Master Sourcing Baseball Card Vending Machines for Maximum
Guide to Baseball Card Vending Machine
- Introduction: Navigating the Global Market for baseball card vending machine
- Understanding baseball card vending machine Types and Variations
- Key Industrial Applications of baseball card vending machine
- Strategic Material Selection Guide for baseball card vending machine
- In-depth Look: Manufacturing Processes and Quality Assurance for baseball card vending machine
- Comprehensive Cost and Pricing Analysis for baseball card vending machine Sourcing
- Spotlight on Potential baseball card vending machine Manufacturers and Suppliers
- Essential Technical Properties and Trade Terminology for baseball card vending machine
- Navigating Market Dynamics, Sourcing Trends, and Sustainability in the baseball card vending machine Sector
- Frequently Asked Questions (FAQs) for B2B Buyers of baseball card vending machine
- Strategic Sourcing Conclusion and Outlook for baseball card vending machine
Introduction: Navigating the Global Market for baseball card vending machine
In today’s rapidly evolving global market, the demand for baseball card vending machines has surged, driven by nostalgia, collectability, and the growing interest in sports memorabilia. These vending machines serve not only as a unique retail solution but also as a gateway to a lucrative niche market for businesses. For international B2B buyers, particularly from regions such as Africa, South America, the Middle East, and Europe, understanding the nuances of sourcing these machines is critical.
This comprehensive guide delves into the various aspects of baseball card vending machines, including the different types available, the materials used in their construction, manufacturing and quality control standards, and key suppliers in the market. By exploring these topics, buyers will gain insights into pricing structures and market trends that will empower them to make informed sourcing decisions.
Moreover, the guide addresses frequently asked questions, providing clarity on common concerns and enhancing the overall purchasing experience. Whether you are a retailer looking to diversify your offerings or an entrepreneur seeking new investment opportunities, this guide equips you with the essential knowledge to navigate the complexities of the baseball card vending machine market effectively. Embrace the potential of this unique product and unlock new avenues for growth and customer engagement in your business.
Understanding baseball card vending machine Types and Variations
Type Name | Key Distinguishing Features | Primary B2B Applications | Brief Pros & Cons for Buyers |
---|---|---|---|
Traditional Vending Machine | Mechanical operation, accepts coins, and bills | Retail stores, sports events | Pros: Low maintenance, familiar operation. Cons: Limited card selection, slower transactions. |
Digital Touchscreen Machine | Touchscreen interface, accepts cards and mobile payments | Shopping malls, conventions | Pros: Fast transactions, customizable displays. Cons: Higher initial cost, requires tech support. |
Mobile Vending Unit | Portable design, battery-operated | Outdoor events, pop-up shops | Pros: Flexibility in location, easy to transport. Cons: Limited capacity, may require frequent restocking. |
Specialty Card Machines | Focused on specific brands or types of cards | Collector fairs, niche markets | Pros: Targeted offerings attract enthusiasts. Cons: Limited audience, may not appeal to casual buyers. |
Hybrid Machines | Combines vending with online ordering options | E-commerce integration, specialty shops | Pros: Expands customer base, integrates with digital sales. Cons: Complex setup, higher operational costs. |
Traditional Vending Machine
Traditional vending machines are the most recognizable type, utilizing mechanical mechanisms to dispense baseball cards. These machines typically accept coins and bills, making them straightforward for users. They are ideal for retail environments and sports events where quick transactions are necessary. However, their limited card selection and slower transaction speeds can be drawbacks for businesses aiming to provide a more extensive range of products.
Digital Touchscreen Machine
Digital touchscreen machines represent the evolution of vending technology, offering an interactive interface that allows users to browse a wider selection of cards. These machines can accept various payment methods, including credit cards and mobile payments, making transactions faster and more convenient. They are particularly suitable for high-traffic areas like shopping malls and conventions. However, the higher initial investment and the need for technical support may deter some buyers.
Mobile Vending Unit
Mobile vending units are designed for portability, making them ideal for outdoor events and pop-up shops. These battery-operated machines can be easily transported and set up in various locations. Their flexibility allows businesses to reach customers in diverse settings. However, they typically have a smaller capacity for inventory, which may require more frequent restocking, potentially impacting profit margins.
Specialty Card Machines
Specialty card machines cater to specific brands or types of baseball cards, targeting niche markets and collectors. These machines can be found at collector fairs and events where enthusiasts seek particular items. Their focused offerings can attract dedicated customers, enhancing sales in specialized markets. However, the appeal may be limited to a smaller audience, which might not be ideal for businesses looking for broader customer engagement.
