Your Ultimate Guide to Sourcing Walmart Vending Machine
Guide to Walmart Vending Machine
- Introduction: Navigating the Global Market for walmart vending machine
- Understanding walmart vending machine Types and Variations
- Key Industrial Applications of walmart vending machine
- Strategic Material Selection Guide for walmart vending machine
- In-depth Look: Manufacturing Processes and Quality Assurance for walmart vending machine
- Comprehensive Cost and Pricing Analysis for walmart vending machine Sourcing
- Spotlight on Potential walmart vending machine Manufacturers and Suppliers
- Essential Technical Properties and Trade Terminology for walmart vending machine
- Navigating Market Dynamics, Sourcing Trends, and Sustainability in the walmart vending machine Sector
- Frequently Asked Questions (FAQs) for B2B Buyers of walmart vending machine
- Strategic Sourcing Conclusion and Outlook for walmart vending machine
Introduction: Navigating the Global Market for walmart vending machine
In today’s fast-paced global market, the demand for innovative retail solutions is surging, and Walmart vending machines stand out as a transformative option for businesses across various sectors. These machines not only enhance customer engagement by providing 24/7 access to products but also streamline operational efficiencies, making them an attractive investment for B2B buyers in regions such as Africa, South America, the Middle East, and Europe.
This comprehensive guide is designed to empower international buyers with critical insights into Walmart vending machines, covering a wide array of topics. Buyers will explore the different types of vending machines available, the materials used in their construction, and the manufacturing and quality control processes that ensure reliability and performance. Additionally, we delve into supplier options, cost considerations, and the broader market trends shaping the vending machine landscape.
Through a detailed FAQ section, this guide aims to address common queries and concerns, providing clarity to facilitate informed sourcing decisions. By leveraging the insights contained within, B2B buyers can confidently navigate the complexities of the vending machine market, identify suitable suppliers, and ultimately enhance their service offerings. Whether you are looking to expand your product distribution channels or improve customer experience, understanding the intricacies of Walmart vending machines is essential for driving growth and success in your business.
Understanding walmart vending machine Types and Variations
Type Name | Key Distinguishing Features | Primary B2B Applications | Brief Pros & Cons for Buyers |
---|---|---|---|
Snack Vending Machines | Typically stock snacks, beverages, and candies | Office break rooms, schools, gyms | Pros: Easy to maintain; Cons: Limited product variety |
Healthy Food Vending Machines | Focus on nutritious options like salads and wraps | Corporate wellness programs, gyms | Pros: Attract health-conscious consumers; Cons: Higher cost |
Technology Vending Machines | Offer tech products like chargers and headphones | Airports, universities, tech hubs | Pros: High demand for convenience; Cons: Higher theft risk |
Customized Vending Machines | Tailored to specific needs, stocking unique items | Events, conferences, specialty shops | Pros: Unique selling proposition; Cons: Longer lead times |
Combo Vending Machines | Combine snacks and beverages in one unit | Retail stores, convenience stores | Pros: Maximizes space efficiency; Cons: Potential for clutter |
Snack Vending Machines
Snack vending machines are designed to provide a variety of snacks, beverages, and candies. They are commonly found in office break rooms, schools, and gyms, making them an essential addition to any location where people seek quick refreshments. When purchasing, B2B buyers should consider factors such as machine size, payment options, and product selection. While they are easy to maintain, buyers should be aware of the limited product variety, which might not cater to all consumer preferences.
Healthy Food Vending Machines
These machines prioritize nutritious food options, such as salads, wraps, and healthy snacks, appealing to health-conscious consumers. They are particularly suitable for corporate wellness programs and gyms, where the demand for healthier choices is growing. B2B buyers should evaluate the machine’s refrigeration capabilities and product sourcing options. Although they attract a specific demographic, the higher costs associated with stocking fresh and healthy items can be a drawback for some businesses.
Technology Vending Machines
Technology vending machines cater to tech-savvy consumers by offering essential gadgets like chargers, headphones, and other electronics. They are ideal for high-traffic areas such as airports, universities, and tech hubs where convenience is paramount. Buyers should assess the machine’s ability to handle various products and payment methods. While there is a strong demand for such machines, the higher risk of theft and damage may pose challenges for B2B buyers.
