Master Sourcing Beaver Vending Machines: A Comprehensive
Guide to Beaver Vending Machine
- Introduction: Navigating the Global Market for beaver vending machine
- Understanding beaver vending machine Types and Variations
- Key Industrial Applications of beaver vending machine
- Strategic Material Selection Guide for beaver vending machine
- In-depth Look: Manufacturing Processes and Quality Assurance for beaver vending machine
- Comprehensive Cost and Pricing Analysis for beaver vending machine Sourcing
- Spotlight on Potential beaver vending machine Manufacturers and Suppliers
- Essential Technical Properties and Trade Terminology for beaver vending machine
- Navigating Market Dynamics, Sourcing Trends, and Sustainability in the beaver vending machine Sector
- Frequently Asked Questions (FAQs) for B2B Buyers of beaver vending machine
- Strategic Sourcing Conclusion and Outlook for beaver vending machine
Introduction: Navigating the Global Market for beaver vending machine
The global market for beaver vending machines is rapidly evolving, providing unique opportunities for B2B buyers across various regions, including Africa, South America, the Middle East, and Europe. These innovative machines not only enhance consumer convenience but also represent a significant revenue stream for businesses looking to diversify their offerings. As urbanization increases and consumer preferences shift towards automated services, understanding the dynamics of beaver vending machines becomes crucial for informed sourcing decisions.
This comprehensive guide is designed to equip international B2B buyers with essential insights into the beaver vending machine market. It covers a wide array of topics, including the different types of machines available, the materials used in their construction, manufacturing processes, quality control standards, and an overview of reputable suppliers. Additionally, it provides a detailed analysis of costs associated with procurement and operational aspects, ensuring buyers can make financially sound decisions.
The guide also addresses frequently asked questions, clarifying common misconceptions and providing practical advice tailored to the unique challenges faced by buyers in diverse markets, such as Egypt and Mexico. By leveraging this information, businesses can confidently navigate the complexities of sourcing beaver vending machines, ensuring they select solutions that align with their operational goals and customer needs. Ultimately, this guide empowers B2B buyers to tap into the burgeoning market for vending solutions, driving growth and innovation in their respective industries.
Understanding beaver vending machine Types and Variations
Type Name | Key Distinguishing Features | Primary B2B Applications | Brief Pros & Cons for Buyers |
---|---|---|---|
Traditional Beaver Vending | Mechanical design, simple interface | Schools, offices, public areas | Pros: Cost-effective, easy maintenance. Cons: Limited product variety, slower service. |
Smart Beaver Vending | Digital interface, cashless payment options | Airports, malls, tech hubs | Pros: Enhanced customer experience, real-time inventory tracking. Cons: Higher upfront cost. |
Customized Beaver Vending | Tailored design to fit specific product needs | Niche markets, specialty products | Pros: Unique offerings, brand visibility. Cons: Longer lead times, potentially higher costs. |
Eco-friendly Beaver Vending | Sustainable materials, energy-efficient operation | Eco-conscious businesses, health facilities | Pros: Attracts eco-aware consumers, reduces operational costs. Cons: Initial investment may be higher. |
Hybrid Beaver Vending | Combines traditional and smart features | Versatile locations, diverse product ranges | Pros: Flexibility in product offerings, appeals to wider audience. Cons: More complex maintenance requirements. |
Traditional Beaver Vending
Traditional beaver vending machines are characterized by their mechanical design and straightforward interface. They are commonly found in schools, offices, and public areas, providing a reliable service for snacks and beverages. B2B buyers appreciate their cost-effectiveness and ease of maintenance. However, the limited product variety and slower service may deter some businesses from selecting this type for high-traffic environments.
Smart Beaver Vending
Smart beaver vending machines feature a digital interface and cashless payment options, making them ideal for modern settings like airports, malls, and tech hubs. They enhance customer experience through real-time inventory tracking and personalized promotions. While they offer significant advantages, the higher upfront costs can be a barrier for some businesses, particularly in regions with budget constraints.
