Your Ultimate Guide to Sourcing Vending Machine Fatalities
Guide to Vending Machine Fatalities
- Introduction: Navigating the Global Market for vending machine fatalities
- Understanding vending machine fatalities Types and Variations
- Key Industrial Applications of vending machine fatalities
- Strategic Material Selection Guide for vending machine fatalities
- In-depth Look: Manufacturing Processes and Quality Assurance for vending machine fatalities
- Comprehensive Cost and Pricing Analysis for vending machine fatalities Sourcing
- Spotlight on Potential vending machine fatalities Manufacturers and Suppliers
- Essential Technical Properties and Trade Terminology for vending machine fatalities
- Navigating Market Dynamics, Sourcing Trends, and Sustainability in the vending machine fatalities Sector
- Frequently Asked Questions (FAQs) for B2B Buyers of vending machine fatalities
- Strategic Sourcing Conclusion and Outlook for vending machine fatalities
Introduction: Navigating the Global Market for vending machine fatalities
In recent years, the global discourse around vending machine fatalities has gained significant traction, highlighting the critical need for safety measures in this widely used equipment. With millions of vending machines operating across diverse markets—from bustling urban centers in Africa and South America to busy streets in Europe and the Middle East—understanding the implications of these fatalities is essential for B2B buyers. This guide delves into the multifaceted dimensions of vending machine safety, encompassing various types of machines, the materials used in their manufacturing, and the quality control measures implemented to ensure safe operation.
By exploring the intricacies of vending machine fatalities, buyers will gain insights into the potential hazards associated with these machines, equipping them with the knowledge to make informed sourcing decisions. The comprehensive scope of this guide also addresses supplier evaluations, cost considerations, and market trends, ensuring that international buyers can navigate the complexities of procurement with confidence.
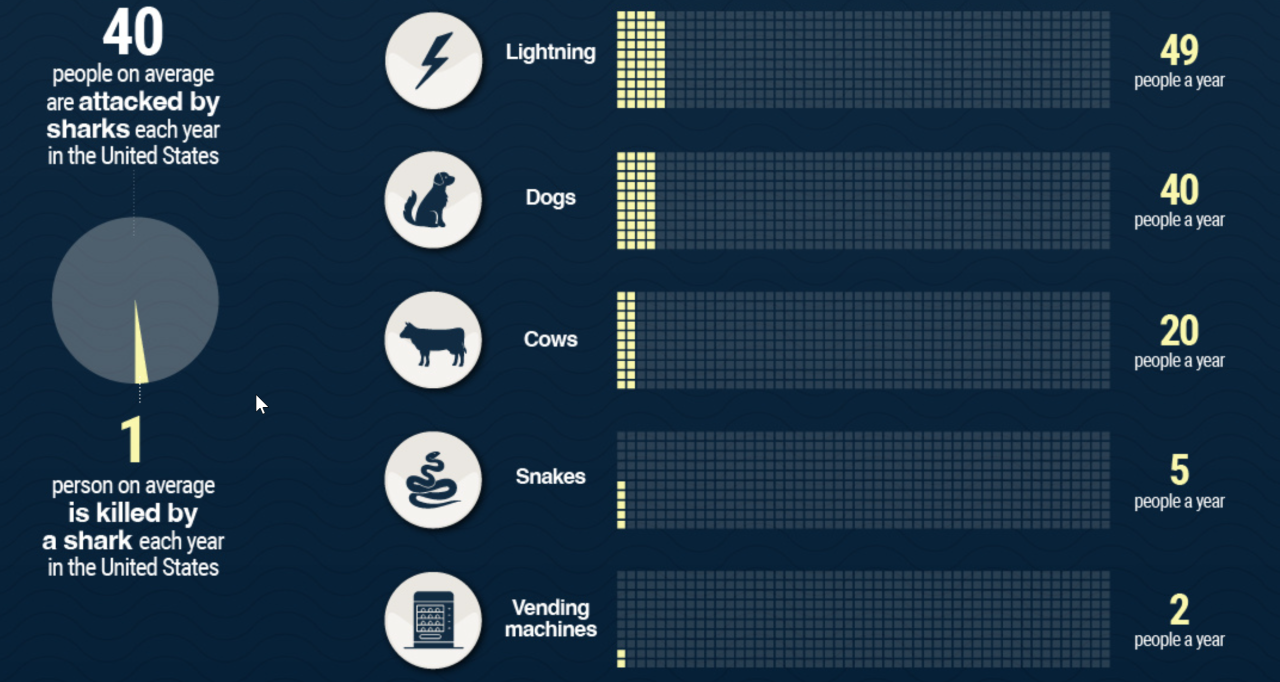
Illustrative Image (Source: Google Search)
Furthermore, the guide answers frequently asked questions, demystifying common concerns related to vending machine safety and compliance. This strategic resource empowers B2B buyers, particularly those from regions such as Africa, South America, the Middle East, and Europe, to enhance their operational safety standards and reduce liability risks. By leveraging this information, businesses can not only protect their customers but also foster a safer vending environment globally.
