Your Ultimate Guide to Sourcing Northwestern Vending
Guide to Northwestern Vending Machines
- Introduction: Navigating the Global Market for northwestern vending machines
- Understanding northwestern vending machines Types and Variations
- Key Industrial Applications of northwestern vending machines
- Strategic Material Selection Guide for northwestern vending machines
- In-depth Look: Manufacturing Processes and Quality Assurance for northwestern vending machines
- Comprehensive Cost and Pricing Analysis for northwestern vending machines Sourcing
- Spotlight on Potential northwestern vending machines Manufacturers and Suppliers
- Essential Technical Properties and Trade Terminology for northwestern vending machines
- Navigating Market Dynamics, Sourcing Trends, and Sustainability in the northwestern vending machines Sector
- Frequently Asked Questions (FAQs) for B2B Buyers of northwestern vending machines
- Strategic Sourcing Conclusion and Outlook for northwestern vending machines
Introduction: Navigating the Global Market for northwestern vending machines
Navigating the global market for northwestern vending machines presents a unique opportunity for international B2B buyers seeking innovative solutions to enhance their operations. These machines have evolved beyond simple snack dispensers into sophisticated, technology-driven platforms capable of delivering a wide array of products, from beverages to electronics. As urbanization and consumer demand for convenience rise, the importance of these machines has never been more critical.
This comprehensive guide delves into various aspects of northwestern vending machines, including the types available, materials used in their construction, manufacturing and quality control processes, and reputable suppliers. We also explore cost considerations, market trends, and address frequently asked questions (FAQs) to empower buyers with the knowledge needed for informed sourcing decisions.
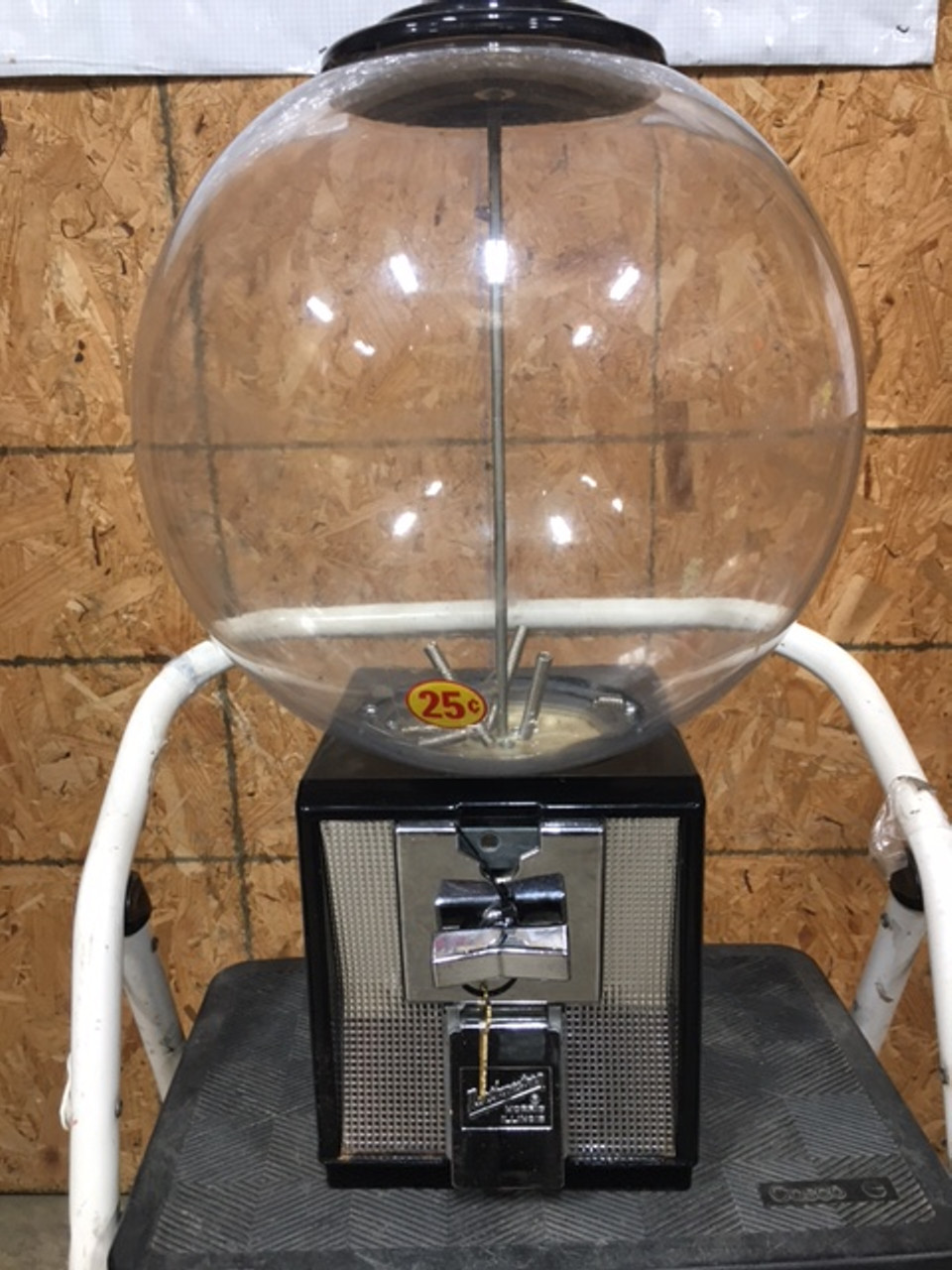
Illustrative Image (Source: Google Search)
For B2B buyers from regions such as Africa, South America, the Middle East, and Europe—including key markets like France and Nigeria—this guide serves as an invaluable resource. By understanding the nuances of the vending machine landscape, buyers can identify the best products that align with their strategic goals, ensuring they remain competitive in a rapidly changing market. Equip yourself with the insights to make well-informed purchasing decisions that cater to the evolving needs of your customers and your business.
Understanding northwestern vending machines Types and Variations
Type Name | Key Distinguishing Features | Primary B2B Applications | Brief Pros & Cons for Buyers |
---|---|---|---|
Snack Vending Machines | Offer a variety of packaged snacks | Offices, schools, public areas | Pros: Easy to maintain; Cons: Limited healthy options |