Customized Vending Machines
Customized vending machines are tailored to meet specific needs and can stock unique items that are not typically found in standard machines. They are well-suited for events, conferences, and specialty shops looking to offer a distinctive experience. B2B buyers should consider customization options and the potential for longer lead times when ordering. While these machines provide a unique selling proposition, they may require more investment and planning.
Combo Vending Machines
Combo vending machines combine snacks and beverages into a single unit, maximizing space efficiency. They are commonly used in retail stores and convenience shops where space is limited. Buyers should evaluate the balance of snack and beverage offerings to meet consumer demand. While combo machines are versatile, they can sometimes lead to clutter and confusion for users, which is a consideration for B2B buyers aiming for a streamlined experience.
Related Video: Machine Learning in 2024 – Beginner’s Course
Key Industrial Applications of walmart vending machine
Industry/Sector | Specific Application of walmart vending machine | Value/Benefit for the Business | Key Sourcing Considerations for this Application |
---|---|---|---|
Healthcare | Dispensing medical supplies and personal protective equipment | Immediate access to essential items, reduced downtime | Compliance with health regulations, temperature control capabilities |
Education | Providing snacks and beverages in schools and universities | Enhances student satisfaction, encourages healthy eating | Variety of products, payment options, durability for high traffic |
Manufacturing | Offering tools and spare parts in factories | Minimizes equipment downtime, boosts productivity | Customizable inventory, robust construction for industrial environments |
Hospitality | Serving quick snacks and beverages in hotels and resorts | Improves guest experience, increases ancillary revenue | Product selection, branding opportunities, compact design |
Corporate Offices | Supplying refreshments in office break rooms | Enhances employee morale, supports workplace culture | Energy-efficient options, diverse product range, smart technology integration |
Healthcare Applications
In healthcare settings, Walmart vending machines can be utilized to dispense medical supplies, such as bandages, gloves, and personal protective equipment (PPE). This ensures immediate access to essential items, which is critical in emergency situations and helps reduce downtime in patient care. For international buyers, particularly in regions like Africa and the Middle East, compliance with health regulations and temperature control capabilities are vital considerations when sourcing these machines.
Education Applications
Walmart vending machines can serve as convenient snack and beverage outlets in schools and universities. By providing healthier food options, these machines enhance student satisfaction and promote better eating habits among young people. For buyers from South America and Europe, it is important to consider the variety of products offered, payment options available, and the machine’s durability to withstand high traffic in educational institutions.
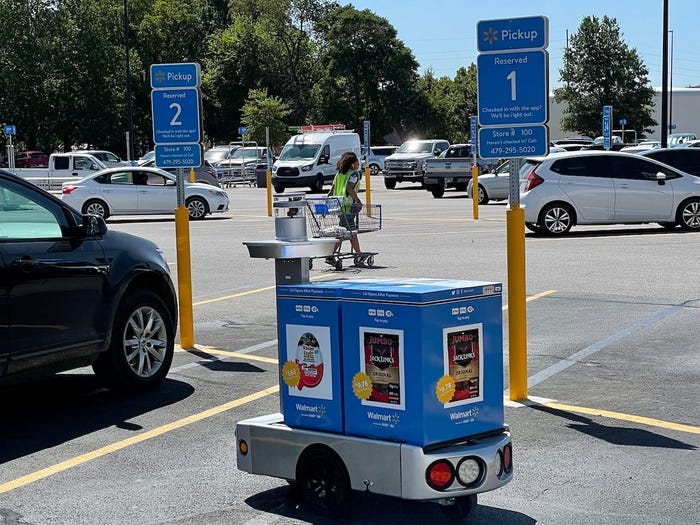
Illustrative Image (Source: Google Search)
Manufacturing Applications
In manufacturing environments, Walmart vending machines can be deployed to provide tools and spare parts directly on the shop floor. This application minimizes equipment downtime by ensuring that workers have immediate access to necessary items, which can significantly boost productivity. Buyers from various regions should focus on customizable inventory options and robust construction to withstand the demands of industrial settings when sourcing these machines.