Customized Beaver Vending
Customized beaver vending machines allow businesses to tailor the design to fit specific product needs, making them suitable for niche markets and specialty products. This customization can enhance brand visibility and cater to unique consumer preferences. However, buyers should consider the longer lead times and potentially higher costs associated with these bespoke solutions.
Eco-friendly Beaver Vending
Eco-friendly beaver vending machines are built with sustainable materials and designed for energy-efficient operation. They are particularly appealing to eco-conscious businesses and health facilities that aim to attract environmentally aware consumers. While they may require a higher initial investment, the long-term operational savings and positive brand image can justify the expense.
Hybrid Beaver Vending
Hybrid beaver vending machines combine traditional and smart features, providing flexibility in product offerings. This versatility makes them suitable for a wide range of locations and diverse product ranges. While they can appeal to a broader audience, buyers should be prepared for more complex maintenance requirements, which may necessitate specialized training for staff.
Related Video: Machine Learning in 2024 – Beginner’s Course
Key Industrial Applications of beaver vending machine
Industry/Sector | Specific Application of Beaver Vending Machine | Value/Benefit for the Business | Key Sourcing Considerations for this Application |
---|---|---|---|
Retail | Automated product dispensing | Increased sales through 24/7 availability | Product size, payment options, and maintenance support |
Healthcare | Dispensing medical supplies | Improved access to essential items in emergencies | Compliance with health regulations and inventory tracking |
Education | Providing snacks and beverages in schools | Enhanced student satisfaction and engagement | Nutritional value of products and machine placement |
Construction | Offering tools and safety gear | Increased productivity by minimizing downtime | Durability of the machine in harsh environments |
Public Transport | Selling tickets and travel essentials | Streamlined customer service and reduced queues | User-friendly interface and payment integration |
Retail
In the retail sector, the Beaver vending machine serves as an automated product dispensing solution that allows businesses to maintain a continuous sales presence, even outside regular hours. This capability can significantly boost sales by providing customers with 24/7 access to popular items. B2B buyers in this sector should consider the machine’s size and product compatibility, as well as the variety of payment options it offers, to ensure it meets their specific needs.
Healthcare
Healthcare facilities utilize Beaver vending machines to dispense medical supplies, such as first-aid kits and over-the-counter medications. This ensures that essential items are readily available, particularly in emergencies or during off-hours. For international buyers, compliance with health regulations and the ability to track inventory are critical considerations when sourcing these machines, as they must meet stringent health and safety standards.
Education
In educational institutions, Beaver vending machines provide students with convenient access to snacks and beverages, enhancing their overall experience and satisfaction. This is particularly valuable during busy school hours when students may not have time to visit a cafeteria. Buyers in the education sector should focus on the nutritional value of the products offered and the strategic placement of machines to maximize usage.
Construction
The construction industry benefits from Beaver vending machines by offering essential tools and safety gear on-site. This reduces downtime by allowing workers to access necessary items without leaving the job site. When sourcing these machines, buyers should prioritize durability, ensuring that the units can withstand harsh environmental conditions and heavy usage while maintaining functionality.
Public Transport
In the public transport sector, Beaver vending machines can streamline operations by selling tickets and travel essentials directly to customers. This reduces wait times and enhances the customer experience. B2B buyers should look for machines with user-friendly interfaces and robust payment integration systems to facilitate smooth transactions and improve service efficiency.
Related Video: DIY Vending Machine – Arduino based Mechatronics Project
Strategic Material Selection Guide for beaver vending machine
When selecting materials for beaver vending machines, it is essential to consider various factors that influence performance, durability, and cost-effectiveness. Below is an analysis of four common materials used in the construction of these machines, focusing on their properties, advantages, disadvantages, and implications for international buyers.
1. Stainless Steel
Key Properties: Stainless steel offers excellent corrosion resistance, high strength, and good temperature tolerance, making it suitable for various environments. It typically withstands temperatures ranging from -200°C to 800°C and is resistant to oxidation and rust.