Beverage Vending Machines | Dispense cold drinks, often with refrigeration | Cafeterias, gyms, events | Pros: High turnover; Cons: Requires regular restocking |
Combo Vending Machines | Combine snacks and beverages in one unit | Multi-purpose locations | Pros: Space-saving; Cons: More complex maintenance |
Fresh Food Vending Machines | Provide perishable items like sandwiches and salads | Hospitals, universities, airports | Pros: Attract health-conscious consumers; Cons: Short shelf life |
Specialty Vending Machines | Offer niche products (e.g., electronics, cosmetics) | Retail environments, tech hubs | Pros: Unique offerings; Cons: Higher initial investment |
Snack Vending Machines
Snack vending machines are designed to provide a range of packaged snacks, including chips, candies, and granola bars. They are commonly found in offices, schools, and public areas where quick, convenient snack options are desired. When considering a purchase, buyers should evaluate the machine’s capacity, ease of maintenance, and the variety of snacks offered, as consumer preferences can vary greatly.
Beverage Vending Machines
These machines are specifically engineered to dispense a wide array of cold beverages, typically featuring refrigeration capabilities to keep drinks chilled. They are ideal for use in cafeterias, gyms, and event venues where quick refreshment is needed. Buyers should consider the machine’s energy efficiency, the variety of drinks it can accommodate, and the frequency of required restocking to maintain inventory levels.
Combo Vending Machines
Combo vending machines combine both snacks and beverages, making them a versatile option for locations with limited space. These machines are particularly suited for multi-purpose environments such as break rooms and waiting areas. When purchasing, buyers should assess the machine’s layout, user interface, and the balance of snack and drink offerings to meet diverse consumer needs.
Fresh Food Vending Machines
Fresh food vending machines offer a selection of perishable items, such as sandwiches, salads, and fruits. They cater to health-conscious consumers and are commonly placed in hospitals, universities, and airports. Key purchasing considerations include the machine’s refrigeration capabilities, the quality and freshness of the food offered, and the logistics of regular inventory turnover to ensure food safety.
Specialty Vending Machines
Specialty vending machines provide unique products that are not typically found in standard vending options, such as electronics, cosmetics, or artisan foods. These machines are often located in retail environments and tech hubs, targeting specific consumer segments. Buyers should evaluate the market demand for the specialty products, the machine’s technology, and the overall investment required for stocking and maintenance.
