Mastering Box Vending Machine Sourcing: Unlock Cost Savings
Guide to Box Vending Machine
- Introduction: Navigating the Global Market for box vending machine
- Understanding box vending machine Types and Variations
- Key Industrial Applications of box vending machine
- Strategic Material Selection Guide for box vending machine
- In-depth Look: Manufacturing Processes and Quality Assurance for box vending machine
- Comprehensive Cost and Pricing Analysis for box vending machine Sourcing
- Spotlight on Potential box vending machine Manufacturers and Suppliers
- Essential Technical Properties and Trade Terminology for box vending machine
- Navigating Market Dynamics, Sourcing Trends, and Sustainability in the box vending machine Sector
- Frequently Asked Questions (FAQs) for B2B Buyers of box vending machine
- Strategic Sourcing Conclusion and Outlook for box vending machine
Introduction: Navigating the Global Market for box vending machine
In the rapidly evolving landscape of global commerce, the box vending machine stands out as a versatile solution for businesses aiming to enhance customer engagement and streamline product distribution. These machines not only cater to traditional vending needs but also offer innovative features such as cashless payments, remote inventory management, and customizable product selections. For B2B buyers in regions like Africa, South America, the Middle East, and Europe, investing in box vending machines can significantly reduce operational costs while maximizing reach and convenience.
This comprehensive guide delves into various aspects of box vending machines, including types available on the market, materials used in construction, manufacturing processes, quality control measures, and a directory of reliable suppliers. Additionally, it provides insights into pricing structures, market trends, and answers to frequently asked questions, ensuring that buyers are well-equipped to make informed decisions.
By empowering international B2B buyers with actionable insights and data-driven analyses, this guide aims to facilitate effective sourcing strategies. Whether you are a retailer looking to expand your product offerings or an entrepreneur seeking new revenue streams, understanding the nuances of box vending machines will enable you to navigate the complexities of the global market confidently. With the right knowledge, you can harness the potential of this technology to elevate your business operations and meet the ever-changing demands of consumers.
Understanding box vending machine Types and Variations
Type Name | Key Distinguishing Features | Primary B2B Applications | Brief Pros & Cons for Buyers |
---|---|---|---|
Traditional Box Vending Machine | Mechanical operation with coin and bill acceptors | Office buildings, schools | Pros: Simple operation, widely accepted. Cons: Limited payment options, lower tech integration. |
Smart Box Vending Machine | Digital interfaces, cashless payment options, remote monitoring | Airports, shopping malls | Pros: Enhanced user experience, diverse payment methods. Cons: Higher initial investment. |
Customized Product Vending Machine | Tailored compartments for specific products (e.g., electronics, cosmetics) | Retail stores, events | Pros: Attracts niche markets, increases brand visibility. Cons: Potentially limited product range. |
Refrigerated Box Vending Machine | Temperature-controlled compartments for perishable goods | Hospitals, gyms, convenience stores | Pros: Expands product offerings to food and beverages. Cons: Requires more maintenance and power. |
Eco-Friendly Box Vending Machine | Uses sustainable materials and energy-efficient technology | Educational institutions, eco-conscious businesses | Pros: Appeals to environmentally conscious consumers. Cons: May have higher upfront costs. |
Traditional Box Vending Machine
Traditional box vending machines are the most recognizable type, featuring mechanical mechanisms for dispensing products. They typically accept coins and bills, making them suitable for locations like office buildings and schools. While they are cost-effective and easy to operate, their limited payment options and lack of technological advancements can be drawbacks for businesses looking to modernize their offerings.
Smart Box Vending Machine
Smart box vending machines incorporate advanced technology, such as digital interfaces and cashless payment systems. These machines are ideal for high-traffic areas like airports and shopping malls, where convenience and speed are paramount. Although they offer a superior user experience and a variety of payment methods, the higher initial investment can be a barrier for some businesses, particularly in developing regions.