Understanding vending machine fatalities Types and Variations
Type Name | Key Distinguishing Features | Primary B2B Applications | Brief Pros & Cons for Buyers |
---|---|---|---|
Toppling Incidents | Machines falling due to improper installation | Public spaces, schools | Pros: High visibility; Cons: Risk of injury; requires secure installation. |
Pinching Hazards | Fingers caught in moving parts | High-traffic areas, malls | Pros: High product turnover; Cons: Liability concerns; requires safety features. |
Electrical Failures | Malfunctions due to electrical issues | Office buildings, factories | Pros: Continuous service; Cons: Potential fire hazards; regular maintenance needed. |
Overcrowding Failures | Machines overloaded with products | Events, concerts | Pros: Increased sales; Cons: Risk of malfunction; requires clear signage. |
Tampering Incidents | Damage from vandalism or misuse | Urban areas, schools | Pros: High foot traffic; Cons: Increased maintenance costs; requires robust design. |
Toppling Incidents
Toppling incidents occur when vending machines are not securely anchored, leading to potential falls. This is particularly relevant in environments with high foot traffic like schools and public spaces. B2B buyers should ensure that machines are installed according to safety guidelines and consider models with a lower center of gravity for stability. This type of incident can lead to significant liability issues and injuries, making proper installation and maintenance critical.
Pinching Hazards
Pinching hazards arise when users’ fingers get caught in the moving parts of vending machines, such as the delivery chute. This is a significant concern in high-traffic areas like malls and airports. For B2B buyers, it is essential to select machines equipped with safety features, such as pinch guards or automatic shut-off mechanisms. While these machines can drive high sales volumes, the potential for injury can lead to costly liability claims.
Electrical Failures
Electrical failures refer to malfunctions that can occur due to wiring issues, short circuits, or overloads. These failures pose risks in office buildings and factories where machines may operate continuously. B2B buyers should prioritize machines with robust electrical components and consider regular maintenance checks to mitigate risks. Although these machines provide consistent service, the potential for electrical fires or malfunctions necessitates careful consideration.
Overcrowding Failures
Overcrowding failures happen when a vending machine is overloaded with products, leading to jams or mechanical failures. This is common in event settings or concerts where demand is high. For buyers, ensuring that machines have clear signage to prevent overloading is crucial. While they can increase sales significantly, the risk of malfunction can deter customers, making it vital to manage inventory levels effectively.
Tampering Incidents
Tampering incidents involve vandalism or misuse of vending machines, common in urban areas and schools. These incidents can lead to significant repair costs and downtime. B2B buyers should invest in machines designed with tamper-resistant features and consider locations with appropriate surveillance. Although these machines can attract high foot traffic, the potential for increased maintenance costs and security concerns must be weighed carefully.
Related Video: CS 198-126: Lecture 12 – Diffusion Models
Key Industrial Applications of vending machine fatalities
Industry/Sector | Specific Application of vending machine fatalities | Value/Benefit for the Business | Key Sourcing Considerations for this Application |
---|---|---|---|
Retail | Emergency response protocols for vending machines | Improved safety, reduced liability, enhanced brand trust | Compliance with local safety regulations, training resources |
Education | Safety audits in school vending areas | Protection of students, legal compliance | Regular maintenance schedules, safety training programs |
Healthcare | Patient and visitor safety in hospital vending areas | Mitigated risk of accidents, improved patient trust | Health and safety certifications, vendor reliability |
Hospitality | Vending machine safety assessments in hotels | Enhanced guest experience, reduced liability risks | Local safety standards, emergency response training |
Manufacturing | Risk management for vending machine operations | Increased operational efficiency, reduced downtime | Equipment durability, maintenance contracts |
Retail
In the retail sector, implementing emergency response protocols for vending machines is critical. These protocols ensure that staff are prepared to handle incidents involving machines that may malfunction or pose safety risks. This application not only enhances customer safety but also mitigates potential liabilities for businesses. International buyers, especially from regions like Africa and South America, should ensure compliance with local regulations and consider training resources to effectively manage these protocols.