Pros & Cons: The primary advantages of stainless steel include its durability, aesthetic appeal, and low maintenance requirements. However, it can be more expensive than other metals, and its manufacturing process may involve complex techniques like welding and polishing, which can increase costs.
Impact on Application: Stainless steel is compatible with a wide range of media, including food and beverages, making it ideal for vending machines that dispense consumables. Its resistance to corrosion ensures longevity in humid or wet environments.
Considerations for International Buyers: Buyers from regions like Europe and the Middle East should ensure compliance with relevant standards such as ASTM A240 or EN 10088. Understanding local preferences for material grades can also guide procurement decisions.
2. Carbon Steel
Key Properties: Carbon steel is known for its high tensile strength and durability. It typically has a temperature rating of up to 400°C but lacks corrosion resistance unless treated.
Pros & Cons: This material is cost-effective and easy to manufacture, making it a popular choice for structural components. However, its susceptibility to rust and corrosion requires protective coatings, which can add to maintenance costs.
Impact on Application: Carbon steel is suitable for non-corrosive environments and can be used in the structural framework of vending machines. It is not recommended for applications involving moisture or corrosive substances.
Considerations for International Buyers: Buyers should be aware of the need for protective coatings and compliance with standards such as ASTM A36. In regions like Africa and South America, where humidity may be higher, additional protective measures are crucial.
3. Aluminum
Key Properties: Aluminum is lightweight, corrosion-resistant, and has good thermal and electrical conductivity. It can withstand temperatures up to 600°C, making it versatile for various applications.
Pros & Cons: The primary advantage of aluminum is its low weight, which can reduce shipping costs and ease installation. However, it is generally less strong than steel and can be more expensive depending on the alloy used.
Impact on Application: Aluminum is suitable for vending machines that require frequent relocation or where weight is a critical factor. Its corrosion resistance makes it ideal for outdoor applications.
Considerations for International Buyers: Buyers should consider the specific aluminum alloy, as different grades offer varying levels of strength and corrosion resistance. Compliance with standards such as ASTM B221 or EN AW-6060 is essential, particularly in Europe.
4. Polycarbonate
Key Properties: Polycarbonate is a high-performance plastic known for its impact resistance and transparency. It can operate effectively in temperatures from -40°C to 120°C.
Pros & Cons: The advantages of polycarbonate include its lightweight nature and excellent shatter resistance, making it suitable for protective panels. However, it may not be as durable as metals when exposed to certain chemicals or UV light, leading to potential degradation over time.
Impact on Application: Polycarbonate is commonly used for viewing windows and protective covers in vending machines. Its transparency allows for product visibility, enhancing customer interaction.
Considerations for International Buyers: Buyers should ensure that the selected polycarbonate meets relevant safety and quality standards, such as ANSI Z26.1. In regions with high UV exposure, selecting UV-stabilized grades is advisable.
Summary Table
Material | Typical Use Case for beaver vending machine | Key Advantage | Key Disadvantage/Limitation | Relative Cost (Low/Med/High) |
---|---|---|---|---|
Stainless Steel | Main structure and components for durability | Excellent corrosion resistance | Higher cost and complex manufacturing | High |
Carbon Steel | Structural framework in non-corrosive environments | Cost-effective and strong | Susceptible to corrosion without treatment | Low |
Aluminum | Lightweight components and outdoor applications | Lightweight and corrosion-resistant | Less strength compared to steel | Medium |
Polycarbonate | Viewing windows and protective covers | Impact-resistant and transparent | Potential degradation from UV exposure | Medium |
This strategic material selection guide provides essential insights for international B2B buyers, enabling informed decisions that align with regional preferences and compliance standards.
In-depth Look: Manufacturing Processes and Quality Assurance for beaver vending machine
The manufacturing of beaver vending machines involves several key stages, each critical for ensuring the final product meets quality and functionality standards. Understanding these processes can help international B2B buyers, particularly in Africa, South America, the Middle East, and Europe, make informed purchasing decisions.
