Your Ultimate Guide to Sourcing Custom Vending Machines
Guide to Custom Vending Machines
- Introduction: Navigating the Global Market for custom vending machines
- Understanding custom vending machines Types and Variations
- Key Industrial Applications of custom vending machines
- Strategic Material Selection Guide for custom vending machines
- In-depth Look: Manufacturing Processes and Quality Assurance for custom vending machines
- Comprehensive Cost and Pricing Analysis for custom vending machines Sourcing
- Spotlight on Potential custom vending machines Manufacturers and Suppliers
- Essential Technical Properties and Trade Terminology for custom vending machines
- Navigating Market Dynamics, Sourcing Trends, and Sustainability in the custom vending machines Sector
- Frequently Asked Questions (FAQs) for B2B Buyers of custom vending machines
- Strategic Sourcing Conclusion and Outlook for custom vending machines
Introduction: Navigating the Global Market for custom vending machines
In today’s dynamic marketplace, custom vending machines have emerged as pivotal assets for businesses seeking to enhance customer engagement and streamline operations. These machines are not merely retail solutions; they represent innovative avenues to diversify product offerings, increase brand visibility, and adapt to unique consumer preferences across different regions. For B2B buyers, particularly in Africa, South America, the Middle East, and Europe, understanding the nuances of custom vending machines is essential for making informed sourcing decisions.
This comprehensive guide delves into the various dimensions of custom vending machines, covering critical topics such as types of machines, materials used, manufacturing processes, and quality control measures. It also provides insights into supplier selection, cost considerations, and the overall market landscape. By addressing frequently asked questions, the guide equips international buyers with the knowledge needed to navigate the complexities of sourcing these machines effectively.
With the right strategies and insights, businesses can leverage custom vending solutions to not only meet market demands but also capitalize on emerging opportunities. This guide empowers B2B buyers to foster strong supplier partnerships, optimize their inventory, and ultimately drive profitability in their vending operations. Whether you are based in bustling cities like Buenos Aires or Paris, this resource is designed to enhance your understanding and facilitate successful investments in custom vending machines.
Understanding custom vending machines Types and Variations
Type Name | Key Distinguishing Features | Primary B2B Applications | Brief Pros & Cons for Buyers |
---|---|---|---|
Food and Beverage Vending | Customizable for snacks, drinks, and fresh food items | Offices, schools, hospitals | Pros: High demand, diverse product range. Cons: Perishable goods require careful inventory management. |
Electronics Vending | Dispenses gadgets, accessories, and tech products | Airports, malls, tech stores | Pros: High-value products, caters to tech-savvy consumers. Cons: Higher initial investment and security concerns. |
Personal Care Vending | Offers cosmetics, hygiene products, and health items | Gyms, airports, hotels | Pros: Targets niche markets, convenience for travelers. Cons: Limited appeal in non-travel contexts. |
Custom Merchandise Vending | Sells branded merchandise or unique local products | Events, concerts, tourist attractions | Pros: Enhances brand visibility, unique offerings. Cons: Seasonal demand fluctuations. |
Specialty Item Vending | Focused on niche products like CBD, vegan snacks, or electronics | Health stores, specialty shops | Pros: Captures specific market segments. Cons: Limited audience, may require extensive marketing. |
Food and Beverage Vending
Food and beverage vending machines are highly customizable, allowing businesses to offer a variety of snacks, drinks, and even fresh food options. They are particularly suitable for high-traffic environments like offices, schools, and hospitals where convenience is paramount. When purchasing, consider factors such as supplier relationships for perishable items, machine maintenance, and the ability to adapt offerings to local tastes. Effective inventory management is crucial to minimize waste and maximize profitability.
Electronics Vending
Electronics vending machines are designed to dispense gadgets, accessories, and tech products, making them ideal for locations like airports, malls, and tech stores. These machines cater to tech-savvy consumers looking for convenience and quick access to high-value items. Buyers should evaluate the security features of these machines, as they often house expensive products. Additionally, understanding the target demographic is essential to stock relevant items that drive sales.
Personal Care Vending
These machines focus on dispensing personal care products, such as cosmetics, hygiene items, and health-related goods. They are commonly found in gyms, airports, and hotels, targeting consumers who value convenience while traveling or engaging in fitness activities. When considering this type, B2B buyers should assess the product range and supplier reliability, as well as compliance with health regulations. Marketing strategies should also be tailored to attract the specific audience in these environments.
Custom Merchandise Vending
Custom merchandise vending machines offer branded items or unique local products, making them a popular choice at events, concerts, and tourist attractions. These machines enhance brand visibility and provide a unique shopping experience. Buyers should consider the seasonality of demand and the potential for partnerships with local businesses to keep offerings fresh and appealing. Understanding the target audience’s preferences is essential for successful merchandising.
