Your Ultimate Guide to Sourcing Small Vending Machine For
Guide to Small Vending Machine For Sale
- Introduction: Navigating the Global Market for small vending machine for sale
- Understanding small vending machine for sale Types and Variations
- Key Industrial Applications of small vending machine for sale
- Strategic Material Selection Guide for small vending machine for sale
- In-depth Look: Manufacturing Processes and Quality Assurance for small vending machine for sale
- Comprehensive Cost and Pricing Analysis for small vending machine for sale Sourcing
- Spotlight on Potential small vending machine for sale Manufacturers and Suppliers
- Essential Technical Properties and Trade Terminology for small vending machine for sale
- Navigating Market Dynamics, Sourcing Trends, and Sustainability in the small vending machine for sale Sector
- Frequently Asked Questions (FAQs) for B2B Buyers of small vending machine for sale
- Strategic Sourcing Conclusion and Outlook for small vending machine for sale
Introduction: Navigating the Global Market for small vending machine for sale
In an increasingly competitive global market, small vending machines have emerged as a versatile solution for businesses seeking to enhance customer engagement and streamline operations. These compact units not only serve as efficient points of sale but also cater to the growing demand for convenience in various sectors, including hospitality, education, and corporate environments. As international B2B buyers, particularly from Africa, South America, the Middle East, and Europe, understanding the nuances of sourcing small vending machines can significantly influence your business’s bottom line.
This comprehensive guide aims to equip you with actionable insights into the world of small vending machines. You will explore the diverse types available, ranging from traditional snack dispensers to advanced smart machines equipped with cashless payment systems. We will delve into materials and manufacturing processes, ensuring you are well-informed about quality standards and compliance requirements.
Moreover, the guide will provide an overview of reputable suppliers worldwide, highlighting key players in different regions, including Poland and Indonesia. You’ll gain insights into cost structures, enabling you to make budget-conscious decisions while assessing the market landscape for potential growth opportunities.
To further empower your sourcing strategy, we will address common FAQs, clearing up any uncertainties you may have. By the end of this guide, you will be positioned to make informed, strategic decisions that align with your business goals, ensuring you maximize the benefits of investing in small vending machines.
Understanding small vending machine for sale Types and Variations
Type Name | Key Distinguishing Features | Primary B2B Applications | Brief Pros & Cons for Buyers |
---|---|---|---|
Snack Vending Machines | Compact design, various snack options, customizable shelves | Offices, schools, gyms | Pros: High demand, low maintenance. Cons: Limited to snacks only. |
Beverage Vending Machines | Refrigerated units, multiple drink selections | Cafes, convenience stores, airports | Pros: High turnover, popular in high-traffic areas. Cons: Requires electricity. |
Healthy Food Vending Machines | Focus on fresh, nutritious options, often refrigerated | Workplaces, universities, health clubs | Pros: Appeals to health-conscious consumers. Cons: Higher initial cost, perishable inventory. |
Combination Vending Machines | Dual-functionality for snacks and beverages | Malls, large offices, event venues | Pros: Versatile offerings, maximizes space. Cons: More complex maintenance. |
Specialty Vending Machines | Unique products (e.g., electronics, cosmetics) | Airports, malls, high-end retail | Pros: Niche market appeal, higher profit margins. Cons: Limited audience, potential for high inventory costs. |
Snack Vending Machines
Snack vending machines are designed to offer a variety of packaged snacks, from chips to candy bars. Their compact size makes them suitable for placement in various environments, including offices, schools, and gyms. B2B buyers should consider the demand for snack options in their target locations, as these machines typically require minimal maintenance and can generate steady revenue. However, their limited product range may not appeal to all consumer preferences.
Beverage Vending Machines
These machines focus on dispensing a wide range of beverages, including soft drinks, juices, and bottled water. They are often refrigerated to ensure product freshness and are best suited for high-traffic areas such as cafes, convenience stores, and airports. For B2B buyers, the potential for high turnover and consistent demand makes beverage vending machines an attractive investment. However, they do require a reliable power source, which should be factored into placement decisions.
Healthy Food Vending Machines
With a growing trend towards health and wellness, these machines offer fresh and nutritious food options, including salads and wraps. They are ideal for workplaces, universities, and health clubs where there is a demand for healthier eating choices. B2B buyers should weigh the appeal of health-oriented products against the higher initial costs and the challenges of managing perishable inventory. This type of machine can differentiate a business in a crowded market.