Manufacturing Process Overview
1. Material Preparation
The first stage involves sourcing and preparing high-quality materials. Common materials used in vending machine manufacturing include:
- Metal Components: Typically steel or aluminum, known for their strength and durability.
- Plastic Parts: Used for various functionalities, such as the outer casing and internal mechanisms.
- Electronic Components: Circuit boards, sensors, and payment systems are vital for machine operation.
Buyers should ensure that suppliers use materials that comply with international standards, such as ISO 9001 for quality management systems.
2. Forming
Once materials are prepared, they undergo various forming techniques:
- Metal Fabrication: Processes like laser cutting, bending, and welding are used to shape metal components.
- Plastic Molding: Injection or blow molding techniques create plastic parts, allowing for complex shapes and designs.
Understanding the forming techniques can help buyers assess the capabilities of manufacturers. For example, advanced CNC machining can lead to higher precision in parts, which is crucial for the machine’s operational efficiency.
3. Assembly
The assembly stage is where individual components come together to form the complete vending machine. This involves:
- Mechanical Assembly: Connecting metal and plastic parts to create the machine’s frame and structure.
- Electrical Assembly: Installing wiring, circuit boards, and payment systems. This stage is critical for the machine’s functionality.
B2B buyers should inquire about the assembly process, including whether it employs automated systems, which can enhance consistency and reduce human error.
4. Finishing
After assembly, machines undergo finishing processes, which may include:
- Painting and Coating: Applying protective coatings to enhance durability and aesthetics.
- Quality Control Testing: Ensuring all components function correctly and meet safety standards before packaging.
A robust finishing process not only improves the product’s lifespan but also its market appeal.
Quality Assurance Protocols
Quality assurance is integral to the manufacturing of beaver vending machines. It ensures that products meet both safety and performance standards.
International Standards
- ISO 9001: This standard outlines criteria for quality management systems, ensuring consistent product quality.
- CE Marking: Required for products sold in the European Economic Area, indicating compliance with health, safety, and environmental protection standards.
- API Standards: Relevant for machines that may involve specific operational protocols, particularly in specialized markets.
QC Checkpoints
Quality control occurs at various stages of production:
- Incoming Quality Control (IQC): Verifies the quality of raw materials upon arrival.
- In-Process Quality Control (IPQC): Monitors production processes to catch defects early.
- Final Quality Control (FQC): Conducted on finished products to ensure they meet specifications before shipping.
International buyers should prioritize suppliers with established QC protocols to minimize risks.
Common Testing Methods
Various testing methods are employed to ensure quality:
- Functional Testing: Verifying that all machine functions operate correctly.
- Safety Testing: Ensuring the machine complies with safety standards.
- Durability Testing: Assessing the machine’s performance under various conditions.
Buyers can ask for documentation of these tests to ensure compliance with standards.
Verifying Supplier Quality Control
B2B buyers should take proactive steps to verify the quality control measures of potential suppliers:
- Audits: Conducting on-site audits can provide insights into the manufacturing processes and quality assurance practices.
- Reports: Requesting quality reports and certifications can offer reassurance regarding the supplier’s commitment to quality.
- Third-Party Inspections: Engaging independent inspection services can provide an unbiased evaluation of the manufacturing processes and final products.
Considerations for International Buyers
When sourcing beaver vending machines from international suppliers, particularly from regions like Africa, South America, the Middle East, and Europe, buyers should be aware of:
- Regulatory Compliance: Different countries have varying regulatory requirements. Understanding these can prevent costly delays and ensure market acceptance.
- Cultural Differences: Communication styles and business practices may vary significantly. Building strong relationships with suppliers can facilitate smoother transactions.
- Logistics and Supply Chain: Consider the implications of shipping costs, delivery times, and customs regulations, which can affect overall project timelines.
By focusing on these manufacturing processes and quality assurance measures, international B2B buyers can make informed decisions, ensuring they partner with suppliers who meet their quality and operational standards.
