Master Sourcing Glass Front Vending Machines for Maximum
Guide to Glass Front Vending Machine
- Introduction: Navigating the Global Market for glass front vending machine
- Understanding glass front vending machine Types and Variations
- Key Industrial Applications of glass front vending machine
- Strategic Material Selection Guide for glass front vending machine
- In-depth Look: Manufacturing Processes and Quality Assurance for glass front vending machine
- Comprehensive Cost and Pricing Analysis for glass front vending machine Sourcing
- Spotlight on Potential glass front vending machine Manufacturers and Suppliers
- Essential Technical Properties and Trade Terminology for glass front vending machine
- Navigating Market Dynamics, Sourcing Trends, and Sustainability in the glass front vending machine Sector
- Frequently Asked Questions (FAQs) for B2B Buyers of glass front vending machine
- Strategic Sourcing Conclusion and Outlook for glass front vending machine
Introduction: Navigating the Global Market for glass front vending machine
In the rapidly evolving landscape of retail and consumer engagement, glass front vending machines have emerged as a pivotal solution for businesses looking to enhance product visibility and accessibility. These machines not only offer an aesthetically pleasing display but also cater to the growing demand for self-service retail options across various sectors, including food, beverages, and non-perishable items. For international B2B buyers from regions such as Africa, South America, the Middle East, and Europe, understanding the nuances of this market is essential for making informed procurement decisions.
This comprehensive guide delves into the multifaceted world of glass front vending machines, covering essential topics such as types, materials, manufacturing processes, quality control standards, and cost considerations. Buyers will gain insights into reputable suppliers and market trends that influence pricing and product availability. Additionally, the guide addresses frequently asked questions, ensuring that potential buyers are equipped with the necessary knowledge to navigate their purchasing journey effectively.
By empowering B2B buyers with actionable insights and a clear understanding of the glass front vending machine market, this guide aims to facilitate informed sourcing decisions that align with their business objectives. Whether you are a buyer from Colombia seeking innovative retail solutions or a distributor in Poland looking to expand your product offerings, this resource is designed to support your strategic initiatives in the global marketplace.
Understanding glass front vending machine Types and Variations
Type Name | Key Distinguishing Features | Primary B2B Applications | Brief Pros & Cons for Buyers |
---|---|---|---|
Snack and Beverage Machine | Combines snacks and drinks in one unit | Offices, schools, hospitals | Pros: Versatile, maximizes space; Cons: Maintenance can be complex. |
Specialty Product Machine | Focused on niche items like organic or vegan snacks | Health food stores, gyms | Pros: Targets specific markets; Cons: Limited audience reach. |
High-Tech Smart Machine | Features touch screens, cashless payment systems | Airports, shopping malls | Pros: Enhanced user experience; Cons: Higher initial investment. |
Mini Vending Machine | Compact design for limited spaces | Small offices, waiting areas | Pros: Space-efficient; Cons: Limited product selection. |
Outdoor Vending Machine | Weather-resistant, larger capacity | Parks, stadiums | Pros: Increased visibility; Cons: Requires robust security measures. |
Snack and Beverage Machine
This type of vending machine is designed to dispense a combination of snacks and beverages, making it ideal for high-traffic areas such as offices, schools, and hospitals. Its dual functionality allows businesses to cater to diverse consumer preferences, enhancing customer satisfaction. When purchasing, buyers should consider the machine’s size, inventory management capabilities, and ease of maintenance, as these factors can influence operational efficiency.
Specialty Product Machine
Specialty product machines focus on niche markets, offering organic, gluten-free, or vegan snacks. They are particularly suitable for health food stores and gyms, where consumer demand for specific dietary options is high. Buyers should evaluate the product selection and branding potential, as well as the machine’s ability to attract and retain a dedicated customer base. However, limited audience reach may pose a challenge in terms of sales volume.
High-Tech Smart Machine
High-tech smart machines incorporate advanced features such as touch screens and cashless payment options, appealing to tech-savvy consumers in locations like airports and shopping malls. These machines enhance the user experience and streamline transactions, making them attractive to businesses looking to modernize their offerings. Buyers should weigh the benefits of increased customer engagement against the higher initial investment and potential technical maintenance requirements.
