Your Ultimate Guide to Sourcing Psa Vending Machine Las
Guide to Psa Vending Machine Las Vegas
- Introduction: Navigating the Global Market for psa vending machine las vegas
- Understanding psa vending machine las vegas Types and Variations
- Key Industrial Applications of psa vending machine las vegas
- Strategic Material Selection Guide for psa vending machine las vegas
- In-depth Look: Manufacturing Processes and Quality Assurance for psa vending machine las vegas
- Comprehensive Cost and Pricing Analysis for psa vending machine las vegas Sourcing
- Spotlight on Potential psa vending machine las vegas Manufacturers and Suppliers
- Essential Technical Properties and Trade Terminology for psa vending machine las vegas
- Navigating Market Dynamics, Sourcing Trends, and Sustainability in the psa vending machine las vegas Sector
- Frequently Asked Questions (FAQs) for B2B Buyers of psa vending machine las vegas
- Strategic Sourcing Conclusion and Outlook for psa vending machine las vegas
Introduction: Navigating the Global Market for psa vending machine las vegas
In the rapidly evolving landscape of automated retail, PSA vending machines have emerged as a pivotal solution for businesses looking to enhance customer engagement and streamline operations. These machines offer a unique advantage by providing easy access to products while reducing overhead costs, making them particularly attractive to international buyers. As B2B procurement becomes increasingly global, understanding the specifics of PSA vending machines in Las Vegas is critical for businesses from Africa, South America, the Middle East, and Europe.
This comprehensive guide delves into the various aspects of PSA vending machines, including the different types available, the materials used in their construction, and the manufacturing and quality control processes that ensure reliability and performance. It also highlights key suppliers in the market, providing insights into cost structures and market dynamics. By addressing frequently asked questions, this guide serves as a valuable resource for international buyers seeking to make informed sourcing decisions.
Empowered with this knowledge, B2B buyers can confidently navigate the complexities of the global market for PSA vending machines, ensuring they select the most suitable options for their specific needs. Whether you are looking to enter the automated retail space or expand your existing offerings, understanding the intricacies of PSA vending machines in Las Vegas will equip you with the tools necessary for success.
Understanding psa vending machine las vegas Types and Variations
Type Name | Key Distinguishing Features | Primary B2B Applications | Brief Pros & Cons for Buyers |
---|---|---|---|
Standard PSA Vending Machine | Offers a variety of products, typically snacks and beverages | Office break rooms, schools | Pros: Easy to use, versatile product range. Cons: May require frequent restocking. |
Specialty PSA Vending Machine | Focused on specific products (e.g., healthy snacks, tech gadgets) | Gyms, universities, tech hubs | Pros: Attracts niche markets, promotes healthier choices. Cons: Limited product variety may reduce customer interest. |
Automated PSA Vending Machine | Fully automated with cashless payment options and smart inventory management | Airports, train stations | Pros: Reduces labor costs, enhances customer convenience. Cons: Higher initial investment and maintenance costs. |
Customizable PSA Vending Machine | Tailored to specific client needs (branding, product selection) | Corporate events, promotions | Pros: Enhances brand visibility, meets specific consumer demands. Cons: Longer lead time for setup and potentially higher costs. |
Mobile PSA Vending Machine | Portable units that can be relocated easily, often used for events | Festivals, trade shows | Pros: Flexibility in location, can target various audiences. Cons: Limited inventory space and may need frequent transport. |
Standard PSA Vending Machine
The Standard PSA Vending Machine is designed to accommodate a wide range of snacks and beverages, making it suitable for various settings such as office break rooms and schools. Its primary advantage lies in its versatility, offering a broad selection that appeals to diverse consumer preferences. However, businesses should consider the potential for frequent restocking, especially in high-traffic areas, which can impact operational efficiency.
Specialty PSA Vending Machine
Focusing on niche markets, the Specialty PSA Vending Machine offers targeted product selections, such as healthy snacks or tech gadgets. This type is ideal for environments like gyms, universities, or tech hubs where specific consumer interests are prevalent. While it can attract a dedicated customer base, its limited product range may deter some consumers, necessitating careful market analysis before deployment.
Automated PSA Vending Machine
The Automated PSA Vending Machine features advanced technology, including cashless payment options and smart inventory management systems. These machines are particularly effective in high-traffic locations such as airports and train stations, where convenience is paramount. Although they reduce labor costs and enhance user experience, buyers must weigh the higher initial investment and ongoing maintenance requirements against potential returns.
Customizable PSA Vending Machine
Designed for businesses seeking to enhance brand visibility, the Customizable PSA Vending Machine allows for tailored branding and product selections. This type is particularly useful for corporate events and promotions, where aligning with specific consumer needs can drive engagement. However, the setup process may be longer, and costs can escalate, making it essential for businesses to evaluate their marketing strategies before investing.
