
4. Finishing
The final stage involves finishing processes, which enhance the appearance and durability of the vending machines. This may include painting, coating, or applying decals.
- Key Techniques:
- Powder Coating: Provides a durable finish that resists scratches and corrosion.
- Quality Checks: Visual inspections and surface testing ensure that the finish meets aesthetic and functional standards.
Quality Assurance
Quality assurance (QA) is a critical component of the manufacturing process for tiny vending machines. It ensures that products meet international standards and customer specifications.
Relevant International Standards
B2B buyers should be aware of various international quality standards that affect vending machine manufacturing:
- ISO 9001: This standard focuses on quality management systems and is essential for ensuring consistent product quality.
- CE Marking: Required for products sold in the European Economic Area, it indicates compliance with health, safety, and environmental protection standards.
- API Standards: Relevant for machines dispensing food or beverages, ensuring safety and hygiene.
Quality Control Checkpoints
Quality control (QC) checkpoints are essential for maintaining product integrity throughout the manufacturing process. Common checkpoints include:
- Incoming Quality Control (IQC): Materials and components are inspected upon arrival to ensure they meet specifications.
- In-Process Quality Control (IPQC): Regular checks are conducted during manufacturing to identify defects early.
- Final Quality Control (FQC): A thorough inspection of the finished product ensures it meets all quality standards before shipping.
Common Testing Methods
To verify the quality of tiny vending machines, manufacturers employ several testing methods:
- Functional Testing: Ensures that all mechanical and electronic components operate correctly.
- Durability Testing: Products are subjected to stress and strain to assess their longevity under typical usage conditions.
- Safety Testing: Compliance with safety standards is verified through rigorous testing protocols.
Verifying Supplier Quality Control
For B2B buyers, ensuring that suppliers maintain high-quality standards is paramount. Here are actionable insights on how to verify a supplier’s QC processes:
- Conduct Audits: Regular audits can help assess a supplier’s adherence to quality standards. Buyers should request an audit schedule and results.
- Request Quality Reports: Suppliers should provide documentation detailing their QC processes, including test results and compliance certifications.
- Third-Party Inspections: Engaging independent inspectors can provide unbiased verification of a supplier’s quality claims.
QC and Certification Nuances for International Buyers
Navigating the complexities of quality assurance and certifications can be particularly challenging for international buyers, especially from regions like Africa, South America, the Middle East, and Europe. Here are some considerations:
- Local Regulations: Understanding local regulations is crucial. For example, certain countries may have specific certifications that differ from international standards.
- Cultural Considerations: Building relationships with suppliers often involves understanding cultural nuances, which can affect communication and negotiation.
- Logistical Challenges: Ensure that suppliers can meet shipping and delivery timelines, as delays can impact business operations.
By comprehensively understanding the manufacturing processes and quality assurance standards, B2B buyers can better assess potential suppliers, negotiate favorable terms, and ultimately secure high-quality tiny vending machines that meet their operational needs.
Related Video: SMART Quality Control for Manufacturing
Comprehensive Cost and Pricing Analysis for tiny vending machine Sourcing
When sourcing tiny vending machines for international markets, understanding the cost structure and pricing dynamics is essential for maximizing profitability and ensuring a sustainable supply chain. Below is a comprehensive analysis that outlines key components of costs, influences on pricing, and strategic tips for buyers.
Cost Components
-
Materials:
– The primary materials for tiny vending machines include metal, plastic, electronic components, and glass. The choice of materials significantly impacts durability and aesthetic appeal, thereby influencing cost.
– Eco-friendly materials may incur higher initial costs but can attract environmentally-conscious consumers. -
Labor:
– Labor costs vary by region and can be influenced by local wage standards. Manufacturing countries like China or Vietnam may offer lower labor costs compared to those in Europe or North America.
– Skilled labor may be required for assembly and quality control, adding to the overall labor costs. -
Manufacturing Overhead:
– This includes utilities, rent, and administrative expenses associated with production facilities. Efficient production processes can help minimize these costs.
– Consider suppliers with advanced manufacturing technologies that reduce overhead expenses through automation. -
Tooling:
– Tooling costs are related to the equipment needed for production. Custom designs may require specialized tools, which can elevate initial costs but may result in better product differentiation.
