Master Soda Vending Machine Rental for Optimal Business
Guide to Soda Vending Machine Rental
- Introduction: Navigating the Global Market for soda vending machine rental
- Understanding soda vending machine rental Types and Variations
- Key Industrial Applications of soda vending machine rental
- Strategic Material Selection Guide for soda vending machine rental
- In-depth Look: Manufacturing Processes and Quality Assurance for soda vending machine rental
- Comprehensive Cost and Pricing Analysis for soda vending machine rental Sourcing
- Spotlight on Potential soda vending machine rental Manufacturers and Suppliers
- Essential Technical Properties and Trade Terminology for soda vending machine rental
- Navigating Market Dynamics, Sourcing Trends, and Sustainability in the soda vending machine rental Sector
- Frequently Asked Questions (FAQs) for B2B Buyers of soda vending machine rental
- Strategic Sourcing Conclusion and Outlook for soda vending machine rental
Introduction: Navigating the Global Market for soda vending machine rental
In today’s fast-paced global marketplace, the demand for convenient beverage solutions has surged, making soda vending machine rental an increasingly attractive option for businesses across various sectors. From bustling urban centers in Kenya to corporate offices in the UK, these machines not only provide instant access to refreshments but also enhance customer satisfaction and boost employee morale. As international B2B buyers navigate this landscape, understanding the intricacies of soda vending machine rental becomes essential.
This comprehensive guide offers a deep dive into the world of soda vending machine rental, covering critical areas such as types of machines available, materials used in their construction, manufacturing processes, quality control measures, and potential suppliers. Additionally, we will explore cost considerations, market trends, and frequently asked questions, equipping buyers with the knowledge needed to make informed sourcing decisions.
For businesses in Africa, South America, the Middle East, and Europe, this guide serves as a vital resource to optimize their vending solutions. By leveraging the insights provided, B2B buyers can confidently select the right machines to meet their operational needs, ensuring a seamless integration into their business environments. With a focus on empowering informed decisions, this guide not only highlights the benefits of vending machine rentals but also underscores their role in fostering efficient, customer-centric experiences.
Understanding soda vending machine rental Types and Variations
Type Name | Key Distinguishing Features | Primary B2B Applications | Brief Pros & Cons for Buyers |
---|---|---|---|
Traditional Soda Vending Machine | Offers a selection of popular soda brands and flavors | Offices, retail stores, schools | Pros: Familiarity, ease of use. Cons: Limited customization options, may require frequent restocking. |
Smart Vending Machines | Equipped with touch screens, cashless payment options, and inventory tracking | Airports, malls, high-traffic areas | Pros: Enhanced customer experience, real-time data analytics. Cons: Higher upfront costs, potential technical issues. |
Micro Markets | Combines vending with retail, allowing customers to browse and select items | Workplaces, universities, hospitals | Pros: Greater product variety, encourages impulse buying. Cons: Requires more space, higher maintenance needs. |
Customized Branded Machines | Tailored designs and product selections based on client branding | Corporate offices, events | Pros: Strong brand visibility, targeted marketing. Cons: Higher costs, longer lead times for setup. |
Eco-Friendly Vending Machines | Focus on sustainable practices, offering organic and low-sugar options | Health-conscious businesses, gyms | Pros: Attracts eco-aware consumers, aligns with corporate social responsibility goals. Cons: Limited product range, potentially higher prices. |
Traditional Soda Vending Machine
Traditional soda vending machines are the most common type found in various settings such as offices, schools, and retail stores. They typically offer a selection of popular soda brands and flavors, making them a familiar choice for consumers. B2B buyers should consider the frequency of restocking, as these machines may require regular maintenance to keep them stocked with popular items. While they are easy to use and maintain, their limited customization options can be a drawback for businesses looking to differentiate their offerings.
Smart Vending Machines
Smart vending machines are equipped with advanced technology features such as touch screens, cashless payment options, and inventory tracking capabilities. They are ideal for high-traffic areas like airports and malls, where enhancing customer experience is crucial. These machines allow businesses to gather real-time data on consumer preferences and sales trends, which can inform inventory decisions. However, B2B buyers should be prepared for higher upfront costs and potential technical issues that may arise with advanced technology.
Micro Markets
Micro markets offer a unique blend of vending and retail by providing an open area where customers can browse and select items, often including fresh food and beverages alongside traditional soda options. They are well-suited for workplaces, universities, and hospitals, where employees or students seek convenient access to snacks and drinks. The greater product variety can encourage impulse buying, but businesses must consider the space required and the higher maintenance needs associated with these setups.