Mobile PSA Vending Machine
The Mobile PSA Vending Machine offers the unique advantage of portability, allowing businesses to target various audiences at events such as festivals or trade shows. This flexibility makes it an appealing option for companies looking to maximize their reach without committing to a fixed location. However, the limited inventory space and the logistics of frequent transportation can pose challenges, necessitating effective planning and management to ensure profitability.
Related Video: Pokemon PSA 10 vending machine in Las Vegas with a bonus booster pack! Did we win or lose money? 👀
Key Industrial Applications of psa vending machine las vegas
Industry/Sector | Specific Application of psa vending machine las vegas | Value/Benefit for the Business | Key Sourcing Considerations for this Application |
---|---|---|---|
Hospitality | 24/7 snack and beverage dispensing for hotels | Increased guest satisfaction and convenience | Space requirements, product variety, and payment systems |
Corporate Offices | Healthy snack options in office break rooms | Improved employee productivity and morale | Nutritional standards, product sourcing, and storage needs |
Healthcare | Medication dispensing for clinics and hospitals | Enhanced patient compliance and safety | Regulatory compliance, security features, and accessibility |
Education | Campus vending for students | Convenient access to food and drinks, promoting healthy choices | Product variety, payment options, and user-friendly design |
Transportation Hubs | On-the-go meal solutions at airports and bus stations | Catering to busy travelers, reducing wait times | Location analysis, product freshness, and logistics |
Hospitality
In the hospitality sector, psa vending machines provide a 24/7 solution for dispensing snacks and beverages in hotels. This application enhances guest experience by offering convenience and accessibility at any time, which is crucial for late-night arrivals or early departures. For international buyers, understanding local preferences for snacks and beverages is essential, as is ensuring compliance with food safety regulations. Additionally, integrating cashless payment options can cater to diverse clientele, particularly in tourist-heavy locations.
Corporate Offices
In corporate environments, psa vending machines serve as healthy snack options in office break rooms. This application is designed to improve employee productivity and morale by providing nutritious choices that can help maintain energy levels throughout the workday. International buyers should consider nutritional standards and local tastes when selecting products. Furthermore, ensuring that the machines accommodate various payment methods will enhance user experience, particularly in regions where cashless transactions are prevalent.
Healthcare
In healthcare settings, psa vending machines can dispense medications in clinics and hospitals. This application addresses the challenge of patient compliance by providing easy access to prescribed medications outside regular pharmacy hours. For B2B buyers in the healthcare industry, it is crucial to ensure that the vending machines meet regulatory compliance and feature secure mechanisms to prevent unauthorized access. Additionally, machines should be designed for accessibility to accommodate patients with disabilities, enhancing overall service delivery.
Education
In educational institutions, psa vending machines offer convenient access to food and drinks for students on campus. This application promotes healthy choices and helps meet the nutritional needs of students, especially in environments where traditional dining facilities may not be available. Buyers from the education sector should focus on product variety and consider the implementation of user-friendly designs that appeal to younger demographics. Furthermore, understanding the payment preferences of students, such as mobile payment options, can significantly enhance usage rates.
Transportation Hubs
In transportation hubs like airports and bus stations, psa vending machines provide on-the-go meal solutions for busy travelers. This application not only caters to the need for quick and convenient food options but also helps reduce wait times during peak travel periods. For international B2B buyers, conducting a location analysis to determine optimal placement of vending machines is vital. Additionally, ensuring product freshness and establishing efficient logistics for restocking will be key considerations to maintain a reliable service that meets traveler expectations.
Related Video: Kooler Ice Vending Machines – IM600XL vs. IM1000
Strategic Material Selection Guide for psa vending machine las vegas
When selecting materials for PSA (Pressure Swing Adsorption) vending machines in Las Vegas, international B2B buyers must consider various factors that influence the performance, durability, and compliance of the machines. Below is an analysis of four common materials used in these applications, focusing on their properties, advantages, disadvantages, and specific considerations for buyers from Africa, South America, the Middle East, and Europe.
1. Stainless Steel (e.g., 304, 316)
Key Properties:
Stainless steel is known for its excellent corrosion resistance, high strength, and ability to withstand high temperatures and pressures. Grades like 316 offer superior resistance to chlorides, making them suitable for harsher environments.
Pros & Cons:
– Advantages: Durable, long lifespan, low maintenance, and aesthetic appeal.
– Disadvantages: Higher initial cost compared to carbon steel, which may be a concern for budget-sensitive projects.
Impact on Application:
Stainless steel is compatible with a wide range of media, including gases and liquids, making it ideal for PSA applications.
Specific Considerations:
International buyers should ensure compliance with standards such as ASTM A240 for stainless steel products. In regions like Europe, adherence to EN standards is also critical.
2. Carbon Steel (e.g., A216 WCB)
Key Properties:
Carbon steel is strong and cost-effective, making it a popular choice for many industrial applications. However, it is susceptible to corrosion without proper coatings or treatments.
Pros & Cons:
– Advantages: Lower cost and good mechanical properties.
