Master Vending Machine Coding to Enhance Your B2B
Guide to Vending Machine Coding
- Introduction: Navigating the Global Market for vending machine coding
- Understanding vending machine coding Types and Variations
- Key Industrial Applications of vending machine coding
- Strategic Material Selection Guide for vending machine coding
- In-depth Look: Manufacturing Processes and Quality Assurance for vending machine coding
- Comprehensive Cost and Pricing Analysis for vending machine coding Sourcing
- Spotlight on Potential vending machine coding Manufacturers and Suppliers
- Essential Technical Properties and Trade Terminology for vending machine coding
- Navigating Market Dynamics, Sourcing Trends, and Sustainability in the vending machine coding Sector
- Frequently Asked Questions (FAQs) for B2B Buyers of vending machine coding
- Strategic Sourcing Conclusion and Outlook for vending machine coding
Introduction: Navigating the Global Market for vending machine coding
In the ever-evolving landscape of global commerce, vending machine coding stands as a critical component that underpins the functionality and reliability of vending operations. As international B2B buyers from regions such as Africa, South America, the Middle East, and Europe seek to enhance their vending solutions, understanding the intricacies of coding becomes imperative. This guide serves as a comprehensive resource, designed to equip decision-makers with the knowledge necessary to navigate the complexities of vending machine coding.
The scope of this guide encompasses a variety of essential topics, including types of vending machine coding, the materials used in manufacturing, quality control standards, and potential suppliers. Moreover, it delves into cost considerations and provides insights into the current market landscape, allowing buyers to make informed decisions.
In addition, the guide addresses frequently asked questions (FAQs) that clarify common concerns and misconceptions about vending machine coding. By empowering B2B buyers with this valuable information, the guide not only facilitates effective sourcing but also promotes strategic partnerships with suppliers who align with their operational needs.
As the demand for innovative vending solutions continues to grow, understanding vending machine coding is not just beneficial—it is essential for businesses looking to thrive in competitive markets.
Understanding vending machine coding Types and Variations
Type Name | Key Distinguishing Features | Primary B2B Applications | Brief Pros & Cons for Buyers |
---|---|---|---|
Mechanical Coding | Uses physical mechanisms (e.g., levers, dials) | Traditional vending setups | Simple to operate, but limited in product variety and flexibility. |
Electronic Coding | Digital interfaces with touchscreens and sensors | High-tech vending machines | Offers extensive customization, but may require more maintenance. |
Mobile Payment Coding | Integration with mobile payment systems | Modern retail environments | Convenient for users, but may face connectivity issues in remote areas. |
Remote Management Coding | Allows for monitoring and management via cloud-based systems | Large scale vending operations | Enhances operational efficiency, but may involve higher initial costs. |
Hybrid Coding | Combines mechanical and electronic systems | Versatile applications in various environments | Offers flexibility and reliability, but can be complex to manage. |
Mechanical Coding
Mechanical coding systems are characterized by their reliance on physical components such as levers and dials. These systems are often simpler and less expensive, making them suitable for traditional vending setups where ease of use is paramount. However, they may limit the range of products offered and can be less adaptable to changing consumer preferences. B2B buyers should consider the operational environment and customer demographics when opting for mechanical coding, especially in less tech-savvy markets.
Electronic Coding
Electronic coding utilizes digital interfaces, touchscreens, and sensors, allowing for a more interactive user experience. This type is increasingly popular in high-tech vending machines that cater to modern consumers. While electronic coding offers extensive customization and the ability to track sales data, it may require more frequent maintenance and updates. Buyers should evaluate the technical support available and the training needed for staff to operate these systems effectively.
Mobile Payment Coding
This variation focuses on integrating mobile payment systems, enabling consumers to make purchases via their smartphones. With the rise of digital wallets and contactless payments, this coding type is essential for modern retail environments. While it enhances convenience and can attract tech-savvy customers, buyers must consider potential connectivity issues, especially in remote or underserved areas. Ensuring robust network coverage is crucial for successful implementation.
Remote Management Coding
Remote management coding allows operators to monitor and manage vending machines through cloud-based systems. This capability is particularly beneficial for large-scale vending operations, as it enhances operational efficiency by enabling real-time inventory tracking and sales analysis. However, the initial investment can be higher due to the technology involved. B2B buyers should assess their operational scale and the potential return on investment when considering remote management solutions.