Specialty Item Vending
Specialty item vending machines focus on niche products, such as CBD items, vegan snacks, or unique electronics. These machines cater to specific market segments and can be found in health stores and specialty shops. B2B buyers need to evaluate market demand and potential competition in their area, as well as the need for targeted marketing strategies to reach the right consumers. The success of these machines often hinges on their ability to offer products that resonate with specific customer interests.
Related Video: Free Custom Vending Machine Setup Tutorial (UEFN) #verse #uefn #fortnite
Key Industrial Applications of custom vending machines
Industry/Sector | Specific Application of Custom Vending Machines | Value/Benefit for the Business | Key Sourcing Considerations for this Application |
---|---|---|---|
Healthcare | Dispensing medical supplies and personal protective equipment | Immediate access to essential items, reducing downtime | Compliance with health regulations, product safety certifications |
Education | Providing snacks and beverages in schools and universities | Enhancing student satisfaction and convenience | Nutritional guidelines adherence, local taste preferences |
Corporate Offices | Offering healthy snacks and beverages in break rooms | Boosting employee morale and productivity | Custom branding options, variety of product offerings |
Retail | Selling niche products like electronics accessories | Expanding product reach without additional staff | Technology integration, payment system compatibility |
Hospitality | Providing quick access to amenities in hotels | Enhancing guest experience and convenience | Customization for local culture, reliable supply chains |
Healthcare
Custom vending machines in healthcare settings provide critical access to medical supplies and personal protective equipment (PPE). By placing these machines in hospitals, clinics, or emergency response areas, healthcare providers can ensure that essential items are readily available, thus minimizing delays in patient care. For international buyers, it’s crucial to source machines that comply with local health regulations and safety standards. Additionally, suppliers should provide certified products to ensure reliability and compliance with health protocols.
Education
In educational institutions, custom vending machines can serve a dual purpose: providing nutritious snacks and beverages while also accommodating students’ diverse dietary needs. Schools and universities can leverage these machines to promote healthy eating habits, ultimately enhancing student satisfaction. Buyers in this sector should consider vending machines that adhere to nutritional guidelines and can be customized to reflect local taste preferences, ensuring greater acceptance among students.
Corporate Offices
Custom vending machines in corporate environments can significantly boost employee morale by offering a variety of healthy snacks and beverages in break rooms. This convenience not only enhances workplace satisfaction but also contributes to increased productivity. When sourcing these machines, businesses should prioritize customization options, allowing for branding that aligns with corporate identity, and ensure a diverse product range to cater to various dietary preferences among employees.
Retail
In the retail sector, custom vending machines can be utilized to sell niche products, such as electronics accessories, without the need for additional staff. This approach allows retailers to expand their product offerings and reach customers in high-traffic areas. B2B buyers should focus on sourcing machines that incorporate advanced technology, such as touchless payment systems and inventory management features, to streamline operations and enhance customer experience.
Hospitality
In the hospitality industry, custom vending machines can enhance guest experiences by providing quick access to amenities like snacks, drinks, and travel essentials. Hotels can place these machines in convenient locations, ensuring guests have what they need without having to leave the premises. Buyers should consider sourcing machines that can be customized to reflect local culture and preferences, as well as establishing reliable supply chains to keep inventory stocked and fresh.
Related Video: Kooler Ice Vending Machines – IM600XL vs. IM1000
Strategic Material Selection Guide for custom vending machines
When selecting materials for custom vending machines, international B2B buyers must consider various factors that impact performance, durability, and compliance with regional standards. Here, we analyze four common materials used in the manufacturing of vending machines, focusing on their properties, advantages, disadvantages, and implications for buyers from diverse regions, including Africa, South America, the Middle East, and Europe.
1. Stainless Steel
Key Properties: Stainless steel is known for its excellent corrosion resistance, high strength, and ability to withstand high temperatures. It is typically rated for temperatures up to 800°C and offers good pressure ratings, making it suitable for various environments.
Pros & Cons: The primary advantage of stainless steel is its durability and resistance to rust, which extends the lifespan of vending machines. However, it can be more expensive than other materials, leading to higher initial costs. Additionally, the manufacturing process can be complex, requiring specialized equipment.
Impact on Application: Stainless steel is ideal for vending machines that dispense food and beverages due to its hygienic properties. It is compatible with various media, including liquids and solids, without risk of contamination.
Considerations for International Buyers: Buyers should ensure compliance with local health and safety regulations, which may specify the use of food-grade stainless steel. Standards such as ASTM A240 for stainless steel sheet and plate should be considered, especially in regions like Europe and North America.
2. Carbon Steel
Key Properties: Carbon steel offers good mechanical properties and is commonly used for structural components. It has a moderate temperature rating but is susceptible to corrosion if not properly coated.
Pros & Cons: Carbon steel is generally more cost-effective than stainless steel, making it an attractive option for budget-conscious buyers. However, its susceptibility to rust and corrosion limits its application in environments with high moisture or exposure to corrosive substances.