Education
Schools and universities benefit significantly from conducting safety audits in areas where vending machines are located. These audits help identify potential hazards and ensure that machines are secure and functioning properly. By prioritizing student safety, educational institutions can avoid legal issues and enhance their reputation. Buyers in the education sector should focus on establishing regular maintenance schedules and implementing safety training programs for staff to manage these risks effectively.
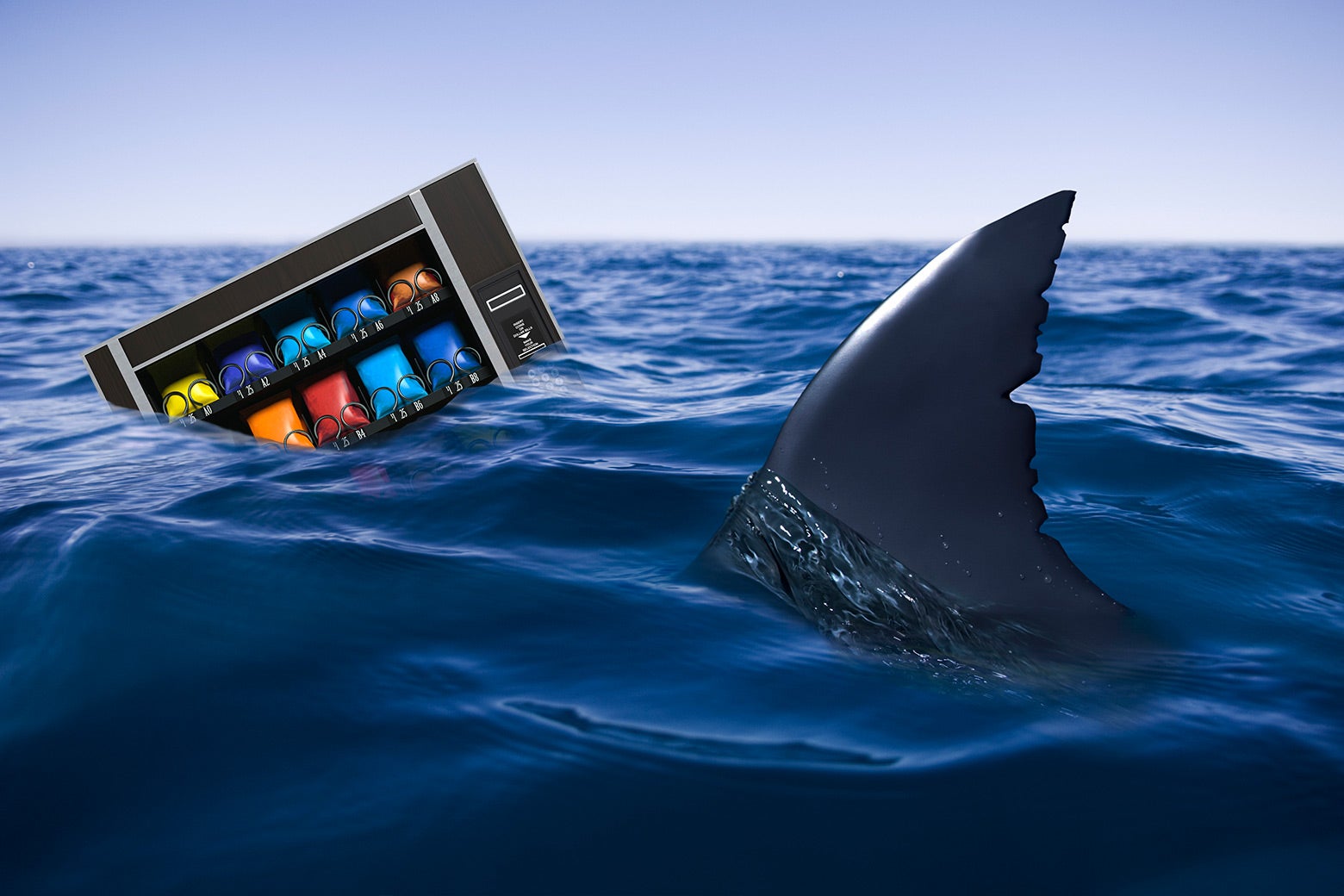
Illustrative Image (Source: Google Search)
Healthcare
In healthcare facilities, ensuring the safety of patients and visitors around vending machines is paramount. The implementation of safety measures can significantly reduce the risk of accidents, fostering a sense of security among patients and their families. This application is particularly important in hospitals where foot traffic is high. Buyers in the healthcare sector need to prioritize health and safety certifications for vending machines and ensure vendor reliability to maintain a safe environment.
