Your Ultimate Guide to Sourcing Pop Mart Vending Machine
Guide to Pop Mart Vending Machine
- Introduction: Navigating the Global Market for pop mart vending machine
- Understanding pop mart vending machine Types and Variations
- Key Industrial Applications of pop mart vending machine
- Strategic Material Selection Guide for pop mart vending machine
- In-depth Look: Manufacturing Processes and Quality Assurance for pop mart vending machine
- Comprehensive Cost and Pricing Analysis for pop mart vending machine Sourcing
- Spotlight on Potential pop mart vending machine Manufacturers and Suppliers
- Essential Technical Properties and Trade Terminology for pop mart vending machine
- Navigating Market Dynamics, Sourcing Trends, and Sustainability in the pop mart vending machine Sector
- Frequently Asked Questions (FAQs) for B2B Buyers of pop mart vending machine
- Strategic Sourcing Conclusion and Outlook for pop mart vending machine
Introduction: Navigating the Global Market for pop mart vending machine
In an era where convenience and efficiency are paramount, the demand for innovative retail solutions has surged globally. The pop mart vending machine stands at the forefront of this trend, offering businesses an agile way to engage customers, reduce operational costs, and optimize inventory management. Particularly for international B2B buyers in regions like Africa, South America, the Middle East, and Europe, these machines present a unique opportunity to tap into evolving consumer behaviors while enhancing service delivery.
This comprehensive guide is designed to equip you with critical insights into the pop mart vending machine market. We will explore various types of machines tailored to diverse consumer needs, the materials that ensure durability and functionality, and the manufacturing and quality control processes that guarantee reliability. Furthermore, we will provide a detailed overview of suppliers, cost considerations, and market trends that shape the landscape of vending solutions.
By delving into frequently asked questions and addressing common concerns, this guide empowers you to make informed sourcing decisions. Whether you are based in the bustling markets of Saudi Arabia or the vibrant cities of Spain, understanding the nuances of the pop mart vending machine ecosystem will position your business for success in a competitive marketplace. Prepare to navigate this dynamic sector with confidence, armed with the knowledge to enhance your operational strategy and meet customer expectations effectively.
Understanding pop mart vending machine Types and Variations
Type Name | Key Distinguishing Features | Primary B2B Applications | Brief Pros & Cons for Buyers |
---|---|---|---|
Standard Snack Vending Machine | Offers a variety of snacks and beverages | Offices, schools, and public spaces | Pros: Easy to stock; Cons: Limited product variety. |
Healthy Options Vending Machine | Focuses on nutritious snacks and drinks | Gyms, health clubs, corporate wellness | Pros: Appeals to health-conscious consumers; Cons: Higher cost. |
Electronic Payment Vending Machine | Accepts credit/debit cards and mobile payments | Airports, shopping malls, tech-savvy locations | Pros: Increased sales; Cons: Maintenance can be complex. |
Customized Merchandise Vending Machine | Sells branded or unique merchandise | Events, concerts, promotional spaces | Pros: High margin potential; Cons: Inventory management can be challenging. |
Interactive Vending Machine | Features touch screens and interactive displays | Tech hubs, educational institutions | Pros: Engaging user experience; Cons: Higher initial investment. |
Standard Snack Vending Machine
The Standard Snack Vending Machine is designed to dispense a wide range of snacks and beverages, making it a versatile choice for various environments. Commonly found in offices, schools, and public spaces, these machines are user-friendly and easy to stock. For B2B buyers, the main considerations include the machine’s capacity, the range of products offered, and the ease of maintenance. While they provide a straightforward solution, the limited variety may not meet the needs of more diverse consumer bases.
Healthy Options Vending Machine
A Healthy Options Vending Machine focuses on providing nutritious snacks and beverages, catering to a growing market of health-conscious consumers. These machines are particularly suitable for gyms, health clubs, and corporate wellness programs, where the demand for healthy choices is high. Buyers should consider factors such as product sourcing, pricing strategies, and potential partnerships with health brands. Although these machines can command a higher price point, they also attract a dedicated clientele willing to pay for premium options.
Electronic Payment Vending Machine
The Electronic Payment Vending Machine is equipped to accept credit/debit cards and mobile payments, making it ideal for high-traffic locations like airports and shopping malls. This type of machine enhances the purchasing experience and can lead to increased sales due to the convenience offered to consumers. B2B buyers should assess transaction fees, payment processing reliability, and the machine’s compatibility with existing systems. While the potential for higher sales is appealing, maintenance and technical support can become complex.
Customized Merchandise Vending Machine
A Customized Merchandise Vending Machine sells branded or unique merchandise, making it a perfect fit for events, concerts, and promotional spaces. This machine allows businesses to leverage their brand identity and engage directly with consumers. Key purchasing considerations include inventory management, branding opportunities, and the machine’s ability to handle various product types. Although this option can yield high margins, effective inventory control is crucial to prevent overstocking or stockouts.