Impact on Application: Carbon steel is suitable for non-corrosive applications, such as housing for vending machines that dispense dry goods. Its strength makes it a good choice for structural support.
Considerations for International Buyers: Buyers should consider protective coatings to enhance corrosion resistance. Compliance with standards such as ASTM A36 for structural steel is essential, especially in regions like South America and Africa, where environmental conditions may accelerate corrosion.
3. Aluminum
Key Properties: Aluminum is lightweight, has good corrosion resistance, and possesses a high strength-to-weight ratio. It typically withstands temperatures up to 600°C and is easily machinable.
Pros & Cons: The main advantage of aluminum is its lightweight nature, which simplifies transportation and installation. However, it may not be as durable as stainless steel or carbon steel in high-stress applications, and its cost can vary significantly based on alloy selection.
Impact on Application: Aluminum is suitable for vending machines located in high-traffic areas due to its lightweight, making them easier to relocate or install. It is compatible with various products, including snacks and beverages.
Considerations for International Buyers: Buyers should check for compliance with regional standards such as ASTM B221 for aluminum extrusions. In regions like the Middle East, where temperature fluctuations can be extreme, ensuring the right alloy is crucial for performance.
4. Polycarbonate
Key Properties: Polycarbonate is a durable thermoplastic known for its high impact resistance and transparency. It can withstand temperatures ranging from -40°C to 120°C, making it suitable for various environments.
Pros & Cons: The key advantage of polycarbonate is its lightweight and shatter-resistant properties, making it ideal for vending machine windows. However, it may not be suitable for high-temperature applications and can be more expensive than other plastics.
Impact on Application: Polycarbonate is often used for transparent panels in vending machines, allowing visibility of products while providing protection. It is compatible with various media, including packaged snacks and drinks.
Considerations for International Buyers: Buyers should ensure compliance with safety standards for plastics, such as ASTM D6400 for biodegradable plastics. In regions like Europe, where environmental regulations are stringent, sourcing from compliant suppliers is essential.
Material | Typical Use Case for custom vending machines | Key Advantage | Key Disadvantage/Limitation | Relative Cost (Low/Med/High) |
---|---|---|---|---|
Stainless Steel | Food and beverage dispensing | Excellent corrosion resistance | Higher initial cost | High |
Carbon Steel | Structural components for dry goods | Cost-effective | Susceptible to corrosion | Low |
Aluminum | High-traffic area vending machines | Lightweight and easy to install | Less durable under high stress | Medium |
Polycarbonate | Transparent panels for product visibility | Shatter-resistant and lightweight | Not suitable for high temperatures | Medium |
This guide provides a comprehensive overview of material selection for custom vending machines, emphasizing the importance of aligning material properties with operational needs and regional compliance standards. By carefully evaluating these materials, international B2B buyers can make informed decisions that enhance the performance and longevity of their vending machine investments.
In-depth Look: Manufacturing Processes and Quality Assurance for custom vending machines
Custom vending machines are increasingly seen as versatile solutions for diverse markets, and understanding their manufacturing processes and quality assurance measures is essential for international B2B buyers. This section provides a detailed overview of typical manufacturing stages, key techniques, and relevant quality control standards that ensure these machines meet market demands.
Manufacturing Processes
The manufacturing of custom vending machines involves several key stages, each crucial for producing high-quality, reliable products. These stages include material preparation, forming, assembly, and finishing.
1. Material Preparation
The first step in the manufacturing process is selecting and preparing the materials. Common materials used in vending machines include:
- Steel: Often used for the frame and structural components due to its strength and durability.
- Plastic: Utilized for outer casings and parts that require flexibility or insulation.
- Electronic components: Such as circuit boards and sensors, which are essential for machine functionality.
Material preparation involves cutting, shaping, and treating the materials to ensure they meet the required specifications. This might include processes like welding for metal parts and molding for plastic components.
2. Forming
Once materials are prepared, the next stage is forming. This involves techniques such as:
- CNC Machining: Computer Numerical Control (CNC) machines are used to achieve precise cuts and shapes, ensuring components fit together correctly.
- Injection Molding: Used for creating complex plastic parts quickly and efficiently.
- Bending and Stamping: Often applied to metal sheets to create the machine’s exterior and internal structures.
These techniques not only enhance the quality of the components but also allow for customization to meet specific customer requirements.
3. Assembly
The assembly stage is where all the components come together. This involves:
- Mechanical Assembly: Attaching the frame, doors, and internal components like shelves and product dispensers.
- Electrical Assembly: Installing wiring, circuit boards, and payment systems, ensuring that all electronic components are correctly integrated.
Quality at this stage is critical, as even minor errors can lead to malfunctioning machines. Skilled labor and automated systems work in tandem to ensure accuracy during assembly.
