Your Ultimate Guide to Sourcing Used Drink Vending Machines
Guide to Used Drink Vending Machines
- Introduction: Navigating the Global Market for used drink vending machines
- Understanding used drink vending machines Types and Variations
- Key Industrial Applications of used drink vending machines
- Strategic Material Selection Guide for used drink vending machines
- In-depth Look: Manufacturing Processes and Quality Assurance for used drink vending machines
- Comprehensive Cost and Pricing Analysis for used drink vending machines Sourcing
- Spotlight on Potential used drink vending machines Manufacturers and Suppliers
- Essential Technical Properties and Trade Terminology for used drink vending machines
- Navigating Market Dynamics, Sourcing Trends, and Sustainability in the used drink vending machines Sector
- Frequently Asked Questions (FAQs) for B2B Buyers of used drink vending machines
- Strategic Sourcing Conclusion and Outlook for used drink vending machines
Introduction: Navigating the Global Market for used drink vending machines
In an increasingly interconnected global economy, the demand for used drink vending machines has surged, presenting lucrative opportunities for international B2B buyers. These machines not only offer cost-effective solutions for businesses looking to enhance their service offerings but also align with sustainable practices by promoting recycling and reusing equipment. Whether you are a retailer in Africa, a distributor in South America, or a facility manager in Europe or the Middle East, understanding the nuances of the used vending machine market can significantly impact your procurement strategy.
This comprehensive guide delves into the essential facets of used drink vending machines, covering various types and materials, manufacturing and quality control standards, and key suppliers. We will also explore the cost factors associated with acquiring these machines and provide insights into the current market trends. To further support your sourcing decisions, we include a FAQs section addressing common queries that arise during the purchasing process.
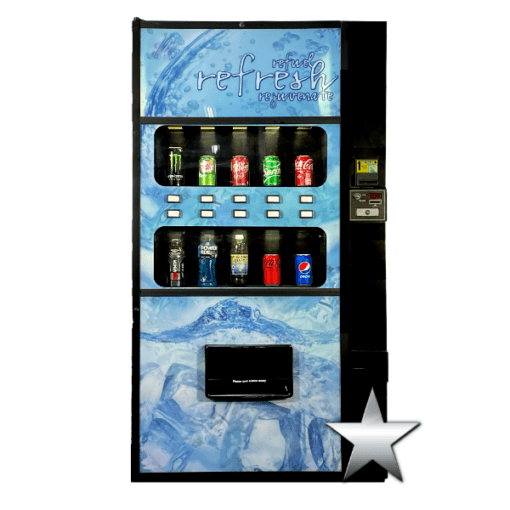
Illustrative Image (Source: Google Search)
By equipping yourself with this knowledge, you empower your business to make informed decisions that can lead to enhanced customer satisfaction and increased profitability. This guide serves as your roadmap to navigating the complexities of the global market for used drink vending machines, ensuring you can source effectively and competitively. Prepare to unlock the potential of your vending operations with strategic insights tailored to your region’s unique market dynamics.
Understanding used drink vending machines Types and Variations
Type Name | Key Distinguishing Features | Primary B2B Applications | Brief Pros & Cons for Buyers |
---|---|---|---|
Traditional Soda Vending | Offers a range of carbonated beverages | Offices, schools, public spaces | Pros: Widely recognized; easy to maintain. Cons: Limited to soft drinks; may not attract health-conscious consumers. |
Healthy Drink Vending | Focus on natural juices, smoothies, and teas | Gyms, health clubs, schools | Pros: Appeals to health-conscious buyers; diverse offerings. Cons: Higher initial cost; may require specialized suppliers. |
Coffee Vending Machines | Brew fresh coffee on demand | Offices, break rooms, cafes | Pros: High demand for coffee; can offer various blends. Cons: Requires regular maintenance; potential for high energy consumption. |
Multi-Product Vending | Dispenses snacks and drinks in one machine | Airports, malls, convenience stores | Pros: Space-efficient; caters to varied consumer preferences. Cons: Complex inventory management; potential for more breakdowns. |
Smart Vending Machines | Integrated with IoT for cashless payments | Tech hubs, universities, offices | Pros: Modern appeal; real-time sales tracking. Cons: Higher upfront investment; reliance on technology may deter some users. |
Traditional Soda Vending
Traditional soda vending machines are the most recognizable type, offering a variety of carbonated beverages. These machines are commonly found in offices, schools, and public spaces. They are favored for their simplicity and ease of maintenance. However, they may not attract health-conscious consumers, limiting their appeal in environments that prioritize wellness. When purchasing, buyers should consider the machine’s capacity, ease of restocking, and the range of products offered.