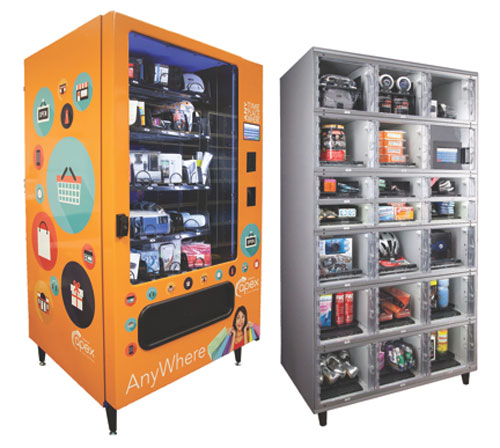
Illustrative Image (Source: Google Search)
Customized Product Vending Machine
Customized product vending machines are designed to cater to specific markets by providing tailored compartments for unique products, such as electronics or cosmetics. These machines are particularly effective in retail environments and at events where brand visibility is crucial. However, while they can attract niche customers, the limited range of products may restrict broader market appeal.
Refrigerated Box Vending Machine
Refrigerated box vending machines provide temperature-controlled compartments, making them suitable for perishable goods like snacks and beverages. They are commonly found in hospitals, gyms, and convenience stores, where fresh food options are in demand. While they significantly expand product offerings, they require more maintenance and higher energy consumption, which can impact operational costs.
Eco-Friendly Box Vending Machine
Eco-friendly box vending machines utilize sustainable materials and energy-efficient technologies, appealing to environmentally conscious consumers. These machines are well-suited for educational institutions and businesses that prioritize sustainability. However, the initial costs may be higher, which could deter some buyers, especially in regions where budget constraints are a significant concern.
Related Video: Machine Learning in 2024 – Beginner’s Course
Key Industrial Applications of box vending machine
Industry/Sector | Specific Application of Box Vending Machine | Value/Benefit for the Business | Key Sourcing Considerations for this Application |
---|---|---|---|
Retail | Automated retail for consumer goods | Increased sales efficiency, reduced labor costs | Payment systems integration, product size compatibility |
Healthcare | Dispensing medical supplies | Streamlined supply management, improved accessibility | Compliance with health regulations, security features |
Education | Providing snacks and beverages in schools | Enhanced student satisfaction, convenience | Nutritional standards, payment methods for students |
Manufacturing | Parts vending for production lines | Just-in-time inventory management, reduced downtime | Inventory tracking systems, rugged design for industrial use |
Hospitality | 24/7 service for snacks and drinks in hotels | Improved guest experience, additional revenue stream | Custom branding options, payment flexibility |
Retail
In the retail sector, box vending machines serve as automated retail outlets for consumer goods, allowing businesses to increase sales efficiency while minimizing labor costs. These machines can be strategically placed in high-traffic areas, providing customers with 24/7 access to products. International buyers should consider payment system integration and product size compatibility when sourcing these machines to ensure they meet local consumer preferences and purchasing behaviors.
Healthcare
In healthcare, box vending machines are utilized for dispensing medical supplies, such as personal protective equipment (PPE) and over-the-counter medications. This application streamlines supply management and improves accessibility for both healthcare professionals and patients. When sourcing for this sector, buyers must ensure compliance with health regulations and incorporate security features to prevent unauthorized access and ensure patient safety.
Education
Educational institutions are increasingly adopting box vending machines to provide snacks and beverages to students. This enhances student satisfaction and convenience, encouraging healthier eating habits when the machines are stocked with nutritious options. Buyers should focus on nutritional standards and payment methods that accommodate students, such as cashless transactions, to ensure a seamless experience.
Manufacturing
In manufacturing, box vending machines are deployed for parts vending, allowing production lines to maintain just-in-time inventory management. This reduces downtime by ensuring that essential components are readily available when needed. Buyers in this sector should prioritize rugged designs suitable for industrial environments and consider integrating inventory tracking systems to monitor usage and restocking needs effectively.
Hospitality
In the hospitality sector, box vending machines can provide 24/7 service for snacks and drinks in hotels, enhancing the guest experience and creating an additional revenue stream. These machines can be customized with hotel branding to create a cohesive guest experience. Buyers should consider custom branding options and payment flexibility to cater to diverse guest preferences, ensuring that the vending solutions align with their overall service strategy.