– Disadvantages: Requires protective coatings to prevent rust, which can increase long-term maintenance costs.
Impact on Application:
While suitable for non-corrosive environments, carbon steel may not be ideal for applications involving moisture or corrosive gases.
Specific Considerations:
Buyers should be aware of local regulations concerning material coatings and corrosion resistance. Compliance with ASTM standards is essential for ensuring quality and safety.
3. Aluminum
Key Properties:
Aluminum is lightweight, corrosion-resistant, and has good thermal conductivity. It is often used in applications where weight savings are critical.
Pros & Cons:
– Advantages: Lightweight, cost-effective for certain applications, and good corrosion resistance.
– Disadvantages: Lower strength compared to stainless steel and carbon steel, which may limit its use in high-pressure applications.
Impact on Application:
Aluminum is suitable for applications involving low-pressure gas storage and transport but may not withstand high-pressure environments effectively.
Specific Considerations:
International buyers should consider the specific alloy used, as different grades have varying properties. Compliance with standards like ASTM B221 is crucial for ensuring material integrity.
4. Polypropylene (PP)
Key Properties:
Polypropylene is a thermoplastic polymer known for its chemical resistance, lightweight nature, and ease of fabrication. It is often used in applications involving corrosive chemicals.
Pros & Cons:
– Advantages: Excellent chemical resistance, low weight, and cost-effective for certain applications.
– Disadvantages: Limited temperature and pressure ratings compared to metals, which may restrict its use in high-stress environments.
Impact on Application:
Polypropylene is ideal for applications involving corrosive gases or liquids but may not be suitable for high-pressure systems.
Specific Considerations:
Buyers should ensure compliance with relevant standards for plastics, such as ASTM D4101, to guarantee quality and performance.
Summary Table
Material | Typical Use Case for psa vending machine las vegas | Key Advantage | Key Disadvantage/Limitation | Relative Cost (Low/Med/High) |
---|---|---|---|---|
Stainless Steel (e.g., 304, 316) | High-pressure gas storage and transport | Excellent corrosion resistance, durable | Higher initial cost | High |
Carbon Steel (e.g., A216 WCB) | General service, non-corrosive fluids | Cost-effective, good strength | Susceptible to corrosion if not protected | Low |
Aluminum | Low-pressure gas storage | Lightweight, good corrosion resistance | Lower strength compared to steel | Medium |
Polypropylene (PP) | Chemical storage and transport | Excellent chemical resistance | Limited temperature and pressure ratings | Low |
This strategic material selection guide provides a comprehensive overview for international B2B buyers looking to procure PSA vending machines in Las Vegas, ensuring they make informed decisions based on material properties, application suitability, and compliance with regional standards.
In-depth Look: Manufacturing Processes and Quality Assurance for psa vending machine las vegas
Manufacturing Processes for PSA Vending Machines
When considering the procurement of PSA vending machines, understanding the manufacturing process is crucial for international B2B buyers. The production of these machines involves several key stages, each with its own set of techniques and quality control measures.
Main Stages of Manufacturing
-
Material Preparation
– Sourcing Raw Materials: The first step involves sourcing high-quality materials such as steel for the frame, plastic for the casing, and electronic components for the vending mechanism. Buyers should ensure that suppliers adhere to international standards for material quality.
– Material Inspection: Before production begins, materials undergo rigorous inspection to verify their compliance with specifications. This includes checking for defects, dimensions, and material properties. -
Forming
– Cutting and Shaping: Materials are cut into precise shapes using CNC machines or laser cutting technologies. This precision is essential for ensuring that parts fit together seamlessly.
– Welding and Assembly of Frame: The frame is constructed through welding techniques, which provide durability. Robotic welding may be employed for consistency and strength. -
Assembly
– Component Integration: This stage involves assembling various components such as the vending mechanism, payment systems, and control panels. Automated assembly lines may be used to enhance efficiency.
– Wiring and Electronic Setup: Technicians install wiring for power supply and data communication between components. This step requires meticulous attention to detail to prevent future operational issues. -
Finishing
– Surface Treatment: After assembly, machines undergo surface treatments such as powder coating or painting to enhance durability and aesthetics. This process also includes applying protective coatings to prevent corrosion.
– Final Assembly: The final assembly includes installing the exterior panels and ensuring that all components are securely fitted and operational.
Quality Assurance Measures
Quality assurance is integral to the manufacturing of PSA vending machines. It ensures that the final product meets both safety and operational standards.
International and Industry-Specific Standards
- ISO 9001: This international standard for quality management systems is crucial. Manufacturers should be certified, indicating that they follow structured processes to ensure quality.
- CE Marking: For machines sold in Europe, CE marking is essential, demonstrating compliance with health, safety, and environmental protection standards.
- API Standards: If applicable, manufacturers should also meet American Petroleum Institute (API) standards, especially if the vending machines deal with specialized products.