Interactive Vending Machine
The Interactive Vending Machine features touch screens and engaging displays, providing an immersive user experience. These machines are particularly effective in tech hubs and educational institutions, where interactivity can enhance customer engagement. B2B buyers should evaluate the technology’s reliability, user interface design, and potential content updates. While the initial investment may be higher, the potential for increased customer interaction and sales can justify the cost.
Related Video: Machine Learning in 2024 – Beginner’s Course
Key Industrial Applications of pop mart vending machine
Industry/Sector | Specific Application of pop mart vending machine | Value/Benefit for the Business | Key Sourcing Considerations for this Application |
---|---|---|---|
Retail | Automated product dispensing | Increases customer convenience and reduces labor costs | Machine size, payment options, and product compatibility |
Hospitality | Guest amenities distribution | Enhances guest experience and satisfaction | Product selection, machine aesthetics, and maintenance support |
Education | Snack and beverage provision | Provides quick access to refreshments for students | Energy efficiency, product variety, and security features |
Transportation | On-the-go food and beverage services | Captures impulse purchases and meets traveler needs | Location feasibility, supply chain logistics, and machine durability |
Healthcare | Medical supplies and convenience items | Improves access to essential items for patients/staff | Compliance with health regulations, product safety, and machine hygiene |
Retail Applications
In the retail sector, pop mart vending machines serve as automated product dispensers, allowing businesses to offer a wide range of products without the need for extensive staffing. This application is particularly beneficial for urban areas where foot traffic is high, enabling quick and convenient purchases. Buyers should consider machine size, payment options, and product compatibility to ensure seamless integration into their retail space. Additionally, the ability to customize offerings based on local preferences can enhance sales and customer loyalty.
Hospitality Applications
In the hospitality industry, pop mart vending machines can be strategically placed in hotels and resorts to distribute guest amenities like snacks, beverages, and personal care items. This enhances the guest experience by providing easy access to essentials at any time, thus improving overall satisfaction. For international buyers, product selection, machine aesthetics, and ongoing maintenance support are critical factors to consider, ensuring that the vending solutions align with brand standards and customer expectations.
Education Applications
Pop mart vending machines in educational institutions cater to the needs of students and staff by providing easy access to snacks and beverages. This application addresses the demand for quick refreshment options during busy school hours. When sourcing these machines, buyers should prioritize energy efficiency, product variety, and security features to ensure a reliable and safe service. Additionally, understanding the dietary preferences of the student population can enhance the machine’s appeal.
Transportation Applications
In the transportation sector, pop mart vending machines are ideal for airports, bus stations, and train terminals, offering on-the-go food and beverage services. This application captures impulse purchases from travelers in transit, fulfilling their immediate needs for refreshments. Buyers must consider location feasibility, supply chain logistics, and machine durability to withstand high usage and varying environmental conditions. Ensuring the machines are stocked with popular and healthy options can significantly boost sales.
Healthcare Applications
Pop mart vending machines in healthcare settings provide essential medical supplies and convenience items for patients and staff. This application addresses the need for quick access to items like over-the-counter medications, snacks, and personal hygiene products. For B2B buyers in this sector, compliance with health regulations, product safety, and machine hygiene are paramount considerations. Implementing features such as contactless payment and regular maintenance can further enhance the reliability and trustworthiness of these vending solutions.
Related Video: How to Start a Vending Machine Business, Cost, Tips, How Much You Make
Strategic Material Selection Guide for pop mart vending machine
When selecting materials for pop mart vending machines, it is essential to consider various factors that impact performance, durability, and cost. Below is an analysis of four common materials used in the manufacturing of these machines, tailored specifically for international B2B buyers from regions such as Africa, South America, the Middle East, and Europe.
1. Stainless Steel
Key Properties: Stainless steel is known for its excellent corrosion resistance, high strength, and ability to withstand a wide range of temperatures. It typically has a temperature rating of up to 800°F (427°C) and is suitable for high-pressure applications.
Pros & Cons: The primary advantage of stainless steel is its durability and low maintenance requirements, making it ideal for outdoor and high-traffic environments. However, it can be more expensive than other materials, and its manufacturing process can be complex, potentially leading to longer lead times.
Impact on Application: Stainless steel is particularly compatible with various media, including food and beverages, due to its non-reactive nature. This makes it a preferred choice for vending machines that dispense consumables.
Considerations for International Buyers: Compliance with food safety standards is crucial, especially in regions like Europe, where regulations are stringent. Buyers should ensure that the stainless steel used meets standards such as ASTM A240 or EN 10088.
2. Mild Steel
Key Properties: Mild steel offers good strength and ductility, with a typical yield strength of around 250 MPa. However, it lacks inherent corrosion resistance and is generally rated for lower temperature applications.
Pros & Cons: Mild steel is cost-effective and easy to work with, making it suitable for high-volume production. On the downside, it requires protective coatings to prevent rust, which can add to long-term maintenance costs.
Impact on Application: While mild steel can be used for structural components of vending machines, it is not suitable for direct contact with consumables unless adequately coated.
Considerations for International Buyers: Buyers in regions with high humidity or coastal environments, such as parts of South America and the Middle East, should be cautious about using mild steel without adequate protective measures. Compliance with local standards like ASTM A36 is also advisable.