Related Video: CS 198-126: Lecture 12 – Diffusion Models
Key Industrial Applications of northwestern vending machines
Industry/Sector | Specific Application of northwestern vending machines | Value/Benefit for the Business | Key Sourcing Considerations for this Application |
---|---|---|---|
Retail | Automated snack and beverage dispensing | Increased sales, reduced labor costs, enhanced customer experience | Machine capacity, product variety, payment system compatibility |
Education | Campus vending for healthy meal options | Promotes healthy eating, provides convenience for students | Nutritional compliance, machine durability, payment options |
Transportation | Vending at transit hubs for on-the-go meals | Captures commuter market, reduces food waste, increases revenue | Space requirements, product freshness, local regulations |
Healthcare | Vending machines for medical supplies and snacks | Provides quick access to essentials, enhances patient satisfaction | Compliance with health regulations, inventory management, reliability |
Corporate Offices | Office snack and beverage stations | Boosts employee morale, increases productivity, saves time | Customization options, machine aesthetics, service frequency |
Retail Applications
In the retail sector, northwestern vending machines serve as automated snack and beverage dispensers in high-traffic areas. They provide a convenient shopping experience, allowing customers to make quick purchases without the need for staff assistance. This not only increases sales but also reduces labor costs, which is particularly important for businesses operating in regions like Africa and South America where labor expenses can be significant. Buyers should consider machine capacity and product variety to meet consumer demand effectively.
Education Sector Integration
In educational institutions, these vending machines can offer healthy meal options, promoting better eating habits among students. They cater to the fast-paced lifestyle of students who may not have time for traditional meals, thus ensuring they have access to nutritious food. For international buyers, especially in Europe, compliance with nutritional guidelines and machine durability are critical factors to address.
Transportation Hubs
Transportation hubs, such as bus and train stations, benefit from northwestern vending machines that provide quick meal options for commuters. This application helps capture the commuter market and reduces food waste by offering fresh, easily consumable products. Buyers in the Middle East and Europe should consider space requirements and local regulations regarding food sales when sourcing these machines.
Healthcare Facilities
In healthcare settings, vending machines can dispense medical supplies, snacks, and drinks, enhancing patient satisfaction by providing quick access to essential items. This is particularly beneficial in hospitals where time is of the essence. Buyers need to ensure that machines comply with health regulations and maintain reliable inventory management to prevent shortages.
Corporate Office Solutions
For corporate offices, northwestern vending machines can serve as snack and beverage stations, boosting employee morale and productivity by saving time during breaks. Customization options allow businesses to tailor offerings to employee preferences. When sourcing these machines, considerations should include aesthetics and the frequency of service to maintain optimal stock levels.
Related Video: Kooler Ice Vending Machines – IM600XL vs. IM1000
Strategic Material Selection Guide for northwestern vending machines
When selecting materials for northwestern vending machines, it is essential to consider various factors that influence performance, durability, and cost-effectiveness. Below, we analyze four common materials used in the construction of these machines, focusing on their properties, advantages, disadvantages, and specific considerations for international B2B buyers.
1. Stainless Steel (e.g., AISI 304/316)
Key Properties: Stainless steel is known for its excellent corrosion resistance, high strength, and ability to withstand high temperatures. It is also easy to clean, making it ideal for vending machines that dispense food and beverages.
Pros & Cons: The primary advantage of stainless steel is its durability and resistance to rust and staining, which prolongs the lifespan of vending machines. However, it can be more expensive than other materials, and its manufacturing process is often more complex due to the need for specialized welding and finishing techniques.
Impact on Application: Stainless steel is compatible with a wide range of media, including water, soft drinks, and snacks. Its non-reactive nature ensures that it does not alter the taste or quality of the products dispensed.
Considerations for International Buyers: Buyers from regions like Africa and South America should ensure compliance with local food safety standards, which may vary. In Europe, adherence to ASTM and DIN standards is crucial, and buyers should verify that the grade of stainless steel meets these requirements.
2. Carbon Steel (e.g., A216 WCB)
Key Properties: Carbon steel is a strong and cost-effective material with good mechanical properties. It can be treated with coatings to enhance corrosion resistance.
Pros & Cons: The main advantage of carbon steel is its affordability and strength, making it suitable for structural components of vending machines. However, it is susceptible to corrosion if not adequately protected, which can lead to maintenance challenges.
Impact on Application: While carbon steel is suitable for non-corrosive fluids and dry products, it may not be ideal for machines dispensing liquids or products that could cause rusting.
Considerations for International Buyers: Buyers should consider the local climate, as humid conditions can accelerate corrosion. Compliance with JIS standards is often required in Japan, while European buyers may look for adherence to EN standards.
3. Aluminum
Key Properties: Aluminum is lightweight, corrosion-resistant, and has good thermal conductivity. It is often used in vending machine panels and frames.
Pros & Cons: The lightweight nature of aluminum makes it easy to handle and install, reducing shipping costs. However, it is less durable than stainless steel and can be prone to denting and scratching.