Hybrid Machines
Hybrid machines combine traditional vending with online ordering capabilities, allowing customers to order cards for pickup or delivery. This innovative approach can significantly expand a business’s customer base, integrating with e-commerce platforms to enhance sales opportunities. While hybrid machines offer unique advantages, such as increased market reach, they also come with higher operational costs and a more complex setup, which buyers must consider carefully.
Related Video: DIY Card Vending Machine – Easy Cardboard Craft
Key Industrial Applications of baseball card vending machine
Industry/Sector | Specific Application of baseball card vending machine | Value/Benefit for the Business | Key Sourcing Considerations for this Application |
---|---|---|---|
Retail | In-store sales of collectible baseball cards | Increases foot traffic and impulse purchases | Quality of cards, machine durability, payment options |
Events and Conventions | Mobile vending at sports events and conventions | Enhances attendee experience and generates additional revenue | Size and portability of machine, card selection, branding |
Educational Institutions | Fundraising opportunities through card sales | Engages students and alumni while raising funds | Customization options, ease of operation, maintenance support |
Online Retail | Integration with e-commerce platforms for card sales | Expands market reach and provides convenience for buyers | Compatibility with online systems, secure payment processing |
Gaming and Entertainment | Vending in arcades or gaming centers | Attracts collectors and enhances the gaming experience | Machine aesthetics, card variety, customer support |
Detailed Applications
Retail: Baseball card vending machines can be strategically placed in retail environments, such as sports shops or general merchandise stores, to drive impulse purchases. By offering a range of collectible cards, businesses can attract foot traffic and encourage customers to spend more time in-store. For international buyers, especially in regions like Africa and South America, understanding local demand for specific sports or players can enhance sales strategies. Key considerations include the quality of the cards offered and the durability of the vending machine, as well as the availability of multiple payment options.
Events and Conventions: At sports events and conventions, baseball card vending machines serve as a unique attraction, allowing fans to purchase cards in a convenient manner. This not only provides attendees with memorabilia but also generates additional revenue for event organizers. Buyers from the Middle East and Europe should focus on the machine’s portability and size, ensuring it can be easily transported and set up at various venues. Additionally, the selection of cards should resonate with the event’s audience to maximize sales.
Educational Institutions: Schools and universities can leverage baseball card vending machines as a fundraising tool. By selling collectible cards featuring notable alumni or historical sports figures, institutions can engage students and alumni while raising funds for various programs. International buyers in regions like Spain and Nigeria should consider customization options that reflect local sports culture and the ease of operation for non-technical staff. Maintenance support is also crucial to ensure uninterrupted service during fundraising events.
Online Retail: Integrating baseball card vending machines with e-commerce platforms can significantly expand a business’s market reach. This setup allows customers to purchase cards online and pick them up at a nearby vending machine, combining the convenience of online shopping with the thrill of vending. For buyers in Europe and South America, compatibility with various online systems and secure payment processing are essential factors to consider when sourcing these machines.
Gaming and Entertainment: Placing baseball card vending machines in arcades or gaming centers can enhance the overall entertainment experience for visitors. These machines attract collectors and casual fans alike, creating a vibrant atmosphere. Buyers should focus on the aesthetics of the machine to ensure it complements the gaming environment, as well as the variety of cards offered to appeal to different demographics. Customer support for machine operation and card restocking is also a key consideration for sustained success in this sector.
Related Video: How to use an OMNY card vending machine
Strategic Material Selection Guide for baseball card vending machine
Analysis of Common Materials for Baseball Card Vending Machines
When selecting materials for baseball card vending machines, it is essential to consider properties that influence performance, durability, and cost-effectiveness. Below is an analysis of four common materials used in the construction of these machines.
1. Stainless Steel
Key Properties:
Stainless steel is known for its excellent corrosion resistance, strength, and durability. It can withstand a wide range of temperatures and pressures, making it suitable for various environments.
Pros & Cons:
The primary advantage of stainless steel is its resistance to rust and corrosion, which is critical in humid or wet conditions. It is also easy to clean and maintain, ensuring a longer lifespan. However, stainless steel can be more expensive than other materials and may require specialized manufacturing processes, increasing overall costs.
Impact on Application:
Stainless steel is ideal for exterior components of vending machines that are exposed to the elements. Its compatibility with various media types, including food products, makes it a safe choice.
Considerations for International Buyers:
Buyers in regions like Africa and the Middle East should ensure compliance with local standards for food safety and corrosion resistance. Certifications such as ASTM and EN standards may be relevant.