– Ensure that tooling costs are factored into the overall pricing strategy, especially for customized machines. -
Quality Control (QC):
– Implementing rigorous QC measures helps maintain product reliability and customer satisfaction. However, this can also increase costs.
– Buyers should inquire about the QC protocols of potential suppliers to ensure compliance with international standards. -
Logistics:
– Logistics costs encompass shipping, handling, and customs duties. These costs can vary significantly based on the shipping method (air vs. sea) and the destination.
– Understanding Incoterms (International Commercial Terms) is crucial, as they dictate the responsibilities of buyers and sellers in shipping arrangements. -
Margin:
– The profit margin for vending machines typically ranges from 10% to 30%, depending on the competitive landscape and demand. Buyers should assess their pricing strategies to ensure adequate margins while remaining competitive.
Price Influencers
-
Volume/MOQ (Minimum Order Quantity): Higher order volumes can lead to significant discounts. Establishing a long-term relationship with suppliers may also provide more favorable pricing.
-
Specifications and Customization: Customized machines with unique features can command higher prices. Understanding the market demand for specific functionalities can guide investment decisions.
-
Materials and Quality Certifications: Higher-quality materials and certifications (e.g., CE, ISO) may raise costs but can enhance marketability and customer trust. Evaluate the trade-offs between cost and quality.
-
Supplier Factors: Supplier reputation, reliability, and production capacity can influence pricing. Engaging with established suppliers can mitigate risks associated with quality and delivery times.
Buyer Tips
-
Negotiation: Always negotiate pricing, especially for bulk orders. Leverage long-term partnerships to secure better deals and terms.
-
Cost-Efficiency: Evaluate the Total Cost of Ownership (TCO), which includes initial purchase price, maintenance, and operational costs. This holistic view helps in making informed purchasing decisions.
-
Pricing Nuances for International Buyers: Be aware of currency fluctuations, tariffs, and import regulations in your region. These factors can impact the overall cost and pricing strategy.
-
Seek Transparent Suppliers: Partner with suppliers who provide clear breakdowns of costs and pricing structures. Transparency fosters trust and facilitates better decision-making.
Disclaimer
Prices and cost structures can vary widely based on market conditions, supplier capabilities, and regional factors. It is advisable to conduct thorough market research and engage in direct negotiations to obtain accurate pricing information tailored to your specific needs.
Spotlight on Potential tiny vending machine Manufacturers and Suppliers
This section offers a look at a few manufacturers active in the ‘tiny vending machine’ market. This is a representative sample for illustrative purposes; B2B buyers must conduct their own extensive due diligence before any engagement. Information is synthesized from public sources and general industry knowledge.
Essential Technical Properties and Trade Terminology for tiny vending machine
Key Technical Properties of Tiny Vending Machines
Understanding the essential technical properties of tiny vending machines is crucial for international B2B buyers. These specifications not only influence operational efficiency but also impact the overall profitability of the vending business. Here are some critical properties to consider:
-
Material Grade
– Definition: This refers to the type of materials used in the construction of the vending machine, such as stainless steel, plastic, or glass.
– Importance: High-grade materials enhance durability and longevity, reducing maintenance costs. For example, stainless steel is resistant to corrosion and easy to clean, making it ideal for food vending applications. -
Capacity
– Definition: The maximum number of products that the machine can hold, often measured in units or weight.
– Importance: Capacity directly affects revenue potential. A higher capacity means more products can be sold without frequent restocking, which is vital in high-traffic areas.
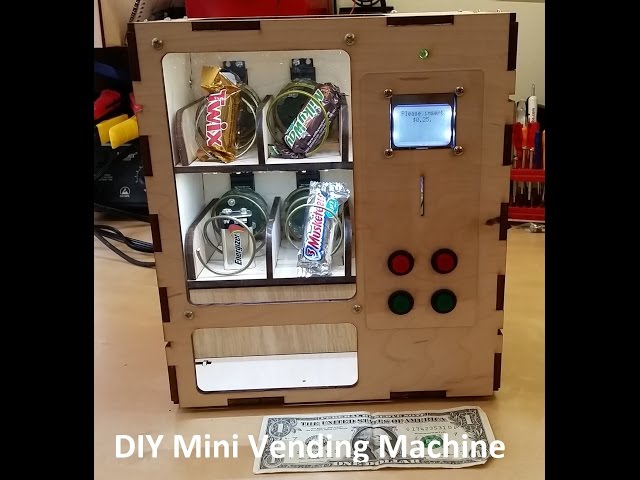
Illustrative Image (Source: Google Search)
-
Power Consumption
– Definition: The amount of electricity the vending machine uses during operation, typically measured in watts.