Impact on Application: Aluminum is suitable for vending machines that dispense lightweight products and is often used in outdoor applications due to its resistance to corrosion.
Considerations for International Buyers: Buyers should ensure that the aluminum used meets local standards for strength and corrosion resistance. In Europe, compliance with EN standards is essential, while in the Middle East, buyers should consider local regulations regarding material sourcing.
4. Polycarbonate
Key Properties: Polycarbonate is a strong, impact-resistant plastic that offers good transparency and UV resistance. It is often used for vending machine windows and components.
Pros & Cons: The major advantage of polycarbonate is its lightweight and shatter-resistant properties, making it ideal for high-traffic areas. However, it can be more expensive than other plastics and may not have the same durability as metals.
Impact on Application: Polycarbonate is suitable for applications where visibility is essential, such as displaying products in vending machines. It is also compatible with a variety of food products.
Considerations for International Buyers: Buyers should check for compliance with food safety regulations, especially in regions where plastic materials are scrutinized. Standards such as FDA compliance in the U.S. or EU regulations in Europe are critical for ensuring safety.
Summary Table
Material | Typical Use Case for northwestern vending machines | Key Advantage | Key Disadvantage/Limitation | Relative Cost (Low/Med/High) |
---|---|---|---|---|
Stainless Steel (e.g., AISI 304/316) | Structural components and surfaces for food and beverage dispensing | Excellent corrosion resistance and durability | Higher cost and complex manufacturing | High |
Carbon Steel (e.g., A216 WCB) | Structural components for dry products | Cost-effective and strong | Susceptible to corrosion without protection | Low |
Aluminum | Panels and frames for lightweight products | Lightweight and easy to install | Less durable, prone to dents | Medium |
Polycarbonate | Windows and transparent components for visibility | Impact-resistant and lightweight | More expensive and less durable than metals | Medium |
This guide provides a comprehensive overview of material selection for northwestern vending machines, helping international buyers make informed decisions based on their specific needs and regional standards.
In-depth Look: Manufacturing Processes and Quality Assurance for northwestern vending machines
Manufacturing Processes for Northwestern Vending Machines
Manufacturing vending machines, particularly those designed for the northwestern market, involves a series of systematic processes that ensure both functionality and quality. Understanding these processes can help international B2B buyers make informed decisions when sourcing these machines.
Main Stages of Manufacturing
-
Material Preparation
– Sourcing Raw Materials: The first step involves sourcing high-quality materials such as steel for the chassis, glass or plastic for the display, and electronic components for operational efficiency. Suppliers should be vetted for reliability and quality assurance.
– Pre-processing: Materials undergo initial treatments like cutting, bending, and coating to enhance durability and aesthetics. This stage often includes surface treatments to prevent corrosion, especially for machines intended for outdoor use. -
Forming
– Metal Fabrication: Using techniques like laser cutting and CNC machining, manufacturers shape the metal components. This precision ensures that parts fit together seamlessly, which is crucial for the overall integrity of the vending machine.
– Injection Molding: For plastic components, injection molding is commonly used. This method allows for the production of complex shapes and ensures uniformity across batches. -
Assembly
– Component Integration: The assembly line integrates various components, including refrigeration units, payment systems, and display interfaces. Each machine is assembled according to strict specifications to ensure compatibility and functionality.
– Electrical Wiring: Skilled technicians handle the wiring of electronic components, ensuring that all systems, from lighting to payment processing, operate correctly. Effective management of this stage is crucial for minimizing electrical failures. -
Finishing
– Quality Coating: The final stage involves applying protective coatings and finishes to enhance the aesthetic appeal and longevity of the machine. This could include powder coating or painting to achieve the desired look.
– Final Assembly Checks: Before the machines are deemed ready for shipment, they undergo final assembly checks to ensure that all parts are securely fitted and that the machine meets design specifications.
Quality Assurance in Manufacturing
Quality assurance (QA) is critical in the manufacturing of vending machines to ensure that they meet international standards and customer expectations.
Relevant International Standards
- ISO 9001: This is a widely recognized standard for quality management systems (QMS). Compliance indicates that the manufacturer consistently meets customer and regulatory requirements.
- CE Marking: For machines sold in Europe, CE marking is essential. It signifies compliance with health, safety, and environmental protection standards set by the European Union.
- API Certification: For vending machines that dispense food or beverages, adherence to the American Petroleum Institute (API) standards ensures safety and operational integrity.