Related Video: How to Start a Vending Machine Business, Cost, Tips, How Much You Make
Strategic Material Selection Guide for box vending machine
When selecting materials for box vending machines, international B2B buyers must consider several factors, including durability, cost, and compliance with regional standards. Below, we analyze four common materials used in the construction of box vending machines, focusing on their properties, advantages, disadvantages, and specific considerations for buyers in Africa, South America, the Middle East, and Europe.
1. Stainless Steel
Key Properties: Stainless steel is known for its excellent corrosion resistance and high strength-to-weight ratio. It can withstand a wide range of temperatures and pressures, making it suitable for various environments.
Pros & Cons: The primary advantage of stainless steel is its durability and resistance to rust and staining, which is crucial for vending machines exposed to moisture. However, it is relatively expensive compared to other materials, and its manufacturing can be complex due to the need for specialized welding techniques.
Impact on Application: Stainless steel is compatible with a variety of media, including food and beverages, making it ideal for vending machines that dispense consumables.
Considerations for International Buyers: Buyers should ensure that the stainless steel used meets international standards such as ASTM A240. In regions like Europe, compliance with food safety regulations is critical, while in Africa and South America, local standards may vary.
2. Mild Steel
Key Properties: Mild steel is characterized by its good tensile strength and ductility. It is less resistant to corrosion compared to stainless steel but can be treated with coatings for added protection.
Pros & Cons: The main advantage of mild steel is its low cost and ease of fabrication, making it a popular choice for many applications. However, its susceptibility to rust without proper treatment can be a significant drawback, especially in humid environments.
Impact on Application: Mild steel is suitable for non-corrosive applications and is often used in the structural components of vending machines. However, it may not be suitable for machines that dispense liquids or food items without protective coatings.
Considerations for International Buyers: Buyers should be aware of the need for protective coatings and ensure compliance with local standards such as DIN EN 10025 for structural steel in Europe. In regions like the Middle East, where humidity can be high, additional corrosion protection may be necessary.
3. Aluminum
Key Properties: Aluminum is lightweight, corrosion-resistant, and has good thermal conductivity. It is also non-magnetic and non-toxic, making it suitable for food-related applications.
Pros & Cons: The key advantage of aluminum is its lightweight nature, which can reduce shipping costs and make installation easier. However, it is generally less strong than steel and can be more expensive than mild steel.
Impact on Application: Aluminum is particularly effective in applications where weight is a concern, such as portable vending machines. It is also compatible with a variety of consumables, ensuring safety and compliance.
Considerations for International Buyers: Buyers should verify that the aluminum used complies with standards such as ASTM B221 for aluminum extrusions. In Europe, adherence to food safety regulations is essential, while buyers in Africa may need to consider local sourcing options.
4. Polycarbonate
Key Properties: Polycarbonate is a high-performance plastic known for its impact resistance and clarity. It is lightweight and can withstand a wide range of temperatures.
Pros & Cons: The primary advantage of polycarbonate is its durability and resistance to shattering, making it ideal for transparent components of vending machines. However, it can be susceptible to scratching and may not be as durable as metals in high-stress applications.
Impact on Application: Polycarbonate is often used for windows and display panels in vending machines, allowing for visibility of products while providing protection. It is suitable for various media, including snacks and drinks.
Considerations for International Buyers: Buyers should ensure that the polycarbonate used meets relevant safety standards such as ISO 11607 for packaging materials. In regions with strict regulations, compliance with local environmental standards regarding plastics is also crucial.
Summary Table
Material | Typical Use Case for box vending machine | Key Advantage | Key Disadvantage/Limitation | Relative Cost (Low/Med/High) |
---|---|---|---|---|
Stainless Steel | Food and beverage dispensing | Excellent corrosion resistance | Higher cost, complex manufacturing | High |
Mild Steel | Structural components | Low cost, easy fabrication | Susceptible to rust, requires coating | Low |
Aluminum | Portable vending machines | Lightweight, good thermal conductivity | Less strength compared to steel | Medium |
Polycarbonate | Windows and display panels | Impact-resistant, lightweight | Susceptible to scratching | Medium |
This strategic material selection guide provides essential insights for international B2B buyers, enabling them to make informed decisions based on performance, cost, and compliance considerations.