– Importance: Lower power consumption translates to reduced operational costs, a critical factor for profit margins, especially in regions with high electricity prices. -
Payment Systems Compatibility
– Definition: The types of payment methods supported by the vending machine, such as cash, credit/debit cards, and mobile payments.
– Importance: Compatibility with diverse payment systems can enhance customer convenience and increase sales. In regions like Europe and the Middle East, cashless transactions are becoming the norm, making this feature essential. -
Dimensions and Weight
– Definition: The physical size and weight of the vending machine, which can affect placement options.
– Importance: Understanding the dimensions is critical for ensuring the machine fits in designated locations and complies with local regulations regarding space and accessibility.
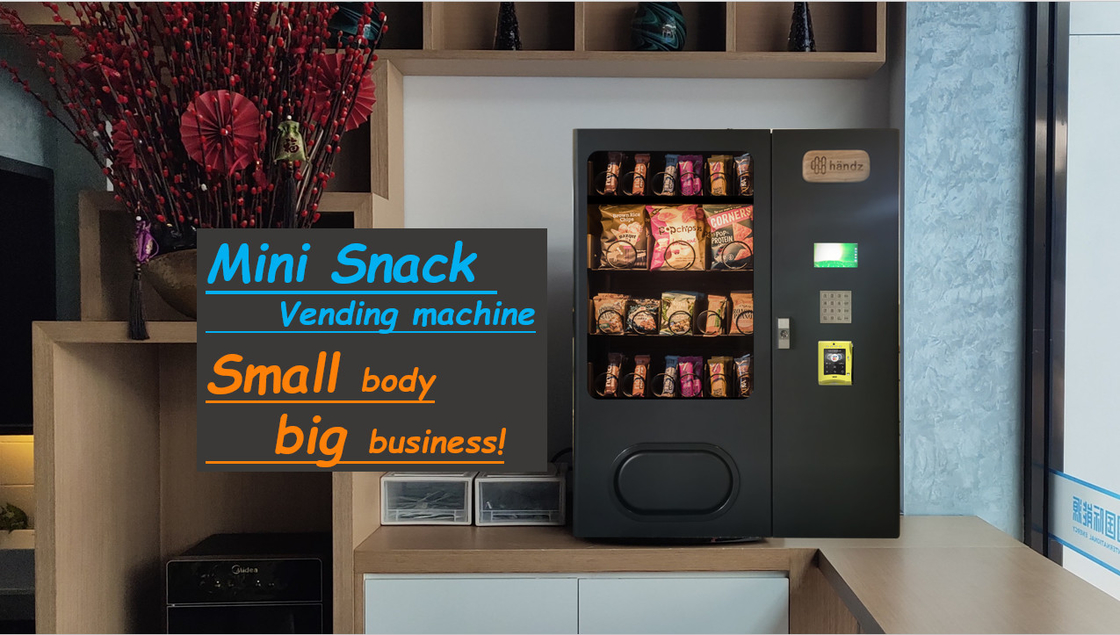
Illustrative Image (Source: Google Search)
- Temperature Control
– Definition: The ability of the vending machine to maintain specific temperatures for perishable items.
– Importance: For machines dispensing food or beverages, effective temperature control is vital for food safety and compliance with health regulations, particularly in markets with stringent food safety laws.
Common Trade Terminology in the Vending Industry
Familiarity with industry jargon is essential for effective communication and negotiation in the B2B vending landscape. Here are some common terms:
-
OEM (Original Equipment Manufacturer)
– Definition: A company that produces parts or equipment that may be marketed by another manufacturer.
– Relevance: Understanding OEM relationships can help buyers secure high-quality machines and components, ensuring reliable performance. -
MOQ (Minimum Order Quantity)
– Definition: The smallest quantity of a product that a supplier is willing to sell.