Combination Vending Machines
Combination vending machines provide both snacks and beverages in one unit, maximizing the use of space and offering a versatile selection. These machines are suitable for environments like malls, large offices, and event venues where diverse consumer needs exist. For B2B buyers, the ability to cater to a wider audience can lead to increased sales. However, the complexity of maintenance and potential for higher operational costs should be carefully considered.
Specialty Vending Machines
Specialty vending machines cater to niche markets by offering unique products such as electronics, cosmetics, or even gourmet food items. They are often found in airports, malls, and high-end retail spaces where consumers seek out exclusive items. B2B buyers can benefit from higher profit margins, but they must also consider the limited audience and potential for higher inventory costs. Understanding the target market is crucial for success in this segment.
Related Video: How to Make a Mini Vending Machine Using Standard Printer, 8.5 x11, Canva and Photoshop Instructions
Key Industrial Applications of small vending machine for sale
Industry/Sector | Specific Application of small vending machine for sale | Value/Benefit for the Business | Key Sourcing Considerations for this Application |
---|---|---|---|
Corporate Offices | Snack and beverage distribution in break rooms | Enhances employee satisfaction and productivity | Product variety, payment options, and maintenance support |
Healthcare Facilities | Dispensing essential medical supplies | Provides quick access to necessary items | Compliance with health regulations, sterilization options |
Educational Institutions | Providing food and drinks for students and staff | Supports student well-being and convenience | Nutritional options, payment systems, and durability |
Manufacturing Plants | Offering snacks and drinks on the production floor | Boosts morale and reduces downtime | Robust construction, ease of restocking, and energy efficiency |
Public Transport Hubs | Vending services for commuters | Increases revenue through high foot traffic | Location strategy, product selection, and security features |
Corporate Offices
In corporate settings, small vending machines serve as convenient snack and beverage sources in break rooms. They enhance employee satisfaction, contributing to a positive workplace culture and increased productivity. For international B2B buyers, it’s crucial to consider product variety that caters to diverse tastes and dietary requirements, as well as reliable payment options (like cashless transactions) to accommodate modern workforce preferences. Maintenance support is also vital to ensure machines remain operational without significant downtime.
Healthcare Facilities
In healthcare environments, small vending machines can dispense essential medical supplies, such as gloves, masks, and sanitizers, in addition to traditional snacks. This application addresses the urgent need for quick access to supplies, thereby improving operational efficiency. Buyers in this sector must prioritize compliance with health regulations and consider options for sterilization to maintain hygiene. The reliability of the vending machine is also essential, as healthcare settings require consistent availability of supplies.
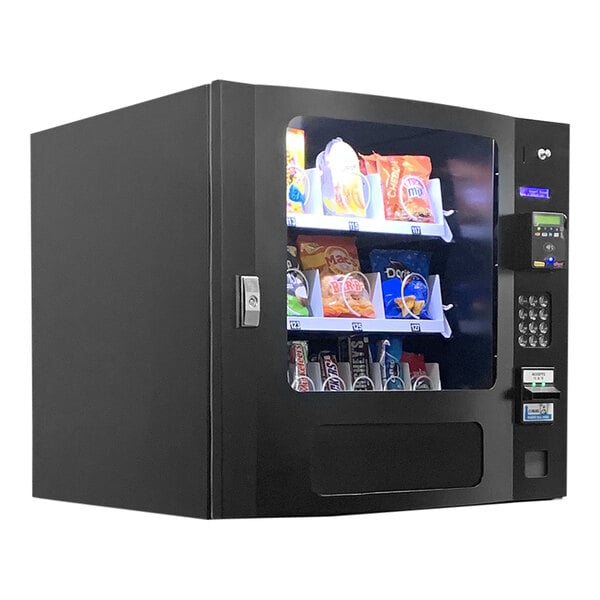
Illustrative Image (Source: Google Search)
Educational Institutions
Educational institutions utilize small vending machines to provide food and beverages to students and staff conveniently. This application supports student well-being, ensuring they have access to nutrition throughout the day. B2B buyers in this sector should focus on offering a variety of nutritional options that cater to different dietary needs, ensuring compliance with local health standards. Additionally, the durability of the machines is important, given the high traffic and potential for misuse in school environments.