Customized Branded Machines
Customized branded machines allow businesses to tailor the design and product selection to align with their branding. This type is particularly effective for corporate offices and events where brand visibility is essential. B2B buyers should weigh the benefits of targeted marketing against the higher costs and longer lead times for setup. These machines can create a unique customer experience, but they require careful planning and investment.
Eco-Friendly Vending Machines
Eco-friendly vending machines focus on sustainability by offering organic, low-sugar, or environmentally friendly products. They are particularly appealing to health-conscious businesses and gyms that want to attract eco-aware consumers. While these machines can enhance a company’s corporate social responsibility profile, buyers should be mindful of the potentially limited product range and higher prices associated with these options.
Related Video: How a soda machine works – Dixie Narco vending machine
Key Industrial Applications of soda vending machine rental
Industry/Sector | Specific Application of soda vending machine rental | Value/Benefit for the Business | Key Sourcing Considerations for this Application |
---|---|---|---|
Corporate Offices | Providing refreshments in break rooms | Enhances employee satisfaction and productivity | Machine capacity, variety of beverages, maintenance support |
Educational Institutions | Vending services in cafeterias and common areas | Convenient access to drinks for students and staff | Compliance with health regulations, payment options |
Hospitality | In-room vending for hotels and resorts | Increases guest convenience and ancillary revenue | Custom branding, product variety, service frequency |
Healthcare Facilities | Placement in waiting areas and lobbies | Improves patient and visitor experience | Health compliance, accessibility features, payment systems |
Events and Conferences | Rental for large gatherings and trade shows | Provides quick refreshments to attendees | Logistics support, delivery and pickup schedules, capacity |
Corporate Offices
Soda vending machine rentals in corporate offices serve as a vital amenity for employees. By providing easy access to beverages, companies can enhance employee satisfaction and productivity. This is particularly important in regions like Kenya and the UK, where workplace culture emphasizes well-being. Buyers should consider the machine’s capacity to handle high traffic, the variety of beverages offered, and the vendor’s maintenance support to ensure seamless operation.
Educational Institutions
In educational settings, soda vending machines are often placed in cafeterias and common areas, offering students and staff convenient access to drinks. This not only satisfies hydration needs but also contributes to a vibrant campus life. For international buyers in South America and Africa, ensuring compliance with local health regulations is crucial. Additionally, payment options should cater to the preferences of the student population, such as mobile payments or cashless systems.
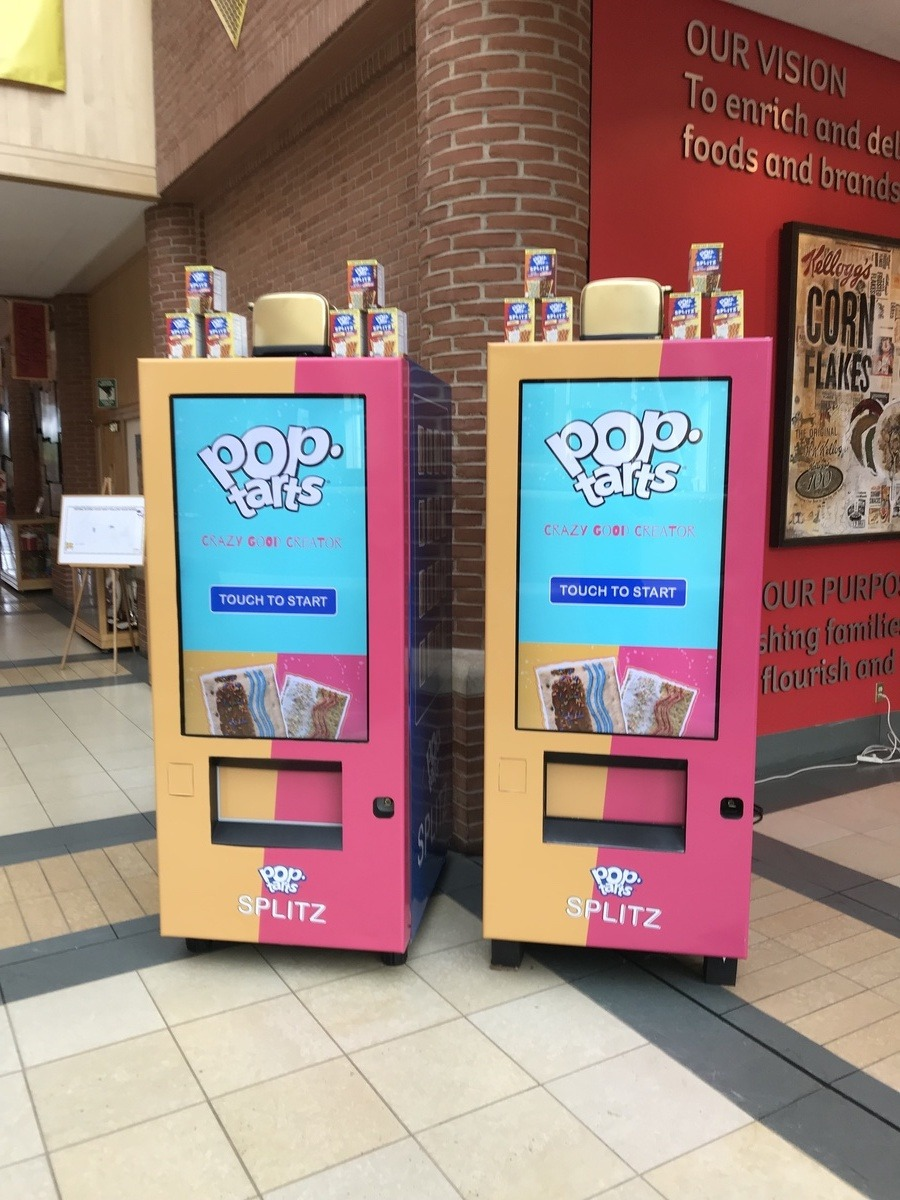
Illustrative Image (Source: Google Search)
Hospitality
Hotels and resorts can significantly benefit from in-room soda vending machines. This service enhances guest convenience by allowing them to enjoy refreshments without leaving their rooms. It can also generate additional revenue for the establishment. When sourcing these machines, hospitality buyers should focus on custom branding options, a diverse product range, and the frequency of service to keep inventory fresh.