Hospitality Applications
Walmart vending machines can enhance guest experience in hotels and resorts by offering quick access to snacks and beverages. This not only improves guest satisfaction but also provides an additional revenue stream for hospitality businesses. For international buyers, factors such as product selection, branding opportunities, and the machine’s compact design for limited space environments are crucial when considering these vending solutions.
Corporate Office Applications
In corporate office settings, Walmart vending machines can supply refreshments in break rooms, thereby enhancing employee morale and fostering a positive workplace culture. A diverse product range that includes healthy snacks and beverages can cater to various employee preferences. Buyers, particularly in Europe and the Middle East, should prioritize energy-efficient options and smart technology integration to optimize the vending machine’s functionality and user experience.
Related Video: How to Start a Vending Machine Business, Cost, Tips, How Much You Make
Strategic Material Selection Guide for walmart vending machine
When selecting materials for Walmart vending machines, international B2B buyers must consider various factors that impact performance, durability, and compliance with regional standards. Below are analyses of four common materials used in vending machine construction, each with its unique properties, advantages, disadvantages, and considerations for different markets.
1. Stainless Steel
Key Properties:
Stainless steel is renowned for its corrosion resistance, high strength, and ability to withstand high temperatures and pressures. It typically has a temperature rating of up to 800°C and is resistant to rust and staining.
Pros & Cons:
Stainless steel is durable and easy to clean, making it ideal for vending machines that dispense food and beverages. However, it is relatively expensive compared to other materials, which can increase the overall cost of the vending machine. The manufacturing process can also be complex due to the need for specialized equipment.
Impact on Application:
This material is suitable for environments where hygiene is paramount, such as in food vending. Its resistance to corrosion makes it ideal for humid or wet conditions, which are common in many regions, including tropical climates in Africa and South America.
Considerations for International Buyers:
Buyers should ensure compliance with food safety standards, such as FDA regulations in the U.S. and EU food safety directives. Understanding local corrosion rates and environmental conditions can also inform the choice of stainless steel grades.
2. Aluminum
Key Properties:
Aluminum is lightweight, has good corrosion resistance, and can withstand moderate temperatures (up to 200°C). It is also a good conductor of heat and electricity.
Pros & Cons:
Aluminum is cost-effective and easy to fabricate, making it a popular choice for vending machine panels and frames. However, it is less durable than stainless steel and can be prone to dents and scratches. This may affect the aesthetic appeal and longevity of the machine.
Impact on Application:
Aluminum is suitable for non-food vending machines or machines in less demanding environments. It can be used effectively in regions with lower humidity levels, but it may not be ideal for areas with high moisture content.
Considerations for International Buyers:
Buyers should verify compliance with local standards, such as ASTM for the U.S. and EN standards for Europe. Additionally, understanding the local market’s preference for aesthetics versus durability can guide material selection.
3. Polycarbonate
Key Properties:
Polycarbonate is a high-strength thermoplastic known for its impact resistance and transparency. It can withstand temperatures up to 120°C and has excellent UV resistance.
Pros & Cons:
This material is lightweight and offers good insulation properties, making it suitable for display windows in vending machines. However, it is less resistant to scratching compared to glass and may require protective coatings. Its cost is moderate, but it may not be as durable as metals.
Impact on Application:
Polycarbonate is often used for the machine’s front panels and product display areas, enhancing visibility and attracting customers. Its lightweight nature allows for easier transportation and installation.
Considerations for International Buyers:
Buyers should consider the impact of UV exposure in their specific regions, as prolonged exposure can degrade polycarbonate. Compliance with local safety standards is also essential, especially in regions with stringent regulations regarding plastics.
4. Mild Steel
Key Properties:
Mild steel is known for its excellent strength and weldability, with a temperature rating of up to 600°C. However, it is susceptible to corrosion if not adequately protected.
Pros & Cons:
Mild steel is cost-effective and widely available, making it a popular choice for structural components of vending machines. However, its susceptibility to rust means it requires protective coatings, which can increase long-term maintenance costs.