Manufacturing Plants
In manufacturing plants, small vending machines offer a convenient solution for providing snacks and drinks directly on the production floor. This application boosts employee morale and reduces downtime by allowing workers to quickly refuel during breaks. Buyers should seek machines with robust construction to withstand industrial environments, as well as features that facilitate easy restocking and energy efficiency to minimize operational costs.
Public Transport Hubs
Small vending machines in public transport hubs cater to the needs of commuters, providing easy access to snacks and beverages. This application capitalizes on high foot traffic, significantly increasing revenue potential for businesses. When sourcing machines for this environment, buyers must consider strategic placement for maximum visibility and accessibility, a diverse product selection to meet varied consumer preferences, and security features to prevent theft or vandalism.
Related Video: How to Start a Vending Machine Business, Cost, Tips, How Much You Make
Strategic Material Selection Guide for small vending machine for sale
When selecting materials for small vending machines, international B2B buyers must consider various factors such as durability, cost, and compliance with regional standards. Below is an analysis of four common materials used in the construction of small vending machines, focusing on their properties, advantages, disadvantages, and specific considerations for buyers from Africa, South America, the Middle East, and Europe.
1. Stainless Steel
Key Properties: Stainless steel is known for its excellent corrosion resistance, high strength, and ability to withstand a wide range of temperatures. It typically has a temperature rating up to 800°C and can handle moderate pressure levels.
Pros & Cons: The primary advantage of stainless steel is its durability and resistance to rust and corrosion, making it ideal for environments with high humidity or exposure to food and beverages. However, it is more expensive than other materials and can be challenging to fabricate, which may increase manufacturing complexity.
Impact on Application: Stainless steel is suitable for vending machines that dispense food and beverages, as it does not react with these media, ensuring safety and hygiene.
Considerations for International Buyers: Buyers should ensure compliance with food safety standards in their respective regions, such as the European Union’s CE marking or the FDA regulations in the United States. Additionally, understanding the grades of stainless steel (e.g., 304, 316) is crucial, as different grades offer varying levels of corrosion resistance.
2. Powder-coated Steel
Key Properties: Powder-coated steel combines the strength of steel with a protective powder coating that enhances its resistance to corrosion and scratches. It can withstand temperatures up to 200°C.
Pros & Cons: This material is cost-effective and offers a variety of colors and finishes, making it aesthetically pleasing. However, while it is resistant to corrosion, the coating can chip or scratch, exposing the underlying steel to rust.
Impact on Application: Powder-coated steel is suitable for indoor vending machines or those placed in dry environments. It is less ideal for outdoor applications unless additional protective measures are taken.
Considerations for International Buyers: Buyers should consider regional climate conditions when selecting powder-coated steel. Compliance with local standards regarding coatings and finishes is also essential, particularly in regions with stringent environmental regulations.
3. Aluminum
Key Properties: Aluminum is lightweight, corrosion-resistant, and has good thermal conductivity. It can handle temperatures up to 250°C and is not prone to rust.
Pros & Cons: The lightweight nature of aluminum makes it easy to transport and install. However, it is softer than steel, which may affect its durability under heavy use or in high-traffic areas.
Impact on Application: Aluminum is suitable for vending machines that require mobility or are designed for temporary setups. It is also a good choice for machines that dispense non-corrosive products.
Considerations for International Buyers: Buyers should ensure that the aluminum used meets the relevant standards in their regions, such as ASTM or ISO standards. Additionally, understanding the alloy composition is critical, as different alloys offer varying strength and corrosion resistance.
4. High-Density Polyethylene (HDPE)
Key Properties: HDPE is a thermoplastic known for its high strength-to-density ratio and excellent chemical resistance. It can withstand temperatures up to 120°C and is resistant to many solvents and acids.
Pros & Cons: HDPE is lightweight, cost-effective, and easy to mold into complex shapes, making it suitable for custom designs. However, it may not be as durable as metal options and can be less aesthetically appealing.
Impact on Application: HDPE is ideal for vending machines that dispense non-food items or in environments where chemical exposure is a concern.