Healthcare Facilities
Soda vending machines in healthcare facilities can be strategically placed in waiting areas and lobbies, improving the experience for patients and visitors. These machines provide a quick refreshment option, which can be especially valuable during long waits. Buyers from the healthcare sector should prioritize compliance with health regulations, ensuring that machines are accessible to all individuals, including those with disabilities. Payment systems must also be user-friendly and secure.
Events and Conferences
For large gatherings and trade shows, renting soda vending machines can streamline refreshment services, allowing attendees to quickly grab drinks as needed. This convenience can enhance the overall experience of participants. Buyers in this sector must consider logistics support, including delivery and pickup schedules, as well as the machine’s capacity to accommodate large crowds. Flexibility in service agreements can also be a key factor in successful sourcing.
Strategic Material Selection Guide for soda vending machine rental
When selecting materials for soda vending machines, it is crucial to consider their properties, advantages, and limitations, especially in diverse international markets. Below, we analyze four common materials used in the construction of soda vending machines, focusing on their performance characteristics and implications for B2B buyers from Africa, South America, the Middle East, and Europe.
1. Stainless Steel
Key Properties:
Stainless steel is known for its excellent corrosion resistance, high strength, and ability to withstand a wide range of temperatures and pressures. It typically has a temperature rating of up to 800°F (427°C) and can handle significant pressure, making it suitable for various environments.
Pros & Cons:
The durability of stainless steel is a significant advantage; it resists rust and staining, which is critical in high-humidity environments. However, it is more expensive than other materials, and manufacturing processes can be complex, leading to higher costs.
Impact on Application:
Stainless steel is compatible with various media, including carbonated beverages, and does not impart flavors or contaminants. Its robustness makes it ideal for machines exposed to the elements.
Considerations for International Buyers:
Buyers must ensure compliance with international standards such as ASTM A240 for stainless steel grades. In regions like Kenya or Brazil, local suppliers may offer alternatives that meet similar specifications at a lower cost.
2. Plastic (Polycarbonate)
Key Properties:
Polycarbonate is a lightweight, high-impact-resistant plastic that can withstand temperatures up to 250°F (121°C). It has good chemical resistance, making it suitable for contact with various beverages.
Pros & Cons:
The primary advantage of polycarbonate is its cost-effectiveness and ease of manufacturing. However, it is less durable than metals and can degrade under UV exposure, which may limit its lifespan in outdoor applications.
Impact on Application:
Polycarbonate is suitable for internal components and transparent panels, allowing visibility of the product. However, it may not be suitable for high-pressure applications.