Mini Vending Machine
Designed for limited spaces, mini vending machines are perfect for small offices and waiting areas. Their compact design allows for easy placement in areas where traditional machines may not fit. Buyers should consider the machine’s product variety and pricing strategy, as limited selections can impact sales. While they offer a space-efficient solution, the trade-off is a reduced product offering that may not satisfy all customer needs.
Outdoor Vending Machine
Outdoor vending machines are built to withstand various weather conditions and typically have a larger capacity to accommodate higher foot traffic in parks and stadiums. Their visibility can drive impulse purchases, making them a profitable investment for businesses in outdoor settings. However, buyers must assess the security features to prevent vandalism and theft, as outdoor machines are often more vulnerable than their indoor counterparts.
Related Video: Dixie Narco DN3800-4 Glass Front Vending Machine @East Las Vegas Community Center, Las Vegas, NV USA
Key Industrial Applications of glass front vending machine
Industry/Sector | Specific Application of glass front vending machine | Value/Benefit for the Business | Key Sourcing Considerations for this Application |
---|---|---|---|
Retail | Snack and beverage sales | Increased impulse purchases, enhanced customer experience | Product visibility, machine size, and payment options |
Healthcare | Pharmaceutical dispensing | Convenient access to medications, improves patient adherence | Compliance with health regulations, security features |
Education | Campus snack and beverage stations | Provides quick access to refreshments for students, boosts campus engagement | Machine capacity, energy efficiency, and payment systems |
Corporate Offices | Employee refreshment stations | Enhances workplace satisfaction, reduces downtime for breaks | Variety of product offerings, maintenance support |
Transportation Hubs | Travel convenience for passengers | Quick access to snacks and drinks, improves traveler satisfaction | Durability, theft protection, and payment options |
Retail
In the retail sector, glass front vending machines are employed to offer snacks and beverages in high-traffic areas. Their transparent design allows for easy visibility of products, which can significantly increase impulse purchases. International B2B buyers should consider the machine’s size and product capacity to fit their specific retail environment, while also evaluating payment options that cater to diverse customer preferences.
Healthcare
Healthcare facilities utilize glass front vending machines for dispensing pharmaceuticals and over-the-counter medications. This application addresses the need for convenient access to medications, thereby improving patient adherence to treatment plans. Buyers in the healthcare sector must ensure that the machines comply with relevant health regulations, including security features to prevent unauthorized access and ensure patient safety.
Education
In educational institutions, glass front vending machines serve as snack and beverage stations on campuses. They provide students with quick access to refreshments, enhancing their overall experience and engagement on campus. Buyers from educational sectors should focus on machine capacity and energy efficiency, as these factors contribute to operational costs and sustainability initiatives within the institution.
Corporate Offices
Corporate offices leverage glass front vending machines to create employee refreshment stations, fostering a positive work environment. These machines allow employees to quickly grab snacks and drinks, minimizing downtime during breaks. B2B buyers in this sector should prioritize a variety of product offerings and reliable maintenance support to ensure the machines remain stocked and functional.
Transportation Hubs
Transportation hubs, such as airports and train stations, benefit from glass front vending machines by offering travelers quick access to snacks and drinks. This convenience can significantly improve traveler satisfaction and overall experience. Key considerations for buyers in this sector include the durability of the machines, effective theft protection, and compatibility with various payment systems to accommodate a diverse customer base.
Strategic Material Selection Guide for glass front vending machine
When selecting materials for glass front vending machines, international B2B buyers must consider various factors, including durability, cost, and compliance with industry standards. Below is an analysis of four common materials used in the construction of these machines, focusing on their properties, advantages, disadvantages, and implications for global buyers.
1. Tempered Glass
Key Properties:
Tempered glass is known for its high strength and thermal resistance, typically rated to withstand temperatures up to 300°C (572°F). It is also resistant to shattering, making it a safe choice for vending machines.
Pros & Cons:
The primary advantage of tempered glass is its durability and safety. It can endure significant impact without breaking, which is essential for high-traffic environments. However, it is more expensive than regular glass and can be challenging to manufacture due to the heating and cooling processes involved.
Impact on Application:
Tempered glass is ideal for vending machines that require visibility and security. Its resistance to thermal shock makes it suitable for machines placed in varying climates, from hot deserts in the Middle East to humid environments in South America.
Considerations for International Buyers:
Buyers should ensure compliance with safety standards such as ASTM C1048 in the U.S. and EN 12150 in Europe. Additionally, understanding local glass manufacturing capabilities can influence procurement decisions.