Hybrid Coding
Hybrid coding combines elements of both mechanical and electronic systems, providing flexibility and reliability. This approach is particularly advantageous in environments where a diverse range of products is offered, catering to varying consumer preferences. While hybrid systems can be more complex to manage, they often yield better performance and customer satisfaction. Buyers should weigh the benefits of versatility against the potential challenges of maintaining such systems.
Related Video: Machine Learning in 2024 – Beginner’s Course
Key Industrial Applications of vending machine coding
Industry/Sector | Specific Application of Vending Machine Coding | Value/Benefit for the Business | Key Sourcing Considerations for this Application |
---|---|---|---|
Retail | Automated Inventory Management | Reduces human error, improves stock accuracy | Compatibility with existing POS systems, data integration capabilities |
Healthcare | Prescription Dispensing Vending Machines | Enhances patient access to medications, reduces wait times | Compliance with health regulations, secure payment processing |
Education | Campus Snack and Beverage Services | Increases student satisfaction, boosts campus revenue | Customization options, reliable supply chain management |
Transportation | Ticketing Vending Machines | Streamlines passenger flow, reduces staffing costs | Integration with public transport systems, user-friendly interfaces |
Hospitality | Mini-bar Vending Solutions | Increases guest convenience, reduces operational costs | Product variety, energy efficiency, and maintenance support |
Retail
In the retail sector, vending machine coding plays a pivotal role in automated inventory management. By employing advanced coding systems, retailers can track stock levels in real-time, reducing human errors that often lead to overstocking or stockouts. This application not only enhances stock accuracy but also provides valuable data analytics for demand forecasting. For international B2B buyers, particularly in Africa and South America, it’s crucial to ensure that the vending systems can integrate seamlessly with existing point-of-sale (POS) systems and offer robust data integration capabilities.
Healthcare
In healthcare, vending machines equipped with coding technology are revolutionizing prescription dispensing. These machines allow patients to access their medications conveniently, significantly reducing wait times at pharmacies. The coding systems ensure that prescriptions are dispensed accurately and securely, adhering to stringent health regulations. B2B buyers in this sector must prioritize compliance with local health regulations and ensure that the machines support secure payment processing, especially in regions like the Middle East where privacy and security are paramount.
Education
Educational institutions are increasingly adopting vending machines for snack and beverage services on campus. Vending machine coding enhances the user experience by offering customized options that cater to diverse dietary preferences. This not only improves student satisfaction but also boosts revenue for the institution. For buyers in Europe, particularly in Italy, it is essential to consider customization options that align with local tastes and preferences, as well as ensuring reliable supply chain management to maintain stock levels.
Transportation
In the transportation sector, vending machines for ticketing streamline passenger flow and reduce the need for staffing at stations. Advanced coding systems enable these machines to process transactions quickly and efficiently, enhancing the overall travel experience. For international buyers, especially in regions with extensive public transport networks, integrating these machines with existing systems is critical. User-friendly interfaces are also essential to cater to a diverse passenger demographic.
Hospitality
The hospitality industry has seen a rise in mini-bar vending solutions, which allow guests to access snacks and beverages conveniently. Vending machine coding in this application enhances guest convenience while reducing operational costs associated with traditional mini-bar setups. Buyers in this sector should focus on sourcing machines that offer a variety of products, energy efficiency, and comprehensive maintenance support to ensure smooth operation and guest satisfaction.
Related Video: DIY Vending Machine – Arduino based Mechatronics Project
Strategic Material Selection Guide for vending machine coding
When selecting materials for vending machine coding, it is crucial to consider various factors that influence performance, durability, and compliance with international standards. Here, we analyze four common materials used in vending machine coding, focusing on their properties, advantages, disadvantages, and specific considerations for international B2B buyers.
1. Stainless Steel (e.g., 304, 316)
Key Properties:
Stainless steel is known for its excellent corrosion resistance, high strength, and ability to withstand high temperatures (up to 870°C for 304 and 925°C for 316). It is also non-reactive, making it suitable for food-grade applications.
Pros & Cons:
The durability of stainless steel is one of its strongest attributes, providing long life and minimal maintenance. However, it can be more expensive than other materials and may require specialized manufacturing processes such as welding and machining, which can increase production costs.
Impact on Application:
Stainless steel is compatible with a wide range of media, including food and beverages, making it ideal for vending machines that dispense consumables. Its resistance to corrosion also ensures that the coding remains legible over time.
