Master the Best Place to Put a Vending Machine for Maximum
Guide to Best Place To Put A Vending Machine
- Introduction: Navigating the Global Market for best place to put a vending machine
- Understanding best place to put a vending machine Types and Variations
- Key Industrial Applications of best place to put a vending machine
- Strategic Material Selection Guide for best place to put a vending machine
- In-depth Look: Manufacturing Processes and Quality Assurance for best place to put a vending machine
- Comprehensive Cost and Pricing Analysis for best place to put a vending machine Sourcing
- Spotlight on Potential best place to put a vending machine Manufacturers and Suppliers
- Essential Technical Properties and Trade Terminology for best place to put a vending machine
- Navigating Market Dynamics, Sourcing Trends, and Sustainability in the best place to put a vending machine Sector
- Frequently Asked Questions (FAQs) for B2B Buyers of best place to put a vending machine
- Strategic Sourcing Conclusion and Outlook for best place to put a vending machine
Introduction: Navigating the Global Market for best place to put a vending machine
The strategic placement of vending machines is a pivotal factor in maximizing profitability and customer engagement in today’s competitive market. For B2B buyers, particularly those operating in diverse regions such as Africa, South America, the Middle East, and Europe—including key markets like Turkey and Saudi Arabia—understanding the optimal locations for vending machines can significantly enhance business outcomes. This guide delves deep into the nuances of vending machine placement, offering a holistic view that encompasses various types of vending machines, material considerations, manufacturing quality control (QC), and supplier sourcing.
By exploring the critical aspects of cost analysis and market trends, this comprehensive resource equips international B2B buyers with the necessary insights to make informed sourcing decisions. You’ll discover how factors such as foot traffic, demographic profiles, and consumer preferences can influence the success of vending machine placements in different environments, whether in high-traffic urban centers, educational institutions, or corporate offices. Additionally, the guide addresses frequently asked questions, providing clarity on common challenges faced in the vending machine industry.
With actionable insights tailored to the unique dynamics of emerging and established markets, this guide serves as an invaluable tool for B2B buyers seeking to optimize their vending machine strategies. By leveraging the information within, businesses can enhance their operational efficiencies and better cater to the needs of their target audiences, ultimately driving sales and fostering long-term growth.
Understanding best place to put a vending machine Types and Variations
Type Name | Key Distinguishing Features | Primary B2B Applications | Brief Pros & Cons for Buyers |
---|---|---|---|
High-Traffic Locations | Placed in areas with heavy foot traffic | Airports, shopping malls | Pros: High sales potential; Cons: Higher competition |
Educational Institutions | Targeted at students and faculty | Schools, universities | Pros: Steady customer base; Cons: Limited operating hours |
Corporate Offices | Installed in break rooms or lounges | Office buildings | Pros: Regular usage by employees; Cons: Space limitations |
Healthcare Facilities | Located in waiting areas or cafeterias | Hospitals, clinics | Pros: Essential for patient and visitor convenience; Cons: Regulatory compliance needed |
Residential Complexes | Positioned in communal areas | Apartment buildings, gated communities | Pros: Consistent demand from residents; Cons: Maintenance and operational challenges |
High-Traffic Locations
High-traffic locations, such as airports and shopping malls, are prime spots for vending machines due to the large volume of potential customers. These areas typically experience constant foot traffic, making them ideal for maximizing sales. Buyers should consider the competitive landscape, as multiple vending options may be available in such locations, necessitating unique product offerings or branding to stand out.
Educational Institutions
Vending machines in educational institutions cater to students and faculty, offering snacks and beverages during breaks. These machines can be strategically placed in cafeterias, libraries, or hallways to capture the attention of a captive audience. However, buyers should be aware of operating hours and the need for healthy product options to comply with school wellness policies.
Corporate Offices
Installing vending machines in corporate offices can provide employees with convenient access to snacks and drinks during work hours. Break rooms or lounges are optimal locations, as they are frequented by staff during breaks. Buyers should evaluate the preferences of the workforce to stock popular items, ensuring consistent patronage while also considering space constraints.
Healthcare Facilities
Healthcare facilities, including hospitals and clinics, require vending machines in waiting areas or cafeterias to serve patients and visitors. These machines should offer healthy and quick meal options, catering to a diverse demographic. Buyers must navigate regulatory compliance and health standards, ensuring that products are suitable for a healthcare environment.
Residential Complexes
Vending machines in residential complexes provide residents with easy access to snacks and drinks without the need to leave the premises. Common areas such as lobbies or lounges are ideal placements. Buyers should consider the demographics of the residents and the types of products that would appeal to them, while also addressing maintenance and operational concerns inherent in residential settings.