4. Finishing
The final manufacturing stage is finishing, which includes:
- Surface Treatment: Processes such as painting, powder coating, or galvanizing to protect against corrosion and enhance aesthetics.
- Quality Checks: Initial inspections to ensure that the machine meets design specifications and quality standards before it moves to the next phase.
This stage is vital for both the longevity of the machine and customer satisfaction.
Quality Assurance
Quality assurance (QA) is a fundamental aspect of the manufacturing process for custom vending machines. International standards and industry-specific regulations guide this process to ensure that products are safe, reliable, and effective.
Relevant International Standards
-
ISO 9001: This is a widely recognized quality management standard that focuses on meeting customer expectations and delivering satisfaction. Compliance with ISO 9001 demonstrates a commitment to quality and continuous improvement.
-
CE Marking: For machines sold in Europe, obtaining CE marking indicates compliance with EU safety, health, and environmental protection standards. This is essential for market access in European countries.
-
API Standards: Particularly relevant for machines that dispense food or beverages, adherence to American Petroleum Institute standards can be necessary for safety and hygiene.
Quality Control Checkpoints
Quality control (QC) checkpoints throughout the manufacturing process help to identify and rectify issues before the final product is delivered. Key QC checkpoints include:
- Incoming Quality Control (IQC): Ensures that raw materials and components meet specified standards before they enter the production process.
- In-Process Quality Control (IPQC): Conducted during the manufacturing stages to monitor processes and detect any deviations from quality standards in real-time.
- Final Quality Control (FQC): A comprehensive inspection of the finished product to ensure it meets all specifications and standards before shipping.
Common Testing Methods
Testing methods vary depending on the components and the intended use of the vending machines. Common methods include:
- Electrical Testing: To ensure that all electronic components function correctly.
- Mechanical Testing: Assessing the durability and functionality of mechanical parts.
- Safety Testing: Conducting tests to ensure compliance with safety standards, particularly for machines that dispense consumables.
Verification of Supplier QC
For international B2B buyers, verifying the quality assurance processes of suppliers is crucial. Here are several strategies:
- Audits: Conduct regular audits of suppliers to assess their compliance with quality standards and practices. This can be done through on-site visits or remote assessments.
- Reports and Certifications: Request detailed reports on quality control measures, including certifications like ISO 9001 or CE marking documentation.
- Third-Party Inspections: Engage third-party inspection services to evaluate the manufacturing processes and quality control measures employed by suppliers.
QC and Certification Nuances for International Buyers
B2B buyers from Africa, South America, the Middle East, and Europe should be aware of specific nuances in quality control and certification. For instance:
- Understanding Regional Standards: Familiarize yourself with local regulations and standards that may differ from international norms. This includes health and safety regulations specific to each market.
- Logistics and Compliance: Ensure that the logistics of importing vending machines comply with both the exporting country’s regulations and those of the importing country.
- Cultural Sensitivity: Recognize that different regions may have varying expectations regarding quality and service, which can affect buyer-supplier relationships.
By comprehensively understanding the manufacturing processes and quality assurance measures, international B2B buyers can make informed decisions, ensuring that the custom vending machines they procure meet their operational needs and comply with relevant standards.
Related Video: Most Satisfying Factory Production Processes And Heavy-Duty Factory Machines!
Comprehensive Cost and Pricing Analysis for custom vending machines Sourcing
Understanding the cost structure and pricing dynamics of custom vending machines is crucial for international B2B buyers, especially those operating in diverse markets such as Africa, South America, the Middle East, and Europe. This analysis provides insights into the various cost components, price influencers, and strategic tips for buyers to optimize their sourcing decisions.
Cost Components of Custom Vending Machines
-
Materials: The choice of materials significantly impacts the overall cost. High-quality metals, plastics, and electronic components are essential for durability and performance. Sourcing locally can sometimes reduce costs, but buyers must balance this with quality and availability.
-
Labor: Labor costs vary by region and can influence the final price. In countries with higher labor costs, such as Western European nations, buyers may face increased prices compared to regions with lower labor costs, like parts of Asia or South America.
-
Manufacturing Overhead: This includes expenses related to factory operations, utilities, and administrative costs. Understanding the manufacturer’s overhead can provide insights into potential pricing strategies and negotiations.
-
Tooling: Custom vending machines often require specialized tooling, which can be a significant upfront cost. Buyers should inquire about tooling costs and whether they can be amortized over large orders.