Considerations for International Buyers:
Compliance with food safety standards (e.g., FDA in the U.S., EU regulations) is essential. Buyers should also be aware of local preferences for grades (e.g., 304 vs. 316) based on environmental conditions, such as humidity and exposure to salt.
2. Aluminum
Key Properties:
Aluminum is lightweight and has good corrosion resistance, particularly when anodized. It can withstand temperatures up to 400°C and is known for its excellent machinability.
Pros & Cons:
The lightweight nature of aluminum allows for easier installation and transportation, reducing overall costs. However, it is less durable than stainless steel and can be prone to scratching and denting, which may affect the appearance of the vending machine over time.
Impact on Application:
Aluminum is suitable for applications that do not involve harsh chemicals or extreme temperatures. It is often used in vending machines that dispense non-perishable items.
Considerations for International Buyers:
Buyers should verify compliance with local standards for aluminum alloys (e.g., ASTM B221) and consider the environmental impact of aluminum production, which may influence purchasing decisions in regions like Europe, where sustainability is a priority.
3. Polycarbonate
Key Properties:
Polycarbonate is a high-performance plastic known for its impact resistance and transparency. It can withstand temperatures up to 135°C and is lightweight.
Pros & Cons:
The transparency of polycarbonate allows for visibility of the product within the vending machine, enhancing customer experience. However, it is less resistant to UV light and can become discolored over time, which may affect its aesthetic appeal.
Impact on Application:
Polycarbonate is ideal for front panels or display areas in vending machines, particularly for snack or beverage machines. Its impact resistance makes it suitable for high-traffic environments.
Considerations for International Buyers:
Compliance with safety standards (e.g., REACH in Europe) is crucial. Buyers should also consider the environmental impact of plastic use and potential recycling options, particularly in regions with stringent waste management regulations.
4. Carbon Steel (e.g., A36)
Key Properties:
Carbon steel is known for its high strength and durability, with a temperature rating of up to 500°C. It is generally less resistant to corrosion compared to stainless steel.
Pros & Cons:
Carbon steel is cost-effective and widely available, making it a popular choice for structural components of vending machines. However, its susceptibility to rust and corrosion necessitates protective coatings, which can add to maintenance costs.
Impact on Application:
Carbon steel is suitable for non-corrosive environments and is often used in the structural framework of vending machines. It is less ideal for components exposed to moisture or food products.
Considerations for International Buyers:
Buyers should ensure that carbon steel components comply with local standards (e.g., ASTM A36) and consider the implications of corrosion resistance in their specific environments, particularly in humid regions like parts of Africa and South America.
Summary Table
Material | Typical Use Case for vending machine coding | Key Advantage | Key Disadvantage/Limitation | Relative Cost (Low/Med/High) |
---|---|---|---|---|
Stainless Steel | Food-grade applications, external casing | Excellent corrosion resistance | Higher cost, complex manufacturing | High |
Aluminum | Non-perishable item dispensers | Lightweight, good machinability | Less durable, prone to scratches | Medium |
Polycarbonate | Front panels, display areas | Impact-resistant, transparent | UV sensitivity, potential discoloration | Medium |
Carbon Steel | Structural components | Cost-effective, high strength | Susceptible to corrosion, needs coating | Low |
This guide aims to equip international B2B buyers with the necessary insights to make informed decisions regarding material selection for vending machine coding, ensuring compliance with relevant standards and suitability for their specific applications.
In-depth Look: Manufacturing Processes and Quality Assurance for vending machine coding
Vending machine coding is a critical component of the overall vending machine manufacturing process, involving multiple stages that ensure quality and functionality. Below is a comprehensive overview of the manufacturing processes and quality assurance measures that B2B buyers should consider when sourcing vending machine coding solutions.
Manufacturing Processes
The manufacturing of vending machine coding involves several key stages:
1. Material Preparation
The first step in the manufacturing process is the preparation of materials. This often includes sourcing high-quality plastics, metals, and electronic components. Material selection is crucial, as it impacts the durability and functionality of the coding systems.
- Key Techniques:
- Supplier Verification: Ensure that materials are sourced from reputable suppliers who comply with international standards.
- Material Testing: Conduct tests to verify material properties such as tensile strength, resistance to corrosion, and electrical conductivity.
2. Forming
Once the materials are prepared, the next phase is forming, which involves shaping the components that will be used in the vending machine coding system.
- Key Techniques:
- Injection Molding: Commonly used for plastic components, ensuring precise shapes and sizes.
- CNC Machining: Utilized for metal parts, providing high accuracy and the ability to create complex geometries.