Considerations for International Buyers:
Buyers should be aware of local regulations regarding plastic materials, particularly in Europe, where compliance with REACH regulations is mandatory. In regions like the Middle East, the heat can affect the material’s performance, necessitating careful selection.
3. Aluminum
Key Properties:
Aluminum is lightweight and has good corrosion resistance, with a melting point of approximately 1,220°F (660°C). It is also a good conductor of heat, which can be beneficial in cooling applications.
Pros & Cons:
Aluminum’s lightweight nature makes it easier to transport and install. However, it can be more expensive than steel and may require additional coatings to enhance corrosion resistance.
Impact on Application:
Aluminum is suitable for various components, including frames and panels. Its thermal properties can help in maintaining the temperature of beverages, but it may not be ideal for high-pressure environments without proper treatment.
Considerations for International Buyers:
Buyers in Europe should consider the European Aluminum Association standards for quality assurance. In South America, local sourcing of aluminum may offer cost advantages.
4. Carbon Steel
Key Properties:
Carbon steel is known for its high strength and durability, with a temperature rating of up to 1,200°F (649°C). It is less resistant to corrosion compared to stainless steel but can be treated with coatings.
Pros & Cons:
The primary advantage of carbon steel is its cost-effectiveness and strength. However, it is susceptible to rusting if not properly coated, which can lead to maintenance issues over time.
Impact on Application:
Carbon steel is suitable for structural components but may require protective coatings for use in humid environments. Its strength makes it ideal for heavy-duty applications.
Considerations for International Buyers:
Buyers should consider local environmental conditions when selecting carbon steel. In regions like Africa, where humidity can be high, proper treatment is essential to ensure longevity.
Summary Table
Material | Typical Use Case for soda vending machine rental | Key Advantage | Key Disadvantage/Limitation | Relative Cost (Low/Med/High) |
---|---|---|---|---|
Stainless Steel | Exterior panels, internal components | Excellent corrosion resistance | Higher cost, complex manufacturing | High |
Plastic (Polycarbonate) | Transparent panels, internal parts | Cost-effective, lightweight | Less durable, UV degradation | Low |
Aluminum | Frames, panels | Lightweight, good thermal properties | More expensive, requires coatings | Medium |
Carbon Steel | Structural components | High strength, cost-effective | Susceptible to corrosion without treatment | Low |
This strategic material selection guide provides B2B buyers with essential insights to make informed decisions when renting soda vending machines, taking into account the diverse requirements and standards across different international markets.
In-depth Look: Manufacturing Processes and Quality Assurance for soda vending machine rental
Manufacturing Processes for Soda Vending Machines
When considering the rental of soda vending machines, understanding the manufacturing processes is crucial for B2B buyers. The manufacturing process typically consists of several key stages: material preparation, forming, assembly, and finishing. Each stage plays a significant role in ensuring the quality and reliability of the vending machines.
Material Preparation
The first step in manufacturing soda vending machines involves sourcing and preparing high-quality materials. Common materials include:
- Metal: Steel and aluminum are often used for the machine’s frame and outer casing due to their durability and resistance to corrosion.
- Plastics: High-density polyethylene (HDPE) and polycarbonate are commonly used for internal components and display panels.
- Electronic components: These include circuit boards, sensors, and payment systems, which must meet specific performance standards.
Before proceeding to the next stage, materials undergo rigorous quality checks to ensure they meet industry specifications.
Forming
Once the materials are prepared, they are formed into their respective shapes. This stage can involve various techniques, such as:
- Stamping: Used for creating metal parts, stamping machines press sheets of metal into desired shapes.
- Injection Molding: This technique shapes plastic components by injecting molten plastic into molds.
- Laser Cutting: Precision laser cutting is employed to create intricate designs and openings for displays and buttons.
These forming techniques ensure that components fit together accurately and function effectively in the final product.
Assembly
The assembly stage is where the individual components come together. This process can be manual or automated, depending on the manufacturer’s capabilities. Key aspects include:
- Component Integration: All parts, including mechanical, electronic, and aesthetic elements, are assembled into a cohesive unit.
- Quality Control Checkpoints: Throughout assembly, manufacturers implement various quality checks to ensure components are correctly installed and functioning.
This step is critical in determining the overall performance and reliability of the vending machine.
Finishing
The finishing stage enhances the machine’s durability and appearance. This may include:
- Painting and Coating: Protective coatings are applied to prevent rust and corrosion, while paint provides aesthetic appeal.
- Labeling: Clear, attractive labeling is crucial for user interface and branding.