Hospitality
Hotels and resorts can enhance guest experiences by conducting safety assessments of vending machines. These assessments help identify and mitigate risks associated with machine usage, ensuring that guests can enjoy services without concern. This proactive approach not only improves guest satisfaction but also reduces liability risks for hospitality businesses. Key considerations for buyers in this sector include adherence to local safety standards and the availability of emergency response training for staff.
Manufacturing
In manufacturing environments, effective risk management for vending machine operations is essential. This involves regular evaluations of machine safety and functionality to prevent accidents that could lead to operational downtime. By prioritizing machine safety, manufacturers can improve overall operational efficiency. International buyers should focus on sourcing durable equipment and establishing maintenance contracts to ensure consistent performance and safety compliance.
Related Video: Warnerwoods Company uses a perpetual Inventory System
Strategic Material Selection Guide for vending machine fatalities
Analysis of Common Materials for Vending Machine Fatalities
When selecting materials for vending machines, especially in the context of safety and preventing fatalities, it is crucial to consider properties that enhance product performance, durability, and compliance with international standards. Here, we analyze four common materials used in vending machine construction and their implications for international B2B buyers.
1. Carbon Steel (e.g., A216 WCB)
Key Properties: Carbon steel offers excellent strength and toughness, with a temperature rating up to 600°F (316°C) and good pressure ratings. However, it is susceptible to corrosion if not properly coated or treated.
Pros & Cons: The primary advantage of carbon steel is its cost-effectiveness and availability, making it a popular choice for structural components. However, its susceptibility to rust and corrosion can limit its lifespan, especially in humid or wet environments, necessitating additional protective measures.
Impact on Application: Carbon steel is suitable for applications where high strength is required, such as frames and support structures. However, it may not be ideal for areas exposed to moisture without proper treatment.
Considerations for International Buyers: Buyers from regions like Africa and South America should be aware of local climate conditions that may affect corrosion resistance. Compliance with standards such as ASTM A36 for structural steel is essential to ensure safety and performance.
2. Stainless Steel (e.g., AISI 304)
Key Properties: Stainless steel is known for its excellent corrosion resistance, high-temperature tolerance (up to 1600°F or 870°C), and mechanical strength.
Pros & Cons: The key advantage of stainless steel is its durability and resistance to rust, making it suitable for food-grade applications. However, it is generally more expensive than carbon steel and may require more complex manufacturing processes.
Impact on Application: Stainless steel is ideal for components that come into contact with food or beverages, ensuring hygiene and safety. Its resistance to corrosion makes it suitable for both indoor and outdoor vending machines.
Considerations for International Buyers: Buyers in Europe and the Middle East should ensure compliance with food safety standards like FDA or EU regulations. The higher cost may be justified by the longevity and reduced maintenance needs.
3. Aluminum
Key Properties: Aluminum is lightweight, with excellent corrosion resistance and a melting point of approximately 1220°F (660°C). It is also easy to fabricate and has good thermal conductivity.
Pros & Cons: The lightweight nature of aluminum makes it easy to handle and transport, reducing shipping costs. However, it is less strong compared to steel, which may limit its use in high-stress applications.
Impact on Application: Aluminum is often used in vending machine panels and frames where weight reduction is beneficial. Its corrosion resistance makes it suitable for outdoor installations.
Considerations for International Buyers: Buyers should consider the cost implications of aluminum, which can be higher than carbon steel but lower than stainless steel. Compliance with standards like ASTM B221 for aluminum extrusions is essential.
4. Polycarbonate
Key Properties: Polycarbonate is a high-impact-resistant plastic with a temperature tolerance ranging from -40°F to 240°F (-40°C to 115°C). It is transparent, allowing for visibility of products inside the vending machine.
Pros & Cons: The primary advantage of polycarbonate is its lightweight and shatter-resistant properties, making it safe for public use. However, it may not withstand extreme temperatures and can be prone to scratching.
Impact on Application: Polycarbonate is ideal for machine windows and protective covers, enhancing visibility while ensuring safety. Its lightweight nature can contribute to overall machine efficiency.
Considerations for International Buyers: Buyers should be aware of UV resistance and potential degradation in sunlight, particularly in regions with high solar exposure. Compliance with relevant safety standards is critical to ensure consumer protection.
Summary Table
Material | Typical Use Case for vending machine fatalities | Key Advantage | Key Disadvantage/Limitation | Relative Cost (Low/Med/High) |
---|---|---|---|---|
Carbon Steel (e.g., A216 WCB) | Structural components, frames | Cost-effective, good strength | Susceptible to corrosion if not protected | Low |
Stainless Steel (e.g., AISI 304) | Food contact areas, structural components | Excellent corrosion resistance | Higher cost, complex manufacturing | High |
Aluminum | Panels, frames | Lightweight, corrosion-resistant | Less strength than steel | Medium |
Polycarbonate | Windows, protective covers | Shatter-resistant, lightweight | Prone to scratching, temperature limitations | Medium |
This guide provides actionable insights for international B2B buyers, ensuring informed decisions when selecting materials for vending machines to enhance safety and compliance.