3. Assembly
The assembly stage is where individual components come together to form the coding system. This stage requires skilled labor and often involves the use of automated machinery.
- Key Techniques:
- Automated Assembly Lines: Streamline the assembly process, enhancing efficiency and reducing labor costs.
- Manual Assembly: Necessary for intricate tasks that require attention to detail, such as wiring connections.
4. Finishing
The final stage in the manufacturing process is finishing, which includes surface treatments and quality checks.
- Key Techniques:
- Surface Coating: Application of protective coatings to enhance durability and aesthetics.
- Functional Testing: Conduct tests to ensure that coding systems operate correctly and meet specified performance standards.
Quality Assurance
Quality assurance is essential to ensure that the vending machine coding systems meet both international and industry-specific standards.
Relevant International Standards
For B2B buyers, understanding the applicable quality standards is critical:
- ISO 9001: This is a widely recognized international standard that outlines requirements for a quality management system (QMS). Compliance indicates a commitment to quality and continuous improvement.
- CE Marking: For products sold in the European market, CE marking indicates compliance with safety, health, and environmental protection standards.
- API Standards: Depending on the coding technology used, adherence to API standards may be relevant, particularly for systems that integrate with payment processing or other electronic functions.
Quality Control Checkpoints
Quality control (QC) checkpoints are integral to the manufacturing process. Common checkpoints include:
- Incoming Quality Control (IQC): Inspection of raw materials upon arrival to ensure they meet specified requirements.
- In-Process Quality Control (IPQC): Continuous monitoring during the manufacturing process to identify and rectify defects early.
- Final Quality Control (FQC): Comprehensive testing of finished products before they are shipped to customers.
Common Testing Methods
Various testing methods are employed to ensure product reliability:
- Functional Testing: Verifies that the coding system performs as intended under normal operating conditions.
- Stress Testing: Assesses the durability of components by subjecting them to extreme conditions.
- Electrical Testing: Ensures that all electronic components function correctly and safely.
Verifying Supplier Quality Control
B2B buyers should take proactive steps to verify the quality control practices of potential suppliers:
- Conduct Audits: Regular audits of suppliers can help ensure compliance with quality standards and identify areas for improvement.
- Request Quality Reports: Suppliers should provide documentation that outlines their quality control processes and results from testing.
- Third-Party Inspections: Engaging independent inspectors can provide an unbiased assessment of a supplier’s quality practices.
QC and Certification Nuances for International Buyers
When sourcing vending machine coding solutions, international buyers, particularly from regions such as Africa, South America, the Middle East, and Europe, should be aware of specific nuances:
- Cultural Considerations: Understand the business practices and communication styles of suppliers in different regions, as this can impact quality and delivery.
- Regulatory Compliance: Be aware of local regulations that may affect product standards and certifications.
- Logistics and Supply Chain: Consider how geographical factors may impact the supply chain, including shipping times and costs.
By understanding the manufacturing processes and quality assurance measures associated with vending machine coding, B2B buyers can make informed decisions that enhance their supply chain and product offerings.
Related Video: SMART Quality Control for Manufacturing
Comprehensive Cost and Pricing Analysis for vending machine coding Sourcing
In the realm of vending machine coding, understanding the cost structure and pricing dynamics is crucial for international B2B buyers. This section outlines the key components of costs, pricing influencers, and strategic tips for making informed purchasing decisions.
Cost Components
-
Materials: The primary materials for vending machine coding include electronic components (e.g., microcontrollers, displays, and sensors) and coding software. Prices can vary significantly based on the quality and specifications of these components.
-
Labor: Labor costs encompass the wages of engineers and technicians involved in the design, programming, and assembly of the vending machine coding systems. Regions with higher labor costs, such as parts of Europe, may see increased pricing compared to regions with lower wage scales.
-
Manufacturing Overhead: This includes utilities, rent, and equipment depreciation in manufacturing facilities. Overhead costs are typically allocated per unit, influencing the final price based on production volume.
-
Tooling: Initial setup costs for production tooling can be significant, especially for customized solutions. These costs are often amortized over larger production runs, making bulk orders more cost-effective.
-
Quality Control (QC): Ensuring compliance with international standards and certifications (such as ISO) can add to costs. Rigorous QC processes are essential to maintain product reliability, particularly in diverse market conditions.
-
Logistics: Transporting components and finished products affects pricing, especially for international shipments. Factors such as shipping method, distance, and customs duties can substantially influence total logistics costs.