Quality Control Checkpoints
-
Incoming Quality Control (IQC)
– Materials are inspected upon arrival to ensure they meet predefined specifications. This initial checkpoint is critical for preventing defects in the final product. -
In-Process Quality Control (IPQC)
– During production, quality checks are performed at various stages. This includes monitoring assembly processes and ensuring that components are installed correctly. -
Final Quality Control (FQC)
– Before shipping, the complete machine undergoes final inspection, where functionality tests are conducted. This includes checking the vending mechanism, payment systems, and overall performance.
Common Testing Methods
- Functional Testing: Ensures that all features operate as intended under various conditions.
- Durability Testing: Machines are subjected to stress tests to evaluate their durability and resistance to wear and tear.
- Safety Testing: Compliance with safety regulations is verified through testing for electrical safety and operational hazards.
Verifying Supplier Quality Control
For international buyers, particularly from Africa, South America, the Middle East, and Europe, verifying supplier quality control is paramount. Here are some actionable steps:
-
Conduct Supplier Audits: Regular audits of suppliers can help ensure adherence to quality standards. Buyers should create a checklist based on international standards and specific industry requirements.
-
Request Quality Control Reports: Suppliers should provide detailed reports on quality control processes and outcomes. This documentation should include results from IQC, IPQC, and FQC.
-
Engage Third-Party Inspectors: Utilizing third-party inspection services can provide an unbiased evaluation of the manufacturing processes and quality assurance measures in place. This is particularly useful for buyers unfamiliar with local practices.
QC and Certification Nuances for International Buyers
Navigating quality control and certification can be complex for international buyers. Here are some nuances to consider:
-
Understanding Local Standards: Different regions may have varying standards and regulations. Buyers must familiarize themselves with local compliance requirements to avoid issues during importation.
-
Language Barriers: Documentation and reports may be in a local language. It is advisable to work with suppliers who can provide English translations or partner with local intermediaries who understand both languages.
-
Logistics and Shipping Compliance: Ensure that the machines meet the shipping regulations of the destination country, which may include additional certifications or inspections.
In summary, understanding the manufacturing processes and quality assurance practices for PSA vending machines is crucial for international B2B buyers. By focusing on the key stages of production, relevant quality standards, and verification methods, buyers can make informed decisions that ensure the procurement of high-quality vending machines that meet their operational needs.
Related Video: The Most Sophisticated Manufacturing Process In The World Inside The Fab | Intel
Comprehensive Cost and Pricing Analysis for psa vending machine las vegas Sourcing
When sourcing PSA vending machines in Las Vegas, international B2B buyers should be aware of the comprehensive cost structure and pricing dynamics involved in the procurement process. Understanding these factors will help buyers make informed decisions that align with their business objectives and budget constraints.
Cost Components
- Materials: The primary components of PSA vending machines include metal casings, electronic parts, and dispensing mechanisms. The quality and type of materials used significantly affect the overall cost. For instance, machines made with high-grade stainless steel or advanced electronic systems typically command higher prices.