In-depth Look: Manufacturing Processes and Quality Assurance for vending machine fatalities
When assessing the manufacturing processes and quality assurance measures related to vending machines, particularly in the context of fatalities, B2B buyers must understand both the production stages and the quality control (QC) frameworks that ensure safety and reliability. This section breaks down these elements, highlighting the necessary steps and standards that buyers should consider.
Manufacturing Processes
The manufacturing of vending machines involves several key stages, each critical to ensuring the final product is safe, functional, and compliant with international standards.
1. Material Preparation
Material selection is vital. Common materials include high-grade steel for the chassis, tempered glass for display panels, and food-grade plastics for product compartments. Buyers should verify the sourcing of materials, ensuring they meet safety standards and regulations specific to their region.
- Sourcing Quality Materials: Look for suppliers that provide material certifications (e.g., ISO 9001) to guarantee that the materials are compliant with safety and quality standards.
- Sustainability Considerations: Increasingly, buyers are seeking suppliers who prioritize eco-friendly materials and processes, aligning with global sustainability initiatives.
2. Forming
This stage involves shaping the prepared materials into parts of the vending machine. Techniques may include:
- Laser Cutting: For precision cutting of metal and plastic components, ensuring tight tolerances.
- Bending and Stamping: Used to create the structure of the machine, including the frame and doors.
Investing in advanced forming technologies can enhance the quality and durability of the final product. Buyers should inquire about the machinery and techniques used to ensure they align with modern manufacturing standards.
3. Assembly
The assembly process combines the various components into a complete vending machine. Key considerations include:
- Automation vs. Manual Labor: Automated assembly lines can improve consistency and reduce human error. However, manual assembly may be necessary for more intricate components.
- Integration of Technology: Modern vending machines often incorporate smart technology for payment processing and inventory management. Suppliers should demonstrate expertise in integrating these systems.
4. Finishing
Finishing processes enhance both the aesthetic and functional aspects of vending machines. This includes:
- Painting and Coating: To protect against corrosion and wear, ensuring longevity.
- Quality Control Checks: Throughout the finishing process, checkpoints should be established to catch defects early.
Quality Assurance
Quality assurance is crucial in preventing vending machine-related fatalities. Implementing a robust QC framework helps ensure compliance with international safety standards.
Relevant International Standards
B2B buyers should familiarize themselves with the following standards:
- ISO 9001: This standard sets out the criteria for a quality management system, ensuring consistent quality in products and services.
- CE Marking: Required for products sold within the European Economic Area, indicating compliance with health, safety, and environmental protection standards.
- API Standards: For machines that handle food or beverages, API standards may apply, ensuring food safety and hygiene.
QC Checkpoints
Effective quality control involves multiple checkpoints throughout the manufacturing process:
- Incoming Quality Control (IQC): Inspect raw materials upon arrival to ensure they meet specified standards.
- In-Process Quality Control (IPQC): Conduct checks during the manufacturing process to identify defects early.
- Final Quality Control (FQC): A thorough inspection of the finished product before shipment, ensuring compliance with all specifications.
Common Testing Methods
Testing methods to verify the quality and safety of vending machines include:
- Functional Testing: Ensuring all mechanical and electronic components operate as intended.
- Safety Testing: Assessing electrical safety, including insulation resistance and grounding tests.
- Durability Testing: Simulating prolonged use to identify potential failure points.
Verification of Supplier QC
International B2B buyers, particularly from diverse regions like Africa, South America, the Middle East, and Europe, should adopt a rigorous approach to verify supplier QC practices:
- Supplier Audits: Regular audits can help ensure compliance with quality standards and identify areas for improvement.
- Quality Reports: Request detailed QC reports from suppliers, which should include inspection results and corrective actions taken for any identified issues.
- Third-Party Inspections: Engaging third-party organizations for independent inspections can provide an unbiased assessment of product quality.
QC and Certification Nuances for International Buyers
Understanding the nuances of quality control and certification is crucial for international buyers. Different regions may have varying regulations and standards that must be adhered to:
- Regional Compliance: Familiarize yourself with local safety regulations in your target market. For instance, the Middle East may have specific standards that differ from those in Europe.
- Documentation Requirements: Ensure that suppliers can provide all necessary documentation, including certifications, test results, and compliance reports.