Impact on Application:
This material is suitable for internal components and frames, where exposure to moisture is limited. It may not be ideal for external parts in humid environments.
Considerations for International Buyers:
Buyers in regions with high humidity or corrosive environments should consider additional protective measures, such as galvanization or powder coating. Compliance with local manufacturing standards (e.g., JIS in Japan, DIN in Germany) is crucial.
Summary Table
Material | Typical Use Case for Walmart Vending Machine | Key Advantage | Key Disadvantage/Limitation | Relative Cost (Low/Med/High) |
---|---|---|---|---|
Stainless Steel | External panels and food compartments | Corrosion-resistant, durable | High cost, complex manufacturing | High |
Aluminum | Frames and non-food vending machines | Lightweight, cost-effective | Less durable, prone to dents | Medium |
Polycarbonate | Display windows and product areas | Impact-resistant, lightweight | Scratches easily, UV degradation | Medium |
Mild Steel | Internal components and structural frames | Cost-effective, strong | Susceptible to corrosion, requires coating | Low |
This guide provides actionable insights for international B2B buyers considering material selection for Walmart vending machines, emphasizing the importance of understanding local conditions and compliance requirements.
In-depth Look: Manufacturing Processes and Quality Assurance for walmart vending machine
Manufacturing Processes for Walmart Vending Machines
Manufacturing vending machines, particularly those designed for Walmart, involves a series of precise steps aimed at ensuring quality, durability, and functionality. Understanding these processes is crucial for international B2B buyers, especially those in Africa, South America, the Middle East, and Europe. Below are the main stages of manufacturing and the key techniques utilized in the production of Walmart vending machines.
Main Stages of Manufacturing
-
Material Preparation
– Material Selection: High-quality materials such as stainless steel, tempered glass, and high-impact plastics are selected for their durability and aesthetic appeal.
– Cutting and Shaping: Materials are cut to specified dimensions using laser cutting or CNC (Computer Numerical Control) machines, ensuring precision and reducing waste. -
Forming
– Metal Forming Techniques: Processes such as stamping, bending, and rolling are employed to create the structural components of the vending machine. This stage ensures that the machine can withstand the physical stresses it will face during operation.
– Component Manufacturing: Internal components like coin mechanisms, display screens, and refrigeration units are manufactured separately and prepared for assembly. -
Assembly
– Sub-Assembly: Various components are assembled into sub-units, such as the control panel, vending mechanism, and cooling system, before the final assembly.
– Final Assembly: All sub-units are assembled into the main body of the vending machine. Automated assembly lines may be used for efficiency, but skilled labor is often employed for quality assurance. -
Finishing
– Surface Treatment: The exterior surfaces are treated to enhance appearance and resistance to corrosion. Techniques may include powder coating or painting.
– Quality Checks: Initial quality checks are performed at this stage to ensure that the assembly meets design specifications and functional requirements.
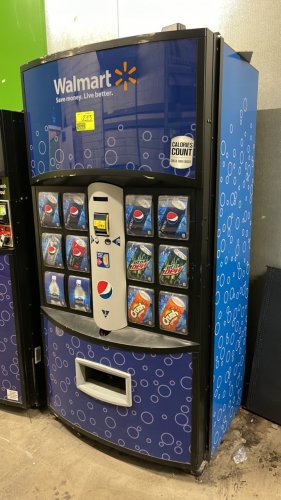
Illustrative Image (Source: Google Search)
Quality Assurance Practices
Quality assurance is critical in the manufacturing of vending machines, particularly for international markets where regulations may vary. The following outlines relevant international standards and industry-specific certifications, along with common quality control checkpoints.
Relevant International Standards
- ISO 9001: This standard outlines the requirements for a quality management system (QMS) and is crucial for ensuring that manufacturers meet customer and regulatory requirements consistently.
- CE Marking: For machines sold in Europe, CE marking indicates conformity with health, safety, and environmental protection standards.
- API Standards: For vending machines that dispense food or beverages, adherence to API standards ensures safety and quality in food handling.