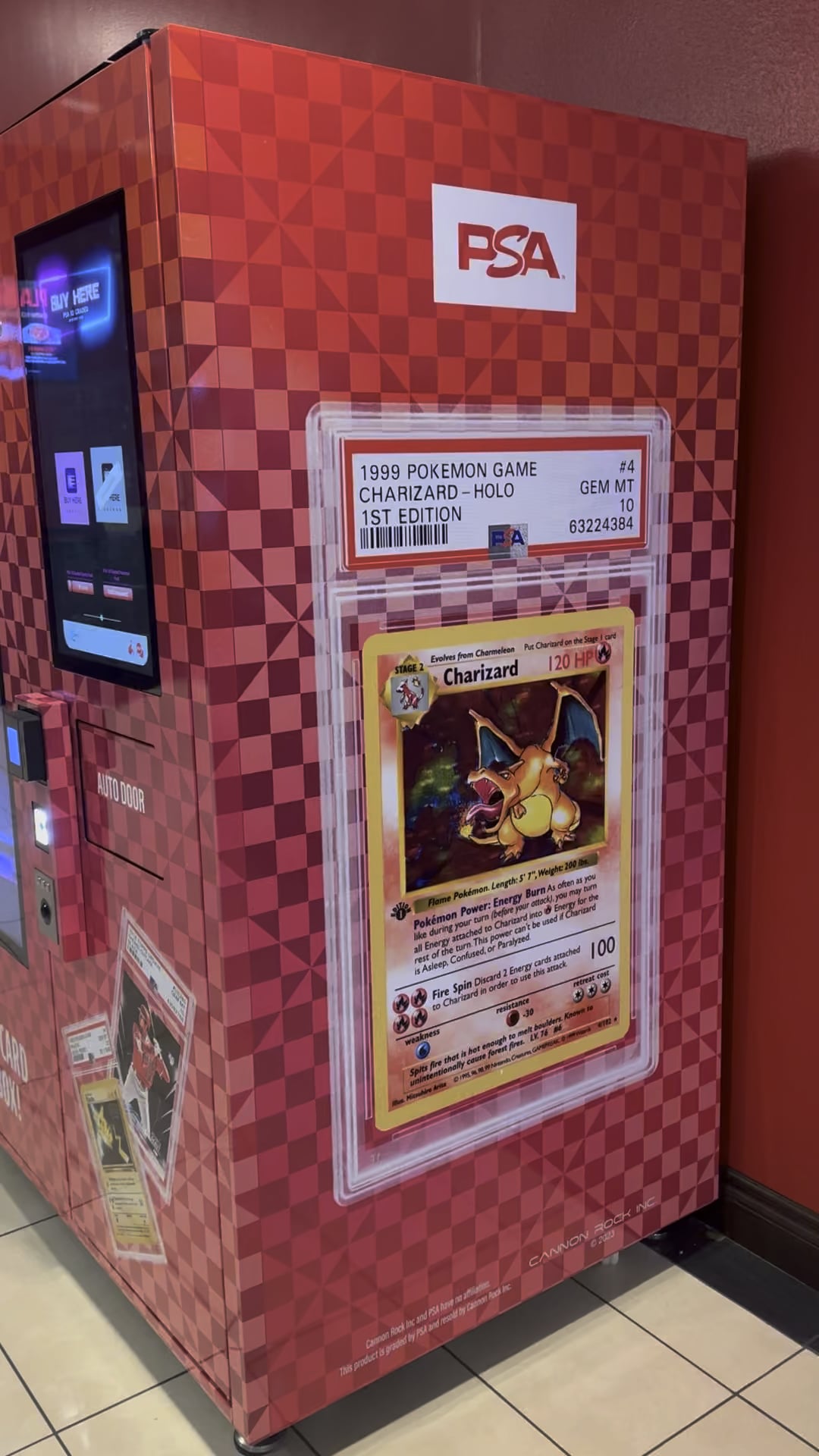
Illustrative Image (Source: Google Search)
-
Labor: Labor costs can vary based on the manufacturing location. In regions with higher labor costs, such as parts of Europe, buyers may face increased pricing. Conversely, sourcing from regions with lower labor costs may offer savings, but this could impact quality and service levels.
-
Manufacturing Overhead: This encompasses indirect costs associated with production, such as utilities, rent, and administrative expenses. Buyers should consider suppliers with efficient manufacturing processes to minimize these overhead costs.
-
Tooling: Custom tooling may be required for specific machine configurations or features. This initial investment can be significant but is often amortized over larger production runs, making it essential to assess the potential for volume orders.
-
Quality Control (QC): Ensuring that machines meet specified quality standards involves additional costs. Suppliers that implement rigorous QC processes may charge more, but this investment can lead to better long-term reliability and customer satisfaction.
-
Logistics: Shipping costs, including freight, customs duties, and insurance, can add to the total cost. Buyers should evaluate various logistics options and Incoterms (e.g., FOB, CIF) to determine the most cost-effective solutions for their specific needs.
-
Margin: Suppliers will include a profit margin in their pricing, which can vary based on market conditions and the competitive landscape. Buyers should be aware of the typical margins in the vending machine industry to gauge the fairness of quotes received.
Price Influencers
-
Volume/MOQ: The minimum order quantity (MOQ) can significantly affect pricing. Higher volume orders usually lead to lower unit costs due to economies of scale. Buyers should negotiate MOQs that align with their demand forecasts.
-
Specifications/Customization: Custom features or specific branding requirements can increase costs. Clearly defining specifications upfront can help manage these costs and avoid surprises during the procurement process.
-
Materials and Quality Certifications: Machines that comply with international quality certifications (e.g., ISO, CE) may have higher upfront costs but can reduce the risk of issues later, making them a worthy investment.
-
Supplier Factors: The reputation and reliability of the supplier can impact pricing. Established suppliers may charge a premium for their services due to their track record of quality and support.
Buyer Tips
-
Negotiation: Engage in open discussions with suppliers to explore pricing flexibility. Consider leveraging multiple quotes to strengthen your negotiating position.
-
Cost-Efficiency: Focus on the total cost of ownership rather than just the initial purchase price. This includes maintenance, energy consumption, and potential resale value.
-
Pricing Nuances: Be aware of regional pricing differences, especially when sourcing from diverse markets like Africa, South America, the Middle East, and Europe. Currency fluctuations and local economic conditions can also affect final costs.
-
Disclaimer for Indicative Prices: Pricing can fluctuate based on market conditions, material availability, and supplier capabilities. Always request detailed quotes to get the most accurate pricing information tailored to your specific requirements.
By understanding these components and influencers, international B2B buyers can navigate the complexities of sourcing PSA vending machines in Las Vegas more effectively, ensuring they make informed and strategic procurement decisions.