In-depth Look: Manufacturing Processes and Quality Assurance for box vending machine
Manufacturing Processes for Box Vending Machines
Manufacturing box vending machines involves several key stages that ensure both efficiency and quality. Understanding these processes is crucial for B2B buyers, as it impacts the overall performance and reliability of the machines.
Main Stages of Manufacturing
-
Material Preparation
– The first step involves selecting high-quality materials such as steel, aluminum, and plastics. These materials are chosen for their durability and ability to withstand various environmental conditions.
– Materials are cut to size using precision cutting tools, ensuring that each component meets the required specifications. This stage may also include treatments such as galvanization or painting to enhance corrosion resistance. -
Forming
– This stage includes processes like stamping, bending, and welding. Advanced CNC (Computer Numerical Control) machines are often used to shape metal components accurately.
– Automated robotic arms may assist in handling heavier parts, reducing human error and improving safety. -
Assembly
– The assembly process can be manual or automated, depending on the complexity of the vending machine design. Key components, such as the vending mechanism, coin acceptor, and electronic controls, are integrated during this phase.
– Assembly lines are often designed for efficiency, allowing for multiple machines to be built simultaneously while maintaining quality control. -
Finishing
– After assembly, machines undergo finishing processes such as painting, labeling, and protective coatings. This not only enhances aesthetics but also provides additional protection against wear and tear.
– Final inspections are conducted to ensure that all components are functioning correctly and that the machine meets design specifications.
Quality Assurance in Manufacturing
Quality assurance (QA) is a critical component of the manufacturing process for box vending machines. It ensures that the final products meet both international and industry-specific standards.
Relevant International Standards
- ISO 9001: This standard outlines the requirements for a quality management system and is applicable to organizations aiming to enhance customer satisfaction through effective system implementation.
- CE Marking: For products sold in the European Economic Area, CE marking indicates compliance with health, safety, and environmental protection standards.
- API Standards: The American Petroleum Institute standards are relevant for vending machines that dispense petroleum products, ensuring safety and reliability.
Quality Control Checkpoints
-
Incoming Quality Control (IQC)
– Raw materials are inspected upon arrival to verify that they meet specified quality standards. This may include checking for defects, dimensions, and material properties. -
In-Process Quality Control (IPQC)
– During manufacturing, periodic checks are performed to ensure that the processes are working correctly. This includes monitoring machinery performance and checking dimensions at various assembly stages. -
Final Quality Control (FQC)
– Before shipping, each vending machine undergoes a comprehensive inspection. This includes functionality tests, safety checks, and aesthetic evaluations to ensure that the product is ready for market.
Common Testing Methods
- Functional Testing: Ensures that all electronic and mechanical components work as intended.
- Durability Testing: Simulates long-term use to identify potential failures.
- Environmental Testing: Assesses how machines perform under varying temperature and humidity conditions.
Verifying Supplier Quality Control
B2B buyers must ensure that their suppliers maintain high-quality standards. Here are actionable strategies to verify supplier QC:
-
Conduct Audits
– Regular audits of supplier facilities can provide insights into their manufacturing processes and quality control measures. This can be done by the buyer or through third-party agencies. -
Request Quality Reports
– Suppliers should provide detailed quality reports, including results from IQC, IPQC, and FQC stages. These documents should clearly outline any issues encountered and corrective actions taken. -
Third-Party Inspections
– Engaging third-party inspection services can provide an unbiased evaluation of the manufacturing processes and final products. This is particularly useful for international buyers who may not have direct access to supplier facilities.
QC and Certification Nuances for International Buyers
For buyers from regions like Africa, South America, the Middle East, and Europe, understanding the nuances of quality certification is essential:
- Local Compliance: Ensure that machines comply with local regulations and standards. For instance, certain countries may have specific energy efficiency standards that must be met.