-
Margin: Manufacturers typically add a profit margin based on their operational costs and market positioning. Understanding this margin can provide insights into pricing flexibility during negotiations.
Price Influencers
-
Volume/MOQ (Minimum Order Quantity): Pricing often decreases with higher volumes. Buyers should assess their demand forecasts to leverage better pricing through bulk purchases.
-
Specifications/Customization: Custom features or specifications can lead to higher costs. Buyers should clearly define requirements to avoid unexpected expenses.
-
Materials: The choice of materials directly impacts cost. Premium components may enhance performance but come with a higher price tag. Balancing quality and cost is essential.
-
Quality/Certifications: Products meeting higher quality standards or certifications may command a premium price. Buyers should consider the long-term benefits of investing in quality.
-
Supplier Factors: The supplier’s reputation, reliability, and service capabilities can affect pricing. Established suppliers may charge more but offer better support and warranty terms.
-
Incoterms: Understanding Incoterms (International Commercial Terms) is vital for managing shipping costs and responsibilities. Different terms can significantly affect the total landed cost of goods.
Buyer Tips
-
Negotiation: Engage in negotiations to explore flexible pricing structures, especially for larger orders. Building a relationship with suppliers can yield better terms and discounts.
-
Cost-Efficiency: Evaluate total cost of ownership (TCO) rather than just the initial purchase price. Consider maintenance, support, and potential downtime in your calculations.
-
Pricing Nuances: Be aware of regional pricing differences. For instance, buyers from Africa and South America may face different cost structures compared to their European counterparts due to local economic conditions.
-
Market Research: Conduct thorough market research to understand pricing trends and competitor offers. This knowledge can empower buyers during negotiations and decision-making.
Conclusion
Understanding the cost structure and pricing dynamics in vending machine coding is vital for international B2B buyers. By considering the various cost components, pricing influencers, and strategic tips provided, buyers can make informed decisions that align with their operational needs and budget constraints. Always keep in mind that prices can vary widely based on numerous factors, and thus, careful analysis is essential.
Spotlight on Potential vending machine coding Manufacturers and Suppliers
This section offers a look at a few manufacturers active in the ‘vending machine coding’ market. This is a representative sample for illustrative purposes; B2B buyers must conduct their own extensive due diligence before any engagement. Information is synthesized from public sources and general industry knowledge.
Essential Technical Properties and Trade Terminology for vending machine coding
Key Technical Properties of Vending Machine Coding
When engaging in the procurement of vending machine coding solutions, understanding the technical specifications is crucial. Here are some essential properties that international B2B buyers should consider:
-
Material Grade
– Definition: The classification of materials used in the construction of vending machines, often specified by standards such as ASTM or ISO.
– Importance: Higher-grade materials (e.g., stainless steel, high-impact plastics) ensure durability and longevity, reducing the need for replacements and maintenance. This is particularly vital in regions with harsh climates. -
Tolerance Levels
– Definition: The permissible limit or limits of variation in a physical dimension or measured value.
– Importance: In coding systems, tight tolerances can ensure that components fit perfectly, enhancing operational efficiency and reducing downtime. This is especially important in high-volume environments where precision impacts throughput. -
Power Supply Specifications
– Definition: Details regarding the electrical requirements (voltage, frequency, and current) necessary for optimal operation of the vending machine.
– Importance: Understanding these requirements helps buyers ensure compatibility with local power grids, avoiding operational issues that could lead to equipment failure or safety hazards.
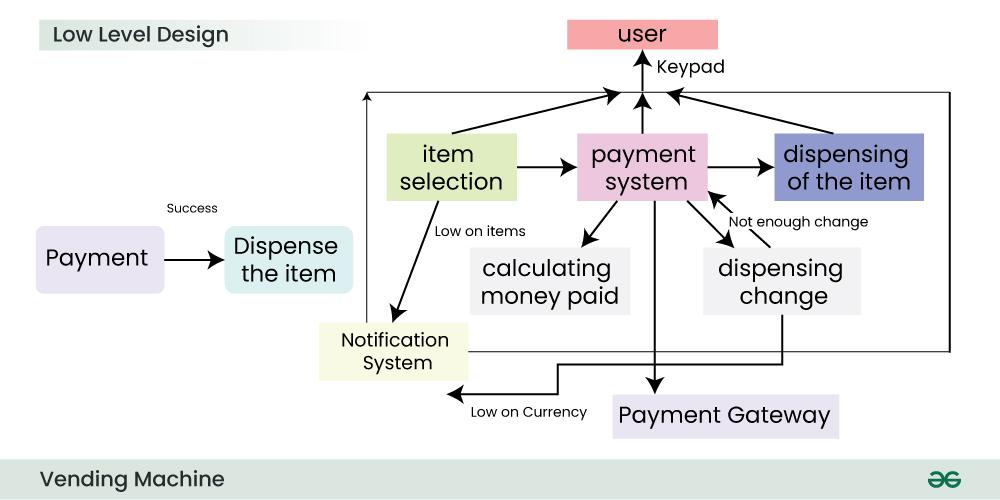
Illustrative Image (Source: Google Search)
-
Environmental Ratings
– Definition: Standards indicating how well a vending machine can withstand environmental factors, such as moisture (IP ratings) and temperature extremes.