- Final Quality Inspections: Before leaving the factory, each machine undergoes final inspections to ensure it meets all design specifications and quality standards.
Quality Assurance in Manufacturing
Quality assurance (QA) is integral to the manufacturing process of soda vending machines. For international B2B buyers, understanding the QA protocols can provide confidence in the supplier’s reliability.
International Standards
Several international standards guide the quality assurance of vending machines:
- ISO 9001: This standard outlines criteria for a quality management system (QMS) and is applicable to any organization. It focuses on meeting customer expectations and delivering customer satisfaction.
- CE Marking: In Europe, the CE mark indicates compliance with health, safety, and environmental protection standards. Machines with this marking meet European Union regulations.
- API Standards: For vending machines that dispense specific products, compliance with American Petroleum Institute (API) standards may be relevant.
These certifications and standards help ensure that the vending machines are safe, reliable, and suitable for international markets.
Quality Control Checkpoints
Quality control (QC) is structured around several checkpoints during the manufacturing process:
- Incoming Quality Control (IQC): Materials are inspected upon arrival to ensure they meet required specifications.
- In-Process Quality Control (IPQC): Ongoing checks during production monitor for defects and ensure adherence to quality standards.
- Final Quality Control (FQC): Comprehensive inspections are conducted on finished products before shipping. This includes functionality tests and visual inspections.
These checkpoints are essential for identifying and rectifying issues early in the manufacturing process.
Common Testing Methods
To verify the quality of soda vending machines, several testing methods are commonly employed:
- Functional Testing: Ensures that all components operate as intended, including payment systems and cooling mechanisms.
- Durability Testing: Simulates real-world usage to assess the machine’s resilience and longevity.
- Safety Testing: Checks for electrical safety, ensuring compliance with relevant safety standards.
Verifying Supplier Quality Control
For B2B buyers, particularly from regions like Africa, South America, the Middle East, and Europe, verifying a supplier’s quality control processes is essential. Here are actionable steps:
- Conduct Audits: Regular audits of the manufacturing facilities can provide insights into the operational standards and quality practices.
- Request Quality Reports: Suppliers should provide documentation of their quality control processes, including testing results and compliance certifications.
- Engage Third-Party Inspectors: Hiring independent inspectors can offer an unbiased assessment of the supplier’s manufacturing practices and product quality.
Quality Control Nuances for International Buyers
International buyers must be aware of specific nuances in quality control when sourcing soda vending machines:
- Regulatory Compliance: Ensure that the machines comply with both local and international regulations, which may vary significantly between regions.
- Cultural Considerations: Different regions may have unique expectations regarding product features, branding, and customer service. Understanding these can aid in selecting the right supplier.
- Language Barriers: Clear communication is vital. Ensure that all specifications and standards are understood by both parties to avoid discrepancies.
Conclusion
Understanding the manufacturing processes and quality assurance practices for soda vending machines is essential for B2B buyers. By focusing on material preparation, forming, assembly, and finishing, as well as leveraging international standards and rigorous quality checks, buyers can make informed decisions that ensure they receive reliable and high-quality vending machines suitable for their markets.
Related Video: How Coca-Cola Is Made In Factory | Coca-Cola Factory Process
Comprehensive Cost and Pricing Analysis for soda vending machine rental Sourcing
The cost structure and pricing for soda vending machine rental are influenced by several key components that international B2B buyers should understand to make informed purchasing decisions.
Cost Components
-
Materials: The primary cost driver in vending machine rentals is the materials used in the machines themselves. This includes the body, cooling systems, payment systems, and other components. The quality of materials directly affects durability and performance, which are critical for long-term use.
-
Labor: Labor costs encompass both the assembly of the machines and ongoing maintenance. In regions with higher labor costs, such as Europe, this can significantly impact rental prices. For buyers in Africa and South America, where labor costs may be lower, this could provide an opportunity for cost savings.
-
Manufacturing Overhead: This includes expenses related to the production process, such as utilities, rent, and equipment depreciation. Understanding the manufacturer’s overhead can provide insights into pricing strategies.
-
Tooling: Customization of vending machines often requires specialized tooling. If buyers need machines tailored to specific requirements, this could increase costs.
-
Quality Control (QC): Effective QC processes ensure product reliability and compliance with safety standards. The cost of implementing rigorous QC measures is often passed on to the buyer.
-
Logistics: Shipping and handling costs can vary dramatically depending on the destination. Incoterms also play a crucial role in determining who bears these costs, impacting the overall price for the buyer.
-
Margin: Suppliers typically include a profit margin in their pricing. This margin can vary based on the supplier’s market positioning and the competitive landscape.