Related Video: Best Places To Put Your Vending Machine in 2025
Key Industrial Applications of best place to put a vending machine
Industry/Sector | Specific Application of best place to put a vending machine | Value/Benefit for the Business | Key Sourcing Considerations for this Application |
---|---|---|---|
Manufacturing | Breakroom and factory floor vending machines | Enhances employee satisfaction and productivity | Machine size, product selection, and maintenance support |
Education | Vending machines in schools and universities | Provides convenient access to snacks and drinks | Compliance with health regulations, payment options |
Healthcare | Vending machines in hospitals and clinics | Offers quick access to healthy snacks and beverages | Nutritional options, sanitation standards, and reliability |
Transportation | Vending machines at airports and train stations | Improves customer experience and convenience | Location accessibility, product variety, and payment systems |
Corporate Offices | Vending machines in office buildings | Increases employee morale and reduces downtime | Customization options, service frequency, and pricing |
Manufacturing
In the manufacturing sector, vending machines are strategically placed in breakrooms and on the factory floor to provide employees with convenient access to snacks and beverages. This placement enhances employee satisfaction, which can lead to increased productivity and reduced downtime. B2B buyers should consider the machine size, product selection, and ongoing maintenance support when sourcing vending machines to ensure they meet the specific needs of their workforce.
Education
Vending machines in educational institutions, such as schools and universities, serve as convenient outlets for students and staff to access snacks and drinks. This application not only caters to the busy schedules of students but also promotes healthier eating habits if equipped with nutritious options. Buyers should focus on compliance with health regulations, such as offering balanced food choices and ensuring proper hygiene, as well as incorporating flexible payment options to accommodate a diverse student body.
Healthcare
In healthcare facilities, vending machines can be installed in hospitals and clinics to provide quick access to healthy snacks and beverages for both staff and visitors. This convenience is essential in high-pressure environments where time is of the essence. Buyers in this sector must prioritize nutritional options, sanitation standards, and the reliability of the machines to ensure that they meet the unique demands of healthcare settings.
Transportation
Vending machines positioned at airports and train stations enhance customer experience by offering travelers quick access to snacks and beverages while they wait. This application is particularly valuable in high-traffic areas where convenience is crucial. B2B buyers should consider factors such as location accessibility, product variety tailored to different demographics, and robust payment systems that cater to international travelers.
Corporate Offices
In corporate office environments, vending machines can significantly boost employee morale by providing easy access to refreshments, thus reducing downtime during work hours. The placement of these machines can be tailored to various office layouts, ensuring that they are easily accessible to all employees. When sourcing, businesses should look for customization options that reflect company culture, service frequency to maintain stock, and competitive pricing to maximize value.
Related Video: How to Start a Vending Machine Business, Cost, Tips, How Much You Make
Strategic Material Selection Guide for best place to put a vending machine
When selecting the best place to put a vending machine, the choice of materials plays a crucial role in ensuring durability, functionality, and compliance with local standards. This analysis focuses on four common materials used in the construction and placement of vending machines, considering their properties, advantages, disadvantages, and specific considerations for international B2B buyers.
1. Stainless Steel
Key Properties:
Stainless steel is known for its excellent corrosion resistance, high tensile strength, and ability to withstand high temperatures. It typically has a temperature rating of up to 800°F (427°C) and is resistant to various chemicals, making it suitable for diverse environments.
Pros & Cons:
The primary advantage of stainless steel is its durability and resistance to rust and corrosion, which is critical in humid or wet environments. However, it can be more expensive than other materials, and its manufacturing process can be complex, requiring specialized equipment.
Impact on Application:
Stainless steel is compatible with a wide range of media, including food and beverages, making it ideal for vending machines in public places. Its aesthetic appeal also aligns well with modern design trends.
Considerations for International Buyers:
Buyers from regions like Europe and the Middle East should ensure compliance with standards like ASTM and DIN for food safety. In Africa and South America, local regulations may vary, so understanding local standards is essential.
2. Carbon Steel
Key Properties:
Carbon steel is a strong material with good mechanical properties, typically rated for pressures up to 3000 psi. It is less resistant to corrosion compared to stainless steel but can be treated with coatings for protection.
Pros & Cons:
The main advantage of carbon steel is its cost-effectiveness and high strength, making it suitable for structural applications. However, its susceptibility to rust and corrosion limits its use in outdoor or humid environments without proper treatment.
Impact on Application:
Carbon steel is suitable for internal components of vending machines that are not exposed to moisture. Its strength makes it ideal for supporting structures.
Considerations for International Buyers:
Buyers should be aware of local corrosion resistance standards, especially in coastal areas of Africa and South America. Compliance with ASTM standards is also crucial for ensuring quality.