Spotlight on Potential psa vending machine las vegas Manufacturers and Suppliers
This section offers a look at a few manufacturers active in the ‘psa vending machine las vegas’ market. This is a representative sample for illustrative purposes; B2B buyers must conduct their own extensive due diligence before any engagement. Information is synthesized from public sources and general industry knowledge.
Essential Technical Properties and Trade Terminology for psa vending machine las vegas
Key Technical Properties of PSA Vending Machines
When considering the procurement of PSA (Professional Sports Authenticator) vending machines, several critical technical specifications must be evaluated to ensure quality, reliability, and performance. Below are essential properties to consider:
-
Material Grade
– Definition: This refers to the quality of materials used in the construction of the vending machine, including metals, plastics, and electronic components.
– Importance: Higher material grades typically ensure durability and longevity, reducing maintenance costs and improving customer satisfaction. For international buyers, understanding material grades helps assess the machine’s resilience against local environmental conditions. -
Power Requirements
– Definition: This specification outlines the voltage and current needed for the vending machine to operate effectively.
– Importance: Ensuring compatibility with local electrical standards is crucial for safe operation. Buyers from regions with different power standards (e.g., Africa and Europe) must verify that the vending machines can be adapted or are available in suitable configurations. -
Capacity and Dimensions
– Definition: This includes the number of items the machine can hold and its physical dimensions (height, width, depth).
– Importance: Understanding capacity helps buyers estimate how much inventory can be stocked, which directly impacts sales potential. Additionally, dimensions must fit within the intended installation space, especially in high-traffic areas. -
User Interface Technology
– Definition: The type of user interface, such as touchscreens, buttons, or mobile app integration.
– Importance: A user-friendly interface can enhance the customer experience and drive sales. Buyers should consider the technological familiarity of their target market, particularly in regions with varying levels of technological adoption. -
Payment Processing Systems
– Definition: This refers to the methods available for customers to complete transactions, including cash, credit/debit cards, and mobile payment options.
– Importance: Diverse payment options can increase sales by accommodating a wider range of consumer preferences. Buyers should ensure that the vending machines support payment systems popular in their respective regions. -
Warranty and Support Services
– Definition: The terms and duration of the warranty provided by the manufacturer, along with available after-sales support.
– Importance: A robust warranty and reliable support services are crucial for minimizing downtime and ensuring operational efficiency. Buyers should evaluate the manufacturer’s reputation for service, especially for international transactions.
Common Trade Terminology
Understanding industry jargon is essential for effective communication and negotiation in the B2B landscape. Here are some common terms relevant to the vending machine market:
-
OEM (Original Equipment Manufacturer)
– Definition: A company that produces parts and equipment that may be marketed by another manufacturer.
– Relevance: Buyers should consider whether they are purchasing directly from an OEM or a reseller, as this affects pricing, warranty, and support. -
MOQ (Minimum Order Quantity)
– Definition: The smallest quantity of a product that a supplier is willing to sell.
– Relevance: Understanding MOQ is crucial for budgeting and inventory management. Buyers must assess if they can meet these requirements based on their expected sales volume. -
RFQ (Request for Quotation)
– Definition: A document issued by a buyer to solicit price quotes from suppliers for specific products or services.
– Relevance: Issuing an RFQ can help buyers compare offers and negotiate better terms, ensuring they receive competitive pricing from various suppliers.
-
Incoterms (International Commercial Terms)
– Definition: A series of predefined commercial terms published by the International Chamber of Commerce that clarify the responsibilities of buyers and sellers in international transactions.
– Relevance: Familiarity with Incoterms is essential for understanding shipping responsibilities, costs, and risks, particularly for international buyers who must navigate cross-border logistics. -
Lead Time
– Definition: The time it takes from placing an order to receiving the product.
– Relevance: Buyers should be aware of lead times to manage inventory levels and meet customer demand effectively, especially in fast-paced markets. -
Freight Forwarding
– Definition: The process of coordinating the shipment of goods from one place to another via a third-party service.
– Relevance: Understanding freight forwarding is essential for international buyers, as it can significantly impact shipping costs and delivery timelines.
By familiarizing themselves with these technical properties and trade terms, international B2B buyers can make informed decisions when investing in PSA vending machines, optimizing their operations and enhancing customer satisfaction.
Navigating Market Dynamics, Sourcing Trends, and Sustainability in the psa vending machine las vegas Sector
Market Overview & Key Trends
The psa vending machine sector in Las Vegas has experienced significant growth, driven by several global factors including an increase in urbanization and a shift towards cashless transactions. The demand for convenience in purchasing has led to the evolution of vending machines, now equipped with advanced technology such as AI and IoT capabilities. For international B2B buyers, particularly those from Africa, South America, the Middle East, and Europe, understanding these trends is crucial.