2. Stainless Steel
Key Properties:
Stainless steel is renowned for its corrosion resistance and strength, with a temperature rating that can exceed 800°C (1472°F). It is also easy to clean, making it suitable for food-related applications.
Pros & Cons:
The key advantage of stainless steel is its longevity and low maintenance requirements. However, it can be costly compared to other metals, and its weight may complicate installation and transport.
Impact on Application:
Stainless steel is often used for the machine’s frame and internal components, ensuring structural integrity and hygiene. Its resistance to corrosion makes it suitable for machines in coastal regions or areas with high humidity.
Considerations for International Buyers:
Buyers should be aware of various grades of stainless steel, such as 304 and 316, which have different corrosion resistance levels. Compliance with standards like ASTM A240 is crucial, especially for food safety.
3. Polycarbonate
Key Properties:
Polycarbonate is a lightweight thermoplastic with high impact resistance and transparency. It can withstand temperatures ranging from -40°C to 120°C (-40°F to 248°F).
Pros & Cons:
The main advantage of polycarbonate is its shatter resistance and low weight, making it easier to handle and install. However, it is less scratch-resistant than glass and can yellow over time when exposed to UV light.
Impact on Application:
This material is often used for protective panels in vending machines, providing visibility while ensuring safety. Its lightweight nature allows for more flexible design options.
Considerations for International Buyers:
Buyers should consider the UV stability of polycarbonate grades, especially in regions with high sun exposure, such as Africa and South America. Compliance with international standards like ISO 4892 for weathering is recommended.
4. Aluminum
Key Properties:
Aluminum is lightweight, corrosion-resistant, and has a melting point of approximately 660°C (1220°F). It is often anodized for additional protection and aesthetic appeal.
Pros & Cons:
The advantages of aluminum include its lightweight nature and resistance to corrosion, making it suitable for outdoor applications. However, it may not provide the same level of strength as stainless steel and can be more expensive than other metals.
Impact on Application:
Aluminum is commonly used for the machine’s exterior and structural components. Its corrosion resistance is particularly beneficial in humid or coastal environments.
Considerations for International Buyers:
Buyers should ensure that the aluminum used meets standards such as ASTM B221 for structural applications. Understanding local regulations regarding aluminum recycling can also be beneficial.
Summary Table
Material | Typical Use Case for glass front vending machine | Key Advantage | Key Disadvantage/Limitation | Relative Cost (Low/Med/High) |
---|---|---|---|---|
Tempered Glass | Front panel and visibility | High durability and safety | Higher cost, complex manufacturing | High |
Stainless Steel | Frame and internal components | Corrosion resistance, low maintenance | Higher cost, heavier weight | High |
Polycarbonate | Protective panels | Lightweight, shatter-resistant | Less scratch-resistant, UV yellowing | Medium |
Aluminum | Exterior and structural components | Lightweight, corrosion-resistant | Weaker than stainless steel | Medium |
This guide provides a comprehensive overview of material options for glass front vending machines, helping international B2B buyers make informed decisions based on their specific needs and regional considerations.
In-depth Look: Manufacturing Processes and Quality Assurance for glass front vending machine
The manufacturing process and quality assurance for glass front vending machines are critical for international B2B buyers to understand, especially when sourcing from various regions such as Africa, South America, the Middle East, and Europe. This section provides a comprehensive overview of the typical manufacturing stages, quality control processes, relevant international standards, and actionable insights for verifying supplier quality.
Manufacturing Processes
The production of glass front vending machines involves several main stages, each requiring precision and adherence to quality standards.
1. Material Preparation
The first step involves sourcing high-quality materials. Key components include:
– Glass Panels: Tempered or laminated glass is preferred for durability and safety.
– Metal Framework: Steel or aluminum is commonly used for the structural components.
– Electronic Components: These include payment systems, refrigeration units, and lighting.
Suppliers should ensure that materials meet international standards to withstand various environmental conditions, particularly in regions with extreme climates.
2. Forming
This stage encompasses the fabrication of machine components:
– Cutting and Shaping: Glass is cut to size using precision cutting tools. The metal framework is shaped using CNC machines to ensure accuracy.
– Assembly of Electronic Components: The integration of electronic systems is performed in a clean environment to prevent contamination.