By prioritizing these manufacturing processes and quality assurance measures, international B2B buyers can mitigate risks associated with vending machine fatalities and ensure the procurement of safe, reliable products that meet global standards.
Related Video: SMART Quality Control for Manufacturing
Comprehensive Cost and Pricing Analysis for vending machine fatalities Sourcing
When sourcing for vending machine fatalities, it’s crucial to understand the cost structure and pricing dynamics involved in the procurement process. This analysis will provide actionable insights for international B2B buyers, especially those operating in Africa, South America, the Middle East, and Europe.
Cost Components
-
Materials: The primary cost driver in the manufacturing of vending machines involves the raw materials used, such as metal casings, electronic components, and refrigeration units. The quality and sourcing of these materials can significantly affect the overall cost. Buyers should consider local suppliers to potentially reduce material costs.
-
Labor: Labor costs vary by region and can be influenced by local wage standards. For instance, labor costs in Africa and South America may be lower compared to Europe, impacting the final price of the machines. Understanding local labor laws and regulations is essential for accurate cost assessment.
-
Manufacturing Overhead: This includes utilities, rent, and other operational costs associated with production. Efficient manufacturing processes can help in minimizing overhead, thus lowering the overall price.
-
Tooling: Customization often requires specialized tools and equipment. The initial investment in tooling can be significant, but it pays off in reduced production costs per unit when ordered in larger volumes.
-
Quality Control (QC): Ensuring that the vending machines meet safety and operational standards is crucial. Quality control processes can add to the cost but are necessary to prevent future liabilities, particularly concerning fatalities.
-
Logistics: Transportation and shipping costs can vary greatly depending on the Incoterms agreed upon. Understanding these terms can help buyers negotiate better shipping arrangements that can save costs.
-
Margin: Suppliers typically include a profit margin in their pricing. This margin can vary based on competition, supplier reputation, and market demand.
Price Influencers
-
Volume/MOQ (Minimum Order Quantity): Bulk purchases often lead to lower per-unit costs. Buyers should assess their needs to negotiate favorable terms.
-
Specifications/Customization: Customized vending machines that meet specific operational requirements may incur additional costs. Buyers should evaluate the necessity of these custom features against their budget.
-
Materials and Quality Certifications: Higher-quality materials and certifications (such as ISO) can increase costs. However, these often translate to better durability and safety, which are critical in preventing fatalities.
-
Supplier Factors: The reliability and reputation of suppliers play a significant role in pricing. Established suppliers may offer better service but at a premium price.
-
Incoterms: Understanding the agreed-upon Incoterms is vital for managing shipping risks and costs. Terms like FOB (Free On Board) or CIF (Cost, Insurance, and Freight) can influence the total landed cost.
Buyer Tips
-
Negotiation: Effective negotiation can yield better pricing. Buyers should be prepared with data on market rates and supplier performance to support their positions.
-
Cost-Efficiency: Evaluate total cost of ownership (TCO) rather than just the initial purchase price. This includes maintenance, operational costs, and potential liabilities related to fatalities.
-
Pricing Nuances: International buyers should be aware of currency fluctuations and import duties that may affect pricing. Establishing long-term relationships with suppliers can also lead to better pricing structures.
-
Local Considerations: For buyers in Africa and South America, understanding local market dynamics and supplier capabilities can lead to significant cost savings. Engaging local suppliers may also enhance logistical efficiency.
Disclaimer
Prices and cost structures mentioned are indicative and subject to change based on market conditions, supplier negotiations, and specific buyer requirements. Always conduct thorough market research and consult multiple suppliers to ensure competitive pricing.
Spotlight on Potential vending machine fatalities Manufacturers and Suppliers
This section offers a look at a few manufacturers active in the ‘vending machine fatalities’ market. This is a representative sample for illustrative purposes; B2B buyers must conduct their own extensive due diligence before any engagement. Information is synthesized from public sources and general industry knowledge.
Essential Technical Properties and Trade Terminology for vending machine fatalities
Key Technical Properties for Vending Machine Safety
When considering vending machine fatalities, understanding critical technical properties is essential for B2B buyers to ensure safety and compliance. Here are some key specifications to consider:
-
Material Grade
– Definition: Refers to the quality and type of materials used in manufacturing the vending machine, such as stainless steel or plastic.
– Importance: Higher-grade materials can withstand environmental stress and reduce the risk of mechanical failure, which may lead to accidents. -
Weight Distribution
– Definition: The design aspect that determines how weight is spread throughout the vending machine.
– Importance: Proper weight distribution ensures stability and minimizes the likelihood of tipping over, thereby reducing the risk of injury during use. -
Tolerance Levels
– Definition: The allowable deviation from specified dimensions in the machine’s design.