2. Acrylic Plastic
Key Properties:
Acrylic is a lightweight, shatter-resistant material with good optical clarity. It is less rigid than glass but offers better impact resistance.
Pros & Cons:
Acrylic is cost-effective and easy to fabricate, which can reduce manufacturing complexity. However, it can scratch easily and may not be suitable for high-traffic areas where durability is paramount. Its lower thermal resistance also limits its use in high-temperature environments.
Impact on Application:
Acrylic is often used for display windows in vending machines, allowing customers to view the products inside. Its transparency enhances the visual appeal of the machine.
Considerations for International Buyers:
Buyers should consider the UV resistance of acrylic, especially in regions with high sun exposure, such as parts of Africa and South America. Compliance with local regulations regarding plastic materials is also crucial.
3. Carbon Steel
Key Properties:
Carbon steel is known for its high strength and toughness. It is relatively inexpensive and can be treated to enhance its corrosion resistance.
Pros & Cons:
The main advantage of carbon steel is its cost-effectiveness and structural integrity, making it suitable for internal components of vending machines. However, it is susceptible to rust if not properly coated or maintained, which can limit its lifespan in outdoor applications.
Impact on Application:
Carbon steel is typically used for structural components and internal frames of vending machines. It is compatible with various mechanical components and can support heavy loads.
Considerations for International Buyers:
Buyers should be aware of the need for protective coatings to prevent corrosion, especially in humid climates. Compliance with standards such as JIS for mechanical properties may be necessary.
4. Aluminum
Key Properties:
Aluminum is lightweight, corrosion-resistant, and has good thermal conductivity. It is also easy to machine and weld.
Pros & Cons:
The lightweight nature of aluminum makes it ideal for portable vending machines. Its corrosion resistance is beneficial in outdoor applications. However, it is generally less strong than steel and can be more expensive depending on the alloy used.
Impact on Application:
Aluminum is often used for frames and casings of vending machines, providing a good balance between weight and durability. It is suitable for various environmental conditions, making it versatile.
Considerations for International Buyers:
International buyers should consider the specific aluminum grade for their application to ensure it meets local standards. Compliance with environmental regulations regarding aluminum recycling may also be relevant.
Summary Table
Material | Typical Use Case for baseball card vending machine | Key Advantage | Key Disadvantage/Limitation | Relative Cost (Low/Med/High) |
---|---|---|---|---|
Stainless Steel | Exterior components exposed to elements | Excellent corrosion resistance | Higher cost and manufacturing complexity | High |
Acrylic Plastic | Display windows for product visibility | Cost-effective and easy to fabricate | Scratches easily and lower thermal resistance | Medium |
Carbon Steel | Structural components and internal frames | Cost-effective and high strength | Susceptible to rust without protection | Low |
Aluminum | Frames and casings for lightweight designs | Lightweight and corrosion-resistant | Generally less strong than steel | Medium |
This guide provides a comprehensive overview of material options for baseball card vending machines, helping international B2B buyers make informed decisions based on regional needs and compliance requirements.
In-depth Look: Manufacturing Processes and Quality Assurance for baseball card vending machine
The manufacturing process for baseball card vending machines involves several key stages, each critical to ensuring the final product meets quality and functionality standards. Below is a comprehensive overview of the typical manufacturing processes and quality assurance practices relevant to international B2B buyers.