3. Aluminum
Key Properties: Aluminum is lightweight, with excellent corrosion resistance and a temperature rating of up to 400°F (204°C). It also has good thermal conductivity, which can be beneficial for temperature-sensitive products.
Pros & Cons: The lightweight nature of aluminum makes it easy to transport and install. However, it is less strong than stainless steel and can be more expensive than mild steel, depending on the grade.
Impact on Application: Aluminum is suitable for components that require frequent handling and transportation, such as the outer shell of vending machines. Its corrosion resistance makes it a good choice for outdoor applications.
Considerations for International Buyers: Buyers should ensure that the aluminum used complies with standards such as ASTM B221 for extrusions and that it is suitable for the specific climate conditions of their region.
4. Polycarbonate
Key Properties: Polycarbonate is a high-performance plastic known for its impact resistance and transparency. It can withstand temperatures up to 270°F (132°C) and is lightweight.
Pros & Cons: The primary advantage of polycarbonate is its ability to provide visibility for products inside the vending machine, enhancing customer interaction. However, it may not be as durable as metals in high-wear applications and can be susceptible to scratching.
Impact on Application: Polycarbonate is ideal for transparent panels and protective covers, allowing customers to see available products while protecting them from external elements.
Considerations for International Buyers: Buyers should verify that the polycarbonate used meets relevant safety standards, such as those outlined by ASTM D635 for flammability, especially in regions with strict safety regulations.
Summary Table
Material | Typical Use Case for pop mart vending machine | Key Advantage | Key Disadvantage/Limitation | Relative Cost (Low/Med/High) |
---|---|---|---|---|
Stainless Steel | Structural components, outer casing | Excellent corrosion resistance, durability | Higher cost, complex manufacturing | High |
Mild Steel | Structural frames, non-contact components | Cost-effective, easy to fabricate | Susceptible to corrosion, requires coating | Low |
Aluminum | Outer shell, structural elements | Lightweight, good corrosion resistance | Less strong than stainless steel | Medium |
Polycarbonate | Transparent panels, protective covers | High impact resistance, visibility | Less durable than metals, scratches easily | Medium |
In-depth Look: Manufacturing Processes and Quality Assurance for pop mart vending machine
Manufacturing Processes for Pop Mart Vending Machines
The manufacturing of Pop Mart vending machines involves several critical stages that ensure durability, efficiency, and user satisfaction. Understanding these processes is vital for international B2B buyers seeking to source high-quality machines.
Material Preparation
The initial stage involves the careful selection and preparation of materials. Common materials used include high-grade steel, aluminum, and durable plastics. These materials are chosen for their strength and resistance to wear and tear.
- Sourcing: Buyers should prioritize suppliers who source materials from reputable vendors to ensure quality.
- Pre-treatment: Materials undergo pre-treatment processes such as cleaning, coating, or galvanization to enhance durability and prevent corrosion.
Forming
Once materials are prepared, they are shaped and formed into the required components. This stage typically employs techniques such as:
- CNC Machining: Computer Numerical Control (CNC) machining ensures precision in cutting and shaping parts.
- Injection Molding: Used for plastic components, this process allows for complex shapes and high-volume production.
- Metal Fabrication: Techniques like laser cutting and bending are utilized for steel and aluminum parts.
Buyers should consider suppliers with advanced machinery and technology to achieve high precision in manufacturing.
Assembly
The assembly stage is where all individual components come together. This process often involves:
- Automated Assembly Lines: Automation increases efficiency and reduces human error.
- Manual Assembly: Certain components may require skilled labor for precise assembly, particularly in intricate parts.
Quality control during assembly is crucial, as this stage significantly impacts the final product’s functionality and aesthetics.
Finishing
The final stage of manufacturing involves finishing touches that enhance both the appearance and functionality of the vending machines. Key processes include:
- Painting and Coating: Protective coatings are applied to prevent rust and wear, while paint enhances aesthetics.
- Quality Inspection: Each machine undergoes a thorough inspection to ensure it meets design specifications and quality standards.
Quality Assurance in Manufacturing
Quality assurance (QA) is an integral part of the manufacturing process for Pop Mart vending machines. It ensures that products meet international standards and fulfill customer expectations.
International Standards
B2B buyers should be aware of the relevant international quality standards, including:
- ISO 9001: This standard focuses on quality management systems and is essential for suppliers aiming to demonstrate their commitment to quality.
- CE Marking: This certification indicates compliance with EU safety, health, and environmental protection standards.
These certifications are crucial for B2B buyers in regions like Europe and the Middle East, where compliance with local regulations is mandatory.
Industry-Specific Standards
In addition to general standards, industry-specific certifications may apply:
- API (American Petroleum Institute): Relevant for vending machines that dispense products related to the petroleum industry.
- RoHS (Restriction of Hazardous Substances): Ensures that electronic components are free from hazardous materials.
Quality Control Checkpoints
Quality control (QC) measures should be integrated at various stages of production:
- Incoming Quality Control (IQC): Materials are inspected upon arrival to ensure they meet specified quality criteria.