Key techniques used during this stage include laser cutting for metal parts and automated glass cutting machines for efficiency and precision.
3. Assembly
In this phase, components are brought together:
– Framework Assembly: The metal structure is assembled, providing the base for the vending machine.
– Installation of Glass Panels: Glass panels are fitted securely into the frame, often using specialized adhesives or mechanical fasteners.
– Electronics Integration: All electronic components, including the power supply and user interface, are installed.
This step requires skilled labor to ensure components fit perfectly and function as intended.
4. Finishing
The final manufacturing stage includes:
– Surface Treatment: This might involve powder coating or painting the metal parts to enhance aesthetics and corrosion resistance.
– Final Assembly Checks: A thorough inspection is conducted to ensure that all components are correctly installed and that the machine operates as designed.
Quality Assurance
Quality assurance is crucial in ensuring that the vending machines meet both safety and performance standards.
International Standards
B2B buyers should be aware of various international quality standards, including:
– ISO 9001: This standard focuses on quality management systems, ensuring consistent quality in products and services.
– CE Marking: Common in Europe, this indicates compliance with health, safety, and environmental protection standards.
– API Standards: Relevant for specific components, especially for machines requiring high durability and reliability.
Quality Control Checkpoints
The quality control process typically involves several key checkpoints:
- Incoming Quality Control (IQC): Materials and components are inspected upon arrival to ensure they meet specified standards.
- In-Process Quality Control (IPQC): Ongoing inspections during manufacturing to catch defects early in the process.
- Final Quality Control (FQC): A comprehensive check of the finished product before it leaves the factory.
Common Testing Methods
Various testing methods are employed to ensure quality:
– Functional Testing: Verifying that all electronic components work correctly.
– Stress Testing: Simulating extreme conditions to assess durability.
– Safety Testing: Ensuring compliance with safety regulations, such as electrical safety standards.
Verifying Supplier Quality
For international B2B buyers, verifying the quality assurance processes of suppliers is vital. Here are actionable strategies:
- Supplier Audits: Conducting on-site audits can provide insights into the manufacturing processes and quality control systems in place. This is particularly important when sourcing from different regions.
- Quality Reports: Requesting detailed quality reports can help assess a supplier’s commitment to quality assurance.
- Third-Party Inspections: Engaging third-party inspection services can add an additional layer of verification, ensuring that products meet required standards before shipment.
QC/CERT Nuances for International Buyers
When sourcing glass front vending machines from diverse regions, buyers should consider:
– Cultural and Regulatory Differences: Understanding local manufacturing practices and regulations can help in evaluating suppliers effectively.
– Language Barriers: Clear communication is essential. Ensure that all quality documentation is available in a language that your team understands.
– Logistical Considerations: Factor in the logistics of transporting machinery, especially when dealing with large glass components, which require careful handling to avoid damage.
By grasping these manufacturing processes and quality assurance practices, B2B buyers can make informed decisions, ensuring they partner with reliable suppliers who meet their quality standards.
Related Video: Amazing Float Glass Production Process – Glass Manufacturing
Comprehensive Cost and Pricing Analysis for glass front vending machine Sourcing
When sourcing glass front vending machines, understanding the cost structure and pricing dynamics is crucial for international B2B buyers. The overall cost is composed of several components, each influencing the final price.
Cost Components
-
Materials: The primary materials include glass, metal frames, electronic components, and refrigeration systems. The quality and source of these materials significantly impact costs. For example, tempered glass can be more expensive but offers better durability.
-
Labor: Labor costs vary widely based on the region of manufacturing. In countries with lower wage standards, labor costs will be lower, but this could affect quality control and craftsmanship.
-
Manufacturing Overhead: This includes utilities, factory maintenance, and administrative expenses. Efficient factories can minimize overhead, which can be passed on as savings to buyers.
-
Tooling: Initial setup costs for molds and specialized machinery can be substantial, especially for custom designs. These costs are typically amortized over the production run.
-
Quality Control (QC): Robust QC processes ensure that machines meet specified standards, which may involve additional testing and inspection costs. Investing in quality can reduce long-term operational issues.
-
Logistics: Transportation costs depend on the distance from the manufacturer to the buyer, as well as the mode of transport. International shipping can add significant costs, especially if customs and tariffs are involved.