Quality Control Checkpoints
-
Incoming Quality Control (IQC)
– This initial checkpoint involves inspecting raw materials upon receipt. Suppliers are assessed for quality compliance, and materials that do not meet specifications are rejected. -
In-Process Quality Control (IPQC)
– Throughout the manufacturing process, quality checks are performed at various stages. This includes monitoring assembly accuracy and functionality of electronic components. Any deviations from the set standards are addressed immediately. -
Final Quality Control (FQC)
– Before shipping, each vending machine undergoes a comprehensive quality inspection. This includes testing for operational efficiency, safety compliance, and aesthetic quality.
Common Testing Methods
- Functional Testing: Ensures that all features of the vending machine operate as intended. This includes testing payment acceptance, dispensing mechanisms, and electronic displays.
- Durability Testing: Machines are subjected to stress tests to simulate long-term usage, ensuring they can withstand environmental factors and user interactions.
- Electrical Safety Testing: This includes verifying that machines are safe for use and comply with electrical standards, preventing potential hazards.
Verifying Supplier Quality Control
For international B2B buyers, particularly those in regions like Africa, South America, the Middle East, and Europe, verifying the quality control processes of suppliers is paramount.
- Audits: Conducting regular audits of the manufacturing facility can provide insights into the QMS in place. Buyers should request audit reports to assess compliance with international standards.
- Quality Reports: Suppliers should provide detailed quality reports that outline the results of IQC, IPQC, and FQC processes. This transparency can help buyers gauge the reliability of the manufacturing process.
- Third-Party Inspections: Engaging third-party inspection services can provide an unbiased assessment of the manufacturing quality. This is particularly useful for buyers who may not be able to visit the manufacturing site.
Quality Control Nuances for International Buyers
Understanding the nuances of quality control can significantly impact the purchasing decisions of international B2B buyers.
- Cultural Considerations: Different regions may have varying standards and expectations regarding quality. Buyers from Africa and South America may need to emphasize specific features that cater to local market demands.
- Regulatory Compliance: Buyers must ensure that the machines comply with local regulations in their respective countries. This may involve additional certifications beyond ISO and CE marking.
- Post-Purchase Support: Establishing clear communication regarding warranty and support services can ensure that buyers have access to assistance in case of operational issues.
By comprehensively understanding the manufacturing processes and quality assurance practices of northwestern vending machines, international B2B buyers can make informed decisions that align with their operational needs and market expectations.
Related Video: Amazing scenes。Top 6 Most Popular Factory Manufacturing Videos in China
Comprehensive Cost and Pricing Analysis for northwestern vending machines Sourcing
When considering the sourcing of northwestern vending machines, understanding the comprehensive cost structure and pricing dynamics is essential for international B2B buyers. This section will delve into the various cost components involved, the factors that influence pricing, and provide actionable insights tailored for buyers from Africa, South America, the Middle East, and Europe.
Cost Components
-
Materials: The primary cost driver in vending machines is the materials used in production. Common materials include stainless steel, plastic, and electronic components. Sourcing high-quality materials can significantly impact the overall price, especially if suppliers are located far from the manufacturing site.
-
Labor: Labor costs vary widely depending on the region of manufacturing. In countries with lower labor costs, such as some in Africa and South America, total production expenses can be reduced. However, consider the trade-offs in terms of quality and expertise.
-
Manufacturing Overhead: This encompasses the indirect costs associated with production, such as utilities, rent, and equipment maintenance. Efficient manufacturing processes can help minimize these costs, making it crucial to assess potential suppliers’ operational efficiencies.
-
Tooling: The initial setup for manufacturing vending machines requires significant investment in tooling. Buyers should inquire about the tooling costs and whether these will be amortized over a large volume of units, which can lower the per-unit cost.
-
Quality Control (QC): Ensuring that vending machines meet international quality standards incurs additional costs. Implementing strict QC measures is essential for long-term reliability and can prevent costly recalls or repairs.
-
Logistics: Shipping and handling costs can fluctuate based on the distance from the manufacturer to the buyer’s location. Buyers should consider the implications of Incoterms, which dictate the responsibilities of buyers and sellers in shipping arrangements.
-
Margin: Suppliers typically add a margin to cover their costs and profits. Understanding the margin expectations of different suppliers can provide leverage during negotiations.
Price Influencers
-
Volume/MOQ (Minimum Order Quantity): Pricing often decreases with higher volumes. Buyers should assess their needs and explore options for bulk purchases to negotiate better rates.
-
Specifications/Customization: Custom features or specifications can increase costs. Clearly defining requirements upfront can help mitigate unexpected price increases later in the process.