– Relevance: Knowing the MOQ is crucial for budgeting and inventory management. It can also affect the negotiation process, especially when sourcing in bulk. -
RFQ (Request for Quotation)
– Definition: A document sent to suppliers to request pricing for specific products or services.
– Relevance: An RFQ can streamline the procurement process, enabling buyers to compare prices and terms from multiple suppliers effectively. -
Incoterms (International Commercial Terms)
– Definition: A set of international rules defining the responsibilities of buyers and sellers in the shipping of goods.
– Relevance: Familiarity with Incoterms helps buyers understand shipping costs and risks, which is particularly important when sourcing from different regions. -
Lead Time
– Definition: The time between placing an order and receiving it.
– Relevance: Understanding lead times is essential for planning inventory and ensuring that machines are stocked promptly, which can directly impact sales. -
Warranty
– Definition: A guarantee provided by the manufacturer regarding the condition of the product and the terms of repair or replacement.
– Relevance: A strong warranty can protect buyers from unexpected costs and downtime, making it a key factor in supplier selection.
By grasping these technical properties and trade terms, international B2B buyers can make informed decisions, optimize their vending operations, and enhance profitability.
Navigating Market Dynamics, Sourcing Trends, and Sustainability in the tiny vending machine Sector
Market Overview & Key Trends
The tiny vending machine sector is witnessing a significant transformation driven by technological advancements and changing consumer behaviors. Globally, there is a surge in demand for contactless payment solutions, which not only enhance user experience but also streamline operations for B2B buyers. As urbanization continues to rise, especially in Africa and South America, tiny vending machines are becoming increasingly popular in high-traffic areas such as offices, universities, and transportation hubs.
Emerging trends in the market include the integration of IoT technology, enabling remote monitoring of inventory and machine performance. This capability allows international buyers to optimize their product offerings and minimize downtime. Additionally, the use of artificial intelligence for predictive analytics is gaining traction, helping businesses anticipate consumer preferences and adjust stock accordingly. In regions like the Middle East, where luxury and convenience are prioritized, tiny vending machines are evolving to offer premium products, catering to a more discerning clientele.
Moreover, sustainability is becoming a core consideration for B2B buyers. Companies are increasingly sourcing eco-friendly products and materials, aligning with global sustainability goals. This trend is particularly relevant in Europe, where consumers are more conscious about environmental impacts, influencing purchasing decisions in the vending sector. Overall, international B2B buyers must stay attuned to these dynamics to remain competitive and meet evolving consumer expectations.
Sustainability & Ethical Sourcing in B2B
Sustainability is no longer a niche consideration; it has become a fundamental aspect of sourcing strategies in the tiny vending machine sector. The environmental impact of vending operations can be substantial, from energy consumption to waste generation. B2B buyers are increasingly required to assess the lifecycle of products and opt for suppliers who prioritize sustainable practices.
Ethical sourcing is paramount in establishing a responsible supply chain. This involves selecting vendors who adhere to fair labor practices and environmental regulations. Buyers should look for certifications such as Fair Trade or Global Organic Textile Standard (GOTS) to ensure that products are sourced responsibly. Additionally, using biodegradable or recyclable materials in vending machine products can significantly reduce environmental footprints.
The adoption of green technologies, such as energy-efficient vending machines that utilize solar power or LED lighting, is also gaining momentum. For international buyers, especially in regions like Africa and South America, implementing such sustainable practices not only enhances brand reputation but also meets increasing regulatory pressures regarding environmental responsibility. Ultimately, prioritizing sustainability and ethical sourcing can lead to improved customer loyalty and market differentiation.
Brief Evolution/History
The tiny vending machine industry has evolved significantly over the past few decades. Initially, vending machines were primarily limited to snacks and beverages, but advancements in technology have diversified their offerings. With the introduction of cashless payment systems and smart vending solutions, machines now cater to a wide array of products, including electronics, personal care items, and healthy food options.
As urban lifestyles became more fast-paced, the demand for convenient access to goods led to the rise of tiny vending machines in various settings. This evolution reflects broader societal trends towards convenience and efficiency, making tiny vending machines a valuable asset for businesses looking to capitalize on consumer demand in today’s fast-moving markets. Understanding this history is crucial for B2B buyers, as it highlights the sector’s adaptability and potential for future growth.