- Cultural and Economic Considerations: Be aware of the local business environment and any potential barriers to quality compliance, such as supply chain disruptions or variations in material quality.
- Language and Documentation: Ensure that all quality documentation is available in the buyer’s preferred language and is clear and comprehensive, facilitating better understanding and compliance.
In conclusion, understanding the manufacturing processes and quality assurance protocols of box vending machines is vital for B2B buyers. By focusing on key manufacturing stages, relevant quality standards, and effective verification methods, buyers can ensure they are making informed purchasing decisions that meet their operational needs.
Related Video: Glenroy’s Flexible Packaging Manufacturing Process
Comprehensive Cost and Pricing Analysis for box vending machine Sourcing
When sourcing box vending machines, understanding the comprehensive cost structure and pricing dynamics is crucial for international B2B buyers. This analysis focuses on key cost components, price influencers, and actionable tips for effective negotiations and purchasing strategies.
Cost Components
-
Materials: The primary cost driver in box vending machines includes the materials used for construction, which typically consist of metal casings, electronic components, and payment systems. The choice of materials can significantly impact both the durability and the overall cost.
-
Labor: Labor costs vary significantly based on the manufacturing location. Regions with lower labor costs, such as parts of Africa and South America, can offer competitive pricing. However, quality assurance and skilled labor for assembly should also be considered.
-
Manufacturing Overhead: This includes costs associated with utilities, rent, and administrative expenses of the manufacturing facility. Buyers should inquire about the supplier’s production capacity and efficiency, as these factors can affect overhead costs.
-
Tooling: Customization of vending machines may require specific tooling, which can add to the initial investment. Understanding whether the supplier has the necessary tooling already in place can reduce costs.
-
Quality Control (QC): Investing in quality control processes ensures product reliability and compliance with international standards. This may increase upfront costs but can reduce total costs in the long run by minimizing defects and returns.
-
Logistics: Transportation and shipping costs can vary greatly depending on the distance from the supplier to the buyer’s location. Incoterms can influence who bears these costs and the associated risks.
-
Margin: Suppliers typically add a profit margin to cover their risks and expenses. Understanding the typical margins within the industry can help buyers identify fair pricing.
Price Influencers
-
Volume/MOQ: Bulk orders often lead to reduced per-unit costs. Buyers should assess their needs to negotiate minimum order quantities (MOQs) effectively.
-
Specifications/Customization: Customized features can significantly alter pricing. Buyers should clearly define their specifications to avoid unexpected costs.
-
Materials and Quality Certifications: Higher quality materials and certifications (e.g., CE, ISO) can increase costs but may be necessary for compliance in certain markets.
-
Supplier Factors: The reputation and reliability of the supplier can influence pricing. Established suppliers may charge a premium for proven quality and service.
-
Incoterms: Understanding the terms of shipment (e.g., FOB, CIF) is essential for accurately calculating total costs, as they dictate who pays for shipping and insurance.
Buyer Tips
-
Negotiation: Engage in negotiations with a clear understanding of your budget and the industry standards for pricing. Leverage competitive quotes from multiple suppliers to strengthen your position.
-
Cost-Efficiency: Evaluate the total cost of ownership (TCO), which includes purchase price, maintenance, and operational costs over the machine’s lifecycle. This approach often reveals hidden costs that can influence the purchasing decision.
-
Pricing Nuances for International Buyers: Buyers from regions like Africa and South America should be aware of currency fluctuations, import duties, and tariffs that can affect final pricing. Building relationships with local distributors can also facilitate better pricing and service.
-
Disclaimer for Indicative Prices: Prices can fluctuate based on market conditions, supplier changes, and economic factors. Always request updated quotes and clarify all components of pricing before finalizing a deal.
By comprehensively understanding the cost structure and pricing dynamics of box vending machines, international B2B buyers can make informed decisions that enhance their purchasing strategies and operational efficiencies.
Spotlight on Potential box vending machine Manufacturers and Suppliers
This section offers a look at a few manufacturers active in the ‘box vending machine’ market. This is a representative sample for illustrative purposes; B2B buyers must conduct their own extensive due diligence before any engagement. Information is synthesized from public sources and general industry knowledge.