Related Video: SMART Quality Control for Manufacturing
Comprehensive Cost and Pricing Analysis for beaver vending machine Sourcing
When sourcing beaver vending machines, understanding the comprehensive cost structure and pricing factors is crucial for international B2B buyers. This analysis provides insights into the key cost components, pricing influencers, and strategic buyer tips tailored for markets in Africa, South America, the Middle East, and Europe.
Cost Components
-
Materials: The primary materials involved in beaver vending machines include high-grade metals for the frame, electronic components, and plastic for the casing. Sourcing quality materials can significantly influence the overall cost.
-
Labor: Labor costs vary by region and depend on the complexity of the machine’s assembly. Countries with lower labor costs may offer competitive pricing, but this could affect quality. It’s essential to evaluate the skill level of the workforce in the supplier’s country.
-
Manufacturing Overhead: This includes utilities, facility costs, and administrative expenses. Suppliers with optimized production processes can keep overhead low, which may reflect in the pricing.
-
Tooling: Custom tooling can be a significant upfront investment, especially for unique designs. Understanding the tooling costs is essential when considering customization options.
-
Quality Control (QC): Implementing rigorous quality control measures ensures product reliability. Suppliers that prioritize QC may have higher prices, but this can lead to lower long-term costs due to reduced failure rates.
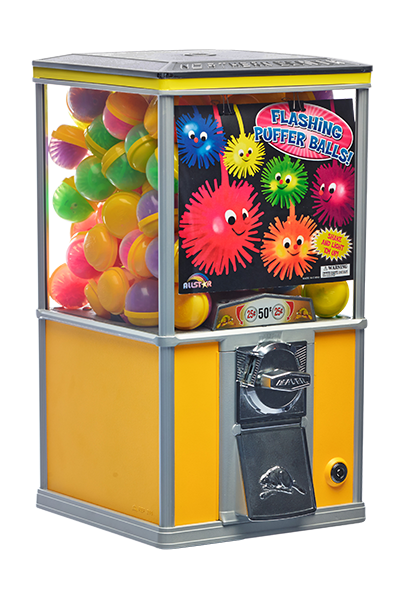
Illustrative Image (Source: Google Search)
-
Logistics: Shipping costs can vary greatly depending on the supplier’s location and the destination market. Factors such as freight mode, distance, and packaging impact logistics costs.
-
Margin: Suppliers typically add a markup to cover their costs and generate profit. Understanding the standard margins in the industry can help in negotiations.
Price Influencers
-
Volume/MOQ (Minimum Order Quantity): Purchasing in bulk often results in lower per-unit costs. Negotiating for larger quantities can lead to better pricing.
-
Specifications/Customization: Customized machines tailored to specific needs will generally incur additional costs. It’s vital to weigh the benefits of customization against the potential price increase.
-
Materials and Quality/Certifications: Higher quality materials and certifications (e.g., CE, ISO) can increase costs. However, they may also enhance the machine’s durability and compliance with local regulations.
-
Supplier Factors: The reputation and reliability of the supplier can influence pricing. Established suppliers with a track record may charge more due to their perceived value.
-
Incoterms: The choice of Incoterms affects logistics costs and responsibilities. Familiarize yourself with terms like FOB (Free on Board) and CIF (Cost, Insurance, and Freight) to understand your total costs.
Buyer Tips
-
Negotiate: Always negotiate pricing with suppliers. Leverage volume commitments or long-term contracts to secure better deals.
-
Focus on Cost-Efficiency: Analyze the total cost of ownership, including maintenance and operational costs, rather than just the upfront price.
-
Understand Pricing Nuances: International buyers should be aware of currency fluctuations, import duties, and taxes that may affect overall costs.
-
Research Local Market Conditions: Different regions may have varying pricing norms and supplier dynamics. Understanding local conditions can provide leverage in negotiations.
-
Seek Multiple Quotes: Obtaining quotes from various suppliers can help identify competitive pricing and terms. Ensure that the quotes are for comparable products to facilitate accurate comparisons.