- In-Process Quality Control (IPQC): Ongoing inspections during manufacturing help catch defects early.
- Final Quality Control (FQC): A comprehensive check of the finished product ensures all specifications are met before shipment.
Buyers should inquire about the specific QC protocols employed by suppliers to ensure adherence to quality standards.
Common Testing Methods
Several testing methods are commonly used to evaluate the quality of vending machines:
- Functional Testing: Ensures that all mechanical and electronic components operate correctly.
- Durability Testing: Machines are subjected to stress tests to evaluate their resistance to wear and tear.
- Safety Testing: Checks for compliance with safety standards, particularly for electrical components.
Verifying Supplier Quality Control
For international B2B buyers, verifying a supplier’s quality control measures is essential for ensuring product reliability.
Audits
Conducting regular audits of the supplier’s manufacturing facilities can provide insights into their quality control processes. Buyers should look for:
- Third-Party Audits: Independent auditors can provide an unbiased assessment of quality practices.
- Supplier Self-Assessments: Suppliers should be encouraged to conduct their own assessments and share results.
Reports
Requesting detailed quality reports can help buyers understand the supplier’s performance over time. Key documents to review include:
- Inspection Reports: These documents detail the results of quality inspections at various stages.
- Non-Conformance Reports: Highlight any defects or issues and the corrective actions taken.
Third-Party Inspection
Engaging third-party inspection agencies can offer additional reassurance regarding quality. These agencies can perform:
- Pre-shipment Inspections: Verify that the products meet quality standards before they leave the factory.
- Random Sampling: Conduct checks on a random selection of machines to ensure consistent quality.
Quality Control Nuances for International Buyers
International buyers, particularly from regions like Africa, South America, the Middle East, and Europe, should consider specific nuances in quality control:
- Cultural Differences: Understanding local manufacturing practices and business cultures can enhance collaboration with suppliers.
- Import Regulations: Familiarize yourself with local regulations regarding product safety and quality standards in your region.
- Communication Barriers: Establish clear communication channels to address any quality concerns promptly.
By thoroughly understanding the manufacturing processes and quality assurance practices for Pop Mart vending machines, B2B buyers can make informed decisions, ensuring they source reliable and high-quality products that meet their market needs.
Related Video: SMART Quality Control for Manufacturing
Comprehensive Cost and Pricing Analysis for pop mart vending machine Sourcing
Understanding the Cost Structure of Pop Mart Vending Machines
When sourcing pop mart vending machines, it is crucial for international B2B buyers to understand the various cost components that contribute to the final pricing. This comprehensive analysis covers essential elements such as materials, labor, manufacturing overhead, tooling, quality control (QC), logistics, and profit margins.
Cost Components
-
Materials: The cost of raw materials is a significant factor in the overall pricing of vending machines. Common materials include steel for the frame, high-quality plastics for the casing, and electronic components for payment systems. Prices for these materials can fluctuate based on global market conditions, so it is essential to stay informed about commodity prices.
-
Labor: Labor costs vary significantly by region. For example, labor costs in Southeast Asia may be lower compared to Europe or North America. When sourcing from different regions, consider the local wage standards and productivity levels, which can impact the final product’s pricing.
-
Manufacturing Overhead: This encompasses the indirect costs associated with production, including utilities, rent, and administrative expenses. These costs can vary by manufacturer, so obtaining detailed quotes is advisable.
-
Tooling: The initial setup for production, including molds and specialized equipment, can be a substantial upfront investment. Buyers should inquire about tooling costs, especially if they require customized machines.
-
Quality Control (QC): Ensuring that the vending machines meet quality standards incurs additional costs. Implementing rigorous QC processes can enhance product reliability but may increase the overall price. Buyers should prioritize suppliers who demonstrate strong QC practices.
-
Logistics: Shipping costs can vary widely depending on the distance, mode of transportation, and current fuel prices. Incoterms can greatly influence logistics costs, so understanding the responsibilities of each party in the shipping process is essential.
-
Margin: Suppliers will typically add a profit margin to cover their expenses and generate profit. This margin can vary based on competition, brand reputation, and market demand.
Price Influencers
Several factors influence the pricing of pop mart vending machines:
-
Volume/MOQ: Purchasing in bulk often leads to significant discounts. Minimum Order Quantities (MOQs) should be negotiated to optimize pricing.
-
Specifications/Customization: Custom features, such as branding or specific product offerings, can increase costs. Be clear about your requirements to avoid unexpected expenses.
-
Materials and Quality/Certifications: Higher-quality materials and certifications (e.g., safety standards) can lead to increased costs. Assess the trade-off between quality and price carefully.
-
Supplier Factors: Supplier reputation, reliability, and financial stability can impact pricing. Consider long-term partnerships with reputable suppliers to ensure consistent quality and pricing.
-
Incoterms: Understanding the implications of different Incoterms (e.g., FOB, CIF) can help in estimating total costs, including shipping and insurance.
Buyer Tips for Cost Efficiency
-
Negotiation: Engage in open discussions with suppliers about pricing and terms. Leverage your purchasing power, especially if you represent a larger organization.