Emerging technologies such as contactless payment systems and smart inventory management are becoming standard. These innovations enhance operational efficiency and customer experience, catering to a tech-savvy clientele. For instance, vending machines that utilize real-time data analytics can adjust stock based on consumer behavior, allowing businesses to optimize their product offerings. Additionally, the rise of eco-friendly products has prompted manufacturers to incorporate sustainable materials into their machines, aligning with global sustainability goals.
Market dynamics are also influenced by regional preferences; for example, European buyers may prioritize energy-efficient models due to stringent regulations. In contrast, buyers from the Middle East may focus on luxury features and high-tech interfaces. Understanding these regional nuances can help international buyers tailor their sourcing strategies effectively.
Sustainability & Ethical Sourcing in B2B
Sustainability is a key consideration in the psa vending machine sector, with a growing emphasis on reducing environmental impact. International B2B buyers are increasingly seeking vendors who prioritize ethical sourcing and sustainable practices. This includes the use of recyclable materials in machine construction and eco-friendly packaging for products sold within these machines.
Adopting sustainable practices not only enhances brand reputation but can also lead to cost savings in the long term. For example, machines that utilize energy-efficient technology reduce electricity costs and comply with environmental regulations, making them appealing to buyers in regions like Europe, where sustainability standards are stringent.
Moreover, certifications such as ISO 14001 for environmental management and LEED (Leadership in Energy and Environmental Design) for energy-efficient building practices are becoming essential for suppliers aiming to attract responsible buyers. B2B buyers should prioritize suppliers who demonstrate a commitment to sustainability, as this can significantly impact their procurement decisions.
Brief Evolution/History
The vending machine industry has evolved considerably since its inception in the early 1880s. Initially serving simple items like postcards and chewing gum, these machines have transformed into sophisticated retail solutions. The introduction of electronic payment systems in the 1990s marked a significant turning point, paving the way for modern machines that cater to diverse consumer needs.
In recent years, the integration of technology has further revolutionized the sector, enabling features such as remote monitoring and personalized customer experiences. This evolution reflects broader trends in retail, where convenience and technological innovation drive consumer expectations. For international B2B buyers, recognizing this historical context is essential for making informed purchasing decisions in a rapidly changing market.
Related Video: How Global Trade Runs on U.S. Dollars | WSJ
Frequently Asked Questions (FAQs) for B2B Buyers of psa vending machine las vegas
-
What should I consider when vetting suppliers for PSA vending machines in Las Vegas?
When vetting suppliers, assess their industry experience, reputation, and customer feedback. Request references from previous clients to gauge reliability. Verify their certifications and compliance with local regulations. Additionally, inquire about their manufacturing capabilities, response times, and after-sales support to ensure they can meet your specific needs. -
Can I customize the PSA vending machines to suit my business requirements?
Yes, many suppliers offer customization options for PSA vending machines. You can specify features such as size, color, branding, and product offerings. Discuss your requirements with potential suppliers early in the negotiation process to understand the extent of customization available and any associated costs. -
What are the typical minimum order quantities (MOQ) and lead times for PSA vending machines?
MOQs vary by supplier but generally range from 5 to 20 units for custom orders. Standard models may have lower MOQs. Lead times can range from 4 to 12 weeks, depending on customization and supplier capacity. Always clarify these details upfront to align your procurement timeline with your business needs. -
What payment terms should I expect when sourcing PSA vending machines?
Payment terms can vary widely among suppliers. Common practices include a 30% deposit upon order confirmation, with the remaining balance due prior to shipment. Some suppliers may offer net 30 or net 60 terms for established businesses. Ensure to negotiate terms that protect your cash flow while securing favorable pricing.