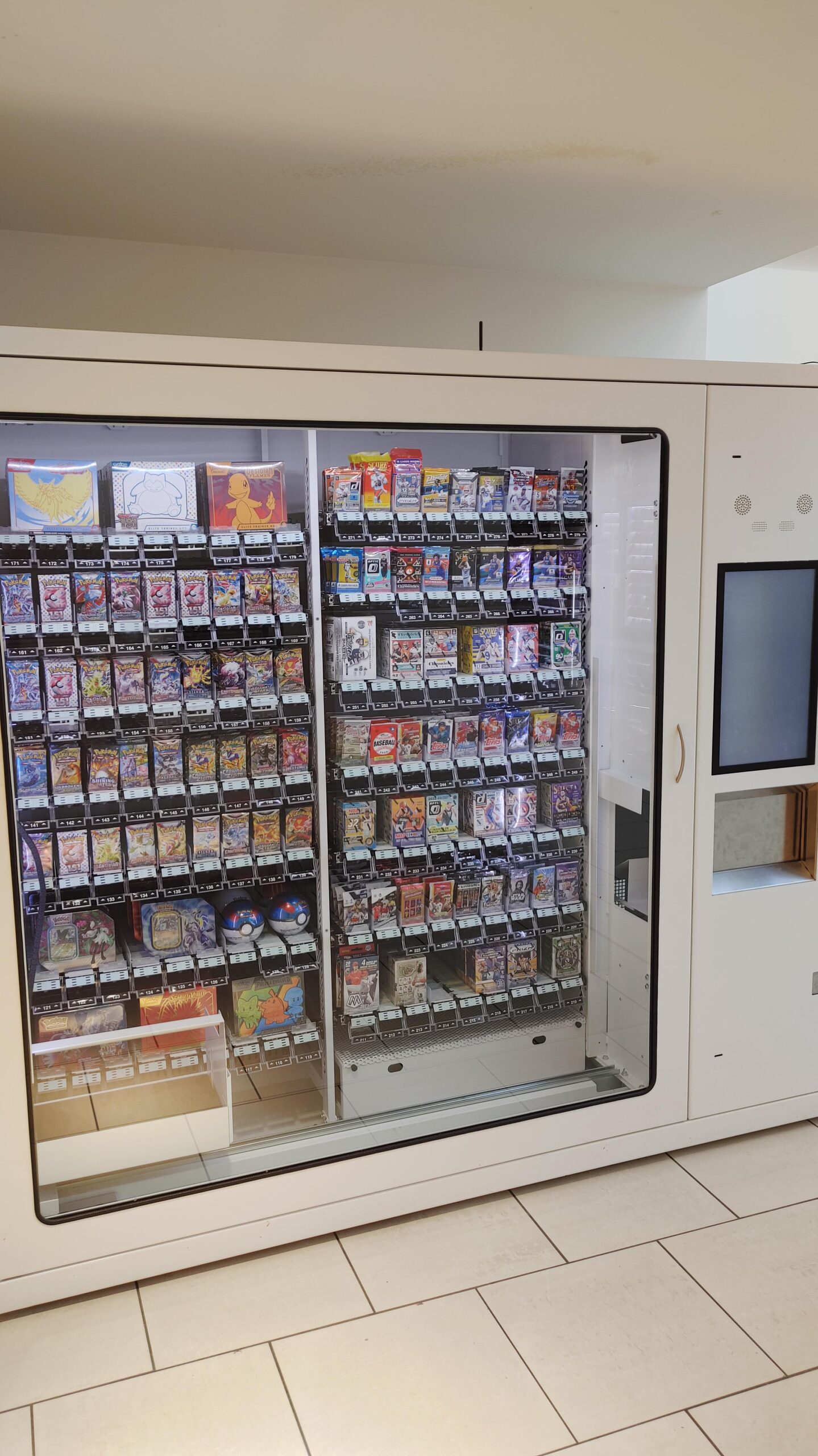
Illustrative Image (Source: Google Search)
Manufacturing Processes
1. Material Preparation
The first stage in the manufacturing process involves the selection and preparation of materials. Common materials used include:
- Metal Components: Steel or aluminum for the machine frame and casing, chosen for their durability and strength.
- Plastics: High-quality polymers for the internal mechanisms and display components.
- Electronic Parts: Circuit boards, sensors, and payment processing modules.
Before production begins, materials undergo rigorous inspections to ensure they meet specified standards. This includes checking for defects, dimensions, and compliance with international material safety standards.
2. Forming
The forming process includes several techniques used to shape materials into the desired components of the vending machine:
- Cutting: Metal sheets are cut into specified dimensions using laser cutting or CNC machines, ensuring precision.
- Bending: Metal parts are bent to form the casing and internal structure, often using hydraulic presses.
- Molding: Plastic components are produced through injection molding, allowing for complex shapes and features that are essential for the machine’s operation.
3. Assembly
Assembly is a critical stage where all components come together. Key steps include:
- Sub-assembly: Individual components like the coin mechanism, card dispenser, and electronic systems are assembled separately.
- Main Assembly: Sub-assemblies are integrated into the main vending machine structure. This involves securing components and connecting electrical wiring.
- Integration Testing: After assembly, systems are tested to ensure they function correctly together. This includes checking the card dispensing mechanism, payment acceptance, and user interface.
4. Finishing
The finishing stage enhances both the aesthetic and functional aspects of the vending machine:
- Surface Treatment: Metal parts may undergo powder coating or painting to improve appearance and corrosion resistance.
- Quality Control Check: Each machine is inspected for visual defects, alignment issues, and operational functionality.
- Packaging: Finally, the completed machines are carefully packaged to prevent damage during transportation.
Quality Assurance
Quality assurance (QA) is a vital aspect of the manufacturing process, ensuring that the final product adheres to international standards and customer specifications.