Disclaimer: The prices and costs mentioned herein are indicative and may vary based on specific supplier terms, market conditions, and buyer negotiations. Always conduct thorough due diligence and consult with financial advisors when necessary.
Spotlight on Potential beaver vending machine Manufacturers and Suppliers
This section offers a look at a few manufacturers active in the ‘beaver vending machine’ market. This is a representative sample for illustrative purposes; B2B buyers must conduct their own extensive due diligence before any engagement. Information is synthesized from public sources and general industry knowledge.
Essential Technical Properties and Trade Terminology for beaver vending machine
Key Technical Properties of Beaver Vending Machines
When considering the procurement of beaver vending machines, several technical specifications are vital to ensure operational efficiency and reliability. Here are the essential properties to consider:
-
Material Grade
The material used in the construction of vending machines significantly impacts their durability and resistance to environmental factors. Common materials include stainless steel and high-grade plastic. Stainless steel offers corrosion resistance, making it ideal for outdoor installations, while high-grade plastics can reduce weight and enhance aesthetic appeal. For B2B buyers, selecting the right material can lead to lower maintenance costs and longer equipment lifespan. -
Dimensions and Weight
The size and weight of the vending machine are crucial for installation and operation. Machines must fit within designated spaces while being robust enough to withstand frequent use. Buyers should consider site-specific requirements, such as access points and floor load capacities. Understanding these dimensions helps in planning for logistics and installation, minimizing potential delays. -
Power Supply Requirements
Different models may have varying power supply needs, including voltage and amperage specifications. Most vending machines operate on standard voltage (110-240V), but specific models may require dedicated circuits. Buyers must ensure that their facilities can accommodate these electrical needs to prevent operational disruptions. -
User Interface Technology
Modern vending machines often feature advanced user interfaces, including touchscreens, mobile payment options, and cashless transactions. The technology used can affect customer engagement and sales. B2B buyers should evaluate how these features align with their target market preferences, as a more intuitive interface can lead to higher customer satisfaction and increased sales. -
Temperature Control Systems
For machines dispensing perishable items, efficient temperature control is essential. Specifications may include temperature ranges and energy consumption rates. Buyers should prioritize machines with energy-efficient cooling systems to reduce operational costs while ensuring product quality. -
Maintenance Accessibility
The design of the vending machine should allow for easy access to internal components for maintenance and restocking. Features like removable panels and intuitive layouts can significantly reduce downtime and labor costs. Ensuring that maintenance accessibility is factored into the purchasing decision can lead to improved operational efficiency.
Common Trade Terminology
Understanding industry-specific terminology is crucial for effective communication and negotiation in B2B transactions. Here are key terms relevant to beaver vending machines:
-
OEM (Original Equipment Manufacturer)
An OEM refers to a company that produces parts and equipment that may be marketed by another manufacturer. In the context of vending machines, it’s important to clarify if the machine is produced by an OEM or if it’s a generic model. This distinction can affect quality, warranty, and service support. -
MOQ (Minimum Order Quantity)
MOQ indicates the smallest quantity of a product that a supplier is willing to sell. For vending machines, understanding the MOQ can help buyers plan their budgets and inventory levels effectively, especially if they are looking to scale operations. -
RFQ (Request for Quotation)
An RFQ is a document used to solicit price proposals from suppliers for specific quantities of goods or services. When purchasing vending machines, issuing an RFQ helps buyers gather competitive pricing and terms, ensuring better financial planning. -
Incoterms (International Commercial Terms)
Incoterms define the responsibilities of buyers and sellers in international trade. They clarify who is responsible for shipping, insurance, and tariffs. Familiarity with these terms helps B2B buyers understand their obligations and risks during the shipping process, which is crucial for successful international transactions. -
Lead Time
Lead time refers to the time taken from placing an order to receiving the product. In the vending machine industry, understanding lead times is essential for planning deployments and ensuring that products are available when needed. -
Warranty and Service Agreements
These are contracts that outline the terms of repair or replacement of machines within a specified period. Buyers should carefully review warranty terms to ensure adequate protection against defects and service downtime.