-
Total Cost of Ownership (TCO): Consider not only the initial purchase price but also the long-term costs associated with maintenance, repairs, and operation. A lower upfront cost may lead to higher TCO if quality is compromised.
-
Pricing Nuances for International Buyers: International buyers should be aware of currency fluctuations, tariffs, and import duties that can affect the final price. Building relationships with local suppliers can mitigate some of these risks.
-
Market Research: Conduct thorough market research to understand pricing trends in your specific region (e.g., Saudi Arabia, Spain) and align your expectations accordingly.
Disclaimer
The prices mentioned in this analysis are indicative and may vary based on market conditions, supplier negotiations, and specific project requirements. Always obtain detailed quotes from multiple suppliers to ensure competitive pricing.
Spotlight on Potential pop mart vending machine Manufacturers and Suppliers
This section offers a look at a few manufacturers active in the ‘pop mart vending machine’ market. This is a representative sample for illustrative purposes; B2B buyers must conduct their own extensive due diligence before any engagement. Information is synthesized from public sources and general industry knowledge.
Essential Technical Properties and Trade Terminology for pop mart vending machine
Key Technical Properties of Pop Mart Vending Machines
When considering the procurement of pop mart vending machines, understanding their technical specifications is crucial for ensuring optimal performance and longevity. Here are some essential properties to evaluate:
-
Material Grade
The material used in the construction of vending machines significantly impacts durability and resistance to environmental factors. Common materials include stainless steel and high-grade plastic. Stainless steel offers corrosion resistance, making it ideal for outdoor use in varied climates, while high-grade plastic can be lightweight and cost-effective. For B2B buyers, selecting the right material ensures the machine can withstand local conditions and user interactions. -
Capacity
Capacity refers to the number of items a vending machine can hold, typically measured in units or liters. This is critical for businesses targeting high-traffic areas where demand is expected to be substantial. A machine with a higher capacity can reduce the frequency of restocking, thus optimizing operational efficiency and minimizing downtime, which is vital for maximizing revenue. -
Power Consumption
Energy efficiency is a significant consideration for businesses looking to reduce operational costs. Power consumption ratings indicate how much electricity the vending machine will use over time. Machines with lower energy consumption not only reduce utility expenses but also align with sustainability goals, appealing to environmentally conscious buyers in regions like Europe and South America. -
User Interface
The design and functionality of the user interface, including touchscreen capabilities and payment methods (cash, credit card, mobile payment), are critical for enhancing user experience. A user-friendly interface can lead to higher transaction rates and customer satisfaction, which is particularly important in competitive markets. -
Temperature Control
For pop mart vending machines that dispense perishable items, temperature control is essential. Machines should maintain consistent temperature ranges to preserve product quality. Understanding the specifications regarding cooling systems and temperature settings can help buyers select machines that meet local health regulations and consumer expectations. -
Warranty and Support
The warranty period and the extent of technical support offered by the manufacturer are crucial for B2B buyers. A robust warranty can provide peace of mind and protect against unexpected repair costs. Buyers should seek vendors that offer comprehensive support services, including maintenance and troubleshooting, to ensure uninterrupted operation.
Common Trade Terms in Vending Machine Procurement
Familiarity with industry terminology can facilitate smoother transactions and negotiations. Here are several key terms relevant to the procurement of pop mart vending machines:
-
OEM (Original Equipment Manufacturer)
This term refers to companies that produce parts and equipment that may be marketed by another manufacturer. For B2B buyers, engaging with OEMs can ensure high-quality components and machines, as these manufacturers are often responsible for the design and production of the equipment. -
MOQ (Minimum Order Quantity)
MOQ is the smallest number of units a supplier is willing to sell. Understanding MOQ is essential for buyers as it can influence budgeting and inventory management. It’s important to negotiate this term to align with business needs, especially for smaller enterprises or those testing new markets. -
RFQ (Request for Quotation)
An RFQ is a document that solicits price quotes from suppliers for specific products or services. For B2B buyers, issuing an RFQ allows for comparison of costs and terms from multiple vendors, facilitating informed purchasing decisions and potentially leading to better pricing and contract terms. -
Incoterms (International Commercial Terms)
These are predefined commercial terms published by the International Chamber of Commerce (ICC) that define the responsibilities of buyers and sellers in international transactions. Understanding Incoterms is crucial for managing shipping costs, risks, and delivery responsibilities, especially for international buyers from Africa, South America, and the Middle East. -
Lead Time
Lead time refers to the time it takes from placing an order to receiving the product. It is a critical factor for B2B buyers who need to plan inventory and ensure timely availability of products. Buyers should clarify lead times with suppliers to align their operational schedules. -
Freight Forwarding
This term describes the process of organizing shipments for individuals or corporations. For B2B buyers, understanding freight forwarding can help in managing logistics and ensuring that vending machines are transported efficiently and cost-effectively from the manufacturer to their destination.
By grasping these technical properties and trade terms, international B2B buyers can make informed decisions that enhance their purchasing strategy and operational efficiency in acquiring pop mart vending machines.