– Importance: Machines with higher environmental ratings are better suited for outdoor installations or humid environments, increasing their reliability and lifespan. -
Communication Protocols
– Definition: Standards governing how vending machines communicate with other systems (e.g., payment processing, inventory management).
– Importance: Compatibility with existing systems is crucial for seamless operations. Buyers should look for widely accepted protocols (like MDB or DEX) to ensure ease of integration. -
User Interface Design
– Definition: The layout and functionality of the machine’s control panel and display features.
– Importance: A well-designed user interface can enhance customer experience, leading to increased sales. Consideration for multi-language support is vital for diverse markets.
Common Trade Terms in Vending Machine Coding
Understanding the terminology used in the vending machine industry can significantly streamline the purchasing process. Here are some common terms:
-
OEM (Original Equipment Manufacturer)
– Definition: A company that produces parts or equipment that may be marketed by another manufacturer.
– Relevance: Buyers often procure components from OEMs to ensure compatibility and quality, particularly in coding systems where precision is key. -
MOQ (Minimum Order Quantity)
– Definition: The smallest quantity of a product that a supplier is willing to sell.
– Relevance: Knowing the MOQ helps buyers plan their inventory and cash flow. In some regions, lower MOQs may be available, which can benefit smaller operators.
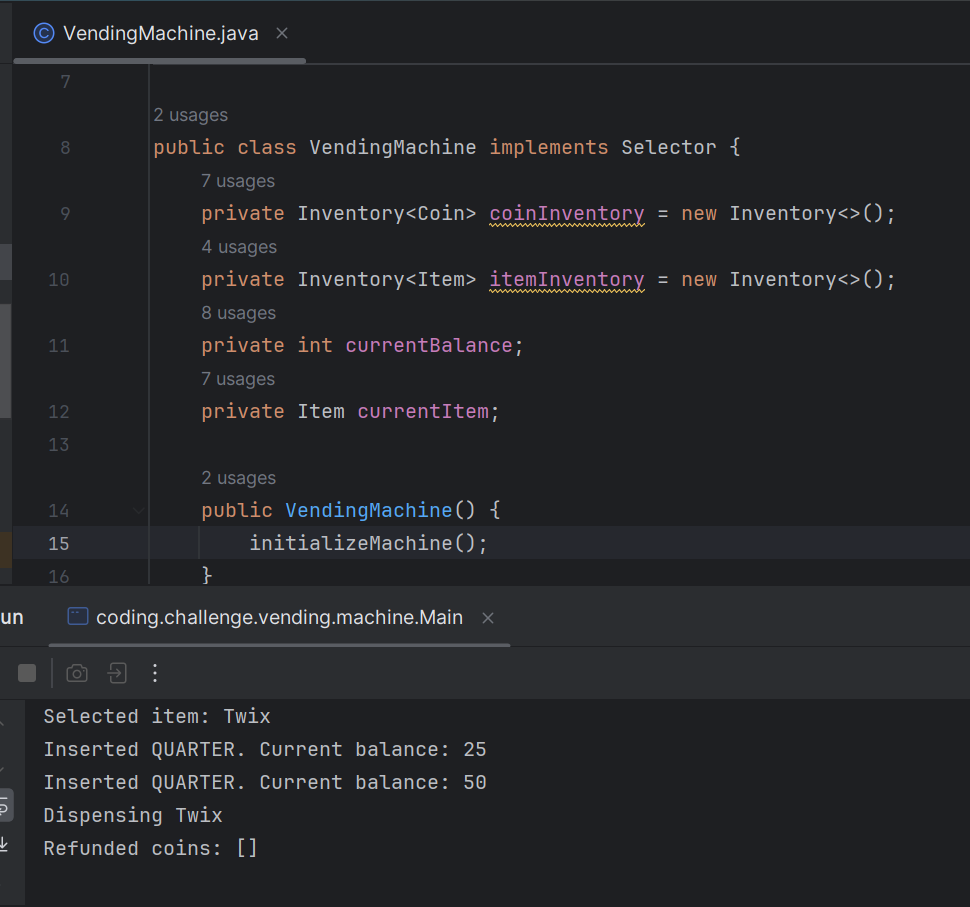
Illustrative Image (Source: Google Search)
-
RFQ (Request for Quotation)
– Definition: A document sent to suppliers to request pricing and terms for specific products.