Quality Control Checkpoints
-
Incoming Quality Control (IQC)
– Materials and components are inspected upon arrival to ensure they meet specified standards. This includes verifying certificates of compliance and conducting random sampling tests. -
In-Process Quality Control (IPQC)
– During manufacturing, regular checks are made at various stages to identify defects early. This may include measuring dimensions, checking assembly alignment, and testing functionality of components. -
Final Quality Control (FQC)
– After assembly, each vending machine undergoes comprehensive testing to ensure it operates correctly. This may involve running the machine through various operational scenarios to assess performance and reliability.
Common Testing Methods
- Functional Testing: Each machine is tested to ensure that all components, such as payment systems and product dispensing mechanisms, work as intended.
- Durability Testing: Vending machines are subjected to stress tests to simulate long-term use and ensure they can withstand environmental factors.
- Safety Testing: Compliance with safety standards is confirmed through electrical safety tests and checks for proper ventilation in refrigerated units.
Verification of Supplier Quality Control
For B2B buyers, especially those sourcing internationally, verifying the quality control processes of suppliers is paramount. Here are several strategies to ensure that suppliers meet quality standards:
- Audits: Conduct on-site audits to evaluate the manufacturing process, quality control measures, and adherence to international standards.
- Quality Reports: Request detailed quality reports that outline testing methods, results, and compliance with relevant standards.
- Third-Party Inspections: Engage third-party inspection services to conduct independent evaluations of the manufacturing process and final products. This adds an additional layer of assurance regarding quality.
Navigating Quality Control Nuances for International Buyers
International B2B buyers must be aware of the unique challenges that come with sourcing products across borders. Here are key considerations:
- Understanding Local Regulations: Each region may have specific regulations governing product safety and quality. Familiarize yourself with these requirements to ensure compliance.
- Cultural Differences in Manufacturing: Manufacturing practices can vary significantly between regions. Understanding these differences can help in assessing the reliability and quality of suppliers.
- Communication: Establish clear communication channels with suppliers to ensure that quality expectations are understood and met. Language barriers can lead to misunderstandings, so consider using interpreters if necessary.
Conclusion
For international B2B buyers looking to invest in Walmart vending machines, a thorough understanding of the manufacturing processes and quality assurance practices is essential. By focusing on key manufacturing stages, adhering to international standards, and implementing robust quality control measures, buyers can ensure they receive high-quality products that meet their operational needs. Additionally, verifying supplier quality control through audits, reports, and third-party inspections can mitigate risks and enhance buyer confidence in their sourcing decisions.
Related Video: SMART Quality Control for Manufacturing
Comprehensive Cost and Pricing Analysis for walmart vending machine Sourcing
Understanding the Cost Structure of Walmart Vending Machines
When sourcing Walmart vending machines, it’s essential for international B2B buyers to comprehend the various cost components involved. The primary cost structure includes:
-
Materials: The quality and type of materials used significantly impact costs. Premium materials enhance durability and aesthetics but increase the initial expenditure.
-
Labor: Labor costs are influenced by the region of manufacturing. Countries with lower labor costs may offer competitive pricing, but this could come at the expense of quality.
-
Manufacturing Overhead: This includes utilities, rent, and administrative expenses. Efficient manufacturers often have streamlined operations that lower overhead costs, benefiting buyers with better pricing.
-
Tooling: Custom designs may necessitate specialized tooling, which can be a one-time high expense. Understanding tooling costs is crucial, especially for tailored solutions.
-
Quality Control (QC): Implementing rigorous QC processes ensures that machines meet specified standards. While this adds to the cost, it can save buyers from future maintenance and replacement issues.
-
Logistics: Shipping costs can vary widely based on the origin and destination, with additional fees for customs and duties. Buyers should factor in these costs when evaluating total expenses.
-
Margin: Manufacturers typically include a profit margin in their pricing. Understanding the margin helps in negotiating better deals.
Influencers of Pricing
Several factors can influence the pricing of Walmart vending machines:
-
Volume and Minimum Order Quantity (MOQ): Bulk purchases often lead to discounts. Buyers should assess their needs and negotiate based on potential volume.