Healthy Drink Vending
Healthy drink vending machines focus on providing natural juices, smoothies, and teas, catering to the growing demand for healthier options. These machines are ideal for gyms, health clubs, and schools where consumers seek nutritious beverages. While they can attract health-conscious buyers, the initial investment is often higher, and suppliers may need to be specialized to ensure product quality. B2B buyers should evaluate the machine’s flexibility in product offerings and the ease of sourcing fresh ingredients.
Coffee Vending Machines
Coffee vending machines brew fresh coffee on demand and are popular in offices, break rooms, and cafes. The high demand for coffee makes these machines a valuable asset for businesses looking to enhance employee satisfaction or customer experience. However, they require regular maintenance to ensure quality and can consume significant energy. Buyers should assess the machine’s brewing capacity, variety of coffee options, and energy efficiency when making a purchasing decision.
Multi-Product Vending
Multi-product vending machines can dispense both snacks and drinks, making them versatile solutions for locations like airports, malls, and convenience stores. Their space-efficient design allows for a broader range of consumer preferences. However, these machines can complicate inventory management and may be more prone to breakdowns due to the complexity of their systems. Buyers should consider the machine’s durability, ease of use, and the diversity of products it can offer.
Smart Vending Machines
Smart vending machines leverage IoT technology for cashless payments and real-time sales tracking, appealing to tech-savvy consumers in environments such as tech hubs, universities, and modern offices. While they provide a modern appeal and operational efficiency, their higher upfront investment and reliance on technology may deter some potential users. B2B buyers should evaluate the machine’s technological features, compatibility with existing payment systems, and the potential for data-driven inventory management.
Related Video: Cheap vs Expensive Drink Vending Machine
Key Industrial Applications of used drink vending machines
Industry/Sector | Specific Application of used drink vending machines | Value/Benefit for the Business | Key Sourcing Considerations for this Application |
---|---|---|---|
Education | Student Cafeterias and Campus Areas | Increases convenience for students, reduces wait times | Machine condition, warranty, and payment systems |
Corporate Offices | Break Rooms and Common Areas | Enhances employee satisfaction, promotes hydration | Energy efficiency, product variety, and maintenance |
Healthcare | Hospitals and Clinics | Provides quick access to beverages for patients and staff | Hygiene standards, accessibility features, and reliability |
Transportation Hubs | Airports and Train Stations | Serves high foot traffic, generates additional revenue | Durability, payment options, and refill frequency |
Retail | Shopping Malls and Supermarkets | Attracts customers, increases impulse purchases | Location analysis, product mix, and marketing support |
Education
Used drink vending machines are particularly beneficial in educational institutions, such as universities and colleges. They provide students with easy access to beverages in cafeterias and common areas, promoting hydration and convenience. This is especially important during busy hours when students may not have time to queue for drinks. Buyers in this sector should prioritize machine condition and warranty, ensuring reliability and minimal downtime during peak usage times.
Corporate Offices
In corporate environments, used drink vending machines can significantly enhance employee satisfaction by offering a variety of beverage options in break rooms and common areas. This convenience can lead to increased productivity and morale among staff. International buyers should consider energy efficiency and the variety of products offered in the machines, as well as the ease of maintenance to ensure continuous operation without disruption.
Healthcare
Healthcare facilities such as hospitals and clinics benefit from used drink vending machines by providing quick access to beverages for both patients and staff. This is crucial for maintaining hydration, especially in high-stress environments. Buyers must ensure that the machines meet strict hygiene standards, incorporate accessibility features for all users, and operate reliably to support the fast-paced healthcare setting.