Price Influencers
Several factors can influence the pricing of soda vending machine rentals:
-
Volume/MOQ: Higher order volumes often lead to lower unit costs. Buyers should negotiate terms based on expected usage to maximize savings.
-
Specifications/Customization: Custom features or specifications can increase costs. Buyers should clearly define their needs to avoid unexpected expenses.
-
Materials Quality/Certifications: Machines made with higher-quality materials or those that meet specific certifications may come at a premium. Buyers should weigh the benefits of quality against the costs.
-
Supplier Factors: The reputation and reliability of suppliers can influence pricing. Established brands may charge more due to perceived value, while less known suppliers might offer competitive pricing to gain market share.
-
Incoterms: Understanding the implications of different Incoterms (e.g., FOB, CIF) is crucial, as they determine shipping responsibilities and costs, affecting the total price.
Buyer Tips
-
Negotiation: Engage suppliers in discussions about pricing, especially for larger orders. Leverage your purchasing power to negotiate better terms.
-
Cost-Efficiency: Look beyond initial rental costs. Consider factors such as maintenance, energy consumption, and the potential for revenue generation from the machines.
-
Total Cost of Ownership (TCO): Assess the TCO rather than just the upfront rental price. This includes maintenance, operational costs, and potential downtime.
-
Pricing Nuances: Be aware of regional pricing variations. Buyers from Africa, South America, the Middle East, and Europe may encounter different pricing strategies based on local economic conditions and market demand.
Disclaimer
Prices are indicative and can vary widely based on specific requirements, supplier negotiations, and market conditions. Always seek detailed quotes from multiple suppliers to ensure competitive pricing.
Spotlight on Potential soda vending machine rental Manufacturers and Suppliers
This section offers a look at a few manufacturers active in the ‘soda vending machine rental’ market. This is a representative sample for illustrative purposes; B2B buyers must conduct their own extensive due diligence before any engagement. Information is synthesized from public sources and general industry knowledge.
Essential Technical Properties and Trade Terminology for soda vending machine rental
When considering the rental of soda vending machines, understanding the essential technical properties and industry terminology is crucial for international B2B buyers. Here’s an overview of the key specifications and common jargon you will encounter in this sector.
Essential Technical Properties
-
Material Grade
Definition: The quality of materials used in the construction of vending machines, such as stainless steel or ABS plastic.
Importance: High-grade materials ensure durability and resistance to corrosion, which is vital for machines placed in various environments, from humid climates in Africa to colder regions in Europe. Buyers should prioritize machines made from robust materials to minimize maintenance costs. -
Capacity
Definition: The number of soda cans or bottles a vending machine can hold. Typical capacities range from 300 to 600 units.
Importance: Understanding capacity is key for meeting consumer demand. In high-traffic areas, a larger capacity reduces the frequency of restocking, thus optimizing operational efficiency. B2B buyers should assess expected foot traffic to determine the appropriate capacity. -
Power Consumption
Definition: The amount of electricity the vending machine uses, often measured in kilowatts per hour (kWh).
Importance: Lower power consumption is essential for cost savings and sustainability. This is particularly relevant for businesses aiming to reduce their carbon footprint or for those operating in regions with high energy costs. -
Payment Systems
Definition: The methods by which customers can pay for their sodas, including cash, credit/debit cards, and mobile payments.
Importance: A flexible payment system increases user convenience and can enhance sales. International buyers should consider local payment preferences and ensure that the vending machines they rent support these options. -
Dimensions
Definition: The physical size of the vending machine, which includes height, width, and depth.
Importance: Understanding the dimensions is crucial for spatial planning in the location where the machine will be installed. It ensures that the machine fits within designated spaces while allowing for adequate access for maintenance. -
Temperature Control
Definition: The system that regulates the internal temperature of the vending machine to keep beverages chilled.
Importance: Effective temperature control is critical for product quality and customer satisfaction. Machines should maintain optimal temperatures to prevent spoilage and ensure that drinks are served cold.
Common Trade Terminology
-
OEM (Original Equipment Manufacturer)
Definition: A company that produces parts and equipment that may be marketed by another manufacturer.
Importance: Understanding OEM relationships is essential for sourcing high-quality vending machines and components, ensuring reliability and brand reputation. -
MOQ (Minimum Order Quantity)
Definition: The smallest quantity of a product that a supplier is willing to sell.