Essential Technical Properties and Trade Terminology for box vending machine
When considering the procurement of box vending machines, international B2B buyers must be well-versed in essential technical properties and trade terminology. This knowledge enables informed decision-making and fosters effective communication with suppliers. Below are critical specifications and common jargon associated with box vending machines.
Key Technical Properties
-
Material Grade
– Definition: The grade of materials used in the construction of the vending machine, typically stainless steel, aluminum, or high-grade plastics.
– Importance: High-quality materials ensure durability, resistance to corrosion, and longevity, which are crucial for machines operating in various environments, particularly in humid or outdoor settings. -
Capacity
– Definition: The total volume or number of items that a vending machine can hold, often measured in liters or number of slots.
– Importance: Understanding capacity is essential for buyers to match the machine to their expected sales volume and product types, ensuring optimal stock management and customer satisfaction. -
Power Supply Requirements
– Definition: The electrical specifications necessary for the vending machine to operate, including voltage (e.g., 110V, 220V) and wattage.
– Importance: Buyers must ensure that the machine’s power requirements align with local electrical standards to avoid operational disruptions or additional installation costs. -
Dimensions and Weight
– Definition: The physical size and weight of the vending machine, often specified in centimeters and kilograms.
– Importance: Knowing the dimensions is crucial for logistical considerations, such as shipping, installation space, and ease of movement, particularly in confined retail environments. -
User Interface Technology
– Definition: The technology used for customer interaction, which may include touch screens, card readers, or mobile payment options.
– Importance: Advanced user interfaces can enhance customer experience and increase sales by offering diverse payment methods, which is particularly important in regions with varying payment preferences.
Common Trade Terminology
-
OEM (Original Equipment Manufacturer)
– Definition: A company that produces parts or equipment that may be marketed by another manufacturer.
– Application: Buyers often work with OEMs to source vending machines that can be customized to meet specific branding or operational needs. -
MOQ (Minimum Order Quantity)
– Definition: The smallest number of units that a supplier is willing to sell.
– Application: Understanding the MOQ helps buyers assess the feasibility of their purchase and negotiate better terms, especially in bulk orders. -
RFQ (Request for Quotation)
– Definition: A document sent to suppliers to solicit price quotes for specific products.
– Application: An RFQ allows buyers to compare pricing and terms from multiple vendors, ensuring competitive sourcing. -
Incoterms (International Commercial Terms)
– Definition: A set of predefined international rules that clarify the responsibilities of buyers and sellers in international transactions.
– Application: Familiarity with Incoterms helps buyers understand shipping responsibilities, costs, and risks, which is vital for budgeting and logistics planning. -
Warranty Period
– Definition: The time frame during which the manufacturer guarantees the machine against defects and failures.
– Importance: A comprehensive warranty is crucial for minimizing long-term operational costs and ensuring reliability in product performance.
By understanding these technical specifications and trade terms, B2B buyers can navigate the complexities of sourcing box vending machines more effectively, ensuring that their investments align with their business objectives and market demands.
Navigating Market Dynamics, Sourcing Trends, and Sustainability in the box vending machine Sector
Market Overview & Key Trends
The box vending machine sector is experiencing a significant transformation, driven by technological advancements, changing consumer behavior, and the need for innovative retail solutions. Globally, the increasing demand for contactless payment methods, particularly in the wake of the COVID-19 pandemic, has accelerated the adoption of smart vending solutions. These machines now offer features such as cashless transactions, real-time inventory management, and interactive touchscreen interfaces, appealing to tech-savvy consumers.
For international B2B buyers, particularly from regions like Africa, South America, the Middle East, and Europe, understanding these dynamics is crucial. In Africa, for instance, mobile payment systems such as M-Pesa are gaining traction, allowing vending machine operators to cater to a growing demographic of cashless users. Similarly, in Brazil and Saudi Arabia, urbanization and a burgeoning middle class are driving demand for convenient retail solutions, making vending machines an attractive investment.