-
Specifications and Customization: Customized machines come with added costs. Buyers should clearly define their requirements to avoid unexpected charges.
-
Material Quality and Certifications: Machines with higher quality materials and necessary certifications (like safety or environmental standards) generally cost more. This is particularly relevant for buyers in regions with strict compliance regulations.
-
Supplier Factors: The reputation and reliability of the supplier can affect pricing. Established suppliers may charge a premium but offer better service and support.
-
Incoterms: Understanding Incoterms is vital for international transactions. These terms dictate who bears the cost and risk at each stage of the shipping process, impacting the final price.
Buyer Tips for Cost Efficiency
To maximize value when sourcing Walmart vending machines, consider the following strategies:
-
Negotiate: Leverage your purchasing power, especially if you are considering bulk orders. Don’t hesitate to ask for discounts or better terms.
-
Focus on Total Cost of Ownership (TCO): Evaluate not just the initial purchase price but also the long-term operational costs, including maintenance, energy consumption, and potential downtimes.
-
Pricing Nuances: Be aware of regional pricing variations. Factors such as local demand, currency fluctuations, and import tariffs can affect costs significantly for buyers from Africa, South America, the Middle East, and Europe.
-
Research and Compare: Conduct thorough market research to compare quotes from multiple suppliers. This not only provides insights into pricing but also helps identify the best quality options available.
-
Build Relationships: Establishing strong relationships with suppliers can lead to better deals and improved service in the long run. Trust can also facilitate smoother negotiations.
Disclaimer
Prices and costs mentioned here are indicative and may vary based on market conditions, location, and specific buyer requirements. It is advisable to consult with suppliers for accurate pricing tailored to your needs.
Spotlight on Potential walmart vending machine Manufacturers and Suppliers
This section offers a look at a few manufacturers active in the ‘walmart vending machine’ market. This is a representative sample for illustrative purposes; B2B buyers must conduct their own extensive due diligence before any engagement. Information is synthesized from public sources and general industry knowledge.
Essential Technical Properties and Trade Terminology for walmart vending machine
Key Technical Properties of Walmart Vending Machines
When considering the procurement of vending machines for retail environments such as Walmart, several technical specifications are critical for ensuring optimal performance, durability, and customer satisfaction. Below are essential properties to evaluate:
-
Material Grade: Vending machines are typically constructed from high-grade steel or aluminum. These materials provide strength and resistance to wear and tear, which is vital in high-traffic areas. For international buyers, selecting machines made from rust-resistant materials is crucial, especially in humid or coastal environments.
-
Dimensions and Capacity: Understanding the size and capacity of the vending machine is essential for space planning. Most Walmart vending machines are designed to fit specific product dimensions and hold a predetermined number of items. Buyers should assess their product offerings and customer volume to select an appropriately sized machine.
-
Temperature Control: For machines offering perishable items, temperature regulation is a key property. Look for machines equipped with reliable refrigeration systems that maintain consistent temperatures, ensuring product freshness and safety. This is particularly important in regions with extreme temperatures.
-
Power Consumption: Energy efficiency is becoming increasingly important in the B2B sector. Vending machines that utilize low-energy LED lighting and efficient cooling systems can significantly reduce operational costs. International buyers should consider the voltage and energy standards in their respective regions to ensure compatibility.
-
User Interface: Modern vending machines often feature touch screens or mobile payment options. A user-friendly interface can enhance customer experience and increase sales. Ensuring that the machine supports multiple languages can be beneficial in diverse markets.
Common Trade Terminology
Understanding trade terminology is essential for effective communication and negotiation in international procurement. Here are several key terms relevant to vending machine transactions:
-
OEM (Original Equipment Manufacturer): Refers to a company that produces parts or equipment that may be marketed by another manufacturer. When purchasing vending machines, buyers may deal with OEMs that provide branded machines or components.
-
MOQ (Minimum Order Quantity): This is the smallest number of units that a supplier is willing to sell. Knowing the MOQ is crucial for budgeting and inventory planning, especially for international buyers looking to minimize upfront costs.
-
RFQ (Request for Quotation): This document is used to solicit price quotes from suppliers. When purchasing vending machines, submitting an RFQ allows buyers to compare prices and terms from different manufacturers, helping them make informed decisions.