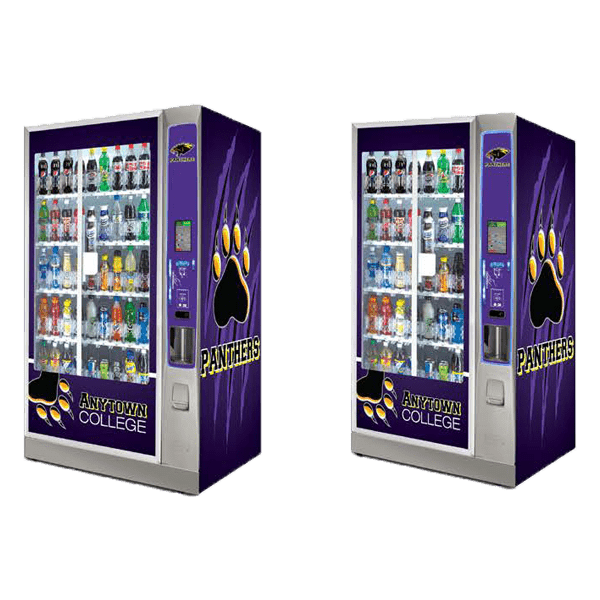
Illustrative Image (Source: Google Search)
-
Quality Control (QC): Ensuring that the machines meet specific standards is critical. QC processes can add to the cost but are necessary to mitigate risks associated with product failures, especially in regulated markets.
-
Logistics: Shipping costs can vary widely based on distance, shipping method, and weight. Buyers should consider Incoterms and their implications on cost and risk management during transportation.
-
Margin: Manufacturers will typically add a margin to cover their costs and ensure profitability. Understanding the typical margin in the industry can help buyers gauge whether they are receiving fair pricing.
Price Influencers
-
Volume/MOQ: The minimum order quantity (MOQ) can greatly influence pricing. Higher volumes often lead to better per-unit pricing, so negotiating larger orders or joining forces with other buyers can yield cost savings.
-
Specifications/Customization: The level of customization required can significantly impact the price. More intricate designs or features typically lead to higher costs, so buyers should clearly define their requirements to avoid unexpected expenses.
-
Materials and Quality Certifications: The sourcing of certified materials may increase costs but can be essential for compliance in certain markets. Buyers should weigh the benefits of certification against the added costs.
-
Supplier Factors: The reputation and reliability of the supplier can influence pricing. Established suppliers may command higher prices due to their track record, while new entrants might offer lower prices to gain market share.
-
Incoterms: Understanding the implications of different Incoterms (e.g., FOB, CIF) is essential for calculating total costs. Incoterms dictate responsibilities for shipping, insurance, and tariffs, all of which can affect the final price.
Buyer Tips
-
Negotiation: Engage in active negotiations with suppliers to secure better pricing. Understanding the supplier’s cost structure can provide leverage during discussions.
-
Cost-Efficiency: Aim for cost-efficient sourcing by considering total cost of ownership (TCO), which includes not just purchase price but also maintenance, operation, and disposal costs.
-
Pricing Nuances: Be aware of currency fluctuations and local economic conditions that may affect pricing. Buyers in volatile markets should consider locking in prices when possible.
-
Build Relationships: Establishing long-term relationships with suppliers can lead to better pricing, improved service, and exclusive offers.
-
Research and Benchmarking: Conduct market research to benchmark prices against industry standards. This can help buyers identify overpricing or find more competitive suppliers.
Disclaimer
Prices and costs mentioned in this analysis are indicative and can vary significantly based on specific requirements, supplier negotiations, and market conditions. Always conduct thorough due diligence before making purchasing decisions.
Spotlight on Potential custom vending machines Manufacturers and Suppliers
This section offers a look at a few manufacturers active in the ‘custom vending machines’ market. This is a representative sample for illustrative purposes; B2B buyers must conduct their own extensive due diligence before any engagement. Information is synthesized from public sources and general industry knowledge.
Essential Technical Properties and Trade Terminology for custom vending machines
Key Technical Properties of Custom Vending Machines
When considering custom vending machines, understanding their technical specifications is crucial for ensuring optimal performance and durability. Below are several critical properties that B2B buyers should evaluate:
- Material Grade
– Definition: This refers to the type of materials used in the construction of the vending machine, such as stainless steel, aluminum, or high-density plastic.
– Importance: The material grade affects the machine’s durability, resistance to corrosion, and overall aesthetic appeal. For operations in diverse climates—like those in Africa or South America—selecting weather-resistant materials is vital to ensure longevity.