3. Aluminum
Key Properties:
Aluminum is lightweight, corrosion-resistant, and has a high strength-to-weight ratio. It can withstand temperatures up to 400°F (204°C) and is easily machinable.
Pros & Cons:
The advantages of aluminum include its lightweight nature, which simplifies transportation and installation. However, it may not be as strong as stainless or carbon steel, and its cost can vary significantly based on the alloy used.
Impact on Application:
Aluminum is suitable for vending machines that require mobility or frequent relocation. Its corrosion resistance makes it ideal for outdoor applications.
Considerations for International Buyers:
In regions like Turkey and Saudi Arabia, where high temperatures are common, aluminum’s thermal properties should be considered. Compliance with local standards for aluminum alloys is also important.
4. High-Density Polyethylene (HDPE)
Key Properties:
HDPE is a thermoplastic known for its high impact resistance and chemical stability. It can operate effectively in temperatures ranging from -40°F to 120°F (-40°C to 49°C).
Pros & Cons:
The key advantage of HDPE is its lightweight nature and resistance to corrosion and chemicals, making it ideal for outdoor use. However, it lacks the structural strength of metals and may not be suitable for heavy-duty applications.
Impact on Application:
HDPE is ideal for vending machines that dispense non-perishable items or those used in less demanding environments. Its versatility allows for creative designs.
Considerations for International Buyers:
Buyers should check for compliance with local environmental regulations, especially in Europe, where recycling standards are stringent. In South America and Africa, understanding local waste management practices is beneficial.
Summary Table
Material | Typical Use Case for best place to put a vending machine | Key Advantage | Key Disadvantage/Limitation | Relative Cost (Low/Med/High) |
---|---|---|---|---|
Stainless Steel | Outdoor vending machines in public areas | Excellent corrosion resistance | Higher cost, complex manufacturing | High |
Carbon Steel | Internal structural components | Cost-effective, high strength | Susceptible to corrosion | Low |
Aluminum | Mobile vending machines | Lightweight, corrosion-resistant | Lower strength compared to steel | Medium |
High-Density Polyethylene (HDPE) | Vending machines for non-perishable items | Lightweight, chemical resistance | Lacks structural strength | Medium |
This guide provides actionable insights into material selection for vending machines, considering the specific needs and standards of international B2B buyers across different regions.
In-depth Look: Manufacturing Processes and Quality Assurance for best place to put a vending machine
Manufacturing Processes for Vending Machines
When considering the placement of vending machines, understanding the manufacturing processes involved in their production is crucial for B2B buyers. This knowledge not only aids in selecting the right supplier but also ensures that the machines meet the required standards for durability and functionality in diverse environments.
Main Stages of Manufacturing
-
Material Preparation
– Selection of Materials: The first step involves sourcing high-quality materials such as steel for structural integrity and plastic for aesthetic components. Suppliers should provide certifications for the materials used, ensuring they meet industry standards.
– Cutting and Shaping: Raw materials are cut and shaped using advanced machinery like CNC machines to achieve precise dimensions. This stage is critical for ensuring that all parts fit together seamlessly during assembly. -
Forming
– Metal Forming Techniques: Techniques such as stamping, bending, and welding are employed to create the frame and panels of the vending machine. These processes must adhere to strict tolerances to ensure structural integrity.
– Plastic Injection Molding: For components like buttons and display cases, injection molding is used. This method allows for mass production while maintaining high precision and uniformity.
-
Assembly
– Component Integration: Once all parts are fabricated, they are assembled. This includes integrating electronic components, refrigeration units, and payment systems. Each assembly line should be equipped with skilled workers to ensure quality workmanship.
– Sub-Assembly Checks: Before final assembly, sub-assemblies undergo individual checks to confirm that each component functions correctly. This reduces the risk of defects in the final product. -
Finishing
– Surface Treatment: This includes processes like powder coating or painting to enhance the aesthetic appeal and protect against corrosion. These finishes must meet specific environmental standards, especially for machines placed outdoors.
– Final Assembly and Quality Control: The final assembly involves installing all components and performing a comprehensive quality check to ensure functionality and safety standards are met.
Quality Assurance Processes
Quality assurance is vital in the manufacturing of vending machines to ensure they operate reliably across various markets.
International Standards and Certifications
- ISO 9001: This standard outlines the criteria for a quality management system, emphasizing consistent product quality and customer satisfaction. Suppliers should be ISO 9001 certified to demonstrate their commitment to quality.
- CE Marking: For machines sold in Europe, CE marking indicates compliance with health, safety, and environmental protection standards. This is particularly important for international buyers from Europe.
- API Standards: Specific to certain vending machines (e.g., those dispensing pharmaceuticals), adherence to API standards ensures safety and efficacy.