-
Incoterms (International Commercial Terms): These are standardized trade terms that define the responsibilities of buyers and sellers in international transactions. Familiarity with Incoterms is vital for understanding shipping costs, risks, and insurance responsibilities, particularly for cross-border transactions.
-
Lead Time: This term refers to the time taken from placing an order to receiving the goods. Understanding lead times is essential for inventory management and ensuring that vending machines are available when needed, especially during peak sales seasons.
-
Warranty Period: This specifies the duration for which the manufacturer is responsible for defects in the vending machine. A robust warranty can significantly reduce the risk for buyers, providing peace of mind regarding the machine’s durability and performance.
By understanding these technical properties and trade terms, international B2B buyers can make informed decisions when procuring Walmart vending machines, ultimately enhancing their operational efficiency and customer satisfaction.
Navigating Market Dynamics, Sourcing Trends, and Sustainability in the walmart vending machine Sector
Market Overview & Key Trends
The global vending machine market, particularly in the context of Walmart, is influenced by several key dynamics. Rapid urbanization and changing consumer lifestyles are driving demand for convenient purchasing options. In emerging markets, particularly in Africa and South America, the growth of urban centers has led to an increased presence of vending machines in public spaces, shopping centers, and workplaces, making them an attractive investment for B2B buyers.
Technological advancements play a crucial role in reshaping the vending machine landscape. Features such as cashless payment systems, touchless interfaces, and IoT connectivity are becoming standard. These innovations not only enhance user experience but also streamline inventory management and improve operational efficiency. International buyers should consider vendors that integrate these technologies to remain competitive.
Sourcing trends are also evolving, with an emphasis on local suppliers to reduce lead times and transportation costs. This shift is particularly relevant in regions like the Middle East, where logistics can be a challenge. Additionally, sustainability is increasingly influencing purchasing decisions; machines that offer eco-friendly options or are manufactured using sustainable practices are gaining traction. For buyers from Europe and beyond, aligning with suppliers who prioritize green practices is not just a trend but a strategic necessity.
Sustainability & Ethical Sourcing in B2B
Sustainability is a pressing concern in the vending machine sector. The environmental impact of traditional vending machines, particularly regarding energy consumption and waste generation, cannot be overlooked. As B2B buyers, particularly those in Europe and the Middle East, it is essential to evaluate the sustainability practices of suppliers. This includes assessing their energy sources, the recyclability of machine components, and waste management strategies.
Ethical sourcing is equally important. Buyers should prioritize suppliers that maintain transparency in their supply chains, ensuring that materials are sourced responsibly and ethically. The demand for ‘green’ certifications, such as ISO 14001 or Energy Star, is on the rise, and machines that meet these standards are increasingly favored. Utilizing eco-friendly materials, such as biodegradable plastics or recycled metals, can significantly reduce the overall carbon footprint of vending machines.
Incorporating sustainable practices not only aligns with global initiatives but also enhances brand reputation among environmentally conscious consumers. As buyers navigate the market, they should seek partnerships with vendors that demonstrate a commitment to sustainability and ethical sourcing.
Brief Evolution/History
The vending machine industry has evolved significantly since its inception in the early 20th century. Initially offering simple snacks and beverages, modern vending machines are now sophisticated, offering a wide range of products, including fresh food and electronics. Walmart’s entry into the vending machine sector aligns with its broader strategy to enhance customer convenience and adapt to shifting consumer preferences.
The integration of technology has transformed these machines from passive retail points into interactive, intelligent systems. Features such as remote monitoring, data analytics, and personalized marketing are now commonplace. This evolution presents unique opportunities for international B2B buyers to invest in innovative solutions that cater to diverse consumer needs across different regions. Understanding this historical context is vital for buyers seeking to leverage the full potential of vending machine offerings in their markets.
Related Video: Global Trade & Logistics – What is Global Trade?
Frequently Asked Questions (FAQs) for B2B Buyers of walmart vending machine
-
What factors should I consider when vetting suppliers for Walmart vending machines?