Navigating Market Dynamics, Sourcing Trends, and Sustainability in the pop mart vending machine Sector
Market Overview & Key Trends
The pop mart vending machine sector is experiencing robust growth, driven by evolving consumer preferences and technological advancements. One of the primary global drivers is the increasing demand for convenience, as consumers seek quick access to snacks, beverages, and other retail products. This trend is particularly prominent in urban areas across Africa, South America, the Middle East, and Europe, where busy lifestyles necessitate efficient purchasing options.
Emerging technologies are reshaping the market dynamics. For instance, cashless payment systems, including mobile wallets and contactless transactions, are gaining traction, making vending machines more accessible and user-friendly. Additionally, the integration of IoT (Internet of Things) technology allows operators to monitor inventory levels and machine performance remotely, optimizing supply chain management and reducing operational costs. International B2B buyers should consider sourcing vending machines equipped with these technologies to stay competitive.
Moreover, sustainability is becoming a key consideration in the vending machine sector. With increasing awareness of environmental issues, consumers are gravitating toward eco-friendly products. This shift is prompting manufacturers to innovate in areas such as energy-efficient machines and biodegradable packaging. For buyers in regions like Saudi Arabia and Spain, partnering with suppliers who prioritize these trends can enhance their brand reputation and meet consumer expectations.
Sustainability & Ethical Sourcing in B2B
As the focus on sustainability intensifies, B2B buyers must prioritize environmentally responsible practices in their sourcing strategies. The pop mart vending machine sector is not exempt from this imperative; the environmental impact of manufacturing and operating vending machines is significant. Buyers should seek suppliers who utilize sustainable materials and practices, such as recyclable plastics and energy-efficient components, to minimize their carbon footprint.
Ethical supply chains are also crucial. Many consumers are becoming increasingly aware of the ethical implications of their purchases, prompting businesses to consider the socio-economic impacts of their sourcing decisions. This includes ensuring fair labor practices and supporting local economies, particularly in developing regions. Buyers should look for suppliers with transparent sourcing practices and certifications that demonstrate commitment to social responsibility.
Additionally, obtaining ‘green’ certifications can enhance a company’s credibility in the market. Certifications such as Energy Star or ISO 14001 can signal to consumers that a business is dedicated to sustainability. By aligning purchasing decisions with ethical sourcing and sustainability principles, B2B buyers can not only reduce environmental impact but also attract a growing segment of eco-conscious consumers.
Brief Evolution/History
The pop mart vending machine sector has evolved significantly since its inception in the early 20th century. Originally designed to dispense simple products, modern vending machines have transformed into sophisticated retail solutions that offer a wide array of goods, from gourmet snacks to electronics. This evolution has been fueled by technological advancements, particularly the integration of digital payment systems and smart technology.
In recent years, the sector has witnessed a shift towards customization and personalization, with machines that cater to specific consumer preferences. This trend is particularly relevant in diverse markets such as Africa and South America, where local tastes and cultural nuances play a significant role in consumer behavior. As the market continues to evolve, B2B buyers must stay informed about these historical shifts to leverage opportunities effectively and meet the changing demands of consumers.
Related Video: Global Trade & Logistics – What is Global Trade?
Frequently Asked Questions (FAQs) for B2B Buyers of pop mart vending machine
-
What key factors should I consider when vetting suppliers of pop mart vending machines?
When vetting suppliers, prioritize their industry experience, reputation, and reliability. Look for verified certifications such as ISO 9001 for quality management and check for any customer reviews or testimonials. Request references from previous clients, particularly those in your region, to gauge their satisfaction with product quality and service. Additionally, assess their financial stability to ensure they can fulfill large orders and provide ongoing support. -
Can I customize the pop mart vending machines to fit my brand?
Yes, most manufacturers offer customization options for pop mart vending machines. This can include branding elements such as logos, color schemes, and product selections tailored to your target market. When discussing customization, clarify the extent of modifications available and any associated costs. Ensure the supplier can meet your branding requirements without compromising the machine’s functionality or compliance with local regulations. -
What are the typical minimum order quantities (MOQs) and lead times for pop mart vending machines?
MOQs for pop mart vending machines can vary significantly based on the supplier and the complexity of the order. Generally, MOQs range from 10 to 50 units for customized orders. Lead times may also differ, typically ranging from 4 to 12 weeks depending on the supplier’s production capacity and your customization requests. Always confirm these details upfront to avoid unexpected delays in your supply chain.