Emerging trends include the integration of IoT (Internet of Things) technology, which allows for remote monitoring and predictive maintenance, reducing operational downtime. Furthermore, eco-friendly machines that utilize sustainable materials and energy-efficient components are becoming increasingly popular. Buyers should also consider the customization capabilities of vending machines, which can be tailored to local preferences and market demands, enhancing the consumer experience and driving sales.
Sustainability & Ethical Sourcing in B2B
Sustainability is a pivotal consideration in the box vending machine industry, as environmental concerns become more pronounced among consumers and regulatory bodies. The environmental impact of traditional vending machines—often associated with high energy consumption and plastic waste—has prompted manufacturers to seek greener alternatives. This shift includes the use of energy-efficient technologies, such as LED lighting and low-energy cooling systems, which significantly reduce the carbon footprint of these machines.
Ethical sourcing practices are equally vital for B2B buyers. Ensuring that materials used in manufacturing are sourced responsibly not only enhances brand reputation but also meets the increasing demand for corporate social responsibility. Buyers should look for vendors that prioritize ethical supply chains, employing sustainable materials and labor practices. Certifications such as ISO 14001 (Environmental Management) and Fair Trade can serve as indicators of a supplier’s commitment to sustainability.
Additionally, the use of recyclable and biodegradable materials in the production of vending machines is gaining momentum. By opting for suppliers that utilize such materials, businesses can align with global sustainability goals and cater to environmentally conscious consumers.
Brief Evolution/History
The evolution of box vending machines can be traced back to ancient Greece, where devices were used to dispense holy water. However, the modern vending machine, as we know it, began to take shape in the early 20th century. The introduction of coin-operated machines in the 1880s marked a significant turning point, leading to the widespread adoption of vending in various sectors.
Over the decades, vending machines have evolved from simple coin-operated units to sophisticated machines that offer a wide range of products, including fresh food and beverages. The rise of technology in the 21st century has further transformed the sector, with features like cashless payments, remote monitoring, and customizable interfaces becoming standard. Today, these machines not only serve as retail outlets but also as innovative solutions for enhancing consumer convenience and engagement.
Related Video: Global Trade & Logistics – What is Global Trade?
Frequently Asked Questions (FAQs) for B2B Buyers of box vending machine
-
What should I consider when vetting suppliers for box vending machines?
When vetting suppliers, prioritize their experience in the industry, production capacity, and reputation. Check for certifications such as ISO for quality assurance and compliance with international standards. Request references from previous clients and review case studies that demonstrate their ability to deliver high-quality products. Additionally, consider their responsiveness and communication style, as these factors can indicate their reliability in fulfilling orders. -
Can I customize my box vending machine order?
Yes, many suppliers offer customization options for box vending machines. You can request modifications in size, design, features, and branding to better fit your market needs. Be specific about your requirements, and ask for a prototype or 3D model before finalizing the order. Ensure that the supplier has a clear process for customization and that they can accommodate changes without significant delays. -
What is the typical minimum order quantity (MOQ) for box vending machines?
The MOQ for box vending machines varies by supplier and is influenced by factors such as production capacity and customization options. Generally, you might encounter MOQs ranging from 10 to 50 units. It’s advisable to discuss your needs directly with the supplier to negotiate terms that work for both parties, especially if you’re looking to test the market with a smaller initial order. -
What are the lead times for delivery once I place an order?
Lead times can vary significantly based on the supplier’s location, order volume, and customization requirements. Typically, you can expect lead times to range from 4 to 12 weeks. Always confirm the estimated delivery schedule before placing your order, and inquire about the supplier’s ability to meet expedited shipping requests if necessary.