Quality Control Checkpoints
-
Incoming Quality Control (IQC)
– Materials and components received from suppliers are inspected for quality and compliance with specifications. This step helps identify potential issues before they enter the production line. -
In-Process Quality Control (IPQC)
– During manufacturing, regular inspections are conducted at various stages to ensure that processes are followed correctly and that components meet quality standards. This proactive approach minimizes defects. -
Final Quality Control (FQC)
– The final product undergoes rigorous testing, including functionality tests, safety checks, and aesthetic inspections. This stage is crucial for ensuring that the vending machines perform as expected in real-world conditions.
Common Testing Methods
- Functional Testing: Ensures all electronic components (e.g., payment systems, displays) work correctly.
- Durability Testing: Machines are subjected to stress tests to simulate real-world usage and assess their longevity.
- Safety Testing: Compliance with electrical safety standards is verified, especially for machines that include heating or refrigeration elements.
Verifying Supplier Quality Control
For B2B buyers, especially from regions like Africa, South America, the Middle East, and Europe, verifying a supplier’s quality control processes is essential.
- Supplier Audits: Conducting regular audits of suppliers can provide insights into their manufacturing processes and quality control measures. This includes reviewing their certifications and quality management practices.
- Quality Reports: Requesting detailed quality reports that outline the results of IQC, IPQC, and FQC can help buyers assess the reliability of the products.
- Third-Party Inspections: Engaging third-party inspection agencies can offer an unbiased assessment of a supplier’s manufacturing quality. This is particularly useful for international buyers who may not be able to visit facilities in person.
Quality Control and Certification Nuances for International Buyers
When engaging with suppliers from different regions, B2B buyers must be aware of the following nuances:
- Regional Compliance: Ensure that suppliers understand and comply with local regulations regarding product safety and environmental impact. For example, machines intended for the EU market must meet CE marking requirements.
- Language Barriers: Communicate clearly with suppliers about quality standards and expectations. Consider hiring local intermediaries to facilitate communication and ensure mutual understanding.
- Cultural Differences: Be mindful of cultural differences that may affect business practices and negotiations. Building strong relationships can enhance trust and ensure smoother transactions.
In summary, understanding the manufacturing processes and quality assurance protocols for vending machines is crucial for B2B buyers. By focusing on quality standards, inspection checkpoints, and supplier verification methods, businesses can ensure they select reliable products that meet their operational needs.
Related Video: SMART Quality Control for Manufacturing
Comprehensive Cost and Pricing Analysis for best place to put a vending machine Sourcing
When considering the best place to install a vending machine, a thorough understanding of the cost structure and pricing dynamics is crucial for international B2B buyers. This analysis will guide you in making informed decisions that align with your financial goals and operational needs.
Cost Components
-
Materials: The cost of materials primarily includes the machine itself, which varies based on features and specifications. Basic machines may start at lower price points, while advanced models with custom features can significantly increase costs. Consider the type of products to be dispensed, as this will also influence the material costs.
-
Labor: Labor costs encompass not just the installation of the vending machines but also ongoing maintenance and restocking. Hiring local technicians can reduce travel expenses, but be mindful of local wage standards which can vary significantly.
-
Manufacturing Overhead: This refers to indirect costs associated with the production of vending machines, including utilities, rent, and salaries of supervisory staff. Buyers should inquire about the manufacturing location, as overhead costs can affect pricing.