Transportation Hubs
In high-traffic areas like airports and train stations, used drink vending machines serve the dual purpose of convenience and revenue generation. They cater to travelers looking for quick refreshment options, thereby enhancing the overall customer experience. Key considerations for sourcing include the durability of the machines to withstand heavy use, the variety of payment options available, and the frequency of refills to maintain stock levels.
Retail
Shopping malls and supermarkets can leverage used drink vending machines to attract customers and increase impulse purchases. Strategically placed machines can enhance the shopping experience by offering refreshments at convenient points. Buyers in the retail sector should conduct thorough location analyses to optimize machine placement, consider the product mix to cater to diverse customer preferences, and explore marketing support options to promote the vending services effectively.
Related Video: Kooler Ice Vending Machines – IM600XL vs. IM1000
Strategic Material Selection Guide for used drink vending machines
When selecting materials for used drink vending machines, it is crucial to consider their properties, advantages, and limitations, especially in the context of international markets. Below is an analysis of four common materials used in the construction of these machines, tailored for B2B buyers from Africa, South America, the Middle East, and Europe.
1. Stainless Steel
Key Properties: Stainless steel is known for its excellent corrosion resistance, high strength, and ability to withstand extreme temperatures. It typically has a temperature rating of up to 1,200°F (649°C) and can handle moderate pressure levels.
Pros & Cons: The durability of stainless steel makes it a preferred choice for vending machines, as it can withstand harsh environments and frequent use. However, it is more expensive than other materials, which can impact the overall cost of the vending machine. Manufacturing complexity is moderate, as stainless steel requires specialized welding techniques.
Impact on Application: Stainless steel is compatible with a wide range of beverages, including acidic drinks, which can corrode other materials. This makes it ideal for vending machines that dispense sodas, juices, and energy drinks.
Considerations for International Buyers: Buyers should ensure compliance with local standards such as ASTM A240 for stainless steel. In regions like Europe, adherence to the EN 10088 standard is critical. Additionally, the availability of stainless steel may vary by region, influencing lead times.
2. Polycarbonate
Key Properties: Polycarbonate is a lightweight, impact-resistant plastic that can withstand temperatures ranging from -40°F to 240°F (-40°C to 115°C). It has good clarity and can be molded into complex shapes.
Pros & Cons: The primary advantage of polycarbonate is its low weight and high impact resistance, making it suitable for the external components of vending machines. However, it is less durable than metals and can be prone to scratching and UV degradation over time, leading to potential replacement costs.
Impact on Application: Polycarbonate is ideal for transparent panels and doors, allowing visibility of the products inside. It is compatible with most beverages but may not be suitable for hot drinks due to its lower temperature resistance.
Considerations for International Buyers: Buyers should check for compliance with safety standards like ASTM D6400 for biodegradability, especially in regions with strict environmental regulations. The availability of specific grades of polycarbonate can also vary, impacting sourcing decisions.
3. Aluminum
Key Properties: Aluminum is lightweight, corrosion-resistant, and has a melting point of around 1,221°F (660°C). It offers a good strength-to-weight ratio, making it suitable for various structural components.
Pros & Cons: The main advantage of aluminum is its cost-effectiveness and ease of fabrication. However, it is softer than steel and may not be suitable for high-impact areas, which could lead to dents and scratches over time.
Impact on Application: Aluminum is often used for the frame and structural components of vending machines, providing adequate support while keeping the overall weight low. It is compatible with a variety of beverages, including carbonated drinks.
Considerations for International Buyers: Buyers should ensure that the aluminum used meets standards such as ASTM B221 for extruded aluminum products. Additionally, the choice between anodized and untreated aluminum can affect durability and maintenance needs.
4. Glass
Key Properties: Glass is a rigid, brittle material with excellent clarity and resistance to chemical corrosion. It typically withstands temperatures up to 400°F (204°C) but is sensitive to thermal shock.
Pros & Cons: Glass offers aesthetic appeal and allows customers to see the products clearly, enhancing sales. However, it is heavy and can break easily, leading to higher maintenance costs and safety concerns.