Considerations for International Buyers: Buyers should verify that HDPE complies with local regulations regarding plastic materials, especially in food-related applications. Understanding the recycling options available in their regions is also important for sustainability considerations.
Summary Table
Material | Typical Use Case for small vending machine for sale | Key Advantage | Key Disadvantage/Limitation | Relative Cost (Low/Med/High) |
---|---|---|---|---|
Stainless Steel | Food and beverage vending machines | Excellent corrosion resistance, durable | Higher cost, complex fabrication | High |
Powder-coated Steel | Indoor vending machines | Cost-effective, aesthetic versatility | Coating can chip, exposing steel to rust | Medium |
Aluminum | Mobile or temporary vending machines | Lightweight, easy to transport | Softer than steel, less durable | Medium |
High-Density Polyethylene (HDPE) | Non-food item vending machines | Lightweight, cost-effective | Less durable, may lack aesthetic appeal | Low |
This guide provides essential insights into material selection for small vending machines, helping international B2B buyers make informed decisions tailored to their specific market needs and regulatory environments.
In-depth Look: Manufacturing Processes and Quality Assurance for small vending machine for sale
When considering the procurement of small vending machines, understanding the manufacturing processes and quality assurance protocols is crucial for B2B buyers. This knowledge not only ensures that the products meet the necessary standards but also helps in establishing a reliable supply chain. Below is an in-depth exploration of typical manufacturing processes, quality control measures, and actionable insights for international buyers.
Manufacturing Processes
The manufacturing of small vending machines involves several critical stages, each contributing to the overall quality and functionality of the final product.
1. Material Preparation
The first step in the manufacturing process is the selection and preparation of materials. Common materials used include:
– Steel and Aluminum: For the frame and outer casing, providing durability and resistance to vandalism.
– Plastic Components: Used for internal parts and dispensing mechanisms, ensuring lightweight and cost-effectiveness.
– Electronic Components: Including payment systems and sensors, which are crucial for operational efficiency.
Buyers should ensure that suppliers source materials that comply with international standards for safety and environmental impact.
2. Forming
Forming is the stage where raw materials are shaped into components. Key techniques include:
– Laser Cutting: Provides precision in cutting metal sheets for the machine casing.
– Injection Molding: Used for creating plastic parts, ensuring uniformity and strength.
– Bending and Welding: Essential for assembling the frame and ensuring structural integrity.
Understanding these techniques allows buyers to assess the technological capabilities of potential suppliers.
3. Assembly
Once components are formed, the assembly process begins. This involves:
– Mechanical Assembly: Connecting the frame, electronic components, and dispensing mechanisms.
– Electrical Assembly: Installing wiring and payment systems, ensuring all electronic parts function correctly.
Buyers should inquire about the assembly line’s efficiency and whether it employs automated processes, which can enhance consistency and reduce labor costs.
4. Finishing
Finishing touches are vital for both aesthetics and protection. This stage includes:
– Painting and Coating: Providing corrosion resistance and appealing visual design.
– Quality Checks: Conducted at each stage to ensure that the product meets the desired specifications.
B2B buyers should look for suppliers that implement strict quality checks during this phase to guarantee the final product’s durability and visual appeal.
Quality Assurance
Quality assurance (QA) is essential for ensuring that small vending machines meet both international standards and specific industry requirements. Here are key aspects of QA that buyers should consider:
International Standards
Adhering to recognized standards can significantly impact product reliability. Important certifications include:
– ISO 9001: Focuses on quality management systems and ensures that manufacturers consistently meet customer and regulatory requirements.
– CE Marking: Indicates compliance with European health, safety, and environmental protection standards.
Buyers from Europe, Africa, South America, and the Middle East should prioritize suppliers with these certifications to mitigate risks associated with product failures.
Industry-Specific Standards
In addition to general certifications, certain standards may be relevant depending on the market:
– API Standards: For vending machines dispensing food products, ensuring safety and compliance with food handling regulations.
Quality Control Checkpoints
Effective quality control involves multiple checkpoints throughout the manufacturing process:
– Incoming Quality Control (IQC): Inspects raw materials upon arrival to ensure they meet specified requirements.
– In-Process Quality Control (IPQC): Monitors the manufacturing process itself, checking for defects and ensuring adherence to specifications.