Importance: For B2B buyers, knowing the MOQ helps in budgeting and inventory management. Suppliers may impose MOQ to ensure profitable transactions, which can impact cost-effectiveness. -
RFQ (Request for Quotation)
Definition: A document sent to suppliers to solicit price quotes for specific products or services.
Importance: An RFQ is a critical tool for buyers to compare prices and negotiate better terms. This process can significantly influence the overall rental cost of vending machines. -
Incoterms (International Commercial Terms)
Definition: A set of predefined commercial terms published by the International Chamber of Commerce, used in international sales contracts.
Importance: Familiarity with Incoterms helps buyers understand the responsibilities and risks associated with shipping and delivery, essential for managing logistics effectively. -
Lead Time
Definition: The time taken from placing an order to the delivery of the product.
Importance: Knowing the lead time is vital for planning and ensuring that vending machines are available when needed. This can affect inventory levels and service delivery in competitive markets. -
Service Level Agreement (SLA)
Definition: A contract that outlines the expected service standards between the provider and the client.
Importance: An SLA ensures that both parties have clear expectations regarding maintenance, uptime, and response times, which is critical for maintaining customer satisfaction and operational efficiency.
By grasping these essential technical properties and trade terms, international B2B buyers can make informed decisions when renting soda vending machines, ultimately enhancing their operational success and customer satisfaction.
Navigating Market Dynamics, Sourcing Trends, and Sustainability in the soda vending machine rental Sector
Global demand for soda vending machine rentals is on the rise, driven by various factors that affect B2B buyers across regions, including Africa, South America, the Middle East, and Europe. One of the primary market dynamics is the increasing consumer preference for convenience and quick access to beverages, particularly in urban areas. This trend is further amplified by the growing number of businesses seeking to enhance employee and customer experiences through automated solutions.
Market Overview & Key Trends
International B2B buyers should be aware of several key trends shaping the soda vending machine rental sector:
-
Technological Advancements: The incorporation of smart technology in vending machines, such as cashless payment systems, touchless interactions, and real-time inventory management, is becoming the norm. These innovations not only enhance user experience but also streamline operational efficiency for businesses.
-
Diverse Product Offerings: With health-conscious consumers on the rise, vending machines are increasingly offering a variety of beverage options, including low-calorie, organic, and functional drinks. This diversification allows businesses to cater to a broader audience, thereby increasing rental revenue.
-
Expansion into New Markets: Emerging markets in Africa and South America present significant growth opportunities for soda vending machine rentals. International B2B buyers should consider local partnerships to navigate regulatory challenges and understand consumer preferences in these regions.
- Data-Driven Decision Making: Utilizing analytics to track consumer behavior and machine performance is becoming critical. B2B buyers can leverage this data to optimize product offerings and machine placements, ensuring higher sales and improved customer satisfaction.
Sustainability & Ethical Sourcing in B2B
Sustainability is a pivotal concern for B2B buyers in the soda vending machine rental sector. The environmental impact of vending machines—ranging from energy consumption to waste generation—necessitates a shift towards more sustainable practices.
-
Environmental Considerations: Many vending machine companies are adopting eco-friendly practices, such as using energy-efficient machines that reduce electricity consumption. Buyers should prioritize suppliers that demonstrate commitment to sustainability.
-
Ethical Supply Chains: Ensuring ethical sourcing of materials is crucial. B2B buyers should seek out suppliers who comply with ethical labor standards and environmental regulations in their manufacturing processes.
-
Green Certifications: Look for machines that have received green certifications, such as Energy Star or ISO 14001, which indicate a commitment to environmental management. Additionally, consider vending machines made from recycled materials, which contribute to a circular economy.
-
Consumer Awareness: As consumers increasingly prefer brands that prioritize sustainability, businesses that adopt eco-friendly vending solutions can enhance their brand image and attract a more conscientious customer base.
Brief Evolution/History
The soda vending machine rental market has evolved significantly since its inception in the early 20th century. Initially designed to dispense simple beverages, these machines have transformed into sophisticated units equipped with advanced technology. The introduction of digital payments and smart inventory systems in the 21st century has revolutionized the sector, making it a vital component of modern retail and service environments. This evolution reflects broader consumer trends toward convenience and personalization, positioning the soda vending machine rental market as an essential service for businesses worldwide.
In conclusion, international B2B buyers must navigate a complex landscape characterized by technological innovation, sustainability concerns, and evolving consumer preferences. By understanding these dynamics, buyers can make informed decisions that enhance their business strategies and align with global trends.