Impact on Application: Glass is commonly used for display windows in vending machines, allowing for product visibility. It is compatible with most drinks but requires careful handling to avoid breakage.
Considerations for International Buyers: Compliance with safety standards such as EN 12150 for tempered glass is essential, particularly in regions with stringent safety regulations. Buyers should also consider the logistics of transporting glass, as it is more fragile than other materials.
Material | Typical Use Case for used drink vending machines | Key Advantage | Key Disadvantage/Limitation | Relative Cost (Low/Med/High) |
---|---|---|---|---|
Stainless Steel | Structural components, internal frameworks | Excellent durability and corrosion resistance | Higher cost compared to other materials | High |
Polycarbonate | Transparent panels and doors | Lightweight and impact-resistant | Prone to scratching and UV degradation | Medium |
Aluminum | Frames and structural components | Cost-effective and easy to fabricate | Softer than steel, prone to dents | Low |
Glass | Display windows | Aesthetic appeal and product visibility | Heavy and fragile | Medium |
This guide provides B2B buyers with a comprehensive overview of material options for used drink vending machines, emphasizing the importance of material selection in ensuring durability, performance, and compliance with international standards.
In-depth Look: Manufacturing Processes and Quality Assurance for used drink vending machines
Manufacturing Processes for Used Drink Vending Machines
The manufacturing of used drink vending machines involves several key stages that ensure the final product meets both functionality and quality standards. Understanding these processes is crucial for international B2B buyers, especially when sourcing from diverse markets across Africa, South America, the Middle East, and Europe.
Main Stages of Manufacturing
-
Material Preparation
– Sourcing: Materials such as stainless steel, plastic, and electronic components are sourced based on durability and regulatory compliance. For regions like Europe, sourcing from local suppliers may ensure adherence to strict environmental regulations.
– Processing: Materials undergo various treatments, such as cutting, bending, and coating, to enhance durability and aesthetics. For instance, stainless steel components might be polished to prevent corrosion. -
Forming
– Fabrication Techniques: Advanced techniques such as laser cutting and CNC machining are employed to achieve precise dimensions for machine parts. This precision is vital for ensuring that all components fit together seamlessly.
– Component Manufacturing: Key parts like the dispensing mechanism and refrigeration units are manufactured separately before being integrated into the vending machine.
-
Assembly
– Modular Assembly: Components are assembled in a modular fashion, allowing for efficient repairs and upgrades. For instance, if a refrigeration unit fails, it can be replaced without dismantling the entire machine.
– Integration: The integration of electronic systems, including payment processing units and user interfaces, is a critical step. This process often involves rigorous testing to ensure compatibility and functionality. -
Finishing
– Surface Treatment: Final touches such as painting, branding, and protective coatings are applied. This step not only enhances the aesthetic appeal but also protects against environmental factors.
– Quality Checks: Before packaging, machines undergo initial quality checks to ensure they meet design specifications and performance standards.
Quality Assurance in Manufacturing
Quality assurance is essential in the manufacturing of used drink vending machines, ensuring that they operate reliably and safely over time. Various international standards and industry-specific regulations guide these processes.
Relevant International Standards
- ISO 9001: This standard focuses on quality management systems and is crucial for manufacturers aiming to improve efficiency and customer satisfaction. Compliance indicates a commitment to maintaining high-quality processes.
- CE Marking: For machines sold in the European market, CE marking ensures compliance with health, safety, and environmental protection standards.
- API Standards: In some regions, particularly where vending machines may dispense food or beverages, adherence to API standards ensures safety and quality in food handling.
Quality Control Checkpoints
-
Incoming Quality Control (IQC)
– This stage involves inspecting raw materials and components upon arrival to ensure they meet predefined specifications. Suppliers should provide certificates of compliance for critical materials. -
In-Process Quality Control (IPQC)
– During the manufacturing process, regular checks are conducted to monitor production quality. This includes verifying dimensions, functionality, and assembly accuracy at various stages. -
Final Quality Control (FQC)
– Once the machine is fully assembled, a comprehensive final inspection is carried out. This includes functionality tests, safety checks, and performance evaluations to ensure the machine operates as intended.