International Standards
For international B2B buyers, understanding relevant quality standards is crucial:
- ISO 9001: This standard focuses on quality management systems, ensuring consistent product quality and continuous improvement.
- CE Marking: Required for products sold in the European Economic Area, indicating compliance with health, safety, and environmental protection standards.
- API Standards: Relevant for electronic components, ensuring they meet specific performance and reliability criteria.
Quality Control Checkpoints
Quality control involves multiple checkpoints throughout the manufacturing process:
- Incoming Quality Control (IQC): This initial inspection checks raw materials and components against specifications before they enter production.
- In-Process Quality Control (IPQC): Ongoing inspections during the manufacturing stages ensure that processes are correctly followed and products are built to specification.
- Final Quality Control (FQC): Before shipping, each vending machine undergoes a comprehensive final inspection to verify that all functions operate correctly and meet quality standards.
Common Testing Methods
Several testing methods are employed to verify the quality and functionality of the vending machines:
- Functional Testing: Ensures that all components operate as intended, including card dispensing and payment processing.
- Durability Testing: Simulates real-world usage to assess the machine’s resilience and longevity.
- Electrical Safety Testing: Verifies that electronic components meet safety standards, protecting against electrical faults.
Verification of Supplier Quality Control
For B2B buyers, especially those from Africa, South America, the Middle East, and Europe, verifying supplier quality control practices is essential:
- Supplier Audits: Conducting on-site audits allows buyers to evaluate manufacturing processes, quality control systems, and compliance with international standards.
- Quality Reports: Requesting documentation of quality control processes, including IQC, IPQC, and FQC results, can provide insights into the supplier’s commitment to quality.
- Third-Party Inspections: Engaging third-party inspection agencies can offer an unbiased assessment of the supplier’s quality practices and product quality before shipment.
QC and Certification Nuances for International Buyers
When purchasing from international suppliers, buyers should be aware of certain nuances:
- Certification Recognition: Ensure that the supplier’s certifications are recognized in your region. For example, CE marking is crucial for products entering European markets but may not be recognized in other regions.
- Cultural and Regulatory Differences: Different regions may have varying expectations regarding quality and compliance. Understanding these nuances can help in evaluating supplier capabilities effectively.
- Communication and Support: Establishing clear communication channels with suppliers can facilitate understanding of quality expectations and timely resolution of any issues that arise.
In conclusion, a thorough understanding of manufacturing processes and quality assurance practices is essential for international B2B buyers of baseball card vending machines. By focusing on quality at every stage of production and verifying suppliers’ capabilities, buyers can ensure they receive high-quality, reliable products that meet their needs.
Related Video: SMART Quality Control for Manufacturing
Comprehensive Cost and Pricing Analysis for baseball card vending machine Sourcing
Understanding the cost structure and pricing dynamics of baseball card vending machines is crucial for international B2B buyers, especially those from diverse markets like Africa, South America, the Middle East, and Europe. This analysis will provide actionable insights to optimize sourcing strategies.
Cost Components
-
Materials: The primary materials include metal for the casing, plastic for the dispensers, and electronic components for payment processing and vending mechanisms. Sourcing materials from local suppliers can reduce costs, but high-quality materials ensure durability and reliability, which are crucial for customer satisfaction.
-
Labor: Labor costs vary significantly by region. In countries like Nigeria and some South American nations, labor may be cheaper, potentially reducing overall manufacturing costs. However, skilled labor is essential for quality assembly, which can influence long-term reliability and maintenance costs.
-
Manufacturing Overhead: This includes costs related to factory utilities, equipment maintenance, and administrative expenses. Efficient production processes can help minimize overhead costs, which is particularly important when scaling production.
-
Tooling: Tooling costs involve the initial investment in molds and machinery necessary for production. These costs can be amortized over larger production runs, so negotiating for higher minimum order quantities (MOQs) can lead to lower unit costs.
-
Quality Control (QC): Implementing robust QC processes ensures that each machine meets safety and operational standards. While this may incur additional costs, it significantly reduces the risk of defects and subsequent warranty claims.
-
Logistics: Shipping and handling costs should be factored into the total cost of ownership. The choice of Incoterms can influence these costs; for instance, opting for DDP (Delivered Duty Paid) can simplify logistics for buyers unfamiliar with customs processes.
-
Margin: Supplier margins can vary based on market conditions and the relationship between the buyer and supplier. Understanding the typical margin in your target region can aid in negotiation.
Price Influencers
-
Volume/MOQ: Larger orders often result in reduced prices per unit due to economies of scale. Buyers should assess their demand forecasts to negotiate favorable pricing on larger orders.