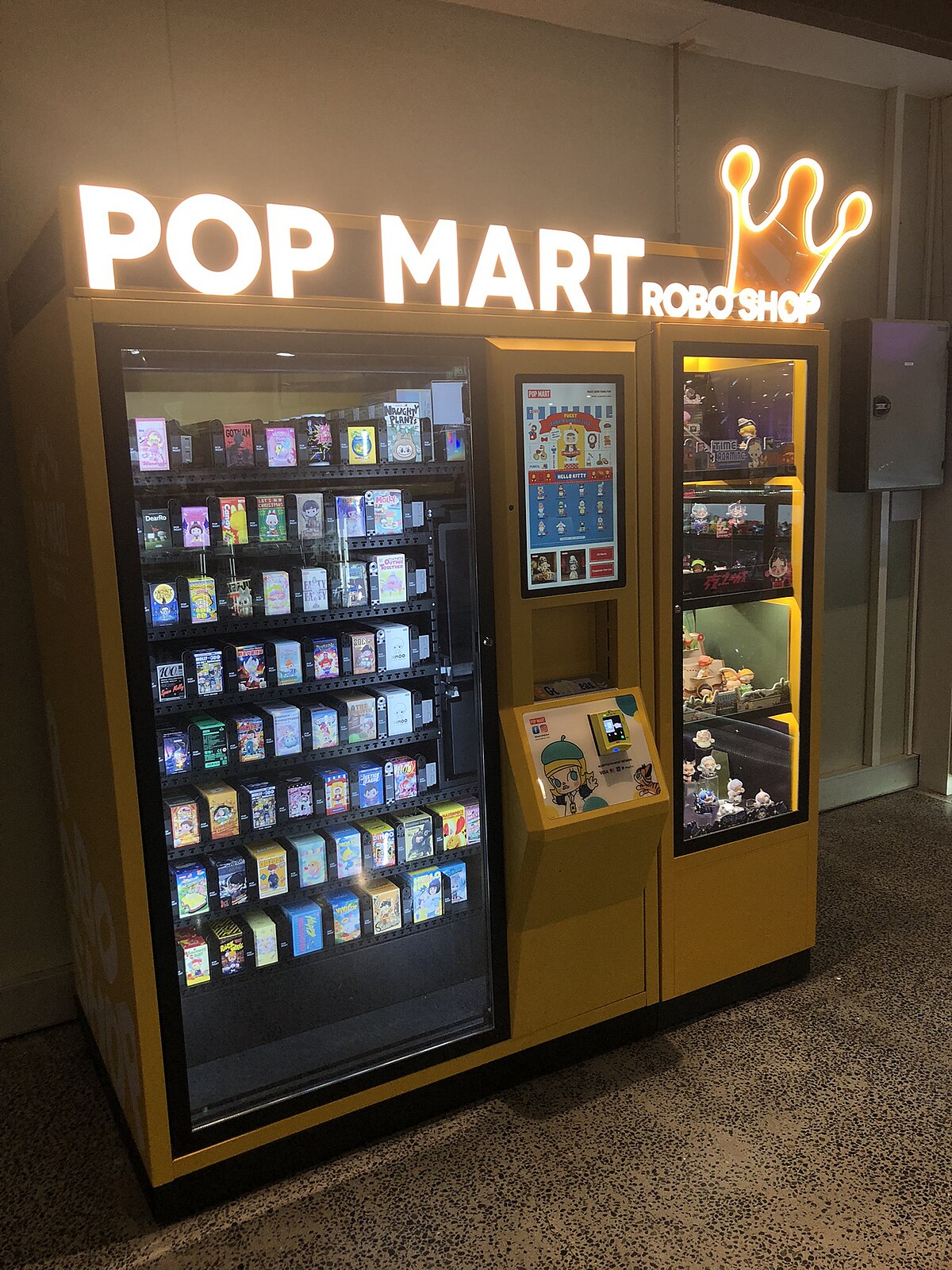
Illustrative Image (Source: Google Search)
-
What payment terms and methods should I expect when purchasing from international suppliers?
International suppliers often accept various payment methods, including wire transfers, letters of credit, and payment platforms like PayPal. Payment terms can vary, with options for partial upfront payments (30-50%) and the balance upon delivery. Ensure that you negotiate terms that protect your investment, and consider using escrow services for large transactions to mitigate risks. Always confirm currency exchange rates if dealing in different currencies. -
How do I ensure quality assurance and compliance certifications for the machines?
Request detailed quality assurance protocols from your supplier, including information on testing standards and inspection processes. Ensure that the machines comply with international safety and quality certifications, such as CE marking in Europe or UL certification in the USA. Ask for documentation proving compliance, and consider third-party inspections for added assurance, especially if you are importing the machines into your country. -
What logistics considerations should I keep in mind when importing pop mart vending machines?
Logistics plays a crucial role in the import process. Evaluate shipping methods (air vs. sea) based on your budget and urgency, and factor in customs clearance times. Collaborate with logistics providers experienced in handling vending machines to ensure proper handling and transport. Understand the import regulations in your country, including tariffs, duties, and required documentation to prevent delays at customs. -
How can I handle disputes or issues with suppliers effectively?
To manage disputes, maintain clear and documented communication throughout the purchasing process. Establish a contract that outlines terms, responsibilities, and dispute resolution procedures, such as mediation or arbitration. If issues arise, address them promptly and professionally, providing evidence and clear reasoning for your position. Building a good relationship with your supplier can also facilitate smoother resolutions and minimize conflicts. -
What are the common maintenance requirements for pop mart vending machines?
Regular maintenance is essential to ensure the longevity and functionality of pop mart vending machines. This includes routine cleaning, restocking products, and checking for mechanical issues. Establish a maintenance schedule with your supplier to receive guidance on best practices and recommended service intervals. Additionally, inquire about warranty coverage and support services available for repairs to ensure minimal downtime and continued operation.