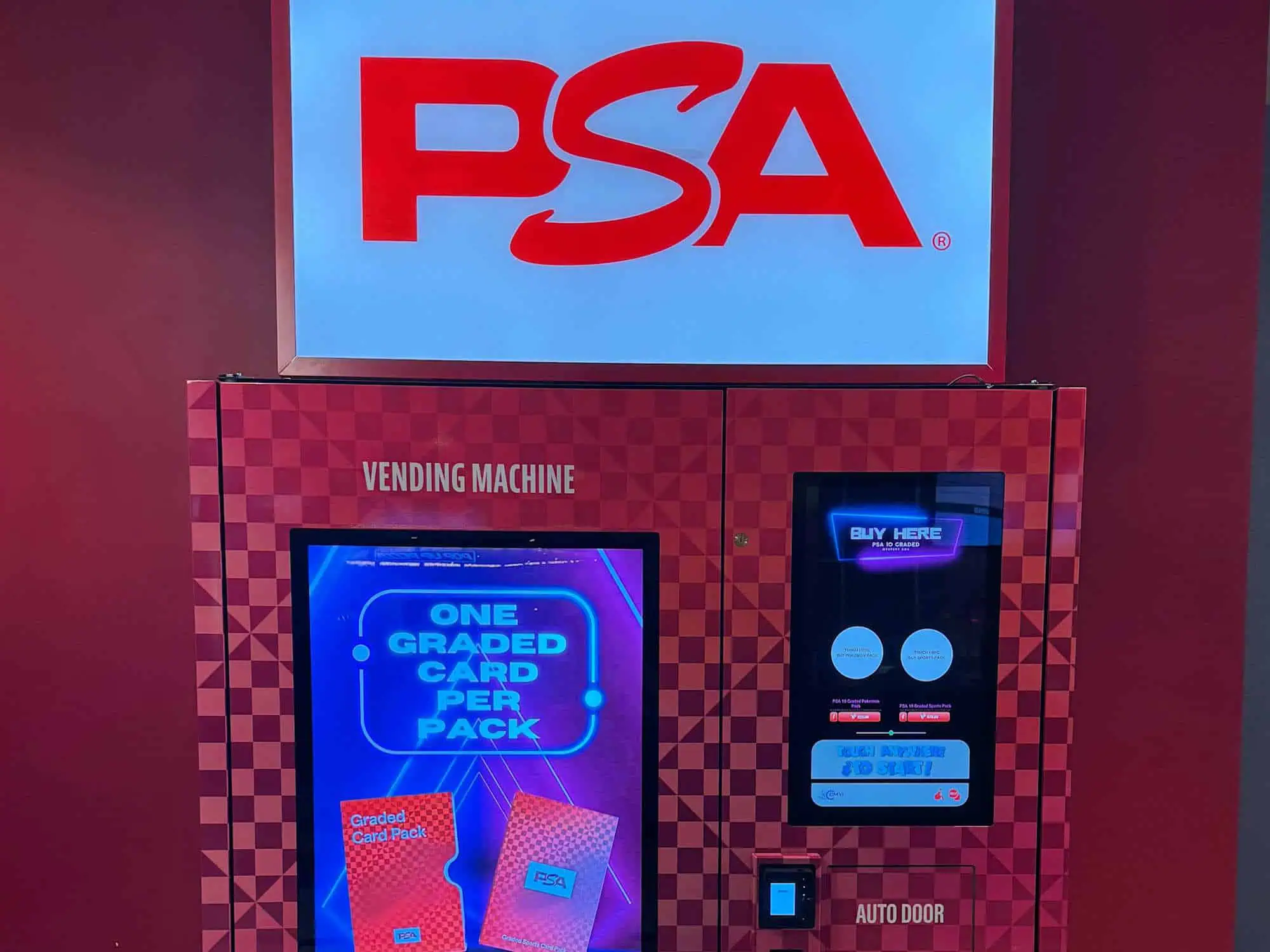
Illustrative Image (Source: Google Search)
-
How can I ensure the quality of the PSA vending machines I purchase?
Request quality assurance (QA) certifications from suppliers, such as ISO 9001, which indicates adherence to international quality management standards. Additionally, consider conducting factory audits or requesting samples for testing. Establish clear quality expectations in your contract to safeguard against defects and ensure product consistency. -
What logistics considerations should I keep in mind when importing PSA vending machines?
Logistics involve several key aspects: shipping methods, customs clearance, and storage upon arrival. Evaluate shipping options (air vs. sea) based on cost and urgency. Ensure the supplier provides necessary documentation for smooth customs processing. It’s also wise to work with a freight forwarder familiar with international shipping regulations to mitigate delays. -
What should I do if I encounter disputes with my supplier regarding PSA vending machines?
Establish a clear dispute resolution process in your contract. This may include negotiation, mediation, or arbitration clauses. Document all communications regarding the issue and seek to resolve matters amicably first. If necessary, consult legal counsel familiar with international trade laws to understand your rights and options for escalation. -
Are there specific certifications required for PSA vending machines in international markets?
Yes, certifications may vary by market. In the U.S., for example, machines must comply with safety standards set by organizations like UL or ETL. In Europe, CE marking may be required. Research the regulations in your target market and ensure that your supplier can meet these certification requirements to avoid compliance issues.
Strategic Sourcing Conclusion and Outlook for psa vending machine las vegas
In conclusion, strategic sourcing for PSA vending machines in Las Vegas presents significant opportunities for international B2B buyers from regions such as Africa, South America, the Middle East, and Europe. By leveraging local suppliers and understanding market dynamics, businesses can optimize their supply chains, reduce costs, and enhance service delivery. The unique demands of each market require tailored approaches that consider cultural preferences and purchasing behaviors, which can greatly influence vending machine product selection and placement.
Moreover, establishing strong relationships with manufacturers and distributors is crucial. This not only ensures a reliable supply but also opens doors to innovative solutions and better pricing structures. As the vending machine industry continues to evolve with advancements in technology and consumer preferences, staying ahead through strategic sourcing will be key.
We encourage international buyers to actively engage with local suppliers and explore the diverse offerings in Las Vegas. By doing so, they can position themselves to capitalize on emerging trends and drive their businesses forward in an increasingly competitive landscape. Embrace the future of vending with strategic sourcing, and let your business thrive.