-
Margin: Manufacturers typically apply a markup to cover their risks and desired profit margins. Understanding standard industry margins can help buyers negotiate better pricing.
Price Influencers
Several factors influence the pricing of glass front vending machines:
-
Volume/MOQ: Higher order volumes often lead to lower per-unit costs due to economies of scale. Negotiating minimum order quantities (MOQ) can yield better pricing.
-
Specifications/Customization: Custom designs or features increase costs. Buyers should evaluate whether customization is necessary or if standard models can suffice.
-
Materials: The choice of materials directly affects pricing. Buyers should consider the long-term benefits of investing in higher-quality materials.
-
Quality/Certifications: Machines that comply with international quality standards or certifications may command higher prices but can reduce operational risks.
-
Supplier Factors: The reputation and reliability of suppliers can influence pricing. Established suppliers may charge more but offer better service and reliability.
-
Incoterms: Understanding shipping terms (like FOB, CIF) is vital, as they dictate who bears shipping costs and risks, affecting overall pricing.
Buyer Tips
-
Negotiation: Always negotiate pricing, especially when dealing with larger orders. Suppliers often have flexibility in their pricing structure.
-
Cost-Efficiency: Evaluate the total cost of ownership (TCO), which includes purchase price, maintenance, and operational costs. A cheaper machine may incur higher long-term costs.
-
Pricing Nuances: International buyers should be aware of currency fluctuations and economic conditions in the supplier’s country, as these can affect pricing.
-
Cultural Sensitivity: Understand the business culture of the supplier’s country; this can aid in negotiations and building long-term relationships.
-
Research Suppliers: Conduct thorough research on potential suppliers, including their production capabilities, delivery timelines, and after-sales service.
Disclaimer
Prices for glass front vending machines can vary widely based on the above factors. It is advisable for buyers to request detailed quotes and conduct market research to ensure competitive pricing.
Spotlight on Potential glass front vending machine Manufacturers and Suppliers
This section offers a look at a few manufacturers active in the ‘glass front vending machine’ market. This is a representative sample for illustrative purposes; B2B buyers must conduct their own extensive due diligence before any engagement. Information is synthesized from public sources and general industry knowledge.
Essential Technical Properties and Trade Terminology for glass front vending machine
Key Technical Properties of Glass Front Vending Machines
When considering the procurement of glass front vending machines, several technical specifications are crucial for ensuring product quality, functionality, and suitability for your market. Here are some key properties to evaluate:
-
Material Grade
– Definition: The quality of materials used, typically stainless steel for the frame and tempered glass for the front.
– Importance: Higher grade materials enhance durability and resistance to corrosion, essential for machines placed in high-traffic or outdoor locations, particularly in climates with extreme temperatures. -
Temperature Control Range
– Definition: The range of temperatures the vending machine can maintain for its contents, often specified in degrees Celsius or Fahrenheit.
– Importance: This is critical for businesses selling perishable goods. A reliable temperature control system ensures food safety and product quality, which is paramount for compliance with health regulations. -
Capacity and Size
– Definition: The total volume of products the vending machine can hold, usually expressed in liters or cubic feet.
– Importance: Understanding capacity helps buyers align the machine with their sales volume and space constraints. Larger capacities may be necessary for high-demand locations, while smaller machines may suit niche markets.
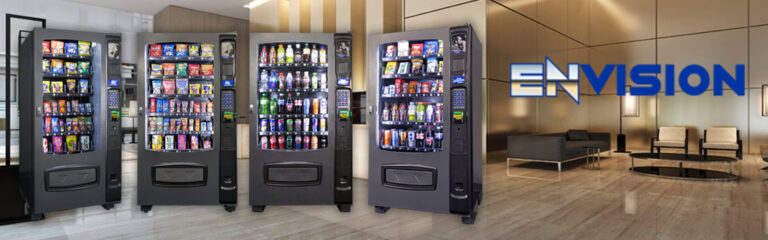
Illustrative Image (Source: Google Search)
-
Power Consumption
– Definition: The amount of electricity the machine uses, typically measured in kilowatts (kW).
– Importance: Energy efficiency is a growing concern, especially in regions where electricity costs are high. Machines with lower power consumption can reduce operational costs and are often more attractive to eco-conscious consumers. -
Payment System Compatibility
– Definition: The types of payment methods the machine can accept, such as coins, bills, credit/debit cards, or mobile payments.