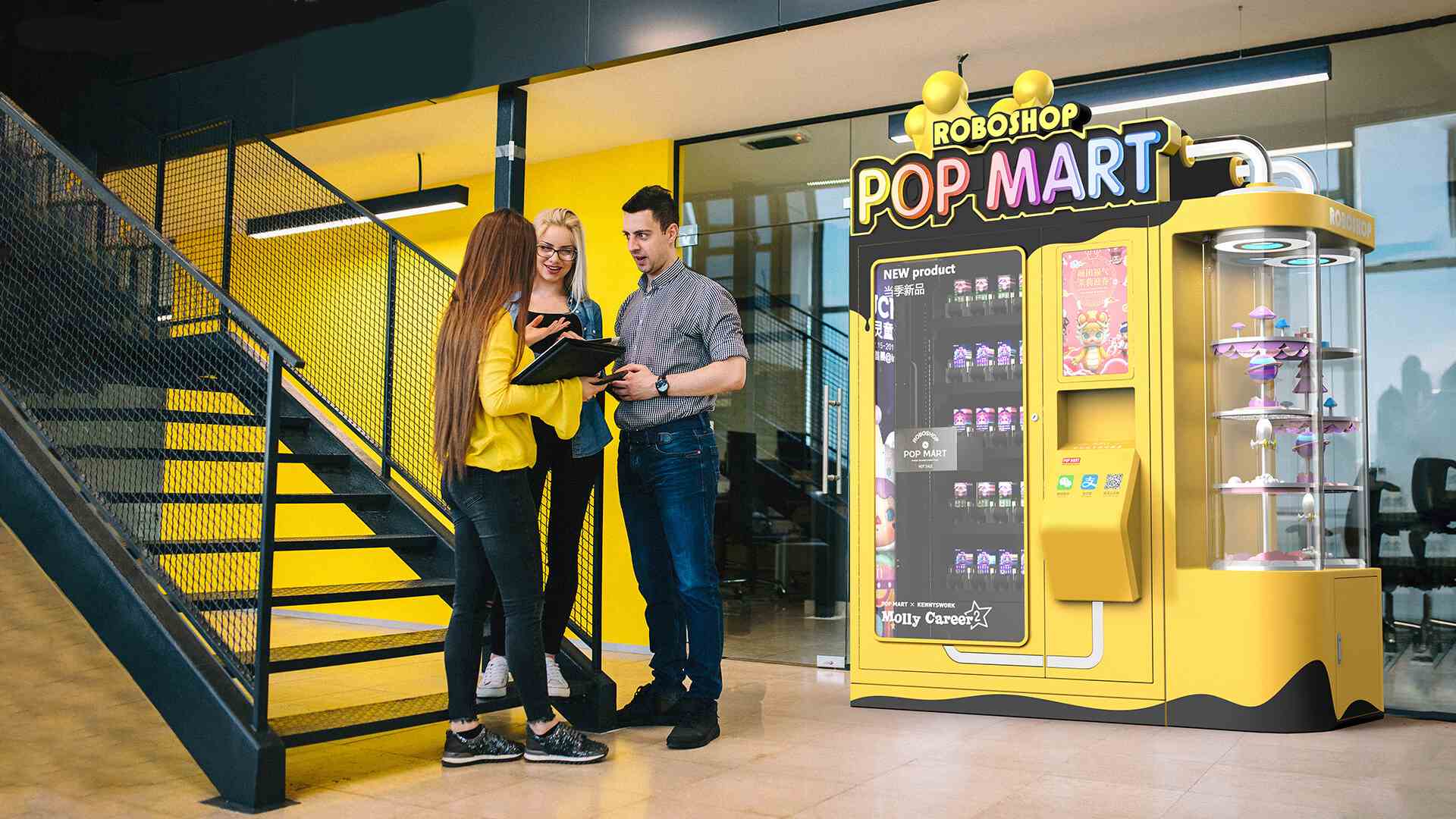
Illustrative Image (Source: Google Search)
Strategic Sourcing Conclusion and Outlook for pop mart vending machine
In summary, the strategic sourcing of Pop Mart vending machines presents significant opportunities for international B2B buyers, particularly in Africa, South America, the Middle East, and Europe. By focusing on key factors such as supplier reliability, technological innovation, and market adaptability, businesses can ensure a competitive edge in a rapidly evolving marketplace.
Key Takeaways:
– Supplier Selection: Prioritize suppliers with a proven track record of quality and service, as this will reduce operational risks and enhance customer satisfaction.
– Technology Integration: Invest in machines that incorporate the latest technology, such as cashless payment systems and IoT capabilities, to meet consumer demands and streamline operations.
– Market Trends: Stay informed about local market trends and consumer preferences, which can inform product offerings and location strategies.
As the vending machine market continues to evolve, the ability to adapt sourcing strategies will be crucial. Buyers are encouraged to engage with diverse suppliers and explore innovative solutions that align with their business goals. Embrace the future of vending technology and position your business for success in this dynamic landscape.