-
Materials and Quality Certifications: Higher quality materials and certifications (like ISO) generally come at a premium. Buyers should weigh the benefits of investing in higher quality against the potential for increased longevity and customer satisfaction.
-
Supplier Factors: The reputation, reliability, and geographic location of suppliers can influence pricing. Established suppliers with a proven track record may charge more but can offer greater assurance of quality and service.
-
Incoterms: The choice of Incoterms can significantly affect the total cost. Understanding terms like FOB (Free on Board) or CIF (Cost, Insurance, and Freight) is crucial for budget forecasting.
Buyer Tips
-
Negotiation: Always approach negotiations with a clear understanding of your requirements and the market landscape. Leverage volume commitments to secure better pricing.
-
Cost-Efficiency: Calculate the Total Cost of Ownership (TCO) by considering not just the purchase price but also maintenance, operational costs, and potential downtime.
-
Pricing Nuances: Be aware of local economic factors that might influence pricing, such as tariffs, currency fluctuations, and regional demand.
-
Research: Invest time in researching potential suppliers and their offerings. A thorough understanding of their capabilities and past performance can guide better purchasing decisions.
Disclaimer
Prices for northwestern vending machines can vary widely based on numerous factors. This analysis provides indicative insights; actual costs may differ based on specific buyer requirements, supplier negotiations, and market conditions. Always request detailed quotes from multiple suppliers to ensure competitive pricing.
Spotlight on Potential northwestern vending machines Manufacturers and Suppliers
This section offers a look at a few manufacturers active in the ‘northwestern vending machines’ market. This is a representative sample for illustrative purposes; B2B buyers must conduct their own extensive due diligence before any engagement. Information is synthesized from public sources and general industry knowledge.
Essential Technical Properties and Trade Terminology for northwestern vending machines
Key Technical Properties of Northwestern Vending Machines
When considering the procurement of vending machines, especially in diverse international markets, understanding the essential technical properties is crucial for making informed purchasing decisions. Here are some critical specifications:
- Material Grade
Vending machines are typically constructed from various materials, including stainless steel, ABS plastic, and tempered glass. Stainless steel is favored for its durability and resistance to corrosion, making it ideal for outdoor or high-traffic environments. The material grade affects not only the machine’s longevity but also its aesthetic appeal, which can influence customer interactions.
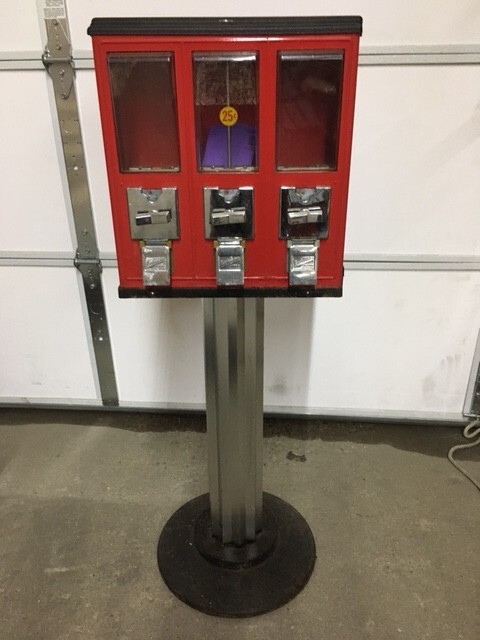
Illustrative Image (Source: Google Search)
-
Temperature Control Range
This specification indicates the operational temperature limits for food and beverage storage. For instance, machines designed for perishable items must maintain a temperature range of 0°C to 4°C. Understanding this range is vital for compliance with health regulations and ensuring product freshness, which directly impacts sales and customer satisfaction. -
Power Consumption
The energy efficiency of vending machines is measured in kilowatt-hours (kWh). Machines with lower power consumption can significantly reduce operational costs, making them more attractive for long-term investment. It’s essential to analyze the energy rating to ensure sustainability and cost-effectiveness, especially for businesses in regions where energy costs are high. -
Capacity and Size
The dimensions and internal capacity of a vending machine determine how many products it can hold. This is crucial for maximizing revenue potential in high-traffic locations. Buyers should assess their space and product offerings to select a machine that meets their specific needs without overcrowding or underutilizing available space. -
User Interface and Payment Options
A user-friendly interface is vital for customer engagement. Modern vending machines often feature touchscreen displays and support multiple payment methods, including cash, credit/debit cards, and mobile payments. The versatility in payment options can enhance the customer experience and increase sales, particularly in urban areas where cashless transactions are preferred. -
Remote Monitoring Capabilities
Advanced vending machines come equipped with IoT technology, allowing operators to monitor inventory levels and machine performance remotely. This capability enables proactive maintenance and reduces downtime, ultimately leading to increased operational efficiency and profitability.