-
Specifications/Customization: Custom features may increase costs. Buyers should clearly outline requirements to avoid unexpected charges.
-
Materials: The choice of materials impacts both cost and quality. Premium materials may lead to higher upfront costs but can enhance machine longevity and reduce maintenance needs.
-
Quality/Certifications: Machines that meet specific international standards (such as CE or ISO certifications) may carry a premium. However, these certifications can also facilitate easier entry into regulated markets.
-
Supplier Factors: Established suppliers with a track record of reliability may command higher prices. However, their proven quality can justify the investment, particularly in competitive markets.
-
Incoterms: Understanding the implications of different Incoterms can lead to significant savings. For instance, FOB (Free on Board) may be more cost-effective if the buyer has established logistics capabilities.
Buyer Tips
-
Negotiation: Leverage volume discounts and long-term partnerships to negotiate better terms. Building a strong relationship with suppliers can lead to more favorable pricing and terms.
-
Cost-Efficiency: Focus on the Total Cost of Ownership (TCO), which includes not just the purchase price but also maintenance, operational costs, and potential downtime.
-
Pricing Nuances: Be aware that currency fluctuations can impact pricing in international transactions. Locking in prices through contracts can mitigate this risk.
-
Market Research: Conducting thorough market research specific to regions like Spain or Nigeria can provide insights into local pricing trends and help identify competitive suppliers.
In conclusion, understanding the intricate cost structure and pricing dynamics associated with sourcing baseball card vending machines is essential for international B2B buyers. By considering these factors, buyers can make informed decisions that enhance their procurement strategies. Always consult with suppliers for the most accurate and up-to-date pricing information, as these figures can fluctuate based on market conditions and supplier capabilities.
Spotlight on Potential baseball card vending machine Manufacturers and Suppliers
This section offers a look at a few manufacturers active in the ‘baseball card vending machine’ market. This is a representative sample for illustrative purposes; B2B buyers must conduct their own extensive due diligence before any engagement. Information is synthesized from public sources and general industry knowledge.
Essential Technical Properties and Trade Terminology for baseball card vending machine
When considering the procurement of baseball card vending machines, it’s essential for international B2B buyers to understand the technical properties and industry-specific terminology that will influence their purchasing decisions. Here’s a comprehensive overview.
Critical Technical Properties
-
Material Grade
The quality of materials used in vending machines, such as stainless steel or high-grade plastics, is crucial for durability and longevity. A higher material grade often translates to better resistance against wear and tear, particularly in high-traffic environments. For B2B buyers, this means reduced maintenance costs and longer service life, enhancing return on investment (ROI). -
Machine Tolerance
Tolerance refers to the permissible limit of variation in a physical dimension. In vending machines, this affects how well components fit together, which is critical for operational efficiency. Accurate tolerances ensure that cards are dispensed correctly and that the machine operates smoothly. Buyers should prioritize machines with tight tolerances to minimize jams and service interruptions. -
Power Consumption
Understanding the power requirements of the vending machine is essential, especially for buyers in regions with limited electricity access. Machines with lower power consumption not only reduce operational costs but also extend the machine’s usability in areas with unstable power supply. This can be a deciding factor for buyers in developing markets. -
Payment System Compatibility
The ability of a vending machine to accept various payment methods (cash, credit/debit cards, mobile payments) can significantly impact its marketability. B2B buyers should assess the payment systems that the machine supports to ensure it meets the preferences of their target customer base. Flexibility in payment options can lead to increased sales and customer satisfaction. -
Capacity and Size
The storage capacity for cards and the physical dimensions of the vending machine are critical factors. A larger capacity can support higher sales volumes, while compact designs may be necessary for locations with limited space. Buyers must evaluate their specific needs based on expected foot traffic and sales volume to select the appropriate machine size. -
User Interface Design
A user-friendly interface can enhance customer experience, which is vital for driving sales. Features such as touchscreen displays, clear instructions, and multilingual options can cater to a diverse customer base. Buyers should consider machines that offer intuitive interfaces to reduce user frustration and increase transaction speed.