– Importance: Tight tolerances are critical in ensuring that all components fit together correctly, thus preventing malfunctions that could lead to safety hazards. -
Safety Features
– Definition: Includes mechanisms such as emergency shut-off switches, reinforced doors, and anti-tip designs.
– Importance: These features are vital for protecting users and preventing fatalities, making them a crucial consideration for buyers looking to enhance safety. -
Electrical Standards Compliance
– Definition: Adherence to safety regulations concerning electrical components, such as grounding and surge protection.
– Importance: Compliance with international electrical standards mitigates risks of electrical shock or fire, which are significant factors in vending machine fatalities. -
Accessibility Design
– Definition: The incorporation of features that ensure ease of access for all users, including those with disabilities.
– Importance: An accessible design not only complies with legal requirements but also reduces the risk of accidents related to reaching or operating the machine improperly.
Common Industry Terms
Understanding industry terminology is crucial for effective communication and negotiation in the vending machine market. Here are some key terms:
-
OEM (Original Equipment Manufacturer)
– Definition: A company that produces parts or equipment that may be marketed by another manufacturer.
– Relevance: Buyers often deal with OEMs for replacement parts or custom configurations, impacting the overall quality and safety of the vending machines. -
MOQ (Minimum Order Quantity)
– Definition: The smallest quantity of a product that a supplier is willing to sell.
– Relevance: Knowing the MOQ helps buyers manage inventory and budget effectively, especially when sourcing safety-critical components. -
RFQ (Request for Quotation)
– Definition: A document issued by a buyer to request price proposals from suppliers for specific products or services.
– Relevance: Issuing RFQs allows buyers to compare pricing and terms, which is essential when assessing suppliers for safety equipment.
-
Incoterms (International Commercial Terms)
– Definition: A set of rules that define responsibilities of sellers and buyers in international transactions.
– Relevance: Understanding Incoterms is crucial for managing risks associated with shipping and delivery, particularly for safety-related components that may have strict compliance requirements. -
CE Marking
– Definition: A certification indicating that a product meets EU safety, health, and environmental protection standards.
– Relevance: Vending machines sold in Europe must bear CE marking to ensure compliance with safety regulations, making it a key consideration for buyers. -
Lead Time
– Definition: The time taken from placing an order to delivery.
– Relevance: Understanding lead times is vital for planning inventory and ensuring that safety measures are implemented promptly.
By familiarizing themselves with these properties and terms, B2B buyers can make informed decisions that enhance the safety and reliability of vending machines in their operations.
Navigating Market Dynamics, Sourcing Trends, and Sustainability in the vending machine fatalities Sector
Market Overview & Key Trends
The vending machine fatalities sector is experiencing significant shifts driven by globalization, technological advancements, and changing consumer behaviors. Key market dynamics include the rise of smart vending machines equipped with IoT technology, enabling real-time monitoring and data collection. This trend is particularly relevant for international B2B buyers from regions such as Africa, South America, the Middle East, and Europe, as it enhances operational efficiency and reduces downtime.
Emerging sourcing trends highlight the growing importance of local suppliers to mitigate risks associated with international logistics. Buyers are increasingly looking for partnerships that emphasize reliability and quick turnaround times, particularly in areas where supply chain disruptions have been prevalent. Additionally, sustainability is becoming a critical factor in procurement decisions. Companies are prioritizing vendors that provide eco-friendly machines and promote responsible sourcing practices.
In terms of global drivers, the surge in urbanization and the demand for contactless services post-pandemic are reshaping the vending machine landscape. B2B buyers should be aware of the increasing consumer preference for healthier options, which is prompting manufacturers to innovate and diversify their product offerings. This evolution presents opportunities for buyers to align with forward-thinking suppliers that prioritize safety and health standards.
Sustainability & Ethical Sourcing in B2B
Sustainability is a pressing concern within the vending machine fatalities sector, as environmental impacts from manufacturing and operational practices come under scrutiny. B2B buyers must consider the environmental footprint of the machines they procure, focusing on energy-efficient models that minimize electricity consumption and reduce waste.
The importance of ethical supply chains cannot be overstated. Buyers should prioritize suppliers that adhere to fair labor practices and demonstrate transparency in their sourcing methods. Certifications such as ISO 14001 (Environmental Management) and Fair Trade can serve as indicators of a supplier’s commitment to sustainability.
Investing in green materials is another critical aspect. Vending machines that utilize recyclable or biodegradable components not only help in reducing environmental impact but also resonate well with eco-conscious consumers. B2B buyers should seek partnerships with manufacturers who are willing to invest in sustainable materials and practices, thus ensuring compliance with evolving regulations and consumer expectations.