Related Video: Global Trade & Logistics – What is Global Trade?
Frequently Asked Questions (FAQs) for B2B Buyers of tiny vending machine
-
How can I effectively vet suppliers for tiny vending machines?
To vet suppliers, start by checking their business credentials, including certifications, licenses, and industry reputation. Look for reviews and testimonials from other B2B buyers, particularly in your region. Request references and contact them to inquire about their experiences. Additionally, visiting the supplier’s facility, if possible, can provide insights into their operational capabilities. Ensure that suppliers have a robust quality assurance process to maintain product standards. -
Can tiny vending machines be customized for my specific needs?
Yes, many suppliers offer customization options for tiny vending machines, allowing you to tailor features such as size, branding, product offerings, and payment systems. When discussing customization, clarify your requirements and ask for examples of previous custom projects. Ensure that the supplier can accommodate your specific needs without compromising on lead times or quality, and get written confirmation of the customization capabilities. -
What are the typical minimum order quantities (MOQs) and lead times for tiny vending machines?
MOQs can vary significantly among suppliers, typically ranging from 5 to 50 units for tiny vending machines. It’s essential to discuss your purchasing plans upfront to find a supplier that meets your volume requirements. Lead times can also vary based on customization and production capacity, generally ranging from 4 to 12 weeks. Always confirm these details in advance to avoid any disruptions in your supply chain.
-
What payment terms should I expect when sourcing tiny vending machines?
Payment terms vary by supplier and may include options such as upfront payments, payment upon delivery, or net payment terms (e.g., net 30 days). Many suppliers may require a deposit (often 30-50%) at the time of order, especially for customized machines. It’s crucial to clarify these terms before entering a contract to ensure both parties have a clear understanding of the payment process and to mitigate any cash flow issues. -
What quality assurance processes should suppliers have in place?
Suppliers should implement rigorous quality assurance processes, including regular inspections and testing of their machines at various production stages. Request documentation of their quality control protocols, such as ISO certification or other relevant quality standards. Ensure that the supplier can provide evidence of compliance with safety and regulatory standards applicable in your region, as this will protect your investment and reputation. -
How should I handle logistics and shipping for tiny vending machines?
Logistics can be complex, so it’s essential to discuss shipping options with your supplier. Determine who will be responsible for shipping costs and customs duties. Opt for suppliers who have experience with international shipping and can provide reliable freight options. Be sure to establish clear timelines for delivery and understand the process for tracking shipments, as well as handling any potential delays or damages during transit. -
What should I do if there’s a dispute with my supplier?
In the event of a dispute, first, attempt to resolve the issue directly with the supplier through open communication. Review your contract for any clauses regarding dispute resolution. If necessary, escalate the matter through formal channels, such as mediation or arbitration, as stipulated in your agreement. Keeping thorough records of all correspondence and transactions will be essential in supporting your case during any dispute resolution process. -
Are there any certifications or standards I should look for in tiny vending machines?
Yes, various certifications can indicate the quality and safety of tiny vending machines. Look for CE marking in Europe, which signifies compliance with health, safety, and environmental protection standards. In the Middle East and Africa, ensure that products meet local regulatory requirements. Additionally, ISO certifications related to quality management can be a good indicator of a supplier’s commitment to maintaining high standards in their manufacturing processes.
Strategic Sourcing Conclusion and Outlook for tiny vending machine
In conclusion, strategic sourcing in the tiny vending machine sector is essential for maximizing profitability and ensuring long-term success. By cultivating strong supplier relationships and understanding local regulations, international B2B buyers can navigate the complexities of the market effectively. Key takeaways include the importance of selecting reliable suppliers, maintaining a diverse product offering, and adhering to legal requirements to avoid potential pitfalls.
As buyers from Africa, South America, the Middle East, and Europe explore new opportunities in this growing industry, they should prioritize partnerships that not only provide quality products but also offer insights into market trends and consumer preferences. Investing in strategic sourcing not only enhances the efficiency of your supply chain but also positions your vending operations for competitive advantage.
Looking ahead, the tiny vending machine market is poised for growth, driven by evolving consumer demands and technological advancements. Now is the time for international B2B buyers to take action—evaluate your sourcing strategies, strengthen supplier collaborations, and adapt to emerging trends to capitalize on this exciting opportunity.