Common Trade Terminology
Understanding industry jargon is essential for effective communication and negotiation in B2B transactions. Here are several key terms that international buyers should know:
-
OEM (Original Equipment Manufacturer)
An OEM refers to a company that produces parts or equipment that may be marketed by another manufacturer. In the vending machine industry, this often relates to components like payment systems or refrigeration units. Buyers should consider OEM partnerships for quality assurance and reliability. -
MOQ (Minimum Order Quantity)
MOQ is the smallest quantity of a product that a supplier is willing to sell. Understanding the MOQ is critical for budgeting and inventory management, especially for businesses looking to scale operations without overcommitting resources. -
RFQ (Request for Quotation)
An RFQ is a standard business process where a buyer solicits price quotes from suppliers for specific products or services. This document outlines quantities, specifications, and terms of delivery, enabling buyers to compare offers effectively. -
Incoterms (International Commercial Terms)
Incoterms define the responsibilities of buyers and sellers in international transactions, covering aspects such as shipping, insurance, and delivery. Familiarity with these terms helps buyers understand their liabilities and negotiate better shipping agreements, particularly when dealing with cross-border suppliers. -
Lead Time
Lead time refers to the time taken from placing an order to receiving the goods. For vending machines, understanding lead times is crucial for planning deployments and ensuring product availability in targeted locations.
- Warranty Period
This term indicates the duration for which the manufacturer guarantees the machine against defects. A longer warranty period often reflects higher quality and can provide peace of mind for buyers, making it an essential consideration in the purchasing decision.
By grasping these technical properties and trade terms, B2B buyers can enhance their purchasing strategies and ensure they select the right vending machines for their markets.
Navigating Market Dynamics, Sourcing Trends, and Sustainability in the northwestern vending machines Sector
Market Overview & Key Trends
The northwestern vending machines sector is undergoing significant transformation driven by technological advancements and changing consumer behaviors. As international B2B buyers, particularly from Africa, South America, the Middle East, and Europe, it is essential to understand these dynamics. Digitalization is one of the key drivers, with smart vending machines equipped with IoT capabilities enhancing inventory management and customer interaction. This trend enables real-time data analytics, allowing operators to optimize stock levels and respond swiftly to consumer preferences.
Another emerging trend is the increased demand for contactless payment solutions. The COVID-19 pandemic accelerated this shift, pushing companies to adopt cashless transactions. Vending machines now commonly accept mobile payments, QR codes, and credit cards, making them more accessible to a broader customer base. Additionally, sustainability is becoming a critical factor in purchasing decisions. Buyers are increasingly favoring vendors that prioritize eco-friendly practices, such as using energy-efficient machines and recyclable materials.
Moreover, the market is witnessing a rise in personalized offerings. Vending machines are evolving from simple snack dispensers to multi-product platforms that provide tailored options, including healthy snacks and beverages that cater to local tastes. This customization is crucial for attracting diverse consumer segments in different regions, particularly in Africa and South America, where dietary preferences vary widely.
Sustainability & Ethical Sourcing in B2B
Sustainability in the northwestern vending machines sector is not just a trend; it’s becoming a necessity for international B2B buyers. The environmental impact of manufacturing and operating vending machines is substantial, necessitating a focus on ethical sourcing and sustainable practices. Buyers must prioritize suppliers who demonstrate a commitment to reducing their carbon footprint, using energy-efficient technologies, and minimizing waste.
The use of green certifications can serve as a valuable guide for B2B buyers. Certifications such as ENERGY STAR, ISO 14001, and LEED can help identify vendors committed to sustainable practices. Additionally, sourcing materials that are recyclable or biodegradable is increasingly important, as it aligns with global efforts to reduce plastic waste. For example, opting for machines made from recycled materials or those that offer products in eco-friendly packaging can significantly enhance a company’s sustainability profile.
Furthermore, ethical supply chains are essential for building trust with consumers and stakeholders. Ensuring that suppliers adhere to fair labor practices and environmental standards not only helps mitigate risks but also enhances brand reputation in a competitive market. As buyers in regions such as Europe and the Middle East become more discerning, the emphasis on ethical sourcing will likely continue to grow.
Brief Evolution/History
The evolution of vending machines dates back to ancient Greece, where simple devices dispensed holy water. However, the modern vending machine as we know it began in the early 20th century, primarily offering candies and cigarettes. Over the decades, advancements in technology have transformed these machines into sophisticated retail platforms. Today, they offer a wide variety of products—from snacks and beverages to electronics—reflecting changes in consumer habits and preferences. This historical context is crucial for B2B buyers, as it highlights the ongoing innovation and adaptability of the sector, which continues to evolve in response to market demands and technological advancements.