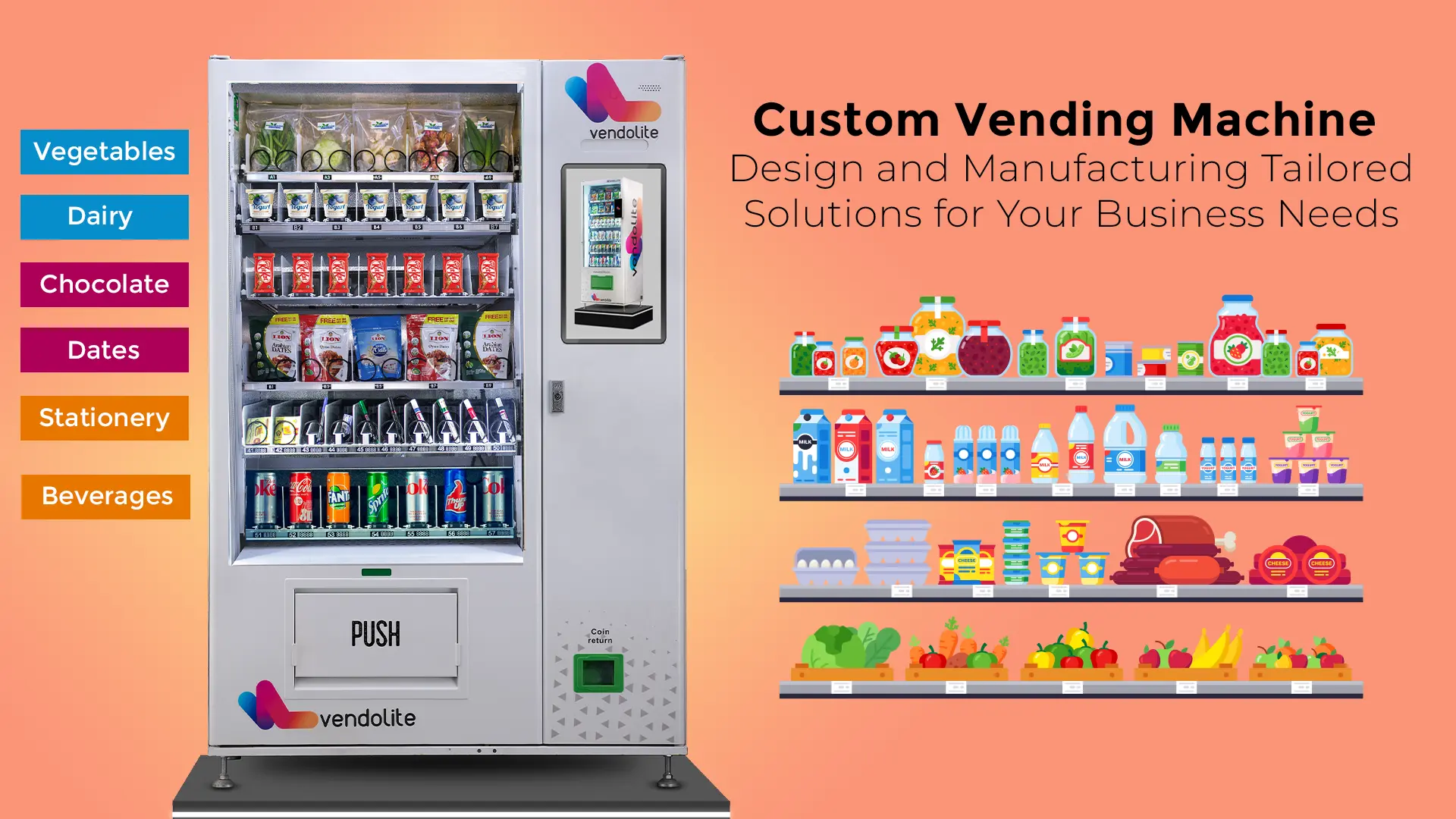
Illustrative Image (Source: Google Search)
-
Tolerance
– Definition: Tolerance indicates the allowable variation in dimensions and specifications of machine components.
– Importance: Precise tolerances ensure that components fit together correctly, which is essential for the smooth operation of the machine. This is particularly important for custom designs that require specific configurations to meet unique customer needs. -
Power Consumption
– Definition: This refers to the amount of electricity the vending machine consumes during operation.
– Importance: Understanding power consumption helps buyers evaluate operational costs and energy efficiency. Machines with lower power consumption are ideal for areas with high electricity costs or limited power supply, such as some regions in the Middle East. -
Capacity
– Definition: Capacity denotes the maximum number of products the vending machine can hold, typically measured in terms of product slots or total weight.
– Importance: Selecting the right capacity is essential for meeting consumer demand without frequent restocking. This is especially relevant in high-traffic locations across Europe, where demand can fluctuate significantly. -
User Interface
– Definition: This encompasses the touchscreen or button panel through which customers interact with the vending machine.
– Importance: A user-friendly interface enhances customer experience and can lead to increased sales. Custom options can cater to different languages and payment methods, making machines more accessible in diverse markets. -
Connectivity Features
– Definition: This includes options for internet connectivity, such as Wi-Fi or Bluetooth.
– Importance: Connectivity features allow for remote monitoring of inventory levels and machine performance, enabling proactive maintenance and inventory management. This is particularly beneficial for businesses operating multiple machines across vast regions.