– Final Quality Control (FQC): Conducts thorough inspections of the finished product before shipping.
Establishing a clear understanding of these checkpoints helps buyers assess the reliability of potential suppliers.
Common Testing Methods
Various testing methods are employed to ensure product quality:
– Functionality Testing: Verifying that all mechanical and electronic components operate as intended.
– Durability Testing: Simulating real-world usage conditions to ensure that the machine can withstand wear and tear.
– Safety Testing: Assessing compliance with safety regulations, particularly for electrical components.
Buyers should request detailed reports on these testing methods to evaluate the quality assurance processes of their suppliers.
Verifying Supplier Quality Control
To ensure that suppliers maintain high standards of quality control, B2B buyers can employ several strategies:
Audits and Reports
Conducting regular audits of suppliers can provide insights into their quality control processes. Buyers should:
– Request documentation on quality management systems.
– Schedule on-site visits to observe manufacturing practices.
Third-Party Inspections
Engaging independent third-party inspection services can offer an unbiased assessment of a supplier’s quality control measures. This is particularly beneficial for international buyers who may not have the resources to conduct thorough audits themselves.
Regional Considerations
Different regions may have unique nuances regarding quality control and certifications. For example:
– Africa: Buyers should be aware of local regulations and standards that may differ significantly from international norms.
– South America: Consideration of trade agreements that may affect compliance requirements.
– Middle East: Regulatory bodies may impose additional certifications for electrical products.
– Europe (e.g., Poland): Emphasis on CE marking and compliance with EU directives.
Understanding these regional differences can help buyers make informed decisions and ensure that their suppliers adhere to the necessary standards.
Conclusion
In the competitive landscape of small vending machines, understanding the intricacies of manufacturing processes and quality assurance is vital for international B2B buyers. By focusing on the key stages of production, relevant standards, and rigorous quality control measures, buyers can ensure they select suppliers that deliver high-quality products. This proactive approach not only mitigates risks but also enhances the overall success of their vending machine procurement strategies.
Related Video: SMART Quality Control for Manufacturing
Comprehensive Cost and Pricing Analysis for small vending machine for sale Sourcing
Understanding the Cost Structure of Small Vending Machines
When sourcing small vending machines, understanding the cost components involved is crucial for making informed purchasing decisions. The primary cost elements include:
-
Materials: This encompasses the raw materials used in manufacturing, such as metal, plastic, and electronic components. The quality and source of these materials significantly affect the overall cost. Local suppliers may offer lower prices, but importing high-quality materials might be necessary for durability.
-
Labor: Labor costs can vary widely based on geographic location and production volume. In regions with lower labor costs, such as parts of Africa and South America, manufacturers can offer competitive pricing. However, consider the skill level of the workforce, as specialized labor may command higher wages.
-
Manufacturing Overhead: This includes indirect costs such as utilities, rent, and administrative expenses associated with production. Understanding a supplier’s overhead structure can provide insights into their pricing strategy.
-
Tooling: Initial costs for molds and machinery used in production can be substantial, particularly for customized vending machines. These costs should be amortized over the expected production volume to determine their impact on unit pricing.
-
Quality Control (QC): Ensuring product quality involves costs related to inspections, testing, and certifications. High-quality machines often come with certifications that assure buyers of their reliability, but these certifications may add to the initial price.
-
Logistics: Transportation and handling costs can significantly influence the final price. Factors such as shipping distance, chosen Incoterms, and mode of transport (air, sea, or land) play critical roles in logistics costs.
-
Margin: Suppliers typically add a profit margin to the total cost of production. This margin can vary based on market conditions, competition, and the supplier’s business strategy.
Key Price Influencers
Several factors can influence the pricing of small vending machines:
-
Volume/MOQ (Minimum Order Quantity): Larger orders often lead to discounts due to economies of scale. Buyers should negotiate favorable terms based on their purchasing power.
-
Specifications/Customization: Customized machines tailored to specific needs may come at a premium. Clear communication of requirements can help avoid unexpected costs.
-
Materials: The choice of materials directly impacts the price. Higher-quality materials may increase initial costs but can lead to lower maintenance and longer lifespan, affecting the Total Cost of Ownership (TCO).
-
Quality/Certifications: Machines with recognized certifications may be priced higher but can provide peace of mind regarding safety and performance standards.