– Relevance: Submitting an RFQ allows buyers to compare multiple offers and negotiate better pricing, essential for budget management. -
Incoterms (International Commercial Terms)
– Definition: A set of predefined international rules that clarify the responsibilities of buyers and sellers regarding shipping, insurance, and tariffs.
– Relevance: Understanding Incoterms is crucial for international transactions, as they define who pays for shipping and insurance, helping to avoid disputes. -
Lead Time
– Definition: The amount of time it takes from placing an order to receiving the product.
– Relevance: Knowing lead times is essential for planning and inventory management, especially in markets with high demand fluctuations. -
Warranty Period
– Definition: The duration during which a product is guaranteed against defects.
– Relevance: A longer warranty period can indicate a supplier’s confidence in their product quality, providing peace of mind for buyers.
By understanding these technical properties and trade terms, B2B buyers can make informed decisions that enhance their operational efficiency and profitability in the vending machine sector.
Navigating Market Dynamics, Sourcing Trends, and Sustainability in the vending machine coding Sector
Market Overview & Key Trends
The vending machine coding sector is experiencing robust growth, driven by several global trends. Key factors include the increasing demand for automation and digital solutions in retail environments, which enhance customer experience and streamline operations. B2B buyers from Africa, South America, the Middle East, and Europe should be aware of the rising integration of IoT (Internet of Things) technologies. These innovations enable real-time data collection and analytics, allowing businesses to optimize inventory management and enhance user engagement through personalized marketing strategies.
Emerging trends also highlight the shift towards contactless payment systems and mobile integration, which are becoming standard features in modern vending machines. Furthermore, the growing interest in sustainability is prompting manufacturers to develop eco-friendly machines that utilize less energy and incorporate recyclable materials. Buyers should consider sourcing from suppliers that are at the forefront of these technological advancements, as they are more likely to offer competitive pricing and superior service.
In addition, the global market dynamics indicate a shift toward localized production and sourcing strategies. This trend is particularly relevant for buyers in regions such as Africa and South America, where local partnerships can facilitate quicker supply chain responses and reduce import tariffs. Understanding these dynamics will enable B2B buyers to make informed decisions that align with both market demands and operational efficiencies.
Sustainability & Ethical Sourcing in B2B
Sustainability is no longer an option but a necessity in the vending machine coding sector. The environmental impact of manufacturing processes, especially concerning energy consumption and waste generation, is a critical consideration for B2B buyers. As businesses increasingly focus on their carbon footprints, sourcing from suppliers who prioritize sustainable practices can enhance corporate responsibility and brand reputation.
Buyers should look for vendors that utilize green certifications such as ISO 14001, which signifies effective environmental management systems. Furthermore, incorporating sustainable materials, such as biodegradable plastics and energy-efficient components, into vending machine designs is gaining traction. This not only reduces environmental impact but also appeals to a growing consumer base that values sustainability.
Ethical sourcing is equally important; ensuring that suppliers adhere to fair labor practices and sustainable resource extraction is crucial. Buyers in the Middle East and Europe, where regulatory frameworks around ethical sourcing are becoming stricter, should prioritize suppliers who can demonstrate transparency in their supply chains. Engaging with vendors committed to ethical practices not only mitigates risks but also fosters long-term partnerships based on shared values.
Brief Evolution/History
The evolution of vending machine coding has been marked by significant technological advancements. Initially, vending machines were simple mechanical devices that relied on coin-based transactions. However, the introduction of electronic and digital technologies in the late 20th century transformed the industry. This shift enabled features such as cashless payments, touchscreen interfaces, and product tracking.