Common Trade Terminology in the Vending Machine Industry
Understanding industry jargon is essential for effective communication and negotiation in the vending machine market. Here are several key terms:
-
OEM (Original Equipment Manufacturer)
– Definition: A company that produces parts and equipment that may be marketed by another manufacturer.
– Significance: Knowing whether a vending machine supplier is an OEM can impact the quality and customization options available. OEMs typically provide better support for customized solutions. -
MOQ (Minimum Order Quantity)
– Definition: The smallest quantity of a product that a supplier is willing to sell.
– Significance: Understanding MOQ is crucial for budgeting and inventory management. Buyers should negotiate MOQs that align with their operational needs without overcommitting resources. -
RFQ (Request for Quotation)
– Definition: A document sent to suppliers to request pricing and terms for specific products or services.
– Significance: Issuing an RFQ allows buyers to gather competitive pricing and terms from multiple suppliers, facilitating better purchasing decisions. -
Incoterms (International Commercial Terms)
– Definition: A set of predefined commercial terms published by the International Chamber of Commerce (ICC) that clarify the responsibilities of buyers and sellers in international transactions.
– Significance: Familiarity with Incoterms helps buyers understand shipping costs, risk management, and delivery responsibilities, which is crucial when sourcing machines from global suppliers. -
Lead Time
– Definition: The amount of time it takes from placing an order until it is delivered.
– Significance: Understanding lead time is essential for effective inventory planning. Longer lead times can impact sales and customer satisfaction, particularly in fast-moving markets. -
Warranty
– Definition: A guarantee provided by the manufacturer regarding the condition and performance of the vending machine for a specific period.
– Significance: Warranties are crucial for mitigating risk. Buyers should seek machines with comprehensive warranties to protect against manufacturing defects and ensure long-term support.
By mastering these technical properties and industry terms, international B2B buyers can make informed decisions that enhance their vending machine operations.
Navigating Market Dynamics, Sourcing Trends, and Sustainability in the custom vending machines Sector
Market Overview & Key Trends
The custom vending machine sector is experiencing a notable transformation driven by technological advancements and evolving consumer preferences. International B2B buyers, especially from regions like Africa, South America, the Middle East, and Europe, should be aware of several key trends shaping the market.
1. Integration of Smart Technology: The rise of IoT (Internet of Things) has revolutionized vending machines, allowing for features such as cashless payments, remote inventory management, and personalized customer experiences. Machines equipped with data analytics can monitor sales trends and customer preferences, enabling operators to optimize product offerings.
2. Increased Customization: Businesses are increasingly seeking vending machines tailored to specific markets or consumer demographics. Customization extends to machine design, product selection, and branding, providing companies a competitive edge in attracting and retaining customers.
3. Sustainability and Eco-friendliness: There is a growing demand for vending machines that utilize sustainable materials and energy-efficient technologies. This trend resonates particularly well with environmentally conscious consumers and businesses looking to enhance their corporate social responsibility (CSR) profile.
4. Emerging Markets: Regions like Africa and South America are witnessing rapid urbanization and changing lifestyles, leading to increased demand for convenient food and beverage options. This presents a significant opportunity for international buyers looking to enter these burgeoning markets.
5. Diverse Product Offerings: The scope of products available through vending machines is expanding beyond traditional snacks and beverages to include healthier options, electronics, and even beauty products. This diversification caters to a wider array of customer needs and preferences.
Sustainability & Ethical Sourcing in B2B
The importance of sustainability in the custom vending machine sector cannot be overstated. As global consumers become more environmentally conscious, B2B buyers must prioritize sustainability in their sourcing strategies.
Environmental Impact: The production and operation of vending machines contribute to carbon footprints through manufacturing processes and energy consumption. Buyers should seek machines that incorporate energy-efficient technologies, such as LED lighting and solar panels, to mitigate these impacts.
Ethical Supply Chains: Establishing ethical supply chains is essential for fostering trust and ensuring compliance with international labor standards. Buyers should conduct thorough due diligence on suppliers, ensuring they adhere to ethical practices and contribute positively to local communities.
Green Certifications and Materials: Utilizing materials that are recyclable or sourced from sustainable origins can enhance a brand’s reputation. Certifications like FSC (Forest Stewardship Council) for wood products or ISO 14001 for environmental management systems can be critical in verifying a supplier’s commitment to sustainability.
By prioritizing sustainability and ethical sourcing, international buyers not only comply with regulatory standards but also align with the values of their customers, thereby enhancing brand loyalty and marketability.
Brief Evolution/History
The custom vending machine industry has evolved significantly since its inception. Originally designed to dispense simple snacks and drinks, vending machines have transformed into sophisticated retail solutions. The introduction of electronic payment systems in the late 20th century marked a turning point, allowing for cashless transactions and improving user convenience.