Common Testing Methods
- Functional Testing: Ensures that all electronic components, including payment systems and display interfaces, work correctly.
- Stress Testing: Machines are subjected to extreme conditions to evaluate their durability and performance under pressure.
- Safety Testing: Includes checks for electrical safety, mechanical hazards, and compliance with food safety regulations where applicable.
Verifying Supplier Quality Control
B2B buyers can take several steps to verify the quality control measures of potential suppliers:
- Supplier Audits: Conducting regular audits of suppliers’ manufacturing processes can provide insights into their quality control practices. This can include reviewing documentation and observing production firsthand.
- Quality Reports: Requesting detailed quality reports can help assess a supplier’s commitment to quality. These reports should include data on defect rates, compliance with standards, and results from quality checks.
- Third-Party Inspections: Engaging third-party inspection services can provide an unbiased evaluation of the manufacturing process and product quality. This is particularly important when sourcing from regions with varying regulatory standards.
Quality Control Nuances for International Buyers
When sourcing used drink vending machines internationally, especially from regions like Africa, South America, and the Middle East, buyers should consider the following:
- Cultural Differences: Understanding the local business culture can facilitate smoother negotiations and clearer communication regarding quality expectations.
- Regulatory Compliance: Different regions may have unique requirements for certifications and compliance. Buyers should be well-informed about these to avoid legal and operational issues.
- Post-Purchase Support: Ensure that suppliers offer adequate support for maintenance and repairs, including access to spare parts and technical assistance.
By understanding the manufacturing processes and quality assurance standards associated with used drink vending machines, B2B buyers can make informed decisions that ensure they acquire reliable and efficient products suited to their specific markets.
Related Video: Amazing coca cola manufacturing line – Inside the soft drink factory – Filling Machine
Comprehensive Cost and Pricing Analysis for used drink vending machines Sourcing
When sourcing used drink vending machines, understanding the cost structure and pricing dynamics is essential for B2B buyers, especially those operating in diverse international markets such as Africa, South America, the Middle East, and Europe. This section provides a comprehensive breakdown of the cost components, price influencers, and strategic buyer tips.
Cost Components
-
Materials: The primary materials involved in used vending machines include metal frames, electronic components, refrigeration units, and dispensers. The condition and quality of these materials significantly influence the overall cost. Machines in better condition or made from higher-quality materials will command higher prices.
-
Labor: Labor costs encompass the workforce involved in disassembling, refurbishing, and testing the machines. The hourly wage varies by region and can be a major component of total costs, particularly in markets with higher labor costs.
-
Manufacturing Overhead: This includes indirect costs associated with production, such as utilities, rent, and administrative expenses. For used machines, overhead might be lower if sourced from suppliers who specialize in refurbishment.
-
Tooling: Specialized tools for refurbishing machines can add to costs, especially if new components need to be fabricated. Buyers should inquire about the extent of refurbishment to understand tooling expenses better.
-
Quality Control (QC): Ensuring that the machines meet industry standards involves quality inspections and testing, which incur additional costs. A rigorous QC process can enhance the reliability of the vending machines but may also increase the price.
-
Logistics: Transportation costs for shipping used vending machines can vary greatly based on distance, mode of transport, and any potential tariffs or customs fees. Logistics should be carefully planned to mitigate unexpected expenses.
-
Margin: Suppliers typically add a profit margin to cover their costs and earn a profit. This margin can fluctuate based on market demand, competition, and the supplier’s position in the supply chain.
Price Influencers
-
Volume/MOQ: The minimum order quantity (MOQ) and the overall volume of the purchase can significantly affect pricing. Bulk purchases often lead to discounts, making it more cost-effective for buyers.
-
Specifications/Customization: Machines that require specific customizations or enhancements can be more expensive. Buyers should clearly define their requirements to avoid unexpected costs.
-
Materials and Quality/Certifications: The quality of components and any certifications (e.g., energy efficiency) can influence the price. Machines that meet higher standards may be priced at a premium but can offer better performance and lower operational costs.