In recent years, the focus has expanded to include smart vending solutions, integrating IoT capabilities that allow machines to communicate with both operators and consumers. This progression reflects broader trends in automation and digitalization across various sectors, making it essential for B2B buyers to stay abreast of innovations in vending machine coding. Understanding this historical context can aid buyers in recognizing the potential for future advancements and align their sourcing strategies accordingly.
Related Video: Is global trade transforming? | Counting the Cost
Frequently Asked Questions (FAQs) for B2B Buyers of vending machine coding
-
What should I consider when vetting suppliers for vending machine coding?
When vetting suppliers, focus on their industry experience, client testimonials, and technical capabilities. Verify their certifications and compliance with international standards, such as ISO or CE, which indicate quality assurance. Additionally, evaluate their production capacity and delivery timelines to ensure they can meet your demands. Engage in direct communication to assess their responsiveness and willingness to customize solutions based on your specific needs. -
Can I customize vending machine coding solutions to suit my business needs?
Yes, many suppliers offer customization options for vending machine coding solutions. This can include adapting the software interface, integrating unique functionalities, or tailoring hardware components to fit specific operational requirements. Discuss your specific needs with potential suppliers during the initial conversations, and request prototypes or demos to evaluate their capabilities in providing tailored solutions.
-
What are the typical minimum order quantities (MOQ) and lead times for vending machine coding?
Minimum order quantities can vary significantly among suppliers, often ranging from a few units to several hundred, depending on the complexity and cost of the coding solution. Lead times are also contingent on factors such as order size, customization requirements, and supplier location. Always inquire about these aspects upfront and factor them into your procurement timeline to avoid disruptions in your operations. -
What payment options are available when sourcing vending machine coding solutions?
Payment options can include bank transfers, letters of credit, and online payment platforms, depending on the supplier’s policies and your location. It’s essential to discuss payment terms early in the negotiation process, including deposit requirements and payment milestones. Ensure that you are comfortable with the payment structure to mitigate risks associated with international transactions. -
How do I ensure quality assurance and certifications for the vending machine coding I source?
Request documentation of quality assurance processes and certifications from your suppliers. Common certifications to look for include ISO 9001 for quality management systems and specific industry-related certifications. Additionally, consider conducting factory audits or third-party inspections to verify compliance with quality standards and ensure that the products meet your specifications. -
What logistics considerations should I keep in mind when importing vending machine coding solutions?
When importing, consider shipping methods, customs clearance processes, and potential tariffs or duties that may apply. Collaborate with suppliers who have experience with international shipping and can provide documentation required for smooth customs clearance. Evaluate logistics partners for their reliability and ability to handle the specific needs of your shipment, including tracking capabilities and delivery timelines. -
How should I handle disputes with suppliers when sourcing vending machine coding?
Establish clear terms in your purchase agreement regarding dispute resolution, including procedures for addressing quality issues or delivery delays. Consider including clauses for mediation or arbitration to resolve conflicts amicably. Maintain open communication with your suppliers throughout the process, documenting all interactions to provide a clear record in case disputes arise. -
What are the best practices for maintaining a successful long-term relationship with suppliers?
Building a successful long-term relationship with suppliers involves consistent communication, regular feedback, and mutual respect. Schedule periodic reviews to discuss performance, address any issues, and explore opportunities for collaboration. Recognize and reward good performance to foster loyalty, and remain open to adapting your partnership terms as your business needs evolve.
Strategic Sourcing Conclusion and Outlook for vending machine coding
In conclusion, the strategic sourcing of vending machine coding solutions presents a significant opportunity for international B2B buyers. By focusing on quality, reliability, and compliance with local regulations, businesses can ensure that their vending machines are equipped with efficient coding technology that meets both consumer demands and operational requirements.
Key Takeaways:
– Invest in Quality: Prioritize suppliers who offer robust, high-quality coding solutions that enhance the longevity and functionality of vending machines.
– Understand Local Regulations: Familiarize yourself with local laws and standards in your target markets to ensure compliance and avoid potential legal issues.
– Leverage Technological Advancements: Stay updated on the latest coding technologies, such as QR codes and NFC, which can enhance customer engagement and streamline operations.
As we look ahead, the demand for innovative and efficient vending solutions is set to grow. International B2B buyers are encouraged to actively engage with suppliers who can provide tailored solutions to meet their unique market needs. By strategically sourcing vending machine coding technologies, businesses can not only improve their operational efficiency but also enhance customer satisfaction and loyalty. Take the next step in your sourcing strategy and explore the vast potential that lies within the vending machine coding landscape.