By understanding these technical specifications and trade terminologies, international B2B buyers can make informed decisions that align with their operational needs and market conditions, ultimately leading to successful investments in beaver vending machines.
Navigating Market Dynamics, Sourcing Trends, and Sustainability in the beaver vending machine Sector
Market Overview & Key Trends
The beaver vending machine sector is experiencing notable growth fueled by several global drivers. Increasing urbanization and a shift towards contactless transactions have become pivotal in shaping the market. For international B2B buyers, particularly from Africa, South America, the Middle East, and Europe, understanding these trends is essential for strategic sourcing decisions.
Technological advancements such as IoT integration and mobile payment systems are revolutionizing vending machine operations. This innovation allows for real-time inventory management and enhanced user experiences. B2B buyers should prioritize vendors offering machines equipped with these technologies, as they can significantly improve operational efficiency and customer satisfaction.
Emerging trends include a rise in demand for customized vending solutions that cater to local tastes and preferences. For instance, in regions like Egypt and Mexico, vending machines that dispense local snacks or beverages are becoming increasingly popular. Buyers should consider partnerships with suppliers that can offer tailored solutions to meet specific market needs.
Additionally, the sustainability narrative is gaining traction in the vending machine industry. With consumers becoming more environmentally conscious, machines that utilize energy-efficient technologies and sustainable materials are attracting attention. This trend presents an opportunity for B2B buyers to align their procurement strategies with sustainability goals, enhancing brand reputation and customer loyalty.
Sustainability & Ethical Sourcing in B2B
Sustainability is no longer a niche concern but a core business imperative in the beaver vending machine sector. The environmental impact of vending operations, from energy consumption to waste generation, necessitates a focus on sustainable practices. B2B buyers should assess the environmental footprint of their suppliers, looking for those who prioritize energy-efficient machines and sustainable sourcing.
Ethical supply chains are also critical. The sourcing of materials used in vending machines should be transparent, ensuring that suppliers adhere to fair labor practices and environmental standards. Buyers should seek vendors that provide certifications, such as ISO 14001 (Environmental Management) and Fair Trade, to guarantee compliance with ethical sourcing principles.
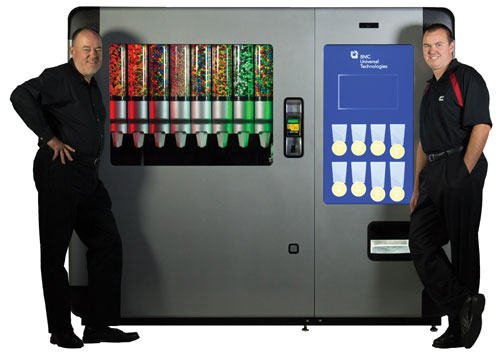
Illustrative Image (Source: Google Search)
Incorporating ‘green’ certifications and materials can enhance the marketability of vending machines. For instance, machines made from recycled plastics or equipped with energy-efficient compressors not only reduce environmental impact but also appeal to eco-conscious consumers. B2B buyers should look for suppliers who can demonstrate a commitment to sustainability through their product offerings and operational practices.
Brief Evolution/History
The evolution of vending machines dates back to ancient times, but the modern beaver vending machine has undergone significant transformations over the past few decades. Initially designed for simple snack and beverage dispensing, advancements in technology have led to the integration of sophisticated payment systems, touchscreen interfaces, and product customization options.
In recent years, the focus has shifted towards enhancing user experience and operational efficiency. The introduction of cashless payment options and remote monitoring capabilities has revolutionized how businesses manage vending operations. This evolution reflects the growing demand for convenience and personalization, essential for international B2B buyers looking to stay competitive in a rapidly changing market. Understanding this historical context can aid buyers in making informed decisions about future procurement strategies.