Brief Evolution/History
The vending machine industry has evolved significantly since its inception in the late 19th century. Initially focused on dispensing simple items like postcards and candy, the sector has expanded to include a diverse range of products, including fresh food and beverages. The introduction of technology in the 21st century marked a pivotal shift, with advancements such as cashless payment systems and smart inventory management transforming the way machines operate.
Today, the focus has shifted towards integrating sustainability and safety measures, a response to both regulatory pressures and changing consumer preferences. As the sector continues to evolve, international B2B buyers must stay informed about the latest trends and technologies to ensure they are making strategic sourcing decisions that align with market demands.
Related Video: Global trade will never be the same again, says Christine Lagarde | Power & Politics
Frequently Asked Questions (FAQs) for B2B Buyers of vending machine fatalities
-
What should I consider when vetting suppliers for vending machines?
When vetting suppliers, prioritize their experience and reputation in the vending machine industry. Request references from previous clients and check online reviews. Evaluate their compliance with international safety standards and certifications relevant to your region. Additionally, assess their financial stability and capacity to handle your orders, which is crucial for ensuring reliability in supply and service. -
Can I customize vending machines to suit my market’s preferences?
Yes, most manufacturers offer customization options for vending machines. You can specify product selections, branding elements, and machine configurations that align with local tastes and preferences. Discuss your requirements during initial consultations and request samples or prototypes to ensure the final product meets your expectations before bulk ordering. -
What are typical minimum order quantities (MOQs) and lead times for vending machines?
MOQs can vary significantly based on the supplier and the type of machine. Generally, expect MOQs ranging from 10 to 100 units. Lead times typically span from 4 to 12 weeks, depending on customization and production capacity. Always confirm these details upfront to align your inventory needs with the supplier’s capabilities.
-
What payment options are commonly available when sourcing vending machines?
Most suppliers accept various payment methods, including bank transfers, letters of credit, and online payment platforms. Discuss payment terms during negotiations, including deposits and payment schedules. Ensure that you understand the implications of each payment method, particularly regarding transaction fees and currency exchange rates, especially for international transactions. -
How can I ensure quality assurance and certifications for vending machines?
Request copies of relevant quality assurance certifications, such as ISO 9001 or compliance with local safety standards. Conduct factory audits if possible, or rely on third-party inspection services to verify quality before shipment. Establish clear quality expectations in your purchase agreement to safeguard against receiving defective products.
-
What logistics considerations should I keep in mind when importing vending machines?
When importing, consider shipping methods, customs clearance processes, and associated costs. Collaborate with logistics providers familiar with your region to ensure smooth transit and adherence to local regulations. Additionally, factor in insurance for high-value shipments to mitigate risks during transportation. -
How should I handle disputes with vending machine suppliers?
Establish clear terms in your contract regarding dispute resolution, including timelines and methods (e.g., mediation or arbitration). Keep detailed records of all communications and transactions to support your claims. If disputes arise, address them promptly and professionally, as maintaining a good relationship with suppliers can be beneficial for future business. -
What are the key factors influencing the resale value of vending machines?
Resale value is influenced by factors such as the machine’s condition, age, brand reputation, and technological features. Machines equipped with modern payment systems and energy-efficient designs tend to retain higher value. Regular maintenance and service records can also enhance resale prospects, so ensure you keep thorough documentation throughout the machine’s lifecycle.
Strategic Sourcing Conclusion and Outlook for vending machine fatalities
As we navigate the complexities of vending machine operations, it becomes increasingly clear that strategic sourcing is paramount to mitigating risks associated with vending machine fatalities. The insights gathered highlight the need for international B2B buyers, particularly in regions like Africa, South America, the Middle East, and Europe, to prioritize safety features in their procurement processes.
Key Takeaways:
– Invest in Safety Technologies: Ensure that the vending machines sourced are equipped with advanced safety features, such as anti-tipping mechanisms and robust locking systems.
– Supplier Evaluation: Conduct thorough evaluations of suppliers to assess their commitment to safety standards and regulations.
– Training and Awareness: Implement training programs for operators and users to foster a culture of safety and awareness around vending machine usage.
The value of strategic sourcing transcends mere cost savings; it encompasses a holistic approach to risk management. By aligning procurement strategies with safety standards, businesses not only protect their investments but also safeguard their customers.
Looking ahead, we encourage international buyers to embrace these principles as they expand their vending machine portfolios. Together, we can enhance safety and reliability in the vending sector, ultimately leading to a more secure environment for all users.