– Importance: Offering diverse payment options enhances customer convenience and can increase sales. Understanding local payment preferences is particularly relevant for international buyers. -
Warranty and Service Support
– Definition: The duration and terms of the manufacturer’s warranty, alongside available service options.
– Importance: A robust warranty and accessible service support are vital for minimizing downtime and maintenance costs, particularly in regions where technical expertise may be limited.
Common Trade Terminology
Familiarity with specific trade terms can facilitate smoother transactions and negotiations. Here are some essential terms to know:
-
OEM (Original Equipment Manufacturer)
– Definition: A company that produces parts and equipment that may be marketed by another manufacturer.
– Relevance: Knowing whether a machine is OEM can affect the quality assurance process and spare parts availability, impacting long-term maintenance. -
MOQ (Minimum Order Quantity)
– Definition: The smallest quantity of a product that a supplier is willing to sell.
– Relevance: Understanding MOQ is crucial for budgeting and inventory planning, especially for smaller businesses or startups. -
RFQ (Request for Quotation)
– Definition: A document used to solicit price bids from suppliers for specific products or services.
– Relevance: An RFQ helps buyers compare prices and terms, ensuring they receive competitive offers tailored to their needs. -
Incoterms (International Commercial Terms)
– Definition: A set of predefined international trade terms published by the International Chamber of Commerce (ICC).
– Relevance: Familiarity with Incoterms helps clarify responsibilities regarding shipping, insurance, and tariffs, which is particularly important for international transactions. -
Lead Time
– Definition: The time taken from placing an order to the delivery of goods.
– Relevance: Understanding lead times is essential for inventory management and ensuring that your operations run smoothly, especially in fast-paced markets. -
After-Sales Service
– Definition: Support provided after the purchase of a product, including maintenance, repairs, and customer support.
– Relevance: Reliable after-sales service can significantly enhance customer satisfaction and loyalty, especially in regions where technical support may be scarce.
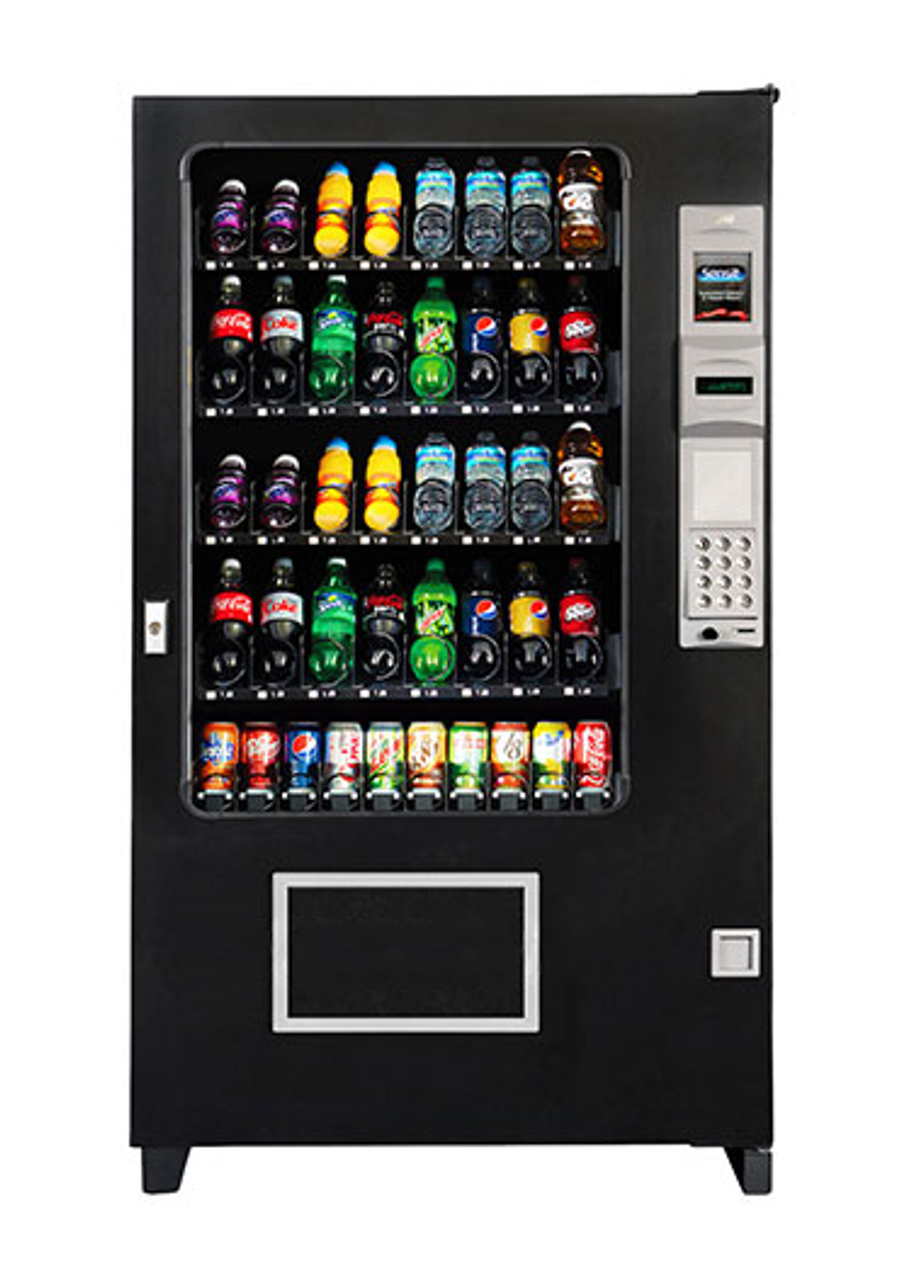
Illustrative Image (Source: Google Search)
By understanding these technical properties and trade terms, B2B buyers can make informed decisions when sourcing glass front vending machines, ensuring they meet their operational needs and market demands.
Navigating Market Dynamics, Sourcing Trends, and Sustainability in the glass front vending machine Sector
Market Overview & Key Trends