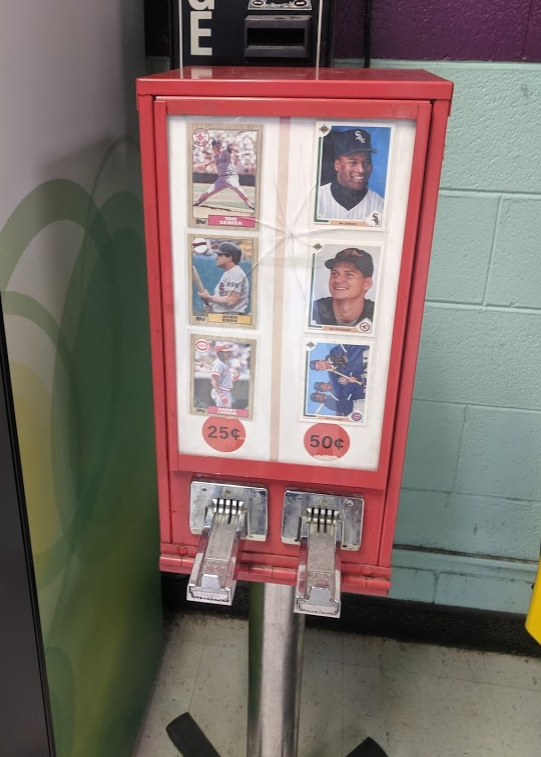
Illustrative Image (Source: Google Search)
Common Trade Terminology
-
OEM (Original Equipment Manufacturer)
Refers to companies that produce parts and equipment that may be marketed by another manufacturer. For B2B buyers, partnering with OEMs can ensure high-quality components and reliability in vending machine operations. -
MOQ (Minimum Order Quantity)
This is the smallest quantity of a product that a supplier is willing to sell. Understanding the MOQ is crucial for buyers, as it can affect initial purchasing costs and inventory management. Buyers should negotiate favorable MOQs based on their market needs. -
RFQ (Request for Quotation)
An RFQ is a document used to solicit price quotes from suppliers for specific products or services. It is a vital step in the procurement process, allowing buyers to compare offers and select the best value for their investment. -
Incoterms (International Commercial Terms)
These are standardized terms that define the responsibilities of buyers and sellers in international transactions. Knowledge of Incoterms is essential for B2B buyers as they outline who is responsible for shipping, insurance, and tariffs, thereby reducing the risk of misunderstandings. -
Lead Time
This term refers to the time it takes from placing an order to receiving the product. Understanding lead times is crucial for inventory planning and ensuring that vending machines are available to meet customer demand. -
Warranty
A warranty is a promise from the manufacturer regarding the condition of the product and the terms of repair or replacement. For B2B buyers, a robust warranty can provide peace of mind and protect against unexpected costs associated with machine failure.
By familiarizing themselves with these technical specifications and trade terminologies, international B2B buyers can make informed decisions that align with their operational needs and market demands.
Navigating Market Dynamics, Sourcing Trends, and Sustainability in the baseball card vending machine Sector
Market Overview & Key Trends
The baseball card vending machine sector is experiencing a notable transformation driven by several global trends. One key driver is the resurgence of interest in collectible cards, fueled by social media and online marketplaces that have made trading and collecting more accessible. This has led to an increase in demand for vending machines that can dispense a variety of cards, particularly in markets across Africa, South America, the Middle East, and Europe. Notably, countries like Nigeria and Spain are witnessing a growing interest in collectibles, which presents a lucrative opportunity for B2B buyers.
Emerging technologies such as mobile payment systems, RFID tagging, and AI-driven inventory management are shaping the future of vending machines. These innovations enhance user experience by providing seamless transactions and personalized offerings. B2B buyers should prioritize suppliers that integrate these technologies, as they can significantly boost sales and customer satisfaction.
Market dynamics are also influenced by consumer behavior shifts towards convenience and instant gratification. Vending machines that offer a broad range of products, including rare or limited-edition cards, cater to this trend. Furthermore, the rise of eco-conscious consumers is compelling manufacturers to consider sustainability in their product offerings, from machine design to packaging.
Sustainability & Ethical Sourcing in B2B
Sustainability is increasingly critical in the baseball card vending machine sector, particularly for international B2B buyers. The environmental impact of manufacturing and distributing vending machines can be significant, necessitating a focus on sustainable practices. Buyers should seek suppliers who utilize eco-friendly materials and production methods, such as recycled plastics and energy-efficient manufacturing processes.
Ethical sourcing is equally important. Ensuring that the supply chain adheres to fair labor practices and environmentally responsible methods is essential for maintaining a positive brand image. Buyers should inquire about certifications such as ISO 14001 (Environmental Management) and FSC (Forest Stewardship Council) for materials used in vending machines. These certifications not only enhance credibility but also resonate with a growing base of environmentally conscious consumers.
Moreover, integrating sustainability into the marketing strategy can differentiate a brand in a crowded marketplace. Buyers should consider how sustainability initiatives can be highlighted in their offerings, potentially increasing customer loyalty and opening doors to new markets.