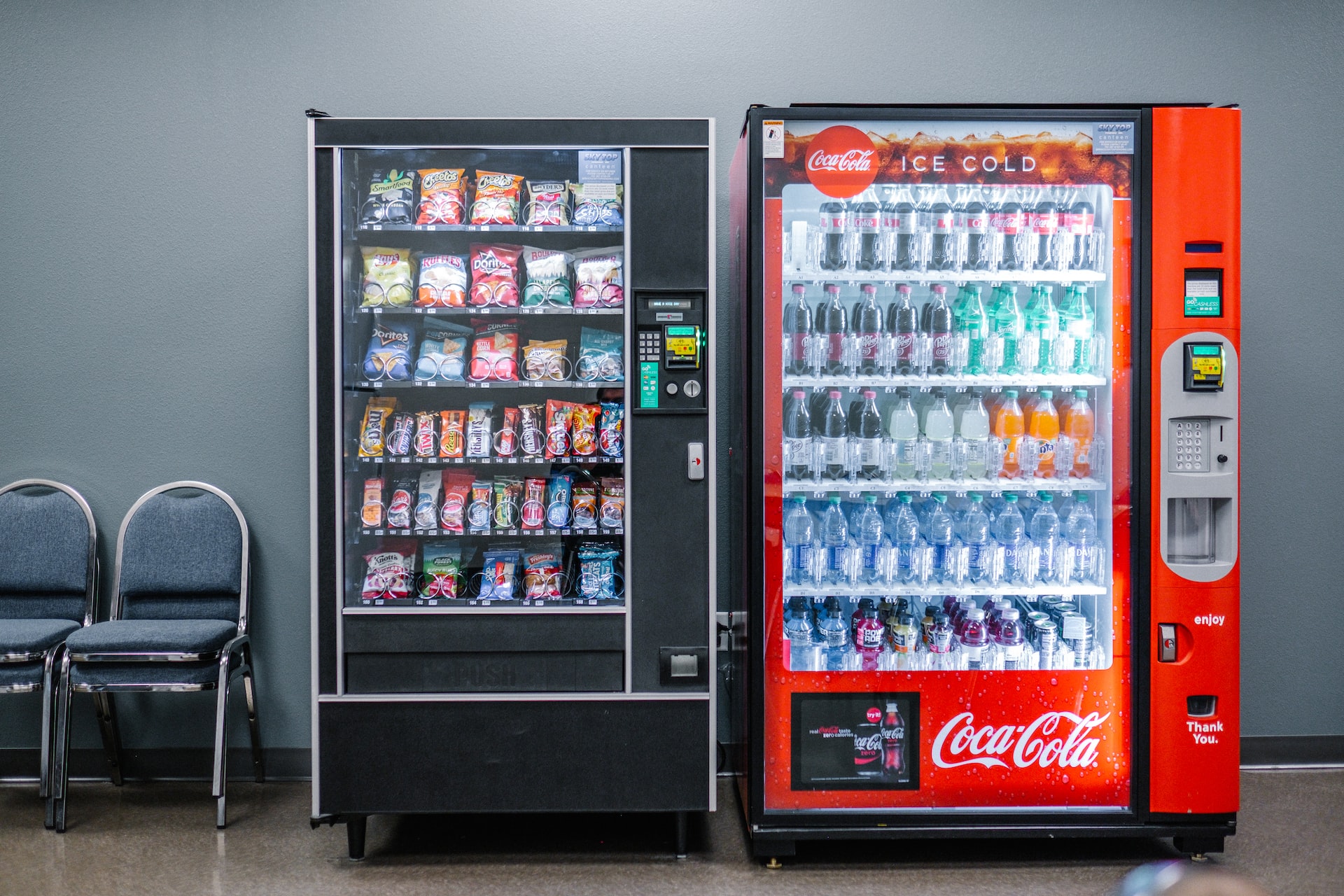
Illustrative Image (Source: Google Search)
-
Tooling: For custom vending machines, tooling costs can add up. If you require specialized designs or modifications, these costs should be factored into your budget.
-
Quality Control (QC): Ensuring the machine meets safety and operational standards is essential. The cost of quality control processes can vary based on supplier certifications and testing procedures. Always check for ISO or other relevant certifications that ensure product reliability.
-
Logistics: Shipping costs can be significant, especially for international buyers. Factors like distance, shipping method (air vs. sea), and local import taxes can dramatically affect the final price.
-
Margin: Suppliers will typically add a profit margin to their costs. Understanding the typical margins in the vending machine industry can help you gauge whether a quoted price is reasonable.
Price Influencers
-
Volume/MOQ: Many suppliers offer discounts based on the volume of machines ordered. Establishing a minimum order quantity (MOQ) can lead to significant savings.
-
Specifications/Customization: Customized machines with specific features will incur higher costs. Buyers should clearly outline their requirements to avoid unexpected expenses.
-
Materials: The choice of materials can influence durability and cost. High-quality materials may come at a premium but can enhance the longevity of the machine, potentially reducing Total Cost of Ownership (TCO).
-
Quality/Certifications: Machines with higher quality standards or certifications might have a higher upfront cost but can lead to lower maintenance costs and fewer operational issues over time.
-
Supplier Factors: The reputation and reliability of the supplier can impact pricing. Established suppliers may charge more due to brand trust but often provide better service and warranty options.
-
Incoterms: Understanding the shipping terms (e.g., FOB, CIF) is essential for budgeting. These terms dictate who is responsible for shipping costs and risks, which can affect your total expenditure.
Buyer Tips
-
Negotiation: Always engage in negotiations. Suppliers may have flexibility in pricing, especially for bulk orders.
-
Cost-Efficiency: Analyze the TCO rather than just the initial purchase price. Consider maintenance, energy consumption, and product turnover rates when evaluating cost-efficiency.
-
Pricing Nuances: International buyers should be aware of currency fluctuations, tariffs, and import duties that can influence the final cost of vending machines.