The glass front vending machine market has witnessed significant growth driven by the increasing demand for convenience and automated retail solutions across various sectors, including food, beverages, and consumer goods. Key drivers include urbanization, changing consumer lifestyles, and advancements in technology such as cashless payment systems and IoT integration. B2B buyers from regions like Africa, South America, the Middle East, and Europe are particularly interested in vending solutions that offer enhanced user experiences and operational efficiencies.
Current trends highlight the shift towards smart vending machines equipped with touchless interfaces and real-time inventory management capabilities. These features not only improve user interaction but also streamline operational processes, making them attractive to international buyers. Furthermore, the rise of health-conscious consumerism has led to a demand for vending machines that offer healthier food options and beverages, reflecting a broader trend toward wellness in consumer behavior.
Emerging sourcing trends include a focus on local suppliers to reduce lead times and logistics costs. Buyers in Europe, for instance, are increasingly inclined to partner with local manufacturers who can provide quick turnaround times and customization options. Additionally, sustainability is becoming a critical factor in purchasing decisions, with buyers seeking products that align with eco-friendly practices and certifications.
Sustainability & Ethical Sourcing in B2B
The environmental impact of manufacturing and operating glass front vending machines is a growing concern for B2B buyers. The industry is under pressure to reduce its carbon footprint and enhance resource efficiency. This has prompted many manufacturers to adopt more sustainable practices, such as using recycled materials and energy-efficient technologies in their vending machine designs.
Ethical sourcing has become paramount, with buyers prioritizing suppliers that adhere to responsible labor practices and transparent supply chains. Certifications like ISO 14001 for environmental management and Fair Trade for ethical labor practices are increasingly sought after by international buyers. By opting for vendors with these certifications, businesses can ensure their purchases contribute to sustainable development goals and demonstrate corporate social responsibility.
The trend towards green materials is notable, with manufacturers exploring the use of biodegradable plastics and energy-efficient refrigeration systems. B2B buyers are encouraged to seek out partners who can provide products with such certifications, as this not only enhances brand reputation but also appeals to a growing consumer base that values sustainability.
Brief Evolution/History
The evolution of glass front vending machines can be traced back to their inception in the early 20th century, initially serving as simple mechanisms for dispensing snacks and beverages. Over the decades, technological advancements transformed these machines into sophisticated retail solutions. The introduction of electronic payment systems in the 1980s marked a significant turning point, enhancing user convenience and expanding market reach.