Brief Evolution/History
The concept of vending machines dates back to the late 19th century, originally dispensing items such as postcards and chewing gum. However, the introduction of baseball card vending machines in the 1980s marked a significant evolution in the collectibles market. These machines provided a novel way for fans to access baseball cards and contributed to the burgeoning hobbyist culture.
Over the years, advancements in technology have transformed these machines from simple coin-operated devices to sophisticated units equipped with digital screens and cashless payment options. The recent digitalization of the collectibles market, coupled with the nostalgia surrounding baseball cards, has revitalized interest and demand for these vending machines, making them a staple in sports venues, retail locations, and events globally. For B2B buyers, understanding this evolution is key to capitalizing on the current market trends and consumer preferences.
Related Video: Can India-US Secure Trade Deal Soon? | Trump Tariffs War | Global Trade War | US News | News18
Frequently Asked Questions (FAQs) for B2B Buyers of baseball card vending machine
-
What should I look for when vetting suppliers of baseball card vending machines?
When vetting suppliers, prioritize their reputation, experience, and customer reviews. Verify their business credentials and check for certifications relevant to your region. Request references from previous clients and assess their responsiveness to inquiries. Additionally, evaluate their production capabilities to ensure they can meet your specific needs, including any customization requirements. -
Can I customize the baseball card vending machines to fit my business needs?
Yes, many suppliers offer customization options for baseball card vending machines. You can often request specific designs, branding elements, or features that align with your market. Discuss your customization needs with potential suppliers to understand their capabilities and any additional costs involved. Ensure that the customization aligns with the machine’s functionality and user experience. -
What are the typical minimum order quantities (MOQs) and lead times for baseball card vending machines?
Minimum order quantities vary by supplier but typically range from 5 to 20 units. Lead times can also vary, often ranging from 4 to 12 weeks depending on the supplier’s production schedule and customization requests. It’s advisable to discuss these factors upfront to avoid any surprises and to plan your inventory accordingly. -
What payment terms are common when sourcing from international suppliers?
Common payment terms include a deposit (often 30-50%) upfront, with the balance due before shipment. Some suppliers may offer payment via letters of credit, especially for larger orders. Always clarify payment terms and methods accepted, such as bank transfers or payment platforms, and consider using escrow services for added security in international transactions. -
How can I ensure quality assurance and certifications for the vending machines?
Request quality assurance documents and product certifications from the supplier, such as ISO certifications or compliance with local safety standards. Conduct a factory audit if possible, or request samples for testing before placing a full order. This will help ensure the machines meet your quality expectations and local regulations.
-
What logistics considerations should I keep in mind for shipping vending machines internationally?
Consider shipping methods, costs, and timelines when planning logistics. Work with suppliers that have experience in international shipping to ensure proper handling and documentation. Factor in customs duties and taxes that may apply in your country. It’s also prudent to discuss insurance options for the shipment to protect against potential damages during transit. -
How can I handle disputes with suppliers if issues arise?
Establish clear communication channels and formal agreements outlining the terms of the purchase, including dispute resolution processes. If issues arise, address them promptly and professionally. Many suppliers may be willing to negotiate solutions. If necessary, consider mediation or arbitration as a means to resolve disputes without resorting to legal action. -
What support can I expect after purchasing the vending machines?
Inquire about the level of after-sales support offered by the supplier, including warranty terms, maintenance services, and technical support. Many reputable suppliers provide training for your staff on machine operation and troubleshooting. Ensure you have access to spare parts and support contacts to minimize downtime in case of machine issues.
Strategic Sourcing Conclusion and Outlook for baseball card vending machine
Strategic sourcing plays a pivotal role in maximizing the profitability and efficiency of baseball card vending machines. As international B2B buyers, particularly from regions such as Africa, South America, the Middle East, and Europe, understanding the dynamics of sourcing can significantly enhance your competitive edge. Key takeaways include the importance of selecting reliable suppliers who can provide quality cards and machines that meet regional demands. Additionally, leveraging local partnerships can streamline logistics and reduce costs, ultimately leading to improved customer satisfaction.
Investing in advanced vending technology that allows for cashless transactions and inventory tracking will not only attract a broader customer base but also facilitate better stock management. As the market evolves, staying ahead of trends—such as the increasing popularity of collectibles and online trading—will be essential for sustained growth.
Looking ahead, now is the time to act. Engage with suppliers who offer innovative solutions and flexible terms tailored to your market needs. By prioritizing strategic sourcing, you can position your business for success in the burgeoning collectibles industry. Embrace this opportunity to enhance your operations and capitalize on the growing demand for baseball card vending machines.