-
Supplier Factors: The reputation, reliability, and location of the supplier can also affect pricing. Established suppliers may charge more due to their proven track record, while new entrants might offer lower prices to gain market share.
-
Incoterms: Understanding the International Commercial Terms (Incoterms) is crucial. They determine who is responsible for shipping, insurance, and tariffs, which can impact the overall cost structure.
Buyer Tips
-
Negotiation: Leverage your purchase volume to negotiate better prices. Suppliers are often willing to offer discounts for larger orders.
-
Cost-Efficiency: Analyze the total cost of ownership, not just the initial purchase price. Consider maintenance, energy consumption, and potential downtime when evaluating machines.
-
Pricing Nuances: Be aware of regional pricing differences. For instance, prices may vary significantly between Europe and Africa due to local market conditions and demand.
-
Supplier Research: Conduct thorough due diligence on suppliers. Check reviews, request references, and ensure they have a history of delivering quality machines.
-
Currency Fluctuations: For international purchases, consider the impact of currency exchange rates on pricing. Locking in prices at favorable rates can save costs.
Disclaimer
All prices mentioned in this analysis are indicative and can vary based on the specific circumstances surrounding each purchase. Always consult with suppliers for the most accurate and up-to-date pricing information.
Spotlight on Potential used drink vending machines Manufacturers and Suppliers
This section offers a look at a few manufacturers active in the ‘used drink vending machines’ market. This is a representative sample for illustrative purposes; B2B buyers must conduct their own extensive due diligence before any engagement. Information is synthesized from public sources and general industry knowledge.
Essential Technical Properties and Trade Terminology for used drink vending machines
Key Technical Properties of Used Drink Vending Machines
When considering the purchase of used drink vending machines, several critical specifications play a significant role in the decision-making process. Understanding these properties can help buyers ensure they are making a sound investment.
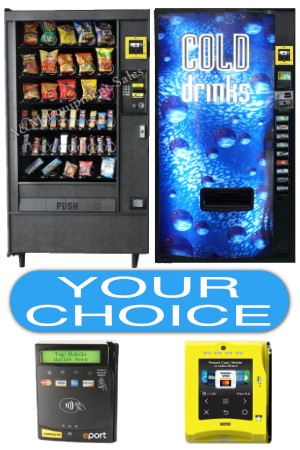
Illustrative Image (Source: Google Search)
-
Material Grade
– Vending machines are typically constructed from stainless steel or high-grade plastics. Stainless steel is preferred for its durability, resistance to corrosion, and ease of cleaning. The material grade affects the longevity and maintenance costs of the machine. For B2B buyers, selecting machines made from high-quality materials can lead to lower total cost of ownership over time. -
Capacity
– This refers to the number of products a vending machine can hold, usually measured in units or liters. Capacity is crucial for businesses that anticipate high foot traffic or have a large customer base. A machine with higher capacity minimizes restocking frequency, thus reducing operational downtime. -
Power Consumption
– Understanding the energy efficiency of a vending machine is essential, especially in regions with high electricity costs. Machines with lower power consumption can significantly reduce operational costs. B2B buyers should inquire about the energy rating and consider machines that offer energy-saving features. -
Temperature Range
– This specification indicates the machine’s ability to maintain specific temperatures for beverages. A wider temperature range allows for better preservation of drink quality. Buyers in hot climates or regions with diverse beverage offerings should prioritize machines that can effectively manage temperature variations. -
User Interface
– The design and functionality of the user interface affect customer experience. Touchscreens, payment options (credit card, mobile payments), and language settings are important features that can enhance usability. An intuitive interface can lead to higher sales and customer satisfaction.