Related Video: International Trade 101 | Economics Explained
Frequently Asked Questions (FAQs) for B2B Buyers of beaver vending machine
-
What should I consider when vetting suppliers for beaver vending machines?
When vetting suppliers, prioritize those with a proven track record in the vending machine industry. Check for certifications like ISO or CE that indicate quality standards. Request references or case studies from other international clients, particularly those in your region (Africa, South America, Middle East, Europe). Additionally, assess their financial stability and ability to provide ongoing support and maintenance, which are crucial for long-term partnerships. -
Can beaver vending machines be customized for my specific needs?
Yes, many suppliers offer customization options for beaver vending machines. You can specify features such as size, color, branding, and product offerings. It is advisable to discuss your requirements during the initial negotiations to ensure that the supplier can meet your expectations. Be sure to ask about the cost implications and lead times for any custom features you want to include. -
What are the typical minimum order quantities (MOQ) and lead times?
Minimum order quantities for beaver vending machines can vary significantly by supplier, typically ranging from 5 to 50 units. Lead times also depend on the order size and customization level, generally spanning from 4 to 12 weeks. Always confirm these details upfront to avoid delays, and consider establishing a phased order approach if you’re uncertain about the total quantity needed initially. -
What payment terms should I expect when sourcing beaver vending machines?
Payment terms can vary widely among suppliers. Common practices include a deposit (20-50%) upon order confirmation, with the balance due before shipment or upon delivery. Some suppliers may also accept letters of credit, especially for larger orders. Always clarify payment methods and terms in your contract to ensure transparency and avoid potential disputes later. -
How can I ensure the quality of beaver vending machines before purchasing?
To ensure quality, request samples or visit the supplier’s factory if possible. Conduct a thorough inspection of the machines, focusing on materials, build quality, and technology. Additionally, ask for quality assurance certifications and inspection reports. If you’re sourcing from overseas, consider hiring a third-party inspection service to verify compliance with your quality standards before shipping. -
What certifications should beaver vending machines have for international trade?
Depending on your region, look for certifications such as CE (European Conformity) for Europe, or ISO standards which ensure quality management systems. In Africa and South America, specific local certifications may apply, so check with local regulations. Compliance with electrical safety standards is also crucial, especially for machines operating in public spaces. -
What logistical considerations should I keep in mind when importing beaver vending machines?
Logistics can be complex, especially for large machinery. Ensure that your supplier has a reliable shipping partner and can provide Incoterms that clarify responsibilities. Consider customs duties, taxes, and import regulations in your country, which can impact overall costs. Working with a freight forwarder can help streamline the process and mitigate potential delays. -
How can I resolve disputes with a supplier?
Establish clear communication channels and document all agreements to minimize misunderstandings. If a dispute arises, try to resolve it amicably through direct negotiation first. If that fails, refer to the terms outlined in your contract regarding dispute resolution, which may include mediation or arbitration. Be aware of the legal frameworks in both your country and the supplier’s location, as this can influence the resolution process.
Strategic Sourcing Conclusion and Outlook for beaver vending machine
The journey of integrating beaver vending machines into your business strategy underscores the importance of strategic sourcing. As international B2B buyers from diverse regions such as Africa, South America, the Middle East, and Europe evaluate their procurement options, leveraging a robust sourcing strategy becomes crucial. This involves understanding market dynamics, selecting suppliers that align with your operational needs, and ensuring that product quality meets consumer expectations.
Key takeaways include the need for thorough market research, establishing strong supplier relationships, and focusing on sustainability and innovation in vending solutions. Investing in high-quality vending machines can yield significant returns through improved customer satisfaction and operational efficiency. Furthermore, the adaptability of beaver vending machines to local preferences can be a game-changer in enhancing user experience.
Looking ahead, the landscape of vending solutions is set to evolve. B2B buyers should proactively engage with suppliers to explore emerging technologies and customizable options that meet the unique demands of their markets. Now is the time to act—evaluate your sourcing strategies, connect with reliable vendors, and position your business for future growth in this dynamic sector.