-
Local Market Insights: For buyers in Africa, South America, the Middle East, and Europe, understanding local market conditions, consumer preferences, and vending machine regulations can provide leverage in negotiations and procurement strategies.
Disclaimer
Prices for vending machines can vary widely based on the factors discussed. It is advisable to obtain multiple quotes and conduct a thorough cost analysis before making purchasing decisions.
Spotlight on Potential best place to put a vending machine Manufacturers and Suppliers
This section offers a look at a few manufacturers active in the ‘best place to put a vending machine’ market. This is a representative sample for illustrative purposes; B2B buyers must conduct their own extensive due diligence before any engagement. Information is synthesized from public sources and general industry knowledge.
Essential Technical Properties and Trade Terminology for best place to put a vending machine
Key Technical Properties for Vending Machine Placement
When considering the optimal placement of vending machines, several technical properties are critical to ensure effectiveness, durability, and profitability. Below are essential specifications that B2B buyers should evaluate:
-
Material Grade
– Definition: This refers to the type of materials used in the construction of the vending machine, such as stainless steel, tempered glass, or high-grade plastics.
– Importance: Higher-grade materials enhance durability, reduce maintenance costs, and improve aesthetic appeal, which can attract more customers. For instance, stainless steel is resistant to corrosion and easier to clean, making it ideal for high-traffic areas. -
Capacity
– Definition: This specification indicates the maximum number of products or items a vending machine can hold.
– Importance: Understanding capacity helps in selecting machines that align with location traffic patterns. A busy area may require a higher capacity machine to meet demand, while less trafficked areas can utilize smaller machines. -
Power Requirements
– Definition: The electrical specifications needed for the vending machine to operate, including voltage and wattage.
– Importance: Ensuring that the location can provide the necessary power is crucial for operational reliability. This is particularly important in regions with unstable electricity supply, as it affects machine functionality and product preservation. -
Temperature Control
– Definition: This refers to the ability of the vending machine to maintain a specific temperature range for perishable items.
– Importance: For vending machines selling food or beverages, effective temperature control is vital to ensure product safety and quality. Machines with better insulation and cooling systems can reduce energy consumption and provide longer-lasting freshness. -
User Interface
– Definition: This encompasses the design and functionality of the machine’s interaction elements, such as touchscreens or keypad interfaces.
– Importance: A user-friendly interface can significantly enhance customer experience, leading to increased sales. Machines with multilingual options or cashless payment systems are particularly appealing in diverse markets.
Common Trade Terminology
Understanding industry jargon is essential for effective communication and negotiation in the vending machine market. Here are some key terms:
-
OEM (Original Equipment Manufacturer)
– Definition: A company that produces parts or equipment that may be marketed by another manufacturer.
– Importance: Knowing OEM partners can help buyers ensure they are sourcing quality machines and parts that meet their specific needs and standards. -
MOQ (Minimum Order Quantity)
– Definition: The smallest quantity of a product that a supplier is willing to sell.
– Importance: Understanding MOQ is crucial for budgeting and inventory management. Buyers must balance the need for cost efficiency with the risk of overstocking. -
RFQ (Request for Quotation)
– Definition: A document issued by a buyer to request pricing and terms from suppliers for specific goods or services.
– Importance: An RFQ helps buyers gather competitive pricing and terms, enabling them to make informed purchasing decisions. -
Incoterms (International Commercial Terms)
– Definition: A set of rules that define the responsibilities of sellers and buyers in international transactions.
– Importance: Familiarity with Incoterms helps in understanding shipping costs, risk management, and delivery obligations, which are critical when sourcing vending machines from international suppliers. -
Lead Time
– Definition: The time taken from the placement of an order until the delivery of the product.
– Importance: Understanding lead times is crucial for planning and inventory management, especially in fast-moving markets where demand can fluctuate rapidly.
By grasping these technical properties and trade terms, international B2B buyers can make more informed decisions regarding the placement and procurement of vending machines, ultimately enhancing their operational efficiency and profitability.
Navigating Market Dynamics, Sourcing Trends, and Sustainability in the best place to put a vending machine Sector
Market Overview & Key Trends
The vending machine sector is experiencing significant transformation driven by various global factors. The rise of urbanization and a growing demand for convenient food and beverage options are pivotal in shaping the market. In regions like Africa and South America, the increasing middle-class population is fueling demand for accessible consumer goods. Conversely, in Europe and the Middle East, the trend is leaning towards health-conscious and sustainable vending solutions.
Emerging technologies are also redefining the landscape. Smart vending machines, equipped with IoT capabilities, offer real-time inventory management and user interaction through mobile apps. This technology is particularly appealing to B2B buyers as it enhances operational efficiency and customer engagement. Additionally, the integration of cashless payment systems is becoming essential, especially in markets that prioritize hygiene and contactless transactions.