-
Supplier Factors: Supplier reputation, reliability, and service level can influence pricing. Established suppliers may charge more due to their proven track record.
-
Incoterms: Understanding the terms of shipping and delivery (e.g., FOB, CIF) can help buyers calculate the total landed cost of the vending machines, which is essential for accurate budgeting.
Buyer Tips for Cost Efficiency
International B2B buyers should keep the following tips in mind:
-
Negotiate Wisely: Always engage in price negotiations with suppliers. Leverage your purchasing power and market knowledge to secure better terms.
-
Assess Total Cost of Ownership (TCO): Evaluate not just the initial purchase price but also long-term costs such as maintenance, energy consumption, and potential downtime. This holistic view can reveal the true cost-effectiveness of different options.
-
Understand Pricing Nuances: Prices can vary significantly based on regional market conditions. For example, buyers from Europe might find different pricing structures compared to those in Africa or South America. Familiarize yourself with local market trends and supplier behaviors to navigate pricing effectively.
-
Explore Multiple Suppliers: Don’t settle for the first offer. Engaging with multiple suppliers can help you compare prices, quality, and service, ultimately leading to a more informed decision.
Disclaimer
Prices for small vending machines can fluctuate based on various factors, including raw material costs, labor rates, and currency exchange rates. It is recommended to obtain updated quotes from multiple suppliers to ensure competitive pricing and accurate budgeting.
Spotlight on Potential small vending machine for sale Manufacturers and Suppliers
- (No specific manufacturer data was available or requested for detailed profiling in this section for small vending machine for sale.)*
Essential Technical Properties and Trade Terminology for small vending machine for sale
Key Technical Properties of Small Vending Machines
When considering the purchase of small vending machines, understanding their technical properties is crucial for ensuring optimal performance and longevity. Here are several essential specifications to consider:
-
Material Grade
The material used in vending machines typically includes stainless steel, aluminum, or high-grade plastic. Stainless steel is preferred for its durability and resistance to corrosion, which is particularly important in humid climates. B2B buyers should assess material grades to ensure the machine can withstand environmental conditions and frequent use. -
Size and Capacity
The dimensions and internal capacity of vending machines affect the number of products they can hold. Smaller units may be suitable for limited space or specialized products, while larger machines can accommodate a broader inventory. Understanding size and capacity helps buyers optimize their product offerings based on their target market’s needs. -
Power Consumption
Power efficiency is a critical consideration, especially in regions with high energy costs. Vending machines with lower power consumption ratings can lead to significant cost savings over time. Buyers should look for energy-efficient models that comply with local energy regulations, as this can also enhance their marketability. -
Payment Systems
Modern vending machines often come equipped with multiple payment options, including cash, credit/debit cards, and mobile payments. The integration of diverse payment systems is essential for catering to a wide customer base. Buyers should prioritize machines that offer flexible payment solutions to enhance user convenience and increase sales. -
Temperature Control
For vending machines that sell perishable items, effective temperature control is vital. Buyers should look for machines with adjustable temperature settings and reliable refrigeration systems to ensure product quality and safety. Understanding the cooling technology used can also inform decisions about suitable product offerings.
Common Trade Terminology
Navigating the procurement process of vending machines involves familiarizing oneself with industry-specific terminology. Here are some key terms that B2B buyers should know:
-
OEM (Original Equipment Manufacturer)
This term refers to companies that produce parts or equipment that may be marketed by another manufacturer. When sourcing vending machines, working with OEMs can ensure that the machines are built to specific standards and can be customized as needed. -
MOQ (Minimum Order Quantity)
MOQ indicates the smallest number of units a supplier is willing to sell. Understanding MOQ is crucial for budgeting and inventory planning. Buyers should negotiate MOQs that align with their market demand to avoid overstocking or stockouts. -
RFQ (Request for Quotation)
An RFQ is a document sent to suppliers requesting pricing and terms for specific products. It is an essential tool for comparing costs and negotiating better deals. Buyers should prepare detailed RFQs that specify their requirements to receive accurate and competitive quotes. -
Incoterms (International Commercial Terms)
These are standardized trade terms that define the responsibilities of buyers and sellers in international transactions. Understanding Incoterms helps buyers clarify shipping responsibilities, insurance, and risk management, which is particularly important in cross-border trade. -
Lead Time
Lead time refers to the period between placing an order and receiving the product. It encompasses manufacturing, processing, and shipping times. Buyers should factor in lead times when planning inventory and sales strategies to ensure timely product availability.