Common Trade Terminology in Vending Machine Procurement
Understanding industry jargon is vital for effective communication and negotiation in the B2B marketplace. Here are some key terms related to the procurement of used drink vending machines:
-
OEM (Original Equipment Manufacturer)
– This term refers to companies that produce parts and equipment that may be marketed by another manufacturer. In the vending machine industry, knowing the OEM can help buyers assess the quality and compatibility of parts, especially for repairs or upgrades. -
MOQ (Minimum Order Quantity)
– MOQ is the smallest number of units a supplier is willing to sell. For buyers, understanding MOQ is essential to manage inventory costs and ensure they are purchasing an adequate quantity to meet demand without overcommitting financially. -
RFQ (Request for Quotation)
– An RFQ is a document issued by a buyer to solicit price quotes from suppliers. It typically includes specifications, quantities, and delivery requirements. B2B buyers should prepare detailed RFQs to ensure they receive accurate pricing and terms from potential vendors. -
Incoterms (International Commercial Terms)
– These are a set of predefined commercial terms published by the International Chamber of Commerce (ICC) that define the responsibilities of buyers and sellers in international trade. Familiarity with Incoterms helps buyers understand shipping responsibilities, risk management, and cost allocation. -
Lead Time
– This term refers to the amount of time it takes from placing an order until it is fulfilled. For used vending machines, lead time can affect inventory management and operational planning. Buyers should consider lead times when making purchasing decisions, especially if they have specific deadlines to meet.
By grasping these technical properties and trade terminologies, international B2B buyers can make informed decisions that align with their operational needs and market demands. This knowledge not only enhances negotiation capabilities but also facilitates smoother transactions in the used drink vending machine market.
Navigating Market Dynamics, Sourcing Trends, and Sustainability in the used drink vending machines Sector
Market Overview & Key Trends
The global market for used drink vending machines is experiencing a significant transformation, driven by several key factors. First, the rising demand for convenient beverage options has led to an increase in the deployment of vending machines in various sectors, including hospitality, education, and corporate environments. International B2B buyers, particularly from Africa, South America, the Middle East, and Europe, are increasingly recognizing the potential of vending machines as a cost-effective solution for improving customer service and enhancing operational efficiency.
Emerging technologies are revolutionizing the vending machine landscape. Features such as cashless payment systems, IoT connectivity, and smart inventory management are becoming essential. These advancements allow businesses to track sales in real-time and manage stock levels efficiently, thus reducing operational costs. For buyers, understanding these tech trends is crucial for selecting machines that align with their business models.
Additionally, market dynamics are influenced by regional trends. For instance, in Europe, there is a strong emphasis on sustainability and eco-friendly practices, while in Africa and South America, the focus might be more on affordability and accessibility. Buyers must adapt their sourcing strategies to consider these varying priorities and local market conditions.
Sustainability & Ethical Sourcing in B2B
Sustainability has become a cornerstone of the used drink vending machine sector. As global awareness of environmental issues grows, buyers are increasingly prioritizing eco-friendly practices in their procurement processes. This includes selecting machines that are energy-efficient and made from sustainable materials. The environmental impact of vending machines extends beyond their operation; the sourcing of materials and components is equally significant.
Ethical supply chains are essential for fostering trust and transparency. Buyers should look for vendors who provide clear information about the sourcing of their materials, ensuring that they are not contributing to environmental degradation or unethical labor practices. Certifications such as ISO 14001 (Environmental Management) and Fair Trade can serve as indicators of a supplier’s commitment to sustainable practices.
Moreover, opting for machines that utilize recyclable materials or are designed for easy disassembly can significantly reduce waste. As consumers increasingly favor brands that demonstrate environmental responsibility, B2B buyers should align their purchasing decisions with these values to enhance their brand reputation and meet consumer expectations.
Brief Evolution/History
The evolution of vending machines dates back to the early 1880s when the first coin-operated machines were introduced in London. Initially focused on dispensing postcards and chewing gum, the concept expanded over the decades to include a variety of products, including drinks. The 1990s saw the introduction of electronic vending machines, which laid the groundwork for the modern era of smart vending solutions.
Today, the market has evolved to meet the needs of a diverse global consumer base, with machines that can offer everything from healthy beverages to gourmet snacks. This historical context is vital for B2B buyers as it highlights the ongoing innovation within the sector and the importance of adapting to consumer preferences and technological advancements. Understanding this evolution can help buyers make informed decisions when sourcing used drink vending machines that will remain relevant and competitive in the marketplace.