International B2B buyers should be aware of regional dynamics. In Turkey and Saudi Arabia, for instance, there is a strong emphasis on local sourcing and partnerships with local suppliers to navigate import regulations and cultural preferences. This approach not only fosters community relations but can also lead to cost efficiencies. Furthermore, understanding local competition and consumer preferences is crucial for positioning vending machines effectively within these diverse markets.
Sustainability & Ethical Sourcing in B2B
Sustainability is becoming a critical consideration in the vending machine sector. As environmental awareness grows, both consumers and businesses are increasingly prioritizing eco-friendly practices. For B2B buyers, this means sourcing vending machines that utilize sustainable materials and energy-efficient technologies. Options such as machines made from recycled materials or those that operate on renewable energy can significantly reduce the environmental footprint.
Moreover, the importance of ethical supply chains cannot be overstated. Buyers should seek vendors who prioritize fair labor practices and transparency in their sourcing processes. Certifications such as ISO 14001 for environmental management or Fair Trade for ethical sourcing can serve as benchmarks when evaluating potential suppliers. By aligning with manufacturers that adhere to these standards, companies not only enhance their brand reputation but also contribute positively to global sustainability efforts.
Incorporating green certifications into the vending machine selection process is essential. Machines that are compliant with environmental standards can help businesses meet regulatory requirements and appeal to a growing demographic of eco-conscious consumers. This trend is particularly relevant in European markets, where sustainability is often a decisive factor in consumer purchasing decisions.
Brief Evolution/History
The vending machine industry has evolved significantly since its inception in the late 19th century. Originally, these machines dispensed simple items like postcards and chewing gum. Over the decades, technological advancements have transformed them into sophisticated retail outlets capable of delivering a wide variety of products, including fresh foods and beverages.
The introduction of digital payment systems in the 2000s marked a pivotal moment, increasing convenience for consumers and broadening the appeal of vending machines in urban environments. More recently, the focus has shifted toward smart technology and sustainability, reflecting broader societal trends toward health, convenience, and environmental responsibility. As this sector continues to innovate, international B2B buyers must stay informed about these developments to make strategic sourcing decisions that align with market demands.
Related Video: ONESOURCE Global Trade: A Truly Global Solution
Frequently Asked Questions (FAQs) for B2B Buyers of best place to put a vending machine
-
What factors should I consider when selecting a location for a vending machine?
When choosing a location for a vending machine, prioritize high foot traffic areas such as office buildings, schools, hospitals, and shopping malls. Assess the demographics of the area to ensure the products offered will appeal to potential customers. Additionally, consider visibility, accessibility, and proximity to competitors. Conducting a site analysis can provide valuable insights into the best-performing locations. -
How can I vet suppliers for vending machines?
To vet suppliers, start by researching their reputation in the market. Look for reviews, testimonials, and case studies from other businesses. Request references and contact them to discuss their experiences. Additionally, verify the supplier’s certifications, financial stability, and warranty policies. Conducting site visits or audits can also help assess the quality of their products and operations. -
What customization options are available for vending machines?
Many suppliers offer customization options such as branding, product selection, and machine design. You can select specific product categories, like healthy snacks or beverages, to align with your target market’s preferences. Discuss your requirements with the supplier to explore options for digital displays, payment systems, and machine color schemes that enhance your brand visibility. -
What are the typical minimum order quantities (MOQ) and lead times for vending machines?
Minimum order quantities can vary significantly by supplier, with some requiring as few as one machine while others might have higher thresholds. Lead times typically range from 4 to 12 weeks, depending on customization and production schedules. Always confirm these details upfront to ensure they align with your operational timelines and business needs. -
What payment options are recommended for international transactions?
When sourcing vending machines internationally, consider using secure payment methods such as letters of credit, PayPal, or escrow services to mitigate risk. These methods provide a level of security for both parties, ensuring that payments are only released when terms are met. Discuss payment terms and conditions with the supplier to establish clear expectations. -
How can I ensure quality assurance for vending machines?
Request quality assurance certificates from your supplier, such as ISO 9001 or CE certifications, which demonstrate compliance with international standards. Establish a quality control process that includes inspections upon delivery and regular maintenance checks. Consider implementing a warranty or service agreement to address any potential issues promptly. -
What logistics considerations should I keep in mind when importing vending machines?
Consider the logistics of shipping, including freight forwarding, customs clearance, and insurance. Work with a reliable logistics partner who understands international shipping regulations and can handle documentation efficiently. Additionally, factor in costs related to shipping, tariffs, and taxes in your budget to avoid unexpected expenses. -
What should I do in case of disputes with suppliers?