By grasping these essential technical properties and trade terms, B2B buyers can make informed decisions that enhance their procurement processes and ultimately drive business success in the vending machine market.
Navigating Market Dynamics, Sourcing Trends, and Sustainability in the small vending machine for sale Sector
Market Overview & Key Trends
The small vending machine sector is witnessing significant transformation driven by technological advancements and changing consumer behaviors. Key global drivers include the increasing demand for convenience and the rise of cashless payment systems, which are reshaping how businesses approach vending solutions. For B2B buyers in Africa, South America, the Middle East, and Europe, the emphasis on multifunctionality—machines that offer snacks, beverages, and even healthy options—has become paramount.
Emerging trends in sourcing include a shift towards smart vending machines equipped with IoT capabilities. These machines not only streamline inventory management through real-time data analytics but also enhance customer engagement through personalized offerings. B2B buyers should consider vendors that provide robust software support, allowing for the integration of loyalty programs and customer feedback systems, which can significantly enhance user experience and retention.
Moreover, sustainability is increasingly influencing purchasing decisions. Buyers are looking for machines that utilize energy-efficient technologies and sustainable materials. In regions like Europe, regulatory frameworks are pushing for greener solutions, making it essential for international buyers to align with suppliers who prioritize eco-friendly practices. Understanding these market dynamics will enable B2B buyers to make informed decisions that align with their strategic goals.
Sustainability & Ethical Sourcing in B2B
Sustainability in the small vending machine sector extends beyond the machines themselves; it encompasses the entire supply chain. B2B buyers must recognize the environmental impact associated with manufacturing and operating vending machines, including energy consumption and waste generation. Choosing suppliers who prioritize sustainability can significantly mitigate these impacts.
Ethical sourcing is crucial for fostering long-term partnerships. Buyers should seek vendors that demonstrate transparency in their supply chains, ensuring that materials are sourced responsibly and ethically. Certifications such as ISO 14001 for environmental management systems or the Forest Stewardship Council (FSC) for wood products can serve as indicators of a supplier’s commitment to sustainability.
Incorporating ‘green’ materials—like recycled plastics or biodegradable components—into vending machines not only meets consumer demand for environmentally friendly products but also enhances brand reputation. By prioritizing sustainable practices, B2B buyers can contribute to a circular economy and appeal to an increasingly eco-conscious market, particularly in regions like Europe and North America where sustainability is a key consumer driver.
Brief Evolution/History
The evolution of vending machines dates back to the early 1880s, initially serving simple functions like dispensing postcards and stamps. Over the decades, the industry has expanded significantly, influenced by technological innovations and changing consumer preferences. The 21st century has seen the introduction of digital payment systems and smart technology, marking a new era for vending machines.
Today, small vending machines are not only designed for convenience but also for a diverse range of products, including healthy snacks and beverages. This evolution reflects broader trends in consumer behavior, with a growing emphasis on convenience and health-conscious options. Understanding this historical context allows B2B buyers to appreciate the trajectory of the market and the importance of adapting to ongoing changes in consumer expectations and technology.
Related Video: The New Trade Order: How Geopolitics Is Breaking Global Supply Chains – IV
Frequently Asked Questions (FAQs) for B2B Buyers of small vending machine for sale
-
What should I consider when vetting suppliers of small vending machines?
When vetting suppliers, prioritize their reputation and experience in the vending machine industry. Look for verified customer reviews, case studies, and any certifications that indicate quality standards compliance. It’s beneficial to request references from previous clients, especially those within your region, to gauge their reliability and service quality. Additionally, assess their production capabilities and inquire about their adherence to international trade regulations to ensure a smooth transaction. -
Can I customize the vending machines to suit my brand?
Yes, many suppliers offer customization options for their vending machines. This can include branding with your logo, color schemes, and even specific product offerings tailored to your target market. When negotiating with suppliers, clarify your customization requirements upfront and request samples or prototypes if possible. This ensures that the final product aligns with your brand identity and meets your customers’ preferences. -
What are typical minimum order quantities (MOQ) and lead times for vending machines?