Related Video: International Trade 101 | Economics Explained
Frequently Asked Questions (FAQs) for B2B Buyers of used drink vending machines
-
What should I consider when vetting suppliers for used drink vending machines?
When vetting suppliers, focus on their track record and reputation in the market. Look for verified reviews and testimonials from previous clients. Ensure the supplier has the necessary certifications and compliance with international trade regulations. Request detailed product specifications and maintenance records for the machines. It’s also beneficial to communicate directly with the supplier to gauge their responsiveness and willingness to address your specific needs. -
Can I customize used drink vending machines to fit my brand?
Yes, many suppliers offer customization options for used drink vending machines. This can include branding elements such as logos, color schemes, and specific product selections. When discussing customization, be clear about your requirements and ask for samples or mock-ups if available. Be mindful that customization may affect the lead time and costs, so ensure you understand these aspects before finalizing your order. -
What are the typical minimum order quantities (MOQ) and lead times for used vending machines?
Minimum order quantities can vary significantly between suppliers, often ranging from one machine to several units. Lead times typically depend on the customization level and the supplier’s inventory. On average, expect a lead time of 2-6 weeks for standard orders. For customized machines, it may take longer, so always confirm these details upfront to align with your project timelines. -
What payment terms should I expect when purchasing used drink vending machines?
Payment terms can differ based on the supplier’s policies and your negotiation. Common practices include a deposit upfront (usually 30-50% of the total order) with the balance due upon delivery or installation. Some suppliers may offer financing options or payment plans. Always ensure that payment terms are clearly defined in the contract to avoid any misunderstandings. -
How can I ensure the quality and reliability of used vending machines?
To ensure quality, request comprehensive quality assurance (QA) documentation from the supplier, including inspection reports and maintenance histories. It’s advisable to ask for warranties or guarantees on the machines, which can indicate the supplier’s confidence in their products. If possible, arrange for a site visit to inspect the machines before purchase or request videos showcasing their operational status. -
What certifications should used drink vending machines have?
Look for certifications relevant to your market, such as CE marking in Europe or UL certification in North America, which indicate compliance with safety and performance standards. Depending on your region, additional certifications may be required to meet local health and safety regulations. Ensure that the supplier provides documentation for these certifications as part of your procurement process. -
What logistics considerations should I keep in mind when importing used vending machines?
Logistics can be complex, especially for international shipments. Confirm the supplier’s shipping methods and whether they handle customs clearance. Assess freight costs and delivery times, and consider insurance options to protect your investment during transit. Collaborate with a reliable logistics partner familiar with international trade regulations to ensure smooth delivery and compliance. -
How should I handle disputes or issues with suppliers?
Establish clear communication channels with your supplier from the outset. In case of disputes, refer to the terms outlined in your contract, including return policies and warranty claims. Document all communications and agreements to have a record of interactions. If resolution cannot be reached directly, consider mediation or arbitration as a more amicable approach than litigation, which can be costly and time-consuming.
Strategic Sourcing Conclusion and Outlook for used drink vending machines
In conclusion, the strategic sourcing of used drink vending machines presents a unique opportunity for international B2B buyers, particularly in emerging markets across Africa, South America, the Middle East, and Europe. The key takeaways from this guide highlight the importance of thorough market research, supplier vetting, and cost-benefit analysis. Leveraging these strategies can significantly enhance procurement efficiency, reduce capital expenditures, and foster sustainable business practices.
Value in Strategic Sourcing:
By focusing on strategic sourcing, businesses can not only save costs but also ensure they acquire high-quality machines that meet their operational needs. Understanding regional market dynamics and supplier capabilities can also help mitigate risks associated with equipment quality and after-sales support.
As we look towards the future, the demand for innovative vending solutions is set to rise. International buyers are encouraged to explore partnerships with reputable suppliers, attend industry trade shows, and utilize digital platforms for sourcing. Embrace the potential of used vending machines as a viable solution for expanding your business’s beverage offerings.
Together, let’s navigate this evolving landscape and unlock new avenues for growth in the vending machine sector.