When vetting suppliers, prioritize their experience in the vending machine industry, especially with Walmart products. Verify their credibility by checking references and customer reviews. Assess their production capacity to ensure they can meet your demand. Additionally, inquire about their certifications, such as ISO or local quality standards, which indicate their commitment to quality assurance. Lastly, ensure they have a responsive customer service team to address any issues that may arise during your partnership. -
Can Walmart vending machines be customized to fit specific business needs?
Yes, customization options are available for Walmart vending machines. Depending on the supplier, you may request modifications such as branding, product selection, and payment systems tailored to your target market. Discuss your specific requirements during the negotiation phase to ensure the supplier can accommodate your needs. Keep in mind that extensive customization may affect lead times and costs, so plan accordingly. -
What are the minimum order quantities (MOQ) and lead times for purchasing Walmart vending machines?
Minimum order quantities vary by supplier and can range from a few units to several dozen, depending on their production capabilities. Lead times typically range from 4 to 12 weeks, influenced by factors such as customization requests, shipping logistics, and supplier production schedules. It’s advisable to confirm MOQs and lead times upfront to align your procurement strategy with your business goals.
-
What payment terms are generally offered for international buyers?
Payment terms for international buyers can vary significantly based on the supplier’s policies and your negotiation outcomes. Common options include letters of credit, bank transfers, or payment upon delivery. Suppliers may require an upfront deposit, especially for large orders, to secure production. It’s crucial to establish clear payment terms in your contract to avoid misunderstandings and ensure smooth transactions. -
How can I ensure the quality of Walmart vending machines before purchase?
To ensure quality, request detailed product specifications and quality assurance certifications from the supplier. Conduct pre-shipment inspections or arrange for third-party quality checks to verify compliance with your standards. Additionally, consider asking for samples or visiting the manufacturing facility if feasible. Establishing a robust quality assurance process will help mitigate risks associated with defects or non-compliance.
- What certifications should I look for when sourcing vending machines?
Look for certifications relevant to safety, quality, and environmental standards. Common certifications include ISO 9001 for quality management systems, CE marking for compliance with European safety standards, and UL certification for electrical safety. Additionally, inquire about any local certifications that may apply in your region, as these can enhance the credibility of the supplier and the reliability of their products.
-
What logistics considerations should I keep in mind when importing vending machines?
When importing vending machines, consider the shipping methods, customs regulations, and potential tariffs applicable in your country. Choose a reliable freight forwarder experienced in handling such equipment to streamline the process. Ensure that all necessary documentation, such as invoices and certificates of origin, is prepared to avoid delays at customs. Additionally, factor in delivery timelines and handling procedures to ensure timely distribution to your locations. -
How can I resolve disputes with suppliers effectively?
To resolve disputes effectively, maintain open communication and document all interactions regarding the issue. Refer to the terms outlined in your contract, which should include dispute resolution mechanisms such as mediation or arbitration. If negotiations stall, consider involving a neutral third party to facilitate discussions. Establishing a clear dispute resolution process in advance will help prevent escalation and foster a more cooperative relationship with your supplier.
Strategic Sourcing Conclusion and Outlook for walmart vending machine
As we conclude our exploration of strategic sourcing for Walmart vending machines, it is clear that a thoughtful approach can yield significant benefits for international B2B buyers. By leveraging the economies of scale, diverse product offerings, and technological advancements inherent in Walmart’s vending solutions, businesses can optimize their operations and enhance customer satisfaction.
Key takeaways include:
– Cost Efficiency: Sourcing directly from Walmart can lead to reduced operational costs through bulk purchasing and streamlined supply chains.
– Diverse Product Range: Access to a wide variety of products caters to diverse consumer preferences, which is essential for markets in Africa, South America, the Middle East, and Europe.
– Innovative Technology: Embracing the latest vending technologies can improve user experience and operational efficiency.
Looking ahead, it is vital for international buyers to engage proactively with Walmart’s offerings to capitalize on these advantages. As the vending industry continues to evolve, now is the time to consider how these strategic partnerships can position your business for future success. Embrace the opportunity to innovate and enhance your vending solutions today.