Related Video: Chapter 9: International Trade
Frequently Asked Questions (FAQs) for B2B Buyers of soda vending machine rental
-
What should I consider when vetting suppliers for soda vending machine rentals?
When vetting suppliers, prioritize their experience in the vending machine industry, particularly in international markets. Check their track record for reliability and customer service. Request references from previous clients, particularly those in your region, to gauge their reputation. Ensure they have a clear understanding of local regulations and compliance standards relevant to your country. Additionally, evaluate their ability to provide support and maintenance services locally. -
Can I customize the vending machines to fit my brand?
Yes, many suppliers offer customization options for vending machines, including branding, color schemes, and product selection. When discussing customization, clarify the extent of modifications available and any associated costs. It’s advisable to request samples or mock-ups of the design to ensure it aligns with your brand identity. Be prepared to provide your branding materials, such as logos and color palettes, to facilitate the customization process. -
What are the typical minimum order quantities (MOQ) and lead times for vending machine rentals?
Minimum order quantities can vary significantly depending on the supplier and your specific needs. Typically, suppliers may have an MOQ ranging from one to ten machines for rental agreements. Lead times for delivery can also differ based on customization requirements and logistical factors, often ranging from two weeks to several months. Always confirm these details upfront to ensure they align with your project timeline and business needs. -
What payment terms are generally offered by suppliers?
Payment terms can vary widely among suppliers, with common practices including upfront payments, deposits, or monthly installments. It’s essential to negotiate terms that suit your cash flow situation. Some suppliers may offer financing options or leasing arrangements to ease the upfront financial burden. Always review the payment terms carefully and ensure they are documented in the rental agreement to avoid misunderstandings. -
What quality assurance measures should I expect from suppliers?
Reputable suppliers should adhere to strict quality assurance protocols, including compliance with international safety and quality standards. Inquire about certifications such as ISO or CE, which indicate adherence to recognized quality management systems. Additionally, ask about the testing processes for their machines before delivery, including functionality checks and maintenance procedures. A solid warranty policy can also serve as a safeguard against defects and malfunctions. -
How are logistics handled for the delivery and installation of vending machines?
Logistics for delivery and installation should be clearly defined in your agreement with the supplier. Most suppliers will manage the transportation of the machines to your location, but it’s important to clarify who bears the cost of shipping and any customs duties. Ensure that the supplier provides installation services or guidance to facilitate setup. Discuss the timeline for delivery and installation to coordinate with your operational schedule effectively. -
What should I do if I encounter disputes with the supplier?
In the event of a dispute, first, refer to the terms outlined in your rental agreement. Most contracts will include a dispute resolution clause, specifying steps for mediation or arbitration. Maintain clear documentation of all communications and agreements with the supplier to support your case. If issues persist, consider seeking legal counsel or utilizing trade associations for guidance on resolving the dispute amicably. -
What ongoing support can I expect after renting the vending machines?
Ongoing support is crucial for the successful operation of your vending machines. Confirm with your supplier what kind of support services they provide, including maintenance, repair services, and product replenishment. Many suppliers offer remote monitoring systems to track sales and machine performance, ensuring timely restocking. Establish clear communication channels for reporting issues and obtaining assistance, which can help minimize downtime and maximize profitability.
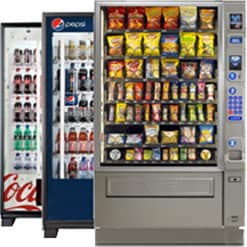
Illustrative Image (Source: Google Search)
Strategic Sourcing Conclusion and Outlook for soda vending machine rental
In conclusion, the strategic sourcing of soda vending machine rentals represents a vital opportunity for international B2B buyers looking to enhance customer experience while optimizing operational efficiencies. By prioritizing partnerships with reputable vendors, businesses can ensure access to high-quality machines and diverse product offerings, catering to varying consumer preferences across different regions, including Africa, South America, the Middle East, and Europe.
Key Takeaways:
– Cost Efficiency: Leverage rental models to minimize upfront capital expenditures while maintaining flexibility in operations.
– Market Adaptation: Choose suppliers that provide customizable solutions tailored to local market demands, ensuring relevance and competitiveness.
– Sustainability Focus: Seek vendors that prioritize eco-friendly practices, which are increasingly important to consumers and can enhance brand reputation.
As we look to the future, international B2B buyers are encouraged to adopt a proactive approach to sourcing. Embrace innovations in technology and customer engagement that vending machines can offer. By doing so, businesses can not only meet current consumer demands but also position themselves as leaders in the evolving market landscape. Start evaluating your options today to capitalize on this growing sector.