In recent years, the integration of smart technology has further advanced the sector, enabling remote monitoring and data-driven decision-making. This evolution reflects broader trends in retail and consumer behavior, making vending machines a viable option for businesses looking to innovate and meet changing market demands. For international B2B buyers, understanding this evolution is crucial in identifying opportunities for investment and partnership in a rapidly growing market.
Related Video: Global Trade & Logistics – What is Global Trade?
Frequently Asked Questions (FAQs) for B2B Buyers of custom vending machines
-
How can I effectively vet suppliers for custom vending machines?
Vetting suppliers is crucial for ensuring quality and reliability. Start by researching potential suppliers through online marketplaces and industry directories. Look for reviews, ratings, and testimonials from other buyers. Request references and verify their business credentials, including certifications and compliance with international standards. Consider conducting factory visits or virtual inspections to assess their operations. Finally, engage in direct communication to evaluate their responsiveness and willingness to address your specific needs. -
What customization options should I consider when sourcing vending machines?
Customization can significantly enhance the functionality and appeal of your vending machines. Consider factors such as size, design, branding, and product selection. Discuss with suppliers the possibility of incorporating advanced technology, such as cashless payment systems, touchscreens, or energy-efficient components. Additionally, ensure that the machines can accommodate a diverse range of products that cater to local preferences. Collaborate closely with suppliers to create a tailored solution that aligns with your business model and target market. -
What are the typical minimum order quantities (MOQ) and lead times for custom vending machines?
MOQs for custom vending machines can vary widely based on the supplier and the complexity of the design. Generally, you can expect MOQs to range from 10 to 100 units. Lead times also differ, typically spanning 4 to 12 weeks, depending on customization requirements and supplier capacity. It is essential to discuss these factors upfront to align your purchasing plans with the supplier’s production schedule and avoid delays in launching your vending operations. -
What payment methods are commonly accepted by vending machine suppliers?
Payment methods can vary by supplier and region. Common options include wire transfers, letters of credit, and online payment platforms. It is advisable to negotiate favorable payment terms, such as a partial upfront payment with the balance due upon delivery or after installation. Ensure that the payment method you choose is secure and provides recourse in case of disputes. Always clarify the currency and any potential fees associated with international transactions to avoid unexpected costs. -
How can I ensure quality assurance and certifications for my custom vending machines?
Quality assurance is vital for maintaining product standards. Request documentation from suppliers that confirms compliance with relevant safety and quality certifications, such as ISO, CE, or local regulatory standards. Consider implementing a quality control process that includes pre-shipment inspections or third-party audits to verify that machines meet your specifications. Establish clear quality expectations in your contracts to hold suppliers accountable and protect your investment. -
What logistics considerations should I keep in mind when importing vending machines?
Logistics play a critical role in the successful importation of vending machines. Assess shipping methods, including air freight for speed or sea freight for cost-effectiveness, and choose a reliable freight forwarder experienced in handling machinery. Understand the customs regulations in your destination country, including any duties and taxes that may apply. Prepare all necessary documentation, such as bills of lading and invoices, to facilitate smooth customs clearance and avoid delays. -
How should I handle disputes with vending machine suppliers?
Disputes can arise from various issues, including quality concerns or delivery delays. The first step is to communicate directly with the supplier to resolve the matter amicably. If direct communication fails, refer to your contract for dispute resolution procedures, which may include mediation or arbitration. Document all communications and agreements related to the dispute for reference. It’s also wise to establish a clear dispute resolution clause in your contracts to protect your interests in future dealings. -
What are the best practices for maintaining a long-term relationship with my vending machine supplier?
Building a long-term relationship with your supplier is beneficial for both parties. Regular communication is key; keep suppliers informed about your needs and feedback on their products. Establishing a partnership mindset can lead to better pricing, priority service, and exclusive product offerings. Consider collaborating on promotional strategies or product launches to enhance mutual success. Additionally, periodically reviewing performance and addressing any concerns proactively can strengthen trust and reliability in your partnership.
Strategic Sourcing Conclusion and Outlook for custom vending machines
In the evolving landscape of custom vending machines, strategic sourcing emerges as a cornerstone for success. By fostering strong supplier relationships and navigating legal frameworks, international B2B buyers can significantly enhance their operational efficiency and profitability. It is essential to prioritize suppliers who offer a diverse range of products and demonstrate reliability to stay competitive in the market.
Key Takeaways:
– Cultivate Partnerships: Strong supplier relationships lead to better pricing, exclusive products, and collaborative growth opportunities.
– Ensure Compliance: Understanding local regulations is crucial to avoid penalties and maintain a positive reputation.
– Adaptability is Key: A diverse product offering allows businesses to meet changing consumer demands effectively.
As we look to the future, the potential for innovation in the vending sector is vast. International buyers, particularly from Africa, South America, the Middle East, and Europe, should embrace these insights to position themselves for sustainable growth. Invest in strategic sourcing today to secure a competitive edge and drive your vending machine business forward.