Understanding these trends and sustainability imperatives will empower international B2B buyers to make informed decisions, ensuring they partner with suppliers who align with their business values and customer expectations.
Related Video: Is global trade transforming? | Counting the Cost
Frequently Asked Questions (FAQs) for B2B Buyers of northwestern vending machines
-
What should I consider when vetting suppliers of Northwestern vending machines?
When vetting suppliers, prioritize their experience in the vending machine industry and their reputation in international markets. Look for certifications such as ISO 9001 for quality management systems. Request references from previous clients, particularly those in your region, to assess their reliability and service quality. Additionally, evaluate their production capabilities, response times, and after-sales support, as these factors significantly impact your business relationship and operational efficiency. -
Can I customize Northwestern vending machines to fit my business needs?
Yes, customization is often available for Northwestern vending machines. Discuss specific requirements such as branding, product selection, payment options, and machine size with potential suppliers. Ensure that the supplier has experience with custom orders and can provide examples of previous projects. This will help you gauge their capability to meet your specific needs while aligning with your brand identity. -
What are the typical minimum order quantities (MOQ) and lead times for these machines?
MOQs can vary significantly depending on the supplier and the complexity of the machines. Generally, you can expect MOQs to range from 5 to 20 units. Lead times typically range from 4 to 12 weeks, influenced by factors such as customization and shipping logistics. It’s advisable to confirm these details upfront and factor in additional time for potential delays, especially when importing goods across international borders. -
What payment terms should I expect when sourcing vending machines internationally?
Payment terms can vary, but common practices include a deposit (usually 30-50%) upfront with the balance due before shipment. Some suppliers may offer letters of credit or escrow services for added security. Ensure you understand the payment terms clearly and negotiate favorable conditions that protect your interests, especially when dealing with international transactions where risks may be higher. -
How can I ensure quality assurance and certifications for the machines?
Request documentation regarding quality assurance processes from your supplier, including inspection reports and compliance certifications. Key certifications to look for include CE marking for European markets and UL certification for safety standards in North America. Additionally, consider arranging for third-party inspections during manufacturing to ensure the machines meet your specifications and standards before shipment. -
What logistics considerations should I keep in mind when importing vending machines?
Logistics plays a crucial role in the successful importation of vending machines. Factor in shipping methods (sea or air freight), customs clearance processes, and potential tariffs or duties. Collaborate with a logistics partner experienced in international trade to navigate these complexities. Ensure you have all necessary documentation ready, such as bills of lading and commercial invoices, to facilitate a smooth shipping process. -
How should I handle disputes with suppliers?
To mitigate disputes, establish clear contracts detailing terms of service, delivery timelines, and quality expectations. In the event of a dispute, try to resolve issues amicably through open communication. If necessary, consider mediation or arbitration as alternatives to litigation. Familiarize yourself with international dispute resolution mechanisms relevant to your jurisdiction, which can provide structured processes for resolving conflicts. -
What are the common challenges faced by international buyers of vending machines?
International buyers often encounter challenges such as language barriers, cultural differences, and varying legal regulations. Additionally, fluctuations in currency exchange rates can impact costs. To address these challenges, work with local agents who understand the market dynamics and can facilitate communication. Stay informed about local laws and regulations concerning vending operations to ensure compliance and smooth business operations.
Strategic Sourcing Conclusion and Outlook for northwestern vending machines
In conclusion, strategic sourcing is pivotal for optimizing procurement processes in the vending machine sector, particularly for international B2B buyers. By leveraging local market insights and supplier relationships, businesses can enhance their operational efficiencies and reduce costs. Key takeaways include the importance of understanding regional market dynamics, evaluating supplier capabilities, and aligning procurement strategies with business objectives.
Moreover, the integration of technology in vending machines presents significant opportunities for value creation through enhanced customer engagement and operational monitoring. Buyers should prioritize suppliers that demonstrate innovation and adaptability to meet evolving consumer demands.
As you navigate the complexities of sourcing vending machines in diverse markets such as Africa, South America, the Middle East, and Europe, consider the long-term benefits of building strategic partnerships. Embrace a proactive approach to sourcing that not only addresses immediate needs but also positions your business for sustainable growth.
Now is the time to take action—evaluate your sourcing strategies, identify potential suppliers, and explore innovative solutions that can elevate your vending machine offerings in the global market.