In recent years, the integration of smart technology has revolutionized the industry, allowing for features such as cashless payments, remote monitoring, and advanced inventory management. This evolution not only reflects changing consumer preferences but also aligns with the broader trend of digital transformation in retail, making glass front vending machines a vital component of modern automated retail strategies. As B2B buyers navigate this landscape, understanding these historical developments can provide valuable context for making informed purchasing decisions.
Related Video: Global Trade & Logistics – What is Global Trade?
Frequently Asked Questions (FAQs) for B2B Buyers of glass front vending machine
-
What should I consider when vetting suppliers for glass front vending machines?
When vetting suppliers, prioritize their experience in manufacturing vending machines and their reputation within the industry. Check for certifications such as ISO 9001, which indicates quality management systems. Additionally, seek references or testimonials from previous clients, and assess their ability to provide after-sales support. Visiting their manufacturing facility, if possible, can also provide insights into their production capabilities and quality control processes. -
Can I customize the glass front vending machine to fit my brand?
Yes, many suppliers offer customization options to align with your branding needs. This may include color, logo placement, size adjustments, and specific internal configurations. Ensure you communicate your requirements clearly during the initial discussions. Request samples or mock-ups to visualize how the final product will appear. Be aware that customization may affect lead times and costs, so factor this into your budget and timeline. -
What is the typical minimum order quantity (MOQ) for glass front vending machines?
MOQs can vary significantly among suppliers, generally ranging from 10 to 100 units. Smaller suppliers may have lower MOQs, while larger manufacturers may require higher volumes to maintain cost-effectiveness. When negotiating, discuss your needs and explore possibilities for smaller initial orders with the option to scale up in the future. This approach can help you manage cash flow while testing market demand. -
What are the typical lead times for ordering glass front vending machines?
Lead times can depend on factors such as customization, order size, and supplier location. Generally, expect lead times of 4 to 12 weeks after order confirmation. It’s advisable to confirm these timelines upfront and consider seasonal fluctuations that might affect production schedules. Establish a clear communication channel with your supplier to receive updates on the manufacturing process and any potential delays. -
What quality assurance measures should I expect from suppliers?
Reputable suppliers will have a robust quality assurance (QA) process in place. This typically includes inspections at various stages of production, adherence to international quality standards, and testing of the final product. Request documentation of their QA procedures and any certifications they hold. Additionally, inquire about their policy for handling defective units, including warranties and return processes. -
What certifications should I look for in glass front vending machines?
Key certifications include CE marking for compliance with European safety standards, UL listing for safety in the United States, and RoHS compliance for hazardous materials. These certifications help ensure the machines meet safety and environmental regulations, which is particularly important when importing products. Verify these certifications with your supplier and ensure they are current and applicable to your specific market. -
How do I handle logistics and shipping for international orders of vending machines?
Logistics can be complex when importing vending machines. Work with your supplier to understand the best shipping methods (e.g., sea freight, air freight) based on your timeline and budget. Ensure that all shipping documents, such as bills of lading and customs declarations, are accurate and complete to avoid delays. Consider hiring a freight forwarder experienced in international trade to streamline the process and navigate customs regulations. -
What steps should I take if I encounter a dispute with a supplier?
In the event of a dispute, first, try to resolve the issue through direct communication with your supplier. Document all interactions and agreements in writing for clarity. If resolution is not possible, refer to the contract terms regarding dispute resolution, which may include mediation or arbitration. Being familiar with international trade laws relevant to your transaction can also aid in resolving disputes effectively.
Strategic Sourcing Conclusion and Outlook for glass front vending machine
In conclusion, the strategic sourcing of glass front vending machines presents a robust opportunity for international B2B buyers, especially those in Africa, South America, the Middle East, and Europe. By focusing on quality suppliers who prioritize innovation, sustainability, and customer service, businesses can enhance their operational efficiency and customer engagement.
Key takeaways include the importance of assessing supplier capabilities, understanding market trends, and leveraging technology for better inventory management. Additionally, forging strong partnerships with manufacturers can lead to more favorable terms and improved product offerings.
As the market evolves, it is crucial for buyers to remain agile and responsive to consumer demands. Embracing these strategies will not only ensure competitive advantage but also foster long-term growth.
Now is the time for B2B buyers to take action—evaluate your sourcing strategies, engage with potential suppliers, and position your business at the forefront of the vending machine revolution. The future is bright for those who are proactive and strategic in their procurement processes.