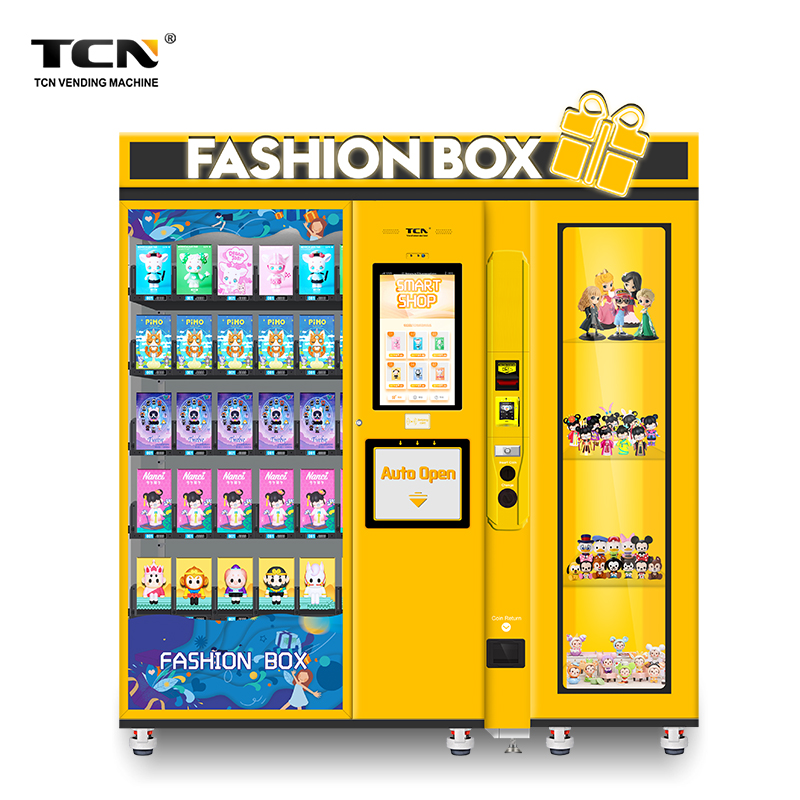
Illustrative Image (Source: Google Search)
-
What payment methods are commonly accepted when sourcing box vending machines?
Most suppliers accept various payment methods, including bank transfers, letters of credit, and secure online payment platforms. It’s important to clarify payment terms before finalizing the order, including deposits, balances, and any currency exchange considerations. Using secure payment methods can help mitigate risks associated with international transactions. -
How do I ensure quality assurance and compliance with standards?
To ensure quality assurance, request documentation of certifications related to manufacturing standards, such as ISO 9001. Ask for detailed quality control processes that the supplier follows during production. It’s also beneficial to conduct factory audits or arrange for third-party inspections to verify that the machines meet your specifications and regulatory requirements. -
What logistics considerations should I keep in mind for shipping box vending machines?
Logistics is crucial when sourcing box vending machines internationally. Consider shipping methods (air vs. sea freight), customs clearance processes, and insurance options. Ensure that the supplier provides the necessary documentation for smooth customs handling. Additionally, discuss delivery terms (Incoterms) to clarify who is responsible for shipping costs, risks, and liabilities during transit. -
How should I handle disputes or issues with the supplier?
In the event of a dispute, first attempt to resolve the issue amicably through direct communication. Maintain clear records of all correspondences and agreements. If resolution is not achieved, refer to the terms outlined in your contract regarding dispute resolution, which may include mediation or arbitration. Consider involving a legal advisor experienced in international trade to navigate complex issues effectively.
Strategic Sourcing Conclusion and Outlook for box vending machine
In conclusion, strategic sourcing for box vending machines presents a substantial opportunity for international B2B buyers. By understanding the nuances of the vending machine market, including supplier capabilities, product specifications, and regional preferences, businesses can optimize their procurement processes. It is essential to engage with reliable manufacturers who offer robust product support and adhere to international quality standards, thereby ensuring long-term value.
Moreover, as global demand for innovative vending solutions continues to rise, companies from Africa, South America, the Middle East, and Europe should consider the advantages of localized sourcing. This approach not only reduces logistics costs but also fosters partnerships that can lead to tailored solutions suited to specific market needs.
As you move forward in your sourcing journey, leverage the insights gained from this guide to make informed decisions that align with your business objectives. Embrace the evolving landscape of vending technology, and explore new avenues for growth and customer engagement. The future of vending is bright, and your strategic sourcing decisions can position your business at the forefront of this dynamic industry.