Establish clear communication channels and documentation practices to prevent disputes. In the event of a disagreement, attempt to resolve the issue amicably through direct negotiation. If necessary, consider mediation or arbitration as alternatives to litigation, which can be costly and time-consuming. Ensure that your contracts include dispute resolution clauses to guide the process effectively.
Strategic Sourcing Conclusion and Outlook for best place to put a vending machine
In conclusion, identifying the optimal placement for vending machines is pivotal for maximizing their profitability and accessibility. Strategic sourcing not only involves selecting the right machine but also understanding consumer behavior and traffic patterns in various environments. Key takeaways include:
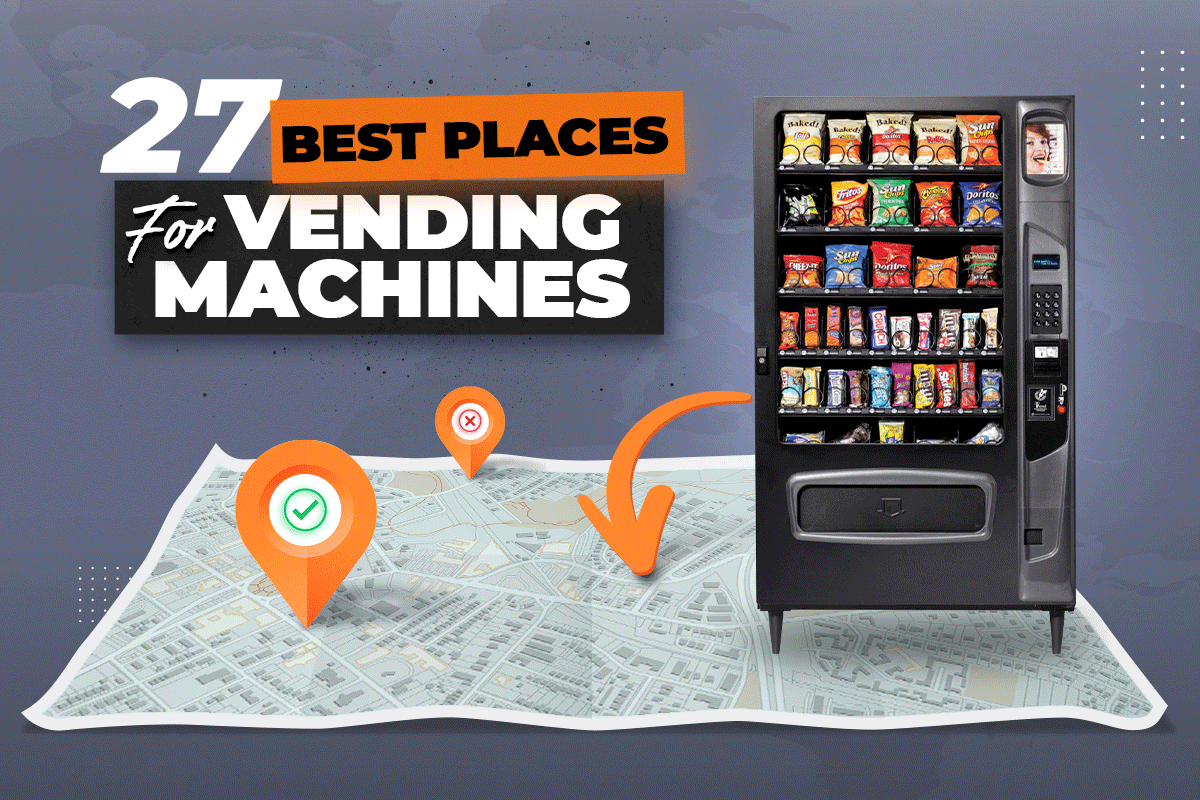
Illustrative Image (Source: Google Search)
- Target High Traffic Areas: Locations such as schools, hospitals, and corporate offices are prime spots that can yield consistent sales.
- Adapt to Local Preferences: Consider regional tastes and demands; for instance, offering healthy snacks may resonate more in urban areas with health-conscious populations.
- Leverage Data Analytics: Utilize foot traffic data and sales patterns to continually refine machine placement and product offerings.
As international B2B buyers from Africa, South America, the Middle East, and Europe explore opportunities in the vending industry, the importance of strategic sourcing cannot be overstated. By aligning placement strategies with local market dynamics, businesses can enhance their competitive edge.
Looking ahead, the vending machine landscape is evolving with technology and consumer preferences. Embrace this change by investing in innovative solutions and remain agile in your sourcing strategies. Join the movement towards smarter vending solutions that cater to diverse consumer needs and drive business success.