MOQs can vary significantly by supplier and the type of vending machines you’re interested in. Generally, expect an MOQ ranging from 10 to 50 units for small vending machines. Lead times can also differ, often spanning from 4 to 12 weeks depending on customization and production schedules. Discuss these factors early in negotiations to align expectations and plan your inventory accordingly. -
What payment options should I consider when purchasing vending machines internationally?
International transactions often involve various payment methods, including wire transfers, letters of credit, and escrow services. Ensure you choose a secure payment method that protects both parties. It’s advisable to negotiate payment terms upfront, such as a deposit followed by the balance upon delivery. This approach mitigates risks and provides assurance regarding the quality of the machines before full payment is made. -
How can I ensure quality assurance and certifications for vending machines?
Request detailed information on quality assurance processes from your supplier. Inquire about certifications such as ISO 9001 or CE marking, which demonstrate compliance with international quality standards. Additionally, consider requesting third-party inspection services before shipment to verify that the machines meet your specifications. This step is crucial, especially for large orders, to avoid costly discrepancies upon delivery. -
What logistics considerations should I keep in mind when importing vending machines?
Logistics can be complex when importing vending machines, so it’s essential to partner with a reliable freight forwarder experienced in handling such equipment. Discuss shipping methods, insurance, and customs clearance procedures to avoid delays. Be aware of any import tariffs or regulations specific to your country, and ensure all documentation is in order to facilitate a smooth import process. -
How can I handle disputes with suppliers effectively?
To handle disputes effectively, establish clear communication channels with your supplier from the outset. Document all agreements, specifications, and communications to provide a reference in case of disagreements. If a dispute arises, try to resolve it amicably through negotiation. If necessary, consider mediation or arbitration as alternative dispute resolution methods, which can be less costly and time-consuming than legal action. -
What are the best practices for maintaining vending machines once purchased?
Once you have acquired vending machines, regular maintenance is crucial for longevity and performance. Establish a routine inspection schedule to check for functionality, cleanliness, and inventory levels. It’s also advisable to train staff on basic troubleshooting and maintenance tasks. Additionally, keep a direct line of communication with your supplier for support and spare parts availability, ensuring minimal downtime for your machines.
Strategic Sourcing Conclusion and Outlook for small vending machine for sale
In navigating the competitive landscape of small vending machines, strategic sourcing emerges as a vital approach for international B2B buyers. By aligning procurement strategies with market demands and supplier capabilities, businesses can optimize costs, enhance product offerings, and improve supply chain resilience. Key takeaways include:
- Market Research: Understand regional preferences and trends to select machines that cater to local tastes and needs.
- Supplier Relationships: Build strong partnerships with manufacturers and distributors to ensure reliability and flexibility in procurement.
- Technology Integration: Leverage innovations such as cashless payment systems and remote monitoring to enhance operational efficiency and customer experience.
As the demand for small vending machines continues to grow across Africa, South America, the Middle East, and Europe, now is the time to act. By prioritizing strategic sourcing, businesses can position themselves for success in an evolving market landscape.
Looking ahead, international B2B buyers are encouraged to explore diverse sourcing options and invest in technologies that can elevate their vending solutions. Engaging with suppliers who understand local markets will not only ensure competitive pricing but also foster sustainable growth. Embrace this opportunity to redefine your vending strategy and capitalize on emerging trends.
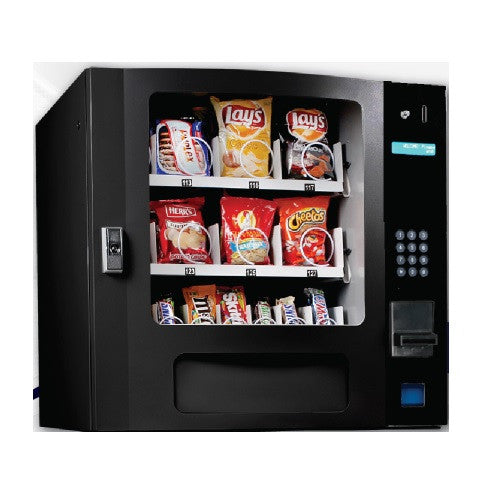
Illustrative Image (Source: Google Search)